铸造用的硅砂及质量控制
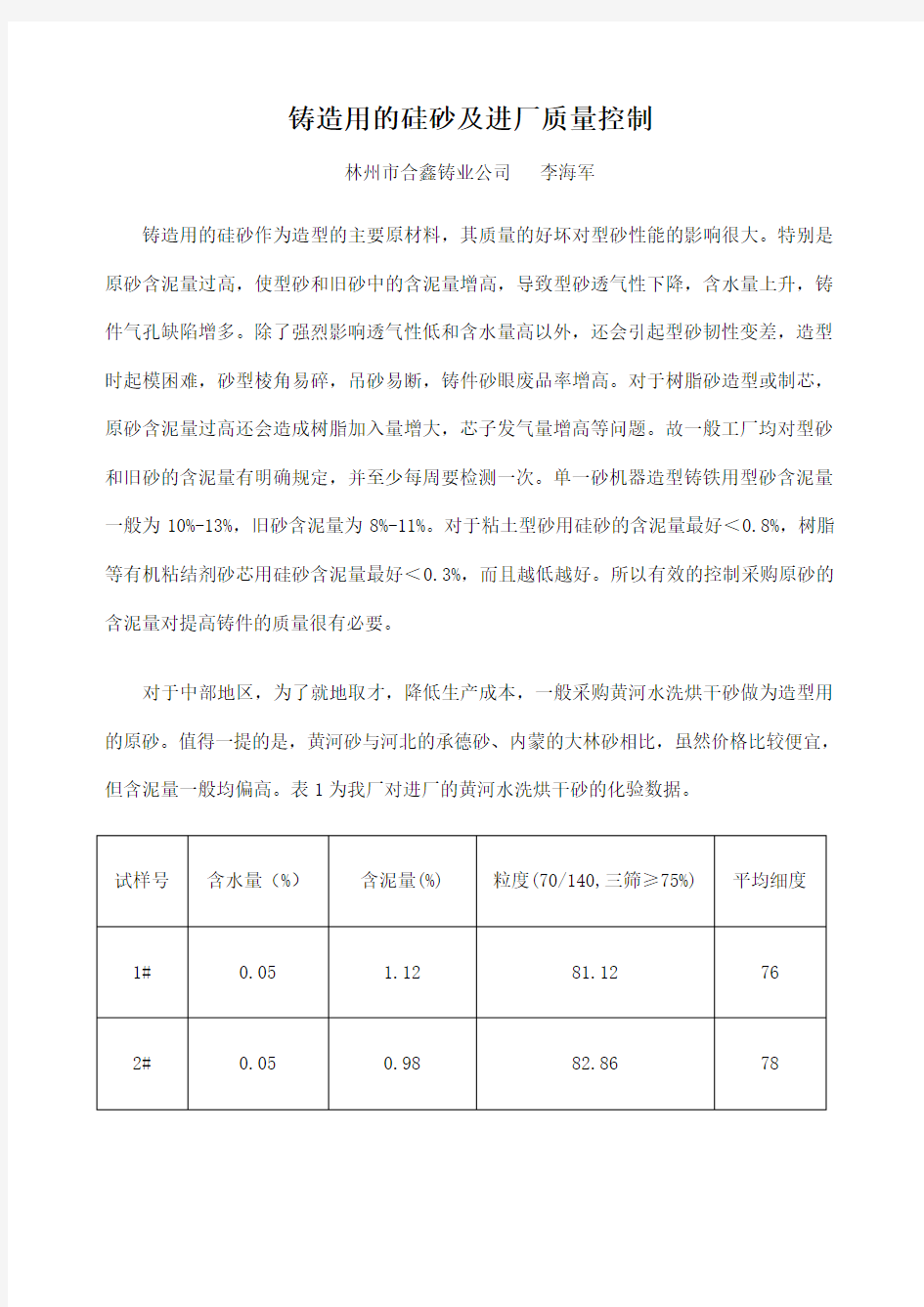

铸造用的硅砂及进厂质量控制
林州市合鑫铸业公司李海军
铸造用的硅砂作为造型的主要原材料,其质量的好坏对型砂性能的影响很大。特别是原砂含泥量过高,使型砂和旧砂中的含泥量增高,导致型砂透气性下降,含水量上升,铸件气孔缺陷增多。除了强烈影响透气性低和含水量高以外,还会引起型砂韧性变差,造型时起模困难,砂型棱角易碎,吊砂易断,铸件砂眼废品率增高。对于树脂砂造型或制芯,原砂含泥量过高还会造成树脂加入量增大,芯子发气量增高等问题。故一般工厂均对型砂和旧砂的含泥量有明确规定,并至少每周要检测一次。单一砂机器造型铸铁用型砂含泥量一般为10%-13%,旧砂含泥量为8%-11%。对于粘土型砂用硅砂的含泥量最好<0.8%,树脂等有机粘结剂砂芯用硅砂含泥量最好<0.3%,而且越低越好。所以有效的控制采购原砂的含泥量对提高铸件的质量很有必要。
对于中部地区,为了就地取才,降低生产成本,一般采购黄河水洗烘干砂做为造型用的原砂。值得一提的是,黄河砂与河北的承德砂、内蒙的大林砂相比,虽然价格比较便宜,但含泥量一般均偏高。表1为我厂对进厂的黄河水洗烘干砂的化验数据。
通过上表可以看出,经过烘干的砂,含水量一般都能满足标准≤0.3%的要求,但含泥量均偏高,70/140目的粒度波动也较大。我们厂曾较长时间的用过河北的承德砂,其含泥量均低于0.6%,而且质量较稳定。
对于手工造型和一般机器造型的工厂来说,为了有效的降低生产成本,可以使用黄河砂做为造型用的原砂,但要尽量控制其含泥量不要超过1%,否则对型砂性能影响较大。对于树脂砂造型、制芯或生产覆膜砂用的原砂,其含泥量最好低于0.6%或更低。
为了对原砂的进厂质量进行控制,工厂要逐步建立型砂化验室。不但对原砂,也能对型砂和旧砂的含泥量、粒度进行检测,从而保证型砂良好的性能,逐渐提高铸件的成品率。
以下为我厂的原砂进厂检验方法及标准,供大家参考。
原砂进厂检验作业指导书
1.目的
为规范铸造用原砂进厂检验及质量考核而制定。
2.适用范围
本指导书适用于铸造车间机器造型、手工造型及树脂砂制芯用原砂进厂检验及质量考核。
3.引用标准
《铸造用硅砂》 GB/T 9442-1998
《铸造用原砂及混合料试验方法》 GB/T 2684-81
4.取样方法
4.1 散装原砂样品从汽车或砂堆中离边缘和表面200-300毫米的各个角及中心部位,
用取样器选取;袋装原砂样品由同一批量的百分之一的袋中选取,但不得少于三袋,其总重量不得少于5公斤。如果根据外观观察,发现对某一部分原砂的质量有疑问时,应单独取样和检验。
4.2 选取样品必须在样品袋上注明名称、产地及取样日期。
4.3 检验所需的试样,由样品中选取。试样的数量可根据检验项目而定。
4.4 选取试样的方法采用“四分法”或分样器。“四分法”为将取得样品堆积,并拍成
圆饼,按十字线分成四等分。选取其中对角的两份。然后重新堆积,再按上述方法缩减,
直至达到所需样品为止。
5.试验方法
5.1含水量的测定
试验时,称试样20±0.01克,均匀铺在盛砂盘中,置入红外线烘干器内,烘干10min 后,取出盛砂盘冷却至室温,然后称量。含水量计算式如下:
x = ×100%
式中:x-试样含水量 [%];
m
-烘干前试样重量[g];
1
-烘干后试样重量[g]。
m
2
5.2含泥量的测定
①称烘干(在红外线烘干器内烘(20分钟)至恒重)试样50±0.01g(如果不需要
进行粒度分析时可称取试样20±0.01g),放入容量为600毫升的专用洗砂杯中,加入390ml蒸馏水和10mL浓度为5%的焦磷酸钠溶液。
②将洗砂杯放在垫有石棉垫的盘式电热炉上,煮沸5min(从试样完全沸腾开始记
时)。在煮沸过程中可用玻璃棒对试样进行搅动,以防烧杯中液体澎溅或烧杯嘣跳,必要时可迅速切断电源。
③待烧杯中液体冷却后,加入清洁自来水至标准高度125mm处,用玻璃棒搅拌约30s后,静置10分钟,用虹吸管吸出水面下100mm以上的混水。以上操作共重复两次。注意:搅拌时应不断改变旋转方向,以免砂粒沉淀时堆积成锥形。并尽量使沉淀后的砂层平坦无凸起处。静置后用虹吸管吸水时,应使虹吸管的入口端沿烧杯内壁逐渐下降,不可一落到底,以免水流过猛而吸出砂粒。
④从第三次起以后的操作均与前相同,但每次静置时间改为5min。要反复进行多次,直到杯中水透明为止。
⑤排掉清水后,倒入盛砂盘中在红外线烘干器中烘干(30分钟)至恒重(所谓恒重指:烘30分钟后,称其重量,然后每烘15分钟,称量一次,直到相邻两次称量之间的差数不超过0.02克为至),冷却至室温时称量。并按下式计算含泥量:
x = × 100%
式中:x-试料含泥量[%];
m
-水洗前试料重量[g];
1
-水洗后试料重量[g]。
m
2
5.3 粒度的测定
①试样采用试验测定过含泥量的烘干试样。如果采用未经测定含泥量的试样时,试样称重50±0.1克。
②首先将电磁微震式筛砂机的定时器设置为12分钟,旋动震幅旋扭,使振幅指示器指在3mm处。将试料放在全套标准筛最上面的6目筛上,再将装有试样的全套筛子紧固在筛砂机上,打开电源按扭,开始筛分,直到筛砂机自动停止。
③松动紧固手柄,取下标准筛,依次将每一个筛子以及底盘上所遗留的砂子分别倒在光滑的纸上,并用软毛刷仔细地从筛网的反面刷下夹在网孔中的砂子。会有一些砂粒夹在网孔中间不被刷下,可以任其停留。切不可用尖锥捅下,或用力敲击筛子,以免筛网变形。
④称量每个筛子上的砂粒重量。计算出每筛上砂子占试样总重量(50g)的百分率。
⑤试验后,将每个筛子及底盘上的砂子重量及含泥量(克)相加,其重量不应超出50±1g,否则试验应重新进行。
⑥根据第6条原砂粒度标准要求,把三筛所占试样的百分数相加即为主要粒度组成三筛所占试样的百分比。
平均细度的计算方法:将上面计算出的每筛上砂子占试样的百分率乘以下表所列的相应的细度因数,然后将各乘积相加,用乘积总和除以各筛号停留砂粒质量百分数的总和,四舍五入取整后即为平均细度。
6.原砂质量标准
进厂原砂的质量指标要符合下表的规定:
质量指标中含水量、含泥量、粒度为必检项目。
7.质量考核(略)
说明:在原砂的含泥量检验时,为了使砂粒上的粘土膜完全分散,按照GB/T2684-1981规定先煮沸3-5min,冷却后再在涡洗式洗砂机上搅拌15min。根据清华大学于振宗教授的资料,搅拌作用有利于打散絮状物,但也有可能将砂粒打碎。如将煮沸时间保持为5min就可使泥分完全分散,不再需要洗砂机搅拌。洗砂烧杯的加热应当在垫有石棉垫和装有调压器的盘式电热炉上,沸腾时应及时降低电压避免澎溅。我们厂目前就采用了此方法来化验原砂的含泥量。
表2为原砂进厂检验报告格式
原砂进厂检验报告表2
检验日
检验员(签字):检验结果:合格
2009.9.18
期:
国家标准
【国家标准】 1、GB-50017-2003、《钢结构设计规范》 2、GB50018-2002、《冷弯薄壁型钢结构技术规范》 3、GB-50205-2001、《钢结构结构施工质量验收规范》 4、GB50191-93、《构筑物抗震设计规范》 5、GB59135-200 6、《高耸结构设计规范》 6、GB500046-2008、《工业建筑防腐蚀设计规范》 7、GB8923-88、《涂装前钢材表面锈蚀等级和涂装等级》 8、GB14907-2002、《钢结构防火涂料通用技术条件》 9、GB-50009-2001(2006)、《建筑结构荷载规范》 10、GBT-50105-2001、《建筑结构制图标准》 11、GB-50045-95、《高层民用建筑设计防火规范》(2001年修订版) 12、GB-50187-93、《工业企业总平面设计规范》 【行业标准】 1、JGJ138-2001/J130-2001、型钢混凝土组合结构技术规程 2、JGJ7-1991、网架结构设计与施工规程 3、JGJ61-2003/J258-2003、网壳结构技术规程
4、JGJ99-1998、高层民用建筑钢结构技术规程(正修订) 5、JGJ82-91、钢结构高强度螺栓连接的设计、施工及验收规程 6、JGJ81-2002/J218-2002、建筑钢结构焊接技术规程 7、DL/T5085-1999、钢-混凝土组合结构设计规程 8、JCJ01-89、钢管混凝土结构设计与施工规程 9、YB9238-92、钢-混凝土组合楼盖结构设计与施工规程 10、YB9082-1997、钢骨混凝土结构技术规程 11、YBJ216-88、压型金属钢板设计施工规程(正修订) 12、YB/T9256-96、钢结构、管道涂装技术规程 13、YB9081-97、冶金建筑抗震设计规范 14、CECS102:2002、门式刚架轻型房屋钢结构技术规程 15、CECS77:96、钢结构加固技术规范 16、YB9257-96、钢结构检测评定及加固技术规范 17、CECS28:90、钢管混凝土结构设计与施工规程 18、YB9254-1995、钢结构制作安装施工规程 19、CECS159:2004、矩形钢管混凝土结构技术规程 20、CECS24:90、钢结构防火涂料应用技术规范 21、CECS158:2004、索膜结构技术规程
铸造常用原辅材料技术标准
铸造常用原辅材料技术条件 1. 范围 本标准规定了铸造生产中常用材料的技术条件。 本标准适用于铸造生产中常用材料的验收检验。 2. 规范性引用文件 下列文件中的条款通过本标准的引用而成为本标准的条款。凡是注日期的引用文件,其随后所有的修改单(不包括勘误的内容)或修订版均不适用于本标准,然而,鼓励根据本标准达成协议的各方研究是否可使用这些文件的最新版本。凡是不注日期的引用文件,其最新版本适用于本标准。 GB/T 467-1997 阴极铜 GB/T 718-2005 铸造用生铁 GB/T 1412-2005 球墨铸铁用生铁 GB/T 2272-1987 硅铁 GB 3518-83 无定形石墨粉 GB/T 3649-1987 钼铁 GB/T 3795-2006 锰铁 GB/T 4137-2004 稀土硅铁合金 GB/T 5235-1985 加工镍及镍合金化学成分和产品形状 GB/T 5683-2008 铬铁 GB 8736-88 铜中间合金锭 GB/T 9442-1998 铸造用硅砂 JB/T 9228-1999 球墨铸铁用球化剂 JB/T 7526-2008 铸造用自硬呋喃树脂 JB/T 8835-1999 铸造用水玻璃 YB/T 5051-1997 硅钙合金 GB/T 2988-87 高铝砖 GB/T 2992-1998 通用耐火砖形状尺寸 GB/T 2994-1994 高铝质耐火泥浆
GB/T 14982-1994 粘土质耐火泥浆 3. 基本要求 3.1金属材料不得有显著的锈层、粘砂、土、油、漆等有害附着物和其它夹杂物。(本厂废铸件可允许有防锈漆)。 3.2 本标准所指块度尺寸均为对角线长度,不能与进货块度要求混淆。 3.3 所有进厂的原材料都应有随货提供质保书或合格证明。 4. 造型材料 4.1 原砂 4.1.1 铸造用硅砂(参照GB/T9442-1998)(见表1) 表1 铸造用硅砂 4.1.2 硅砂要求 4.1.2.1 硅砂中不得混入煤屑、小石块、碎木片、石灰石等杂物。 4.1.2.2 散装硅砂投入生产前,必须过筛,以清除杂物。 4.2 树脂 4.2.1 树脂检验以游离甲醛和糠醇,以及使用生产现场型砂按1%树脂加入量混制的型砂试块经24小时固化后检测其抗拉强度不小于0.6MPa为验收依据。对现场抗拉强度未能达到验收要求的供方树脂,允许供方加入0.2-0.3%的硅烷进行调整,但供应商应随货提供用于调整树脂强度的对应比例硅烷重量。 4.2.2 铸钢件生产用树脂含氮量作为验收依据,铸铁件不作验收依据;其它外观和水分仅作参考。 4.2.3 树脂应密封,存放于阴凉干燥处,不可靠近热源或曝晒,保存期限半年以上。
铸造质量控制
铸造质量控制 摘要:铸造是一个复杂的生产过程,环境、设备、工艺、人员、原辅材料等都可能引起铸造质量的波动,铸件质量也包含两方面的内容:一是铸件产品质量,二是铸造过程质量。铸造过程质量直接决定着产品质量,控制好铸造过程,必须从细节抓起,通过工艺文件、指控点建立、企业文化凝聚、设备保证等多方面一起建立一个稳定的铸造质量控制全过程。 关键词:铸造质量控制过程控制质量 一、铸造质量 铸件是铸造生产的产品,铸造质量的本质体现是各类铸件产品的质量。铸件质量也包含两方面的内容:一是铸件产品质量,二是铸造过程质量。铸件产品质量,即铸件满足用户要求的程度;或按其用途在使用中应取得的功效,这种功效是反映铸件结构特征、材质的工作特性和物理力学特性的总和,是评价铸件质量水平和技术水平的基本指标。铸造过程质量直接决定着产品质量,是指铸件产品的生产过程对产品质量的保证程度,即铸件在具体使用条件下的可靠性,这个指标在相当大的程度上决定于所取得的功效,还与稳定性、耐用性和工艺性等指标有关。 在现在的生产条件下,随着铸造技术的不断发展,虽然设备和技术的保证能力不断提高,但是中国的铸造过程仍存在许多不稳定的质量控制盲区,也只有从过程控制的细节入手,不断深入过程质量控制,保证工艺的有效实施才能从根本上提高改善铸造过程和铸件产品质量。 二、铸造质量控制要点: 1、工艺控制文件 1.1作业指导书 作业指导书是工序质量控制点必备的重要控制文件,是在工序卡片的基础上发展起来的一种新形式的工艺文件,它比工序卡片更加细化和完善,是正确指导现场生产工人操作、控制和检查的规程。但是作业指导书必须防止“两张皮”和不协调现象。作业指导书是指导现场操作的基础,必须保证能通过作业指导书能够准确的进行现场操作,一般情况下作业指导书的内容有如下四大部分组成:1)简介明了的工序示意图。(铸造一般现实工序件的照片为佳,例如组芯工序应该添加本工序组芯照片,然后标出哪些地方需要增加粘结剂,哪些地方需要补刷灰等,一定要形象具体。) 2)通俗易懂的操作要领和工艺规程(如最简单的取放芯子,应该标出手拿芯子那个部位最好不会引起损伤芯子,不易脱手,保证第一操作也不会出错)。 3)明确严格的控制要求:检验项目、检验频次、检具要求、控制手段等。 4)符合现场要求的工艺参数。 制定作业指导书要注意如下问题: 1)在操作要领、工艺规程中要将生产工人所积累的经验和加工技巧总结进去,以利于指导工人正确进行操作。 2)注意与工序质量分析表相呼应。 3)作业指导书所要求的内容要做到完整、准确。 4)操作要领、工艺规程要规定得详细、具体,不应出现诸如“见某某文件”等现象。
铸造用锆砂、粉
行业标准《铸造用锆砂、粉》解读 1 标准概况 在铸造生产中,锆砂主要用于大型厚壁铸钢件、铸铁件的型(芯)砂,锆粉主要用于型砂铸造用涂料。目前,伴随我国铸造行业的快速发展,对铸件质量要求的提高,铸件尺度的增大,使用铸造用锆砂、粉的需求量有不断增大的趋势。新修订的标准有效解决了标龄老化问题,缩短铸造用锆砂、粉技术指标与国际先进水平的差距,有力推动我国造型材料的发展。 本标准是对JB/T 9223-1999《铸造用锆砂》的修订,由苏州兴业材料科技股份有限公司(原苏州市兴业铸造材料有限公司)负责起草,2012年10月由全国铸造标委会造型材料分技术委员会在苏州组织行业专家对送审稿进行审查,对标准送审稿作了进一步的修改、整理和完善,形成了标准报批稿。 2 新旧标准主要内容差异 2.1 名称 将JB/T 9223-1999《铸造用锆砂》改名为《铸造用锆砂、粉》,锆砂在铸造生产中作为原砂的应用量并不多,但在型砂铸造用涂料中却大量应用。因此,新标准中增加了锆粉的内容,不仅增加标准的适用性,扩大了标准的适用范围,而且对行业发展更具有现实的指导意义。 2.2 范围 本标准规定了铸造用锆砂、粉的术语和定义,分级、分组及牌号,技术要求,试验方法,检验规则以及包装、标志、运输、贮存和质量证明书。本标准适用于铸造生产造型(芯)用锆砂、粉。 2.3 规范性引用文件 新标准中引用了7项国家和行业标准,全部为非注日期引用,比旧标准增加了GB/T 4984《含锆耐火材料化学分析方法》、GB/T 5611《铸造术语》、GB/T 9442《铸造用硅砂》、GB 11743《土壤中放射性核素的γ能谱分析方法》及JB/T 9156《铸造用试验筛》等5个引用标准,比旧标准查询更方便。 2.4 术语和定义 旧标准中只规定峰值含量、酸耗值二个定义,新标准中增加了除GB/T 5611《铸造术语》中界定的术语和定义外,还有铸造用锆砂、粉,含水量,含泥量,原砂细度,细粉含量五个术语及定义;删除了峰值含量定义。 2.5 分级、分组及牌号 旧标准中将铸造用锆砂根据其二氧化锆(铪)含量分为w[(Zr·Hf)O2]≥66 %、w[(Zr·Hf)O2]≥65%、w[(Zr·Hf)O2]≥63 % 和w[(Zr·Hf)O2]≥60 %四级。考虑到目前铸造生产上大量使用澳洲、印尼等进口的锆砂其二氧化锆(铪)含量一般为w[(Zr·Hf)O 2 ]≥6 6 %和w [(Z r·H f)O2]≥6 5 %,含量为w[(Zr·Hf)O2]≥63 %,也很少,含量为w[(Zr·Hf)O2]≥60 %及国内低质、量少的锆砂几乎已无使用。为规范市场,新标准中删除了旧标准中二氧化锆(铪)含量为w[(Zr·Hf)O2]≥60% 等级。 目前所使用锆砂的其他含量SiO2、TiO2、Fe2O3、P2O5及含水量等均小于旧标准的要求,Al2O3成分对锆砂、粉品质的影响不大,因此,本次修订时将TiO2、Fe2O3、Al2O3、P2O5等指标进行调整,新、旧标准中铸造用锆砂、粉根据二氧化锆(铪)含量分级,各级的化学成分见表1。 旧标准中将铸造用锆砂根据其粒度组成分为特细砂、细砂、中细砂,其对应的目数特细砂为(140/270)、细砂为(100/200)、中细砂为(70/140)。新标准中铸造用锆砂、粉按粒度组成分组见表2
铸造原辅原材料检验规程.
山东遨游汽车制动系统股份有限公司标准 QB/AY001-2011 铸造原辅原材料验收规范 编制: 审核: 批准: 2011-03-10发布2011-03-10实施 1 山东遨游汽车制动系统股份有限公司
山东遨游汽车制动系统股份有限公司标准 QB/AY001-2011 铸造原辅材料验收规范 前言 本标准是企业根据现有工艺条件对铸造选用原辅原材料进行质量控制的企业检验标准。 本标准由山东遨游汽车制动系统股份有限公司于2011年3月制订,于2011年3月10日正式实施。 本标准起草单位:山东遨游汽车制动系统股份有限公司 技术中心、质量部、铸造制造部。 本标准起草人:吕广慈、李学联、韩建华、韩见波。 2 山东遨游汽车制动系统股份有限公司发布2011-03-10实施
山东遨游汽车制动系统股份有限公司标准 QB/AY001-2011 铸造原辅材料验收规范 目录 前言 一、主题内容及适用范围 二、引用标准 三、原材料管理原则 四、金属材料 五、非金属材料
山东遨游汽车制动系统股份有限公司发布2011-03-10实施 山东遨游汽车制动系统股份有限公司标准 QB/AY001-2011 铸造原辅材料验收规范 一、主题内容与适用范围 1.1.1本标准根据国家标准,结合本企业具体情况 制定所用原材料的技术条件及检验标准。 1.1.2本标准适用于企业型砂铸造铸造件生产。 二、引用标准 GB1348-88 《球墨铸铁件》 GB1412-85 《球墨铸铁用生铁》 GB9442-88 《铸造用硅砂》 ZBJ31009-90 《铸造用膨润土和粘土》 GB/T4138-93 《稀土镁硅铁合金》 GB2272 -87 《硅铁》 GB3795-87 《锰铁》 ZBJ31002-88 《湿型铸造用煤粉》
国内中频炉铸造标准
国内中频炉铸造标准 国内中频炉铸造行业准入条件目的在于根据国家有关法规和政策引导我国铸造行业健康、有序和可持续发展,提升我国装备制造业整体水平和为国民经济各行业提供优质铸件,实现我国从世界铸造大国向铸造强国转变。 实施铸造行业准入制度,按照“铸造行业准入条件”加快淘汰那些规模小且工艺落后、耗能大、污染严重、作业条件恶劣的铸造企业,遏制行业内的恶性竞争和资源浪费。在实施铸造行业准入制度过程中将积极引导企业通过兼并、重组,形成合理经营规模;在有条件的地区积极发展铸造产业集群或铸造工业园区,优化资源配置,大力发展清洁生产和循环经济;培育一批“专、特、精、新”的中小铸造企业,提高企业综合竞争力、铸件产品质量和企业效益。 铸造企业的布局及厂址的确定应符合国家产业政策和相应法规,符合各省、自治区、直辖市装备制造业发展规划。在一类区内不能新建、扩建铸造厂,已有的铸造厂其污染物排放(含水、气和噪声等)指标应符合国家一类区有关标准的规定。在二类区和三类区,新建铸造厂和原有铸造厂的污染物(含水、气和噪声等)排放指标均应符合国家或地区有关标准的规定。说明:一类区指国务院有关主管部门和省、自治区、直辖市人民政府划定的风景名胜区、自然保护区和水源地及其他需要特别保护的区域;二类区指城镇规划中确定的居住区、商业交通居民混合区、文化区、一般工业区和农村地区以及一、三类区不包括的地区;三类区指特定的工业区。鉴于目前我国东、中、西部地区社会、经济和工业发展程度的差异,锻造中频炉在进行铸造行业结构调整和实施准入制度时,应区别对待。 企业规模(产能) 1.现有的砂型铸铁件(含离心铸铁管及其他离心铸造)、铸钢件与有色铸件生产企业铸件年产能按所在地区(见表1)和类别(一、二、三类)不同应不低于表1所列的吨位。 2.采用砂型及离心铸造工艺之外的其他铸造工艺(包括压铸、低压铸造、金属型铸造、挤压铸造、熔模铸造、V法铸造、消失模铸造等)的铸造企业规模不在以上限制之列,具体标准待此后另行公布。 3.对于“专、特、精、新”的中小铸造企业,其企业规模的限制可以适当放宽。“专、特、精、新”的中小铸造企业认定标准和实施细则另行公布。 铸造方法及工艺: 1.根据生产铸件的材质、品种、批量,合理选择粘土湿型砂铸造、树脂自硬砂铸造、水玻璃自硬砂铸造、V法铸造、熔模铸造、消失模铸造、金属型铸造(重力、离心、压铸、低压等)等铸造工艺。 2.逐步淘汰粘土砂干型等落后铸造工艺。 铸造装备(造型、制芯、熔炼、砂处理、清理等)中频炉 1.必须配备与生产能力相匹配的熔炼设备,如电炉、冲天炉等金属熔炼设备,炉前化学成分分析、金属液温度测量设备,并应配有相应有效的除尘设备与系统。提倡大批量生产铸铁件产品的企业根据铸件要求采用冲天炉-电炉双联熔炼工艺,或采用中频感应炉熔炼,推荐采用大容量(熔化率≥10t/h)、长炉龄(一次开炉连续使用4周以上)、富氧、外热送风冲天炉。在全国范围内逐步淘汰熔化率<3t/h、环保排放不达标的冲天炉,新建铸造企业一律不再采用熔化率<5 t/h的冲天炉。 2.禁止新增容量1t以上无磁扼的铝壳电炉,原有无磁扼的感应电炉限2年内逐步淘汰。 3.必须配有与生产能力相匹配的造型、制芯、砂处理、清理设备,采用树脂砂、
铸造用的硅砂及质量控制
铸造用的硅砂及进厂质量控制 林州市合鑫铸业公司李海军 铸造用的硅砂作为造型的主要原材料,其质量的好坏对型砂性能的影响很大。特别是原 砂含泥量过高,使型砂和旧砂中的含泥量增高,导致型砂透气性下降,含水量上升,铸件气 孔缺陷增多。除了强烈影响透气性低和含水量高以外,还会引起型砂韧性变差,造型时起模 困难,砂型棱角易碎,吊砂易断,铸件砂眼废品率增高。对于树脂砂造型或制芯,原砂含泥 量过高还会造成树脂加入量增大,芯子发气量增高等问题。故一般工厂均对型砂和旧砂的含 泥量有明确规定,并至少每周要检测一次。单一砂机器造型铸铁用型砂含泥量一般为 10%-13%,旧砂含泥量为8%-11%。对于粘土型砂用硅砂的含泥量最好<0.8%,树脂等有机粘结剂砂芯用硅砂含泥量最好<0.3%,而且越低越好。所以有效的控制采购原砂的含泥量对提 高铸件的质量很有必要。 对于中部地区,为了就地取才,降低生产成本,一般采购黄河水洗烘干砂做为造型用的 原砂。值得一提的是,黄河砂与河北的承德砂、内蒙的大林砂相比,虽然价格比较便宜,但 含泥量一般均偏高。表1为我厂对进厂的黄河水洗烘干砂的化验数据。 表1 试样号含水量(%)含泥量(%) 粒度(70/140,三筛≥75%) 平均细度1# 0.05 1.12 81.12 76 2# 0.05 0.98 82.86 78 3# 0.05 1.0 79.04 73 4# 0.10 0.98 82.24 76 5# 0.15 1.16 73.78 66 6# 0.10 1.28 73.4 66 7# 0.05 1.30 74.82 71 通过上表可以看出,经过烘干的砂,含水量一般都能满足标准≤0.3%的要求,但含泥量均偏高,70/140目的粒度波动也较大。我们厂曾较长时间的用过河北的承德砂,其含泥量均低于0.6%,而且质量较稳定。 对于手工造型和一般机器造型的工厂来说,为了有效的降低生产成本,可以使用黄河砂 做为造型用的原砂,但要尽量控制其含泥量不要超过1%,否则对型砂性能影响较大。对于树脂砂造型、制芯或生产覆膜砂用的原砂,其含泥量最好低于0.6%或更低。
铸造品质如何控制
如何做好铸造质量 一.要有好的模具 1.模具预量(加放量)的合理控制 1.1生产的机器设备考虑(铸造机的精度要好) 1.2铸造方式考虑(重力、低压、压铸等) 1.3金属(铝合金)缩收考虑 1.4铸件的部位考虑(如浮渣面、一工程耳部) 1.5铸造后站作业考虑(切冒口夹变形,T6变形、加工定位、加工精度) 1.6脱模角度考虑(铝合金一般大于7°) 1.7模具设计的圆角考虑(消除内应力、主要为内尖角) 1.8经济性及结晶质量考虑(避免无谓增加余量) 1.9脱模时变形考虑 2.0黑皮的产生和防范 2.流路系统的设计 2.1流路系统的组成(a.滤槽b.浇道c.流道d.补水块e.铸口f.浇口) 2.2流路系统设计考虑因素 2.2.1收缩之处的补水(补水块) 2.2.2模具中的气体疏导 2.2.3防范杂质进入模具 2.2.4入水口处的咬模考虑 2.2.5敲除流路的变形考虑 2.2.6流体进入模穴的平稳、迅速、均匀性考虑 2.2.7透气之考虑 2.3流路系统的设计原理 2.3.1蛇形原理 2.3.2凹凸原理(沉淀、浮渣) 2.3.3由大到小及上大下小原理 2.3.4瓶颈原理 2.4多处入水(分枝流路)利弊 2.4.1有利因素:a.模温均匀b.缩短浇注时间c.减少入水口咬模d.强度好 e.适于冷凝度h.改善水痕 2.4.2不利因素:a.熔料(铝料)增加b.入水口质量不良因素增加c.冷却增加 d.模具制作费用增加 2.5浇道、流道、铸口的比例分配(铸喉与反铸喉设计) 3.冒口设计
3.1冒口的种类:有敞开式的冒口(现厂内叫冒口)及封闭式冒口(盲冒口)或顶 冒口及侧冒口(厂内设计的小流道) 3.2冒口的作用:补水功能(它属于铸模内馈补给系统) 3.3影响冒口效能的因素:冒口的大小、形状、位置、铸件的重量、尺寸、形 状、材料种类及其收缩性、浇注速度、流路系统的设计、冒口相接面的 绝热性与温度 3.4冒口设计的重点 3.4.1在铸件截面的最大处即最后凝固的位置 3.4.2冒口的直径为铸件截面厚度的1.5倍以上 3.4.3冒口的高度与直径相等为佳 3.4.4冒口设计的经济性(避免过大造成铝料浪费及铸造时间延长) 3.4.5冒口的凝固终了时间必须晚于铸件 3.4.6冒口的保温性考虑(除保温材料) 4.模具冷却盒及冷激件和冷凝件的设计 4.1入水口处的冷却盒(边模、上模冷却盒) 4.2冷激件和冷凝件适用于砂模 4.3冷却盒之大小(因模具的大小而定,同模具的尺寸成正比) 5.模具冷凝梯度的设计 5.1模具的厚度应结合铸件所需之冷凝梯度 5.2模具厚较不易散热亦不利铸件凝固(此点仅为经验只作参考) 5.3铝合金轮圈铸件冷凝梯度介绍 6.铸件的设计控制 6.1铸件设计追求完美:功能、强度、美观、铸造性、加工性、经济性 6.2铸件设计必须考虑因素 6.2.1金属收缩的考虑 A.金属于冷凝时及凝固后由高温至常温皆有收缩 B.收缩产生的铸疵a.黑皮、凹陷b.热裂c.缩孔d.变形e.漏气f.影响强度 C.凝固规律:由底温到高温、由外到内、由薄到厚 D.造成缩孔的原因:a.模温过低或不均b.熔料温度太低c.冒口的设计不合 理d.冷却或保温(含涂模)不当e.铸件肉厚梯度不合理f.流路系统设计不 合理等 6.2.2脱模角度考虑 A.铝合金脱模角度大于7°为佳设计时适当考虑加大 B.脱模角度不足之危害:a.容易拉裂b.严重变形c.影响产能d.容易咬伤 C.脱模角度对经济性的影响(须适度考虑) 6.2.3铸件肉厚的控制(同第1点) 7.变形量具的制作与使用 7.1量具测量点确立(直径四点定位或造型吻合)
一 、锻造过程质量控制
一、锻造过程质量控制 1,锻造 ◆什么叫做锻造: □在加压设备及工(模具)的作用下,使坯料产生局 部或全部的塑性变形,以获得一定的几何形状,形 状和质量的锻件的加工方法称为锻造. ◆锻造的分类: □自由锻造 只用简单的通用性工具,或在锻造设备上、下砧间直 接使坯料变形而获得所需的几何形状及内部质量的锻 件. 模锻 利用模具使毛坯变形而获得锻件的锻造方法. □自由锻造的方法 镦粗:使毛坯高度减小,横断面积增大的锻造工序. 局部镦粗:在坯料上某一部分进行的镦粗. 镦粗的过程控制: 1.为了防止镦粗时产生纵向弯曲,圆柱体坯料的高度与直径之比不应超过 2.5-3,且镦粗前坯料端面应平整,并与轴心线垂直. 镦粗时要把坯料围绕着轴心线不断转动坯料发生弯曲时必须立即矫正。 芯棒拔长: 它是在空心毛坯中加芯棒进行拔长以减小空心处径(壁厚)而增加其长度的锻造工序,用于锻造长筒类锻件. 芯棒拔长的过程控制: 1.芯棒拔长都应以六角形为主要变形阶段 即圆→六角→圆,芯棒拔长应尽可能在V 型下砧或110°下槽中进行. 2.翻转角度要准确,打击量在均匀,发现有壁 厚不均匀及两端面过度歪斜现象,应及时 把芯棒抽出,用矫正镦粗法矫正毛坯. 3.芯棒加工应有1/100~2/100日锥度. 拔长:使毛坯横断面积减小,长度增加的 锻造工序. 拔长锻造工艺参数的选择就是要在保证质量的前提下提高效率 1. 每次锤击的压下量应小于坯料塑性所允许的数值,并避免产生折叠,因此每次压缩后的锻件宽度与高度之比应小于2~ 2.5,b/h<2~2.5,否则翻转90°再锻造时容易产生弯曲和折叠。 2.每次送进量与单次压下量之比应大于1~1.5,即L/△h/2>1~1.5生产中一般采用L=(0.6~0.8) h (h为坯料高度)。如图
铸造质量控制
一、铸件质量控制 铸件质量决定于每一道工艺过程的质量。对铸件质量进行控制,实际上是全过 程质量控制(%&’),将过程处于严格控制之中,不出现系统误差(由异常原因造成的误 差)。过程中由随机原因产生的随机误差,其频率分布是有规律的。这种利用数理统 计方法将铸造过程中系统误差和随机误差区分开来是质量控制 的基本方法。这种方 法又称之为统计过程控制(()’)。 ·+$*# · 第一章铸件质量 铸件质量控制首先在于稳定生产过程,避免系统误差的出现和随机误差的积累。 其次要提高工艺过程精度,缩小误差频率分布范围或分散程度。过程控制包括技术准备过程、图样和验收条件的制订;铸造工艺、工装设计的验 证;原材料验收;设备检查;工装几何形状、尺寸精度和装配关系检查等;另外,还包括 熔炼、配砂、造型、制芯等工艺参数的控制。 控制方法是定期记录工艺参数进行统计分析,判断车间参数误差频率分布及性
质,对每一中间工序的结果进行检查。图! " # " $ 表示出铸铁车间的铸造工艺过程 质控站(%&)及整个控制程序。 图! " # " $ 铸铁件生产过程质控站(%&)布置 建立过程质量控制站(简称质控站)或管理站是质量管理中行之有效的措施。质 控站能为缺陷分析提供生产过程背景材料以及原始记录和统计资料,凡是对铸件质 量特性有重大影响的工序或环节,一般都应设置质控站。 质控站还应贯彻并使操作者严格执行操作规程。工厂考核铸件质量,按铸件产 生缺陷的原因,追究个人或生产小组的责任。由于铸件产生缺陷的原因是多方面的 和复杂的,有些缺陷是由多个因素引起的,故不容易划分各自应承担责任的百分比。 为了解决由于划分不公引起争端,应该加强中间检查,应对每一道工序的质量(特别 是主要工艺参数和执行操作规程的情况)进行严格的控制,从而确定个人或小组的质 ·’)(’ · 第九篇铸造生产质量检验与铸件缺陷分析处理 量责任。例如质控站按规程抽查型砂的性能,如果不符合标准的
铸造相关标准
1 铸造通用基础及工艺标准规范汇编 1.1 GBT 5611-1998 铸造术语 1.1.1 基本术语1.1.2 砂型铸造1.1.3 特种铸造1.1.4 造型材料1.1.5 铸件后处理1.1.6 铸件质量1.1.7 铸造工艺设计及工艺装备1.1.8 铸造合金及熔炼、浇注 1.2 GBT 5678-1985铸造合金光谱分析取样方法 1.3 GBT 60601-1997 表面粗糙度比较样块铸造表面 1.4 GBT 6414-1999 铸件尺寸公差与机械加工余量 1.5 GBT1 1351-1989 铸件重量公差 1.6 GBT 15056-1994 铸造表面粗糙度评定方法 1.7 JBT 2435-1978 铸造工艺符号及表示方法 1.8 JBT 40221-1999 合金铸造性能测定方法 1.9 JBT 40222-1999 合金铸造性能测定方法 1.10 JBT 5105-1991 铸件模样起模斜度 1.11 JBT5106-1991 铸件模样型芯头基本尺寸 1.12 JBT 6983-1993 铸件材料消耗工艺定额计算方法 1.13 JBT7528-1994 铸件质量评定方法 1.14 JBT 7699-1995 铸造用木制模样和芯盒技术条件 2 铸铁标准规范汇编 2.1 GBT 1348-1998 球墨铸铁件 2.2 GBT 3180-1982 中锰抗磨球墨铸铁件技术条件 2.3 GBT 5612-1985 铸铁牌号表示方法 2.4 GBT 5614-1985 铸铁件热处理状态的名称、定义和代号 2.5 GBT 6296-1986 灰铸铁冲击试验方法 2.6 GBT 7216-1987 灰铸铁金相 2.7 GBT 8263-1999 抗磨白口铸铁件 2.8 GBT 8491-1987 高硅耐蚀铸铁件 2.9 GBT 9437-1988 耐热铸铁件 2.10 GBT 9439-1988 灰铸铁件 2.11 GBT 9440-1988 可锻铸铁件 2.12 GBT 9441-1988 球墨铸铁金相检验 2.13 GBT 17445-1998 铸造磨球 2.14 JBT 2122-1977 铁素体可锻铸铁金相标准 2.15 JBT 3829-1999 蠕墨铸铁金相 2.16 JBT 4403-1999 蠕墨铸铁件 2.17 JBT 5000.4-1998 重型机械通用技术条件铸铁件 2.18 JBT 7945-1999 灰铸铁力学性能试验方法 2.19 JBT 9219-1999 球墨铸铁超声声速测定方法 2.20 JBT 9220.1-1999 铸造化铁炉酸性炉渣化学分析方法总则及—般规定 2.21 JBT 9220.2-1999 铸造化铁炉酸性炉渣化学分析方法高氯酸脱水重量法测定二氧化硅量 2.22 JBT 9220.3-1999 铸造化铁炉酸性炉渣化学分析方法重铬酸钾容量法测定氧化亚铁量 2.23 JBT 9220.4-1999 铸造化铁炉酸性炉渣化学分析方法亚砷酸钠—亚硝酸钠容量法测定—氧化锰量 2.24 JBT 9220.5-1999 铸造化铁炉酸性炉渣化学分析方法氟化钠—EDTA容量法测定三氧化二铝量 2.25 JBT 9220.6-1999 铸造化铁炉酸性炉渣化学分析方法 DDTC分离EGTA容量法测定氧化钙量 2.26 JBT 9220.7-1999 铸造化铁炉酸性炉渣化学分析方法高锰酸钾容量法测定氧化钙
铸造生产过程控制程序
铸造生产过程控制程序 1.目的 为使产品铸件的整个生产过程的质量、环境、职业健康安全处于受控状态。 2.适用范围 铸造车间所生产的本公司铸件的生产全过程。 3.职责 3.1车间主任负责各工序的生产管理,组织贯彻实施质量管理、环境管理、职业健康安全管理各控制程序,对铸件生产中的质量、环境、职业健康安全负责。 3.2车间计划调度员根据公司生产技术部下达的生产指令安排组织生产活动。3.3车间技术组负责编制工艺文件,并对工艺文件的正确性、完整性、适用性负责。 3.4车间安全员负责车间生产的环境管理和职业健康安全管理的日常工作。 3.5各班组长对本班组的产品质量、生产作业计划及进度、环境管理、职业健康安全管理的完成情况负责。 4.工作程序 4.1过程准备 4.1.1车间计划调度员按照生产技术部下发的项目计划编制各班组的生产计划,及时下发到各班组,完成调度指令兑现率,准备好各种工装器具及原材料。 4.1.2车间生产所需各种工装器具及原材料放在有明显标识的指定区域,由车间统一管理。 4.1.3车间技术组由专人负责管理图纸和技术资料,进行分类、标识、定址存放,建立文件资料目录及管理规定。
4.1.4技术组的技术人员根据当月车间生产计划准备技术资料、图纸,并保证这些资料正确、清晰、完整、有效。 4.1.5原料、辅料和工艺装备上场前有关人员应检验其是否符合规定要求,检验结果应记录并明确标识。 4.1.6车间设备员要做好设备的日常管理和检查,其结果应记录备案。 4.1.7操作者上岗前应经过培训,培训合格后持证上岗,特殊过程(熔炼、浇注、造型、焊接、热处理、机动车司机)必须经过专门培训,考试结果记录备案。 4.2过程控制 4.2.1图纸资料的控制 4.2.1.1车间技术组负责图纸、技术文件的收发、归档、管理和更改。 4.2.1.2车间技术组签收图纸、资料后,加盖本车间专用标记章,填写《收图登记》,分类放置。 4.2.1.3车间技术组收到改图通知后,按要求更改,保证零件图、工艺图、工装图的有效性,做出更改标识并通知到相关技术人员。车间技术组对车间图纸、资料的正确性、完整性负责,保证在生产过程中使用的图纸资料为有效版本。 4.2.1.4归口本部门管理的定型产品工艺改进、工装设计及新增零件的工艺、工装设计、履行审核、批准手续。 4.2.1.5车间的图纸、资料一律不外借,外部门人员借用需经主管主任批准,并填写《借阅登记》,当日归还,特殊情况当日不能归还的,需经车间主任签字批准限期归还。 4.2.2工艺设计控制 4.2.2.1车间技术组负责铸件铸造工艺的编制,并对其正确性、适用性负责,主管技术人员校对、审核、标准化后,主管主任签字批准,并正确执行冶炼工艺。
国家标准《GBT_9439-2009_灰铸铁件》最新修订说明
新修订的四项 铸铁国家标准
东南大学材料学院 孙国雄
新修订的四项铸铁国家标准
? GB/T 1348-(2009) 球墨铸铁件 ? GB/T 9439-(2009) 灰 铸 铁 件 ? GB/T 9441 -(2009) 球墨铸铁金相检验 ? GB/T 7216 -(2009) 灰铸铁金相检验
原标准已经迫切需要修订
? 原标准分别修订于20年前(灰铸铁金相标准修订于 1987年,其余三项修订于1988年)。20年来中国的铸 造业无论从规模、产量、技术、装备及管理都有了极大 的变化与发展。2001年起我国就已经成为世界铸件产量 最大的国家。 ? 20年来世界科学技术的发展及对于清洁生产的迫切化, 提高了对铸件的要求,促进了铸造技术(工艺、材质、 铸造方法、装备及控制等)及铸造工厂现代管理的快速 发展。 ? 经济全球化的发展使中国的铸造业已经进入国际竞争的 阶段,出现了“国际竞争国内化和国内竞争国际化”的状 况。中国的铸件已经销往世界上大多数制造业大国。因 此我们的国家标准也应该与相应的国际标准接轨。
修订国际标准的目的:
? 解决我国国家标准总体技术水平低、市 场适应性差、体系结构不合理等问题; ? 建立先进科学、适应社会主义市场经济 体制的标准体系 ; ? 全面落实国家标准的维护和管理任务, 建立相应的管理机制,从根本上提高国 家标准的时效性。
2,中华人民共和国国家标准
GB/T 9439-XXXX 代替GB/T 9439-1988
灰铸铁件 grey iron castings
中国铸造行业标准
中国铸造行业标准 第一条 制定中国铸造行业准入条件目的在于根据国家有关法规和政策引导我国铸造行业健康、有序和可持续发展,提升我国装备制造业整体水平和为国民经济各行业提供优质铸件,实现我国从世界铸造大国向铸造强国转变。 第二条 实施铸造行业准入制度,按照“铸造行业准入条件”加快淘汰那些规模小且工艺落后、耗能大、污染严重、作业条件恶劣的铸造企业,遏制行业内的恶性竞争和资源浪费。 第三条 在实施铸造行业准入制度过程中将积极引导企业通过兼并、重组,形成合理经营规模;在有条件的地区积极发展铸造产业集群或铸造工业园区,优化资源配置,大力发展清洁生产和循环经济;培育一批“专、特、精、新”的中小铸造企业,提高企业综合竞争力、铸件产品质量和企业效益。 第四条 铸造企业的布局及厂址的确定应符合国家产业政策和相应法规,符合各省、自治区、直辖市装备制造业发展规划。
在一类区内不能新建、扩建铸造厂,已有的铸造厂其污染物排放(含水、气和噪声等)指标应符合国家一类区有关标准的规定。在二类区和三类区,新建铸造厂和原有铸造厂的污染物(含水、气和噪声等)排放指标均应符合国家或地区有关标准的规定。 说明:一类区指国务院有关主管部门和省、自治区、直辖市人民政府划定的风景名胜区、自然保护区和水源地及其他需要特别保护的区域;二类区指城镇规划中确定的居住区、商业交通居民混合区、文化区、一般工业区和农村地区以及一、三类区不包括的地区;三类区指特定的工业区。 第五条鉴于目前我国东、中、西部地区社会、经济和工业发展程度的差异,在进行铸造行业结构调整和实施准入制度时,应区别对待。 第六条企业规模(产能) 1.现有的砂型铸铁件(含离心铸铁管及其他离心铸造)、铸钢件与有色铸件生产企业铸件年产能按所在地区(见表1)和类别(一、二、三类)不同应不低于表1所列的吨位。 2.采用砂型及离心铸造工艺之外的其他铸造工艺(包括压铸、低压铸造、金属型铸造、挤压铸造、熔模铸造、V
铸造工艺学期末复习资料
造型材料:用于造型制芯的各种原砂、粘结剂、添加剂以及由各种原材料所组成型砂和芯砂的材料。角形系数:铸造用硅砂的实际比表面积与理论比表面积的比值。烧结点:原砂颗粒表面或沙粒间的混杂物开始熔化的温度。比强度:每1%的粘结剂可获得的芯砂干拉强度。可使用时间:自硬树脂砂混砂后能够制作出合格砂芯的那一段时间。脱模时间:从混砂结束开始在芯盒内制的砂芯硬化到能满意地将砂芯从芯盒中取出,而不致发生砂芯变形所需的时间间隔。溃散性:铸件浇注并凝固后,砂型、砂芯被打碎的难易程度,也叫除砂性。1、涂料作用?优质涂料应具有的性质?一)1)砂型和砂芯是微孔——多孔隙体系,涂敷涂料,既填塞了砂型和砂芯表面空隙,也在铸型和金属液之间建立起一道有效的耐火屏障,避免铸件表面粗糙、机械粘砂、化学粘砂,使铸件表面粗糙 度得到很好的改善。2)涂 敷涂料也可防止或减少铸 件产生与砂子有关的其他 铸造缺陷或质量问题。3) 用涂料来产生冶金效应, 改善铸件局部的表面性能 和内在质量。二)1)好 的悬浮性及再搅拌性。2) 有一定的触变性。3)好 的覆盖能力。4)具有适 当的渗透性。5)具有良 好的粘结强度和耐激热性。 6)好的抗粘砂性。7)低 的发气性。8)好的贮存 性。9)各种原材料资源 丰富,成本低廉,并能满 足劳动卫生方面的要求。2、 列举常用吹二氧化碳的方 法。吹气速度及时间对砂 的硬度和强度有什么影响? 答:方法:1、插管法(大 型砂型或砂芯)2、盖罩 法(较小型砂或砂芯)3、 通过模样吹气法4、脉冲 吹气法5、真空CO2 僵化 法,又叫VRH-CO2 僵化法 或真空置换僵化法。影响: 低流速有利于钠水玻璃化 学反应,可以得到较高的 初始强度与硬度,但降低 终强度并促进放热;高流 速促进脱水及吸热物理反 应,是化学反应迟缓,可 得到较高的力学性能及较 好的存放性。从吹气时间 看,如果低流速且长时间 吹气,将得到强度低、表 面酥脆的型和芯,这就是 所谓的过吹。3、什么是 热砂问题?热砂问题有什 么不良影响?请论述解决 措施和途径。答:热砂: 一般型砂温度高于室温10 度以上成为热砂。影响:1、 砂温高,水分容易蒸发,使 型砂紧实率不易控制;2、 热砂蒸发的水蒸气,会凝 结在冷的皮带、砂斗和模 板表面上,使型砂的运送 和起模困难,还会降低铸 件表面的光洁程度;3、热 砂使型砂表面容易脱水, 降低表面强度,浇注时引 起冲砂和砂眼缺陷;4、热 砂发出的水蒸气会凝聚在 冷铁和砂芯上,使铸件产 生气孔。措施:1、加强 落砂、过筛、运输和混砂 过程中的通风,利用旧砂
最新铸造标准
最新铸造标准规范汇编 │目录.txt 7.39 KB ├─1铸造通用基础及工艺标准规范汇编 │1_1 GBT 5611-1998 铸造术语.pdf 2.05 MB │1_10 JBT 5105-1991 铸件模样起模斜度.pdf 459.19 KB │1_11 JBT5106-1991 铸件模样型芯头基本尺寸.pdf 1.03 MB │1_12 JBT 6983-1993 铸件材料消耗工艺定额计算方法.pdf 887.80 KB │1_13 JBT7528-1994 铸件质量评定方法.pdf 1.37 MB │1_14 JBT 7699-1995 铸造用木制模样和芯盒技术条件.pdf 813.12 KB │1_2 GBT 5678-1985铸造合金光谱分析取样方法.pdf 547.41 KB │1_3 GBT 60601-1997 表面粗糙度比较样块铸造表面.pdf 477.20 KB │1_4 GBT 6414-1999 铸件尺寸公差与机械加工余量.pdf 751.29 KB │1_5 GBT1 1351-1989 铸件重量公差.pdf 116.19 KB │1_6 GBT 15056-1994 铸造表面粗糙度评定方法.pdf 395.49 KB │1_7 JBT 2435-1978 铸造工艺符号及表示方法.pdf 1.26 MB │1_8 JBT 40221-1999 合金铸造性能测定方法.pdf 474.26 KB │1_9 JBT 40222-1999 合金铸造性能测定方法.pdf 630.48 KB ├─2铸铁标准规范汇编 (0 folders, 31 files, 20.70 MB, 20.70 MB in total.) │2_1 GBT 1348-1998 球墨铸铁件.pdf 764.01 KB │2_10 GBT 9439-1988 灰铸铁件.pdf 0.96 MB │2_11 GBT 9440-1988 可锻铸铁件.pdf 568.96 KB │2_12 GBT 9441-1988 球墨铸铁金相检验.pdf 1.49 MB │2_13 GBT 17445-1998 铸造磨球.pdf 698.91 KB │2_14 JBT 2122-1977 铁素体可锻铸铁金相标准.pdf 0.97 MB │2_15 JBT 3829-1999 蠕墨铸铁金相.pdf 1.21 MB │2_16 JBT 4403-1999 蠕墨铸铁件.pdf 820.70 KB │2_17 JBT 5000.4-1998 重型机械通用技术条件铸铁件.pdf 640.51 KB │2_18 JBT 7945-1999 灰铸铁力学性能试验方法.pdf 668.51 KB │2_19 JBT 9219-1999 球墨铸铁超声声速测定方法.pdf 544.11 KB │2_2 GBT 3180-1982 中锰抗磨球墨铸铁件技术条件.pdf 490.58 KB │2_20 JBT 9220.1-1999 铸造化铁炉酸性炉渣化学分析方法总则及—般规定.pdf 361.44 KB │2_21 JBT 9220.2-1999 铸造化铁炉酸性炉渣化学分析方法高氯酸脱水重量法测定二氧化硅量.pdf KB │2_22 JBT 9220.3-1999 铸造化铁炉酸性炉渣化学分析方法重铬酸钾容量法测定氧化亚铁量.pdf │2_23 JBT 9220.4-1999 铸造化铁炉酸性炉渣化学分析方法亚砷酸钠—亚硝酸钠容量法测定—氧化锰量.pdf 516.27 KB │2_24 JBT 9220.5-1999 铸造化铁炉酸性炉渣化学分析方法氟化钠—EDTA容量法测定三氧化二铝 量.pdf 437.86 KB │2_25 JBT 9220.6-1999 铸造化铁炉酸性炉渣化学分析方法 DDTC分离EGTA容量法测定氧化钙量.pdf KB │2_26 JBT 9220.7-1999 铸造化铁炉酸性炉渣化学分析方法高锰酸钾容量法测定氧化钙.pdf 61│2_27 JBT 9220.8-1999 铸造化铁炉酸性炉渣化学分析方法DDTC分离EDTA容量法测定氧化镁.pdf │2_28 JBT 9220.9-1999 铸造化铁炉酸性炉渣化学分析方法磷矾钼黄—甲基异丁基甲酮萃取光度法测定量.pdf 419.32 KB
铸造用硅砂标准
铸造用硅砂检验规程 1.1 主题内容与适用范围。 本标准规定了铸造硅砂的技术要求。 本标准适用于铸铁件用硅砂。 1.2 引用标准 GB/T 9442-1998(铸造用硅砂) 1.3 技术条件 1.3.1 化学成份及性能。 铸造用硅砂的化学成分及性能应符合表1规定。 表1 硅砂名称分级代号SiO2 含量 (%)含泥量 (%) 有害杂质(%)含水量(%) K2O+Na2O +CaO+MgO Fe2O3 铸铁用树脂沙用硅砂(擦洗沙)93 ≥93≤0.2<0.5<0.5袋装≤0.2 散装<5 1.3.1.1 铸造用硅砂的二氧化硅及有害杂质(k2O、Na2O、CaO、MgO、Fe2O3)的含量作为选矿和抽查的验收依据。 1.3.1.2 各种硅砂的含泥量作为每批进厂材料的验收依据。 1.3.1.3 铸造用硅砂袋装时的含水量作为验收依据。 1.3.1.4 铸铁树脂沙用散装硅砂,必须烘干,烘干后含水量应≤0.2%。 1.3.2 粒度。 铸造用硅砂粒度应符合表2规定 表2 硅砂名称筛 号 ︿ 目 ﹀ 主要粒度 组成部分 筛孔尺寸 (mm) 主要粒度 组成部分 上筛含量下筛含量 集中数 量(%) 中间筛 留量(%) 试验 筛号 含量 (%) 试验 筛号 含量 (% ) 铸铁树脂用 硅砂(擦洗沙)40/ 70 0.425 0.300 0.212 ≥7525 12目+以 上各筛目 之和 <5200目+260目 +底盘留量之 和 ≤ 1.0 1.3. 2.1 铸造用硅砂主要粒度组成部分的集中数量,中间筛留量作为验收依据。 1.3. 2.2 铸铁树脂用硅砂200至底盘的微粉含量作为验收依据。 1.3. 2.3 铸造用硅砂主要粒度组成部分波动值的绝对误差不得大于5%。 1.3.3 铸造树脂砂用硅砂酸耗值<5ml。 1.3.3.1 铸造树脂砂用硅砂酸耗值作为选矿和抽查指标。 1.3.4 铸造树脂砂用硅砂的灼减量应<0.5%。