生产物料退料控制程序

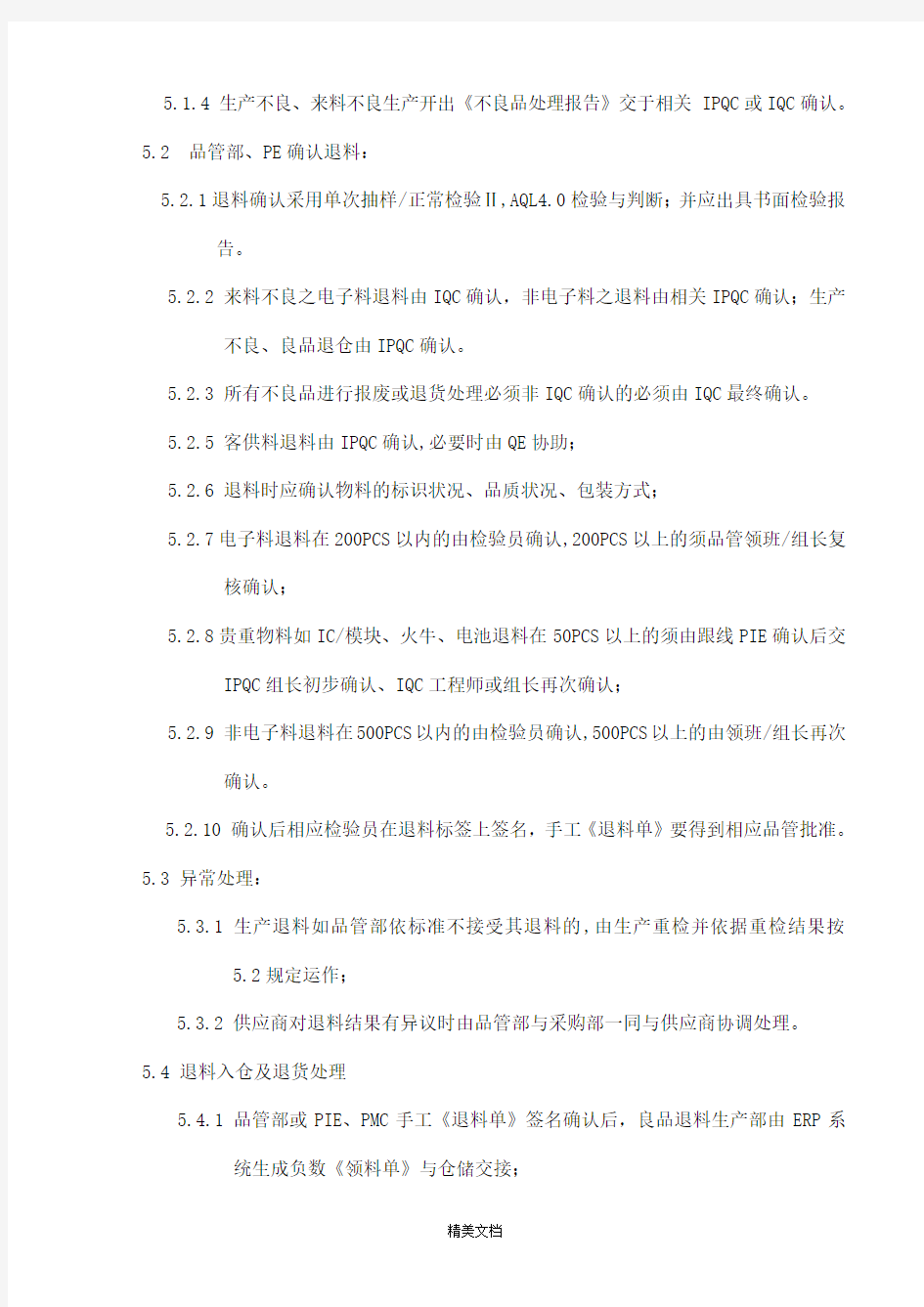
生产物料退料控制程序
1.目的:明确退料作业流程,使之能有效的进行管理。
2.适用范围:适用于公司生产不良、来料不良、良品退料的处理。
3.职责:
3.1 仓储科:清点、不良入库、与供应商办理退料。
3.2 生产部:退料按要求标识及交给IPQC确认。
3.3品质部:退料的检验确认。
3.4 采购部:统筹并与供应商签订退料协议,联系供应商回收退料、补料,协调退料争议。
3.5 PMC部:生产损坏之不良物料报废申请。
4. 定义:
4.1手工《退料单》:用于品质判定、退补货等的依据。
4.2负数《领料单》:ERP系统依据手工《退料单》生成。
4.3负数《外购入库单》:ERP系统依据手工《退料单》生成。
5.作业程序:
5.1 生产部退料:
5.1.1将生产不良物料依物料种类型号规格分开包装并标识;
5.1.2 选别出的来料不良须组长确认,物料依据供应商及不同物料分开包装, 如供应
商有特别需求,依供应商来料时包装方式包装并退料;来料不良或生产不良均
应在红色标签上进行标注。
5.1.3 良品退料生产开出手工《退料单》,通过ERP系统打负数《领料单》并交权责
人员签名确认后交于相关IPQC或IQC确认。
5.1.4 生产不良、来料不良生产开出《不良品处理报告》交于相关IPQC或IQC确认。
5.2 品管部、PE确认退料:
5.2.1退料确认采用单次抽样/正常检验Ⅱ,AQL4.0检验与判断;并应出具书面检验报
告。
5.2.2 来料不良之电子料退料由IQC确认,非电子料之退料由相关IPQC确认;生产
不良、良品退仓由IPQC确认。
5.2.3 所有不良品进行报废或退货处理必须非IQC确认的必须由IQC最终确认。
5.2.5 客供料退料由IPQC确认,必要时由QE协助;
5.2.6 退料时应确认物料的标识状况、品质状况、包装方式;
5.2.7电子料退料在200PCS以内的由检验员确认,200PCS以上的须品管领班/组长复
核确认;
5.2.8贵重物料如IC/模块、火牛、电池退料在50PCS以上的须由跟线PIE确认后交
IPQC组长初步确认、IQC工程师或组长再次确认;
5.2.9 非电子料退料在500PCS以内的由检验员确认,500PCS以上的由领班/组长再次
确认。
5.2.10 确认后相应检验员在退料标签上签名,手工《退料单》要得到相应品管批准。
5.3 异常处理:
5.3.1 生产退料如品管部依标准不接受其退料的,由生产重检并依据重检结果按
5.2规定运作;
5.3.2 供应商对退料结果有异议时由品管部与采购部一同与供应商协调处理。
5.4 退料入仓及退货处理
5.4.1 品管部或PIE、PMC手工《退料单》签名确认后,良品退料生产部由ERP系
统生成负数《领料单》与仓储交接;
5.4.2如属供应商来料不良的,仓储列印出负数《外购入库单》,由仓储主管签名后,
经财务部盖印才可放行退供应商;
5.4.3如属生产不良的,由仓务员统一收集整理,PMC部根据实际情况提出报废申
请;
5.5 补货或扣款:
5.5.1退料如需补货,手工《退料单》由PMC 交一份给采购部, 由PMC 督促采购安排
退补;如不需补货,采购部与供应商协调后确定是否扣款,通知财务部执行。
5.5.2 采购部需根据手工《退料单》通知供应商补货或取回退货。
5.6 退料作业注意事项:
5.6.1 必须注明退料原因,且有权责主管或代理人核准。
5.6.2 对于物、单不符的退回原部门重新处理后再依程序退料。
5.7 仓管需对退料单确认注意事项:
5.7.1 是否注明退料日期和订单号。
5.7.2 是否注明退料人。
5.7.3 是否注明退料原因及品管部相关人员签署。
5.7.4 是否有权责部门主管核准。
5.7.5所退物料的料号与规格是否一致。
6.支持性文件:无
7.记录:
7.1手工《退料单》
7.2负数《领料单》
7.3负数《外购入库单》