纯净钢
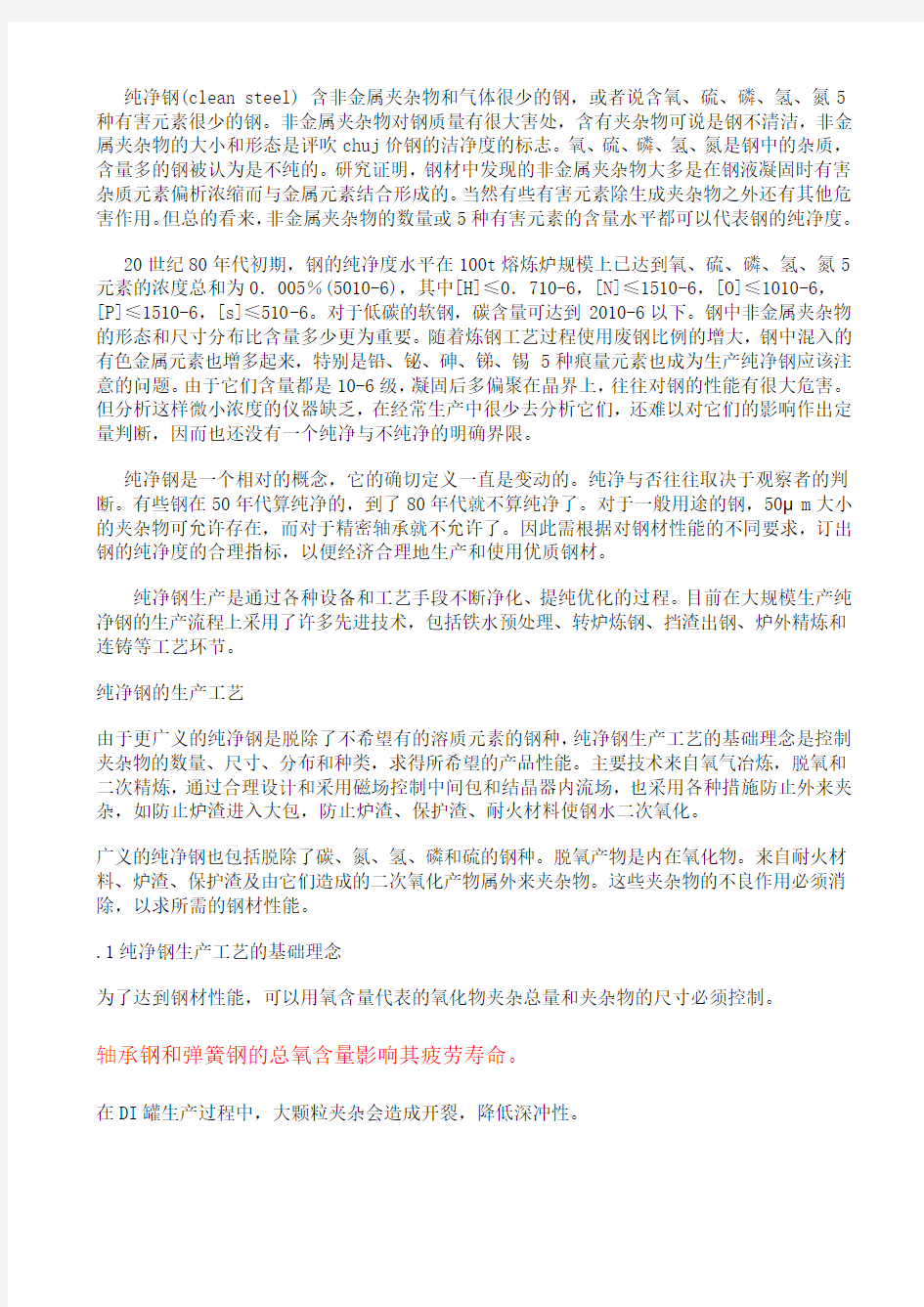

纯净钢(clean steel) 含非金属夹杂物和气体很少的钢,或者说含氧、硫、磷、氢、氮5种有害元素很少的钢。非金属夹杂物对钢质量有很大害处,含有夹杂物可说是钢不清洁,非金属夹杂物的大小和形态是评吹chuj价钢的洁净度的标志。氧、硫、磷、氢、氮是钢中的杂质,含量多的钢被认为是不纯的。研究证明,钢材中发现的非金属夹杂物大多是在钢液凝固时有害杂质元素偏析浓缩而与金属元素结合形成的。当然有些有害元素除生成夹杂物之外还有其他危害作用。但总的看来,非金属夹杂物的数量或5种有害元素的含量水平都可以代表钢的纯净度。
20世纪80年代初期,钢的纯净度水平在100t熔炼炉规模上已达到氧、硫、磷、氢、氮5元素的浓度总和为0.005%(5010-6),其中[H]≤0.710-6,[N]≤1510-6,[O]≤1010-6,[P]≤1510-6,[s]≤510-6。对于低碳的软钢,碳含量可达到2010-6以下。钢中非金属夹杂物的形态和尺寸分布比含量多少更为重要。随着炼钢工艺过程使用废钢比例的增大,钢中混入的有色金属元素也增多起来,特别是铅、铋、砷、锑、锡5种痕量元素也成为生产纯净钢应该注意的问题。由于它们含量都是10-6级,凝固后多偏聚在晶界上,往往对钢的性能有很大危害。但分析这样微小浓度的仪器缺乏,在经常生产中很少去分析它们,还难以对它们的影响作出定量判断,因而也还没有一个纯净与不纯净的明确界限。
纯净钢是一个相对的概念,它的确切定义一直是变动的。纯净与否往往取决于观察者的判断。有些钢在50年代算纯净的,到了80年代就不算纯净了。对于一般用途的钢,50μm大小的夹杂物可允许存在,而对于精密轴承就不允许了。因此需根据对钢材性能的不同要求,订出钢的纯净度的合理指标,以便经济合理地生产和使用优质钢材。
纯净钢生产是通过各种设备和工艺手段不断净化、提纯优化的过程。目前在大规模生产纯净钢的生产流程上采用了许多先进技术,包括铁水预处理、转炉炼钢、挡渣出钢、炉外精炼和连铸等工艺环节。
纯净钢的生产工艺
由于更广义的纯净钢是脱除了不希望有的溶质元素的钢种,纯净钢生产工艺的基础理念是控制夹杂物的数量、尺寸、分布和种类,求得所希望的产品性能。主要技术来自氧气冶炼,脱氧和二次精炼,通过合理设计和采用磁场控制中间包和结晶器内流场,也采用各种措施防止外来夹杂,如防止炉渣进入大包,防止炉渣、保护渣、耐火材料使钢水二次氧化。
广义的纯净钢也包括脱除了碳、氮、氢、磷和硫的钢种。脱氧产物是内在氧化物。来自耐火材料、炉渣、保护渣及由它们造成的二次氧化产物属外来夹杂物。这些夹杂物的不良作用必须消除,以求所需的钢材性能。
.1纯净钢生产工艺的基础理念
为了达到钢材性能,可以用氧含量代表的氧化物夹杂总量和夹杂物的尺寸必须控制。
轴承钢和弹簧钢的总氧含量影响其疲劳寿命。
在DI罐生产过程中,大颗粒夹杂会造成开裂,降低深冲性。
汽车板生产过程中,板坯的皮下夹杂物和针孔必须消除,不然会在板材表面造成
起皮。
对钢丝的拔制性讲,生产轮胎钢丝(子午线)或不锈钢钢丝的小方坯中夹杂物必
须控制其化学成分使其可以变形。这些就是纯净钢生产工艺的基础理念。
.2纯净钢生产的主要技术内容和应用这些技术后纯净钢的物化特性
.2.1降低氧化(jiang4 di1 yang3 hua4)物夹杂总量
在精炼领域,与顶吹相比,采用顶底复吹转炉在相同脱碳量时氧含量更低。这是因为底吹强化了碳的传输。采用RH和DH真空脱气,在相同碳含量时可降低氧含量。可用无渣出钢和钢水脱氧后用铝或铝粒降低炉渣的氧位,尽量减少大包内顶渣造成的二次氧化。连铸方面用电磁方法AMEPA,在大包钢渣开始进入中间包时就检测出来并关闭塞棒就可减少钢渣进入中间包的量。
在中间包上采用保护措施可减少顶渣造成的二次氧化。中间包和结晶器保护渣应防止钢水与空气直接接触。
.2.2 减少大颗粒夹杂
如60t的大容量中间包和H形中间包,前者可促进大颗粒夹杂长时间逗留,而后者则在浅熔池情况下使夹杂物向顶渣上浮而被除去。直弯型连铸机与弧型相比也更有利于大颗粒夹杂在结晶器内脱除。在板坯厚度方向上采用静态磁场,即所谓LMF(液面磁场),使浸入式水口两个孔的钢流出口速度下降,结晶器窄面的下降钢流减弱,使下降钢流的终点位于更浅的地位,结果使大颗粒夹杂上浮至洁净器顶渣的几率增加,不然就会造成内部缺陷。控制结晶器液面,选择最佳的结晶器保护渣和控制结晶器内流场可最大程度减少结晶器保护渣的卷入。
.2.3 降低板坯表面及皮下夹杂物
采用结晶器电磁搅拌(EMS)就感应形成平行于板坯表面的水平钢流。这种钢流向夹杂物施加Safman力,使夹杂物与生长的初始坯壳分离。
纯净铸钢和超纯净钢
1. 纯净铸钢
纯净铸钢系指不含氧化物、硫化物和氮化物等宏观夹杂的高质量铸钢件。氧化物、氮化物和硫化物夹杂的数量标示钢液的纯净度。对铸造碳钢和低合金钢而言,纯净铸钢杂质应控制在:[S]+[O](或[N])<200×10-6的水平。
影响铸钢纯净度的夹杂物来源主要是两类,其一是来自钢渣、型砂和耐火材料等,可归结为外来夹杂。其二是来自再氧化过程和脱氧剂在钢液中的化学反应产物,约占钢中夹杂的80%。如果脱氧产物中氧化物夹杂颗粒达到10μm以上,可认为是宏观夹杂。而氧化物宏观夹杂是造成铸钢件表面缺陷和内部缺陷最主要的原因。统计表明,铸钢件20%的直接成本消耗在清理
与氧化物有关的缺陷上。一般情况下,加铝脱氧的氧化物夹杂颗粒在5μm以下。聚集为大颗粒夹杂才有利于上浮排除。因此,控制夹杂物的数量、尺寸、形态和组成从而得到纯净铸钢件是采用控制熔炼工艺的一个重要内容。氩气净化、喂线、AOD、VOD和LF等精炼工艺是生产纯净钢液的较先进的工艺。
感应电炉生产纯净铸钢也是非常重要的领域。由于感应电炉主要功能是熔化,不进行氧化还原等冶金工艺过程,要获得纯净钢液和规定成分,主要依靠原材料的质量。采取氩气保护措施,将钢液表面尽可能与空气隔绝,是行之有效的方法,能够净化钢液,降低合金加入量和延长炉衬寿命。感应电炉的快速熔化技术、批量熔化技术和IF-AOD精炼技术是感应电炉生产纯净钢和超低碳不锈钢液的新工艺。
2.超纯净钢
超纯净钢可定义为[S]+[O](或[N])<100×10-6(对碳钢和低合金钢而言),有许多炼钢工艺可实现超纯净钢的精炼,如钢包喷粉、氩气净化、Ca-Si线喷射、真空精炼、EAF/AOD 双联工艺以及EAF/AOD/VOD三联工艺等。超纯净钢有许多优点,其韧塑性很高,容许缺陷的临界尺寸大,特别是低温性能显著改善以及大大减少铸造和形变产品的缺陷。总之,其力学性能随着有害杂质元素含量的降低而不断提高。
超纯净钢由于[O]、[S]、[N]和[H]等元素含量极低,因此表现出某些特殊的行为和特性,这些特性有可能对质量和性能带来不利的影响,因而在纯净钢生产过程中,要掌握和控制超精炼工艺对钢液的行为、随后的微观组织和各项性能以及质量的影响。例如,极低气体含量的超纯净钢液在出钢和浇注过程由于再氧化和吸入氢、氮气体而可能二次污染钢液。特别是用Al 脱氧的超低硫钢液,对氮的吸附更为突出。见图1。
含[O]极低也会有同样的作用。具有表面活性和起晶核作用的杂质元素的减少,是超纯净钢液一个重要特征。如果没有掌握相应的控制熔炼工艺,超纯净钢有些质量问题,就会出现如粗大晶粒、冰糖状断口、铸件缺陷(皮下气孔,热裂,宏观夹杂等)、未达到力学性能指标、氢脆、宏观组织特征、夹杂物的组成和含量确定等。采取相应的控制工艺措施包括加强出钢口的维护以保持密实钢流出钢,减少再氧化和吸收氮、氢气体;钢包氩气净化;在包中和浇注过程加Al,减少Al的加入量;采用局部陶瓷耐火材料浇注系统和浇注过程氩气保护,减少MgO 夹杂来源和防止结瘤;控制夹杂物组成和形态,保持一定比例的Ca量等。这些工艺措施是针对超纯净钢的特征而在生产中获得应用。
国内外纯净钢生产新技术
摘要:概述了近年来国内外先进炼钢厂的纯净钢生产新技术,系统地分析了碳、硫、磷、氢、氧、氮等元素在钢中的行为和降低钢中杂质元素的措施。分钢种(高级别管线钢、IF钢等)和厂家(新日铁、JFE、POSCO、宝钢、武钢等)统计了世界纯净钢生产先进指标。指出多工序分阶段精炼,大规模经济地生产纯净钢是发展趋势。
关键词: 纯净钢生产技术夹杂物IF钢管线钢
1 前言
随着市场对纯净钢需求的不断增加,国内外各大钢厂为了占有更大的市场份额和追求更高的利润,在开发和创新了许多纯净钢生产新技术的同时,不断扩大高附加值产品的生产。
生产纯净钢,一是要提高钢的纯净度,二是严格控制钢中非金属夹杂物的数量和形态。不同钢种对纯净度的要求和对夹杂物的敏感性不同。例如,氧化铝簇夹杂物可导致汽车和电气产品用薄钢板表面缺陷,也能引起DI罐用薄钢板裂纹,还可造成轮胎子午线等线材断线,以及使轴承钢等棒钢的疲劳性能恶化;对模具钢来说,提高其纯净度已经成为提高模具性能和寿命的重要手段,当SKD(H13)的硫含量从0.03%降低到0.01%时,可使钢的冲击韧性提高1倍。18Cr2NiMo不锈钢中磷含量从0.026%降到0.002%时,其耐硝酸腐蚀的能力提高100倍以上。表1为不同用途钢中的夹杂物含量的限制和尺寸要求。
表1 典型钢种的洁净度要求
钢种有害元素含量上限,/×10-4 % 夹杂物尺寸上限,/ μm
汽车板和深冲板[C]≤30, [N]≤30 100
DI罐[C]≤30, [N]≤30,T.O.≤20 20
管线[S]≤30, [N]≤35, T.O.≤30 ; [N]≤50 100
滚珠轴承T.O.≤10 15
轮胎帘线[H]≤2, [N]≤40, T.O.≤15 10
厚板[H]≤2; [N]30-40, T.O.≤20 单个夹杂13 ,点簇状夹杂200
线材[N]≤60; T.O.≤30 20
2 国内外纯净钢的研究和生产水平
目前,世界纯净钢生产与研发水平最高的是日本,其次是欧美和韩国。日本神户制钢250马氏体时效钢全氧含量已经达到(2~5)×10-4%。最近,新日铁开发了控制钢中夹杂物的新技术,通过向钢水中添加镁,控制夹杂物的成分,并细化夹杂物颗粒。采用该方法,使夹杂物的变形性能接近钢的变形性能,可以提高产品的韧性和加工性能,从而提高产品质量。
纯净钢生产是通过各种设备和工艺手段不断净化、提纯优化的过程。国内外各大钢厂在大规模生产纯净钢的生产流程上(包括铁水预处理、转炉炼钢、挡渣出钢、炉外精炼和连铸等工艺环节)采用了许多先进技术。
2.1 铁水预处理
20世纪80年代以来,铁水预处理已成为生产优质低磷、低硫钢必不可少的经济工序。其目标是将入转炉的铁水磷、硫含量脱至成品钢种水平。欧美各国铁水预处理一般以预脱硫为主,而日本铁水“三脱”预处理比例在90%以上。目前,基于铁水预处理的纯净钢冶炼工艺有两种:一种是铁水深脱硫处理+转炉脱磷、脱碳+钢水炉外喷粉脱磷、脱硫;另一种是铁水三脱预处理+复吹转炉少渣炼钢+钢水炉外喷粉脱硫。两种工艺均能生产[P]<0.010%、[S]<0.005%的纯净钢,但后者经济效益显著高于前者。
2.2 转炉生产
炼钢工序对产品质量起着决定性作用,采用转炉顶底复合吹炼技术可显著地降低钢水中的碳、磷含量。近十几年来,日本发明了转炉铁水预处理工艺,主要有SRP法(住友)、ORP法(新日铁)、NRP法(日本钢管)、H炉工艺(神户)、MURC法(室兰厂)等。据统计,转炉脱碳渣用于另一座转炉脱磷的“双联法”,生产1吨铁水的钢铁料消耗比传统方法减少25kg,石灰消耗减少40%,吨钢成本降低约65元。“双联法”适于大量地、经济地生产纯净钢。另外,转炉出钢挡渣效果对钢的纯净度和生产成本有严重影响。
2.3 炉外精炼
炉外精炼处理技术的兴起和发展,极大地丰富和扩展了炼钢流程的冶金功能,钢包精炼炉成为生产纯净钢的重要设备。在炼钢生产中,精炼炉具有脱硫、气体搅拌、合金化、升温、调节连铸节奏和控制夹杂物形态等功能。目前,日本先进钢厂生产的纯净钢杂质总含量已达到了0.005%。根据钢材对纯净度的不同要求,选择和组合不同的炉外精炼工艺,可以实现超纯净钢的生产。
2.4 连铸工艺
连铸工序对钢的纯净度影响很大,采用保护浇注﹑中间包冶金﹑新型中间包覆盖剂﹑调整保护渣性能及设置电磁搅拌等手段还可继续去除及控制夹杂物,降低废品率。国内外先进炼钢厂纯净钢生产各工序钢中全氧量参见表2。
此外,电磁搅拌技术和轻压下在连铸工序得到了广泛应用。当今世界上有400多台方坯连铸机安装了电磁搅拌装置,电磁搅拌已成为先进方坯连铸机的标准配置;许多板坯连铸机也安装了电磁搅拌和凝固末端轻压下设备。电磁搅拌和轻压下技术可改善铸坯内部凝固结构、扩大等轴晶区,从而减轻中心偏析和中心疏松。目前,奥钢联的动态轻压下和新日铁的面压下是比较先进的轻压下技术。
表2 国内外先进钢铁厂纯净钢生产各工序钢中全氧量
钢厂T.[O]/ ×10-4% 时间/年
精炼方法钢水包中间包结晶器板坯
美国Inland厂4号BOF LMF 30 24 21 15 1990
RH-OB 60-80 8-30 2003
美国阿姆克Middletown厂RH 60-105 15-40(25)16.9-23.8 1991 美钢联Lorain厂BOP 真空脱气13-17 1991
北美某厂20-35 20-30 10-15 1991
加拿大Dofasco钢厂 LF+RH 19 13
美国Weirton炼钢车间DravO-RH 23±10 22±12 1995
芬兰Rautaruukki Raahe钢厂48±12 32 38 17 1993
芬兰Koerhar厂气体搅拌32 23 2000
德国Dillinger厂10-15 10 ≤15 1994
荷兰霍戈文Ijmuiden厂真空脱气IF钢20-30 1994
法国索拉克Dunkirk厂RH-DB 20-50 1997
英钢联RH <10 1994
日本JFE川崎千叶厂RH 40 20 1989
韩国POSCO LF+RH 25-31 <10 1991
台湾中钢公司LF+RH <30 12 1994
中国武钢第2炼钢厂RH 28-34 24-26 12-19 2000
中国攀钢RH-MFB 20-24 2000
中国宝钢集团公司LF+RH 40 23 10 8 2003
注:()内数据为平均值
3 氧化物冶金
近10年来,氧化物冶金技术是国际冶金材料学术界和产业界广为关注的前沿技术。氧化物冶金技术的关键是通过精确地控制钢水凝固前沿的凝固条件对夹杂物的种类、大小和形态进行控制。该技术对改善高强度低合金钢种(HSLA)的焊接热影响区(HAZ)的韧性、开发超细晶粒钢有十分重要意义,有望得到大规模产业化应用。
4 高级别管线钢、IF钢等纯净钢的生产
目前,国内外先进流程生产的纯净钢(IF深冲汽车板和管线钢等)中有害元素[C、S、P、N、H、T?O] 之和可控制在100×10-4%以下,一些冶金学家还提出了超纯净钢的概念,并将超纯净钢界定为夹杂物[C、S、P、N、H、T?O]之和在40×10-4%以下。2000年钢中各杂质元素单体控制水平为:[C]:4×10-4%;[S]:0.6×10-4%;[P]:3×10-4%;[N]:6×10-4 %;[H]:0.5×10-4%;T?[O]:2×10-4%。
宝钢在纯净钢单项生产技术开发的基础上,较为妥善地解决了各工序间的配合关系、杂质元素相关制约关系、净化后钢水再污染等问题。IF钢纯净度达到[C]≤16×10-4%、[N]≤15×10-4%、T[O]≤19×10-4%;管线钢纯净度可达到[S]≤9×10-4%,[P]≤50×10-4%,T[O]≤16×10-4% [N]≤30×10-4%,[H]≤1. 5×10-4%;达到了国际同类产品的先进水平。
武钢的深脱碳、深脱硫、钙处理及控制氮、氧的纯净钢冶炼工艺,使钢中有害元素总量指标达到国际先进水平,生产出以IF钢为代表的超低碳、低氮、低全氧的冷轧深冲薄板,及以X60、X70为代表的具有良好冲击韧性、冷弯性能和抗腐蚀、抗裂纹性的高级管线钢,彩电系列用钢、制币钢、精密轴瓦用钢、冷轧
电磁钢等。目前,武钢三个炼钢厂的铁水预脱硫比均达到70%以上,硫含量可达20×10-4%以下,脱硫率达90%以上。钢的碳含量最低为9×10-4%、氮含量最低为12×10-4%、氧含量最低为10×10-4%。该厂的产品已供货一汽、二汽等多家汽车公司。
攀钢的SP52超细晶粒钢性能达到510MPa强度级别,用于冲压东风汽车零部件。
2003年6月12日,鞍钢第一炼钢厂精炼后的钢水有害元素[S、P、N、H、T?O]之和达到63.96×10-4%,是目前国内最好水平。
欧美和日本的先进钢厂正致力于建立以转炉为中心的大规模生产纯净钢的生产流程,其IF钢的生产比例达到了50%~70%,[S]≤0.003%的超低硫钢生产比例达到了20%~30%。国内外一些先进钢厂的纯净钢生产水平参见表3。
表3 国内外一些先进钢厂的纯净钢生产水平Unit:×10-4%
厂家[C][P][S][N][H] T.[O]合计钢种工艺
日本神户制钢 3 20 2-3 6-9 1.0 2-5 41(34) 250马氏体时效钢真空感应炉
日本新日铁10(3) 25 3 14 1.0 5 58(52) 深冲钢LD-OB +RH
德国蒂森20 15 5 15 0.7 10 65.7 深冲钢LD+真空脱气
韩国浦项5-8 80(未计[c])轴承钢BOF+LF+RH
中国宝钢≤15 15 5-10 11 ≤1.0 ≤8-15 67(55)IF钢.管线钢BOF+LF+RH
中国武钢9 40 3.4 12 1.0 10 81.4 IF钢.管线钢BOF+LF+RH
中国攀钢18 24 12 2.0 18 74(未计[c])深冲钢BOF+LF+RH
中国鞍钢20 5 20 0.96 18 63.96(未计[c])管线钢BOF+LF+VD
注:()内为最低值
5 结论
纯净钢与非金属夹杂物是当今冶金界的科研热点,近20年来有关夹杂物的文章超过1万份。目前,氧化物冶金技术成为广为关注的前沿技术,对开发超细晶粒钢有十分重要意义。
随着炼钢技术的发展,钢水成分的控制范围越来越窄,钢的机械性能越来越稳定。多工序分阶段精炼,大规模经济地生产纯净钢是发展趋势。
武钢生产实习报告
生产实习报告 一、实习目的 生产实习是材料成型及控制工程专业重要的教学环节,是专业课教学的一个重要组成部分。通过在实习厂主要岗位的生产劳动、现场参观、现场教学和讨论,熟悉各实习厂的生产工艺流程及其原理;了解主要设备的性能和结构;了解主要经济技术指标的制定依据及测试手段。 1.将所学的《物理冶金学基础》、《材料科学基础》、《机械设计基础》、《材料成型力学》等专业基础课知识与生产实践相结合,进一步加深对理论知识的理解。 2.了解材料成型相关生产工艺流程,原料及产品,生产设备及主要技术经济指标,获得材料成型工艺、设备基本知识,为进一步深入学习专业知识打好基础。 3.培养学生调查研究,搜集整理资料,分析问题和解决实际问题的能力。 4.学习工程技术人员和工人师傅在长期实践中积累的丰富经验,学习他们勤奋工作的精神和实事求是的工作作风。 二、实习要求 2.1习期间,要听从厂房技术人员的指挥,不得任意行动 2.2 “两穿一戴”,穿劳保服劳保鞋,戴安全帽 2.3 认真对待各级交待的实习安排,不缺勤,不早退,注意安全。 2.4 遵守交通规则及车间劳动纪律,严防安全事故的发生。 2.5 认真听课,勤做笔记,按时独立完成实习报告。 三、实习内容 3.1武汉钢铁集团简介 武钢是新中国成立后由国家投资建设的第一个特大型钢铁联合企业,于1955年10月破土动工,1958 年9月13日正式投产。武钢厂区座落在武汉市青山区,占地面积21平方公里。所辖的4座铁矿、2座辅助原料矿分布在鄂东、鄂南及河南焦作。 武钢是中国重要的板材生产基地,拥有从矿山采掘、炼焦、烧结、冶炼、轧钢等一整套工艺设备。改革开放特别是党的十四大以来,武钢循序渐进地深化内部改革,高起点地推进技术进步,持续不断地强化企业管理,坚持不懈地培育“四有”职工队伍,成功地走出了一条质量效益型与科技创新型相结合的道路。到2003年底,武钢已拥有固定资产原值473.13亿元,净值239.10亿元;累计生产铁1.50亿吨、钢1.41亿吨、钢材1.10亿吨;累计实现利税524亿元,其中上缴国家405.18亿元,是国家对武钢投资64.2亿元的6.3倍。武钢现已形成年产钢铁各900万吨的综合能力,主要生产热轧卷板、冷轧卷板、镀锌板、镀锡
包钢生产实习报告
包钢生产实习报告 一、实习目的: 生产实习是我们冶金专业知识结构中不可缺少的组成部分。通过这次对炼钢厂的生产实习,在老师的讲解和共人师傅的解说,以及自己在炼钢厂各个岗位实践下,我们对钢铁生产的主要设备和工艺流程,运输联系、工厂布局,有了一个较全面的认识。通过理论和实际的相结合更深入的学到了炼钢知识,同时也学到一些基本安全技术知识。这些实际知识,对我们学习后面的课程乃至以后的工作,都是十分必要的基础。这也是我们将走向工作岗位前的一次演练。 二、实习时间:2008年9月 三、实习地点:包头钢铁(集团)有限责任公司 四、实习的部门: 炼铁厂4号高炉:1值班室2热风炉岗位3岗位炉前岗位4高炉供料岗位5喷吹站岗位6烧结厂炼钢厂二部:1连铸2 炉外精炼3转炉炼钢4脱硫扒渣 五、包钢概况: 包钢是我国重要的钢铁工业基地和全国最大的稀土生产、科研基地,是内蒙古自治区最大的工业企业。1954年建厂,公司位于内蒙古自治区包头市河西工业区,中心厂区占地面积36平方公里。包钢拥有“包钢股份”和“包钢稀土”两个上市公司,截至2007年末,集团资产总额572亿元,员工5.7万人。 包钢有得天独厚的资源优势。包钢白云鄂博矿是举世瞩目的铁、稀土等多元素共生矿,是西北地区储量最大的铁矿,稀土储量居世界第一位,铌、钍储量居世界第二位,包头也因白云鄂博矿而被誉为“世界稀土之都”。 包钢拥有世界一流水平的冷轧和热轧薄板及宽厚板、无缝钢管、重轨及大型材、线棒生产线,是我国三大钢轨生产基地之一、品种规格最齐全的无缝钢管生产基地之一、西北地区最大的薄板生产基地。包钢已经进入我国千万吨级钢铁企业行列。 截止2006年9月,包钢累计产铁9620万吨,产钢9348万吨,生产商品坯材6818万吨,累计上缴税金215亿元,有力地支持了国民经济的发展。今年包钢预计产钢1000万吨,其中8月份,包钢生铁产量突破80万吨,达到8072万吨,创月产铁量历史新纪录。包钢是自治区最大的纳税户,上缴税金占自治区地方财政收入的1/10左右。包钢现有近10万名职工(包括在岗职工、离职退休职工和离职休养职工),是自治区最大的就业基地,并且职工收入不断提高,特别是1998年改制以来,职工收入大幅增长,2007年包钢职工人均收入高达3.5万元。 包钢始终以高度的社会责任感节约资源、保护环境。在行业内首家实现高炉全干法除尘,率先建设全国示范生态工业园区,被列为全国首批循环经济试点单位之一,在我国2007年首次评比的“中国能源绿色企业50佳”中,包钢位列第一。 六、实习内容: (一)炼铁厂 1.炼铁厂简介 在包钢炼铁厂有6座高炉,我们小组被分到在4号高炉进行生产实习,包钢4号高炉于1995年11月14日建成投产,当时处于世界先进水平。四号高炉采用四座外燃式热风炉皮带上料,炉顶引进了卢森堡无钏布料器,炉前是环形出铁口,炉内采用美国霍尼韦尔公司计算机控制系统,通过触摸式控制台使高炉冶铁实现全部自动化操作。 2.高炉主控室 高炉值班室是整个高炉的控制系统,对于每一个岗位的现场操作有基本的监视与控制,而工作就正常记录高炉现场配料与边料的计算与调整,炉温和炉缸的工作状况,煤气分布,风温及风压。而对于煤气流分布失常,炉冷与炉热,难行与悬料,连续崩料,管道行程与偏料,炉缸堆积与冻结等事故进行预防和处理。我们值班室发现师傅在每隔一段时间就要进行一次记录,每次都有一次对比,当发生有什么不对的地方就要和现场的师傅及时的进行沟通,以进行预防和处理。
高强钢炼钢生产的工艺研究与应用
高强钢炼钢生产的工艺研究与应用 丁中刁承民张海民刘国刘建伟 (济南钢铁集团公司炼钢厂,济南 250101) 摘 要 本文研究了高强钢的生产工艺路线和关键控制因素,以及对操作进行的优化和改进。同时对生产过程的控制参数进行了研究和分析,优化了生产工艺流程,实现了低合金高强钢单线稳定、批量生产的目的。 关键词 高强钢夹杂物软吹氩脱氢 The Studies and Applications of High Strength Steel in the Steelmaking Plant Ding Zhong Diao Chengmin Zhang Haimin Liu Guo Liu Jianwei (Steelmaking Plant of Jinan Iron and Steel Group Corp, Jinan, 250101) Abstract The article introduced the high strength steel production process , key controlling factor , optimized and ameliorated of the operation. And studied and analyzed the parameters process controlling, optimizing the routing, realizing to producting stabile and in a large scale the high strength steel. Key words high strength steel, inclusion, soft bubbling, dehydrogenation 随着社会经济的发展,工程机械和煤机行业用高强钢向着高参数化、轻量化、大型化的方向发展,因此提高低合金产品强度和质量是钢铁企业发展的趋势,也是提高市场竞争力的必要手段。济钢210t转炉作业区充分利用现有装备的有利条件,在低合金高强钢的生产过程中通过工艺优化和技术改进获得了丰富的生产经验,并掌握了高强钢生产的关键技术,完善了设备的冶金功能,逐步实现了一系列低合金高强度钢批量生产的能力。 1 生产工艺 1.1生产设备状况简介 济钢炼钢厂210t转炉作业区于2009年12月26日建成投产,现有KR铁水脱硫、210t转炉、LF精炼炉、RH精炼炉各一座、DANIELI板坯连铸机一台,主要生产250mm厚度的铸坯,钢种包含船板钢、高强度钢、容器钢、管线钢以及其他一些特殊用钢,年产量150万吨左右。目前该区域已经实现了100%钢水精炼处理工艺,其中RH处理比率平均达到58%左右 1.2低合金高强钢的生产工艺 根据低合金高强度钢的轧制以及用户使用要求,实际生产中制定了相应的工艺路线,按照KR-转炉-LF-RH-CCM的生产工艺路线进行生产。 丁中,男,本科,工程师,从事炼钢、炉外精炼技术研究和管理工作,tinsion8888@https://www.360docs.net/doc/933471213.html,
ASEA-SKF钢包精炼炉脱氧工艺研究(doc 9页)
ASEA-SKF钢包精炼炉脱氧工艺研究(doc 9页)
方案出钢/kg。t-1倒包/kg。t-1真空后净化搅拌/min 1 加铝0.6 加铝0.9 喂Ca-Si线1.5kg/t 吹氩,15 2 脱氧剂1.6 脱氧剂2.2 喂Al线Als=0.020% 吹氩,10 3 脱氧剂1.6 脱氧剂2.2 Al 0.25kg/t,Si-Al-Ba 1.5kg/t 电磁搅拌,5 注:表中脱氧剂指钙系脱氧剂 表2 脱氧材料成份(w) % 材料名称 C Ca Si Al Ba Ca-Si 28.4 55.6 钙系脱氧剂 20 37.2 16 Si-Al-Ba 36.24 19.79 12.76 3 几种脱氧材料的冶金特性 3.1 铝 铝主要用于钢液脱氧,其脱氧产物为固态的 Al 2O 3 ,反应式为: 2[Al]+3[O]=Al 2 O 3 ΔG°=1225000-393.8T (1) 由热力学计算可以看到铝的脱氧基本上在1873K高温下完成,即加铝后的片刻之内,绝大部分氧就由溶解态转变为氧化物而析出。文献资料[1]表明,含碳0.50%的钢,铝脱氧的二、三次脱氧产物占总量的22.5%~50.4%,这也说明铝脱氧速度很快,脱氧产物主要为一次生成。由式(1),若设[Al](w)为0.025%,钢液在1520℃~1600℃变化时,钢中溶解氧可以从3×10-6降至0.5×10-6。因此,在精炼条件下,脱氧过程是一个夹杂物去除过程,一般可将这样一个脱氧过程看成一个准一级反应,即: [O] t =[O] exp(-S/V。kt) (2) 式中[O] t ——精炼后t时间的含氧量/×10-6 V——钢液体积/m3 [O] o ——精炼初始时刻的含氧量/×10-6 k——钢液脱氧的传质系数/m。s-1 S——钢渣界面积/m2 t——脱氧时间/s
武钢参观实习报告
目录 1. 实习概况 (1) 1.1实习时间 (1) 1.2实习地点 (1) 2.实习地点简介 (1) 2.1武汉钢铁集团简介 (1) 3. 实习内容及过程 (3) 3.1参观炼铁厂.......................................... 错误!未定义书签。 3.2参观炼钢厂.......................................... 错误!未定义书签。 3.3热轧厂.............................................. 错误!未定义书签。 3.4参观冷轧钢厂........................................ 错误!未定义书签。 3.5武钢博物馆.......................................... 错误!未定义书签。 3.6武钢高新技术产业园.................................. 错误!未定义书签。 3.7通信分公司.......................................... 错误!未定义书签。 4.参观体会................................................. 错误!未定义书签。
1.实习概况 1.1 实习时间:2016年7月27日至 2013年8月9日 1.2 实习地点:武汉钢铁公司 2.实习地点简介 2.1武汉钢铁集团简介 武汉钢铁公司,以下简称武钢。武钢是新中国成立后兴建的第一个特大型钢铁联合企业,于1955年开始建设,1958年9月13日建成投产,是中央和国务院国资委直管的国有重要骨干企业。本部厂区座落在湖北省武汉市东郊、长江南岸,占地面积21.17平方公里。武钢拥有从矿山采掘、炼焦、炼铁、炼钢、轧钢及配套公辅设施等一整套先进的钢铁生产工艺设备,是我国重要的优质板材生产基地,为我国国民经济和现代化建设作出了重要贡献。武钢联合重组鄂钢、柳钢、昆钢后,已成为生产规模近4000万吨的大型企业集团,居世界钢铁行业第四位,2010年,武钢跻身世界500强行列。
纯净钢生产工艺及其应用
纯净钢生产工艺及其应用 由于更广义的纯净钢是脱除了不希望有的溶质元素的钢种,这类代表性钢种要求的这类溶质元素的含量及其生产流程。重点是有害氧化物夹杂的纯净化。纯净钢生产工艺的基础理念是控制夹杂物的数量、尺寸、分布和种类,求得所希望的产品性能。 主要技术来自氧气冶炼,脱氧和二次精炼,通过合理设计和采用磁场控制中间包和结晶器内流场,也采用各种措施防止外来夹杂,如防止炉渣进入大包,防止炉渣、保护渣、耐火材料使钢水二次氧化。然后根据IISI的纯净钢工作小组最近的报告总结了世界纯净钢生产的概况。最后讨论了纯净钢的特性、使用效果和钢中夹杂物物化性能的关系和经济可行性。 广义的纯净钢也包括脱除了碳、氮、氢、磷和硫的钢种。脱氧产物是内在氧化物。来自耐火材料、炉渣、保护渣及由它们造成的二次氧化产物属外来夹杂物。这些夹杂物的不良作用必须消除,以求所需的钢材性能。 1纯净钢生产工艺的基础理念 为了达到钢材性能,可以用氧含量代表的氧化物夹杂总量和夹杂物的尺寸必须控制。轴承钢和弹簧钢的总氧含量影响其疲劳寿命。在DI罐生产过程中,大颗粒夹杂会造成开裂,降低深冲性。汽车板生产过程中,板坯的皮下夹杂物和针孔必须消除,不然会在板材表面造成起皮。对钢丝的拔制性讲,生产轮胎钢丝(子午线)或不锈钢钢丝的小方坯中夹杂物必须控制其化学成分使其可以变形。这些就是纯净钢生产工艺的基础理念。 2纯净钢生产的主要技术和应用这些技术后纯净钢的物化特性 2.1降低氧化物夹杂总量 在精炼领域,与顶吹相比,采用顶底复吹转炉在相同脱碳量时氧含量更低。这是因为底吹强化了碳的传输。采用RH和DH真空脱气,在相同碳含量时可降低氧含量。可用无渣出钢和钢水脱氧后用铝或铝粒降低炉渣的氧位,尽量减少大包内顶渣造成的二次氧化。连铸方面用电磁方法AMEPA,在大包钢渣开始进入中间包时就检测出来并关闭塞棒就可减少钢渣进入中间包的量。在中间包上采用保护措施可减少顶渣造成的二次氧化。中间包和结晶器保护渣应防止钢水与空气直接接触。 2.2减少大颗粒夹杂 如60t的大容量中间包和H形中间包,前者可促进大颗粒夹杂长时间逗留,而后者则在浅熔池情况下使夹杂物向顶渣上浮而被除去。直弯型连铸机与弧型相比也更有利于大颗粒夹杂在结晶器内脱除。在板坯厚度方向上采用静态磁场,即所谓LMF(液面磁场),使浸入式水口两个孔的钢流出口速度下降,结晶器窄面的下降钢流减弱,使下降钢流的终点位于更浅的位置,结果使大颗粒夹杂上浮至洁净器顶渣的几率增加,不然就会造成内部缺陷。控制结晶器液面,选择最佳的结晶器保护渣和控制结晶器内流场可最大程度减少结晶器保护渣的卷入。 2.3降低板坯表面及皮下夹杂物 采用结晶器电磁搅拌(EMS)就感应形成平行于板坯表面的水平钢流。这种钢流向夹杂物施加Safman力,使夹杂物与生长的初始坯壳分离。当粘性拉力与Saf man力共同作用,最终使夹杂物速度大于初始坯壳的生长速度时,夹杂物就不可能为生长的坯壳所捕获,即EMS 感生的钢流把夹杂物洗刷出去了。直径100μm的夹杂物可用速度为0.3m/s的水平钢流洗刷掉。 在电磁连铸中(EMC),在结晶器外水平绕一线圈,并通以交流电。垂直磁场和铸件内感生的水平方向的次级电流相互作用产生的劳伦兹(Lorenz)力即使交流电流方向改变也总是向内的。这样,对初始坯壳总形成一个束紧的力,并支撑着坯壳,初始坯壳与结晶器表面间的间隙就增大,从结晶器吸收的热量下降,实现了缓冷。由于较低的冷却速度,初始坯壳不会在弯月
纯净钢专题
纯净钢专题 摘要:本文从杂质元素对钢材机械性能的影响开始,引出纯净钢的概念,并分析了纯净钢的应用领域以及目前国内外先进的纯净钢生产技术和未来纯净钢的发展方向,最后列出纯净钢检测方法以期指导纯净钢生产实践。 关键词:纯净钢超纯净零非金属夹杂钢 引言:炼钢工业化的百年历史是沿着钢材纯净化和合金化的方向不断前进的。近年来随着钢铁材料在材料领域的广泛应用,外界对钢材的质量要求越来越高标准化。在关系国计民生的汽车、建筑、天然气、压力容器、电工材料等领域都要求钢材的优良机械性能和使用性能,纯净钢的发展适时的满足了这写领域的需要,但同时这些领域也为纯净钢发展提出了新的要求和方向。 一、钢中杂质元素对其机械性能的影响 硫:硫在钢中以硫化物(MnS、FeS、CaS等)形式存在,对力学性能的影响是::(1) 使钢材横向、厚度方向强度、塑性、韧性显著低于轧制方向(纵向),特别是钢板低温冲击性能; (2) 显著降低钢材抗氢致裂纹能力,因此用于海洋工程、铁道桥梁、高层建筑、大型储氢罐,钢板[ S] ≤50×10-6。硫还影响钢材抗腐蚀性能,用于输送含H2 S等酸性介质油气管线钢,[ S]降至(5~10)×10- 6。此外硫对钢材热加工性能、可焊性均发生不利影响。 磷:由于磷是表面活性杂质,在晶界及相界面偏析严重,往往达到平均浓度的数千倍,因此洁净钢要求[ P] ≤100×10- 6。 氮:氮对钢材的危害是:(1) 加重钢材时效;(2)降低钢材冷加工性能;(3) 使焊接热影响区脆化。 氧:钢中氧含量过高会引起角状夹杂物及宏观夹杂物增多,易于发生脆性断裂,而且非金属氧化物夹杂物含量过高也会影响钢表面质量。 钢中的碳含量直接影响钢中组织形态,对于不同钢种其标准不同。 表1钢中杂质元素对其机械性能的影响
武钢实习报告
机械工程及自动化专业认识实习报告武汉科技大学机械自动化学院(2013年9月)实习学生: 2011级机工1106班姓名文维学号 201103130230 一、实习目的 1.初步了解钢铁联合企业主要生产流程及主要设备所在位置与用途 2.通过在实习厂主要岗位的现场参观、现场学习和讨论,提高分析问题和解决问题的能力,培养科学的思维方法和加强理论联系实际的能力。 3.在学习工程技术人员和工人师傅在长期实践中积累的丰富知识和经验的同时,学习他们勤奋工作的精神和实事求是的作风,增强热爱专业,热爱劳动的思想。 4.了解自己专业方面的知识和专业以外的知识,让我们早认识到我们将面临的工作问题,让我明白了以后读大学是要很认真的读,要有好的专业知识,才能为好的实际动手能力打下坚实的基础。 5.通过认识实习认识钢铁生产企业的概貌,了解钢铁企业的主要生产工艺,增加对安全工程专业学科的感性认识,了解安全工程专业在国民经济建设中的地位、作用和发展趋势,熟悉安全工程技术人员的工作职责和工作程序,了解企业安全管理的现状和模式。 二、实习内容 武钢简介:武钢1955年始建,1958年9月13日建成投产。拥有从矿山采掘、炼焦(产能吨)、炼铁(产能吨)、炼钢(产能吨)、轧钢及配套公辅设施等一整套先进的钢铁生产工艺设备,是我国重要的优质板材生产基地。
武钢现已成为生产规模近4000万吨的大型企业集团,居世界钢铁行业第四位,2010年,武钢跻身世界500强行列。现有钢铁制造业、高新技术产业和国际贸易三大主业。产品主要有热轧卷板、热轧型钢、热轧重轨、中厚板、冷轧卷板、镀锌板、镀锡板、冷轧取向和无取向硅钢片、彩涂钢板、高速线材等几百个品种。 (一).炼铁厂实习报告 实习时间2013年09月16日实习地点武钢炼铁厂指导老师:王涛 1.武钢股份公司炼铁总厂简介 武钢股份公司炼铁总厂于2008年6月成立,包括烧结分厂、炼铁分厂,是武钢生产烧结矿和制钢生铁、铸造生铁的首道工序厂,具有精良的生产装备和先进的技术优势,主要经济技术指标在国内外同行业中处于领先地位。 武钢炼铁主要原料包括烧结矿、球团矿、块矿(海南矿、南非矿以及澳矿等)、熔剂(以石灰石和白云石为主)、焦炭、煤粉和热风等,这些都有相应的车间进行准备。高炉的入炉熟料率达80%~85%,外加少量品位较高的块矿和球团矿,炉料碱度为1.8。高炉炉顶采用并罐式无钟炉顶设备,可以使炉顶压力相应提高,有利于高压操作。并罐式无钟炉顶由受料漏斗、称量料罐、中心喉管、气密箱、旋转溜槽等五部分组成。 2.炼铁厂主要生产流程 炼铁是指将金属铁从含铁矿物(主要为铁的氧化物)中提炼出来的工艺过程,主要有高炉法,直接还原法,熔融还原法,等离子法 高炉炼铁是指把铁矿石和焦炭,一氧化碳,氢气等燃料及熔剂装入高炉中冶炼,去掉杂质而得到金属铁(生铁)。 其反应式为: Fe2O3+3CO=3CO2+2Fe Fe2O3+3H2=3H2O+2Fe 2Fe2O3+3C=3CO2+4Fe 高炉炼铁主要设备有高炉、高炉热风炉、铁水罐车。高炉是横断面为圆形的炼铁竖炉,用钢板作炉壳,里面砌耐火砖内衬。高炉生产是连续进行的。生产时,从炉顶(一般炉顶是
首钢“一级研发、多地分布”技术创新体系建设
首钢“一级研发、多地分布”技术创新体系建设 钢铁业作为国家重点要求推进兼并重组的行业,经过几年来的结构调整,其产业集中度逐步提高。兼并重组后的大型钢铁企业为解决大而不强的问题,不断加大研发投入,加强科技创新,以提高企业的自主创新能力和国际竞争力。大型企业集团形成跨地域分布的格局后,如何聚集技术源和技术资源,如何合理布局和高效利用科技资源,保证技术创新体系的科学构建和有效运行,成为大型企业科技创新过程中需要解决的突出问题。因此,建立适合跨地域大型企业的科研体系是各大型企业集团增强自主创新能力,保证快速发展的必然选择。首钢自主创建并日趋完善的“一级研发、多地分布”技术创新体系,为我国钢铁企业搬迁调整和跨地区兼并重组后技术资源的合理布局与高效利用,技术的快速转移与技术系统的有效管控,体制与机制的创新提供了借鉴和示范。 随着我国产业结构调整和优化升级,越来越多的大型企业逐步形成了跨地区的发展格局。现有的大型跨地区企业研发模式主要是“集中研发”和“分散研发”。“集中研发”有利于各地研发人员形成合力,保证新产品和工艺技术实验室研究的高效运行,但不可避免地会出现实验室研究与生产现场需求脱离、研发成果难以高效应用的问题。“分散研发”有利于研发工作与生产现场的紧密结合,保证研发成果快速向生产现场的转移,但不利于全公司范围的资源共享、产品研发和生产的统一管理。首钢在分析上述两种研发模式的基础上,结合自身实际,调整技术创新发展战略,创建了“一级研发、多地分布”技术创新体系。实践证明,这种科研体系实现了科技资源的合理布局和技术创新体系高效运行。 1 首钢技术创新体系建设的基本思路 按照有利于新建生产线尽快发挥效能、新产品快速开发、科技成果的快速培育、科技成果快速转化为生产力、集团技术创新能力的提高、建设创新型企业的指导思想,以科技资源的合理布局和技术系统的高效管控为原则,通过观念和组织模式的创新,派驻站的合理定位,科研管理的创新,技术管理一体化,对外合作的统一管理等措施,取得了明显成效,对国内大型钢铁集团技术创新体系的构建和优化具有借鉴和示范作用。 2 首钢技术创新体系建设的创新实践 2.1 观念及组织模式创新 作为首钢技术创新实施层核心的首钢技术研究院,担负着首钢工艺技术进步及新产品开发,对首钢集团技术系统的管控以及公司人才孵化培养的任务。随着钢铁业“一业多地”的形成,首钢产品结构开始由长材向板材转型,由于缺乏板材生产经验和理解,高品质板材产品技术积累不足,使科研开发工作面临巨大挑战。针对实际问题,首钢采取两项举措:一是充分利用社会优势资源,解决技术源的问题,建立了汽车板、电工钢、宽厚板三个长期长效实体式的产学研合作平台;二是为充分利用技术研究院的技术资源,采取科研重心向生产线下移的方式,在首秦、迁钢、顺义冷轧、京唐建立派驻工作站,把科研人员放到生产一线。 在这一框架下,技术研究院、派驻工作站及生产基地技术力量的职能和任务进行了新的分工。技术研究院主要按照四地生产和研发的需要,统一规划和组织相关的科技研发和技术管理工作,为四地提供技术支持,主要针对多地的共性关键工艺技术、用户技术和重大产品开发开展科研攻关。生产基地不再设立研发机构,其技术力量主要配合新产品开发和生产线的技术措施和技术改造的实施及其技术管理。派驻工作站一方面把研究院共性工艺技术和产品开发的研究任务带到现场,结合各生产线实际积累技术,丰富经验,攻克难关,把取得的科研成果及时应用到生产上,服务于生产实际,另一方面把一些前沿的、需要深入研究和分析的问题,带回技术研究院总部,充分利用总部的设备和人才库,进一步深入研究。 派驻工作站作为公司科研和技术管理与生产基地融合的纽带、科研人员贴近现场的工作平台、现场产品开发的一支重要力量以及复合型人才的培养基地,实现了科技资源的合理布
ASEA-SKF钢包精炼炉脱氧工艺研究
注:表中脱氧剂指钙系脱氧剂 表2 脱氧材料成份(w) % 3 几种脱氧材料的冶金特性 3.1 铝 铝主要用于钢液脱氧,其脱氧产物为固态的 Al 2O 3 ,反应式为: 2[Al]+3[O]=Al 2 O 3 ΔG°=1225000-393.8T (1) 由热力学计算可以看到铝的脱氧基本上在1873K高温下完成,即加铝后的片刻之内,绝大部分氧就由溶解态转变为氧化物而析出。文献资料[1]表明,含碳0.50%的钢,铝脱氧的二、三次脱氧产物占总量的22.5%~50.4%,这也说明铝脱氧速度很快,脱氧产物主要为一次生成。由式(1),若设[Al](w)为0.025%,钢液在1520℃~1600℃变化时,钢中溶解氧可以从3×10-6降至0.5×10-6。因此,在精炼条件下,脱氧过程是一个夹杂物去除过程,一般可将这样一个脱氧过程看成一个准一级反应,即: [O] t =[O] exp(-S/V。kt) (2) 式中[O] t ——精炼后t时间的含氧量/×10-6 V——钢液体积/m3 [O] o ——精炼初始时刻的含氧量/×10-6 k——钢液脱氧的传质系数/m。s-1 S——钢渣界面积/m2 t——脱氧时间/s 由(2)可见,精炼时间越长,钢中氧含量越低,即通过有效的搅拌和足
够的精炼时间,可以使Al 2O 3上浮去除,从而降低钢中的氧含量。 3.2 硅铝钡 Si-Al 复合脱氧的产物可能是SiO 2,Al 2O 3,3Al 2O 3。2SiO 2及FeO 。 Al 2O 3,2FeO 。 SiO 2等,但在一般的炼钢过程中,钢液中[Si ]、[Al ]、[O ]都处于常规范围内,Si-Al 复合脱氧的产物主要为3Al 2O 3。2SiO 2或Al 2O 3。在钢液中[O ]含量较高时,脱氧产物主要是3Al 2O 3。2SiO 2,而随着氧含量的降低,脱氧产物以Al 2O 3为主。 Si-Al 复合脱氧反应式为: 6[Al ]+2[Si ]+13[O ]=3Al 2O 3。2SiO 2(s) ΔG°=-4679530.9+1506.14T (3) 1600K 时,K=[O ]13[Si ]2[Al ]6=1.29×10-52 在Si-Al 复合脱氧的基础上引入钡,形成硅铝钡复合脱氧剂,这种脱氧材料近几年在冶金中的应用越来越广。钡的高沸点是优于钙、镁的重要特性。钡对夹杂物的变性作用主要表现为降低夹杂物的熔点,改善夹杂物的形状和尺寸以及使杂物分布均匀化。因此,含钡合金应用于炼钢过程,除能减少铝的消耗外,还能改变钢中夹杂物的形态及结晶组织的弥散度和均匀性,减少钢中夹杂物的含量,净化钢液,从而提高钢材质量,优化使用性能。 3.3 钙 金属钙是很好的钢液净化剂,大多用于钢液的深脱氧和深脱硫。硅铝 脱氧的钢,钢中[O ]已很低,一般在5×10-6 左右,此时,钙直接脱氧反应不是主要的,但钙可以与大量存在于钢中的Al 2O 3发生反应,其反应式为: xCa+yAl 2O 3= {x(CaO)。(y-1/3x)Al 2O 3}+2/3xAl (4) 钙在这些Al 2O 3夹杂颗粒中扩散,使钙连续地进入铝的位置,置换出来的铝进入钢液。随着钙的扩散,在Al 2O 3夹杂表面CaO 含量升高,当CaO >25%时,钙铝酸盐呈液态,这种含CaO 量高的液态钙铝酸盐夹杂物大部分浮出钢液,进入渣层,从而降低钢中的全氧。 钙也是一种很好的深脱硫剂,其反应式为: Ca (g)+[S ]=CaS (s) ΔG°=-136380+40.94T (5) 近年来,许多厂家采用了一种新型的钙系脱氧剂,其主要成分为碳化
鞍钢冶金固体废弃物的应用技术与实践
鞍钢冶金固体废弃物的应用技术与实践 戴龙 经过高炉、转炉生产而产生的各种含铁物料种类繁杂,含铁品位高低不一,并时常含有一些特殊元素,如何应用好这些物料备受关注。 鞍钢经过多年的研究与实践,使用各种粉状含铁物料生产出一种叫还原球的产品,在高炉、转炉等工序使用,具有成本低、应用广、经济性好等特点,是各种粉状含铁物料应用的有效途径。 在高炉渣回收处理方面,鞍钢引进国内第一条德国立式磨矿渣粉生产线,对粒化高炉矿渣进行深加工,年可生产60万吨矿渣粉和45万吨矿渣硅酸盐水泥。在转炉钢渣处理加工方面,鞍钢采用熔融钢渣热焖技术、宽带高效新型带磁技术、磁选产品深加工提纯技术等全套工艺技术,对转炉钢渣进行充分有效的处理与利用。此外,鞍钢还率先研发了用精炼炉渣制球替代转炉助熔剂的技术,节约了炼钢成本,做到利废增效,实现了循环经济。同时,鞍钢将脱硫渣磁选后得到的脱硫渣钢和成球后变成高密度球体的脱硫磁选粉直接用于电炉炼钢,用以调节冶炼温度,充分利用钢渣中的废钢资源,降低了炼钢成本,使脱硫渣得到了有效利用。 高效利用靠先进的技术支撑 高炉渣的回收与处理技术。2002年,鞍钢从德国蒂森克虏伯伯利休斯公司引进了国内第一条德国立式磨矿渣粉生产线,用来处理高炉渣。鞍钢先将高炉渣经过水淬处理后得到粒化高炉矿渣,随后粒化高炉矿渣经该生产线磨细,生产出的矿渣粉可代替熟料生产水泥。该矿渣粉掺到高标号混凝土中,可改善混凝土各项性能;将该矿渣粉和熟料按一定比例混合,可生产出各种标号矿渣硅酸盐水泥,能够有效降低水泥的生产成本。而且,粒化高炉矿渣中含铁约0.3%,鞍钢采用外循环双磁道提铁法,充分回收了金属铁,提高了矿渣粉的品质与产量,提取后的铁珠含铁品位大于90%,将其压制成球后作为废钢用于转炉炼钢,可创造巨大的经济效益。 2012年,鞍钢从德国蒂森克虏伯伯利休斯公司引进的4条立式磨矿渣粉生产线建成投产。目前,鞍钢共有6条矿渣粉生产线,总产能为420万吨/年,成为东北地区矿渣粉生产的龙头企业。 转炉钢渣焖渣工艺技术。鞍钢本部采用简易焖渣法对熔融钢渣进行露天打水、热焖、陈化后进行磁选加工。鞍钢鲅鱼圈分公司采用熔融钢渣热焖工艺,从物理、化学两方面对钢渣的性质进行改变,消除了钢渣的膨胀性,这是对传统钢渣热焖方式的一次革命性转变。熔融钢渣热焖工艺与传统钢渣热焖工艺相比,其焖渣周期大幅缩短,符合现代化钢厂短流程的需要;粉化率更高,渣铁分离更彻底,便于从钢渣中提取钢铁物料,是钢尾渣实现高附加值应用的前提;实现了用最少的时间、最低的成本对钢渣进行效果最好的前处理,为钢渣的100%高附加值应用创造了有利条件。 在鞍钢鲅鱼圈分公司熔融钢渣热焖生产过程中,该公司经过不断实践、改造和创新,成功解决了焖渣爆炸、熔渣搅拌不均匀、渣池衬板易损坏、循环水利用、
二次精炼渣钢反应及成渣热对钢液温度的影响
二次精炼渣钢反应及成渣热对钢液温度的影响李晶傅杰王平黄成钢李铮易继松 摘要通过现场实验,分阶段定量分析了出钢至出VD过程,渣钢反应热及成渣热对钢液温度的影响。结果表明,这两种热对钢液温降的影响极小,完全可以忽略。 关键词LF VD 渣钢反应热成渣热 Effect of Slag-Steel Reacting Heat and Slag Forming Heat on Liquid Steel Temperature during Secondary Refining Li Jing, Fu Jie and Wang Ping (University of Science and Technology, Beijing 100083) Huang Chenggang, Li Zhen and Yi Jisong (Daye Special Steel Corp Ltd) Abstract Based on the experiment in practice, the slag-steel reacting heat and slag forming heat have been analyzed quantitatively at different stag from tapping to end of VD process. The results showed that the slag-steel reacting heat and slag forming heat could be ignored, of which the effect on liquid steel temperature decrease wasn't appreciable. Material Index Ladle Furnace, Vacuum Degassing, Slag-Steel Reaction Heat, Slag Forming Heat 钢液温度是保证工艺顺行及钢材质量的重要因素。尤其二次精炼的发展以及它在炼钢生产中的作用日益显著,钢液温度的控制越显其重要性。影响钢液温度的因素较多[1],但一般研究认为渣钢反应热及成渣热对钢液温度的影响较小而忽略。本文通过现场实验,分析了出钢至出VD 整个过程渣钢反应热及成渣热对钢液温度的影响,以定量了解渣钢反应热及成渣热对钢液温度的影响程度。 1 电炉钢生产工艺流程 目前电炉配LF/VD的生产工艺如下: 电炉出钢→钢包吹氩→入LF→送电加热→测温取样→钢液成分微调→加热升温→钢包停氩开出LF→入VD真空处理→真空结束→钢包吊至连铸台 2 现场实验及渣中氧化物、钢中元素的变化 进行了10多炉生产实验,各炉次不同阶段渣中氧化物及钢中元素含量的变化基本相同。如炉次7D2631,渣中各组份的变化(见图1),钢中
精炼渣各成分配比及所起作用
精炼渣各成分配比及所起作用 2012-05-02 15:55 来源:我的钢铁网 分享到: 合成渣精炼脱硫技术是生产超低硫纯净钢的关键技术之一,国内外不少学者对精炼渣的性能做了大量研究,通过试验得出了多种不同配比的精炼渣,见精炼渣成分配比表: 精炼渣成分配比 CaO-SiO2-Al2O3-MgO-CaF2-Na2O56.1:15.5:15.4:8.8:2:2.2 CaO-SiO2-Al2O3-MgO-CaF2 53:17:10:10:10 59:15:8.5:10:7.5 54.2:12.3:22:87:28 50.41:0.59:30:10:9 CaO-SiO2-Al2O3-MgO53:4:35:8 CaO-SiO2-Al2O3-CaF232.5:5:57.5:5 CaO-MgO-Al2O3-SiO250:15:20:15 CaO-SiO2-Al2O365:10:25 其相同之处在于基础渣一般多选CaO-SiO2-Al2O3系三元相图的低熔点位置的渣系。基础渣系最重要的作用是控制渣的碱度,这对精炼过程的脱硫效果有较大影响。 精炼渣的不同之处在于对基础渣系的微调,根据不同成分所起的作用不同控制加入添加剂的种类及含量,以期达到预期效果。精炼渣各种成分的作用如下表:
成分作用 CaF2降低渣的熔点,改善渣的 CaO调节渣碱度,脱硫剂 SiO2调节渣碱度和粘度 Al2O3调整CaO-SiO2-Al2O3三元系渣处于低熔点位置 CaCO3脱硫剂、发泡剂 MgCO3(MgO)发泡剂,分解后产生氧化镁对包衬起保护作用 BaCO3(BaO)发泡剂、脱硫剂,并可抑制钢液回磷 Na2CO3(Na2O)发泡剂、脱硫剂、助熔剂 K2CO3(K2O)发泡剂、脱硫剂、助熔剂 Li2CO3(Li2O)发泡剂、脱硫剂、助熔剂 Al 强脱氧剂,且优先与CaO脱硫发生氧反应,提 高脱硫效果 Si-Fe 脱氧剂,净化钢液 为了提升连铸坯质量,降低降价坯比例,炼钢车间在冶炼过程中成分按中限控制,强调钢包底吹的作用,保证软吹时间,均匀了成分和温度;终点控制上采用高拉碳法,不仅能降低合金、增碳剂、钢铁料等消耗,而且减少了由于增碳剂的加入带来的杂质。连铸车间开机前对准备工作进行确认,尤其是中间包及水口的烘烤情况,保证中间包、水口的干燥,减少气泡夹杂的产生;对二冷区的喷嘴及水条进行检查清理,减少冷却不均造成的脱方、裂纹等缺陷,及时清理铸坯辊道冷钢、残钢,保证辊道的光滑,减少划痕等缺陷;在浇注过程中,他们稳定控制中间包液面,避免液面波动,减少卷渣造成的连铸坯夹渣缺陷。同时为改善连铸坯质量,减少温降,该厂改进了原大包包盖,实施浇注全程盖包盖,减少钢水的二次氧化,
金属材料开题报告
金属材料开题报告 金属材料开题报告范文金属材料和社会、经济以及各种科学活动有着重大的影响和强大的动力,人类社会发展到今天,和金属材料的获得和研发都密不可分.随着现代社会的飞速发展,各种工业发展已经得到了强有力的推进,然而金属的替代品也在不断研发出,金属材料当前的发展现状和未来的前景需要有明确的认识.本文针对此进行精了简要的叙述和分析. 一、前言 社会的发展需要能源、信息和材料供应.而材料供应根据其特殊的材料可以分为金属材料、非金属材料等,金属材料是人类历史发展到现在为止最重要的材料.从古代打铁工艺、金子、银子等的制作和推广,金属材料都占据着人们的生活.金属材料根据其特点具有韧度高、硬度强度大等特点,而且金属材料容易获得,且不少金属制作简易.随着现代金属工艺的发展和推广、科学技术的发展壮大,金属材料在机械制作、国防领域、工业、农业、电子信息等行业,都有明显的性价比优势和广阔的发展前景市场. 二、金属材料当前发展现状 (一)钢铁材料发展现状 钢铁是整个国民紧急发展的基础,各种大楼的兴建、各
种器材的使用、汽车等工业的发展都离不开钢铁工业的发展.随着整个国民经济的发展和科技的进步,不锈钢工艺的不断提升,钢铁工业的发展,应当以不锈钢工艺为主要的发展方向,不锈钢是在常温或者其他特殊条件下,利用钢铁内部的特点能够生成钢材不生锈的情况,但当前不锈钢的发展工艺依然成本过高,可以推测不久的常来,不锈钢的工艺能取得更快的发展. 此外,钢铁材料的发展也带动着新需求和新技术的不断出现,特别是在航空航天、能源工业等都出现更多的需求.这些需求带动着更多新技术、新工艺的产生和发展.例如:当前较为流行的钢铁工艺为超纯净钢生产工艺.随着钢铁工艺技术的发展和生产设备的更新和发展.钢铁材料也从大体积生产逐渐转化成为小钢铁、微钢铁工艺的生产和开发. 为了实现上述的钢铁材料的需求,钢铁材料工艺可以预见将会采用更多新兴工艺方式来发展,例如:铁水预处理、全自动转炉吹炼、二次精炼、保护浇注和无缺陷连铸等重大新工艺技术等.总而言之,高性能、高精度连轧工艺技术轧钢工艺的发展就是围绕着整个“三高”的技术发展. 1.高性能:通过采用控轧控冷工艺,控制钢材的组织结构,提高钢材的性能,特别是强度、韧性指标; 2.高精度:除了精确控制轧材的尺寸精度外,进一步减小长型材的椭圆度和提高板材的板形控制精度及表面质量; 3.高效率:包括进
炉外精炼复习题答案完整版
1 概述 1 名词解释:长流程短流程炉外精炼 长流程:以氧气转炉炼钢工艺为中心的钢铁联合企业生产流程 短流程:以电炉炼钢工艺为中心的小钢厂生产流程 炉外精炼:凡是在熔炼炉(如转炉、电炉)以外进行的,旨在进一步扩大品种提高钢的质量、降低钢的成本所采用的冶金过程统称为炉外精炼。 2 转炉炼钢和电弧炉炼钢的不足之处有哪些?(07级A) 电炉炼钢的不足 (1)还原渣有较强的脱硫能力,但炉内渣钢接触面积太小,脱硫能力不能充分利用。氧化期出钢[S]0.02%~0.04% (2)在氧化期H降低到2.5~3ppm,在还原期又回升至5~7ppm (3)在还原期O≤80ppm,终脱氧后O≤30ppm,出钢过程100~200ppm (4)不能充分发挥超高功率电弧炉的作用 转炉炼钢的不足 (1)温度成分不均匀 (2)一般出钢[C]≥0.04%,很难将[C]控制在≤0.02%下出钢 (3)一般出钢[O]≥500ppm,出钢合金化后[O]≥100ppm (4)脱硫率为30%左右; 若铁水[S]≤0.03%,出钢[S]≤0.02%; 若铁水[S]0.002-0.005%,出钢[S]0.004-0.007% (5)脱磷率≥90%,终点[P]0.005-0.015%,出钢过程中回磷 (6)氧化性渣FeO≥15% 3 炉外精炼的作用和地位?经济合理性有哪些? 作用和地位: 1 提高质量扩大品种的主要手段 2 优化冶金生产流程,提高生产效率节能降耗降低成本主要方法 3 炼钢-炉外精炼-连铸-热装轧制工序衔接 炉外精炼的经济合理性 1 提高初炼炉的生产率 2 缩短生产周期 3 降低产品成本 4 产品质量提高 炉外精炼的任务?炉外精炼的三个特点? 对精炼手段的有哪些要求?(07级A 炉外精炼的任务 1 钢水成分和温度的均匀化 2 精确控制钢水成分和温度 3 脱氧脱硫脱磷脱碳 4 去除钢中气体(氢氮)及夹杂物 5 夹杂物形态控制 炉外精炼的三个特点 1 二次精炼 2 创造较好的冶金反应的动力学条件 3 二次精炼的容器具有浇注的功能
武钢博物馆实习报告doc
武钢博物馆实习报告 篇一:武钢实习报告 机械工程及自动化专业认识实习报告 武汉科技大学机械自动化学院(XX年9月)实习学生:XX级机工1106班姓名文维学号XX03130230 一、实习目的 1.初步了解钢铁联合企业主要生产流程及主要设备所在位置与用途 2.通过在实习厂主要岗位的现场参观、现场学习和讨论,提高分析问题和解决问题的能力,培养科学的思维方法和加强理论联系实际的能力。 3.在学习工程技术人员和工人师傅在长期实践中积累的丰富知识和经验的同时,学习他们勤奋工作的精神和实事求是的作风,增强热爱专业,热爱劳动的思想。 4.了解自己专业方面的知识和专业以外的知识,让我们早认识到我们将面临的工作问题,让我明白了以后读大学是要很认真的读,要有好的专业知识,才能为好的实际动手能力打下坚实的基础。 5.通过认识实习认识钢铁生产企业的概貌,了解钢铁企业的主要生产工艺,增加对安全工程专业学科的感性认识,了解安全工程专业在国民经济建设中的地位、作用和发展趋势,熟悉安全工程技术人员的工作职责和工作程序,了解企
业安全管理的现状和模式。 二、实习内容 武钢简介:武钢1955年始建,1958年9月13日建成投产。拥有从矿山采掘、炼焦(产能吨)、炼铁(产能吨)、炼钢(产能吨)、轧钢及配套公辅设施等一整套先进的钢铁生产 工艺设备,是我国重要的优质板材生产基地。 武钢现已成为生产规模近4000万吨的大型企业集团,居世界钢铁行业第四位,XX年,武钢跻身世界500强行列。现有钢铁制造业、高新技术产业和国际贸易三大主业。产品主要有热轧卷板、热轧型钢、热轧重轨、中厚板、冷轧卷板、镀锌板、镀锡板、冷轧取向和无取向硅钢片、彩涂钢板、高速线材等几百个品种。 (一).炼铁厂实习报告 实习时间XX年09月16日实习地点武钢炼铁厂指导老师:王涛 1.武钢股份公司炼铁总厂简介武钢股份公司炼铁总厂于XX年6月成立,包括烧结分厂、炼铁分厂,是武钢生产烧结矿和制钢生铁、铸造生铁的首道工序厂,具有精良的生产装备和先进的技术优势,主要经济技术指标在国内外同行业中处于领先地位。 武钢炼铁主要原料包括烧结矿、球团矿、块矿(海南矿、