贵州大学《冲压工艺及模具设计》课设
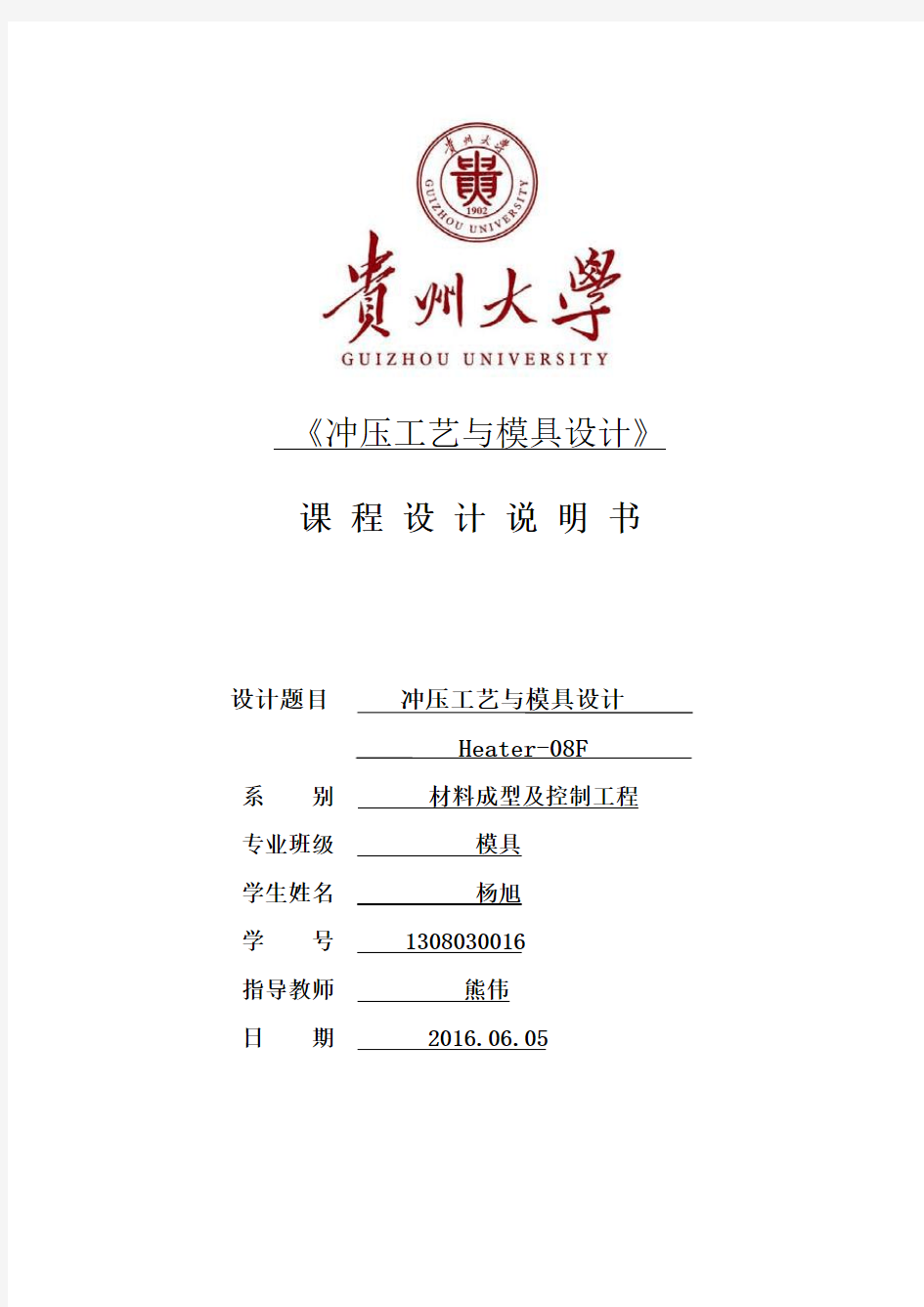
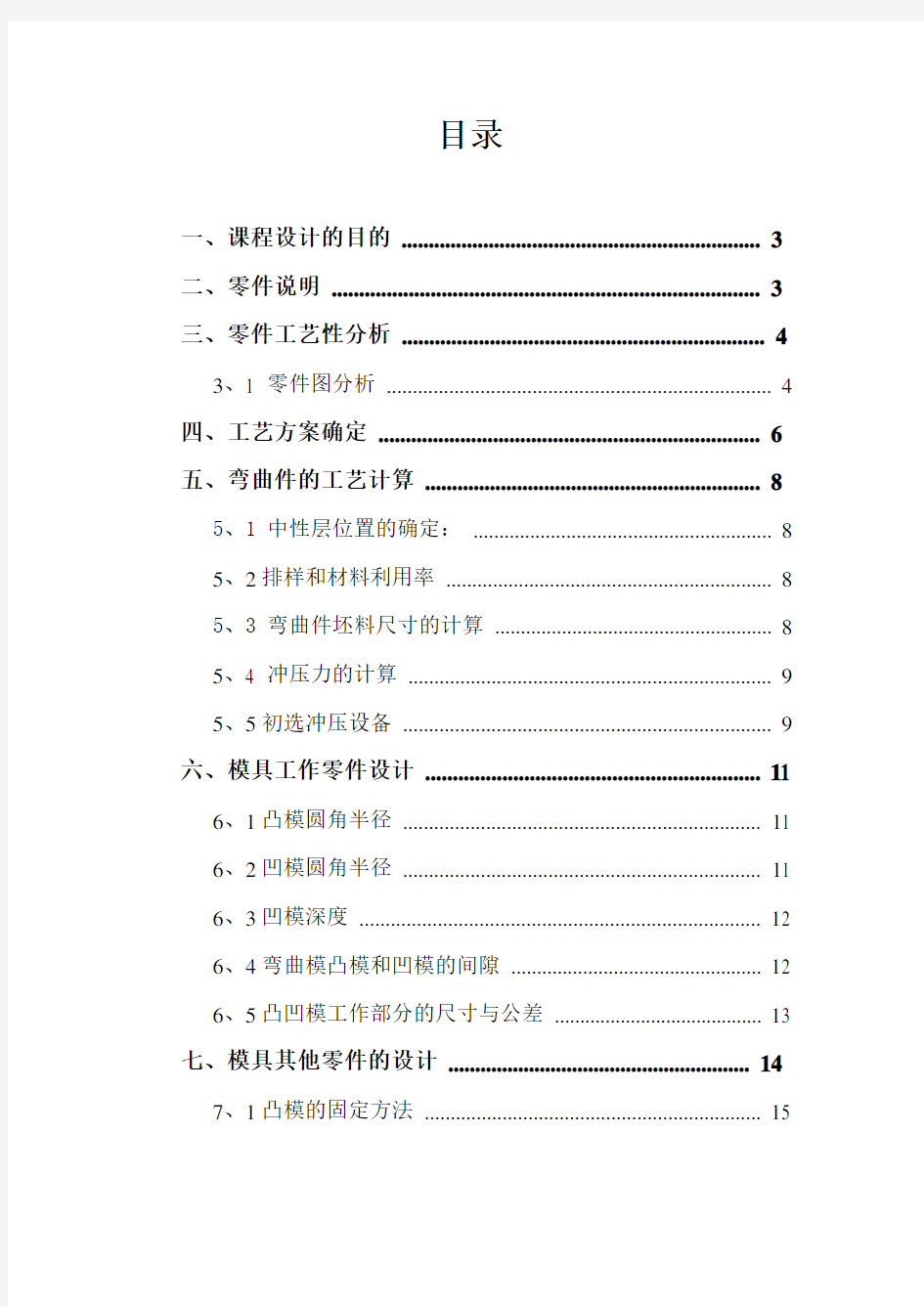
《冲压工艺与模具设计》
课程设计说明书
设计题目冲压工艺与模具设计
Heater-08F
系别材料成型及控制工程
专业班级模具
学生姓名杨旭
学号 1308030016 指导教师熊伟
日期 2016.06.05
目录
一、课程设计的目的 (3)
二、零件说明 (3)
三、零件工艺性分析 (4)
3、1 零件图分析 (4)
四、工艺方案确定 (6)
五、弯曲件的工艺计算 (8)
5、1 中性层位置的确定: (8)
5、2排样和材料利用率 (8)
5、3 弯曲件坯料尺寸的计算 (8)
5、4 冲压力的计算 (9)
5、5初选冲压设备 (9)
六、模具工作零件设计 (11)
6、1凸模圆角半径 (11)
6、2凹模圆角半径 (11)
6、3凹模深度 (12)
6、4弯曲模凸模和凹模的间隙 (12)
6、5凸凹模工作部分的尺寸与公差 (13)
七、模具其他零件的设计 (14)
7、1凸模的固定方法 (15)
7、2定位装置的设计 (15)
7、3模柄的选择 (15)
7、4 模架的选择 (16)
7、5紧固件及其它零件的选用 (16)
7、6垫板的确定 (16)
7、7顶件装置选用 (16)
八、该模具设计的优缺点 (18)
九、填写工艺卡片 (19)
十、心得体会 (21)
十一、参考文献 (22)
一、课程设计的目的
本课程设计是在学生学完“冲压工艺与模具设计”理论课并进行了生产实习之后进行的一个重要教学环节。是学生运用所学理论,联系实际,提高工程技术能力和培养严谨细致作风的一次重要机会。通过本次设计要达到以下目的:
1、巩固与扩充“冲压工艺与模具设计”以及有关技术基础课程所学的内容,掌握制订冲压工艺规程和设计冲压模具的方法。
2、培养综合运用本专业所学课程的知识,解决生产中实际问题的工程技术能力(包括:设计、计算、绘图、技术分析与决策、文献检索以及撰写技术论文的能力)。
3、养成严肃、认真、细致地从事技术工作的优良作风。
近几年来,我国模具技术有了很大发展,模具设计与制造水平有了较大提高,大型、精密、复杂高效和长寿命模具的需求量大幅度增加,模具质量、模具寿命明显提高,模具交货期较前缩短,模具CAD/CAM技术也得到了相当广泛的应用。冲压技术广泛应用于航空、汽车、电机、家电和通信等行业零部件的成形。由于冲压工艺具有生产率高,能成形复杂零件,适合大批量生产等优点,在某些领域已经取代机械加工,并正逐步扩大其应用范围。据国际生产技术协会预测到本世纪中,机械零部件中60%的粗加工,80%的精加工要由模具来完成。因此冲压技术对发展生产、增加效益、更新产品等方面具有重要作用。
二、零件说明
制件如下图所示:
该制件名称为Heater,其技术要求为:
1,未注尺寸公差按GB/T15505的m级;
2,毛刺小于0.15;
3,质件要求平整,不允许有拉裂、起皱的现象; 4,中批量生产;
材料:08F,t=1.0mm
三、零件工艺性分析
3、1 零件图分析
表2——1
结合三视图和三维图分析:零件是Heater,材料是08F,属于优质碳素结构钢,强度、硬度低,塑性极好,深冲压、深拉延性好,冷加工性、焊接性好,成分偏析倾向大,时效敏感性大,故冷加工时,可采用消除应力热处理或水韧处理,防止冷加工断裂。
化学成分(%):C:0.05~0.11,Si≦0.03,Mn:0.25~0.50,Cr≦0.10,Ni≦0.30,Ca≦0.25
力学性能:抗剪强度
b 为270~340MP
a
,抗拉强度σ
b
不小于300MP
a
,屈服
强度σ
s 为180MP
a
,断面收缩率60%,伸长率不小于35%。材料厚度是1mm,精度
无特殊要求,要求表面无划痕,孔不允许严重变形。
该件为带有孔和折弯的对称件,尺寸精度要求不高,由冲裁和弯曲就可以成形,冲裁的难点在于先折外角后,然后在折内角。
生产批量:大批量;
设备情况、械具制造条件及水平;
各种技术标准、设计手册及有关资料。
四、工艺方案确定
完成此工件需要落料、冲孔和弯曲三道工序。其加工工艺方案分为以下:(一)方案种类。
根据制件工艺性分析,要加工此零件,分析出以下四种方案。
方案一:1)落料与冲孔复合;2)弯曲外角;3)弯曲U形内角;4)弯曲L形内角;
方案二:1)落料与冲孔复合;2)弯曲U形内角;3)弯曲L形内角;4)弯曲外角;
方案三:1)落料与冲孔复合;2)弯曲外角;3)弯曲L形内角;3)弯曲U形内角;
(二):方案分析并选出最优方案。
方案一的优点:模具结构简单,寿命长,制造周期短,工件的回弹易控制,操作简单,工人劳动强度低,取件容易。
方案二在内角后再弯曲外角,势必会增加弯曲步骤,加大弯曲难度,取件难,使工件的精度降低,生产率下降,生产成本增加。
方案三具有方案一得优点,但是方案一在最后一步弯曲L形内角更好定位。相比方案一、方案二和方案三在操作、成本、生产率上及定位上,本设计模具采用方案一。
模具压力中心是指冲压时各个冲压部分冲压力合力的作用点。为了确保压力机和模具正常工作,应使冲模的压力中心与压力机滑块的中心相重合。对于带有模柄的冲压模,压力中心应通过模柄的轴心线。否则会使冲模和压力机滑块产生偏心载荷,使滑块和导轨之间产生过大的磨损,模具导向零件加速磨损,降低模具和压力机的使用寿命。
冲模的压力中心,可按下述原则来确定:
(1)对称形状的单个冲裁件,冲模的压力中心就是冲裁件的几何中心。冲裁直线段时,其压力中心位于直线段的中点。
(2)工件形状相同且分布位置对称时,冲模的压力中心与零件的对称中心相重合。
(3)冲裁形状复杂的零件或多凸模的零件时,其压力中心可以通过解析计算法求出。
现在需要冲孔的零件是一个筒状件,在其底部正中心需要冲孔,所以其压力中心就是其几何中心。
五、弯曲件的工艺计算
5、1 中性层位置的确定:
直边段L1, L2,L1=25.04mm ,L2=115.4mm 由公式: xt r p += 式中 r —零件的内弯曲半径 t —板料的厚度 x —中性层位移系数
查表4-4[]1可得板料弯曲时中性层位移系数5.0x = 则
mm xt r p 5.115.01=?+=+=
5、2排样和材料利用率
由于坯料形状为矩形,采用单排排料最便宜,取搭边a1=2.8mm,a2=2.4mm,板
料宽度为B=160.4+2×2.8=166.0mm ;进距h 为88+2.4=90.4mm ;板料选用规格为4mm ×900mm ×2000mm 。 采用纵裁时:
每板条料树n1=900/166=5条,余70mm , 每条制件数n2=(2000-2.8)/90.4=22件,
33.8×2000余料利用件数n3=2000/166=12件,余8mm 。
由此可知,纵单排排料材料利用率高,从弯曲纤维方向性上,横向单排排料最好,由于材料08F 塑性好,故采用纵向单排排样,以降低成本,提高经济性,达到最优方案。
5、3 弯曲件坯料尺寸的计算
根据零件特性,进行折弯时,零件折弯半径只有1mm,而板厚为1mm 则使用圆角半径r >0.5t 的弯曲件计算。
由公式:180
)xt r (L L 180L L L 2121Z +π?++=πρ?
+
+= 式中 Lz —坯料展开总长度 ?—弯曲中心角
则根据实际坯料零件尺寸,设L 1=35mm L 2=130mm. 得出零件展开尺寸为
mm xt r L L L L L Z 04.212180
5
.239030153180
)
(180
2121=??+
+=++
+=+
+=ππ?πρ?
5、4 冲压力的计算
由于弯曲力受到材料的力学性能,零件形状与尺寸,板料厚度,弯曲方式,模具结构形状与尺寸,模具间隙和模具工件表面质量等多种因素的影响,很难用理论分析方法进行准确计算。因此,在生产中均采用经验公式估算弯曲力。L 形弯曲件是在自由弯曲阶段相当于弯曲U 形件的一半,而且应设置压料装置,所以可近似地取弯曲力为:(由于二次弯曲,按U 形弯曲计算。)
自由弯曲力 F1=)/(2t r kbt p b +σ=0.7*88*1*1*300/(0.4+1)=13200N 校正弯曲力 F2=QP=88*76*80=535040N 为了可靠起见,将F1与F2和在一起, 即F0=F1+F2=548240N
5、5初选冲压设备
确定压力机的额定压力不仅要考虑能完成弯曲加工,而且要注意防止压力机过载。由于前述计算所得的弯曲力均为弯曲过程中可能出现的最大弯曲力数值,即短时间内出现的峰值,如果压力机的额定压力等于或略大于该计算值,并不能保证在整个弯曲过程中压力机不过载。因此,在确定压力机的压力时,应预留出较大的安全范围。
一般情况下,压力机的公称压力应大于或等于冲压总工艺力的1.3倍,可以取压力机的压力为
F 压机≥1.3 F 总
代入数据得:
F
≥712.4KN
压机
查表9-4[]2,初选压力机J23-80,其主要技术参数为:
六、模具工作零件设计
6、1凸模圆角半径
弯曲件的相对弯曲半径t
r
较小时,凸模角半径凸r 可取弯曲件的内弯曲半径r ,
但不能小于允许的最小弯曲半径m in r 。如果t
r
值小于最小相对弯曲半径,应先弯
成较大的圆角半径,然后再用整形工序达到要求的圆角半径。当弯曲件的相对弯
曲半径t
r
较大且精度要求较高时凸模圆角半径应根据回弹值进行修正。
由于影响t
r min
的因素很多,t r min 值的理论计算公式并不实用。所以在生产中
主要参考经验数据来确定
t
r min
值。查表4-2[]1可查得: 08钢在垂直于纤维方向时,最小相对弯曲半径
1.0t
r min
=。 由于该制件的相对弯曲半径r/t 较小,故凸模圆角半径凸r 需根据弯曲件的回弹值来进行相应的修正。
6、2凹模圆角半径
凹模圆角半径凹r 的大小直接影响坯料的弯曲成形。凹模的圆角半径凹r 不能过小,否则弯曲时坯料拉人凹模的阻力大,厚度易拉薄,擦伤工件表面。凹r 太大,会影响毛坯定位的准确性。凹r 的值通常按材料厚度t 来选取。 查表4-9[]1得当板料厚度t 为1mm 时 凹模圆角半径mm t r 6~3)6~3(==凹
6、3凹模深度
凹模的工件深度将决定板料的进模深度,对于常见的弯曲件,弯曲时不需全部直边进入凹模内。只有当直边长度较小且尺寸精度要求高时,才能直边全部进入凹模内,凹模深度过大,不仅增加模具的消耗,而且将增加压力机的工作进程,使最大弯曲力提前出现。中小型弯曲件通常都使用模具在机械压力机上进行加工,最大弯曲力提前出现,对压力机是很不利的。凹模深度过小,可能造成弯曲件直边不平直,降低其精度。因此,凹模深度要适当。
对于弯边高度不大或要求两边平直U 形件,凹模深度应大于零件高度,高差用m 表示。
查表4-11[]1得3m = 则凹模深度mm 40L 0=
6、4弯曲模凸模和凹模的间隙
弯曲L 形时,必须选择适当的凸、凹模间隙。间隙过大则回弹量大,工件的形状和尺寸误差增大。间隙过小,使弯曲力增大,直边壁厚变薄,增大摩擦,容易擦伤工件表面,加速凹模的磨损,降低凹模的使用寿命。
同时考虑到下列因素的影响:弯曲件宽度较大时,受模具制造和装配误差的影响,将加大间隙的不均匀程度,因此间隙应取大些。宽度较小时间隙值可以取小些,硬材料则应取大些,弯曲件相对弯曲半径r/t 较小时可以取大些。此外还应考虑弯曲尺寸精度和板料厚度偏差的影响。
U 形件弯曲模的凹、凸模单边间隙可按下式计算:
ct t Z +=max 式中 Z —弯曲模的凹、凸模单边间隙 t —工件材料厚度,t=1mm max t —工件的最大厚度,max t =1mm c —间隙系数,查表4-13[]1取c=0.1
计算,可得Z=1.1t=1.1mm
6、5凸凹模工作部分的尺寸与公差
模具工作零件结构的确定即弯曲模凸、凹模工作尺寸的确定。
弯曲凸、凹模工作尺寸的计算与工件尺寸的标注行成有关。一般原则是:当工件标注为外形尺寸时,应以凹模为基准件,间隙取在凸模上,弯曲间隙通过增大凹模刃口尺寸取得,并以此配作凹模;当工件标注内行尺寸时,应以凸模为基准件,
综上所述,根据图4-34[]1,以凹模为计算基准件,可得: 凹模 凹凹凸
δ++=0
)Z 2(L L (4-23)
凸模 0
_min )75.0(凸凸δ?+=L L (4-24) 式中 凹L —凹模的基本尺寸 凸L —凸模的基本尺寸 max L —弯曲件的最大极限尺寸 △—弯曲件的宽度的尺寸公差
凹δ,凸δ—凹模、凸模的制造公差,一般按IT9级选用 Z 为凹、凸模双面间隙
查互换性表1——8得偏差79偏差为0.087mm,32.5偏差为0.062 将数据代入式(4-21)、(4-22)得:
0087.007.790087.0087.075.0790)75.0min (-=-?+=-?+=)(凸
凸δ
L L mm;
087
.00
087.00027.811.1207.79Z)2L +++=?+=+=)((凹凸凹δL mm;
0_)75.0min (凸
凸δ?+=L L =78.070087.0-mm