加热炉自控制系统
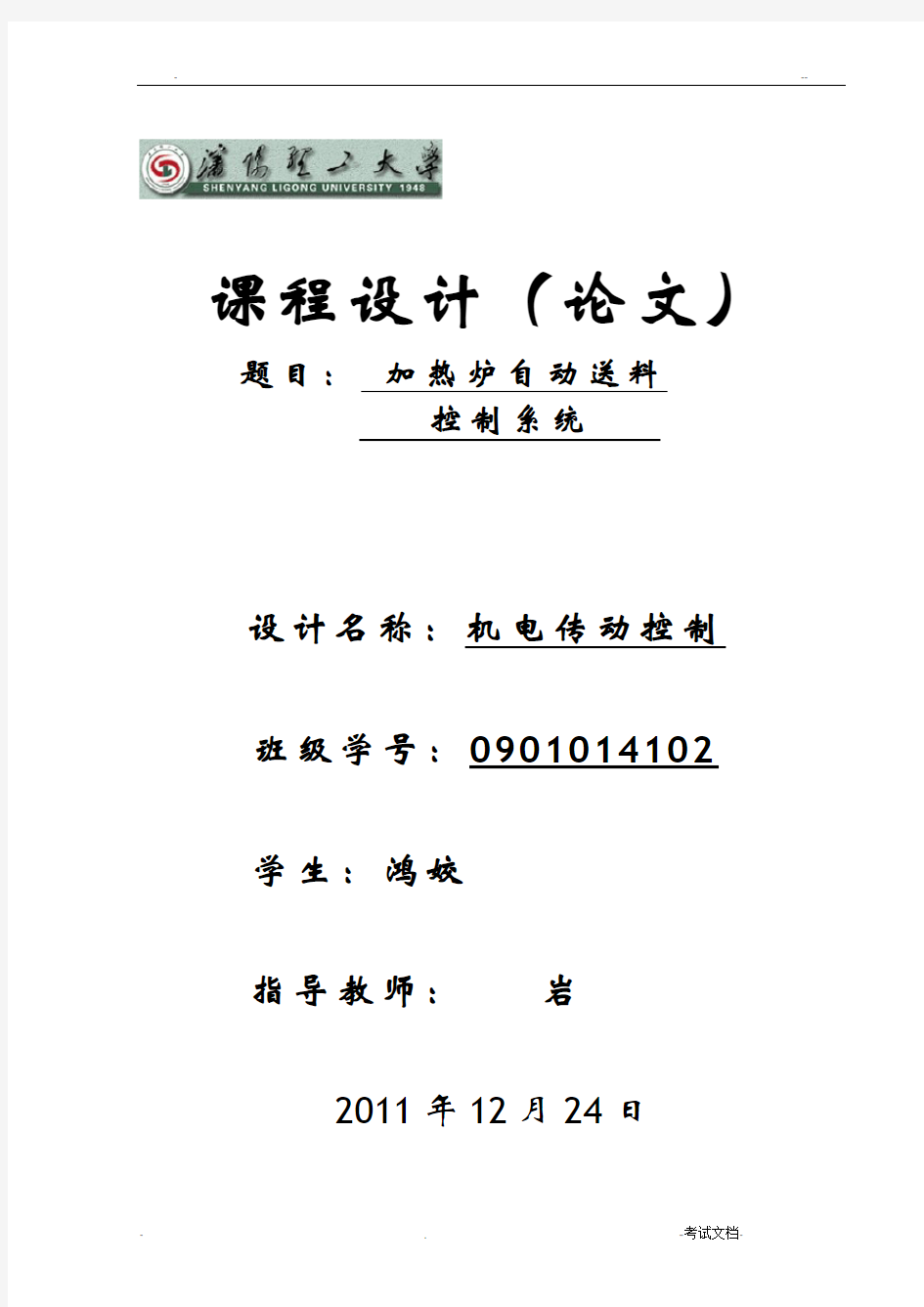

- --
课程设计(论文)
题目:加热炉自动送料
控制系统
设计名称:机电传动控制
班级学号:0901014102
学生:鸿姣
指导教师:岩
2011年12月24日
目录
前言 (2)
课程设计的任务和要求 (3)
课程设计的任务 (3)
设计容: (3)
设计要求: (3)
课程设计的基本要求 (3)
控制要求 (3)
总体设计 (5)
PLC选型: (5)
PLC端子接线 (6)
PLC程序设计 (7)
设计思想 (8)
PLC顺序功能图 (9)
PLC梯形图 (11)
程序调试说明 (18)
结束语 (19)
参考文献 (20)
前言
加热炉自动控制(automatic control of reheating furnace)对加热炉的出口温度、燃烧过程、联锁保护等进行的自动控制.早期加热炉的自动控制仅限控制出口温度,方法是调节燃料进口的流量.现代化大型加热炉自动控制的目标是进一步提高加热炉燃烧效率,减少热量损失.为了保证安全生产,在生产线中增加了安全联锁保护系统.
这种控制的主要目的是在工艺允许的条件下尽量降低过剩空气量,保证加热炉高效率燃烧.简单的控制方案是通过测量烟道气中的含氧量,组成含氧量控制系统,或设计燃料量和空气量比值调节系统,再利用含氧量信号修正比值系数.含氧量控制系统能否正常运行的关键在于检测仪表和执行机构两部分.现代工业中都趋向于用氧化锆测氧技术检测烟道气中的含氧量.应用时需要注意测量点的选择、参比气体流量和锆管温度控制等问题.加热炉燃烧控制系统中的执行机构特性往往都较差,影响系统的稳定性.一般通过引入阻尼滞后或增加非线性环节来改善控制品质.
在加热炉燃烧过程中,若工艺介质流量过低或中断烧嘴火焰熄灭和燃料管道压力过低,都会导致回火事故,而当燃料管道压力过高时又会造成脱火事故.为了防止事故,设计了联锁保护系统防止回火和温度压力选择性控制系统防止脱火.
联锁保护系统由压力调节器、温度调节器、流量变送器、火焰检测器、低选器等部分组成.当燃料管道压力高于规定的极限时,压力调节系统通过低选器取代正常工作的温度调节系统,此时出料温度无控制,自行浮动.压力调节系统投入运行保证燃料管道压力不超过规定上限.当管道压力恢复正常时,温度调节系统通过低选器投入正常运行,出料温度重新受到控制.当进料流量和燃料流量低于允许下限或火焰熄灭时,便会发出双位信号,控制电磁阀切断燃料气供给量以防回火.
随着节能技术不断发展,加热炉节能控制系统正日趋完善.以燃烧过程数学模型为依据建立的最佳燃烧过程计算机控制方案已进入实用阶段.例如,按燃烧过程稳态数学模型组成的微机控制系统已开始在炼油厂成功使用.有时利用计算机实现约束控制,使加热炉经常维持在约束条件边界附近工作,以保证最佳燃烧.随着建立燃烧模型工作的进展和计算机技术的应用,加热炉燃烧过程控制系统将得到进一步的完善.
课程设计的任务和要求
课程设计的任务
设计容:
1)完成《课程设计指导书》所要求的控制循环.
2)按停止按钮,立即停止.
3)要求可以实现回原点、单周期、连续控制.
设计要求:
1)画出端子分配图和顺序功能图
2)设计并调试PLC控制梯形图
3)设计说明书
课程设计的基本要求
控制要求
启动——装料台取料——装料1#炉——夹钳冷却——装料台取料——装料2#炉——台车退到1#炉(1#炉加热完毕)——1#炉出料——卸料台卸料——夹钳冷却——装料台取料——装料1#炉——台车前进到2#炉(2#炉加热完毕)——2#炉出料——卸料台卸料
图1.1 送料系统示意图
总体设计
PLC选型:
西门子公司的SIMATIC S7-200系列属于小型PLC,即可用代替继电器的简单控制场合,也可用于复杂的自动化控制系统.
PLC的控制主机,使用西门子S7-200系列作为整个系统的主控制机,我们使用的是28个输入、8个输出共36个数字量的I\O点的CPU,选用S7-200CPU226.
1、本机的数字输入:32路数字量输入
2、本机的数字输出:16路数字量输出
3、最大的数字量I\O:256
4、最大的模拟量I\O:32AI\32AO
5、扩展模块数量:7个模块
6、部存储器位:256位
7、定时器总数:256定时器
8、计数器总数:256计数器
PLC端子接线
1#炉限位
2#炉限位
冷却槽左限位
冷却槽右限位
夹钳冷却下限位
取料台上限位
取料台下限位
卸料台上限位
卸料台下限位
1#炉上限位
1#炉下限位
2#炉上限位
2#炉下限位
夹紧
松开
上升
下降
左行
右行
冷却槽左行
冷却槽右行
回原点
单周期
连续
启动
停止
PLC程序设计
设计思想
PLC应用系统时,首先是进行PLC应用系统的功能设计,即根据被控对象的功能和工节要求,明确系统必须要做的工作和必备的条件,然后是进行PLC的系统功能分析,即通过分析系统功能,提出PLC控制系统的结构形式、控制信号的种类、数量、系统的规模、布局.最后根据系统分析的结果,具体的确定PLC的机型和系统的具体配置.其控制系统的设计思想及其步骤如下:
1、深入了解和分析被控对象的工艺条件和被控要求,如控制的基本
方式、操作方式.
2、根据被控对象对PLC控制系统的功能要求和所需的输入输出的信
号点数等,选择合适类型的PLC.
3、根据控制要求所需的用户输入输出设备,确定PLC的I\O点数,
并设计I\O端口接线图.
4、根据生产工艺要求,画出系统的工作循环图表.
5、根据系统工作循环图表设计出梯形图.
PLC顺序功能图
PLC梯形图
夹钳下降冷却
左行
下降
上升
夹紧
M0.6 M2.2 M3.2 M4.6 M5.6 M7.1( )
Q0.1 ( ) Q0.2
( )
Q0.3
M0.3
M0.7
M1.3
M1.7
M2.3
M2.7
M3.3 M3.7
M4.3
M4.7
M5.3
M5.7
M7.0
M0.1
M0.5
M1.2
M2.1
M1.5
M2.5
M3.1
M3.6
M4.1
M4.5
M5.1
M5.5
M7.0
( )
Q0.6
M3.5
( )
Q0.5
( )
Q0.4
M1.0M2.4M3.0M3.4M5.4M6.0M6.0
M0.4M2.0M5.0M7.1
M1.4M4.0
M1.1( )
Q0.7
程序调试说明
在程序调试过程中,最开始遇到的问题是发现定时器不开始定时,经过询问同学才知道,原来不止是线圈不能重复,定时器也不能重复使用,否则就会不开始工作.
在运行过程中,PLC上电后,SM0.1得电,然后根据梯形图,逐个按下限位开关和动作按钮,对应的线圈会得电,输出的对应的Q会亮,表示这步运行正常.
在这次运行中,基本实现了课程设计指导书上的要求,即回原点、单周期以及连续的运行要求.
结束语
经过一周的课设,使我对PLC的使用有了进一步的了解.我本来对一些PLC 的梯形图的编写不太熟练,对题目分析的不太准确,但我在老师和同学的帮助下,让我不断地学习、改进、进步,完成了这次课设.虽然其中仍有不足之处,但这让我了解到,人就是在不断实践中进步的.这次课设锻炼了我们的动手和动脑能力,使我对PLC这门课有了进一步的认识,更加激发了我的学习兴趣.相信只要这样学下去,总有成功的一天.