显影、蚀刻、去膜(DES)工艺指导书
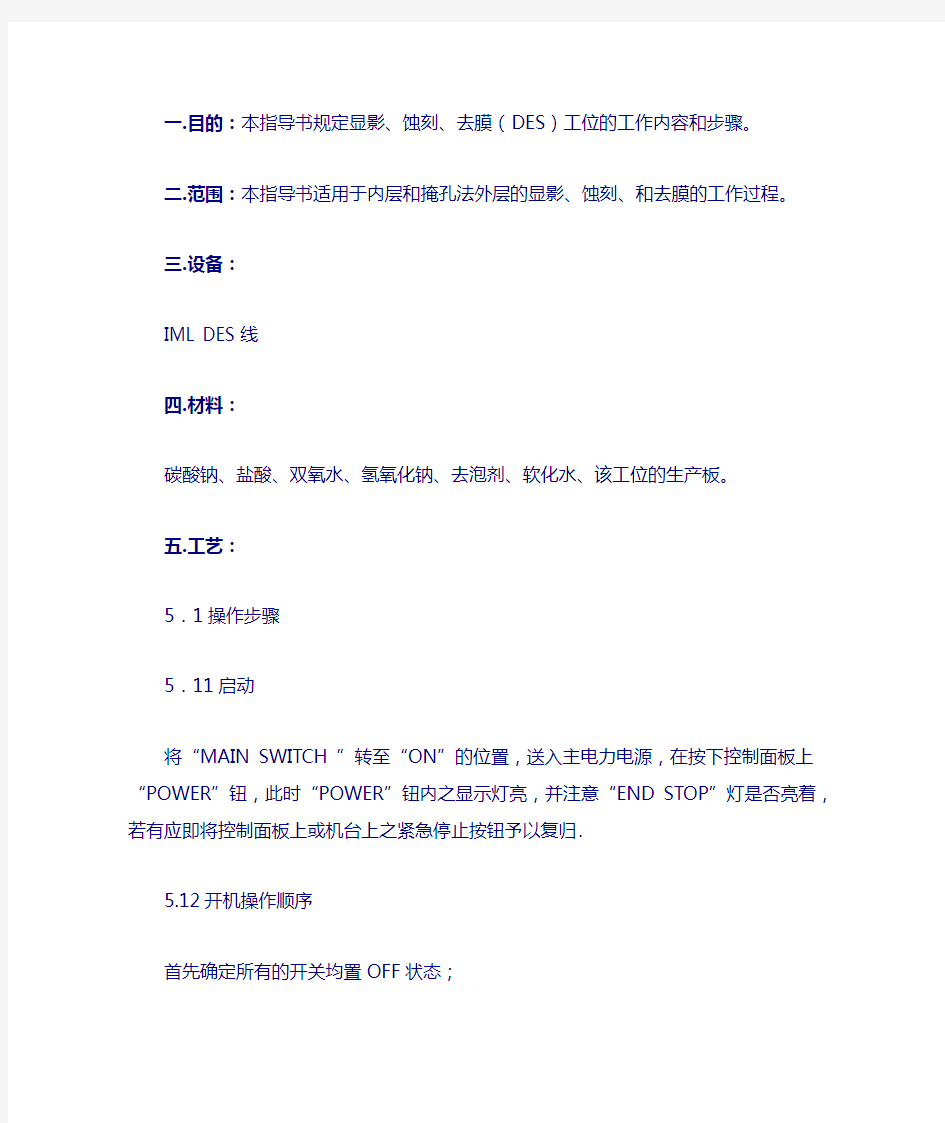

一.目的:本指导书规定显影、蚀刻、去膜(DES)工位的工作内容和步骤。
二.范围:本指导书适用于内层和掩孔法外层的显影、蚀刻、和去膜的工作过程。
三.设备:
IML DES线
四.材料:
碳酸钠、盐酸、双氧水、氢氧化钠、去泡剂、软化水、该工位的生产板。
五.工艺:
5.1操作步骤
5.11启动
将“MAIN SWITCH ”转至“ON”的位置,送入主电力电源,在按下控制面板上“POWER”钮,此时“POWER”钮内之显示灯亮,并注意“END STOP”灯是否亮着,若有应即将控制面板上或机台上之紧急停止按钮予以复归.
5.12开机操作顺序
首先确定所有的开关均置OFF状态;
将CONTROL SOURCE的旋钮旋开,使电源输入;
将所有的加热系统依流程顺序压下,先使其预热;
再将所有的温度设定器,依流程顺序,设定在所需的作业温度;
压上CON钮使其输送,再调整CON SP ADJ旋钮并调整适当的作业速度;
待温度到达所设定之温度时再将所有的PUMP钮依顺序压下即完成作业前的开机程序;
放板前10分钟润湿辊轮。
5.13关机操作顺序
依显影、蚀刻、去膜顺序依次关掉PUMP钮,关掉所有加热,热风车继续送风,观察蚀刻段温度有否升高趋势。当热风车自动停止,且蚀刻段温度没有升高趋势时,压下STOP按钮,关掉总电源POWER,将MAIN SWITCH 转至OFF。
5.14警报发生系统
故障警报系统依停机与否分二大类:
a.停机:
此项警报定义为主机或其一电器元件发生异常而无法运做或为保护人体安全而设置,如其一故障或保护条件成立便会使系统停止,须将故障或异常问题排除后再启动系统否则启动无效。
b.不停机:
此项警报定义为预先警报或周边设备警报发生不会影响主机系统生产,所以异常发生本身停止运转,而不会停止主系统运转。
故障紧急处理方式:
步骤:
当紧急状况发生是时,须先按"紧急停止"钮,瞬间停止设备之一切动作,以保安全;
停机后如内部尚有板子在内时,先行确认输送系统无异常后,可用"EMG CON"钮以寸动的方式强行使输送部分运转,将板子送出;
将其板子全部输送后,再将操作箱上之电源开关关闭然后再检查故障区域;
依指示区检查确认故障区的警示灯是何处故障;
待将所有的故障区全部检修完毕,再开机;
开机时请遵守操作顺序开机;
接板时不允许有叠板现象。
5.2工艺控制:
5.21显影段:
传送速度:1.3-1.5m/min 控制点:1.4m/min
显影槽温度:28-32℃ 控制点:30℃
建浴槽温度: 28-32℃ 控制点:30℃
药水浓度:0.8-1.1% 控制点:1.0%
显影压力:上总压:1.5-2.5 BAR 控制点:2.0 BAR
下总压:1.5-2.5 BAR 控制点:2.0 BAR
烘干温度:50℃
溶液更换与配制:
显影槽: 每天更换槽液(由建浴槽直接注入)。
建浴槽: 低液位予警时配置。
配置方法: 建浴槽低液位予警时,把7.5瓶500克碳酸钠倒入建浴槽(通过建浴槽滤网)然后向建浴槽注入软化水,到指定位置(500升处),启动建浴槽搅拌和加热。
*显影时先做四块首板,检板人员检验合格后方能批量生产。
5.22蚀刻段:
传送速度:
内层 : H oz 1.9-2.1m/min 控制点:2.0m/min、1 oz 0.8-1.2m/min 控制点:1.1m/min、2 oz 0.5-0.7m/min 控制点:0.6m/min。
外层: 底铜,H oz 0.8-1.1m/min 控制点:0.9m/min、1 oz 0.5-0.7m/min 控制点:0.6m/min。蚀刻温度:48℃
蚀刻压力:一槽:上总压:2.9 kg/cm2下总压:2.5kg/cm2
二槽:上总压:3.0 kg/cm2 下总压:2.4kg/cm2
AQUA控制器设定值(只由工艺工程师设定)
S.G : 1.26-1.30 控制点:1.28
HCL : 2.50-3.50 控制点:3.00
H2O2 : 18.0-25.0 控制点:20.0
TEMP: 40.0-45.0℃ 控制点:40.0 ℃
盐酸和双氧水添加槽低液位时分别添加精制盐酸和双氧水
(***两个槽千万不能加错***)
*蚀刻时先做4块首板,确认无残铜并经检板人员确认后,方能批量生产。
5.23去膜段
传送速度: 1.3-1.5m/min 控制点:1.4m/min
去膜槽温度: 38-42℃ 控制点:40℃
建浴槽温度: 38-42℃ 控制点:40℃
药水浓度: 1.5-2.5% 控制点:2%
去膜压力: 2.2-2.4 kg/cm2 控制点:2.3 kg/cm2
烘干温度:70℃
溶液更换与配置:
去膜槽:隔一天更换去膜槽药液.
建浴槽:低液位予警时配制.
配制方法:将20瓶500克氢氧化钠倒入建浴槽,(通过建浴槽滤网),然后向建浴槽注入软化水至指定位置(500升处)启动建浴槽搅拌和加热。
去泡剂添加槽:低液位时加入去泡剂400ml,然后加满软化水。
*确任4块首板无残膜时方能批量生产。
5.3维护保养:
每天清洗各水洗段滤网,更换水槽中的水。每天目视检查各喷嘴是否堵塞。
每周对显影段和去膜段以及水洗段进行彻底清洗,清洗方法如下:
a. 把槽中溶液排净,往显影槽和去膜槽中以及水洗槽中注入软化水,在显影槽和去膜槽中各加20升浓碱(氢氧化钠),三段水洗各加10升浓碱(氢氧化钠),开启喷淋,循环30分钟,停止喷淋。
b. 排净槽中清洗液。重新往显影槽和去膜槽中以及水洗槽中注入软化水,开启喷淋,循环30分钟,停止喷淋,排净槽中清洗液。
c. 把槽中溶液排净,往显影槽和去膜槽中以及水洗槽中注入软化水,显影槽和去膜槽中加20升浓盐酸,三段水洗各加10升浓盐酸,开启喷淋,循环30分钟,停止喷淋。
d. 排净槽中清洗液。重新往显影槽和去膜槽中以及水洗槽中注入软化水,开启喷淋,循环30分钟,停止喷淋,排净槽中清洗液。
e. 然后在显影槽和去膜槽中分别添加已经配制好的碳酸钠和氢氧化钠溶液。向水洗段加满软化水。开始生产。
六、安全事项:
谨慎操作,若有疑问,与工艺联系。
操作者在处理过显影液后必须洗手.在添加盐酸和双氧水时戴塑胶手套,面具、口罩,穿防护服,若药液溅到皮肤或眼睛立即用干净布或纸擦干,并用大量清水冲洗,必要时就医..添加氢氧化钠时戴塑胶手套,若沾到固碱或药液,立即用大量清水清洗,必要时就医.
七、自检:
显影后: 图形必须完整,无残膜,无过显影、无显影不清。
蚀刻后: 图形必须完整,无残铜。
去膜后:无残膜。
八、记录表单:<施工票>、<返工单>、<报废单>。
除锈涂装作业指导书(全面详细)
除锈涂装作业工艺指导书 目次 1.内容与适用范围------------------------------------------ 2.引用标准--------------------------------------------------- 3.涂装作业原则要求--------------------------------------- 4.喷丸除锈作业--------------------------------------------- 5.涂装前表面清洁作业----------------------------------- 6.环境条件-------------------------------------------------- 7.涂装程序------------------------------------------------- 8.涂装作业------------------------------------------------- 9.修补涂装作业------------------------------------------- 10.报验项目-------------------------------------------------
1.内容与适用范围 本标准规定了船舶建造中涂装前表面处理、涂装及涂层修补、报检项目等作业内容的工艺规范。 本标准适用于船舶产品(除特殊要求船舶外)、海上设施及其它钢结构的除锈涂装作业。 2.引用标准 GB8923-88 涂装前钢材表面锈蚀等级和除锈等级 CB*3230-85 船体二次除锈评定等级 CB/T3513-93 船舶除锈涂装质量验收技术要求 CB/T231-98 船舶涂装技术要求 CB/T3718-95 船舶涂装膜厚检测要求 CB*3381-91 船舶涂装作业安全规程 3.涂装作业原则要求 3.1建造方针书中应对涂装技术、工序、建造方法、涂装作业程序等作出明确规定。3.2 在保证新产品涂装质量的前提下,尽量选择减少重复施工、降低劳动强度、充分实施现代化的壳舾涂一体化的作业。 3.3 体现高空作业平地做、场外作业场内做、封闭作业敞开做、水上作业陆地做、仰立作业俯向做的指导思想。 3.4 按阶段,按区域逐步完善的作业方式。 3.5 涂装工艺阶段分为钢材预处理、分段涂装、船台涂装、码头涂装、坞内涂装及舾装件涂装。 3.6 分段涂装和舾装件涂装应尽量避免露天作业。 3.7 船台涂装、码头涂装和坞内涂装严格控制环境的温度和湿度。 3.8 涂装作业的表面清理、漆膜检验及报验项目按CB/T3513-93(船舶除锈涂装质量验收技术要求)中 3.2船舶除锈涂装验收项目(见表 3.8.1)和 5.2表面清理质量要(见表3.8.1)
TFT屏幕工艺标准流程经过
第二章TFT 显示器的制造工艺流程和工艺环境要求 清洗—成膜—光刻—刻蚀—剥离 阵列段是从投入白玻璃基板,到基板上电气电路制作完成。具体见下图: CF 工序是从投入白玻璃基板,到黑矩阵、三基色及ITO 制作完成。具体见下 成膜 [膜[Glass 基[PR 塗布 曝光 [Mask 現像 刻蚀 剥離 [TFT 基 重复[Glass 基
Cell工序是从将TFT基板和CF基板作定向处理后对贴成盒,到切割成单粒后贴上片光片。具体见下图: Module工序是从LCD屏开始到驱动电路制作完成,形成一个显示模块。具体示意图如下: [LCD 绑 [驱动 装 [连接电 [保护 [BLU] [信号基 検 [LCD Module] 第一节阵列段流程 一、主要工艺流程和工艺制程 (一)工艺流程 上海天马采用背沟道刻蚀型(BCE)TFT显示象素的结构。具体结构见下图:
C ' Storage capacitor ITO pixel electrode Cros-s ection -C’ a-Si TFT C Select line Data line 对背沟道刻蚀型TFT结构的阵列面板,根据需要制作的膜层的先后顺序和各层膜间的相互关系,其主要工艺流程可以分为5个步骤(5次光照):第一步栅极(Gate)及扫描线形成 具体包括:Gate层金属溅射成膜,Gate光刻,Gate湿刻等工艺制程(各工艺制程的具体介绍在随后的章节中给出)。经过这些工艺,最终在玻璃基板上形成扫描线和栅电极,即Gate电极。工艺完成后得到的图形见下图:
第二步 栅极绝缘层及非晶硅小岛(Island )形成 具体包括:PECVD 三层连续成膜,小岛光刻,小岛干刻等工艺制程(各工艺制程的具体介绍在随后的章节中给出)。经过这些工艺,最终在玻璃基板上形成 TFT 用非晶硅小岛。工艺完成后得到的图形见下图: C C' Cross-section CC’ C C' SiN a-Si/n+
覆膜工艺作业指导书
3.1工艺部:负责制订/变更各制程工艺规范 3.2生产部:负责依据工艺规范执行相关操作 3.3品管部:负责监督工艺规范的执行状况 4.名词定义: 4.1:覆膜:广告公司最常见的一种工艺技术。它主要是将膜制作的画面黏贴在亚克力、灯布、油漆产品等各种产品面上制作成各种产品标志。 5.作业环境: 车间要求无杂物、无垃圾、无砂尘,设备干净,工作平台干净,个人卫生干净,空气干湿度、温度要合适。场空气的温度与湿度对膜的粘接关系非常密切,湿度大,尤其是布与膜的表面有湿气,在干贴时易产生小气泡,影响覆膜与画面效果。 6.作业说明 6.1 亚克力贴膜: 作业流程: 清洁面板撕底膜喷水定位喷水刮画面自检 6.1.1 清洁面板: a) 检查亚克力板是否平滑和凹凸不平现象; b)首先用酒精清洁亚克力板表面,除去污迹,然后再 用1:500洗洁精水溶液清洗板面2-3次。 6.1.2 撕底膜喷水: 撕底膜时一定要边撕去膜上的离心纸边洒上洗洁精水溶液;以防贴膜粘接在一起。 6.1.3 定位 放在画好定位线的亚克力面板上。 6.1.4刮面画 a) 在贴膜上喷洒洗洁精水; b) 用丝印刮板将画面刮平。撕底膜 喷水 清洁面板
注意: 开始刮板不能用力,并且从中间向两边刮,不能来回刮,否则会使画面整体偏移。刮膜时要多刮几遍(刮的过程中须喷洗洁精水),然后四周一定要用平滑的3M 或AFC 刮板彻底的刮去膜内剩余的水份。 备注:当产品尺寸过大,膜的尺寸无法满足时,则会存在膜之间的拼缝,叠边缝2—3mm 宽。 6.1.4自检 a) 膜贴好后要检查是否有气泡、垃圾点使整体画面达到满意效果。 b) 当产品制作完工后,要及时放在指定的区域。 6.2 油漆面板贴膜: 作业流程: 画对位线 清洁面板 撕底膜 喷水 定位 喷水 刮画面 自检 6.2.1 画对位线 a) 检验面板,用手摸油漆面板无明显 颗粒垃圾,无凹凸现象。 b) 用直角尺在面板上画好对位线,不 少于3条线。 6.2.2 清洁面板 2-3mm 刮画面 画对位线
工艺流程图识图基础知识
工艺流程图识图基础知识 工艺流程图是工艺设计的关键文件,同时也是生产过程中的指导工具。而在这里我们要讲的只是其在运用于生产实际中大家应了解的基础知识(涉及化工工艺流程设计的内容有兴趣的师傅可以找些资料来看)。它以形象的图形、符号、代号,表示出工艺过程选用的化工设备、管路、附件和仪表等的排列及连接,借以表达在一个化工生产中物量和能量的变化过程。流程图是管道、仪表、设备设计和装置布置专业的设计基础,也是操作运行及检修的指南。 在生产实际中我们经常能见到的表述流程的工艺图纸一般只有两种,也就是大家所知道的PFD和P&ID。PFD实际上是英文单词的词头缩写,全称为Process Flow Diagram,翻译议成中文就是“工艺流程图”的意思。而P&ID也是英文单词的词头缩写,全称为Piping and Instrumentation Diagram,“&”在英语中表示and。整句翻译过来就是“工艺管道及仪表流程图”。二者的主要区别就是图中所表达内容多少的不同,PFD较P&ID内容简单。更明了的解释就是P&ID图纸里面基本上包括了现场中所有的管件、阀门、仪表控制点等,非常全面,而PFD图将整个生产过程表述明白就可以了,不必将所有的阀门、管件、仪表都画出来。 另外,还有一种图纸虽不是表述流程的,但也很重要即设备布置图。但相对以上两类图而言,读起来要容易得多,所以在后面只做简要介绍。 下面就介绍一下大家在图纸中经常看到的一些内容及表示方法。 1 流程图主要内容 不管是哪一种,那一类流程图,概括起来里面的内容大体上包括图形、标注、图例、标题栏等四部分,我们在拿到一张图纸后,首先就是整体的认识一下它的主要内容。具体内容分别如下: a 图形将全部工艺设备按简单形式展开在同一平面上,再配以连接的主、辅管线及管件,阀门、仪表控制点等符号。 b 标注主要注写设备位号及名称、管段编号、控制点代号、必要的尺寸数据等。 c 图例为代号、符号及其他标注说明。 d 标题栏注写图名、图号、设计阶段等。
蚀刻工序作业指导书
蚀刻工序作业指导书 1.0 目的 建立详细的作业规范,籍以稳定品质,提升生产效率,并作为设备保养、员工操作的依据,此文件同时也是本岗位新员工培訓之教材。 2.0 适用范围 本作业规范适用于本公司蚀刻(含去膜、退锡)工序。 3.0 职责 电镀班具体负责落实本指导书的实施及蚀刻设备的维护与保养。 4.0 作业内容 4.1 作业流程 4.1.1 内层(负片)蚀刻作业流程 烤板→检查→蚀刻→氨水洗→压力水洗→水洗→退膜→清洗→烘干→蚀检→转黑化工序 4.1.2 镀锡板蚀刻作业流程 退膜→检查→蚀刻→氨水洗→压力水洗→水洗→强风吹干→自检→退锡→烘干→蚀检→转下工序 4.1.3 镀金板蚀刻作业流程 退膜→检查→蚀刻→氨水洗→压力水洗→水洗→强风吹干→自检→酸洗→清洗烘干→蚀检→转下工序 4.1.3 若外层线路使用负片菲林,其蚀刻流程同4.1.1。 4.2 蚀刻工序设备及物料清单 蚀刻机、褪膜机、褪锡机、排骨架、猪笼架、放板台、去膜槽、水洗台、软毛刷、 蚀刻子液、褪铅锡药水、褪膜篮、NaOH、氨水、柠檬酸、胶盆。
4.3 基本流程说明 4.3.1 退膜:通过强碱溶解表面油墨/干膜使之退去,露出所需之铜。 4.3.2 蚀刻:在碱性强氧化剂的条件下,将线路板上之多余铜面除去。 4.3.3 退锡:去除蚀刻后图形上的抗蚀锡层。 4.3.4 酸洗:清洗金面轻微氧化,防止氧化加深。 4.4 工艺参数及操作条件
4.5 工艺维护 4.5.1 退膜槽配槽 4.5.1.1 打开槽底排水开关和水泵,把废液抽至污水处理站,抽完后关闭 水泵。 4.5.1.2 戴上长袖耐酸碱橡胶手套及防护面具,关闭排水开关,注满清水; 4.5.1.3 开启电源与泵浦,对整个槽体全面喷洒5min,然后关闭电源与泵浦; 4.5.1.4 打开盖板,用清洗工具彻底清洗槽内壁; 4.5.1.5 打开槽底排水开关,把废液排出,并用高压水枪冲洗干净; 4.5.1.6 将槽内注入3/5槽体积的清水; 4.5.1.7 另用一小槽注满水,加入9kg NaOH,搅拌至完全溶解 4.5.1.8 将泵浦电源打开,让水流动起來,再緩緩将NaOH溶液倒入槽内; 4.5.1.9 添加完成后,循环20min,使药水达到完全搅拌均勻; 4.5.1.10 通知化验人取样化验,各项管控点都在要求范围之内后方可进行 生产。 4.5.2 每月对蚀刻清洗维护一次,步骤如下: 4.5.2.1 戴上长袖耐酸碱橡胶手套及防护面具,接好回收管路;把母液抽 至储存槽,盖上纸盖以避免PH值过低; 4.5.2.2 用清水冲洗干净蚀刻槽,排掉废水; 4.5.2.3 加入2/3槽体积的清水,然后再加入10ml/L的工业盐酸,再加水至 液位,开机循环搅拌30min; 4.5.2.4 排掉盐酸清洗废液,用清水彻底清洗槽内、槽盖等部件; 4.5.2.5 拆下上下喷嘴,清理干净后按原位置安装上去; 4.5.2.6 在槽内注入4/5体积的清水,加入1/5槽体积的新液; 4.5.2.7 檢查各视窗盖板是否盖好,确认ok后,将循环泵浦与药水泵浦及 摆动开启,喷淋1小时; 4.5.2.8 检查喷管、喷嘴有无堵塞(并疏通堵塞的喷管、喷嘴); 4.5.2.9 将废液抽到废液储存槽,用碎布擦拭槽壁,并清理槽底残余的杂 质,及用高压水枪沖洗槽体(注意將水排干净);
SUS304不锈钢蚀刻工艺说明
銘瑞通SUS304不锈钢蚀刻工艺说明 Designer:张辉亭 DATE:2014/9/17
SUS304不锈钢蚀刻背胶工艺流程 清洗清洗 开料预烤曝光显影检验蚀刻脱模清洗烘干检验 贴胶压合拆废料检验包装出货
开料 1.开料前检验钢片原材料有无擦花、刮伤、折角、并弯折钢片有无弹性,以检验钢片韧性及硬度是否合格. 2.用卡尺测量钢片厚度,看是否与流转单上所要求厚度一致. 3.开料尺寸公差控制在±1mm内,要求在裁切时需一次裁断,裁切后钢片边缘不能有卷边,毛刺等现象. 4.开料时需戴厚棉手套操作,避免被钢片边缘割伤. 5.开料钢片时规定专用剪床开料,每次开料前后对剪床各部件加以擦拭,打油,每2个月对剪床刀口进行一次抛光.
清洗 1.钢片来料如有油渍,污垢等不良,需浸泡浓度10﹪碱性除油剂30min 2.双面磨板,速度2.0m/min 厚度0.1-0.15mm,磨刷压力2.5-2.7A,厚度为0.2-0.25mm磨刷压力2.3-2.5A, 烘干温度85±3℃ 3.清洗时不能过酸性除油,微蚀等一切呈酸性物质
涂布 固化 1.用湿膜丝印,湿膜不可以加开油水,保证湿膜丝印性能,油墨不可过期使用 2.采用双面涂布机涂布,用猪笼架插架避免板面划伤。 3.丝印后静止10min,方可烘烤,烘烤第一面80℃ 20min, 4.注意插架时避免擦花油墨,涂布时不可污染钢片表面,注意台面清洁,不能用洗网水清洁台面,台面不能贴任何胶带和异物导致蚀刻后造成板面凹坑不良。
曝光 1.曝光前先检查菲林版本或型号有无出错,如有异形钢片菲林(单PCS过大或者拼板不规则)通知工程确认 2.对底片时对准菲林四周阴阳盘夹边,烫底片时至少保证烫点离阴阳焊盘至少5mm 3.夹边时夹条需采用与生产钢片相等厚度的FR4或PET夹边.如菲林是生产0.2mm的钢片就用0.2mm的FR4或PET夹边 4.生产时每生产5PNL必须检查一次菲林,查看菲林四周阴阳PAD有无透光偏位,菲林有无擦花 5.曝光擦气时需真空延时5秒后才可擦气,以防止曝光不良,曝光能量设定为8-9格
覆膜作业指导书
篇一:覆膜机作业指导书 覆膜作业指导书 一、目的 确保本机组生产出符合要求的产品,防止不合格品流入下道工序。二、工具 直尺、内六角扳手、壁纸刀三、各岗位职责 1、机台长负责本机组生产人员、设备、质量的管理工作,填写生产记录。 2、机台长负责对上道工序的半成品进行复检,并对本工序产品质量进行自检。 3、辅助工在分纸和收纸的过程中特别注意产品的异常情况,生产结束后对产品进行标识,并转入下道工序,来料加工的自检合格后办理入库手续。四、操作要求和质量要求 1、开机前对设备进行检查,将薄膜按规定的方向经导辊、消皱辊、调节辊进入压合部位。注意检查机器转动部位是否灵活、平稳无异常噪声,有无偏移现象,检查各部位机构准确度,有无漏油现象。 2、无胶复合膜与输送带送来的印刷品一起经热辊筒及橡胶辊进行热压合后至收料转轴上,压合时热辊温度为70--100℃,传感器与热辊筒表面间隙为0.2mm,贴合压力为10--13mpa 之间,常用压为10--12mpa,薄纸压力为6—10mpa。 3、覆膜产品应贴合牢固无气泡,光泽度好,首件产品经检验合格方可批量生产,分割产品应无破损、不露膜,不拉松规距。 4、每班工作完毕后应速将加热滚筒和压合橡胶辊脱离接触,然后才允许停止运转,并用稀释剂(稀料)将加热滚筒及压合橡胶辊上的残留膜,碎纸及油墨擦干,保证压合胶辊上干净光滑,严格做好机台日常环境卫生工作。五、异常情况及处理六、设备保养 每班完工后及时擦洗加滚筒及压合滚筒,关键传动部位及时加注润滑油脂,做好机台日保养及卫生工作。篇二:覆膜工艺作业指导书 篇三:017覆膜机作业指导书深圳市同心诚光电有限公司 覆膜机作业指导书1.目的 此规范目的为建立覆膜机标准作业程序,以减少失误确保质量,防止不良品的产生 2.范围 适用于覆膜机作业员、品质人员和相关工程师。 3.权责 3.2验证过程中所发生之失效,研发/工程单位应尽快协助处理,并提出改善对策。 4.内容: 深圳市同心诚光电有限公司 覆膜机作业指导书深圳市同心诚光电有限公司 覆膜机作业指导书篇四:覆膜机操作、维护保养作业指导书 1. 目的 加强覆膜产品的过程控制,使覆膜产品满足客户的需求。 2. 范围 适用于覆膜产品从材料到交付客户的整个过程控制。 3. 定义(无) 4. 职责 4.1覆膜机操作人员必须严格按照其作业指导书对覆膜机进行使用、维护、保养,并做好相应的记录,确保压痕机状态稳定,满足生产要求。 5. 内容 5.1开机前的准备工作 5.1.1开机前对设备进行检查,将薄膜按规定的方向经导辊、消皱辊、调节辊进入压合部位。注意检查机器转动部位是否灵活、平稳无异常噪声,有无偏移现像,检查各部位机构准确度,有无漏油现像; 5.2覆膜机操作方法 5.2.1无胶复合膜与输送带送来的印刷品一起经热辊筒与橡胶辊进行热压合后至收料传轴上,压合是热辊温度为80-100℃,传感器与热辊筒表面间隙为0.2mm,贴合压力为10-13mpa之间。
蚀刻天线制作方法与制作流程简介
目前我们了解的天线制作技术主要有三种:绕线式天线、印刷天线和蚀刻天线。此外还有真空镀膜法生产RFID天线的,上述几种生产方法的特点比较如下: 2.1 绕线式天线 绕线和印刷技术在中国大陆得到了较为广泛的应用,大部分的 RFID标签制造商也是采用此技术。 利用线圈绕制法制作RFID标签时,要在一个绕制工具上绕制标签线圈并进行固定,此时要求天线线圈的匝数较多。这种方法用于频率围在125-134KHz的RFID标签,其缺点是成本高、生产速度慢、生产效率较低。 2.2 印刷天线 印刷天线是直接用导电油墨(碳浆、铜浆、银浆等)在绝缘基板(或薄膜)上印刷导电线路,形成天线的电路。主要的印刷方法已从只用丝网印刷扩展到胶印、柔性版印刷、凹印等制作方法,较为成熟的制作工艺为网印与凹印技术。其特点是生产速度快,但由于导电油墨形成的电路的电阻较大,它的应用围受到一定的局限。 2.3 蚀刻天线 印制电路的蚀刻技术主要应用于欧洲地区,而在,目前仅少数软性电路板厂有能力运用此技术制造RFID标签天线。 蚀刻技术生产的天线可以运用于大量制造13.56M、UHF频宽的电子标签中,它具有线路精细、电阻率低、耐候性好、信号稳定等优点。 3、蚀刻天线制作方法简介 蚀刻天线常用铜天线和铝天线,其生产工艺与挠性印制电路板的蚀刻工艺接近。 3.1 蚀刻天线的制作流程 挠性聚酯覆铜(铝)板基材――贴感光干膜/印感光油墨――连续自动曝光――显像――蚀刻――退膜--水洗--干燥—质检—包装 3.2 制作流程说明 挠性聚酯覆铜(铝)板基材:采用软板专用的合成树脂胶(环氧胶、丙烯酸胶)将铜箔(铝箔)与聚酯膜压合在一起,经高温后固化后而成,其电性能、耐高温性、耐腐蚀性较强。材料的组成截面图如下:
前处理作业指导书
前处理(磷化)作业指导书 REV :A01 文件编号: 一、 范围 用于指导材料为冷轧钢或镀锌钢板的工件喷涂前进行磷化处理,及规范磷化处理的工艺要求及其质量要求。 适用于光荣机电(深圳)有限公司喷涂工场的作业指导及质量控制。 二、 工艺设备及流程 前处理设备包括脱脂、弱脱脂、水洗、酸洗、表面调整、磷化、热水洗、油水分离、磷化沉渣等11个槽子;还有供水系统、排污系统、抽风系统、燃烧机、排烟系统、输油系统、输送系统、操作电控柜等。完成除油、水洗、酸洗、表面调整、磷化等工序,各工序均采用浸渍作业,适用于钢件表面磷酸锌处理。此外,设有水份烘干炉,用于磷化处理后水份烘干,采用辊导输送机的辊子带动工件进出烘炉。 根据公司设备情况,前处理工艺流程为: (1) 冷轧钢板类 脱脂 (弱脱脂 )第1水洗 第2水洗 酸洗 第1水洗 表面调整 磷化 第3水洗 水份烘干 (2) 镀锌板类 脱脂 第1水洗 第2水洗 表面调整 磷化 第3水洗 热水洗水份烘干 三、 处理工艺表: 水份烘干炉的烘干温度设定为150℃±5℃,烘干时间:根据工件情况设定为15-30 分钟。对油水分离槽,控制温度为70-80℃。
四、操作规范 1.严格按照公司制定的《前处理操作规程》进行操作,注意操作安全。详细参见《前处理操作规程》 2.操作前应按设备点检记录表点检设备,并作好记录。发现异常情况及时通知担当或设备维修人员。 3.操作过程注意,用电葫芦起吊工件吊框要平稳,注意不能撞碰槽壁。 4.按零件批次记录水份烘炉温度和烘干时间,并保存以备查验。 5. 磷化后至喷涂的时间间隔不能大于24小时,若超过24小时,应重新磷化处理。 6. 磷化后待喷粉的零件必须保持清洁、干燥、严禁赤手触摸。 8.对前处理槽液成份和药液浓度必须进行控制,使各槽液调整到控制范围,并作好槽液管理记录,对化验结果低于工艺规定值,必须补充化学处理剂。 各槽液控制工艺参数见上表:
化工工艺流程图画法
第十二章化工工艺图
第十二章 化工工艺图 ?教学内容: ?1、化工制图中的一些标准规范和绘制方法; ?2、化工制图前的准备工作; ?3、化工工艺图。 ?教学要求: ?1、熟悉化工设备图样的基本知识; ?2、掌握化工流程方案图、带控制点的工艺流程图 的画法与阅读。 ?重难点: ?化工流程方案图、带控制点的工艺流程图的画法。
?§1 化工制图中的一些标准规范和绘制方法 ?一、视图的选择 ?绘制化工专业图样(这里主要指化工零件图、化工设备图),首先要选定视图的表达方案,其基本要求和机械制图大致相同,要求能准确地反映实际物体的结构、大小及其安装尺寸,并使读图者能较容易地明白图纸所反映的实际情况。 ?大多数化工设备具有回转体特征,在选择主视图的时候常会将回转体主轴所在的平面作为主视图的投影平面。如常见的换热器、反应釜等。一般情况下,按设备的工作位置,将最能表达各种零部件装配关系、设备工作原理及主要零部件关键结构形状的视图作为主视图。
?主视图常采用整体全剖局部部分剖(如引出的接管、人孔等)并通过多次旋转的画法,将各种管口(可作旋转)、人孔、手孔、支座等零部件的轴向位置、装配关系及连接方法表达出来。 ?选定主视图后,一般再选择一个基本视图。对于立式设备,一般选择俯视图作为另一个基本视图;而对于卧式设备,一般选择左视图作为另一个基本视图。另一个基本视图主要用以表达管口、温度测量孔、手孔、人孔等各种有关零部件在设备上的周向方位。 ?
?有了两个基本视图后,根据设备的复杂程度,常常需要各种辅助视图及其他表达方法如局部放大图、某某向视图等用以补充表达零部件的连接、管口和法兰的连接以及其他由于尺寸过小无法在基本视图中表达清楚的装配关系和主要尺寸。需要注意,不管是局部放大图还是某某向视图均需在基本视图中作上标记,并在辅助视图中也标上相同的标记,辅助视图可按比例绘制,也可不按比例绘制,而仅表示结构关系。
一、工艺流程示意图
一、工艺流程示意图 二、工艺简介 1、格栅 格栅主要用于拦截漂浮物与悬浮物物质,如纤维、果皮、塑料制品等,以便减轻后续处理构筑物的处理负荷和防止水泵堵塞。 2、调节池 调节池的作用是使污水的水量和水质(浓度、水温等指标)实现稳定和均
衡,从而改善污水可处理性的构筑物。 3、水解酸化 水解(酸化)处理方法是一种介于好氧和厌氧处理法之间的方法,和其它工艺组合可以降低处理成本提高处理效率。水解酸化工艺根据水解发酵菌、产酸菌与产甲烷菌生长速度不同,将厌氧处理控制在反应时间较短的厌氧处理第一和第二阶段,即在大量水解发酵细菌、酸化菌作用下将不溶性有机物水解为溶解性有机物,将难生物降解的大分子物质转化为易生物降解的小分子物质的过程,从而改善废水的可生化性,为后续处理奠定良好基础。水解是指有机物进入微生物细胞前、在胞外进行的生物化学反应。微生物通过释放胞外自由酶或连接在细胞外壁上的固定酶来完成生物催化反应。酸化是一类典型的发酵过程,微生物的代谢产物主要是各种有机酸。 4、生物接触氧化 生物接触氧化技术是好氧生物膜污水处理方法,该系统由浸没于污水中的填料、填料表面的生物膜、曝气系统和池体构成。在有氧条件下,污水与固着在填料表面的生物膜充分接触,通过生物降解作用去除污水中的有机物、营养盐等,使污水得到净化。接触氧化池内均安装了生物填料,具有以下几方面特点: (1)由于填料的比表面积大,池内的充氧条件良好,生物接触氧化池内单位容积的生物固体量都高于活性污泥法曝气池及生物滤池,因此,生物接触氧化池具有较高的容积负荷,接触氧化法的容积负荷可高达 3~10KgCODc r/ ( m3·d) ,高于SBR 法的2~5KgCODc r/ ( m3·d) ,因此缩短了处理时间,减少了处理设备的体积,降低了投资。处理时间短,节约占地面积。 (2)由于相当一部分微生物固着生长在填料表面,生物膜的脱落和生长可以保持很好的平衡,不存污泥膨胀问题,运行管理简便。 (3)由于生物接触氧化池内生物固体量多,水流属完全混合型,因此生物接触氧化池对水质水量的骤变有较强的适应能力,曝气加速了生物膜的更新,使生物膜活性提高。
IC工艺流程简介
晶体的生长 晶体切片成wafer 晶圆制作 功能设计à模块设计à电路设计à版图设计à制作光罩 工艺流程 1) 表面清洗 晶圆表面附着一层大约2um的Al2O3和甘油混合液保护之,在制作前必须进行化学刻蚀和表面清洗。 2) 初次氧化 有热氧化法生成SiO2 缓冲层,用来减小后续中Si3N4对晶圆的应力 氧化技术 干法氧化Si(固) + O2 àSiO2(固) 湿法氧化Si(固) +2H2O àSiO2(固) + 2H2 干法氧化通常用来形成,栅极二氧化硅膜,要求薄,界面能级和固定电荷密度低的薄膜。干法氧化成膜速度慢于湿法。湿法氧化通常用来形成作为器件隔离用的比较厚的二氧化硅膜。当SiO2膜较薄时,膜厚与时间成正比。SiO2膜变厚时,膜厚与时间的平方根成正比。因而,要形成较厚的SiO2膜,需要较长的氧化时间。SiO2膜形成的速度取决于经扩散穿过SiO2膜到达硅表面的O2及OH基等氧化剂的数量的多少。湿法氧化时,因在于OH基在SiO2膜中的扩散系数比O2的大。氧化反应,Si 表面向深层移动,距离为SiO2膜厚的0.44倍。因此,不同厚度的SiO2膜,去除后的Si表面的深度也不同。SiO2膜为透明,通过光干涉来估计膜的厚度。这种干涉色的周期约为200nm,如果预告知道是几次干涉,就能正确估计。对其他的透明薄膜,如知道其折射率,也可用公式计算出 (d SiO2) / (d ox) = (n ox) / (n SiO2)。SiO2膜很薄时,看不到干涉色,但可利用Si的疏水性和SiO2的亲水性来判断SiO2膜是否存在。也可用干涉膜计或椭圆仪等测出。 SiO2和Si界面能级密度和固定电荷密度可由MOS二极管的电容特性求得。(100)面的Si的界面能级密度最低,约为10E+10 -- 10E+11/cm –2 .e V -1 数量级。(100)面时,氧化膜中固定电荷较多,固定电荷密度的大小成为左右阈值的主要因素。 3) CVD(Chemical Vapor deposition)法沉积一层Si3N4(Hot CVD或LPCVD)。 1 常压CVD (Normal Pressure CVD) NPCVD为最简单的CVD法,使用于各种领域中。其一般装置是由(1)输送反应气体至反应炉的载气体精密装置;(2)使反应气体原料气化的反应气体气化室;(3)反应炉;(4)反应后的气体回收装置等所构成。其中中心部分为反应炉,炉的形式可分为四个种类,这些装置中重点为如何将反应气体均匀送入,故需在反应气体的流动与基板位置上用心改进。当为水平时,则基板倾斜;当为纵型时,着反应气体由中心吹出,且使基板夹具回转。而汽缸型亦可同时收容多数基板且使夹具旋转。为扩散炉型时,在基板的上游加有混和气体使成乱流的装置。 2 低压CVD (Low Pressure CVD) 此方法是以常压CVD 为基本,欲改善膜厚与相对阻抗值及生产所创出的方法。主要特征:(1)由于反应室内压力减少至10-1000Pa而反应气体,载气体的平均自由行程及扩散常数变大,因此,基板上的膜厚及相对阻抗分布可大为改善。反应气体的消耗亦可减少;(2)反应室成扩散炉型,温度控制最为简便,且装置亦被简化,结果可大幅度改善其可靠性与处理能力(因低气压下,基板容易均匀加热),因基可大量装荷而改善其生产性。 3 热CVD (Hot CVD)/(thermal CVD) 此方法生产性高,梯状敷层性佳(不管多凹凸不平,深孔中的表面亦产生反应,及气体可到达表面而附着薄膜)等,故用途极广。膜生成原理,例如由挥发性金属卤化物(MX)及金属有机化合物(MR)等在高温中气相化学反应(热分解,氢还原、氧化、替换反应等)在基板上形成氮化物、氧化物、碳化物、硅化物、硼化物、高熔点金属、金属、半导体等薄膜方法。因只在高温下反应故用途被限制,但由于其可用领域中,则可得
网版制作工艺流程(doc 6)
网版制作工艺流程 目前,市场网版制作工艺因其原材料不同,生产工艺也就有所不同。据了解,目前市场上用来制作网版的原材料有三种类型:液态型直接法感光胶,预敏化型的直接法胶片及间接法胶片。由于三种原材料的特性与功能不同,其使用操作工艺也就有所不同。 一、液态型直接法感光胶 感光胶的优点是工艺简单、经济、实用。其特性有曝光速度快,网版经久耐用而且去膜容易,优良的耐溶性,其生产工艺流程是: 网前处理及选网→配胶→涂胶→干燥→曝光→显影→待用 其工作环境为温度15~20℃,相对温度50~65%,黄灯下暗房操作。 ※网前处理及选网 新丝网在使用前必须用磨网膏进行网前处理,每个网版都要用脱脂剂彻底脱脂,具体操作方法是用水淋湿丝网两面,涂上磨网膏或脱脂剂,然后用毛刷涂均匀并静置1分钟,最后用清水冲洗干净。 使用过的网如果不再使用,可用脱膜剂浸泡,然后清洗干净,使用前必须做脱脂处理工艺。 丝网清洗好后,烘干处理待用。制网者可根据所需要的网牍目数进行选网:丝
印线路一般用120T/cm,阻焊100-120T/cm,字符100-120T/cm,碳桥油43-120T,印剥离兰胶18-36T。 ※配胶 直接法感光胶目前市上有二种类型:一种是单液型,这种类型是把敏化剂在生产时直接配制的感光胶,可直接使用的类型;另一种是“二元固化”感光胶。这种感光胶在使用前必须进行配置,即把敏化剂加入适量水均匀搅拌后倒入感光胶中,经过上下左右充分搅拌,即配制完成。配胶工作最少要在使用前两个小时完成,最佳的方法是在前一个工作日下班前配好胶,第二天上班即用。切记,配好的胶必须静置2小时以上,让胶中泡沫消失才可使用,否则会出现意想不到的质量事故。 ※涂胶 把干燥好的待用网放置在涂胶台上,把适量的感光胶倒入刮刀内,先涂印刷面(丝网的凸面),后涂油墨面(丝网的凹面),一般每面3刀次,如果要求厚网版,那么可分多次涂刷,即第一次涂胶后,立即放入30-40℃的烘箱中烘干,取出丝网再次涂胶,根据所要求厚度,决定涂胶次数,注意一般印刷面(凸面)要比油墨面(凹面)多涂2-3刀次。 涂胶工艺十分重要,网版质量好坏,全靠涂胶,要求版面厚度均匀一致,有立体感。 ※干燥 丝印感光胶涂刷完后,先静置1-2分钟,然后把丝网放进40℃左右的烘箱中
显影、蚀刻、去膜(DES)工艺指导书
一.目的:本指导书规定显影、蚀刻、去膜(DES)工位的工作内容和步骤。 二.X围:本指导书适用于内层和掩孔法外层的显影、蚀刻、和去膜的工作过程。 三.设备: IML DES线 四.材料: 碳酸钠、盐酸、双氧水、氢氧化钠、去泡剂、软化水、该工位的生产板。 五.工艺: 5.1操作步骤 5.11启动 将“MAIN SWITCH ”转至“ON”的位置,送入主电力电源,在按下控制面板上“POWER”钮,此时“POWER”钮内之显示灯亮,并注意“END STOP”灯是否亮着,若有应即将控制面板上或机台上之紧急停止按钮予以复归. 5.12开机操作顺序 首先确定所有的开关均置OFF状态; 将CONTROL SOURCE的旋钮旋开,使电源输入; 将所有的加热系统依流程顺序压下,先使其预热; 再将所有的温度设定器,依流程顺序,设定在所需的作业温度; 压上CON钮使其输送,再调整CON SP ADJ旋钮并调整适当的作业速度; 待温度到达所设定之温度时再将所有的PUMP钮依顺序压下即完成作业前的开机程序; 放板前10分钟润湿辊轮。
5.13关机操作顺序 依显影、蚀刻、去膜顺序依次关掉PUMP钮,关掉所有加热,热风车继续送风,观察蚀刻段温度有否升高趋势。当热风车自动停止,且蚀刻段温度没有升高趋势时,压下STOP按钮,关掉总电源POWER,将MAIN SWITCH 转至OFF。 5.14警报发生系统 故障警报系统依停机与否分二大类: a.停机: 此项警报定义为主机或其一电器元件发生异常而无法运做或为保护人体安全而设置,如其一故障或保护条件成立便会使系统停止,须将故障或异常问题排除后再启动系统否则启动无效。 b.不停机: 此项警报定义为预先警报或周边设备警报发生不会影响主机系统生产,所以异常发生本身停止运转,而不会停止主系统运转。 故障紧急处理方式: 步骤: 当紧急状况发生是时,须先按"紧急停止"钮,瞬间停止设备之一切动作,以保安全; 停机后如内部尚有板子在内时,先行确认输送系统无异常后,可用"EMG CON"钮以寸动的方式强行使输送部分运转,将板子送出; 将其板子全部输送后,再将操作箱上之电源开关关闭然后再检查故障区域; 依指示区检查确认故障区的警示灯是何处故障; 待将所有的故障区全部检修完毕,再开机; 开机时请遵守操作顺序开机;
金属蚀刻工艺流程
金属蚀刻工艺流程 (一)金属蚀刻工艺流程 金属的种类不同,其蚀刻的工艺流程也不同,但大致的工序如下:金属蚀刻板→除油→水洗→浸蚀→水洗→干燥→丝网印刷→千燥→水浸2~3min→蚀刻图案文字→水洗→除墨→水洗→酸洗→水洗→电解抛光→水洗→染色或电镀→水洗→热水洗→干燥→软布抛(擦光)光→ 喷涂透明漆→干燥→检验→成品包装。 1.蚀刻前处理 在金属蚀刻之前的工序都是前处理,它是保证丝印油墨与金属面具有良好附着力的关键工序,因此必须要彻底清除金属蚀刻表面的油污及氧化膜。除油应根据工件的油污情况定出方案,最好在丝印前进行电解除油,保证除油的效果。除氧化膜也要根据金属的种类及膜厚的情况选用最好的浸蚀液,保证表面清洗干净。在丝网印刷前要干燥,如果有水分,也会影响油墨的附着力,而且影响后续图纹蚀刻的效果 甚至走样,影响装饰效果。 2.丝网印刷 丝网印刷要根据印刷的需要制作标准图纹丝印网版。图纹装饰工序中,丝印主要起保护作用,涂感光胶时次数要多些,以便制得较厚的丝网模版,这样才使得遮盖性能好,蚀刻出的图纹清晰度高。丝网版的胶膜在光的作用下,产生光化学反应,使得光照部分交联成不溶于水的胶膜,而未被光照部分被水溶解而露出丝网空格,从而在涂有胶膜丝网版上光刻出符合黑白正阳片图案的漏网图纹。 把带有图纹的丝印网版固定在丝网印刷机上,采用碱溶性耐酸油墨,在金属板上印制出所需要的图纹,经干燥后即可进行蚀刻。 3.蚀刻后处理 蚀刻后必须除去丝印油墨。一般的耐酸油墨易溶于碱中。将蚀刻板浸入40~60g/L的氢氧化钠溶液中,温度50~80℃,浸渍数分钟即可退去油墨。退除后,如果要求光亮度高,可进行抛光,然后进行染色,染色后为了防止变色及增加耐磨、耐蚀性,可以喷涂透明光漆。 对于一些金属本身是耐蚀性能好而且不染色的,也可以不涂透明漆,要根据实际需要而定。 (二)化学蚀刻溶液配方及工艺条件 蚀刻不同的金属要采用不同的溶液配方及工艺条件,常用金属材料的蚀刻溶液配方及工艺条件见表6―4~表6-6。
蚀刻去膜作业指导书
1.目的: 规范蚀刻、去膜操作的内容和步骤。 2.范围: 适用二楼自动拉线路蚀刻、去膜的工作过程。 3.设备: 自动线 4.材料: YX-550酸性蚀刻液、氢氧化钠、消泡剂、水,生产PCB板。 5.工艺: 首先确定所有的开关均置关闭状态; 将总电源开关旋钮旋开,使电源输入; 将所有的加热系统依流程顺序压下,先使其预热; 再将所有的温度设定器,依流程顺序,设定在所需的作业温度; 压上传送钮使其输送,再调整速度旋钮并调整适当的作业速度; 待温度到达所设定之温度时再将所有的开关按钮依顺序压下即完成作业前的开机程序. 5.1蚀刻开机操作顺序 开机前准备: 必须检查蚀刻槽添加槽化学蚀刻槽水洗槽液位是否正常,检查比重计,添加泵等是否工作正常,补充添加槽液位。必须检查箱体内喷嘴是否堵塞,清洗蚀刻槽过滤网及水洗槽过滤网,每周打开箱体检查并清洗喷嘴。 必须检查腐蚀溶液的参数是否正常(工作温度、比重、压力等) 5.1.1打开总电源电闸 5.2.2打开总电源开关信号灯绿灯亮 5.2.3打开启动开关 5.2.4打开所有的蚀刻加热开关 5.2.5打开传送 5.2.6打开蚀刻下喷Ⅰ-Ⅱ-Ⅲ 5.2.7打开循环水洗Ⅰ-Ⅱ-Ⅲ 5.2去墨开机操作顺序 5.1.1打开总电源电闸 5.2.2打开总电源开关信号灯绿灯亮 5.2.3打开启动开关 5.2.4打开所有的去墨加热开关 5.2.5打开传送 5.2.6打开去墨下喷Ⅰ-Ⅱ 5.2.7打开循环水洗Ⅰ-Ⅱ-Ⅲ 5.3机操作顺序 待板出来完,依蚀刻、去膜顺序依次关掉开关按钮,先关掉所有加热,压下所有按钮,关掉总电源. 5.4故障紧急处理方式: 步骤: 当紧急状况发生是时,须先按"紧急停止"钮,瞬间停止设备之一切动作,以保安全; 停机后如内部尚有板子在内时, 关闭机器开关,先行确认输送系统无异常后,用将板子送出; 将其板子全部输送后,再将操作柜上的所有电源开关关闭然后再检查故障原因;
显影、蚀刻、去膜(DES)工艺指导书
显影、蚀刻、去膜(DES)工艺指导书
一.目的:本指导书规定显影、蚀刻、去膜(DES)工位的工作内容和步骤。 二.范围:本指导书适用于内层和掩孔法外层的显影、蚀刻、和去膜的工作过程。 三.设备: IML DES线 四.材料: 碳酸钠、盐酸、双氧水、氢氧化钠、去泡剂、软化水、该工位的生产板。 五.工艺: 5.1操作步骤 5.11启动 将“MAIN SWITCH ”转至“ON”的位置,送入主电力电源,在按下控制面板上“POWER”钮,此时“POWER”钮内之显示灯亮,并注意“END STOP”灯是否亮着,若有应即将控制面板上或机台上之紧急停止按钮予以复归. 5.12开机操作顺序 首先确定所有的开关均置OFF状态; 将CONTROL SOURCE的旋钮旋开,使电源输入; 将所有的加热系统依流程顺序压下,先使其预热; 再将所有的温度设定器,依流程顺序,设定在所需的作业温度; 压上CON钮使其输送,再调整CON SP ADJ旋钮并调整适当的作业速度; 待温度到达所设定之温度时再将所有的PUMP钮依顺序压下即完成作业前的开机程序; 放板前10分钟润湿辊轮。
5.13关机操作顺序 依显影、蚀刻、去膜顺序依次关掉PUMP钮,关掉所有加热,热风车继续送风,观察蚀刻段温度有否升高趋势。当热风车自动停止,且蚀刻段温度没有升高趋势时,压下STOP按钮,关掉总电源POWER,将MAIN SWITCH 转至OFF。 5.14警报发生系统 故障警报系统依停机与否分二大类: a.停机: 此项警报定义为主机或其一电器元件发生异常而无法运做或为保护人体安全而设置,如其一故障或保护条件成立便会使系统停止,须将故障或异常问题排除后再启动系统否则启动无效。 b.不停机: 此项警报定义为预先警报或周边设备警报发生不会影响主机系统生产,所以异常发生本身停止运转,而不会停止主系统运转。 故障紧急处理方式: 步骤: 当紧急状况发生是时,须先按"紧急停止"钮,瞬间停止设备之一切动作,以保安全; 停机后如内部尚有板子在内时,先行确认输送系统无异常后,可用"EMG CON"钮以寸动的方式强行使输送部分运转,将板子送出; 将其板子全部输送后,再将操作箱上之电源开关关闭然后再检查故障区域; 依指示区检查确认故障区的警示灯是何处故障; 待将所有的故障区全部检修完毕,再开机; 开机时请遵守操作顺序开机;
蚀刻工艺
蚀刻工艺 蚀刻是金属板模图纹装饰过程中的关键,要想得到条纹清晰、装饰性很强的图纹制品,必须注意控制好蚀刻工艺的条件。主要是蚀刻溶液的温度和蚀刻时间。溶液温度稍高,可以提高金属溶解的速度,也就是蚀刻的速度,缩短蚀刻所需要的时间,但是蚀刻溶液一般都是强酸液,强酸液在温度高的情况下腐蚀性强,容易使防护的涂层或耐蚀油墨软化甚至溶解,使金属非蚀刻部位的耐蚀层附着力下降,导致在蚀刻和非蚀刻交界处的耐蚀涂层脱落或溶化,使蚀刻图纹模糊走样,影响图纹的美观真实和装饰效果,因此温度不宜超过45℃。同样,如果蚀刻的时间太长,特别是蚀刻液温度较高的情况下,耐蚀油墨或防护涂层浸渍时间过长,也同样起到上述的副作用和不良后果,因此时间控制上也要适当,不能浸得太久,一般不宜超过20~25min。 (四)化学蚀刻图纹装饰实例 1.装饰用的材料 装饰用的金属板材:普通钢材、不锈钢、铜及铜合金、铝及铝合金等,以不锈钢板为例说明,板厚l~3mm。 化工原料:丝印感光胶(例如浙江昆山市化工涂料厂生产的DH重氮型),耐酸油墨有 99-956型和99-200K型等一(广东顺德大良油墨厂产品),其他为常用化学化工药品。 2.工艺流程 不锈钢板→除油→水洗→干燥→丝网印刷→干燥→水浸→蚀刻图纹叶(片)水洗→除墨→水洗→抛光→水洗→着色→水洗叶(片)硬化处理→封闭处理→清洗叶(片)干燥→检验→产品。 3.具体操作及注意事项 (1)除油除油是为了使丝印油墨与板材有良好的附着力,所以金属板在印前必须彻底把油除干净。除油的方法很多,可以根据情况及需要选择,例如采用常规的化学除油、表面活性剂除油,甚至电解除油、超声除油等,也可以选用商品的专用除油剂。彻底清洗干净后,经干燥再转入丝网印刷。 (2)丝网印刷选用l50目不锈钢、聚酯或尼龙单丝维网,用绷网机固定在网框上,再用上浆器刮涂DH重氮型感光胶,涂覆2~3次,涂膜干燥后,将拍摄好的图纹黑白胶片附着在涂膜丝网上,经曝光、显影后,即制得丝印模板,然后再将不锈钢板、图纹模板固定在丝网印刷机对应位置上,采用碱溶性的耐酸油墨,印上所需要的图纹,自然干燥(或烘干)。如果烘烤,则温度不宜过高及时间不宜过长,否则油墨的碱溶性降低,到除油墨时,不易清除干净。一般情况下,自然干燥1h。烘干为55~60℃,4~5min。
晶圆制造工艺流程
晶圆制造工艺流程 Revised as of 23 November 2020
晶圆制造工艺流程 1、表面清洗 2、初次氧化 3、 CVD(Chemical Vapor deposition) 法沉积一层 Si3N4 (Hot CVD 或 LPCVD) 。(1)常压 CVD (Normal Pressure CVD) (2)低压 CVD (Low Pressure CVD) (3)热 CVD (Hot CVD)/(thermal CVD) (4)电浆增强 CVD (Plasma Enhanced CVD) (5)MOCVD (Metal Organic CVD) & 分子磊晶成长 (Molecular Beam Epitaxy) (6)外延生长法 (LPE) 4、涂敷光刻胶 (1)光刻胶的涂敷 (2)预烘 (pre bake) (3)曝光 (4)显影 (5)后烘 (post bake) (6)腐蚀 (etching)
(7)光刻胶的去除 5、此处用干法氧化法将氮化硅去除 6 、离子布植将硼离子 (B+3) 透过 SiO2 膜注入衬底,形成 P 型阱 7、去除光刻胶,放高温炉中进行退火处理 8、用热磷酸去除氮化硅层,掺杂磷 (P+5) 离子,形成 N 型阱 9、退火处理,然后用 HF 去除 SiO2 层 10、干法氧化法生成一层 SiO2 层,然后 LPCVD 沉积一层氮化硅 11、利用光刻技术和离子刻蚀技术,保留下栅隔离层上面的氮化硅层 12、湿法氧化,生长未有氮化硅保护的 SiO2 层,形成 PN 之间的隔离区 13、热磷酸去除氮化硅,然后用 HF 溶液去除栅隔离层位置的 SiO2 ,并重新生成品质更好的 SiO2 薄膜 , 作为栅极氧化层。 14、LPCVD 沉积多晶硅层,然后涂敷光阻进行光刻,以及等离子蚀刻技术,栅极结构,并氧化生成 SiO2 保护层。 15、表面涂敷光阻,去除 P 阱区的光阻,注入砷 (As) 离子,形成 NMOS 的源漏极。用同样的方法,在 N 阱区,注入 B 离子形成 PMOS 的源漏极。 16、利用 PECVD 沉积一层无掺杂氧化层,保护元件,并进行退火处理。 17、沉积掺杂硼磷的氧化层 18、溅镀第一层金属 (1)薄膜的沉积方法根据其用途的不同而不同,厚度通常小于 1um 。 (2)真空蒸发法( Evaporation Deposition )