集装箱试验QC作业指导书
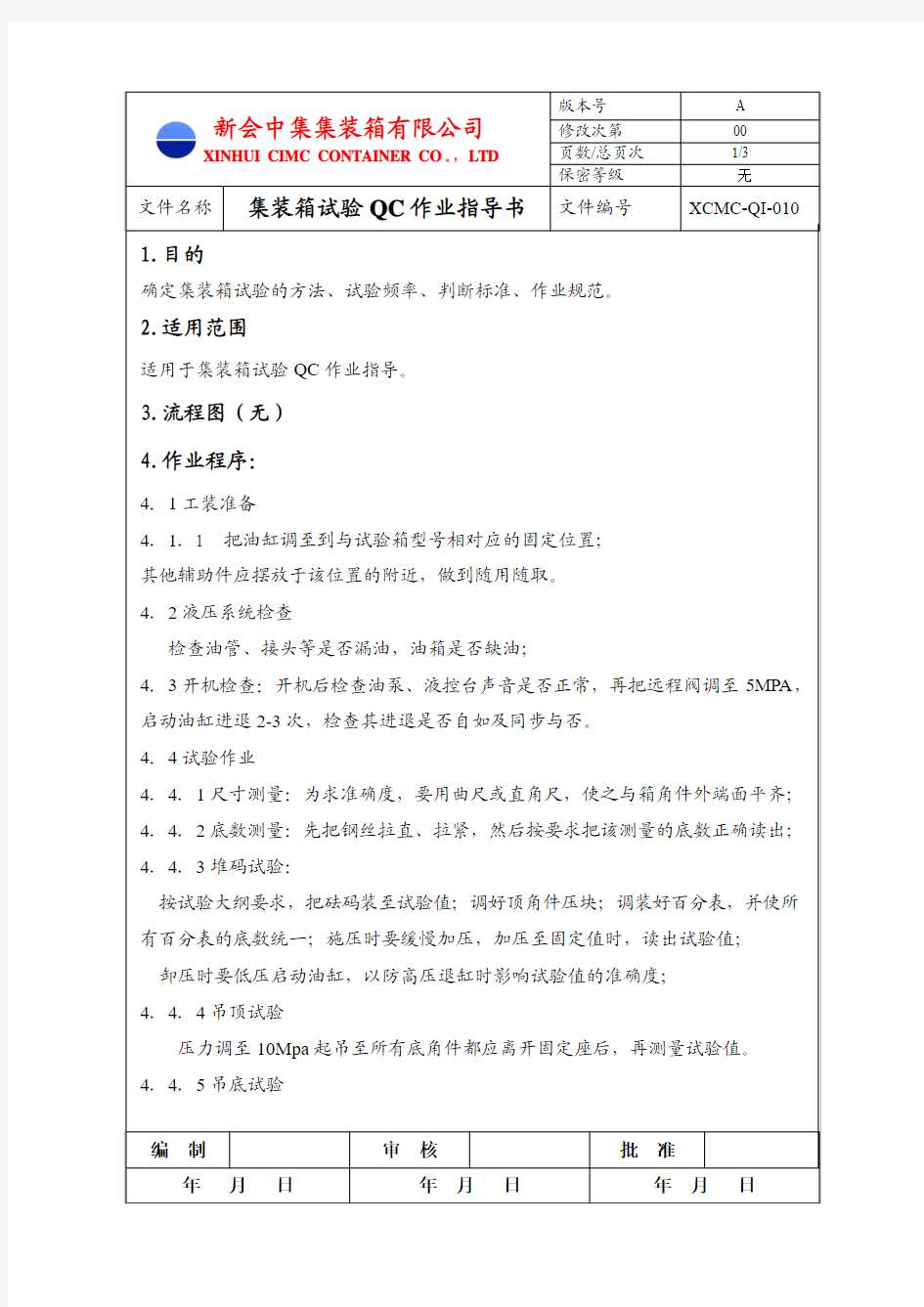

文件名称
文件名称
文件名称
机加工作业指导书
南京市江宁区怀银五金加工厂质量体系文件 产品图纸目录 RX/CP-7.5.1-01 受控状态: 版本号: A 编辑: 批准: 发放号: 2013-3-20 发布 2013-4-01实施
南京市江宁区怀银五金加工厂质量体系文件 机加工作业指导书 RX/CP-7.5.1-03 受控状态: 版本号: A 编辑: 批准: 发放号: 2013-3-20 发布 2013-4-01实施
HS/CP7.5-03 车床作业指导书及操作规范 1.目的:规范安全操作,防患于未然,杜绝安全隐患以达到安全生产并保证加工质量。2.范围:适用于本公司车床所有操作者。 3.作业内容及要求: 3.1.开机前检查机床各手柄位置及传动部位是否合理,并擦拭各滑动导轨,加施润滑油, 各油池、油盒、弹子油盅等按规定进行加油。 3.2.车头箱手柄挂到最低档,开机运行3分钟。并查看油窗油位是否达到了1/3油窗位置,否则通知有关人员按规定加油。 3.3.为了保证加工质量和提高工作效率,应根据工件材料、精度要求和机床、刀具、夹具等情况合理选择切削用量。加工铸件时,为了避免表面夹砂、硬化层等损坏刀具,在许可的条件下切削深度应大于夹砂或硬化层深度。 3.4.当粗、精加工在同一台机床上进行时,粗加工后一般应松开工件,待其冷却后重新装夹,松紧劲适中控制变形,否则要借助工装。 3.5.凡下面工序需要进行淬火、磨削或超声波探伤的工件表面,本工序加工的表面粗糙度Ra值不得大于6.3um。 3.6.粗加工时的倒角、倒园、槽深等都应按精加工余量加大或加深,以保证精加工后达到设计要求。 3.7.在本工序后无去尖角毛刺工序时,本工序加工产生的毛刺应在本工序去除。 3.8.在切削过程中,若机床、刀具、工件等发出不正常的声音,或加工表面的粗糙度突然变差,应立即退刀停车检查。 3.9.在批量生产中,必须进行首件检查,合格后方能继续加工。 3.10. 加工中进行自检测量时要正确使用量具。使用塞规、千分尺等时必须轻轻推入或旋入,不得用力过猛;使用卡尺、千分尺、百分表、千分表等时,事先应调好零位。3.11. 凡加工件成组或配加工的工件,加工后应作标记(或编号)。 3.12. 细长容易弯曲的轴类零件,在加工过程中如间断加工较长时间时,需在轴中间加中心托架,或将轴落下采取吊挂式存放。 4. 程序
首件作业指导书
履历表
1.内容: 为正确并顺利进行首件,而实施的作业准备。 2.责任部门: 成形车间 3. 责任者 首件作业者 4. 记录 《首件产品样品卡》 《成型科机台生产日报表》 《标准成形条件表》 《成形条件日常管理表》 5.步骤 首件前 5.1 首件前所须备齐的各类文件及表格: 5.1 相关文件有: (1)《工单》 (2)《标准成形条件表》 (3)《检查基准书》 (4)《作业指示书》 (5)《品质异常纪录》 5.2 相关表格有 (1)《成型首件确认表》 (2) 《模具日常保养记录表》 (3) 《成型科生产日报表》 (4) 《产品样品卡》 (5)《成形条件日常管理表》 (6)《标准成形条件表》 5.2 填写时的注意事项 5.2.1 《成形条件日常管理表》必须每天记录,如有更改立即报告上级主管。 5.2.2 当P/N、螺杆直径变了时,用新的《成形条件日常管理表》和《标准成形条 件表》进行填写,若只是取数变了,只须用新的《成形条件日常管理表》进 行填写。 5.2.3 在首件前备齐以上表格,先把能填写的地方填写完毕,剩余的部分进行完首 件后及时填写。 5. 3 进行首件前,先确认好《工单》、模具型号以及材料。
5. 4 生产前应确认机器、模具及附加设备的清洁情况,如机器导柱、导轨上的油污、 模具导柱及导孔上的油污、若上面粘有油污,应用酒精、碎布擦拭干净,对多油 及顶出易飞的产品机台应追加防护罩,对于模具导柱及导孔清扫后,再涂一层油。 5.5 对于生产中的机台每日09:00-12:00由成型技术人员对机台进行点检。 首件时 进行首件时,如需交换材料,先将其交换。(注意材料与前一个产品材料不同时, 必须确认材料的干燥温度) 5. 6 如机器内存有此产品成型条件表,则调出成型条件,如没有则依据《标准成型条 件表》输入成型条件,确认完前一次产品的条件后打开加热器进行预热。 5. 7 在安装模具前,请确认好取数、埋头孔尺寸以及水管位置提前安装水嘴。 5. 8 安装好模具和水管后,打开模温机进行模具加热,在此期间依据《成型首件表》 内容进行首件确认,确认完成后,用手接触模具,确认模具温度是否上升,模具 温度上升以后,再次设置低压保护。 5.9 开始启动机器时,由于条件还不稳定,必须使用缺料法慢慢进行注塑。备注:当 实际取数、实际循环时间与标准条件有所不同时,必须取得上级的确认,确认后 方可进行调试。制造部负责人负责将情况以EMAIL的形式反映给相关部门。 5.10 最开始时,先进行半自动注塑,连续2模取数检验,取数OK后,查看机器生产 管理画面,确认机器射出是否稳定,射出稳定后,取连续2模次外观检验,进行 确认。所有调机过程中的产品属于不良产品,应与良品区分开。外观确认OK后, 方可送首件。并将所有调机过程产生的产品和废料拿至物料房做好数量登记,打 开计数器。 首件检查 5.11检查员依据《检查基准书》做检查,检查OK后,首件作业者将机器升温开机作业, 不良品脱离机台。如产品检查NG,成型技术员确认原因并改善后重新进行首件 作业。 异常恢复 5.15 成型机紧急停止的时候,从全自动模式切换为手动模式 5.16解除成型机警报( 紧急停止) 5.17警报发生,产品隔离,通过成型机警报履历确认警报内容 5.18警报发生时的产品在模具内有剩余的时候,用手动动作取出实物进行确认,在 实物有发生缺陷的时候,报告组长或部长并对量产中产品的处理请求指示(像夜班等不在的时候向组长报告。处理内容通过组长向部长报告。) 5.19根据各警报方式进行逐个处理※关于处理,在需要成型条件调整及模具·附带
过程检验作业指导书
1.目的 为明确公司半成品灌、包装过程检验规范,确保成品品质得到有效控制,从而避免不合格品流入下一道工序或客户手中,特制定作业指导书。 2. 适用范围 本作业指导书适用于所有产品的批量生产,适用于本公司所有半成品灌、包装过程品质控制。 3. 解释 检验流程:首检/巡检。 检验标准与检验方法:任何批次半成品灌、包装过程均分两个步骤进行检验:首检、巡检。 4. 内容 4.1首件检验 4.1.1各生产车间在批量投产前,当班首件(包括设备更换、修理后及工艺参数改变,包装批号变更,使用的半成品批号变更、班组人员更换)时都必须在各工艺参数调整稳定并且都符合BOM(物料清单)表文件、生产作业指导书、标样规定要求后,自检及互检合格后,首件送给品质部进行检查。 4.1.2首件检查待确认样品车间组长负责进行标识,IPQC在接到首件后必须马上(在五分钟内)安排首件检查,以免耽误生产。 4.1.3考虑到首件检的时效限制,气密性试验及理化、卫生指标另行检验。 4.1.4品质部IPQC严格按照标样/生产作业指导书/检验规范进行检查,仅当所有的外观及功能性项目检查合格后才可判定首件检查结果合格,并将检查结果记录在首件确认表上,并确认首件检验记录表上必须明确记录该包装批号,及与其对应所使用的所有装配半成品批号,以保证从装配到包装过程批号的可追溯性。 4.1.5 首件检查合格后,即时回复生产线可进行批量灌/包装。
4.1.6首件检查不合格时,品质部IPQC必须马上(在五分钟内)反馈给生产车间并在首件确认表上好记录,生产车间必须重新调整好工艺参数后重新送样检查,品控部IPQC应重新填写首件确认表记录。 4.1.7同一批成品的灌、包装过程分段先后报检,先后检验、先后签复。 4.1.8 生产部接责任检验员签复的《装配首件确认表》和《包装首件确认表》后区别其确认段对应批量作业。 4.1.9 如果没有经过首件检查合格,生产车间就擅自投入生产,并因此而产生的不合格品,生产车间必须负全部责任。 4.1.10 首件检验产品由品质部负责留样以保证后续出现质量问题时的可追溯性。 4.2装配首检 4.2.1半成品合格标识: 待装配半成品物料卡品名品牌与计划装配产品品名品牌完全一致。有相关说明的,须按备注要求装配,物料卡上须签有品质部签字盖章。目测。 4.2.2装配机: 选用装配机需与待装配产品状态相适应。换品种装配前,装配机须确认已经拆洗干净至料斗内、各通料管道及触料之相关零部件完全无残余剩料并消毒吹干后方可下料(若需要转料斗装料时装料勺须干净并消好毒,易起泡的半成品下料时切忌下料过急以免溅起泡)。下完料后的空桶及原桶盖仍盖好以防生产完有需要时重装回退料。流水线上与待生产品种无关的物料须及时清理出线。目测。 4.2.3半成品外观、色泽、气味:取成品标准样板一支,核对其符合成品标准样板内容物之外观状态、透度、目测稠度、细腻度、色泽和气味,并要求无任何杂质、分离等异状。目测、嗅、手感。 4.2.4同批装配产品总抽样数不得少于30PCS(总装配量少于30PCS除外),当出现个别较严重异常(如漏料等)时,需加大两倍抽检量,仍异常,则要求机台隔离该时段装配品全检,必要时停机处理。 4.3包装首检 完成首件确认后,进行首期检查。首期检查一般抽取10pcs,核对彩盒/套装盒/标签/说明书/吸塑/外盒包装/收膜/成品配套完整性。 4.3巡检
机加工检验作业指导书
机加工检验作业指导书 Company Document number:WUUT-WUUY-WBBGB-BWYTT-1982GT
机加工检验作业指导书 一、适用范围 生产部各部门自制件及外协件 二、作业要求 1、凡机械加工件必须符合产品图样、工艺规程和作业要求。 2、经加工的零件表面不允许有锈蚀和磕碰、划伤、裂纹等缺 陷。 3、除有特殊要求外,加工后的零件不允许留有尖棱、尖角和 毛刺。 4、滚压精加工的表面,滚压后不得有剥离及脱皮现象。 5、精加工后的表面、摩擦面和定位面等工作表面不允许在其 上打印标记。 6、经加工后的零件在搬运、存放时,必须防止受到损伤、腐 蚀及变形。 7、成组配对加工的零件需有标记。 三、未注尺寸公差参阅附件:技术标准 JB/T 5936-91 四、未注形状和位置公差参阅附件:技术标准 JB/T 5936-91 五、未注公差角度的极限偏差参阅附件:技术标准 JB/T 5936-91 六、螺纹、键和键槽参阅附件:技术标准 JB/T 5936-91 七、中心孔 1、图样中未注明、加工中又需要中心孔的零件,在不影响使 用和外观的情况下,加工后中心孔可以保留。 2、中心孔需符合GB 145的规定。 八、检验规则 1、凡经机械加工件,由制造厂质量检验部门按图样、有关技 术文件和本要求进行检查和验收。 2、机械加工件的外观按规定要求进行检查。 3、主要机械加工件需每件检查几何形状与尺寸。 九、标志
1、入库的机械加工件应有的标志 2、标志的位置应不使机械加工件的质量受到损伤。 3、机械加工件入库应附有吊牌。其中应注明:名称、零件名 称、图号;制造日期。 编制:标准:审核:审批:
机械加工作业指导书
机械加工作业指导书标准化管理处编码[BBX968T-XBB8968-NNJ668-MM9N]
浙江超伟机械有限公司质量管理体系文件 机械加工作业指导书 手册编号:QB/—2013 版本号:A/0 分发号: 2013年 7 月 1 日发布 2013年 87 月1 日实施 浙江超伟机械有限公司发布 电焊机作业规范 ⑴合理选择电源\线容量; ⑵用规定电压等级; ⑶用专用防护罩,穿戴专用手套、服装; ⑷使用专用电焊线,不可用普通电线代替; ⑸电流调节要适当; ⑹注意防潮,防止电焊机因潮湿发生短路造成损坏; ⑺不可在潮湿的环境中使用,防止触电; ⑻电焊机置放场地必须清洁,干燥,绝对不可以有铁渣等金属物体,以防工作 是产生磁力,造成电焊机短路,导致损坏;
⑼使用完毕,必须切断电源方可离开; ⑽移动电焊机时不可直接拉电源线或焊接线。 砂轮切割机作业规范 ⑴轮切割机属移动性机具,在使用前需空载运行10秒,检查电机及开关是否正 常,砂轮片是否安装牢固; ⑵被切割物料需装夹牢固,不允许在不做装夹的情况下作业; ⑶切割进轮速度需合理,不得过快进速,造成砂轮片快速磨损; ⑷切割抛溅需做挡阻及收集尘粒; ⑸操作人员需偏离砂轮平面线,防止砂粒及砂轮片破碎时伤人; ⑹更换砂轮片时,需先清除防护罩内堆积物,使砂轮片正确就位在轴径上,不得 敲击砂轮片,并随之锁紧,再用手转动,检查是否安装正确,再做空载运转10秒,无异常时方可使用。 锯床作业规范 ⑴锯床原则上只作圆材及厚材切割用,不准锯4mm以下材料及φ20以下圆材; ⑵每班前对各活动部分加一次油,对滑枕部位,每班需加两次油; ⑶需对被锯物装夹紧固,防止松动后,造成锯割不准及崩断锯条; ⑷合理正常安装锯条,注意锯条平直度及拉紧螺杆的适当力度; ⑸检查物料装夹平行度,使与锯割面垂直;
机械加工通用作业指导书
机械加工通用作业指导书 1、操作者应仔细看清图纸和工艺文件的各项说明,保持图纸和工艺文件的清洁与完整,并应严格按设计图纸、工艺规程和技术标准进行零部件的加工,不得随意自行更改。 2、操作者按照工艺要求查看借用的工、夹、量、刀具是否符合工艺及使用要求,若有疑问,应立即与组长或车间生产管理者联系。 3、操作者应将工、夹、量、刀具分别整齐地放置在工具箱上或其它适当的地方,但不准直接放在机床上,并应妥善保管好,不得任意拆卸而改变原来尺寸或形状。 4、在加工前,操作者首先应检查、抽查毛坯或经由上道工序加工并和本工序有关的尺寸,以确定余量是否符合工艺要求。 5、操作者应按照工艺规定的定位基面安装零件。工艺未规定定位基面的,允许操作者自行选择定位基面和装夹方法,但是必须保证加工出来的工件符合图纸和工艺上的尺寸和精度要求。在装夹工具前,应将夹具和工件清理干净,在定位基面上不得有铁屑、毛刺、污物及磕碰现象。 6、预压紧工件后,应按工艺要求进行工件的校正,若工艺未作出规定时,可按下列方法校正工件: 6.1、当在本工序或本工步中加工到成品尺寸,且以后该加工面不再加工,装配时也不再调整或刮研时,可以按定位基面到加工面技术要求的1/3值校正,最后加工完成后应保证图纸中的技术要求。 6.2、在本工序或本工步中加工的加工面以后尚需加工或刮研,
则按该加工面下道工序余量的1/3值校正,加工后要按此检验。 6.3、在本工序或本工步中加工的加工面到成品尺寸,以后该加工面不再加工,且图纸、工艺卡片内对该加工面与定位面无任何要求时,加工后应达到通用技术标准。 7、按工艺要求进行压紧,如工艺上无要求,零件压紧时注意压紧力的位置、大小和方向,并允许自加各种辅助支承,以增强刚性。压紧前与压紧后都要测量,防止变形和磕碰。 8、凡加工面末到成品尺寸而工艺卡片又未规定工序的粗糙度时,粗车、粗铣、粗刨、粗镗和粗插的表面粗糙度应为Ra6.3(△4),磨削前的各种表面粗糙Z应为Rd3.2(△5),粗磨时外围的表面粗糙度应为Ra0.8(△7),平面、轴、孔互为Ral.6(△6);刮研前的加工面应为Ra3.2~Ral.6(△5~△6)。 9、当工艺未规定时,工件的首件检验应该在自由状态下进行,不得压紧在起具上。换刀后的首件也应首检。 10、对连续加工的工序或工步,为避免最后成批报废,操作者应分工序及工步进行自检,必要时可提请检验员配合检验。 11、倒角与倒棱、沉割槽时都应按余量加大或加深,保证加工完成后达到图纸要求和国家标准。 12、图纸或工艺中未规定的棱边处一律倒钝,且一般情况下应在加工有关面时进行。车内外螺纹时口端都要倒成和螺距的大小及牙形角一样的成形角,零件倒毛刺应由操作者在本工序完成。 13、工件在各工序加工后应由操作者保持清洁,达到无屑、无水、
机械加工产品检验作业指导书
一汽解放青岛汽车厂质量保证部技术文件 编号:IPQC-JYZD-7-2009 批准:宋宗强 机械加工产品 检验作业指导书 2008年12月31日发布2009年1月1日实施
一汽解放青岛汽车厂质量保证部发布
前言 本检验作业指导书依据有关汽车标准及一汽解放青岛汽车厂技术文件制定。是一汽解放青岛汽车厂质量保证部技术文件之一。 本检验作业指导书与国家标准、企业标准及相关技术文件相一致。 从实施之日起,原《IPQC-JYZD-7-2008机械加工产品验作业指导书》同时废止。各相关部门检验机械加工产品质量时,都需要按本检验作业指导书的规定执行。 本标准由一汽解放青岛汽车厂质量保证部起草。 本检验作业指导书起草人:林桂升 本检验作业指导书审核人:石建通
1 主要内容与适用范围 本检验作业指导书规定了机械加工产品的检验方式及质量记录。 本检验作业指导书主要适用于机加工车间。 2 引用标准 下列标准包括的条文,通过在本检验作业指导书中的引用而构成本标准的条文。在本检验作业指导书发布时,所示版本均为有效。所有标准都会被修订,使用本标准的各方应探讨使用下列标准最新版本的可能性。 CA/CBG-1-82 切削零件未注公差尺寸的公差 CA/CBG-9-91 未注公差角度的极限偏差 3 检验及质量记录规定 3.1所有机加工产品必须按产品标准、技术要求等进行自检控制。 3.2检验零件时,按控制计划合理选用量检具,并正确操作。 3.3未注公差尺寸的极限偏差
3.3.2 两孔的中心距和孔与零件边缘距离的未注公差尺寸的公差按下表执行。(以孔径为基本尺寸查选。当两孔径不相等时,其轴心距的公差按两孔直径的算术平均值确定。)如 3.3.4 L查选。
精加工过程检验作业指导书
公司版本Ver:A0 工作文件页数第 1 页共 5 页 1 目的 1.1 为规范深加工过程质检检验作业,确保产品符合技术图纸、标准性能及客户要求,特制 定此检验指导书。 2 适用范围 2.1 适用于公司深加工车间精加工模块过程质检质量控制。 3 职责与权限 3.1职责 3.1.1按订单及技术图纸,对加工后的产品是否符合订单及技术图纸要求、相关标准要求 负责; 3.1.2对岗位生产产品质量控制,对产品加工时首检、批量生产时抽检、结束加工作业时 尾检,保证产品合格性负责; 3.1.3 对深加工生产过程、班组操作作业方式进行监督; 3.1.4 对工作交接不清楚,造成质量事故负责; 3.1.5 对违反检验规程,造成漏检或批量质量事故负责; 3.1.6 对填写相关检验记录和产品标识的真实、完整、清晰负责; 3.1.7 对问题反映不及时或未反映,造成延误交货期,影响生产及造成客户或下一工序 投诉负责; 3.1.8 对上级下发的指令不执行或跟进不完全,而造成质量事故负责; 3.2权限 3.2.1对深加工产品生产过程产品质量控制权; 3.2.2对深加工生产产品工艺、班组操作作业方式监督权; 3.2.3对深加工过程质量判定权; 3.2.4对深加工继续生产不合格品的制止权; 3.2.5对深加工员工执行自检作业的监督权; 编制审核批准发布日期年月日 实施日期年月日
公司版本Ver:A0 工作文件页数第 2 页共 5 页 3.2.6对深加工检验区域内的型材和所使用的计量器具的防护权 3.2.7对深加工生产车间改善生产工艺、操作方式的建议权; 4 工作内容 4.1接班 4.1.1接班前须提前15分钟到深加工车间,参加班前会; 4.1.2班前会班长主要强调相关重要事项及相关质量问题提示等,并在检验过程中应用控 制;接班时与上一班质检进行当面工作及共用检具交接并在交接班记录及点检表上 签名; 4.1.3与上班质检交接正常生产的产品质量信息及注意事项,样板的交接、不良品、待处 理品摆放位置及了解不合格品的原因,跟进上一班质检交代的待处理品; 4.2检验准备 4.2.1接班后查看当班排产计划,针对班前会提示当班生产控制重点;对排产单上品质专 员备注的品质信息及订单进行了解,特别新客户、新产品、不同合金、订单特殊 要求及备注等;准备好需要做相关检验记录表格; 4.2.2并将本岗位的班前会重点提示内容,记录在当班交接记录本重点提示框内,以利于 工作指导和监督; 4.2.3 开始检测前使用的对检测工具(量具)进行检查校对,保障检测工具准确性; 4.2来料产品检验 4.2.1 产品开始生产前核对订单、型号、表面质量、长度、颜色、产品尺寸、加工 方式是否一致,准备好相关的加工图纸; 4.2.1.1 核对订单,型号是否与技术图纸一致,截面尺寸是否符合客户图纸要求,并做 相关记录;型号不确定时通知品质专员进行确认;特殊设计型材必要时对开口 尺寸5%抽检并记录; 4.2.1.2 喷涂氧化料按照订单要求检测膜厚,注意客户有无特殊要求,客户没有特殊要 求按照相关标准验收; 4.2.1.3 检测来料长度与订单要求是否一致,核对来料长度能否满足开锯倍数; 4.2.1.4 了解订单要求的加工方式以及客户特殊要求,并在生产过程中注意控制; 硬度:硬度检验按比例5%抽检,检测按照型材大小使用韦氏硬度钳和里氏硬度
ISO9001-2015首件确认作业指导书
首件确认作业指导书 (ISO9001:2015) 1.目的 对生产新订单的首件产品进行检验,防止批量性的问题出现,保证生产产品的质量 2.适用范围 适用新订单生产前的产品。 3.职责 生产部:负责首样的制作、自检、签名确认及送检的工作。 品质部:负责根据工厂订单、生产通知单核对资料、检验性能。 工程部:负责核对首样是否与BOM一致。 4.作业流程 生产部:1、接到新订单产品时,由拉长按工厂订单及生产通知单制作首件 2、根据工厂订单及生产通知单核对资料进行自检,并在首件检验 报告中填写订单号、机型、颜色、线别、首件数量、送检日期 与时间且签名确认 3、自检完毕后,将产品连同首样检验报告一并送至品质部交给 PQA进行复检
品质部:1、在接到生产部的首件样品后,按照成品检验作业指导书进行外观及性能检测 2、按照包材资料核对铭牌、彩盒、外箱、说明书、保修卡的信息 3、按照工厂订单及生产通知单核对包装方式及客户特要求的注意事项 4、检验、核对完毕后,按照首样检验报告的项目进行签字确认, 然后将产品与首样检验报告一并送至工程部交给PE进行复查工程部:1、在接到品质部的首件样品后,按照BOM表核对首件是否与BOM 表一致 2、按照工厂订单及生产通知单对首件进行复查 3、核对完毕后,在首样检验报告中的“PCBA板的型号”、“电源线厂家及规格”、“发热丝厂家及规格”、“各部件结构是否符合标准”的位置进行确认,并签名填写完成时间 4、将产品与首样检验报告交付给生产部拉长,并放置在拉头的位置,一张订单生产完后,由拉长拿着成品入库单及首件检验报告给PQA签字 5、首件确认时间:电动类30分钟(切菜机、雪糕机)、加热类1小时(干果机)5.首件确认异常处理: 品质部与工程部任何一个部门在确认首样的过程中出现了异常,都必须将不良信息及时反馈给生产部,若是外观性问题,需要更换一台OK的首样产品,重新
机械加工检验标准及方法
机加工检验规范 1 范围 本标准适用于机加工各检验特性的检验。在本标准中,机加工包括切削加工(车,铣,刨,磨,镗),钻加工,冲加工等,本标准规定了尺寸检验的基本原则、对环境的要求、线性尺寸公差要求、形位公差要求、螺纹的检验、表面粗糙度的检验、外观检验标准、检验制度。 2 规范性引用文件 下列文件对于本文件的应用是必不可少的,其最新版本(包括所有的修改单)适用于本文件。GB/T 1804- 2000 一般公差未注公差的线性和角度尺寸的公差 GB/T 1184 - 1996 形状和位置公差未注公差值 GB/T 15055-2007 冲压件未注公差尺寸极限偏差 GB/T 13916-2002 冲压件形状和位置未注公差 GB/T 6403.4-2008 零件的倒圆与倒角 QGS12.05 《机械加工过程检验作业指导书》 QGS12.05-02 《过程巡检记录表(机械车间)》 QGS12.05-03 《过程检验记录表(机械车间)》 QGS12.05-04 《机械加工过程检验不合格记录表》 QGS12.07-03 《最终检验记录表(3)》 QPS13 《不合格品控制程序》 QGS12.03 《委外机加工件检验作业指导书》 3 检验条件 户内,环境温度:-10℃~+55℃。 注:部分精密测量仪器使用时需要工作台要稳固,远离大型机加工设备,起重设备等振源。 4 检验原则 4.1 基本原则 理论上应只接收位于规定的尺寸验收极限的工件。对于有配合要求的工件,其尺寸检验应符合泰勒原则,有配合要求的孔,轴,其局部实际尺寸与形状误差都要控制在尺寸公差带以内。 4.2 阿贝原则 被测量线应处于被测量线或被测量线的延长线上。 4.3 最小变形原则 为了保证测量结果的准确可靠,应尽量使各种因素的影响而产生的变形为最小。 4.4 最短尺寸链原则 为保证一定的测量精度,测量链的环节应减到最少,即测量链应最短。 4.5 封闭原则 在测量中,如能满足封闭条件,则其间隔偏差的总和为零,即是封闭原则。 4.6 基准统一原则 测量基准应与设计基准、工艺基准保持一致。 4.7 其他规定 尺寸测量的结果和形状误差的测量结果综合考虑,确定工件是否合格。 5 检验要求 5.1 线性尺寸和角度尺寸公差 5.1.1基本要求 图纸上对线性尺寸和角度尺寸公差明确公差要求的,按照图纸要求进行检验;技术要求注明(未注)公差的,按照要求进行判定。 注:线性尺寸未注公差一般按照GB/T 1804-2000 中等精度(M)进行检验,各项要素未注
产品检验作业指导书介绍
XXXXX公司作业文件 检验作业指导书 1 主题内容与适用范围 本指导书规定了服装生产用面料、里料和辅料的进货质量检验、生产过程中的工序质量检验、产品完工质量检验和成衣出厂质量检验、外协产品的质量检验的内容和方法以及外检的项目。本规定适用于服装生产过程中的所有质量检验工作。 2 目的对产品的特性进行监视和测量,以验证产品的质量要求已得到满足。 3 规范性引用文件 3. 1 GB / T2660—1999 衬衫 3. 2 GB / T2666—2001 男、女西裤 3. 3 GB / T13661—1992 一般防护服 3. 4 GB/12014---2009 防静电工作服 3. 5 GB/8965---2009 阻燃工作服 3. 6 FZ / T80004—1998 服装成品出厂检验规则 3. 7 FZ / T81008—2004 茄克衫 4 职责 4. 1 技术质量部负责本检验规程的制定。 4. 2 技术质量部负责组织服装生产全过程的质量检验工作,负责本检验规程的贯彻实施。 4. 3 质量检验员负责按本检验作业指导书的规定实施产品的质量检验工作。 5 检验的方法和内容 5.1 进货质量检验 5.1.1 采购物资按对服装产品质量影响程度的分类 A类:指构成服装产品的主要部分和关键部分,直接影响服装的外观质量和使用性能,有可能导致顾客严重投诉的采购产品。如面料、特殊服装的里料、有纺粘合衬、缝纫线、拉链、绣花、印花等。 B类:指构成服装产品的其它部分,一般不会影响服装的使用效果,即使略有影响,也可以采取补救措施的采购产品。如一般里料、钮扣、四合扣、无纺粘合衬、口袋布、垫肩、松紧、商标等。 C类:指不直接用于服装产品本身,但又起到服装保护作用的采购产品。如包装纸箱、塑
首件检验流程作业指导书
1、目的 本文件规定了公司产品生产过程中对新品首件检验、批首件检验的要求及规定,以利于整批产品加工得到满足顾客的要求。 2 适用范围 本文件规定了公司在生产过程中对新品的首件检验、批首件检验的要求及工作程序。 本规定适用于公司在生产过程中对新品的首件检验、批首件检验的控制。 3 职责 3.1生产部门负责组织安排首件检验工作。 3.2未经新品首件、批首件检验或首件检验不合格,而擅自生产产品,由此引起的质量事故,由直接责任者负责。 3.3检验员、生产线负责人对首件检验的正确性负责。 3.4 对首件确认工作未完成,检验员开始出具质量凭证,造成的质量事故,责任由检验员负责。 4 控制要求 4.1 对生产部门首次连续性生产的第一个完工的半成品和成品,必须经过首件检验和确认。 4.2 对于常规生产产品,须按批次进行首件检验。 4.3由于设备、工艺等原因造成的停机,停产后的再生产要进行首件检验和确认。 4. 4 产品材料、规格变更后投入生产时要进行首件检验和确认。 4.5新品首件检验时,应由生产单位负责通知检验有关人员,按现行有效的图纸、清单(或顾客提供的样件)、工艺文件进行检验,检验员填写检验记录,检验合格后在首件卡上签字,并将卡片挂在首件产品上做好首件标记;首件检验不合格应立即退回,重做首件,并做好记录。未经首件检验合格的产品不得进行验收。 4.6 首件作为批量生产的样件,由生产部门负责保留到全批生产结束后才能最后送交。 4.7首件检验中应检查产品生产过程所用的所有原辅材料必须与规定相符。 5工作程序 5.1 在首件制作过程中,生产线负责人、检验人员应到生产现场监督检查实际生产者按生产工艺流程,根据现行有效的生产工艺文件自行完成首件,并对每一生产工序进行监督检查,发现问题及时予以纠正解决。 制作:审批:核准:
制程QC作业指导书
制程QC作业指导书 1.目的 规范各工序的检验流程,防止批量事故的发生,正确引导IPQC做到及时发现问题,反映问题及跟进问题的改善措施,协助产线做的产品品质符合规定的品质标准确,满足市场和客户的需求。 2.范围 适用于各工序的制程检验员更加明确自己的工作职责. 3.定义 3.1 严重缺陷:不良缺陷,足使产品失去规定的主要或全部功能,特別情况下可能帶来安全問題, 或者为客戶或市场拒绝接受的特別规定之缺点,称为严重缺陷. 3.2 主要缺陷:不良缺陷,足使产品失去部分功能,或者相对严重的结构及外观异常,从而明显 降低产品使用性的缺点,称为主要缺陷. 3.3 次要缺陷:不良缺陷,可以造成产品部分性能偏差或一般外观缺陷, ,但不会影响产品使用 性能,称为次要缺陷. 3.4 抽样方案 4.责任部门 生产部:负责按照PMC排产计划执行标准作业. 品管部:负责首件和不良品的确认,生产作业的监督和记录,异常的反馈及跟踪. 工程部:负责对发生异常时的原因分析和提供处理异常的改善措施. 5.作业程序 5.1首检的时机:当人(操作员)、机(设备)、物(物料)、法(工艺条件)中的任何一项变更 时须作首检,如常规的每天上班时、换型号、换治具、调参数时均须作首检。 5.2首检的取样数量:开料至裁切段为每次1—2张,分粒至覆膜段为每次5片, 具体以各段相应的《检验指导书》为准。 5.3首检的程序: 5.3.1各机台操作员在确定设备运转正常、参数符合参数表、物料/材料符合规格书后,生产首 件产品,并按相应的工序的检验标准检查是否符合品质要求。 5.3.2生产员工自检OK后交给生产组长作首件确认, 5.3.3生产组长首检OK后再交给相应QC作最终首件确认。 5.3.4 常规产品的非首次批量经5.3.1---5.3.3首检OK后即可开始批量生产, 此文件属【深圳市雅视科技有限公司】之体系管理文件,未经【深圳市雅视科技有限公司】的许可,不得擅自复印!
机械零件检验作业指导书
1、目的 本文件旨在规定零件检验的质量保证、技术要求。 2、范围 本文件适用于本公司所有的机械加工类零件。 3、引用标准 :无 4、定义: 无。 5、检验方法 5.1零件的表面处理的检验 依照下列四个文件检验 1、零件氧化发黑检验作业指导书 2、零件镀铬检验作业指导书 3、零件镀锌检验作业指导书 4、零件镀镍检验作业指导书 5.2 表面粗糙镀检验 5.2.1、目测检测 当工件表面粗糙度比规定的粗糙度明显的好或不好,不需使用更精确的方法检验,工件表面存在着明显影响表面功能的表面缺陷,选择目测检验判定。 5.2.2、比较检测 若用目测检查不能做出判定,可采用视觉或显微镜将被测表面与粗糙度比较样块比较判定。 5.3硬度检验:
根据图纸的技术要求用洛氏硬度机、布氏硬度机检验零件的硬度。 5.4 尺寸公差: 5.4.1标注尺寸公差 对于尺寸公差带在0.1以内的要用千分尺或比千分尺精度更高的检验仪器检验,对于公差带在0.1以上的,可用游标卡尺检验。 5.4.2未标注尺寸公差 按GB/T 1804-f标准检验 GB/T 1804-f 基本尺寸 0.5-3 >3-6 >6-30 >30-120 >120-400 >400-1000 >1000公差 ±0.05 ±0.05 ±0.1 ±0.15 ±0.2 ±0.3 ±0.5 5.5形状公差 5.5.1直线度的检验 用指示器法检验直线度。 其检验方法为:将被测零件支撑在平板上,平板工作面为检验基准,按一定的方式(此出用直线式)布点,用指示器对被测表面上各测点进行检验并记录所测数据,然后,按一定的方法评定其误差值。
指示器直线度、平面度布点示意图 5.5.2平面度的检验 用指示器法检验零件的平面度 5.6位置度公差 5.6.1平行度检验 常用平板、心轴或V型架来模拟平面、孔或轴作基准,然后检验被测线、面上各点到基准的距离之差,以最大相对差作为平行度误差。 5.6.2垂直度检验 有光隙法检验垂直度,其方法为: 1.按下图所示,将被测零件的基准和宽座角尺放在检验平板上,并用塞尺(厚薄规)检查是否接触良好(以最薄的塞尺不能插入为准) 2.移动宽座角尺,对着被测表面轻轻靠近,观察光隙部位的光隙大小,用厚薄规检查最大和最小光隙尺寸值,并将其值记录下来。 3.最大光隙值减去最小光隙值即为垂直度误差。
检验作业指导书
检验作业指导书 1.进货检验 1.1目的 进货检验就是为了有效控制供方不合格品进入仓库,确保供方所提供的产品能满足公司及客户的质量要求。 1.2适用范围 适用于公司外购或委外加工的原材料、零部(配)件、半成品、成品的检验1.3职责 负责供方物料的质量判定与质量状态的标识 1.4作业程序 1.4.1进货检验部分 1、进货检验根据采购部下发的物资采购订单每周汇总表做好检验准备,准 备好测量工具(游标卡尺,卷尺,角度尺等)、工艺、零件图纸、检具及检验标准等; 2、仓管员收到送货单后进行检验,根据送货单上的订单号,规格,核对产 品是否正确。核对无误后根据 MIL-STD-105E抽样标准进行抽样检验。检验合格后在送货单上签字,并做好《进货检验记录》,次日交质管部; 3、产品经检验判定合格后须贴好合格标签,并做入库处理。产品不合格须 贴不合格标签,作退货或挑选处理,并立即开出《不合格品处理单》,经质管部长或以上领导审核签字后及时反馈供方、业务,检验员还须对退货的产品以及不良品挑选过程作好跟踪和验证; 4、对于供方送检的新产品的首件,进货检验员要填写《首件检验表》交研 发部门确认,最终由检验部门来判定该产品是否合格,确认后立即将确认结果传真供方。 5、各项记录要规范填写,数据要真实,特别是现象的描述要清晰、易懂,必要 事可以用简图来描述。 1.5检验方法 1.5.1外观检验:一般采取目测,手感,样板对照等; 1.5.2尺寸规格检验:卡尺,卷尺,角度尺,千分尺,螺纹环规等;
1.5.3承重测试:按指导书要求加载相应的重物作禁止和滚动测试; 1.5.4组装测试:与配套的产品进行组装。 1.6检验项目 1.6.1管材类 1、依采购订单型号,规格与送货单核对,有无质保书; 2、管材表面擦拭干净,检查表面有无焊道开裂、模具压痕及材质麻点、凹 坑等,方管四处R角是否一致; 3、检查尺寸是否正确,方管及圆管壁厚公差±0.05; 4、管材直线度、平面度、扭曲度能否满足加工要求,公差范围参照《管材 的质量要求》; 5、表面要求无严重的划伤,无明显的麻点凹坑,无锈斑等; 6、一般管材接头管≤2%, 如有特殊要求则不可有接头管; 7、特殊管材类检查捆包是否符合要求,有无因保护不当导致运输过程中造 成的划伤。 1.6.2冲压件 1、依采购订单型号,规格与送货单核对; 2、依零件图纸检验其尺寸,方向,材质等是否符合要求; 3、进行组装配合,以了解其功能是否可行; 4、检查毛边是否过大(落料毛边,剪板毛边,冲孔毛刺,攻丝毛刺等), 以不刮手为准。 1.6.3五金件、标准件:螺丝,螺母,铆钉,脚座等 1、依采购订单型号,规格与送货单核对,不锈钢系列须提供材质证明; 2、螺母片,管内套及各种螺母须用螺纹塞规检验,尺寸及螺纹垂直度是否 达到要求; 3、各类螺钉的螺纹须用螺纹环规进行测试检验; 4、铆钉系列要做好与配套产品的组装,并进行强度测试; 5、脚座和轮子的螺栓规格是否和订单一样,要用螺纹环规进行测试; 6、特殊螺丝要做好组配测试(例如:沉头螺丝等)。 1.7抽样检验标准
数控车床作业指导书模板
数控机床作业指导书及操作规范 1.目的:明确工作职责,确保加工的合理性、正确性及可操作性。 规范安全操作,防患于未然,杜绝安全隐患以达到安全生产并保证加工质量。 2.范围:适用于数控机床所有操作者。 3.职责:指导数控机床操作者按CNC加工及设备维护、保养等工作。 4.工作流程 (一):作业流程 1)查看当班作业计划 2)阅读图纸及工艺------CNC工程师编制加工程序 3)核对图纸、工艺是否相符 4)校表、分中、找正工件 5)拷贝并核对程序 6)加工并自检 7)送检 (二):基本作业 1)查看当班作业计划:按作业计划顺序及进度要求进行作业,以满足生产进度 的需要。 2)核对图纸程序单及工件:将图纸打开与工件进行核对,清楚工件的装夹方向、 基准点、所使用的刀具、夹具等。 3)校对工、量具:按图纸及加工工艺领取加工所需工、量具并进行校对。 4)机床回零:操作前将机床各轴回零。 5)清理工作台:把工作台清理干净,准备好所需用的垫块等。 6)校表分中:装夹好工件后进行校表,打表应选最大面来进行校正,校平衡时 应取基准边来校正,分中时取边的中心位置进行分中(碰单边时不允许使用感应寻边器),分好中后必须输入指令进行检查(G0G90G54X0Y0),输入指令前要把主轴先抬高到安全高度。
7)拷贝程序及校对:拷程序前要看清程序单上的程序名是否和电脑上的一致, 打开程序对里面的加工参数进行检查,如有不合理之处将其改正过来,对每一条程序都要进行刀路模拟,确认无误后方可加工。 8)加工工件及检查:加工前准备好所需刀具,对好刀,开始加工下刀到安全高 度后,要检查机上的参数是否有误方可加工,加工过程中要注意检查刀具磨损,如刀具磨损要停下来进行刀具半径及长度补偿量的调整,调整完成后再继续加工。 9)自检:所有工件加工完了以后都要进行自检,譬如一些加工没有到位,接面 没接顺等,发现问题须马上解决。 10)首件检验:在批量生产中,必须进行首件检查,合格后方能继续加工。靠程 序加工及空间尺寸,加工落活后无法检测的件,落活前或在加工过程中通知和协助检验员到机床上进行检验。 11)送检:工件加工完以后及时送检,不得锈蚀,送检过程中避免磕碰,并在图 纸上加工工艺栏及轮班作业计划签字(外加工件附送货单及自检报告)送检。 12)当班下班前,需将机床擦拭干净,工作台台面涂上一层防锈油,且关闭机床电 源。 5.规范内容: 1)每班各机床操作者开车前确认本机台的状况是否正常。 2)机器作业前需基本确认事项: 3)各个开关是否灵敏,安全装置是否有效。 4)润滑油是否充足。 5)冷却水泵运转是否正常。 6)机床前、后、左、右、上、下各方向移动、滑动是否正常。 6.注意事项及设备保养 1)工作时按公司规定穿戴好防护用品。 2)按设备要求定期更换润滑油、切削液。 3)机床开始运行前,确认机床运动部件附近无人。 4)上电时,首先接通电柜上的总电源开关,而后再拔出急停按钮;断电时,先 按下操作站上的急停按钮,再断总电源开关。
首件标准作业指导书
材料有限公司 首件标准作业指导书版本版次: 页次:1/3 生效日期:2010-03-26 1.目的 为维持生产的正常导入,降低不良率﹑杜绝批量不良的发生,从而确保生产的顺利进行,特制定本规范 2.适用范围 生产各工艺制作流程皆适用之 3.职责﹑权限 生产车间各班组作业人员负责首件的制作及送检,现场干部和在线品管负责对首件的先后确认,在线品管负责首件确认情况记录和再次确认的跟踪 4.定义 首件:批量生产前制作的第一个合格产品 5.作业要求 5.1正常时首件的制作 每日排线或开机生产时,生产各工序作业员依据生产制令单﹑生产计划安排及客户质量要求制作第一个自检后认为符合要求的产品,送品管确认(必要时先经现场干部确认). 5.2异常时首件的制作 批量生产进行时,因机器设备故障﹑生产换线﹑材料变更﹑质量出现异常等情况发生时需暂停批量生产,重新制作首件进行确认 5.3首件的确认 在线品管收到制作的首件,依据客户订单要求﹑规格﹑检验标准书和客户确认样品, 对首件从外观﹑结构尺寸﹑功能和性能等方面进行全面的测量,各项指标皆满足客户要求后,方
材料有限公司 首件标准作业指导书版本版次: 页次:2/3 生效日期:2010-03-26 可于首件上贴合格标示,核准批量生产. 5.4不合格的再确认 当在线品管收到的首件,经检验判定不合格时,于首件上贴不合格标示并注明不合格原因(必要时,品管须知会现场干部),退回重新制作,直到制作的首件被确认合格为止 5.5不合格的处理 当制作的首件确认不合格时,制作者(必要时,包括现场干部)必须进行检讨,分析不合格的原因,采取措施,消除不合格原因,方可进行再次试制(以防止无方向性尝试,造成大批量的调试不良品,品管员须对造成的此类不良进行管制:开出异常单,限责任单位回复改善对策) 5.6首件检验记录 品管员每日将所作首件检验的状况及结果详细记录于巡检报表上并填写首件标签。 6.附件 首件标签:
机械加工产品检验作业指导书
一汽解放汽车厂质量保证部技术文件 编号:IPQC-JYZD-7-2009 批准:宋宗强 机械加工产品 检验作业指导书 2008年12月31日发布 2009年1月1日实施 一汽解放汽车厂质量保证部发布
前言 本检验作业指导书依据有关汽车标准及一汽解放汽车厂技术文件制定。是一汽解放汽车厂质量保证部技术文件之一。 本检验作业指导书与国家标准、企业标准及相关技术文件相一致。 从实施之日起,原《IPQC-JYZD-7-2008机械加工产品验作业指导书》同时废止。各相关部门检验机械加工产品质量时,都需要按本检验作业指导书的规定执行。 本标准由一汽解放汽车厂质量保证部起草。 本检验作业指导书起草人:林桂升 本检验作业指导书审核人:石建通
1 主要容与适用围 本检验作业指导书规定了机械加工产品的检验方式及质量记录。 本检验作业指导书主要适用于机加工车间。 2 引用标准 下列标准包括的条文,通过在本检验作业指导书中的引用而构成本标准的条文。在本检验作业指导书发布时,所示版本均为有效。所有标准都会被修订,使用本标准的各方应探讨使用下列标准最新版本的可能性。 CA/CBG-1-82 切削零件未注公差尺寸的公差 CA/CBG-9-91 未注公差角度的极限偏差 3 检验及质量记录规定 3.1所有机加工产品必须按产品标准、技术要求等进行自检控制。 3.2检验零件时,按控制计划合理选用量检具,并正确操作。 3.3未注公差尺寸的极限偏差 3.3.1 切削零件的轴类、孔类、非孔轴类的未注公差尺寸的公差按下表执行。
(以孔径为3.3.2 两孔的中心距和孔与零件边缘距离的未注公差尺寸的公差按下表执行。 基本尺寸查选。当两孔径不相等时,其轴心距的公差按两孔直径的算术平均值确定。)如果是两孔组之间的轴心(中心)距按3.3.1条规定执行。 3.3.4 切削件未注公差角度的极限偏差按下表执行,其值按角度的短边长度L查选。 3.3.5 螺纹长度尺寸L未注公差的极限偏差:对非全螺纹,长度L偏差为0~+1.5P;对全螺纹,长度L偏差为-1.5P~0。(P:螺纹的螺距) 3.4 正常路线件 3.4.1 对有明确公差要求的尺寸,检查员按不低于1/30的频次抽检并形成质量记录。每日记录5——7种,在此类制件中,其它无明确公差要求的尺寸可按不低于1/50的频次检