钢的纯净度评测及其控制
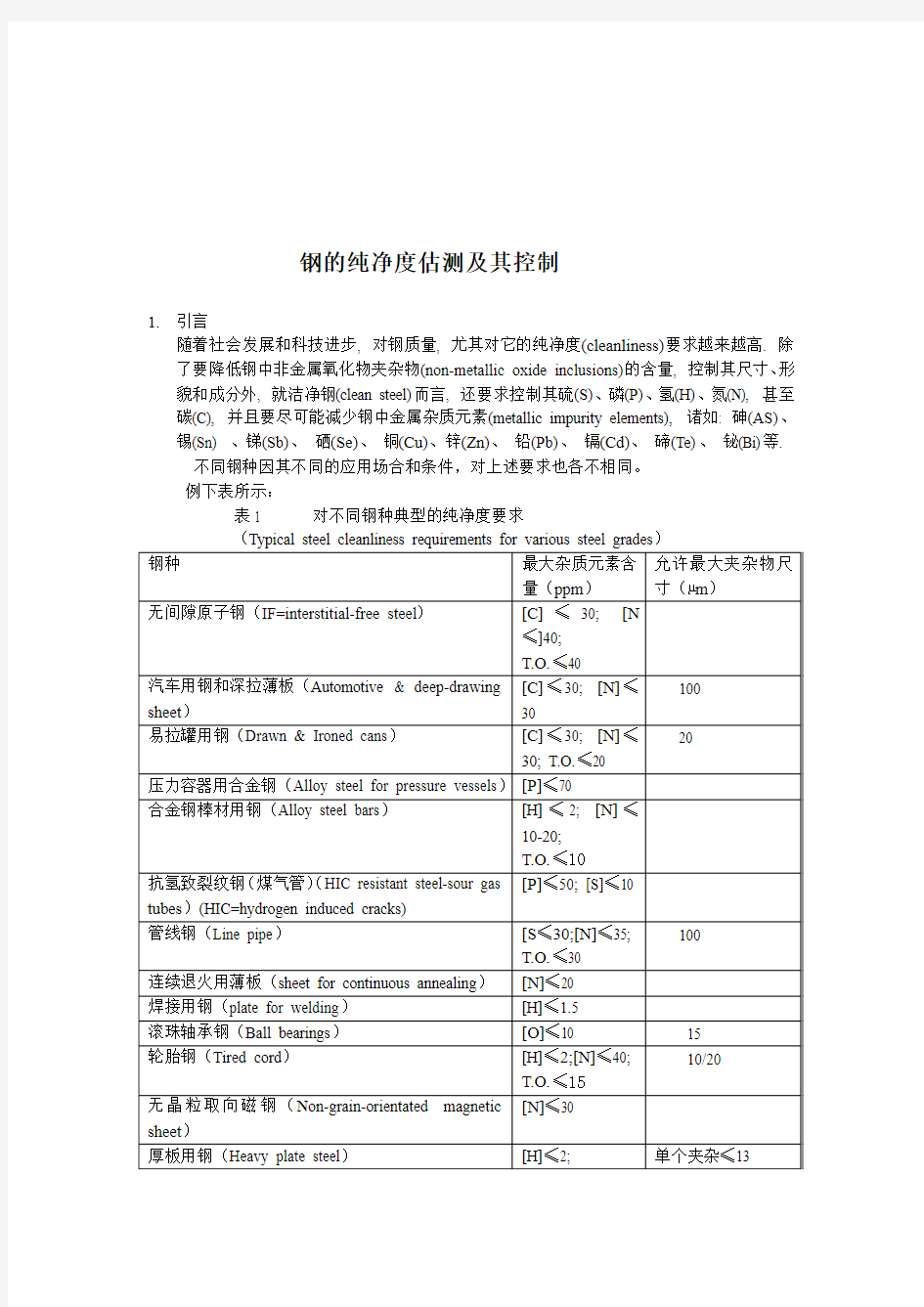

钢的纯净度估测及其控制
1.引言
随着社会发展和科技进步, 对钢质量, 尤其对它的纯净度(cleanliness)要求越来越高. 除了要降低钢中非金属氧化物夹杂物(non-metallic oxide inclusions)的含量, 控制其尺寸、形貌和成分外, 就洁净钢(clean steel)而言, 还要求控制其硫(S)、磷(P)、氢(H)、氮(N), 甚至碳(C), 并且要尽可能减少钢中金属杂质元素(metallic impurity elements), 诸如: 砷(AS)、锡(Sn) 、锑(Sb)、硒(Se)、铜(Cu)、锌(Zn)、铅(Pb)、镉(Cd)、碲(Te)、铋(Bi)等.
不同钢种因其不同的应用场合和条件,对上述要求也各不相同。
例下表所示:
表1 对不同钢种典型的纯净度要求
(Typical steel cleanliness requirements for various steel grades)
钢中的金属杂质元素(metallic impurity elements)通常被视为残余元素(trace elements).由于它们在炼钢和精炼过程很难去除,所以在钢中不断累积,成为废钢供应的一大问题。
鉴于钢中如存在超量的残余金属元素,会造成晶间偏析(intergranular segregation)、有害析出物和其它一些问题。
目前,在钢的生产过程中为了克服钢中残余元素造成的危害,尤其是电炉炼钢,通常采用严格控制废钢的种类和用量。近年来世界各国普遍采用高炉铁水、直接还原铁、海绵铁、碳化铁或其它相对纯的铁来替代废钢,旨在降低钢中残余元素含量。
从钢中残余元素角度讨论钢纯净度问题近年来已有不少相关研究的报道和论文发表。我们今天主要讨论钢厂普遍存在,大家又十分关注并想得到解决的问题:〈低碳铝镇静钢氧化物夹杂对其纯净度的影响〉。
钢中夹杂物会使产品产生很多不同类型的缺陷。例如:低碳铝镇静钢(LCAKS)生产易拉罐时,由于不适量夹杂物的存在而缺乏成形性(formability)致使产生有裂纹的折边(cracked flanges)和用于生产其它制品时出现的疲劳寿命(fatigue life)等问题。
钢的成形性和疲劳寿命很大程度上是受它所含的硫化物(sulfides)和氧化物(oxides)夹杂物的影响。
微裂纹缺陷(sliver defects)往往以线状沿钢板表面平行于轧制方向存在。它用于汽车板时会造成浅表的不完整(cosmetic imperfections)和成形性问题。
据美国内陆钢铁公司(Inland Steel CO.)、国家钢铁公司(National Steel Co.)和日本川崎钢铁公司(Kawasaki Steel Co.)等研究结果认为,它们通常含有来自脱氧产物中的三氧化二铝或者来自由卷入的结晶器保护渣所形成的复杂非金属夹杂物(complex non-metallic inclusions)。
就钢的纯净度而言,除了考虑夹杂物的含量外,很大程度上取决于夹杂物的尺寸分布、形貌和它的成分,其中尤以钢中夹杂物的尺寸分布特别重要。因为大型宏观夹杂物(macro-inclusions)对钢的机械性质(mechanical properties)最为有害。
有人统计得到:1Kg典型的低碳铝镇静钢中含有107-108个夹杂物,其中只有400个80-130μm;10个130-200μm和少于1个200-270 μm的夹杂物。显而易见,通常在钢中要检测到特大的夹杂物也是并不容易的。
从夹杂物的数量而言,小型夹杂物远超过大形夹杂物。但是大型夹杂物所占总的体积分数(total volume fraction)可能是较大的。有时候在整炉钢中造成灾难性缺陷(catastrophic defect)的正是由于单个大型夹杂物所致。因此,就清洁钢而言,不仅只是控制钢中夹杂物的平均含量,而且要避免对产品造成致命危害的大于临界尺寸的有害夹杂物的存在。基于这一目的,在表1中列出了对钢中最大夹杂物尺寸限制的要求。夹杂物尺寸分布的重要性在下图1中作了进一步阐述。
图1
测得钢包和中间包中>30μm夹杂物含量分别为1.61ppm 和0.58ppm。因此,尽管中间包钢水中的总氧含量和总夹杂物含量略高于它们在钢包中的含量。但中间包中钢比钢包中的钢更纯净了。
钢中非金属夹杂物的来源有:
1)脱氧的产物(Deoxidation products)。
在低碳铝镇静钢中的主要内生夹杂物(Indigenous inclusions)是三氧化铝。它是脱氧剂(例如:铝)和钢中溶解氧(dissolved oxygen)化学反应形成的。当在高含氧量的条件下,三氧化二铝呈树枝状,如图2(a)和(b)所示;或可能是由图2(c)中的这些较小夹杂物颗粒经碰撞所形成的。
图2
2)二次氧化的产物(Reoxidation products)。
例在下述情况下形成的三氧化铝。当:
10)残留在钢中的铝被FeO、MnO、SiO2和熔渣及耐火材料中的氧化物氧化形成;
20)铝暴露在大气中,被空气中的氧所氧化形成。
3)卷渣(slag entrapment)。
当冶金熔剂(metallurgical fluxes)被卷入钢中。尤其发生在炼钢、精炼和连铸过程中。这种条件下形成的夹杂物通常呈球形(spherical inclusions),如图2(d)所示。
4) 外来夹杂物(Exogenous inclusions)。
这类夹杂物主要来自钢包和中间包等的残渣、污物、灰尘和垃圾;破碎的耐火砖;硅酸盐包衬材料的侵蚀物。它的特点是颗粒大且呈不规则形状(Irregular shaped)。它可能成为三氧化二铝异类物质形核的核心;也可能成为图2(c)中所示夹杂物的颗粒中心。
5)化学反应的产物(Products of chemical reaction)。
例如当不正确的钙处理(Calcium treatment)进行夹杂物变性(Inclusion modification)所产生的氧化物。
确认钢中夹杂物的来源并不是很容易的事。例如含有CaO的夹杂物也可能是由卷渣造成的。
钢纯净度控制可以通过生产全过程中各个环节得以实现。诸如:炼钢原材料的选择和处理;炼钢过程中的合理用氧,避免过吹和重吹;冶炼过程中的正确监控,实现终点碳和温度的最佳控制;炉外精炼方法的合理选择和最佳工艺匹配;合理选用耐火材料尽量减少因受钢渣侵蚀而造成外来夹杂;合理的中间包形状、合适的容量和深度、最佳的流场和温度场;采用全程保护浇铸;应用较强吸收钢中夹杂物能力的冶金熔剂(钢包调渣剂、中间包覆盖剂和结晶器保护渣)等。
尽管如此,钢中不可避免地存在氧化物(Oxides);硫化物(Sulfides);硫氧化合物(Oxysulfides);氮化物(Nitrides)和碳氮化合物(Carbonitrides)等。
然而,为了提供生产清洁钢(Clean steel)的有价值信息,核心问题是钢中三氧化二铝夹杂物的控制和对钢纯净度评测方法现状的了解。
2.钢纯净度评测方法
为了研究和控制钢的纯净度,关键的问题是要有正确评测方法。夹杂物的数量、尺寸分布、形状和成分应该在钢生产的全过程都要测定。
测定的方法有直接法(direct method)和间接法(indirect)。前者准确但昂贵;后者快而经济,但准确性没有前者高。
2.1.直接法
有几种评测钢纯净度的方法。现将其总结和比较在]下表2。
表2 直接法评测钢纯净度的比较
(Comparison of direct methods for evaluating steel cleanliness)
2.1.1.固态钢中夹杂物的二维检测法
有几种常规的固态钢中夹杂物二维检测法。
1)金相显微镜观测法(Metallographic Microscope Observation)。
在这种常规的方法中,通过钢样试片用光学显微镜(Optical Microscope)检测并凭眼观测定量。当采用具有复杂形状的夹杂物(Complex shaped inclusions)检测时,就会发生问题。例图2(a)照片所示的夹杂物是由可能被错误地解释为一些较小夹杂物形成的簇状的单个夹杂物来显示的。此外,用此法测定小型夹杂物太耗时,而大型夹杂物并不多见。
2)图像分析法(Image analysis)。
它比用眼观测的金相显微镜法有了改进。它采用高速计算机(High-speed computer),由视频扫描显微镜图像(Video-scanned microscope image)来识别灰色基体上的黑白区域。
此法能比金相显微镜法容易地检测较大范围和较多数量的夹杂物。然而,由于试样上的擦伤(scratches)、蚀坑(pitting)和非金属斑点而造成检测误差。
3)硫印(Sulfur print)。
这种常规而经济的宏观照相法,通过对试样的硫酸酸洗,就能检测宏观夹杂和裂。/ 4)扫描电子显微镜法(Scanning Electron Microscopy)。
此法能容易地检测到被测试样的三维形貌和每一个夹杂物的成分。例如图2(b)就是用电子探针显微分析仪(Electron Probe Micro Analyzer)测得的成分。为了找到暴露的夹杂物,试样加工的工作量很大。
5)光学发射光谱法(带有脉冲识别分析功能)。
此法分析熔解在钢水中的元素。Ovako钢铁公司改进了这种方法后,可以在取样后1min 内检测钢的总氧量、微观夹杂物尺寸分布和化学成分。
6)激光显微探针质谱仪(Laser Microprobe Mass Spectrometry)。
由于夹杂物确定的化学状态,当单个夹杂物被脉冲激光束(Pulsed laser beam)照射后,超过它离子化门槛值(threshold value)时的最低激光强度,选择为特征光谱图(characteristic spectrum patterns)。根据参考样比较得到的结果,在激光现微探针质谱仪测定的光谱峰值是与化学元素有关的。
7)X-射线光电子光谱法(X-rays Photoelectron Spectroscopy)。
此法应用X射线可描述大于10μm单个夹杂物的化学状态。
7)俄歇电子光谱法(Auger Electron Spectroscopy)。
此法可采用电子束来描述靠近平板式试样表面附近小范围内的化学成分。2.1.2.固态钢中夹杂物的三维检测法
有几种方法可直接用三维法测固态钢中的夹杂物。
1)常规超声波扫描法(Conventional Ultrasonic Scanning)
这种非破坏性方法(Non-destructive method)能检测凝固了的钢中大于20μm夹杂物的数量和成分。
2)曼内斯曼夹杂物检测法(Mannesmann Inclusion Detection)
试样首先要经过加工去除缩孔(porosity),然后用超声波扫描来探测固体夹杂物及固体夹杂物和气孔的混和物(compound)。近来此法又被用作为液态取样热轧[加工]法(Liquid Sampling Hot Rolling Method)。
3)扫描声波显微镜法(Scanning Acoustic Microscope)
此法将连铸产品(Continuous-cast product)加工成圆锥形试样(Cone-shaped sample),用螺旋形探测仪(Spiraling detector)进行扫描。这种超声波系统(Ultrasonic System)可以自动检测到试样表面范围内各部位的夹杂物,包括从表面的中心线(Centerline).
4)X-射线检测法(X-ray detection)
通过将试样分割成几个薄片,并将每一个薄片用常规的X-射线(Conventional X-ray)打印出X光照片(Radiographs)作图像分析(Image Analysis)。
5斯拉姆法[电解法](Slime-Electrolysis)
这是一种准确但耗时的检测方法。它是将相当大(200g-20kg)的钢样完全熔解在盐酸中,然后把残留在其中的非金属夹杂物收集起来用于检测、计数和进一步分析。同时,为了保护FeO夹杂物,用电流通过浸在FeCl2 或FeSO4溶液中的钢样,使大部分夹杂物的分离任务完成。
此法用于显示如图2所示的单个完整的夹杂物。
6)电子束熔化法(Electron Beam Melting)
在真空条件下将铝镇静钢试样(Aluminium Killed Steel Sample)用电子束熔化。夹杂物浮到液态试样上表面并形成一个形似《筏》(raft)。通常电子束指数(Electron Beam Index)即为这筏形夹杂物的比表面(specific area)。图3是用电子束法和金相显微镜观测发对同一个试样测定结果的比较,它们只是性质上相似。
7)冷坩埚熔化法(Cold crucible melting)
在电子束熔化法检测时,夹杂物首先集中在熔化了的试样表面。冷却以后,然而试样表面被溶解,接着夹杂物从溶解物中过滤出来。此法通过溶化大的试样对电子束熔化法作了改进,并且能测夹杂物中的SiO2。
8)部分热分解法(Fractional Thermal Decomposition)
当钢样的温度超过熔点,夹杂物会在暴露在熔体表面,随之分解。不同氧化物夹杂在不同的温度条件下选择性还原,例如氧化铝基氧化物(Alumina-based oxides)1400℃或1600℃或高温夹杂物在1900℃。钢中总氧量是各个加热阶段测得的氧含量之和。2.1.3.测定钢中夹杂物的尺寸分布
1)柜式计算器分析法(Coulter Counter Analysis)
利用夹杂物能使缝隙电导率发生变化的原理。当夹杂物颗粒通过小孔进入传感器时而被测定。此法能测定由斯拉姆法分离得到的和悬浮在水中的夹杂物的尺寸分布。
2) 光散射法(Photo Scattering Method)
夹杂物(采用另外一些方法分离得到的,如:斯拉姆法)的光散射信号被用来估测其尺寸分布。
4)激光衍射粒子尺寸分析仪(Laser-diffraction particle Size Analyzer)
这种激光技术能用来估测由其它方法(诸如:斯拉姆法)分离得到的夹杂物的尺寸分布。2.1.4.液态夹杂物的估测
有几种方法能用来估测熔体中夹杂物的量和尺寸分布。
1)对液态系统的超声波技术(Ultrasonic Technique for Liquid System)
此法能通过获得的超声波反射信号来在线检测钢水中的夹杂物。
2)钢水纯净度分析仪(Liquid Metal Cleanliness Analyzer)
这种在线传感器是利用柜式计算器直接检测钢水中夹杂物的原理。通常此法用于铝和其它金属的测定。对应用于钢的测定还在研究和开发中。
3)共焦点扫描激光显微镜法(Confocal Scanning Laser Microscope)
这种新的现场检测法能观察单个夹杂物在钢水表面的形为,包括:它们的成核、相互间碰撞和成团以及界面推进的过程。
2.2.间接法(Indirect Methods)
由于直接检测法贵,耗时和取样的困难,在钢铁生产中钢纯净度的测定一般采用刚中总氧量、吸氮和其它直接法。
2.2.1.总氧量测定(Total Oxygen measurement)
钢中总氧量是自由氧(溶解氧)和结和成为非金属夹杂物中的氧之和。自由氧(或称之为活性氧)能用定氧探头(oxygen sensor)相对容易地测定。它主要由脱氧元素(deoxidation elements),例如铝的平衡热力学(equilibrium thermodynamics)来控制的。当用脱氧时铝和氧之间的平衡如图4所示。
图4
对于含铝量低的条件下,由下述方程(1)表述,它包括了温度的影响。
logK=log([%Al]2[%O]2)= -62780/T(K)+20.54 (1)
根据图4和方程(1),假定[%Al]=0.03-0.06,在1600℃条件下,自由氧为3-5ppm。因为自由氧的变化不大,所以钢中氧化物夹杂的总量有理由可以代表钢中的总氧量。由于钢中大型夹杂物的量少,对于用小尺寸试样(一般为20g)测定钢中总氧量时,很难发现有大型夹杂物。因此总氧量实际上仅代表了钢中小型小型氧化物夹杂物的含量。正如图5所示,在总氧量低的情况下,很显然减少了大型夹杂物存在的可能性。为此,总氧量还是非常重要的,并且它是钢纯净度的一个通用指标。由图6中可以看到,钢中测得的总氧量与成品微裂纹之间存在着粗略的对应关系。尤其从中间包中取的试样的到的检测结果可作为衡量钢纯净度的指标。例如:日本川崎(Kawasaki)规定冷轧板用钢当中间包中钢的含氧量小30ppm时可不作特殊检测;当氧含量在30-55ppm之间时需要作关键性检测;凡氧含量超过55ppm的炉次都要降级处理。
对于一些钢厂生产低碳铝镇静钢各个工艺环节总氧量水平的数据汇总在下表3(表中空格表示没有可利用的数据)。
表3 生产低碳铝镇静钢不同工艺环节钢中总氧量(ppm)
# 为超纯净钢。
从表3可以的出下面的一般性结论:
1)随着新技术的应用,低碳铝镇静钢的总氧量不断降低。例如;日本钢铁公司(Nippon Steel)总氧量从70年代40-50ppm 到90年代降到20ppm。
2)采用RH脱气装置的工厂可以较低的总氧量(10-30ppm);而用钢包气体搅拌的工厂的总氧量为35-45ppm.
3)在钢生产过程中,钢中的总氧量呈不断降低的趋势:钢包中40ppm; 中间包25ppm;结晶器20ppm;板坯中15ppm.。
2.2.2.吸氮(Nitrogen Pickup)问题
在生产过程中,测定各工艺环节钢中含]氧量,就可以清楚地了解钢水吸气的情况。例如:Weirton厂对一些重要钢种规定从钢包到中间包的吸氮不能超过10ppm。脱氧后,钢中的熔解氧含量低而容易吸收空气。因此,钢吸氮量的多少可以衡量钢中的总氧量、钢的纯净度和
二次氧化造成的钢的质量问题,如图7所示。
图7
实际生产中观察到氧在气/钢解面具有高的吸收动力学特点,因此,吸氧总是比测得的吸氮的结果要大许多倍。此外,当钢中的氧和硫含量较低时,吸氮速率较快。为了减少钢的吸氮,所以最好是在出钢后在进行脱气处理。工厂的实测结果证实了这一事实。从出钢时脱氧吸氮10-20ppm降低到出钢后脱氧时吸气仅5 ppm。表4和5总结了几个厂测得不同生产工艺过程中低碳铝镇静钢的最小吸氮量和钢中含氮量。
表4 不同钢厂在不同工艺阶段吸氮数据,(ppm)
表5 不同钢厂生产低碳铝镇静钢不同工艺过程的氮含量,(ppm)
从上述二表可以得到下述结论:
(1)大多数钢厂,低碳铝镇静钢板坯中氮含量为30-40ppm。它主要由转炉和电炉炼钢操作过程来控制;当然也受到精炼和浇铸过程的影响。
(2)由于新技术的应用和操作工艺的改进,钢中含氮量呈逐年降低的趋势。例如:Sollac Dunkirk钢厂,从中间包到结晶器的吸氮量从1988年的9ppm 降到1992年的1ppm。(3)一般而言,从钢包到结晶器的吸氮可以控制在1-3ppm 。在稳态浇铸条件下,吸氮可以控制在<1ppm。
2.2.3.钢中溶解铝损失的测定
对生产低碳铝镇静钢来说,钢中铝含;量的减少也反映了二次氧化的发生。然而,此法没有测吸氮的方法准确,原因也可能铝被熔渣氧化。
2.2.4.熔渣成分的测定
首先,分析操前后熔渣成分的变化可以估计吸收钢中夹杂物的情况。其次,测定钢中夹杂物矿相和化学组分与使用的渣(如:结晶器保护渣)比较,可以判断是否有卷渣造成的钢中缺陷。然而,采用这些方法并不容易,由于取样困难和必须考虑到热力学平衡(thermodynamic equilibrium)问题。
2.2.5.浸入式水口堵塞问题(Submerged entry nozzle clogging)
由于SEN堵塞而造成它的寿命短,以此可表明钢的纯净度差。连铸低碳铝镇静钢典型的化学成分为:51.7%Al2O3+44Fe%+2.3%MnO+1.4SiO2+0.6%CaO。从这成分中可以判断,
水口堵塞经常是由于小的Al2O3夹杂物和冷钢同时凝结(buildup)的结果。因此,SEN堵塞的频率可以作为衡量钢纯净度的另一个方法。
2.3.成品检验(Final Product Tests)
最终测定钢的纯净度是采用破坏性机械试验法(destructive mechanical tests)来测定其成形性(formability)、深拉性(deep-drawing)和/或弯曲性能(bending properties),或者是试样或产品的疲劳寿命(fatigue life);另一些试片还包括氢致裂纹试验(hydrogen induced cracks)和磁谱法检验(magnetoscopy)。这些试验表明钢中非常小的夹杂物(<1μm)具有潜在的优势,它并不影响钢的纯净度。
前面的讨论说明:没有单一的理想方法足以判定钢的纯净度。一些检测方法对质量监测较好;然而其它一些方法对研究问题比较合适。因此,在给定的操作条件下,为了更准确地评测钢的纯净度,必须结合几种方法一起考虑。例如:日本钢铁公司(Nippon Steel)用钢中总氧量和电子束熔化法测定小型夹杂物;用拉姆斯法(Slime)和改进型电子束熔化法(EB-EV)测定大型夹杂物。Usinor公司用部分热分解法(FTD),光学发射光谱法(带有脉冲识别功能)(OES-PDA),图像分析法(IA)和扫描电子显微镜法(SEM)测定小型夹杂物;用电解法和曼内斯曼夹杂物检测法(MIDAS)测大型夹杂物。例图8是取二个板坯试样的厚度方向采用钢中总氧量(TO),脉冲识别分析法(PDA)和图像分析法(IA)测得的夹杂物分布比较。这三种方法测定的结果表明,A钢比B钢具有较少的平均夹杂物含量,在移动边表面和中心之间存在最大值。宝钢应用钢中总氧量,金相显微经法,扫描电子显微经法测小型夹杂物;用拉姆斯法和扫描电子显微镜法测大型夹杂物;用定氮来判定钢的二次氧化;根据熔渣成分分析来推断吸收夹杂(inclusion absorption)和卷渣的发生(slag entrainment)。3.清洁钢生产的钢包操作(Ladle Operation for Clean Steel)
精炼和连铸操作控制钢的纯净度。例如:去除钢中夹杂物的系统研究发现,钢包处理可降低钢中夹杂物65%-75%;中间包中去除夹杂物20%-25%;结晶器中为5%-10%。因此钢包操作极其重要,它包括出钢氧(tap Oxygen)的控制;渣中FeO 和MnO含量;钢包搅拌和夹杂物变性处理(inclusion deformation treatment)。
3.1.出钢氧问题
出钢氧含量是指出钢时或加脱氧剂前测得的钢包中的氧量。出钢氧含量典型的数据,例:Weirton 厂为450-800ppm;美国国家钢铁公司大湖分厂(Great Lake division of National Steel)为800-1200ppm;日本钢铁公司(Nippon Steel)为250-650ppm;奥钢联林茨厂(V oest-Alpine Linz)为600ppm;武钢三炼钢厂(WISCO No.3)生产IF钢时为700-900ppm。
用铝作为脱氧剂加入钢水中会形成大量三氧化二铝夹杂物。因此,对于生产清洁钢,建议限制出钢氧含量。然而,如图9所示,出钢氧含量和钢的纯净度之间没有必然的联系。
图9
由于大量的铝加入钢中后会容易地形成三氧化铝蔟上浮进入钢包渣中得到分离,残留在钢中的Al2O3蔟都是<30μm的。
当然,是否不考虑出钢氧的问题要取决于夹杂物浮升是否有足够的时间和钢包精炼的条件。因为钢包精炼可排除大部分所形成的钢中夹杂物,图10所示。
图10
不考虑初始出钢氧含量,采用RH处理后都可以达到相同的结果的最终总氧量。只要脱气时间足够长,例如15min。最终要考虑的是出钢氧含量对于生产超低碳钢的脱碳速度的影响。
3.2.渣中FeO和MnO含量的问题
钢发生重氧化(二次氧化)的一个重要途经是炼钢炉出钢时进入钢包的带渣(carryover of slag from the steelmaking furnace)。这种熔渣中含有高的FeO和MnO。这些液态氧化铁与熔解在钢中的铝发生反应形成钢水中的固态Al2O3。下列反应有很利的热力学条件:FeO+2[Al]=Al2O3+3[Fe] ⊿G0l=-853700+239.9T (Jmol-1)
3MnO+2[Al]=Al2O3+3Mn ⊿G0l=-337700+1.4T (Jmol-1)
钢包渣中FeO 和MnO含量越高,二次氧化的可能性越大,由此会形成Al2O3夹杂物。成品中产生的许多微裂纹经证实即是源于钢包渣中的FeO的二次氧化。图11表明:
图11
钢包、中间包和结晶器中的总氧量与钢包渣中FeO%+MnO%含量之间粗略的对应关系。当包衬材料中含有高的SiO2,这些渣中的杂质特别有害。图12显示了对钢中熔解铝损失和中间包中夹杂物含量的增加的相同作用。
减轻FeO 和MnO对钢水污染作用的措施可总结如下:
1)出钢时减少从炼钢炉到钢包的带渣
# 提高目标终点碳(aim turndown carbon);避免重吹(reblows),因此可减少钢中熔解铝含量,能减少炉渣中的FeO量。
# 在转炉炼钢中应用副枪(sublance),可减少重吹的可能性。
# 采用有效的挡渣塞,诸如挡渣球,可以使出钢时从炉中带渣进入钢包减少到3Kg/t 钢。为了提高收得率,采用灵活的探渣器;包括红外(infrared)和电磁系统(electromagnetic system)。
# 炼钢炉的几何形状和出钢口的布置尽可能达到减少形成旋涡和带渣。
# 出钢后,钢包中厚的渣层,说明了严重带渣。钢包除渣后,控制钢包渣的厚度应该在25-40mm。
2)采用钢包渣还原处理
降低钢包渣中FeO 和MnO的另一条途经是加调渣剂(Slag conditioner)(即渣还原或脱氧处理)。调渣剂是铝和焙烧石灰或石灰石的混合物。表6总结了几个经钢包渣还原处理后FeO+MnO含量的降低。如图14所示,这种处理方法可平均将渣中FeO+MnO 将到低于5%。
表6 不同钢厂生产低碳铝镇静钢钢包渣处理的效果
图14。
SOLLAC DUNKIRK厂报导,采用了这种方法以后,钢的清洁度明显改善。对于生产低碳铝镇静钢,采用了减少带渣,加碱性钢包渣和使用碱性包衬可使钢包渣中的FeO+MnO降到1%-2%,总氧量降到10ppm。
3.3.钢包搅拌操作
钢包搅拌和精炼工艺,例如RH钢包脱气,大大地促进了夹杂物的生长和排除,一些冶金反应需要强的渣/金混合(例如:脱硫和脱磷);而在其它条件下必须使渣/金柔和混合,不能使钢水裸露(例如:脱氧和去除钢中夹杂物)。如表7对比的各种不同工艺方法产生不同的搅拌功。
表7
不同的钢包处理对板坯夹杂物含量的影响由图15所示。
图15
由图表明,通过钢包中的吹氩搅拌来改进RH真空处理,可以得到较高的钢的纯净度。它与表7的数据相符。钙基喷粉具有显著效果,除了它脱氧和形成液态夹杂物的主要作用外,另一方面原因由于其具有较大的搅拌功。有些钢厂RH脱气和钙处理结合可使总氧量降到15ppm。日本NKK公司应用了改进型的RH法,经20min的脱气处理后,可使低碳铝镇静钢的总氧量降到5ppm。搅拌功对脱氧速度的影响示于图16和17。
图16 图17
从图中看到,只要搅拌功不要大到不合适的程度,随搅拌功的提高有利于夹杂物的去除。合金化后,确保足够的搅拌时间(>10min)也是重要的,使钢中Al2O3夹杂物循环上浮进入熔渣而被去除。过分强烈搅拌和过长的处理时间也有多方面不利作用:(1)钢水过快的循环上浮而进入熔渣,形成无渣区(slag-free region)而使钢水裸露,产生二次氧化,也有可能造成卷渣(slag entrainment);(2)钢包包衬受到侵蚀,增加外来夹杂物;(3)强烈搅拌促使夹杂物颗粒碰撞,形成大的宏观夹杂物。有人建议,钢水处理时一开始采用强搅拌以促使小型夹杂物间的混合和碰撞,并成大颗粒的夹杂物,接着通过最后阶段的柔和搅拌促使钢水慢的循环,利于经碰撞后形成的较大颗粒的夹杂物易于分离进入渣中。
脱氧处理时间应该是混合时间(h m)的几倍。一些研究者估计h m是搅拌功(j)的函数。例如,通常Nakanishi方程表达为:
H m[s]=800j[watt/ton]-0.4
不同工艺过程的单位搅拌功(specific stirring power)见表7。
表7 不同工艺方法搅拌功数据
它可用来估算混合时间。例:对RH而言,搅拌功200-400w/t时,混合时间约1.2-1.6min。在工业生产精炼操作中,纯脱气时间通常为5-10min,是脱气时间的3-6倍。
3.4.夹杂物变性处理(Inclusion Modification)
对于低碳铝镇静钢进形钙处理是有吸引力的,因为它能使氧化物和硫化物在钢水中呈液态并改变它们的形状和在凝固的钢中的变形能力(deformability)。液态铝酸钙比固态蔟状铝酸钙更易聚合长大和上浮,这样利于它们从渣中排除和降低钢中总氧量,另外避免水口堵塞。为了得到液态夹杂物,钙必须要以正确的比例加入。钙在钢中的含量范围窄,它取决于钢中三氧化二铝的含量,正如平衡相图所示。此外,为了使铝镇静钢保持在整个铝含量范围呈液态夹杂物,硫含量必须要低,如图18所示。因为钙是活泼元素,只有当钢水经脱氧处理和避免卷入含FeO 和MnO的渣才能起作用。
4.清洁钢生产的中间包操作
发生在中间包中的重要现象图示在19。
图19
中间包操作大大地影响钢的纯净度,取决它的操作工艺,中间包可以作为将钢中夹杂物排除进入渣层的进一步的精炼装置,或许它由于卷渣;重氧化和耐火采料熔解而使钢水受到污染。一些重要的因素讨论如下:
中间包的温度和容积;换包操作;中间包内衬耐火材料;中间包覆盖剂;气体搅拌和钢水在中间包中的流动控制。
4.1.中间包深度和容积(Tundish Depth and Capacity)
深的中间包具有大的容积,增加钢水在中间包内的滞留时间(Residence Time),因而促进了如图20所示的夹杂物的分离;深的中间包也可避免漩涡的形成,为换包操作提供了更多的时间,且不会造成卷渣。
在过去20年中,在世界范围内,对用于生产低碳铝镇静钢的中间包的尺寸有很大的扩大,典型的中间包已达到可容纳钢水60-80吨;深度超过1778mm(70吋)。
4.2.非稳态浇注条件(Casting Transitions)
当每个浇次(casting sequence)的开浇;换包操作;换水口和浇注结束都会发生非稳态浇注现象。它们对钢因清洁度问题产生缺陷起很大作用。当非稳态浇注时,常常会使钢中增加夹杂物;若非稳态持续的时间长,会使更多的钢水受到污染。研究发现,开浇第一炉钢的裂纹缺陷指数比中间浇次高5倍,甚至是连浇炉次(successive casting heats)的15倍。当在上述提及的非稳态浇注阶段,卷渣和吸收空气比较容易,由次造成钢的二次氧化。例在美国国家钢铁公司当非稳态浇注时中间包中的总氧量达到50-70ppm,而稳态浇注时仅25-50 ppm。在其它一些工厂,差别只有3 ppm。Lukens厂报导,非稳态浇注时中间包中总氧量为19.2 ppm,稳态浇注时为16 ppm。Dafasco厂的总氧量分别为27±5 ppm和24±5 ppm。日本钢铁公司,在当浇注时中间包吸氮为5-12ppm,当浇注到12.5min时(处于稳态浇注状态),吸氮降到0-2ppm。
图21所示三种不同浇注条件下中间包中的总氧量。当开浇第一炉时,由于中间包钢流呈散流而吸气和卷渣,随之使中间包的初始氧含量达到最大值(包括渣和三氧化铝夹杂物)。开浇时敞开浇注使中间包钢中的总氧量比整个炉次中总氧量的正常值高1倍。(图21中第一种情况)。
图21
在加中包覆盖剂前必须由钢包向中间包浇钢几分钟。最后,当稳态浇注时,钢中总氧量降到较低的值,主要含有三氧化铝。
当换钢包时,一个措施是直到中间包再有钢水流入时方开始=向结晶器注如钢水并且通过塞棒吹气促使钢中夹杂物上浮分离;另一个措施是新换的钢包要装上浸入式保护套管(长水口)。采用这些措施后,Dofasco厂的整个浇次具有更稳定的钢水质量,钢中总氧量从长41±14ppm 降到31±6ppm(如图21第二种情况)。
接近浇注结束时,由于钢包出口处形成旋涡而使钢包中的渣卷入中间包。出现这种现象应该使钢包中残留一部分钢水(约4吨左右)。另外,当钢包关闭后,中间包中的钢水深度降低,破坏了中间包的钢水正常的流动状态,并可能产生熔渣的旋涡而卷入结晶器,增加结晶器中钢水的总氧量。据Dofosco厂报道,该厂正在开发电磁液位探测器(An electro-magnetic level indicator)。
4.3.包衬耐火材料
钢水中熔解的铝可以与包衬耐火材料中的氧反应。这些氧可能来自一氧化碳(carbon monoxide),它是耐火材料中的碳与粘合剂(binders)和杂质(impurities),或者硅质耐火材料分解的氧反应的结果。
二氧化硅基中间包衬比镁基喷涂料更糟糕。
SiO2+4/3[Al]=2/3Al2O3+[Si] ⊿G l O=-219400+35.7T (Jmol-1)
上述反应进行的程度可以通过由钢水中硅的含量来判断。
另一个因素是包衬材料的蚀损速率(wear rate)。在日本川崎公司的Mizushima厂使用了三种不同类型的包衬渣线(slag line)材料(高铝砖、氧化铝-碳化硅-碳砖和镁碳砖)。它们在使用中的蚀损速率分别为1.0、0.34 和0.16mm/炉。包衬材料受到侵蚀性强的中包覆盖剂和熔渣的侵蚀。在这三种材料中,镁碳砖有最高的使用寿命(highest durability)。
4.4.中间包覆盖剂(Tundish Flux)
中间包覆盖剂具有几个功能。首先,它必须使钢水能防止过多的热损失(excessive heat loss)和防止空气卷入而使钢水重氧化(air entrainment and reoxidation)。例如:在IMEXSA 钢厂(墨西哥),通过改变使用的中间包覆盖剂,使钢包到结晶器的吸氮(nitrogen pick up)从16ppm 降到5ppm。其次,在理想的条件下(idea circumstances),它也应该具备吸收钢中夹杂物的能力,使钢水进一步得到净化。常用的中包覆盖剂是碳化稻壳(burnt rice hulls)。它价格低,是一种较好的隔热材料,它还有良好的覆盖功能而不易使钢水表面结壳。然而,碳化稻壳含有高的二氧化硅(大约在80%左右),它被还原而成为钢中夹杂物的来源(反应式:SiO2+4/3[Al]=2/3Al2O3+Si)。它也容易污染环境并含较高的碳(约在10%左右),容易使超低碳钢增碳。
碱性覆盖剂(basic fluxes)以CaO-Al2O3-SiO2基。从理论上讲,它对低碳铝镇静钢的精炼效果较好,并使中间包中的钢水具有较低的氧含量。例:川崎公司Mizushima厂使用的覆盖剂碱度从0.83提高到11,使钢中的总氧量从25-50ppm降到19-35ppm.。在Dofasco厂第二炼钢车间,使用碱性覆盖剂(40%CaO+245Al2O3+18%MgO+0.5%SiO2+0.5%Fe2O3+8%C)并结合挡渣墙与原来使用的覆盖剂(3%CaO+10-15Al2O3+3%MgO+65-75%SiO2+2-3%Fe2O3)进行比较。当换包操作时,总氧量从41ppm降到21ppm;当处于稳态浇注(steady state casting)
时,总氧量从39ppm降到19ppm。其它一些试验结果(例图22所示),较高碱度覆盖剂(25%SiO2+10%Al2O3+59.5%CaO+3.5%MgO)和碳化稻壳对降低钢水总氧量方面的比较,没有发现有所改善。这也许是因为碱性覆盖基中仍含有太多的二氧化硅;更有可能,碱性中包覆盖剂没有使用效果,由于它熔速较快,且结晶温度(crystallization temperature)高,而容易使钢水表面结壳(crust at the surface of molten steel)。
正因为如此,当浇注时容易使长水口附近钢水的无渣区面积扩大,不仅使钢水过氧化加剧,而且也增加了辐射热损失,使钢包操作平台(ladle platform)上的操作工人受高温之苦。而且,一般来说碱性中包覆盖剂具有较低的粘度,所以容易卷入钢中。为避免这种现象的发生,AK钢铁公司Ashland厂建议采用双层覆盖剂(double layer flux),将低熔点的碱性覆盖剂放在下面,可起到吸收钢中夹杂物的作用;将碳化稻壳放在上层起到隔热作用。由此可使钢中总氧量从22.4ppm降到16.4ppm。
4.5.中间包搅拌(Tundish stirring)
从中间包底部吹氩可以改善钢水的混合条件,促进夹杂物间的相互碰撞和上浮排除。在Luken钢铁公司,已成功地应用了这一技术。使中间包钢水中的总氧量降到16ppm。应用这一技术的危害在于有时夹杂物随气泡卷入结晶器而进入铸坯,造成严重缺陷。
4.6.中间包流动控制(Tundish Flow Control)
中间包中钢水的流动方式应考虑到增加钢水在中间包中的滞留时间(residence time),防止钢水发生“短路”(short circuiting)现象,并能促进夹杂物排除。中间包中钢水流动控制是由它的几何形状;液面高度;长水口设计以及流动控制装置,诸如:冲击垫(impact pads);堰(weirs);坝(dams);缓冲器(baffles);和过滤器(Filters)。如图23中所示的中间包冲击垫是很廉价的流动控制装置,它可以防止钢包中注入钢水的冲击侵蚀;它更重要的作用在于抑止钢水进入区域的紊流现象,可以起到减少卷渣(slag entrainment)的危险;尤其在开浇时它也可以削减冲击钢流的动量(incoming stream momentum),并可使高温钢流自然浮升(natural buoyancy)而避免短路。特别当换包时,如能正确对中,并和堰、坝配合起来,冲击垫还能起到纯净钢水的作用。例如:美国LTV厂采用了冲击垫,当换包(ladle transitions)时,使钢中三氧化二铝从48ppm降到15ppm。在Lukens钢厂用(domed)冲击垫改成(hubcap)后,钢中三氧化二铝从26ppm降到22ppm。在韩国浦项钢铁公司,采用带有77孔的坝作为部分过滤器,使钢的清洁度(steel cleanliness)得到改善。在Dofasco第二炼钢厂,尤其在换包时,使用了缓冲装置后改善了产品质量(product quality)。因此,如图21中第三种情况所示,缓冲装置和中包盖结合使用,当处于稳态浇注条件时,可使中间包的平均总氧量从39±8ppm降到24±5ppm。在排除夹杂物方面,陶瓷过滤器(ceramic filter)非常有效。但因它的成本和使用中容易堵塞的问题使它的应用受到限制。
5.清洁钢生产的几个重要工艺环节
对钢的清洁度控制而言,从钢包到中间包和从中间包到结晶器这两个环节是非常重要的。Mcpherson和Mclean总结了从中间包到结晶器操作的不同方面,集中考虑到不同保护浇注的设计问题。最主要的钢水吸收氧的来源之一是上述操作过程中钢水被空气中的氧氧化。由此产生的夹杂物会造成水口堵塞以及成品缺陷(final product defects)。为了减少和杜绝这种现象的发生,可以通过优化保护浇注、吹氩和浸入式水口(submerged entry nozzle)来解决。
5.1.敞开浇注和保护浇注(Open pouring and shrouding)
当更换钢包和中间包时,采用优化的保护浇注措施可大大地降低钢水重氧化。例如:上海宝钢采用钢包保护套管(长水口)与敞开浇注比较,钢水吸氮从24ppm降到3ppm.。在美国钢铁公司Fairfield厂,更换了中间包浇注箱(tundish pour box)和长水口(shroud),可使钢包到中间包吸氮从7.5ppm 降到4ppm,同时可防止因换包时发生的卷渣现象。在英
国钢铁公司Ravenscraig厂,改进了从钢包到中间包的保护系统,吸氮14ppm从降到3ppm。在另一个钢厂,采用了保护从钢包到中间包的钢流后,减少了溶解铝损失(dissolved aluminium loss)从130ppm 到70ppm,而总氧量只增加12ppm。在小方坯(billet)连铸时一般不采用保护浇注,控制注流的状态十分重要。圆滑的注流比紊流和散流吸氮少得多。在操作中,为了能形成中间包和结晶器之间圆滑的注流,必须使定径水口(metering nozzle)保持完好,并要避免通过水口的钢流流速太大。采用惰性气体(inert gas)保护系统(shrouding system)也是很有帮助的。
5.2.开包操作(ladle opening)
钢保应能自动开浇而不用吹氧。如果烧氧开浇必须将长水口移开,特别当开始的635mm 到1270mm的铸坯容易发生重氧化。图24所示:
图24
烧氧开浇炉次(lanced-opened heats)的钢中总氧量比自动开浇的高10ppm。认真仔细地安放引流沙(ladle opening sand)有助于实现自东开浇。因为引流沙中含有高的而氧化硅,所以它也是发生钢水重氧化的原因之一。
5.3.氩气保护密封(Argon protection sealing)
在许多场合应用惰性气体能防止钢水重氧化。为了防止卷渣,所以中包覆盖剂(tundish fluxes)是等中间包中已有了一定的钢水后才加入。在开浇的15民min.内,开钢包时钢水散流而使空气卷入(air entrainment)。为了解决这个问题,在开包之前,用惰性气体取代空气进行保护,它使开浇阶段能起到降到钢中总氧量和防止吸氮的两个作用。使用具有保护功能的中间包包盖(tundish cover)并仔细地将角部密封也可使钢中总氧量从41.5ppm降到38ppm.。为了提高钢的清洁度和防止水口堵塞,认真密封长水口的接缝处也是非常重要的。改进钢包水口(ladle nozzle)和长水口之间的密封,可使吸氮从8ppm降到<1ppm。加强浸入式水口的密封,可使吸氮从1.8ppm降到0.3ppm。
吹氩(Argon injection)密封保护套管能有助于防止钢水(molten steel)被通过任何接缝和泄漏处进入空气中氧的重氧化。有文献报导了为了确保水口内部呈正压(positive presure)的最小氩气流量。往中间包塞棒(tundish stopper rod)吹氩,改善密封条件降低从中间包到板坯的吸氮量由5ppm到1.8ppm;降低板坯的总氧量从31ppm到22ppm,减少了在板坯中三氧化二铝蔟状夹杂物的尺寸,并减少了水口堵塞。有文献报导,通过塞棒吹氩后,用MIDAS法检测,获知夹杂物的数量减少了25-80%。通过滑动水口(slide gate)上滑板(upper plate)吹氩减少50-100μm 尺寸的夹杂物数量从3个/cm2 0.6个/cm2;,并降低100-200μm的宏观夹杂物(macro-inclusions)数量从1.4个/cm2到0.4/cm2。
5.4.水口堵塞(Nozzle clogging)
水口堵塞是由于重氧化或钢中固体氧化物(Al2O3)和硫化物(CaS)累积所引起的。它除了影响正常生产;中间包水口和浸入式水口堵塞从多方面分析会对钢的纯净度造成危害。首先,脱落下来的堵塞物不是被卷入钢中,就是改变保护渣的化学成分,造成铸坯缺陷。其次,堵塞物改变了水口的流动方式和水口出口处的钢流特征,干扰结晶器中钢水的流场,导致卷渣和铸坯的表面缺陷。第三,当流动控制装置(flow control devices)(塞棒或滑动水口)为了弥补堵塞而带来的问题进形调整时,势必影响到结晶器液面控制(mold level control)。在Dofasco厂,将三滑板式的滑动水口改成了塞棒形式,减少了堵塞现象的发生。
有大量文献报导了防止水口堵塞的措施。除了减少钢中夹杂物的一般性措施外,通过控制水口材料的化学成分(避免Na, K Si杂质),或在水口壁上凃纯三氧化二铝(pure alumina);BN或其它抗堵塞材料来解决。
RH-LF 和LF-VD 工艺生产管线钢洁净度的比较
RH-LF和LF-VD工艺生产管线钢洁净度的比较 一、电弧炉炼钢的时代特点 1、变为初炼炉 进入20 世纪80年代后,随着炉外精炼技术、工艺、装备的快速发展,原冶炼工艺中在电弧炉内完成的合金钢、特殊钢的脱氧、合金化、除气、去夹杂的电炉“重头戏”移到炉外精炼炉去进行了。电弧炉及转炉皆变为只须向炉外精炼炉提供含碳、硫、磷、温度、合金化合格或基本合格的钢水就算完成任务的炼钢初炼炉。改变和结束了原电弧炉的熔时长(三个多小时)、老三期操作(熔化期、氧化期、还原期)以及产量低、渣量大、炉容小、成本高的状况。 2、炉容大型化 随着电炉—炉外精炼—连铸—直接轧材工艺的发展,这种短流程(相对于焦化、烧结—高炉—转炉—炉外精炼炉—连铸—)轧材工艺而言的轧机产量要求电炉与之相匹配,例如长材年产50-80 万t、板材100-200 万t 、热轧卷年产200万t以上,因此单一匹配电炉的炉容量和生产率,生产速率必须与轧机相衔接. 目前, 较多采用公称炉容量80-120万t 左右的电弧炉,从趋势看炉容量仍在提高。变压器向超高功率发展(1000KV A/t)。 3 、电炉转炉化 氧气顶吹转炉依靠铁水为原料,吹氧冶炼故冶炼周期短(20min左右),产量高,即获得了比电炉高的多的生产率和生产速率( 科技工作者在20 世纪50年代在电弧炉上吹氧(炉门和炉顶)兑入约30%~50%的铁水(EOF 炉),把转炉的工艺优势移植过来,电炉的冶炼周期大大缩短,目前均在45min 左右( 故电炉顶吹氧、热装铁水、电炉双炉壳很快得到推广。 4、电弧炉钢产量大幅增长 在上述三项电炉自身工艺变化的同时,随着社会发电技术,能力的增长(核电站、水力发电等)及社会废钢量的增加,直接还原铁DRI、HBI、Fe3C 技术工艺的发展,都为电弧炉快速发展提供了条件. 因此,世界各国电弧炉钢产量由1950 年占世界总产钢量的6.5%增至1990 年的27.5% , 2003 年的36%. 5、提质、降耗、防污染使电弧炉获得新的活力 电弧炉使用废钢为原料与使用高炉铁水的转炉相比,总能耗是高炉-转炉工艺的1/2~1/3。
洁净室温湿度如何控制
如何对洁净室温湿度进行控制 洁净室的温湿度主要是根据工艺要求来确定,但在满足工艺要求的条件下,应考虑到人的舒适度感。随着空气洁净度要求的提高,出现了工艺对温湿度的要求也越来越严的趋势。净化工程具体工艺对温度的要求以后还要列举,但作为总的原则看,由于加工精度越来越精细,所以对温度波动范围的要求越来越小。例如在大规模集成电路生产的光刻曝光工艺中,作为掩膜板材料的玻璃与硅片的热膨胀系数的差要求越来越小。直径100 um的硅片,温度 洁净室的温湿度主要是根据工艺要求来确定,但在满足工艺要求的条件下,应考虑到人的舒适度感。随着空气洁净度要求的提高,出现了工艺对温湿度的要求也越来越严的趋势。 净化工程具体工艺对温度的要求以后还要列举,但作为总的原则看,由于加工精度越来越精细,所以对温度波动范围的要求越来越小。例如在大规模集成电路生产的光刻曝光工艺中,作为掩膜板材料的玻璃与硅片的热膨胀系数的差要求越来越小。直径100 um的硅片,温度上升1度,就引起了0.24um线性膨胀,所以必须有±0.1度的恒温,同时要求湿度值一般较低,因为人出汗以后,对产品将有污染,特别是怕钠的半导体车间,这种车间不宜超过25度。 湿度过高产生的问题更多。相对湿度超过55%时,冷却水管壁上会结露,如果发生在精密装置或电路中,就会引起各种事故。相对湿度在50%时易生锈。此外,湿度太高时将通过空气中的水分子把硅片表面粘着的灰尘化学吸附在表面耐难以清除。相对湿度越高,粘附的难去掉,但当相对湿度低于30%时,又由于静电力的作用使粒子也容易吸附于表面,同时大量半导体器件容易发生击穿。对于硅片生产最佳温度范围为35—45%。 洁净室中的气压规定 对于大部分洁净空间,为了防止外界污染侵入,需要保持内部的压力(静压)高于外部的压力(静压)。压力差的维持一般应符合以下原则: 1.洁净空间的压力要高于非洁净空间的压力。 2.洁净度级别高的空间的压力要高于相邻的洁净度级别低的空间的压力。 3.相通洁净室之间的门要开向洁净度级别高的房间。 压力差的维持依靠新风量,这个新风量要能补偿在这一压力差下从缝隙漏泄掉的风量。所以压力差的物理意义就是漏泄(或渗透)风量通过洁净室的各种缝隙时的阻力。 洁净室中的气流速度规定 这里要讨论的气流速度是指洁净室内的气流速度,在其他洁净空间中的气流速度在讨论具体设备时再说明。 对于乱流洁净室由于主主要靠空气的稀释作用来减轻室内污染的程度,所以主要用换气次数这一概念,而不直接用速度的概念,不过对室内气流速度也有如下要求; (1)送风口出口气流速度不宜太大,和单纯空调房间相比,要求速度衰减更快,扩散角度更大。 (2)吹过水平面的气流速度(例如侧送时回流速度)不宜太大,以免吹起表面微粒重返气流,而造成再污染,这一速度一般不宜大干0.2m/s。 对于平行流洁净室《习惯上称层流洁净室),由于主要靠气流的“活塞打挤压作用排除行染,所以截面上的速度就是非常重要的指标。过去都参考美国20gB标准,采用0.45m/s.但人们也都了解到这样大速度所需要的通风量是极大的,为了节能,也都在探求降低速一风速的可行性。 在我国,《空气洁净技术措施》和<洁净厂房设计规范))都是这样规定的 垂直平行流(层流)洁净室≥0.25m/s 水平平行流(层流)洁净室≥0.35 m/s 研究表明以上规定基本上满足控制污染的要求,但认为应区别不同情况分出不同的档别,更能体现节能的目的。
钢结构制作质量控制
山东金宇钢构股份有限公司 钢结构制作质量控制程序编制: 审核: 审批:
总则 1. 本技术文件是根据GB50205-2001《钢结构施工及验收规范》及 JGJ81-2002《建筑钢结构技术规程》而制订的。 2. 本技术文件可作为我公司在制作、检验钢结构产品时的使用根据。 3. 钢结构制作质量控制分为产品工序质量控制和检验工作质量控 制。 4. 在钢结构制作过程中,各主要工序必须实行三级质量检验,即: 3.1 自检:责任生产人员自检;每道工序操作者自检合格后, 填写自检记录并签字认可,并在工件上标上√表示合格,方可 将工件及自检记录移交工序质量检验员。 3.2复检:工序质量检验员对主控项目及重要结构尺寸复检,复 检合格后会同班长签字确认,方可将工件及自检记录移交下工 序。 3.3:下工序对上工序工件进行的检查。下工序质量检验员首先 检查工件有无合格标示√(无标示拒绝接收),然后按上工序自 检记录复检,完成交接性检验并签字确认。发现不合格项(品),立即报告班长,班长再报告质检员。 5. 产品工序质量的考核有以下几项指标: ①工序交验合格率=移交工件合格数/移交工件数×100℅ ②返修率=移交工件不合格数/移交工件数×100℅ ③出厂合格率=出厂工件合格数/出厂工件合格数×100℅
6. 生产部专职检验人员应进行抽检和巡检。 6.1抽检:专职检验员按工序先检查自检记录,然后对记录中 最大偏差的20%工件进行抽检,填写专检记录签字认可,并在 构件上用(√)表示合格。 6.2巡检:专职检验员在完成工序抽检后,应在车间巡视检查, 主要检查重点工序、返工返修件、重要部位、主控项目及重要 结构尺寸。 7. 检验工作质量考核有以下几项指标: ①漏检率=实检工件数/应检工件数×100℅ ②检验及时率=及时检验工件数/应检工件数×100℅ 8. 放行:经专业质量检查员检验,确认为合格品后由质量主管出具 此放行通知单,放行权归质量主管。 9. 不合格项(品)的控制:在交检、专检中发现的不合格项(品), 由质检员判定为:⑴不符合;⑵不合格品;按中国第五冶金建设公司QEO不合格品控制程序处置。 10.各级质量控制责任人: 责任生产工人(自检)班长 专业质量检查员(抽检和巡检)质量主管(放行)。 11.编制产品工艺文件时,应将本技术文件所规定的各项检验要求编 入,以此程序进行产品检验。后列检验项目分为轻钢结构和重钢结构两部分。
钢结构工程质量控制重点
钢结构工程质量检查控制要点 一、检查依据 1.国家标准《钢结构工程施工质量验收规范》GB50205-2001 2.国家标准《钢结构设计规范》GB50017-2003 3.国家标准《冷弯薄壁型钢结构技术规范》GB50018-2002 4.国家标准《钢结构工程质量检验评定标准》GB50221—95 5.国家标准《碳素结构钢》GB/T700—88 6.国家标准《低合金高强度结构钢》GB/T1591—94 7.行业标准《建筑钢结构焊接规程》JGJ81—2002 8.行业标准《高层建筑钢结构技术规程》JGJ99—98 9.行业标准《钢结构高强度螺栓技术规程》JGJ82—91 10.行业标准《网架结构工程质量检验评定标准》JGJ78—91 11.标准化协会标准《门式钢架轻型房屋钢结构技术规程》CECS 102: 2002 12.标准化协会标准《钢结构防火涂料应用技术规范》CECS 24:90 13.天津地方标准《钢结构防火涂料工程施工验收规范》DB29-134-2005 14.施工图设计文件 二、施工前质量控制重点内容 1、现场施工单位资质、质量保证体系审查及钢结构加工厂资质审查 (1)钢结构工程施工单位应具备相应的钢结构工程施工资质,从事钢结构工程施工的施工企业资质等级标准分为一、二、三级。施工现场质量管理应有相应的施
工技术标准、质量管理体系、质量控制及检验制度,施工现场应有经技术负责人审批的施工组织设计、施工方案等技术文件。 (2) 监理单位对钢结构分包单位的认可记录。必须明确监理合同中是否对钢结构加工过程进行监理,建议建设单位在监理合同书中明确规定。 2、监理单位资质、质量控制体系审查 (1) 监理企业承担监理任务应与其资质相符。监理人员配备必须符合招投标文件规定,若调换人员必须由建设单位的书面同意文件。项目总监兼管其他工地的,数量不得超过3个工程,而且必须提供各个工程建设单位的书面认可文件。在满足上述条件下,每个工程必须配备一名总监代表,总监代表应持证上岗。 (2)监理人员应具有相应的专业监理资格。监理员无权在检验批、隐蔽验收、分项、分部质量控制资料中签字。所有签字的监理人员必须在签字处加盖个人注册方章,否则视为无效资料。 (3)项目监理人员的工作方式,要求做到见证、旁站、巡视和平行检验。见证是指由监理人员现场监督某工序全过程完成情况的活动;旁站是指在关键部位或关键工序施工过程中,由监理人员在现场进行的监督活动;巡视是指监理人员对正在施工的部位或工序在现场进行的定期或不定期的监督活动;平行检验是指项目监理机构利用一定的检查或检测手段,在承包单位自检的基础上,按照一定的比例独立进行检查或检测的活动。 (4) 监理人员在工作中要敢于管理,树立自身威信。在处理现场质量问题时,应坚持工作程序和工作标准,果断、坚决、不拖泥带水。对新技术或不了解的专业问题,应先咨询有关部门或专家,做到有根有据后再做决定。 (5) 需要见证取样复试的建筑材料、构配件、成品、半成品,监理工程师应在报
洁净区人员控制管理制度
洁净区人员控制管理制度 目的:制定洁净室从员控制管理规定,确保洁净室洁净度不低于控制标准。 二、适用范围:适用于生产部洁净区各生产岗位。 三、责任者:生产部管理人员、生产操作者、QA监督员。 四、管理规定: 1.洁净室仅限于该区域生产操作人员、生产部管理人员和经批准的人员进入。 2.洁净室内生产操作人同定员上岗,限制操作人同和管理人员进入的人数。3.洁净室生产操作人员定员和允许进入的最多人员如下:
环境突发事故应急救援预案 目录 编写说明………………………………………………………………… 1.基本情况……………………………………………………………… 2.环境污染目标及其特性、对周围的影响…………………………… 3、应急救援组织机构、组成、职责划分…………………………… 4.报警、通讯联系方式………………………………………………… 5.事故发生后应采取的处理措施…………………………………… 6.人员紧急疏散、撤离……………………………………………… 7.危险区的隔离……………………………………………………… 8.检测、抢险、救援及控制措施…………………………………… 9.现场保护与现场洗消……………………………………………… 10.应急救援保障……………………………………………………… 11.事故应急救援终止程序…………………………………………… 12.应急救援培训计划………………………………………………… 13.附件: ……………………………………………………………… (1)组织机构名单………………………………………………… (2)值班联系电话………………………………………………… (3)组织应急救援有关人员联系电话…………………………… (4)政府有关部门联系电话…………………………………… (5)平面布置图…………………………………………………… (6)周边区域的单位、社区、重要基础设施分布图及有关联系方式,供电、供水单位的联系方式…………………………… (7)保障制度………………………………………………………
(完整word版)钢结构质量控制要点
钢结构质量控制要点 1、质保体系检查: 1)施工单位的资质条件及焊工上岗证; 2)原材料(钢材、连接材料、涂料)及成品的贮运条件; 3)构件安装前的检验制度。 2、设计图纸和施工组织设计:详细查看图纸说明和施工组织设计、明确设计对钢材和连接、涂装材料的要求,钢材连接要求,焊缝无损探伤要求,涂装要求及预拼装和吊装要求。 3、质保资料: 1)钢材、焊接材料、高强螺栓连接、防腐涂料、防火涂料等的质量证明书、试验报告、焊条的烘焙记录; 2)钢构件出厂合格证和设计要求作强度的构件试验报告; 3)高强螺栓连接面滑移系数厂家试验报告和安装前复验报告; 4)螺栓连接预拉力或扭矩系数复试报告(包括制作和安装); 5)一、二级焊缝探伤报告(包括制作和安装); 6)首次采用的钢材和材料的焊接工艺评定报告; 7)高强螺栓连接检查记录(包括制作和安装); 8)焊缝检查记录(包括制作和安装); 9)构件预拼装检查记录; 10)涂装检验记录。 4、现场实物检查: (1)焊接 1)焊接外观质量及焊缝缺陷; 2)焊钉的外观质量; 3)焊钉焊接后的弯曲检验; (2)高强螺栓连接 1)连接摩擦面的平整度和清洁度; 2)螺栓穿入方式和方向及外露长度; 3)螺栓终拧质量。
(3)钢结构制作 1)钢结构切割面或剪切面质量; 2)钢构件外观质量(变形、涂层、表面缺陷); 3)零部件顶紧组装面; (4)钢结构安装 1)地脚螺栓位置、垫板规格与柱底接触情况; 2)钢构件的中心线及标高基准点等标志; 3)钢结构外观清洁度; 4)安装顶紧面; (5)钢结构涂装 1)钢材表面除锈质量和基层清洁度; 2)涂层外观质量(包括防腐和防火涂料)。 5、施工质量 (1)钢结构的制作、安装单位的资质等级及工艺和安装施工组织设计;(2)钢结构工程所采用的钢材应具有质量证明书,并应符合设计要求和有关规定: 1)承重结构的钢材应具有抗拉强度、伸长率、屈服强度和硫、磷含量的合格保证; 2)市场结构的钢材强屈比不应小于1.2,伸长率应大于20%; 3)采用焊接连接的节点,当板厚大于或等于50mm,并承受沿板厚方向的拉力时,应进行板厚方向的材料性能试验; 4)进口钢材应严格遵守先试验后的原则,除具有质量证明和商检报告外,进场后,应进行机械性能和化学成分的复试; 5)当钢材表面有锈蚀、麻点或划痕等缺陷时,其深度不行大于该钢材厚度负偏差的1/2; (3)钢结构所采用的连接材料应具有出厂质量证明书,并符合设计要求和有关规定: 1)焊接用的焊条、焊丝和焊剂,应与主体金属强相适应; 2)不得使用药皮脱落或焊芯生锈的焊条和受潮结块的焊剂,焊丝、焊钉在前应
钢结构工程的几个重要质量控制点
钢结构工程的几个重要质量控制点 地脚螺栓的预埋 地脚螺栓的预埋质量直接影响钢结构的安装质量,控制好地脚螺栓(群)的位置、垂直度、长度和标高,对于减少扩孔及调整工作量(甚至避免返工),提高结构安装质量具有重要意义。地脚螺栓的预埋方法可采用直接预埋法,也可采用预留孔法。基础砼浇筑前监理工程师必须严格检查预埋螺栓施工方法的合理性、可靠性,以及各项实测指标是否在规范规定范围内。 焊接工程质量控制 焊接工程是钢结构制作和安装工程最重要的分项之一,监理工程师必须从事前准备,施焊过程和成品检验各个环节,切实作好焊接工程的质量控制工作。焊接质量问题较多存在于手工焊缝,这些问题有:焊瘤、夹渣、气孔、没焊透、咬边、错边、焊缝尺寸偏差大、不用引弧板、焊接变形不矫正、飞溅物清理不净等。鉴于这种情况,监理工程师必须做好以下各项工作: 1.检查焊接原材料出厂质量证明书; 2.检查焊工上岗证; 3.督促进行必要的焊接工艺试验; 4.施焊过程中加强巡视检查,监督落实各项技术措施; 5.严格进行焊缝质量外观检查和焊缝尺寸实测;
6.督促进行无损检测工作。 高强度螺栓连接工程 高强度螺栓连接工程也是钢结构工程最重要的分项之一,也是目前施工质量的薄弱环节之一,主要表现在: 1.高强度螺栓有以次充好现象,(用普通精制螺栓代替高强度螺栓); 2.高强度螺栓连接面处理达不到规范规定要求,包括表面处理情况,平整密贴情况,螺栓孔质量情况等; 3.高强度螺栓施拧不按规范规定进行,如不分初拧、终拧而一次完成,不用扭矩扳手、全凭主观估计等。为保证高强度螺栓连接工程的施工质量,监理工程师必须以高度的责任心,在督促承包单位提高质量意识、加强质量管理、落实质量保证措施的同时,积极采用旁站监督、平行检验等工作方法,只有这样才能使高强度螺栓连接工程的施工质量处于严格的控制之下。 钢结构除锈及涂装工程 钢结构的除锈和涂装是目前钢结构承包单位较易忽视的一项工作,也是钢结构工程施工的薄弱环节。这种现象不纠正,对钢结构的施工质量影响甚大,因为除锈和涂装质量的合格与否直接影响钢结构今后使用期间的维护费用,还影响钢结构工程的使用寿命、结构安全及发生火灾时的耐火时间(防火涂装)。造成这种现象的思想根源在于承包单位有关人员对涂装工作的重要性认识不足,再加上缺乏质量责任心,甚至惟利是图,最终导致涂装工程质量经常出现问题。故监理工程师必须对除锈和涂装工作给予高度重视,对各个工序进行严格
洁净室温湿度如何控制精编版
洁净室温湿度如何控制公司标准化编码 [QQX96QT-XQQB89Q8-NQQJ6Q8-MQM9N]
如何对洁净室温湿度进行控制 提高,出现了工艺对温湿度的要求也越来越严的趋势。 净化工程具体工艺对温度的要求以后还要列举,但作为总的原则看,由于加工精度越来越精细,所以对温度波动范围的要求越来越小。例如在大规模集成电路生产的光刻曝光工艺中,作为掩膜板材料的玻璃与硅片的热膨胀系数的差要求越来越小。直径100 um的硅片,温度上升1度,就引起了线性膨胀,所以必须有±度的恒温,同时要求湿度值一般较低,因为人出汗以后,对产品将有污染,特别是怕钠的半导体车间,这种车间不宜超过25度。 湿度过高产生的问题更多。相对湿度超过55%时,冷却水管壁上会结露,如果发生在精密装置或电路中,就会引起各种事故。相对湿度在50%时易生锈。此外,湿度太高时将通过空气中的水分子把硅片表面粘着的灰尘化学吸附在表面耐难以清除。相对湿度越高,粘附的难去掉,但当相对湿度低于30%时,又由于静电力的作用使粒子也容易吸附于表面,同时大量半导体器件容易发生击穿。对于硅片生产最佳温度范围为35—45%。 洁净室中的气压规定 对于大部分洁净空间,为了防止外界污染侵入,需要保持内部的压力(静压)高于外部的压力(静压)。压力差的维持一般应符合以下原则: 1.洁净空间的压力要高于非洁净空间的压力。 2.洁净度级别高的空间的压力要高于相邻的洁净度级别低的空间的压力。 3.相通洁净室之间的门要开向洁净度级别高的房间。 压力差的维持依靠新风量,这个新风量要能补偿在这一压力差下从缝隙漏泄掉的风量。所以压力差的物理意义就是漏泄(或渗透)风量通过洁净室的各种缝隙时的阻力。 洁净室中的气流速度规定 这里要讨论的气流速度是指洁净室内的气流速度,在其他洁净空间中的气流速度在讨论具体设备时再说明。 对于乱流洁净室由于主主要靠空气的稀释作用来减轻室内污染的程度,所以主要用换气次数这一概念,而不直接用速度的概念,不过对室内气流速度也有如下要求; (1)送风口出口气流速度不宜太大,和单纯空调房间相比,要求速度衰减更快,扩散角度更大。 (2)吹过水平面的气流速度(例如侧送时回流速度)不宜太大,以免吹起表面微粒重返气流,而造成再污染,这一速度一般不宜大干s。 对于平行流洁净室《习惯上称层流洁净室),由于主要靠气流的“活塞打挤压作用排除行染,所以截面上的速度就是非常重要的指标。过去都参考美国20gB标准,采用s.但人们也都了解到这样大速度所需要的通风量是极大的,为了节能,也都在探求降低速一风速的可行性。 在我国,《空气洁净技术措施》和<洁净厂房设计规范))都是这样规定的 垂直平行流(层流)洁净室≥s 水平平行流(层流)洁净室≥ m/s 研究表明以上规定基本上满足控制污染的要求,但认为应区别不同情况分出不同的档别,更能体现节能的目的。
钢结构施工质量控制要点
钢结构施工质量控制要点 一、钢结构工程准备工作(事前)监理控制要点 01 施工单位资质审查 由于钢结构工程专业性较强,对专业设备、加工场地、工人素质以及企业自身的施工技术标准、质量保证体系、质量控制及检验制度要求较高,一般多为总包下分包工程,在这种情况下施工企业资质和管理水平相当重要。因此,资质审查是重要环节,其审查内容: (1)施工资质经营范围是否满足工程要求。 (2)施工技术标准、质量保证体系、质量控制及检验制度是否满足工程设计技术指标要求。 (3)考察施工企业生产能力是否满足工程进度要求。 02 焊工素质的审查 焊工必须经考试合格并取得合格证书,持证焊工必须在其考试合格项目及其认可范围施焊。 (1)检查数量:全数检查(现场人员)。 (2)检查方法:检查焊工合格证及其认可范围、有效期。 03 图纸会审及技术准备 按监理规划中图纸会审程序,在工程开工前熟悉图纸,召集并主持设计、业主、监理和施工单位专业技术人员进行图纸会审,依据设计文件及其相关资料和规范,把施工图中错漏、不合理、不符合规范和国家建设文件规定之处解决在施工前。 协调业主、设计和施工单位针对图纸问题,确定具体的处理措施或设计优化。督促施工单位整理会审纪要,最后各方签字盖章后,分发各单位。
04 施工组织设计(方案)审查 (1)督促施工单位按施工合同编制专项施工组织设计(方案)。经其上级单位批准后,再报监理。 (2)经审查后的施工组织设计(方案),如施工中需要变更施工方案(方法)时,必须将变更原因、内容报监理和建设单位审查同意后方可变动。 05 例会 组织参加每周召开一次由建设、施工、监理单位三方共同参加的工地例会,及时解决施工中的问题。 06 钢结构工程准备工作具体控制要点 (1)根据《建筑工程施工质量验收统一标准》GB50300-2013以及《钢结构工程施工质量验收规范》GB50205-2011规定,作为一个分部工程,又下分钢结构焊接、紧固件连接、钢零件及钢部件加工、钢部件组装、钢结构预拼装、钢结构安装工程、压型金属板、钢结构涂装等分项工程、关于钢结构原材料(包括钢材、焊材、涂装材料等),由于其对钢结构的质量影响很大,在钢结构规范里单独成章。 (2)检查焊工合格证及其认可范围、有效期。 (3)施工方对其首次采用的钢材、焊接材料、焊接方法、焊接热处理等,应进行焊接工艺评定,并根据评定报告确定焊接工艺。监理方全数检查焊接工艺评定报告,按设计要求焊缝质量等级标准检查。(4)钢构件安装前检查建筑物的定位轴线(开间尺寸和跨度尺寸)和标高、预埋件的规格及其紧固应符合设计要求。 (5)工程柱上钢筋混凝土牛腿顶的预埋钢板直接作为钢构件的支承
各行业无尘室及洁净度特点
各行业无尘室及洁净度特点 电子制造业: 随着计算机、微电子和信息技术的发展,推动了电子制造业的飞速发展,也带动了洁净室技术的发展,同时对洁净室的设计提出了更高的要求,电子制造业的无尘车间设计是一项综合的技术,只有充分了解电子制造业的无尘车间设计特点,做到设计合理,才能让电子制造产业的产品次品率降低,提高生产效率。 电子制造业洁净室的特点: 洁净度等级要求高,风量、温度、湿度、压差、设备排风按需受控,照度、洁净室截面风速按设计或规范受控,另外该类洁净室对静电要求极其严格。其中对湿度的要求尤甚。因为过于干燥的厂房内极易产生静电,造成CMOS集成损坏。一般来说,电子厂房的温度应控制在22℃左右,相对湿度控制在50-60%之间(特殊洁净车间有相关温湿度规定)。这时可有效地消除静电,并使人也感觉舒适。芯片生产车间、集成电路无尘室和磁盘制造车间是属于电子制造行业洁净室的重要组成部分,由于电子产品在制造、生产过程中对室内空气环境和品质的要求极为严格,主要以控制微粒和浮尘为主要对象,同时还对其环境的温湿度、新鲜空气量、噪声等作出了严格的规定。 1、电子制造厂万级洁净室内的噪声级(空态):不应大于65dB(A)。 2、电子制造厂洁净室垂直流洁净室满布比不应小于60%,水平单向流洁净室不应小于40%,否则就是局部单向流了。 3、电子制造厂洁净室与室外的静压差不应小于10Pa,不同空气洁净度的洁净区与非洁净区之间的静压差不应小于5Pa。
4、电子制造行业万级洁净室内的新鲜空气量应取下列二项中的最大值: (1)补偿室内排风量和保持室内正压值所需的新鲜空气量之和。 (2)保证供给洁净室内每人每小时的新鲜空气量不小于40m3。 (3)电子制造行业洁净室净化空调系统加热器,应设置新风,超温断电保护,若采用点加湿时应设置无水保护,寒冷地区,新风系统应设置防冻保护措施。无尘室的送风量,应取下面三项最大值:保证电子制造厂无尘室空气洁净度等级的送风量;根据热,湿负荷计算确定电子厂洁净室的送风量;向电子制造厂洁净室内供给的新鲜空气量。 生物制造业: 生物制药工厂的特点: 1、生物制药工厂不仅设备费用高、生产工艺复杂、洁净级别和无菌的要求高,而且对生产人员的素质有严格的要求。 2、在生产过程中会出现潜在的生物危害,主要有感染危险,死菌体或死细胞及成分或代谢对人体和其他生物致毒性、致敏性和其他生物学反应,产品的致毒性、致敏性和其他生物学反应,环境效应。 洁净区: 需要对环境中尘粒及微生物污染进行控制的房间(区域),其建筑结构、装备及其使用均具有防止该区域内污染物的引入、产生和滞留的功能。 气锁间: 设置于两个或数个房间之间(如不同洁净度级别的房间之间)的具有两扇或多扇门的隔离空间。设置气锁间的目的是在人员或物料出入其间时,对气流进
钢结构工程质量保证措施
工程质量保证措施 按照本工程招标文件的要求及我公司的实力,我们确保该工程达 到优良标准,为此特制定如下措施: 一、质量保证体系 1、质量体系(见附页) 公司结合施工生产管理实际,编制了企业质量体系文件,并保持其运行中的适应性、有效性,确保公司的各项质量活动始终处于受控状态,不断提高企业的质量保证能力和工程质量、服务质量水平。 2、过程控制 (1)施工过程中使用合适和合格的施工设备,对设备进行保养、 维护,使其处于完好状态。 (2)根据工程合同的要求,按照《钢结构施工验收规范》(GB50205 —2001 )和《公司质量管理内控标准》在施工组织设计中制定工程质量计划,对施工过程进行重点控制。 A、施工图纸会审:与本工程有关人员对设计图纸认真审阅,尽快熟悉掌握图纸内容。首先由技术部组织有关技术人员对图纸进行预审,然后会同本工程业主、设计单位的有关人员进行图纸会审,由技术部填写出图纸会审记录,记录必须由建设方、设计方、施工方三方签字盖章后生效,发至技术部、生产部、质检部、项目部各一份,由工地技术负责人存放并根据图纸会审记录的内容修改图纸,组织施
B、编制施工组织设计:由项目部经理组织有关人员编制《施工组织设计》由技术总负责人审批后,交建设方审批后,付储实施。 C、施工现场准备:工地负责现场准备工作按照建筑总平面图定位放线,设置永久性标志;建立健全项目部岗位责任制,明确职责,所有施工、质量、安全人员必须经过培训,并持证上岗。 D、技术交底:技术负责人负责编写分项工程技术交底,签发 给生产部、项目部,并严格按技术要求生产施工,做好施工日志的填 写和存放。 本工程质量保证体系 技术交底的编写依据为图纸、规范、规程、国家有关规定及施工组织 设计。
钙处理工艺对低碳冷镦钢洁净度的影响
118 2007年炉外精炼年会论文集 钙处理工艺对低碳冷镦钢洁净度的影响 高振波1)梁海庆1)吴坚1)胡义贵1)李颂1)杜松林1, 2) 1) 马钢第三钢轧总厂,安徽马鞍山,243000 2) 北京科技大学冶金与生态工程学院,北京100083 摘要本文对钙处理工艺过程中夹杂物变性处理需要的钙含量以及硫化钙的生成条件进行了 热力学计算,确定了LF处理后硫含量需控制的上限和钙处理后钙含量所需的下限;并对温度和 喂钙线量对钙的收得率的影响、钙处理后弱吹氩时间对钢中钙和铝的损失进行了试验摸索。以理 论计算和试验结果为基础,优化钙处理工艺,保证LF处理后钢液含硫不大于0.007%,按每炉钢 喂钙线100~200m、喂钙线后弱吹氩15~30分钟,最终提高低碳冷镦钢夹杂物合格率达到92%。 关键词冷镦钢;钙处理;弱吹氩;洁净度;夹杂物 冷镦钢主要用于制造紧固件产品,客户对冷 镦钢的使用性能和加工性能要求很高,这样要求冷镦钢具有较好的内部质量,夹杂物大小、分布、数量、种类均较好。作为衡量钢材质量的一个重要指标—夹杂物等级,通过电镜扫描、能谱分析等手段,根据冷镦钢夹杂物评级标准,检测到马钢第三钢轧总厂(以下简称三钢轧)冷镦钢夹杂物合格率83%,B类和DS类夹杂物超标较多。实践证明,钙处理是控制夹杂物的重要环节。本文通过理论计算和试验并结合生产实践,提出了钙处理工艺优化的方向,并付诸实践,有效提高了低碳冷镦钢洁净度。1工况条件简介 1.1 工艺路线 铁水预处理—50t复吹转炉—吹氩合金微调站—70t LF炉—六机六流140mm方坯连铸机—高速线材轧机 LF工序配备双管喂线机; 140mm方坯连铸机浇注方式为“外装式浸入水口+保护渣”。 1.2 钢种内控成份 冷镦钢成分请见表1 表1 马钢冷镦钢内控成分/% Table 1 controlled component of cold heading steel/% wt/% C Si Mn S P Al ≤0.10 ≤0.08 0.20~0.5≤0.015 ≤0.030 0.020~0.040 1.3 检测方法 (1)使用瑞士ARL-4460型光谱仪快速分析钢中C、Si、Mn、P、S、Al等元素; (2)通过电镜扫描观察夹杂物形态,能谱分析夹杂物组成; (3)采用小样电解分析夹杂物总量; (4)采用TOS针状全氧取样器取样,检验全氧、氮。 2 试验结果及分析 钙处理主要目是使高熔点的Al2O3变性为低熔点的铝酸钙,再经过一段时间弱吹氩,降低非金属夹杂物含量,从而改善钢液的可浇性,提高钢液的洁净度。 由于钙的沸点低(约1487℃)、蒸气压大、在钢中溶解度低,向钢包钢液内喂钙线进行钙处理过程钢液沸腾非常严重,这必然导致钢液的二次氧化,因此,怎样既能达到钙处理的目的,又能使二次氧化程度降到最小,以及喂过钙线后弱吹氩时间的掌握成为钙处理技术的关键。 2.1 钙处理前钢中硫含量对钙处理效果的影响 在钢包和中间包取样,通过电镜扫描和能谱分析,结果在钢包样里发现了少量硫化钙,在中间包样发现了更多硫化钙夹杂,请见图1和图2 。
钢结构工程施工监理质量控制要点.doc
钢结构工程施工监理质量控制要点 杭州西湖文化广场A、B、 C、E 区各单体建筑中有一部分选用了钢结构作为主体结 构构件,我公司将严格按照新执行的《钢结构工程施工质量验收规范》(GB50205-2001) 并参照如下的钢结构工程施工验收标准体系:建设工程质量管理条例→工程建设标准 强制性条文→钢结构工程施工质量验收规范→工艺及评优推荐性标准→企业标准,对 高层钢结构、门式刚架、网架、压型钢板、组合结构及焊接、高强螺栓连接、栓焊等 方面的质量进行监督管理、验收评定。 1监理控制总体思路 钢结构工程施工质量验收过程中,始终以《建筑工程施工质量验收统一标准》 (GB50300-2001)为基础,贯彻“验评分离、强化验收、完善手段、过程控制”十六字 方针,结合钢结构工程的特点,并且努力做到“三个协调和一个接口”,即与《建筑 工程施工质量验收统一标准》相协调,与《钢结构设计规范》相协调,与其他13 部建 筑工程专业施工质量验收规范相协调,为后续施工工艺和评优标准等推荐性标准留有 接口。 2钢结构施工质量监理控制要点 2.1 主要验收控制内容 根据钢结构工程施工的特点,结合设计规范及钢结构工程施工质量验收规范,本 工程钢结构部分大致应划分成10 个分项工程,即:焊接工程、螺栓连接工程、钢零件 及钢部件加工工程、钢构件组装工程、钢构件预拼装工程、单层钢结构安装工程、多 层及高层钢结构安装工程、钢网架结构安装工程、压型金属板工程及钢结构涂装工程 等。 在分项工程中,严格按照新规范对施工工艺或工艺顺序规定的“主控项目” 和“一 般项目”的检查内容检查验收。“主控项目”全部达到合格质量标准,“一般项目” 不允许突破 80%的界限,所检验项目方能达到合格质量标准。 2.2 其他验收控制内容 结合钢结构工程的特点,遵照新的统一标准的规定,其他验收控制内容主要有: (1)加强管理方面的验收,要求施工单位必须健全质量管理和质量控制体系; (2)强调和强化钢结构工程用各种主要材料的进场准入,提醒验收人员在每个分项工程验收时都必须首先进行进场验收; (3)强调检验批的验收是最小验收单位,同时也是最基本的验收工作,检验批的划分 遵循下列原则:①单层钢结构按变形缝或空间刚度单元划分;②多层钢结构按楼层或施工 段划分;③进场验收可根据工程规模及进料实际情况划分;④压型钢板安装可按屋面、墙 面、楼面等用途划分;⑤根据施工单位的加工和安装能力或分包情况,结合工期要求划 分。按照上述原则并结合本工程实际情况,由监理和施工单位在施工前,
纯净钢好
纯净钢 纯净钢一般是指钢中杂质元素磷、硫、氧、氮、氢、碳和非金属夹杂物含量很低的钢。在这里的杂质是随钢种变化的,这是因为某一类元素在某钢种内是有害杂质,但可能在另一种钢内其有害程度会减轻或者甚至是有益元素。也就是说对于钢性能要求不同,纯净钢所要求的控制因素和控制力度也不同。 纯净钢要求钢中硫含量小于50PPM,磷含量小于50PPM,氧含量小于10PPM,氢含量小于30PPM,氮含量小于50PPM。对于具体钢种会用不同标准。 钢材中的夹杂物可引起许多缺陷,钢的洁净度取决于钢中非金属夹杂物的数量、形态和尺寸分布, 因钢种及其用途不同而定义不同。 研究和控制钢的洁净度的关键是其精确的评价方法, 在炼钢生产的各个阶段测定夹杂物的数量、尺寸分布、形状和化学成分。尽管测定技术有多种(有精确而昂贵的直接测定法, 还有快速而廉价的间接测定法) , 只有可靠性是相对的选择依据。 直接测定法: (1) 金相显微镜观测(MMO );(2) 图像扫描( I A )法;(3) 硫印法;(4) 电解(蚀)法;(5) 电子束熔炼(EB)法;(6) 水冷坩埚熔炼法(CC);(7) 扫描电子显微术(SEM );( 8) 脉冲鉴别分析光谱测量法(O ES -PDA );(9) 曼内斯曼夹杂物检测法(M I DA S) ;(10) 激光衍射颗粒尺寸分析法(LDPSA );(11) 常规的超声波法(CU S);(12) 锥形样品扫描法;(13) 分级热分解法(FTD);(14) 激光显微探针质谱分析法(LAMM S);(15) X2射线光电子光谱法(XPS);(16) 俄歇电子光谱法(AES);(17) 光电扫描法;(18) 库尔特计数分析法;(19) 液态金属洁净度分析法(L I MCA );(20) 钢水超声技术。 间接方法: (1)定氧;(2)吸氮检测;(3)溶解铝减少值的检测;(4)炉渣成分检测;(5)检测浸入式水口结瘤。
《管道内部清洁度质量控制管理规定》
管道内部清洁度质量控制管理规定 (A版) 中国石油工程建设公司 宁夏石化炼油项目经理部
前言 本管理规定是根据《项目质量计划》(A 版)的要求编写的,是《项目质量计划》的支持性文件。 本规定由项目QA/QC 部提出。 本规定由QA/QC 部起草并负责管理。 本规定主要起草人:高安翔 审核人:张志 批准人:王家君
目录 1. 适用范围 (4) 2. 目的 (4) 3. 职责 (4) 4. 工作程序及要求 (4) 5. 相关资料 (9) 6. 附则 (9) 7. 附表 (9)
1. 适用范围 本管理规定适用于宁夏石化500 万吨/年炼油改造项目工程建设的管道内部清洁度质量控制。 2. 目的 明确和规范管道施工全过程各环节内部清洁度质量控制要求,确保设备、管线内清洁无异物,缩短管道吹扫、清洗、试车时间。 3. 职责 3.1 QA/QC 部: 3.1.1 3.1.2 3.2 3.2.1 3.2.2 负责项目管道内部清洁度质量控制管理规定的制定和修订; 监督、检查管道内部清洁度质量控制的实施情况。 施工技术部: 对施工承包商管道内部清洁度质量控制情况进行全程管理; 对管道内部清洁度质量控制不达标的施工承包商进行处理、 整顿。 3.3 采购部: 3.3.1 负责总承包单位采购的管道组成件的到货检验和发放施工承包商前的仓储管理。 3.4 3. 4.1 3.4.2 施工承包商: 在管道施工全过程对管道内部清洁度实施质量控制; 对管道系统内部清洁度进行自检,并形成确认记录。 4. 工作程序及要求 4.1 管道内部清洁度的质量控制应贯穿材料保管、防腐、预制、安
钢结构质量控制程序
一、工程质量及质量管理 1、项目质量管理的主要对象是工程质量,它是一个综合性的指标,包括如下几个方面: 1.1工程投产运行后,所生产的产品的质量,该工程的可用性,使用效果和产出效果、运行的安全性和可靠性。 1.2工程结构设计和施工的安全性和可靠性。 1.3所使用的材料、设备、工艺、结构的质量以及他们的耐久性和整个工程的寿命。 1.4工程的其它方面,如外观造型、与环境的协调、项目运行费用的高低以及可维护性和可检查性等。 2、搞好质量管理、提高质量意识 2.1首先是各级领导对质量管理的重视,搞好质量管理工作。 2.2搞好对员工的质量管理培训工作,高度提高全员的质量意识。 2.3牢固树立“质量第一”的原则,做到人人重视质量。 3、认真学习相关技术规范及工艺规程,提高员工队伍的整体素 质
3.1基层管理人员首先熟悉了解相关的技术规范及工艺规程,并组织自己的队伍进行学习、掌握相关知识并指导应用于实际生产中去。 3.2操作者要熟悉施工图纸及本工程的精度要求,明确自己所操作的工作内容和所要达到的质量目标。 3.3质检部门定期做好相关标准的培训,提高质检人员的技术水平及沟通能力,做到即使质检员又是指导员。 二、报检管理流程 各道工序完成后,必须进行三检制,即:自检、互检、专检。经过三检合格后才允许转入下道工序。(见流程图)报检管理流程图:
三、原材料质量管理 1、主材进厂质量检验 1.1质保书审核:依据相关标准 1.2外观质量检验:材料规格和表面质量
四、钢结构加工制造过程的质量控制 必须按施工图纸施工,严格执行相关标准及工艺规程,保证其加工制造精度,如发现图纸有误及工艺不完善的问题及时反馈给相关部门,待处理后按新的方案执行。 1.钢板预处理 钢结构加工制造的第一道工序是主材的预处理。预处理的作用有三点:第一是对钢材轧制时的内应力有消除作用;第二是对钢材有赶平的作用;第三就是对钢材的起到临时防腐作用。钢材预处理要做好以下三点: 1.1经过预处理流水线对主材进行预处理。 1.2做好钢板规格及炉批号的移植工作。 1.3对预处理表面的漆膜厚度进行检查。 2.钢板拼接(荒料、成料) 2.1接荒料是未进行下料之前先接宽或接长。 2.2接成料就是先下好线形再拼接。 2.3拼板时注意正确使用引、熄弧板。 2.4焊接区域要按要求进行清理打磨。
钢结构质量管控要点
钢结构质量管控要点 xx公司技术部 二〇一九年十月
目录 一、基本规定 (2) 二、施工验算 (3) 三、材料 (3) 四、焊接 (4) 五、紧固件连接 (6) 六、构件组装及加工 (6) 七、钢结构预拼装 (7) 八、钢结构安装 (7) 九、防护涂装 (8) 十、施工测量、施工监测 (9) 十一、施工检测 (9)
钢结构质量管控要点 一、基本要求 1、钢结构工程实施前,应有经钢结构施工单位技术负责人审批的施工组织设计、与其相应配 套的专项施工方案(如吊装方案、脚手架搭设方案、支撑系统卸载方案)等技术文件,并经总承包单位技术负责人、相关部门负责人、项目经理审批。 2、工程部审核完钢结构施工方案报工程技术部、设计部等相关部门审核后,再报主管工程领 导审批后实施。 3、跨度≥36m、悬挑长度≥12m的钢结构及跨度≥60m的网架和索膜结构安装工程的施工技术 方案和安全应急预案,应由总包单位组织专家进行论证。项目公司工程部、监理单位、工程技术部参与。 4、钢结构图纸下发后7日内,工程部组织相关人员参加图纸会审。工程部于图纸会审后2天内 将会审记录提交设计部确认,设计部接到会审记录一周内下发经设计部确认的会审记录给与会部门,并抄报工程管理及监察部。 5、钢结构工程施工及质量验收时,钢结构施工单位、总承包单位、监理单位和检测机构的计 量器具及检查工具应在有效期内,工程部应对各方的计量器具及检查工具每月进行检查。 6、现行《钢结构工程施工规范》未涉及的新技术、新工艺、新材料和新结构,首次使用时, 工程部应组织钢结构施工单位、总承包单位按国家标准对其进行相应的试验,并根据试验结果确定相应的施工方案和验收标准,设计部组织专家论证通过后,方可实施。 7、工程部每周应向工程技术部报备钢结构焊缝、紧固件检验批及分项分部检测验收结果(附 检测报告)。 8、工程部应委托具有资质的第三方按照规范、设计要求对钢结构焊缝、紧固件进行检测。 9、钢结构施工单位在钢构件组装完毕自检合格后,报总包单位、工程部验收,工程技术部抽 查不少于10%。 10、钢结构制造和安装应满足设计要求,过程中的检查结果应有文字记录和有日期的影像资 料。 11、工程部应每月对钢结构生产单位进行例行检查,检查内容包括零部件材料、构件生产质 量等。
钢结构工程施工质量控制论文
刍议钢结构工程施工质量的控制 摘要:随着我国钢铁工业的发展,钢材在建筑业中的应用亦有很大的变化。国家建筑技术政策由以往的限制使用钢结构转变为积极合理推广应用钢结构,从而大大推动了建筑钢结构的快速发展。钢结构工程由于其造价低、结构性能好、施工速度快,大量的钢结构工业厂房、住宅小区、高层建筑、桥梁相继出现取代了传统的砖混结构、混凝土框架结构建筑,由于钢结构工程在建筑领域被广泛应用,施工质量的好坏就直接影响工程结构的安全,如何控制工程施工质量的好坏已引起业内人士的重视。因此,监理工程师对钢结构施工质量的控制就显得尤为重要。结合实际就监理过程中对钢结构施工质量控制谈几点体会。 关键词:钢结构建筑施工质量控制 abstract: with the development of steel industry in our country, in the application of steel construction industry also have a big change. national construction technology by past policies limiting the use of steel structure into positive reasonable application steel structure, which greatly promoted the rapid development of construction steel structure. steel structure engineering because of its low cost, the structure, good performance, construction speed is quick, a large amount of steel structure industry workshop, residential districts and high-rise buildings, bridges