通孔盲孔埋孔的区别
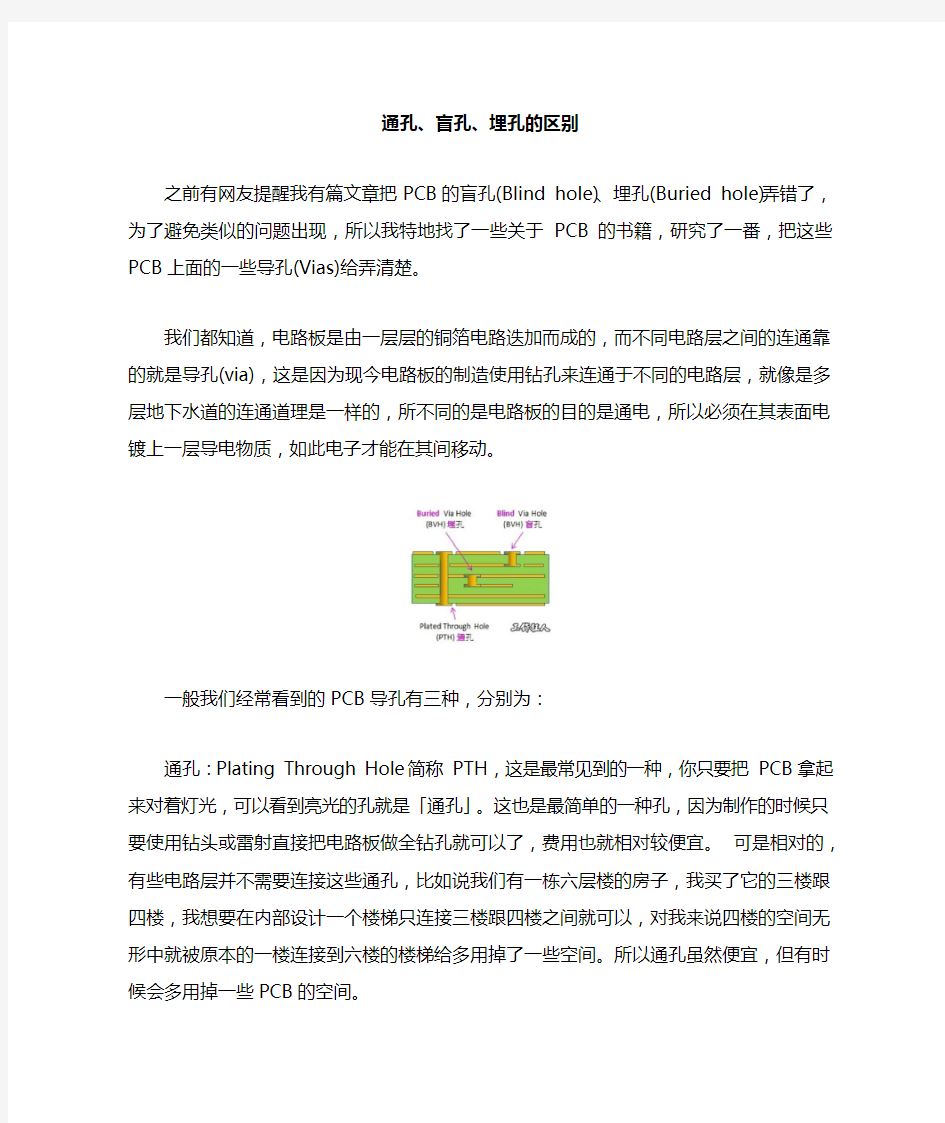

通孔、盲孔、埋孔的区别
之前有网友提醒我有篇文章把PCB的盲孔(Blind hole)、埋孔(Buried hole)弄错了,为了避免类似的问题出现,所以我特地找了一些关于PCB的书籍,研究了一番,把这些PCB上面的一些导孔(Vias)给弄清楚。
我们都知道,电路板是由一层层的铜箔电路迭加而成的,而不同电路层之间的连通靠的就是导孔(via),这是因为现今电路板的制造使用钻孔来连通于不同的电路层,就像是多层地下水道的连通道理是一样的,所不同的是电路板的目的是通电,所以必须在其表面电镀上一层导电物质,如此电子才能在其间移动。
一般我们经常看到的PCB导孔有三种,分别为:
通孔:Plating Through Hole 简称PTH,这是最常见到的一种,你只要把PCB拿起来对着灯光,可以看到亮光的孔就是「通孔」。这也是最简单的一种孔,因为制作的时候只要使用钻头或雷射直接把电路板做全钻孔就可以了,费用也就相对较便宜。可是相对的,有些电路层并不需要连接这些通孔,比如说我们有一栋六层楼的房子,我买了它的三楼跟四楼,我想要在内部设计一个楼梯只连接三楼跟四楼之间就可以,对我来说四楼的空间无形中就被原本的一楼连接到六楼的楼梯给多用掉了一些空间。所以通孔虽然便宜,但有时候会多用掉一些PCB的空间。
盲孔:Blind Via Hole,将PCB的最外层电路与邻近内层以电镀孔连接,因为看不到对面,所以称为「盲通」。为了增加PCB电路层的空间利用,应运而生「盲孔」制程。这种制作方法就需要特别注意钻孔的深度(Z轴)要恰到好处,不可此法经常会造成孔内电镀困难所以几乎以无厂商采用;也可以事先把需要连通的电路层在个别电路层的时候就先钻好孔,最后再黏合起来,可是需要比较精密的定位及对位装置。
埋孔:Buried hole,PCB内部任意电路层的连接但未导通至外层。这个制程无法使用黏合后钻孔的方式达成,必须要在个别电路层的时候就执行钻孔,先局部黏合内层之后还得先电镀处理,最后才能全部黏合,比原来的「通孔」及「盲孔」更费工夫,所以价钱也最贵。这个制程通常只使用于高密度(HDI)电路板,来增加其他电路层的可使用空间。
通孔回流工艺
穿孔回流焊是一项国际电子组装应用中新兴的技术。当在PCB的同一面上既有贴装元件,又有少量插座等插装元件时,一般我们会采取先贴片过回流炉,然后再手工插装过波峰焊的方式。但是,如果采取穿孔回流焊技术,则只需在贴片完成后,进回流炉前,将插件元件插装好,一起过回流炉就可以了。 通过这项比较,就可以看出穿孔回流焊相对于传统工艺的优越性。首先是减少了工序,省去了波峰焊这道工序,在费用上自然可以节省不少。同时也减少了所需工作人员,在效率上也得到了提高。其次是回流焊相对于波峰焊,生产桥接的可能性要小得多,这样就提高了一次通过率。穿孔回流焊技术相对传统工艺在经济性、先进性上都有很大的优势。所以,穿孔回流焊技术是电子组装中的一项革新,必然会得到广泛的应用。 但如果要应用穿孔回流焊技术,也需要对器件、PCB设计、网板设计等方面提出一些不同于传统工艺的要求。 a)元件: 穿孔元件要求能承受回流炉的回流温度的标准,最小为230度,65秒。这一过程包括在孔的上面涂覆焊膏(将在回流焊过程中进入孔中)。为使这一过程可行,元件体应距板面0.5毫米,所选元件的引脚长度应和板厚相当,有一个正方形或U形截面,(较之长方形为好)。 b)计算孔尺寸 完成孔的尺寸应在直径上比引脚的最大测量尺寸大0.255毫米(0.010英寸),通常用引脚的截面对角,而不包括保持特征。钻孔的尺寸比之完成孔再大0.15毫米(0.006英寸),这是电镀补偿,这样算得的孔就是可接受的最小尺寸。 c)计算丝网:(焊膏量) 第一部分计算是找出焊接所需的焊膏量,孔的体积减去引脚的体积再加上焊角的体积。(需要什么样的焊接圆角)。所需焊接体积乘以2就是所需焊膏量,因为焊膏中金属含量为50%体积(以ALPHA 的UP78焊膏为例)。丝印过程中将焊膏通过网孔印在PCB上,由于压力一般能将焊膏压进孔中0.8毫米(当刮刀与网板成45度角时)。我们计算进入孔中焊膏的体积,从所需焊膏量中减去它就得到在网孔中留下的焊膏的体积。这一体积除以网板的厚度就可以求出网孔所需的面积了。 d)网板设计: 网板的位置将取决于以下几个因素: 1、网孔的一边到孔中心的最小距离要求等于钻孔半径。 2、网孔总是比焊盘要大,所以焊膏将涂在阻焊层上,回流焊后确认不会有焊膏残留在阻焊盘上,网孔的边要求笔直,因为当回流焊过程焊膏进入孔中,将不会有焊膏在表面进行回流焊。 3、器件底面的下模形状有设计限制,下底面和丝印的焊膏之间需要有0。2毫米的空间。(在设计中必须包含) 4、在插座上,许多网孔提供笔直和窄的丝印,所以元件定位和在穿孔插座旁的测试点要留下一定的空间给焊膏层。 5、一般元件比如晶振,在元件下有足够的空间满足丝印需要的面积,这意味着将没有必要将焊膏涂覆在元件的外部。 e)元件管脚的准备: 管脚有一个正确的长度非常重要,当它们进入这一过程之前它们必须被预先剪切以达到比板厚多1.5毫米的条件。所有的引脚尺寸和网孔尺寸的变动偏差都将会被焊接圆角的量所包含,所以一些变动会体现在焊接圆角的高度变动上。 回流炉的温度曲线要求设置成:在4.5分钟内平滑提升到165+20度,从165~220+5度只经过一个温区,在220+5度保持50秒。 f)焊接: 由于实际原因,当穿孔回流焊时总是有焊膏的变动,所以设计有一个焊接圆角,可以解决一系列变
通孔埋孔盲孔
简介: 导通孔(VIA):一种用于内层连接的金属化孔,其中并不用于插入元件引线或其它增强材料。 盲孔(BIIND VIA):从印制板内仅延展到一个表层的导通孔。(从字面意思理解,看不穿看不透的孔,比如一个6层板,钻孔只从1层到4层,这样的就叫盲孔) 埋孔(BURIED VIA):未延伸到印制板表面的一种导通孔。(埋孔两头都不通的孔,比如一个6层板,钻孔只从3层到4层通,这样的就埋孔) 过孔(THROUGH VIA):从印制板的一个表层延展到另一个表层的导通孔。元件孔(COMPONENT HOLE):用于元件固定于印制板及导电图形电气连接的孔。 摘要:在高速PCB 设计中,过孔设计是一个重要因素,它由孔、孔周围的焊盘区和POWER 层隔离区组成,通常分为盲孔、埋孔和通孔三类。在PCB 设计过程中通过对过孔的寄生电容和寄生电感分析,总结出高速PCB 过孔设计中的一些注意事项。 关键词:过孔;寄生电容;寄生电感;非穿导孔技术 目前高速PCB 的设计在通信、计算机、图形图像处理等领域应用广泛,所有高科技附加值的电子产品设计都在追求低功耗、低电磁辐射、高可靠性、小型化、轻型化等特点,为了达到以上目标,在高速PCB 设计中,过孔设计是一个重要因素。 1、过孔 过孔是多层PCB 设计中的一个重要因素,一个过孔主要由三部分组成,一是孔;二是孔周围的焊盘区;三是POWER 层隔离区。过孔的工艺过程是在过孔的孔壁圆柱面上用化学沉积的方法镀上一层金属,用以连通中间各层需要连通的铜箔,而过孔的上下两面做成普通的焊盘形状,可直接与上下两面的线路相通,也可不连。过孔可以起到电气连接,固定或定位器件的作用。过孔示意图如图1 所示。 过孔一般又分为三类:盲孔、埋孔和通孔。 盲孔,指位于印刷线路板的顶层和底层表面,具有一定深度,用于表层线路和下面的内层线路的连接,孔的深度与孔径通常不超过一定的比率。
通孔回流焊接的工艺技术
通孔回流焊接的工艺技术如图2,可实现在单一步骤中同时对通孔元件和表面贴装元件(SMC/SMD)进行回流焊。相对传统工艺,在经济性、先进性上都有很大的优势。所以,通孔回流工艺是电子组装中的一项革新,必然会得到广泛的应用。 二通孔回流焊接工艺与传统工艺相比具有以下优势: 1、首先是减少了工序,省去了波峰焊这道工序,多种操作被简化成一种综合的工艺过程; 2、需要的设备、材料和人员较少; 3、可降低生产成本和缩短生产周期; 4、可降低因波峰焊而造成的高缺陷率,达到回流焊的高直通率。; 5、可省去了一个或一个以上的热处理步骤,从而改善PCB可焊性和电子元件的可靠性,等等。 尽管用通孔回焊可得到良好的工艺效果,但还是存在一些工艺问题。 1、在通孔回焊过程中锡膏的用量比较大,由于助焊剂挥发物质的沉积会增加对机器的污染,因而回流炉具有有效的助焊剂管理系统是很重要的; 2、对THT元件质量要求高,要求THT元件能经受再流焊炉的热冲击,例如线圈、连接器、屏蔽等。有铅焊接时要求元件体耐温235℃,无铅要求260℃以上。许多THT元件尤其是连接器无法承受回流焊温度;电位器、铝电解电容、国产的连接器、国产塑封器件等不适合回流焊工艺。 3、由于要同时兼顾到THT元件和SND元件,使工艺难度增加。 本文重点是确定对通孔回流工艺质量有明显影响的各种因素,然后将这些因素划分为材料、设计或与工艺相关的因素,揭示在实施通孔回流工艺之前必须清楚了解的关键问题。 1. 通孔回流焊焊点形态要求 2. 获得理想焊点的锡膏体积计算 3. 锡膏沉积方法 4. 设计和材料问题 5. 贴装问题 6. 回流温度曲线的设定 下面将逐项予以详细描述。
四层PCB之过孔、盲孔、埋孔
四层PCB之过孔、盲孔、埋孔 过孔(Via):也称之为通孔,是从顶层到底层全部打通的,在四层PCB中,过孔是贯穿1,2,3,4层,对不相干的层走线会有妨碍。过孔主要分为两种: 1、沉铜孔PTH(Plating Through Hole),孔壁有铜,一般是过电孔(VIA PAD)及元件孔(DIP PAD)。 2、非沉铜孔NPTH(Non Plating Through Hole),孔壁无铜,一般是定位孔及螺丝孔。 盲孔(Blind Via):只在顶层或底层其中的一层看得到,另外那层是看不到的,也就是说盲孔是从表面上钻,但是不钻透所有层。盲孔可能只要从1到2,或者从4到3(好处:1,2导通不会影响到3,4走线);而过孔是贯穿1,2,3,4层,对不相干的层走线有影响,.不过盲孔成本较高,需要镭射钻孔机。盲孔板应用于表面层和一个或多个内层的连通,该孔有一边是在板子之一面,然后通至板子之内部为止;简单点说就是盲孔表面只可以看到一面,另一面是在板子里的。一般应用在四层或四层以上的PCB板。 埋孔(Buried Via):埋孔是指做在内层过孔,压合后,无法看到所以不必占用外层之面积,该孔之上下两面都在板子之内部层,换句话说是埋在板子内部的。简单点说就是夹在中间了,从表面上是看不到这些工艺的,顶层和底层都看不到的。做埋孔的好处就是可以增加走线空间。但是做埋孔的工艺成本很高,一般电子产品不采用,只在特别高端的产品才会有应用。一般应用在六层或六层以上的PCB板。 过孔几乎所有的PCB板都会用到,是最基本也是最常用的孔,因此在这里不做说明,主要来讲一下盲孔和埋孔。首先我们从传统多层板讲起。标准的多层电路板的结构,是含内层线路及外层线路,再利用钻孔,以及孔内金属化的制程,来达到各层线路之内部连结功能。但是因为线路密度的增加,零件的封装方式不断的更新。为了让有限的电路板面积,能放置更多更高性能的零件,除线路宽度愈细外,孔径亦从DIP插孔孔径1 mm缩小为SMD的0.6 mm,更进一步缩小为0.4mm或以下。但是仍会占用表面积,从而就有了盲孔和埋孔的产生。 在四层板中,中间的两个层主要是用来走电源层(VCC)和地层(GND)的,如果板子元件多密度大,那么内层也可以走些普通的信号线,可以在主元件层(主元件层一般是在顶层)的相邻内部层用做地层,整层用来敷铜,然后另外一个内层用来做主要的走线层,次元件层(次元件层一般是在底层)也走些线。 正片与负片:四层板,首先要搞明白的是正片和负片,就是layer和plane的区别。正片就是平常用在顶层和地层的的走线方法,既走线的地方是铜线,用Polygon Pour进行大块敷铜填充。负片正好相反,既默认敷铜,走线的地方是分割线,也就是生成一个负片之后整一层就已经被敷铜了,要做的事情就是分割敷铜,再设置分割后的敷铜的网络。在PROTEL之前的版本,是用Split来分割,而现在用的版本Altium Designer中直接用Line,快捷键PL,来分割,分割线不宜太细,我用30mil(约0.762mm)。要分割敷铜时,只要用LINE画一个封闭的多边形框,在双击框内敷铜设置网络。正负片都可以用于内电层,正片通过走线和敷铜也可以实现。负片的好处在于默认大块敷铜填充,在添加过孔,改变敷铜大小等等操作都不需要重新Rebuild,这样省去了重新敷铜计算的时间。中间层用于电源层和地层时候,层面上大多是大块敷铜,这样用负片的优势就较明显。 采用盲孔和埋孔的优点:在非穿导孔技术中,盲孔和埋孔的应用,可以极大地降低PCB的尺寸和质量,减少层数,提高电磁兼容性,增加电子产品特色,降低成本,同时也会使得设计工作更加简便快捷。在传统PCB设计和加工中,通孔会带来许多问题。首先它们占居大量的有效空间,其次大量的通孔密集一处也对多层PCB内层走线造成巨大障碍,这些通孔占去走线所需的空间,它们密集地穿过电源与地线层的表面,还会破坏电源地线层的阻抗特性,使电源地线层失效。且常规的机械法钻孔将是采用非穿导孔技术工作量的20倍。在PCB设计中,虽然焊盘、过孔的尺寸已逐渐减小,但如果板层厚度不按比例下降,将会导致通孔的纵横比增大,通孔的纵横比增大会降低可靠性。随着先进的激光打孔技术、等离子干腐蚀技术的成熟,应用非贯穿的小盲孔和小埋孔成为可能,若这些非穿导孔的孔直径为0.3mm,所带来的寄生参数是原先常规孔的1/10左右,提高了PCB的可靠性。由于采用非穿导孔技术,使得PCB上大的过孔会很少,因而可以为走线提供更多的空间。剩余空间可以用作大面积屏蔽用途,以改进EMI/RFI 性能。同时更多的剩余空间还可以用于内层对器件和关键网线进行部分屏蔽,使其具有最佳电气性能。采用非穿导孔,可以更方便地进行器件引脚扇出,使得高密度引脚器件(如BGA 封装器件)很容易布线,缩短连线长度,满足高速电路时序要求。 采用盲孔和埋孔的缺点:最主要的缺点就是板子成本高,加工制做复杂。既增加成本还有加工风险,调试时会更不好测试测量,因此建议尽量不用盲孔和埋孔,除非在板子尺寸受限,迫不得已的情况下才用。
盲孔填孔不良分析
电镀盲孔填孔不良分析 目前多阶HDI板的层间互连大多采用微孔叠孔及交错连接方式设计,一般采用电镀铜填孔方式进行导通,但电镀填盲孔技术与传统电镀有一定差别,且在工艺参数,流程设计,设备方面更有严格要求,填孔过程中出现空洞、凹陷、漏填也是厂内控制的难点,下面将厂内填孔缺陷进行分析,提供些填孔不良的思路; 一、填孔不良分析: 针对厂内填孔不良切片分析分类,统计如下: 二、原因分析: 通过切片分析确认,不良主要为凹陷、漏填、空洞,其中凹陷、漏填比例较高,其次为空洞,现针对厂内填孔不良可能原因进行分析. 2.1添加剂浓度失调:盲孔的填孔主要是通过添加剂中各组成分的协调作用、吸附差异平衡化完成,浓度失控势必会造成添加剂在盲孔内吸附平衡的破坏影响填孔效果. 2.2打气喷管堵塞:填孔槽打气大小直接影响到填孔过程中孔内药水交换效果,若打气效果差必然会造成孔内药水交换导致填孔效果欠佳凹陷值偏大.
2.3导电性不良:夹头或挂具损坏、飞靶和V型座接触不好,导致电流分布不均,板内电流小区域必然会出现盲孔凹陷或漏填现象. 2.4填孔前微蚀异常:填孔前微蚀不足均可能导致个别盲孔孔内导电不良,孔内电阻偏高,在填孔时不利于添加剂分布导致填孔失败. 2.5板子入槽时变形导致局部盲孔突起,局部盲孔漏填或凹陷. 2.6泵浦吸入口漏气,必然会造成大量空气进入槽内,通过过滤泵循环过滤将起泡带入整个槽内通过气流进入盲孔,阻碍孔内药水交换导致盲孔漏填现象. 三、效果验证: 实验前通过对药水调整至最佳状态,检查打气管道、夹头(挂具)、打气状况,维修设备接触不良处并用稀硫酸清洗、微蚀速率控制在20—30u”,保证板为垂直状态后进行填孔测试,测试结果无异常. 四、结论: 通过改善前后对比可以看出:厂内填孔不良主要为药水浓度、打气、导电性、填孔前微蚀量异常及槽内有气泡导致填孔异常,当然影响盲孔填孔异常的因素还有很多,只有平时做到长期监控,细心维护设备,认真排查造成填孔不良的每一个可能因素,才能真正运用好填孔技术,解决厂内填孔异常.
thr通孔回流焊技术要求(1)
通孔回流焊技术要求 近年来,表面贴装技术(SMT)迅速发展起来,在电子行业具有举足轻重的位置。除了全自动化生产规模效应外,SMT还有以下的技术优势:元件可在PCB的两面进行贴装,以实现高密度组装;即使是最小尺寸的元件也能实现精密贴装,因此可以生产出高质量的PCB组件。 然而,在一些情况下,这些优势随着在PCB上元件贴着力的减少而削弱。让我们观察图1的例子。SMT元件的特点是设计紧凑,并易于贴装,与通孔的连接器在尺寸和组装形式上有明显的区别。 图1 PCB上组装有SMT元件(左)和一个大理通孔安装的连接器(右) 用于工业领域现场接线的连接器通常是大功率元件。可满足传输高电压、大电流的需要。因此设计时必须考虑到足够的电气间隙与爬电距离,这些因素最终影响到元件的尺寸。 此外,操作便利性、连接器的机械强度也是很重要的因素。连接器通常是PCB主板与“外界部件”通信的“接口”,故有时可能会遇到相当大的外力。通孔技术组装的元件在可靠性方面要比相应的SMT元件高很多。无论是强烈的拉拽、挤压或热冲击,它都能承受,而不易脱离PCB。 从成本考虑,大部分PCB上SMT元件约占80%,生产成本仅占60%;通孔元件约占20%,生产成本却占40%,如图2所示。可见,通孔元件生产成本相对较高。而对许多制造公司来说,今后面临的挑战之一便是开发采用纯SMT工艺的印刷线路板。
图2 带有通孔无件和SMT元件的PCB 根据生产成本以及对PCB的影响,SMT+波峰焊和SMT+压接技术(press in)等现有的工艺还不完全令人满意,因为在现有的SMT工序需要进行二次加工,不能一次性完成组装。 这就对采用通孔技术的元件提出了下列要求:通孔元件与贴片元件应该使用同样的时间、设备和方法来完成组装。 THR如何与SMT进行整合 根据上述要求发展起来的技术,称之为通孔回流焊技术(Through-hole Reflow,THR),又叫“引脚浸锡膏(pin in paste,PIP)”工序,如图3所示。 图3 通孔回流焊技术的工序
盲孔、埋孔制造技术
采用盲孔和埋孔是提高多层板密度、减少层数和板面尺寸的有效方法,并大大减少了镀覆通孔的数量。BUM板几乎都采用埋孔和盲孔结构。 埋孔和盲孔大都是直径为0.05~0.15mm的小孔。埋孔在内层薄板上,用制造双面板的工艺进行制造;而盲孔的制造开始用控制Z轴深度的钻小孔数控床,现普遍采用激光钻孔、等离子蚀孔和光致成孔。激光钻孔有二氧化碳激光机和Nd:YAG紫外激光机。日本日立公司的二氧化碳激光钻孔机,激光波长为9.4弘m,1个盲孔分3次钻成,每分钟可钻3万个孔。 随着电子产品向高密度,高精度发展,相应对线路板提出了同样的要求。而提高pcb 密度最有效的方法是减少通孔的数量,及精确设置盲孔,埋孔来实现。 盲/埋孔板的基础知识 谈到盲/埋孔,首先从传统多层板说起。标准的多层板的结构,是含内层线路及外层线路,再利用钻孔,以及孔内金属化的制程,来达到各层线路之内部连结功能。但是因为线路密度的增加,零件的封装方式不断的更新。为了让有限的PCB面积,能放置更多更高性能的零件,除线路宽度愈细外,孔径亦从DIP插孔孔径1 mm缩小为SMD的0.6 mm,更进一步缩小为0.4mm以下。但是仍会占用表面积,因而又有埋孔及盲孔的出现,其定义如下: A. 埋孔(Buried Via) 见图示,内层间的通孔,压合后,无法看到所以不必占用外层之面积 B. 盲孔(Blind Via) 见图示,应用于表面层和一个或多个内层的连通 埋孔设计与制作 埋孔的制作流程较传统多层板复杂,成本亦较高,图显示传统内层与有埋孔之内层制作上的差异,图20.3则解释八层埋孔板的压合迭板结构. 图20.4则是埋孔暨一般通孔和PAD 大小的一般规格 密度极高,双面SMD设计的板子,会有外层上下,I/O导孔间的彼此干扰,尤其是有VIP(Via-in-pad)设计时更是一个麻烦。盲孔可以解决这个问题。另外无线电通讯的盛行, 线路之设计必达到RF(Radio frequency)的范围, 超过1GHz以上. 盲孔设计可以达到此需求,图20.5是盲孔一般规格。
TSV硅通孔技术的研究解析
西安电子科技大学 硕士研究生课程考试试卷 科目集成电路封装与测试 题目硅通孔(TSV)工艺技术 学号 1511122657 班级 111504 姓名马会会 任课教师包军林 分 数 评卷人 签名 注意事项 1.考试舞弊者做勒令退学或开除学籍 2.用铅笔答题一律无效(作图除外) 3.试题随试卷一起交回 硅通孔TSV工艺技术
1511122657 马会会 摘要:本文主要介绍近几年封装技术的快速发展及发展趋势。简单介绍了TSV技术的发展前景及其优势。详细介绍了硅通孔工艺以及其关键技术。并针对TSV 中通孔的形成,综述了国内外研究进展,提出了干法刻蚀、湿法刻蚀、激光钻孔和光辅助电化学刻蚀法(PAECE)等四种TSV通孔的加工方法、并对各种方法进行了比较,提出了各种方法的适用范围。 关键词:后摩尔时代;封装技术;TSV;硅通孔 Abstract:This paper mainly introduces the rapid development and development trend of packaging technology in recent years.In the brief introduction of several vertical packaging technology, the paper focuses on the development of TSV technology and its advantages. The technology of Si - through hole and its key technologies are introduced in detail. In this paper, the research progress of TSV was summarized, and the method of dry etching, wet etching, laser drilling and photo assisted electrochemical etching (PAECE) was proposed, and four kinds of TSV through hole were compared. Keywords:Post Moore era; packaging technology; TSV; silicon through hole 引言 集成电路技术在过去的几十年里的到了迅速的发展。集成电路的速度和集成度得到了很大的提高并且一直遵循摩尔定律不断发展,即单位集成电路面积上可容纳的晶体管数目大约每隔18个月可以增加一倍。然而,当晶体管尺寸减小到几十纳米级后,想再通过减小晶体管尺寸来提升集成电路的性能已经变得非常困难,要想推动集成电路行业继续遵循摩尔定律发展就不得不寻求新的方法。 自从集成电路发明以来,芯片已无可辩驳地成为电子电路集成的最终形式。从那以后,集成度增加的速度就按照摩尔定律的预测稳步前进。摩尔定律的预测在未来若干年依然有效的观点目前仍然被普遍接受,然而,一个同样被广泛认同的观点是,物理定律将使摩尔定律最初描述的发展趋势停止。在这种情况下,电子电路技术和点路设计的概念将进入一个新的发展阶段,互连线将在重要性和价值方面得到提升。在被称作“超越摩尔定律”的新兴范式下,无论是物理上还是使用上,在z轴方向组装都变得越来越重要。目前在电子封装业中第三维正在被广泛关注,成为封装技术的主导。 图1 封装的技术演变与长期发展图
盲孔和通孔同步电镀工艺-solidst
印制线路板盲孔电镀填充工艺 熊海平 摘要介绍了一种利用直流电源进行微盲孔和通孔同时电镀的工艺,同时给出了相关的工艺条件和电镀效果。 关键词盲孔通孔同步电镀 Printed Circuit Board Micro-via′s Filling Process Abstract This paper introduced a copper plating process for micro-via filling and through hole plating simultaneously in DC application. Meanwhile, the plating parameters and results were been expressed Key Words Micro-via filling through hole plating 0 前言 微盲孔(Blind Micro-via)电镀铜填充多用于IC晶片载板产业,在电子产品轻、薄、短、小化的发展趋势要求下,印制线路板的布线密度越来越高,这就要求板上的孔径必须越来越小.在导通盲孔上直接叠孔的结构是实现最高布线密度的有效方法之一.就常规的垂直线电镀经验而言,一般通孔中的电镀层厚度要小于板面电镀铜层的厚度,由此可推断,盲孔在电镀过程中,由于受电镀液在孔内的对流性差以及其它客观条件的限制,要想得到理想的填充效果,存在相当大的技术难度。因此,水平电镀设备,脉冲电源等被应用来解决这类难题。是不是垂直电镀线就没办法使盲孔和通孔在同一制程中达到理想的电镀效果呢?事实并非如此,只要我们对设备合理改进,设定合理的工艺流程和参数,对孔径在180微米以下,深度不超过100微米的任意孔径/深度的盲孔,一般能得到较完美的填充。 1.设备要求 毫无疑问,传统的阴极移动加空气搅拌的垂直线电镀方式是不可能圆满完成盲孔填充任务的,必须在此基础上对设备进行适当的改造。最常见的改进方法是,添加高速循环泵,如果电镀槽尺寸许可,在阴极两侧添置两排喷射管,让经循环泵高速流出的镀液,经喷管喷射阴极范围内的有效电镀区域。很多设备商已经在此方面做了相当成功的研究,生产线上已不乏成功使用的范例。 2.工艺流程及电镀参数设定 酸性电镀铜添加剂中的各组份功能和作用原理在很多文献中有详尽的描述,一般而言,常规的全板和图形电镀添加剂中包含着加速剂、抑制剂、润湿剂等主要成分,它们的作用和功能各异,电镀的效果取决于它们的协同效应。作为盲孔电镀的添加剂,如果继续采用这种常规的方式,很难得到理想的填充效果,因为加速剂在孔周的吸附浓度远大于盲孔内壁和底部吸附浓度,铜离子在孔周的交换速率也远大于孔内,因此,在孔周镀层增长速度远大于孔底和孔壁,最终结果如果往往是在盲孔填充过程中,孔内容易出现空洞,如图1。
应用于三维封装中的硅通孔技术
- 18 - 收稿日期:2012-03-26 应用于三维封装中的硅通孔技术 邓小军1,曹正州2 (1.无锡创立达科技有限公司,江苏 无锡 214142;2.中国电子科技集团公司第58研究所,江苏 无锡 214035) 摘 要:随着集成电路日新月异的发展,当半导体器件工艺进展到纳米级别后,传统的二维领域封装已渐渐不能满足电路高性能、低功耗与高可靠性的要求。为解决这一问题,三维封装成为了未来封装发展的主流。文章简要介绍了三维封装的工艺流程,并重点介绍了硅通孔技术的现阶段在CSP 领域的应用,以及其未来的发展方向。关键词:三维封装;硅通孔;CSP 中图分类号:TN305.94 文献标识码:A 文章编号:1681-1070(2012)09-0018-06 The Through Silicon Via Technology Using in 3D Packaging DENG Xiao-jun 1, CAO Zheng-zhou 2 (1. Wuxi TreasureStar Technology Co ., LTD ., Wuxi 214142, China ; 2. China Electronics Technology Group Corporation No .58 Research Institute , Wuxi 214035, China ) Abstract: With the development of now day integrated circuit, the traditional 2D packaging can not satisfy the requirement of high function, low power and high reliability when the semiconductor device develops into nano level. To solve the problem, 3D packaging becomes the mainstream of future package. In this paper, authors introduce the process flow of 3D package and emphasize the through silicon via (TSV )technology using in CSP area and the further development’s direction. Key words: 3D packaging; TSV; CSP 1 引言 在过去的三十年间,半导体技术已经在二维领域得到了广泛的应用。一个关键原因就是金属氧化物半导体(MOS )器件数量的快速增长趋势是可以根据摩尔定律预测的[1] 。但是近年来实际的器件增长趋势已经和理想模型的预测有所差别了。因为随着芯片功能的增强,芯片内集成的晶体管数目越来越多,体积也越来越大,功耗也越来越高,kT /q 比无法继续在现有技术层面缩小,因此在不提高泄漏上限的基础上降低MOS 器件的阈值电压就变得十分困难。而阈值电压无法降低,降低功耗和提高器件 的性能这两种要求就会产生冲突。尤其是在高集成 度条件下,单个芯片内各个系统的互连引线过长和过多,其阻容延迟和寄生电容会使器件工作速度降低。另外,其所引发的信号传输延迟、信号带宽不足和控制时序的不一致性,会制约当前通信技术和大型计算机技术的发展。还有,互连引线过长引起的噪声问题也不容忽视,而各种噪声均与信号在互连引线中的传输距离密切相关。要满足上述性能要求,必须突破当前二维器件技术水平的制约。 大规模集成电路的结构是其中一种解决方案。随着电路集成度越来越高,信号的延迟主要取决于引线长度和引脚电容。三维大规模集成电路是一种能提升性能同时不需要增加功耗的解决途径。带来
通孔盲孔埋孔的区别
通孔盲孔埋孔的区别公司标准化编码 [QQX96QT-XQQB89Q8-NQQJ6Q8-MQM9N]
通孔、盲孔、埋孔的区别 之前有网友提醒我有篇文章把PCB的盲孔(Blind hole)、埋孔(Buried hole)弄错了,为了避免类似的问题出现,所以我特地找了一些关于PCB的书籍,研究了一番,把这些PCB上面的一些导孔(Vias)给弄清楚。 我们都知道,电路板是由一层层的铜箔电路迭加而成的,而不同电路层之间的连通靠的就是导孔(via),这是因为现今电路板的制造使用钻孔来连通于不同的电路层,就像是多层地下水道的连通道理是一样的,所不同的是电路板的目的是通电,所以必须在其表面电镀上一层导电物质,如此电子才能在其间移动。 一般我们经常看到的PCB导孔有三种,分别为: 通孔:Plating Through Hole 简称 PTH,这是最常见到的一种,你只要把PCB 拿起来对着灯光,可以看到亮光的孔就是「通孔」。这也是最简单的一种孔,因为制作的时候只要使用钻头或雷射直接把电路板做全钻孔就可以了,费用也就相对较便宜。可是相对的,有些电路层并不需要连接这些通孔,比如说我们有一栋六层楼的房子,我买了它的三楼跟四楼,我想要在内部设计一个楼梯只连接三楼跟四楼之间就可以,对我来说四楼的空间无形中就被原本的一楼连接到六楼的楼梯给多用掉了一些空间。所以通孔虽然便宜,但有时候会多用掉一些PCB的空间。 盲孔:Blind Via Hole,将PCB的最外层电路与邻近内层以电镀孔连接,因为看不到对面,所以称为「盲通」。为了增加PCB电路层的空间利用,应运而生「盲孔」制程。这种制作方法就需要特别注意钻孔的深度(Z轴)要恰到好处,不可此法经常会造成孔内电镀困难所以几乎以无厂商采用;也可以事先把需要连通的电路层在个别电路层的时候就先钻好孔,最后再黏合起来,可是需要比较精密的定位及对位装置。 埋孔:Buried hole, PCB内部任意电路层的连接但未导通至外层。这个制程无法使用黏合后钻孔的方式达成,必须要在个别电路层的时候就执行钻孔,先局部黏合内层之后还得先电镀处理,最后才能全部黏合,比原来的「通孔」及「盲孔」更费工夫,所以价钱也最贵。这个制程通常只使用于高密度(HDI)电路板,来增加其他电路层的可使用空间。
硅基片微型通孔加工技术
收稿日期:2004203202;修订日期:2004203229 基金项目:2003年中国科学技术大学青年基金资助项目(K B0910) 作者简介:赵钢(1977-),男,河北人,博士,研究方向为基于并行压电探针的超高密度信息存储技术、微机电系统器件的加工与工艺技术研究;褚家如(1963-),男,安徽人,教授,博士生导师,博士,研究方向为三维微纳米器件的加工,微型传感器、致动器的集成以及微纳机电系统的封装技术等。 文章编号:100328213(2004)022******* 硅基片微型通孔加工技术 赵 钢,褚家如,徐 藻 (中国科学技术大学精密机械与精密仪器系,合肥230027) 摘要:介绍了硅基片微型通孔的用途及在微机电系统发展中的重要性,从原理、过程、 优缺点等方面详细叙述了激光打孔法、湿法刻蚀法、深度反应离子刻蚀法(DRIE )和 光辅助电化学刻蚀法(PAECE )等四种硅基片微型通孔的加工方法,并对各种方法进行了比较,提出了各种方法的适用范围。 关 键 词:微型通孔;微机电系统;深度反应离子刻蚀法;光辅助电化学刻蚀法中图分类号:TN405 文献标识码:A 1 引言 硅基片微型通孔是指贯穿硅片的孔径在微米量级。在通孔中填充金属可使之成为导电通孔,常用于微机电系统(M EMS )和多层半导体器件的电信号传输。图1为硅基片导电通孔的示意图。使用微型导电通孔进行电信号的传输,有助于减小基片单面布线的复杂程度,提高阵列器件的排列密度,促进多层半导体结构的发展。 图2所示的悬臂梁探针阵列[1]采用倒装片技术,电信号通过导电通孔传导到硅片背面,这既可以避免引线接线柱对探针阵列并行工作时的干涉,又可以减小器件所在面的复杂程度,降低制造的难度。 图3所示的是多层硅片层叠的结构[2-3],导电通孔所起的作用是完成不同层 之间电信号的传输,这种结构大大提高了系 统的集成度 。 图1 硅基片导电通孔示意图 与硅基片导电通孔类似,在印刷电路板 上也有承担传导电信号任务的通孔,但由于M EMS 对器件尺寸和阵列排列密度的要求, 第2期2004年6月微细加工技术 MICROFABRICA TION TECHNOLO GY №.2J un.,2004
通孔盲孔埋孔的区别
通孔盲孔埋孔的区别文稿归稿存档编号:[KKUY-KKIO69-OTM243-OLUI129-G00I-FDQS58-
通孔、盲孔、埋孔的区别 之前有网友提醒我有篇文章把PCB的盲孔(Blind hole)、埋孔(Buried hole)弄错了,为了避免类似的问题出现,所以我特地找了一些关于PCB 的书籍,研究了一番,把这些PCB上面的一些导孔(Vias)给弄清楚。 我们都知道,电路板是由一层层的铜箔电路迭加而成的,而不同电路层之间的连通靠的就是导孔(via),这是因为现今电路板的制造使用钻孔来连通于不同的电路层,就像是多层地下水道的连通道理是一样的,所不同的是电路板的目的是通电,所以必须在其表面电镀上一层导电物质,如此电子才能在其间移动。 一般我们经常看到的PCB导孔有三种,分别为: 通孔:Plating Through Hole 简称 PTH,这是最常见到的一种,你只要把PCB拿起来对着灯光,可以看到亮光的孔就是「通孔」。这也是最简单的一种孔,因为制作的时候只要使用钻头或雷射直接把电路板做全钻孔就可以了,费用也就相对较便宜。可是相对的,有些电路层并不需要连接这些通孔,比如说我们有一栋六层楼的房子,我买了它的三楼跟四楼,我想要在内部设计一个楼梯只连接三楼跟四楼之间就可以,对我来说四楼的空间无形中就被原本的一楼连接到六楼的楼梯给多用掉了一些空间。所以通孔虽然便宜,但有时候会多用掉一些PCB的空间。
盲孔:Blind Via Hole,将PCB的最外层电路与邻近内层以电镀孔连接,因为看不到对面,所以称为「盲通」。为了增加PCB电路层的空间利用,应运而生「盲孔」制程。这种制作方法就需要特别注意钻孔的深度(Z轴)要恰到好处,不可此法经常会造成孔内电镀困难所以几乎以无厂商采用;也可以事先把需要连通的电路层在个别电路层的时候就先钻好孔,最后再黏合起来,可是需要比较精密的定位及对位装置。 埋孔:Buried hole, PCB内部任意电路层的连接但未导通至外层。这个制程无法使用黏合后钻孔的方式达成,必须要在个别电路层的时候就执行钻孔,先局部黏合内层之后还得先电镀处理,最后才能全部黏合,比原来的「通孔」及「盲孔」更费工夫,所以价钱也最贵。这个制程通常只使用于高密度(HDI)电路板,来增加其他电路层的可使用空间。
通孔再流焊接技术
通孔再流焊接技术 1 引言 目前PCB组装中,表面贴装元件约占800/0,成本为60%,而穿孔元件约占20%,成本为40%。这种混合板采用传统再流焊技术是不能进行焊接,需采用再流焊与波峰焊两道工序。然而波峰焊接技术被应用于过孔插装元件(THD)印制板组件的焊接有许多不足之处:不适合高密度、细间距元件焊接;桥接、漏焊较多;需喷涂助焊剂;印制板受到较大热冲击易翘曲变形。 为了适应表面组装技术的发展,解决以上焊接难点,通孔再流焊接技术得到应用,可以实现一道工序完成焊接。通孔再流焊接技术(THR,Through-hole Reflow),又称为穿孔再流焊PIHR(Pin-in-Hole Reflow)。该技术原理是在印制板完成贴片后,使用一种安装有许多针管的特殊模板,调整模板位置使针管与插装元件的过孔焊盘对齐,使用刮刀将模板上的焊膏漏印到焊盘上,然后安装插装元件,最后插装元件与贴片元件同时通过再流焊完成焊接。 通孔再流焊在很多方面可以替代波峰焊来实现对插装元件的焊接,特别是在处理焊接面上分布有高密度贴片元件(或有线间距SMD)的插件焊点的焊接,这此采用传统的波峰焊接已无能为力,另外通孔再流焊能极大地提高焊接质量,这足以弥补其设备昂贵的不足。通孔再流焊的出现,对于丰富焊接手段、提高线路板组装密度(可在焊接面分布高密度贴片元件)、提升焊接质量、降低工艺流程,都大有帮助。 2 通孔再流焊(THR&PIP)工艺过程 一般元件都可以加工成为表面贴装元件,但是部分异型元件,如连接器、变压器和屏蔽罩等,为了满足机械强度和大电流需要,仍然需要加工成为接插元件,通孔式接插元件有较好的焊点机械强度。 接插元件应用于通孔再流焊工艺时应考虑2个问题:一为并不是所有接插元件都可以满足通孔再流焊工艺需求,即元件材料不会因再流高温而破坏,表1为可(不可)用于再流焊工艺的元件材料汇总;二是虽然通孔式接插元件可利用现有的SMT设备来组装,但在许多产品中不能提供足够的机械强度,而且在大面积PCB上,由于平整度的关系,很难使表面贴装式接插元件的所有引脚都与焊盘有一个牢固的接触,就需重新设计模板、再流焊温度曲线及引脚与开孔直径比例等。
通孔、盲孔、埋孔的区别
通孔、盲孔、埋孔的区别 之前有网友提醒我有篇文章把PCB的盲孔(Blind hole)、埋孔(Buried hole)弄错了,为了避免类似的问题出现,所以我特地找了一些关于PCB的书籍,研究了一番,把这些PCB上面的一些导孔(Vias)给弄清楚。 我们都知道,电路板是由一层层的铜箔电路迭加而成的,而不同电路层之间的连通靠的就是导孔(via),这是因为现今电路板的制造使用钻孔来连通于不同的电路层,就像是多层地下水道的连通道理是一样的,所不同的是电路板的目的是通电,所以必须在其表面电镀上一层导电物质,如此电子才能在其间移动。 一般我们经常看到的PCB导孔有三种,分别为: 通孔:Plating Through Hole 简称PTH,这是最常见到的一种,你只要把PCB拿起来对着灯光,可以看到亮光的孔就是「通孔」。这也是最简单的一种孔,因为制作的时候只要使用钻头或雷射直接把电路板做全钻孔就可以了,费用也就相对较便宜。可是相对的,有些电路层并不需要连接这些通孔,比如说我们有一栋六层楼的房子,我买了它的三楼跟四楼,我想要在内部设计一个楼梯只连接三楼跟四楼之间就可以,对我来说四楼的空间无形中就被原本的一楼连接到六楼的楼梯给多用掉了一些空间。所以通孔虽然便宜,但有时候会多用掉一些PCB的空间。 盲孔:Blind Via Hole,将PCB的最外层电路与邻近内层以电镀孔连接,因为看不到对面,所以称为「盲通」。为了增加PCB电路层的空间利用,应运而生「盲孔」制程。这种制作方法就需要特别注意钻孔的深度(Z轴)要恰到好处,不可此法经常会造成孔内电镀困难所以几乎以无厂商采用;也可以事先把需要连通的电路层在个别电路层的时候就先钻好孔,最后再黏合起来,可是需要比较精密的定位及对位装置。 埋孔:Buried hole,PCB内部任意电路层的连接但未导通至外层。这个制程无法使用黏合后钻孔的方式达成,必须要在个别电路层的时候就执行钻孔,先局部黏合内层之后还得先电镀处理,最后才能全部黏合,比原来的「通孔」及「盲孔」更费工夫,所以价钱也最贵。这个制程通常只使用于高密度(HDI)电路板,来增加其他电路层的可使用空间。
埋盲孔
二十盲/埋孔 谈到盲/埋孔,首先从传统多层板说起。标准的多层板的结构,是含内层线路及外层线路,再利用钻孔,以及孔内金属化的制程,来达到各层线路之内部连结功能。但是因为线路密度的增加, 零件的封装方式不断的更新。为了让有限的PCB面积,能放置更多更高性能的零件,除线路宽度愈细外,孔径亦从DIP插孔孔径1 mm缩小为SMD的0.6 mm,更进一步缩小为0.4mm以下。但是仍会占用表面积,因而又有埋孔及盲孔的出现,其定义如下: A. 埋孔(Buried Via) 见图示20.1,内层间的通孔,压合后,无法看到所以不必占用外层之面积 B. 盲孔(Blind Via) 见图示20.1,应用于表面层和一个或多个内层的连通 20.1埋孔设计与制作 埋孔的制作流程较传统多层板复杂,成本亦较高,图20.2显示传统内层与有埋孔之内层制作上的差异,
图20.3则解释八层埋孔板的压合迭板结构. 图20.4则是埋孔暨一般通孔和PAD大小的一般规格
20.2盲孔设计与制作 密度极高,双面SMD设计的板子,会有外层上下,I/O导孔间的彼此干扰,尤其是有VIP(Via-in-pad)设计时更是一个麻烦。盲孔可以解决这个问题。另外无线电通讯的盛行, 线路之设计必达到RF(Radio frequency)的范围, 超过1GHz以上. 盲孔设计可以达到此需求,图20.5是盲孔一般规格。 盲孔板的制作流程有三个不同的方法,如下所述 A.机械式定深钻孔 传统多层板之制程,至压合后,利用钻孔机设定Z轴深度的钻孔,但此法有几个问题 a.每次仅能一片钻产出非常低 b.钻孔机台面水平度要求严格,每个spindle的钻深设定要一致否则很难控制每个孔的深度
通孔焊接新工艺
通孔焊接新工艺 通孔回流焊接技术起源于日本SONY公司,90年代初已开始应用.但它主要应用于SONY自己的产品上,如电视调谐器及CDWalkman.通孔回流焊接技术采用的是点印刷及点回流的方式,所以又称为SpotReflowProcess,即点焊回流工艺.笔者所在的企业采用此工艺.主要用于CD,DVD激光机芯伺服板以及DVD-ROM伺服板的生产.取得了较好的效益. 一.通孔回流焊接生产工艺流程 它的生产工艺流程与SMT流程极其相似,即印刷锡浆à插入组件à回流焊接.无论对于单面混装板还是双面混装板,都是一样的流程,如下所示:SMT机板印刷锡浆:使用机器将锡浆印刷在线路板上。手工插机:人工插件。点焊回流炉:使用热风回流机器焊接。 二.通孔回流焊接工艺的特点 1.对某些如SMT组件多而穿孔组件较少的产品,这种工艺流程可取代波峰焊. 2.与波峰焊相比的优点:(1)焊接质量好,不良比率DPPM可低于20.(2)虚焊,连锡等缺陷少,极少的返修率.(3)PCBLayout的设计无须象波峰焊工艺那样特别考虑.(4)工艺流程简单,设备操作简单.(5)设备占地面积少.因其印刷机及回流炉都较小,故只需较小的面积.(6)无锡渣的问题.(7)机器为全封闭式,干净,生产车间里无异味.(8)设备管理及保养简单. 3.印刷工艺中采用了印刷模板,各焊接点及印刷的锡浆份量可根据需要调节。 4.在回流时,采用特别模板,各焊接点的温度可根据需要调节。 5.与波峰焊相比的缺点.(1)此工艺由于采用了锡浆,焊料的价格成本相对波峰焊的锡条较高。(2)须订制特别的专用模板,价格较贵.而且每个产品需各自的一套印刷模板及回流焊模板.(3)回流炉可能会损坏不耐高温的组件。在选择组件时,特别注意塑胶组件,如电位器等可能由于高温而损坏.根据我们的经验,一般的电解电容,连接器等都无问题.根据我们测试的结果,实际使用回流炉时组件表面最高温度在120-150度. 三.通孔回流焊接工艺设备 1.锡浆印刷机。采用的机器:SS-MD(SONY锡浆印刷机)。需用特别的模板配合印刷机使用. 1.1基本原理。以一定的压力及速度下,用塑胶刮刀将装在模板上的锡浆通过模板上的漏嘴漏印在线路板上相应位置。步骤为:送入线路板-->线路板机械定位--->印刷锡浆--->送出线路板 1.2锡浆印刷示意图:刮刀:采用赛钢材料.无特别的要求.刮刀与模板之间间距为0.1-0.3mm,角度为9度.模板:厚度为3mm,模板主要由铝板及许多漏嘴组成.漏嘴:漏嘴的作用是锡浆通过它漏到线路板上.漏嘴的数量与组件脚的数量一样,漏嘴的位置与组件脚的位置一样,以保证锡浆正好漏在需要焊接的组件位置.漏嘴下端与PCB之间间距为0.3mm,目的是保证锡浆可以容易的漏印在PCB上.漏嘴的尺寸可以选择,以满足不同焊锡量的要求.印刷速度:可调节,印刷速度的快慢对印在PCB 上锡浆的份量有较大的影响. 1.3工艺窗口:印刷速度:在机器设置完成后,只有印刷速度可通过电子调节.要达到好的印刷品质,必须具备以下几点:1.漏嘴的大小合适,太大引起锡浆过多而短路;太小引起锡浆过少而少锡. 2.模板平面度好,无变形. 3.各参数设置正确(机械设置):(1)漏嘴下端与PCB之间