轻量化设计

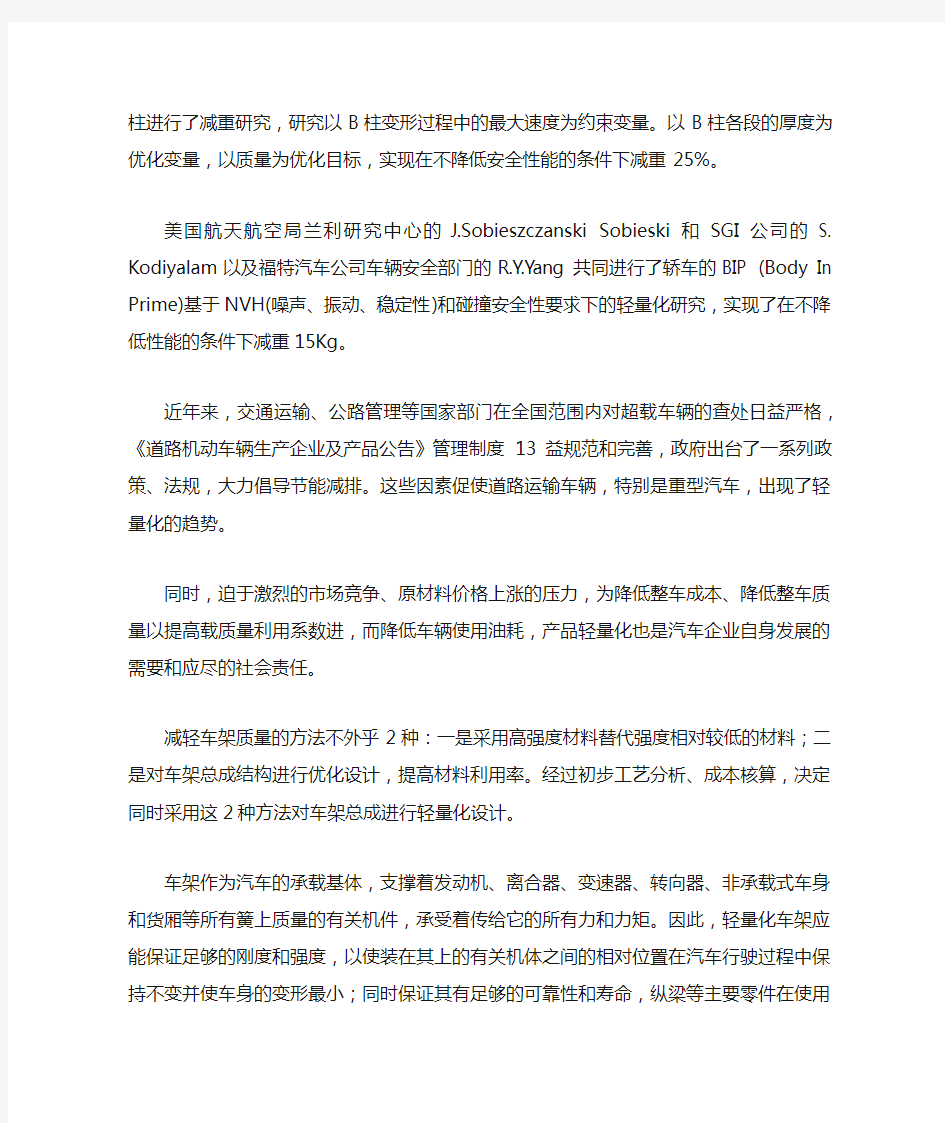
受到能源和环境保护的压力,世界汽车工业很早就开始了轻量化的研究虽然应用轻金属。现代复合材料是现代车辆轻量化研究的热点之一但是这些新材料应用在主要承载部件上的成本较高。因此在短时间内很难普及另一方面,车辆的传统材料钢材,由于其强度高成本低、工艺成熟,并且是最适于回收循环利用的材料。因此利用钢材实现轻量化的可能性备受关注。
1994年,国际钢铁协会成立了由来自全世界18个国家的35个钢铁生产企业组成的ULSAB项目组。其目的是在保持性能和不提高成本的同时,有效降低钢制车身的质量。ULSAB项目于1998年5月完成,其成果是显著的ULSAB试制的车身总质量比对比车的平均值降低25% ,同时扭转刚度提高80% ,弯曲刚度提高52% ,一阶模态频率提高58%,满足碰撞安全性要求,同时成本比对比车身造价降低15%。
从1997年5月启动的ULSAC、ULSAS和1999年1月启动的ULSAB_A VC 为ULSAB的后续项目也在轻量化研究上取得很大成绩。
除了以上提到的国际上著名的四个轻量化项目外,全世界范围内对基于结构优化的轻量化技术也进行了大量的研究。韩国汉阳大学J.K.Shin、K.H.Lee、S.I.Song和G.J.Park应用ULSAB的设计理念和组合钢板的工艺,对轿车前车门内板进行了结构优化,成功地使前车门内板的质量减重8.72%。此技术己在韩国一家汽车企业中得到应用。
通用汽车公司的R.R.MAYER 密西根大学的N.KIKUCHI和R.A.SCOTT应用拓扑优化技术以碰撞过程中最大吸收能量为目标对零件进行优化设计,此技术已应用到一款轿车的后围结构上。
瑞典Linkoping University的P.O.Marklund和L.Nilsson从碰撞安全性角度对轿车B柱进行了减重研究,研究以B柱变形过程中的最大速度为约束变量。以B柱各段的厚度为优化变量,以质量为优化目标,实现在不降低安全性能的条件下减重25%。
美国航天航空局兰利研究中心的J.Sobieszczanski Sobieski和SGI公司的S. Kodiyalam以及福特汽车公司车辆安全部门的R.Y.Yang共同进行了轿车的BIP (Body In Prime)基于NVH(噪声、振动、稳定性)和碰撞安全性要求下的轻量化研究,实现了在不降低性能的条件下减重15Kg。
近年来,交通运输、公路管理等国家部门在全国范围内对超载车辆的
查处日益严格,《道路机动车辆生产企业及产品公告》管理制度13益规范和完善,政府出台了一系列政策、法规,大力倡导节能减排。这些因素促使道路运输车辆,特别是重型汽车,出现了轻量化的趋势。同时,迫于激烈的市场竞争、原材料价格上涨的压力,为降低整车成本、降低整车质量以提高载质量利用系数进,而降低车辆使用油耗,产品轻量化也是汽车企业自身发展的需要和应尽的社会责任。
减轻车架质量的方法不外乎2种:一是采用高强度材料替代强度相对较低的材料;二是对车架总成结构进行优化设计,提高材料利用率。经过初步工艺分析、成本核算,决定同时采用这2种方法对车架总成进行轻量化设计。
车架作为汽车的承载基体,支撑着发动机、离合器、变速器、转向器、非承载式车身和货厢等所有簧上质量的有关机件,承受着传给它的所有力和力矩。因此,轻量化车架应能保证足够的刚度和强度,以使装在其上的有关机体之间的相对位置在汽车行驶过程中保持不变并使车身的变形最小;同时保证其有足够的可靠性和寿命,纵梁等主要零件在使用期内不应有严重变形和开裂[1]。
为缩短计算时间、降低计算难度,用于有限元分析的车架数学模型、各零部件的约束以及负荷,都已经过数学简化。这就注定了有限元分析与实际情况或多或少存在差异。为采集真实试验数据以验证有限元
分析的准确性,有必要进行车架台架试验。而且,车架作为重型汽车的基础构件,与大量其他部件有装配关系,一旦车架结构改动,很可能牵一发而动全身。所以,稳妥起见,也有必要进行车架台架试验。
为减轻节能车车架质量,获得良好的燃油经济性
既然车架台架试验是为了验证有限元分析,那么台架试验就应该按照有限元分析的方法(即弯曲、扭转2种工况)进行。
台架试验的主要内容包括各工况的应力测量、弯曲工况疲劳试验、扭转工况疲劳试验,试验严格按欧洲标准进行。
为了得到尽可能符合实际需要的设计,必须选择足够多的状态变量。但是为了加快优化进程,必须消除不必要或冗余的状态变量。太多的设计变量增大了收敛到局部最小而非全局最小的概率,必须尽量减少设计变量。采用变量关联的方法,将车架结构上互相有联系的非独立尺寸按照比例关系确定。将设计参数分为4类:梁的厚度、梁的截面宽度、梁的截面高度和布置尺寸。
随着汽车轻量化技术日益受到重视,对高强钢、铝合金等轻量化材料的应用、液压成型等先进制造工艺的工程化、新型轻量化结构等方面的探讨,将成为汽车行业研究人员关注的热点。而本文给出的概念模
型拓扑优化分析实例,进一步说明拓扑优化技术在寻找新型轻量化结构方面,将起到举足轻重的作用。
车辆轻量化是减少原材料的消耗、降低车辆的生产成本、减少排放的最有效措施之一。对于特种重型专用车,车架自重和其所占整车重量比例均较大,因此减轻车架自重对车辆轻量化研究具有重要的意义。减轻车架自重一般有两种途径:一是从新材料人手,采用轻金属或现代复合材料”3等低密度材料制作车架,以减轻结构重量;二是从优化设计人手,对现有钢结构车架进行结构优化设计,在保证承载能力和可靠性的前提下减轻其质量。前者轻量化效果明显,减重幅度比较大,但具有研发成本高,工艺复杂等困难;后者成本低容易实现,如果方案得当也能得到良好的轻量化效果
专用车通常采用边梁式车架结构,影响车架重量的主要因素为结构参数,如车架的几何尺寸和板壳厚度。如果以结构参数
为设计变量,以车架结构重量
为优化目标,则车架轻量化结构优化设计数学模型一般可表示为:
中,gi (X)为不等式约束函数,hj (x)为等式约束函数,m为不等式约束个数,l为等式约束个数。约束条件可以是强度约束、刚度约束、动态特性约束以及几何约束等。
考虑到纵粱在车架质量中占有较大的比例,因此选择纵梁作为优化的具体对象。等截面纵粱的腹板和上下翼板厚度沿长度方向不变。优化方案jiang纵梁土翼板和腹板分别划分为前、中、后三段;将下翼板分为有加强板和无加强板两段;加强腹板整体作为一部分。取各段各板的厚度为变量,一共可得到9个优化设计变量。优化设计变量初始值以及优
虽然优化结果使得纵粱各段钢板厚度不相等,会增加制造困难,但采取工艺改进实际上是可以实现的,因此本文的方法和结果对重型车架从理论上和实际上均有良好的参考价值。
如果将纵横粱所有构件的厚度均作为优化设计变量,优化效果可能会更好。但大量试算表明,设计变量太多,计算规模太大,所需计算机资源要求较高,导致在有效的时间内难以完成实际计算。
建筑结构设计
65 建筑结构设计分析 张亚超 魏强 西安骊山建筑规划设计院 摘 要:本文主要介绍建筑结构的基本内容,然后针对目前建筑结构设计当中墨守成规的现象,提倡采用概念设 计思想来促进结构工程师的创造性,推动结构设计的发展,对建筑结构设计常见问题做了分析,为以后的设计提供参考。 关键词:建筑;结构设计;方法;概念设计 而建筑结构设计优化方法的应用则既能满足建筑美观、造型优美的要求,又能使房屋结构安全、经济、合理,成为实质意义上的“经济适用”房。 1 结构设计的基本内容 1.1 屋顶(面)结构图 当建筑是坡屋面时,结构的处理方式有两种:梁板式及折板式。梁板式适用于建筑平面不规整,板跨度较大,屋面坡度及屋脊线转折复杂的坡屋面。反之,则适用折板式。两种形式的板均为偏心受拉构件。板配筋时应有部分或全部的板负筋拉通以抵抗拉力。板厚基于构造需要一般不宜小于 120 厚。此外梁板的折角处钢筋的布置应有大样示意图。至于坡屋面板的平面画法, 建议采用剖面示意图加大样详图的表示方法(实践证明此方法便于施工人员正确理解图纸)。1.2 结构平面图 在绘制结构平面布置图前有个问题需要说明一下, 就是要不要输入结构软件进行建模的问题。当建筑地处抗震设防烈度为 6 度区时,根据建筑抗震设计规范,是可以不用进行截面抗震验算的但应符合有关的抗震措施要求。那么对于砌体结构来讲如果时间不是很充足的话应该可以不用在软件中建模的,直接设计即可,但要注意受压和局部受压的问题。必要时进行人工复核。对于局部受压的防御措施是要按规定对梁下设梁垫以及设置构造柱等措施。如果时间不是很紧张的话建议还是输入建模较好, 有一个便利就是可以利用软件来进行荷载导算。另外,当建筑地处抗震设防烈度为 7 度及以上时我的观点是必须要输入软件建模计算的, 绘制结构平面图时如果没有建模的话就可以直接在建筑的条件图上来绘制结构图了, 这一步必不可少的是删除建筑图中对结构来讲没有用的部分,简单快捷的方法是利用软件的图层功能,直接冻结相关的层。然后再建立新的结构图层:圈梁层、构造柱层、梁层、文字层、板钢筋层等等。这样做的目的是提高绘图效率, 方便在不同结构平面图间的拷贝移动和删除。1.3 楼梯 楼梯梯板要注意挠度的控制, 梯梁要注意的是梁下净高要满足建筑的要求, 梯梁的位置尽量使上下楼层的位置统一。局部不合适处可以采用折板楼梯。折板楼梯钢筋在内折角处要断开分别锚固防止局部的应力集中。阁楼层处的楼梯由于有 分户墙的存在要设置抬墙梁。注意梁下的净空要求, 并要注意梯板宽度的问题。首段梯板的基础应注意基础的沉降问题, 必要时应设梯梁。1.4 基础 基础要注意混凝土的标号选择应符合结构耐久性的要求。基础的配筋应满足最小配筋率的要求(施工图审查中心重点审查部位)。条基交接部位的钢筋设置应有详图或选用标准图。条基交叉处的基底面积不可重复利用,应注意调整基础宽度。局部墙体中有局部的较大荷载时也要调整基础的宽度(因软件计算的是墙下的平均轴力)。基础图中的构造柱,当定位不明确时应给予准确定位。 2 概念设计 所谓的概念设计一般指不经数值计算, 尤其在一些难以做出精确理性分析或在规范中难以规定的问题中, 依据整体结构体系与分体系之间的力学关系、结构破坏机理、震害、试验现象和工程经验所获得的基本设计原则和设计思想, 从整体的角度来确定建筑结构的总体布置和抗震细部措施的宏观控制。运用概念性近似估算方法, 可以在建筑设计的方案阶段迅速、有效地对结构体系进行构思、比较与选择,易于手算。所得方案往往概念清晰、定性正确,避免后期设计阶段一些不必要的繁琐运算,具有较好的经济可靠性能,同时,也是判断计算机内力分析输出数据可靠与否的主要依据。 概念设计的重要性:概念设计是展现先进设计思想的关键,一个结构工程师的主要任务就是在特定的建筑空间中用整体的概念来完成结构总体方案的设计,并能有意识地处理构件与结构、结构与结构的关系。一般认为,概念设计做得好的结构工程师,随着他的不懈追求,其结构概念将随他的年龄与实践的增长而越来越丰富,设计成果也越来越创新、完善。遗憾的是,随着社会分工的细化,大部分结构工程师只会依赖规范、设计手册、计算机程序做习惯性传统设计,缺乏创新,更不愿(不敢)创新,有的甚至拒绝对新技术、新工艺的采纳(害怕承担创新的责任)。大部分工程师在一体化计算机结构程序设计全面应用的今天,对计算机结果的明显不合理、甚至错误不能及时发现。 3 建筑结构设计常见问题 (下转第67页)
全铝车身结构设计
汽车轻量化解决方案—全铝车身结构设计 摘要:解决汽车节能环保的问题,有提高传统燃油发动机的能效、发展新能汽车、应用轻量化技术三个方向。比较以上三种技术路线,在当今发动机技术提升难度日益加大、动力电池效率不高的背景下,不论对传统燃油汽车,还是新能源汽车,汽车轻量化技术都是一项共性的基础技术。大力发展并推进汽车轻量化技术,成为节能、减排的主导之一。而实现汽车轻量化技术又有三个技术途径:一种“轻量化材料”要通过一种“轻量化工艺”来实现一种“轻量化结构”。 关键词:汽车轻量化全铝车身型材截面优化 Stiffness Mass Efficient 由于世界能源的随时枯竭与环境的日益恶化,世界各行各业都积极行动起来,根据政府的优惠政策与民众的强烈要求,在节能、环保方面进行了高投入研发其高效节能、积极环保的产品。汽车产业首当其冲,其汽车零部件的制造,迁联到能源、钢材、铝材、合金、塑料、橡胶、玻璃、化工、机械、电器、信息等各行各业,对汽车节能环保的要求,就是对其它相关行业的要求。对汽车进行轻量化结构的研究,要联系相关行业的专业知识,进行综合性的研究。 一、汽车轻量化的目的 就汽车产业而言,根据汽车产品的特点,降低油耗或提高燃油效率、减少或清洁排放对环境的污染,是节能环保研发的主要目的。从全球汽车产业来看,解决汽车节能环保问题主要采用以下三种方式:
一是大力发展先进发动机技术,通过对传统发动机的改良和一系列汽车电子技术的应用,来提高燃烧效率,改善燃油经济性。 二是大力发展新能源汽车,通过研发先进新型发动机技术和推广使用气体燃料、生物质燃料、煤基燃料、高效电池等动力替代传统能源来减少汽车燃油消耗和对石油资源的依赖。 三是大力发展汽车轻量化技术,在保障汽车安全性和其他基本性能的前提下,通过减轻汽车自身重量降低能耗来实现节能减排的目的。 比较以上三种技术路线,在当今发动机技术提升难度日益加大、动力电池效率不高的背景下,不论对传统燃油汽车,还是新能源汽车,汽车轻量化技术都是一项共性的基础技术。大力发展并推进汽车轻量化技术,成为节能、减排的主导之一。 汽车的轻量化,英文名:Lightweight of Automobile,涵义是“在保证汽车的强度和安全性能的前提下,尽可能地降低汽车的整备质量,从而提高汽车的动力性,减少燃料消耗,降低排气污染。” 世界节能与环境协会的研究报告指出:汽车自重每减少10%, 燃油消耗可降低6%—8%,排放降低5%—6%。而燃油消耗每减少1升,CO2排放量减少2.45kg。燃油消耗量减少不仅有利于节约能源,也可有效减少污染物排放。当前,由于节能和环保的需要,汽车的轻量化已经成为世界汽车发展的潮流。 伴随着技术进步,制造汽车车身的材料已经不仅仅是钢铁了,越来越多的新材料被应用到车身的制作中。其中包括:玻璃钢、铝合金、
汽车轻量化技术及实现途径-汽车设计课程论文
本科课程论文 题目汽车轻量化技术及实现途径课程汽车设计 专业机械制造及其自动化 班级2012级1班 学号 姓名 联系方式 2015年6月26日
目录 摘要: (3) 1.前言 (3) 2.轻量化技术及其发展现状 (3) 3.实现汽车轻量化的主要途径 (4) 3.1合理的结构设计 (4) 3.2使用新型材料 (5) 3.2.1有色合金材料 (6) 3.2.2高强度钢 (7) 3.2.3塑料和复合材料 (7) 3.2.4其他轻量化材料 (8) 4.汽车轻量化发展面临的问题 (8) 5.结论 (9) 参考文献 (9)
汽车轻量化设计技术 *** 西南大学工程技术学院,重庆 400716 摘要:本文简要介绍了目前汽车轻量化技术的发展状况,包括轻量化设计概况、各种轻量化材料的性能及运用,阐述了汽车轻量化的实施途径。 关键词:汽车轻量化发展 1.前言 有关研究数据表明, 若汽车整车质量降低10%, 燃油效率可提高6% ~ 8% ; 若滚动阻力减少10%, 燃油效率可提高3% ; 若车桥、变速器等机构的传动效率提高10% , 燃油效率可提高7%。由此可见, 伴随轻量化而来的突出优点就是油耗显著降低。汽车车身约占汽车总质量的30% , 空载情况下, 约70% 的油耗用在车身质量上, 因此车身的轻量化对减轻汽车自重, 提高整车燃料经济性至关重要。同时, 轻量化还将在一定程度上带来车辆操控稳定性和一定意义上碰撞安全性的提升。车辆行驶时颠簸会因底盘重量减轻而减轻,整个车身会更加稳定; 轻量化材料对冲撞能量的吸收, 又可以有效提高碰撞安全性。因此汽车轻量化已成为汽车产业发展中的一项关键性研究课题。 2.轻量化技术及其发展现状 汽车轻量化的技术内涵是:采用现代设计方法和有效手段对汽车产品进行优化设计,或使用新材料在确保汽车综合性能指标的前提下,尽可能降低汽车产品自身重量,以达到减重、降耗、环保、安全的综合指标。 然而,汽车轻量化绝非是简单地将其小型化。首先应保持汽车原有的性能不受影响,既要有目标地减轻汽车自身的重量,又要保证汽车行驶的安全性、耐撞性、抗振性及舒适性,同时汽车本身的造价不被提高,以免给客户造成经济上的压力。 汽车轻量化技术包括汽车结构的合理设计和轻量化材料的使用两大方面。一方面汽车轻量化与材料密切相关;另一方面,优化汽车结构设计也是实现汽车轻量化的有效途
汽车车身轻量化结构设计
汽车车身轻量化结构设计 2011届分类号: 单位代码 :10452 本科专业职业生涯设计 题目汽车车身轻量化结构设计 姓名 学号 年级 2007级 专业车辆工程 系 (院) 工学院 指导教师 2011年4月24日星期日 目录 人生需要梦想 ............................................ 2 ,一, 引言 ............................................. 4 ,二, 自我分 析 ......................................... 4 ,三, 环境条件分 析 ..................................... 4 3.1 家庭条件分 析 (4)
3.2 社会环境的分析 ...................................... 4摘 要 (5) ABSTRACT (5) 汽车车身轻量化概述 ................................ 6 第1章 1.1 汽车轻量化的意义 .................................... 6 1.2 汽车轻量化的发展 .................................... 6 第2章汽车车身轻量化设计的材料选择 . (7) 2.1 高强度钢是占主导地位的轻量化材料 (7) 2.2铝合金是最有希望取代钢铁材料的轻量化材料 (11) 2.3塑料和复合材料 ...................................... 12 第3章汽车轻量化设计的分析 .............................. 13 3.1轻量化设计的分析原则 ................................ 13 3.2减重:轻量化评价参 量 ................................ 14 3.3性能:满足各类碰撞法 规 .............................. 15 3.4轻量化与成本的关 系 .................................. 16 第4章运用CAE技术进行某微型客车车架结构的分析与优化设计 16 4.1 CAE技术 ............................................ 16 4.2动力学分析 .......................................... 17 4.3静力分 析 ............................................ 20 4.4优化设 计 ............................................ 23 第五章结束 语 .......................................... 24 参考文 献 ............................................... 25 谢 辞 (26) 2
10kv及以下客户供用工程典型设计方案_new
10KV及以下客户 供用电工程典型设计方案 省电力公司 第一分册配电房工程 总设计说明 1 概述 配电房工程典型设计适用于10/0.4kV配电房新建工程(建筑物新建或箱式变电站),变压器为油浸式变压器,室内变压器容量为100~1600kV A,箱式变压器容量为100~800kV A。 配电房工程分册共分五章。根据配电变压器(以下简称变压器)容量的大小或10kV接线方式的不同分为四章:第一章适用于变压器容量范围100~250kV A,根据变压器安装地点的不同分为变压器室外安装、箱式变电站、变压器室内安装三节;第二章适用于变压器容量范围315~400kV A,根据变压器安装地点的不同分为变压器室外安装、箱式变电站、变压器室内安装三节;第三章适用于变压器容量范围500~1600kV A,10kV侧单电源,根据变压器安装地点及数量的不同
分为箱式变电站(单台变压器)、箱式变电站(两台变压器)、变压器室内安装(单台变压器)、变压器室内安装(两台及以上变压器)四节;第四章适用于变压器容量范围500~1600kV A,10kV侧双电源,根据10kV侧结线方式的不同分为10kV侧单母线接线、10kV侧单母线分段接线两节。第五章为前四章的公共部分,共分三节,分别归纳了设备选择、断面图及二次接线图。 10kV侧标注所有设备的型号及技术参数,0.4kV侧对总路断路器及无功补偿的容量、型号及技术参数进行标注(根据不同的变压器容量,对受变压器容量影响较大的设备技术参数在第五章设备选择中单独列表标注);对出线仅标注设备型号、示意出线回路数,出线设备技术参数应根据工程实际情况选择,出线回路数也可根据工程实际情况酌情增减,图纸标注的设备型号仅作参考。 2 设计范围 从10kV侧电缆进线的电缆头、架空进线的变压器安装引下线起,至0.4kV出线配电屏电缆头止这一范围内的电气安装设计(不含电缆头)。 3 设计目的和原则 3.1 采用标准化、规范化的典型设计,规范市场、提高安装质量,从而保证供电可靠性。 3.2 箱式变电站工厂化。
浅谈汽车车身结构轻量化
浅谈汽车车身结构轻量化 【摘要】本文综述了汽车轻量化技术应用的必要性、汽车轻量化的效果和意义、汽车轻量化的途径和技术,以及与节能环保和安全的关系,强调了车身轻量化设计是实现汽车轻量化的主要途径之一。汽车轻量化是汽车产业的发展方向之一,也是一个汽车厂商和国家技术先进程度的重要标志。 【关键词】汽车车身;车身结构;轻量化 0 引言 随着国民经济的蓬勃发展,汽车已一跃成为当前极为重要的交通运输工具。从全世界范围来看,目前还找不出一个无汽车的现代化社会的先例。因此,汽车工业在带动其他各行各业的发展中,已日益显示出其作为重要支柱产业的作用。 在扩大汽车的服务领域和满足各方面多样化要求的前提下,作为汽车上三大总成之一的车身,已后来居上越来越处于主导地位。据统计,客车、轿车和多数专用汽车车身的质量约占整车自身质量的40%~60%;货车车身质量约占整车自身质量的16%~30%;其各车型的车身占整车制造成本的百分比甚至还略超过以上给出的上限值。因此,仅从这个意义上来衡量汽车车身,其经济效益也远远高于其他两大总成。 如果从节能、节材等几方面来考虑,则其潜力更大。此外,纵观国内、外车身制造和装配等工艺流程,不难发现,尽管随着科学技术的进步,吸取了大量的尖端技术,机械化和自动化程度很高,但是仍有两化无能为力而又必须由手工操作来完成的部分(特别是车身的内、外装饰和附件的装配)。 1 汽车轻量化技术应用的必要性 汽车轻量化对于节约能源、减少废气排放十分重要。而在驾驶方面,汽车轻量化后其加速性能也将得到提高,而在碰撞时由于惯性小,制动距离也将减少,便于主动安全控制。 纵观世界汽车工业沿革,可以看出,现代汽车是沿着“底盘”→“发动机”→“车身”逐步发展完善过来的。这个发展过程在很大程度上取决于当时的科学技术水平和物质生活条件。由于汽车与人们的日常生活息息相关,为了适应各种不同的目的和用途乃至车身的更新换代等,其关键在于车身。 国内外汽车生产的实践一再表明:整车生产能力的发展取决于车身的生产能力;汽车的更新换代在很大程度上也决定于车身;在基本车型达到饱和的情况下,只有依赖车身改型或改装才能打开销路。凡此等等都足以说明,汽车工业发展到今天成为重要的支柱产业,而重中之重则非车身莫属。 2 汽车轻量化的效果 汽车轻量化的主要目的是降低油耗。如图1所示,车辆行驶的燃油消耗量与车辆质量的关系。一般情况下,对于1000kg自重的轿车,车辆质量减轻8%,可降低油耗约10%以上。 图1 车辆行驶油耗与质量的关系 另外,世界铝业协会的报告指出:整车质量每减少100KG,其百公里油耗可节降低0.4-1.0L,每公里二氧化碳排放也将相应减少7.5克到12.5克。而车身质量占整车质量的1/3,空载情况下,约70%的油耗用在车身质量上。这意味着:只要通过科学的方式,将车身轻量化后,就可以有效减少燃油消耗。 3 车身轻量化的意义
汽车结构的轻量化设计方法综述李传博
Value Engineering 0引言 随着快速增长的汽车保有量,一方面,汽车作为方便、快捷的交通工具改善了人们的生活和工作方式;另一方面,却加剧了能源消耗,带来尾气、噪声等环境污染以及交通安全危害。汽车产业面临着节能、安全和环保的巨大压力。 针对上述问题,解决的重要途径是在对动力系统进行改进的同时积极开发和寻找替代能源及相关技术。 但受技术难度、开发周期和市场份额等问题制约,仅靠这一途径很难满足国家和市场的要求;另一个重要途径是整车轻量化。有关研究数据表明,若车桥、变速器等机构的传动效率提高10%,燃油效率可提高7%;若汽车整车质量降低10%,燃油效率可提高6% ~8%[1,2] 。车身占整个汽车制造成本60%,占汽车总重量的30~40%,空载情况下,70%的油耗将用于车身质量上[3]。图1展现了日本统计的乘用车自重与油耗之间关系。显而易见,当车辆的自重从1500kg 下降到1000kg 时,每升燃油平均行驶的里程由10km 上升到17.5km ,即每减重100kg ,每升油可多行驶1.5km ,也就是说在此区间内,燃油的经济性提高了5.7%-10%。 1车身结构轻量化设计的研究内容和方法 车身结构轻量化设计研究,主要从三个方面进行:一是结构优 化或创新,改进车身结构,使零部件薄壁化、中空化、小型化和复合化[6],采用CAD/CAE/CAM/CAPP 数字化设计和制造技术提高零部件 开发质量;二是采用先进的车身制造工艺,如激光拼焊、 中高温成形、滚压或液压成形等;三是采用轻质高强度材料[7] 。宝马汽车轻量化设计方案就是综合运用各种技术在保证汽车性能前提下,最大限度的减轻汽车重量,如图2所示。 2轻量化材料在汽车结构轻量化中的应用 2.1高强度钢板高强度钢板材料在强度、塑性、抗冲击能力、回收使用及低成本方面具有综合优势。高强度钢板的明显优点是在车身结构设计上采用更薄的钢板,并获得相同的强度,在钢板厚度分别减小0.05、0.10和0.15mm 时可以使车身分别减重6%、12%和 18%[8] 。因此,在高强度钢板比传统钢在价钱上更贵的情况下,减轻了重量可使得两者实际成本相近。 未来十年,高强度钢在汽车中的应用会大幅度增加。 2.2铝合金比强度和比刚度十分优良的铝金属基复合材料研究开发的成功,是汽车轻量化的进一步发展的一个很好途径。据统计2010年每辆轿车的平均铝使用量与1998年相比增长53%,上升到130kg 。铝材的强度和刚度虽然是比钢材小很多,通过框架结构设计及采用更厚的板材也可以补偿这个不足,车身空间框架结构质量在使用铝材后下降47%,与此同时采用改进的断面形式将使车身 汽车结构的轻量化设计方法综述 The Review of Design Methods for Lightweight of Automobile Structure 李传博①Li Chuanbo ;谢然②Xie Ran ;郭琳②Guo Lin (①商洛学院城乡发展与管理工程系,商洛726000;②广州汽车集团股份有限公司汽车工程研究院,广州510640) (①Urban and Rural Development and Project Management Department of Shangluo University , Shangluo 726000,China ;②Guangzhou Automobile Group Co.,Ltd.GAC Automotive Engineering Institute ,Guangzhou 510640,China ) 摘要:汽车结构轻量化对降低汽车排放和油耗具有重要意义。文章介绍了汽车结构轻量化的几个代表性研究项目;对高强度钢板、铝镁合金 及塑料等轻质高强度材料在车身结构轻量化中的应用进行了阐述;围绕新材料的先进成形工艺,如激光拼焊板、液压和气压成形,热冲压工艺等 成形工艺,以及自冲铆接等先进连接工艺进行了分析;同时还介绍了有关的汽车结构优化和创新设计方法。最后对汽车结构轻量化设计方法的发展动向进行了展望。 Abstract:Lightweight of automobile structure is important for vehicle emissions reduction and fuel consumption.It can be realized by using lightweight-high-strength materials,relative advanced forming process for automobile structure parts,connection technology and structure optimization or other innovation methods.This article describes a few representative research projects on automotive structural lightweight;elaborates the use of high strength steel,aluminum-magnesium alloy,plastics and other lightweight-high-strength materials in the lightweight of body structure;analyzes advanced forming process for new materials,such as tailored blanks,hydraulic and pneumatic forming,hot stamping,and advanced connectivity technology of the self-pierce riveting.It also presents the relative methods for structural optimization and innovative design.Finally,it prospects the development trend of design method for lightweight of automobile structure. 关键词:汽车轻量化;高强度钢板;激光拼焊板;自冲铆接Key words:lightweight of automobile ;high strength steel ;laser tailor-welded board ;self-piercing riveting 中图分类号:U462 文献标识码:A 文章编号:1006-4311(2012)19-0029-03 —————————————————————— —作者简介:李传博(1981-),男,陕西商洛人,硕士,讲师,研究方向为车辆检 测与诊断技术 。 ·29·
汽车轻量化低碳设计
汽车轻量化低碳设计 轻量化不仅意味着车架和钢板重量的减轻,也包括了发动机、传统系统、驱动系统以及油箱等每一个可能降低重量的部分。轻量化到底能带来多大效果,根据奥迪方面的研究,现在,一辆采用轻量化科技的奥迪A5,比普通A5可减轻重量350公斤,意味着每百公里可以降低油耗约1升。足见汽车轻量化设计是不折不扣的“低碳”经济。 “低碳”经济如今成为全球最热话题,随着上海世博会出行普通采用纯电动、混合动力、燃料电池等新能源汽车以及新能源汽车补贴政策的实施,汽车行业也燃起了一股“低碳”经济热潮。不过大家关注汽车行业低碳经济的时候,往往首先想到的就是新能源汽车,事实上,只要有利于减少排放和污染的技术都可以称之为低碳技术。今天我们就来讲讲汽车行业的另类“低碳”经济——全球汽车轻量化设计风潮。 汽车轻量化是不折不扣的“低碳”经济 汽车轻量化,并非没有技术含量的简单降低汽车重量,事实上诸如碳纤维代表着当今最先进的汽车技术。汽车轻量化是在保证汽车强度和安全性能的前提下,尽可能地降低汽车的整备质量,从而提高汽车的动力利用率,减少燃料消耗,降低排气污染。汽车轻量化对于节约能源、减少废气排放十分重要。权威研究显示,若汽车整车重量降低10%,燃油效率可提高6%—8%;汽车整备质量每减少100公斤,百公里油耗可降低0.3—0.6升;汽车重量降低1%,油耗可降低0.7%。而在驾驶方面,汽车轻量化后其加速性能也将得到提高,而在碰撞时由于惯性小,制动距离也将减少。此外,车辆每减轻100公斤,二氧化碳排放可减少约5克/公里。可见汽车轻量化的节能环保效益觉不亚于汽车发动机技术节油技术。 当前,由于环保和节能的需要,汽车轻量化已成为世界汽车发展的潮流。实施汽车轻量化的主要材料有碳纤维、铝合金、镁合金、钛合金、工程塑料、复合材料和高强度钢等,主要用来改造和替代车身材料。汽车轻量化大致可以分为三类:车身轻量化、发动机轻量化、底盘轻量化。其目的均是在保证性能的前提下通过使用更轻材料降低车重,从而实现节能环保功能。将车身轻量化运用到极致的当属大量使用碳纤维的F1赛车,不过由于追求速度和激情,燃油消耗依然严重再次不做介绍,但可以肯定的是如果F1赛车不采取轻量化车身,其燃油消耗将更为惊人。 宝马、奥迪引领发动机和底盘轻量化 发动机和底盘的轻量化,一般都是采用铝合金或镁铝合金结构代替笨重的铸铁发动机部件和普通钢制悬架部件,从而实行更强强度和更轻的质量。以这一代宝马530的前悬挂和直列6缸引擎为例,铝合金材料的大量运用,有效的控制了二者的自重,从而帮助设计师实现了降低12%单位油耗的既定目标。
轻量化设计
受到能源和环境保护的压力,世界汽车工业很早就开始了轻量化的研究虽然应用轻金属。现代复合材料是现代车辆轻量化研究的热点之一但是这些新材料应用在主要承载部件上的成本较高。因此在短时间内很难普及另一方面,车辆的传统材料钢材,由于其强度高成本低、工艺成熟,并且是最适于回收循环利用的材料。因此利用钢材实现轻量化的可能性备受关注。 1994年,国际钢铁协会成立了由来自全世界18个国家的35个钢铁生产企业组成的ULSAB项目组。其目的是在保持性能和不提高成本的同时,有效降低钢制车身的质量。ULSAB项目于1998年5月完成,其成果是显著的ULSAB试制的车身总质量比对比车的平均值降低25% ,同时扭转刚度提高80% ,弯曲刚度提高52% ,一阶模态频率提高58%,满足碰撞安全性要求,同时成本比对比车身造价降低15%。 从1997年5月启动的ULSAC、ULSAS和1999年1月启动的ULSAB_A VC 为ULSAB的后续项目也在轻量化研究上取得很大成绩。 除了以上提到的国际上著名的四个轻量化项目外,全世界范围内对基于结构优化的轻量化技术也进行了大量的研究。韩国汉阳大学J.K.Shin、K.H.Lee、S.I.Song和G.J.Park应用ULSAB的设计理念和组合钢板的工艺,对轿车前车门内板进行了结构优化,成功地使前车门内板的质量减重8.72%。此技术己在韩国一家汽车企业中得到应用。 通用汽车公司的R.R.MAYER 密西根大学的N.KIKUCHI和R.A.SCOTT应用拓扑优化技术以碰撞过程中最大吸收能量为目标对零件进行优化设计,此技术已应用到一款轿车的后围结构上。 瑞典Linkoping University的P.O.Marklund和L.Nilsson从碰撞安全性角度对轿车B柱进行了减重研究,研究以B柱变形过程中的最大速度为约束变量。以B柱各段的厚度为优化变量,以质量为优化目标,实现在不降低安全性能的条件下减重25%。 美国航天航空局兰利研究中心的J.Sobieszczanski Sobieski和SGI公司的S. Kodiyalam以及福特汽车公司车辆安全部门的R.Y.Yang共同进行了轿车的BIP (Body In Prime)基于NVH(噪声、振动、稳定性)和碰撞安全性要求下的轻量化研究,实现了在不降低性能的条件下减重15Kg。 近年来,交通运输、公路管理等国家部门在全国范围内对超载车辆的
汽车轻量化论文
摘要:汽车轻量化对于降低汽车燃油消耗和减少排放污染起着举足轻重的作用,采用轻质材料是实现汽车轻量化的重要途径。文章详细分析了轻量化技术 在现在汽车种的应用,包括铝合金镁合金钛合金3种轻合金的特点。轻量化 设计技术以及金属成型方法和连接技术,说明了汽车轻量化的意义,对汽车的 轻量化技术发展有一定的指导作用。 关键词:汽车;轻量化;车身 1轻量化技术在汽车上的应用 目前,国内外应用于汽车的请炼化技术主要有:1)轻质材料技术的应用,如铝合金镁合金钛合金高强度钢塑料粉末冶金生态复合材料及陶瓷等的应用越来越多;2)结构优化及计算机辅助设计和分析技术的应用;3)汽车制造中新的成型方法和连接技术的不断应用。 1.1.1基于材料的轻量化技术的应用 1.11高强度钢在汽车上的应用 高强度刚已成为颇具竞争力的汽车轻量化材料,它在抗碰撞性能,加工工艺和成本方面与其他材料相比具有较大的优势。采用高强度钢板,首先能改善汽车的安全和碰撞性能,传统的碳素钢虽然可以吸收碰撞能量,但其缺点是质量大,影响燃油经济性;高强度钢板用于汽车车身,除了能减薄车身部件厚度降低自重之外还可以提高汽车表面件的抗凹陷性及抗破坏能力,在降低燃油消耗率的同时又可以提高汽车的安全性。 国外高强度钢在汽车上的应用以日本最为典型。在日本,车身零件实际应用高强度钢始于20世纪70年代,最早应用于车身外表件,然后应用到内部零件和结构件。目前,日本悬架结构和支撑件的强度已达到800-1000MPa。 抗拉强度410 MPa的高强度钢多用于内部件,即将采用590 MPa高强度钢用于内部件,有望进一步减薄零件厚度。
1.12铝合金在汽车上的应用 铝具有高的导电性和导热性,密度小,塑性好,易成型,易回收利用。 可通过铸锻冲压工艺制造各类汽车零件。自1991年使用高强度铝合金以来,北美汽车上铝的用量已增加2倍,运动多用途车皮卡和微型厢式车上的铝的用量呈3倍增长。 目前,铝合金已经广泛应用于汽车车身底盘零部件以及发动机的某些部件上。现代轿车发动机活塞几乎都采用铸铝合金,这是因为活塞作为主要的往复运动件要靠减重来减小惯性,减轻曲轴配重,提高效率,并需要材料有良好的导热性,较小的热膨胀系数,以及在350度左右有良好的力学性能,而铸铝合金符合这些要求。同时由于活塞连杆采用了铸铝合金件,减轻了质量,从而降低了发动机的振动,降低了噪声,使发动机的油耗下降,这也符合汽车的发展趋势。 近年来,一些新型铝合金材料也开始在汽车上应用,如快速凝固铝合金TiAi金属间化合物泡沫铝材铝复合材料铝基粉末冶金材料和铝拼焊冲压坯材料。 1.13 镁合金在汽车上的应用 镁合金的基本特性如下: 1)质量轻。镁合金比铝合金轻33%,比钢轻77%,为常用结构金属材料中最轻的材料。同时,镁能制造出与铝同样复杂的零件而质量则较后者轻 1/3.镁合金用于车辆,将显著地降低其起动惯性,降低燃油消耗,减少 环境污染。 2)比强度高,刚性强。同等形状下,镁合金制品的刚性为塑料的10倍以上。 如用镁合金代替ABS塑料,则制品的质量可以减少36%,厚度可以降低 64%。
汽车座椅轻量化结构设计与优化
汽车座椅轻量化结构设计与优化 摘要:随着汽车总保有量的不断增加,汽车与能源、环保之间的矛盾己成为制约汽车产业可持续发展的突出问题。面对低碳时代的到来和节能减排的巨大压力,汽车轻量化是解决这一问题最有效、最现实的途径之一。从而推动了新材料新工艺在汽车工业中的应用和发展。其中,尤为引人注目的是铝合金在汽车轻量化中的应用和发展。本文从座椅骨架材质轻量化、结构优化设计及成形工艺分析等方面入手对汽车座椅进行了轻量化设计研究。 关键词:汽车座椅;轻型化;结构设计;铝合金;低压铸造 随着汽车总保有量和新增量的不断增加,汽车耗油量及汽车二氧化碳、有害气体及颗粒的排放量也在快速增加。在能源日益紧缺,环境同益恶化的今天,这种矛盾己成为制约汽车产业可持续发展的突出问题。面对能源危机和低碳环保的巨大压力,解决这一矛盾最有效、最现实的方法之一,也是当今世界汽车工业发展的潮流,就是实现汽车的轻量化。 1.汽车轻量化概念 汽车轻量化(Lightweight of Automobile)就是必须在保证汽车使用性能,如强度、刚度和安全性的前提下,降低汽车的重量,从而提高汽车的动力性能,燃油经济性,并且降低废气污染。汽车轻量化并不只是简单地降低汽车重量,还包含了许多新理论、新材料、新工艺。 根据美国铝协会研究,若汽车整车重量降低10%,其燃油效率可提高6%~8%;汽车整车重量每减少100kg,其百公里油耗可降低O.3~0.6L,二氧化碳排放量可减少约59/km。 总的来说,实现汽车轻量化主要有2种途径:一是利用有限元方法,拓扑优化方法改进汽车整车结构及零部件结构,实现结构件材料分布最优化;二是利用各种轻量化材料,包括高强度钢板材料和轻质材料。 结构轻量化设计就是利用有限元法和现代优化设计方法进行结构分析和结构优化,以减轻汽车车身、各零部件如发动机、承载件件和内饰件的重量。结构优化设计即在保证产品达到某些性能目标(如强度、刚度)并满足一定约束条件的前提下,改变某些设计变量,使结构的重量最轻,这不但节省了材料,也便于运输和安装。优化设计以数学规划为理论基础,将设计问题的物理模型转换成数学模型,运用最优化数学理论,以计算机和商业软件为优化工具,在充分考虑多种约束的前提下满足设计目标的最佳设计方案。有限元法在结构设计中被广泛使用,它可以使任何复杂的工程问题,简化为有限元模型进行分析研究。目前广泛使用的结构优化工具Altair Optistruct,以有限元法为基础,提供拓扑优化、尺寸优化、形貌优化、自由形状优化等多种优化方法,可以对汽车车架结构及各零部件结构进行分析和优化。在有效满足设计功能及外型要求的前提下,先经过概念
家庭分布式光伏典型设计方案
家庭分布式光伏典型设计方案 家庭屋顶一般采用瓦片结构和水泥结构,安装方在推销光伏或者接到用户申请时,要去现场考察,因为并不是每家屋顶都适合安装光伏。 1、选择合适的安装场地 首先要确定屋顶的承载量能不能达到要求,太阳能电站设备对屋顶的承载要求大于30kg/平米,一般近5年建的水泥结构的房屋都可以满足要求,而有10年以上的砖瓦结构的房屋就要仔细考察了;其次要看周边有没有阴影遮挡,即使是很少的阴影也会影响发电量,如热水器,电线杆,高大树木等,公路旁边以及房屋周边工厂有排放灰尘的,组件会脏污,影响发电量;最后要看屋顶朝向和倾斜角度,组件朝南并在最佳倾斜角度时发电量最高,如果朝北则会损失很多发电量。遇到不适合装光伏的要果断拒绝,遇到影响发电量的需要和业主实事求是讲清楚,以免后续有纠份。 2、选择合适的光伏组件 光伏组件有多晶硅,单晶硅,薄膜三种技术路线,各种技术都有优点和缺点,在同等条件下,光伏系统的效率只和组件的标称功率有关,和组件的效率没有直接关系,组件技术成熟,国内一线和二线品牌的组件生产厂家质量都比较可靠,客户需要选择从可靠的渠道去购买。光伏组件有60片电池和72片电池两种,分布式光伏一般规模小,安装难度大,所以推荐用60片电池的组件,尺寸小重量轻安装方便。
按照市场规律,每一年都会有一种功率的组件出货量特别大,业内称为主流组件,组件的效率每一年都在增加,2017年是多晶265W,单晶275W,这种型号性价比最高,也比较容易买到,到2018年预计是多晶270W,单晶280W性价比最高。 3、选择合适的支架 根据屋顶的情况,可以选择铝支架,C型钢,不锈钢等支架,另考虑到光伏支架强度、系统成本、屋顶面积利用率等因素。在保证系统发电量降低不明显的情况下(降低不超过1%)尽可能降低光伏方阵倾斜角度,以减少受风面,做到增加支架强度,减少支架成本、提高有限场地面积的利用率。 漏雨是安装光伏电站过程中需要注意的问题,防水工作做好了,光伏电站才安全。光伏支架安装在屋顶支撑着组件,连接着屋顶。它的设计多采用顶上顶的方式,不会对屋面原有防水进行穿孔、破坏;压块采用预制构件,不用现场浇注,可以避免了太阳能支架安装对屋面防水层的硬性破坏。 4、光伏方阵串并联设计 分布式光伏发电系统中,太阳能电池组件电路相互串联组成串联支路。串联接线用于提升直流电压至逆变器电压输入范围,应保证太阳能电池组件在各种太阳辐射照度和各种环境温度工况下都不超出逆变器电压输入范围。 工作电压在逆变器的额定工作电压左右,效率最高,单相220V逆变器,逆变器输入额定电压为360V,三相380V逆变器,逆变器输入额定电压为650V。如3kW逆变器,配260W组件,工作电压30.5V,配12块工作电压366V,功率为3.12kW 为最佳。10KW逆变器配260W组件,接40块组件,每一路20串,电压为610V,总功率为10.4kW为最佳。
基于ANSYS的汽车结构轻量化设计
2005年6月 农业机械学报 第36卷第6期 基于ANSYS 的汽车结构轻量化设计 赵 韩 钱德猛 【摘要】 建立了基于A N SYS 的某型号半挂车车架的有限元模型,并且进行了模拟实际工况的应力计算和试验验证。从有限元分析结果出发,形成了优化设计的数学模型,通过计算提出较为合理的车架轻量化设计方案。 关键词:车架 有限元法 优化设计中图分类号:U 463.32 文献标识码:A Research on Lightweight Design of Automobile Structure Based on ANSYS Zhao Han Qian Demeng (H ef ei Univer sity o f Technology ) Abstract The kind of finite element model o f the frame o f a semi-trailer w as established based on ANSYS and stress calculation and ex periment validation simulating the actual wo rking conditions w er e perform ed .Then the math mo del of optim al design was form ed fro m the analysis result of finite element m ethod .In the end the relativ e r easonable pr oject of lightw eight desig n w as put fo rw ard thro ug h calculation.The result prov ided certain g uidance function not o nly for the technicians of the facto ries but also fo r the users of the ANSYS. Key words Fram e ,Finite element method ,Optimal design 收稿日期:2003 1110 赵 韩 合肥工业大学机械与汽车工程学院 教授 博士生导师,230009 合肥市钱德猛 合肥工业大学机械与汽车工程学院 博士生 引言 汽车结构的轻量化对汽车节能和环保都具有重要的意义。据统计,客车、轿车和多数专用汽车的车身质量约占整车自身质量的40%~60%。所以,减轻汽车自身的质量一方面节约了原材料,降低了生产成本;另一方面也降低了燃油消耗,减少了排放,有利于环保[1]。目前,国内对汽车结构件的设计与研究已经从主要依靠经验设计逐渐发展到应用有限元等现代设计方法进行静强度计算和分析阶段,但是尚未像汽车整车和主要零部件的参数确定那样广泛应用优化设计方法。所以汽车结构参数优化设计仍是近些年的重要研究领域。汽车车架是汽车结构件中结构和载荷都很复杂的重要部件[2],也是人们首先开展结构分析和结构优化设计的研究对象。 本文采用有限元法对某型号半挂汽车车架结构的应力分布进行了分析,形成了车架的初始设计方 案,进而从有限元分析的结果出发形成优化设计即轻量化设计所需要的数学模型。并在对有限元模型进行试验验证的基础上,提出了该车架结构的轻量化设计方案并进行了有限元强度分析,确定了较合理的设计方案。 1 车架结构轻量化设计模型 1.1 结构分析模型 该型号半挂汽车车架是以型钢作为骨架再覆以钢板而成的板架组合结构,承受垂直于车架平面的均布压力。根据计算模型的准确性原则,建模时略去了车架上的附属结构(图1)。由于该车是多轴车,为静不定结构,为了得到车架结构的真实应力分布,必 须考虑悬挂系统的变形情况。因此,整个车架有限元模型由车架有限元模型和悬挂系统等效有限元模型组成。根据车架的结构形式和受力特点,梁架为薄壁结构,选取弹性壳单元(四节点四边形等参元,代号
建筑结构设计规范和设计方法
建筑结构设计规范和设计方法 建筑结构设计规范和设计方法 摘要:本文分析了几个建筑设计中结构设计方面存在的普遍问题,并提出了针对这些问题的防治方法,供大家参考借鉴。 关键词:建筑结构设计存在问题 建筑设计是一项繁重而又责任重大的工作,直接影响到建筑物的安全、适用、经济和合理性。但在实际设计工作中,常常发生建筑结构设计的种种概念和方法上的差错,这些差错的产生,有的是由于设计人员没有对一般建筑尤其是多层建部设计引起高度重视,盲目参照或套用其他的设计的结果;有的则是由于设计对设计规范和设计方法缺乏理解;还有的是由于设计者的力学概念模糊,不能建立正确的计算模式,对结构验算结果也缺乏判断正确与否的经验,为了避免或减少类似的情况发生,确保建筑设计质量能上一个台阶,应从以下几个方面对结构设计中的常见问题加以改进: 1 剪力墙砌体结构挑梁裂缝问题 底层框架剪力墙砌体结构房屋是指底层为钢筋混凝土框架--剪 力墙结构,上部为多层砌体结构的房屋。该类房屋多见于沿街的旅馆、住宅、办公楼,底层为商店,餐厅、邮局等空间房屋,上部为小开间的多层砌体结构。这类建筑是解决底层需要一种比较经济的空间房屋的结构形式。部分设计者为追求单一的建筑立面造型来增加使用面积,将二层以上的部分横墙且外层挑墙移至悬挑梁上,各层设计有挑梁,但实际结构的底层挑梁承载普遍出现裂缝,该类挑梁的设计与出现裂缝在临街砌体结构房屋中比较常见。 原因是原设计各层挑梁均按承受本层楼盖及其墙体的荷载进行 计算。但实际结构中,悬挑梁上部墙体均为整体砌筑,且下部墙体均兼上层挑梁的底摸,这样挑梁上部的墙体及楼盖的荷载实际上是由上往下传递。上述挑梁的设计计算与实际工程中受力及传力路线不符是导致底层挑梁承载力不足并出现受力裂缝的主要原因,解决的办法要么改变计算简图及受力路线,要么注意施工顺序和施工工序。