加工变形原因分析及工艺诊断

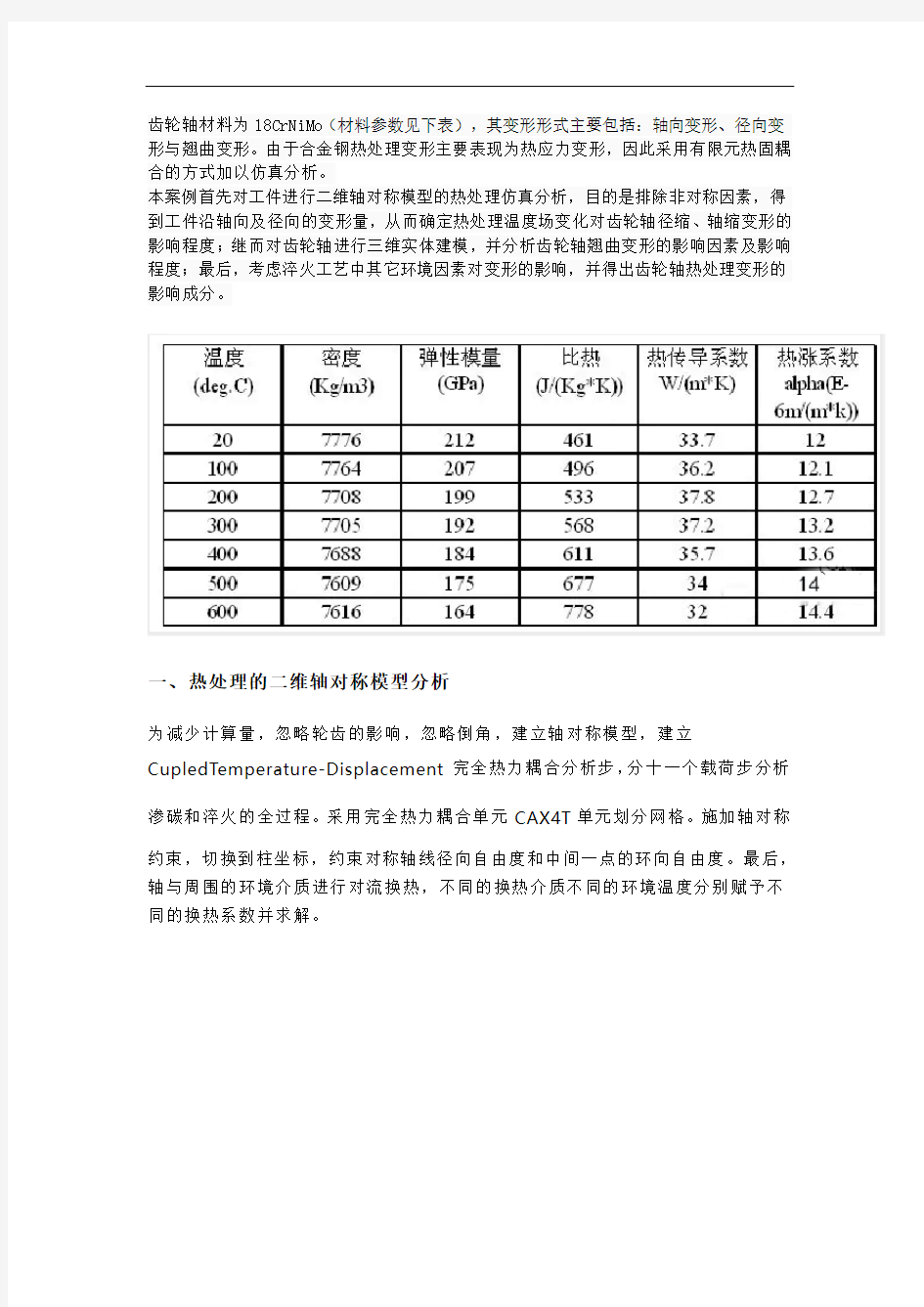
加工变形原因分析及工艺诊断
“变形”是指由于应力、温度、时间、环境介质以及人为操作等因素造成的结构件的实际尺寸与理想尺寸之间的偏差,当其超过了设计指标允许的范畴,便会凸显为结构件的“变形问题”——部分甚至全部丧失原有的功能。结构件的“加工变形”问题是由残余应力、切削力、切削热、装夹等多种因素的耦合造成的,由于上述因素的隐蔽性与偶然性,难以凭借经验根据现场记录对上述变形原因进行逐一排查;结构件加工过程的复杂程度——成型、热处理及切削加工等多重工序作用结果的累积效应,进一步增加了加工变形原因分析的难度。
加工变形原因分析与工艺诊断是通过实验检测辅助加工工艺仿真,寻求和探索制造加工的变形原因、规律和机理,建立加工变形的预测模型,为优化制造加工工艺提供理论依
据,从而减少和避免相似变形问题的重复发生。
输出长齿轮轴工艺诊断案例
大型输出长齿轮轴是应用于水电、风电、船舶动力等领域传动系统中的关键部件,通常的加工工艺为:锻造-退火-正火-粗加工-滚齿-渗碳-淬火-回火-精加工。由于处在传动系的末级,工作环境为高周次、低载荷(增速箱),或者低周次、高载荷(减速箱),因此,必须通过合金化与热处理强化力学性能,并通过提高加工与装配精度保证其动平衡性。然而,为了保证材料的可加工型与成品力学性能而引入的复杂热处理工艺,在零件的成型与加工过程产生机械-温度的强耦合,严重的影响尺寸精度,同时,其工艺复杂性及其与诸多因素的二次耦合,为变形原因的排查及解决方式的探究增加了新的难度。
齿轮轴材料为18CrNiMo(材料参数见下表),其变形形式主要包括:轴向变形、径向变形与翘曲变形。由于合金钢热处理变形主要表现为热应力变形,因此采用有限元热固耦合的方式加以仿真分析。
本案例首先对工件进行二维轴对称模型的热处理仿真分析,目的是排除非对称因素,得到工件沿轴向及径向的变形量,从而确定热处理温度场变化对齿轮轴径缩、轴缩变形的影响程度;继而对齿轮轴进行三维实体建模,并分析齿轮轴翘曲变形的影响因素及影响程度;最后,考虑淬火工艺中其它环境因素对变形的影响,并得出齿轮轴热处理变形的影响成分。
一、热处理的二维轴对称模型分析
为减少计算量,忽略轮齿的影响,忽略倒角,建立轴对称模型,建立CupledTemperature-Displacement完全热力耦合分析步,分十一个载荷步分析渗碳和淬火的全过程。采用完全热力耦合单元CAX4T单元划分网格。施加轴对称
约束,切换到柱坐标,约束对称轴线径向自由度和中间一点的环向自由度。最后,轴与周围的环境介质进行对流换热,不同的换热介质不同的环境温度分别赋予不同的换热系数并求解。
二、热处理过程的三维仿真:
对比二维和三维热处理仿真结果,发现工件经过热处理后轴向与径向变形情况与工件的实际变形十分接近,因此可以确定上述变形主要是由于热处理工艺环节的温度场变化造成的。但三维仿真得到翘曲变形与实际情况仍存在一定差距,关于该部分变形的原因还需要进行进一步的分析。
?其它因素仿真分析:
由上述分析可见,齿轮轴热处理变形主要是由于温度场变化不均匀导致的热应力造成的。真实的热处理过程中对工件温度、温度变化速度、变形等的影响因素更为复杂,还包括:
?工件进入淬火前的残余应力与变形情况;
?工件淬火过程的入油速度与入油顺序;
?淬火过程中工件与淬火油温度场的耦合作用;
?淬火工程中工件的摆放方式;
?淬火过程中淬火油液池的容量、材质及其与油液的热交换方式等。
综合考虑上述因素后,进行多轴淬火过程仿真,并以横截面代替整根轴,观察上述因素对圆截面上温度场变化的影响如下图。
由上图可知,建立“轴—液—池”淬火过程温度—应力变化模型,在整个淬火降温过程中,温度梯度不再单纯沿齿轮轴径向分布,而是根据多根轴的相对位置关系,呈现靠近几何中心位置的温度较高,四周温度较低的分布规律。而该温度梯度分布规律将显著影响齿轮轴的淬火应力,及其淬火后的变形特征,尤其是翘曲变形。
下表进行了两种条件下的齿轮轴淬火仿真结果与实际情况的相似度对比,复杂仿真条件下对齿轮轴翘曲变形的仿真准确性有显著提高。可见,根据上述变形机理与原因分析,已经建立了相对准确的工件热处理变形模型,并可依次模型及对应的变形原因,在仿真环境下快捷、高效的以较低成本指导并设计相应的热处理工艺优化方案。
在广义的“失效分析”领域,按材料的损伤机理分类,变形问题与材料的断裂、磨损、腐蚀问题为材料失效的四种主要形式。同时,变形问题可分为加工阶段的即时变形与服役阶段的延迟变形,由于后者主要是由于前者引入的残余应力与工况载荷、时间、温度等因素耦合造成的,因此,有必要建立加工过程仿真及变形预测模型,完善工艺诊断与加工变形分析体系,为加工变形问题解决方案的探寻提供快捷、高效、直接的路径。
02注塑产品变形解决办法
一、翘曲变形是指注塑制品的形状偏离了模具型腔的形状,它是塑料制品常见的缺陷之一。出现翘曲变形的原因很多,单靠工艺参数解决往往力不从心。结合相关资料和实际工作经验,下面对影响注塑制品翘曲变形的因素作简要分析。 二、模具的结构对注塑制品翘曲变形的影响。 在模具方面,影响塑件变形的因素主要有浇注系统、冷却系统与顶出系统等。1.浇注系统注塑模具浇口的位置、形式和浇口的数量将影响塑料在模具型腔内的填充状态,从而导致塑件产生变。 流动距离越长,由冻结层与中心流动层之间流动和补缩引起的内应力越大;反之,流动距离越短,从浇口到制件流动末端的流动时间越短,充模时冻结层厚度减薄,内应力降低,翘曲变形也会因此大为减少。一些平板形塑件,如果只使用一个中心浇口,因直径方向上的收缩率大于圆周方向上的收缩率,成型后的塑件会产生扭曲变形;若改用多个点浇口或薄膜型浇口,则可有效地防止翘曲变形。 当采用点浇口进行成型时,同样由于塑料收缩的异向性,浇口的位置、数量都对塑件的变形程度有很大的影响。 另外,多浇口的使用还能使塑料的流动比(L/t)缩短,从而使模腔内熔体密度更趋均匀,收缩更均匀。同时,整个塑件能在较小的注塑压力下充满。而较小的注射压力可减少塑料的分子取向倾向,降低其内应力,因而可减少塑件的变形。 2. 冷却系统 在注射过程中,塑件冷却速度的不均匀也将形成塑件收缩的不均匀,这种收缩差别导致弯曲力矩的产生而使塑件发生翘曲。 如果在注射成型平板形塑件(如手机电池壳)时所用的模具型腔、型芯的温度相差过大,由于贴近冷模腔面的熔体很快冷却下来,而贴近热模腔面的料层则会继续收缩,收缩的不均匀将使塑件翘曲。因此,注塑模的冷却应当注意型腔、型芯的温度趋于平衡,两者的温差不能太大(此时可考虑使用两个模温机)。 除了考虑塑件内外表的温度趋于平衡外,还应考虑塑件各侧的温度一致,即模具冷却时要尽量保持型腔、型芯各处温度均匀一致,使塑件各处的冷却速度均衡,从而使各处的收缩更趋均匀,有效地防止变形的产生。因此,模具上冷却水孔的布置至关重要。在管壁至型腔表面距离确定后,应尽可能使冷却水孔之间的距离小,才能保证型腔壁的温度均匀一致。同时,由于冷却介质的温度随冷却水道长度的增加而上升,使模具的型腔、型芯沿水道产生温差。因此,要求每个冷却回路的水道长度小于2米。在大型模具中应设置数条冷却回路,一条回路的进口位于另一条回路的出口附近。对于长条形塑件,应采用直通型水道。(而我们的模具大多是采用S型回路----既不利于循环,又延长周期。) 3. 顶出系统 顶出系统的设计也直接影响塑件的变形。如果顶出系统布置不平衡,将造成顶出力的不平衡而使塑件变形。因此,在设计顶出系统时应力求与脱模阻力相平衡。另外,顶出杆的截面积不能太小,以防塑件单位面积受力过大(尤其在脱模温度太高时)而使塑件产生变形。顶杆的布置应尽量靠近脱模阻力大的部位。在不影响塑件质量(包括使用要求、尺寸精度与外观等)的前提下,应尽可能多设顶杆以减少塑件的总体变形(换顶杆为顶块就是这个道理)。 用软质塑料(如TPU)来生产深腔薄壁的塑件时,由于脱模阻力较大,而材料又较软,如果完全采用单一的机械顶出方式,将使塑件产生变形,甚至顶穿或产生折叠而造成塑件报废,如改用多元件联合或气(液)压与机械式顶出相结合的方式效果会更好(以后会用到)。 三、塑化阶段对制品翘曲变形的影响 塑化阶段即由玻璃态料粒转化为粘流态熔体的过程(培训时讲过原料塑化的三态变化)。在这个过程中,聚合物的温度在轴向、径向(相对螺杆而言)温差会使塑料产生应力;另外,注射机的注射压力、速率等参数会极大地影响充填时分子的取向程度,进而引起翘曲变形。 四、充填及冷却阶段对制品翘曲变形的影响 熔融态的塑料在注射压力的作用下,充入模具型腔并在型腔内冷却、凝固。此过程是注射成型的关键环节。
注塑件常见品质问题及原因分析、解决方法
注塑件常见品质问题及原因分析、解决方法 一、注塑件常见品质问题 塑胶件成型后,与预定的质量标准(检验标准)有一定的差异,而不能满足下工序要求,这就是塑胶件缺陷,即常说的品质问题,要研究这些缺陷产生原因,并将其降至最低程度,总体来说,这些缺陷不外乎是由如下几方面造成:模具、原材料、工艺参数、设备、环境、人员。现将缺陷问题总结如下: 1、色差:注塑件颜色与该单标准色样用肉眼观看有差异,判为色差,在标准的光源下(D65)。 2、填充不足(缺胶):注塑件不饱满,出现气泡、空隙、缩孔等,与标准样板不符称为缺胶。 3、翘曲变形:塑胶件形状在塑件脱模后或稍后一段时间内产生旋转和扭曲现象,如有直边朝里,或朝外变曲或平坦部分有起伏,如产品脚不平等与原模具设计有差异称为变形,有局部和整体变形之分。 4、熔接痕(纹):在塑胶件表面的线状痕迹,由塑胶在模具内汇合在一起所形成,而熔体在其交汇处未完全熔合在一起,彼此不能熔为一体即产生熔接纹,多表现为一直线,由深向浅发展,此现象对外观和力学性能有一定影响。 5、波纹:注塑件表面有螺旋状或云雾状的波形凹凸不平的表征现象,或透明产品的里面有波状纹,称为波纹。 6、溢边(飞边、披锋):在注塑件四周沿分型线的地方或模具密封面出现薄薄的(飞边)胶料,称为溢边。 7、银丝纹:注塑件表面的很长的、针状银白色如霜一般的细纹,开口方向沿着料流方向,在塑件未完全充满的地方,流体前端较粗糙,称为银丝纹(银纹)。
8、色泽不均(混色):注塑件表面的色泽不是均一的,有深浅和不同色相,称为混色。 9、光泽不良(暗色):注塑件表面为灰暗无光或光泽不均匀称为暗色或光泽不良。 10、脱模不良(脱模变形):与翘曲变形相似,注塑件成型后不能顺利的从模具中脱出,有变形、拉裂、拉伤等、称为脱模不良。 11、裂纹及破裂:塑胶件表面出现空隙的裂纹和由此形成的破损现象。 12、糊斑(烧焦):在塑件的表面或内部出现许多暗黑色的条纹或黑点,称为糊斑或烧焦。 13、尺寸不符:注塑件在成型过程中,不能保持原来预定的尺寸精度称为尺寸不符。 14、气泡及暗泡:注塑件内部有孔隙,气泡是制品成型后内部形成体积较小或成串孔隙的缺陷,暗泡是塑胶内部产生的真空孔洞。 15、表面混蚀:注塑件表面呈现无光、泛白、浊雾状外观称为混蚀。 16、凹陷:注塑件表面不平整、光滑、向内产生浅坑或陷窝。 17、冷料(冷胶):注塑件表面由冷胶形成的色泽、性能与本体均不同的塑料。 18、顶白/顶高:注塑件表面有明显发白或高出原平面。 19、白点:注塑件内有白色的粒点,粒点又叫“鱼眼”,多反映在透明制品上。 20、强度不够(脆裂):注塑件的强度比预期强度低,使塑胶件不能承受预定的负裁 二、常见品质(缺陷)问题产生原因 1、色差: ①原材料方面因素:包括色粉更换、塑胶材料牌号更改,定型剂更换。
塑胶产品变形的一些原因
塑胶产品变形的一些原因 翘曲变形是指注塑制品的形状发生畸变而翘曲不平,偏离了制件的形状精度要求,它是注射模设计和注射生产中常见的较难解决的制品缺陷之一。 随着塑料工业的发展,特别是电子信息产业的发展,对塑料制品的外观和使用性能要求越来越高。如笔记本及掌上电脑,扁薄手机等塑壳制件,翘曲变形程度已作为评定产品质量的重要指标之一,越来越受到模具设计者的关注与重视。希望在设计阶段预测出塑料件可能产生的翘曲原因,以便优化设计,减小产品的翘曲变形,达到产品设计的精度要求。 1、翘曲变形产生的原因 翘曲变形是制品在注射工艺过程中,应力和收缩不均匀而产生的。脱模不良,冷却不足,制件形状和强度不宜,模具设计和工艺参数不佳等也使塑件发生曲变。 模温不匀,塑件内部温度不均匀。 塑件壁厚差异和冷却不均匀,导致收缩的差异。 塑件厚向冷凝压差和冷却速差。 塑件顶出时温度偏高或顶出受力不匀。
塑件形状不当,具有弯曲或不对称的形状。 模具精度不良,定位不可靠,致使塑件易翘曲变形。 进料口位置不当,注射工艺参数不佳,使收缩方向性明显,收缩不均匀。 流动方向和垂直于流动方向的分子链取向性差异,致使收缩率不同。 凸凹模壁厚向不对称冷却,冷却时间不足,脱模后冷却不当。 2、模具结构对注塑件翘曲变形的影响 在模具设计方面,影响塑件翘曲变形的因素主要有三大系统,分别是浇注系统、冷却系统与顶出系统等。 浇口的设计 注塑模浇口是整个浇注系统的关键部分,它的位置、形式和浇口的数量直接影响熔料在模具型腔内的填流状态,导致塑料固化、收缩和内应力的异变。常用的浇口类型有侧浇口、点浇口、潜伏式浇口、直浇口、扇形浇口以及薄膜型浇口等。 浇口位置的选择应使塑料的流动距离最短。流动距离越长,内部流动层与外部冻结层之间的流动差增加,这样冻结层与中心流动层之间流动和补缩引起的内应力愈大,塑件变形也随之增大;反之,流动距离越短,从浇口到制件流动末端的流动时间越短,充模时冻结层厚度减薄,内应力降低,翘曲变形也会因此减小。 如精密薄壁较大塑件,使用一个中心浇口或一个侧浇口,因径向收缩率大于周向收缩率,成型后的塑件会产生较大的扭曲变形;若改用多个点浇口或薄膜型浇口,则可有效地防止翘曲变形,因此设计时须进行流动比计算校核。 当采用点浇口成型时,同样由于塑料收缩的异向性,浇口的位置、数量都对塑件的变形程度有很大的影响。
注塑产品缺陷的解决
注意: 1)放电加工原理,放电加工是利用电能转换成工件热能,使工件急速熔融的一种热性加工方法。放电加工时,电极与工件的间隙中产生过渡电弧放电现象,进而对工件产生热作用,同时,加工中液体由于受到放电压力及热作用产生气化爆发现象,此时工件的熔融部份,将伴随液体气化融入加工液中,工件因放电的作用产生放电痕,如此反复进行,我们所希望的形状便可加工完成了。 2)线切割原理,铜丝接近工件(并未与工件接触),对工件及铜线加上电压而产生电弧和高温(9000o C—10000o C),融蚀后将金属残屑吹出,铜丝继续前进,工件冷却后即形成粗糙的被切割面。 七、塑胶射出成型产品的外观问题与对策 1、塑胶射出成型产品的外观问题 积风(Air Trap);发赤(Blush);毛边(Flash);流痕(Flow Line or Flow Mark);喷流(蛇纹)(Jetting);短射(Short Shot);凹陷或缩孔(Sink Mark or Vord);条纹(Streak);熔接线(Weld Line) 2、积风——Air Trap 积风的定义:空气或气体不及排出,被溶胶波前包夹在型腔内。 ●成品 1)壁厚差异太大,产生跑道效应(Race Track Effect),壁厚差异太大时,薄壁处塑流迟缓,溶胶循厚壁快速超前,有可能对型腔中空气或气体进行包抄,
行程积风。 2)CAE可以预测充填模式(Filling Pattern)和可能的积风点。更改厚度分布,使壁厚尽可能保持均一,以避免积风。 ●模具 1)浇口(Gate)位置不当:a.浇口位置不当时,塑流有可能包抄空气或气体,形成积风;b. CAE可以预测充填模式(Filling Pattern)和可能的积风点。 更改浇口位置,可以改变充填模式,积风有可能避免。 2)流道(Runner)或浇口尺寸不当:a.多浇口设计时,流道或浇口尺寸如果不当,塑流有可能赶超空气或气体,形成积风;b. CAE可以预测充填模式(Filling Pattern)和可能的积风点。更改浇口位置,可以改变充填模式,积风有可能避免。 3)排气不良:a.若是排气不良,波前收口处会卷入空气或气体,形成积风;b. CAE可以预测充填模式(Filling Pattern)和可能的积风点。在可能的积风点加排气口,以避免积风。 ●射出成形机 射速过高时,产生喷流(Jetting),有可能卷入气体而形成积风。降低射速,可以稳定塑流,防止喷流,避免积风。 3、发赤——Blush 发赤的定义:浇口附近产生的云状色变。有时会在塑流通道中形成阻碍处发现。原因是溶胶破折(Fracture)。
注塑件变形的原因及解决方法
注塑件变形解决方法 注塑件形状与模腔相似但却是模腔形状的扭曲版本。可能出现问题的原因: ??? (1)弯曲是因为注塑件内有过多内部应力。 ??? (2)模具填充速度慢。??? (3)模腔内塑料不足。 ??? (4)塑料温度太低或不一致。??? (5)注塑件在顶出时太热。 ??? (6)冷却不足或动、定模的温度不一致。 ??? (7)注塑件结构不合理(如加强筋集中在一面,但相距较远)。 ?? 补救方法: ??? (1)降低注塑压力。???? (2)减少螺杆向前时间。 ??? (3)增加周期时间(尤其是冷却时间)。从模具内(尤其是较厚的注塑件)顶出后立即浸入温水中(38℃)使注塑件慢慢冷却。 ??? (4)增加注塑速度。??? (5)增加塑料温度。??? (6)用冷却设备。 ??? (7)适当增加冷却时间或改善冷却条件,尽可能保证动、定?模的模温一致。 (8)根据实际情况在允许的情况下改善塑料件的结构。 透明塑料注塑过程中应注意的常见问题
透明塑料由于透光率要高,必然要求塑料制品表面质量要求严格,不能有任何斑纹、气孔、泛白、雾晕、黑点、变色、光泽不佳等缺陷,因而在整个注塑过程对原料、设备、模具、甚至产品的设计,都要十分注意和提出严格甚至特殊的要求。其次由于透明塑料多为熔点高、流动性差,因此为保证产品的表面质量,往往需要较高的温度,注射压力、注射速度等工艺参数也要作细微调整,使注塑料时既能充满模,又不会产生内应力而引起产品变形和开裂。? ??? 因此从原料准备,对设备和模具要求、注塑工艺和产品的原料处理几方面都要进行严格的操作。??? (一)原料的准备与干燥 ??? 由于在塑料中含有任何一点杂质,都可能影响产品的透明度,因此和储存、运输、加料过程中都必须注意密封,保证原料干净。特别是原料中含有水分,加热后会引起原料变质,所以一定要干燥。在注塑时,加料必须使用干燥料斗。还要注意一点的是干燥过程中,输入的空气最好应经过滤、除湿,以便保证不会污染原料。其干燥工艺如下表,透明塑料的干燥工艺: 材料干燥温度(℃)干燥时间(h)料层厚度(mm)备注 PMMA 70~80 2~4 30~40 PC 120~130 >6 <30 采用热风循环干燥 PET 140~180 3~4 采用连续干燥加料装置为佳透明塑料注塑过程中应注意的常见问题??? (二)机筒、螺杆及其附件的清洁
注塑件变形的原因及解决方法
注塑件形状与模腔相似但却是模腔形状的扭曲版本。可能出现问题的原因: (1)弯曲是因为注塑件有过多部应力。 (2)模具填充速度慢。(3)模腔塑料不足。 (4)塑料温度太低或不一致。(5)注塑件在顶出时太热。 (6)冷却不足或动、定模的温度不一致。 (7)注塑件结构不合理(如加强筋集中在一面,但相距较远)。 补救方法: (1)降低注塑压力。(2)减少螺杆向前时间。 (3)增加周期时间(尤其是冷却时间)。从模具(尤其是较厚的注塑件)顶出后立即浸入温水中(38℃)使注塑件慢慢冷却。 (4)增加注塑速度。(5)增加塑料温度。(6)用冷却设备。 (7)适当增加冷却时间或改善冷却条件,尽可能保证动、定模的模温一致。
(8)根据实际情况在允许的情况下改善塑料件的结构。 透明塑料由于透光率要高,必然要求塑料制品表面质量要求严格,不能有任何斑纹、气孔、泛白、雾晕、黑点、变色、光泽不佳等缺陷,因而在整个注塑过程对原料、设备、模具、甚至产品的设计,都要十分注意和提出严格甚至特殊的要求。其次由于透明塑料多为熔点高、流动性差,因此为保证产品的表面质量,往往需要较高的温度,注射压力、注射速度等工艺参数也要作细微调整,使注塑料时既能充满模,又不会产生应力而引起产品变形和开裂。 因此从原料准备,对设备和模具要求、注塑工艺和产品的原料处理几方面都要进行严格的操作。 (一)原料的准备与干燥 由于在塑料中含有任何一点杂质,都可能影响产品的透明度,因此和储存、运输、加料过程中都必须注意密封,保证原料干净。特别是原料中含有水分,加热后会引起原料变质,所以一定要干燥。在注塑时,加料必须使用干燥料斗。还要注意一点的是干燥过程中,输入的空气最好应经过滤、除湿,以便保证不会
注塑零件翘曲变形机理
Warpage WARPAGE Warpage can be defined as a dimensional distortion in a molded product after it is ejected from the mold at the end of the injection molding process. Warpage is sometimes called ``potato-chipping'' because the part tends to appear wavy. Machine Inadequate Injection Pressure or Time Explanation: If too little injection pressure is used the plastic material will tend to cool and solidify before the mold is packed out. If no packing is achieved the individual molecules are not held tightly together and have space to move while the part is cooling. Also, if the injection hold time is not long enough, the packing process is minimized and the molecules can relax before full solidification occurs. In either case, as the part cools it is uncontrolled and the plastic is allowed to move because it is not being constrained. Each area of the part cools at a different rate and warpage will occur due to the differences. Solution: Increase the injection pressure or time applied. This will ensure the total part is cooling while constrained and the tendency for warpage will be minimized. Inadequate Residence Time Explanation: Residence time is the amount of time a material must spend being exposed to heat in the barrel. The time is determined by the ability of the specific resin to absorb heat enough to be properly processed. Inadequate residence time will result in under-heated material, which causes the material to be stiff. It will cool off before the mold is packed and individual molecules will be unconstrained while they solidify. Molecules that are not constrained during cooling will shrink at differing rates throughout the part and warpage will occur. Solution: Increase the residence time by adding time to the cooling portion of the cycle. While increased cycle time may add cost to the final product, each material requires a specific minimum amount of time to absorb heat in the barrel, and if the time is not long enough warped parts will occur.
2017《注塑缺陷的原因分析与解决对策》--邓益善
注塑缺陷的原因分析与解决对策 【主办单位】一六八培训网 【时间地点】2017年04月15-16日上海 04月22-23日深圳 2017年08月19-20日上海 08月26-27日深圳 2017年12月16-17日深圳 12月23-24日上海 【收费标准】¥3200元/人(包括资料费、午餐及上下午茶点等) 3. 大量典型实例讲解、分析; 4. 学员自带不良品、现场解决问题、互动探讨; 5. 世界最先进的、全国独有的系统,全真展现注塑生产过程,动态显示生产现场看得见以及 看不见的环节和变化,等于将注塑车间搬到培训大厅。 片面的经验,对一些综合性的问题缺乏科学系统的分析能力,对已经出现的生产问题缺乏解决问题的措施。 邓益善老师基于扎实的生产实践与技术指导经历,将实实在在从根源上帮助解决这些问 第二部分:最佳注塑工艺设定方法 1. 如何设定各项关键注塑工艺参数;
2. 时间、温度、压力、速度、位置等参数设定要点; 3. 螺杆相关设定要点; 4. 多段充填的设定与实际使用; 5. 多段保压的设定与实际使用; 6. 速度/压力切换点的设定方法; 7. 多视窗注塑成型技术运用; 8. 塑料分子排向对质量的影响以及如何控制 9. 注塑残余内应力对质量的影响以及如何控制 第三部分:注塑现场问题分析与解决对策 注塑问题描述、原因分析,如常见的缩孔、缩水、不饱模、毛边、熔接痕、银丝、喷痕、烧焦、翘曲变形、开裂/破裂、尺寸超差及其它等等,以及在产品结构设计、模具设计、成型工艺控制及塑料材料等方面之全面解决对策。 1. 注塑件周边缺胶、不饱模的原因分析及解决对策; 2. 批锋(毛边)的原因分析及解决对策; 3. 注塑件表面缩水、缩孔(真空泡)的原因分析及解决对策; 4. 银纹(料花、水花)、烧焦、气纹的原因分析解决对策; 5. 注塑件表面水波纹、流纹(流痕)的原因分析及解决对策; 6. 注塑件表面夹水纹(熔接痕)、喷射纹(蛇纹)的原因分析及解决对策; 7. 注塑件表面裂纹(龟裂)的原因分析及解决对策; 8. 注塑件表面色差、光泽不良、混色、黑条、黑点的原因分析及解决对策; 9. 注塑件翘曲变形、内应力开裂的原因分析及解决对策; 10. 注塑件尺寸偏差的原因分析及解决对策; 11. 注塑件透明度不足、强度不足(脆断)的原因分析及解决对策; 12. 学员自带产品问题解答。 第四部分:模具设计优化 实际上目前有相当部分产品品质问题是由模具设计不合理导致的,只是很多模具设计相关人员将责任推给了注塑相关人员。 1. 如何设计注塑车间生产OK的模具; 2. 如何设计注塑车间稳定、高效生产的模具; 3. 如何设计上档次的模具; 4. 浇口合理设计; 5. 流道合理设计; 6. 冷却水路合理设计; 7. 产品缩水率的设定与调整; 第五部分:模流分析技术应用(融汇于第三、四部分) 如何利用目前世界最强大的Moldflow模流分析技术快速地有效地预测问题、优化注塑工艺
注塑制品变形的原因分析
注塑制品变形、弯曲、扭曲现象的发生主要是由于塑料成型时流动方向的收缩率比垂直方向的大,使制件各向收缩率不同而翘曲,又由于注射充模时不可避免地在制件内部残留有较大的内应力而引起翘曲,这些都是高应力取向造成的变形的表现。所以从根本上说,模具设计决定了制件的翘曲倾向,要通过变更成型条件来抑制这种倾向是十分困难的,最终解决问题必须从模具设计和改良着手。这种现象的主要有以下几个方面造成: 1.模具方面: (1)制件的厚度、质量要均匀。 (2)冷却系统的设计要使模具型腔各部分温度均匀,浇注系统要使料流对称避免因流动方向、收缩率不同而造成翘曲,适当加粗较难成型部份的分流道、主流道,尽量消除型腔内的密度差、压力差、温度差。 (3)制件厚薄的过渡区及转角要足够圆滑,要有良好的脱模性,如增加脱模余度,改善模面的抛光,顶出系统要保持平衡。 (4)排气要良好。 (5)增加制件壁厚或增加抗翘曲方向,由加强筋来增强制件抗翘曲能力。(6)模具所用的材料强度不足。 2.塑料方面: 结晶型比非结晶型塑料出现的翘曲变形机会多,加之结晶型塑料可利用结晶度随冷却速度增大而降低,收缩率变小的结晶过程来矫正翘曲变形。 3.加工方面:
(1)注射压力太高,保压时间太长,熔料温度太低速度太快会造成内应力增加而出现翘曲变形。 (2)模具温度过高,冷却时间过短,使脱模时的制件过热而出现顶出变形。 (3)在保持最低限度充料量下减少螺杆转速和背压降低密度来限制内应力的产生。 (4)必要时可对容易翘曲变形的制件进行模具软性定型或脱模后进行退火处理。 成型时主流道粘模的原因分析 注塑成型时主流道粘模的原因及排除方法: (1)冷却时间太短,主流道尚未凝固。 (2)主流道斜度不够,应增加其脱模斜度。 (3)主流道衬套与射嘴的配合尺寸不当造成漏流。 (4)主流道粗糙,主流道无冷却井。 (5)射嘴温度过低,应提高温度。 成型时生产缓慢的原因分析 注塑成型时生产缓慢的原因及解决方法如下: (1)塑料温度、模具温度高,造成冷却时间长。 (2)熔胶时间长。应降低背压压力,少用再生料防止架空,送料段冷却要充分。
【精品】注塑制品翘曲变形
1231慧聪网塑料讯:注塑制品翘曲变形是指注塑制品的形状偏离了模具型腔的形状,它是塑料制品常见的缺陷之一。随着塑料工业的发展,人们对塑料制品的外观和使用性能要求越来越高,翘曲变形程度作为评定产品质量的重要指标之一也越来越多地受到模具设计者的关注与重视。模具设计者希望在设计阶段预测出塑料件可能产生翘曲的原因,以便加以优化设计,从而提高注塑生产的效率和质量,缩短模具设计周期,降低成本。 本文主要对在注塑模具设计过程中影响注塑制品翘曲变形的因素加以分析. ●模具的结构对注塑制品翘曲变形的影响 在模具设计方面,影响塑件变形的因素主要有浇注系统、冷却系统与顶出系统等。 1.浇注系统的设计 注塑模具浇口的位置、形式和浇口的数量将影响塑料在模具型腔内的填充状态,从而导致塑件产生变形. 流动距离越长,由冻结层与中心流动层之间流动和补缩引起的内应力越大;反之,流动距离越短,从浇口到制件流动末端的流动时间越短,充模时冻结层厚度减薄,内应力降低,翘曲变形也会因此大为减少。图1为大型平板形塑件,
如果只使用一个中心浇口(如图1a所示)或一个侧浇口(如图1b所示),因直径方向上的收缩率大于圆周方向上的收缩率,成型后的塑件会产生扭曲变形;若改用多个点浇口(如图1c所示)或薄膜型浇口(如图1d所示),则可有效地防止翘曲变形. a)中心浇口b)侧浇口c)多点浇口d)薄膜型浇口 当采用点浇进行成型时,同样由于塑料收缩的异向性,浇口的位置、数量都对塑件的变形程度有很大的影响。图2为一箱形制件在不同浇口数目与分布下的试验图。 a)直浇口b)10个点浇口c)8个点浇口 d)4个点浇口e)6个点浇口f)4个点浇口 由于采用的是30%玻璃纤维增强PA6,而得到的是重量为4.95kg的大型注塑件,因此沿四周壁流动方向上设有许多加强肋,这样,对各个浇口都能获得充分的平衡.实验结果表明,按图f设置浇口具有较好的效果。但并非浇口数目越多越好。实验证明,按图c设计的浇口比图a的直浇口还差。 另外,多浇口的使用还能使塑料的流动比(L/t)缩短,从而使模腔内物料密度更趋均匀,收缩更均匀.同时,整个塑件能在较小的注塑压力下充满.而较小的注射压力可减少塑料的分子取向倾向,降低其内应力,因而可减少塑件的变形。
塑料件翘曲变形分析总结
塑料件翘曲变形分析 塑料件的翘曲变形是塑料件常见的成型质量缺陷。 塑料件的翘曲变形主要是因为塑料件受到了较大的应力作用,主要分为外部应力和 内部应力,当大分子间的作用力和相互缠结力承受不住这种应力作用时,塑料件就 会发生翘曲变形。 1、外部应力导致的翘曲变形 此类翘曲变形主要为制件顶出变形,产生的原因为模具顶出机构设计不合理或成型 工艺条件不合理。 1.1、模具顶出机构设计不合理 顶出机构设计不合理,顶出设计不平衡,或顶杆截面积过小,都有可能使塑料件局 部受力过大,承受不住应力作用发生塑性形变而导致翘曲变形。 防止顶出变形需改善脱模条件:如平衡顶出力;仔细磨光新型侧面;增大脱模角度;顶杆布置在脱模阻力较大的地方,如加强筋,Boss柱等处。 1.2、成型工艺参数设置不合理 冷却时间不足,凝固层厚度不够,塑料件强度不足,脱模时容易导致产品翘曲变形。 可以延长冷却时间,增加凝固层厚度来解决。 2、内部应力导致的翘曲变形 2.1、塑料内应力产生的机理 塑料内应力是指在塑料熔融加工过程中由于受到大分子链的取向和冷却收缩等因素 而产生的一种内在应力。内应力的本质为大分子链在熔融加工过程中形成的不平衡 构象,这种不平衡构象在冷却固化时不能立刻恢复到与环境条件相适应的平衡构象,这种不平衡构象实质为一种可逆的高弹形变,而冻结的高弹形变以位能情势储存在 塑料制品中,在合适的条件下,这种被迫的不稳定的构象将向自在的稳定的构象转化,位能改变为动能而开释。当大分子间的作用力和相互缠结力承受不住这种动能时,内应力平衡即受到破坏,塑料制品就会产生翘曲变形,严重时会发生应力开裂。 2.2、塑料内应力的种类 2.2.1 取向内应力 取向内应力是塑料熔体在充模流动和保压补料过程中,大分子链沿流动方向定向排列,构象被冻结而产生的一种内应力。 取向应力受塑胶流动速率和粘度的影响。如图一所示,A 层是固化层,B层是流动 高剪切层,C层是熔胶流动层。A层为充填时紧贴两侧模壁,瞬间冷却固化层。B层 是充填时紧靠A层的高剪切区域所形成的,由于与A层具有最大速度差,所以形成 最大剪切流动应力效果(如图二所示),塑胶充填结束时本区尚未完全凝固,因外 层A固化层有绝热效果,使B层散热较慢,而C层所受剪切作用较小,若产品厚度 有变化,则主要影响C层厚度,若是薄件成品则C层的厚度将会变小。
关于电饭煲注塑件的结构设计的分析
关于电饭煲注塑件的结构设计的分析 发表时间:2018-08-06T11:22:11.073Z 来源:《建筑学研究前沿》2018年第8期作者:朱喜青[导读] 塑料与钢铁、水泥、木材并称为四大工程材料。随着科学技术的进步,塑料的运用变得越来越广泛。 43018119861117xxxx 528311 摘要:塑料与钢铁、水泥、木材并称为四大工程材料。随着科学技术的进步,塑料的运用变得越来越广泛。与金属相比,塑料具有耐腐蚀、电绝缘、重量轻和成本低等优点;且塑料材质丰富、形状多变,使其具有很理想设计特性,既避免金属件必要的价格不低的二次加工和表面处理,又减少了成型对设计的限制,扩大了设计自由(注塑件可以将几个零件功能集合到某一个零件中)。电饭煲产品中,为了 成型方便、降低成本,除了发热盘、内锅、外锅、加强板等需要耐高温或刚性强的零件使用金属材料,大部分的机体零件使用各种塑料材料进行设计。由于塑料的机械性能随温度等因素影响很大,如高温使塑料的刚度和强度会降低,低温使塑料变脆;不同温度下,塑料的收缩量也不同;同时因为模具结构也有限制,不合理的设计会致一些试模及装配阶段才会发现的隐形问题,加大研发成本及耽误项目进度。基于此,本文从选材、常规设计、模具的工艺性、变形等不同方面介绍电饭煲的注塑件的结构设计。 关键词:结构设计;电饭煲;注塑件 1、电饭煲的概述 电饭煲又称作电锅、电饭锅。是利用电能转变为内能的炊具,使用方便,清洁卫生,还具有对食品进行蒸、煮、炖、煨等多种操作功能。常见的电饭锅分为保温自动式、定时保温式以及新型的微电脑控制式三类。如下图所示。 2、电饭煲注塑件的结构设计的要点 2.1材料选择 作为一个产品设计师,尤其设计结构部分,选择合理的材料是一项非常关键的工作,是成功设计一款产品、每个零件的前提条件。通常来说,不是材料不好,而是各种材料有不同的特定性能,需要设计师根据零件的使用环境、性能要求选择合适的材料。塑料的种类繁多,性能各异,而且还添加有各种增强剂、色母等填料;同时各种材料的性能数据都是在特定条件下的测试数据,与实际工作情况下有一定差别,这些都影响着材料种类的选择。虽然材料选择具有复杂性,但是在选材时也是有简单规律可参考。对于注塑件,通常首先考虑零件的工作条件,比如载荷、耐温等条件,以缩小选材范围,同时配合零件的成型工艺、外观方面要求、装配方式等要求,比如透明性、运动部件的耐磨性等确定材料选定。电饭煲为加热产品,有运动部件,同时也有食品安全要求,作为小家电,对外观配合也要求美观精良。有经验的结构设计师通常参考成熟产品、根据以往经验或者考虑供应商的推荐来选择合适的材料。电饭煲产品常用的几种塑料为PP、ABS、POM。例如,面盖、底座、内盖、支撑环等零件因为要求耐温,一般都选择食品级的PP料;装饰板、电镀件通常都选择ABS;开盖按钮推块等运动部件则都选择POM;一些需要特别耐高温的部件则选择尼龙或者PET材料;一些特殊要求的部件比如电路板支架需要选择具有阻燃性能的塑料。 2.2壁厚合理设计 合理设计壁厚对一个注塑件来说是非常关键的,注塑件的壁厚数值一般为2~3mm。一般壁厚过薄则强度和刚度弱,同时成型困难;壁厚过厚则容易缩水、成型时间长、浪费成本,对于壁厚偏厚的地方要掏胶等做防缩水工艺性设计。同时制品壁厚的设计应该均匀、圆滑过渡,若不均匀容易出现翘曲变形或者缩水等不良外观问题。电饭煲产品中,通过经验总结,底座、支撑环、内盖等对刚度和强度要求高的部件一般设计壁厚为2.5或者2.8mm厚,面盖等部件一般设计2.2mm厚,个别透明件或者无载荷的零件设计壁厚低于2mm。 2.3加强筋设计 在注塑件设计中,为了增加零件的刚度和强度,通常设计加强筋来满足要求,这样既减少塑料用量又减轻重量,在结构上也能防止注塑件翘曲变形,成型时辅助塑料流动。加强筋的设计通常要注意三个要点:第一是厚度,厚度过薄起不到加强作用也难以填充,厚度过厚会导致缩水等缺陷。电饭煲使用PP料比较多,考虑PP料容易缩水,一般设计加强筋的壁厚为主料厚的一般,非外观件可以适当厚些,一般不超过主料厚三分之二;第二是高度,适当的高度能保证刚度也易于填充成型,通常设计高度在料厚的3倍以内;第三是数量,通常数量越多,效果越好,但是考虑成本及模具结构等因素,一般数量不宜过多,排练可以稀疏些。同时由于塑料的刚度和强度相对偏弱,设计加强筋时,尽量让加强筋是受拉状态,避免失稳。 2.4拔模斜度设计 由于注塑件的成型工艺限制,设计时需要设计一定的拔模斜度。通常根据塑料的收缩率、塑料性能、制品形状及壁厚来设计拔模斜度的大小。通常结构复杂、深度偏深,难以脱膜的零件都设计有比较大的拔模斜度,电饭煲产品中PP料使用比较多,考虑其收缩率比较大,在不影响外观、装配的情况下,都尽量设计较大的拔模斜度;另外对尺寸精度要求高的运动部件或者外观斜度限制的面盖、底座等零件,都尽量设计较小的拔模斜度。 2.5避免变形、收缩设计
注塑件变形的原因及解决办法
精心整理 注塑件形状与模腔相似但却是模腔形状的扭曲版本。可能出现问题的原因: (1)弯曲是因为注塑件内有过多内部应力。 透明塑料由于透光率要高,必然要求塑料制品表面质量要求严格,不能有任何斑纹、气孔、泛白、雾晕、黑点、变色、光泽不佳等缺陷,因而在整个注塑过程对原料、设备、模具、甚至产品的设计,都要十分注意和提出严格甚至特殊的要求。其次由于透明塑料多为熔点高、流动性差,
因此为保证产品的表面质量,往往需要较高的温度,注射压力、注射速度等工艺参数也要作细微调整,使注塑料时既能充满模,又不会产生内应力而引起产品变形和开裂。 因此从原料准备,对设备和模具要求、注塑工艺和产品的原料处理几方面都要进行严格的操作。 (一)原料的准备与干燥 性差的树脂存在,因此在使用前、停机后都应用螺杆清洗剂清洗干净各件,使其不得粘有杂质,当没有螺杆清洗剂时,可用PE、PS等树脂清洗螺杆。当临时停机时,为防止原料在高温下停留时间长,引起解降,应将干燥机和机筒温度降低,如PC、PMMA等机筒温度都要降至160℃以
下(料斗温度对于PC应降至100℃以下)。 (三)在模具设计上应注意的问题(包括产品的设计) 为了防止出现回流动不畅,或冷却不均造成塑料成型不良,产生表面缺陷和变质,一般在模具设计时,应注意以下几点。 a)壁厚应尽量均匀一致,脱模斜度要足够大; b)过渡部分应圆滑,并逐步过渡,防止有尖角、锐边产生,特别是PC c)注射压力:一般较高,以克服熔料粘度大的缺陷,但压力太高会产生内应力造成脱模因难和变形; d)注射速度:在满足充模的情况下,一般宜低,最好能采用慢一快一慢多级注射; e)保压时间和成型周期:在满足产品充模,不产生凹陷、气泡的情况
注塑产品缺陷汇总及解决方法
注塑产品缺陷汇总及解决方法 一、溢料飞边 故障分析及排除方法 (1)合模力不足。当注射压力大于合模力使模具分型面密合不良时容易产生溢料飞边。对此,应检查增压是否增压过量,同时应检查塑件投影面积与成型压力的乘积是否超出了设备的合模力。成型压力为模具内的平均压力,常规情况下以40mpa计算。生产箱形塑件时,聚乙烯,聚丙烯,聚苯乙烯,及ABS的成型压力值约为30mpa;生产形状较深的塑件时,成型压力值约为36mpa;在生产体积小于10cm3的小型塑件时,成型压力值约为60mpa。如果计算结果为合模力小于塑件投影面积与成型压力的乘积,则表明合模力不足或注塑定位压力太高。应降低注射压力或减小注料口截面积,也可缩短保压及增压时间,减小注射行程,或考虑减少型腔数及改用合模吨位大的注塑机。 (2)料温太高。高温熔体的熔体粘度小,流动性能好,熔料能流入模具内很小的缝隙中产生溢料飞边。因此,出现溢料飞边后,应考虑适当降低料筒,喷嘴及模具温度,缩短注射周期。 对于聚酰胺等粘度较低的熔料,如果仅靠改变成型条件来解决溢料飞边缺陷是很困难的。应在适当降低料温的同时,尽量精密加工及修研模具,减小模具间隙。 (3)模具缺陷。模具缺陷是产生溢料飞边的主要原因,在出现较多的溢料飞边时必须认真检查模具,应重新验核分型面,使动模与定模对中,并检查分型面是否密着贴合,型腔及模芯部分的滑动件磨损间隙是否超差。分型面上有无粘附物或落入异物,模板间是否平行,有无弯曲变形,模板的开距有无按模具厚度调节到正确位置,导合销表面是否损伤,拉杆有无变形不均,排气槽孔是否太大太深。根据上述逐步检查的结果,对于产生的误差可采用机械加工的方法予以排除。 (4)工艺条件控制不当。如果注射速度太快,注射时间过长,注射压力在模腔中分布不均,充模速率不均衡,以及加料量过多,润滑剂使用过量都会导致溢料飞边,操作时应针对具体情况采取相应的措施。 值得重视的是,排除溢料飞边故障必须先从排除模具故障着手,如果因溢料飞边而改变成型条件或原料配方,往往对其他方面产生不良影响,容易引发其他成型故障。 二、熔接痕 故障分析及排除方法 (1)温太低。低温熔料的分流汇合性能较差,容易形成熔接痕。如果说塑件的内外表面在同一部位产生熔接细纹时,往往是由于料温太低引起的熔接不良。对此,可适当提高料筒及喷嘴温度或者延长注射周期,促使料温上升。同时,应节制模具内冷却水的通过量,适当提高模具温度。 一般情况下,塑件熔接痕处的强度较差,如果说对模具中产生熔接痕的相应部位进行局部加热,提高成型件熔接部位的局部温度,往往可以提高塑件熔接处的强度。 如果由于特殊需要,必须采用低温成型工艺时,可适当提高注射速度极增加注射压力,从而改善熔料的汇合性能。也可在原料配方中适当增用少量润滑剂,提高熔料的流动性能。 (2)模具缺陷。模具浇注系统的结构参数对流料的熔接状况有很大的影响,因为熔接不良主要产生于熔料的分流汇合。因此,应尽量采用分流少的浇口形式并合理选择浇口位置,尽量避免充模速率不一致及充模料流中断。在可能的条件下,应选用一点式浇口,因为这种浇口不产生多股料流,熔料不会从两个方向汇合,容易避免熔接痕。
(完整版)汽车研发注塑件工艺流程及参数解析
汽车研发注塑件工艺流程及参数解析! 塑料化是当今国际汽车制造业的一大发展趋势,尤其内外饰上大部分件都是塑料件。内饰塑料件大致有仪表盘配件、座椅配件、地板配件、顶板配件、方向盘配件、车门内饰件、后视镜以及各种卡扣和固定件;外观塑料件有前后车灯、进气格栅、挡泥板、倒车镜。今天和大家一起聊聊注塑件的工艺流程及相关重要参数。 一 定义 注塑成型工艺是指将熔融的原料通过填充、保压、冷却、脱模等操作制作一定形状的半成品件的工艺过程。
二 工艺流程 注塑工艺流程图如下: 1填充阶段 填充是整个注塑循环过程中的第一步,时间从模具闭合开始注塑算起,到模具型腔填充到大约95%为止。理论上,填充时间越短,成型效率越高。但是在实际生产中,成型时间(或注塑速度)要受到很多条件的制约。填充又可分为高速填充和低速填充。 1)高速填充 高速填充时剪切率较高,塑料由于剪切变稀的作用而存在粘度下降的情形,使整体流动阻力降低;局部的粘滞加热影响也会使固化层厚度变薄。因此在流动控制阶段,填充行
为往往取决于待填充的体积大小。即在流动控制阶段,由于高速填充,熔体的剪切变稀效果往往很大,而薄壁的冷却作用并不明显,于是速率的效用占了上风。 2)低速填充 热传导控制低速填充时,剪切率较低,局部粘度较高,流动阻力较大。由于热塑料补充速率较慢,流动较为缓慢,使热传导效应较为明显,热量迅速为冷模壁带走。加上较少量的粘滞加热现象,固化层厚度较厚,又进一步增加壁部较薄处的流动阻力。 2保压阶段 保压阶段的作用是持续施加压力,压实熔体,增加塑料密度(增密),以补偿塑料的收缩行为。在保压过程中,由于模腔中已经填满塑料,背压较高。在保压压实过程中,注塑机螺杆仅能慢慢地向前作微小移动,塑料的流动速度也较为缓慢,这时的流动称作保压流动。
塑料制品的翘曲变形分析
一、引言 翘曲变形是指注塑制品的形状偏离了模具型腔的形状,它是塑料制品常见的缺陷之一。随着塑料工业的发展,人们对塑料制品的外观和使用性能要求越来越高,翘曲变形程度作为评定产品质量的重要指标之一也越来越多地受到模具设计者的关注与重视。模具设计者希望在设计阶段预测出塑料件可能产生翘曲的原因,以便加以优化设计,从而提高注塑生产的效率和质量,缩短模具设计周期,降低成本。 本文主要对在注塑模具设计过程中影响注塑制品翘曲变形的因素加以分析。 二、模具的结构对注塑制品翘曲变形的影响 在模具设计方面,影响塑件变形的因素主要有浇注系统、冷却系统与顶出系统等。 1.浇注系统的设计 注塑模具浇口的位置、形式和浇口的数量将影响塑料在模具型腔内的填充状态,从而导致塑件产生变形。 流动距离越长,由冻结层与中心流动层之间流动和补缩引起的内应力越大;反之,流动距离越短,从浇口到制件流动末端的流动时间越短,充模时冻结层厚度减薄,内应力降低,翘曲变形也会因此大为减少。图1为大型平板形塑件,如果只使用一个中心浇口(如图1a所示)或一个侧浇口(如图1b所示),因直径方向上的收缩率大于圆周方向上的收缩率,成型后的塑件会产生扭曲变形;若改用多个点浇口(如图1c所示)或薄膜型浇口(如图1d所示),则 可有效地防止翘曲变形。 a)中心浇口 b) 侧浇口 c)多点浇口 d) 薄膜型浇口 图 1 浇口形式对塑料件变形的影响 当采用点浇进行成型时,同样由于塑料收缩的异向性,浇口的位置、数量都对塑件的变形程度有 很大的影响。图2为一箱形制件在不同浇口数目与分 布下的试验图。 a)直浇口 b)10个点浇口 c)8个点浇口 d)4个点浇口 e) 6个点浇口 f) 4个点浇口 图2 实验浇口的设置 由于采用的是30%玻璃纤维增强PA6,而得到的是重量为4.95kg的大型注塑件,因此沿四周壁流动方向上设有许多加强肋,这样,对各个浇口都能获得充分的平衡。实验结果表明,按图f设置浇口具有较好的效果。但并非浇口数目越多越好。实验证 注塑制品的翘曲变形分析