常减压蒸馏考试资料
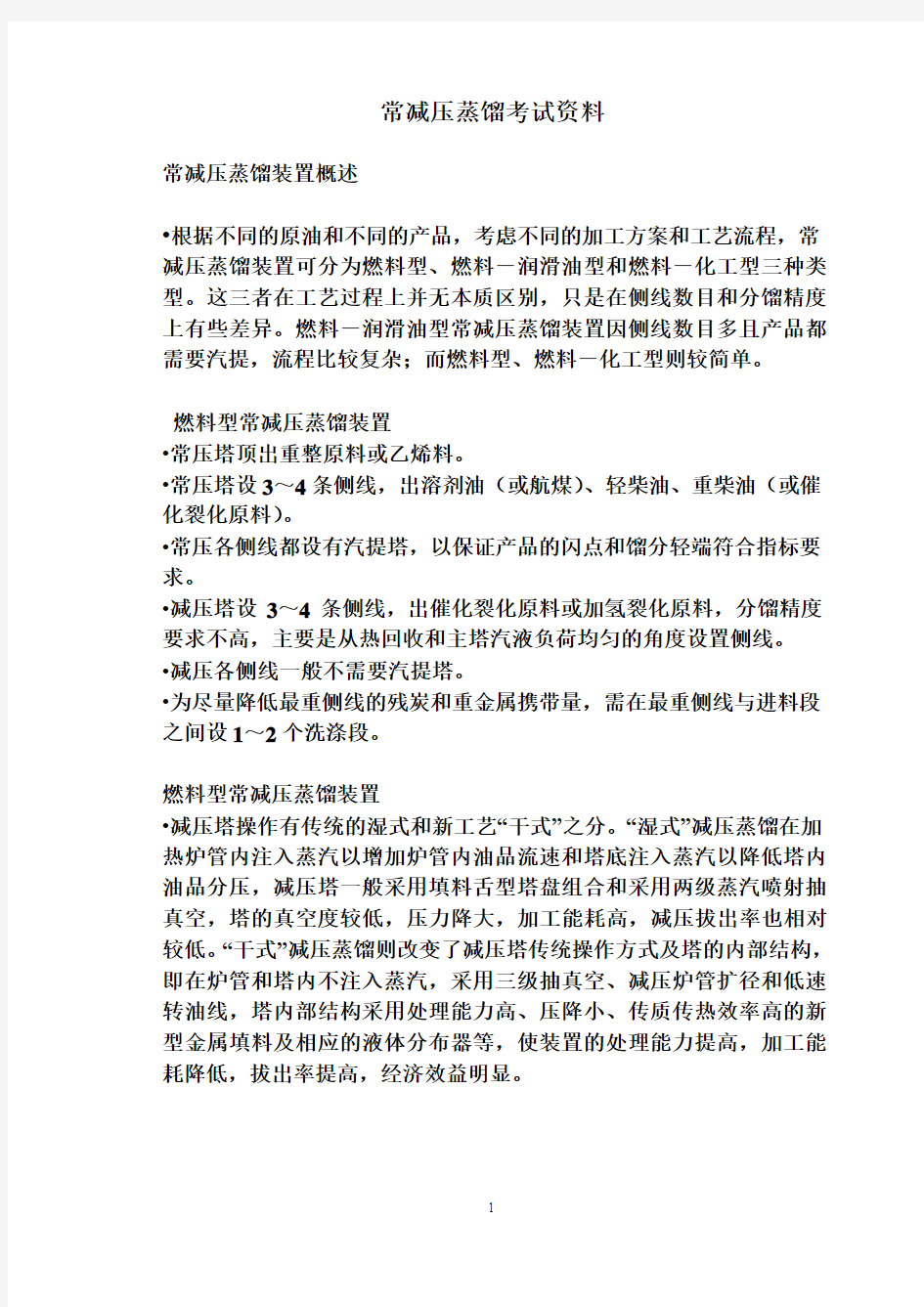

常减压蒸馏考试资料
常减压蒸馏装置概述
?根据不同的原油和不同的产品,考虑不同的加工方案和工艺流程,常减压蒸馏装置可分为燃料型、燃料-润滑油型和燃料-化工型三种类型。这三者在工艺过程上并无本质区别,只是在侧线数目和分馏精度上有些差异。燃料-润滑油型常减压蒸馏装置因侧线数目多且产品都需要汽提,流程比较复杂;而燃料型、燃料-化工型则较简单。
燃料型常减压蒸馏装置
?常压塔顶出重整原料或乙烯料。
?常压塔设3~4条侧线,出溶剂油(或航煤)、轻柴油、重柴油(或催化裂化原料)。
?常压各侧线都设有汽提塔,以保证产品的闪点和馏分轻端符合指标要求。
?减压塔设3~4条侧线,出催化裂化原料或加氢裂化原料,分馏精度要求不高,主要是从热回收和主塔汽液负荷均匀的角度设置侧线。?减压各侧线一般不需要汽提塔。
?为尽量降低最重侧线的残炭和重金属携带量,需在最重侧线与进料段之间设1~2个洗涤段。
燃料型常减压蒸馏装置
?减压塔操作有传统的湿式和新工艺“干式”之分。“湿式”减压蒸馏在加热炉管内注入蒸汽以增加炉管内油品流速和塔底注入蒸汽以降低塔内油品分压,减压塔一般采用填料舌型塔盘组合和采用两级蒸汽喷射抽真空,塔的真空度较低,压力降大,加工能耗高,减压拔出率也相对较低。“干式”减压蒸馏则改变了减压塔传统操作方式及塔的内部结构,即在炉管和塔内不注入蒸汽,采用三级抽真空、减压炉管扩径和低速转油线,塔内部结构采用处理能力高、压降小、传质传热效率高的新型金属填料及相应的液体分布器等,使装置的处理能力提高,加工能耗降低,拔出率提高,经济效益明显。
燃料-化工型常减压蒸馏
?常压塔设2~3个侧线,产品去做裂解原料,分馏精度要求不高,塔盘数目也比较少。
?各侧线不设汽提塔。
?减压系统与燃料型基本相同。
燃料-润滑油型常减压蒸馏装置
?常压塔与燃料型基本相同。
?减压塔一般设4~5条侧线,每条侧线对粘度、馏分、馏程、宽度、油品颜色和残炭都有指标要求。
?减压各侧线一般都有汽提塔以保证产品的闪点和馏分轻端符合指标要求。
?减压加热炉出口最高温度控制在4000C,并且炉管逐级扩径尽量减少油品受热分解,以免润滑油料品质下降。
?为使最重润滑油侧线的残炭和颜色尽可能改善,在最重润滑油侧线与进料之间需设置1~2个洗涤段,以加强洗涤效果。
?燃料-润滑油型减压塔,国内外当前仍以湿法操作为主,塔顶二级抽真空。
?另外还有“拔头型”,主要生产重整原料、汽油组分、煤油、柴油、燃料油或重油催化裂化原料,不生产润滑油组分和加氢裂化原料。?由于常减压装置的目的是将原油分割成为各种不同沸点范围的组分,以适应产品和下游工艺装置对原料的要求,因而不同原油和产品要求就有不同的加工方案和工艺流程,其典型流程可分为常减压蒸馏和常压蒸馏两种。
常减压蒸馏装置面临的新问题
?作为炼油企业的“龙头”,常减压蒸馏装置运行水平的高低,不仅关系到原油的有效利用,而且对全厂的产品质量、产品收率、经济效益产生很大的影响。这就要求我们积极应用先进适用的技术,不断推进常减压蒸馏技术的进步。但长期以来,特别是近几年来,常减压蒸馏工业运行中所暴露出的问题已引起重视(同时新的实用技术和高效设备
也不断被开发和应用),主要体现在以下四个方面:
?1、装置综合能耗偏高。2001年中国石化平均能耗为11.85kg标油/t,国外的先进水平已达10.22 kg标油/t。原因是:①装置规模小,开工负荷率低(国外炼油厂常减压装置单套加工能力已高达15Mt/a,开工率一般在85%以上,国内中石化仅为10Mt/a,平均负荷率70%多)。②加热炉燃料消耗大,排烟温度高,烟气含氧量高,辐射、对流管积灰严重,低温露点腐蚀加剧,原油的换热终温低造成了加热炉燃料消耗大。③装置电耗高:装置负荷率低,变频技术应用少,电机“大马拉小车”等现象严重。
?2、分馏精度和减压拔出率低
?特别是生产润滑油料时,减压塔的侧线分馏精度至关重要,只有足够的减压分馏精度,才能确保减压侧线馏分“窄馏程,浅颜色”;而常压拔的分馏精度目前尚未引起足够的重视。
?在国内,常减压蒸馏减压拔出偏低,是与国外主要差距之一。可通过降低汽化段压力,提高汽化段温度等途径来实现减压拔出率的提高。
?3、电脱盐运行工况不理想
?电脱盐已不仅仅是一种单纯的防腐手段,伴随着电脱盐、脱水、脱金属技术的日趋成熟,它已成为了下游装置提供优质原料所必不可少的原油预处理工艺。而造成运行工况不理想的主要原因有:①原油品种发生变化,破乳化剂的品种,注入量没有随之调整,造成破乳、脱盐效果下降。②电脱盐操作条件没有随原油品种、处理量的变化及时调整优化。③常减压蒸馏装置扩量,电脱盐没有相应配置扩量,导致电脱盐罐内原油线速偏高,脱盐停留时间偏短。
?4、含硫原油加工的适应性较差
?国内自产陆上原油与进口油相比,其性质主要差异是重质、低硫、含蜡,所以过去按加工国内自产陆上原油设计的常减压蒸馏装置对进口含硫原油加工适应性差。近几年,随着国内原油加工量的增加进口原油比例也明显增加。此外国内自产陆上原油的硫含量也呈上升趋势,因此对含硫原油加工适应性较差的问题也愈显突出,由于原油高含硫造成设备管线腐蚀严重而引起的非计划停工事故时有发生。
常减压蒸馏装置发展趋向
?近十年来,世界各国围绕提高常减压蒸馏装置的经济效益、社会效益
及环境效益这个中心,采用了大量的新技术、新工艺、新设备、新材料。归纳起来有四大趋势:装置规模趋向大型化,加工原油品种趋向多样化,生产操作趋向智能化,使用功能趋向多样化,具体表现在以下四个方面:
?1)在节能方面,采用原油闪蒸(初馏)流程、窄点技术优化换热流程、提高换热终温、计算机优化塔中段回流取热、电机变频调速技术、降低装置电耗。
?2)采用先进控制及新型塔器内部构件提高质量和增加收率,减少加工损失。
?3)在电脱盐技术方面,采用电动态脱盐工艺(国外),国内则开发了交直流电脱盐工艺,最近也正开发新一代国产高电脱盐技术可有效地解决了各种原油的深度脱盐问题。
?4)在装置长周期运作方面,采用抗腐蚀的设备材料如高温部分Cr5Mo,塔盘1Cr18Ni9Ti及防腐技术使生产周期39~53个月。
含硫原油的常减压蒸馏技术
?根据中东原油的特点,加工中东含硫原油需要处理好以下几方面的问题:
?(1)原油中的轻烃加以回收利用。
?(2)提高常压蒸馏的处理能力,避免常压蒸馏和减压蒸馏负荷失衡。?(3)充分回手利用低温余热。
?(4)减压深拔,多产馏分油,少产高硫渣油。
?(5)工艺设备的防腐,实现长周期安全生产。
原油蒸馏中的轻烃回收
?一、常减压与催化裂化联合回收轻烃
?二、提压操作法回收轻烃
?三、采用增压机增压的方法回收轻烃
选择不同的工艺提高处理能力
?选择新型的常压塔内件,提高处理能力
?原油分两次闪蒸,提高处理能力
?初馏塔提压操作和初底油降压闪蒸,减少常压塔负荷
低温位热的回收利用
?原油分多段换热,充分利用低温位热源
?采用“窄点”技术,优化换热网络
减压深拔技术
?提高常压塔拔出率,促进减压深拔
?采用全填料减压塔,提高真空度达到深拔
?控制减压塔底油温度,减少裂解气产生
?改善减压塔闪蒸段分离效果,减少雾沫夹带
?一段净洗和低液量分配,改善深拔瓦斯油质量
?减压深拔生产重交沥青
蒸馏设备的腐蚀及其防腐措施
?产生腐蚀的原因及其分类
?原油的深度脱盐
?塔顶的“三注”-----注中和剂、注水、注缓蚀剂
?高温部位腐蚀及其防腐措施
产生腐蚀的原因及其分类
?硫化物分解与温度的关系:
?T≤120℃,硫化物未分解,在没有水存在的情况下设备无腐蚀,但当有水存在时,则形成对轻油部位的H2S-H2O型腐蚀。
?120℃?T≤240℃原油中活性硫化物未分解,故设备无腐蚀。?240℃?T≤340℃,硫化物开始分解,生成H2S对设备开始产生腐蚀,随着温度的升高腐蚀加重。
?340℃?T≤400℃,H2S开始分解,生成H2和S,此时生成的FeS 本身具有防止进一步发生腐蚀设备的保护膜作用,但当有HCl存在时,HCl与FeS反应破坏了FeS保护膜,使腐蚀进一步发生,强化了腐蚀。?426℃?T≤430℃,高温硫对设备腐蚀最快。
?T>480℃,H2S几乎完全分解,腐蚀率下降。
原油的性质与评价
原油的一般性状
?原油(或称石油)通常是黑色、褐色或黄色的流动或半流动的粘稠液体,相对密度一般介于0.80~0.98之间。世界各地所产的原油在性质上都有不程度的差异,随着产地的不同而不同。原油的颜色深浅取决
于原油中含有胶质和沥青质的多少;原油有的有很浓的臭味,这是由于原油含有一些臭味的硫化物;不同的原油有着不同的凝固点,主要是原油中含有一定数量的蜡;原油的粘度取决于原油中含有润滑油馏分和胶质的多少;原油的比重(相对密度)取决于原油所含有的重质馏分、胶质、沥青质的多少。
原油的元素组成
?对于原油,其化学组成基本上由五种元素即碳、氢、硫、氮、氧所组成。原油中碳的质量分数一般为83.0%~87.0%,氢的质量分数一般为11.0%~14.0%,硫的质量分数一般为0.05~8.0%,氮的质量分数一般为0.02%~2.0%,氧的质量分数一般为0.05%~2.00%。微量元素包括钒、镍、铁、铜、铅,非金属元素包括氯、硅、磷、砷等,这些元素虽然极为微量,但对原油炼制工艺过程中影响很大。
?这些元素并非以单质出现,组成原油的化合物主要是碳元素和氢元素,是以烃类化合物的形式存在。硫、氮、氧这些元素则以各种含硫、含氮、含氧化合物以及兼含有硫、氮、氧多种元素的高分子的胶状和沥青质物质存于原油中,它们统称为非烃类化合物。
原油中的烃类化合物
?原油中的烃类主要含有烷烃、环烷烃、芳香烃,一般不含烯烃,只有在原油的二次加工产品中含烯烃。这些烃类组成是以气态、液态、固态的化合物存在。
?原油伴生气主要是甲烷及其低分子同系物组成的,因组成不同可分为干气(贫气)及湿气(富气)。在干气中,含有大量的甲烷和少量的乙烷、丙烷等气体。而在湿气中,除含有较多的甲烷、乙烷外,还含有少量易挥发的液态烃如戊烷、已烷直至辛烷蒸汽,还可能有少量的芳香烃及环烷烃存在。
?在原油伴生气中还经常杂有非烃气体,其中最主要的是二氧化碳、氮气。在含硫原油产地的原油伴生气中,常有硫化氢的存在。
?原油含的液体状态烃按其沸点不同,可分为低沸点馏分、中间馏分以及高沸点馏分,如在汽油馏分中含有C5-C11的正构烷烃、异构烷烃、单环环烷烃、单环芳香烃(苯系)。
?中间馏分如在煤油、柴油馏分含有C10-C20的正异构烷烃、带侧链的单环环烷烃、双环及三环环烷烃、双环芳烃、环烷一芳香的混合烃。
?高沸点馏分如润滑油馏分中含有C20-C36左右的正异构烷烃、环烷烃和芳香烃。环烷烃包括从单环直到六环甚至高于六环的带有环戊烷或环已烷的环烷烃,其结构主要是以稠环类型为主。芳香烃除包含单环、双环、三环芳香环外,还含有四环的甚至多于四个芳香环的芳烃。此外,在芳香环中还含有为数不等,多至5-6个环的环烷-芳香混合烃,它们主要也是呈稠合型的。
?原油中还含有一些高熔点、在常温下为固态的烃类,它们通常在原油中是处于溶解状态,但如果温度降低到一定程度,其溶解度降低就会有一部分结晶析出,在工业上称之为蜡。它们主要是分子量很大的正构烷烃,少量的异构烃、环烷烃及极少量芳香烃。
原油中的非烃化合物
?原油中含有相当数量的非烃化合物,尤其在原油重馏分中其含量更高。非烃化合物的存在对原油的加工及产品的使用性能具有很大的影响。在原油加工过程中,绝大多数的精制过程都是为了解决非烃化合物的问题。
?原油中的非烃化合物主要包括含硫、含氮化合物以及胶状、沥青状物质。
?在原油馏分中的分布一般是随着馏分沸程的升高而增加,大部分硫均集中在重馏分和渣油中。硫在原油中的存在形态已经确定的有:元素硫、硫化氢、硫醇、硫醚、环硫醚,二硫化物,噻吩及其同系物。直馏汽油馏分中的有机含硫化合物有硫醇,硫醚以及少量二硫化物和噻吩。直馏中间馏分中的硫化物主要是硫醚类和噻吩类。高沸馏分中含硫化合物大部分也是稠环、硫原子也多在环结构上。
?原油中的氧大部集中在胶状、沥青状物质中,除此之外,原油中氧均以有机化合物状态存在。这些含氧化合物,可分为酸性氧化物和中性氧化物两类。酸性氧化物中有环烷酸、脂肪酸以及酚类,总称为石油酸。中性氧化物有醛、酮等它们在原油中含量极少。在原油的酸性氧化物中,以环烷酸为最重要,它约占原油酸性氧化物的90%左右,环烷酸的含量,因原油产地不同而异,一般多在1%以下。环烷酸在原油馏分中的分布规律很特殊,在中间馏分中(沸程约为250-350℃左右)环烷酸含量最高,而在低沸馏分以及高沸重馏分中环烷酸含量都比较低
?原油中氮含量一般在万分之几至千分之几。我国大多数原油含氮量均低于千分之五。大部分氮也是以胶状、沥青状物质形态存在于渣油中。原油中的氮化物可分为碱性和非碱两类。所谓碱性氮化物是指能用高氯酸在醋酸溶液中滴定的氮化物。非碱性氮化物则不能。
?在原油非烃化合物中,大部分是胶状、沥青状物质。它们在原油中的含量相当可观,我国目前各主要原油中,含有大约百分之十几至四十几的胶质和沥青质。胶状、沥青状物质是原油中结构最复杂,分子量最大的物质,在其组成中除了碳、氢外还含有硫、氧、氮以及一些金属元素。
原油的馏分组成
?原油是一个多组分的复杂混合物,其沸点范围很宽,从常温一直到500℃以上,所以,无论是对原油进行研究或进行加工利用,都必须对原油进行分馏。分馏就是按照沸点的差别将原油“切割”成若干“馏分”,每个馏分的沸点范围简称为馏程或沸程。一般把原油中从常压蒸馏开始馏出的温度(初馏点)到200℃(或180℃)之间的轻组分称为汽油馏分(或称为轻油、石脑油馏分),常压蒸馏200℃(或180℃)~350℃之间的中间馏分分称为煤柴油馏分或常压瓦斯油(简称为AGO)。由于原油从350℃开始有明显的分解现象,所以对于沸点高于350℃的馏分,需要在减压下进行蒸馏,在减压下蒸出馏分的沸点再换算成常压沸点。一般将相当于350℃~500℃的高沸点馏分称为减压馏分或润滑油馏分或减压瓦斯油(简称为VGO);而减压蒸馏后残留的>500℃的油称为减压渣油(简称VR);同时也将>350℃的油称为常压渣油(简称AR)。
原油的评价
?原油评价方法概述:原油评价按照其目的的不同,可以分为三个层次:原油的一般性质;常规评价,除了原油的一般性质外,还包括原油的实沸点蒸馏数据及窄馏分性质;总合评价,除了上述两项内容外,还包括直馏产品的产率和性质。根据需要,也可以增加某些馏分的化学组成、某些重馏分或渣油的二次加工性能等。
?原油的一般性质;原油一般性质分析:比重、粘度、凝点、含蜡量、沥青质、硅胶胶质、残炭、水分含量、含盐量、灰分、机械杂质、元素分析、微量金属及馏程等。
?原油的实沸点蒸馏及窄馏分性质:分析原油切割窄馏分收率及性质,并给出原油实沸点曲线。实沸点蒸馏是用来考察石油馏分组成的实验方法。原油实沸点蒸馏所用的试验装置和操作条件都有一定规定。试验装置是一种间歇式精馏设备,精馏柱的理论板数为15~17,精馏过程在回流比为5:1的条件下进行。馏出物的最终沸点一般为500~520℃,釜底残留物则为渣油。为了避免原油的裂解,蒸馏时釜底温度不得超过350℃,因此整个蒸馏过程分为三段进行:常压蒸馏、减压蒸馏(10mmHg)、二段减压蒸馏(1~2mmHg,不带精馏柱)。
?直馏产品的性质及产率:直馏产品一般为较宽组分,为了取得其较准确的性质数据作为设计和生产的数据,必须由实验实际测定。通常的作法是先由实沸点蒸馏将原油切割成多个窄馏分和残油,然后根据产品的需要把相邻的几个馏分按其在原油中的含量比例混合,测定该混合物的性质。也可以直接由实沸点蒸馏切割得相应于该产品的宽馏分。?有了原油评价的总合评价过程所提供的原油及其它馏分的性质数据,就可以对原油进行加工之前提出加工方案,确定原油的加工方案,主要是使用上述原油评价过程中实沸点中各组分的产率及性质测定数据制成的原油实沸点蒸馏——性质曲线及各石油馏分的产率——性质曲线,按产品规格进行比较,确定各种产品的切割温度,从而也就能预测各种产品能够达到的产率和产品质量的情况。
原油的分类方法
?原油的组成复杂,对原油的确切分类是很困难。原油性质的差异,主要在于化学组成的不同,所以一般偏向于化学分类,但有时为了应用方便,也采用工业分类。化学分类法有关键馏分特性分类法、特性因素分类法、相关系数分类法、结构组成分类法。
?关键馏分特性分类法:1935年美国矿务局提出了对原油的关键馏分特性分类法,该方法能够较好的反映原油的化学组成特性,我国也广泛使用该法。用原油简易蒸馏在常压下蒸馏得到250~275℃馏分作为第一关键馏分,残油用没有填料柱的蒸馏瓶在40mmHg残压下蒸馏,切取275~300℃馏分(相当于395~425℃)作为第二关键馏分。将分别
测定上述两个关键馏分的密度对照关键馏分分类指标表:密度分类标准,决定两个关键馏分的属性,最后按照原油关键馏分特性分类表来确定该原油属于哪一类。
商品分类法
?A、密度分类(20℃密度)
?轻质原油:>34。API;〈0.852
?中质原油:34~20。API;0.852~0.930
?重质原油:20~10>。API;0.931~0.998
?特稠原油:〈10。API;>0.998
?B、硫含量分类:
?低硫原油:硫含量〈0.5%。
?含硫原油:硫含量0.5~2.0%。
?高硫原油:硫含量>2.0%。
?C、含蜡量分类:
?低蜡原油:蜡含量0.5~2.5%
?含蜡原油:2.5~10%
?高蜡原油:>10%。
开停工与事故处理
装置开工:
1、开工前的准备工作
2、设备、工艺管线蒸汽贯通试压(气密)
3、减压抽真空试验
4、加热炉烘炉(必要时才做)
5、进退油
6、试油压、闭路循环
7、加热炉点火,恒温脱水。
8、设备热紧
9、切换原油,常压开侧线
10、抽真空,减压开侧线
11、调整操作
1.3 减压抽真空试验
?检查抽真空系统及有关设备(真空泵)是否符合要求和满足工艺要求。?通过气密试验,检验减压塔及其系统的泄漏情况。
检验标准:
?无负荷时,真空度不得小于93 kpa(残压小于8kpa)
?停真空泵后,减压系统真空度下降速度小于2kpa/h,否则要重新查找漏点。
1.4 加热炉烘炉(必要时才做)
?通过缓慢加热除去炉体内砌筑的耐火砖及耐火材料中的水分,并使耐火胶泥得到充分的烧结,以防在开工时炉温上升太快,水分汽化膨胀造成炉体胀裂或变形,甚至炉墙倒塌等设备事故。
?进一步熟悉炉区仪表的性能,并考验其是否符合生产要求。
?考核加热炉炉体各零部件及炉管在热状态下的性能。
?考验各火嘴的使用性能并进行岗位练兵,达到提高操作水平的目的。
1.5 进退油
?目的是打通装置主流程,将装置内的存水退出。
?进油前装置必须达到四不开汽的条件,并经有关部门确认。
?进油前必须联系好原油罐及退油罐。
?进油前详细检查原油系统流程,对于放空阀,排污阀,联通阀,蒸汽扫线阀必须检查是否关严,严防跑油、串油,同时打开塔顶安全阀的手阀和塔顶系统放空流程。
?进油前仪表要启用,机泵送好电。
?启动原油泵并跟着受油流程作详细检查,严防跑油、串油。
?启动渣油泵后,退油开始, 以一定的速度进退油4~6个小时,期间切换原油泵及各塔底泵以赶净装置存水。
?进退油流程如图
1.6 试油压、闭路循环
?退油开始后,转入试油压阶段,初馏塔、常压塔底、减压塔底液面稍控高点。
?试油压前,安排好?°看压人、蹩压人和检查人?±,放慢进退油速度。试油压过程重点检查法兰、垫片、阀盖、温度计等处的严密性。
?试油压顺序,流程如下:
?原油泵出口→脱前换热器→电脱盐罐→脱后换热器→初馏塔
?初底泵出口→换热器→常压炉进料→常压塔(用常压炉出口阀调压)。?常底泵出口→炉进料→减压塔。
?渣油泵→换热器→渣油冷却器→退油线。
?试完油压后装置改闭路循环(也可以在装置改闭路循环后试油压)
说明:若装置检修质量较高,漏点少,一般此阶段需要2小时
1.7 加热炉点火,恒温脱水。
?检查加热炉烟道挡板、风门、风机状态、燃料油、燃料气调节阀是否灵活好用。
?改通初顶、常顶、减顶瓦斯放空流程,冷却器给上冷却水,减顶水封罐给上水封。
?加热炉管给上介质。
?吹扫瓦斯系统管线,引系统瓦斯进入装置,经气体采样分析合格后准备点火。
?点火后,常压炉以35℃/h的速度升温,循环油温达80℃时,电脱盐罐送电。
?常压炉出口温度150℃时,开始恒温脱水。
?恒温脱水时要保证常压塔顶温度>110℃(若塔顶温度达不到要求应适当提高常压炉出口温度),确保水能从塔顶脱尽。恒温脱水4小时后,循环油开始采样分析水份,直至含水<1.0%为止。
?循环油含水<1.0%后,恒温脱水阶段结束。
说明:脱水主要是将水从常压塔顶脱除,送电后电脱盐罐也可以脱除部分水,一般需4~6小时;此阶段只是对塔底主流程进行脱水,各侧线及中段回流难以实现,因此开工过程中各中段回流很容易抽空。
1.8 设备热紧
?常压炉继续升温,温度达250℃时进行恒温设备热紧。
说明:设备热紧阶段只对塔底主要流程的工艺管线、设备进行热紧,侧线及中段回流部位在本阶段无法热紧。这些部位的热紧只能在切换原油后进行。此阶段需2~4小时。
1.9 切换原油,常压开侧线
?设备热紧结束后,常压炉继续以35℃/h的速度升温。
?常压炉出口温度达300 ℃左右时(各装置视油种及各自情况定),切换原油,常压开侧线。
?切换原油后,常压炉以40℃/h向正常操作温度升温(350 ℃~360 ℃)。常压塔底给上吹汽。
?初、常顶挥发线注上氨、缓蚀剂和水。
?常压塔由上到下逐条开侧线,从上而下启动中段回流泵。
?常压侧线上量正常后,常压汽提塔给上吹汽,常压各油品颜色正常后送出装置。
1.10 抽真空,减压开侧线
?常压系统以及减底液面正常后,建立减顶回流,启动一、二级抽真空。?减压炉以40℃/h的速度升温,减压炉出口温度达320℃(各装置视自己情况定)时炉管给注汽,减压塔底给上吹汽。
?减顶挥发线注上氨、缓蚀剂。
?减压系统从上而下建立中段回流、从上而下开减压侧线。
?减压各侧线来油及中段回流正常后,减压汽提塔给上吹汽。
1.11 质量调整
?操作全面平稳后电脱盐注上一、二级水;
?蒸汽发生器并网
?引三塔顶瓦斯至炉烧或到轻烃回收装置。
?如果有用封油的装置,减压侧线来油正常后各塔底泵引注封油(注意赶水)。
?有初侧线的投用。
?联系分析产品质量。
?按调度要求提量调整。
装置停工
装置停工主要步骤
?准备工作。
?降量、降温。
?熄火,关侧线,装置改循环。
?退油、工艺管线吹扫及蒸塔。
停工前的准备工作
?学习停工方案。
?提前3?a5天落实计划,收配好氨.碱.缓蚀剂和破乳剂,以免收配过多造成不必要的浪费和影响环保。
?检查装置含油污水道清理畅通,落实好各项安全措施。
?降量前扫通装置循环线,渣油冷却器走正线,开足水量。
?停工前回炼完污油。
降量、降温
?首先按要求降量。降量过程中常、减压各侧线压轻出装置,降量过程中要注意调节各冷却器的冷后温度。
?降量达到降温条件,停止降量,炉子以40℃/h的速度开始降温。逐个停油嘴。
?电脱盐停注水、停注破乳化剂。
?联系油品改罐。
?减顶真空瓦斯改出炉子。
?常压炉出口温度约300℃时,炉子改自然通风,停炉管注汽。
熄火,关侧线,装置改循环
?初、常顶瓦斯改往塔顶放空,并开掩护蒸汽。
?常压炉出口温度<260℃时,常压炉熄火。
?减压炉出口温度<280℃时,停炉管注汽,减压炉熄火,吹扫燃料油线。?关常、减压塔底吹汽及汽提塔吹汽,自产蒸汽改放空。
?常压塔从下而上关侧线,侧线泵抽空后才停泵,关侧线冷却水,并放净存水。
?减压塔从下而上关侧线,关所有冷却器循环水进出口阀。
?关侧线后当塔顶温度不高时停打中段回流和循环回流。塔顶温<80℃时停打冷回流,停注缓蚀剂、氨和水。
?减压系统破真空,先破一级后二级。
?停原油泵,装置改闭路循环。吹扫渣油出装置阀后管线。
?停无盐水泵,打开各蒸汽发生器底无盐水排污阀 放空。
退油、工艺管线吹扫及蒸塔
?装置循环至减压塔底温度不大于140℃时装置停循环。开始退油,尽量降低减底液面,保持初镏塔、常压塔液面在工艺指标范围。
?电脱盐罐打开顶放空阀,用泵将罐内存油经退油线退出装置。
?常减压塔改好蒸塔流程,准备蒸塔。
?扫线原则:先重后轻,先长后短,汽、煤、柴油线先水顶后扫线。?冲洗及吹扫时,水量及蒸汽量要按要求。
?小于1.0MPa的压力表和真空表引压阀要关死,小于250℃的温度计
要取出或更换。
?吹扫冷换设备的管程和壳程时,必须打开另一程管线的阀门,严防憋压,同时冷却水必须在扫线之前放净。
?蒸汽扫线时,流量计走付线,以免损坏流量计。
?蒸塔时塔底不存液面,蒸煮时水温不小于90℃,蒸气吹扫、蒸煮时间不能小于60小时。容器吹扫时间不小于24小时。
?各塔、容器打开人孔后,要注意防止FeS自燃。
事故处理
事故处理的基本原则
不超温:
尤其是加热炉,要特别注意其低量偏流,局部过热和分支、出口、炉膛温度的超温问题,一旦超温要及时平衡流量,降温直至熄火;
不超压:
尤其是初、常顶、换热器、容器压力不超标,一旦超标,降原油、调吹汽、开空冷、放火炬,停泵消压;
不超液面:
尤其注意塔底液面,低则机泵易抽空,应及时降抽出量或停泵;高则易冲塔,要及时降原油量,直至切断原油进料,罐液面超标易带油或易溢出油品,扩大事态,应及时调整。
加热炉不回火:
减压系统不串入空气:
破真空时一定要关闭减压系统各放空阀,否则一旦空气串入减压塔会发生爆炸事故。因此除非是减压系统有泄漏,否则应待减压塔内油品温度降低到200℃以下再全破真空。
装置需紧急停工的情况
在装置生产过程中,当遇到突发的重大事故时,一时难以下手,为了迅速控制事态,避免事故的扩大和蔓延,保护人身、设备的安全,最大限度地减少损失,可果断地采取紧急停工手段,这些突发的重大事故,可以归纳为以下几类:
(1)本装置内发生重大着火、爆炸事故或外装置重大事故严重危及本装置安全。
(2)重大的灾害如地震等
(3)加热炉管严重烧穿、漏油着火
(4)主要机泵如:原油泵、塔底泵等严重故障无法运行或漏油着火
(5)公用系统,如水、电、风等长时间中断
(6)主要设备、工艺管线严重漏油着火无法处理。
装置工艺管线穿孔漏油是否需要停工处理,视情况而定,塔顶及塔底两条主流程泄漏如果无法通粘补或打卡注胶处理的应做停工处理。其余各侧线、中段回流泄漏一般可以将其切出,适当降低处理量即可。
紧急停工要点
(1)及时汇报调度和上级领导,通知消防队掩护或灭火。
(2)加热炉迅速熄火降温,塔顶瓦斯改放火炬或放大气。
(3)切断原油进料,停掉所有机泵(原油泵、塔底泵、侧线泵、回流泵、燃油泵、引风机等)。
(4)关闭所有汽提蒸汽,过热蒸汽放空。
(5)减压塔破真空,停真空泵前要关闭减顶瓦斯去炉子或放大气阀,严防空气倒串入塔。
(6)设备内给蒸汽掩护(微正压),其存油迅速拿走、退净。
(7)迅速切除与事故相关的管线、设备。
(8)严防超温、超压、超液面情况发生。
(9)其余工作按正常停工处理。
装置全面停电
因所有机泵停运,装置按紧急停工处理。
?加热炉立即熄火,三顶瓦斯改放空。
?各塔停吹汽,自产蒸汽改放空。
?立即关闭各泵出口阀并按下停电按钮。
?若短时间内不能恢复供电,则破真空。
?其他按正常停工处理。
装置停水(循环水)
因各冷却器无冷却水,初、常顶油气及减顶不凝气无法冷却,会造成塔顶安全阀起跳等安全事故,一些装置使用循环水做机泵冷却水的会造成密封泄漏。因此装置按紧急停工处理。
?加热炉立即熄火,三顶瓦斯改放空。
?各塔停吹汽,自产蒸汽改放空。
?若机泵冷却水使用循环水的立即关闭各泵出口阀并按下停电按钮。?减压破真空。
?其它步骤按正常停工处理。
装置停仪表风
?有与非净化风连通的立即打开连通阀,维持正常生产。
?若两种风全停,则将重点部位改副线操作(加热炉进料、燃料油燃料气控制阀),确实无法维持正常生产且停风时间较长时,请示上级作熄火改循环处理。
停系统蒸汽
蒸馏装置一般都有自产蒸汽,基本满足本装置使用,因此停系统蒸汽一般不须停汽。一、三、四蒸馏均有1.0Mpa及0.4Mpa两个蒸汽发生器,停系统蒸汽时只要适当关小外输蒸汽就可,同时稳定产汽热源尽量减小蒸汽压力波动。二蒸馏因无 1.0Mpa蒸汽发生器,而1.0Mpa蒸汽使用点有减压炉管注汽及加热炉油嘴雾化蒸汽,因此停1.0Mpa蒸汽时应停烧油嘴,增烧高压瓦斯和自产瓦斯,同时停减压炉管注汽并适当降低减压炉出口温度维持生产。
塔底泵喷油着大火
?立即切断该泵电源将泵停下,关闭泵进出口阀。若火太大无法接近时,联系电工在变电所拉下该泵电源,关闭最接近该泵的两头阀门。
?若火势可以控制,立即除组织人员扑火,迅速通知消防队和调度,并启动备泵维持生产。
?若火势过大无法控制时,按紧急停工处理。
炉管破裂
?若破裂后着火较小,按正常停工处理;若破裂后着火较大,按紧急停工处理。
?立即通知消防队和调度。
?加热炉立即熄火,开火嘴吹扫蒸汽和炉膛消防蒸汽。
?切断破裂的那一路炉管进料并给大该路吹扫蒸汽。
?若是常压炉炉管破裂,其余步骤按正常停工处理。
?若是减压炉炉管破裂,应尽快破除真空,减压塔底吹汽暂不停,其余
步骤按正常停工处理。
炉用风机自停
?立即检查炉火是否熄灭,若未熄火,则迅速打开自然通风门
?迅速启动备用风机(若有),正常后关自然通风门;
?若炉火已全熄灭,立即关闭所有火嘴,吹扫炉膛,然后炉子重新点火。
常减压蒸馏装置开工方案
常减压蒸馏装置开工方案 装置开工程序包括:物质、技术准备、蒸汽贯通试压,开工水联运、烘炉和引油开工等几部份,蒸汽贯通试压已完成,装置本次检修为小修,水联运、烘炉可以省略,本次开工以开工前的准备,设备检查,改流程,蒸汽暖线,装置引油等几项内容为主。 一、开工前的准备 1、所有操作工熟悉工作流程,经过工艺、设备、仪表以及安全操作等方面知识的培训. 2、所有操作工已经过DCS控制系统的培训,能够熟练操作DCS。 3、编制开工方案和工艺卡片,认真向操作工贯彻,确保开车按规定程序进行。 4、准备好开工过程所需物资。 二、设备检查 设备检查内容包括塔尖、加热炉、冷换设备、机泵、容器、仪表、控制系统、工艺管线的检查,内容如下: (一)塔尖 1、检查人孔螺栓是否把好,法兰、阀门是否把好,垫片是否符合安装要求。 2、检查安全阀、压力表、热电偶、液面计、浮球等仪表是否齐全好用。 3、检查各层框架和平台的检修杂物是否清除干净。 (二)机泵:
1、检查机泵附件、压力表、对轮防护罩是否齐全好用。 2、检查地脚螺栓,进出口阀门、法兰、螺栓是否把紧。 3、盘车是否灵活、电机旋转方向是否正确,电机接地是否良好。 4、机泵冷却水是否畅通无阻。 5、检查润滑油是否按规定加好(油标1/2处)。 6、机泵卫生是否清洁良好。 (三)冷换设备 1、出入口管线上的连接阀门、法兰是否把紧。 2、温度计、压力表、丝堵、低点放空,地脚螺栓是否齐全把紧。 3、冷却水箱是否加满水。 (四)容器(汽油回流罐、水封罐、真空缓冲罐、真空罐、真空放空罐) 1、检查人孔螺栓是否把紧,连接阀门、法兰是否把紧。 2、压力表、液面计、安全阀是否齐全好用。 (五)加热炉 1、检查火嘴、压力表、消防蒸汽、烟道挡板,一、二次风门、看火门、防爆门、热电偶是否齐全好用。 2、检查炉管、吊架、炉墙、火盆是否牢固、完好,炉膛、烟道是否有杂物。 3、用蒸汽贯通火嘴,是否畅通无阻,有无渗漏。 (六)工艺管线 1、工艺管线支架、保温、伴热等是否齐全。
减压蒸馏
一、实验目的 1、学习减压蒸馏的基本原理。 2、掌握减压蒸馏的基本操作。 二、实验原理 减压蒸馏是分离可提纯有机化合物的常用方法之一。它特别适用于那些在常压蒸馏时未达沸点即已受热分解、氧化或聚合的物质。 液体的沸点是指它的蒸气压等于外界压力时的温度,因此液体的沸点是随外界压力的变化而变化的,如果借助于真空泵降低系统内压力,就可以降低液体的沸点,这便是减压蒸馏操作的理论依据。 液体有机化合物的沸点随外界压力的降低而降低,温度与蒸气压的关系 温度与蒸气压关系图液体在常压、减压下的沸点近似关系图 *1mmHg≈133Pa *1mmHg≈133Pa 所以设法降低外界压力,便可以降低液体的沸点。沸点与压力的关系可近似地用下式求出: p为蒸气压;T为沸点(热力学温度);A,B为常数。 如以lg p为纵坐标,1/T为横坐标,可以近似地得到一直线。 三、基本操作训练:(含仪器装置和主要流程图) 减压蒸馏装置主要由蒸馏、抽气(减压)、安全保护和测压四部分组成。 蒸馏部分由蒸馏瓶、克氏蒸馏头、毛细管、温度计及冷凝管、接受器等组成。抽气部分实验室通常用水泵或油泵进行减压。 减压蒸馏装置 四、主要试剂用量 乙酰乙酸乙酯15mL 实验关键及注意事项: 1、仪器安装好后,先检查系统是否漏气,方法是:关闭毛细管,减压至压力稳定后,夹住连接系统的橡皮管,观察压力计水银柱有否变化,无变化说明不漏气,有变化即表示漏气。 2、为使系统密闭性好,磨口仪器的所有接口部分都必须用真空油脂润涂好,检查仪器不漏气后,加入待蒸的液体,量不要超过蒸馏瓶的一半,关好安全瓶上的活塞,开动油泵,调节毛细管导入的空气量,以能冒出一连串小气泡为宜。 3、当压力稳定后,开始加热。液体沸腾后,应注意控制温度,并观察沸点变化情况。待沸点稳定时,转动多尾接液管接受馏分,蒸馏速度以0.5~1滴/S为宜。 4、蒸馏完毕除去热源,慢慢旋开夹在毛细管上的橡皮管的螺旋夹,待蒸馏瓶稍冷后再慢慢开启安全瓶上的活塞,平衡内外压力,(若开得太快,水银柱很快上升,有冲破测压计的可能),然后关闭抽气泵。 五、思考题
实验九:减 压 蒸 馏
实验九、减压蒸馏 一、实验目的 1.了解减压蒸馏的基本原理 2.学会使用水(油)泵进行减压蒸馏的操作。 3.学习减压蒸馏装置的搭装和气密性的检查 4.掌握压力—沸点经验曲线的用法。 二、基本原理 Log P = A + B/T 式中:P为液体表面的蒸汽压;T为溶液沸腾时的绝对温度;A和B为常数。如果用logP 为纵坐标,1/T为横坐标可近似的得到一条直形,从二元组分已知的压力和温度可算出A和B 的数值,再将所选择的压力带入上式即可求出液体在这个压力下的沸点。 减压蒸馏适用于在常温下沸点较高,常压蒸馏时易发生分解、氧化、聚合等热敏性有机化合物的分离提纯。一般把低于一个大气压的气态空间称为真空,因此,减压蒸馏也称为真空蒸馏。 三、各种真空度范围 1. 10~760 mmHg 为粗真空,有机试验常用 2. 10-3~10 mmHg 为低真空,用于精细试验 3. 10-8~10-4 mmHg为高真空 4. <10-9 mmHg为超高真空 760mmHg —(n格/10) 760 mmHg 四、液体在常压、减压下沸点的近似图
1. 例如:水在760 mmHg时的沸点为100度,若求20mmHg时水的沸点值,可先在B线上 100度这一点上与C线上20mmHg这一点连线并延长至A线上,在A线上的交点即为20 mmHg时水的沸点22度。 2. 另外,压力对沸点的影响还可以做以下估算: 3. 从大气压降到25 mmHg,高沸点(250~300度)的化合物的沸点随之下降100~125 度左右; 4. 当减压降至25mmHg以下时,压力每降低一半时,沸点下降10度。 五、减压蒸馏的注意事项 A为常量蒸馏装置,B为微量蒸馏装置。本次试验用电热套加热、用水泵减压蒸馏。 1. 玻璃仪器有:100ml圆底烧瓶,克氏蒸馏头,直冷,双股接引管,圆底烧瓶50ml×2, 50ml量筒一支,抽气管,减压毛细管,温度计及其套管 2. 蒸馏瓶内液体不可超过一半,因为减压下蒸汽的体积比常压下大得多。 3. 装仪器时,首先要求检查磨口仪器是否有裂纹。安装仪器时每一个磨口都必须配合好, 同时为了提高气密性要求在磨口上涂凡士林。 4. 由于蒸汽体积比常压时大地多,故减压操作时要缓慢平稳地进行。避免蒸汽过热。减压 蒸馏时仪器不能有裂缝,不能使用薄壁及不耐压的仪器(如锥形瓶、平底烧瓶),仪器安装正确,不能有扭力和加热后产生内应力。 5. 为便于接收,减压蒸馏应使用双股接引管或多股接引管。 6. 在减压情况下,沸石已起不到汽化中心的作用,一般用毛细管通人空气或惰性气体,进 行气动搅拌。 7. 装好仪器后,首先检查气密性。 8. 空试操作:旋紧D(抽气管的螺旋夹),打开G(安全瓶活塞,开动泵,关闭G,观看 真空度。若真空度能顺利达到要求,打开D,慢开G,控制进气量,并观察压力瓶回到原位后,停泵。若空试时,系统达不到所需的真空度,需要细心检查,可用手卡住安全瓶与真空接引管间的胶管,观察真空度是否变化。如果真空度不变,可能泵本身漏气,或者泵效能有问题。若真空度可以上升,即说明仪器装置系统有漏气之处,应一个个接口处仔细查找。检查出漏气之处,排除故障后,才能进入正常操作。 7. 减压系统仪器装置要做到气流通畅又密封,各种仪器安装尽量紧凑。
常减压蒸馏
常减压蒸馏 一、蒸馏的形式 蒸馏有多种形式,可归纳为闪蒸(平衡气化或一次气化)、简单蒸馏(渐次气化)和精馏三种方式。 简单蒸馏常用于实验室或小型装置上,如恩氏蒸馏。而闪蒸和精馏是在工业上常用的两种蒸馏方式,前者如闪蒸塔、蒸发塔或精馏塔的气化段等,精馏过程通常是在精馏塔中进行的。 1、闪蒸 闪蒸(flash distillation):加热某一物料至部分气化,经减压设施,在容器(如闪蒸罐、闪蒸塔、蒸馏塔的气化段等)的空间内,于一定温度和压力下,气、液两相分离,得到相应的气相和液相产物,叫做闪蒸。 闪蒸只经过一次平衡,其分离能力有限,常用于只需粗略分离的物料。如石油炼制和石油裂解过程中的粗分。 2、简单蒸馏
简单蒸馏(simple distillation):作为原料的液体混合物被放置在蒸馏釜中加热。在一定的压力下,当被加热到某一温度时,液体开始气化,生成了微量的蒸气,即开始形成第一个汽泡。此时的温度,即为该液相的泡点温度,液体温合物到达了泡点状态。生成的气体当即被引出,随即冷凝,如此不断升温,不断冷凝,直到所需要的程度为止。这种蒸馏方式称为简单蒸馏。 在整个简单蒸馏过程中,所产生的一系列微量蒸气的组成是不断变化的。从本质上看,简单蒸馏过程是由无数次平衡汽化所组成的,是渐次气化过程。简单蒸馏是一种间歇过程,基本上无精馏效果,分离程度也还不高,一般只是在实验室中使用。 3、精馏 精馏(rectification)是分离液相混合物的有效手段,它是在多次部分气化和多次部分冷凝过程的基础上发展起来的一种蒸馏方式。 炼油厂中大部分的石油精馏塔,如原油精馏塔、催化裂化和焦化产品的分馏塔、催化重整原料的预分馏塔以及一些工艺过程中的溶剂回收塔等,都是通过精馏这种蒸馏方式进行操作的。
人教版高中化学必修1-1.1《蒸馏和萃取》知识总结
第一节化学实验基本方法 第3课时蒸馏和萃取 知识点一:蒸馏 1. 原理:利用互溶的液体混合物中各组分的沸点不同,用蒸馏的方法除去易挥发、难挥发或不挥发的杂质。 2. 实验仪器 ①蒸馏烧瓶:蒸馏烧瓶属于烧瓶类。 蒸馏烧瓶与普通烧瓶不同的地方,在于瓶颈部位有一略向下的支管,它是专门用来蒸馏液体的容器。蒸馏烧瓶有减压蒸馏烧瓶及常压蒸馏烧瓶2类。常压蒸榴烧瓶也分支管在瓶颈上都、中部和下部的3种,蒸馏沸点较高的液体,选用支管在瓶颈下部的蒸馏烧瓶,沸点较低的则用支管在上都的蒸馏烧瓶。而支管位于瓶颈中部者,常用来蒸馏一般沸点的液体。 蒸馏烧瓶的规格以容积大小区别,常用为150mL和250mL 2种。 ②冷凝器:冷凝器又叫冷凝管,是用来将蒸气冷凝为液体的仪器。 冷凝器根据不同使用要求有多种结构不同的类型。内管有直型(如图1-3中所示)、蛇形和球形3种。直型冷凝器构造简单,常用于冷凝沸点较高的液体,蛇形冷凝管特别适用于沸点低、易挥发的有机溶剂的蒸馏回收。而球形者两种情况都适用。 冷凝管的规格以外套管长度表示,常用为200 mm、300 mm、400 mm、500 mm和600 mm等几种。 直形冷凝器使用时,既可倾斜安装,又可直立使用,而球形或蛇形冷凝器只能直立使用,否则因球内积液或冷凝液形成断续液柱而造成局部液封,致使冷凝液不能从下口流出。 ③应接管:也叫尾接管或称接受器又名牛角管。它与冷凝器配套使用,将蒸馏液导入承接容器。 应接管的弯角约为105°,便于和蒸馏烧瓶支管75"角相配,安装后二者保持平行。 应接管的规格以上口外径和长度表示,常用为18×l50mm、25×180mm和 30×200mm 3种)。
强烈推荐2.s1-1-2蒸馏和萃取知识点精华
强烈推荐2.S1-1-2蒸馏和萃取知识点精华(总2页) -CAL-FENGHAI.-(YICAI)-Company One1 -CAL-本页仅作为文档封面,使用请直接删除
1S 1-1-2 蒸馏和萃取 一、蒸馏 1. 原理 利用混合物中个组分的沸点不同,除去液态混合物中易挥发、难挥发或不挥发的杂质的方法。 2. 仪器及装置图 3.注意事项 (1)蒸馏时,在烧瓶中放少量碎瓷片或沸石,防止液体暴沸。 (2)冷凝管中冷却水从下口进,上口出。先通冷凝水,再加热,蒸馏结束时先熄灭酒精灯,再停止通冷却水。 (3)分离多种液体时使用蒸馏烧瓶和温度计,且温度计水银球在蒸馏烧瓶的支管口处。(制取蒸馏水则用烧瓶即可,无需温度计) (4)烧瓶中所盛液体体积一般应介于其容积的1/3 ~2/3 之间。 (5)给蒸馏烧瓶加热时,要垫上石棉网。 (6)装置组装顺序:从下到上,从左到右。 4.应用(制取蒸馏水) 二、萃取和分液 1.原理 (1)萃取 利用物质在互不相溶的溶剂里溶解度的不同,用一种溶剂把物质从它与另一种溶剂所组成的溶液里提取出来的方法。 (2)分液 把两种互不相溶的液体分开的操作。(例如:分离四氯化碳和水) 2.实例(用四氯化碳萃取碘水中的碘) (1)仪器:分液漏斗、烧杯、铁架台 (2)步骤 1
3.注意事项及说明 (1)分液漏斗使用前一定要检漏,方法如下: 在分液漏斗中注入少量的水,塞上瓶塞,倒置看是否漏水,如不漏,正立后把瓶塞旋转1800,再倒置看是否漏水。 (2)萃取剂必须具备的三点性质 ①萃取剂与水互不相溶 ②萃取剂和溶质不发生反应 ③溶质在萃取剂中的溶解度远大于在原溶剂中的溶解度。 (3)分液操作的注意事项 ①振荡时,要不时旋开活塞放气,以防止分液漏斗内压强过大引起危险。 ②分液时,要将上口玻璃塞打开,或使塞上的凹槽(或小孔)对准漏斗上的小孔。保证漏斗内外气压相同,同时使漏斗下端紧贴烧杯内壁,使液体顺利流下。 ③下层液体要从下口放出,上层液体要从上口倒出。 (4)常见萃取剂 苯、汽油:无色液体,难溶于水,密度小于水。 四氯化碳:无色液体,难溶于水,密度大于水。 (5)溴、碘的性质 均易溶于有机溶剂,在水中的溶解度不大。 碘的四氯化碳溶液呈紫红色;溴的四氯化碳呈橙色。 (6)由于酒精与水互溶,故酒精一般不做萃取剂。
常减压蒸馏装置的操作
常减压蒸馏装置的操作 主讲人:王立芬 一、操作原则 ●根据原料性质,选择适宜操作条件,实现最优化操作。 ●严格遵守操作规程,认真执行工艺卡片,搞好平稳操作。 ●严格控制各塔、罐液面、界面30~70%。 ●严格控制塔顶及各部温度、压力,平稳操作 ●根据原油种类、进料量、进料温度调整各段回流比,在提高产品质量的同时提高轻质油 收率和热量回收率。 二、岗位分工 ●负责原油进料、电脱盐罐、初馏塔液面、常顶回流罐、初顶回流罐液面界面、常一线、 常二线、常三线汽提塔液面以及常一中、常二中蒸发器液面调节,和本岗位计量仪表的数据计量工作。 ●调节各回流量及各部温度、流量,保证产品合格。 ●负责空冷风机的开停操作。 ●负责低压瓦斯罐及低压瓦斯去减压炉操作。 ●负责本岗位塔、容器、换热器、冷却器及所属工艺管线、阀门、仪表等设备的正确操作、 维护保养、事故处理。 ●负责与中心化验室的联系工作,及时记录各种分析数据。 ●负责本岗位消防设施管理。 ●负责本岗安全生产工作,生产设备出现问题要及时向班长汇报,并迅速处理。 ●.负责本岗位所属工艺管线、阀门等防凝防冻工作。 ●如果班长不在,常压一操执行班长的生产指挥职能或由车间指派。 ●负责仪表封油、循环水、风、9公斤蒸汽等系统的调节。 1 正常操作法 初馏塔底液面调节 控制目标:50% 控制范围:±20% 控制方式:正常操作时,初馏塔底液面LIC-105与原油控制阀FIC-102进行 串级控制,当LIC-105低于设定时,FIC-102开大,当LIC-105 高于设定时,FIC-102关小,从而实现初馏塔底液面的控制。
2 初馏塔塔顶压力调节 控制目标:≤0.08MPa 控制方式:正常操作时,初馏塔塔压通过塔顶风机运转数量调节,压力升高, 增加风机的运转数量,压力下降,减少风机运转的数量,从而实现 初馏塔塔压的控制。 异常处理 3 初馏塔塔顶温度调节 控制目标:≤125℃ 控制范围:视加工原油情况和产品质量控制调节,上下波动不超过10% 控制方式:正常操作时,初馏塔塔顶温度TIC-107与塔顶回流控制阀FIC- 103进行串级控制,当TIC-107低于设定时,FIC-103开大,当 TIC-107高于设定时,FIC-103关小,从而实现初馏塔塔顶温度 的控制。
常减压蒸馏装置的三环节用能分析
2003年6月 石油学报(石油加工) ACTAPETROLEISINICA(PETROLEUMPROCESSINGSECTION)第19卷第3期 文章编号:1001—8719(2003)03—0053—05 常减压蒸馏装置的“三环节"用能分析ENERGYANALYSIS0FATMoSPHERICANDVACUUMDISTILLATION UNITBASEDONTHREE-LINKMETHoD 李志强,侯凯锋,严淳 LIZhi—qiang,HOUKai—feng,YANChun (中国石化工程建设公司,北京100011) (SINOPECEngzneeringIncorporation,BeOing100011,China) 摘要:科学地分析评价炼油过程用能状况是节能工作的基础。笔者以某炼油厂常减压蒸馏装置为例,运用过程系统三环节能量结构理论,依据热力学第一定律和热力学第二定律进行了装置的能量平衡和炯平衡计算及分析,并根据分析结果指出了装置的节能方向,提出了节能措施。 关键词:常减压蒸馏;节能;三环节能量结构;能量平衡和炯平衡分析 中图分类号:TE01文献标识码:A Abstract:Energy—savinginrefineriesneedstobecarriedoutbasedonthescientificallyenergyanalysisandevaluationoftheprocessingunits.Theatmosphericandvacuumdistillationunitinarefinerywastakenasanexample,its energy andexergybalanceswerethenworkedoutthroughcalculationaccordingtothethree—linkmethodforprocessintegrationfollowingtheFirstLawandtheSecondLawofthermodynamics.Theresultswereanalyzed,andthecorrespondingmeasuresforenergy—savingwereproposed. Keywords:atmosphericandvacuumdistillationunit;energy~saving;three—linkenergymethod;energyandexergybalanceanalysis 炼油生产过程中为分离出合格的石油产品,需要消耗大量的能量。因此,能源消耗在原油加工成本中占有很大的比例。炼油过程的节能不仅可以降低加工成本,而且关系到石油资源的合理利用和企业的经济效益¨J。与国外先进的炼油厂相比,我国炼油企业的吨油能耗相对较高。2001年,中国石化股份有限公司所属炼厂平均能耗为77.85kg标油/t原油,与目前世界上大型化复杂炼厂的能耗不大于75kg标油/t原油的先进指标相比,差距较大,节能空间也更大。因此,加强节能技术的应用,降低炼油过程的能耗,是我国炼油企业降本增效、提高市场竞争力、实现可持续发展的必由之路。 炼油企业的用能水平因生产规模、加工流程、工艺装置的设计、操作和管理水平以及加工原油的品种和自然条件等不同而差别较大。因此,炼油企业的节能工作必须因厂而异,因装置而异,节能措施要有针对性。科学地分析评价炼油过程用能状况则是节能工作的基础【2J。笔者以某炼油厂的常减压蒸馏装置为例,运用过程系统三环节能量结构理论,依据热力学第一定律和热力学第二定律进行了装置的能量平衡和炯平衡计算,并根据计算结果对装置的用能状况进行了分析与评价,指出了能量利用的薄弱环节和装置的节能方向,提出了相应的节能措施。 1三环节能量结构理论 炼油生产过程的用能有3个特点:(1)产品分离和合成需要外部供应能量,以热和功两种形式传给 收稿日期:2002—07—23 通讯联系人:侯凯锋
《蒸馏和萃取》知识总结教学提纲
《蒸馏和萃取》知识 总结
第一节化学实验基本方法 第3课时蒸馏和萃取 知识点一:蒸馏 1. 原理:利用互溶的液体混合物中各组分的沸点不同,用蒸馏的方法除去易挥发、难挥发或不挥发的杂质。 2. 实验仪器 ①蒸馏烧瓶:蒸馏烧瓶属于烧瓶类。 蒸馏烧瓶与普通烧瓶不同的地方,在于瓶颈部位有一略向下的支管,它是专门用来蒸馏液体的容器。蒸馏烧瓶有减压蒸馏烧瓶及常压蒸馏烧瓶2类。常压蒸榴烧瓶也分支管在瓶颈上都、中部和下部的3种,蒸馏沸点较高的液体,选用支管在瓶颈下部的蒸馏烧瓶,沸点较低的则用支管在上都的蒸馏烧瓶。而支管位于瓶颈中部者,常用来蒸馏一般沸点的液体。 蒸馏烧瓶的规格以容积大小区别,常用为150mL和250mL 2种。 ②冷凝器:冷凝器又叫冷凝管,是用来将蒸气冷凝为液体的仪器。 冷凝器根据不同使用要求有多种结构不同的类型。内管有直型(如图1-3中所示)、蛇形和球形3种。直型冷凝器构造简单,常用于冷凝沸点较高的液体,蛇形冷凝管特别适用于沸点低、易挥发的有机溶剂的蒸馏回收。而球形者两种情况都适用。 冷凝管的规格以外套管长度表示,常用为200 mm、300 mm、400 mm、500 mm和600 mm等几种。 直形冷凝器使用时,既可倾斜安装,又可直立使用,而球形或蛇形冷凝器只能直立使用,否则因球内积液或冷凝液形成断续液柱而造成局部液封,致使冷凝液不能从下口流出。 ③应接管:也叫尾接管或称接受器又名牛角管。它与冷凝器配套使用,将蒸馏液导入承接容器。 应接管的弯角约为105°,便于和蒸馏烧瓶支管75"角相配,安装后二者保持平行。
应接管的规格以上口外径和长度表示,常用为18×l50mm、25×180mm和30×200mm 3种)。 使用时,应接管的上口通过单孔橡胶塞与冷凝器的下端管口相连。应接管的下口直接伸入承接容器内。 ④温度计:温度计是用于测量温度的仪器。其种类很多,有数码式温度计,热敏式温度计等。而实验室中常用为玻璃液体温度计,简称温度计。 温度计可根据用途和测量精度分为标准温度计和实用温度计2类。标准温度汁的精度高,它主要用于校正其它温度计。实用温度计是指所供实际测温用的温度计,主要有实验用温度计、工业温度计、气象温度计、医用温度计等。中学常用棒式工业温度汁。其中酒精温度计的量程为100°C,水银温度计有量程为200°C和量程为360°C两种规格。 使用时应选择适合测量范围的温度计。严禁超量程使用温度计。禁止用温度汁代替玻璃棒用于搅拌。用完后应擦拭干净,装入纸套内,远离热源存放。 ⑤锥形瓶:充当承接容器,由于口径较小,能减少液体挥发,比烧杯适合作承接容器。也有人把锥形瓶与应接管的组合称为接收器。 【要点提示】实验注意事项 ①蒸馏装置的连接应按由下至上,从左到右的顺序。 ②蒸馏烧瓶配置温度计时,应选用合适的橡胶塞,特别要注意检查气密性是否良好。加热时应放在石棉网上,使之均匀受热。 ③用水作冷却介质,将蒸气冷凝为液体。冷凝水的走向要从低处流向高处,即如图1-3所示下口进水,上口出水,千万不能将进水口与出水口接反(注意:冷水的流向要与蒸气流向的方向相反)。 ④测液体温度时,温度计的液泡应完全浸入液体中,但不得接触容器壁。测蒸汽温度时液泡应在液面以上。测蒸馏馏分温度时,液泡应略低于蒸馏烧瓶支管(精确地说,温度计的液泡的上缘要恰好与蒸馏瓶支管接口的下缘在同一水平线上。如图1-3所示)。
蒸馏和萃取教学设计
蒸馏和萃取教学设计 课题:蒸馏和萃取 教科书版本:新人教版 课型:新授课 教学内容和学生情况分析: 教学内容:上节课讲了过滤和蒸发两个分离提纯的方法,这节课中心将放在蒸馏和萃取的讲解。蒸馏装置的安装注意事项以及四氯化碳萃取碘水中的碘的实验操作,特别是分液漏斗的正确使用。 学生情况:学生在初中学习过一些基本的实验操作,随着时间的过去都有所遗忘。学生来自不同的中学所以实验操作技能水平肯定是参差不齐。教师在教学中不仅要做好与初中知识的衔接还要照顾到一些实验操作技能差的同学。 教学目标: 知识与技能: 1、初步学会蒸馏、萃取等分离方法 2、知道现实生活中常见的一些混合物分离和提纯的方法,用已 有的生活经验使学生加深对混合物分离、提纯等实验的认识。 过程与方法: 1、通过创设情境,导入实验安全标识、化学品安全使用标识, 进而掌握实验的基本准备常识,并形成良好的实验习惯。 2、通过独立思考、探索,在对物质性质研究的同时,能设计出 自己的实验方案,并逐渐在设计中体现自己的个性,具有一 定的创造性。 情感态度价值观: 1、体验科学探究的过程,学习运用以实验为基础的研究方法, 提高学生的科学素养,为学生的终身可持续发展奠定基础 2、发展学习化学的兴趣,乐于探究物质变化的奥秘,体验科学 探究的艰辛和喜悦,逐渐培养科学精神和科学品质 3、树立绿色化学思想,形成环境保护的意识 教学重点:萃取实验步骤 教学难点:萃取实验步骤
教学方法:讲授法实验法 教学媒体:传统教学媒体 教学过程: 〖导入新课〗在实验室中溶解固体药品时要用到蒸馏水,同学们知不知道蒸馏水是怎么制得的吗? 〖教师讲解〗蒸馏定义、蒸馏装置及其安装时的注意事项 〖教师板书〗 一、蒸馏:利用液体沸点不同,提纯液态纯净物的方法 1、蒸馏瓶中放入少量碎石片防止液体爆沸 2、冷凝管中冷却水下进上出 3、蒸馏烧瓶液体在其容积的1/3至2/3之间 4、加热时蒸馏烧瓶要加石棉网 5、温度计水银球应在烧瓶支管口处 〖过渡〗怎么检验蒸馏水中是否含有Cl-? 〖教师板书〗Cl-的检验: ①加稀硝酸酸化 ②加AgNO3 〖过渡〗海水中含有少量的碘可以用蒸发的方法提纯,但是蒸发会耗大量的能量,于是科学家们找到一种新方法提取碘——萃取 〖教师板书〗二、萃取 1、定义:用一种溶剂把溶在另一种溶剂中的溶质提取出来的方法〖过渡〗在萃取中要用到分液漏斗,展示分液漏斗 〖教师实验〗做四氯化碳萃取碘水中的碘的实验,边做实验边讲解分液漏斗使用时的注意事项。展示实验过程中现象的变化 〖过渡〗萃取实验做完,两种互不相溶的溶液要将它们分开就要涉及到分液操作 〖教师板书〗三、分液 1、定义:把两种互不相溶的液体分开的操作 2、下层液体从下管放出,上层液体由上口倒出 〖教师活动〗引导学生归纳出萃取剂的选择 〖教师板书〗2、萃取剂
常减压蒸馏原理
常减压蒸馏原理 摘要:常压蒸馏是石油加工的“龙头装置”,后续二次加工装置的原料,及产品都是由常减压蒸馏装置提供。常减压蒸馏主要是通过精馏过程,在常压和减压的条件下,根据各组分相对挥发度的不同,在塔盘上汽液两相进行逆向接触、传质传热,经过多次汽化和多次冷凝,将原油中的汽、煤、柴馏分切割出来,生产合格的汽油、煤油、柴油及蜡油及渣油等。(1)由此掌握常减压蒸馏原理对于从事相关工作的人员来说显得尤其重要。本文先从蒸馏的基本概念和原理说起,然后分别对常压蒸馏、减压蒸馏的原理做一个简要介绍。 关键词:蒸馏、基本概念和原理、常压蒸馏、减压蒸馏 一、蒸馏的基本概念和原理 1、基本概念 1.1饱和蒸汽压 任何物质(气态、液态和固态)的分子都在不停的运动,都具有向周围挥发逃逸的本领,液体表面的分子由于挥发,由液态变为气态的现象,我们称之为蒸发。挥发到周围空间的气相分子由于分子间的作用力以及分子与容器壁之间的作用,使一部分气体分子又返回到液体中,这种现象称之为冷凝。在某一温度下,当液体的挥发量与它的蒸气冷凝量在同一时间内相等时,那么液体与它液面上的蒸气就建立了一种动态平衡,这种动态平衡称为气液相平衡。当气液相达到平衡时,液面上的蒸气称为饱和蒸汽,而由此蒸气所产生的压力称为饱和蒸汽压,简称为蒸汽压。蒸气压的高低表明了液体中的分子离开液面气化或蒸发的能力,蒸气压越高,就说明液体越容易气化。 在炼油工艺中,根据油品的蒸气压数据,可以用来计算平衡状态下烃类气相和液相组成,也可以根据蒸气压进行烃类及其混合物在不同压力下的沸点换算、计算烃类液化条件等。 1.2气液相平衡 处于密闭容器中的液体,在一定温度和压力下,当从液面挥发到空间的分子数目与同一时间内从空间返回液体的分子数目相等时,就与液面上的蒸气建立了一种动态平衡,称为气液平衡。气液平衡是两相传质的极限状态。气液两相不平衡到平衡的原理,是气化和冷凝、吸收和解吸过程的基础。例如,蒸馏的最基本过程,就是气液两相充分接触,通过两相组分浓度差和温度差进行传质传热,使系统趋近于动平衡,这样,经过塔板多级接触,就能达到混合物组分的最大限度分离。 2、蒸馏方式 在炼油厂生产过程中,有多种形式蒸馏操作,但基本类型归纳起来主要有三种,即闪蒸、简单蒸馏和精馏 2.1闪蒸(平衡汽化) 加热液体混合物,达到一定的温度和压力,在一个容器的空间内,使之气化,气
高中生物 知识点考点解析含答案 植物有效成分的提取知识讲解
植物有效成分的提取 【学习目标】 1、掌握提取芳香油的基本原理。(重点、难点) 2、举例说出从生物材料中提取特定成分的过程。 3、明确提取胡萝卜素的基本原理。(重点) 4、掌握提取胡萝卜素的技术和纸层析法的操作方法。 【要点梳理】 要点一、植物芳香油的提取【高清课堂:植物有效成分的提取高清未发布课题1:基础知识】 1、基础知识 (1)植物芳香油的概念:是指用物理的方法从芳香植物(植物的花、叶、茎、根或果实)分离得到的高度挥发性的液态物质 (2)植物芳香油的化学成分:植物芳香油(精油)中最多的组分是萜类化合物及其衍生物, 还有其他成分,如酯类、醇类、醛类、酮类、酚类等有机物。 (3)植物芳香油的用途 ①香料: 用于化妆品、香水、肥皂 ②调味品:用于糕点、糖果、饮料等生产 ③药物:如清凉油 (4)植物芳香油的提取方法 提取方法提取原理适用精油特点 水蒸气蒸馏法(常用)利用水蒸气将挥发性强的植物芳香油携带 出来,形成油水混合物,冷却后分离油层和 水层 (水中、水上和水气蒸馏) 化学性质稳定、挥发性强、不溶于 水、易溶于有机溶剂 压榨法机械压榨, 从原料中榨出精油在水中蒸馏易导致原料焦糊或有效成分 被破坏,如柑橘、柠檬 萃取法将粉粹、干燥的植物原料用有机溶剂浸泡, 使芳香油溶解在有机溶剂中,再蒸出有机 溶剂 不适合用水蒸气蒸馏的原料 2、玫瑰精油的提取 (1)用途:是制作高级香水的主要成分。 (2)性质:化学性质稳定,难溶于水,易溶于有机溶剂,能随水蒸气一同蒸馏。 (3)方法:一般可采用水蒸气蒸馏法提取,同时根据其化学性质,也可采用萃取法提取 (4)流程:鲜玫瑰花+清水(1:4)→水蒸气蒸馏→油水混合物(加入NaCl)→分离油层(加入无水Na2SO4)→除水→过滤→玫瑰油 3、橘皮精油的提取 (1)性质:无色透明,具有诱人的橘香味 (2)成分:主要为柠檬烯。 性质:化学性质稳定,难溶于水,易溶于有机溶剂,能随水蒸气一同蒸馏。 (3)用途:是食品、化妆品和香水配料的优质原料 (4)方法:一般采用压榨法。 (5)流程:石灰水浸泡→漂洗→压榨→过滤→静置→再次过滤→橘皮油 要点诠释:
4.减压蒸馏方法
减压蒸馏 一、实验目的 1、学习减压蒸馏的原理及其应用。 2、掌握减压蒸馏装置的安装和操作技能。 二、实验操作、现象及注意事项 实验操作及现象现象的解释及注意事项 (1)将待蒸馏物质加入蒸馏烧瓶中,量不要超过蒸馏瓶的一半。安装减压蒸馏装置。仪器安装好后,先打开安全瓶上的活塞,使体系与大气相通,再适当旋紧毛细管上的螺旋夹。 (2)开启油泵抽气,慢慢关闭安全瓶上的二通活塞,同时注意观察压力计读数的变化。通过小心旋转安全瓶上的旋塞,使体系真空度调节至所需真空度。若从毛细管导入的气流太大,可适当调节毛细管上的螺旋夹,使液 减压蒸馏装置是由蒸馏装置、安全瓶、气体吸收装置、缓冲瓶及测压装置组成。蒸馏装置由蒸馏烧瓶、克氏蒸馏头、毛细管、温度计及冷凝管、真空接引管(燕尾管)及接受瓶组成。采用克氏蒸馏头可避免液体暴沸而冲入冷凝管;而从克氏蒸馏头直插蒸馏瓶底的是未端如细针般的毛细管,其作用是导入微空气流,使沸腾平稳,避免液体过热而发生暴沸。如果要进行微量减压蒸馏,可用磁搅拌子代替毛细管。在减压蒸溜过程中,开启磁力搅拌器,以保持平稳蒸馏。如果待蒸馏物对空气敏感,在磁力搅拌下减压蒸馏更合适。若仍使用毛细管,则应通过毛细管导入情性气体(如氮气)。毛细管口距瓶底约l~2mm。在毛细玻璃管上口套一段软橡皮管,橡皮管中插入一段铜丝,并用螺旋夹夹住,通过调节螺旋夹可控制导入的气流量。蒸出液接收部分,通常用多尾接液管连接两个或三个梨形或圆底烧瓶,在接收不同馏分时,只需转动接液管就可改换接受瓶接出不同的馏分。在减压蒸馏系统中切勿使用有裂缝或薄壁的玻璃仪器.尤其不能用不耐压的平底瓶(如锥形瓶等),以防止内向爆炸。抽气部分用减压泵抽气。最常用的减压泵有水泵和油泵两种。安全保护部分一般设有安全瓶,若使用油泵,还必须有冷阱及分别装有粒状氢氧化钠、块状石蜡及活性炭或硅胶、无水氯化钙等吸收干燥塔,以避免低沸点溶剂,特别是酸和水汽进入油泵而降低泵的真空效能和损坏真空泵。测压部分采用测压计。 用油泵减压蒸馏前必须在常压或水泵减压下蒸除所有低沸点液体和水以及酸、碱性气体。开油泵后,要注意观察压力计。如果发现体系压力无多大变化,或系统不能达到油泵应该达到的真空度,那么就该检查系统是否漏气。检查前先缓慢打开安全瓶的二通阀,待体系与大气相通,再将油泵关闭,然后分段查那些连接部位。如果是蒸溜装置漏气,可以在蒸馏装置的各个连接部位适当地涂一点真空油脂,并通过旋转仪器相互连接处使磨口处吻合致
常减压蒸馏装置操作参数十六大影响因素
常减压蒸馏装置操作参数十六大影响因素((十一)常压塔底液位 常压塔底液位发生变化,会影响常压塔底泵出口流量发生波动,如果减压炉没有及时调整火嘴的发热量,会导致减压炉出口温度波动,即为减压塔进料温度发生变化,这样会导致减压塔操作波动,严重时会使减压侧线产品质量指标不合格。所以,常压塔底液位稳定是减压系统平稳操作的前提条件。一般,常压塔底液位控制在50%±10%的范围内。常压塔底液位的影响因素有:常压塔进料量、常底泵出口流量、汽化率(进料温度、进料性质、侧线抽出量多少.塔底注汽量、塔顶压力)。 1.进料量 常压塔底进料量主要由初底油泵出口流量控制,进料量增大,则常压塔底液面将升高,进料量减小,则常压塔底液面将降低。但是,如果改变了初底泵出口的流量,会引起初馏塔底液位的变化,就需要调节原油泵出口流量,这是不可取的,所以,一般不会采取调节初馏塔底泵出口流量来调节常压塔底液位。 2.常底泵出口流量 常底泵出口流量增大,则常压塔底液面将降低;常底泵出口流量减小,则常压塔底液面将升高。但是在调节常底泵出口流量的同时,也要考虑减压系统的操作平稳性,常底泵出口流量波动,一定要提前做好减压炉的相关调节工作,如燃料油火嘴和燃料气火嘴阀门的开
度、炉膛负压等,以保证减压塔进料的温度稳定,进而稳定整个减压塔的操作稳定。 3.汽化率 常压塔的汽化率主要是指常顶气体、常顶汽油、常一线、常二线、常三线产品的产率总和。常压塔底的汽化率升高,即为常顶产品和常压侧线产品的产率增加,则常底液面将下降;汽化率降低,则说明本应该汽化并从侧线馏出的组分没有馏出而是留存在塔底,使得常底液面将升高。常压塔底汽化程度是常压塔底液位影响的很重要的因素。 (1)进料性质 保持常压塔底温度不变,进科中轻组分的比例增大,则汽化率将升高。反之,降低。保持常压塔底温度、塔顶温度和压力不变,如果进料密度变小,进料中轻组分的比例增大,则常顶产品产量将会增加,汽化率将升高。反之,降低。 常底进料密度变小,说明本应该在初馏塔汽化馏出的组分没有馏出,而是随初底原油一同进入到了常压塔,这些组分便会在常顶馏出,如果不考虑塔顶压力的影响因素,常底进料性质的变化一般不会影响常压侧线产品的产率。 (2)进料温度 进料温度会促进油分的汽化,温度升高,则汽化率将升高;反之,则降低。 常压塔底进料温度与常压炉的加热程度和原油三段换热终温有关,从初馏塔底至常压炉进口这一段原油的换热系统称为原油三段换
化学实验的基本方法──蒸馏、萃取和分液
一、考点突破 蒸馏、萃取和分液是物质分离的基本方法。这部分内容主要在选择题和夹杂于综合实验题中考查。本讲我们主要的学习目的是: 1. 掌握蒸馏的实验原理和操作技能。 2. 掌握萃取、分液的实验原理和操作技能。 3. 加深对物质分离和提纯的理解。 二、重难点提示 蒸馏与萃取的实验原理、操作方法和实验注意事项。 引入:地球上水的储量很大,但淡水只占总水量的2.5%,其中易供人类使用的淡水不足1%。 如何获得淡水资源? 一、海水淡化的原理——蒸馏
蒸馏:利用混合物中各组分的沸点不同,使低沸点组分蒸发,再冷凝,以分离整个组分的操作过程。 插入视频──蒸馏水的制取和石油的分馏 问题: ①温度计的作用和位置?(控温以显示加热范围,如:自来水蒸馏时温度≈100℃水银球在支管口处) ②产物收集方式?(冷凝收集) ③自来水蒸馏后蒸馏瓶内物质?(在100℃时难以挥发,不挥发的杂质) ④冷凝管中水流方向?(水从下口进,上口出) ⑤为什么加碎瓷片?(防暴沸) 想一想:对于互溶的液体,我们可以采用蒸馏的方法进行分离,如果分离油与水这种不互溶的液体,还能用蒸馏的方法进行分离吗? 插入视频—柴油和水的分离 二、用CCl4萃取碘水中的碘并分液 实验步骤: 1. 检验分液漏斗活塞和上口的玻璃塞是否漏液。
2. 把10毫升碘水和4毫升CCl4加入分液漏斗中,并盖好玻璃塞。 3. 倒转漏斗用力振荡,并不时旋开活塞放气,最后关闭活塞,把分液漏斗放正。 4. 把分液漏斗放在铁架台的铁圈中,静置,分层。 5. 将漏斗上口的玻璃塞打开(或使塞上的凹槽或小孔对准漏斗口上的小孔)。 6. 旋开活塞,用烧杯接收下层溶液。 7. 从分液漏斗上口倒出上层水溶液。 想一想: 1. 碘易溶于酒精,能否用酒精将碘水中的碘萃取出来? 2. 萃取之后用什么方法将有机溶剂与溶质进一步分离开来? 3. 试管中盛有已分层的有机溶剂和水的混合液,但不知道哪一层液体是“油层”。试设计一种简便的判断方法。 知识点1:蒸馏、萃取等实验基本操作 例题1 下列关于蒸馏操作的叙述,不正确的是() A. 蒸馏操作的主要仪器是:蒸馏烧瓶、酒精灯、铁架台、冷凝管、锥形瓶、牛角管、温度计等 B. 蒸馏操作使用的温度计的水银球应插入到液体内 C. 在蒸馏烧瓶内放入少量碎瓷片,目的是防止暴沸 D. 冷凝管进出水的方向是下口进、上口出 思路导航:蒸馏操作中,温度计的水银球在蒸馏烧瓶的支管口处,目的是为了测定馏分蒸气的温度,故B项错误。 答案:B 例题2 下列实验操作中错误的是() A. 使用分液漏斗分液时,应将漏斗颈上的玻璃塞打开 B. 蒸馏实验不一定使用温度计 C. 用CCl4萃取碘水中的碘 D. 过滤(如图)时,可将悬浊液从烧杯直接倒入漏斗中 思路导航:蒸馏实验并非一定需要温度计,如蒸馏水的制取;过滤时应将液体沿玻璃棒慢慢流入漏斗中,不可直接倾倒。 答案:D 例题3 实验室里从海藻中提取碘的流程图如下:
《蒸馏和萃取》教案
《蒸馏和萃取》教学教案 蒸发 利用沸点不同,沸点低的先汽化,在冷凝成液 体收集 物质提纯方法
2. 蒸馏的实验装置 【课件放映】在之前学过的过滤、蒸发操作当中有一些需要注意的地方,细节,同样在蒸馏的实验操作当中有哪些我们需要注意的呢? 气密性检查: 连接好装置,在冷凝器的出口处接一橡胶管,并将橡胶管插入水中,将烧瓶微热,水中有气泡产生,冷却到室温,橡胶管中有一段水柱,则气密性良好。 实验操作注意事项: ①在蒸馏烧瓶中放少量沸石或碎瓷片,防止液体暴沸。 ②温度计水银球的位置与支管口下端位于同一水平线上,用于测馏出物的沸点。 ③蒸馏烧瓶中所盛液体不能超过其容积的2 3,也不能少于1 3。 ④为了确保馏出的蒸气及时得到冷却,要先向冷凝管中通冷却水,然后才能加热。冷凝管中冷却水从下口进,从上口出,以使馏出物充分冷却。 ⑤加热温度不能超过混合物中沸点最高的物质的沸点。 ⑥蒸馏完毕,应先停止加热,然后停止通水、拆除仪器。拆除仪器的顺序和装配的顺序相反,先取下锥形瓶,然后拆下尾接管、冷凝管和蒸馏烧瓶。 几种新仪器的用途: ● 蒸馏烧瓶:用于液体蒸馏或分馏的仪器。 ● 直形冷凝管:主要用于沸点低于140℃的液体蒸馏、分馏操作。(高于140℃ 的一般用球形冷凝管,冷凝效果更好) ● 球形冷凝管:一般用于有机化合物的气体合成装置中的回流作用。 ● 尾接管:又名牛角管,通常和冷凝器配套使用,将蒸馏液导入承接容器。(比 导管内部接触面积大,冷凝效果好) 3. 习题 例题1、在蒸馏实验中,下列叙述不正确的是()
A. 在蒸馏烧瓶中盛约2 3体积的自来水,并放入几粒沸石 B. 将温度计水银球插入自来水中 C. 冷水从冷凝管下口入,上口出 D. 收集到的液体取少量滴入硝酸银和稀硝酸,无明显现象 例题2、已知丙酮(C 3H 6O)通常是无色液体,可溶于水,密度小于1 g/mL ,沸点约为56℃。要从水与丙酮的混合物里将丙酮分离出来,下列方法中,最合理的是( ) A .蒸馏 B .升华 C .过滤 D .蒸发 例题3、下列制取蒸馏水的实验装置与操作的说法中,不正确的是( ) A .温度计的水银球应插入蒸馏烧瓶中的自来水中 B .冷凝管中的水流方向是从下口进入,上口排出 C .实验中需要在蒸馏烧瓶中加入几粒碎瓷片,防止出现暴沸现象 D .蒸馏烧瓶必须垫石棉网 例题4、将下面实验操作注意事项填写完整 ①蒸馏烧瓶中的液体不得超过容积的,在加热时蒸馏烧瓶里面应放入 ,防止溶液。 ②冷凝管中冷却水从 口进,从口出。 ③蒸馏完毕,应先,再。 例题5、现有一瓶物质甲与乙的混合物,已知甲和乙的某些性质如下: 物质 化学式 熔点(℃) 沸点(℃) 密度(g/cm 3) 水中溶解性 甲 C 3H 6O 2 -98 57.5 0.93 可溶 乙 C 4H 8O 2 -84 77 0.90 可溶 据此,将甲和乙相互分离的最佳方法是什么?说出你的理由。 例题6、请简要叙述下图所示的实验装置、方法、操作中存在的错误。 4. 萃取的原理 a) 萃取:利用物质在互不相溶的溶剂里溶解度的不同,用一种溶剂把物质 从它与另一种溶剂所组成的溶液里提取出来。 b) 分液:将萃取以后两种互不相溶的液体分开的操作。 c) 萃取剂:用来进行萃取的溶剂。 d) 萃取剂的选择原则:与原溶剂互不相溶,更不能与溶质和原溶剂发生反 应;溶质在萃取剂中的溶解度远大于在原溶剂中的溶解度。 5. 萃取的实验装置 ①装液:将原溶液和萃取剂依次装入分液漏斗,盖好瓶塞。 ②振荡:用压住分液漏斗的口部,捏住活塞部分,把分液漏斗倒转过来用力振荡。 ③静置:把分液漏斗放在上,静置。 ④分液:待后,将打开,或使对准漏斗上的小空打开上活塞,再将分液漏斗下面的拧开,使下层液体慢慢沿烧杯内壁流下,上层液体从倒出。
减压蒸馏 附思考题
减压蒸馏 一、实验目的: (1)了解减压蒸馏的原理和应用范围。 (2)认识减压蒸馏的主要仪器设备。 (3)掌握减压蒸馏仪器的安装和操作方法。 二、减压蒸馏的意义 减压蒸馏是分离和提纯高沸点和性质不稳定的液体以及一些低熔点固体有机物的常用方法。 应用这一方法可将沸点高的物质以及在普通蒸馏时还没达到沸点温度就已分解,氧化或聚合的物质纯化。 三、减压蒸馏原理 已知液体的沸点是指它的蒸气压等于外界大气压时的温度。所以液体沸腾的温度是随外再压力的降低而降低的。因而用真空泵连接盛有液体的容器,使液体表面上的压力降低,即可降低液体的沸点。这种在较低压力下进行蒸馏的操作称为减压蒸馏,减压蒸馏时物质的沸点与压力有关。 获得沸点与蒸气压关系的方法: ①查文献手册,(见P209水的饱和蒸气压与沸点) ②经验关系式,压力每相差133.3Pa(1mmHg),沸点相差~1℃ ③压力—温度关系图查找:(图2-28) 四、减压蒸馏的装置 通常认为有四部分组成:蒸馏部分、安全保护装置、测压装置、抽气(减压)装置。 主要仪器设备:①双颈蒸馏烧瓶②接收器③吸收装置④压力计⑤安全瓶⑥减压泵 1.双颈蒸馏烧瓶或用克氏蒸馏头配园底烧瓶代替。(为什么要用双颈?)
其目的是为了避免减压蒸馏时瓶内液体由于沸腾而冲入冷凝管中,瓶的一颈中插入温度计,另一颈中插入一根距瓶底约1-2mm的末端拉成细丝的毛细管的玻管。毛细管的上端连有一段带螺旋夹的橡皮管,螺旋夹用以调节进入空气的量,使极少量的空气进入液体,呈微小气泡冒出,作为液体沸腾的气化中心,使蒸馏平稳进行,又起搅拌作用。 装上一端拉成毛细管的玻璃管的作用是什么? ①起沸腾中心作用,避免液体过热而产生暴沸溅跳现象,又起搅拌作用 ②调节进入瓶中的空气量调节压力 2.接受器 蒸馏150℃以下物质时接受瓶前应连接冷凝管冷却;若蒸馏不能中断或要分段接收馏出液时,要采用多头接液管。转动多尾接液管,就可使不同的馏分进入指定的接受器中。 3.吸收装置——目的保护减压设备(用水泵时可免除) 4.测压计:封闭式水银测压计:所读高度差即为系统压力 开口式水银测压计:所读高度差为真空度(h ?) 系统压力=760mmHg h - ? 5.安全瓶:缓冲调节压力保护装置及放气,安全瓶与减压泵和测压计相连。6.减压泵:有水泵和油泵两种。若不需要很低的压力时可用水泵,其抽空效率可达到1067~3333Pa(8~25mmHg),水泵所能抽到的最低压力,理论上相当于当时水温下的水蒸气压力。 五、操作方法 ①按图安装(使用循环水泵,免除吸收装置),磨口玻璃涂上真空脂(油) ②检查系统是否达到要求(是否漏气) ③加入蒸馏的液体(本实验用水练习操作) ④关上安全瓶活塞→先抽气→调节毛细管导入适量空气→加热蒸馏 ⑤蒸馏完毕:先去热源→放气(不能太快)→打开安全瓶活塞→关水泵 六、数据记录和处理