烟气半干法脱硫技术方案

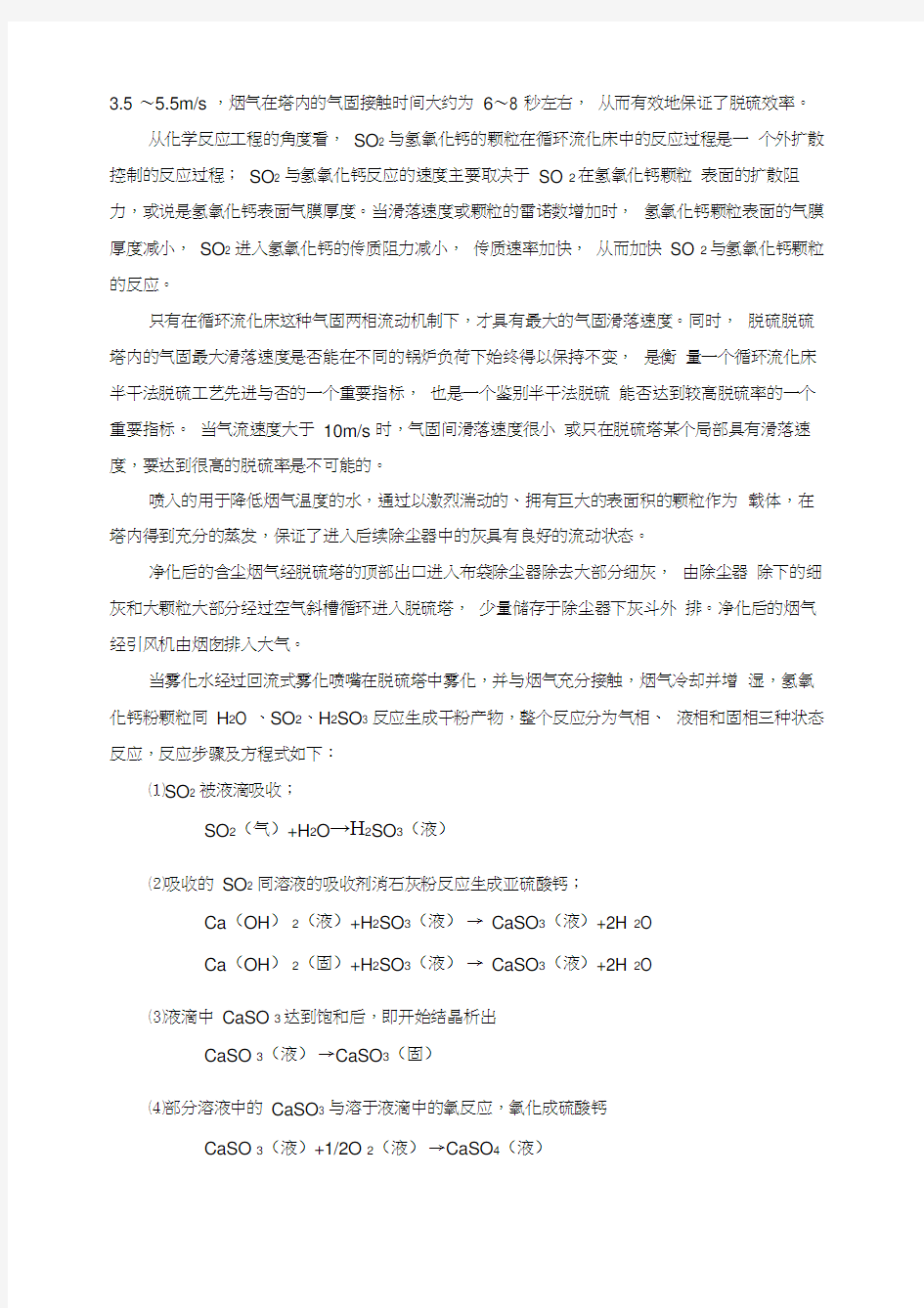
烟气半干法脱硫技术方案
1. 吸收塔
1.1 工艺流程
图1-1 循环流化床半干法工艺流程示意图
原烟气由循环流化床半干法净化装置底部进入循环悬浮流化床脱硫塔。Ca(OH) 2 原料经过螺旋输送机送入脱硫塔,流态化的物料和烟气中的二氧化硫在脱硫塔中发生化学反应,脱除掉大部分的二氧化硫。烟气通过脱硫塔底部的文丘里管的加速,进入循环流化床体,物料在循环流化床里,气固两相由于气流的作用,产生激烈的湍动与混合,充分接触,在上升的过程中,不断形成絮状物向下返回,而絮状物在激烈湍动中又不断解体重新被气流提升,使得气固间的滑落速度高达单颗粒滑落速度的数十倍;脱硫塔顶部结构进一步强化了絮状物的返回,进一步提高了塔内颗粒的床层密度,使得床内的Ca/S 比高达50 以上。这样循环流化床内气固两相流机制,极大地强化了气固间的传质与传热,为实现污染物高脱除率提供了根本的保证。
喷嘴的安装位置设置在文丘里扩散段,喷入的雾化水以降低脱硫塔内的烟温,从而使得SO2 与Ca(OH) 2 的反应转化为可以瞬间完成的离子型反应。吸收剂、循环脱硫灰在文丘里段以上的塔内进行第二步的充分反应,生成副产物CaSO 3·1/2H 2O,还与SO3 等反应生成相应的副产物CaSO 4·1/2H 2O 等。
烟气在上升过程中,颗粒一部分随烟气被带出脱硫塔,一部分因自重重新回流到循环流化床内,进一步增加了流化床的床层颗粒浓度和延长吸收剂的反应时间。烟气在文丘里以上的塔内流速为
3.5 ~5.5m/s ,烟气在塔内的气固接触时间大约为6~8 秒左右,从而有效地保证了脱硫效率。
从化学反应工程的角度看,SO2 与氢氧化钙的颗粒在循环流化床中的反应过程是一个外扩散控制的反应过程;SO2 与氢氧化钙反应的速度主要取决于SO 2在氢氧化钙颗粒表面的扩散阻力,或说是氢氧化钙表面气膜厚度。当滑落速度或颗粒的雷诺数增加时,氢氧化钙颗粒表面的气膜厚度减小,SO2 进入氢氧化钙的传质阻力减小,传质速率加快,从而加快SO 2与氢氧化钙颗粒的反应。
只有在循环流化床这种气固两相流动机制下,才具有最大的气固滑落速度。同时,脱硫脱硫塔内的气固最大滑落速度是否能在不同的锅炉负荷下始终得以保持不变,是衡量一个循环流化床半干法脱硫工艺先进与否的一个重要指标,也是一个鉴别半干法脱硫能否达到较高脱硫率的一个重要指标。当气流速度大于10m/s 时,气固间滑落速度很小或只在脱硫塔某个局部具有滑落速度,要达到很高的脱硫率是不可能的。
喷入的用于降低烟气温度的水,通过以激烈湍动的、拥有巨大的表面积的颗粒作为载体,在塔内得到充分的蒸发,保证了进入后续除尘器中的灰具有良好的流动状态。
净化后的含尘烟气经脱硫塔的顶部出口进入布袋除尘器除去大部分细灰,由除尘器除下的细灰和大颗粒大部分经过空气斜槽循环进入脱硫塔,少量储存于除尘器下灰斗外排。净化后的烟气经引风机由烟囱排入大气。
当雾化水经过回流式雾化喷嘴在脱硫塔中雾化,并与烟气充分接触,烟气冷却并增湿,氢氧化钙粉颗粒同H2O 、SO2、H2SO3 反应生成干粉产物,整个反应分为气相、液相和固相三种状态反应,反应步骤及方程式如下:
⑴SO2 被液滴吸收;
SO2(气)+H2O→H2SO3(液)
⑵吸收的SO2 同溶液的吸收剂消石灰粉反应生成亚硫酸钙;
Ca(OH)2(液)+H2SO3(液)→ CaSO3(液)+2H 2O
Ca(OH)2(固)+H2SO3(液)→ CaSO3(液)+2H 2O
⑶液滴中CaSO 3达到饱和后,即开始结晶析出
CaSO 3(液)→CaSO3(固)
⑷部分溶液中的CaSO3 与溶于液滴中的氧反应,氧化成硫酸钙
CaSO 3(液)+1/2O 2(液)→CaSO4(液)
⑸CaSO 4(液)溶解度低,从而结晶析出
CaSO 4(液)→CaSO4(固)
⑹对未来得及反应的Ca(OH)2 (固),以及包含在CaSO 3(固)、CaSO 4(固)内的Ca(OH)2 (固)进行增湿雾化。
Ca(OH)2 (固)→Ca(OH)2 (液)
SO2(气)+H2O→H2SO3(液)
Ca(OH)2 (液)+H2SO3(液)→CaSO3(液)+2H2O
CaSO 3(液)→CaSO3(固)
CaSO 3(液)+1/2O 2(液)→CaSO4(液)
CaSO 4(液)→CaSO4(固)
⑺布袋除尘器脱除的烟灰中的未反应的Ca(OH)2 (固),以及包含在CaSO 3(固)、CaSO4(固)内的Ca(OH)2 (固)循环至脱硫塔内继续反应。
Ca(OH)2 (固)→Ca(OH)2 (液)
SO2(气)+H2O→H2SO3(液)
Ca(OH)2 (液)+H2SO3(液)→CaSO3(液)+2H2O
CaSO 3(液)→CaSO3(固)
CaSO 3(液)+1/2O 2(液)→CaSO4(液)
CaSO 4(液)→CaSO4(固)
1.2 工艺、结构特点:
1) 采用计算流场模拟,优化吸收塔结构
通过计算机模拟技术,对吸收塔进出口导流板设置以及文丘里设计提供指导,采用七
孔文丘里,使塔内流场均匀,无烟气死角,平衡吸收塔阻力,防止塔内积灰。
2) 设备使用寿命长、维护量小。
塔内完全没有任何运动部件和支撑杆件,操作气速合理,塔内磨损小,没有堆积死 角,设备
使用寿命长、检修方便。特别是由于通过进气结构的改进设计,使烟气负荷在 30% ~110%变化范围内,均可保证塔内良好的气固混合和充分的接触,无须在塔内增
加絮流圈,保证了塔内不出现
单孔文丘里流场 经过优化的七孔文丘里流场
图 1-2 脱硫反应器流场数值模拟计算
堆积死角。
吸收塔文丘里部分选用耐磨的16Mn 钢,防止高速烟气的快速磨损。
3)烟气与物料接触时间长、接触充分,脱硫效率高。
由于设计选择最佳的操作气速,使得气固两相流在脱硫塔内的滑落速度最大,脱硫反应区床层密度高,颗粒在脱硫塔内停留时间长,烟气在塔内的气固接触时间长,使得脱硫塔内的气固混合、传质、传热更加充分,优化了脱硫反应效果,从而保证了达到较高的脱硫效率。
4)控制简单。
投标人提供的循环流化床半干法脱硫技术的工艺控制过程主要通过三个回路实现(见图1-2),这三个回路相互独立,互不影响。
图1-3 CFB-FGD 工艺控制回路图
a. SO2 排放控制:根据脱硫塔出口烟气SO2 浓度控制消石灰粉的给料量,保证达到按要求的SO2 排放浓度。
b. 温度控制:为了促进消石灰和SO2 的反应,通过向脱硫塔内喷水来降低烟气的温度。
通过对脱硫塔出口温度的测定,控制双流体喷嘴向脱硫塔内喷水,以使温度降低到设定值。工艺水通过水泵以一定的压力注入,经雾化后喷入至脱硫塔中。脱硫系统停止运行时,工艺水会自动停止注入。
c. 脱硫塔的压降控制:脱硫塔的压降由烟气压降和固体颗粒压降两部分组成。由于循环流化床内的固体颗粒浓度(或称固-气比)是保证流化床良好运行的重要参数,在运行中只有通过控制脱硫塔的压降来实现调节床内的固-气比,以保证脱硫塔始终处于良好的运行工况,它是通过调节除尘器灰斗下料进空气斜槽的物料量,以控制送回脱硫塔的再循环量,从而保证了床内脱硫反应所需的固体颗粒浓度。
加入脱硫塔的消石灰和水是相对独立的,便于控制消石灰用量及喷水量,从而使操作温度的控
制变得更加容易。
5) 无须防腐。循环流化床半干法脱硫塔内具有优良的传质传热条件,使塔内的水分迅速蒸发,并且可脱除几乎全部的SO3,烟气温度高于露点15 ℃以上,脱硫塔及其下游设备不会产生腐蚀。
6) 良好的入口烟气二氧化硫浓度变化适应性。当要求的脱硫效率发生变化时,无需增加任何工艺设备,仅需调节脱硫剂的耗量便可以满足更高的脱硫率的要求。
2. 布袋除尘器详细说明除尘器采用布袋除尘器,当净化反应后的含尘气体由烟道进入布袋除尘器进风口,考虑到净化除尘效果的要求,布袋除尘器内部结构上增设了沉降室,起到预分离的作用,进一步加强布袋预收尘,并保证布袋除尘器安全运行。在此沉降段内,烟气与导流板相撞击,粗颗粒粉尘掉入灰斗。
气流随后折转向上,通过内部装有金属架的滤袋,粉尘被捕集在滤袋的外表面,使气体净
化。净化后的气体进入滤袋室上部的清洁室,汇集到出风管排出。随着除尘器的连续运行,当滤袋表面的粉尘达到一定厚度时,气体通过滤料的阻力增大,布袋的透气率下降,用脉冲气流清吹布袋内壁,将布袋外表面上的粉饼层吹落,尘层跌入灰斗,滤袋又恢复了过滤功能。该系统分为多个室,采用“离线脉冲反吹清灰”的清灰方式。清灰采用“定时清灰”和“差压清灰”两种控制方式,采用优先控制原则,时间到,定时清灰优先;差压到,差压清灰优先。定时清灰:当清灰时间到,布袋除尘器将自动清灰,清灰结束后,重新计时;定压清灰:当布袋除尘器进出口压差达到设定值1200Pa (可根据
调试情况调整),布袋除尘器将自动清灰,清灰结束后,重新计时。布袋除尘器本体设有旁路烟道,当温度或差压超过设定值时,旁路自动运行,以保证系统安全平稳工作。
除尘器的底部灰斗中的灰部分经流量控制阀排出。除尘器灰斗上设有电加热保温,在冷态情况下启动或临时停运时使用,保证布袋除尘器本体内壁不至于出现酸结露,在锅炉正常运行的条件下加热器关闭。烟气经布袋除尘器除尘后,经烟道进入引风机后被排入大气。
本系统供气由独立贮气罐供给,气源由业主提供。
本系统除尘效率≥99.997%,阻力≤1200Pa,保证阻力≤1500Pa 。
(1) 本工程布袋除尘器总体技术性能:
1) 布袋除尘器入口烟尘浓度按800 ~1200g/Nm 3考虑
2) 除尘器出口排放浓度:≤30mg/Nm3。
3) 除尘器采用定阻、定时两种清灰程序自动控制。
4) 除尘器漏风率:≤1%。
5) 除尘器过滤风速:0.749m/min 。
6) 滤袋材质:PPS+PTFE 浸渍处理。
7) 布袋规格Φ160×6800,单进风双排共12 室,共有滤袋数量1512 只。总过滤面
积5160m 2。
8) 除尘器设有旁路阀,旁路阀本体的泄漏率为零。
9) 除尘器所有的传动部件充分考虑到结构的热膨胀、烟气中的灰尘以及酸腐蚀,并采用完善
的技术措施,实现影响锅炉运行的故障率为0。
10) 所提供的设备为当代成熟技术制造,并具有良好的启动灵活性和可靠性,能满足机组变
负荷的需要及技术参数的要求,并能在招标方所提供的烟气含尘条件和自然条件下长期、安全地运行并达到排尘要求。除尘主体设备的使用寿命为30 年。
11) 电磁脉冲阀使用寿命可达到100 万次。
12) 除尘器按承受正压7000Pa ,负压8000Pa 设计。
3. 消化站
为了统一考虑现有2×85t/h 循环流化床锅炉和新建1×135t/h 锅炉脱硫吸收剂——消石灰的供应,降低消石灰的采购成本,同时提高消石灰品质,降低建设造价,故利用现有建材厂的现有设备,进行改造,提高消石灰品质。
吸收剂消石灰粉制备存储及输送系统主要包括生石灰粉仓系统(仓顶布袋除尘器、压力释放阀、仓底流化风、高低料位,该设备利旧) 、手动插板阀、计量给料机( 含称重仓)、生石灰缓冲仓、三级干消化器、星形锁气器、消化水泵、消化水箱、输送仓泵 (利旧)、散装机、罗茨风机、管道等。
生石灰粉品质要求:
纯度:≥85%
细度:≤2mm
加适量水后4min 内温度可升高至60 ℃
干消化器采用三级干消化器,生石灰粉从现有生石灰粉仓通过气体输送至生石灰缓冲仓,通过计量给料机(含称重仓)进入三级干消化器,先在第一级消化器中进行预消化,然后再第二级消化器中,第三极消化器中进行消化,然后通过锁气器,喷射泵输送至消石灰粉仓储存。
其中,2×85t/h 循环流化床锅炉脱硫反应器消石灰粉仓,利用现有仓泵,移至新建
消石灰粉仓。通过散装机,密封槽车,运至新建1×135t/h 锅炉脱硫反应器消石灰仓。
消化器中设置挡板,挡板高度可调,调节石灰在消化器的停留时间。
图3-1 消化站控制界面
4. 吸收剂仓防板结措施
由于消石灰流动性较差,为了防止消石灰仓板结、下灰不畅,采取以下措施:
(1)对消石灰进行全面物性分析的前提下,考虑了料仓防渗漏及安息角等因素,储仓下部的锥斗与水平夹角不小于60 的大角度设计,有效的避免棚料的发生;
(2)储仓内壁设计光滑,无任何突出物限制消石灰的流动;
(3)消石灰仓的底部锥体内表面均布流化板,采用流化风给消石灰仓底部流化,以备当料仓低料位时松动吸收剂,确保料仓下料通畅。
以上措施充分保证了消石灰仓不产生堵塞、积灰现象。