罩式退火炉加热罩炉衬耐火材料国产化改造

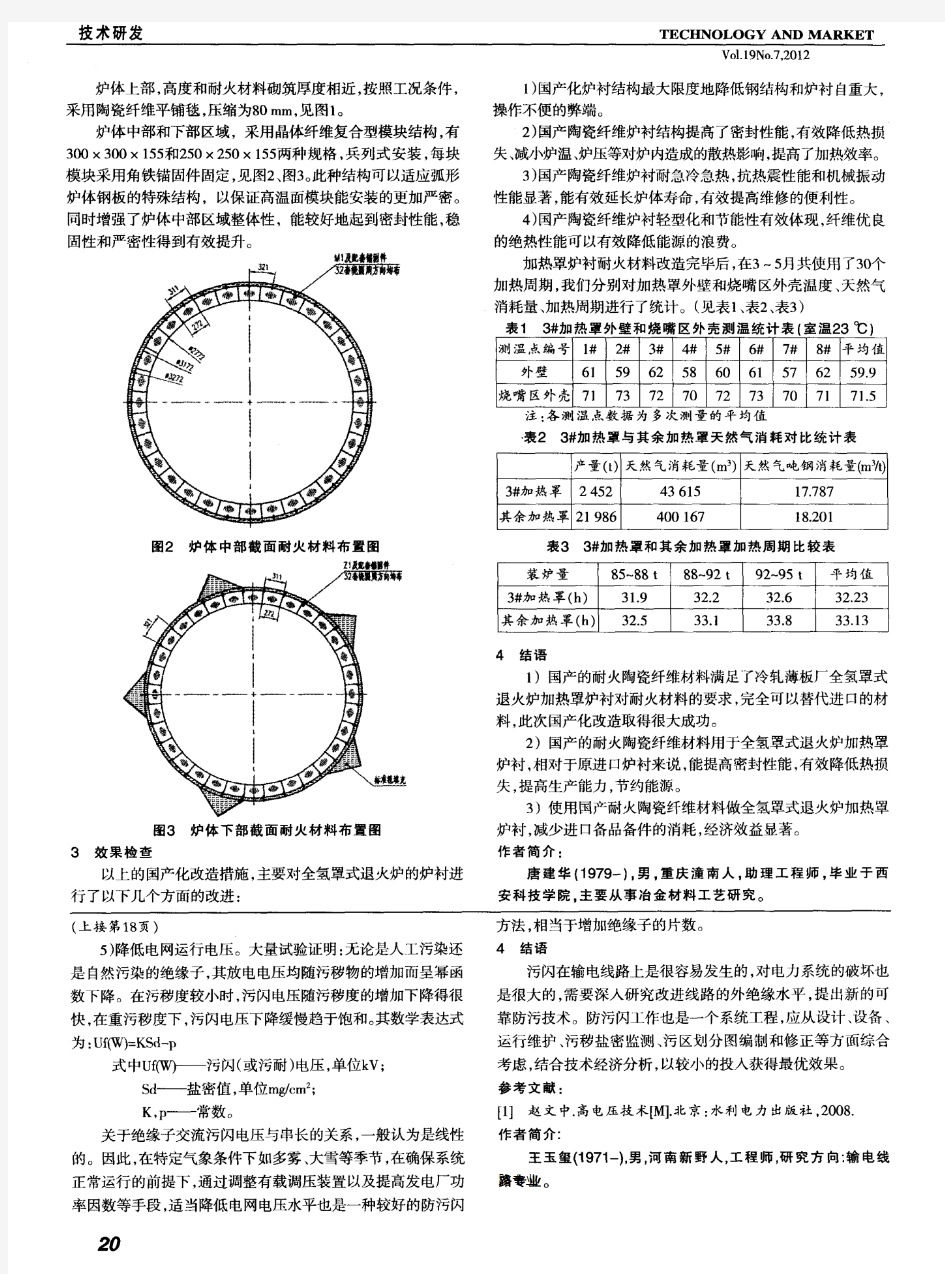
节能热处理技术和设备在轴承行业的应用
节能热处理技术和设备在轴承行业的应用 一、轴承行业现状及热处理技术和装备概况 1.我国轴承行业持续快速稳定的发展 我国轴承行业经过建国以来五十多年的建设和发展,特别是改革开放以来持续、快速、稳定的发展,已形成了较大的产业规模。2007年全行业生产各类轴承90亿套,实现销售收入760亿元。轴承产量和销售收入居世界第三位。 我国轴承进出口贸易额逐年攀升。2007年轴承出口创汇21亿美元,进口用汇21亿美元,进出口持平。 “九五”以来,我国轴承行业经济成分发生了深刻的变化。至2006年,按销售额计算,已形成国有:民营:三资=16:63:21的格局。 我国轴承行业技术水平逐步提高,已具有一定的技术实力。有一所(洛轴所)、一院(中机十院)、一校(河南科大)作为依托。全行业现有国家级企业技术中心5个(万向、瓦轴、哈轴、洛轴、西北)、博士后科研工作站5个(万向、龙溪、洛轴所、西北、杭州中心)、国家级实验室6个(洛轴所、杭州中心、上海所、万向、龙溪、瓦轴)。全行业的产品开发能力有很大提高,掌握的轴承品种规格已由1999年的39000种增加到2005年的66000多种。为重大装备和重点主机的配套率达到80%左右。高端产品开发有重大突破。以“神五”、“神六”、“嫦娥一号”配套轴承为代表的航天航空轴承及其他国防装备配套轴承均已立足国内,具有完全自主知识产权。长期制约为国内主机配套和扩大出口的微小型深沟球轴承的振动噪声和密封性能问题,通过中国轴协组织的全行业技术攻关,已取得显著效果,基本上可以满足国内主机配套和扩大出口的要求,部分企业的产品已达到或者接近国际同类产品的水平。 2.我国轴承热处理技术和装备取得的长足进步 “六五”、“七五”、“八五”经济建设时期,有二十多家轴承制造企业先后从日本、英国、美国、瑞士、西德、奥地利、意大利等工业发达国家引进设备的使用、消化吸收,其中的主要类型设备在“八五”末期基本实现了国产化,有力地促进了我国轴承热处理装备的技术进步和电炉行业的制造水平。 推杆式等温球化退火炉在轴承行业得到广泛应用,目前该类型设备是轴承零件退火的主要设备。轴承零件保护气氛退火已开始引起重视,并开始在生产上广泛应用。 轴承零件淬回火设备主要有网带炉、铸链、辊底炉、多用炉、转底炉、滚筒炉生产线,这些生产线是我国轴承行业热处理设备的主力设备,也代表了我国轴承热处理装备水平,这些装备的推广应用,大大提高了我国轴承零件热处理质量水平,工件淬火后氧化脱碳层由原来的0.06~0.1 mm降到0.03 mm以下,批量硬度差由原来的2HRC降到1.5HRC以下,同件硬度差由原来的1.5HRC降到1HRC 以内,压缩磨削留量1/3~1/2,提高磨工效率15%~22%,为我轴承质量总体水平的提高做出了贡献。 渗碳热处理设备主要有推杆式、辊底式、网带式气体渗碳自动生产线,也有多用炉、真空渗碳炉、井式炉、周期式渗碳炉,渗碳气氛的碳势控制大多采用自动控制系统,也有采用流量控制。
钟罩式退火炉常用英语单词
BAF单词 1.Batch Annealing Furnace (BAF) : 罩式退火炉 2.workbase: 炉台 3.inner cover: 内罩 4.heating bell: 加热罩 5.cooling bell: 冷却罩 6.coil: 钢卷 7.final cooling stand: 终冷台 8.valve stand: 阀站 9.pressure regulation station: 减压站 10.convector plate: 对流板 11.stack: 堆垛 12.hydraulic unit: 液压机组 13.piping: 管道 14.tilter: 翻卷机 15.workbase frame: 炉台底板 16.guide post: 导向柱 17.guide pin: 小导向柱 18.guide arm: 导向臂 19.clamping cylinders: 夹紧缸 20.fan motor: 风机马达 21.sealing: 密封圈 22.impeller: 叶轮 23.control cabinet: 控制柜 24.power cabinet: 电源柜 25.terminal box: 接线盒 26.hose: 软管 27.pressure switch: 压力开关 28.pressure gauge: 压力表 29.regulating valve: 减压阀 30.radial flow fan: 射流风机 31.thermocouple: 热电偶 32.recuperator: 换热器 33.damper: 挡板 34.expansion joint: 膨胀节 35.solenoid valve: 电磁阀 36.motorized valve: 马达阀 37.positioner: 定值器
全氢罩式退火炉氢气用量对退火时间的影响分析
全氢罩式退火炉氢气用量对退火时间的影响分析 摘要:采用全氢罩式退火时,影响退火时间因素比较多,主要有氢气用量、循环风量等各个因素。本文构建出全氢罩式炉内传热数学模型,再通过实测验证之后,分析氢气用量和退火时间之间关系。增加氢气用量和退火时间长短间并不属于简单比例关系,因此在选择氢气用量之时就要适当选择。 关键词:退火时间;氢气用量;全氢罩式退火炉 1 前言 影响退火炉钢卷传热主要参数就是对流换热系数,一些专家通过研究发现,对流换热系数和氢气用量之间存在密切关系。氢气用量过小必然会影响到炉内的传热效果,氢气用量过大也会提升设备投资。所以合理采用氢气用量是确定退火时间的关键因素之一。因此,探究氢气用量影响退火时间具有实际意义。 2 全氢罩式退火炉传热研究 2.1 该退火炉的性能介绍 罩式退火是冷轧钢卷传统的退火工艺。冷轧带钢通过再结晶退火达到降低钢的硬度、消除冷加工硬化、改善钢的性能、恢复钢的塑性变形能力之目的。退火时,各钢卷之间放置对流板,扣上保护罩(即内罩),保护罩内通保护气体,再扣上加热罩(即外罩),将带钢加热到一定温度保温后再冷却。全氢罩式炉采用100%的H2作为退火介质,使钢卷的径向导热系数较大,提高钢卷内部的传热速度,减少升温过程中钢卷的内外温差,能获得更好的机械性能;采用全氢退火,不脱碳、不增碳,带钢表面的润滑剂能更容易蒸发,能确保带钢表面的光亮程度;由于氢气的比重较小,采用相同流量的炉台循环风机时电耗就较小,节约能源。外罩加热采用天然气,有效控制成本。全氢罩式炉自动化系统的控制范围是从内罩上炉台开始,直到钢卷退火结束,内罩吊离炉台为止的全过程。 即全过程包括:内罩上炉台、夹紧油缸将内罩夹紧、加热罩上炉台、冷泄漏检查、氮气吹扫、自动点火、氢气吹扫氮气、升温、保温、热密封检查、加热罩吊离炉台、冷却罩上炉台、风冷、水冷、出炉温度达到、冷却罩吊离炉台、内罩松开并吊离炉台等全退火过程。 2.2数学模型及验证 该炉内的退火钢卷导热方式为:(1)该式子中的ρ表示钢的密度,为kg/m3;Cp 表示钢热容量,单位为J/(kg.0c);λδ表示钢导热系数,单位为W/(m.0C);λγ表示钢卷径向等效的导热系数,其单位为W/(m.0C;Ti表示第i卷钢温度,单位为0C。
强对流球化退火炉-操作使用说明书解读
杭州杭申节能炉窑有限公司 强对流球化退火炉 (型号:HS-300/240) 操作使用说明书 二O一四年
目录 一、强对流球化退火炉使用材料及配件 (2) 二、主要技术参数 (3) 三、保养须知………………………………………………………4-5 四、注意事项 (6) 五、球化退火炉操作步骤 (7) 六、电气控制操作说明……………………………………………8-20
一、使用材料及配件 1、炉盖自动升降系统,采用气缸升降,悬吊回旋机轴 1、炉胆盖部设有充气、排气、氮气甲醇等接口装置。 1、炉盖上设有带变频18.5kw强对流循环风机,循环风机采用双水冷式轴承组。 2、炉体外部带变频2.2kw 高压强冷风机。 1、外壳由8mm钢板焊接而成,炉衬内采用陶瓷纤维棉,通过模具压缩制成,粘贴在炉墙上,双面保温组成炉膛。发热元件采用电 阻带悬挂在炉膛上,采用高铝耐火螺栓形拧紧固定,分为上中下三区控温。 6、炉胆材质不锈钢310S*8mm厚不锈钢卷焊制成桶身,内桶底 部采用圆底封头,材质310S,厚度12mm。导流桶采用5mm厚不 锈钢卷焊制成桶身。 7、炉底采用硅酸铝陶瓷纤维棉、耐火砖、保温砖彻筑而成 8、电气控制系统采用触摸屏及变频器、PLC采用欧姆龙可编程控器、电力调整器控制、其他配件采用正泰及茗熔集团产。 2
二、强对流球化退火炉主要技术参数 1、型号: HS-300/240悬臂型 2、额定功率: 380KW 3、额定电压: 380V 4、额定温度: 950℃ 5、额定频率:50HZ 6、控制区: 3区 7、接线方法: YYY 8、工作尺寸: 9、炉体尺寸: 8、用电功率: 8、处理材料:Φ3000mm×2400mm Φ4150mm×5400mm 用电功率:380kw(3相380),实际使用时,在升温阶段为100%输出即380kw/h;在保温阶段为40%输出即 380kw×40%=152kw/h;在降温阶段为10%输出即380kw×10%=38kw/h。 中低碳钢、中低合金钢等线材球化退火。 12、装载量: 12-16T 13、炉体重量:约21T
全氢罩式炉的技术特点及其在不锈钢生产中的应用
强对流全氢罩式炉的技术特点及其在不锈钢生产中的应用 李钧 (宝钢股份不锈钢分公司冷轧厂,XX 200431) 摘要:介绍了强对流全氢罩式炉的一般结构,分析比较了强对流全氢罩式炉技术特点,阐述了强对流全氢罩式炉在不锈钢带材冷轧生产中的具体应用。 关键词:强对流全氢罩式退火炉技术特点不锈钢生产 The technical characteristics of HPH furnace and the application in stainless steel production LI Jun (Baosteel Stainless Steel Branch, Cold Rolling mill, Shanghai 200431 China) ABSTRACT The basic configuration and technical characteristics of HPH furnacewere discussed, andits main application was also simply introduced. KEY WORDS HPH furnacetechnical characteristics stainless steel production 1 引言 强对流全氢罩式炉是目前世界上最先进的间歇式退火炉之一,它采用氢气作为保护气体,利用高速循环风机,使氢气在内罩内快速对流传热,达到快速、均匀地加热和冷却退火材料,产品性能均匀、生产效率高,被广泛地应用于钢铁、有色金属的退火处理。 2 强对流全氢罩式炉的基本结构 1-加热罩 2-内罩 3-钢卷 4-中间对流板 5-炉台 6-炉台阀站 7-循环风机 图1 强对流全氢罩式炉结构示意图 图1为强对流全氢罩式退火炉的结构示意图,强对流全氢罩式退火炉主要由强对流炉台、加热罩、内罩、冷却罩、炉台阀站等部分组成。 (1)强对流炉台 炉台是罩式炉的基础部分,退火钢卷放置在炉台上,同时内罩也扣在上面,形成密闭的退火空间。设有高功率的耐高温循环风机,在钢卷加热和冷却时,保持内罩内保护气体的强循环。
全氢罩式退火炉安全控制
编号:SM-ZD-25258 全氢罩式退火炉安全控制Organize enterprise safety management planning, guidance, inspection and decision-making, ensure the safety status, and unify the overall plan objectives 编制:____________________ 审核:____________________ 时间:____________________ 本文档下载后可任意修改
全氢罩式退火炉安全控制 简介:该安全管理资料适用于安全管理工作中组织实施企业安全管理规划、指导、检查和决策等事项,保证生产中的人、物、环境因素处于最佳安全状态,从而使整体计划目标统一,行动协调,过程有条不紊。文档可直接下载或修改,使用时请详细阅读内容。 1概述 强对流全氢罩式退火炉(以下简称全氢罩式炉)是在原低氢罩式炉的基础上于70年代发展起来的,具有低能耗、高效率、退火产品品质优良等众多特点。国外在1984年开始大量应用于宽带钢卷的退火,至今已有近千座全氢罩式炉在世界各地建成。在奥地利的奥钢联、德国的克勒克纳冷轧厂和蒂森冷轧厂、美国的l-TV钢厂和USX钢厂等钢铁企业中,都可以见到正在工作的全氢罩式炉。 直到80年代末、90年代初,全氢罩式炉这项先进的生产工艺才随着国外生产工艺、控制技术的成熟逐步引进到国内,并迅速得到推广。国内已有鞍钢、武钢、本钢、上海益昌冷轧薄板厂、海南鹏达冷轧薄板厂等单位先后引进、建成了全氢罩式炉,生产、使用情况良好。近年建设或改造的冷轧薄板厂正在大量采用全氢罩式炉,原有的低氢罩式炉正面临被全氢罩式炉替代的局面。
连退工艺篇培训教材
(内部资料,妥善保存) 冷轧薄板连续退火生产线 工艺篇 马钢第四钢轧总厂职工培训教材编写组
前言
钱海帆(签名) 2005年9月连续退火生产线工艺篇 编写: 审稿:
2005年9月 目录 第一章总论 (5) 第一节什么是退火 (5) 第二节退火的主要目的 (5) 第三节冷轧带钢的再结晶退火 (5) 第四节连续退火的优点 (6) 第五节连退机组选型 (7) 第二章连退线生产工艺及生产组织 (7) 第一节连退线生产工艺 (7) 第二节产品大纲 (12) 第三节基本工艺参数 (17) 第四节活套特性及功能 (20) 第五节其他要考虑的问题 (21) 第六节退火工艺参数 (23) 第七节产能计算 (24) 第八节钢卷时间图表理论计算 (48)
第一章总论 第一节什么是退火 退火是将钢加热到临界点以上,保温后再缓慢冷却的一种热处理工艺。 第二节退火的主要目的 1)降低钢的硬度。 2)提高塑性,消除冷加工硬化,便于后续冷变形加工。 3)消除组织缺陷,改善钢的性能。 4)消除钢中残余内应力,稳定组织,防止变形。 5)均匀钢的组织和化学成分 第三节冷轧带钢的再结晶退火 退火是冷轧带钢生产中最主要的热处理工序之一。冷轧中间退火的目的主要是使受到高度冷加工硬化的金属重新软化,对于大多数钢带来说,这种处理基本上是再结晶退火。在退火前面的冷轧工序中,带钢经60%~90%以上的大压下率冷轧,晶粒组织被延伸和硬化,这样的带钢几乎不能进行任何进一步的加工成形。因此为了成形加工,必须进行再结晶退火,适当调整退火晶粒的成长和恢复所需的塑性。同时为了得到良好的成形性,期望形成一致的适合成形的结晶织构。这就是进行退火的目的。
退火炉温度控制系统
本科生课程设计 题目:退火炉温度控制系统 课程:电力拖动自动控制系统 专业:电气工程及其自动化 班级: 学号: 姓名: 指导教师: 完成日期: 2015年3月20日
任务书 一、课程设计的目的 通过电力拖动自动控制系统的设计、了解一般交直流调速系统设计过程及设计要求,并巩固交直流调速系统课程的所学内容,初步具备设计电力拖动自动控制系统的能力。为今后从事技术工作打下必要的基础。 二、课程设计的要求 1、熟悉交直流调速系统设计的一般设计原则,设计内容以及设计程序的要求。 2、掌握控制系统设计制图的基本规范,熟练掌握电气控制部分的新图标。 3、学会收集、分析、运用自动控制系统设计的有关资料和数据。 4、培养独立工作能力、创造能力及综合运用专业知识解决实际工程技术问题的能力。 三、课程设计的内容 退火炉温度控制系统由一台上位机操作台、一台SIEMENS S7-200 PLC控制柜、一台变频器控制柜,3台风机,3台水煤浆输送泵组成。加热段的三个炉段,各段于炉顶设一支热电偶,根据热电偶采集的炉温信号,与设定值比较,经PID 计算后输出控制信号变频器调节水煤浆流量,改变烧嘴的输出功率,实现温度自动控制。同时根据助燃风量的改变及空/燃比例阀的配比,手动调节助燃风流量燃气的流量,实现最佳空/燃配比。 四、进度安排:共1.5周 本课程设计时间共1.5周,进度安排如下: 1、设计准备,熟悉有关设计规范,熟悉课题设计要求及内容。(1.5天) 2、分析控制要求、控制原理设计控制方案(1.5天) 3、绘制控制原理图、控制流程图、端子接线图。(2天) 4、编制程序、梯形图设计、程序调试说明。(1.5天) 5、整理图纸、写课程设计报告。(1.5天) 五、课程设计报告内容 完成下列课题的课程设计及报告(课题工艺要求由课程设计任务书提供)退火炉温度控制系统
冶钢热处理连续退火炉改造方案
冶钢热处理连续退火炉改造方案 1
冶钢热处理连续退火炉改造方案 〔初稿〕 二〇〇六年三月 2
目录 概述 (1) 一、改造方案设计 (1) 1.1热处理退火炉改造方框图 (2) 1.2改造测量点统计 (3) 二.DCS集散系统控制方案 (4) 2.1重庆重庆川仪控制系统有限公司控制方案 (4) 2.2浙江中控技术有限公司控制方案 (9) 三.外围设备改造方案 (11) 3.11#连续退火炉 (11) 3.1.1外围设备说明 (11) 3.1.2方框图 (12) 3.22#连续退火炉 (13) 3
3.2.1外围设备说明 (13) 3.2.2方框图 (14) 3.3其它退火炉 (15) 3.3.1外围设备说明 (15) 3.3.2方框图 (17) 3.4煤气净化站 (18) 3.4.1外围设备说明 (18) 3.4.2方框图 (20) 四.附录 (21) 附1:连续退火炉蝶阀直径明细表 (22) 附2:热处理厂测量网络分布图 (23) 概述 1.冶钢热处理厂1#、2#连续退火炉燃烧控制系统是八十年代重庆自动化研究所安装的286计算机控制系统,当前已全部瘫痪多年,生产仅仅靠人工手动控制,1~12段温度波动在规定设定值的±10℃,生产出的钢材质量极不稳定,而且煤气与空气配比控制不是 4
很理想,造成煤气未完全燃烧而被排放,能源浪费很大,为了新冶 钢早日实现产量型转向质量型;质量型转向稳定型;稳定型转向品 牌型;经过品牌转向自主创新型;以自主创新型转向专业化服务型; 向高、精、尖发展先进企业的目标,达到集约化的目的,建议实施 以1#、2#连续退火炉燃烧控制系统为中心,安装一套DCS集散 系统,改造分二步进行,第一部完成1#、2#连续退火炉燃烧控制 系统,第二部可辐射厂房内所有的1~8#罩式退火炉、13#退火 炉、14#高温炉、15#、16#氮基炉、煤气净化站及能源计量系统 等所有生产设施。因煤气净化站点离连续退火炉控制室有200 米距离,若微弱信号衰减较大,准备采用MOX转换器,光纤电缆传 输方式,来保证信号的稳定性和可靠性,最后在连续退火炉控制站 提供数据能上新冶钢内部网络,并向有关单位进行OPC发布。 让热处理厂全部测量信息达到共享和远程控制,随着自动化程度 的提高,从人力、物力计算,生产成本可大幅度下降,产品质量控 制可得到保证。 一、改造方案设计: 1.1 热处理退火炉改造方框图〔见第2页〕 第1页1.2改造测量点统计: 热处理区域测量点规格统计 5
罩式炉概述
罩式炉概述 罩式退火是钢丝卷新生的退火方式,比传统的退火方式质量更优,效率更高;钢丝通过再结晶球化退火处理,达到降低钢的硬度、消除冷加工硬化、恢复钢丝的塑性变形能力之目的。退火时,将各钢丝卷放置炉台上,扣上保护罩(即内罩) ,保护罩内通保护气体,再扣上加热罩(即外罩) ,加热到一定温度保温后再冷却。退火时采用保护气氛,防止钢丝氧化和脱碳,使其表面的润滑剂能更容易蒸发,同时又能获得更好的机械性能。 罩式退火炉机组主要有加热罩、冷却罩、内罩、炉台、炉台阀站、及自动化控制系统组成。 自动化控制部分:主要由操作站,西门子S7-300PLC组成工业控制网络。 主要功能:自动化控制系统的主要功能就是指罩式炉能按:液压锁紧内罩→冷态密封检查→冲氮吹扫→点火升温→进保护气保护→保温→冷却→最终冲氮吹扫等工作程序进行自动操作,并出具生产报表,与上级管理机通讯,预存和调用工艺曲线,控制整个炉台生产的全过程。 主要特点:我公司设计制造的罩式退火炉设备充分吸收了国外同等产品的先进技术,并在我国拥有十多项专利技术,主要特点如下: ①由耐热钢构成高保温层炉台座,绝热性能好。 ②最新结构的半敞开式炉台,插片式导流扩散器,不仅导风性能好,且无变形,抗开裂。 ③炉座法兰、内罩法兰均经消除焊接应力后再进行机加工,确保在使用过程中无变形。 ④炉台法兰面,内罩法兰面均设有水冷却槽,增强了密封圈的冷却效果。 ⑤全密封水冷却变频电机,具有超温、超电流保护。 ⑥长叶片、耐高温的叶轮,结合高效能的导流扩散器,风量大,风压高。 ⑦分两层布置的高速燃烧烧嘴,高性能的自动空气、燃气比例调节阀,能迅速捕捉火焰中的烟尘,提高燃烧效果,节约能源。 ⑧实行集中空气预热,既降低了烟气排放温度,又提高火焰燃烧强度,降低了燃气消耗。空气预热温度能达到420℃,烟气排放温度能降低到200℃。 ⑨炉衬采用陶纤模块与陶纤毯的组合型成,陶纤模块密度能达到240㎏/m3,散热损失小,保温性能好。 ⑩圆滑流畅型的波纹内罩,既增加了刚度,又增大了传热和散热面积,且无死角,
退火炉工作计划
昆钢镀锌彩涂工程镀锌机组退火炉 施工方案 编制:雍雄文审核:批准: 中国第十九冶昆明公司机装昆明工程处 2003年12月10日 目录 一、工程概况.........................................................2 二、编制依据 (2) 三、工程特点............................................................2 四、过程内容 (3) 五、施工工艺流程......................................................3 六、主要技术措施 (4) 七、施工工期安排.................................................9 八、人工计划......................................................9 九、机具计划.........................................................10 十、材料计划 (10) 十一、质量保证措施 (11) 十二、安全及文明施工 (11) 一、工程概况 退火炉是昆钢镀锌机组的一个主要设备,其组成主要为炉子支撑钢结构、炉体及管道系 统等。其中炉体沿长度方向分为五段,即预热段(phs)、无氧化加热段(nof)、辐射管加热 和均热段(rth)、喷射冷却段(ghs)、转向段(tds)。管道系统包括冷却水管道、压缩空气 管道、氮气管道、nh保护气体管道、助燃空气管道、cog煤气管道和排烟系统管道。设备制 作安装量约为700t。 二、编制依据 1、《钢结构制作、安装施工规程》(yb9254-95); 2、《钢结构工程施工质量验收规范》 (gb50205-2001); 3、《冶金机械设备安装工程施工验收规范—液压、气动及润滑系统》(ybj207-85); 4、《冶金机械设备安装工程施工验收规范—轧钢设备》—(yb9249-93) 5、《冶金机械 设备安装工程施工验收规范—通用规定》—(ybj201-83) 6、甲方提供的施工图纸、技术资 料及设计变更; 7、我方在类似钢结构安装工程上积累的经验,以及现有的技术力量和施工装备。 三、工程特点: 1、施工任务重。该项目包括了炉子设备及炉体钢结构的安装、炉子支撑钢结构及炉子所 有管道系统的制作安装。设备安装量为700t,制作量为300t。 2、施工难度大。炉子施工是 一个系统工程,需各工种密切配合,而施工较小,给施工组织带来了很大难度。 3、施工工期短。根据土建施工、到图时间及设备到货情况,预计12月才能进行钢结构 制作。到4月1日点火烘炉,施工工期不足5个月,施工工期很短。 四、工程内容 五、施工工艺流程(如下图) 六、主要技术措施 1、施工前的准备 1)、安装前,应按设备、构件明细表核对进场的设备、构件进行检查,核查质量证明 书、设计更改文件及交工所必需的技术资料。 2 )、安装前应清除附在设备表面的灰尘、油污和泥土等杂物,钢构件的柱、梁、支撑等 主要构件安装就位后应立即进行校正、固定,对不能形成稳定空间体系的构件应进行临时加
罩式退火和连续退火优缺点
罩式退火和连续退火优缺点 1)生产工艺 全氢罩式退火炉是冷轧钢卷以带有少量残余乳化液的状态,未作脱脂便送入罩式退火炉进行退火处理,在氢气气氛中冷却,然后通过平整机中间库直接送往平整机,再检查等,设备布置空间大,生产周期长,但产品规格和产量变化灵活性强。连续退火线上冷轧带卷在进口段进行脱脂,在连续退火的第一段进行退火,随后采用气体或水等进行冷却,在退火第二段进行时效处理,然后进行在线平整,检查等,设备布置紧凑,占地面积小,生产周期短,但产品规格范围覆盖面不宜太宽,产量不宜太低。 2)总成本 所谓总成本包含工艺设备新建的投资费用再加上生产运行费用。对于全氢罩式退火工艺途径来说,其投资、消耗与维修费用与连续退火线相比都要低,只有人员较多和材料损失比较高。此外,对于连续退火线而言,还应累加冶炼深冲钢种所需的附加费用(用于真空脱气、微合金化等)以及较昂贵的酸洗费用(用于清除热轧卷取温度较高而形成的红色氧化铁皮)。所以,从有关的资料评价估计全氢罩式退火炉的总成本比连续退火机组低。 3)品种性能 品种方面,全氢罩式退火通常生产的品种有CQ、DQ和DDQ,生产EDDQ、S―EDDQ、HSLA等品种难度很大,适合小批量、多品种生产。连续退火品种有CQ、DQ、DDQ、EDDQ、S―EDDQ、HSLA、HSS等,生产厚规格(大于2.5mm)产品有困难,规格范围太宽将增加控制难度,适合大批量、少品种生产。表面洁净度方面,全氢罩式退火通过建立正确退火制度,加上在热轧、冷轧的预防措施(严格控制板形、新型轧制技术、一定程度的均匀粗糙度、精确的卷取张力等),减少粘结、折边、碳黑等缺陷。而连续退火后的钢板表面十分光洁,不会出现粘结、折边、碳黑等缺陷,适合生产表面质量要求高的钢板。深冲性方面,对于铝镇静钢而言,一般用全氢罩式退火比用连续退火质量要优,其机械性能均匀,塑性应变比r 值、加工硬化指数n值一般都能高于连续退火的产品。近年发展起来的微合金化超深冲(IF)钢,又称无间隙原子钢,该钢具有极优良的成形性,即高r值(r>2.0)、高n值(n>0.25)、高伸长率(8>50%)和非时效性(AI=0)。用连续退火生产出的IF钢的深冲性要优于用全氢罩式退火生产出的铝镇静钢的深冲性。无论用全氢罩式退火还是用连续退火均可生产微合金化超深冲(IF)钢,但用全氢罩式退火生产(IF)钢效率较低。连续退火工艺是以严格控制钢的成份为基础的,炼钢工序中需低碳、低锰,磷、硫等杂质含量要低,而这些控制技术难度高,工艺操作复杂。国外(日本等)IF钢的退火主要采用连续退火工艺,国内F钢的退火则主要采用全氢罩式退火工艺。用全氢罩式退火生产一般冷轧板热轧中低温卷取即可,用连续退火生产一般冷轧板热轧中需高温卷取。用连续退火生产IF钢时可省去过时效处理,热轧又可采用低温加热及低温卷取,比用全氢罩式退火生产IF钢优势大。对于汽车上的难冲件,用IF钢生产比用铝镇静钢生产成品率高。 强度方面,高强度板按强化机理主要有:固溶强化型加磷钢板、弥散强化型高强度低合金钢板、相变强化型双相钢板和马氏体钢板、烘烤硬化型的BH钢板等等。全氢罩式退火一般生产软质钢板,生产的低合金结构高强钢(HSLA)强度级别和深冲等级均受到限制,不适宜作高强度原板。连续退火既能生产多种深冲等级(如CQ、DQ、DDQ等)深冲钢板,又能生产强度和深冲均好的深冲高强钢板(其中CQ―HSS强度级别为340MPa和590MPa,DQ―HSS强度级别为340MPa和440MPa,DDQ―HSS强度级别为340MPa和440MPa,BH―HSS强度级别为340MPa,DP―HSS强度级别为340MPa、440MPa、590Mpa、780MPa,TRIP―HSS 强度级别为590MPa和780MPa等等)。温度均匀性方面,全氢罩式退火以紧卷状态进行处理,热工性能差,在加热和冷却过程中,其两端、内外层和中心的温度存在一定程度的不均
全氢罩式退火炉安全控制
全氢罩式退火炉安全控制 1概述 强对流全氢罩式退火炉(以下简称全氢罩式炉)是在原低氢罩式炉的基础上于70年代发展起来的,具有低能耗、高效率、退火产品品质优良等众多特点。国外在1984年开始大量应用于宽带钢卷的退火,至今已有近千座全氢罩式炉在世界各地建成。在奥地利的奥钢联、德国的克勒克纳冷轧厂和蒂森冷轧厂、美国的l-TV钢厂和USX钢厂等钢铁企业中,都可以见到正在工作的全氢罩式炉。 直到80年代末、90年代初,全氢罩式炉这项先进的生产工艺才随着国外生产工艺、控制技术的成熟逐步引进到国内,并迅速得到推广。国内已有鞍钢、武钢、本钢、上海益昌冷轧薄板厂、海南鹏达冷轧薄板厂等单位先后引进、建成了全氢罩式炉,生产、使用情况良好。近年建设或改造的冷轧薄板厂正在大量采用全氢罩式炉,原有的低氢罩式炉正面临被全氢罩式炉替代的局面。 全氢罩式炉的安全性是至关重要的,这主要是由干在退火过程中采用了易燃、易爆的氢气充当退火产品的保护气体和热传导体,稍有不慎即有可能发生着火或爆炸事故。如果没有可靠的安全保障措施,即控制系统没有完善的控制策略,不仅全氢罩式炉的生产不能进行,而且还有破坏整个生产设施的可能。本文针对全氢罩式炉保护气体应用的安全性,介绍全氢保护气体控制过程的安全控制策略,以增强对这-问题的认识。
2全氢罩式炉设备及工艺过程简介 全氢罩式炉是用来消除由冷轧变形而使带钢产生的内应力的一种处理装置。通过使带钢升温、保温、降温的过程进行带钢的再结晶退火。 一座全氢罩式炉的基本设备包括: (1)一个带有底部循环风机的炉台及其附属介质供给管路。 (2)一个底部敞开、其余封闭焊接成整体的保护罩(以下简称内罩)。将它扣在炉台上即与炉台构成一个封闭的小空问(以下简称退火空间),退火带钢就置于退火空间之中。在退火过程中,退火空间即充满纯氢气以保护带钢在高温下不至干氧化。 (3)一个制成罩形的加热装置(以下简称加热罩)。加热罩扣在内罩之上,两罩之间形成一个燃烧室,燃料在此燃烧,热量通过内罩传递到退火空间内。 (4)一个制成罩形的带冷却风机的冷却装置(以下简称冷却罩)。 (5)一套快冷装置。这种装置有两种,一种为在冷却罩内向内罩喷水的喷淋冷却装置,一种为将保护气体循环通过换热器进行快冷的底部循环快冷装置。 (6)一套全氢罩式炉过程控制系统。 全氢罩式炉一个生产周期包括:装带卷、扣内罩;退火空间冷密封试验;氮气吹扫;扣加热罩加热;带钢保温;退火空间热密封试验;加热罩吊走和扣冷却罩进行风冷;快速冷却;退火空间氮气后吹扫、
全氢罩式退火炉安全控制
全氢罩式退火炉安全控 制 集团企业公司编码:(LL3698-KKI1269-TM2483-LUI12689-ITT289-
全氢罩式退火炉安全控制 1概述 强对流全氢罩式退火炉(以下简称全氢罩式炉)是在原低氢罩式炉的基础上于70年代发展起来的,具有低能耗、高效率、退火产品品质优良等众多特点。国外在1984年开始大量应用于宽带钢卷的退火,至今已有近千座全氢罩式炉在世界各地建成。在奥地利的奥钢联、德国的克勒克纳冷轧厂和蒂森冷轧厂、美国的l-TV钢厂和USX钢厂等钢铁企业中,都可以见到正在工作的全氢罩式炉。 直到80年代末、90年代初,全氢罩式炉这项先进的生产工艺才随着国外生产工艺、控制技术的成熟逐步引进到国内,并迅速得到推广。国内已有鞍钢、武钢、本钢、上海益昌冷轧薄板厂、海南鹏达冷轧薄板厂等单位先后引进、建成了全氢罩式炉,生产、使用情况良好。近年建设或改造的冷轧薄板厂正在大量采用全氢罩式炉,原有的低氢罩式炉正面临被全氢罩式炉替代的局面。 全氢罩式炉的安全性是至关重要的,这主要是由干在退火过程中采用了易燃、易爆的氢气充当退火产品的保护气体和热传导体,稍有不慎即有可能发生着火或爆炸事故。如果没有可靠的安全保障措施,即控制系统没有完善的控制策略,不仅全氢罩式炉的生产不能进行,而且还有破坏整个生产设施的可能。本文针对全氢罩式炉保护气体应用的安全
性,介绍全氢保护气体控制过程的安全控制策略,以增强对这-问题的认识。 2全氢罩式炉设备及工艺过程简介 全氢罩式炉是用来消除由冷轧变形而使带钢产生的内应力的一种处理装置。通过使带钢升温、保温、降温的过程进行带钢的再结晶退火。 一座全氢罩式炉的基本设备包括: (1)一个带有底部循环风机的炉台及其附属介质供给管路。 (2)一个底部敞开、其余封闭焊接成整体的保护罩(以下简称内罩)。将它扣在炉台上即与炉台构成一个封闭的小空问(以下简称退火空间),退火带钢就置于退火空间之中。在退火过程中,退火空间即充满纯氢气以保护带钢在高温下不至干氧化。 (3)一个制成罩形的加热装置(以下简称加热罩)。加热罩扣在内罩之上,两罩之间形成一个燃烧室,燃料在此燃烧,热量通过内罩传递到退火空间内。 (4)一个制成罩形的带冷却风机的冷却装置(以下简称冷却罩)。 (5)一套快冷装置。这种装置有两种,一种为在冷却罩内向内罩喷水的喷淋冷却装置,一种为将保护气体循环通过换热器进行快冷的底部循环快冷装置。 (6)一套全氢罩式炉过程控制系统。 全氢罩式炉一个生产周期包括:装带卷、扣内罩;退火空间冷密封试验;氮气吹扫;扣加热罩加热;带钢保温;退火空间热密封试验;加
全氢罩式退火炉安全控制(新版)
全氢罩式退火炉安全控制(新 版) Security technology is an industry that uses security technology to provide security services to society. Systematic design, service and management. ( 安全管理 ) 单位:______________________ 姓名:______________________ 日期:______________________ 编号:AQ-SN-0311
全氢罩式退火炉安全控制(新版) 1概述 强对流全氢罩式退火炉(以下简称全氢罩式炉)是在原低氢罩式炉的基础上于70年代发展起来的,具有低能耗、高效率、退火产品品质优良等众多特点。国外在1984年开始大量应用于宽带钢卷的退火,至今已有近千座全氢罩式炉在世界各地建成。在奥地利的奥钢联、德国的克勒克纳冷轧厂和蒂森冷轧厂、美国的l-TV钢厂和USX钢厂等钢铁企业中,都可以见到正在工作的全氢罩式炉。 直到80年代末、90年代初,全氢罩式炉这项先进的生产工艺才随着国外生产工艺、控制技术的成熟逐步引进到国内,并迅速得到推广。国内已有鞍钢、武钢、本钢、上海益昌冷轧薄板厂、海南鹏达冷轧薄板厂等单位先后引进、建成了全氢罩式炉,生产、使用情况良好。近年建设或改造的冷轧薄板厂正在大量采用全氢罩式炉,
原有的低氢罩式炉正面临被全氢罩式炉替代的局面。 全氢罩式炉的安全性是至关重要的,这主要是由干在退火过程中采用了易燃、易爆的氢气充当退火产品的保护气体和热传导体,稍有不慎即有可能发生着火或爆炸事故。如果没有可靠的安全保障措施,即控制系统没有完善的控制策略,不仅全氢罩式炉的生产不能进行,而且还有破坏整个生产设施的可能。本文针对全氢罩式炉保护气体应用的安全性,介绍全氢保护气体控制过程的安全控制策略,以增强对这-问题的认识。 2全氢罩式炉设备及工艺过程简介 全氢罩式炉是用来消除由冷轧变形而使带钢产生的内应力的一种处理装置。通过使带钢升温、保温、降温的过程进行带钢的再结晶退火。 一座全氢罩式炉的基本设备包括: (1)一个带有底部循环风机的炉台及其附属介质供给管路。 (2)一个底部敞开、其余封闭焊接成整体的保护罩(以下简称内罩)。将它扣在炉台上即与炉台构成一个封闭的小空问(以下简称
罩式退火炉现状分析
我公司罩式退火炉发展现状分析 罩式退火炉是我公司的传统产品,在公司的发展历程上曾起到至关重要的作用。近年来,随着我们产品结构的调整和战略重点的转移,我公司的罩式炉产品仍停留在几年前的水平上,没能够进一步发展,而我们的同行,在技术和质量上都取得了长足的进步。且不说EBNER和LOIS等国际知名品牌,有许多后起之秀也超过甚至赶上了我们,比如凯特尔、威尔士等。对于我公司罩式炉产品的发展现状我从安装和生产的角度阐述一下个人意见,不足之处请领导批评指正。 一、我公司罩式炉结构上的特点; 我们生产的罩式炉不论燃气还是电炉,从始至终都是一个模式,也就形成了我们结构上独特之处。当然,和其它公司生产的罩式炉相比,这种结构从其诞生之日起就有他独特的优势和劣势。 1.他的优势在于:我公司一直注重信誉,从材料的选择上讲究真材实料,有严格的来 料检验制度,所以我们生产的炉子从来没有出现过大的质量事故,绝大多数都能保 证生产要求和相对较长的使用寿命。再加上我们时刻为客户着想的独特的售后服务 理念,得到了很多用户的认可。另外,我们所用的内罩结构为正弦波形,较凯特尔 所采用的梯形波纹内罩有更好的刚度,通过邯郸卓立工程做一下对比,同样材质的 内罩,我们做的要比凯特尔公司生产的好一些。再者,全封闭的不锈钢炉台,也上 我们的一大特色,其特点是结构简单,支撑可靠,我认为从一开始就是一个相对成 熟的结构。 2.我们在制作成本和安装成本上处于绝对的劣势。先说用料,我们单从这一点我们同 凯特尔公司的加热罩做一下对比。邯郸卓立同时使用我公司和凯特尔公司生产的罩 式退火炉,我们的加热罩采用活顶结构,加热罩筒体全部使用6mm钢板。加热罩 底环板采用20mm钢板。凯特尔公司生产的加热罩采用固定罩顶,筒体采用5mm 钢板,底环板大约16mm,(可能还要薄)只是在开孔部位做了一些加强。相比之 下,我们所用材料差别就显而易见了:顶盖法兰一片、顶盖螺丝20套以及钢板的 差额。这止是管中窥豹,其它方面需要优化的地方就更多了,虽然我没有经过计算,但从凯特尔炉业所生产的东西使用情况来看,也没有什么问题。就这些事情我多次 向技术部的若干专家们提到过。再说安装成本,我们也做一下对比:泰钢所用的 EBNER公司生产的罩式炉,炉台、加热罩、阀架以及电控系统全部在生产基地完 成,并做了预装,现场工作量已经很小。并且EBNER所有的控制程序和操作界面 都在生产基地完成调试。与之相比,我们现场做保温、现场做控制箱、现场编程序、现场调试。安装成本可想而知。另外,工地安装的质量控制也没有办没和公司制作 相提并论。举个例子说明一下:我们在吉林宏大安装的时候,同期也有一个炉窑公 司在安装罩式炉,同是两组炉子,我们十五个人,用了三十五天。对方只有五个人,用了十五天时间。天壤之别。胜芳会兴也有同样的事情发生过,不知道有人向领导 反映过没有。 二、我公司生产的罩式炉还有很多需要改进的地方。 1.通过我们客户投诉和售后服务中发现的问题表明,我们还有许多地方应该下大力气 改进。津西金兰的导流板倒塌,重庆广际的结构开裂变形等,这与我们技术设计支 撑结构时的失误和制作过程中的缺陷不无关系,众所周知,任何一个结构的设计都 要相对完整的设计说明和计算书,而我们从未对我们的工程师提出过这样的要求, 审核更是敷衍了事,更谈不上论证,这就是我们以前谈到的,为什么其它公司可以
罩式炉
强循环光亮罩式退火炉 第一章热处理基本知识 1、冷轧的概念 所谓“冷轧”,顾名思义,就是钢材在冷态下,即不经过加热,直接进入轧机,利用机械的力量,按选定的成品参数进行轧制的一种工艺过程。根据工艺需要,其变形量可达40%-70%,甚至更高,然而,冷轧后的钢材不仅存在着“加工硬化”现象,而且,对钢材的组织性能有更大的影响。 2、加工硬化 经过冷轧机多道次轧制之后,钢板即从厚板变成了薄板或极薄板,这对钢板而言,即发生了塑型变形。随着变形度的增加,硬度与强度随之升高,塑性下降。于是,我们把这种因冷轧变形而引起的金属强化现象称之为“加工硬化”,当然,这种“硬化”之后的钢板是不能作为商品钢板出售的,因为经轧制之后的钢板有着塑性变形强大抗力,给原板的再加工成形带来了很大的困难。 3、再结晶退火概念 凡是经过塑性变形之后的金属,它本身就有力图恢复到变形前原来组织状态的倾向,对于冷轧机轧制后的钢板而言也不例外。在室温下,没有一定的外界条件,由于钢中原子扩散能力的不足,处于不稳定状态的变形之后的金属,能够维持相当长的时间不致发生明显的组织变化。假如我们提供给以热能,对金属进行加热升温,来提高原子的扩散能力,金属的组织和性能就会迅速发生变化。 简而言之,所谓再结晶,就是金属的晶粒在一定的能量之下,重新成长、长大、排列和组合的过程,即用各种不同温度对钢卷进行加热,使因冷轧变形所引起的组织与性能的变化得到恢复。 人们把这种行成一种完全新的、完全消除了应力的组织的过程,称之为再结晶退火。 要想材质的性能恢复到正常值或期望值,晶体结构必须恢复到变形前的状态,即要以晶体的重新形成为前提条件。对于钢板机械性能的恢复程度,则取决于材质、温度和时间等方面的因素,正确地选定退火工艺曲线,才能达到再结晶退火的目的。 4、退火工艺曲线 退火工艺曲线就是钢卷中(或退火炉内)某一点在整个退火过程中温度变化的轨迹。通过记录仪记录下来,就成了退火工艺曲线。 一种退火工艺曲线要制定得合理、准确、可靠是要经过多次的退
全自动罩式退火炉设备说明
全自动罩式退火炉设备说明
我国连续铸钢技术装备发展现状及应注意的问题 把高温钢水连续不断地浇铸成具有一定断面形状和一定尺寸规格铸坯的生产工艺过程叫做连续铸钢。连续铸钢是一项节能工艺,它具有降低能量消耗、节省工序、缩短流程、提高金属收得率、生产过程机械化和自动化程度高、钢种扩大、产品质量高等许多传统模铸技术不可比拟的优点。自从20世纪50年代,连续铸钢技术进入工业性应用阶段后,不同类型、不同规格的连铸机及其成套设备应运而生。20世纪70年代以后,连铸技术发展迅猛,特别是板、方坯连铸机的发展对加速连铸技术替代传统的模铸技术起到了决定性作用。 连铸坯的吨数与总铸坯(锭)的吨数之比叫做连铸比,它是衡量一个国家或一个钢铁企业生产发展水平的重要标志之一,也是连铸设备、工艺、管理以及和连铸有关的各生产环节发展水平的综合体现。1970年至1980年,世界平均连铸比从4.4%发展到28.4%,中国的连铸比从2.1%发展到6.2%;至1990年,世界和中国的连铸比分别发展到62.8%和22.4%;到2001年,又分别发展到87.6%和92.0%。2003年,中国连铸比达到95.3%左右,估计世界平均连铸比2003年接近90%。从统计数字可以看出,中国的连铸技术在近10多年内得到了迅速发展。 世界连铸技术的发展及我国存在的差距 世界上有许多连铸技术实力较强的公司,如西马克·德马格、奥钢联、日本JSP公司、达涅利(包括戴维)公司等。以板坯连铸机为例,
西马克·德马格公司从1962年至2001年新设计和改造板坯连铸机共约370台;奥钢联从1959年至2000年新建和改造板坯连铸机共约181台;日本JSP公司截止2001年新建并改造板坯连铸机共约150台;达涅利的戴维公司也设计了10多台连铸机。2001年末,世界上共有各类投产的板坯连铸机约550台800流(有一些是重复改造的,按估计值未计入)。 截止到2002年底,中国共有551台(1749流)连铸机,其中板、方坯连铸机分别为101台(130流)、429台(1564流),圆坯、异形坯连铸机分别为20台(52流)、1台(3流)。这些统计中,绝大部分连铸机是立足于中国国内设计制造的。 我国加入WTO后,人才、知识、科技与经济的全球化趋势越来越清晰地展现出来。由于历史及其他各方面原因,国外先进技术和管理方式显然具有竞争优势。近几年,我国经济发展较快,冶金企业投放的技改资金比较大,新上项目很多,连续铸钢项目也较多,但连铸机设备和技术大部分还是靠引进。我国薄板坯连铸连轧已经引进了将近10条生产线;从2000年开始,我国先后全部引进或引进核心部位设备与技术的常规板坯连铸机共有24台27流,还有继续引进的趋势;中薄板坯连铸机、异型坯连铸机全部引进;大方坯连铸机也有引进的倾向。其原因主要是我国连铸技术与国外先进水平还存在一定差距。以板坯连铸机为例,主要表现在: ●板坯连铸机本体设备的四个关键设备明显落后于国外。结晶器国外已采用紧凑式结构,我们还是老式的带外框架的结构;国内外新投