过氧化法制备对苯二酚

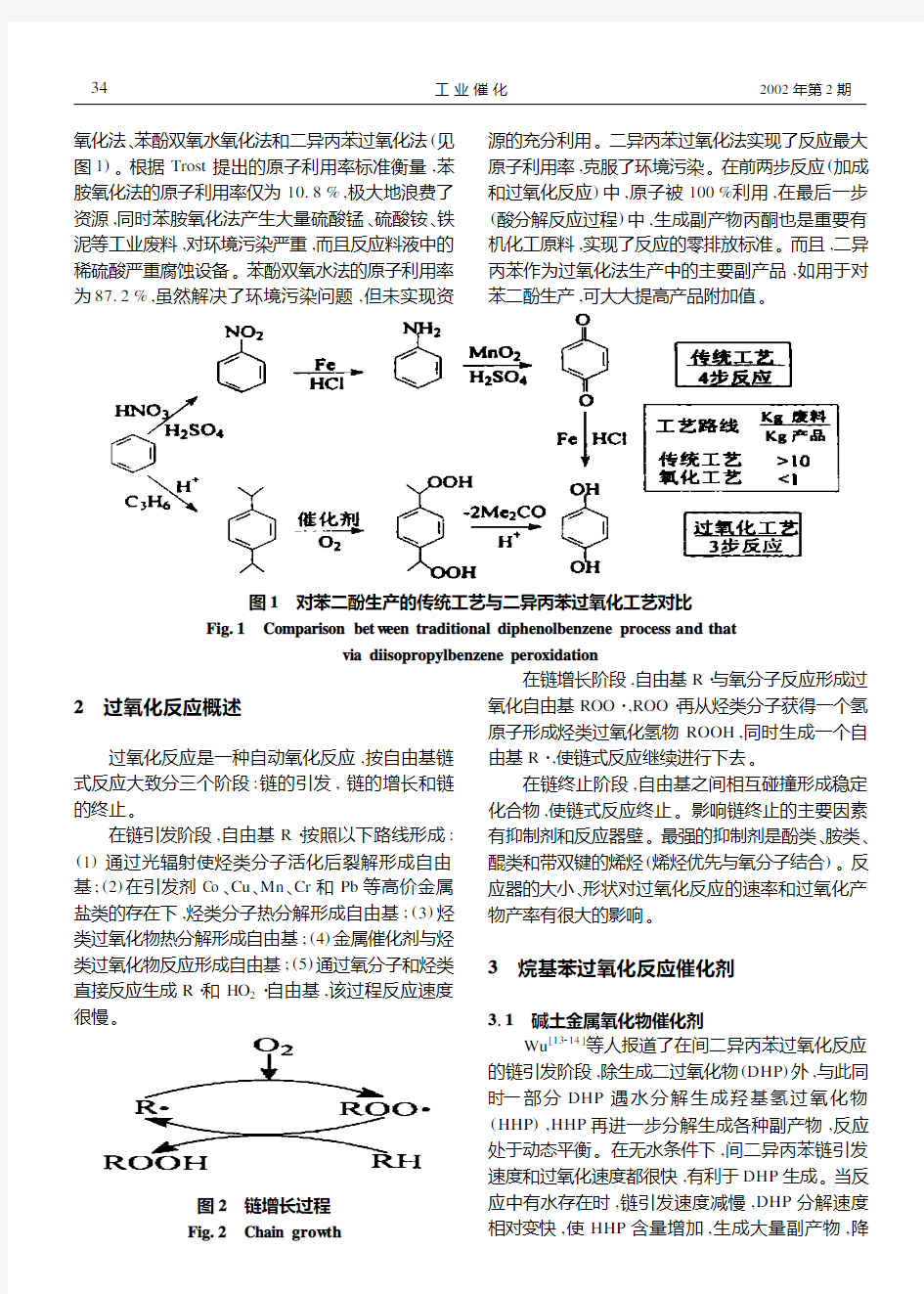
收稿日期:2001211207
作者简介:王日杰(1962—
),男,辽宁省人,博士,副教授,研究方向为工业催化。有机化工与催化
烷基芳烃过氧化反应及其催化剂研究进展
王日杰,薛常海,张继炎
(一碳化工国家重点实验室,天津大学化工学院,天津300072)
摘 要:烷基芳烃过氧化反应是酚类合成反应的关键步骤。与传统的酚类合成路线相比,该反
应具有低污染、100%原子利用率等优点,是理想的绿色合成路线。本文简要叙述了烷基芳烃过氧化反应的各类催化剂研究进展。
关键词:绿色化学;自由基;过氧化反应中图分类号:O625.1;TQ426.6 文献标识码:A 文章编号:100821143(2002)022*******
R esearches in peroxid ation of alkyl arom atics and the catalyst
W A N G Ri 2jie ,X U E Chang 2hai ,ZHA N G Ji 2yan
(State key Laboratory C 1chemistry ,School of chemical Engineering ,
Tianjin University ,Tianjin 300072,China )
Abstract :Peroxidation of alkyl aromatics is the key step to synthesis of https://www.360docs.net/doc/9f12942492.html,pared with traditional phenol synthesis routes ,the reaction is featured by low pollution and 100%utilization of reactant atoms ,which makes it an ideal green synthesis route.This article reviews researches in various catalysts for alkyl aromatics peroxidation.K ey w ords :green chemistry ;radical ;peroxidation
C LC number :O625.1;TQ426.6 Document code :A Article I
D :100821143(2002)022*******
烷基芳烃过氧化反应的产物是重要的化工原料,广泛用于漂染、聚合引发剂等。同时,该反应还是由异丙基取代芳烃制备其对应的酚类化合物的关键反应步骤之一,具有低污染、100%原子利用率的优点。异丙苯过氧化合成苯酚由Hock 和Lang 发现,并最先实现工业化,是一条绿色合成苯酚工艺路线,广泛被世界各国采用。随着异丙苯过氧化制苯酚的工业化成功和对环境保护的要求日益提高,二异丙苯、异丙基萘和二异丙苯基萘等的过氧化反应也受到广泛重视。目前广泛研究的过氧化反应有异丙苯[124]、二异丙苯[5]、异丙基萘[627]、间异丙基甲苯[8]、乙苯[9210]、二异丙基萘的过氧化反应等。本文就催化过氧化反应进展加以评述。
1 过氧化反应———理想的绿色合成反应
美国化学家Trost 首次提出原子经济性概
念[11],认为高效的有机合成应最大限度地利用原料分子的每一个原子,使之全部结合到目标产物分子中,达到零排放的目的。原子经济性可以用原子利用率衡量:
原子利用率%=
目标产物的分子量
参加反应物质的原子质量总和×100% 同传统的酚类生产工艺对比,过氧化法工艺是较为理想的绿色合成工艺路线[12]。以对苯二酚生产工艺为例,目前世界主要的生产路线可分为苯胺
第10卷 第2期
2002年3月
工业催化INDUSTRIAL CA TAL YSIS Vol.10 No.2Mar .2002
氧化法、苯酚双氧水氧化法和二异丙苯过氧化法(见
图1)。根据Trost 提出的原子利用率标准衡量,苯胺氧化法的原子利用率仅为10.8%,极大地浪费了资源,同时苯胺氧化法产生大量硫酸锰、硫酸铵、铁泥等工业废料,对环境污染严重,而且反应料液中的稀硫酸严重腐蚀设备。苯酚双氧水法的原子利用率为87.2%,虽然解决了环境污染问题,但未实现资
源的充分利用。二异丙苯过氧化法实现了反应最大原子利用率,克服了环境污染。在前两步反应(加成和过氧化反应)中,原子被100%利用,在最后一步(酸分解反应过程)中,生成副产物丙酮也是重要有机化工原料,实现了反应的零排放标准。而且,二异丙苯作为过氧化法生产中的主要副产品,如用于对苯二酚生产,可大大提高产品附加值
。
图1 对苯二酚生产的传统工艺与二异丙苯过氧化工艺对比Fig.1 Comparison bet w een traditional diphenolbenzene process and that
via diisopropylbenzene peroxidation
2 过氧化反应概述
过氧化反应是一种自动氧化反应,按自由基链
式反应大致分三个阶段:链的引发,链的增长和链的终止。
在链引发阶段,自由基R ?按照以下路线形成:(1)通过光辐射使烃类分子活化后裂解形成自由基;(2)在引发剂Co 、Cu 、Mn 、Cr 和Pb 等高价金属盐类的存在下,烃类分子热分解形成自由基;(3)烃类过氧化物热分解形成自由基;(4)金属催化剂与烃类过氧化物反应形成自由基;(5)通过氧分子和烃类直接反应生成R ?和HO 2?自由基,该过程反应速度很慢
。
图2 链增长过程Fig.2 Chain grow th
在链增长阶段,自由基R ?与氧分子反应形成过
氧化自由基ROO ?,ROO ?再从烃类分子获得一个氢原子形成烃类过氧化氢物ROOH ,同时生成一个自由基R ?,使链式反应继续进行下去。
在链终止阶段,自由基之间相互碰撞形成稳定化合物,使链式反应终止。影响链终止的主要因素有抑制剂和反应器壁。最强的抑制剂是酚类、胺类、醌类和带双键的烯烃(烯烃优先与氧分子结合)。反应器的大小、形状对过氧化反应的速率和过氧化产物产率有很大的影响。
3 烷基苯过氧化反应催化剂
311 碱土金属氧化物催化剂
Wu [13214]等人报道了在间二异丙苯过氧化反应
的链引发阶段,除生成二过氧化物(DHP )外,与此同时一部分DHP 遇水分解生成羟基氢过氧化物(HHP ),HHP 再进一步分解生成各种副产物,反应处于动态平衡。在无水条件下,间二异丙苯链引发速度和过氧化速度都很快,有利于DHP 生成。当反
应中有水存在时,链引发速度减慢,DHP 分解速度相对变快,使HHP 含量增加,生成大量副产物,降
34
工业催化 2002年第2期
低了DHP的选择性。在对二异丙苯过氧化中,当碱土金属氧化物BaO催化剂的加入量为01002%~0.025%(wt),氧分压3415~1376kPa,引发剂015%~5%(wt),反应温度80~100℃时,催化效果最好,过氧化物收率可以达到35145mol%。BaO催化剂粒径5~20毫米,可以促进其在反应液中的扩散,提高反应速度。少量BaO催化剂与反应的有机物相发生反应变成乳状,提高了二异丙苯过氧化反应选择性。反应结束后停止搅拌,保持反应温度, BaO仍然在乳液相中,但降到室温后,乳状BaO催化剂重新变为颗粒状BaO催化剂,溶液恢复澄清状态。
312 过渡金属氧化物催化剂
Varma[15]在反应温度80℃条件下,对Co3O4、MnO2、NiO、Cu2O等过渡金属氧化物催化剂进行了异丙苯过氧化反应研究。当催化剂的加入量均为0.1g/ml时(以异丙苯为基准),催化剂的反应活性顺序为:Co3O4>MnO2>NiO>Cu2O。催化剂加入量存在临界值,当催化剂加入量超过临界值后,反应速率急剧下降。Co3O4临界值为1185g/ml。Varma 将这种现象解释为催化剂表面存在着对反应有利的活性吸附中心和阻碍反应活性的吸附中心。阻碍反应的吸附活性中心优先吸附过氧化物,但不形成自由基;而有利反应吸附活性的中心在阻碍反应活性吸附中心饱和吸附后,开始吸附过氧化物形成RO?自由基,引发反应进行。催化剂作用机理分为存在过氧化物和无过氧化物两种情况,见表1。
表1 过氧化物对引发机理的影响(M代表催化剂) T able1Inflence of peroxide on initiation
machanism for the reaction(M:catalyst)
无过氧化物引发机理有过氧化物引发机理
CO3++RH→R?+CO2++H+ROOH…M→RO?…M+?OH…M
2Co2++1
2
O2→2Co3++O2-RO?…M+RH→ROH+R?
2H++O2-→H2O?OH…M+RH→H2O+R?
Srivastava[16]考察了Cr2O3、MnO2、Fe2O3催化剂对异丙苯过氧化反应的影响,在催化剂加入量均为0101g/ml条件下,催化剂反应活性顺序为:MnO2 >Fe2O3>Cr2O3。催化剂加入量同样存在临界值。Cr2O3、MnO2和Fe2O3加入量的临界值分别为019g/ml、011g/ml和111g/ml。Fe2O3、NiO/Al2O3和NiO/C的活化能分别为4110kJ/mol、6619kJ/mol 和5114kJ/mol。
Maksimov[19]通过溶胶凝胶法,以ZrO2、TiO2、Al2O3为载体制备了负载型氧化物催化剂,并对其在异丙苯过氧化反应中的活性中心研究表明,催化剂表面的铁活性中心决定催化剂活性。至少存在两种以上同FeO6多面体有关的催化剂表面活性中心,一种是Fe=O端基中的氧原子通过电子激发造成电子从O2-到Fe3+的移动,获得由表面氧阴离子自由基所形成的活性中心;另一种是催化剂的表面结构缺陷所形成的活性中心,当Fe2O/ZrO2催化剂中Fe含量很低时(015wt%),Fe=O端基与载体的相互作用造成了这种表面缺陷的高活性。
313 碱/过渡金属氧化物复合催化剂
Takac[18,19]研究了过渡金属铜氧化物催化剂对异丙基萘过氧化反应的作用。发现NaOH溶液+ Cu2O催化剂的反应速率高于NaOH溶液+CuO催化剂,但前者的选择性(65%)低于后者(75%)。Takac认为:铜氧化物是通过铜原子的氧化还原反应产生自由基来实现过氧化反应的催化作用。由于Cu2O活泼性高于CuO,所以在Cu2O+NaOH溶液作用下反应速率高于CuO+NaOH溶液。NaOH溶液对二异丙基萘过氧化反应有很好的催化活性,但Na+离子浓度过高时,由于过氧化物的分解,会导致收率和选择性降低。NaOH溶液通过Na2O2实现对反应的催化作用。当Cu+/Na+非常低和非常高时,催化剂中分别是NaOH和CuO作为主催化剂。在低Cu+/Na+时,过氧化物收率很低;随着Cu+/Na+增加,过氧化物收率增加;当Cu+/Na+过高时,过氧化物收率也降低。存在一个临界最佳Cu+/Na+范围,使过氧化反应收率、选择性最佳。纯氧和空气对反应的作用相同,相同条件下,反应选择性、收率相同
。
图3 冠醚化双西佛钴催化剂
Fig.3 Crow ned Schiff’s B ase Cobalt C atalyst
秦圣英[20,21]由苯并2152冠25,经二硝基化后还原制得4’,5’2二氨基苯并215冠25,再与水杨醛及其
2002年第2期 王日杰等:烷基芳烃过氧化反应及其催化剂研究进展 35
衍生物反应,合成了冠醚化双西佛钴催化剂(见图3)。该催化剂克服了水杨醛西佛碱合钴易失活的缺点,能够可逆吸附分子氧。同时由于引入了取代基,实现了通过电子效应,增大空间位阻和疏水性来调控中心金属离子的配位环境,有利于与分子氧形成1:1加合物。这种加合物是催化氧化反应中的活性物种。在用空气作氧源、常压和其它条件相同的情况下,冠醚化络合物催化剂比非冠醚化络合物催化剂能更有效地加速异丙苯过氧化反应的进行,反应一段时间后,又能加速异丙苯过氧化物分解成苯乙酮。
张铭俊[8]以间异丙基甲苯为原料,考察了无机盐(硫酸铜、碳酸锆、硫酸铈、硫酸镉、硫酸钍)、有机盐(乙酸锆、乙酸锌、硬脂酸镉、环烷酸镁、环烷酸锌、环烷酸镉)、金属络合物(乙酰丙酮铜、水杨醛铜、西佛碱铜、甘氨酸铜、乙酰丙酮甘氨酸铜等)、有机碱(四乙基氢氧化铵、四丁基氢氧化铵、四甲基氢氧化铵)、有机膦(三苯基膦)和含氮有机物(联吡啶、四甲基吡啶)催化剂对间异丙基甲苯过氧化反应影响。无机铜盐和铜的络合物虽然缩短了反应时间,但反应收率(217%~311%)和选择性(615%~719%)大幅降低,而其它无机金属盐、金属络合物、有机碱、有机膦和含氮化合物对反应收率(16%~22%)和选择性(60%~75%)无明显影响。金属有机盐虽然比金属无机盐易溶解在有机相中,增加了催化剂在反应液相中的分配比例,但对反应仍无明显促进作用。文献提出一种复合催化剂9023,可以缩短反应时间近一半,提高反应的选择性3~4个百分点。
314 以高分子聚合物为载体的负载型催化剂文献报道[22224]分别将016mmol的Cu(OAc)2负载于110g离子交换树脂Chelex100(简写为CHX)、聚乙烯吡啶、SiO2载体上,并在80℃、常压反应条件下考察了各自的异丙苯催化氧化性能。结果表明,以CHX为载体所构成的催化剂Cu(OAc)22 CHX2016效果最佳(异丙苯转化率为5136%,CHP 选择性9914%)。将相同摩尔量的Mn(OAc)2、Co (OAc)2、Ni(OAc)2、FeCl2分别负载于110gCHX载体上,所得异丙苯的氧化速度为:Mn(Ⅱ)>Cu(Ⅱ) >Co(Ⅱ)>Ni(Ⅱ)>Fe(Ⅱ)。Mn(OAc)22CHX2016催化剂易催化CHP分解成22苯基222丙醇,因而CHP选择性较低。将Cu(OAc)2负载于苯乙烯2二乙烯苯共聚物上得到Cu(OAc)22BR2016催化剂,在相同条件下得到类似结果(异丙苯转化率为6.8%,选择性为99%)。该催化剂在110℃能保持稳定,氧化速率可通过增大催化剂用量与金属负载量、提高反应温度等手段加以提高。聚合物载体的作用在于其骨架能够阻止金属中心的配位环境发生改变,减少了反应过程中目标产物CHP的分解反应。此类金属负载型催化剂的氧化速率顺序如下:Mn (OAc)22BR2016>Co(OAc)22BR2016>FeCl22BR2 016>Cu(OAc)22BR2016>Cr(NO3)32BR2016>Ni (OAc)22BR2016。催化剂具有高选择性,但活性相对较低。
4 结 论
根据上述对各种烷基芳烃过氧化反应催化剂的研究推测,单一类型催化剂不能实现对过氧化反应的催化剂活性与选择性最优化。采用同时存在固体碱和过渡金属氧化物两种活性中心的复合型催化剂,可能会实现催化性能最优化。目前对烷基芳烃过氧化反应的自由基反应机理已经达到共识,但对何种催化剂活性中心有利,催化剂如何促进反应的研究还很不够,应予进一步深入的研究。为开发新型高效的过氧化反应催化剂奠定理论基础。
参考文献:
[1]He Yu2Feng,Wang Rong2Min,liu Yu2yang,et al.J Mol
Catal[J],2000,(159):101-113.
[2]Hsu Y F,Cheng C P.J Mol Catal[J],1998,(136):1211.
[3]Csányi L J,Jáky K,K iss J T.J Mol Catal[J],1993,
(80):532364.
[4]Zawadiak J,G ilner Danuta,Mazurkiewicz R.Tetrahedron
Letters[J].1999,(40):405924062.
[5]Vodnár J,Békássy S,Farkas J.React K inet Catal Lett[J],
1999,(68):2132219.
[6]BoyacíF G,Takc S,Oezdamar T H.Appl Catal A[J],
1998,(172):59266.
[7]BoyacíF G,Takc S,Oezdamar T H.Appl Catal A[J],
2000,(197):2792287.
[8]张铭俊,张秀峰,王桂霞,等.石油化工[J],1996,25(6):
3812385.
[9]Alcántara R,Canoira L,Joao P G,et al.Appl Catal A[J],
2001,(218):2692279.
[10]李自明,于学敏,张秀岚.石油化工[J],1992,21(2),732
77.
[11]Trost B M.Science[J],1991,(254):147121477.
36 工业催化 2002年第2期
[12]Sheldon R A.CHEM TECH[J],1994,(9):5662576.
[13]Wu,et al.Hydroperoxidation of https://www.360docs.net/doc/9f12942492.html,:
4935551[P].
[14]Wu,et al.Preparation of Diisopropylebenzene Hydroper2
https://www.360docs.net/doc/9f12942492.html,:4282384.
[15]Varma G R,Graydon W F.J Catal[J],1973,(28):
2362244.
[16]Srivastava R K,Srivastava R D.J Catal[J],1975,(39):
3172323.
[17]Maksimov Y V,Suzdalev I P,Tsodikov M V.J Mol Catal
A Chemical[J].1996,(105):1672173.
[18]Takac S,Boyaci F G,Zdamar T H.Chem Eng Sci[J],
1998,(71):37248.
[19]Takac S,;zdamar T H.Appl Catal A[J],1993,(95):352
51.
[20]秦圣英,李仲辉.合成化学[J],1994,2(3):1972199.
[21]李仲辉,秦圣英,李建章,等.应用化学[J],1998,(15):
43246.
[22]Y ing Fang Hsu,Mei Hueiyen,Chen Pyeng Cheng.J Mol
Catal[J],1996,105:1372144.
[23]Y ing Fang Hsu,Chen Pyeng Cheng.J Mol Catal[J],
1998,136:1211.
[24]Y ing Fang Hsu,Chen Pyeng Cheng.J Mol Catal[J],
1997,120(13):1092111
国外动态
替代光气的聚碳酸酯熔融聚合工艺催化剂的改进
聚碳酸酯焙融聚合工艺中存在的固有问题是在反应条件下聚合物会倾向于重排,并生成支链的芳基酮类,这种支链物质存在于聚碳酸酯内高达2500~3000ppm,这致使其延展性降低,流变性变差。通用电器(GE)公司发现使用亚硫酸盐代替常用的碱性金属氢氧化物为聚合催化剂可明显减少支链物质的数量(世界专利号01/25310)。
当使用焦亚硫酸钠(Na2S2O5)代替NaOH和Na (CH3)OH组合物,支链物质可由2763ppm,减少到484ppm,平均分子量也由8252提高到8459。另外,系统的p H值也由1116降低到413。
熔融聚合生产的聚碳酸酯是无光气工艺,在此过程中,二苯基碳酸酯是二甲基碳酸酯与苯酚先反酯化得到的中间产物。
采用替代光气乳化聚合的熔融聚合法正在呈现新的应用潜力。GE公司是世界上最大的聚碳酸酯生产商,占世界总能力37%。它正在使用熔融法技术建设新的装置,西班牙塔拉戈纳12万t/a装置将于2002年投产。
钱伯章据E uropean Chem N ew s2001,1968(75):21
国内动态
小型合成氨厂催化剂部分更换技术
南京化学工业集团公司催化剂厂开发的小型合成氨生产装置快速变换部分合成氨催化剂的新技术,目前已在国内8个小型氨肥厂成功地应用于生产之中。
南京化学工业集团公司催化剂厂根据我国小合成氨厂生产实际需求开发成功的该项技术,较好地解决了小型氮肥厂生产装置同操作原因引起催化剂上部失活而影响生产,需更换失活部分催化剂的技术难题。该项技术能克服保护措施不足等困难,大大缩短恢复正常生产的时间,若采用多塔生产的厂家还可以采取其它塔保持轻负荷生产,完成催化剂部分更换工作,且使催化剂的使用情况迅速恢复到最好的工艺水平。
南京化学工业(集团)公司氮肥厂 江镇海
2002年第2期 王日杰等:烷基芳烃过氧化反应及其催化剂研究进展 37
间苯二酚的技术进展
- 26 -
中 间 体 精细化工原料及中间体
2008 年第 5 期
间苯二酚的技术进展
李文骁 李付刚 于守智 张今越 ( 沈阳化工研究院 辽宁 沈阳 110021)
摘 要: 介绍了国内外间苯二酚生产的技术现状, 并对其中的方法进行了简要的评述。指出异丙苯法是 一种最有前景的合成方法。
关键词: 间苯二酚 合成方法
The Pr ogr ess of Resor cinol Pr oduction Technique
Abstr act: The current situation og resorcinol production technique at home and abroad are intoduced.these synthesis methods were divided.the most prospect is cumene method.
Keywor d: resorcinol; synthesis method
间苯二酚俗称雷锁辛, 化学名称为 1, 3- 苯二 酚, 是一种重要的有机化工原料, 其用途十分广泛。 橡胶工业中, 主要用于生产帘子布浸胶剂, 随着我国 汽车工业的大发展, 我国轮胎产量已跃居世界前列。 今后我国轮胎产量还有较大空间, 因而橡胶制品对 间苯二酚的需求将稳步增长; 木材加工业中, 主要用 于生产低温快速木材胶粘剂, 随着近来国内建筑业 的复苏, 建筑材料及房屋装修材料需求增长快速, 刺 激了木材粘合剂的消费, 今后粘合剂对间苯二酚的 需求会有一定的增长; 医药工业上, 可用于制备杀菌 剂、驱虫剂和抗结核病药等; 农业方面, 主要可用于 合成杀虫剂和除草剂。此外, 间苯二酚还用于生产化 妆品、紫外线吸收剂、偶氮染料、阻燃剂、防腐剂和炸 药等。因此, 间苯二酚未来的发展前景非常乐观。
1. 合成工艺 根据所用原料的不同, 目前间苯二酚的合成方
法与工艺主要为: 苯磺化碱熔法、间二异丙苯氧化 法、芳化法、取代法等几种。
1.1 苯磺化碱熔法[1- 5] 该法是生产间苯二酚的传统方法, 工艺条件简
单, 反应平缓, 投资少, 技术成熟。我国大多数生产间 苯二酚的厂家均采用此法。磺化法在日本 70 年代研 究比较多, 80 到 90 年代研究较少, 主要是一些简单 的技术改进。
1.1.1 工艺基本原理 首先用苯与 20%发烟硫酸在 70 ̄80℃进行一次
磺化, 再与 65%发烟硫酸在 130 ̄160℃下进行二次 磺化, 生成间苯二磺酸, 然后用氢氧化钠碱熔, 温度 为 300 ̄320℃, 生成间苯二酚钠,
铝表面阳极氧化处理方法
铝表面阳极氧化处理方法 一、表面预处理 无论采用何种方法加工的铝材及制品,表面上都会不同程度地存在着污垢和缺陷,如灰尘、金属氧化物(天然的或高温下形成的氧化铝薄膜)、残留油污、沥青标志、人工搬运手印(主要成分是脂肪酸和含氮的化合物)、焊接熔剂以及腐蚀盐类、金属毛刺、轻微的划擦伤等。因此在氧化处理之前,用化学和物理的方法对制品表面进行必要的清洗,使其裸露纯净的金属基体,以利氧化着色顺利进行,从而获得与基体结合牢固、色泽和厚度都满足要求且具有最佳耐蚀、耐磨、耐侯等良好性能的人工膜。 (一)脱脂 铝及铝合金表面脱脂有有机溶剂脱脂、表面活性剂脱脂、碱性溶液脱脂、酸性溶液脱脂、电解脱脂、乳化脱脂。几种脱脂方法及主要工艺列于表-1。在这些方法中,以碱性溶液特别是热氢氧化钠溶液的脱脂最为有效。 表-1 脱脂及主要工艺 脱脂方法溶液组成用量g/L 温度/度时间min 后处理备注 有机溶剂汽油、四氯化碳、三氯乙烯等适量常温或蒸汽适当无浸蚀 表面活性剂肥皂、合成洗涤剂适量常温-80 适当. 水清洗无浸蚀 碱性溶液NaOH 50-200 40-80 0.5-3 水洗后用100-500g/L硝酸溶液中和及除挂灰脱脂兼腐蚀除去自然氧化,硝酸可用稀硫酸+铬酸代替 十二水磷酸钠NaOH硅酸钠40-608-1225-30 60-70 3-5 水清洗NaOH可用40-50g/L 碳酸钠代替,总碱度按NaOH计算为1.6%-2.5% 多聚磷酸钠碳酸钠磷酸钠一水硼酸钠葡萄糖酸液体润湿剂15.64.84.84.80.3ml0.1ml 60 12-15 水清洗使用前搅拌4个小时 十二水磷酸钠硅酸钠液体肥皂50-7025-353-5 75-85 3-5 水清洗 碳酸钠磷酸钠25-4025-40 75-85 适当水清洗 磷酸钠碳酸钠NaOH 20106 45-65 3-5 水清洗 强碱阻化除油剂40-60 70 5 水清洗除油不净可延长处理时间 酸性溶液硫酸50-300 60-80 1-3 水清洗 硝酸162-354 常温3-5 水清洗松化处理 磷酸硫酸表面活性剂3075 50-60 5-6 水清洗 磷酸(85%)丁醇异丙醇水100%40%30%20% 常温5-10 水清洗溶液组成以体积记 电解溶液阳极氧化用电解质常温适当交流电或阴极电流电解 NaOH 100-200 常温0.5-3 水清洗后中和铝制品为阴极,电流密度为4-8A/dm2 乳化溶液石蜡三乙醇胺油酸松油水8.0%0.25%0.5%2.25%89% 常温适当水清洗溶液组成以体积记
氧化石墨烯的制备方法总结
氧化石墨烯的制备方法: 方法一: 由天然鳞片石墨反应生成氧化石墨,大致分为3 个阶段,低温反应:在冰水浴中放入大烧杯,加入110mL 浓H2SO4,在磁力搅拌器上搅拌,放入温度计让其温度降至4℃左右。加入-100目鳞片状石墨5g,再加入NaNO3,然后缓慢加入15g KMnO4,加完后记时,在磁力搅拌器上搅拌反应90min,溶液呈紫绿色。中温反应:将冰水浴换成温水浴,在磁力搅拌器搅拌下将烧杯里的温度控制在32~40℃,让其反应30 min,溶液呈紫绿色。高温反应:中温反应结束之后,缓慢加入220mL 去离子水,加热保持温度70~100℃左右,缓慢加入一定双氧水(5 %)进行高温反应,此时反应液变成金黄色。反应后的溶液在离心机中多次离心洗涤,直至BaCl2检测无白色沉淀生成,说明没有SO42-的存在,样品在40~50℃温度下烘干。H2SO4、NaNO3、KMnO4一起加入到低温反应的优点是反应温度容易控制且与KMnO4反应时间足够长。如果在中温过程中加入KMnO4,一开始温度会急剧上升,很难控制反应的温度在32~40℃。技术路线图见图1。 方法二:Hummers 方法 采用Hummers 方法[5]制备氧化石墨。具体的工艺流程在冰水浴中装配好250 mL 的反应瓶加入适量的浓硫酸搅拌下加入2 g 石墨粉和1 g 硝酸钠的固体混合物再分次加入6 g 高锰酸钾控制反应温度不超过20℃搅拌反应一段时间然后升温到35℃左右继续搅拌30 min再缓慢加入一定量的去离子水续拌20 min 后并加入适量双氧水还原残留的氧化剂使溶液变为亮黄色。趁热过滤并用5%HCl 溶液和去离子水洗涤直到滤液中无硫酸根被检测到为止。最后将滤饼置于60℃的真空干燥箱中充分干燥保存备用。方法三:修正的Hummers方法 采用修正的Hummers方法合成氧化石墨,如图1中(1)过程。即在冰水浴中装配好250 mL的反应瓶,加入适量的浓硫酸,磁力搅拌下加入2 g 石墨粉和1 g硝酸钠的固体混合物,再缓慢加入6 g高锰酸钾,控制反应温度不超过10 ℃,在冰浴条件下搅拌2 h后取出,在室温下搅拌反应5 d。然后将样品用5 %的H2SO4(质量分数)溶液进行稀释,搅拌2 h后,加入6 mL H2O2,溶液变成亮黄色,搅拌反应2 h离心。然后用浓度适当的H2SO4、H2O2混合溶液以及HCl反复洗涤、最后用蒸馏水洗涤几次,使其pH~7,得到的黄褐色沉淀即为氧化石墨(GO)。最后将样品在40 ℃的真空干燥箱中充分干燥。将获得的氧化石墨入去离子水中,60 W功率超声约3 h,沉淀过夜,取上层液离心清洗后放入烘箱内40 ℃干燥,即得片层较薄的氧化石墨烯,如图1中(2)过程。
石墨烯的制备与表征综述
氧化石墨烯还原的评价标准 摘要还原氧化石墨烯(RGO)是一种 有趣的有潜力的能广泛应用的纳米 材料。虽然我们花了相当大的努力 一直致力于开发还原方法,但它仍然 需要进一步改善,如何选择一个合适 的一个特定的还原方法是一个棘手 的问题。在这项研究中,还原氧化石 墨烯的研究者们准备了六个典型的 方法:N2H4·H2O还原,氢氧化钠还 原,NaBH4还原,水浴还原 ,高温还原以及两步还原。我们从四个方面系统的对样品包括:分散性,还原程度、缺陷修复程度和导电性能进行比较。在比较的基础上,我们提出了一个半定量判定氧化石墨烯还原的评价标准。这种评价标准将有助于理解氧化石墨烯还原的机理和设计更理想的还原方法。 引言 单层石墨烯,因为其不寻常的电子性质和应用于各个领域的潜力,近年来吸引了巨大的研究者的关注。目前石墨烯的制备方法,包括化学气相沉积(CVD)、微机械剥离石墨,外延生长法和液相剥离法。前三种方法因为其获得的石墨烯的产品均一性和层数选择性原因而受到限制。此外,这些方法的低生产率使他们不适合大规模的应用。大部分的最有前途生产的石墨烯的路线是石墨在液相中剥离氧化然后再还原,由于它的简单性、可靠性、大规模的能力生产、相对较低的材料成本和多方面的原因适合而适合生产。这种化学方法诱发各种缺陷和含氧官能团,如羟基和环氧导致石墨烯的电子特性退化。与此同时,还原过程可能导致发生聚合、离子掺杂等等。这就使得还原方法在化学剥离法发挥至关重要的作用。 到目前为止,我们花了相当大的努力一直致力于开发还原的方法。在这里我们展示一个简单的分类:使用还原剂(对苯二酚、二甲肼、肼、硼氢化钠、含硫化合物、铝粉、维生素C、环六亚甲基四胺、乙二胺(EDA) 、聚合电解质、还原糖、蛋白质、柠檬酸钠、一氧化碳、铁、去甲肾上腺素)在不同的条件(酸/碱、热处理和其他类似微波、光催化、声化学的,激光、等离子体、细菌呼吸、溶菌酶、茶溶液)、电化学电流,两步还原等等。这些不同的还原方法生成的石墨烯具有不同的属性。例如,大型生产水分散石墨烯可以很容易在没有表面活性稳定剂的条件下地实现由水合肼还原氧化石墨烯。然而,水合肼是有毒易爆,在实际使用的过程中存在困难。水浴还原方法可以减少缺陷和氧含量的阻扰。最近,两个或更多类型的还原方法结合以进一步提高导电率或其他性能。例如,水合肼还原经过热处理得到的石墨烯通常显现良好的导电性。
阳极氧化新工艺
近十年来,我国的铝氧化着色工艺技术发展较快,很多工厂已采用了新的工艺技术,并且在实际生产中积累了丰富的经验。已经成熟和正在发展的铝及其合金阳极氧化工艺方法很多,可以根据实际生产需要,从中选取合适的工艺。 在选取氧化工艺之前,应对铝或铝合金材质情况有所了解,因为,材料质量的优劣、所含成份的不同,是会直接影响到铝制品阳极氧化后的质量的。关于这一点,洪九德、范济同志已有专门论述(参看《电镀与涂饰》1982年第2期P.27)。比如,铝材表面如有气泡、划痕、起皮、粗糙等缺陷,经阳极氧化后,所有疵病依然会显露出来。而合金成份,对阳极氧化后的表面外观,也产生直接的影响。比如,含1~2%锰的铝合金,氧化后呈棕蓝色,随铝材中含锰量的增加,氧化后的表面色泽从棕蓝色到深棕色转化。含硅0.6~1.5%的铝合金,氧化后呈灰色,含硅3~6%时,呈白灰色。含锌的呈乳浊色,含铬的呈金黄至灰色的不均匀色调,含镍的呈淡黄色。一般而言,只有含镁和含钛量大于5%的铝含金,经氧化后可以得到无色透明且光亮、光洁的外观。 在选择好铝及铝合金材料后,自然就要考虑到选取合适的阳极氧化工艺。目前,我国广泛应用的硫酸氧化法、草酸氧化法及铬酸氧化法,均在手册、书刊上有过详细的介绍,不必赘述。本文谨就目前在国内正在发展中的一些新工艺,以及国外的一些方法,作扼要的介绍。 一、国内已发展的新工艺 (一)草酸-甲酸混合液交流快速氧化 采用草酸-甲酸混合液,是因为考虑到甲酸是一种强氧化剂,在这样的槽液中,甲酸起到对氧化膜内层(阻挡层和障壁层)加速溶解,从而使成为多孔层(即氧化膜外层)的作用。这种槽液的导电率可以得到提高(即可提高电流密度),使氧化膜能快速生成。与纯草酸氧化法相比,这种溶液能使生产率提高37.5%,减少电耗量(草酸氧化法耗电量为3.32度/平方米,此法为2度/平方米),节约电力40%。 工艺配方为:草酸4~5%、甲酸0.55%,三相交流44士2伏,电流密度2~2.5A/d㎡,温度30±2℃。 (二)混合酸氧化 此法于1976年正式纳入日本国家标准,并为日本北星日轻家庭用品株式会社所采用。其特点是成膜快,膜的硬度、耐磨、耐腐蚀性能都比普通的硫酸氧化法高,膜层呈银白色,适用于印花、着色产品。我国铝制品行业赴日考察后,于1979年开始推荐使用。其推荐工艺配方为:H2SO4 10~20%,COOHCOOH·2H2O 1~2%,电压10~20V,电流密度1~3A/d ㎡,温度15~30℃,时间30分钟。 (三)瓷质氧化 瓷质氧化主要以铬酸、硼酸、草酸钛钾为电解质,用高电压和较高温度作电解处理。其膜层外观像瓷器上的釉,有高度的抗腐蚀性能,耐磨性能良好,膜层可用有机或无机的染料染色,使外观有特殊的光泽和色泽。目前多应用于铝炊具、打火机、金笔等产品上,很受群众喜爱。 (四)国防色氧化 国防色氧化主要应用在军用铝制品的装饰上,因而要求有特殊的防护作用。氧化膜呈军绿色、无光泽、耐磨耐用,防护性能良好。工艺是:首先进行草酸氧化,生成金黄色膜层后,再用高锰酸钾20g/l、H2SO41g/l的溶液进行阳极氧化处理而成。沈阳铝制品厂曾应用此工艺生产军用水壶及炊具用品。 (五)多色氧化 将已染色而未封闭的阳极氧化层,用铬酸或草酸润湿,使CrO3铺展,已染色的制品的
氧化石墨烯的制备及表征
氧化石墨烯的制备及表征 文献综述 材料0802班 李琳 200822046
氧化石墨烯的制备及表征 李琳 摘要:石墨烯(又称单层石墨或二维石墨)是单原子厚度的二维碳原子晶体,被认为是富勒烯、碳纳米管和石墨的基本结构单元[1]。石墨烯可通过膨胀石墨经过超声剥离或球磨处理来制备[2,3],其片层厚度一般只能达到30~100 nm,难以得到单层石墨烯(约0.34 nm),并且不容易重复操作。所以寻求一种新的、容易和可以重复操作的实验方法是目前石墨烯研究的热点。而将石墨氧化变成氧化石墨,再在超声条件下容易得到单层的氧化石墨溶液,再通过化学还原获得,已成为石墨烯制备的有效途径[4]。通过述评氧化石墨及氧化石墨烯的制备、结构、改性及其与聚合物的复合,展望了石墨烯及其复合材料的研究前景。 关键词:氧化石墨烯,石墨烯,氧化石墨,制备,表征 Oxidation of graphite surfaces preparation and Characterization LI Lin Abstrat:Graphite surfaces (also called single graphite or 2 d graphite )is the single atoms thickness of the 2 d carbon atoms crystal, is considered fullerenes, carbon nanotubes and graphite basic structure unit [1].Graphite surfaces can through the expanded graphite after ultrasonic stripping or ball mill treatment topreparation [2,3], a piece of layer thickness normally only up to 30 to 100 nm, hard to get the single graphite surfaces (about 0.34 nm), and not easy to repeated operation. So to search a new, easy to operate and can be repeated the experiment method of the graphite surfaces is the focus of research. And will graphite oxidization into oxidation graphite, again in ultrasonic conditions to get the oxidation of the single graphite solution, again through chemical reduction get, has become an effective way of the preparation of graphite surfaces [4]. Through the review of graphite oxide and oxidation graphite surfaces of the preparation, structure, modification of polymer and the
硬质阳极氧化Word版
硬质阳极氧化是一种厚膜阳极氧化法,这是一种铝和铝合金特殊的阳极氧化表面处理工艺。此种工艺,所制得的阳极氧化膜最大厚度可达250微米左右,在纯铝上能获得1500kg/mm2的显微硬度氧化膜,而在铝合金上则可获得400~600kg/mm2的显微硬度氧化膜。其硬度值,氧化膜内层大于外层,即阻挡层大于带有孔隙的氧化膜层,因氧化膜内有松孔,可吸附各种润滑剂,增加了减摩能力,氧化膜层导热性很差,其熔点为2050℃,电阻系数较大,经封闭处理(浸绝缘物或石蜡)击穿电压可达2000V,在大气中较高的抗蚀能力,具有很高的耐磨性,也是一种理想的隔热膜层,也有良好的绝缘性,并具有与基体金属结合得很牢固等一系列优点,因此在国防工业和机械零件制造工业上获得及其广泛的应用。主要应用于要求高耐磨、耐热、绝缘性能好等的铝和铝合金零件上。如各种作为圆筒的内壁,活塞、汽塞、汽缸、轴承、飞机货舱的地板、滚棒和导轨、水利设备、蒸汽叶轮、适平机、齿轮和缓冲垫等零件。用硬质氧化工艺来代替传统的镀硬铬镀层,与硬铬工艺相比它具有成本低,膜层结合牢固,镀液,清洗废液处理方便等优点。但此工艺所得膜层的缺点是膜层厚度较大时,对铝和铝合金的机械疲劳强度指标有所影响。硬质阳极氧化电解方法很多,例如:硫酸、草酸、丙二醇、磺基水杨酸及其它的无机盐和有机酸等。所用电源可分为直流、交流和交直流叠加电源等几种,目前广泛应用的有下列两种硬质阳极氧化。 (1)硫酸硬质阳极氧化直流法; (2)草酸硬质阳极氧化交直流重选法。 其中,硫酸法是目前得到较广泛应用的一种硬质氧化法. 1 硬质阳极氧化原理 铝合金硬质阳极氧化原理,就是在电场的作用下,加速铝合金表面氧化膜的形成即用铅板作阴极,铝合金制作阳极,稀硫酸溶液作电解液,当通过直流电时,H+便向阴极移动,产生阴极反应: 4H2+4e=2H2↑而OH-便向阳极运动产生阳极反应: 4OH--4e=2H2O+2O↑当在阳极上失去多余的电子,所析出的氧呈原子状态,由于原子状态的氧要比分子状态的氧更为活泼,更易与铝起反应: 2A1+3O→A12O3 上述—反应在铝和铝合金制件表面是均匀地,同时进行地。 氧化膜随着通电时间的增加,电流增大而促使氧化膜增厚。与此同时,由于(Al2O3)的化学性质有两重性,即它在酸性溶液中呈碱性氧化物,在碱性溶液中呈酸性氧化物。无疑在硫酸溶液中氧化膜液发生溶解,只有氧化膜的生成速度大于它的溶解速度,氧化膜才有可能增厚,当溶解速度与生成速度相等时,氧化膜不再增厚。当氧化速度过分大于溶解速度时,铝和铝合金制件表面易生成带粉状的氧化膜。 硬质阳极氧化的电解液时在-10℃~+5℃左右的温度下电解。由于硬质阳极氧化所生成的氧化膜层具有较高的电阻,会直接影响到电流强度的氧化作用。为了取得较厚的氧化膜,势必要增加外电压,其目的是为了消除电阻大的影响,而使电流密度保持一定,但电流较大时会产生激烈的发热现象,加上生成氧化膜时会放出大量的热量,使零件周围电解液温度剧烈上升,温度上升将会加速氧化膜的溶解,使氧化膜无法变厚。另外,发热现象在膜层与金属的接触处最严重,如不及时解决,加工零件的局部表面会因温度上升而被烧坏。 解决办法,就是采用冷却设备和搅拌相结合。冷却设备使电解液强行降温,搅拌是为了使整槽电解温度均匀,以利于获得较高质量的硬质氧化膜。 2 硬质阳极氧化法工艺要求 为了得到质量较好的硬质阳极氧化膜,并能保证零件所需要尺寸,必须按下列要求来进行加工. 2.1 锐角倒圆被加工零件不允许有锐角、毛刺以及其它各种尖锐的有棱角的地方因为硬质氧化,一般阳极氧化时间均是很长的,而且氧化过程(A1+O2→A12O3+ Q )本身就是一个放热反应。又由于一般零件棱角的地方往往又是电流较为集中的部位所以这些部位最易引起零
氧化石墨烯的制备讲义
实验十、氧化石墨烯的制备实验 一、实验目的 1、掌握Hummers法制备氧化石墨烯。 2、了解氧化石墨烯结构与性能表征。 二、实验原理 1、氧化石墨烯 氧化石墨烯是石墨烯的氧化物,其颜色为棕黄色,市面上常见的产品有粉末状、片状以及溶液状的。氧化石墨烯薄片是石墨粉末经化学氧化及剥离后的产物,氧化石墨烯是单一的原子层,可以随时在横向尺寸上扩展到数十微米,因此,其结构跨越了一般化学和材料科学的典型尺度。氧化石墨烯可视为一种非传统型态的软性材料,具有聚合物、胶体、薄膜,以及两性分子的特性。氧化石墨烯长久以来被视为亲水性物质,因为其在水中具有优越的分散性,但是,相关实验结果显示,氧化石墨烯实际上具有两亲性,从石墨烯薄片边缘到中央呈现亲水至疏水的性质分布。 经过氧化处理后,氧化石墨仍保持石墨的层状结构,但在每一层的石墨烯单片上引入了许多氧基功能团。这些氧基功能团的引入使得单一的石墨烯结构变得非常复杂。鉴于氧化石墨烯在石墨烯材料领域中的地位,许多科学家试图对氧化石墨烯的结构进行详细和准确的描述,以便有利于石墨烯材料的进一步研究,虽然已经利用了计算机模拟、拉曼光谱,核磁共振等手段对其结构进行分析,但由于种种原因(不同的制备方法,实验条件的差异以及不同的石墨来源对氧化石墨烯的结构都有一定的影响),氧化石墨烯的精确结构还无法得到确定。大家普遍接受的结构模型是在氧化石墨烯单片上随机分布着羟基和环氧基,而在单片的边缘则引入了羧基和羰基。 图1 氧化石墨烯的结构 2、氧化石墨烯的制备 氧化石墨烯的制备一般有三种方法:brodie法、Staudenmaier法、hummers法。这三种方法的共同点都是利用石墨在酸性质子和氧化剂的作用下氧化而成的,但是不同的方法各有优点。Brodie 等人于1859年首次用高氯酸和发烟硝酸作为氧化剂插层制备出
石墨烯的氧化还原法制备及结构表征
实验目的: (1)了解石墨烯的结构和用途。 (2)了解氧化后的石墨烯比纯石墨烯的性能有何提升 (3)了解Hummers法的原理 一、实验原理: 天然石墨需要进行先氧化,得到氧化石墨,再经过水合肼的作用下还原,才能得到在水相条件下稳定分散的石墨烯。 石墨的氧化过程采用浓硫酸和高锰酸钾这两种强氧化剂,氧化过程中先加浓硫酸,搅拌均匀后再加高锰酸钾,氧化过程从石墨的边沿进行,然后再到中间,氧化程度与持续时间有关。氧化过程中要增加石墨的亲水性,以便于分散,分散一般使用超声分散法。 氧化后的氧化石墨烯需要进行离心处理,使得pH值在6到7之间,目的是洗去氧化石墨烯的酸性,根本原因是研究表明氧化石墨烯和石墨烯在碱性条件下可以形成稳定的悬浮液。 氧化石墨烯的还原有多种方法,化学还原和热还原等,化学还原采用水合肼,热还原采用作TGA后,加热到200℃,一般大部分的含氧官能团都能除去。 二、实验内容: 1、利用氧化还原法制备石墨烯 2、对制得的石墨烯进行结构表征 三、实验过程: 实验利用Hummers法进行实验: 1、在三颈瓶外覆盖冰块,制造冰浴环境,并在三颈瓶内放入搅拌磁石; 2、将冰状天然石墨4g和硝酸钠2g倒入三颈瓶中; 3、将92ml浓硫酸倒入三颈瓶中; 4、开启磁力搅拌器,把溶液搅拌均匀后再缓慢加入高锰酸钾12g,在冰浴环境下搅拌3h; 5、升温至35℃,保持搅拌0.5h或1h,此时是对石墨片层中间进行氧化作用,氧化程度与持续时间有关; 6、加入去离子水184ml,缓慢滴加,保持温度低于100℃,升温至90℃,保温3h,溶液变红; 7、加300ml去离子水和30%的双氧水溶液10ml,使得高锰酸钾反应掉,静置一晚,倒掉上层清液; 8、对溶液进行离心操作7-8次,使得pH值在6-7; 9、减压蒸馏,进行还原反应得到石墨烯; 10、对得到的产物进行结构表征。
阳极氧化
7.3 铝及其合金的氧化处理 铝及铝合金的氧化处理的方法主要有两类:①化学氧化,氧化膜较薄,厚度约为0.5~4微米,且多孔,质软,具有良好的吸附性,可作为有机涂层的底层,但其耐磨性和抗蚀性能均不如阳极氧化膜;②电化学氧化,氧化膜厚度约为5~20微米(硬质阳极氧化膜厚度可达60~200微米),有较高硬度,良好的耐热和绝缘性,抗蚀能力高于化学氧化膜,多孔,有很好的吸附能力。 7.3.1铝及铝合金的化学氧化处理 铝及铝合金的化学氧化处理设备简单,操作方便,生产效率高,不消耗电能,适用范围广,不受零件大小和形状的限制。 铝及铝合金化学氧化的工艺按其溶液性质可分为碱性氧化法和酸性氧化法两大类。 按膜层性质可分为:氧化物膜、磷酸盐膜、铬酸盐膜、铬酸-磷酸盐膜。 <1>铝及铝合金碱性铬酸盐化学氧化溶液的配方及工艺条件如表7-4。
注:①配方1,2适用于纯铝,铝镁合金,铝锰合金和铝硅合金的化学氧化。膜层颜色为金黄色,但后二种合金上得到的氧化膜颜色较暗。碱性氧化液中得到的膜层较软,耐蚀性较差,孔隙率较高,吸附性好,适于作为涂装底层。 ②配方3中加入硅酸钠,获得的氧化膜为无色,硬度及耐蚀性略高,孔隙率及吸附性略低,在硅酸钠的质量分数为2%的溶液中封闭处理后可单独作为防护层用,适合于含重金属铝合金氧化用。 溶液中,室温下 ③工件经氧化处理后为提高耐蚀性,可在20g/L的CrO 3 钝化处理5~15s,然后在低于50℃温度下烘干。 <2>铝及铝合金酸性铬酸盐化学氧化溶液配方及工艺条件如表7-5。 注:①配方1得到的氧化膜较薄,韧性好,耐蚀性好,适用于氧化后需变形的铝及铝合金,也可用于铸铝件的表面防护,氧化后不需要钝化或填充处理。
化学还原法制备石墨烯的研究进展
化学还原法制备石墨烯的研究进展近年来,研究人员利用多种方法开展了石墨烯的制备工作,主要包括化学剥离法、金属表面外延法、SiC表面石墨化法和化学还原法等[1]。目前应用最广泛的合成方法是化学还原法。石墨烯在氧化的过程中会引入一些化学基团,如羧基(-COOH)、羟基(-OH)、羰基(-C = O)和环氧基(-C-O-C)等,这些基团的生成改变了C-C之间的结合方式,导致氧化石墨烯的导电性急剧下降,并且使具有的各种优异性能也随之消失。因此,对氧化石墨烯进行还原具有非常重要的意义,主要是先将氧化石墨烯分散(借助高速离心、超声等)到水或有机溶剂中形成稳定均相的溶胶,再按照一定比例用还原剂还原,得到单层或者多层石墨烯。还原得到的石墨烯有望在电子晶体管、化学传感器、生物基因测序以及复合材料等众多领域广泛应用。 目前,制备氧化石墨烯的技术已经相当成熟,其层间距(0.7~1.2 nm)较原始石墨烯层间距大,更有利于将其他物质分子插入。研究表明氧化石墨烯表面和边缘有大量的羟基、羧基等官能团,很容易与极性物质发生反应,得到改性氧化石墨烯。氧化石墨烯的有机改性可使其表面由亲水性变为亲油性,表面能降低,从而提高与聚合物单体或聚合物之间的相容性,增强氧化石墨烯与聚合物之间的粘接性。如果使用适当的剥离技术(如超声波剥离法、静电斥力剥离法、热解膨胀剥离法、机械剥离法、低温剥离法等),那么氧化石墨烯就能很容易的在水溶液或有机溶剂中分散成均匀的单层氧化石墨烯溶液,使利用其反应得到石墨烯成为可能。氧化还原法最大的缺点是制备的石墨烯有一定的缺陷,因为经过强氧化剂氧化得到的氧化石墨烯,并不一定能被完全还原,可能会损失一部分性能,如透光性、导热性,尤其是导电性,所以有些还原剂还原后得到的石墨烯在一定程度上存在不完全性,即与严格意义上的石墨烯存在差别。但氧化还原方法价格低廉,可以制备出大量的石墨烯,所以成为目前最常用制备石墨烯的方法。
阳极氧化完整工艺流程
陽極氧化工藝流程名词解释Ⅰ机械与化学表面处理 金属需经过抛光或刷光,随后除油及脱脂,检查外观质量,以为后续处理工序作表面准备。Ⅱ阳极氧化 通过认为的手段,形成一层厚氧化铝膜,即阳极氧化膜。即吸附氧化膜。这是吸附着色的先决条件。Ⅲ染色 在阳极氧化膜之微孔结构内沉积染料分子。Ⅳ封孔 封住微细孔,使染料固定于氧化膜内。吸附着色的理论依据吸附现象是采用染料水溶液浸渍染色的特点。与其他着色技术不同的是,其产生颜色之化合物并非产生自工艺本身而是存在于开初的介质中。“吸附”这一术语的意思是染料分子沉积并积聚氧化膜微孔的内表面,此阳极氧化膜的孔隙率为氧化膜的20m2/g。导致吸附的是铝氧化膜与染料分子之间的键合力起作用。这键合是不稳定的,相反,吸附在阳极氧化膜上的染料(染色强度)与溶液中的染料之间达到平衡。倘若溶液的染料浓度增大,则吸附量会增大,直至达到饱和点(颜色强度最大)时为止。又倘若溶液的燃料浓度下降,比如下降到零,而水中又全无亲质,便会出现解吸附,导致褪色合色料扩散。因此,在完成染色之后的多孔膜封闭工序是必不可少的。尽管染料迅速吸附,但整个着色过程的速度并非取决这一原始的现象,而是取决于染料分子随后怎样进入狭窄的微孔内。这一过程以略低的速率进行。分子的直径平均为0.0025µm,而用硫酸直流氧化法制备的阳极氧化膜的
微孔平均直径为0.02µm。 ***********************************************************铝的级别和铝的阳极氧化铝材的物理成分以及级别是吸附着色是否成功的重要因素。铝材分为高纯铝、纯铝和合金铝。高纯铝只含不超过痕量(不超过0.05%,依次排级)的亲质金属;纯铝的亲质金属含量不超过1%。由于铝本身的强度不足以应付各种用途,因而相当多是与其他金属形成合金,主要的是镁、锌、锰、铜等。合金中的这些成分越高。耐机械磨损性便越强,但对装饰性着色的适应性则相对的越差。吸附着色本身是不会改善阳极氧化膜的物理特性的。Ⅰ质量要求 必须选用阳极氧化级的铝材,才能保证在阳极氧化和着色后仍然能保持吸引人的外观。这一级别的铝材是专门为阳极氧化和着色而特别制备并经过特别检测的。Ⅱ合金成分对色泽和透明度的影响 铝和铝合金原有的颜色分别随其纯度级别与所含成分不同而异。而吸附着色的色调又受原来的底色所影响。1 镁量大于5%时,阳极氧化膜会暗哑;2 含锰及铬量即使低至仅1%,氧化膜便带黄色,超过此含量时,金属色调便会变的暗黑;3 硅有使氧化膜带灰色的趋向,不过,很大程度上取决于它存在于合金中的形式。如果以固溶体形式存在而含量低于1%时,它不会使氧化膜明显暗哑。超过此含量及以非固溶体形式存在时,金属就会呈浑浊的灰色。有一种特别的含硅3%~6%的铝合金就被称为“灰色调和金”。
阳极氧化工艺参数的影响
阳极氧化工艺参数的影响 1)H2SO4浓度。改变H2SO4浓度对氧化膜的阻挡层厚度,溶液的导电性、氧化膜的耐蚀性和耐磨性以及后处理的封孔质量都将产生一定的影响。 H2SO4浓度阻挡层厚度维持电压耐蚀、耐磨性气化膜质量 膜层发灰,疏松,膜孔外层孔径大,封孔困难 2)槽液温度 阳极氧化过程中,部分电能会转化为热能,槽液温度会不断上升,而随着温度的上升,膜层损失会增加而且成膜质量变差,膜耐磨性下降,尤其对15um以上膜层,甚至在空气中就会出现“粉化”现象,因此过程中需要对槽液降温,以维持适宜的温度。 一般来说: 槽温在一定范围内提高,获得氧化膜重量减小,膜变软但较光亮。 槽液温度高,生成的氧化膜外层膜孔径和度变大,造成封孔困难,也易产生封孔“粉霜”。槽温较高时,氧化膜易染色。但对于保持颜色深浅一致时较难,所以一般染色膜的氧化温度为20~25℃降低温度,得到的氧化膜硬度高,耐磨性好,在氧化过程中维持电流密度所需电压较高,能耗大,所以一般普通氧化选择18~22℃ 3)氧化电压 阳极氧化电压决定氧化膜的孔径大小,低压生成的膜孔径小,孔数多,而高压生成的膜孔径大,孔数小,一定范围内高压有利于生成致密,均匀的膜。 4)电流密度 电流密度大,成膜快,生产效率高,但过高则易烧伤工件。一般电流密度控制在~dm2范围内 电流密度低,生产效率低,但处理面光亮(约1A/dm2) 电流密度高,成膜快,但易产生软膜,甚至烧伤 如果冷冻能力足够,搅拌良好,则采用较大电流氧化,有利于提高膜的耐磨性。 5)搅拌 足够的搅拌可保持槽液温度的均匀和恒定,对于控制膜厚,膜层质量,着色均匀性均有好处。 6)铝离子和其它杂质的影响 铝离子。Al3+离子含量升高会使电流密度下降。铝含量较高会使染色困难,而一定的铝含量对氧化膜厚度,耐蚀性,耐磨性有很大好处。一般来说铝含量1~10g/L会产生有利影响,超过10g/L造成不利影响。我国大多厂家选择控制为12~18g/L 其他阳离子杂质铁含量超过25~50mg/g时会导致光亮度下降,膜层松软等。铜、镍总量超过100mg/g时,将使氧化膜原有的耐蚀性降低,易产生盐雾试验不合格。 一、表面预处理无论采用何种方法加工的铝材及制品,表面上都会不同程度地存在着污垢和缺陷,如灰尘、金属氧化物(天然的或高温下形成的氧化铝薄膜)、残留油污、沥青标志、人工搬运手印(主要成分是脂肪酸和含氮的化合物)、焊接熔剂以及腐蚀盐类、金属毛刺、轻微的划擦伤等。因此在氧化处理之前,用化学和物理的方法对制品表面进行必要的清洗,使其裸露纯净的金属基体,以利氧化着色顺利进行,从而获得与基体结合牢固、色泽和厚度都满足要求且具有最佳耐蚀、耐磨、耐侯等良好性能的人工膜。 (一)脱脂 铝及铝合金表面脱脂有有机溶剂脱脂、表面活性剂脱脂、碱性溶液脱脂、酸性溶液脱脂、电解脱脂、乳化脱脂。
阳极氧化的原理及相关知识
阳极氧化的原理及相关知识 铝/铝合金阳极氧化的原理 内容:以铝或铝合金制品为阳极置于电解质溶液中,利用电解作用,使其表面形成氧 化铝薄膜的过程,称为铝及铝合金的阳极氧化处理。铝阳极氧化的原理实质上就是水电解的原理。当电流通过时,将发生以下的反应: 在阴极上,按下列反应放出H2 : 2H + +2e 宀H2 在阳极上,40H -4e T 2H2O + O2, 析出的氧不仅是分子态的氧(02),还包括原子氧(0),以及离子氧(0-2),通常在反应中以分子氧表示。作为阳极的铝被其上析出的氧所氧化,形成无水的1203膜:4A1 + 302 = 2A12O3 + 3351J 应指出,生成的氧并不是全部与铝作用,一部分以气态的形式析出。阳极氧化的种类阳极氧化早就在工业上得到广泛应用。冠以不同名称的方法繁多,归纳起来有以下几种分类方法:按 电流型式分有:直流电阳极氧化;交流电阳极氧化;以及可缩短达到要求厚度的生产时间,膜层既厚又均匀致密,且抗蚀性显着提高的脉冲电流阳极氧化。按电解液分有:硫酸、草酸、铬酸、混合酸和以磺基有机酸为主溶液的自然着色阳极氧化。按膜层性质分有:普通膜、硬质膜(厚膜)、瓷质膜、光亮修饰层、半导体作用的阻挡层等阳极氧化。直流电硫酸阳极氧化法的应用最为普遍,这是因为它具有适用于铝及大部分铝 合金的阳极氧化处理;膜层较厚、硬而耐磨、封孔后可获得更好的抗蚀性;膜层无色 透明、吸附能力强极易着色;处理电压较低,耗电少;处理过程不必改变电压周期,有利于连续生产和实践操作自动化;硫酸对人身的危害较铬酸小,货源广,价格低等优点。近十年来,我国的建筑业逐步使用铝门窗及其它装饰铝材,它们的表面处理生产线 都是采用这种方法。 铝及铝合金阳极氧化法综述
石墨烯的制备方法概述
石墨烯的制备方法概述 1物理法制备石墨烯 物理方法通常是以廉价的石墨或膨胀石墨为原料,通过机械剥离法、取向附生法、液相或气相直接剥离法来制备单层或多层石墨烯。这些方法原料易得,操作相对简单,合成的石墨烯的纯度高、缺陷较少。 1.1机械剥离法 机械剥离法或微机械剥离法是最简单的一种方法,即直接将石墨烯薄片从较大的晶体上剥离下来。Novoselovt等于2004年用一种极为简单的微机械剥离法成功地从高定向热 解石墨上剥离并观测到单层石墨烯,验证了单层石墨烯的独立存在。具体工艺如下:首先利用氧等离子在1mm厚的高 定向热解石墨表面进行离子刻蚀,当在表面刻蚀出宽20μm —2mm、5μm的微槽后,用光刻胶将其粘到玻璃衬底上, 再用透明胶带反复撕揭,然后将多余的高定向热解石墨去除并将粘有微片的玻璃衬底放入丙酮溶液中进行超声,最后将单晶硅片放入丙酮溶剂中,利用范德华力或毛细管力将单层石墨烯“捞出”。 但是这种方法存在一些缺点,如所获得的产物尺寸不易控制,无法可靠地制备出长度足够的石墨烯,因此不能满足工业化需求。
1.2取向附生法—晶膜生长 PeterW.Sutter等使用稀有金属钌作为生长基质,利用基质的原子结构“种”出了石墨烯。首先在1150°C下让C原子渗入钌中,然后冷却至850°C,之前吸收的大量碳原子就会浮到钌表面,在整个基质表面形成镜片形状的单层碳原子“孤岛”,“孤岛”逐渐长大,最终长成一层完整的石墨烯。第一层覆盖率达80%后,第二层开始生长,底层的石墨烯与基质间存在强烈的交互作用,第二层形成后就前一层与基质几乎完全分离,只剩下弱电耦合,这样制得了单层石墨烯薄片。但采用这种方法生产的石墨烯薄片往往厚度不均匀,且石墨烯和基质之间的黏合会影响制得的石墨烯薄片的特性。 1.3液相和气相直接剥离法 液相和气相直接剥离法指的是直接把石墨或膨胀石墨(EG)(一般通过快速升温至1000°C以上把表面含氧基团除去来获取)加在某种有机溶剂或水中,借助超声波、加热或气流的作用制备一定浓度的单层或多层石墨烯溶液。Coleman等参照液相剥离碳纳米管的方式将墨分散在N-甲基-吡咯烷酮(NMP)中,超声1h后单层石墨烯的产率为1%,而长时间的 超声(462h)可使石墨烯浓度高达1.2mg/mL。研究表明,当溶剂与石墨烯的表面能相匹配时,溶剂与石墨烯之间的相互作用可以平衡剥离石墨烯所需的能量,能够较好地剥离石墨烯
电化学法制备石墨烯
电化学法制备石墨烯 石墨烯(Graphene,GN)是由sp2杂化C原子组成的具有蜂窝状六边形结构的二维平面晶体。石墨烯独特的结构特征使其具有优异的物理、化学和机械等性能,在晶体管太阳能电池传感器、锂离子电池、超级电容器、导热散热材料、电发热膜、场发射和催化剂载体等领域有着良好的应用前景。石墨烯的制备方法对其品质和性能有很大影响,低成本、高品质、大批量的制备技术是石墨烯能得到广泛应用的关键。现有制备石墨烯的方法有很多,包括机械剥离石墨法、液相剥离法、溶剂热合成法、化学气相沉积法、外延生长法和电化学法等。其中,电化学方法因其成本低、操作简单、对环境友好、条件温和等优点而越来越受到人们的关注。据最新研究报道,通过电化学方法制备的石墨烯可以达到克量级,这为石墨烯的工业化生产带来了曙光。 电化学制备技术则是通过电流作用进行物质的氧化或还原,不需要使用氧化剂或还原剂而达到制备与提纯材料的目的,具有生产工艺简单、成本低、清洁环保等优点,已在冶金、有机与聚合物合成、无机材料制备等方面得到广泛应用。而且通过电化学电场作用,可以实现外在电解液离子(分子)对一些层状材料的插入,如锂离子电池石墨负极充电时就是锂离子在石墨层间的插入及石墨层间化合物的电化学制备。根据电化学原理主要有两种路线制备石墨。 1、通过电化学氧化石墨电极可得氧化石墨烯,再通过电化学还原以实 现电化学或化学氧化的氧化石墨烯的还原而得到石墨烯材料。 2、采用类似液相剥离,但施以电场力作用驱动电解液分子以电化学方式直接对石墨阴极进行插层,使石墨层间距变大,层间范德华力变弱,以非氧化方式直接对石墨片层进行电化学剥离制备得到石墨烯。 电化学法制备石墨烯的优势主要为:1)与普通化学氧化还原法相比,不需要用到强氧化剂、强还原剂及有毒试剂,成本低,清洁环保;2)通过电化学方式,在氧化时可以更多地以离子插入方式剥离而减少氧化程度降低对石墨烯结构的破坏,电化学还原时则能更彻底还原,因此制得的石墨烯具有更好的物理化学性质;3)以石墨工作电极为阴极进行非氧化直接剥离时,石墨片层结构没有受到破坏,可以得到与液相或机械剥离法一样高品质的石墨烯片,但因为电化学的强电场作用,比单纯的溶剂表面作用力或超声作用力要大得多,剥离的效率更高,与液相或机械剥离法相比,电化学剥离易实现高品质石墨烯批量制备;4)电化学制备过程中,电流与电压很容易精确控制,因此容易实现石墨烯的可控制备与性能调控,而且电化学法工艺过程与设备简单,容易操作控制;5)与CVD 及有机合成法相比,电化学法采用石墨为原料,我国石墨产量居世界前列,原料丰富成本低廉,不需要用到烯类等需大量进口的高价石化原料。 一、石墨阳极氧化剥离制备石墨烯 阳极氧化剥离制备石墨烯就是将石墨作为阳极,电源在工作时电解质中的阴离子向阳极移,进而进入阳极石墨导致石墨被插层而体积膨胀,当阳极石墨的体积增加到一定程度时,就会由于层间范德华作用力的减小而最终从块体上脱落下来,形成层状具有一定含氧官能团的石墨烯或氧化石墨烯(包括单层和2~10层的少层氧化石墨烯)。石墨由于电化学氧化和酸性阴离子的插层导致表面体积剧烈膨胀,这种现象在很早之前就有报道。近年来提出了电化学法阳极氧化石墨制备石墨烯的机理,在进行电化学反应时电解液中的阴离子会向阳极迁移,由于石
阳极氧化工艺流程完整版
阳极氧化工艺流程 HEN system office room 【HEN16H-HENS2AHENS8Q8-HENH1688】
铝及铝合金阳极氧化着色工艺流程及原辅材料 铝及铝合金阳极氧化着色工艺规程 1、工艺流程(线路图) 基材→装挂→脱脂→碱蚀→中和→阳极氧化→电解着色→封孔→电泳涂 漆→固化→卸料包装→入库 2、装挂: 装挂前的准备。 2.1.1检查导电梁、导电杆等导电部位能否充分导电、并定期打磨、清洗或修理。 准备好导电用的铝片和铝丝。 检查气动工具及相关设备是否正常。 核对流转单或生产任务单的型号、长度、支数、颜色、膜厚等要求是否与订单及实物相符。 根据型材规格(外接圆尺寸、外表面积等)确定装挂的支数和间距、色料间距控制在型材水平宽度的倍左右,白料间距控制在型材宽度的1倍左右。 选择合适的挂具,确保正、副挂具的挂钩数与型材的装挂支数一致。 装挂: 装挂时应先挂最上面一支,再固定最下面一支,然后将其余型材均匀排布在中间、并旋紧所有铝螺丝。 装挂前在型材与铝螺丝间夹放铝片,以防型材与挂具间的导电不良而影响氧化、着色或电泳。 装挂时,严禁将型材全部装挂在挂具的下部或上部。 装挂的型材必须保持一定的倾斜度(>5°)以利于电泳或着色时排气,减少斑点(气泡)。 装挂时必须考虑型材装饰面和沟槽的朝向、防止色差、汽泡、麻点产生在装饰面上。
易弯曲、变形的长型材,在型材的中间部位增加一支挂具或采用铝丝吊挂以防型材间碰擦或触碰槽内极板,而擦伤或烧伤型材表面。 选用副杆挂具时,优先选用插杆,采用铝丝绑扎时,一定要间隔均匀,露头应小于25mm。 截面大小、形状悬殊的型材严禁装挂在同一排上。 装挂或搬运型材,必须戴好干净手套,轻拿轻放、爱护、防护好型材表面,严禁野蛮操作。 装挂或搬运型材时必须加强自检和互检,不合格的型材严禁装挂,表面沾有油污或铝屑(毛刺)的型材必须采取适当的措施处理干净。 剔除不合格型材后,必须按订单支数及时补足。 装挂区的型材不宜存放太久,以防废气腐蚀型材表面。 认真填写《装挂记录》和《氧化工艺流程卡》上装挂部分的记录,准确计算填写每挂氧化面积,随时核对订单,确保型号、支数、颜色不出差错。 认真做好交接班手续和工作区的环境卫生。 3、氧化台生产前的准备工作: 检查各工艺槽的液面高度,根据化验报告单调整各槽液浓度,确保槽液始终符合工艺要求,并经常清除槽液中的污物。 检查行车、冷冻机、整流器、循环酸泵、水泵、转移车、固化炉等设备是否正常,如有异常应及时排除,严禁带病运行。 检查纯水洗槽和自来水洗槽的PH(或电导率)和洁净度、不符合工艺要求的应及时更换或补水溢流。 打开碱蚀、热纯水槽、封孔槽的蒸汽或冷却水,打开氧化槽、着色槽、电泳槽的循环冷却系统,确保槽液均匀、温度达到工艺要求。 检查罗茨风机和抽、排风机,并在生产前开启。 认真核对《氧化工艺流程卡》,明确生产要求,准备好比色用色板。 4、氧化台操作的通用要求: 每次吊料不准超过两挂,并且两挂之间必须保持一定的间距,以防型材之间的碰擦伤。 型材吊进、吊出槽液时必须斜进、斜出,倾斜度应控制在30°左右。