不良品处理流程
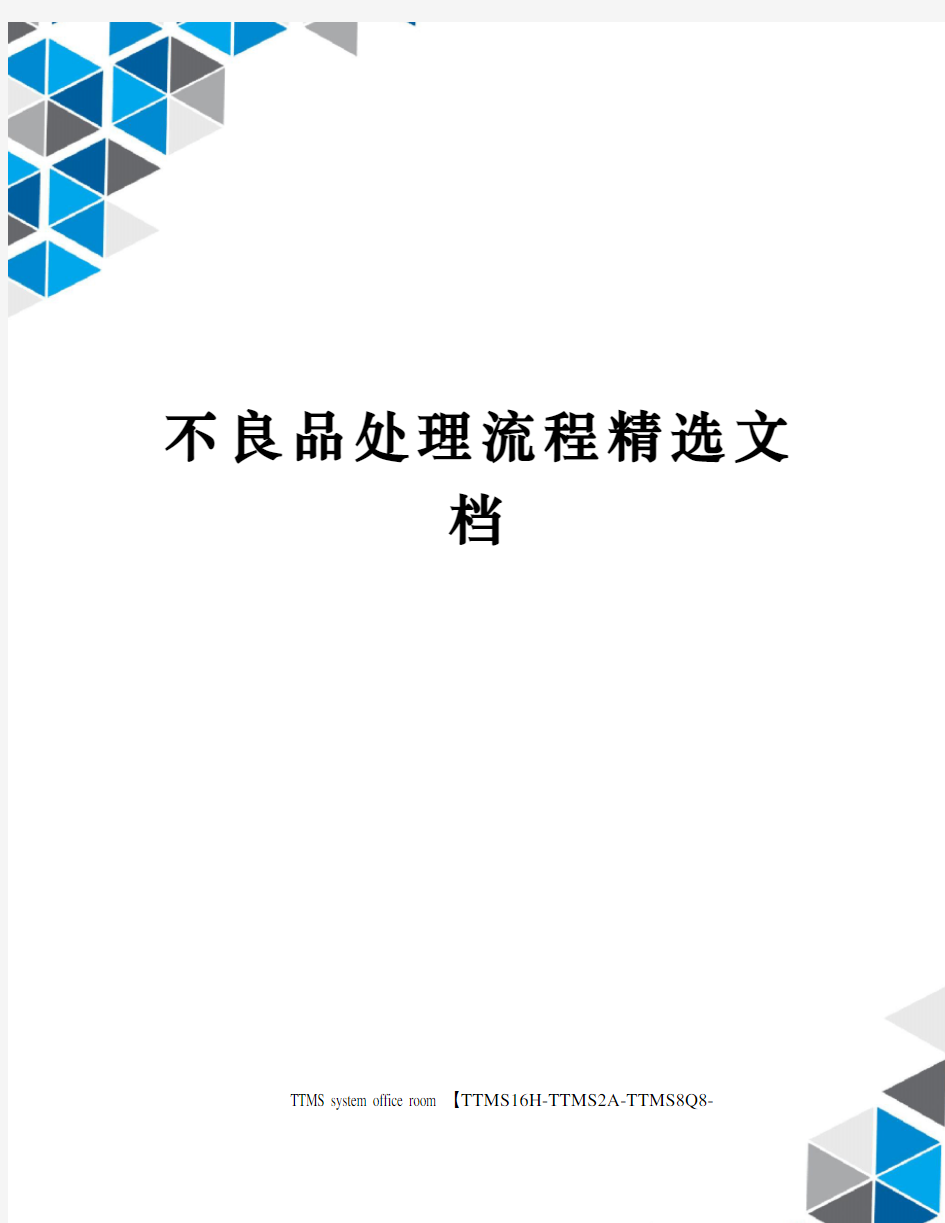

不良品处理流程精选文
档
TTMS system office room 【TTMS16H-TTMS2A-TTMS8Q8-
.1.0
目的:
加强不良物料的管制,完善公司物料管制流程,降低公司物料损失。2.0?范围:
所有我司物料。
3.0定义:
1.不良物料:
不能直接用于生产使用的物料,包括来料不良品,制程不良品
2.来料不良:
来料时就已经不能直接上线使用物料,包括来料时由IQC检验出的不良品,在线生产过程挑选出未使用的不良品,生产过程返修时由客户认可的制程不良品.
3.制程不良:
生产过程中因不良操作将良品物料损坏,不能再用于生产使用的,
责任属于生产线
4.报废物料:
制程不良品,已经没有使用价值并且不能退回给供应商,副总确认可以报废处理,经部门会签报废处理的物料
4.0权责:
生产:
1.严格按照工程WI来生产产品
2.将不良物料分类整理,交IPQC和IQC确认物料状态后退不良仓库IPQC:
1.生产的首件确认.
2.不良物料确认,严格确认来料不良及制程不良品,在确认的不良品中签名核实
3.批量性不良材料开出《品质异常联络单》,协助产线将不良品退给不良仓库
工程:
1.
按生产要求写出WI?
2.对于生产异常的分析和给出改善措施,协助IPQC确认不良材料的状态.
不良仓库:
1.确认产线退给不良仓库的物料,严格区分来料不良和制程不良
2.将不良物料分类整理,提交不合格物料清单
3.主导不良品退给供应商,确保公司利益.
5.0?
不良仓库作业流程
1.
对于来料不良,经《IQC来料检验报告》判断为退供应商物料
1.1?由供应商直接来料到我司的物料,经IQC检验不合格,
《IQC来料检验报告》判定为退货.仓库收到《IQC来料检验报告》退货通知后,及时将来料不良退至采购处理。
1.2?由采购与供应商协商什么时间和什么方式退回供应商.
1.3?退货时,由仓库开出退货单及开出放行条,经公司正常手续完成退货1.4?若供应商直接送货到我司的物料,经IQC检验不合格,
《IQC来料检验报告》判定结果为挑选,
IQC在主导完成挑选动作后,将良品、不良品区分标示后转移至仓库入库,由采购与供应商协商退货的日期及方法,并及时通知仓库退货处理2.
对于生产过程中的不良品
2.1?IPQC确认产线的不良材料状态,在每个材料上标示清楚不良原因是来料还是制程不良
2.2?生产部将IPQC确认好的物料按IPQC确认的状态,填写《退料单》于当日下班前退给仓库。
2.3?生产线在退料过程中,部分特殊的物料虽然是制程造成,但是供应商同意以来料不良退给供应商的,必须附上(有供应商确认)《品质异常联络单》,以便在退料时有依据.若没有《品质异常联络单》的,必须制程不良来区分.
2.4?仓库确认不良物料的状况,严格分清制程不良和来料不良,理清物料的状态与数量
2.5?在确认过程中有不同的意见,由IQC、工程、IPQA,生产主管协商处理
2.6?每周四不良仓库盘点,当天不良物料计入下周盘点的报表中。将不良材料清单分发以下部门:
仓库,计划,品质,采购,抄送副总,报告不良材料处理的进度及遇到的困难,报告必须有不良产生的原因和预计的处理方法和时间
3.完成确认动作的不良物料的处理
3.1?将清理的不良材料做出材料清单,分发仓库,计划,品质,采购
3.2?由采购与供应商协商不良品的处理方法及时间,原则上上周做出的不良材料清单必须在本周内退走,或者是采购与供应商确认好,签名暂放在不良仓库.此类物料计为已经退走处理
3.2?若与供应商不能达成一致,并且采购与供应商确认不能够退供应商的材料,则由IQC写出不能处理的报告,确认清楚原因及供应商意见,仓库每周报告一次,经副总确认,由来料不良转为制程不良
3.3?每周确认制程物料中没有可能退供应商,并且没有再次使用价值的,由生产提出报废,经品质审核,转到仓库报废仓,定期报废处理
3.4?不良品的退料作为不良仓管员的月度考核内容之一.
4.在下列情况下,仓库有权拒收不良物料:
4.1?单据确认流程未完成
4.2?不良物料区分有误,来料不良与制程不良未分清楚
4.3?物料编号不清晰或与实物不一致
4.4?物料无IPQC确认的不良标签
5.来料不良判别标准:
5.1?产线未使用功能或者外观不良的物料
5.2物料一定在生产过程才出现的不良,因而返修拆下,但无造成二次破坏的不良物料
5.3?由供应商确认可判为来料不良的物料,并且附有供应商或采购认可签名的不良物料
5.4?IQC抽检或检验损耗的不良物料
5.5挑选出的未使用的物料
5.6?除以上5项外,其余判为制程不良
6.IQC对来料不良物料确认流程和要求