知名企业注塑模具技术规范
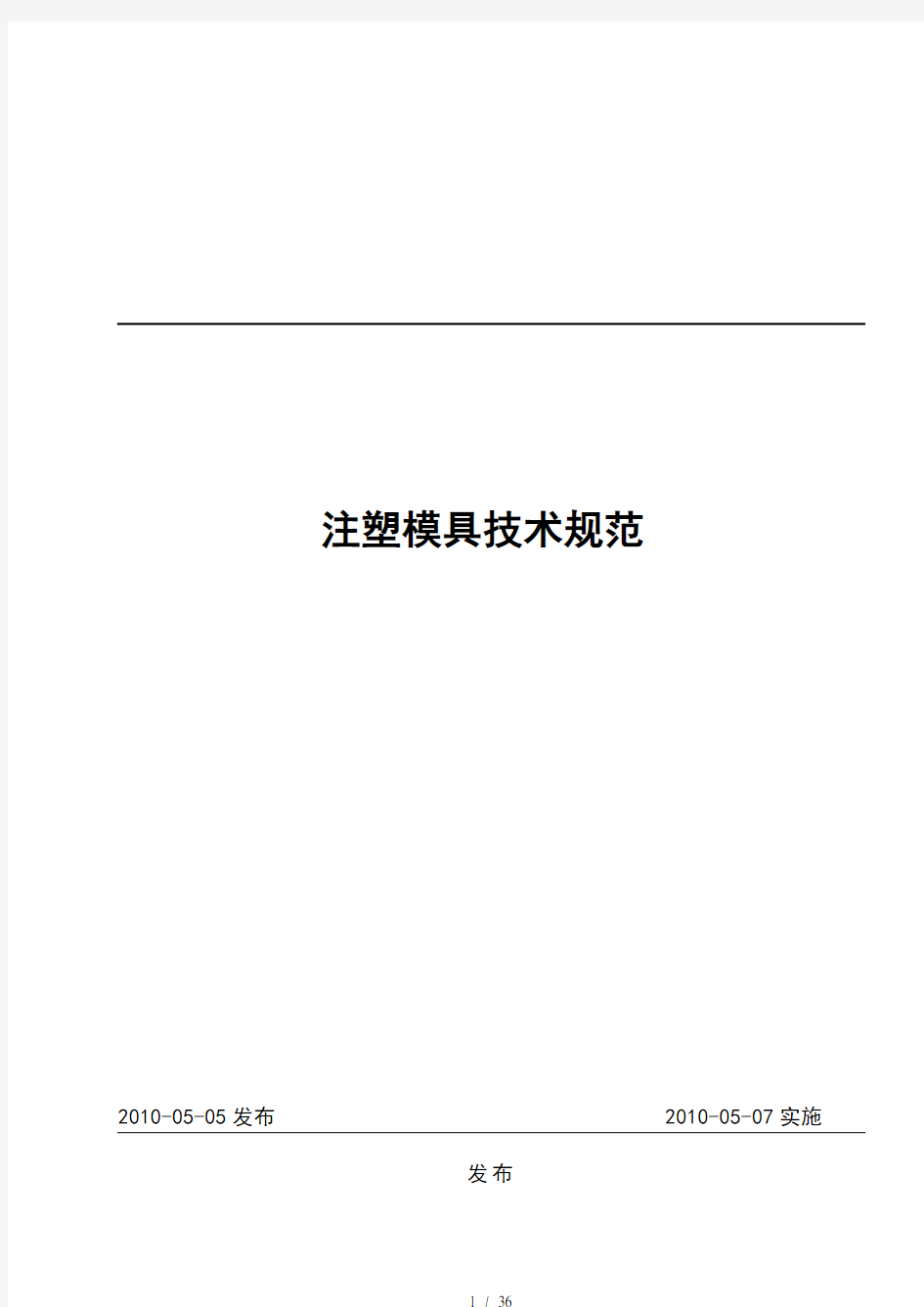

知名企业注塑模具技术规范
注塑模具技术规范
发布
1.目的
1.1 为不断提升模具质量和模具产出,确保模具制造出合格产品并正常稳定的生产;
1.2 通过实现模具的一致性来达到产品的一致;
1.3 进一步细化和规范注塑模具模具设计与制造,
2. 范围
本标准适用于家用空调国内事业部注塑模具设计与制造。
3.规范性引用文件
无
4.术语和定义
无
5.模具分类:根据模架尺寸将模具分为大、中、小三类。
5.1模架尺寸6060以上称为大型模具;
5.2模架尺寸3030~6060之间为中型模具;
5.3模架尺寸3030以下为小型模具。
6. 模架选用
6.1 模架的指定供方
名称模架类型指定供方
模架模架系统标准、非标准龙记、环盛、德胜科达、昌辉
6.2 优先选用标准模架,若选用非标模架,应优先选用标准板厚。
6.3 大型非标模架,导柱直径不小于Φ60mm。
6.4 三板细水口的大型/中型模架,导套材质采用青铜石墨套。例如:分体机底盘。
6.5 大型非标模架导套孔壁厚与模架边不得小于20mm,回针孔壁厚与模架边为35~40mm,回针直径不小于Φ30。
6.6 模架非成型部分的模板零件应采用1050材质, 硬度HB170-220。
6.7 钢导柱、导套及回针等所用材料的表面硬度不低于HRC602°。
6.8 A板、B板镶件框壁厚一般为:(小模)30~50mm、(中模)50~80mm、(大模)80~120mm。
6.9 开镶件框后B板厚度一般为:(小模)30~50mm、(中模)50~80mm、(大模)80~120mm。
6.10 镶件成型部位厚度一般为:(小模)25~35mm、(中模)35~50mm、(大模)50~70mm。
7. 模具钢材
7.1 模具钢材的选用
7.2 模具钢材的指定供方
7.3 模具钢材的热处理
7.3.1 滑块材料(外观)用2738H、2083H钢料,硬度为 HRC34~38,(非外观)用738、2083钢料,硬度 HRC29~33。
7.3.2 斜顶材料用LKM738钢料,表面进行氮化处理,硬度HV700。
7.3.3 铍铜硬度HRC36~42。
7.3.4 硬片、滑块压板、中间导滑条用2510钢料淬火至HRC48~52。
7.3.5 其中2344、2316、S136钢料需淬火至HRC48~52。
8. 标准件选用
9.模具外观
9.1 模具表面喷涂油漆进行表面防锈;所有的棱边和孔均有1mm~2mm×45°的倒角。
9.2 油漆颜色为蓝色(美的蓝)与美的商标颜色相同。
9.3 铭牌的格式、尺寸、事项、材料及加工方式符合美的文件要求;铭牌槽深3mm,周边避空0.25mm,四个用铆钉铆紧。铭牌字体为宋体18030 ,“美的家用空调国内事业部”字高4mm,其它字高3mm;铭牌边框线宽均为0.5mm;制作铭牌的字体及边框线采用蚀纹或雕刻;铭牌材料为SUS201(不锈钢),料厚为0.6mm。
9.4 铭牌内容如下:
9.5 铭牌槽及模具安装方向箭头加工示意图:
9.6 铭牌必须安装在操作人员这侧。
9.7 模具安装方向要求用箭头标明安装方向。模具(长500mm(包括500mm) 以上的模具)箭头高105mm ,宽62mm ,
模具(长500mm以下的模具)箭头高70mm ,宽40mm。
9.8 模架上各模板基准角必须倒出10X10倒角。
9.9 模架表面不允许有凹坑、锈迹,进出水、气、油孔等及其他影响外观的缺陷。
9.10 大型非标模架A板、B板起吊螺钉孔为M36~M48。
9.11 模具吊环大小和吊环孔位置要能保证吊装平衡,吊环要求旋到底;模具各板至少有2个以上吊环,模具长度方向超过600mm时,两侧必须下吊环。
9.12 模具吊环不能与水嘴、油缸、预复位杆等模具零部件干涉。模具要便于吊装、运输,吊装时原则上不得拆卸模具零部件。吊环与水嘴、油缸、预复位杆等干涉,可以更改吊环孔位置。
9.13 模具吊装平衡的标准:模具(长700mm(包括700mm) 以下的模具)吊模倾角小于3°,模具(长700mm以上的模具)吊模倾角小于5°。如不符合要加吊模块。图示如下:
9.14模具冷却水接头采用塑料快插接头,接头不能高出模具表面;冷却水嘴避空孔为¢25X25,外沿有倒角,
倒角大于 1.5×45°,倒角一致;模板运水接头有两种分别为BSPT1/4"(适合¢6,¢8,¢10,¢11运水),BSPT3/8"(适合¢12,¢14运水)。统一用¢10外接水管。斜顶有运水时要足够顶出空间接水嘴。
9.15 冷却水嘴进出标记,进水为IN,出水为OUT,上模用A,B,C表示,下模用1,2,3顺序号,如上模A IN、
A OUT,下模1 IN,1 OUT。从模架基准开始按顺时排序。
9.16 油路有多组时必须加工集油块或在模板上做油路,管接头必须有进出标记,进油为O (油)IN ,出油为O (油)OUT , OIN 、OOUT 后加顺序号,如01N1 、O1UT1。英文字符和数字为大写10号钢印字码,位置在油管接头正下方10mm 处,要求字迹清晰、美观整齐、间距均匀。
9.17 气管接头必须有进出标记,进气为G (气)IN ,出气为G (气)OUT , GIN 、GOUT 后加顺序号,如GIN01 、GOUT01 。英文字符和数字为大写10号钢印字码,位置在气管接头正下方10mm 处,要求字迹清晰、美观整齐、间距均匀。气管为透明胶管,便于区分。
9.18 模具锁模片,必须漆有警示颜色,统一使用红色,以便于安装模具和拆卸模具不会忘了拆卸和安装,保证模具安全打开和吊落。模具(长400mm(包括400mm) 以上的模具)锁模片安装1个在操作侧上方,模具(长400mm 以上的模具)锁模片安装2个,1个在操作侧上方,1个在反作侧下方。二板模锁模片,尺寸按70X30X15加工。三板模锁模片,长度可按模具高度调节,尺寸按5mm递增。
9.19 分体机面板、面框、出风框、底盘、导风条;柜机出风框、面板、顶盖、底盘、下面板、进风格栅;等成型大件细水口模必须在模具外侧,靠近限位导柱的部位对称安装重型拉勾,如图所示:
9.20 所有八条导柱结构的三板模必须在前模外侧不影响正常操作的位置增加限位拉板加以保护。
限位拉板
9.21 模架主开模面AB板之间有1MM间隙。
10. 制品模具工艺性
10.1 制品应有足够的强度和刚性。
10.2 制品壁厚均匀,变化一般不超过60%;对于特别厚的部位要采取减胶措施。
10.3 加强筋大端的厚度不超过制品壁厚的一半。
10.4 制品上的文字原则上采用凸型字,以便于加工。
10.5 制品形状应避免产生模具结构上的薄钢位。
10.6 工艺圆角是否考虑制品使用性能,是否有利于机械加工。
11.产品脱模斜度确定
11.1 客户资料有明确脱模斜度要求且合理时,按客户资料要求设计脱模斜度;
11.2 客户资料的脱模斜度不合理时,与客户沟通确定合理的脱模斜度;
11.3 客户资料未注或未有明确的脱模斜度时,应明确客户要求后再确定;
11.4 在设计脱模斜度时,也应考虑到增加脱模斜度后的制件与配合件的装配关系;
11.5 不影响制品装配的部位应设计1°以上的脱模斜度,但需防止缩水;对可能影响产品装配的部位,应通过计算确定合理的脱模斜度;有特殊要求(如蚀皮纹等)的制品,脱模斜度应不小于2.5°。
12.注塑参数校核方法
12.1 容模尺寸校核:
12.2 模具厚度+顶出距离+取出制品的距离<最大开模距离。
12.3 模具厚度>注塑机模板最小闭合距离。
12.4 模具外形尺寸不得与所配套注塑机的导柱干涉。
12.5 码模板尺寸小于注塑机模板的最大装夹尺寸。
锁模力:F≥P.A.10-2
注: F——注射机的公称锁模力(t)
P——模内平均压力(25~40MPa)
A——投影面积(包括制品、流道)cm2
13.模具与设备匹配
13.1 所有模具必须在底板上面安装欧姆龙合模保护开关,开关型号为SHL-02255;开关安装必须低于模板表面。要求:靠非操作一侧顶面安装;出线用三芯的航空对插进行固定;出线要有导线槽或孔安状方式一致。安装
合模保护
开关安装
位置示意
13.2 模具定位圈应符合指定的注塑机,定位圈高出顶板10mm;隔热板厚度为6mm,定位圈外径¢100用二个M6 或¢150用三个M8 的内六角螺丝进行固定。定位圈外径必须负0.1至0.3mm。(如指定用海天注塑机必须符合下表海天注塑机定位圈外径尺寸要求)
注塑机型号注塑机喷嘴伸出长度海天注塑机定位圈外径尺寸1250T、1000T、800T、750T 90 250 650T、460T、80 200
360T、300T 50 160
150T 20 125
13.3 浇口套球R和入口直径应大于注塑机喷嘴球R和入口直径;唧嘴球R全部为R22。360T以下唧嘴口部直径¢4mm,800T以下唧嘴口部直径¢5mm,1600T以下唧嘴口部直径¢6mm,主流道最大处不得大于¢12。
13.4 如模具采用延伸喷嘴,唧嘴内部要有足够大的空间即唧嘴内径≥¢70mm,以保证标准注塑机带加热圈的加长喷嘴可以伸入。
13.5 模具顶出孔直径应比顶出杆大5-10mm,模具长度或宽度尺寸有一个大于400mm时,原则上不能只用一个中心顶出;K.O.孔设计尽可能多且均匀分布,如果KO孔数量≥6个时,中心KO孔可以不要,尽量使顶出力量平衡,模具长度≤400mm时,KO孔排布按图1,可选择其中3个加工,直径用¢40mm,模具长度>400mm KO孔排布按图2,可选择其中6个KO孔加工。底板顶出孔位置(长400mmX宽100mm),KO孔直径为¢55mm,中心顶出孔直径为用¢70mm。
14.模具型腔与型芯
14.1 型腔模具排位应有利于各腔同时、均匀进胶。
14.2 多腔模具各型腔产品排位紧凑,有利于缩短流道长度。
14.3 多腔模具各型腔产品间距不小于15mm。
14.4 多腔模的各进胶点压力相同原则。
14.5 前后模表面必须平整、无凹坑、锈迹其他影响外观的缺陷。分型面保持干净,整洁,不能用手提砂轮打磨避空,封胶部分无缺陷。
14.6 型腔图纸必须标明模具抛光后需达到的表面粗糙度。模具后模正面的刀纹一般情况下不用去除,应仔细保护、不能破坏原有纹路,如不能保留,则须用油石去除所有纹路、刀痕、火花纹。
14.7 通常分型面封胶部分应超过25mm。
14.8所有模具分模面上必须采用分型面精定位机构,即直身锁、锥度锁或虎口定位,产品上有夹线要求的模具需采用内模互锁定位。
14.9 如前模插入后模或后模插入前模,四周如用斜面锁紧,要求70%以上面积碰到。如不用锁紧则加工避空。
14.10 型腔,型芯采用多件镶拼时需用侧压块或斜面固定。对于深腔模具不采用侧压块固定,需用斜面固定及要反插入后模。
14.11 侧压块
14.11.1 侧压块规格、参数列表:
14.11.2 侧压块装配要求
14.11.3 清角R要求:H为30~40深,为R6.5;H为50~70深,为R8。
14.12 插穿部分应有至少2°的斜度或插穿部分至少有0.3mm的落差斜度,以免起刺,插穿部分应无薄钢。14.13 前模和后模筋位、柱的表面,必须仔细省模,去掉火花纹、刀痕,并尽量抛光。司筒针孔表面必须仔细