局部阻力计算
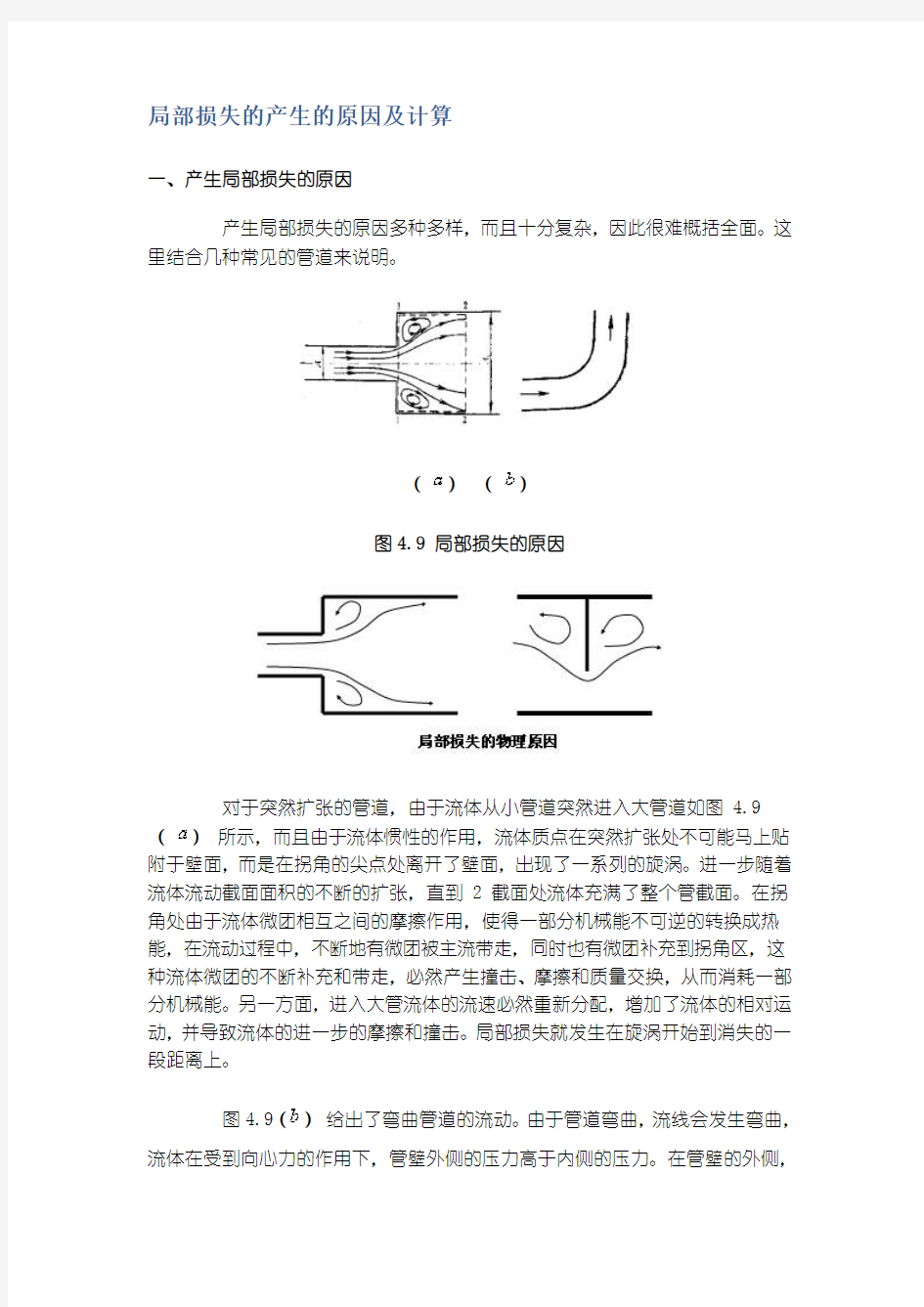
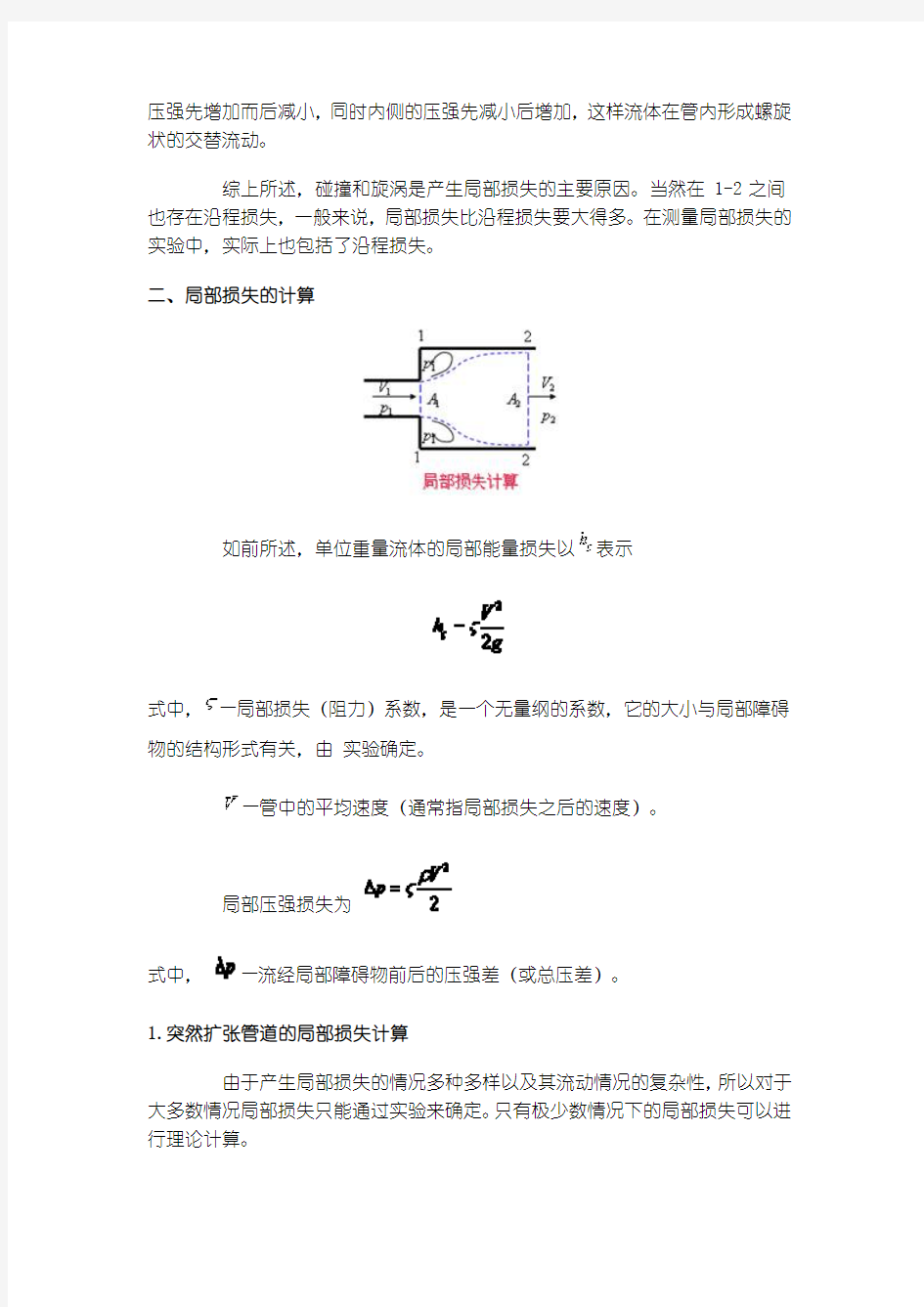
局部损失的产生的原因及计算
一、产生局部损失的原因
产生局部损失的原因多种多样,而且十分复杂,因此很难概括全面。这里结合几种常见的管道来说明。
( ) ( )
图4.9 局部损失的原因
对于突然扩张的管道,由于流体从小管道突然进入大管道如图 4.9 ( ) 所示,而且由于流体惯性的作用,流体质点在突然扩张处不可能马上贴附于壁面,而是在拐角的尖点处离开了壁面,出现了一系列的旋涡。进一步随着流体流动截面面积的不断的扩张,直到 2 截面处流体充满了整个管截面。在拐角处由于流体微团相互之间的摩擦作用,使得一部分机械能不可逆的转换成热能,在流动过程中,不断地有微团被主流带走,同时也有微团补充到拐角区,这种流体微团的不断补充和带走,必然产生撞击、摩擦和质量交换,从而消耗一部分机械能。另一方面,进入大管流体的流速必然重新分配,增加了流体的相对运动,并导致流体的进一步的摩擦和撞击。局部损失就发生在旋涡开始到消失的一段距离上。
图4.9()给出了弯曲管道的流动。由于管道弯曲,流线会发生弯曲,流体在受到向心力的作用下,管壁外侧的压力高于内侧的压力。在管壁的外侧,
压强先增加而后减小,同时内侧的压强先减小后增加,这样流体在管内形成螺旋状的交替流动。
综上所述,碰撞和旋涡是产生局部损失的主要原因。当然在 1-2之间也存在沿程损失,一般来说,局部损失比沿程损失要大得多。在测量局部损失的实验中,实际上也包括了沿程损失。
二、局部损失的计算
如前所述,单位重量流体的局部能量损失以表示
式中,—局部损失(阻力)系数,是一个无量纲的系数,它的大小与局部障碍物的结构形式有关,由 实验确定。
—管中的平均速度(通常指局部损失之后的速度)。
局部压强损失为
式中, —流经局部障碍物前后的压强差(或总压差)。
1.突然扩张管道的局部损失计算
由于产生局部损失的情况多种多样以及其流动情况的复杂性,所以对于大多数情况局部损失只能通过实验来确定。只有极少数情况下的局部损失可以进行理论计算。
对于突然扩大的情况,可以通过理论推导得到局部损失的计算公式。流体在如图 4.9 ( ) 所示的突然扩张的管道内流动,由于流体的碰撞、惯性和附面层的影响,在拐角区形成了旋涡,引起能量损失。由图可见,流体到 2截面充满整个管道。取1-1和2-2截面以及侧表面为控制体,并设截面1处的面
积为 ,参数为 ;截面2处的面积为 ,参数为 ,则根据柏努力方程,有
于是局部损失为
对 1-1和2-2截面运用连续方程,即
对所取得控制面应用动量方程,考虑到 1-1和2-2截面之间的距离比较短,通常可以不计侧表面上的表面力,于是动量方程可写为
将动量方程和连续方程代入的表达式得
令 , ,则局部损失可写为
(4.35)
式中, 分别表示局部损失(阻力)系数。式(4.35)表明,用公式计算局部损失时,采用的速度可以是损失前的也可以是损失后的,但局部损失系数也不同。由式(4.35)及局部损失系数的表达式可以看出,突然扩大的局部损失系数仅与管道的面积比有关而与雷诺数无关,实际上根据实验结果可知,在雷诺数不很大时,局部损失系数随着雷诺数的增大而减小,只有当雷诺数足够大(流动进入阻力平方区)后,局部损失系数才与雷诺数无关。
下面给出的几种比较常见的局部损失系数的计算,且一般情况下,局部损失系数均指对应发生损失后的速度给出的。
2.渐扩管
流体流过逐渐扩张的管道时,由于管道截面积的逐渐扩大,使得流速沿流向减小,压强增高,且由于粘性的影响,在靠近壁面处,由于流速小,以至于动量不足以克服逆压的倒推作用,因而在靠近壁面处出现倒流现象从而引起旋涡,产生能量损失。渐扩管的扩散角 越大,旋涡产生的能量损失也越大,
越小,要达到一定的面积比所需要的管道也越长,因而产生的摩擦损失也越大。
所以存在着一个最佳的扩散角 。在工程中,一般取 ,其能量损失
最小。 在 左右损失最大。渐扩管的局部损失系数为
(4.36)
3.突然缩小管道
图 4.10 突然缩小的管道
流体在突然缩小的管道中流动如图 4.10 所示,当管道的截面积突然收缩时,流体首先在大管的拐角处发生分离,形成分离区,然后在小管内也形成一个分离区。最后才占据管道的整个截面。局部损失系数的确定可以根据实验确定。对于不可压缩流动,实验结果为
(4.37)
在特殊情况下, ,即流体从一个大容器进入管道且进口处
具有尖锐的边缘时,局部损失系数为 。若将进口处的尖锐边缘改成圆角
后,则局部损失系数 随着进口的圆滑程度而大大降低,对于圆形匀滑的边缘
;入口极圆滑时 。
4.渐缩管
为了减小突然缩小的流动损失,通常采用渐缩管。在渐缩管中,流线不会脱离壁面,因此流动阻力主要是沿流程的摩擦引起的。对应于缩小后的流速的
局部损失系数为 ,由此可见,在渐缩管中的流动损失很小。
5.弯管
图 4.11 流体在弯管内的流动
在弯管内的流动由于流体的惯性,流体在流过弯管时内外壁面的压力分布不同而 流线发生弯曲,流体受到向心力的作用,这样,弯管外侧的压强就高
于内侧的压强 如图 4.11 所示。 图中 区域内,流体压强升高,点以后,
流体的压强渐渐降低。与此同时,在弯管内侧的 区域内,流体作增速降压
的流动, 区域内是增压减速流动。在 和 这两个区域内,由于流
动是减速增压的,会引起流体脱离壁面,形成漩涡区,造成损失。此外,由于粘性的作用,管壁附近的流体速度小,在内外压力差的作用下,会沿管壁从外侧向内侧流动。
同时,由于连续性,管中心流体会向外侧壁面流去。从而形成一个双旋涡形状的横向流动,整个流动呈螺旋状。横向流动的出现,也会引起流体能量的损失。弯管的局部损失系数可按下列经验公式计算:
(4.38a)
系数 的计算式为
(4.38b) 式中, 是弯管中线的曲率半径, 为管径。
4.4.2减小和利用局部损失
在各种管道的设计中,应尽量减小局部损失。为了减小局部损失,应尽量避免流通截面积发生突然的变化,在截面积有较大变化的地方常采用锥形过渡,在要求比较高的管道中应采用光滑的流线型壁面。以下举几个例子来说明减小局部损失的方法。
1、弯曲管道
由弯管的局部损失计算公式可知,弯管的局部损失取决于管道的直径、曲率半径和管道的弯曲角。因此在设计管道时,为了减小局部损失,应尽量避免
采用弯转角过大的死弯。对于直径较小的热力设备管道,通常采用 。
对于直径较大的排烟风道来说,横向的二次流动比较突出。为了减小二次流动损失,一方面可以适当的加大管道的曲率半径,以减小流体转弯时的离心力,另一方面通常在弯管内安装导流叶片如图 4.12 所示。这样既可减小弯道两侧的压强差,又可以减小二次流影响的范围。根据实验,在没有安装导流叶片的情况下,
直角弯管的 ;安装簿板弯成的导流叶片后,;当导流叶片呈流线
月牙形时, 。可见当安装导流叶片后,并适当选择导流叶片的形状,对减小局部损失有明显的效果。
2、流通截面的变化
将突然扩张的管道改为渐扩管,由于涡流区的大小和涡流强度的减小,其局部损失有很大的改善。但是当扩张(或收缩)的面积比一定时,渐变管的长度相应地加长,使得沿程损失有所增加,所以设计时应取最佳值。管长的增加会增加管道设计的成本或带来制造上的困难。有些情况下,还要受到几何空间的限制,因此在管道设计中,应根据具体问题、具体情况全面折衷考虑。
在设计渐扩管时,当面积比较大时,可用隔板或用几个同心扩张管来达到正常的扩张角。扩张角一般控制在 的范围内。
图 4.12 装有导流片的弯管
( a)渐扩管的扩张角 (b)具有隔板的渐扩管
图 4.13 渐扩管的扩张角
3、三通
工程中有各种各样的三通接头,其局部阻力系数也各不相同,使用时可查阅流体力学手册。这里说的是为了减少流体流过三通的能量损失,可以在总管
中根据支管的流量安装分流板和合流板如 图 4.15所示。从减小局部损失的角度来讲,应尽量避免采用直角三通 。
图 4.14三通管道中的合流板和分流板
4、局部损失的利用
在日常生活中,局部损失还可以被利用。阀门就是利用局部损失来控制流量的一个例子。在航空发动机上,为了防止燃烧室出口的高温高压燃气进入滑油腔内,可以利用如图 4.16 所示的封严装置将燃气和滑油腔隔开。封严装置的原理是根据燃气每经过一个密封齿,压强就有所降低,经过几个密封齿后,压强就降低到与滑油腔内的压强基本相等。这样最后一个齿的前后的压强差很小,达到阻隔燃气流入滑油腔的目的,起到密封的作用。
图 4.15 封严装置
4.4.3流动损失叠加及当量长度法
一、流动损失的计算
一般情况下,流体在管路系统中的流动必将存在若干沿程损失和局部损失,总的能量损失符合叠加原理,在不考虑其相互干扰的情况下,单位重量流体沿流程的总损失为式 4.6
二、当量长度法
由上面的沿程损失和局部损失计算公式可知,这两种损失均与流速的平方成正比。假定能够找出在流速相同的条件下,某段长度的管件能产生同样长度的沿程损失,这段长度就叫做该管件的当量长度。它能在流动损失等效的条件下,以某段等经直管的沿程损失代替局部损失,这种当量长度法对于管路系统的计算是非常方便的。这种当量关系为
即
( 4.39)
式中 称为该管件的当量长度,或者称为此局部损失的等价管长。
如果管路系统的管径和沿程阻力损失系数处处相等,则有
于是
( 4.40)
引用了当量长度的概念,可方便地估算出局部损失所占的比例,为复杂管路系统的能量损失的计算提供了简便的分析方法。
4.4.4 进口起始段内的流动
图 4.16 进口起始段内的流动
在各种管道计算中,会遇到管道起始段的流动问题,本节讨论进口起始段的沿程能量损失。在这段管流中,流体质点的运动与完全发展的管内流动完全不同,流体质点的速度在不断的变化。图 4.17 给出了进口比较圆滑的圆管进口段内的流动。流体从进口几乎均匀地流入管内,由于粘性的影响,在壁面上速度为零,然后沿法线方向流速逐步增加到中心线上的速度。另一方面,随着流体的不断流入,管壁对流动的影响加大,但因在流动中要满足连续方程,即流量保持不变,因此,管轴附近的流体将相应加速。在这个过程中,流体质点存在着从管壁到管轴的横向运动,且横截面上的速度分布也发生了变化,直到轴线上的速度达到该流量下的完全发展的最大速度为止,此时即可认为进口初始段的流动过程结束。下面分别讨论进口起始段长度的计算方法和能量损失。
一、进口起始段长度
从进口开始到管中形成完全发展的流动时对应的这段流程定义为进口
起始段.进口起始段的长度用 表示.
一般情况下,对于比较光滑的进口,管中完全发展的流动是层流流动,此时进口起始段的长度可按如下方法推得.如果管道轴线上的流动速度
作为起始段结束,则起始段长度为
(4.41) 将 代入上式,可得
工程上常将 作为起始段结束,则起始段长度为
(4.42) 如果把 代入上式,可得
(4.43)
如果管中完全发展的流动为湍流流动,则根据大量实验结果可知,若按
作为起始段结束,则起始段长度为 ;若按
作为起始段结束,则起始段长度为 。
对于进口比较尖锐的管道,流体进入管道是将出现先收缩后扩张的离壁现象,其间管壁对流体的影响减弱,相应起始段的长度将有所增加。
流动损失测量装置
二、进口起始段的能量损失
在进口起始段内,不仅存在着由于摩擦影响引起的沿程损失,而且也存在流体质点横向脉动而引起的局部损失,因此 进口起始段的能量损失应为这两
者的之和。设 局部损失系数为 ,则 起始段的能量损失为
( 4.44)
对于层流流动,当管道进口尖锐时, ;当管道进口圆滑时,
。
对于湍流流动,当管道进口尖锐时, ;当管道进口圆滑时, 。
从以上数据可以看出,在同样流速下,湍流流动的 局部损失比 层流时小得多,这主要是由于湍流流动时,由于流体质点的无规则横向脉动,使得进口段湍流脉动所占的比例相对较小。
工程计算中,常常将 局部损失折合到沿程损失中一起计算。
当起始段内的流动为层流时,取沿程损失系数 ,当 时,能量损失为
( 4.45) 式中 A 为实验常数,水的实验常数列入下表中:
表 4-4 水的实验常数A
2.5 5 7.5 10 12.5 15 17.5 20 25 28.75
A 122 105 96.66 88 82.4 79.16 76.14 74.375 71.5 69.56
如果 当 时,能量损失为
( 4.46)
对于管道内的湍流流动,或管长 , 通常不计进口段的流动损失。
在工程中,会涉及到许多管道设计与计算问题。除了工程中的石油、化工、建筑、供暖和水利中的管路系统外,在航空、航天中的诸如飞机滑油系统和发动机起动管路系统、飞机空调系统等都会遇到管路计算问题。
工程中所遇到管路设计与计算问题多种多样,遇到的管件类型以及所涉及的物理量也很多,但管路设计与计算中所遇到的典型情况一般有三类。这三类基本问题为:
1)已知管道布局、 几何尺寸 和管路系统允许的 压力降 ,求通过的 流量 (确定管道的输送能力)。
2)已知 管道布局 、 几何尺寸 和通过的 流量 ,求流动 损失 ,即确定管路系统的压力降。
3)已知管道布局、通过的 流量 和允许的 压力降 ,确定管路 几何尺寸 。
对于上述1)、3)两类问题,通常需要多次的迭代计算。具体计算可
假设一个沿程损失系数 ,按总的损失计算确定流速 ,并计算雷诺数 ,
判别流动状态,然后对假设的 进行校核,直到求出较为准确地 后,最后用
总的能量损失公式计算速度 ,从而 求出 通过管道的流量或管径 。对于上
述的第2)种情况,若能事先计算出 ,则根据 可以确定流动状态及 该 流
动所属的流动范围,亦即确定 ,可直接确定管路的压力降。
根据前面的讨论,一条管路中的能量损失等于各段上的沿程损失和局部损失之和,即
在管路设计之前,通常要进行经济核算。若管径大,初期投资大,流动损失小,所需动力设备小,经常运转的费用小。
工程中需要先定出经济流速,可根据输送的流量定出合适的管径。可见管路中能量损失的计算是管路计算的关键。
在水力机械中经常用到管路特性曲线。所谓的管路特性曲线是指一条管路上的能量损失与流量之间的函数关系。
管路计算中的经济核算
4.5.1串联管路的计算
串联管路是指各种不同(或相同)直径的管路 依次连接 组成的管路系统如图4.18 所示。
在不可压缩流动中,对于直径相同的同径串联管道,由于管道截面积相同,通过管道各截面上的流量相等,因此通过各截面上的平均流速也 相等 。对于直径不同的串联管道,根据连续方程,通过管道各截面上的流量仍相等,但平均流速不再相等。无论是同径管道还是异径串联管道,计算的基本原则为: 1)串联管路中,各管段的流量相等;2)串联管路系统的总损失等于各种流动损失之和,即:
( 4.47)
(4.48)
对于图 4.17 的 管路系统,流体自容器 A经串联管路系统流入容器B,对于两容器的自由液面应用柏 努力方程 得
图 4.18 串联管路
当自由液面的压强为大气压强时, , 当容器足够大时,
,代入上式得
( 4.49)
即水位的降低用来克服各种流动损失。
当已知通过管道的流量和管道的几何尺寸时,即可利用连续方程求出流量和雷诺数,由 可以确定 ,并由管件具体形式确定局部损失系数 ,从而确定总的流动损失。
当已知总的流动损失和通过管道的流量时,采用迭代法确定管道的直径。可以先假设一个流速 ,由此求出 、 、 和 ,比较计算出的
与已知的总损失 的差别,调整流速 ,重新计算,直到两者误差在允许的范围内。
当已知总的流动损失和管道的几何尺寸时,也同样采用迭代法确定管道的流量。可以先假设一个 ,求出流速 ,之后计算 ,再求新的 值,
由 计算新的速度,直到收敛为止。
4.5.2并联管路的计算
所谓的并联管道是指 如 图 4.18 示的各管道进口汇合在一起,出口也汇合在一起,即从一点分叉又在另一点汇合的管路称为并联管路。并联管路系统各支管可以是同径并联管路,也可以是异径并联管路。
并联管路的特点是各支管的流量不同,但总流量等于各支管流量之和,并联管路中,各支管的流动损失 相同(这里假设汇合后的流体参数已经掺混均匀),根据并联管路的特点即可得出并联管路两个重要的计算公式为
( 4.50)
(4.51)
在并联管路的计算中,虽然各管段的 流动损失 相同,但由于各管
段的流量和管径不同,因此各支管的沿程损失系数 并不相同。为了简化计算,
图 4.18 并联管路
对工程中的湍流问题常按阻力平方区计算。 计算步骤如下:
已知 总流量和管道尺寸 ,求 流量分配 ,用试凑法
1、设过管1的流量 ,求管1的流动损失 ;
2、用 求其他管的流量 , , … …, 及 ;
3、设总流量 在各管中按 相同的比例分配,即
4、根据 计算各管中的流动损失并校正流量的正确性。
4.5.3管网计算基础
管网是指有一系列管道相互连接组成的管路系统,分为树状管网和环状管网。树状管网管线短,投资少。但可靠性较差。环状管网管线长,投资高,但当局部管线损坏时,可以用其它管线代替,便于维护。
树状管网:几根管道自一点分叉而不再汇合的管路系统叫分叉管路系统。分叉管路系统的分枝上又有分叉管路,一直分下去的管路系统。树状管路是工程中常见的管路形式,在供水、供气管路中广泛采用。 枝状 管路是将主干道中的流体引向不同的地点,以满足用户的需求。图 4.19(a) 给出了 树状管网 的示意图,假设管路中各段的长度、直径和流量已知,可以计算出管路系统中的能量损失。每一分支可以按串联管路计算,即
计算出每一分枝管路上的 ,其中的最大者即是所要求的树状管网系统的能量损失。
(a) 树状管网 (b) 环状管网
图 4.19 树状管网和环状管网
环状管网:图4.19 b) 为 环状管网 示意图 。管网计算的基本出发点为:树状根据能量方程,环状管网的任意闭合环路上各管段的流动损失总和等于零。每一节点上流入的流量等于流出的流量。
在设计新管网时,其计算步骤如下:
1、 确定管网布局方式(树状、环状或混合状),管线位置和各管段的长度。
2、 根据用户的流量需求,确定各管段的流量,选择各管段的经济流速,并根据流量确定各管段的管径。
3、 计算各管段的流动损失,根据水头控制点确定供流设备的供流水头(如水塔高度等)。一般选取供流设备的最远供流端(图 (a) 中的点
4、9和 (b) 中的点 8、12)为水头的控制点,应满足这些最不利点的水头要求。
4、对于环状管网,需要调整流量分配来满足各闭合环路的流动损失为零的要求。
实验三 管路局部阻力系数测定实验
实验三 管路局部阻力系数测定实验 一、实验目的要求: 1.掌握三点法,四点法测量局部阻力系数的技能。 2.通过对圆管突扩局部阻力系数的表达公式和突缩局部阻力系数的经验公式的实验与分析,熟悉用理论分析法和经验法建立函数式的途径。 3.加深对局部阻力损失机理的理解。 二、实验成果及要求 1.记录计算有关常数。 实验装置台号No d 1=D 1= 1.4 cm , d 2=d 3= d 4= D 2=1.9 cm , d 5=d 6=D 3= 1.4 cm , l 1—2=12cm , l 2—3=24cm , l 3—4=12cm , l 4—B =6cm , l B —5=6cm , l 5—6=6cm , 2 2 1) 1(A A e - ='ξ= 0.21 ,) 3 1(5.05A A s - ='ξ= 0.23 。 2.整理记录、计算表。 表1 记录表
表2 计算表 3.将实测ζ值与理论值(突扩)或公认值(突缩)比较。 三、实验分析与讨论 1.结合实验成果,分析比较突扩与突缩在相应条件下的局部损失大小关系: 1)不同R e 的突扩ξe 是否相同? 2)在管径比变化相同的条件下,其突扩ξe 是否一定大于突缩ξs ? 答:由式 g v h j 22 ζ = 及 ()21d d f =ζ 表明影响局部阻力损失的因素是v 和21d d 。由于有 突扩:2 211???? ? ?-=A A e ζ
突缩:???? ? ?-=2115.0A A s ζ 则有 () () 2 12 212115.0115.0A A A A A A K e s -= - -= = ζζ 当 5.021?A A 或 707.021?d d 时,突然扩大的水头损失比相应的突然收缩的要大。在本实验最大流量Q 下,突然扩大损失较突然缩小损失约大一倍,即817.160.3/54.6==js je h h 。 21d d 接近于1时,突然扩大的水流形态接近于逐渐扩大管的流动, 因而阻力损失显著减小。 2.结合流动仪演示的水力现象,分析局部阻力损失机理何在?产生突扩与 突缩局部阻力损失的主要部位在哪里?怎样减小局部阻力损失? 答:流动演示仪1-7型可显示突扩、突缩、渐扩、渐缩、分流、合流、阀道、绕流等三十多种内、外流的流动图谱。据此对于局部阻力损失的机理分析如下: 从显示的图谱可见,凡流道边界突变处,形成大小不一的漩涡区。漩涡是产生损失的主要根源。由于水质点的无规则运动和激烈的紊动,相互磨擦,便消耗了部分水体的自储能量。另外,当这部分低能流体被主流的高能流体带走时,还须克服剪切流的速度梯度,经质点间的动能交换,达到流速的重新组合,这也损耗了部分能量。这样就造成了局部阻力损失。 从流动仪可见,突扩段的漩涡主要发生在突扩断面以后,而且与扩大系数有关,扩大系数越大,漩涡区也越大,损失也越大,所以产生突扩局部阻力损失的主要部位在突扩断面的后部。而突缩段的漩涡在收缩断面均有。突缩前仅在死角区有小漩涡,且强度较小,而突缩的后部产生了紊动度较大的漩涡环区。可见产生突缩水头损失的主要部位是在突缩断面后。 从以上分析可知,为了减小局部阻力损失,在设计变断面管道几何边界形状时应流线型化或昼接近流线形,以避免漩涡的形成,或使漩涡区尽可能小。如欲减小管道的局部阻力,就应减小管径比以降低突扩段的漩涡区域;或把突缩进口的直角改为圆角,以消除突缩断面后的漩涡环带,可使突缩局部阻力系数减小到原来的21~101。突然收缩实验管道使
阻力损失的计算方法
1.5阻力损失 1.5.1两种阻力损失 直管阻力和局部阻力 化工管路主要由两部分组成:一种是直管,另一种是弯头、三通、阀门等各种管件。 直管造成的机械能损失称为直管阻力损失(或称沿程阻力损失) 管件造成的机械能损失称为局部阻力 注意 将直管阻力损失与固体表面间的摩擦损失相区别 阻力损失表现为流体势能的降低 由机械能衡算式(1-42)可知: ρρρ212211P P g z p g z p h f -=??? ? ??+-???? ??+= (1-71) 层流时直管阻力损失 流体在直管中作层流流动时,因阻力损失造成的势能差可直接由式(1-68)求出: 232d lu μ?= ? (1-72) 此式称为泊稷叶(Poiseuille)方程。层流阻力损失遂为: 232d lu h f ρμ= (1-73) 1.5.2湍流时直管阻力损失的实验研究方法 实验研究的基本步骤如下: (1)析因实验-寻找影响过程的主要因素
对所研究的过程作初步的实验和经验的归纳,尽可能的列出影响过程的主要因素。对湍流时直管阻力损失f h ,经分析和初步实验获知诸影响因素为: 流体性质:密度ρ、粘度μ; 流动的几何尺寸:管径d 、管长l 、管壁粗糙度ε(管内壁表面高低不平): 流动条件:流速u 。 于是待求的关系式为: ) ,,,,,(ερμu l d f h f = (1-74) (2)规划实验-减少实验工作量 因次分析法的基础是:任何物理方程的等式两边或方程中的每一项均具有相同的因次,此称为因次和谐或因次的一致性。 以层流时的阻力损失计算式为例,式(1-73)可写成如下形式 ???? ????? ??=??? ? ??dup d l u h f μ322 (1-75) 式中每一项都为无因次项,称为无因次数群。 换言之,未作无因次处理前,层流时阻力的函数形式为: ) ,,,,(u l d f h f ρμ= (1-76) 作无因次处理后,可写成
管道内的局部阻力及损失计算
管道内的局部阻力及损失计算 第四节管道内的局部阻力及损失计算 在实际的管路系统中,不但存在上一节所讲的在等截面直管中的沿程损失,而且也存在有各种各样的其它管件,如弯管、流道突然扩大或缩小、阀门、三通等,当流体流过这些管道的局部区域时,流速大小和方向被迫急剧地发生改变,因而出现流体质点的撞击,产生旋涡、二次流以及流动的分离及再附壁现象。此时由于粘性的作用,流体质点间发生剧烈的摩擦和动量交换,从而阻碍着流体的运动。这种在局部障碍物处产生的损失称为局部损失,其阻力称为局部阻力。因此一般的管路系统中,既有沿程损失,又有局部损失。 4.4.1 局部损失的产生的原因及计算 一、产生局部损失的原因 产生局部损失的原因多种多样,而且十分复杂,因此很难概括全面。这里结合几种常见的管道来说明。 , , , , 图4.9 局部损失的原因 对于突然扩张的管道,由于流体从小管道突然进入大管道如图 4.9 , ,所示,而且由于流体惯性的作用,流体质点在突然扩张处不可能马上贴附于壁面,而是在拐角的尖点处离开了壁面,出现了一系列的旋涡。进一步随着流体流动截面面积的不断的扩张,直到 2 截面处流体充满了整个管截面。在拐角处由于流体微团相互之间
的摩擦作用,使得一部分机械能不可逆的转换成热能,在流动过程中,不断地有微团被主流带走,同时也有微团补充到拐角区,这种流体微团的不断补充和带走,必然产生撞击、摩擦和质量交换,从而消耗一部分机械能。另一方面,进入大管流体的流速必然重新分配,增加了流体的相对运动,并导致流体的进一步的摩擦和撞击。局部损失就发生在旋涡开始到消失的一段距离上。 图4.9,,给出了弯曲管道的流动。由于管道弯曲,流线会发生弯曲,流体在受到向心力的作用下,管壁外侧的压力高于内侧的压力。在管壁的外侧,压强先增加而后减小,同时内侧的压强先减小后增加,这样流体在管内形成螺旋状的交替流动。 综上所述,碰撞和旋涡是产生局部损失的主要原因。当然在 1-2之间也存在沿程损失,一般来说,局部损失比沿程损失要大得多。在测量局部损失的实验中,实际上也包括了沿程损失。 二、局部损失的计算 如前所述,单位重量流体的局部能量损失以表示 式中,—局部损失,阻力,系数,是一个无量纲的系数,它的大小与局部障碍物的结构形式有关,由实验确定。—管中的平均速度,通常指局部损失之后的速度,。 局部压强损失为 式中, —流经局部障碍物前后的压强差,或总压差,。 突然扩张管道的局部损失计算
风管阻力计算总结
通风管道阻力计算 对于空调通风专业来说,我们最终的目的是让整个系统达到或接近设计及业主的要求。对于整套空调系统而言主要应该把握几个关键的参数:风量、温度、湿度、洁净度等。可见无论空调是否对新风做处理,我们送到房间的风量是一定要达到要求。否则别的就更不用考虑了。管道内风量主要是由风管内阻力影响的。 风管内空气流动的阻力有两种,一种是由于空气本身的粘滞性及其与管壁间的摩擦而产生的沿程能量损失,称为摩擦阻力或沿程阻力;另一种是空气流经风管中的管件及设备时,由于流速的大小和方向变化以及产生涡流造成比较集中的能量损失,称为局部阻力。下边为标准工况且没有扰动的情况下的计算,如实际不是标准工况且有扰动需要进行修正。 一:摩擦阻力(沿程阻力)计算 摩擦阻力(沿程阻力)计算一:(公式推导法) 根据流体力学原理,无论矩形还是圆形风管空气在横断面形状不变的管道内流动时的摩擦阻力(沿程阻力) 按下式计算:ΔPm=λν2ρL/2D 以上各式中: ΔPm———摩擦阻力(沿程阻力),Pa。 λ————摩擦阻力系数【λ根据流体不同情况而改变不具有规律性,不可用纯公式计算,只能靠实验得到许多不同状态的半经验公式: 其中最常用的公式为:,《K-管壁的当量绝对粗糙度,mm (见表1-1);D-风管当量直径,mm(见一下介绍) ;Re雷诺数判断流体流动状态的准则数,(见表1-1);其实λ一般由莫台图所得,见图】 莫台曲线图
表1-1 一般通风管道中K、Re、λ的经验取值 ν————风管内空气的平均流速,m/s; 【其中ν=Q/F;Q为管内风量m3/S,F为管道断面积M2 ;其中矩形风管F=a×b;圆形风管F=πD2 /4,一般设计也直接选风速见表1-2】表1-2 一般通风系统中常用空气流速(m/s) ρ————空气的密度,Kg/m3;【在压力B0=101.3kPa、温度t0=20℃、一般情况下取ρ=1.205Kg/m3; 见表1-3】 L ———风管长度,m 【横断面形状不变的管道长度】 D———风管的当量直径,m; 【矩形风管流速当量直径:;流量当量直径:;圆形风管D为风管直径】
管道阻力损失计算
管道的阻力计算 风管内空气流动的阻力有两种,一种是由于空气本身的粘滞性及其与管壁间的摩擦而产生的沿程能量损失,称为摩擦阻力或沿程阻力;另一种是空气流经风管中的管件及设备时,由于流速的大小和方向变化以及产生涡流造成比较集中的能量损失,称为局部阻力。通常直管中以摩擦阻力为主,而弯管以局部阻力阻力为主(图6-1-1)。 图6-1-1 直管与弯管 (一)摩擦阻力 1.圆形管道摩擦阻力的计算 根据流体力学原理,空气在横断面形状不变的管道内流动时的摩擦阻力按下式计算: (6-1-1) 对于圆形风管,摩擦阻力计算公式可改为: (6-1-2) 圆形风管单位长度的摩擦阻力(又称比摩阻)为: (6-1-3) 以上各式中 λ——摩擦阻力系数;
v——风秘内空气的平均流速,m/s; ρ——空气的密度,kg/m3; l——风管长度,m; Rs——风管的水力半径,m; f——管道中充满流体部分的横断面积,m2; P——湿周,在通风、空调系统中即为风管的周长,m; D——圆形风管直径,m。 摩擦阻力系数λ与空气在风管内的流动状态和风管管壁的粗糙度有关。在通风和空调系统中,薄钢板风管的空气流动状态大多数属于紊流光滑区到粗糙区之间的过渡区。通常,高速风管的流动状态也处于过渡区。只有流速很高、表面粗糙的砖、混凝土风管流动状态才属于粗糙区。计算过渡区摩擦阻力系数的公式很多,下面列出的公式适用范围较大,在目前得到较广泛的采用: (6-1-4) 式中K——风管内壁粗糙度,mm; D——风管直径,mm。 进行通风管道的设计时,为了避免烦琐的计算,可根据公式(6-1-3)和(6-1-4)制成各种形式的计算表或线解图,供计算管道阻力时使用。只要已知流量、管径、流速、阻力四个参数中的任意两个,即可利用线解图求得其余的两个参数。线解图是按过渡区的λ值,在压力B0=101.3kPa、温度t0=20℃、宽气密度ρ0=1.204kg/m3、运动粘度 v0=15.06×10-6m2/s、管壁粗糙度K=0.15mm、圆形风管等条件下得出的。当实际使用条件下上述条件不相符时,应进行修正。 (1)密度和粘度的修正 (6-1-5) 式中Rm——实际的单位长度摩擦阻力,Pa/m; Rmo——图上查出的单位长度摩擦阻力,Pa/m; ρ——实际的空气密度,kg/m3; v——实际的空气运动粘度,m2/s。
过滤器阻力损失计算及滤网规格
过滤器阻力损失计算 ΔP--阻力损失,Pa λ--摩擦系数,无因次 Re-雷诺数,Re=(ω·dn)/u,无因次 ω-流体速度,m/s ρ-流体密度,kg/m3 μ-动力粘度,kg/m·s u-运动粘度u=μ/ρ,m2/s L-当量直管段长度,m,类管件过滤器查阅下表“类管件过滤器公称直径与当量直管段长度关系” D-类管件过滤器内径,m dn-当量直径m,类管件过滤器取管件内径"D",筒壳式过滤器取‘4s/c’ S-液体流通面积,m2 C-液体湿周(湿润周长),C=2X(筒体内径+筒体高度)m ξ-入口阻力系数,取1.1 ξ-出口阻力系数,取0.5 类管件过滤器公称直径与当量直管段长度关系 公称直径DN 50 80 100 150 200 当量直管段长度L 25∽30 18∽23 15∽20 22∽38 32∽40 (×103mm) 公称直径DN 250 300 350 400 450 当量直管段长度L 27~43 58~65 48~85 60~95 62~98 (×103mm) 对于‘筒壳’类过滤器,按下式计算: 过滤面积及孔目数 过滤面积通常指丝网的有效流通面积,可以查阅下表“滤网规格”得知有效面积,滤网总面积与有效面积率的乘积即为过滤面积(有效流通面积)。通常,考虑过滤面积按过滤器公称通径的20倍设计,已足够满足使用场合。除非在非常见的特殊环境使用,才予以特殊考虑。 孔目数(目数/英寸)的选择,主要考虑需拦截的杂质粒径,依据介质流程工艺要求而定。各种规格丝网可拦截的粒径尺寸查下表“滤网规格”。 滤网规格
不锈钢丝网的技术特性一般金属丝网的技术特性 孔目数目英寸丝径mm 可拦截的 粒径um 有效面积%孔目数目 英寸 丝径mm 可拦截的 粒径um 有效面积% 10 0.508 2032 64 10 0.559 1981 61 12 0.475 1660 61 12 0.457 1660 61 14 0.376 1438 63 14 0.367 1438 63 16 0.315 1273 65 16 0.315 1273 65 18 0.315 1096 61 18 0.315 1096 61 20 0.273 955 57 20 0.274 996 62 22 0.234 882 59 22 0.274 881 59 24 0.234 785 56 24 0.254 804 58 26 0.234 743 59 26 0.234 743 59 28 0.234 673 56 28 0.234 673 56 30 0.234 614 53 30 0.234 614 53 32 0.234 560 50 32 0.213 581 54 36 0.234 472 46 36 0.213 534 52 38 0.234 455 46 38 0.213 493 50 40 0.193 442 49 40 0.173 462 54 50 0.152 356 50 50 0.152 356 50 60 0.122 301 51 60 0.122 301 51 80 0.102 216 47 80 0.102 216 47 100 0.081 173 46 100 0.08 174 50 120 0.081 131 38 120 0.07 142 50 (1)金属材料温度适用范围 铸铁-10~200℃碳钢-20~400℃低合金钢-40~400℃不锈钢-190~400℃(2)辅助密封材料温度适用范围 丁晴橡胶-30~100℃氟橡胶-30~150℃石棉板报≤300℃石墨金属缠绕垫≤650℃ 公称压力:按照过滤管路可能出现的最高压力确定过滤器的压力等级,也可通过技术协议要求,考虑进出口管路的统一性,选择与出口管路中最高压力相匹配的压力等级过滤器实际适用最高压力与介质 P--过滤器所能承受的最高工作压力Mpa P--过滤器的公称压力Mpa T--过滤器使用工作温度(应考虑裕度)℃ ΔT--温度偏差ΔT=T-200 ℃ K--强度减弱系数Mpa/℃ K值按如下原则选取: ①工作温度≤200℃时,K=0; ②铸铁过滤器(200-300℃),K=0-0.004; ③碳钢过滤器(200-400℃),K=0.0016-0.008; ④低合金钢过滤器(200-400℃),K=0.0006-0.006; ⑤不锈钢过滤器(200-400℃),K=0.00018-0.006;
(完整版)管道内的局部阻力及损失计算
第四节管道内的局部阻力及损失计算 在实际的管路系统中,不但存在上一节所讲的在等截面直管中的沿程损失,而且也存在有各种各样的其它管件,如弯管、流道突然扩大或缩小、阀门、三通等,当流体流过这些管道的局部区域时,流速大小和方向被迫急剧地发生改变,因而出现流体质点的撞击,产生旋涡、 二次流以及流动的分离及再附壁现象。此时由于粘性的作用,流体质点间发生剧烈的摩擦和动量交换,从而阻碍着流体的运动。这种在局部 障碍物处产生的损失称为局部损失,其阻力称为局部阻力。因此一般的管路系统中,既有沿程损失,又有局部损失。 4.4.1 局部损失的产生的原因及计算 一、产生局部损失的原因 产生局部损失的原因多种多样,而且十分复杂,因此很难概括全面。这里结合几种常见的管道来说明。 ()() 图4.9 局部损失的原因 对于突然扩张的管道,由于流体从小管道突然进入大管道如图 4.9 ()所示,而且由于流体惯性的作用,流体质点在突然扩张 处不可能马上贴附于壁面,而是在拐角的尖点处离开了壁面,出现了一系列的旋涡。进一步随着流体流动截面面积的不断的扩张,直到 2 截面处流体充满了整个管截面。在拐角处由于流体微团相互之间的摩擦作用,使得一部分机械能不可逆的转换成热能,在流动过程中,不断地 有微团被主流带走,同时也有微团补充到拐角区,这种流体微团的不断补充和带走,必然产生撞击、摩擦和质量交换,从而消耗一部分机械 能。另一方面,进入大管流体的流速必然重新分配,增加了流体的相对运动,并导致流体的进一步的摩擦和撞击。局部损失就发生在旋涡开 始到消失的一段距离上。 图4.9()给出了弯曲管道的流动。由于管道弯曲,流线会发生弯曲,流体在受到向心力的作用下,管壁外侧的压力高于内侧的 压力。在管壁的外侧,压强先增加而后减小,同时内侧的压强先减小后增加,这样流体在管内形成螺旋状的交替流动。 综上所述,碰撞和旋涡是产生局部损失的主要原因。当然在 1-2之间也存在沿程损失,一般来说,局部损失比沿程损失要大得多。 在测量局部损失的实验中,实际上也包括了沿程损失。 二、局部损失的计算 如前所述,单位重量流体的局部能量损失以表示
通风管道阻力计算
通风管道阻力计算 风管内空气流动的阻力有两种,一种是由于空气本身的粘滞性及其与管壁间的摩擦而产生的沿程能量损失,称为摩擦阻力或沿程阻力;另一种是空气流经风管中的管件及设备时,由于流速的大小和方向变化以及产生涡流造成比较集中的能量损失,称为局部阻力。 一、摩擦阻力根据流体力学原理,空气在横断面形状不变的管道内流动时的摩擦阻力按下式计算: ΔPm=λν2ρl/8Rs 对于圆形风管,摩擦阻力计算公式可改写为: ΔPm=λν2ρl/2D 圆形风管单位长度的摩擦阻力(比摩阻)为: Rs=λν2ρ/2D 以上各式中 λ————摩擦阻力系数 ν————风管内空气的平均流速,m/s; ρ————空气的密度,Kg/m3; l ————风管长度,m ; Rs————风管的水力半径,m; Rs=f/P f————管道中充满流体部分的横断面积,m2; P————湿周,在通风、空调系统中既为风管的周长,m; D————圆形风管直径,m。 矩形风管的摩擦阻力计算 我们日常用的风阻线图是根据圆形风管得出的,为利用该图进行矩形风管计算,需先把矩形风管断面尺寸折算成相当的圆形风管直径,即折算成当量直径。再由此求得矩形风管的单位长度摩擦阻力。当量直径有流速当量直径和流量当量直径两种; 流速当量直径:Dv=2ab/(a+b) 流量当量直径:DL=1.3(ab)0.625/(a+b)0.25 在利用风阻线图计算是,应注意其对应关系:采用流速当量直径时,必须用矩形中的空气流速去查出阻力;采用流量当量直径时,必须用矩形风管中的空气流量去查出阻力。 二、局部阻力当空气流动断面变化的管件(如各种变径管、风管进出口、阀门)、流向变化的管件(弯头)流量变化的管件(如三通、四通、风管的侧面送、排风口)都会产生局部阻力。
矿井通风阻力计算方法
矿井通风阻力 第一节通风阻力产生的原因 当空气沿井巷运动时,由于风流的粘滞性和惯性以及井巷壁面等对风流的阻滞、扰动作用而形成通风阻力,它是造成风流能量损失的原因。 井巷通风阻力可分为两类:摩擦阻力(也称为沿程阻力)和局部阻力。 一、风流流态(以管道流为例) 同一流体在同一管道中流动时,不同的流速,会形成不同的流动状态。当流速较低时,流体质点互不混杂,沿着与管轴平行的方向作层状运动,称为层流(或滞流)。当流速较大时,流体质点的运动速度在大小和方向上都随时发生变化,成为互相混杂的紊乱流动,称为紊流(或湍流)。(降低风速的原因) (二)、巷道风速分布 由于空气的粘性和井巷壁面摩擦影响,井巷断面上风速分布是不均匀的。 在同一巷道断面上存在层流区和紊区,在贴近壁面处仍存在层流运动薄层,即层流区。在层流区以外,为紊流区。从巷壁向巷道轴心方向,风速逐渐增大,呈抛物线分布。 巷壁愈光滑,断面上风速分布愈均匀。 第二节摩擦阻力与局部阻力的计算 一、摩擦阻力 风流在井巷中作沿程流动时,由于流体层间的摩擦和流体与井巷壁面之间的摩擦所形成的阻力称为摩擦阻力(也叫沿程阻力)。 由流体力学可知,无论层流还是紊流,以风流压能损失(能量损失)来反映的摩擦阻力可用下式来计算: H f =λ×L/d×ρν2/2pa λ——摩擦阻力系数。 L——风道长度,m
d——圆形风管直径,非圆形管用当量直径; ρ——空气密度,kg/m3 ν2——断面平均风速,m/s; 1、层流摩擦阻力:层流摩擦阻力与巷道中的平均流速的一次方成正比。因井下多为紊流,故不详细叙述。 2、紊流摩擦阻力:对于紊流运动,井巷的摩擦阻力计算式为: H f =α×LU/S3×Q2 =R f×Q2pa R f=α×LU/S3 α——摩擦阻力系数,单位kgf·s2/m4或N·s2/m4,kgf·s2/m4=9.8N·s2/m4 L、U——巷道长度、周长,单位m; S——巷道断面积,m2 Q——风量,单位m/s R f——摩擦风阻,对于已给定的井巷,L,U,S都为已知数,故可把上式中的α,L,U,S 归结为一个参数R f,其单位为:kg/m7 或N·s2/m8 3、井巷摩擦阻力计算方法 新建矿井:查表得α→h f→R f 生产矿井:已测定的h f→R f→α,再由α→h f→R f 二、局部阻力 由于井巷断面,方向变化以及分岔或汇合等原因,使均匀流动在局部地区受到影响而破坏,从而引起风流速度场分布变化和产生涡流等,造成风流的能量损失,这种阻力称为局部阻力。由于局部阻力所产生风流速度场分布的变化比较复杂性,对局部阻力的计算一般采用经验公式。 1、几种常见的局部阻力产生的类型: (1)、突变 紊流通过突变部分时,由于惯性作用,出现主流与边壁脱离的现象,在主流与边壁之间形成涡漩区,从而增加能量损失。
谈通风管道局部阻力计算方法
谈通风管道局部阻力计算方法 胡宝林 在通风除尘与气力输送系统中,管道的局部阻力主要在弯头、变径管、三通、阀门等管件与重杂物分离器、供料器、卸料器、除尘器等设备上产生。由于管件形状与设备结构的不确定性以及局部阻力的复杂性,目前许多局部阻力系数还不能用公式进行计算,只能通过大量的实验测试阻力再推算阻力系数,并制成表格供设计者查询。例如在棉花加工生产线上,常规的漏斗形重杂物分离器压损为300a P 左右,离心式籽棉卸料器压损为400a P 左右,这些都就是实测数据,由于规格结构不同差异也会很大,所以仅供参考。只有一些常见的形状或结构比较确定的管件及设备可通过公式计算阻力系数,例如弯头、旋风除尘器等。局部阻力就是管道阻力的重要组成部分,一个4R D = 90°弯头的阻力相当于2、5~6、5m 的直管沿程阻力。由于涉及到局部阻力的管件种类繁多,不便一一列举,因此,本文以弯头等常用管件为例重点讨论在纯空气下与带料运行时的局部阻力系数的变化及局部阻力计算方法。 一、纯空气输送时局部阻力与系数 1、局部阻力 当固体边界的形状、大小或者两者之一沿流程急剧变化,流体的流动速度分布就会发生变化,阻力大大增加,形成输送能量的损失,这种阻力称为局部阻力。在产生局部损失的地方,由于主流与边界分离与漩涡的存在,质点间的摩擦与撞击加剧,因而产生的输送能量损失比同样长的直管道要大得多,局部阻力与物料的密度及速度的平方成正比,局部阻力计算公式: 2 2 j d H H ρυξξ=?=? 式中:j H —局部阻力,a P ; ξ—局部阻力系数,实验取得或公式计算; d H —动压,a P ; ρ—空气密度,1、2053/kg m (20°℃); υ—空气流速,/m s
矿井通风阻力计算方法
矿井通风阻力 第一节通风阻力产生的原因当空气沿井巷运动时,由于风流的粘滞性和惯性以及井巷壁面等对风流的阻滞、扰动作用而形成通风阻力,它是造成风流能量损失的原因。 井巷通风阻力可分为两类:摩擦阻力(也称为沿程阻力)和局部阻力。 一、风流流态(以管道流为例)同一流体在同一管道中流动时,不同的流速,会形成不同的流动状态。当流速较低时,流体质点互不混杂,沿着与管轴平行的方向作层状运动,称为层流(或滞流)。当流速较大时,流体质点的运动速度在大小和方向上都随时发生变化,成为互相混杂的紊乱流动,称为紊流(或湍流)。(降低风速的原因) (二)、巷道风速分布 由于空气的粘性和井巷壁面摩擦影响,井巷断面上风速分布是不均匀的。在同一巷道断面上存在层流区和紊区,在贴近壁面处仍存在层流运动薄层,即层流区。在层流区以外,为紊流区。从巷壁向巷道轴心方向,风速逐渐增大,呈抛物线分布。 巷壁愈光滑,断面上风速分布愈均匀。 第二节摩擦阻力与局部阻力的计算 一、摩擦阻力风流在井巷中作沿程流动时,由于流体层间的摩擦和流体与井巷壁面之间的摩擦所形成的阻力称为摩擦阻力(也叫沿程阻力)。 由流体力学可知,无论层流还是紊流,以风流压能损失(能量损失)来反映的摩擦阻力可用下式来计算: 2 H = λ×L/d ×ρν/2 Pa λ——摩擦阻力系数。 L ---- 风道长度,m d――圆形风管直径,非圆形管用当量直径;
空气密度,kg/m3 断面平均风速,m/s; 1、层流摩擦阻力:层流摩擦阻力与巷道中的平均流速的一次方成正比。因井下多为紊流,故不详细叙述。 2、紊流摩擦阻力:对于紊流运动,井巷的摩擦阻力计算式为: H = α ×LU∕S3×Q2 =R f ×Q2 Pa 3 R f=α× LU∕S3 α --- 摩擦阻力系数,单位kgf ?s2∕m4或N ? s7m4, kgf ?s7m4=9.8N ? s7m4 L、U――巷道长度、周长,单位m S—巷道断面积,m Q ---- 风量,单位m/s R ——摩擦风阻,对于已给定的井巷,L,U S都为已知数,故可把上式中的α, L, U, S归结为一个参数R,其单位为:kg∕m7或N ?s7m8 3、井巷摩擦阻力计算方法 新建矿井:查表得α→ h f → R f 生产矿井:已测定的h f → R f → α, 再由α→ h f → R f 二、局部阻力 由于井巷断面,方向变化以及分岔或汇合等原因, 使均匀流动在局部地区受到影响而破坏, 从而引起风流速度场分布变化和产生涡流等,造成风流的能量损失,这种阻力称为局部阻力。由于局部阻力所产生风流速度场分布的变化比较复杂性,对局部阻力的计算一般采用经验公式。 1、几种常见的局部阻力产生的类型: (1)、突变紊流通过突变部分时,由于惯性作用,出现主流与边壁脱离的现象,在主流与边壁之间形成涡漩区,从而增加能量损失。 (2)、渐变 主要是由于沿流动方向出现减速增压现象, 在边壁附近产生涡漩。因为压差
局部阻力损失实验报告
局部阻力损失实验 前言: 工农业生产的迅速发展, 使石油管路、给排水管路、机械液压管路等, 得到了越来越广泛的应用。为了使管路的设计比较合理, 能满足生产实际的要求, 管路设计参数的确定显得更为重要。管路在工作过程中存在沿程损失和局部阻力损失,合理确定阻力系数是使设计达到实际应用要求的关键。但是由于扩张、收缩段的流动十分复杂,根据伯努利方程和动量方程推导出的理论值往往与具体的管道情况有所偏差,一般需要实验测定的局部水头损失进行修正或者得出经验公式用于工业设计。 在管路中, 经常会出现弯头, 阀门, 管道截面突然扩大, 管道截面突然缩小等流动有急剧变化的管段, 由于这些管段的存在, 会使水流的边界发生急剧变化, 水流中各点的流速, 压强都要改变, 有时会引起回流, 旋涡等, 从而造成水流机械能的损失。例如,流体从小直径的管道流往大直径的管道, 由于流体有惯性, 它不可能按照管道的形状突然扩大, 而是离开小直径的管道后逐渐地扩大。因此便在管壁拐角与主流束之间形成漩涡, 漩涡靠主流束带动着旋转, 主流束把能量传递给漩涡、漩涡又把得到的能量消耗在旋转中( 变成热而消散) 。此外, 由于管道截面忽然变化所产生的流体冲击、碰撞等都会带来流体机械能的损失。 摘要: 本实验利用三点法测量扩张段的局部阻力系数,用四点法量测量收缩段的局部阻力系数,然后与圆管突扩局部阻力系数的包达公式和突缩局部阻力系数的经验公式中的经验值进行对比分析,从而掌握用理论分析法和经验法建立函数式的技能。进而加深对局部阻力损失的理解。 三、实验原理 写出局部阻力前后两断面的能量方程,根据推导条件,扣除沿程水头损失可得: 1.突然扩大 采用三点法计算,下式中12 f h -由 23 f h -按流长比例换算得出。 实测 2 2 1 12 21212[()][()]22je f p p h Z Z h g g αυαυγ γ -=+ + -+ + + 理论 212 (1)e A A ζ'=- 2.突然缩小 采用四点法计算,下式中B 点为突缩点,4f B h -由 34 f h -换算得出, 5 fB h -由 56 f h -换算 得出。 实测 2 2 5 54 44455[()][()]22js f B fB p p h Z h Z h g g αυαυγ γ --=+ + --+ + +
通风阻力计算公式汇总
通风阻力计算公式汇总
————————————————————————————————作者:————————————————————————————————日期:
1、 巷道几何参数的测算 (1)梯形: 断面积 SL=H L *B L 周长 U L =4.16*L S (2) 半圆拱: 断面积 S L =(H L -0.1073B L )*B L 周长 U L =3.84*L S (3)三心拱: 断面积 S L =(HL-0.0867B L )*B L 周长 U L =4.10*L S (4)圆形: 断面积 S L =π*R 2 周长 U L =2*π*R (5)矩形: 断面积 S L = H L * B L 周长 U L =2*(H L +B L ) 式中: S L —巷道断面面积,m 2 U L —巷道断面周长,m ; H L —巷道断面全高,m ; B L —巷道断面宽度或腰线宽度,m ; R —巷道断面圆半径,m ; π—圆周率,取3.14159。 以上有关参数均通过实测获取,而巷道各分支长度由地测部门提供。 2、 巷道内风量的计算 (1)两测点之间巷道通过的风量按如下原则确定: Q=(Q i +Q i+1)/2 , m 3/min (2)井巷内风量、风速按以下公式计算: Q L =S L *V L , m 3/min V L =((S-0.4)/S )*(a X+ b ) , m 3/min 式中: Q L --井巷内通过的风量,m 3/min ; S L (S )--井巷断面面积,m 2 V L --井巷内平均风速,m/min X —表风速,m/min a 、 b —风表校正系数 3 井巷内空气密度的计算 湿空气密度用下列公式计算: i b i=d 0.0348(Pi 0.379P )273.15+t ?-ρ , kg/ m 3 式中:i ρ—测点i 处湿空气密度(i ?≠0), kg/ m 3 Pi --测点i 处空气的绝对静压(大气压力),Pa ; d t --测点i 处空气的干温度,℃;
通风阻力 计算公式汇总
1、 巷道几何参数的测算 (1)梯形: 断面积 SL=H L *B L 周长 U L (2) 半圆拱: 断面积 S L =(H L -0.1073B L )*B L 周长 U L =3.84* (3)三心拱: 断面积 S L =(HL-0.0867B L )*B L 周长 U L (4)圆形: 断面积 S L =π*R 2 周长 U L =2*π*R (5)矩形: 断面积 S L = H L * B L 周长 U L =2*(H L +B L ) 式中: S L —巷道断面面积,m 2 U L —巷道断面周长,m ; H L —巷道断面全高,m ; B L —巷道断面宽度或腰线宽度,m ; R —巷道断面圆半径,m ; π—圆周率,取3.14159。 以上有关参数均通过实测获取,而巷道各分支长度由地测部门提供。 2、 巷道内风量的计算 (1)两测点之间巷道通过的风量按如下原则确定: Q=(Q i +Q i+1)/2 , m 3/min (2)井巷内风量、风速按以下公式计算: Q L =S L *V L , m 3/min V L =((S-0.4)/S )*(a X+ b ) , m 3/min 式中: Q L --井巷内通过的风量,m 3/min ; S L (S )--井巷断面面积,m 2 V L --井巷内平均风速,m/min X —表风速,m/min a 、 b —风表校正系数 3 井巷内空气密度的计算 湿空气密度用下列公式计算: i b i=d 0.0348(Pi 0.379P )273.15+t ?-ρ , kg/ m 3 式中:i ρ—测点i 处湿空气密度(i ?≠0), kg/ m 3 Pi --测点i 处空气的绝对静压(大气压力),Pa ; d t --测点i 处空气的干温度,℃; i ?--测点i 处空气的相对湿度,%; P b —测点i 处d t 空气温度下的饱和水蒸气压力,Pa 。
管道阻力损失计算(终审稿)
管道阻力损失计算公司内部档案编码:[OPPTR-OPPT28-OPPTL98-OPPNN08]
管道的阻力计算 风管内空气流动的阻力有两种,一种是由于空气本身的粘滞性及其与管壁间的摩擦而产生的沿程能量损失,称为摩擦阻力或沿程阻力;另一种是空气流经风管中的管件及设备时,由于流速的大小和方向变化以及产生涡流造成比较集中的能量损失,称为局部阻力。通常直管中以摩擦阻力为主,而弯管以局部阻力阻力为主(图6-1-1)。 ? 图6-1-1 直管与弯管 (一)摩擦阻力 1.圆形管道摩擦阻力的计算 根据流体力学原理,空气在横断面形状不变的管道内流动时的摩擦阻力按下式计算: (6-1-1) 对于圆形风管,摩擦阻力计算公式可改为:
(6-1-2) 圆形风管单位长度的摩擦阻力(又称比摩阻)为: (6-1-3) 以上各式中 λ——摩擦阻力系数; v——风秘内空气的平均流速,m/s; ρ——空气的密度,kg/m3; l——风管长度,m; Rs——风管的水力半径,m; f——管道中充满流体部分的横断面积,m2; P——湿周,在通风、空调系统中即为风管的周长,m; D——圆形风管直径,m。 摩擦阻力系数λ与空气在风管内的流动状态和风管管壁的粗糙度有关。在通风和空调系统中,薄钢板风管的空气流动状态大多数属于紊流光滑区到粗糙区之间的过渡区。通常,高速风管的流动状态也处于过渡区。只有流速很高、表面粗糙的砖、混凝土风管流动状态才属于粗糙区。计算过渡区摩擦阻力系数的公式很多,下面列出的公式适用范围较大,在目前得到较广泛的采用: (6-1-4) 式中 K——风管内壁粗糙度,mm;
D——风管直径,mm。 进行通风管道的设计时,为了避免烦琐的计算,可根据公式(6-1-3)和(6-1-4)制成各种形式的计算表或线解图,供计算管道阻力时使用。只要已知流量、管径、流速、阻力四个参数中的任意两个,即可利用线解图求得其余的两个参数。线解图是按过渡区的λ值,在压力 B0=、温度t0=20℃、宽气密度ρ0=m3、运动粘度v0=×10-6m2/s、管壁粗糙度K=、圆形风管等条件下得出的。当实际使用条件下上述条件不相符时,应进行修正。 (1)密度和粘度的修正 (6-1-5) 式中 Rm——实际的单位长度摩擦阻力,Pa/m; Rmo——图上查出的单位长度摩擦阻力,Pa/m; ρ——实际的空气密度,kg/m3; v——实际的空气运动粘度,m2/s。 (2)空气温度和大气压力的修正 (6-1-6) 式中 Kt——温度修正系数。 KB——大气压力修正系数。 (6-1-7) 式中 t——实际的空气温度,℃。 (6-1-8) 式中 B——实际的大气压力,kPa。
(八)局部阻力损失实验
局部阻力损失实验 实验人:王琦PB10030015 苏拓 一、实验目的要求 1、掌握三点法、四点法量测局部阻力系数的技能; 2、通过对园管突扩局部阻力系数的表达公式和突缩局部阻力系数的经验公式的实验验证与分析,熟悉用理论分析法和经验法建立函数式的途径: 3、加深对局部阻力损失机理的理解。 二、实验装置 本实验装置如图8.1所示 4567891011 12 321 1 2 3 4 5 6 图 8.1 局部阻力系数实验装置图 1.自循环供水器; 2.实验台; 3.可控硅无级调速器; 4.恒压水箱; 5.溢流板; 6.稳水孔板; 7.突然扩大实验管段; 8.测压计; 9.滑动测量尺; 10.测压管; 11.突然收缩实验管段; 12.实验流量调节阀. 实 验管道由小—大—小三种已知管径的管道组成,共设有六个测压孔,测孔1—3和3—6分别测量突扩和突缩的局部阻力系数。其中测孔1位于突扩界面处,用以测量小管出口端压强值。 三、实验原理 写出局部阻力前后两断面能量方程,根据推导条件,扣除沿程水头损失可得: 1、突然扩大 采用三点法计算,下式中21-f h 由32-f h 按流长比例换算得出。 实测 ]2)[(]2)[(212 2 2 22 11 1-++ + -+ + =f je h g p z g p z h αυγ αυγ g h je e 2/ 2 1αυζ= 理论 2 2 1)1(A A e - =' ζ
g a h e je 22 1υζ'=' 2、突然缩小 采用四点法计算,下式中B 点为突缩点,B f h -4由43-f h 换算得出,5-fB h 由65-f h 换算得出。 实测 ]2)[(]2)[(52 55 5424 4 4--++ + --+ + =fB B f js h g p Z h g p Z h αυγ αυγ g h js s 2/ 2 5αυζ= 经验 )1(5.03 5 A A s - =' ζ g h s js 22 5αυζ'=' 实验结果及要求 1.记录,计算有关常数: d1=D1=1.03cm, d2=d3=d4=D2=1.95cm, d5=d6=D3=1.01cm, 122334455612,24,12,6,6,6B B l cm l cm l cm l cm l cm l cm ------======5198.0)1(2 21'=- =A A e ζ 3659.0)1(5.03 5'=-=A A s ζ 2.整理、记录并计算: 表1 局部阻力损失实验记录表 次数 流量,cm^3/s 测压管读数/cm 体积 时间 流量 1 2 3 4 5 6 1 915 7.15 127.972 14.3 18.5 18.1 18 0 0 2 1120 9.07 123.484 15.6 19.7 19.3 19.2 2.8 0 3 1420 13.04 108.8957 19.3 22.6 22.3 22.2 8.8 7.5 4 1150 15.06 76.36122 27.9 29.5 29.4 29.4 22.6 21.8 表2 局部阻力损失实验记录表 次数 阻力 流量cm^3/s 前断面cm 后断面 cm hj,cm § hj',cm αv^2/2g E αv^2/2g E 1 突扩 127.97 2 12.04719 26.6390 3 0.93777 19.81532 6.619626 0.549475 6.2621 2 123.484 11.21701 27.13538 0.873148 20.97519 5.956109 0.530989 5.8306 3 108.8957 8.723228 28.41711 0.679028 23.74025 4.523792 0.518591 4.5343
风管计算局部阻力系数
知识就绘力量 风管计算局部阻力系数 1.3.2局部組力廉散 竇杵彳进凤口的AM1力嬴故 A 1安装庄堵上的风曾 吗风管为短形时?门対臓逮芳H直住◎ 出这种管件的入口外装有网幡时.应进行修疋「边醴较弾时.BP S/D?h05时fo = I十氐边壁较阜时.即J/P>0.05时* 式中A—管件的局部阻力累裁*见上樂——福的 局诽阻力慕数.见管杵G-乩^-2不安在惓埴上的 權足甑妁則叭口 4 -.. 丄 ■ 02B聞4已fid100140IBD U. 026 1.00.96IKM0亠肺w0.69 4.590.30 o. os 1.0c,as IL帥0,?5 C.fl7乩站0.53仇的fe * 0,1& 1.0
577 知识就姥力量 当断简①处有期格时,按式<8.3-2)进行修正。 /?3安装在端堪上的锥形渐缩剤叭口 当断面①处有网格时,应按式(8.3 2)修正。 *4罩形进风门 若斷面①处有剧祜时.应按式<8<3-2)进行修正。 4-5带或不带凸边的渐缩型罩子。 矶?) 0 20 40 w ?0 ]00 120 1W 1W 180 L0 O.ll 0N6 0.W 044 0.18 0.27 - O.A3 <1. W 20 40 8C- 100 120 uo 160 l?J : 1.0 0.L9 0.13 0U6 0<2l 0.27 0.33 0.33 0.52 : 对于矩形罩子,&系招大角。 管件B 岀风口的局部81力系数 B-1直管出风口 瓷o = 1?0 当岀口断面处有网格时,应按式(8.3?2) 进行修正? B-2健形出风口.園风管 1 D C 10 20 M 40 60 100 13 180 O.OZL o.so 0.U 仇45 C.43 0.41 0.40 0.42 0.45 O.M 0.05 0.W 0.45 0.1( 0.W 0.33 0.30 0>35 0.42 O.ati 0.OT5 OeSO 0.42 0.36 O.2C 0.28 0.23 0.30 0.40 0.50 0.10 0.50 0.W 0.S2 0.2S 几22 0.18 0.27 C.M 0.50 0.1$ 0.60 0.37 0.Z7 9.20 ).16 0.15 0.25 0-37 0.50 ? 0?3 0.50 0.27 0.18 _ !>.13 3.11 0.12 0.23 0.36 C.50 0.1 0.2 0.3 0.4 0.5 0?b 0.7 0.8 ?.9 ■ 0 2?$ 1.8 i?5 1.1 1.3 1.2 l.Z 1.1 l.l 15 1.3 o.$o o.a 0.41 0.30 0.29 0.2S 0-25