机械设计外文翻译英文原文1概要
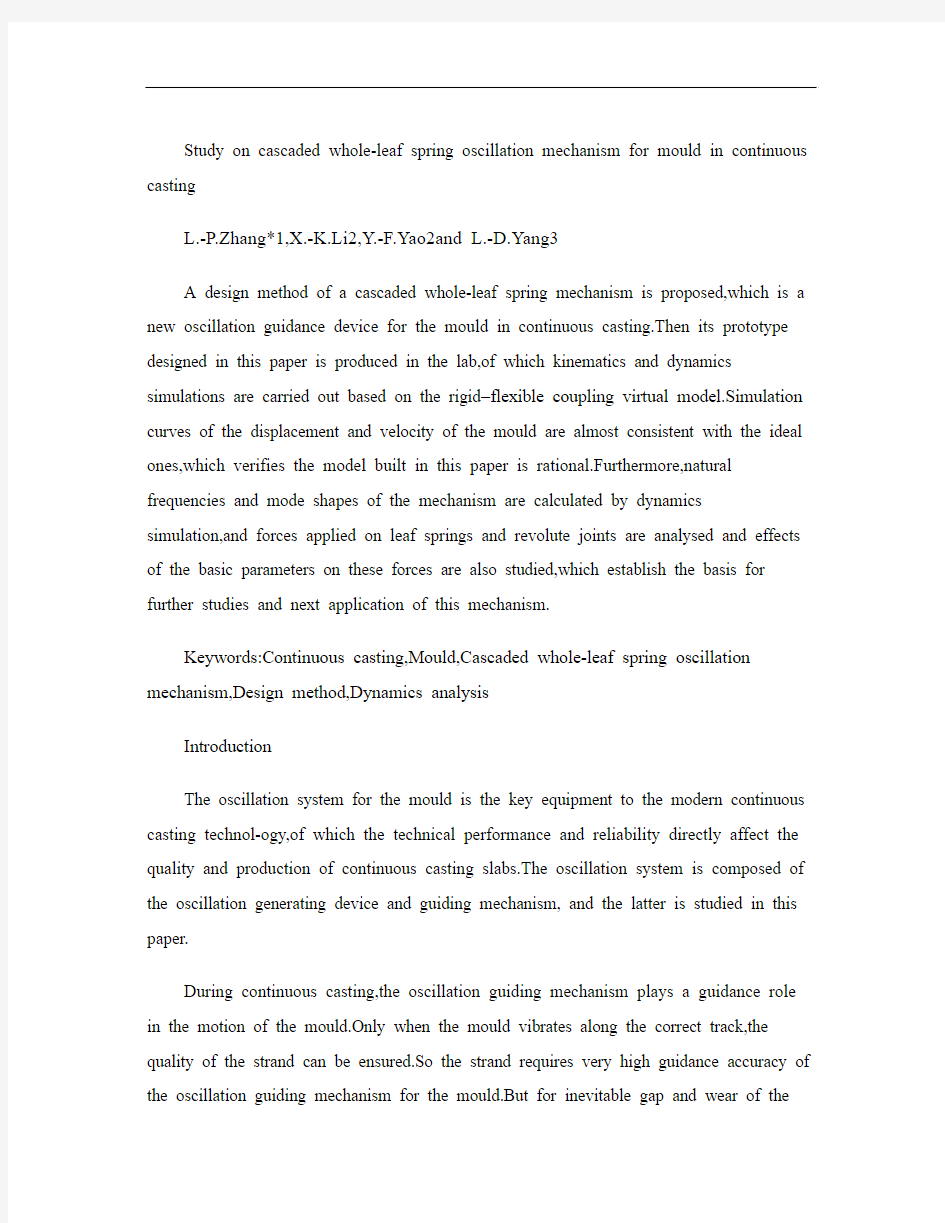

Study on cascaded whole-leaf spring oscillation mechanism for mould in continuous casting
L.-P.Zhang*1,X.-K.Li2,Y.-F.Yao2and L.-D.Yang3
A design method of a cascaded whole-leaf spring mechanism is proposed,which is a new oscillation guidance device for the mould in continuous casting.Then its prototype designed in this paper is produced in the lab,of which kinematics and dynamics simulations are carried out based on the rigid–flexible coupling virtual model.Simulation curves of the displacement and velocity of the mould are almost consistent with the ideal ones,which verifies the model built in this paper is rational.Furthermore,natural frequencies and mode shapes of the mechanism are calculated by dynamics simulation,and forces applied on leaf springs and revolute joints are analysed and effects of the basic parameters on these forces are also studied,which establish the basis for further studies and next application of this mechanism.
Keywords:Continuous casting,Mould,Cascaded whole-leaf spring oscillation mechanism,Design method,Dynamics analysis
Introduction
The oscillation system for the mould is the key equipment to the modern continuous casting technol-ogy,of which the technical performance and reliability directly affect the quality and production of continuous casting slabs.The oscillation system is composed of the oscillation generating device and guiding mechanism, and the latter is studied in this paper.
During continuous casting,the oscillation guiding mechanism plays a guidance role in the motion of the mould.Only when the mould vibrates along the correct track,the quality of the strand can be ensured.So the strand requires very high guidance accuracy of the oscillation guiding mechanism for the mould.But for inevitable gap and wear of the
bearings,the four-eccentric axes and four-bar linkage oscillation mechanisms widely used in modern casting will cause uncontrolled deviation in motions of the mould,which badly affects the quality of the strand.1Therefore,the semi-and whole-leaf spring mechanisms are gradually used as guidance mechanisms for the mould in billet and slab continuous casting.2,3In recent years,with further development of the semi-and whole-leaf spring oscilla-tion mechanisms,the cascaded whole-leaf spring oscilla-tion mechanism is developed abroad,4which has a longer life,higher lateral rigidity and reliability and so on.
However,until now,reports on this oscillation mechanism are few.5,6Its working principle has been proposed by the authors,7based on which design method of the cascaded whole-leaf spring oscillation mechanism is proposed in this paper and its experi-mental prototype is manufactured.Furthermore,the rigid–?exible coupling virtual model of the cascaded whole-leaf spring oscillation mechanism is built and its kinematics and dynamics simulations are analysed using many types of software,such as ANSYS.System modes and the forces applied on leaf springs and revolute joints of the mechanism are analysed,which establish the basis for further studies and application of this mechanism.
Working principle of cascaded whole-leaf spring guidance mechanism
The structure of the cascaded whole-leaf spring oscilla-tion mechanism is shown in Fig.1.It mainly consists of the cascaded leaf spring,vibration table and frame, which can be driven by machinery(Fig.1a,or hydraulics servo(Fig.1b,generating device of sinusoi-dal or non-sinusoidal oscillation.And the cascaded leaf spring is composed of four steel plate springs divided into two sets.All leaf springs’extension lines join to the circular ar c centre of the continuous caster and their ends are separately connected to the vibration table and the frame,as shown in Fig.2,and then two sets of leaf springs,the vibration table and the frame form two four-bar linkage guidance devices.During the mould vibrat-ing,?exible leaf springs produce elastic deformations, which make two leaf spring four-
bar linkage guidance devices alternately play a guidance role in the mould without any interference by the generating device.7
1The Mechatronics and Information Engineering School,Foshan
University,Foshan528000,China
2College of Mechanical Engineering,Yanshan University,Qinhuangdao 066004,China
3No.2Research Development Department,Xi’an Heavy Machinery Research Institute,Xi’an710032,China
*Corresponding author,email zhanglpok@https://www.360docs.net/doc/a81187293.html,
204?2010Institute of Materials,Minerals and Mining
Published by Maney on behalf of the Institute
Received14November2008;accepted16September2009
DOI10.1179/030192309X12573371383677Ironmaking and
Steelmaking2010VOL37NO3
Design of cascaded whole-leaf spring oscillation mechanism
From working principle of the cascaded whole-leaf spring oscillation mechanism,it can be seen that two leaf spring four-bar linkages carry on the guidance to the mould.If design is unreasonable,the motion of the two leaf spring four-bar linkages will interfere during vibration,which will block the mould.Therefore,how to design these two leaf spring four-bar linkages becomes the key problem.
Design method of cascaded whole-leaf spring oscillation mechanism
According to the characters of the cascaded whole-leaf spring mechanism developed from the short-arm four-bar linkage,its design method is proposed as following:(ibased on the design principles of the short-arm
four-bar linkage simulating arc,8design two rigid four-bar linkages under the same basic para-meters of the mould by optimum design,which fulfil the requirement for guiding accuracy of the mould simulating arc
(iifor settling interference of the two four-bar
linkages,rigid linkages optimised in step (iare substituted by steel plate springs with elastic deformation and then form two leaf spring four-bar linkages
(iiibased on the basic principles of the short-arm
four-bar linkage,arrange two leaf spring four-bar linkages according to Fig.2.That is,end-points A 1,C 1and A 2,C 2are fixed on the frame;endpoints B 1,D 1and B 2,D 2are connected to the vibration table of the mould.In this way,two leaf spring four-bar linkages are cascaded,so a cascaded whole-leaf spring mechanism is designed.
Calculation example
Calculations of parameters and guidance accuracy of rigid four-bar linkages
According to the geometry relations and the movement relationships of the four-bar linkage guidance devices of the arc caster (see Fig.2,the position of any point on the mould can be calculated during the mould vibration.In this paper,taken the bottom point E on the outer arc of the mould as an example,formulas of the track and the guiding accuracy of point E are deduced,as listed in Table 1,with only one rigid four-bar linkage guiding for the mould.
To calculate conveniently,it is assumed that l 1,l 2,l 3and l 4are respectively the lengths of linkages of A 1C 1,A 1B 1,B 1D 1and C 1D 1,and A 2C 2,A 2B 2,B 2D 2and
C 2
D 2;S is the amplitude of the mould;D Q is the swing angle of the linkage of B 1D
1and B 2D 2under the max displace-ment of the mould downward;R is the caster’s basic radius;R 1and R 2are radius respectively from the arc centre to two endpoints of linkages A 1C 1,B 1D 1,A 2C 2and B 2D 2;H 1and H 2are the heights of both sides to the horizontal centerline of the mould;a is the included angle between OE and the horizontal centreline of the arc caster when the mould is at equilibrium position;h 1,h 2,r 1and r 2are respectively the included angles between linkages of A 1C 1,A 2C 2,B 1D 1,B 2D 2and the horizontal centreline of the caster;D R E is the simulated arc error of the mould.
Mathematical model and optimisation of linkages
Oscillation parameters of the mould and the installation positions of linkages are the primary designing terms of the guidance mechanism.Taking arc caster for
example,outside penalty function optimisation method is adopted in optimum design of the two rigid four-bar linkages.In four-bar linkages design,it is the goal that the trajectory error of the mould meets the requirement for guiding accuracy.So the objective function of the optimisation mathematical model can be written by f(x ~D R E ~OE ’{R ?0:02
(1
According to Table 1,it can be seen that the design optimisation variables are x
~R ,S ,h ,r ,R 1,R 2? T
(2
By experience,geometric dimensions and installation positions of two four-bar linkages must meet the following
constraints
2Layout of cascaded whole-leaf
spring
a mechanic driven;
b hydraulics servodriven
1Cascaded whole-leaf spring oscillation mechanism
Zhang et al.Cascaded whole-leaf spring oscillation mechanism for mould in continuous casting
Ironmaking and Steelmaking 2010
VOL
37
NO
3205
30D ?R ?50D 2?S j j ?10R 1w 0,h w 0R 2w R 1,r w h 0:91R ?R 2v R 0:82R ?R
1?0:91R
(3
where D is the thickness of billet;h and r are included angles between linkages and horizontal centreline of the caster.Based on the objective function (equation
(1,optimisation variables (equation (2and constraints established in equation
(3,optimisation procedure of outside penalty function is compiled by C language and two four-bar linkages are separately optimum designed.
Optimisation results
In optimisation,it is assumed that the mould is arranged symmetrically about its equilibrium position and its height H 1z H 25900mm;the thickness of the billet D
5150mm;the guiding accuracies of two rigid four-bar linkages D R E
50?02mm.Therefore,the geometrical parameters and the guiding accuracies of the two rigid four-bar linkages are optimum designed (Table 2.By the optimised results,rigid linkages are substituted by leaf springs arranged according to Fig.2;then a cascaded whole-leaf spring mechanism is designed.
Experimental prototype of cascaded whole-leaf spring oscillation mechanism
Based on the optimised results,the experimental proto-type of the cascaded whole-leaf spring oscillation mechan-ism for the mould is manufactured,as shown in Fig.3,in which leaf spring four-bar linkage A 1C 1B 1D 1is composed of leaf springs 1and 4;and leaf spring four-bar linkage A 2C 2B 2D 2is made up of leaf springs 2and 3.Leaf spring four-bar linkages A 1C 1B 1D 1and A 2C 2B 2D 2are located at both sides of the mould in the vertical direction of casting.And parameters of the prototype are rounded numbers of Table 2and guidance accuracy is calculated after round-ing,as listed in Table 3.
Flexible multibody theory
Vectors of location,velocity and acceleration of point on flexible body
Based on the small deformation theory,complicated motion of the ?exible body can be decomposed to several
Table 2Optimised results of two rigid four-bar linkages
Four-bar linkage A 1B 1C 1D 1
Four-bar linkage A 2B 2C 2D 2R ,mm 5974.695902.74S,mm ?3.33?3.19h ,rad
0.050.08r ,rad 0.170.14R 1,mm 5219.795233.23R 2,mm 5490.995505.41
D R ,mm
20.02
0.
019
3Experimental prototype
Table 1Formulas of parameters of two rigid four-bar linkages and error of bottom point E on mould Four-bar linkage A 1B 1C 1D 1
Four-bar linkage A 2B 2C 2D 2
l 15l 35R 22R 1l 15l 35R 22R 1
a 5arcsin(H 2/R
a 5arcsin(H 2/R
D Q 52arcsin(S /2l 1cos r 1D Q 52arcsin(S /2l 1cos r 1l 252R 1sin[(r 12h 1/2]l 252R 1sin[(r 12h 1/2]l 452R 1sin[(r 12h 1/2]
l 452R 1sin[(r 22h 2/2]
D 1
E ~?R 2
2z R 2{2R 2R cos (r 1{a 1=2D 2E ~?R 2
1z R 2{2R 1R cos (r 2{a 1=2
C 1E ~?R 2
2z R 2{2R 2R cos (h 1{a 1=2
C 2E ~?R 2
1z R 2{2R 1R cos (h 2{a 1=2
A 1D 1’~f l 21z l 2
2z 2l 1l 2sin ?(r 1{h 1=2z D Q g 1=2
A 2D 2’~f l 21z l 2
2{2l 1l 2sin ?(r 2{h 2=2{D Q g 1=2
c ~arccos ?(l 2
4z D 1E 2{C 1E 2 (2l 4:D 1E
c ~arccos ?(l 2
4z D 2E 2{C 2E 2 (2l 4:D 2E
v ~arccos ?(l 24
z AD 1’2
{l 23.(2l 4:AD 1’ v ~arccos ?(l 24z AD 2’2
{l 2
3.(2l 4:AD 2’
b ~arccos ?(l 21z AD 1’2
{l 2
2.(2l 1:AD 1’
b ~arccos ?(l 21z AD 2’2
{l 2
2.(2l 1:AD 2’
OD 1’~?R 21
z l 2
1z 2R 1l 1cos D Q 1=2OD 2’~?R 22z l 21{2R 2l 1cos D Q 1=2 w ~arccos ?(OD 1’2
z l 21{R 2
1.(2OD 1’:l 1
w ~arccos ?(OD 2’2
z l 21{R 2
2.(2OD 2’:l 1
d 5w z c z v z b
d 5w z c 2(v z b
OE ’~?D 1E 2z OD 1’2
{2D 1E :OD 1’:cos d 1=2OE ’~?D 2E 2z OD ’22
{2D 2E :OD 2’:cos d 1=2D R E 5OE 92R D R E 5OE 92R
Table 3Parameters of prototype
Leaf spring four-bar linkage A 1B 1C 1D 1
Leaf spring four-bar linkage A 2B 2C 2D 2R ,mm 6000.006000.00S ,mm
?3.00?3.00h ,u 3.005.00r ,u 10.008.00R 1,mm 5220.005235.00R 2,mm 5490.005505.00
D R ,mm
20.016
0.018
Zhang et al.Cascaded whole-leaf spring oscillation mechanism for mould in continuous casting
206Ironmaking and Steelmaking 2010
VOL
37
NO
3
simple motions.So the location vector of any point on the ?exible body can be expressed as equation (4.9
r p ~r 0z A (s P z u P
(4
where A is the matrix of direction cosine;r P is the vector of point P in the inertial coordinate system;r 0is the vector of the origin of moving coordinate in the inertial coordinate system;s P is the vector of point P in moving coordinate system when the
?exible body is undeformed;and u P is the relative de?ec tion of point P expressed by modal coordinates namely u P 5W P q (where W P is the assumed modal matrix and q is the generalised coordinate of deformation.
Differentiating equation (4with respect to time,vectors of velocity and acceleration are calculated
:
r p ~:r 0z :A (s P z u P z A W P :q
::r p ~::r 0z ::A (s P z u P z 2:A W P :q z A W P ::
q
(5Flexible multibody dynamic equation
Considering the location,direction and mode of point P on the ?exible body,the generalised coordinate is selected,as in equation (6.
j ~x y z y h w q i (i ~1,:::,M ? T ~r y q ? T
(6
The motion equation of ?exible body is deduced from d L L
: {L L z l L y T {Q ~0
y ~08><>:
(7where y is restraint equation;l is Lagrange multiplier corresponding to restraint equation;Q is generalised force projected to generalised coordinate j ;L is Lagrange item with L 5T 2W ,and T and W respectively denote kinetic energy and potential energy.
The kinetic energy of ?exible body is calculated by T ~12
:
j T M (j :j
(8
where M (j is mass matrix and M (j ~M tt M tr M tm M T tr M rr
M rm M T tm M T
rm M mm
2
435;subscripts t ,r and m respectively denote translation,revolution and modal freedom.
The potential energy of ?exible body includes the gravitational potential energy and the elastic potential energy,that is
W ~W g (j z 1
2
j T K j
(9where K is generalised stiffness matrix corresponding to modal coordinates and is a constant.
Because the mass of the ?exible leaf springs is very small comparing to other parts of the oscillation mechanism with cascaded whole-leaf spring,its potential energy could be ignored.So substituting equations (8and (9into equation (7,differential equation of motion of the ?exible body is written as follows M ::j z :M :j {
12L M L j :j T :j z K j z l L y L j
j
T
~Q (10
Kinematics simulation of cascaded
whole-leaf spring oscillation mechanism
Based on the ?exible multibody theory,the virtual design and then kinematics simulation of the experi-mental prototype of the cascaded whole-leaf spring oscillation
mechanism for the mould with non-sinusoi-dal oscillation are carried out using many types of softwares,such as ANSYS,10,11and curves of displace-ment and velocity of the mould are obtained and compared with the ideal ones.
Simulation model
Based on the structural characteristic of the cascaded whole-leaf spring oscillation mechanism,it is assumed as follows:
(ithe vibration table is symmetric about x –y plane
and direction of –y is the casting direction,with the coordinate as shown in Fig.4
(iileaf springs with elastic deformation are regarded
as flexible bodies.Eccentric shaft,connecting rod,vibration table and frame with big stiffness are taken for rigid bodies.
So the simulation model of the experimental prototype is built,in which leaf springs 1and 4are composed of two groups of leaf spring four-bar linkage A 1C 1B 1D 1;and leaf springs 2and 3are formed by two groups of leaf spring four-bar linkage A 2C 2B 2D
2(Fig.4.
Kinematics simulation and results
To simulate the actual non-sinusoidal motion law of the
mould with the guidance of the cascaded whole-leaf spring mechanism,a non-uniform rotational speed is imposed on the eccentric shaft,as shown in Fig.4,in which the frequency f 52Hz,the de?ection ratio of oscillation a 530%and the amplitude of the mould h 53mm.
The displacement and velocity curves of the vibration table (i.e.movement curves of the mouldare shown in Fig.5,of which the errors compared with the ideal curves are shown in Fig.6.
From Fig.5,it can be seen the virtual vibration table can move along the given non-sinusoidal rule.Although the oscillation waveform of the mould in simulation has error compared with the ideal curves (Fig.6,the maximum errors of the displacement and the velocity are very small (0?0068mm and 0?1287mm s 21respec-tively,and can be ignored.Therefore,it is concluded that the virtual model is rational and can be used
for
4Simulating model
Zhang et al.Cascaded whole-leaf spring oscillation mechanism for mould in continuous casting
Ironmaking and Steelmaking 2010
VOL
37
NO
3207
further study on the cascaded whole-leaf spring mechanism.
Dynamics simulation of oscillation mechanism
Based on the dynamic simulation of the cascaded whole-leaf spring oscillation mechanism,system modal and the forces applied on leaf springs and revolute joints are analysed.
Modal analysis of oscillation mechanism
Using the instantaneous freezing method of mechan-ism,12modal analysis of the cascaded whole-leaf spring
guidance mechanism is carried out,from which system modals and natural frequencies are obtained.For the frequency of non-sinusoidal oscillation in continuous casting is not very high,13natural frequencies and mode shapes from the ?rst to the ?fth are emphasised in this paper with related information of the modals listed in Table
4.Limited by space,only the ?rst to th e third mode shapes are shown in Fig.7.
From modal analysis of the mechanism above,it is known that the ?rst and the second natural frequencies are lower and resonance may occur on the mould in continuous casting.14When resonance occurs,the mould will de?e ct from the correct trajectory,which badly impacts on the quality of strand.So it must be ensured that the working frequency in continuous casting is far from the ?rst and the second natural frequencies of the cascaded whole-leaf spring oscillation mechanism.
Analysis of forces applied on leaf springs
Owing to the symmetry about the x –y plane,leaf springs in both sides of the cascade whole-leaf spring oscillation mechanism have the same forces and deformations,only the one at the positive axis of z is analysed.For the cascade whole-leaf spring mechanism,leaf
spring four-bar linkage A 1C 1B 1D 1and A 2C 2B 2D 2alternately play the guidance role on the mould and forces applied on the leaf spring and their deformations are very complicated.So it is dif?cult to analyse leaf springs well only by experiments and computer simulation has important signi?cance.In this paper,based on the virtual proto-type technology,dynamics simulation is carried out,by which forces curves of leaf springs are obtained during the mould movement.Furthermore,effects of basic oscillation parameters on these forces are analysed,which establish the basis for further study on the reliability of the
mechanism.
5a displacement and b velocity curves of vibration
table
Table 4Natural frequ encies and modes shapes from ?rst to ?fth order Modality order Natural frequency,Hz Mode shapes
172058Vertical vibration of the vibration table along the casting direction (–y 211.4723Deviated swing of the vibration table about the axis of x 323.7038Vibration of leaf spring 1
423.70685
24.0872
Transverse vibration of the vibration table along the z axis z vibration of leaf spring
冲压模具技术外文翻译(含外文文献)
前言 在目前激烈的市场竞争中,产品投入市场的迟早往往是成败的关键。模具是高质量、高效率的产品生产工具,模具开发周期占整个产品开发周期的主要部分。因此客户对模具开发周期要求越来越短,不少客户把模具的交货期放在第一位置,然后才是质量和价格。因此,如何在保证质量、控制成本的前提下加工模具是值得认真考虑的问题。模具加工工艺是一项先进的制造工艺,已成为重要发展方向,在航空航天、汽车、机械等各行业得到越来越广泛的应用。模具加工技术,可以提高制造业的综合效益和竞争力。研究和建立模具工艺数据库,为生产企业提供迫切需要的高速切削加工数据,对推广高速切削加工技术具有非常重要的意义。本文的主要目标就是构建一个冲压模具工艺过程,将模具制造企业在实际生产中结合刀具、工件、机床与企业自身的实际情况积累得高速切削加工实例、工艺参数和经验等数据有选择地存储到高速切削数据库中,不但可以节省大量的人力、物力、财力,而且可以指导高速加工生产实践,达到提高加工效率,降低刀具费用,获得更高的经济效益。 1.冲压的概念、特点及应用 冲压是利用安装在冲压设备(主要是压力机)上的模具对材料施加压力,使其产生分离或塑性变形,从而获得所需零件(俗称冲压或冲压件)的一种压力加工方法。冲压通常是在常温下对材料进行冷变形加工,且主要采用板料来加工成所需零件,所以也叫冷冲压或板料冲压。冲压是材料压力加工或塑性加工的主要方法之一,隶属于材料成型工程术。 冲压所使用的模具称为冲压模具,简称冲模。冲模是将材料(金属或非金属)批量加工成所需冲件的专用工具。冲模在冲压中至关重要,没有符合要求的冲模,批量冲压生产就难以进行;没有先进的冲模,先进的冲压工艺就无法实现。冲压工艺与模具、冲压设备和冲压材料构成冲压加工的三要素,只有它们相互结合才能得出冲压件。 与机械加工及塑性加工的其它方法相比,冲压加工无论在技术方面还是经济方面都具有许多独特的优点,主要表现如下; (1) 冲压加工的生产效率高,且操作方便,易于实现机械化与自动化。这是
外文翻译
Load and Ultimate Moment of Prestressed Concrete Action Under Overload-Cracking Load It has been shown that a variation in the external load acting on a prestressed beam results in a change in the location of the pressure line for beams in the elastic range.This is a fundamental principle of prestressed construction.In a normal prestressed beam,this shift in the location of the pressure line continues at a relatively uniform rate,as the external load is increased,to the point where cracks develop in the tension fiber.After the cracking load has been exceeded,the rate of movement in the pressure line decreases as additional load is applied,and a significant increase in the stress in the prestressing tendon and the resultant concrete force begins to take place.This change in the action of the internal moment continues until all movement of the pressure line ceases.The moment caused by loads that are applied thereafter is offset entirely by a corresponding and proportional change in the internal forces,just as in reinforced-concrete construction.This fact,that the load in the elastic range and the plastic range is carried by actions that are fundamentally different,is very significant and renders strength computations essential for all designs in order to ensure that adequate safety factors exist.This is true even though the stresses in the elastic range may conform to a recognized elastic design criterion. It should be noted that the load deflection curve is close to a straight line up to the cracking load and that the curve becomes progressively more curved as the load is increased above the cracking load.The curvature of the load-deflection curve for loads over the cracking load is due to the change in the basic internal resisting moment action that counteracts the applied loads,as described above,as well as to plastic strains that begin to take place in the steel and the concrete when stressed to high levels. In some structures it may be essential that the flexural members remain crack free even under significant overloads.This may be due to the structures’being exposed to exceptionally corrosive atmospheres during their useful life.In designing prestressed members to be used in special structures of this type,it may be necessary to compute the load that causes cracking of the tensile flange,in order to ensure that adequate safety against cracking is provided by the design.The computation of the moment that will cause cracking is also necessary to ensure compliance with some design criteria. Many tests have demonstrated that the load-deflection curves of prestressed beams are approximately linear up to and slightly in excess of the load that causes the first cracks in the tensile flange.(The linearity is a function of the rate at which the load is applied.)For this reason,normal elastic-design relationships can be used in computing the cracking load by simply determining the load that results in a net tensile stress in the tensile flange(prestress minus the effects of the applied loads)that is equal to the tensile strength of the concrete.It is customary to assume that the flexural tensile strength of the concrete is equal to the modulus of rupture of the
机械专业毕业论文外文翻译
附录一英文科技文献翻译 英文原文: Experimental investigation of laser surface textured parallel thrust bearings Performance enhancements by laser surface texturing (LST) of parallel-thrust bearings is experimentally investigated. Test results are compared with a theoretical model and good correlation is found over the relevant operating conditions. A compari- son of the performance of unidirectional and bi-directional partial-LST bearings with that of a baseline, untextured bearing is presented showing the bene?ts of LST in terms of increased clearance and reduced friction. KEY WORDS: ?uid ?lm bearings, slider bearings, surface texturing 1. Introduction The classical theory of hydrodynamic lubrication yields linear (Couette) velocity distribution with zero pressure gradients between smooth parallel surfaces under steady-state sliding. This results in an unstable hydrodynamic ?lm that would collapse under any external force acting normal to the surfaces. However, experience shows that stable lubricating ?lms can develop between parallel sliding surfaces, generally because of some mechanism that relaxes one or more of the assumptions of the classical theory. A stable ?uid ?lm with su?cient load-carrying capacity in parallel sliding surfaces can be obtained, for example, with macro or micro surface structure of di?erent types. These include waviness [1] and protruding microasperities [2–4]. A good literature review on the subject can be found in Ref. [5]. More recently, laser surface texturing (LST) [6–8], as well as inlet roughening by longitudinal or transverse grooves [9] were suggested to provide load capacity in parallel sliding. The inlet roughness concept of Tonder [9] is based on ??e?ective clearance‘‘ reduction in the sliding direction and in this respect it is identical to the par- tial-LST concept described in ref. [10] for generating hydrostatic e?ect in high-pressure mechanical seals. Very recently Wang et al. [11] demonstrated experimentally a doubling of the load-carrying capacity for the surface- texture design by reactive ion etching of SiC
毕业设计外文翻译资料
外文出处: 《Exploiting Software How to Break Code》By Greg Hoglund, Gary McGraw Publisher : Addison Wesley Pub Date : February 17, 2004 ISBN : 0-201-78695-8 译文标题: JDBC接口技术 译文: JDBC是一种可用于执行SQL语句的JavaAPI(ApplicationProgrammingInterface应用程序设计接口)。它由一些Java语言编写的类和界面组成。JDBC为数据库应用开发人员、数据库前台工具开发人员提供了一种标准的应用程序设计接口,使开发人员可以用纯Java语言编写完整的数据库应用程序。 一、ODBC到JDBC的发展历程 说到JDBC,很容易让人联想到另一个十分熟悉的字眼“ODBC”。它们之间有没有联系呢?如果有,那么它们之间又是怎样的关系呢? ODBC是OpenDatabaseConnectivity的英文简写。它是一种用来在相关或不相关的数据库管理系统(DBMS)中存取数据的,用C语言实现的,标准应用程序数据接口。通过ODBCAPI,应用程序可以存取保存在多种不同数据库管理系统(DBMS)中的数据,而不论每个DBMS使用了何种数据存储格式和编程接口。 1.ODBC的结构模型 ODBC的结构包括四个主要部分:应用程序接口、驱动器管理器、数据库驱动器和数据源。应用程序接口:屏蔽不同的ODBC数据库驱动器之间函数调用的差别,为用户提供统一的SQL编程接口。 驱动器管理器:为应用程序装载数据库驱动器。 数据库驱动器:实现ODBC的函数调用,提供对特定数据源的SQL请求。如果需要,数据库驱动器将修改应用程序的请求,使得请求符合相关的DBMS所支持的文法。 数据源:由用户想要存取的数据以及与它相关的操作系统、DBMS和用于访问DBMS的网络平台组成。 虽然ODBC驱动器管理器的主要目的是加载数据库驱动器,以便ODBC函数调用,但是数据库驱动器本身也执行ODBC函数调用,并与数据库相互配合。因此当应用系统发出调用与数据源进行连接时,数据库驱动器能管理通信协议。当建立起与数据源的连接时,数据库驱动器便能处理应用系统向DBMS发出的请求,对分析或发自数据源的设计进行必要的翻译,并将结果返回给应用系统。 2.JDBC的诞生 自从Java语言于1995年5月正式公布以来,Java风靡全球。出现大量的用java语言编写的程序,其中也包括数据库应用程序。由于没有一个Java语言的API,编程人员不得不在Java程序中加入C语言的ODBC函数调用。这就使很多Java的优秀特性无法充分发挥,比如平台无关性、面向对象特性等。随着越来越多的编程人员对Java语言的日益喜爱,越来越多的公司在Java程序开发上投入的精力日益增加,对java语言接口的访问数据库的API 的要求越来越强烈。也由于ODBC的有其不足之处,比如它并不容易使用,没有面向对象的特性等等,SUN公司决定开发一Java语言为接口的数据库应用程序开发接口。在JDK1.x 版本中,JDBC只是一个可选部件,到了JDK1.1公布时,SQL类包(也就是JDBCAPI)
机器人外文翻译
英文原文出自《Advanced Technology Libraries》2008年第5期 Robot Robot is a type of mechantronics equipment which synthesizes the last research achievement of engine and precision engine, micro-electronics and computer, automation control and drive, sensor and message dispose and artificial intelligence and so on. With the development of economic and the demand for automation control, robot technology is developed quickly and all types of the robots products are come into being. The practicality use of robot products not only solves the problems which are difficult to operate for human being, but also advances the industrial automation program. At present, the research and development of robot involves several kinds of technology and the robot system configuration is so complex that the cost at large is high which to a certain extent limit the robot abroad use. To development economic practicality and high reliability robot system will be value to robot social application and economy development. With the rapid progress with the control economy and expanding of the modern cities, the let of sewage is increasing quickly: With the development of modern technology and the enhancement of consciousness about environment reserve, more and more people realized the importance and urgent of sewage disposal. Active bacteria method is an effective technique for sewage disposal,The lacunaris plastic is an effective basement for active bacteria adhesion for sewage disposal. The abundance requirement for lacunaris plastic makes it is a consequent for the plastic producing with automation and high productivity. Therefore, it is very necessary to design a manipulator that can automatically fulfill the plastic holding. With the analysis of the problems in the design of the plastic holding manipulator and synthesizing the robot research and development condition in recent years, a economic scheme is concluded on the basis of the analysis of mechanical configuration, transform system, drive device and control system and guided by the idea of the characteristic and complex of mechanical configuration,
机械设计外文翻译(中英文)
机械设计理论 机械设计是一门通过设计新产品或者改进老产品来满足人类需求的应用技术科学。它涉及工程技术的各个领域,主要研究产品的尺寸、形状和详细结构的基本构思,还要研究产品在制造、销售和使用等方面的问题。 进行各种机械设计工作的人员通常被称为设计人员或者机械设计工程师。机械设计是一项创造性的工作。设计工程师不仅在工作上要有创造性,还必须在机械制图、运动学、工程材料、材料力学和机械制造工艺学等方面具有深厚的基础知识。如前所诉,机械设计的目的是生产能够满足人类需求的产品。发明、发现和科技知识本身并不一定能给人类带来好处,只有当它们被应用在产品上才能产生效益。因而,应该认识到在一个特定的产品进行设计之前,必须先确定人们是否需要这种产品。 应当把机械设计看成是机械设计人员运用创造性的才能进行产品设计、系统分析和制定产品的制造工艺学的一个良机。掌握工程基础知识要比熟记一些数据和公式更为重要。仅仅使用数据和公式是不足以在一个好的设计中做出所需的全部决定的。另一方面,应该认真精确的进行所有运算。例如,即使将一个小数点的位置放错,也会使正确的设计变成错误的。 一个好的设计人员应该勇于提出新的想法,而且愿意承担一定的风险,当新的方法不适用时,就使用原来的方法。因此,设计人员必须要有耐心,因为所花费的时间和努力并不能保证带来成功。一个全新的设计,要求屏弃许多陈旧的,为人们所熟知的方法。由于许多人墨守成规,这样做并不是一件容易的事。一位机械设计师应该不断地探索改进现有的产品的方法,在此过程中应该认真选择原有的、经过验证的设计原理,将其与未经过验证的新观念结合起来。 新设计本身会有许多缺陷和未能预料的问题发生,只有当这些缺陷和问题被解决之后,才能体现出新产品的优越性。因此,一个性能优越的产品诞生的同时,也伴随着较高的风险。应该强调的是,如果设计本身不要求采用全新的方法,就没有必要仅仅为了变革的目的而采用新方法。 在设计的初始阶段,应该允许设计人员充分发挥创造性,不受各种约束。即使产生了许多不切实际的想法,也会在设计的早期,即绘制图纸之前被改正掉。只有这样,才不致于堵塞创新的思路。通常,要提出几套设计方案,然后加以比较。很有可能在最后选定的方案中,采用了某些未被接受的方案中的一些想法。
机械类毕业设计外文翻译
本科毕业论文(设计) 外文翻译 学院:机电工程学院 专业:机械工程及自动化 姓名:高峰 指导教师:李延胜 2011年05 月10日 教育部办公厅 Failure Analysis,Dimensional Determination And
Analysis,Applications Of Cams INTRODUCTION It is absolutely essential that a design engineer know how and why parts fail so that reliable machines that require minimum maintenance can be designed.Sometimes a failure can be serious,such as when a tire blows out on an automobile traveling at high speed.On the other hand,a failure may be no more than a nuisance.An example is the loosening of the radiator hose in an automobile cooling system.The consequence of this latter failure is usually the loss of some radiator coolant,a condition that is readily detected and corrected.The type of load a part absorbs is just as significant as the magnitude.Generally speaking,dynamic loads with direction reversals cause greater difficulty than static loads,and therefore,fatigue strength must be considered.Another concern is whether the material is ductile or brittle.For example,brittle materials are considered to be unacceptable where fatigue is involved. Many people mistakingly interpret the word failure to mean the actual breakage of a part.However,a design engineer must consider a broader understanding of what appreciable deformation occurs.A ductile material,however will deform a large amount prior to rupture.Excessive deformation,without fracture,may cause a machine to fail because the deformed part interferes with a moving second part.Therefore,a part fails(even if it has not physically broken)whenever it no longer fulfills its required function.Sometimes failure may be due to abnormal friction or vibration between two mating parts.Failure also may be due to a phenomenon called creep,which is the plastic flow of a material under load at elevated temperatures.In addition,the actual shape of a part may be responsible for failure.For example,stress concentrations due to sudden changes in contour must be taken into account.Evaluation of stress considerations is especially important when there are dynamic loads with direction reversals and the material is not very ductile. In general,the design engineer must consider all possible modes of failure,which include the following. ——Stress ——Deformation ——Wear ——Corrosion ——Vibration ——Environmental damage ——Loosening of fastening devices
毕业设计外文翻译附原文
外文翻译 专业机械设计制造及其自动化学生姓名刘链柱 班级机制111 学号1110101102 指导教师葛友华
外文资料名称: Design and performance evaluation of vacuum cleaners using cyclone technology 外文资料出处:Korean J. Chem. Eng., 23(6), (用外文写) 925-930 (2006) 附件: 1.外文资料翻译译文 2.外文原文
应用旋风技术真空吸尘器的设计和性能介绍 吉尔泰金,洪城铱昌,宰瑾李, 刘链柱译 摘要:旋风型分离器技术用于真空吸尘器 - 轴向进流旋风和切向进气道流旋风有效地收集粉尘和降低压力降已被实验研究。优化设计等因素作为集尘效率,压降,并切成尺寸被粒度对应于分级收集的50%的效率进行了研究。颗粒切成大小降低入口面积,体直径,减小涡取景器直径的旋风。切向入口的双流量气旋具有良好的性能考虑的350毫米汞柱的低压降和为1.5μm的质量中位直径在1米3的流量的截止尺寸。一使用切向入口的双流量旋风吸尘器示出了势是一种有效的方法,用于收集在家庭中产生的粉尘。 摘要及关键词:吸尘器; 粉尘; 旋风分离器 引言 我们这个时代的很大一部分都花在了房子,工作场所,或其他建筑,因此,室内空间应该是既舒适情绪和卫生。但室内空气中含有超过室外空气因气密性的二次污染物,毒物,食品气味。这是通过使用产生在建筑中的新材料和设备。真空吸尘器为代表的家电去除有害物质从地板到地毯所用的商用真空吸尘器房子由纸过滤,预过滤器和排气过滤器通过洁净的空气排放到大气中。虽然真空吸尘器是方便在使用中,吸入压力下降说唱空转成比例地清洗的时间,以及纸过滤器也应定期更换,由于压力下降,气味和细菌通过纸过滤器内的残留粉尘。 图1示出了大气气溶胶的粒度分布通常是双峰形,在粗颗粒(>2.0微米)模式为主要的外部来源,如风吹尘,海盐喷雾,火山,从工厂直接排放和车辆废气排放,以及那些在细颗粒模式包括燃烧或光化学反应。表1显示模式,典型的大气航空的直径和质量浓度溶胶被许多研究者测量。精细模式在0.18?0.36 在5.7到25微米尺寸范围微米尺寸范围。质量浓度为2?205微克,可直接在大气气溶胶和 3.85至36.3μg/m3柴油气溶胶。
机械手外文翻译 修改版
密级 分类号 编号 成绩 本科生毕业设计 (论文) 外文翻译 原文标题Simple Manipulator And The Control Of It 译文标题简易机械手及控制 作者所在系别机械工程系 作者所在专业xxxxx 作者所在班级xxxxxxxx 作者姓名xxxx 作者学号xxxxxx 指导教师姓名xxxxxx 指导教师职称副教授 完成时间2012 年02 月 北华航天工业学院教务处制
译文标题简易机械手及控制 原文标题 Simple Manipulator And The Control Of It 作者机电之家译名JDZJ国籍中国 原文出处机电之家 中文译文: 简易机械手及控制 随着社会生产不断进步和人们生活节奏不断加快,人们对生产效率也不断提出新要求。由于微电子技术和计算软、硬件技术的迅猛发展和现代控制理论的不断完善,使机械手技术快速发展,其中气动机械手系统由于其介质来源简便以及不污染环境、组件价格低廉、维修方便和系统安全可靠等特点,已渗透到工业领域的各个部门,在工业发展中占有重要地位。本文讲述的气动机械手有气控机械手、XY轴丝杠组、转盘机构、旋转基座等机械部分组成。主要作用是完成机械部件的搬运工作,能放置在各种不同的生产线或物流流水线中,使零件搬运、货物运输更快捷、便利。 一.四轴联动简易机械手的结构及动作过程 机械手结构如下图1所示,有气控机械手(1)、XY轴丝杠组(2)、转盘机构(3)、旋转基座(4)等组成。 图1.机械手结构 其运动控制方式为:(1)由伺服电机驱动可旋转角度为360°的气控机械手(有光电传感器确定起始0点);(2)由步进电机驱动丝杠组件使机械手沿X、Y轴移动(有x、y轴限位开关);(3)可回旋360°的转盘机构能带动机械手及丝杠组自由旋转(其电气拖动部分由直流电动机、光电编码器、接近开关等组成);(4)旋转基座主要支撑以上3部分;(5)气控机械手的张合由气压控制(充气时机械手抓紧,放气时机械手松开)。 其工作过程为:当货物到达时,机械手系统开始动作;步进电机控制开始向下
机械类外文翻译
机械类外文翻译 塑料注塑模具浇口优化 摘要:用单注塑模具浇口位置的优化方法,本文论述。该闸门优化设计的目的是最大限度地减少注塑件翘曲变形,翘曲,是因为对大多数注塑成型质量问题的关键,而这是受了很大的部分浇口位置。特征翘曲定义为最大位移的功能表面到表面的特征描述零件翘曲预测长度比。结合的优化与数值模拟技术,以找出最佳浇口位置,其中模拟armealing算法用于搜索最优。最后,通过实例讨论的文件,它可以得出结论,该方法是有效的。 注塑模具、浇口位臵、优化、特征翘曲变形关键词: 简介 塑料注射成型是一种广泛使用的,但非常复杂的生产的塑料产品,尤其是具有高生产的要求,严密性,以及大量的各种复杂形状的有效方法。质量ofinjection 成型零件是塑料材料,零件几何形状,模具结构和工艺条件的函数。注塑模具的一个最重要的部分主要是以下三个组件集:蛀牙,盖茨和亚军,和冷却系统。拉米夫定、Seow(2000)、金和拉米夫定(2002) 通过改变部分的尼斯达到平衡的腔壁厚度。在平衡型腔充填过程提供了一种均匀分布压力和透射电镜,可以极大地减少高温的翘曲变形的部分~但仅仅是腔平衡的一个重要影响因素的一部分。cially Espe,部分有其功能上的要求,其厚度通常不应该变化。 pointview注塑模具设计的重点是一门的大小和位臵,以及流道系统的大小和布局。大门的大小和转轮布局通常被认定为常量。相对而言,浇口位臵与水口大小布局也更加灵活,可以根据不同的零件的质量。 李和吉姆(姚开屏,1996a)称利用优化流道和尺寸来平衡多流道系统为multiple 注射系统。转轮平衡被形容为入口压力的差异为一多型腔模具用相同的蛀牙,也存
引进外资外文翻译资料
河南科技学院新科学院 2013届本科毕业生论文(设计) 英文文献及翻译 Foreign capital inflows and welfare in an economy with imperfect competition 学生姓名:王艳杰 所在院系:经济系 所学专业:国际经济与贸易 导师姓名:侯黎杰 完成时间:2013年4月15日
Foreign capital inflows and welfare in an economy with imperfect competition Abstract:This paper examines the resource allocational and welfare effects of exogenous inflows of foreign capital in a general-equilibrium model with oligopolistic competition and unemployment. Although the welfare impact for the short run is ambiguous and dependent upon the strength of excess profits and scale economies relative to unemployment in manufacturing, in the long run additional inflows of foreign capital always improve national welfare with capital mobility. Hence, attracting foreign capital remains a sound policy for economies characterized by imperfect competition, scale economies,and regional unemployment. Keywords: International capital mobility; Imperfect competition; Welfare 1.Introduction The welfare effects of exogenous inflows of foreign capital in the presence of trade restrictions have been extensively studied. Brecher and Diaz Alejandro (1977) show that when imports are subject to tariffs, an introduction of fo reign capital inflows accentuates the tariff distortion and hence reduces national welfare if the import-competing sector is relatively capital-intensive. In contrast, Dei (1985) shows that when imports are restricted by quotas,foreign capital inflows in the presence of foreign-owned capital always improve welfare by depressing the rental and so lowering the payments to existing foreign-owned capital. Recently, Neary (1981), using a common framework for both tariffs and quotas, obtains more general results of foreign capital inflows; the welfare effect of such inflows depends crucially on whether foreign-owned capital exists initially in the home country. In addition, Khan (1982) and Grinols (1991) have examined the effects of foreign capital inflows for a generalized Harris-Todaro economy under tariff protection. Khan finds that the result by Brecher and Diaz Alejandro is still valid even in the presence of unemployment, whereas Grinols argues that increased foreign capital need not be detrimental to welfare if the opportunity costs of labor are sufficiently low. Noteworthy is that the models used by these authors are all based upon the premise of perfect competition along with constant returns-to-scale technology. Although perfect competition serves as a useful assumption in crystallizing theoretical insights, it nevertheless fails to depict many of the real-world phenomena. The real-world economy is characterized, to a large extent, by imperfect competition and economies of scale. The policy implications of imperfect competition and economies