塑料桶吹塑工艺简述

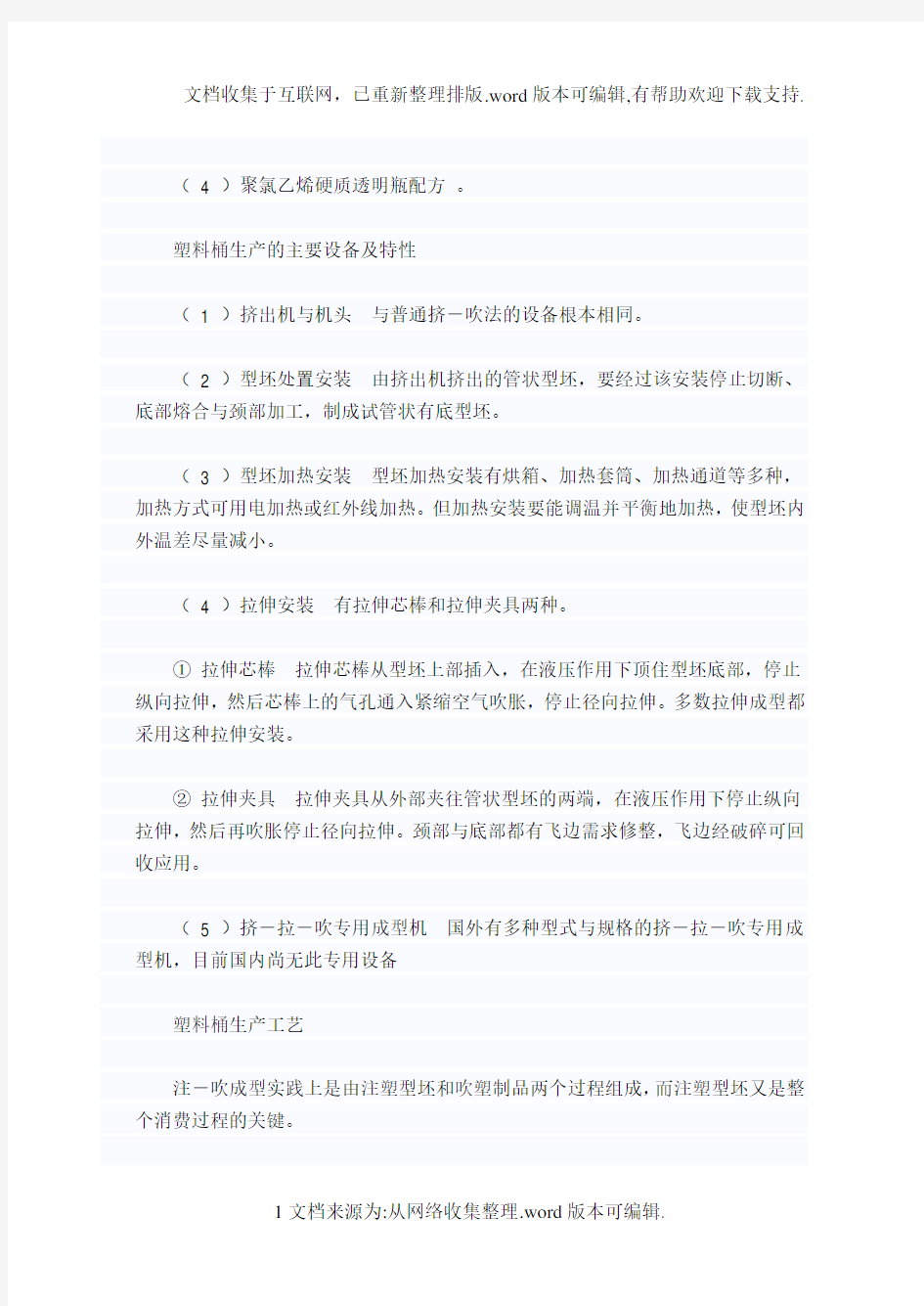
塑料桶吹塑工艺简述
?塑料桶中空吹塑根本上能够分为两大类:挤出—吹塑和注射—吹塑。两者的主要不同点在于型坯的制备,然后的吹塑过程根本相同。在这两种成型办法的根底上开展起来的有:挤出—拉伸—吹塑(简称挤—拉—吹),注射—拉伸—吹塑(简称注—拉—吹)以及多层映塑等。注射-吹塑(简称注-吹)塑料瓶是采用注射成型法先将塑料制成有底型坯,再把型坯趁热移到吹塑模中吹塑成型的中空制品。注-吹中空容器没有飞边,尺寸稳定性好,瓶口与螺纹质量优良,型坯厚度可预先调理,制品光泽度好,俭省原料。但注-吹成型不合适消费大型和外形复杂的容器,又由于要运用注射和吹塑两副模具,所以设备投资较大。注-吹中空容器以外形筒单的小型瓶体为主,它能够用聚氯乙烯、聚乙烯、聚丙烯和聚苯乙烯、聚酯、聚酰胺等多种树脂来消费。主要用于医药、食品、化装品等的包装用于中空吹塑的塑料种类有聚乙烯、聚氯乙烯、聚丙烯、聚苯乙烯、线形聚酯、聚碳酸酯、聚酰胺、醋酸纤维素和聚缩醛树脂等。其中高密度聚乙烯的耗费量占首位。它普遍应用于食品、化工和处置液体的包装。高分子量聚乙烯适用于制造大型燃料醝罐和桶等。聚氯乙烯由于有较好的透明度和气密性,所以在化装品和洗濯剂的包装方面得到普遍应用。
随着无毒聚氯乙烯树脂和助剂的开发,以及拉伸吹塑技术的开展,聚氯乙烯容器在食品包装方面的用量疾速增加,并且曾经开端用于啤酒和其它含有二氧化碳气体饮料的包装。线形聚酯资料是近几年进入中空吹塑范畴的新型资料。由于其制品具有光泽的外观、优秀的透明性、较高的力学强度和容器内物品保管性较好,废弃物燃烧处置时不污染环境等方面的优点,所以在包装瓶方面开展很快,特别在耐压塑料食品容器方面的运用最为普遍。聚丙烯因其树脂的改性和加工技术的进步,运用量也逐年增加。
主要原料及典型配方
(l )聚乙烯普通选用熔体指数为l ~6 的聚乙烯树脂。
(2 )聚丙烯普通选网熔体指数为2 一4 的聚丙烯树脂。
(3 )聚苯乙烯普通选用通用型或抗冲型的注射级聚苯乙烯树脂。
(4 )聚氯乙烯硬质透明瓶配方。
塑料桶生产的主要设备及特性
(1 )挤出机与机头与普通挤-吹法的设备根本相同。
(2 )型坯处置安装由挤出机挤出的管状型坯,要经过该安装停止切断、底部熔合与颈部加工,制成试管状有底型坯。
(3 )型坯加热安装型坯加热安装有烘箱、加热套筒、加热通道等多种,加热方式可用电加热或红外线加热。但加热安装要能调温并平衡地加热,使型坯内外温差尽量减小。
(4 )拉伸安装有拉伸芯棒和拉伸夹具两种。
①拉伸芯棒拉伸芯棒从型坯上部插入,在液压作用下顶住型坯底部,停止纵向拉伸,然后芯棒上的气孔通入紧缩空气吹胀,停止径向拉伸。多数拉伸成型都采用这种拉伸安装。
②拉伸夹具拉伸夹具从外部夹往管状型坯的两端,在液压作用下停止纵向拉伸,然后再吹胀停止径向拉伸。颈部与底部都有飞边需求修整,飞边经破碎可回收应用。
(5 )挤-拉-吹专用成型机国外有多种型式与规格的挤-拉-吹专用成型机,目前国内尚无此专用设备
塑料桶生产工艺
注-吹成型实践上是由注塑型坯和吹塑制品两个过程组成,而注塑型坯又是整个消费过程的关键。
吹塑、吸塑工艺介绍
吹塑 吹塑 blow moulding 也称中空吹塑,一种发展迅速的塑料加工方法。热塑性树脂经挤出或注射成型得到的管状塑料型坯,趁热(或加热到软化状态),置于对开模中,闭模后立即在型坯内通入压缩空气,使塑料型坯吹胀而紧贴在模具内壁上,经冷却脱模,即得到各种中空制品。吹塑薄膜的制造工艺在原理上和中空制品吹塑十分相似,但它不使用模具,从塑料加工技术分类的角度,吹塑薄膜的成型工艺通常列入挤出中。吹塑工艺在第二次世界大战期间,开始用于生产低密度聚乙烯小瓶。50年代后期,随着高密度聚乙烯的诞生和吹塑成型机的发展,吹塑技术得到了广泛应用。中空容器的体积可达数千升,有的生产已采用了计算机控制。适用于吹塑的塑料有聚乙烯、聚氯乙烯、聚丙烯、聚酯等,所得之中空容器广泛用作工业包装容器。 根据型坯制作方法,吹塑可分为挤出吹塑和注射吹塑,新发展起来的有多层吹塑和拉伸吹塑。 塑料模具常识- 挤出吹塑 挤出吹塑是一种制造中空热塑性制件的方法。广为人制的吹塑对象有瓶、桶、罐、箱以及所有包装食品、饮料、化妆品、药品和日用品的容器。大的吹塑容器通常用于化工产品、润滑剂和散装材料的包装上。其他的吹塑制品还有球、波纹管和玩具。对于汽车制造业,燃料箱、轿车减震器、座椅靠背、中心托架以及扶手和头枕覆盖层均是吹塑的。对于机械和家具制造业,吹塑零件有外壳、门框架、制架、陶罐或到有一个开放面的箱盒。 聚合物 最普通的吹塑挤塑料原料是高密度聚乙烯,大部分牛奶平时有这种聚合物制成的。其他聚烯烃也常通过吹塑来加工。根据用途,苯乙烯聚合物、聚氯乙烯、聚酯、聚氨酯、聚碳酸酯和其他热塑性塑料也可以用来吹塑。 最近工程塑料在汽车行业被广泛接受。材料选择是以机械强度、耐候性、电学性能、光学性能和其他性能为依据的。 工艺 3/4的吹塑制品是由挤出吹塑法制造的。挤出工艺是强迫物料通过一个孔或模具来制造产品。 挤出吹塑工艺由5步组成:1.塑料型胚(中空塑料管的挤出);2.在型胚上将瓣合模具闭合,夹紧模具并切断型胚;3.向模腔的冷壁吹胀型培,调整开口并在冷却期间保持一定的压力,打开模具,写下被吹的零件;5.修整飞边得到成品。 挤塑 聚合物混配备定义为通过熔体混合使聚合物或聚合物体系提高等级的一种过程。混配过程从单一添加剂的加入到多种添加剂处理、聚合物合金和反应性混培,其范围甚广。据估计,美国三分之一的聚合物生产要经过混佩。混配料可根据最终应用的性
吹塑-作业指导书
吹塑作业指导书--吹塑簿膜生产工艺及常见故障 分析 大多数热塑性塑料都可以用吹塑法来生产吹塑薄膜,吹塑薄膜是将塑料挤成薄管,然后趁热用压缩空气将塑料吹胀,再经冷却定型后而得到的筒状薄膜制品,这种薄膜的性能处于定向膜同流延膜之间:强度比流延膜好,热封性比流延膜差。吹塑法生产的薄膜品种有很多,比如低密度聚乙烯(LDPE)、聚丙烯(PP)、高密度聚乙烯(HDPE)、尼龙(PA)、乙烯一乙酸乙烯共聚物(EVA)等,这里我们就对常用的低密度聚乙烯(LDPE)薄膜的吹塑生产工艺及其常见故障进行简单的介绍。 聚乙烯吹塑薄膜材料的选择 1.选用的原料应当是用吹膜级的聚乙烯树脂粒子,含有适量的爽滑剂,保证薄膜的开口性。 2.树脂粒子的熔融指数(MI)不能太大,熔融指数(MI)太大,则熔融树脂的粘度太小,加工范围窄,加工条件难以控制,树脂的成膜性差,不容易加工成膜;此外,熔融指数(MI)太大,聚合物相对分子量分布太窄,薄膜的强度较差。因此,应当选用熔融指数(MI)较小,且相对分子量分布较宽的树脂原料,这样既能满足薄膜的性能要求,又能保证树脂的加工特性。吹塑聚乙烯薄膜一般选用熔融指数(MI)在2~6g/10min范围之间的聚乙烯原料。 吹塑工艺控制要点 吹塑薄膜工艺流程大致如下: 料斗上料一物料塑化挤出→吹胀牵引→风环冷却→人字夹板→牵引辊牵引→电晕处理→薄膜收卷但是,值得指出的是,吹塑薄膜的性能跟生产工艺参数有着很大的关系,因此,在吹膜过程中,必须要加强对工艺参数的控制,规范工艺操作,保证生产的顺利进行,并获得高质量的薄膜产品。在聚乙烯吹塑薄膜生产过程中,主要是做好以下几项工艺参数的控制: 1.挤出机温度 吹塑低密度聚乙烯(LDPE)薄膜时,挤出温度一般控制在160℃~170℃之间,且必须保证机头温度均匀,挤出温度过高,树脂容易分解,且薄膜发脆,尤其使纵向拉伸强度显著下降;温度过低,则树脂塑化不良,不能圆滑地进行膨胀拉伸,薄膜的拉伸强度较低,且表面的光泽性和透明度差,甚至出现像木材年轮般的花纹以及未熔化的晶核(鱼眼)。 2.吹胀比 吹胀比是吹塑薄膜生产工艺的控制要点之一,是指吹胀后膜泡的直径与未吹胀的管环直径之间的比值。吹胀比为薄膜的横向膨胀倍数,实际上是对薄膜进行横向拉伸,拉伸会对塑料分子产生一定程度的取向作用,吹胀比增大,从而使薄膜的横向强度提高。但是,吹胀比也不能太大,否则容易造成膜泡不稳定,且薄膜容易出现皱折。因此,吹胀比应当同牵引比配合适当才行,一般来说,低密度聚乙烯(LDPE)薄膜的吹胀比应控制在2.5~3.0为宜。 3.牵引比 牵引比是指薄膜的牵引速度与管环挤出速度之间的比值。牵引比是纵向的拉伸倍数,使薄膜在引取方向上具有定向作用。牵引比增大,则纵向强度也会随之提高,且薄膜的厚度变薄,但如果牵引比过大,薄膜的厚度难以控制,甚至有可能会将薄膜拉断,造成断膜现象。低密度聚乙烯(LDPE)薄膜的牵引比一般控制在4~6之间为宜。 4.露点 露点又称霜线,指塑料由粘流态进入高弹态的分界线。在吹膜过程中,低密度聚乙烯(LDPE)在从模口中挤出时呈熔融状态,透明性良好。当离开模口之后,要通过冷却风环对膜泡的吹胀区进行冷却,冷却空气以一定的角度和速度吹向刚从机头挤出的塑料膜泡时,高温的膜泡与冷却空气相接触,膜泡的热量会被冷空气带走,其温度会明显下降到低密度聚乙烯(LDPE)的粘流温度以下,从而使其冷却固化且变得模糊不清了。在吹塑膜泡上我们可以看到一条透明和模糊之间的分界线,这就是露点(或者称霜线)。 在吹膜过程中,露点的高低对薄膜性能有一定的影响。如果露点高,位于吹胀后的膜泡的上方,则薄膜的吹胀是在液态下进行的,吹胀仅使薄膜变薄,而分子不受到拉伸取向,这时的吹胀膜性能接近于流延膜。相反,如果露点比较低,则吹胀是在固态下进行的,此时塑料
吹塑工艺
吹塑工艺、注塑工艺和滚塑工艺的区别是什么?怎么辨别三种工艺的产品? 三种工艺,吹塑产品都是中空的;注塑因为有注塑口,所以成型后的产品会多出一小快不要的部分,会有道工序把它剪掉,不过如果仔细观察还是可以发现的;滚塑产品最大的特点是无接缝,无注塑口。 塑料的成型和加工方法 塑料成型加工是一门工程技术,所涉及的内容是将塑料转变为塑料制品的各种工艺。在转变过程中常会发生以下一种或几种情况,如聚合物的流变以及物理、化学性能的变化等。 塑料成型方法 1.压缩模塑。压缩模塑又称模压,是模塑料在闭合模腔内借助加压(一般尚须加热)的成型方法。通常,压缩模塑适用于热固性塑料,如酚醛塑料、氨基塑料、不饱和聚酯塑料等。 压缩模塑由预压、预热和模压三个过程组成: 预压为改善制品质量和提高模塑效率等,将粉料或纤维状模塑料预先压成一定形状的操作。 预热为改善模塑料的加工性能和缩短成型周期等,把模塑料在成型前先行加热的操作。 模压在模具内加入所需量的塑料,闭模、排气,在模塑温度和压力下保持一段时间,然后脱模清模的操作。 压缩模塑用的主要设备是压机和塑模。压机用得最多的是自给式液压机,吨位从几十吨至几百吨不等。有下压式压机和上压式压机。用于压缩模塑的模具称为压制模具,分为三类;溢料式模具、半溢料式模具不溢式模具。 压缩模塑的主要优点是可模压较大平面的制品和能大量生产,其缺点是生产周期长,效率低。 2.层压成型。用或不用粘结剂,借加热、加压把相同或不相同材料的两层或多层结合为整体的方法。层压成型常用层压机操作,这种压机的动压板和定压板之间装有多层可浮动热压板。 层压成型常用的增强材料有棉布、玻璃布、纸张、石棉布等,树脂有酚醛、环氧、不饱和聚酯以及某些热塑性树脂。 3.冷压模塑。冷压模塑又叫冷压烧结成型,和普通压缩模塑的不同点是在常温下使物料加压模塑。脱模后的模塑品可再行加热或借助化学作用使其固化。该法多用于聚四氟乙烯的成型,也用于某些耐高温塑料(如聚酰亚胺等)。一般工艺过程为制坯-烧结-冷却三个步骤。 4.传递模塑。传递模塑是热固性塑料的一种成型方式,模塑时先将模塑料在加热室加热软化,然后压入巳被加热的模腔内固化成型。传递模塑按设备不同有工种形式:①活板式;②罐式;③柱塞式。传递模塑对塑料的要求是:在未达到固化温度前,塑料应具有较大的流动性,达到固化温度后,又须具有较快的固化速率。能符合这种要求的有酚醛、三聚氰胺甲醛和环氧树脂等。 传递模塑具有以下优点:①制品废边少,可减少后加工量;②能模塑带有精细或易碎嵌件和穿孔的制品,并且能保持嵌件和孔眼位置的正确;③制品性能均匀,尺寸准确,质量高;④模具的磨损较小。缺点是:⑤模具的制造成本较压缩模高;⑥塑料损耗大;⑦纤维增强塑料因纤维定向而产生各向异性; ⑧围绕在嵌件四周的塑料,有时会因熔按不牢而使制品的强度降低。 5.低压成型。使用成型压力等于或低于1.4兆帕的摸压或层压方法。 低压成型方法用于制造增强塑料制品。增强材料如玻璃纤维、纺织物、石棉、纸、碳纤维等。常用的树脂绝大多数是热固性的,如酚醛、环氧、氨基、不饱和聚酯、有机硅等树脂。 低压成型包括袋压法、喷射法。 (1) 袋压成型。借助弹性袋(或其它弹性隔膜)接受流体压力而使介于刚性模和弹性袋之间的增强塑料均匀受压而成为制件的一种方法。按造成流体压力的方法不同,一般可分为加压袋成型、真空袋压成型和热压釜成型等。 (2) 喷射成型。成型增强塑料制品时,用喷枪将短切纤维和树脂等同时喷在模具上积层并固化为制品的方法。 6.挤出成型。挤出成型也称挤压模塑或挤塑,它是在挤出机中通过加热、加压而使物料以流动状态连续通过口模成型的方法。
PET塑料瓶的加工工艺和吹塑设备介绍
PET吹塑瓶可分为两类,一类是有压瓶,如充装碳酸饮料的瓶;另一类为无压瓶,如 充装水、茶、油等的瓶。茶饮料瓶是掺混了聚萘二甲酸乙二酯(PEN)的改性PET瓶或PET与热塑性聚芳酯的复合瓶,在分类上属热瓶,可耐热80℃以上;水瓶则属冷瓶, 对耐热性无要求。在成型工艺上热瓶与冷瓶相似。笔者主要讨论冷瓶中的有压饮料瓶 成型工艺。 1 设备 随着科技的不断进步和生产的规模化,PET吹瓶机自动化程度越来越高,生产效率 也越来越高。设备生产能力不断提高,由从前的每小时生产几千个瓶发展到现在每小 时生产几万个瓶。操作也由过去的手动按钮式发展为现在的全电脑控制,大大降低了 工艺操作上的难度,增加了工艺的稳定性。 目前,注拉吹设备的生产厂家主要有法国的SIDEL公司、德国的KRONES公司等。虽然生产厂家不同,但其设备原理相似,一般均包括供坯系统、加热系统、吹瓶系统、控制系统和辅机五大部分。 2 吹塑工艺 PET瓶吹塑工艺流程。 影响PET瓶吹塑工艺的重要因素有瓶坯、加热、预吹、模具及环境等。 2.1 瓶坯 制备吹塑瓶时,首先将PET切片注射成型为瓶坯,它要求二次回收料比例不能过高(5%以下),回收次数不能超过两次,而且分子量及粘度不能过低(分子量31000-50000,特性粘度0.78-0.85cm3/g)。注塑成型的瓶坯需存放48h以上方能使用。加 热后没用完的瓶坯,必须再存放48h以上方能重新加热使用。瓶坯的存放时间不能超 过六个月。
瓶坯的优劣很大程度上取决于PET材料的优劣,应选择易吹胀、易定型的材料,并制定合理的瓶坯成型工艺。实验表明,同样粘度的PET材料成型的瓶坯,进口的原料 要比国产料易吹塑成型;而同一批次的瓶坯,生产日期不同,吹塑工艺也可能有较大 差别。瓶坯的优劣决定了吹塑工艺的难易,对瓶坯的要求是纯洁、透明、无杂质、无 异色、注点长度及周围晕斑合适。 2.2 加热 瓶坯的加热由加热烘箱来完成,其温度由人工设定,自动调节。烘箱中由远红外灯 管发出远红外线对瓶坯辐射加热,由烘箱底部风机进行热循环,使烘箱内温度均匀。 瓶坯在烘箱中向前运动的同时自转,使瓶坯壁受热均匀。 灯管的布置在烘箱中自上而下一般呈"区"字形,两头多,中间少。烘箱的热量由灯 管开启数量、整体温度设定、烘箱功率及各段加热比共同控制。灯管的开启要结合预 吹瓶进行调整。 要使烘箱更好地发挥作用,其高度、冷却板等的调整很重要,若调整不当,吹塑时 易出现胀瓶口(瓶口变大)、硬头颈(颈部料拉不开)等缺陷。 2.3 预吹 预吹是二步吹瓶法中很重要的一个步骤,它是指吹塑过程中在拉伸杆下降的同时开 始预吹气,使瓶坯初具形状。这一工序中预吹位置、预吹压力和吹气流量是三个重要 工艺因素。 预吹瓶形状的优劣决定了吹塑工艺的难易与瓶子性能的优劣。正常的预吹瓶形状为 纺锤形,异常的则有亚铃状、手柄状等,如图2所示。造成异常形状的原因有局部加 热不当,预吹压力或吹气流量不足等,而预吹瓶的大小则取决于预吹压力及预吹位置。在生产中要维持整台设备所有预吹瓶大小及形状一致,若有差异则要寻找具体原因, 可根据预吹瓶情况调整加热或预吹工艺。
PET瓶吹塑生产工艺流程
1.PET 塑料简介 PET 塑料是英文Polyethylene terephthalate的缩写,简称PET或PETP。中文意思是:聚对苯二甲酸类塑料,主要包括聚对苯二甲酸乙二酯PET和聚对苯二甲酸丁二酯PBT。 聚对苯二甲酸乙二醇酯又俗称涤纶树脂,俗称涤纶树脂。它是对苯二甲酸与乙二醇的缩聚物,与PBT一起统称为热塑性聚酯,或饱和聚酯。聚酯是以PET为代表的热塑性线型饱和聚酯的总称 ,包括 PET、PBT、PEN、PCT及其共聚物。 PET是开发最早、产量最大、应用最广的聚酯产品。 PET再生塑料可以用在食品包装物上,可以实现无限次的再生循环利用。这是我国触手可及的环保工艺技术。由于塑料包装的原材料来自石油,为了节约资源,许多发达国家都研制出了塑料包装的回收再利用技术,早在1991年就已经将再生PET塑料切片用做食品包装材料。 2.我国PET塑料发展现状目前我国的聚酯pet塑料的包装容器目前主要局限于双向拉伸聚酯吹塑瓶。故以下主要从我国PET 瓶的发展来介绍我国的PET塑料的发展现状,并列举两例PET瓶生产行业的领先集团。 我国双向拉伸聚酯吹塑瓶在塑料包装行业中起步较晚,但自20世纪80年代从日本引入注拉吹PET瓶生产线之后即在以可乐为代表的饮料包装中取得了很好的效果,随后引进了大量国外先进的注拉吹PET瓶生产设备,同时在消化国外先进技术的基础上,研发了具有自主知识产权、适合我国国情的、结构简单的二步法PET拉伸吹塑机,它与通用注射机配合使用,利用通用注射机制造的PET瓶坯,吹制PET双向拉伸瓶。国产二步法双向拉伸PET吹瓶机中,有的机型不仅能生产普通PET 双向拉伸瓶,还能生产耐热型双向拉伸PET瓶,所能生产的产品的容积基本上覆盖了进口设备所能生产的从几十毫升的小瓶到5加仑的大桶的广阔的领域。这些简易式吹瓶机不仅具有造价低廉、机动性强的优点,而且控制得当也能生产出品质优良、实用性好的双向拉伸PET吹瓶,因此得到了国内外塑料加工界的普遍认同,除了国内大量使用之外,已部分出口外销。尽管这些设备和进口的先进设备之间还存在生产效率较低、自动化程度较差、制品尺寸精度较差的差距,对于一些要求特别严格的应用领域(如可口可乐、百事可乐等产品的包装),其应用上尚有一定困难。 此外,多层共吹塑PET瓶的生产设备国内尚待开发,但国产二步法双向拉伸PET吹瓶机的开发利用对于促进PET瓶生产的高速发展起到了不容忽视的、巨大的推动作用。 目前,我国的PET瓶生产企业中既有拥有世界上各知名企业制造的最先进的PET瓶自动生产线(如日本ASB公司、青木固公司的全自动PET瓶生产线,法国 SEDEL公司的全自动PET瓶生产线以及意大利SIPA公司的全自动PET瓶生产线)的大型骨干企业,同时,也有大量采用我国自行设计制造的各种不同自动化程度的简易、实用型双向PET吹瓶机的中小型企业,呈现出一个前所未有的百花争艳、欣欣向荣的局面。 目前我国PET瓶生产行业中,产量最大的骨干企业是珠海中富和上海紫江集团,分别占有国内PET瓶市场份额的约30%和20%。珠海中富集团是国内最早获得可口可乐、 百事可乐公司认可的PET瓶生产厂家,2001年该集团PET瓶产量达到32亿个,其中热灌装7亿个,销售额达到23.4亿元,在各地拥有30多家工厂。 上海紫江集团近年来也发展很快,设在各地的控股公司已发展到15家,占据了武汉、郑州、天津、长春、昆山、成都等地的市场,新建的年产 1.2亿个PET热灌装瓶已投产,2002年又在上海、广州、成都、北京等地投资建厂,热灌装瓶的生产能力达到4.85亿个。 在PET瓶迅速发展的同时,我国瓶级PET树脂的生产也得到了迅速的发展。据报道,1995年我国瓶级PET树脂的用量为10万t,其中国内生产量为6万t,到2000年我国瓶级PET树脂的用量为52万t,国内生产能力已达50万t。除了量的飞速增长外,质量方面也有很大的提高,仪征化纤、上海远东、常州华源等公司生产的瓶级PET树脂均已获得可口可乐公司的
(工艺技术)关于吹塑工艺介绍
吹塑 blow moulding 也称中空吹塑,一种发展迅速的塑料加工方法。热塑性树脂经挤出或注射成型得到的管状塑料型坯,趁热(或加热到软化状态),置于对开模中,闭模后立即在型坯内通入压缩空气,使塑料型坯吹胀而紧贴在模具内壁上,经冷却脱模,即得到各种中空制品。吹塑薄膜的制造工艺在原理上和中空制品吹塑十分相似,但它不使用模具,从塑料加工技术分类的角度,吹塑薄膜的成型工艺通常列入挤出中。吹塑工艺在第二次世界大战期间,开始用于生产低密度聚乙烯小瓶。50年代后期,随着高密度聚乙烯的诞生和吹塑成型机的发展,吹塑技术得到了广泛应用。中空容器的体积可达数千升,有的生产已采用了计算机控制。适用于吹塑的塑料有聚乙烯、聚氯乙烯、聚丙烯、聚酯等,所得之中空容器广泛用作工业包装容器。 根据型坯制作方法,吹塑可分为挤出吹塑和注射吹塑,新发展起来的有多层吹塑和拉伸吹塑。 塑料模具常识- 挤出吹塑 挤出吹塑是一种制造中空热塑性制件的方法。广为人制的吹塑对象有瓶、桶、罐、箱以及所有包装食品、饮料、化妆品、药品和日用品的容器。大的吹塑容器通常用于化工产品、润滑剂和散装材料的包装上。其他的吹塑制品还有球、波纹管和玩具。对于汽车制造业,燃料箱、轿车减震器、座椅靠背、中心托架以及扶手和头枕覆盖层均是吹塑的。对于机械和家具制造业,吹塑零件有外壳、门框架、制架、陶罐或到有一个开放面的箱盒。 聚合物 最普通的吹塑挤塑料原料是高密度聚乙烯,大部分牛奶平时有这种聚合物制成的。其他聚烯烃也常通过吹塑来加工。根据用途,苯乙烯聚合物、聚氯乙烯、聚酯、聚氨酯、聚碳酸酯和其他热塑性塑料也可以用来吹塑。 最近工程塑料在汽车行业被广泛接受。材料选择是以机械强度、耐候性、电学性能、光学性能和其他性能为依据的。 工艺 3/4的吹塑制品是由挤出吹塑法制造的。挤出工艺是强迫物料通过一个孔或模具来制造产品。 挤出吹塑工艺由5步组成:1.塑料型胚(中空塑料管的挤出);2.在型胚上将瓣合模具闭合,夹紧模具并切断型胚;3.向模腔的冷壁吹胀型培,调整开口并在冷却期间保持一定的压力,打开模具,写下被吹的零件;5.修整飞边得到成品。 挤塑 聚合物混配备定义为通过熔体混合使聚合物或聚合物体系提高等级的一种过程。混配过程从单一添加剂的加入到多种添加剂处理、聚合物合金和反应性混培,其范围甚广。据估计,美国三分之一的聚合物生产要经过混佩。混配料可根据最终应用的性能要求进行定制。混配产品具有杂混的性能,例如高光泽和优良的抗冲击强度,或精密模塑性和良好的刚度。 混配好的聚合物通常被切粒用于进一步加工。然而工业上越来越来感兴趣的是将混配与下一步过程结合起来,例如型材挤出,这样可避免再次加热聚合物。 混合 人们使用各种类型的熔体混合设备,从辊炼机和分批混合机到单螺杆和双螺杆挤塑机。连续混配给(挤塑机)是最常用的设备,因为他可提供质量一致的产品,并且可降低操作费用。有两种混合类型:分布式混合品料再婚配料中无需采用高剪切应力就可以均匀地分布。这类混合液被称为延伸性混合或层流性混合。 分散式混合亦称强力混合,其中施加高剪切应力来打碎内聚成团的固体。例如当添加剂料团被打碎时,实际的颗粒尺寸就变小了。 混配操作经常在一个过程中需要两种混合类型。
吹塑工艺
4-1 概论 中空成形亦称吹压成形,顾名思意就是制成中空形状的热塑品。 其主要制程可分为下列之步骤,如图4-1所示。 (a) 将塑料熔融,经螺杆挤压成中空之型胚(parison)。 (b) 型胚垂落于分成两半之模具中,再将模具闭合。 (c) 将压缩空气注入于型胚中,充胀型胚而与模具贴合。 (d) 吹胀之产品冷却后脱模。 (e) 修整毛边,即得成品。 上述之制法亦称押出中空成形(extrusion-blow-molding),另外一种常见的为射出中空成形 (injection-blow-molding),其法为利用射出成形在心蕊吹针上形成型胚且瓶颈也一起成形,然后型胚连同吹针传送到吹模模具内,再经由吹针贯入空气将型胚胀满整个模穴,最后转至顶出站而得成品,如图4-2为三站式之射吹成形。
至于押吹与射吹成形两者间之比较可由表4-1查知。 若是将中空成形与射出成形相比,则中空成形适合:2大型品,厚肉品。 2可为双层壁构造。 2多种少量。 射出成形适合: 2较小型品,薄肉品。 2精密成形。 2大量生产。 若再欲深入之比较,则有以下几点:
(a) 强度上:以同重量或同体积来比较,中空成形品绝对比射出成形品为强。 (b) 加工温度:中空成形之成形加工温度较低,对收缩、翘曲、凹痕及热裂解之倾向较小。 (c) 使用原料:射出成形须使用流动性较佳的原料,若是加了玻纤,则容易产生应力。 (d) 应力集中:中空成形之压力约在4~5kgf/cm2间,为射出成形的1%,所以几乎无应力集中之现象。 (e) 模具设备成本:因射出成形为高压成形,所须之模具际较强且精密,故成本极高。而中空成形为低压成形,所用模具可为铝、锌、或铝合金。 中空成形之成形周期极短,以制造一个175毫升(6-OZ)之容器而言,其成形周期可在12秒内。若有8个模穴的话,则每一小时可制出2400个产品,且可加装自动切离边料设备以省却人工处理成本。 4-2 模具设计 4-2-1 制造材料 1. 铁与钢材: 属机械功能的,如安装、导引、滑动、夹断、切割、打孔等部位所须之组配件以钢材为主。安装平台与杆可用一般工具钢制造,而导销与衬套等导引装置则最好以表面处理过之硬化钢制造。嵌入物因型胚被夹断时须紧闭模具而产生环绕应力,所以最好以抗磨耗性钢料制造之。吹压心轴、校正心轴及吹针,可用一般之工具钢来制造。 在正常情况下,钢制中空成形模具之使用寿命为一千万次以上,但对有嵌入物之模具,应定时的整修,以使型胚得以俐落的分离。 2. 铝及铝合金: 其特性为比重低、导热度高、耐候性与抗化学性佳。它们会形成一层保护层膜,以抵抗氧化。高耐热处理之铝合金材料(70/75),因为机械加工性极佳,所以常被用于中空成形之模具。 3. 铍铜合金: 适用于须热传导性和耐侵蚀性佳之模具,其焊接、冷却系统之插销组装极为方便,可惜价格太高约为铝合金之三倍。 4. 高等级锌合金: 有好之导电度及与铝和铜制成的合金,尺寸精确度极佳,但较易受侵蚀。与钢模同厚度的锌合金,其使用寿命才为前者的1/10,所以除非有钢质的接合刃,否则必须经常予以整修保养。 4-2-2 冷却系统
PET瓶吹塑设备及加工工艺概述
PET瓶吹塑设备及加工工艺概述 吹塑瓶可分为两类, 一类是有压瓶, 如充装碳酸饮料的瓶; 另一类为无压瓶, 如充装水、茶、油等的瓶。茶饮料瓶是掺混了聚萘二甲酸乙二酯(PEN)的改性瓶或与热塑性聚芳酯的复合瓶, 在分类上属热瓶, 可耐热80℃以上; 水瓶则属冷瓶, 对耐热性无要求。在成型工艺上热瓶与冷瓶相似。笔者主要讨论冷瓶中的有压饮料瓶成型工艺 1 设备 随着科技的不断进步和生产的规模化,吹瓶机自动化程度越来越高, 生产效率也越来越高。设备生产能力不断提高, 由从前的每小时生产几千个瓶发展到现在每小时生产几万个瓶。操作也由过去的手动按钮式发展为现在的全电脑控制, 大大降低了工艺操作上的难度, 增加了工艺的稳定性。 当前, 注拉吹设备的生产厂家主要有法国的SIDEL公司、德国的KRONES公司等。虽然生产厂家不同, 但其设备原理相似, 一般均包括供坯系统、加热系统、吹瓶系统、控制系统和辅机五大部分。 2 吹塑工艺 瓶吹塑工艺流程。影响瓶吹塑工艺的重要因素有瓶坯、加热、预吹、模具及环境等。 2.1 瓶坯 制备吹塑瓶时, 首先将切片注射成型为瓶坯, 它要求二次回收料比例不能过高(5%以下), 回收次数不能超过两次, 而且分子量及粘度不能过低(分子量31000-50000, 特性粘度0.78-0.85cm3/g)。注塑成型的瓶坯需存放48h以上方能使用。加热后没用完的瓶坯, 必须再存放48h以上方能重新加热使用。瓶
坯的存放时间不能超过六个月。 瓶坯的优劣很大程度上取决于材料的优劣, 应选择易吹胀、易定型的材料, 并制定合理的瓶坯成型工艺。实验表明, 同样粘度的PET材料成型的瓶坯, 进口的原料要比国产料易吹塑成型; 而同一批次的瓶坯, 生产日期不同, 吹塑工艺也可能有较大差别。瓶坯的优劣决定了吹塑工艺的难易, 对瓶坯的要求是纯洁、透明、无杂质、无异色、注点长度及周围晕斑合适。 2.2 加热瓶坯的加热由加热烘箱来完成, 其温度由人工设定, 自动调节。烘箱中由远红外灯管发出远红外线对瓶坯辐射加热, 由烘箱底部风机进行热循环, 使烘箱内温度均匀。瓶坯在烘箱中向前运动的同时自转, 使瓶坯壁受热均匀。灯管的布置在烘箱中自上而下一般呈区字形, 两头多, 中间少。烘箱的热量由灯管开启数量、整体温度设定、烘箱功率及各段加热比共同控制。灯管的开启要结合预吹瓶进行调整。 要使烘箱更好地发挥作用, 其高度、冷却板等的调整很重要, 若调整不当, 吹塑时易出现胀瓶口(瓶口变大)、硬头颈(颈部料拉不开)等缺陷。 PET注坯及吹瓶工艺要点 https://www.360docs.net/doc/9c461375.html, 发布: -6-4 17:13:53 来自: 模具网浏览: 218 次PET在饮料包装领域的应用推动了饮料包装业的高速发展。与此同时, 饮料包装业的发展也为PET的应用提供了发展空间。严格控制PET注坯及吹瓶工艺是保证PET瓶的外观与其经济性的关键。 PET的特性
实验01 挤出吹塑薄膜成型工艺实验
实验一挤出吹塑薄膜成型工艺实验 一、实验目的 l、加深对挤出理论的理解,明确挤出吹塑薄膜成型的原理及工艺参数对产品质量的影响。 2、了解挤出机及辅机的基本结构,掌握挤出吹塑薄膜生产线的操作方法。 3、通过平挤上吹法制取聚乙烯薄膜,为性能测试提供样品。 二、实验原理 挤出成型是热塑性塑料十分重要的成型方法,其产量也居各成型方法的首位。 通过更换机头口模,挤出成型可生产多种制品,其中挤出吹塑薄膜是挤出生产的主要产品之一。 塑料薄膜是指厚度在0.005~0.25mm,长而成卷的软质片状聚合物材料。工业上生产塑料薄膜的方法大体有四种:压延法、拉伸法、流延法和挤出吹塑法。相对于其它方法,挤出吹塑薄膜具有以下优点: ①设备装置简单,投资少,见效快。 ②操作工艺易于控制,同一模具可以生产多种规格的薄膜。 ③薄膜经吹胀和牵引后,双轴定向,在一定程度上消除了机械性能的方向性。 ④可生产超宽薄膜,且不需切边,废料少成本低。 ⑤制品为圆筒状,特别适合于制作包装产品。 挤出吹塑薄膜生产的主要缺点是厚度均匀性差,产量低。尽管如此,由于挤出吹塑薄膜具有上述一系列优点,所以其应用范围较广,在整个薄膜生产中占有很重要的地位。 挤出吹塑薄膜生产的工作原理如下:当塑料加入挤出机料斗后,随着螺杆的旋转被螺槽强制推向机头,此时塑料一方面被外部热源加热,另一方面由于塑料本身在压缩、剪切和搅动过程中,与料筒、螺杆之间的外摩擦以及大分子之间的内摩擦,也产生很大的热量。与此同时,由于螺杆螺槽深度逐渐减小,加之滤网、多孔板和机头的阻力,使塑料压实,从而改善了它的热传导性。这样在内、外热及压力的联合作用,使塑料温度逐渐上升直至熔融,粘度也逐步达到成型所要求的范围。当熔融塑料进入机头后,经环隙形口模成型为薄膜管坯,此时人工将管坯端部封闭并引至牵引辊,从芯模孔道吹入压缩空气,使管坯横向膨胀,同时牵引辊连续纵向牵伸,使膜管达到所要求的厚度及折径。膜管经冷却风环冷却定型并由人字板压叠成双折薄膜,通过牵引辊以恒定的速度进入卷取装置,到一定量时可进行切割即成为膜卷。在挤出吹塑薄膜生产装置中,牵引辊又是压辊,它通过完全压紧已折叠的双层薄膜,使膜管内的空气不能越过牵引辊的缝隙处而使膜管内部保持恒定的空气量和压力,保证薄膜的尺寸不变,因此吹塑薄膜生产中,只是在生产初期鼓入压缩空气,待薄膜尺寸确定后,不需再使用压缩空气。 挤出吹塑薄膜由引膜方向的不同可分为上吹法、下吹法和平吹法,本实验所用的是上吹法,其主要特点是机头、辅机结构简单,安装、操作方便,但薄膜厚度均匀性差,不宜生产折径大的产品。
矿泉水瓶挤出吹塑成型工艺开题报告
华侨大学厦门工学院毕业设计(论文)开题报告系(部):机械工程及自动化专业班级:****** 姓名*** 学号******* 指导 教师 **** 职称 学历 副教授 课题名称矿泉水瓶挤出吹塑成型工艺及模具设计 毕业设计(论文)类型(划√)工程设计应用研究开发研究基础研究其他√ 一、本课题的研究目的和意义: 本课题来源于工程实践,是结合学生的专业特点和就业方向而设计的一个课题。通过本次设计,掌握塑料件挤出吹塑成型模具设计的过程和基本技能;利用计算机辅助模具设计;掌握模具制造、装配的工艺要求。 模具设计全程应用CAD/CAM/CAE技术以及UG三维制图软件,从设计到最后出现成品都用现代先进的模具设计软件完成,已达到提高生产效率和成品精度的要求,减少重复设计的繁琐操作。并且在设计过程中尽量采用标准件来完成整个模具的设计,以便于以后的维修及零部件的更换。 通过对矿泉水的性质和流通环境的分析,设计能在流通过程中起保护作用的包装,设计合理的包装不仅仅能保护产品、方便储运,而且还能在很大程度上起到介绍产品和促进销售的作用。本设在矿泉水在流通过程得到保护,同时激起人们的购买欲望,从而促进其销售。为了设计一款兼有良好的容装性,保护性,方便性,有美观经济的优点,满足消费者购买和使用习惯的矿泉水水瓶包装也是很有经济价值和市场前景的。
二、文献综述(国内外研究情况及其发展): 模具生产技术水平的高低,已成为衡量一个国家产品制造水平高低的重要标志,因为模具在很大程度上决定着产品的质量、效益和新产品的开发能力。经国务院批准,从1997 年到2000 年,对80 多家国有专业模具厂实行增值税返还70%的优惠政策,以扶植模具工业的发展。所有这些,都充分体现了国务院和国家有关部门对发展模具工业的重视和支持。 年来我国的模具工业也有了很大的提高,有的模具已达到国际水平,年出口额达7.38亿美元。由于近年来市场需求的强劲拉动,中国模具工业高速发展,市场广阔,以2003年为例,年增长就达25%之多,广东、江苏、浙江、山东等地的增长甚至在25%以上,其中广东模具生产企业近7000余家,年产值早巳超过200亿元,占全国模具年产值的40%多,几成就了我国模具工业的半壁江山。目前我国塑料模具市场中国外模具约占,其中大型、精密、复杂、长寿命模具约占左右。被国外称为“金钥匙”、“进入富有社会的原动力”的模具由于经济发展较快时期产品畅销, 自然要求模具能跟上,而经济发展滞缓时期产品不畅销企业必然想方设法开发新产品,这同样会给模具带来强劲的需求因此模具工业被称为“不衰亡工业”模具市场发展走势总体将是平稳向上并且随着以塑代钢、以塑代木、少无切削等的进一步发展实施,结合我国国民经济各部门发展规划,我国的发展速度将高于世界平均水平,预计“十五”期间我国模具工业将以年均10%以上的速度发展,而塑料模具将20%以上的速度发展。 吹塑,这里主要指中空吹塑 ( 又称吹塑模塑 ) 是借助于气体压力使闭合在模具中的热熔型坯吹胀形成中空制品的方法,是第三种最常用的塑料加工方法,同时也是发展较快的一种塑料成型方法。吹塑用的模具只有阴模 ( 凹模 ) ,与注塑成型相比,设备造价较低,适应性较强,可成型性能好 ( 如低应力 ) 、可成型具有复杂起伏曲线 ( 形状 ) 的制品。吹塑成型起源于 19 世纪 30 年代。直到1979 年以后,吹塑成型才进入广泛应用的阶段。这一阶段,吹塑级的塑料包括:聚烯烃、工程塑料与弹性体;吹塑制品的应用涉及到汽车、办公设备、家用电器、医疗等方面;每小时可生产 6 万个瓶子也能制造大型吹塑件 ( 件重达 180kg) ,多层吹塑技术得到了较大的发展;吹塑设备已采用微机、固态电子的闭环控制系统,计算机 CAE/CAM 技术也日益成熟;且吹塑机械更专业化、更具特色。国外的情况 PET容器已经成为全球各国广泛使用的包装材料和容器,在食品、饮料、酒类、化妆品、日用品、工业用品、交通用品、农业用品包装等方面得到越来越广泛的应用,近年来PET 容器在饮料包装中的应用发展更为迅猛。如美国软饮料 PET 瓶的数量1990 年为76 亿只,1992 年达近100 亿只,1997 年超过200 亿只,2000 年和2001 年分别为220 亿只和225 亿只。由于PET 瓶的容量比金属罐和玻璃瓶都要大得多,所以PET 瓶装软饮料在容量比例上的优势更为明显,1990 年已为1/3,1993 年达4 成,1997 年以后均占到一半以上。美国一些啤酒厂正开始转向采用塑料瓶包装啤酒,并有增多的趋势。堪萨斯州的 DonyExpress 牌啤酒包装正在从玻璃瓶改用三层琥珀色 PET 塑料瓶,而且可以仍采用现有灌装设备。马里兰州的Constar 国际公司制备塑料瓶型坯和吹塑成型三层瓶,其外层和内层材料为PET,阻隔芯层材料为特殊尼龙MXD6。Constar 公司声称其还采用了高性能吸氧剂Oxbar,因而实际上没有氧渗入瓶的不良后果,并大大降低了碳酸气的速漏问题。 GreatPlains 啤酒公司于2003 年7 月6 日开始生产塑料瓶包装的啤酒,通过国内零售商分销给宾馆、运动场和娱乐场所。并计划想中国出口,该公司在 Olathe 的分厂目前每年能生产15000 个三层瓶中的阻隔层,并已订购设备进一步扩大生产能力。
吹塑成型说明书
课程设计 中空吹塑成型模具设计 姓名郭胜 学号 11051021032 院系机电工程学院 专业材料成型及控制工程年级 2011级 指导教师贾焕丽 2015年1月15日
目录 摘要 (1) 1 吹塑件结构与材料分析 (3) 1.1 软件简介 (3) 1.2 模具设计与制造的一般流程 (3) 1.3吹塑件结构分析 (5) 1.4吹塑件材料分析 (7) 2 吹塑模具的结构与材料分析 (8) 2.1吹塑模结构分析 (8) 2.2 吹塑模具的材料分析 (9) 3 挤出吹塑机头尺寸计算 (11) 3.1出模膨胀系数选择 (11) 3.2 挤出机头设计原则 (11) 4 吹塑模具的型腔的设计 (14) 4.1分型面选择 (14) 4.2型腔表面处理 (14) 4.3型腔尺寸计算 (14) 5 吹塑模具的颈部及底部嵌块设计 (16) 6 吹塑模具的夹坯口与余料槽设计 (18) 6.1剪口尺寸 (18) 6.2剪口部位 (19)
7 吹塑模具的冷却系统设计 (20) 7.1 冷却系统设计原则 (20) 7.2 开设冷却系统 (21) 8 吹塑模具的排气系统设计 (22) 9 成型设备选择 (23) 参考文献 (24) 致谢 (25)
摘要 根据矿泉水瓶的用途和使用要求进行分析,合理设计矿泉水瓶的形状造型结构,包括容积、壁厚、外形、底部和瓶口螺纹等的设计,并根据吹塑工艺选择制矿泉水瓶的材料。 矿泉水瓶吹塑模设计,采用平行移动式模具,设计内容包括模具材料选择、模具型腔、模具主体、冷却系统、切口部分、嵌块部分、排气孔槽和导向部分等。 根据本次设计的矿泉水瓶的功能、材料及各个工艺特点,吹塑工艺采用挤出吹塑,矿泉水瓶的成型包括成型设备和成型工艺条件等的分析设计。 关键词:矿泉水瓶;吹塑模;挤出吹塑;模具设计
挤出、注塑、吹塑三大塑料成型工艺介绍!
挤出、注塑、吹塑三大塑料成型工艺介绍!塑料成型加工是一门工程技术,所涉及的内容是将塑料转变为塑料制品的各种工艺。 注塑成型 注射成型,其原理是将粒状或粉状的原料加入到注射机的料斗里,原料经加热熔化呈流动状态,在注射机的螺杆或活塞推动下,经喷嘴和模具的浇注系统进入模具型腔,在模具型腔内硬化定型。影响注塑成型质量的要素:注入压力,注塑时间,注塑温度。 优点: 1、成型周期短、生产效率高、易实现自动化 2、能成型形状复杂、尺寸精确、带有金属或非金属嵌件的塑料制件 3、产品质量稳定 4、适应范围广 缺点: 1、注塑设备价格较高 2、注塑模具结构复杂 3、生产成本高、生产周期长、不适合于单件小批量的塑件生产 应用: 在工业产品中,注射成型的制品有:厨房用品(垃圾筒、碗、水桶、壶、餐具以及各种容器),电器设备的外壳(吹风机、吸尘器、食品搅拌器等),玩具与游戏,汽车工业的各种产品,其它许多产品的零件等。
挤出成型 挤出成型:又称挤塑成型,主要适合热塑性塑料的成型,也适合部分流动性较好的热固性和增强塑料的成型。其成型过程是利用转动的螺杆,将被加热熔融的热塑性原料,从具有所需截面形状的机头挤出,然后由定型器定型,再通过冷却器使其冷硬固化,成为所需截面的产品。工艺特点: 1、设备成本低; 2、操作简单、工艺过程容易控制、便于实现连续自动化生产; 3、生产效率高;产品质量均匀、致密; 4、通过改变机头口模可成型各种断面形状的产品或半成品。 应用: 在产品设计领域,挤出成型具有较强的适用性。挤出成型的制品种类有管材、薄膜、棒材、单丝、扁带、网、中空容器、窗户、门的框架、板材、电缆包层、单丝以及其它异型材等。 吹塑成型 吹塑成型:是将从挤出机挤出的熔融热塑性原料,夹入模具,然后向原料内吹入空气,熔融的原料在空气压力的作用下膨胀,向模具型腔壁面贴合,最后冷却固化成为所需产品形状的方法。吹塑成型分为薄膜吹塑和中空吹塑两种: 薄膜吹塑:
吹塑成型发展现状
吹塑成型发展现状 发布日期:2006-10-23 9:53: 摘要:介绍吹塑成型方法、吹塑成型控制因素及吹塑成型的新进展,讨论吹塑品质量的影响因素和常见制品缺陷的改进方法。吹塑成型技术是仅次于挤出成型、塑成型的第三类塑料成型方法,可生产具有复杂、不规则形状的中空制品。 吹塑,这里主要指中空吹塑 ( 又称吹塑模塑 ) 是借助于气体压力使闭合在模中的热熔型坯吹胀形成中空制品的方法,是第三种最常用的塑料加工方法,同时也发展较快的一种塑料成型方法。吹塑用的模具只有阴模 ( 凹模 ) ,与注塑成型相比,设备造价较低,适应性较强,可成型性能好 ( 如低应力 ) 、可成型具有复杂伏曲线 ( 形状 ) 的制品。吹塑成型起源于 19 世纪 30 年代。直到 1979 年以后吹塑成型才进入广泛应用的阶段。这一阶段,吹塑级的塑料包括:聚烯烃、工程塑与弹性体;吹塑制品的应用涉及到汽车、办公设备、家用电器、医疗等方面;每小可生产 6 万个瓶子也能制造大型吹塑件 ( 件重达 180kg) ,多层吹塑技术得到了大的发展;吹塑设备已采用微机、固态电子的闭环控制系统,计算机 CAE/CAM 技术也日益成熟;且吹塑机械更专业化、更具特色。笔者从吹塑成型方法、制品种类、量控制、发展趋势等方面予以介绍。 1 吹塑成型方法 1.1 成型方法 不同吹塑方法,由于原料、加工要求、产量及其成本的差异,在加工不同产品具有不同的优势。详细的吹塑成型过程可参考文献。这里从宏观角度介绍吹塑的特点。中空制品的吹塑包括三个主要方法:挤出吹塑:主要用于未被支撑的型坯加工注射吹塑:主要用于由金属型芯支撑的型坯加工;拉伸吹塑:包括挤出一拉伸一吹塑、注射一拉伸一吹塑两种方法,可加工双轴取向的制品,极大地降低生产成本和进制品性能。此外,还有多层吹塑、压制吹塑、蘸涂吹塑、发泡吹塑、三维吹塑等但吹塑制品的 75 %用挤出吹塑成型, 24 %用注射吹塑成型, 1 %用其它吹塑成型;在所有的吹塑产品中, 75 %属于双向拉伸产品。挤出吹塑的优点是生产效率高,设备成本低,模具和机械的选择范围广,缺点是废品率较高,废料的回收、利差,制品的厚度控制、原料的分散性受限制,成型后必须进行修边操作。注射吹塑优点是加工过程中没有废料产生,能很好地控制制品的壁厚和物料的分散,细颈产成型精度高,产品表面光洁,能经济地进行小批量生产。缺点是成型设备成本高,
吹塑工艺控制要点
大多数热塑性塑料都可以用吹塑法来生产吹塑薄膜,吹塑薄膜是将塑料挤成薄管,然后趁热用压缩空气将塑料吹胀,再经冷却定型后而得到的筒状薄膜制品,这种薄膜的性能处于定向膜同流延膜之间:强度比流延膜好,热封性比流延膜差。吹塑法生产的薄膜品种有很多,比如低密度聚乙烯(LDPE)、聚丙烯(PP)、高密度聚乙烯(HDPE)、尼龙(PA)、乙烯一乙酸乙烯共聚物(EVA)等,这里我们就对常用的低密度聚乙烯(LDPE)薄膜的吹塑生产工艺及其常见故障进行简单的介绍。 聚乙烯吹塑薄膜材料的选择 1.选用的原料应当是用吹膜级的聚乙烯树脂粒子,含有适量的爽滑剂,保证薄膜的开口性。 2.树脂粒子的熔融指数(MI)不能太大,熔融指数(MI)太大,则熔融树脂的粘度太小,加工范围窄,加工条件难以控制,树脂的成膜性差,不容易加工成膜;此外,熔融指数(MI)太大,聚合物相对分子量分布太窄,薄膜的强度较差。因此,应当选用熔融指数(MI)较小,且相对分子量分布较宽的树脂原料,这样既能满足薄膜的性能要求,又能保证树脂的加工特性。吹塑聚乙烯薄膜一般选用熔融指数(MI)在2~6g/10min范围之间的聚乙烯原料。 吹塑工艺控制要点 吹塑薄膜工艺流程大致如下: 料斗上料一物料塑化挤出→吹胀牵引→风环冷却→人字夹板→牵引辊牵引→电晕处理→薄膜收卷 但是,值得指出的是,吹塑薄膜的性能跟生产工艺参数有着很大的关系,因此,在吹膜过程中,必须要加强对工艺参数的控制,规范工艺操作,保证生产的顺利进行,并获得高质量的薄膜产品。在聚乙烯吹塑薄膜生产过程中,主要是做好以下几项工艺参数的控制: 1.挤出机温度 吹塑低密度聚乙烯(LDPE)薄膜时,挤出温度一般控制在160℃~170℃之间,且必须保证机头温度均匀,挤出温度过高,树脂容易分解,且薄膜发脆,尤其使纵向拉伸强度显著下降;温度过低,则树脂塑化不良,不能圆滑地进行膨胀拉伸,薄膜的拉伸强度较低,且表面的光泽性和透明度差,甚至出现像木材年轮般的花纹以及未熔化的晶核(鱼眼)。 2.吹胀比 吹胀比是吹塑薄膜生产工艺的控制要点之一,是指吹胀后膜泡的直径与未吹胀的管环直径之间的比值。吹胀比为薄膜的横向膨胀倍数,实际上是对薄膜进行横向拉伸,拉伸会对塑料分子产生一定程度的取向作用,吹胀比增大,从而使薄膜的横向强度提高。但是,吹胀比也不能太大,否则容易造成膜泡不稳定,且薄膜容易出现皱折。因此,吹胀比应当同牵引比配合适当才行,一般来说,低密度聚乙烯(LDPE)薄膜的吹胀比应控制在2.5~3.0为宜。 3.牵引比 牵引比是指薄膜的牵引速度与管环挤出速度之间的比值。牵引比是纵向的拉伸倍数,使薄膜在引取方向上具有定向作用。牵引比增大,则纵向强度也会随之提高,且薄膜的厚度变薄,但如果牵引比过大,薄膜的厚度难以控制,甚至有可能会将薄膜拉断,造成断膜现象。低密度聚乙烯(LDPE)薄膜的牵引比一般控制在4~6之间为宜。 4.露点 露点又称霜线,指塑料由粘流态进入高弹态的分界线。在吹膜过程中,低密度聚乙烯(LDPE)在从模口中挤出时呈熔融状态,透明性良好。当离开模口之后,要通过冷却风环对膜泡的吹胀区进行冷却,冷却空气以一定的角度和速度吹向刚从机头挤出的塑料膜泡时,高