数控车床主轴设计说明

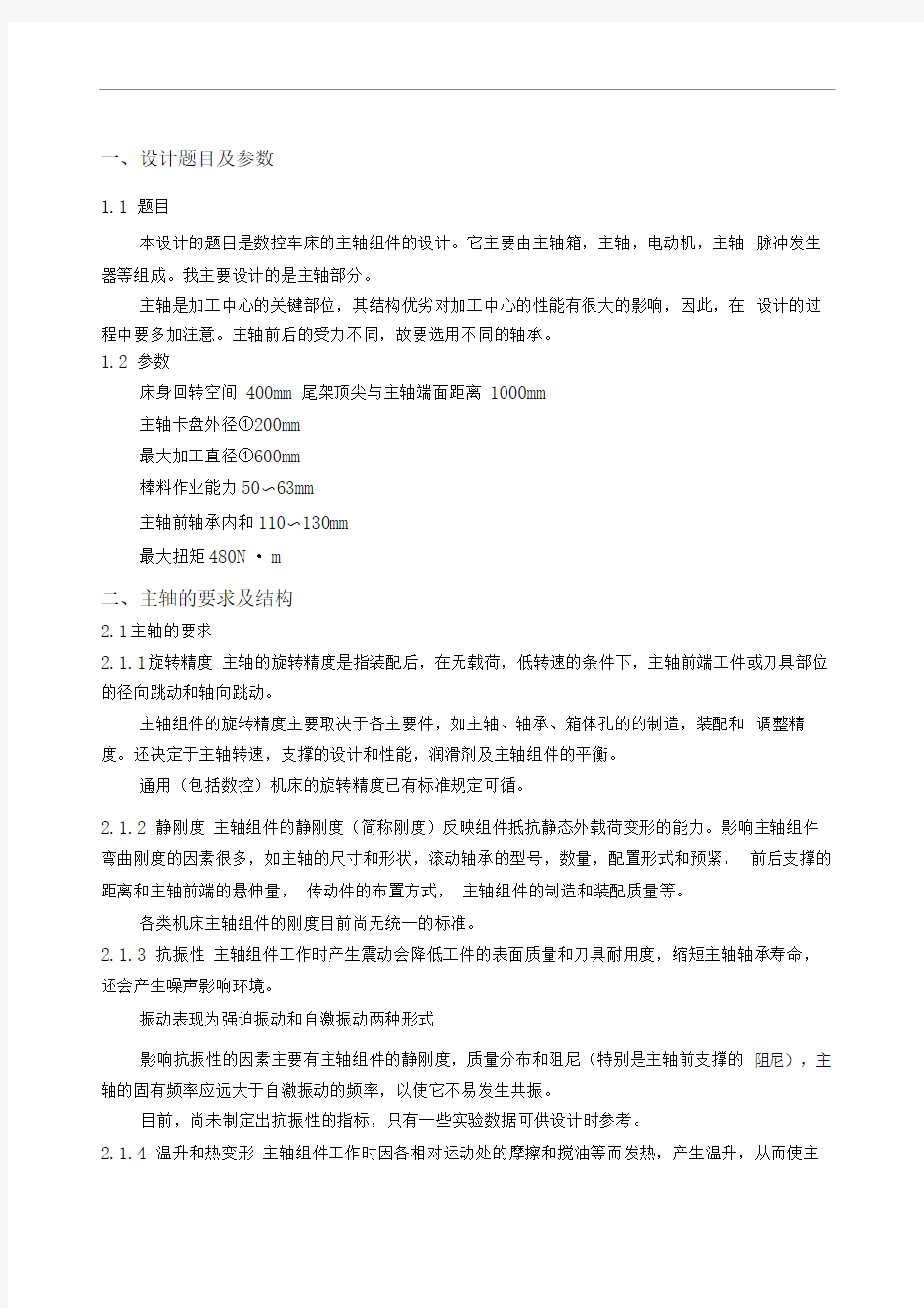
随着市场上产品更新换代的加快和对零件精度提出更高的要求,传统机床已不能满足要求。数控机床由于众多的优点已成为现代机床发展的主流方向。它的发展代表了一个国家设计、制造的水平,在国内外都受到高度重视。
现代数控机床是信息集成和系统自动化的基础设备,它集高效率、高精度、高柔性于一身,具有加工精度高、生产效率高、自动化程度高、对加工对象的适应强等优点。实现加工机床及生产过程的数控化,已经成为当今制造业的发展方向。可以说,机械制造竞争的实质就是数控技术的竞争。
本课题的目的和意义在于通过设计中运用所学的基础课、技术基础课和专业课的理论知识,生产实习和实验等实践知识,达到巩固、加深和扩大所学知识的目的。通过设计分析比较机床的某些典型机构,进行选择和改进,学习构造设计,进行设计、计算和编写技术文件,达到学习设计步骤和方法的目的。通过设计学习查阅有关设计手册、设计标准和资料,达到积累设计知识和提高设计能力的目的。通过设计获得设计工作的基本技能的训练,提高分析和解决工程技术问题的能力,并为进行一般机械的设计创造一定的条件。
一、设计题目及参数
1.1 题目
本设计的题目是数控车床的主轴组件的设计。它主要由主轴箱,主轴,电动机,主轴脉冲发生器等组成。我主要设计的是主轴部分。
主轴是加工中心的关键部位,其结构优劣对加工中心的性能有很大的影响,因此,在设计的过程中要多加注意。主轴前后的受力不同,故要选用不同的轴承。
1.2 参数
床身回转空间400mm 尾架顶尖与主轴端面距离1000mm
主轴卡盘外径①200mm
最大加工直径①600mm
棒料作业能力50?63mm
主轴前轴承内和110?130mm
最大扭矩480N ? m
二、主轴的要求及结构
2.1主轴的要求
2.1.1旋转精度主轴的旋转精度是指装配后,在无载荷,低转速的条件下,主轴前端工件或刀具部位的径向跳动和轴向跳动。
主轴组件的旋转精度主要取决于各主要件,如主轴、轴承、箱体孔的的制造,装配和调整精度。还决定于主轴转速,支撑的设计和性能,润滑剂及主轴组件的平衡。
通用(包括数控)机床的旋转精度已有标准规定可循。
2.1.2 静刚度主轴组件的静刚度(简称刚度)反映组件抵抗静态外载荷变形的能力。影响主轴组件弯曲刚度的因素很多,如主轴的尺寸和形状,滚动轴承的型号,数量,配置形式和预紧,前后支撑的距离和主轴前端的悬伸量,传动件的布置方式,主轴组件的制造和装配质量等。
各类机床主轴组件的刚度目前尚无统一的标准。
2.1.3 抗振性主轴组件工作时产生震动会降低工件的表面质量和刀具耐用度,缩短主轴轴承寿命,还会产生噪声影响环境。
振动表现为强迫振动和自激振动两种形式
影响抗振性的因素主要有主轴组件的静刚度,质量分布和阻尼(特别是主轴前支撑的阻尼),主轴的固有频率应远大于自激振动的频率,以使它不易发生共振。
目前,尚未制定出抗振性的指标,只有一些实验数据可供设计时参考。
2.1.4 温升和热变形主轴组件工作时因各相对运动处的摩擦和搅油等而发热,产生温升,从而使主
轴组件的形状和位置发生变化(热变形)。
主轴组件受热伸长,使轴承间隙发生变化。温度使润滑油粘度降低,降低了轴承的承载能力。
主轴箱因温升而变形,使主轴偏离正确位置。前后轴承的温度不同,还会导致主轴轴线倾斜。
由于受热膨胀是材料固有的性质,因此高精度机床要进一步提高加工精度,往往受热变形的限制。研究如何减少主轴组件的发热,如何控制温度,是高精度机床主轴组件的研究的主要课题之一。
2.1.5 耐磨性主轴组件的耐磨性是指长期保持原始精度的能力,即精度保持性。对精度有影响的首
先是轴承,其次是安置刀,夹具和工件的部位,如锥孔,定心轴径等。
为了提高耐磨性,一般机床主轴上的上述部分应淬硬至HRC6左右,深约1mm.
2.1.6 材料和热处理主轴承载后允许的弹性变形很小,引起的应力通常远远小于钢的强度极限。因此,强度一般不做为选材的依据。
主轴的形状,尺寸确定之后,刚度主要取决于材料的弹性模量。各种材料的弹性模量几乎相同,因此刚度也不是选材的依据。
主轴材料的选择主要根据耐磨性和热处理变形来考虑。普通机床的材料通常是45号或60号优质中碳钢,数控机床需调质处理和淬火。
2.2 主轴的结构为了提高刚度,主轴的直径应该大些。前轴承到主轴前端的距离(称悬伸量)应尽可能小一些。为了便于装配,主轴通常作成阶梯形的,主轴的结构和形状与主轴上所安装的传动
件,轴承等零件的类型,数量,位置和安装方法有直接的关系。
主轴中的孔主要用于通过棒料,拉杆或其它工具。为了能够通过更大的棒料,车床的中空希望大些,但受刚度条件的影响和限制,孔径一般不宜超过外径的70%。主轴的结构如(附图1)。
图1
三、主传动系统变速方式
为了适应不同的加工要求,数控机床主传动主要有以下几种配置方式:
(1)带有变速齿轮的主传动。这种方式在大、中型数控机床采用较多。通过少数几对
齿轮降速,扩大了输出扭矩,以满足主轴的输出扭矩特性的要求,一部分小型数控机床也采用此种传动方式。以获得强有力的切削时所需要扭矩。数控机床使用可调无级变速交流、直流电动机。所以经齿轮变速后,实现8段无级变速,调速范围增加。其优点是可满足各种切削运动输出转矩,具有大范围调速能力。但是由于结构复杂,需要增加润滑及温度控制装置。成本较高,此外,制造和维修也比较困难。(参图a)
(2)—级带传动变速方式。这种传动方式主要应用在中小型数控机床上。采用V型带或同步带传动,可以避免齿轮传动时可引起的振动与噪声,适用于低扭矩特性要求的主轴。这种方式结构简单,安装方便,调试容易,被广泛用于许多数控机床传动中。(参图b)(3)调速电机直接驱动方式,这种主轴传动方式大大简化了主轴箱体与主轴的结构,有效地提高主轴部件的刚度,由于结构紧凑,占用空间少,加工中心的可加工空间相对变大。但是主轴转速的变化及扭矩的输出和电动机输出特性完全一致,电动机的发热对主轴的精度影响大,最好装有冷却装置,否则使用还是受到约束。(参图c)
(4)电主轴直接驱动方式:这种驱动方式其实和(c图)方式差不多,但这种传动方式结构方式更为紧凑,占用空间更小。它主要是将主轴作为电机的转子,箱体壳(与主轴配合箱体壳)作为电机的定子。但是这种电机形式的主轴结构,连带主轴组件都是成套,
要求很高,精度也高。另外制造成本也很高。且容易发热,同样会影响主轴精度以下为传
动方式的结构图:
图(d)电主轴直接驱动方式
综上所述,进行各种传动方式优缺点进行分析
和比较来选取本设计所采用的主轴传动
方式。首先是该设计为数控车床,主轴选用带
传动(同步齿形带),主轴主要是车削加工,
必须保证其加工精度,而带传动能缓和冲击、
吸收振动,故传动平稳。由此选用一级带传动
变速方式。
四、机床夹具的确定
本次设计的数控车床所加工工件长度约为300m长(附图2),夹具相对设计较单一,选用卡
盘夹紧工具即可满足加工要求。卡盘夹紧工件与主轴联接,并与主轴同步旋转。
对于数控车床夹具主要就是卡盘夹具。卡盘从它的工作原理上分为以下几种类型:
①手动松紧卡盘
②液压松紧卡盘
③气动松紧卡盘
④电动松紧卡盘
首先从数控车床的自动化程度讲,手动卡盘属人工操作,不合适。另外液压和气动松紧卡盘
实际工作原理相似,一个是油泵进行驱动,一个是气泵驱动,结构设计简明,传动机构简单。另外电动卡盘同样结构紧凑,效率高,但综上所述,我们选择液压卡盘,液压卡盘结构紧凑,自动化程度高,结构比电动卡盘简单,有时可改装为与其相似的气动卡盘。
(参图d)图(a)带有变速齿轮的主传动图(b)一级带传动变速方式
图(c)调速电机直接驱动方式
另外所设计的数控车床许多装置重于用液压系统,所以用液压卡盘是比较合理的。液压卡盘的控制原理实质为一锁紧回路(附图3)
-O
「软爪2 T型螺母3卡爪座4卡盘体5支椁板
图1液压卡盘
五、主轴主要参数的计算及校核
5.1主轴主要参数的计算
主轴的主要参数是:主轴前端直径D1,主轴内径d。主轴悬伸量a和主轴支撑跨距L
5.1.1主轴前端直径D1
主轴D1 (按电机功率)如下表5-1 (mm:
表5-1
车床、铣床、镗床、加工中心等机床因装配的需要,主轴直径常是自前往后逐渐减小的。前轴颈直径D1大于后轴直径D2对于车、铣床一般D2(0.7?0.9)D j,由上表可取D仁 110mm
因此可知由式子