化工系统模拟与优化
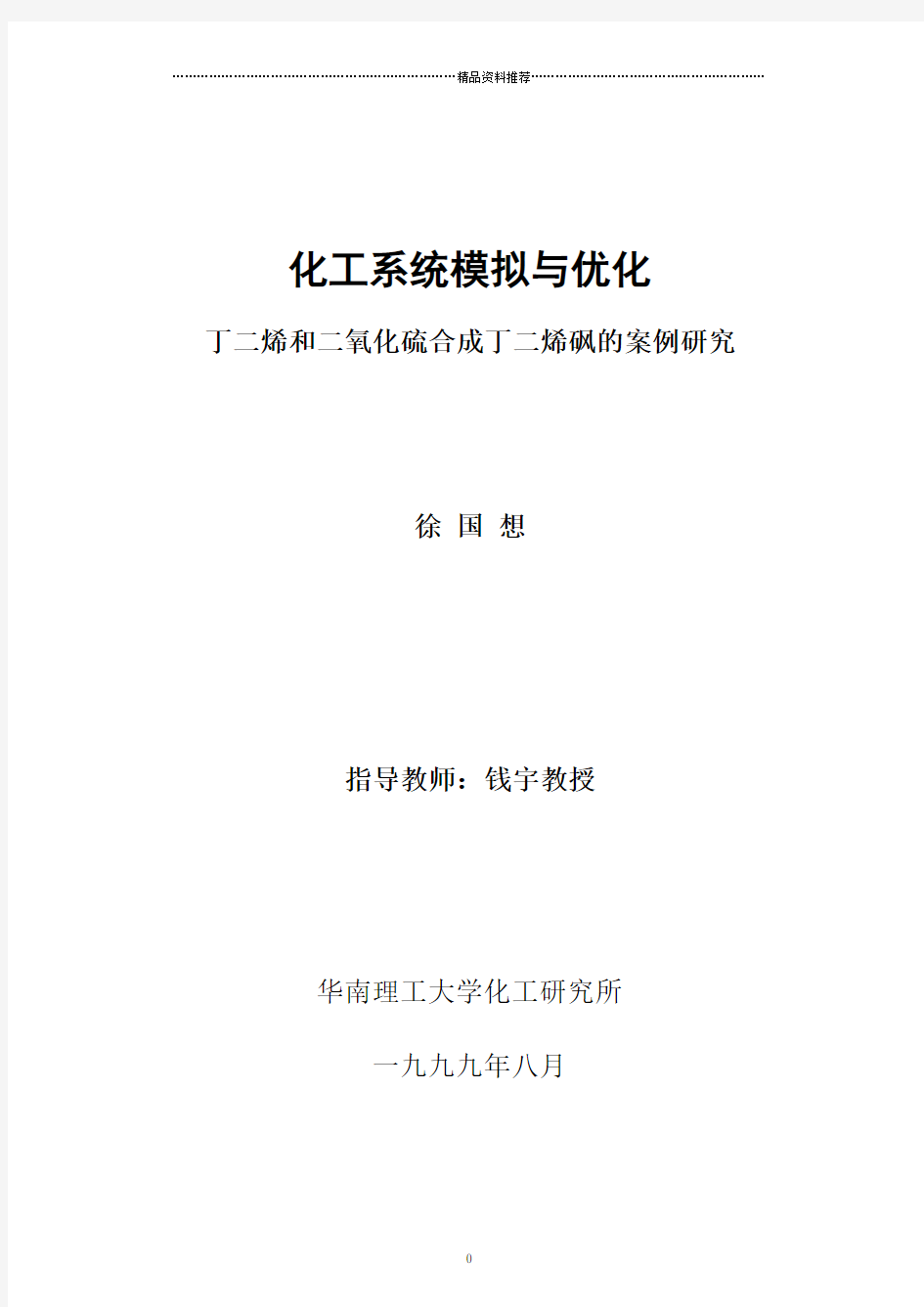

化工系统模拟与优化
丁二烯和二氧化硫合成丁二烯砜的案例研究
徐国想
指导教师:钱宇教授
华南理工大学化工研究所
一九九九年八月
目录
序言
0.输入信息
1.间歇对连续
2.流程图的输入-输出结构
2.1.流程图的输入-输出结构
2.2.设计变量和物料衡算的步骤
3.流程图的循环结构
3.1.过程循环结构的决策
3.2.流程的物料衡算
4.分离系统
4.1.分离序列的综合
4.2.分离系统的总体结构
5.丁二烯制备丁二烯砜过程的全流程模拟5.1.丁二烯制备丁二烯砜过程的全流程图5.2.丁二烯制备丁二烯砜过程的全流程经济衡算参考文献
附录 PRO/ⅡKEYWORD输入文件
序言
概念设计是依据开发性基础研究的结果、文献的数据、现有类似装置的操作数据和工程经验,按照所开发的新技术工业化规模而做出的预想设计。概念设计的目标就是寻找最佳工艺流程和估算最佳设计条件,用以指导过程研究及提出对开发性基础研究进一步的试验要求,所以,它是基础研究与过程研究的指南,是整个开发研究过程中十分关键的一个步骤。经验指出,如果要考虑所有的可能性,则对任何过程的流程图一般都可以提出许多方案(经常是104~109个),采用分层次决策的方法,就可以在很大程度上避免了漏掉某些重要方案选择的情况。概念设计的目标就是寻找最佳“方案”,所以,需要尽快降低要予以考虑的方案数目,而基于数量级分析法的简捷算法常常精确得足以消去90%左右无效益的方案。采用简捷算法和分层次决策方法也可以尽快地把信息反馈给正致力于开发该过程的化学家手中,将有助于化学家去收集那些有可能获取最大效益操作范围内的数据,并且终止掉那些在有效益操作范围之外的实验。分层次决策方法就是把设计问题简化为分层次的决策,其步骤如下:
1. 间歇对连续;
2. 流程图的输入 输出结构;
3. 流程图的循环结构;
4. 分离系统的总体结构;
5. 热交换器网络。
0 输入信息
1. 反应信息
a. 可逆反应:
?H R =-48,000Btu/mol , K eq =(6.846×10-11)exp[-36,940/T(0R)], k 1=(8.172×1015)exp[-52,200/T(0R)], k 1=k -1K eq [mol/(ft 3·h)], 反应速率符合化学计量关系,并且采用CSTR 反应器。 b. 反应条件:反应温度=90 0F , 反应器压力=150psia 。 c.假设反应的选择性为1:
x ==
尔数
反应器进料中丁二烯摩转化的丁二烯摩尔数
丁二烯转化率
d. 反应动力学:反应在产品沸点下有显著的逆反应速率,这时应选择适宜的反应
温度、二氧化硫与丁二烯的摩尔比,不仅要求转化率高,还要求生产控制稳定、产品成本低,一般选择二氧化硫与丁二烯的摩尔比r =1.0,丁二烯的转化率为40% e. 液相,无催化剂
2. 丁二烯砜产量:P 丁二烯砜 = 80mol/h
3. 丁二烯砜的产品纯度:x D ≥ 0.985
4. 物化数据:一般需要的信息是分子量、沸点、蒸汽压、热容、汽化热、反应热、液体密度和逸度系数(或状态方程)。
5. 费用数据:SO 2=0.064$/mol ,丁二烯=
6.76$/mol ,丁二烯砜=8.50$/mol ,反应器的年均建设费是3150558.0R V [$/(ft 3·a)]。
1间歇对连续
采用间歇操作颇为有利的因素
1.产率:
a.当产率低于10×106lb/a时,有时采用间歇;
b.如果产率低于1×106lb/a时,一般采用间歇;
c.多产品装置。
2.市场的力量:
a.季节性生产;
b.产品的生存期短。
3.放大问题:
a.反应的时间非常长;
b.要处理低流速的浆料;
c.快速结垢性的物料。
产率较低,约为0.17×106lb/a(操作时数按8150 h/a计),一般采用间歇,但根据反应的特点,决定选择一个连续的过程,操作费用和物流费用以年为基准,操作时数为8150 h/a 。
2流程图的输入-输出结构
2.1 流程图的输入-输出结构
1. 净化进料物流情况:不需净化进料物流。
2. 可逆的副产品情况:无可逆副产物。
3. 气相循环。
4. 产品物流的数目。所有组分的去向在表2.1中给出,只有一股产品物流。
初步的流程图见图2.1:
2.2. 设计变量和物料衡算的步骤
可能出现在第2层次上的设计变量:对复杂反应有反应器转化率,反应物摩尔比,反应温度/或压力等;过量反应物的情况,过量反应物是指既不回收,又不是气体循环和放空的反应物。
正常情况下,可由设计变量开发总物料平衡的公式,而根本不必考虑任何循环流量。只要总方程式定义不足,就必须寻找一个或多个设计变量来完善该问题的定义,而这些设计变量总是对应于“主要的过程优化”问题。因此,最初的分析总是应该只集中于输入-输出的流量。
开发总物料平衡的步骤:
1.从规定的产率入手
2.由化学计量关系求出副产物流量和原料需用量(以设计变量表示)
3.在反应物需要全部回收和循环的场合,计算进料物流内杂质的进口流率和出口流率
4.在反应物既不回收也不循环的场合(循环和放空或是空气或是水),以规定的过剩量表示,计算各反应物的出口流率
5.计算随第四步中的反应物流带入的杂质的进口流率和出口流率。
3流程图的循环结构
3.1过程循环结构的决策:
1、需采用一套反应器系统
只有一个主反应,只需要一个反应器系统。由于反应转化率不可能达到100%,故原料要循环回反应器。
2、采用一股气相循环物流
全流程有一个回到反应器去的循环物流。其流程图见图2. 3。
3、在反应器入口处无需过量反应物
4、配置气体压缩机一台
反应在高压下进行,需要一台进料气压缩机。
5、反应器采用预热方式进料
6、通过改变反应器的停留时间来调节平衡转化率。
图2.3 丁二烯制备丁二烯砜过程循环结构
3.2 流程的物料衡算
初期物料衡算是基于所有有价值物流全部回收的假设,衡算结果将为用PRO/II作流程模拟提供初值。严格的物料衡算待确定分离系统的细节后由PRO/II流程模拟结果给出。
1. 设计变量。将产物分布关联为有限反应物的单程转化率的函数,即设计变量为丁二烯的单程转化率。
2. 物料衡算。从图2.3看到,所有进入该过程的丁二烯都转化了(没有丁二烯离开系统),这是基于丁二烯完全回收的假设,即忽略掉产品物流中有任何丁
二烯的损失。当反应转化率为x 、反应选择性为S 、丁二烯砜产率为P 丁二烯砜时,该过程的丁二烯新鲜进料量FF C4H6必须为
S
P FF SO H C H 2
646C4
(2-1) 令进入反应器的丁二烯流率为F C4H6,当转化率是x 时,离开反应器的丁二烯量是F C4H6 (1-x )。对于完全回收的分离系统,离开反应器的流率将等于循环流率。在反应器前的混合器作一衡算,则有
FF C4H6+ F C4H6 (1-x ) = F C4H6 (2-2)
于是反应器的进料量为
F C4H6=FF C4H6/x (2-3)
4分离系统
4.1 分离序列的综合
选用探试法选择简单塔塔序。探试法的搜索速度一般比数学规划法要高得多,如果探试法则使用得当,不需要过多的计算便可迅速获得接近最优的分离序列。Nadgir和Liu提出的有序探试法,就是一种较好的分离序列综合的探试法。
Nadgir和Liu把探试法则分为四大类:
①分离方法探试(M探试)法则;
②设计探试(D探试)法则
③组分探试(S探试)法则;
④组成探试(C探试)法则。
这四类探试法则中包括如下探试法则,这些探试法则必须依次顺序采用,不可颠倒:
规则1(M1法则),尽量采用直接分离法(只用能量分离剂的分离方法,如普通精馏),避免采用间接分离法(需要用质量分离剂的分离方法)。但当关键组分的相对挥发度(或分离系数)小于1.05~1.10时,不推荐用普通精馏,该采用质量分离剂,但分离剂应在下一个分离器中分离出来。
规则2(M2法则),避免温度和压力过于偏离环境条件。如果必须偏离,也宁可向高温或高压方向偏离,而尽量不向低温、低压方向偏离。如不个、得不采用真空蒸馏,可以考虑用液液萃取来代替。如果需要冷冻,可以考虑吸收等替代方案。
规则3(D1法则),倾向于产生的产品个数最少的分离序列,也就是避免分离那些在同一目标产物组中的组分。
规则4(S1法则),优先分离具有腐蚀性或毒性的成分。
规则5(S2法则),难于分离的组分最后分离。特别是关键组分的相对挥发度接近于1.0时,应当在没有非关键组分存在的条件下进行分离。
规则6(C1法则),在相对挥发度允许的条件下,进料组成最大的组分优先分离。
规则7(C2法则),在进料组分的组成相差不大,且相对挥发度允许的条件下,倾向于将进料一分为二的分离,即将进料等摩尔地分成塔顶和塔底产品。若难以判断哪一种分离最接近一分为二,则可以把易分离系数(CES)值最大的分离点优先分离。
易分离系数定义如下:
(3-1) 其中f为产品摩尔流率比,定义为
(3-2) 式中 D—塔顶出料摩尔流率;
B—塔底出料摩尔流率。
式(3-1)中?为
(3-3)
或 (3-4) 式(3-3)表示轻重关键组分间沸点差,式(3-4)中α为轻重关键组分相对挥发度。易分离系数越大,表示轻、重关键组分越易被分离,所需分离费用一般也较低。
4.2 分离系统的总体结构
从反应器的操作条件(90 0F ,150psia)下出来的液相混合物,温度大约在90 0F,经过换热器进行间接升温至340 0F进入分离系统,再通过分别设计蒸汽回收系统和液体分离系统来实现相的最终分离。丁二烯制备丁二烯砜过程的分离系统总体结构如图4.2.1所示:
根据PRO/II的模拟计算知,可采用两个串联的闪蒸器来分割反应器的出料,气相循环到反应器入口处和新鲜进料混合,经过气体压缩机压缩至150psia、477.40F,再经过换热器降温至90 0F 进反应器。丁二烯制备丁二烯砜过程分离系统的初步结构如图4.2.2所示:
图4.2.2 丁二烯制备丁二烯砜过程分离系统的初步结构
该分离系统可采用各种替代方案:
1.升高混合物的温度或降低它的压力,利用闪蒸器来实现相的分离。
2.升高混合物的温度,采用精馏塔来分割物流。
3.升高混合物的温度,采用稳定塔来分割物流。
以上各种替代方案按照费用递增的顺序排列,故希望采用排列靠前的方案。
5丁二烯制备丁二烯砜过程的全流程模拟
5.1丁二烯制备丁二烯砜过程的全流程图
在以上分析的基础上,可进行全流程的模拟,利用PRO/II软件进行模拟计算,其流程如图5.1所示。
图5.1丁二烯制备丁二烯砜过程的全流程图
5.2丁二烯制备丁二烯砜过程的全流程经济衡算 5.2.1过程的经济潜力
以年操作时数8150小时为基准,过程的经济潜力为: EP=产品的价值-原料费用-设备费用
1.原料及产品费用
SO 2=0.064$/mol ,丁二烯=6.76$/mol ,丁二烯砜=8.50$/mol 2.反应器的费用模型
采用CSTR 反应器,反应器的年均建设费可按下式计算: 3150558.0R V [$/(ft 3·a)] 3.闪蒸器的费用模型
一般闪蒸器的停留时间为15min 左右(0.25h ),故闪蒸器的体积可按下式计算:
v Q V 25.0=
式中V 是闪蒸器的体积(ft 3),Q v 是进入闪蒸器物流的体积流率(ft 3/h )。取闪蒸器的L/D=1.5,则闪蒸器的直径和长度为:
31
)64(π
V
D =;L=12D
在引入投资偿还因子1/3后,闪蒸器的年度建设费用可按下式计算:
)18.2(9.101)280
&(31802.0066.1c F H D S M + 在本设计中M&S 取792,F c =3.67*1.0。 4.换热器的费用模型
换热器的热负荷均由PRO/II 计算得到,换热所需传热面积由下式计算: m
c c
c T U Q A ?=
式中Q c 为换热器的热负荷(Btu/h ft 2 0F ),U c 为传热系数100Btu/h ft 2 0F ,△T m 是换热器的对数温差,A c 为换热器所需换热面积(ft 2)。
在引入投资偿还因子1/3后,换热器的年度建设费用可按下式计算:
)29.2(3.101)280
&(3165
.0c c F A S M +
在本设计中M&S 取792,当采用碳钢制造的浮头式换热器时F c =1.0。 另外,换热器的年度操作费用(消耗的冷却水费用)可按下式计算: 8150))(34.81)(1000$06.0(
??c
c
T Q lb gal gal
式中冷却水的价格为0.06$/1000gal ,△T c 是冷却水的进出口温差,年操作时数为8150小时。
换热器年度费用=换热器年度建设费用+换热器年度操作费用 5.压缩机的费用模型
对于初期设计,假定压缩机效率为90% ,压缩机理论功率h p 由PRO/II 流程模拟结果给出,则制动马力为 用Guthrie 关联式计算压缩机的建设费用
操作费用按压缩机电机效率为90%和电费为0.035 $ / kWh 计算
()()8150035.09.0????
??=p bh 年度操作费用
式中bh p 单位为kW 。 5.2.2全流程经济衡算 一、费用数据
二氧化硫费用
0.064 $ / kmol 丁二烯费用 6.76$ / kmol 丁二烯砜价值 8.50 $ / kmol 电 价 0.035 $ / kWh 冷却水
1.427×10 - 4 $ / kmol
设备费用估算价格指数M&S = 792 , 并引入投资偿还因子1/3年,以便把建设费用置于年度的基准上。 二、经济潜力估算 以反应转化率x = 0.4为例
1.原料二氧化硫费用= (0.064$/mol)(80 mol / h)(8150h/a) = 4.173 104 $/a 原料丁二烯费用= (6.76$/mol)(80 mol / h)(8150 h/a) = 4.408 106$/a 产品丁二烯砜价值= (8.50$/mol)(80 mol / h)(8150 h/a) = 5.542 106$/a 2. 反应器费用
反应器进料体积流率 v 0= 0.384 km 3/h 反应的速度常数 k=1.045 s -1 (T =90 0F)
()()??
?????--+=95.04.04.011
ln 95.01045.110v V =0.592 s =1.646×10- 4h 反应器容积 V = 0.065 m 3
反应器年度费用=3150558.0R V [$/(ft 3·a)] ×35.315 ft 3/ m 3=2.420 104 $/a 3.闪蒸器费用
v Q V 25.0==0.25×0.307×35.315=2.709 ft 3
式中V 是闪蒸器的体积(ft 3),Q v 是进入闪蒸器物流的体积流率(ft 3/h )。取闪蒸器的L/D=1.5,则闪蒸器的直径和长度为:
31
)64(π
V
D ==0.831 ft
L=1.5D=1.247 ft
闪蒸器的年度建设费用=)18.2(9.101)280
&(31802.0066.1c F H D S
M +×2
=1.101 104$/a
4. 换热器费用
建设费用= )29.2(3.101)280
&(3165
.0c c F A S M +×3
=×3= 1.376 104$/a 消耗的冷却水费用=8150))(34.81)(1000$06.0(
??c
c
T Q lb gal gal
=5.396 104$/a
换热器年度费用=换热器年度建设费用+换热器年度操作费用 5.压缩机费用
制动功率=692.64/0.9 0.7457 =573.9 kW
年度投资费用 =()()??
?
??+??? ??300.111.29.5735.51728079282.0
= 2.778 105 $/a
()()8150035.09.0???? ??=p h 年度操作费用=1.637 105 $/a 6.经济潜力 EP = 5.49 105 $/a
按以上步骤可以估算出其它转化率下的经济潜力,并由模拟可知,反应转化率越大,过程经济潜力越大。但由于受平衡的限制,本文选择转化率x = 0.4 作为反应段的操作条件。从计算结果可以看出,压缩机的年度费用为最大,因此,要想提高过程的经济潜力,如何降低压缩机的年度费用也须考虑。
参考文献
[1]蒋楚生等译Douglas中文版,化工过程的概念设计,化学工业出版社,1994
年
[2]杨冀宏等编著,过程系统工程导论,烃加工出版社,1989年
[3]陈甘棠主编,化学反应工程,化学工业出版社,1990年
[4]天津大学化工原理教研室编,化工原理,天津科学技术出版社,1987年
[5]天津大学物理化学教研室编,物理化学,高等教育出版社,1992年
[6] Simsci Co. :PRO/II,PRO Vision User’s Manual,1995
(完整word版)化工过程分析与合成
名词解释 1.夹点的意义 (夹点处,系统的传热温差最小(等于ΔT min ),系统用能瓶颈位置。夹点处热流量为 0 ,夹点将系统分为热端和冷端两个子系统,热端在夹点温度以上,只需要公用工程加热(热阱),冷端在夹点温度以下,只需要公用工程冷却(热源);) 2.过程系统能量集成 (以用能最小化为目标的考虑整个工艺背景的过程能量综合) 3.过程系统的结构优化和参数优化 (改变过程系统中的设备类型或相互间的联结关系,以优化过程系统;参数优化指在确定的系统结构中,改变操作参数,是过程某些指标达到优化。) 4、化工过程系统模拟 (对于化工过程,在计算机上通过数学模型反映物理原型的规律) 5、过程系统优化 (实现过程系统最优运行,包括结构优化和参数优化) 6、过程系统合成 (化工过程系统合成包括:反应路径合成;换热网络合成;分离序列合成;过程控制系统合成;特别是要解决由各个单元过程合成总体过程系统的任务) 7、过程系统自由度 (过程系统有m个独立方程数,其中含有n个变量,则过程系统的自由度为: d=n-m,通过自由度分析正确地确定系统应给定的独立变量数。) 填空题 1.稳态模拟的特点是,描述过程对象的模型中( 不含 )时间参数 2.( 集中参数模型)认为状态变量在系统中呈空间均匀分布,如强烈搅拌的反应罐就可以用这一类模型来描述. 3. ( 统计模型 )又称为经验模型,纯粹由统计、关联输入输出数据而得。 (确定性模型 )又称为机理模型 4.( 结构 )优化和( 参数 )优化是过程系统的两大类优化问题,它们贯穿于化工过程设计和化工过程操作。 5.换热网络的消耗代价来自三个方面: (换热单元(设备)数) ( 传热面积) (公用工程消耗) 6.过程系统模拟方法有、和。 7.试判断图a中换热匹配可行性 1 , 2 , 3 , 4 。
系统优化设计模拟
系统优化设计 一.填空(30分) 1.系统工程是用于系统设计、实现、技术管理、运行使用和退役的专业学科方法论。 2.系统工程师在引导系统架构的开发、需求的定义和分配、设计方案的评价与权衡、系统间技术风险均衡、系统接口的定义与评估、验证和确认活动的全面监督,以及许多其他任务中起关键的作用。3.在NPR7123.1《NASA系统工程流程和需求》中包括三类技术流程:系统设计、产品实现及技术管理。 4.对飞行和地面保障项目,NASA寿命周期的两个阶段又分为以下7个递进阶段: ●A前阶段:概念探索(即确定确定可行备选方案)。 ●阶段A:概念研究和技术开发(即项目定义,明确和组织必要的 技术)。 ●阶段B:初步设计和技术完善(即建立初步设计方案,开发必要 的技术)。 ●阶段C:详细设计和制造(即完成系统设计,进行组件的建造/ 编码)。 ●阶段D:系统组装、集成、试验和投产(即集成组件,验证系统, 系统投入生产并准备运行使用)。 ●阶段E:运行使用与维护(即运行与维修系统)。 ●阶段F:退役处置(即处置系统,分析数据)。
5.产品交付流程:产品实施、产品集成、产品验证、产品确认、产品交付。 6.产品验证流程分为5个主要步骤:(1)验证计划(准备实施验证的计划); (2)验证准备(准备进行验证);(3)执行验证(进行产品验证);(4)分析验证结果;(5)获得验证工作产品。 7.技术管理:技术规划、需求管理、接口管理、技术风险管理、技术状态管理、技术数据管理、技术评估、决策分析。 二.(30分) A.直升机的主动防御系统 B.坦克的主动防御系统 三.简答题(20分) A.系统设计的关键 B.系统设计各流程间相互关系 C.产品实现流程图 D.产品实现的关键 四.(10分) 运用系统工程的方法简述对系统总师的认识
简述各种化工流程模拟软件的特点及优缺点
简述几种化工流程模拟软件的功能特点及优缺点 化学工艺09级1班 摘要:化工过程模拟是计算机化工应用中最为基础、发展最为成熟的技术。本 文综合介绍了几种主要的化工流程模拟软件的功能及特点,并对其进行了简单的比较。 关键词:化工流程模拟,模拟软件,Aspen Plus, Pro/Ⅱ,HYSYS, ChemCAD l 化工过程概述 化工流程模拟(亦称过程模拟)技术是以工艺过程的机理模型为基础,采用数学方法来描述化工过程,通过应用计算机辅助计算手段,进行过程物料衡算、热量衡算、设备尺寸估算和能量分析,作出环境和经济评价。它是化学工程、化工热力学、系统工程、计算方法以及计算机应用技术的结合产物,是近几十年发展起来的一门新技术[1]。现在化工过程模拟软件应用范围更为广泛,应用于化工过程的设计、测试、优化和过程的整合[2]。 化工过程模拟技术是计算机化工应用中最基础、发展最为成熟的技术之一,化工过程模拟与实验研究的结合是当前最有效和最廉价的化工过程研究方法,它可以大大节约实验成本,加快新产品和新工艺的开发过程。化工过程模拟可以用于完成化工过程及设备的计算、设计、经济评价、操作模拟、寻优分析和故障诊断等多种任务。[3]当前人们对化工流程模拟技术的进展、应用和发展趋势的关注与日俱增。 商品化的化工流程模拟系统出现于上世纪70年代。目前,广泛应用的化工流程模拟系统主要有ASPEN PLUS、Pro/Ⅱ、HYSYS和ChemCAD。 2 Aspen Plus 2.1 Aspen Plus简述 “如果你不能对你的工艺进行建模,你就不能了解它。如果你不了解它,你就不能改进它。而且,如果你不能改进它,你在21世纪就不会具有竞争 力。”----Aspen World 1997 Aspen Plus是大型通用流程模拟系统,源于美国能源部七十年代后期在麻省理工学院(MIT)组织的会战,开发新型第三代流程模拟软件。该项目称为“过
化工过程分析与合成考点(精华)
化工过程分析与合成考点 1、什么叫过程: (1)客观事物从一个状态到另一个状态的转移。【过程】 (2)在工艺生产上,对物料流进行物理或化学的加工工艺称作过程工艺。【过程工艺】 (3)以天然物料为原料经过物理或化学的加工制成产品的过程。 化工过程包括:原料制备、化学反应、产品分离 (4)由被处理的物料流联接起来,构成化工过程生产工艺流程。 (5)【最重要的单元过程】化学反应过程、换热过程、分离过程、输送过程、催化反应过程 (6)【化学反应过程举例】热裂解反应过程、电解质溶液离子反应过程生化反应过程、分散控制 (7)【过程控制技术发展历程】计算机集中控制、集散控制(我国多)、现场总线控制 第二章、化工过程系统稳态模拟与分析 【模块】模型和算法,一是要建模,二是这个模型的算法,两者组一起才能算作模块。 【单元模型类型】理论模型、经验模型、半经验模型。 【什么叫稳态(化工过程稳态模拟)】各个工艺参数状态量不随时间而发生变化的叫做稳态。 【么叫模拟】对过程系统模型进行求解就叫模拟。 【过程系统模拟可以解决哪些问题(会画图)】(1)过程系统模拟分析问题;(2)过程系统设计问题;(3)过程系统参数优化问题。 过程系统模拟分析问题:已知决策变量输入,已知过程参数,求输出,是一个正向求解问题,最简单的模型。 2)过程系统设计问题:已知输出设计结果,已知过程参数,求决策变量输入;看起来是已知输出求输入,实际上是假设输入猜值去计算输出与已知输出进行比较再调整猜值进行计算。只能单项求解,从左到右
3)过程系统参数优化问题:过程系统模型与最优化模型联立求解,得到一组使工况目标函数最佳的决策变量,从而实施最佳工况。 【过程系统模拟三种基本方法,及其优缺点】(1)序贯模块法(不适于解算设计、优化问题,只适于模拟问题(2)面向方程法(3)联立模块法(同时有(1)、(2)的优点) 【单元模块】是依据相应过程单元的数学模型和求解算法编制而成的子程序。具有单向性特点 【断裂】通过迭代把高维方程组降阶为低维方程组的办法。它适用于不可分割子系统; 【不可分割子系统】过程系统中,若含有再循环物流,则构成不可分割子系统。 【断裂基本原则】1) 切割流线总数最少、2) 切割流线所含变量数最少、3) 切割流线的总权重最小、4) 环路切割的总次数最少 【简单回路】包含两个以上流股,且其中的任何单元只被通过一次。矩阵:行→回路;列→物流。 【适合于收敛单元应满足要求:】(1)对初值的要求不高、(2)数值稳定性好、(3)收敛速度快、(4)占用计算机存储空间少 【面向方程法(适用于线性化,非线性方程组先线性化)】 第四章、化工过程系统的优化 【最优化问题包括要素(内容)】(1)目标函数(2)优化变量(3)约束条件(4)可行域 【可行域】满足约束条件的方案集合,构成了最优化问题的可行域。 【最优解】过程系统最优化问题是在可行域中寻求使目标函数取最小值的点。 【最优化问题的建模方法】机理模型、黑箱模型、混合模型 【系统最优化方法的分类】无约束最优化与有约束最优化、、线性规划LP(目标函数约束条件全部都为线性函数称为线性规划,剩一个为非线性函数为非线性规划、单维最优化和多维最优化、解析法与数值法、可行路径法与不可行路径法 【标准型】目标函数值一定是最小值、约束条件中没有不等式约束,全是等式约束、所有的变量全是非负条件 第七章、换热网络合成 【换热网络合成】通俗地讲就是将物流匹配在一起,充分利用热物流去加热冷物流,提高系统的热回收,以便尽可能地减少辅助加热与辅助冷却负荷。 【换热网络合成目的】让某一个物料从初始温度到目标温度(一定要达成)、尽可能的回收余热、尽可能的减少换热设备数。 【温度区间求夹点(会画温度区间表)】将热物流的起始温度与目标温度减去最小允许温差△Tmin,然后与冷物流的起始、目标温度一起按从大到小排序,构成温度区间。 【夹点】在温度区间中,高温度区间向低温度区间传递的热量为零的点,不是接受热量为零的点(判断) 对于热公用工程是260C。,对于冷公用工程是250C。。 物理意义:温焓图上组合曲线垂直距离最低的点。 【夹点的三个特性】能量特性、位置特性、传热特性
氧化铝蒸发系统的模拟优化
氧化铝蒸发系统的模拟优化 第32 卷第 2 期文章编导:10064148f2001)024)01103 氧化铝蒸发系统的模拟优化郭海燕(辽阳石油化工高等专科学校辽阳111003)摘要以某氧化铝厂蒸发系统的实际操作数据为依据,建立数学模型,进行计算机模拟,提 出两项改造方案.进行了比较,评价. 关键词蒸发系统,模拟,节能,改造 I 丽菁蒸发是重要的化工单元操作之一.在工业蒸发操作中,往往要蒸发大量的水分,消耗大量的水蒸汽,因此提高加热蒸汽的利用率,是节能的关键问题.在氧化铝生产中.需要耗费大量热能,蒸发除去溶液中的水.例如,拜耳法氧化铝厂,1 吨氧化铝的平均热能为15.5?15.9x1焦耳,其费用相当于氧化铝成本的13%?14%.用烧结法处理霞石的氧化铝厂, 热耗约为8.36~109焦耳/吨,其费用相当于成本的7?10%,因此降低氧化铝生产的热耗是降低氧化铝生产成本的主要途径. 2 模拟计算 2.1 氧化铝蒸发系统操作参数及物性数据进人蒸发系统原料液体积流量为90.1m/h,质量流量为112.625吨/h,进料温度为60C,其它操作参数如下: 以NaOH 溶液浓度为基准(质量百分率)原料液进料浓度Bo=01393 原料液出料浓度BJ=0.2508 原料液体积流量V=90.1mVh 原料液质量流量Go=ll2.625吨/h 原料液的温度t~=609C 新蒸汽的温度S1155.1C 新蒸汽的压力=5.934kgf/cm C 末效的二次蒸汽温度ST(六)=64.99C 末效的二次蒸汽压力P=0.254kgf/em2 新蒸汽的汽化潜热Rc=2102.8kJ/kg 2.2数学模型的建立 收稿日期:2oo1--o5~17 作者筒彳r:韩海燕,(1968 —).女.黑龙江人.jI石油化工高等々科{杖化工系.实验师,从事实验教学和科研工作. (1)总蒸发水量
离散系统的Simulink仿真
电子科技大学中山学院学生实验报告 院别:电子信息学院课程名称:信号与系统实验 一、实验目的 1.掌握离散系统Simulink的建模方法。 2.掌握离散系统时域响应、频域响应的Simulink仿真方法。 二、实验原理 离散系统的Simulink建模、仿真方法与连续系统相似,其系统模型主要有z域模型、传输函数模型和状态空间模型等形式。 现采用图1的形式建立系统仿真模型,结合如下仿真的命令,可得到系统的状态空间变量、频率响应曲线、单位阶跃响应和单位冲激响应的波形。 图1 系统响应Simulink仿真的综合模型 仿真命令: [A,B,C,D]=dlinmod(‘模型文件名’)%求状态空间矩阵,注意:‘模型文件名’不含扩展名 dimpulse(A,B,C,D) %求冲激响应 dimpulse(A,B,C,D,1,N 1:N 2 ) %求k=N 1 ~N 2 区间(步长为1)的冲激响应 dimpulse(A,B,C,D,1,N 1:△N: N 2 ) %求冲激响应在k=N 1 ~N 2 区间(步长为△N) 的部分样值 dstep(A,B,C,D) %求阶跃响应 dstep(A,B,C,D,1,N 1:△N:N 2 ) dbode(A,B,C,D,T s )%求频率响应(频率范围: Ts ~ π ω=,即π ~ 0=)。T s 为 取样周期,一般去T s =1. dbode(A,B,C,D, T s ,i u ,w :△w:w 1 ) %求频率响应(频率=范围:ω=w ~w 1 , 即θ=(w0~w1)T s,△w为频率步长);i u为系统输入端口的编号,系统只有一个输入端
化工过程分析与合成
一、单项选择题。本大题共14个小题,每小题5.0 分,共70.0分。在每小题给出的选项中,只有一项是符合题目要求的。 重质油催化剂裂化制轻质油的反应过程是(B)。 脱氢过程 裂化反应 热裂解反应过程 催化过程 数值稳定性好,通常,迭代收敛过程有(C)。 很缓慢 很快 四种可能情况 收敛解 氨合成过程的物料必须进行循环,主要集中在(D)。 制气工段 压缩工段 脱硫工段 氨合成工段 蒸馏的原理是(A)。 物质的沸点不同 物质分子量大小 物料的浓度 进料快慢 过程系统结构的优化属于过程系统的(B)。 过程系统的问题 合成问题 过程系统的分析 优化问题 氨厂包括的工序有(A)。 原料气制备 原料气脱硫 氨的分离 空气净化 天然气中的主要成分是(B)。 氩 甲烷(CH4) 氢气 氮气 实验数据归纳的模型被称为(A)。 经验模型 半经验模型 特定模型 多级参数模型 工业上已得到广泛应用的低能耗分离技术是(D)。
吸附分离技术 非定态技术 变压吸附 乙苯脱氢制苯乙烯的反应过程是(A)。 脱氢反应 制苯乙烯 裂解反应过程 催化过程 对均一系物料的气相分离,可采用(A)。 吸附吸收 汽提 蒸发 萃取 变压吸附是在工业上已经得到广泛应用的(D)。 气体分离技术 非定态技术 节能分离技术 吸附分离技术 化工过程系统合成是(C)。 产品生产合成 设备合成 换热网络合成 反应物料合成 泡点温度是指气液平衡时与液相组成相对应的(C)。 液相起泡时温度 沸腾温度 平衡温度 气相温度 二、多项选择题。本大题共6个小题,每小题5.0 分,共30.0分。在每小题给出的选项中,有一项或多项是符合题目要求的。 用人工智能技术模拟人脑的思维过程,两种不同的成功途径是(DE)。 离散模拟 模糊模拟 非数值模拟 客观模拟 微观模拟 单元操作模拟中每个模块中包含有(AB)。 单元操作相关方程 相关的物性计算程序 物流焓值 进口物料组成 出口组成 对化工过程进行描述的数学模型有(CD)。
化工仿真实习总结
化工仿真实习总结 化工091 邱伟康23 为期一周的化工仿真实习结束了,虽然只是每天进出机房,对着电脑进行操作,但是学到的知识却比课堂更为直接,理解的更为深刻。 仿真实验是以仿真机为工具,用实时运行的动态数学模型代替真实工厂进行教学实习的一门新技术。仿真机是基于电子计算机、网络或多媒体部件,由人工建造的,模拟工厂操作与控制或工业过程的设备,同时也是动态数学模型实时运行的环境。 仿真实验为学生提供了充分动手的机会,可在仿真机上反复进行开车、停车训练,在仿真机上,学生变成学习的主体。学生可以根据自己的具体情况有选择地学习。例如自行设计、试验不同的开、停车方案,试验复杂控制方案、优化操作方案等。可以设定各种事故和极限运行状态,提高学生分析能力和在复杂情况下的决策能力。真实工厂决不允许这样做。高质量的仿真器具有较强的交互性能,使学生在仿真实验过程中能够发挥学习主动性,实验效果突出。主要内容为精选化工单元操作与典型的工业生产装置,如离心泵、换热器、压缩、吸收、精馏、间歇反应、连续反应、加热炉及石油化工中的催化裂化装置、常减压装置、合成氨中的转化装置等。采用计算机进行仿真操作的方式。 在这里我就总结下我们主要学习的5个仿真实验:离心泵、换热器、脱丁烷塔、吸收解吸单元、离子膜烧碱。 离心泵是我们最初接触的化工仿真实验,它是比较简单的一个实验,但是起初对着屏幕我们大多数人还是摸不着头脑,后来经过一段时间的摸索熟悉,很快就将仿真实验的操作流程掌握了,再针对离心泵实验的一些特点以及注意点(例如罐液位,泵出口压力,泵进口压力,灌压)按照指示正规的步骤进行操作,没过2个小时我就将离心泵的开车停车过程做到了满分。 换热器是第二个实验,再离心泵的基础上面对换热器不会那么茫然了,它本身也是一个比较简单的流程,先进行冷流体进液然后热流体进液让它们进行换热,但是要想做好它,必须控制好冷流入口流量控制FIC101,冷流出口温度TI102,热流入口温度控制TIC101,PI101泵出口压力。了解好步骤以及注意点后我专注的进行了一次开车,第一次不尽完美,但却是第二次完美开车的完美参
化工过程优化与集成
《化工过程优化与集成》课程教学大纲 一、课程性质 《化工过程优化与集成》是化学工程与工艺专业的核心专业基础课程之一,它是应用化工过程优化和系统集成的理论和方法来研究化工过程系统的开发、设计、最优操作一门课程。本门课程的任务是使学生能运用优化和系统集成的观点和方法分析化工过程,使化工过程系统在开发、设计、操作、管理等各个层面上达到最优化,使整体能耗最小,费用最小,环境污染最少。 二、教学目的 培养高年级学生综合运用学过的《化工原理》、《化工热力学》、《化学反应工程》等课程,以及技术经济、环境保护方面的基础知识,并结合本课程的优化和系统集成的观点和方法,加强学生处理化学工业实际问题的能力,培养学生抽象思维和演绎分析的能力及优化和集成观念。 三、教材教参 (二)主要参考书 1. 杨友麟编,《实用化工系统工程》,化学工业出版社,1989 2. 邓亚龙编,《化工中的优化方法》,化学工业出版社,1992 3. 马国喻编,《化工最优化基础》,化学工业出版社,1982 四、教学方式 本课程将以启发互动式教学为主要方式,板书与多媒体结合,配以CAI课件。 五、教学内容及时数 1 绪论(2学时) 1.1 过程系统工程 1.2 过程系统工程研究的基本问题 1.3 过程系统工程的研究方法 1.4 学习过程系统工程课程的方法建议 第一篇过程系统模拟 2 过程系统稳态模拟(3学时) 2.1 过程系统稳态模拟的基本概念 2.2 过程系统模拟的序贯模块法 2.3 过程系统模拟的联立方程法 2.4 过程系统模拟的联立模块法 2.5 过程模拟的应用 2.6 过程稳态模拟发展趋势 3 过程系统动态模拟(3学时) 3.1 过程系统动态模拟基础 3.2 过程系统动态模拟方法 3.3 精馏过程动态模拟 3.4 过程系统动态模拟实例
简述各种化工流程模拟软件的特点及优缺点
简述几种化工流程模拟软件的功能特点及优缺点摘要:化工过程模拟是计算机化工应用中最为基础、发展最为成熟的技术。本文综合介绍了几种主要的化工流程模拟软件的功能及特点,并对其进行了简单的比较。 关键词:化工流程模拟,模拟软件,Aspen Plus, Pro/Ⅱ,HYSYS, ChemCAD l 化工过程概述 化工流程模拟(亦称过程模拟)技术是以工艺过程的机理模型为基础,采用数学方法来描述化工过程,通过应用计算机辅助计算手段,进行过程物料衡算、热量衡算、设备尺寸估算和能量分析,作出环境和经济评价。它是化学工程、化工热力学、系统工程、计算方法以及计算机应用技术的结合产物,是近几十年发展起来的一门新技术[1]。现在化工过程模拟软件应用范围更为广泛,应用于化工过程的设计、测试、优化和过程的整合[2]。 化工过程模拟技术是计算机化工应用中最基础、发展最为成熟的技术之一,化工过程模拟与实验研究的结合是当前最有效和最廉价的化工过程研究方法,它可以大大节约实验成本,加快新产品和新工艺的开发过程。化工过程模拟可以用于完成化工过程及设备的计算、设计、经济评价、操作模拟、寻优分析和故障诊断等多种任务。[3]当前人们对化工流程模拟技术的进展、应用和发展趋势的关注与日俱增。 商品化的化工流程模拟系统出现于上世纪70年代。目前,广泛应用的化工流程模拟系统主要有ASPEN PLUS、Pro/Ⅱ、HYSYS和ChemCAD。 2 Aspen Plus Aspen Plus简述
“如果你不能对你的工艺进行建模,你就不能了解它。如果你不了解它,你就不能改进它。而且,如果你不能改进它,你在21世纪就不会具有竞争力。”----Aspen World 1997 Aspen Plus是大型通用流程模拟系统,源于美国能源部七十年代后期在麻省理工学院(MIT)组织的会战,开发新型第三代流程模拟软件。该项目称为“过程工程的先进系统”(Advanced System for Process Engineering,简称ASPEN),并于1981年底完成。1982年为了将其商品化,成立了AspenTech 公司,并称之为Aspen Plus。该软件经过20多年来不断地改进、扩充和提高,已先后推出了十多个版本,成为举世公认的标准大型流程模拟软件,应用案例数以百万计。全球各大化工、石化、炼油等过程工业制造企业及着名的工程公司都是Aspen Plus的用户。 Aspen Plus特点 (1)产品具有完备的物性数据库物性模型和数据是得到精确可靠的模拟结果的关键。人们普遍认为Aspen Plus 具有最适用于工业、且最完备的物性系统。许多公司为了使其物性计算方法标准化而采用Aspen Plus 的物性系统,并与其自身的工程计算软件相结合。Aspen Plus 数据库包括将近6000种纯组分的物性数据:①纯组分数据库,包括将近6000 种化合物的参数。 ②电解质水溶液数据库,包括约900种离子和分子溶质估算电解质物性所需的参数。③固体数据库,包括约3314种固体的固体模型参数。④ Henry 常数库,包括水溶液中61种化合物的Henry 常数参数。⑤二元交互作用参数库,包括Ridlich-Kwong Soave、Peng Robinson、Lee Kesler Plocker、BWR Lee Starling,以及Hayden O’Connell状态方程的二元交互作用参数
化工仿真实习报告
?化工仿真实习报告 ?仿真(simulation)是利用模型复现实际系统中发生的 本质过程,并通过系统模型进行实验和研究的应用技术科学。 按所用模型的类型(物理模型、数学模型、物理—数学模型)分为物理仿真、计算机仿真(数学仿真)、半实物仿真,按对象的性质分为宇宙飞船仿真、化工系统仿真、经济系统仿真等。化学化工仿真就是化学化工过程的数学仿真,它是以起初的化学化工过程基本规律为依据,建立数学模型后,在计算机上再现该化学化工过程的一种应用技术。 20世纪80年代中期以来,由于国产化工过程仿真培训系统的研制成功,采用仿真技术解决生产实习的化工类大学及职业院校迅速增多。1995年以后,随着微型计算机性能大幅度提高,价格下降,以及国产化仿真培训系统日趋成熟,为仿真实习技术广泛普及创造了条件。计算机技术和设备的开发成功,促进了计算机技术的多媒体化、智能化。化工仿真系统软件的开发通常有两种方式: ?一是应用多媒体合成平台,将多媒体素材有机组装成所 要的系统,这一类平台具有代表性的是北大方正的方正奥思(Founder Author)以及Macromedia公司的Authorware ?二是应用可视化开发语言工具,如Microsoft公司的 Visual C++和Visual Basic,以及Borland公司的C++ Builder 和Delphi等。 ?对新开发的化学化工仿真软件的基本要求是:
?操作系统的运行环境是Windows中文版,或者带有中文 平台的Windows英文版; ?人机界面友好,全部采用标准的Windows图形窗口; 图像分辨率高;可实现多任务操作,方便用户使用。 仿真操作训练:这是化工仿真系统的核心。根据正确的操作步骤,通过鼠标直接操作阀门或仪表等设备,可以完成仿真的全部过程,并依据仿真操作情况给出仿真的操作成绩。 ?化工数据的读取及数据的处理:在实验装置已处 于稳定运行状态下,在相应的仪表上读取原始数据,只有在完整读取数据之后,才可以调用数据处理模块对数据进行处理,并将处理结果以图、表的形式显示出来。 ?思考题测试:在本系统中,将基本实验知识以选 择题的形式给出,学生可以选择正确的选项,并对测试进行评分。 ?帮助系统:在进行仿真操作的过程中,可以充分 利用Windows的多任务操作,从完全Windows风格的帮助系统中获得有关实验或生产原理、实验或生产的目的、实验操作步骤或开车停车的过程、数据处理及软件的使用等方面的帮助信息。 ?其它辅助功能:软件可以提供快速信息提示功 能,每个化工过程均有众多的设备及仪表,当鼠标在相应设备或仪表上停留一、两秒钟后,就会弹出浮动信息条,提示该设
对系统优化与仿真的认识
对系统优化与仿真的认识 随着网络技术的日益提高,带动着物流业的迅猛发展。物流管理也变得越来越繁琐。由此诞生了物流系统。物流系统是一个大跨度的系统:一是地域跨度大,二是时间跨度大;并且稳定性较差而动态性较强;它属于中间层次系统范围,本身具有可分性,可以分解成若干个子系统;同时,物流系统的复杂性使系统结构要素间有非常强的"背反"现象,常称之为"交替损益"或"效益背反"现象,处理时稍有不慎就会出现系统总体恶化的结果。在物流系统变得越来越复杂并且内部关联性越来越强的背景下,建模与仿真的方法在物流系统的完善和决策中变得日益重要。 由于物流系统要求在一定条件下达到物流总费用最省、顾客服务水平最好、全社会经济效益最高的综合目标,同时,由于物流系统包含多个约束条件和多重因素的影响,难以达到最有状态,物流系统的优化问题由此被提出并受到广泛关注。物流系统优化是指确定物流系统发展目标,能实现服务性和快捷性,能有效的利用面积和空间,使规模适当化,达到存储控制的目的,并设计达到该目标的策略以及行动的过程,它依据一定的方法、程度和原则,对与物流系统相关的因素,进行优化组合,从而更好实现物流系统发展的目标。最常用的方法主要有三种:运筹学方法、智能优化方法和模拟仿真法。 仿真是利用计算机来运行仿真模型,模拟时间系统的运行状态及其随时间变化的过程,并通过对仿真运行过程的观察和统计,得到被仿真系统的仿真输出参数和基本特性,以此来估计和推断实际系统的真实参数和真实性能。计算机仿真的类型有离散事件(系统)仿真、连续系统仿真、混合系统仿真,还有蒙特卡罗仿真等。物流系统是复杂的离散事件系统,在系统设计与控制过程中存在许多优化问题,用系统仿真为解决复杂物流系统的问题提供了有效的手段,它不仅可提供用于决策的定量信息而且可以提高决策者对物流系统工作原理的理解水平,仿真技术为复杂物流系统设计提供了技术性和经济性的最佳结合点和直观有效的分析方法。 下面,我主要介绍一下供应链的优化。 提到供应链优化,首先想到的是供应链管理。现在,物流管理的观念被大多
石油化工流程模拟、先进控制与过程优化技术的现状与展望
石油化工流程模拟、先进控制与过程优化技术的现状与展望 摘要:流程模拟、先进控制和过程优化技术的研究与应用是石油化工过程的一个重要方面。本文论述了该技术的发展现状和趋势,分析了我国在该研究中存在的主要问题、面临的机遇与挑战,指出了关键的技术问题。此外,对流程模拟、先进控制和过程优化技术的经济效益与应用前景也做了分析。最后,对于如何在我国开展石油化工流程模拟、先进控制与过程优化技术的研究与应用提出了几点建议和对策。 关键词:石油化工,流程模拟,先进过程控制,优化技术,过程建模Abstract: The development and applications of flow simulations, advanced process control, and process optimization technology are very important for petrochemical industry. In this paper, the status quo and prospects for flow simulations, advanced process control, and process optimization technology are discussed. The main problems existing in our research, the opportunities, and challenges are detailedly analyzed. At the same time, the key technical problems are also pointed out. In addition, the economy benefits and application prospects on flow simulations, advanced process control, and process optimization technology are investigated. Finally, some suggestions and countermeasures on how to work on the development and applications of flow simulations, advanced process control, and process optimization technology in our country are brought forward. Keywords:Petrochemical Industry, Flow Simulations, Advanced Process Control, Optimization Technology, Process Modeling 引言 石油化工是我国国民经济的支柱产业之一,其所实现的利润约占全国国有及国有控股企业总利润的1/4左右。但是,面临国际市场激烈的竞争和国内需求的不稳定,我国各石油化工企业均面临严重的挑战,与国际上发达国家的石化企业相比,我国的石化企业在质量、成本、规模、效益等方面尚存在较大的差距。以中国石化集团公司为例,综合商品率1996年为91.4%,1997年为91.12,1998年为91.67%,而同期美国为93.0%,英国为92.3%,法国为92.5%,国外平均水平大于92%。中石化的平均加工损失率1996年为1.29%,而1994~1995年美国、英国和法国分别为0.2%,0.3%和1.04%,世界平均水平为1%。中石化轻油收率1996年为65.11%,1997年为67.14%,1998年为67.95%,世界平均水平>70%[1]。每加工1吨原油的燃料动力费用中石化总公司1996年为63元,亚太地区平均水平为47元。 随着国内外市场竞争日趋激烈,要求石油化工企业对市场和生产环境的变化做出快速而有效的响应,以获得最大的经济效益。随着我国加入WTO的日益临近,深化改革企业的运行机制和管理体制,运用信息技术改造和提升传统产业,使其保持可持续发展,对于增强企业在国内、外市场的竞争能力具有十分重要的意义。世界各国的经验表明,流程模拟、先进控制与过程优化技术是提高企业的经济效益、降低生产成本、提高其在国际市场中的创新力、应变力、适应力和综
2020年整理化工系统过程模拟与优化.doc
学号:20095053007 《化工系统工程》课程论文 学院化学化工学院 专业化学工程与工艺 年级2009级 姓名 论文题目化工系统过程模拟与优化 指导教师职称讲师 成绩 2012年6月15日
目录
化工系统过程模拟与优化 摘要:化工系统过程模拟是计算机化工应用中最为基础、发展最为成熟的技术之一。本文从分子模拟、单元过程模拟及流程模拟三个模拟层次综述其发展现状及发展趋势。并对过程的优化和当前流行的国际国内商业化化工过程模拟软件及其主要功能、应用领域作了系统的总结。 关键词:过程优化;分子模拟;过程模拟;流程模拟 Abstract:Chemical process simulation system is the most basic computer chemical application, development of one of the most mature technology. This article from molecular simulation, unit process simulation and process simulation three simulation in its development level situation and the development tendency. And the process optimization and the current popular international and domestic commercial chemical process simulation software and its main function and application field is the summary of the system. Keywords:Process optimization; Molecular simulation; Process simulation; Process simulation 前言 利用计算机高超的能力解算化工过程的数学模型[1],以模拟化工过程系统的性能,这种技术早在50 年代已开始在化学工业中应用。经过40年的发展,现已成为一种普遍采用的常规手段,广泛应用于化工过程的研究开发、设计、生产操作的控制与优化,操作工的培训和老厂技术改造。而且随着计算机硬件的性能价格比的迅速提高、软件环境的改善与丰富,过程模拟技术发展的势头有增无减。 1 发展迅猛的成因 这种发展的成因可以归结为以下几个方面: 首先,化工行业市场竞争剧烈,要求化工新产品、新工艺开发周期短,用数学模拟可以大大加快筛选进度、减少实验工作、提高工程放大倍数、降低研究开发成本,
化工过程分析与综合习题答案
习题解答 2-1(1)d=n-m n=4(c+2) m=c+c+1+1=2c+2 d=4(c+2)-(2c+2)=2c+6 给定流入流股:2(c+2) 平衡级压力:1 所以没有唯一解 (2)存在热损失n=4(c+2)+1 m= =2c+2 d=2c+7 给定2c+5 所以没 有唯一解 (3)n=2(c+2)+2+2+1=2c+9 m=1+c+2=c+3 d=c+6 给定进料:c+2 冷却水进口温度:1 所以没有唯一解 2-2(1)N v=3(c+2) (2)物料衡算:F i Z Fi=Vy Fi+Lx Fi (i=1,2……c) 热量衡算:FH F=VH V+LH L 相平衡:y Fi=k i x Fi (i=1,2……c) 温度平衡:T V=T L 压力平 衡:P V=P L (3)N e=2c+3 (4)d= N v- N e=c+3 (5)进料(c+2)和节流后的压力(1) 2-3N x u 压力等级数 1 进料变量数 2(c+2)=4+3=7 合计9 N a u 串级单元数 1 回流分配器 2 侧线采出单元数 2 传热单元数 5 合计15 N v u=9+15=24 d=24 给定的不满足要求,还需给定入塔混合物的温度,两塔的操作压力,塔2 的回流比。 2-4N x u 压力等级数N+M+1+1+1(N 和M 为两个塔的塔板数) 进料变量数c+2 合计c+N+M+5 N a u 串级单元数 4 回流分配器 4 侧线采出单元数 1 传热单元数 4 合计10 N v u= c+N+M+5+10= c+N+M+15
d= c+N+M+15 2-5 2-6 2-7 简捷算法:Reflex Ratio:-1.3 Light Key:Methanol 0.95 Heavy Key:Ethanol 0.1585 Pressure:Condenser:1.9 公斤Reboiler:1.8 公斤 最小回流比为:3.529 实际回流比:4.588 最小理论板数:14.47 实际板数:26.18 进料板:10.47 逐板计算:27 块塔板,11 板进料,塔顶采出:31.67kmol/hr,回流比:4.6
交通运输方案模拟优化生成系统
交通运输方案模拟优化生成系统 /一、研究背景和目的 着眼对运输中装载、运送业务流程进行辅助决策,提高工作效率,提升工作质量,本项目计划开发的交通运输方案模拟优化生成系统主要具有三大功能: /(一)制定装备、器材、物资装载方案。对当前主要装备、弹药、器材物资箱组的体积、重量、装载要求等特征,/以及主要运输车辆、列车的容量、载重等性能进行数字化描述,为其/建立三维模型,建立装载性能参数系统数据库。/根据待运装备器材物资,运输车辆或列车的数量、种类,调用系统数据库中待运装备和承运车辆两者的空间、重量、载重等参数,进行仿真计算,将不同待运装备、物资与运输车辆进行合理匹配,制定最优化的装载方案,绘制三维装载图进行形象描述,辅助装载行动,最大限度发挥运力的效能。/(演示) /(二)制定公路运输计划。建立主要公路里程数据库,根据不同运输任务的待运装备物资的数量种类和目的地、到达时限要求,将各项任务进行科学整合,综合计算
运力需求,制定运输计划,确定行驶路线、里程、休息时间、中转地点等要素,提高运力使用率,计算油料消耗需求。/(演示) /(三)模拟演示。将计划中装备物资装载计划、车辆编队计划输入系统,实现任一分队所属装备物资战时装载位臵查询,装载、运输流程模拟三维显示。 /三、技术实现 /利用专业数据库,对各类装备、器材、物资和运输车辆装载参数等基础数据进行存储调用,确保数据的稳定性和存储查询高效,利用专业开发平台进行系统开发,给各业务流程建立计算模型,对任务需求进行数学抽象,通过数据输入、计算,得出最优化结果,生成相关方案计划,结合三维动画技术,实现立体显示。 1、制定装载方案是什么意思? 答:就是在不同种类的大量货物堆积在一起的时候,往往不知道把它们如何科学搭配装载在一辆或者多辆运输车上,才能节约空间,发挥最大效益。我们的思路是,将目前常见的如被装、给养、弹药、维修器材箱组等待装载的
化工仿真实习总结
化工仿真实习总结 为期两周的仿真实训结束了,这段时间的实验心情是复杂的。从这里可以看出,这个实训让我学到了很多,获得了很多以前单纯从课堂上无法获得的知识、经验。 在实验的过程中,使学生对装置的工艺流程,正常工况的工艺参数范围,控制系统的原理,阀门及操作点的作用以及开车规程等更加详细的了解,并掌握典型化工生产过程的开车、停车、运行和排除事故的能力。 在实验中我学到了许多经验,这位以后进入岗位实践提供了宝贵的资源。比如,在操作之前做到熟悉工艺流程,熟悉操作设备,熟悉控制系统,熟悉开车规程;分清各个操作流程的顺序性;分清阀门开大还是开小;操作切忌大起大落;先低负荷开车达正常工况后再缓慢提升负荷;建立物料平衡概念等。 两周的仿真实验,模拟了这许多的化工过程的操作流程。这种经历使得我们这些即将面向社会,走向工作岗位的毕业生们对各种过程的流程和相关程序有了感性上深刻的认识和了解,也让我们接触到了企业实际生产的去盘工作流程,将书本上的知识与实际情况很好的结合,做到学以致用。 感谢学校能给我们提供这么好的学习机会!也感谢老师的悉心指导。 2化工模拟仿真实验心得半个学期的校内化工模拟仿真实验结束了,这段时间的实验心情是复杂的。从这里可以看出,这个实验让我学到了很多,获得了很多以前单纯从课堂上无法获得的知识、经验。对于半个学期来的实验,在这里我以一种总结和自省的心态来完成这份报告。也以此纪念我在校内的实验生活。 仿真实验是以仿真机为工具,用实时运行的动态数学模型代替真实工厂进行教学实习的一门新技术。仿真机是基于电子计算机、网
络或多媒体部件,由人工建造的,模拟工厂操作与控制或工业过程 的设备,同时也是动态数学模型实时运行的环境。 仿真实验为学生提供了充分动手的机会,可在仿真机上反复进行开车、停车训练,在仿真机上,学生变成学习的主体。学生可以根 据自己的具体情况有选择地学习。例如自行设计、试验不同的开、 停车方案,试验复杂控制方案、优化操作方案等。可以设定各种事 故和极限运行状态,提高学生分析能力和在复杂情况下的决策能力。真实工厂决不允许这样做。高质量的仿真器具有较强的交互性能, 使学生在仿真实验过程中能够发挥学习主动性,实验效果突出。主 要内容为精选化工单元操作与典型的工业生产装置,如离心泵、换 热器、压缩、吸收、精馏、间歇反应、连续反应、加热炉及石油化 工中的催化裂化装置、常减压装置、合成氨中的转化装置等。采用 计算机进行仿真操作的方式。 在实验的过程中,使学生对装置的工艺流程,正常工况的工艺参数范围,控制系统的原理,阀门及操作点的作用以及开车规程等更 加详细的了解,并掌握典型化工生产过程的开车、停车、运行和排 除事故的能力。 在这里我举一些具体的实验例子来说明我们学习的内容: “精馏”、“吸收”是化学工业中进行混合物分离的两种单元操作,在化学工业中占有重要的地位。这两部分理论较抽象,只在课 堂上向学生传授相应的理论知识,学生觉得难以理解;由于没有实物 参照,教师在教授这部分内容时也感到有些被动。因此学生在学习 这两部分内容的同时,进行相应的实践课就显得尤为必要。 通过仿真实验,学生在学习了“精馏”、“吸收”两章的理论知识后,到实验室实际操作筛板精馏塔和填料吸收塔。实验室内“精馏”、“吸收”流程小巧、简洁,方便学生观察物料的反应。学生 在实训时,边操作、边观察、边思索、边讨论,不但可以解决课堂 的遗留问题,还可以将课本上的理论知识应用于实际的操作中。这 样一方面增强了学生的学习兴趣,激发了他们的学习积极性;一方面 给教学工作增添了许多色彩。
化工仿真实习心得体会
化工仿真实习心得体会 篇一:仿真实习的学习心得及体会 仿真实习的学习心得及体会 (兰州理工大学技术工程学院化学工程与工艺09160207) 经过连续两周的仿真实习,我们练习了离心泵、换热器、液位的控制、精馏塔的冷态开车、正常停车以及相应事故处理的仿真。通过这次仿真实习基本单元操作方法;增强了我对工艺过程的了解,进而也更加熟悉了控制系统的设计及操作。让我对离心泵、换热器、精馏塔等有了更深刻的了解和认识。通过本次的化工仿真实习收获颇多,对工艺流程、控制系统有了一定的了解,基本掌握了开车、停车等的规程。 开始接触化工仿真软件时,感觉很迷漫也很好奇,在后来的实习过程中我首先仔细阅读了课本上实习的具体流程,
基本明白了操作的规程。 特别是在练习精馏塔单元等复杂的化工过程的时候,我觉得应该: (1)要仔细认真的阅读课本上相应的流程操作,对每一步操作都应该要有所领会、理解,因为过程的熟悉程度在操作中使至关重要的。过程不够熟悉也许会误入歧途,错误的操作,最后事倍功半,也不能很好的掌握所需学习的内容。 (2)面对一个复杂的工艺过程时,如果不能事先了解到它们的作用和相应的位置,以及各自开到什么程度,在开车时我们可能会手忙脚乱,导致错误的操作,因此,在开车前最重要的准备工作就是熟悉整个的工艺过程。 (3)在开车后的操作中一定要有耐心,不能急于求成。无比达到每一步的工艺要求之后,才能进行下一步的操作,否则可能造成不可挽回的质量错误。因此在面对一个工艺流程,必须要了解这个工艺流程的作用是什么,要达到怎样
的目的,了解流程中的各个环节,是如何进料的,操作条件又是如何,要达到什么样的要求。只有这样我们才能更好的学习或掌握所练习的学习内容。 总之,通过二周的仿真实习,我明白了许多,同时也懂得了许多,在操作过程中对每一步工艺操作都要耐心的完成,要达到规定的要求,不能急于求成,否则会事倍功半。要不断的吸取失败的教训,虚心向老师和优秀的同学请教,总结经验。此外,在以后的学习和生活中,要更加刻苦、努力的学习自己的专业知识,夯实基础、扩大自己的知识面,从而在以后的工作或生活中,更好的为我所用,为以后踏上工作岗位打下基础! 篇二:化工仿真实习报告 目录 绪论 (1) 第一章仿DCS系统的操作方法 (2)