模具标准
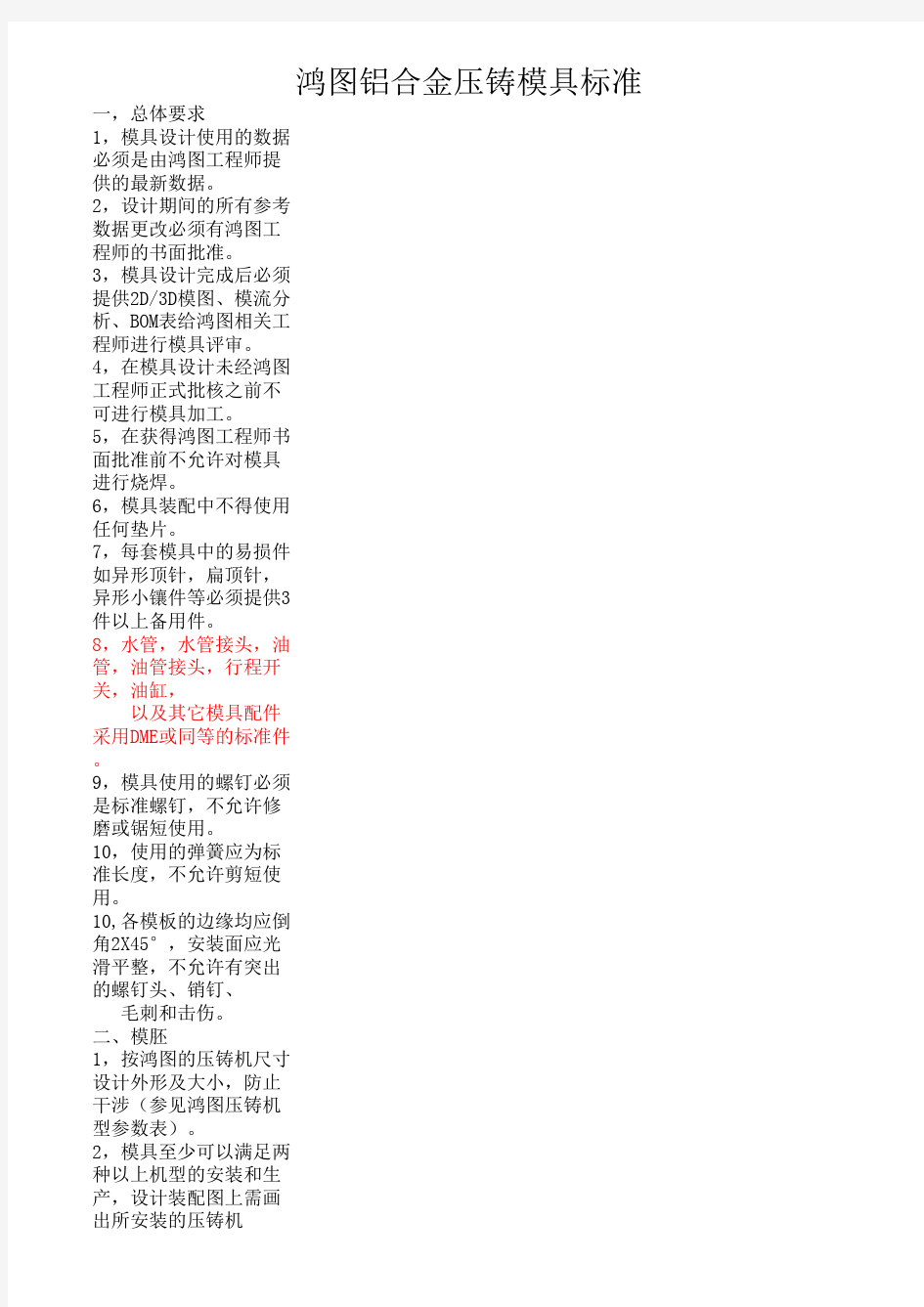

一,总体要求
1,模具设计使用的数据必须是由鸿图工程师提供的最新数据。
2,设计期间的所有参考数据更改必须有鸿图工程师的书面批准。
3,模具设计完成后必须提供2D/3D模图、模流分析、BOM表给鸿图相关工程师进行模具评审。4,在模具设计未经鸿图工程师正式批核之前不可进行模具加工。
5,在获得鸿图工程师书面批准前不允许对模具进行烧焊。
6,模具装配中不得使用任何垫片。
7,每套模具中的易损件如异形顶针,扁顶针,异形小镶件等必须提供3件以上备用件。8,水管,水管接头,油管,油管接头,行程开关,油缸,
以及其它模具配件采用DME或同等的标准件。
9,模具使用的螺钉必须是标准螺钉,不允许修磨或锯短使用。
10,使用的弹簧应为标准长度,不允许剪短使用。
10,各模板的边缘均应倒角2X45°,安装面应光滑平整,不允许有突出的螺钉头、销钉、 毛刺和击伤。
二、模胚
1,按鸿图的压铸机尺寸设计外形及大小,防止干涉(参见鸿图压铸机型参数表)。
2,模具至少可以满足两种以上机型的安装和生产,设计装配图上需画出所安装的压铸机 大杠的尺寸及位置,开模、顶出位置。
3,模具铭牌必须安装在操作者侧经加工出的凹槽中。其上必须注明模具尺寸(长X宽X高) 、重量、适合机型、压射中心位置、生产厂家、产品名称、产品编号、模具编号。
4,重量大于10Kg的模板必须有吊环孔,起吊模具的吊环孔尺寸按下表标准,数量至少2个, 需设计于模具的重心位置(每半模),以利于吊装时的安全。
吊环孔尺寸要求
注:表中的“模具最大重量”的标准制定是建立在两个吊环对称且在重心上。
5,动定模上方距分型面10~15mm处设计宽15mm深5mm的排水槽,一直延伸到模架边缘
(除非模架上方没有安装任何运水装置)6,模具码模槽按下表选用
特殊情况请与压铸工程师协商解决。码模槽尺寸要求
鸿图铝合金压铸模具标准
前模
后模排水槽
分型面
吊环孔
7,所有模具动模侧必须有码模板,不允许用使用支撑柱直接与压铸机中板接触。8,模具应加尽量多的支撑柱。支撑柱直径(或宽度)不小于60mm,
并尽可能靠近压射中心容易变形的部位。模具设计完成时必须进行模具强度校核, 后附校核表。
9,浇口套配合尺寸参考下表
浇口套、压室和压射冲头的配合尺寸压室基本尺寸
D 0浇口套 D (F7)压室D 0(H7)
压射冲头d (e8)50~80
+0.060+0.030+0.0300-0.060-0.10680~120
+0.071+0.036+0.0350-0.072-0.126120~180+0.083
+0.043+0.0400-0.085-0.148
10,模具分型面对动、定模板安装平面的平行度要求请参考下表:
动、定模板安装平面的平行度
5,模具动模上方必须安装防尘板。材质可以选1mm厚不锈钢板。
6,在定模点冷凹槽上要加盖板。
在凹槽下端要开排水槽。
11,模具各部分的尺寸关系,在不与压铸机干涉的前提下,如果没有特别说明,
请按以下关系进行设计。
极限偏差防尘板
盖板
三、前后模镶件
1,模具材料根据模具设计寿命选用8407、4Cr5MoSiVI(H13)、
DH21、DH31-S(日本大同优质钢材)等材料。
2,淬火热处理硬度为HRC48~52.
3,型腔成型表面粗糙度Ra不大于0.4,型腔侧面表面粗糙度应不大于Ra0.2
(客户特殊要求除外),所有表面不允许有击伤,擦伤和微裂纹。
4,型腔最小铸造圆角R0.5,最小拔模斜度为1°,客户特别说明的除外。
擦穿/碰穿位角度应不小于5°
5,多腔模具需要型腔附近刻印型腔号。并在模具图相应型腔部位表示出来。
6,压铸材料需在分流锥上雕刻出来,分流锥在滑块上的则在横浇道上雕刻出来。
7,压铸件加工余量
在铸件的精度所不能保证产品的要求的情况下、例如:直角度、平面度、表面粗糙度等, 应设计加工余量,通过机械加工的方法达到。
设计加工余量时请参考下表(根据GB/T15114-1994制定)
铝合金压铸件的平面度公差
被测量部位尺寸铸件平面度公差矫正后铸件平面度公差适当的加工余量<250.200.100.50
25~630.300.150.50
63~1000.400.200.50
100~1600.550.250.60
160~2500.800.300.70
250~400 1.100.400.80
400~630 1.500.50 1.00 >630 2.000.70 1.00 8,孔的加工余量,
被测量孔的直径适当的加工余量
<60.20
6~100.40
10~180.60
18~300.80
30~50 1.00
50~80 1.20
>80 1.50
三、滑块
3,对于宽度大于200mm的滑块必须在滑块中间加导向装置。
滑道材料为T8A热处理HRC48~52,嵌合在模架上用螺钉锁紧,
滑块座与导轨摩擦面需表面淬硬或氮化处理。
4,油压抽芯应采用楔紧块锁紧,避免用油缸压力来提供锁紧力,对于方向特殊的抽芯应 与鸿图压铸工程师协商滑块锁紧的解决方案。
5,使用斜销抽芯时,滑块两侧到斜销孔的距离最小为10mm。
6,斜销可采用DME或同等规格的标准件。
7,合模后滑块与楔紧块应压紧,接触面积不小于滑块座斜面面积的3/4,
开模后定位应准确可靠。
8,抽芯油缸应采用标准压铸模用油缸,油封必须可以耐高温。
9,楔紧块用T8A或T10A,热处理硬度HRC50~55,
楔紧块斜面角度应为10°~25°与滑块座配做。
10,抽芯行程需避开顶杆位置,如果抽芯和顶杆有干涉,则该模具必须设计拉杆回位装置 并在图纸上说明。
11,滑块抽出行程最小为脱出产品边缘35mm以上。
12,行程杆直径、行程板行程开关型号,按鸿图行程开关标准设计。
13,所有行程开关需装直插式接头。
模具抽芯油缸的行程开关应采用带指示灯的行程开关,并且应能够防水。
14,桥式链接的油缸与滑块座应用半圆活块连接,对于大于5kg的滑块应设M16的吊环孔以
抽芯与滑块座的连接应采用嵌合式的螺钉连接。
16,抽芯支架上要考虑吊装,两侧抽芯在重心上方开设M16的吊环孔,上抽芯则在重心上 开设对称的两个吊环孔。
17,滑块上要尽可能安装冷却回路,特殊情况可与鸿图工程师协商解决。
四、型芯
1,易困气部位和易冲蚀部位需做成镶拼结构。
2,镶件上应加排气结构,并与模胚上的排气槽连通。
3,易冲蚀区表面应披覆或涂层处理。
4,对于长度大于2倍直径的穿孔镶针必须采取加固措施以防镶针弯曲变形。
型芯和镶件应切实固定,防止产生后退和转动现象。
5,形成通孔的型芯碰穿面需留0.1~0.2mm的间隙,以免合模时碰伤。
6,非对称的镶块或型芯需要增设定位结构并编号防止错装。
7,型芯表面是否做氮化或其它处理需根据产品的特性决定,并在模具设计时考虑。8,型芯拔模斜度单边至少0.5°,或按客户图纸要求,擦穿/擦碰面角度需大于5°, 特殊情况需要修改的,要经过鸿图工程师书面批准。
9,长径比不大于3的孔可以铸出,对于长径比大于3的孔可以只铸出一段。
还可以设置镔子孔的形式用加工的方法钻出,除非有特别要求。
7,直径较大、周围壁厚较大或较长的型芯需要考虑安装冷却水。
8,避免型芯在浇口处被冲刷,内浇口应避免直接冲击型芯和镶块,在无法避免的情况下 应考虑取消型芯,或做成局部镶拼结构以便更换。
五,顶出系统
1,模具码模板上应设置限位钉。
2,根据顶出行程,顶针板前应设置推出限位块,以防模具顶出时受损。
3,顶出机构受力中心要求与压铸机的推出装置基本一致。
4,所有模具拉杆接头必须低于码模板1~2mm。
5,顶针如需定位时,顶针头要做定位结构并编号。
右图为推荐的两种顶针止转形式。
6,模具如需要开设钩针时,钩针必须切实定位,开口方向向操作者侧。
钩针开口可参考以下标准制作
钩针开口尺寸参考标准
钩针直径D(mm)开口直径/顶针直径开口长L(mm)
开口斜度 a Φ5~Φ71/37.5
3°Φ8~Φ91/310
6°Φ101/312
7°Φ11~Φ121/3129°
需经过鸿图工程师的书面批准。
9,对所有的顶针需要进行编号,以防错装。
10,拉杆螺纹请按以下标准制作
拉杆螺纹孔参考标准
11,顶针应选用全硬化顶针,不允许使用表面硬化的顶针。
六、冷却系统
1,直通冷却:用Φ10mm的水冷通道,1/4"的管螺纹,配标准管接头,管长以安装后 露出模架约60mm为准。
点冷:点冷需采用可靠的防止漏水的结构,采用DME或同等标准件。
2,冷却水到型腔的距离,到型腔和复杂的滑块表面以及浇道为20mm,到顶杆孔、螺纹孔。 可以为10mm,距离型腔转弯或尖角处应大于30mm
3,尽可能对型芯进行冷却,对于大于Φ25mm的型芯、抽芯等要设置冷却水道。4,运水图铭牌需固定于模具操作者侧。
5,运水的进出口需统一刻印并编号,如IN1,OUT1,IN2,OUT2…… ,
定模点冷用F1,F2,F3… ,动模点冷用M1,M2,M3… .
6,点冷进出口采用集中汇流,入水统一连接到压铸机操作者侧,软管标识为黑色, 出水汇集到后门,软管标识为红色;当有特殊原因不能安装到两侧时,
可以安装在模具上方,但要考虑避开吊装时钢丝绳与运水集成器干涉。
7,冷却水道应畅通不允许有渗漏现象。
七、浇注系统与分型面
1,浇注系统和分型面要与鸿图相关工程师协商后确定。
2,必须提供模具设计时使用的铸造条件表给鸿图工程师以供试模时参考。
3,浇道转接处应光滑,镶拼处应紧密,脱模角度不小于5°,表面粗糙度不大于Ra0.4。4,冲头附近正面冲击型芯的内浇口应加一个搭接转折, 以防冲击力太大而造成粘模和冲蚀。
搭接
冲头
内浇口
5,合模后分型面应紧密贴合局部间隙不大于0.05mm(排气槽除外)。
6,每套模具必须设置排气块
排气块至少设置9级,并且最后3级间隙为0.4mm,其余为0.6mm。
真空排气块同样至少设置9级间隙由0.9mm到0.5mm递减,还需开设真空孔G1 7,对于采用真空压铸的模具需与鸿图压铸工程师协商排气方案。
8,典型排气道形式,
9,带排气块的典型排气道形式,
(排气块分型面必须与镶块分型面一致,合模时要紧密贴合)
审。起吊模具的吊环孔尺寸按下表标准,数量至少2个,
等,