金属热处理原理

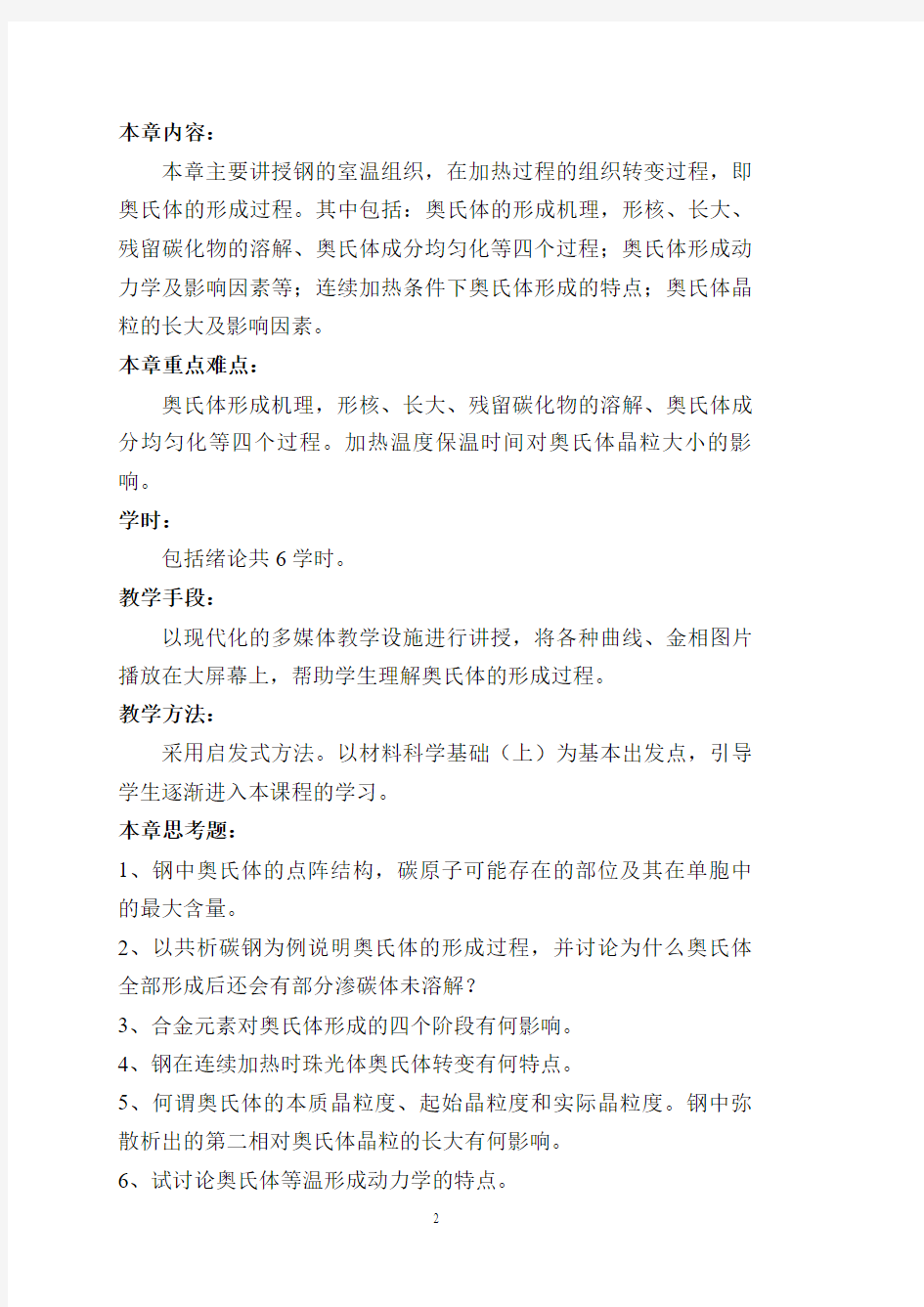
金属热处理原理
绪论
一、研究的内容和任务
金属热处理原理是以金属学原理为基础,着重研究金属及合金固态相变的基本原理和热处理组织与性能之间关系的一门课程。
金属学原理:着重讨论的是金属及合金的本质及影响因素、缺陷及其交互作用和它们对性能的影响、状态图、塑性变形、回复、再结晶等等。
热处理原理:着重讨论的是金属及合金在固态下的相变规律、影响因素、动力学、非平衡转变,以及在热处理中的应用,研究热处理组织和性能之间的关系等等。
金属材料从服役条件出发,选择什么样的材料、如何对材料进行处理,在使用和处理过程中会出现什么问题,如何解决出现的问题,最终可能得到什么样的性能,如何改进现有材料、挖掘其潜力,试制新材料等,无不与热处理原理有着密切的关系。
固态金属(包括纯金属及合金)在温度和压力改变时,组织和结构会发生变化,这种变化统称为金属固态相变。金属中固态相变的类型很多,有的金属在不同的条件下会发生几种不同类型的转变。掌握金属固态相变的规律及影响因素,就可以采取措施控制相变过程,以获得预期的组织,从而使其具有预期的性能。对于金属材料常用的措施就是特定加热和冷却,也就是热处理。
二、热处理发展概况
人们在开始使用金属材料起,就开始使用热处理,其发展过程大体上经历了三个阶段。
1、民间技艺阶段
根据现有文物考证,我国西汉时代就出现了经淬火处理的钢制宝剑。史书记载,在战国时期即出现了淬火处理,据秦始皇陵开发证明,当时已有烤铁技术,兵马俑中的武士佩剑制作精良,距今已有两千多年的历史,出土后表面光亮完好,令世人赞叹。古书中有“炼钢赤刀,用之切玉如泥也”,可见当时热处理技术发展的水平。但是中国几千年的封建社会造成了贫穷落后的局面,在明朝以后热处理技术就逐渐落后于西方。虽然我们的祖先很有聪明才智,掌握了很多热处理技术,但是把热处理发展成一门科学还是近百年的事。在这方面,西方和俄国的学者走在了前面,新中国成立以后,我国的科学家也作出了很大的贡献。
2、技术科学阶段(实验科学)—金相学
此阶段大约从1665年1895年,主要表现为实验技术的发展阶段。
1665年:显示了Ag—Pt组织、钢刀片的组织;
1772年:首次用显微镜检查了钢的断口;
1808年:首次显示了陨铁的组织,后称魏氏组织;
1831年:应用显微镜研究了钢的组织和大马士革剑;
1864年:发展了索氏体;
1868年:发现了钢的临界点,建立了Fe—C相图;
1871年:英国学者T. A. Blytb 著“金相学用为独立的科学”在伦敦出版;
1895年:发现了马氏体;
3、建立了一定的理论体系—热处理科学
“S”,曲线的研究,马氏体结构的确定及研究,K—S关系的发现,对马氏体的结构有了新的认识等,建立了完整的热处理理论体系。
本章内容:
本章主要讲授钢的室温组织,在加热过程的组织转变过程,即奥氏体的形成过程。其中包括:奥氏体的形成机理,形核、长大、残留碳化物的溶解、奥氏体成分均匀化等四个过程;奥氏体形成动力学及影响因素等;连续加热条件下奥氏体形成的特点;奥氏体晶粒的长大及影响因素。
本章重点难点:
奥氏体形成机理,形核、长大、残留碳化物的溶解、奥氏体成分均匀化等四个过程。加热温度保温时间对奥氏体晶粒大小的影响。
学时:
包括绪论共6学时。
教学手段:
以现代化的多媒体教学设施进行讲授,将各种曲线、金相图片播放在大屏幕上,帮助学生理解奥氏体的形成过程。
教学方法:
采用启发式方法。以材料科学基础(上)为基本出发点,引导学生逐渐进入本课程的学习。
本章思考题:
1、钢中奥氏体的点阵结构,碳原子可能存在的部位及其在单胞中的最大含量。
2、以共析碳钢为例说明奥氏体的形成过程,并讨论为什么奥氏体全部形成后还会有部分渗碳体未溶解?
3、合金元素对奥氏体形成的四个阶段有何影响。
4、钢在连续加热时珠光体奥氏体转变有何特点。
5、何谓奥氏体的本质晶粒度、起始晶粒度和实际晶粒度。钢中弥散析出的第二相对奥氏体晶粒的长大有何影响。
6、试讨论奥氏体等温形成动力学的特点。
7、试讨论影响奥氏体形成速度的因素。
8、试叙述奥氏体晶粒的长大过程及影响因素。
第一章钢在加热和冷却时的转变
§1—1 概述
一、热处理及其作用
热处理是将钢在固态下加热到预定的温度,保温一定的时间,然后以预定的方式冷却到室温的一种热加工工艺。其工艺曲线如图7.1
所示。
热处理的作用:改善材料工艺性能和使用性
能,充分挖掘材料的潜力,延长零件的使用奉
命,提高产品质量,节约材料和能源。此外,还
可以消除材料经铸造、锻造、焊接等热加工工艺
造成的各种缺陷、细化晶粒、消除偏析、降低内
应力,使组织和性能更加均匀。
最终热处理:在生产过程中,工件经切削加工等成形工艺而得到最终形状和尺寸后,再进行的赋予工件所需使用性能的热处理称为最终热处理。
预备热处理:热加工后,为随后的冷拔、冷冲压和切削加工或最终热处理作好组织准备的热处理,称为预备热处理。
二、钢临界温度
1、Fe—Fe3C相图上的临界温度
共析钢:PSK线(A1)γ→P(α+Fe3C)
亚共析钢:原始组织F+P PSK线(A1)P→γGS线(A3)F→γ
过共析钢:原始组织Fe3CF+P PSK线(A1)P
→γES线(A cm)Fe3C溶入γ
2、实际加热、冷却条件下的临界温度
实际加热奥氏体的形成总是在一定过热条件下发
生的,因此,相变开始的温度必然会偏离相图上的平
衡临界温度,加热时偏向高温,而冷却时偏向低温,
称为“滞后”,随着加热(冷却)速度增加奥氏体形
成温度偏离平衡点越远,如图所示。通常加热时的临
界温度用脚标C表示,A C1、A C3、A Ccm;冷却时的
临界温度用脚标r表示,A r1、A r3、A rcm。
§1—2 钢在加热时的转变
钢的热处理种类很多,其中除淬火后的回火,消除应力的退火等少数热处理外,均需加热到钢的临界以上,使钢部分或全部转变为奥氏体,然后再以适当的冷却速度冷却,使
奥氏体转变为一定的组织并获得所需的性能。
钢在加热过程中,由加热前的组织转变为奥氏体被称
为钢的加热转变功奥氏体化过程。由加热转变所得的奥氏
体组织状态,其中包括奥氏体晶粒的大小、形状、空间取
向、亚结构、成分及其均匀性等,均将直接影响在随后的
冷却过程中所发生的转变及转变所得产物和性能。因此,
弄清钢的加热转变过程,即奥氏体的形成过程是非常重要
的。
一、奥氏体形成的热力学条件
从Fe—Fe3C状态图可知,珠光体被加热到A1(727℃)以上时将转变为奥氏体。这是因为珠光体与奥氏体的自由能均随温度的升高而降低,但是下降的速度不同,相交于某一温度,该交点所对应的温度即A1(727℃)。图1-1是珠光体、奥氏体的自由能与温度的关系。高于A1(727℃)时,奥氏体的自由能低于珠光体的自由能,珠光体将转变为奥氏体。转变的驱动力即珠光体与奥氏体的体积自由之差ΔG V。
奥氏体形成时系统总的自由能变化为
ΔG=ΔG V +ΔG S +ΔG e
式中:ΔG V为新相奥氏体与母相珠光体之间的体积自由能差;ΔG S为形奥氏体时所增加的界面能;ΔG e为形成奥氏体时所增加的应变能。其中ΔG V是奥氏体转变的驱动力,ΔG S与ΔG e是相变的阻力。因为奥氏体在高温下形成,ΔG e一项较小,相变的主要阻力是ΔG S。从能量方程可以看出:
当T
当T=T0时,ΔG V=G A-G P=0 ΔG>0 珠光体不能转变为奥氏体;
当T>T0时,ΔG V=G A-G P<0 ΔG<0 珠光体有可能转变为奥氏体;
因此奥氏体形成的热力学条件是:必须在A1温度以上,即在一定的过热条件下奥氏体才能形成。只有当珠光体与奥氏体的体积自由能之差能克服界面能和应变能时,珠光体向奥氏体转变才能使系统向低能状态转变,奥氏体才能自发地形成。
二、奥氏体的形成过程
(一)奥氏体的结构、组织和性能
1、奥氏体的结构
奥氏体是碳溶于γ-Fe所形成的固溶体。在合金钢中,除了碳原子外,溶于γ-Fe中的还有合金元素原子。
(1)碳原子在点阵中的位置
X射线结构分析证明,碳原子位于γ-Fe八面体间隙位置中心,即面心立方点阵晶胞的中心或棱边的中点,如图1-2所示。假如每一个八面体中心容纳一个碳原子,则碳的最
大溶解度应为20%(重量%)。但实际上碳在γ-Fe中的最大溶
解度仅2.11%(重量%)。这是因为γ-Fe的八面体间隙半径仅
5.2×10-2nm(0.52?),小于碳原子的半径7.7×10-2nm
(0.77?),碳原子的溶入将使八面体发生膨胀而使周围的八面
体中心的间隙减小。因此不是所有的八面体中心均能容纳一个碳
原子。
(2)碳原子在奥氏体中的分布
碳原子在奥氏体的分布是不均匀的,存在着浓度起伏。奥氏
体中碳的分布是呈统计均匀的。用统计理论计算结果表明,在含碳0.85%的奥氏体中可能存在大量比平均碳浓度高八倍的微区,相当于渗碳体的碳含量。
(3)碳含量与点阵常数的关系
碳原子的溶入使的γ-Fe点阵发生畸变,点常数增
大。溶入的碳愈多,点阵常数愈大。如图1-3所示。
2、奥氏体的组织
在一般的情况下奥氏体的组织是由多边形的等轴
晶粒所组成,在晶粒内部有时可以看到相变孪晶。如
图1-4所示。
3、奥氏体的性能
Fe-C合金中的奥氏体在室温下是不稳定相。但是
在Fe-C合金中加入足够数量的能扩大γ相区的元素,可使奥氏体在室温,甚至在低温成为稳定相。因此,奥氏体可以是钢在使用时的一种重要组织形态。以奥氏体状态使用的钢称为奥氏体钢。
(1)磁性:奥氏体具有顺磁性,故奥氏体钢又可作为无磁钢。
(2)比容:在钢的各种组织中,奥氏体的比容最小。可利用这一点调整残余奥氏体的量,以达到减少淬火工件体积变化的目的。
(3)膨胀:奥氏体的线膨胀系数比铁素体和渗碳体的平均线膨胀系数高出约一倍。故奥氏体钢也可被用来制作要求热膨胀灵敏的仪表元件。
(4)导热性:除渗碳体外,奥氏体的导热性最差。因此,为避免热应力引起的工件变形,奥氏体不可采用过大的加热速度加热。
(5)力学性能:奥氏体具有高的塑性、低的屈服强度,容易塑性变形加工成形。因为面心立方点阵是一种最密排的点阵结构,至密度高,其中铁原子的自扩散激活能大,扩散系数小,从而使其热强性好。故奥氏体可作为高温用钢。
(二)奥氏体的形成过程
以共析钢为例说明奥氏体的形成过程。从珠光体向奥氏体转变的转变方程,
α + Fe3C →γ
C% 0.0218 6.69 0.77
晶格类型体心立方复杂斜方面心立方
我们可以看出:珠光体向奥氏体转变包括铁原子的点阵改组,碳原子的扩散和渗碳体的溶解。实验证明珠光体向奥氏体转变符合一般的相变规律,是一个晶核的形成和晶核长大过程。共析珠光体向奥氏体转变包括奥氏体晶核的形成、晶核的长大、残余渗碳体溶解和奥氏体成分均匀化等四个阶段。
1、奥氏体的形核
(1)形核条件
奥氏体晶核的形成条件是系统的能量、结构和成分起伏。
(2)形核部位
奥氏体晶核通常优先在铁素体和渗碳体的相界面上形成,此外,在珠光体团的边界,过冷度较大时在铁素体内的亚晶界上也都可以成为奥氏体的形核部位。在铁素体和渗碳体相界上优先形核的原因,可做如下的解释:界面两侧两相的碳含量相差很大(0.0218%和6.69%),因此在界面上碳浓度分布很不均匀,比较容易满足成分起伏;界面两侧晶体结构相差较大,原子排列不规则,原子的活动能力较强,比较容易满足结构起伏;界面上原子排列不规则,位错等晶体学缺陷密度较大,处于能量较高的状态,比较容易满足能量起伏,同时新相晶核形成时,可以使部分晶体学缺陷消失,使系统的能量进一步下降,因此在相界面处是奥氏体形核的首选位置。
2、奥氏体的长大
奥氏体晶核形成后便开始长大。奥氏体长大的机制可做如下的解释。在A C1以上某一t1形成一奥氏体晶核。奥氏体晶核形成之后,将产生两个新的相界面,一个是奥氏体与渗碳体相界面,另一个是奥氏体与铁素体相界面。为讨论问题的方便,我们假定两个相界面
都是平直的(参见图1-5)。根据Fe-Fe3C 相图可知,奥氏体与铁素体相邻的边界处的碳浓度为Cγ-α,奥氏体与渗碳体相邻的边界处的碳浓度为Cγ-c。此时,两个边界处于界面的平衡状态,这是系统自由能最低的状态。由于Cγ-c>Cγ-α,因此,在奥氏体出现碳的浓度梯度,从而引起碳在奥氏体中由高浓度向低浓度的扩散,使奥氏体内部的碳的分布驱于均匀分布,即使奥氏体与铁素体相邻的边界处碳浓度升高,而奥氏体与渗碳体相邻的边界处碳浓度降低。从而破坏了相界面处的碳浓度平衡,使系统自由能升高。为了恢复平衡,渗体体势必溶入奥氏体,使它们相邻界面的碳浓度恢复到Cγ-c,与此同时,另一个界面上将发生铁素体向奥氏体的晶格改组,使其相邻边界的碳浓度恢复到Cγ-α,从而恢复界面的平衡,降低系统的自由能。这样相当于奥氏体的晶核分别向渗碳体和铁素体中推移,奥氏体晶核得以长大。由于界面处碳浓度的恢复又增加了奥氏体中的碳浓度分布梯度,又会引起碳在奥氏体中的扩散,破坏界面处碳浓度的平衡,引起渗碳体的溶解和铁素体的转变,再次恢复平衡。此过程循环往复地进行,奥氏体便不断地向铁素体和渗碳体中长大。直到将铁素体和渗碳体消耗完了奥氏体晶核的长大结束。
由图1-5,在铁素体内,铁素体与渗碳体和铁素体与奥氏体两个相界面之间也存在着碳浓度差Cα-c-Cα-γ,因此,当碳在奥氏体中进行扩散的同时,在铁素体中也进行着扩散。扩散的结果,也将促进铁素体向奥氏体的转变,从而促进奥氏体的长大。
3、剩余渗碳体的溶解
实验表明在珠光体向奥转变过程中,铁素体和渗碳体并不是同时消失,而总是铁素体首先消失,将有一部分渗碳体残留下来。这部分渗碳体在铁素体消失后,随着保温时间的延长或温度的升高,通过碳原子的扩散不断溶入奥氏体中。一旦渗碳体全部溶入奥氏体中,这一阶段便告结束。
为什么铁素体和渗碳体不能同时消失,而总有部分渗碳体剩余?
按相平衡理论,从Fe-Fe3C相图可以看出,在高于A C1温度,刚刚形成的奥氏体,靠近Cem的C浓度高于共析成分较少,而靠近F处的C浓度低于共析成分较多(即ES线的斜率较大,GS线的斜率较小)。所以,在奥氏体刚刚形成时,即F全部消失时,奥氏体的平均C浓度低于共析成分,这就进一步说明,共析钢的P刚刚形成的A的平均碳含量降低,低于共析成分,必然有部分碳化物残留,只有继续加热保温,残留碳化物才能逐渐溶解。
碳化物溶入A的机理,现在还不十分清楚,有人认为是通过碳化物中的碳原子向奥氏体中扩散和Fe原子向贫碳的渗碳体区扩散,以及Fe3C向A晶体点阵改组来完成的。
4、奥氏体成分均匀化
珠光体转变为奥氏体时,在残留渗碳体刚刚完全溶入奥氏体的情况下,C在奥氏体中的分布是不均匀的。原来为渗碳体的区域碳含量较高,而原来是铁素体的区域,碳含量较低。这种碳浓度的不均匀性随加热速度增大而越加严重。因此,只有继续加热或保温,借助于C原子的扩散才能使整个奥氏体中碳的分布趋于均匀。
以上共析碳钢珠光体向奥氏体等温形成过程,可以用下图形象地表示出来。
5、奥氏体非扩散形成简介
(1)无扩散形核,扩散长大;
(2)铁素体全部以无扩散方式转变为低碳的奥氏体;
(3)最近的研究成果:铁素体向奥氏体转变直接受加热速度控制,快速加热可以为无扩散形核,而缓慢加热则以扩散方式形成。
三、奥氏体的形成速度(奥氏体形成动力学)
相变的动力学研究的是:转变温度、转变量和转变时间的关系。
奥氏体形成动力学可分为等温形成动力学和连续加热形成动力学。
(一)奥氏体等温形成动力学
等温形成动力学即在一定温度下的转变量和转变时间的关系(即在一定温度下的转变速度)。
研究表明,奥氏体的形成速度决定于奥氏体的形核率和晶核的线长大速度,它受钢的成分、原始组织状态、等温温度等条件的影响。
1、奥氏体等温形成动力学曲线
(1)共析碳钢奥氏体等温形成图
试样:厚2mm 左右,直径约为10mm 的小圆片;
原始状态:每个试样均有相同的原始组织状态;
温度:在A C1以上设定不同的温度,如730℃、745℃、
765℃、……;
时间:在每个温度下保持一系列时间,如1S 、5S 、
10S 、20S 、……;
冷却:在盐水中急冷到室温;
观察:在显微镜下测出试样中马氏体的数量(相当于高
温下奥氏体的数量);
做图:做出每个温度下奥氏体形成量和保温时间的关系
曲线,即得到了奥氏体等温形成的动力学曲线。为方便,通
常把不同温度下转变转变相同数量所需时间,综合在温度和
时间坐标系内,这样就得到了奥氏体等温形成图。
上图只表示了珠光体向奥氏体转变刚刚完成的情况,实
际上,此时钢中仍有部分残留碳化物存在,还需要保温一段
时间后才能使碳化物完全溶解,碳化物溶解完了之后,还需要保持一段时间后才能使奥氏体成分均匀。
珠光体向奥氏体等温转变过程示意图
0.86%钢a)奥氏体形成动力学曲线b)等温形成图
(2)奥氏体等温形成的特点 ①在高于A C1温度保温时,奥氏体并不立即形成,而是需要经过一定时间后,才开始形成。温度越高,所需时间越短。通常称为孕育期。 孕育期:从保温开始到转变开始的这段时间称为孕育期。孕育期的实质是相变的准备阶段,是所有扩散型相变的共同特点。 ②奥氏体形成速度在整个过程中是不同的,开始时速度较慢,以后逐渐加快;在转变量达到50%时,转变速度达到极大值,以后转变速度又开始逐渐减慢。 ③温度越高,奥氏体形成所需的全部时间越短,即奥
氏体的形成速度越快。换言之,随温度升高,奥氏体形成
始终是加速的。
④在奥氏体刚刚形成后,还需一段时间使残留碳化物溶解和奥氏体成分均匀化。
(3)过共析和亚共析碳钢奥氏体等温形成图
①过共析碳钢:原始组织为P+Cem ,且P 的数量随钢的C%增加而减少。
②亚共析碳钢:原始组织为P+F ,且P 的数量随钢的C%增加而增加。
对于这类钢,当加热到A C1以上某一温度,珠光体转变为奥氏体后,如果保温时间不太长,可能有部分铁素体或渗碳体被残留下来。对于含碳量比较高的亚共析钢,在A C1以上,当铁素体全部转变为奥氏体后不久,有可能仍有部分碳化物残留。
2、奥氏体等温形成动力学的分析
奥氏体等温形成动力学图示出的温度升高奥氏体形成速度加快的规律,是由于随着温度升高奥氏体的形核率和长大速度均增加的缘故。有人做过试验,把奥氏体的形成温度从740℃提高到800℃时,奥氏体的形核率N 增加270倍,而长大速度G 增加了80倍。因此,随着温度升高,奥氏体形成速度迅速增加。
(1)奥氏体的形核率
研究指出,在奥氏体均匀形核条件下,形核率N 和温度之间的关系可以表示为:
KT W KT Q e e C N --'=
C ˊ-常数; Q-扩散激活能; T-绝对温度; K-波尔茨曼常数;
W-临界形核功,在忽略应变能时,23V
G A W ??'=σ A ˊ-常数;σ-奥氏体与旧相的界面能;
ΔG V -奥氏体与旧相之间单位体积自由能之差;
1)因温度升高,形核率N 以指数关系迅速增加;
共析碳钢奥氏体等温形成图
(a )过共析钢(W C 1.2%)和(b )亚共析钢(W C 0.45%)奥氏体等温形成图
2)因ΔG V 随温度升高而增大,使W 减小,使N 进一步增大;
3)随温度升高原子扩散速度加快,不仅有利于铁素体向奥氏体点阵改组,而且也促进渗碳体溶解,这也加速奥氏体的形核;
4)随温度升高铁素体的C%沿QP 线增加,另一方面奥氏体在铁素体中形核时所需的碳浓度沿SG 而降低,结果减小了奥氏体形核所需要的碳的浓度起伏,促进奥氏体的形核。
(2)奥氏体晶体的长大速度G
奥氏体晶体的长大速度,实质上就是奥氏体的相界面向铁素体和渗碳体中推移速度的总和。它首先取决于碳在奥氏体中的扩散速度和浓度梯度,其次取决于铁素体向奥氏体点阵改组的速度,即铁原子的自扩散速度。
关于奥氏体晶体的长大速度,有不少研究者利用扩散规律导出一些计算公式,具有代表性的如下:
γ
ααγγααγ→→→-?+?-=C C dx dc D dx dc D K V C C 2211 γαC
C D D ,……碳在铁素体和奥氏体中的扩散系数; 2211,dx dc dx dc ……铁素体和奥氏体界面处碳在铁素体和奥氏体中的浓度梯度; γααγ→→-C C ……奥氏体与铁素体相界面间的碳浓度差。
负号表示下坡扩散。 由于碳在铁素体中的浓度梯度很小,故可以近似把11dx dc 看作是0。上式可以改写为:
γ
ααγγαγ→→→-?-=C C dx dc D K V C 利用碳在渗碳体中的浓度梯度等于零的特点,可得界面向渗碳体中推移的速度表达式:
cem
C cem cem C cem C dx dc
D K C C dx dc D K V →→→→-?-=-?-=γγγγγγ67.6 cem cem C C →→-γγ……渗碳体与奥氏体相界面间的碳浓度差。
dx dc ……碳在奥氏体中的浓度梯度;
通过对上式的分析,不难得出,升高温度总是使奥氏体晶体长大速度加快的。
1)温度升高,扩散系数D (RT Q e D D -=0)增大,同时奥氏体的两相界面之间碳浓度差C r-cem -C r-a 增加,增大了碳在奥氏体中的浓度梯度,从而使奥氏体的长大速度加快;
2)温度升高,在铁素体中有利于奥氏体形核的部位增加,原子的扩散距离相对缩短了,同样有利于奥氏体的长大;
3)温度升高,奥氏体与铁素体相界面处的碳浓度差C r-a -C a-r 以及渗碳体与奥氏体相界面处的碳浓度差C cem-r -C r-cem 均减小,因此也会加速奥氏体晶体长大。
综上所述:奥氏体形成时,升高温度(或增加过热度)始终是有利于奥氏体形成的,
所以加热温度越高,奥氏体形成的孕育期以及整个相变过程所需时间越短,即奥形成速度越快。换言之:随温度的升高(或过热度的增大)奥氏体的形成是加速的。
3、影响奥氏体形成速度的因素
(1)温度
温度升高,奥氏体形成速度加快。在各种影响因素中,温度的作用最为强烈,因此控制奥氏体的形成温度十分重要。
(2)碳含量
钢中碳含量越高,奥氏体的形成速度越快。C%增加原始组织中碳化物数量增多,增加了铁素体与渗碳体的相界面,增加了奥氏体的形核部位,同时碳的扩散距离相对减小。(3)原始组织的影响
如果钢的化学成分相同,原始组织中碳化物的分散度越大相界面越多,形核率便越大;珠光体片间距离越小,奥氏体中碳浓度梯度越大,扩散速度便越快;碳化物分散度越大,使得碳原子扩散距离缩短,奥氏体晶体长大速度增加。
(4)合金元素的影响
1)合金钢中奥氏体形成的特点
合金钢中的奥氏体形成规律与碳素钢的相同,奥氏体形成机理并不发生变化。但是,由于合金元素的加入,可以改变碳化物的稳定性,可以影响碳在奥氏体中的扩散系数。关于合金元素对奥氏体形成速度的影响可以从以下几个方面来说明:
①通过对碳扩散速度影响奥氏体的形成速度
强碳化物形成元素Cr、Mo、W等,降低碳在奥氏体中扩散系数,推迟珠光体转变为奥氏体;非碳化物形成元素Co、Ni等增大碳在奥氏体中的扩散系数,使奥氏体形成速度加快;Si、Al等对碳原子的扩散系数影响不大,因此对奥氏体的形成无明显的影响。
②合金元素通过改变碳化物稳定性影响奥氏体的形成速度
通常使碳化物稳定提高的元素,将延缓奥氏体的形成。钢中加入W、Mo和其它强碳化物形成元素,由于在钢中可以形成稳定性极高的特殊类型的碳化物,加热时不易溶解,将使奥氏体形成速度减慢。下面以Cr元素来说明。
Cr含量为2%及6%时,延缓奥氏体的形成,但Cr含量为11%时,奥氏体形成速度反而比6%时快。原因如下:
2%Cr时形成较稳定的不易溶解的(FeCr)3C,延缓奥氏体的形成;
6% Cr时形成更稳定的不易溶解的(FeCr)7C3,延缓奥氏体的形成;
11%Cr时形成含碳较少、较易溶解、稳定性较低的碳化物(FeCr)23C6,一方面(FeCr)23C6较不稳定,另一方面C%相同时可以形成更多的碳化物,从而使相界面面积增加,这些都会加速奥氏体的形成。
③对临界点的影响
合金元素的加入改变了临界点A1、A3、A cm的位置,并使它们成为一个温度范围,当温度一定时,临界点的变化相当于过热度的改变。
Ni、Mn、Cu等降低A1温度;Cr、Mo、Ti、Si、Al、W、V等升高A1温度。
④合金元素通过对原始组织的影响也影响奥氏体的形成速度
Ni、Mn等往往使珠光体细化,有利于奥氏体的形成。
2)合金钢中奥氏体均匀化
钢中的合金元素在原始组织各相中(F和Cem)分配是不均匀的,在退火状态下,碳化物形成元素主要集中在碳化物中,而非碳化物形成元素则主要集中在铁素体中,合金元素这种不均匀分布,一直到碳化物溶解完毕后,还显著地保留在钢中,这样合金钢奥氏体形成后,除了碳的均匀化外,还要进行合金元素的均匀化。
在其它条件相同的情况下,合金元素在奥氏体中的扩散速度比碳在奥氏体中的扩散速度小100-10000倍。此外,碳化物形成元素还会减小碳在奥氏体中的扩散速度,这将降低
碳的均匀化速度,因此,合金钢均匀化所需时间常常比碳钢长得多。
(二)连续加热时奥氏体的形成
工件实际热处理时,在绝大多数(如高频感应加热、火焰表面加热、高温盐浴加热等)情况下,奥氏体的形成是属于非等温或连续加热转变。
奥氏体形成时将吸收热量,转变开始后,如果供给工件的热量等于转变所消耗的热量,工件所取得的热量均用于奥氏体的形成,温度不再升高,转变在恒温下进行。相反如果供热大于转变所需热量,此时除转变所需热量,多余的热量将使工件的温度继续升高,故在转变进行的同时,温度还在继续升高,此时转变是在温度不断升高的条件进行的。
实验表明连续加热时奥氏体形成的基本过程和等温转变相似,也是由奥氏体的形成、残留碳化物溶解和奥氏体成分均匀化三个阶段组成。现已证明,影响这些过程的因素也大致与等温形成时相同。但是,因为奥氏体的形成是在连续加热条件下进行的,所以要相变动力学及相变机理上常会出现若干等温转变所没有的特点。
1、在一定的加热速度范围内,临界点随加热速度增大而升高
奥氏体形成的开始温度和终了温度均随加热速度增大而升高。当钢的加热速度大到某一范围时,所有亚共析钢的转变温度均相同,加热速度约在105-106℃/S范围内时含碳在0.2~0.9%的钢的转变温度均约在1130℃。
2、相变是在一个温度范围内完成的
加热速度越快奥氏体的温度范围越宽,但形成速度确加快,奥氏体形成时间缩短。3、可以获得超细晶粒
超快速加热时,过热度很大,奥氏体晶核不仅在可以在铁素体和渗碳体相界面上形成,而且也可以在铁素体内的亚晶界上形成,因此奥氏体成核率很大,如果加热时间极短,在奥氏体晶体来不极长大,所以可带来奥氏体晶粒的超细化的特点。
4、钢中原始组织的不均匀使连续加热时的奥氏体化温度升高
5、快速连续加热时形成的奥氏体成分不均匀性增大C r-a降低,C r-cem升高。
6、在超快速加热条件下,铁素体转变为奥氏体的点阵改组属于无扩散型相变。
四、奥氏体晶体长大及控制
(一)奥氏体晶粒度
晶粒度:是表示晶粒大小的一种尺度。对钢来说,如果不特别指明,一般是指奥氏体后的实际晶粒大小。奥氏体晶粒度有以下三个不同的概念。
1、起始晶粒度:指临界温度以上奥氏体形成刚刚完成,其晶粒边界刚刚互相接触时的晶粒大小。
2、实际晶粒度:指在某一热处理加热
条件下,所得到的晶粒尺寸。
3、本质晶粒度:是根据标准实验条
件,在930±10℃,保温足够时间(3~8小
时)后,测定的钢中奥氏体晶粒的大小。
按此法,晶粒度在5~8级者称为本质细晶
粒钢,在1~4级者称为本质粗晶粒钢。本
质晶粒度并不是实际晶粒大小,它只是描
述了晶粒长大的趋势,它说明本质细晶粒
钢加热时,奥氏体晶粒长大的倾向小,而
本质粗晶粒钢加热量奥氏体晶粒长大的倾
向大。实际加热条件下,本质粗晶粒钢的
晶粒不一定粗,而本质细晶粒钢的晶粒不
一定细。
4、奥氏体晶粒的评定标准
一般生产中把奥氏体晶粒大小分为1~8个级别,其中1级最粗,8级最细,超过8级以上的称为超细晶粒。
晶粒度的级别N ˊ与晶粒大小之间的关系为:
n ˊ=2N ˊ-1或n=2N ˊ+3
n ˊ……为放大100倍进行金相观察时每平方英寸(6.45cm 2)视野中所含的平均晶粒
数目。
n ……实际上每1mm 2试样面积中的平均晶粒数目。
(二)晶粒长大与第二相颗粒的影响
1、晶粒长大的机理
奥氏体刚刚形成后,起始晶粒一般均很细小,而且也不均匀。界面弯曲,晶界面积大,界面能高。从热力学分析,界面能越高,则界面越不稳定,必然要自发地向减少晶界面积,降低界面能的方向发展。就是说,弯曲晶界变成平直晶界,小晶粒合并成大晶粒是一种自发过程。
稳定存在的晶粒形状是六边形的,晶界均成直线,且三条
晶界相交于一点时互成120°角,在二维平面上每个晶粒均有
6 个相邻接的晶粒,这种状态的晶粒不易长大稳定性极高。但
实际上晶粒并非如此均匀,在同一视野内晶粒大小是有很大差
别的。
当晶粒尺寸小于平均尺寸时,其相邻的晶粒就必然减少,
可能只有3~5个,界面的夹角也要小于120°,此时界面张力的合力不等于零,存在一个指向小晶粒曲率中心的力,该力将牵引晶界向小晶粒的曲率中心称动,使小晶粒收缩,最终消失。
当晶粒尺寸大于平均晶粒尺寸时,其相邻接的晶粒数目就必然增加,可能不只有6个,界面夹角也将大于120°,界面张力的合力也不为零,存在一个背向大晶粒曲率中心的力,该力将牵引晶界向外移动,使大晶粒长大。
其结果是在初期出现大晶粒吞并小晶粒的晶粒长大过程。当晶粒大小相当后,此过程结束。如果此时继续加热或保温晶粒还会继续长大。
通常将大晶粒吞并小晶粒而长大的过程叫不均匀长大,而将大晶粒继续长大的过程称为均匀长大。一般情况下晶粒长大是由这两个阶段组成的。
晶粒长大的驱动力G 和晶粒尺寸及界面能的大小有关,可用下式表示:
R G '
'-=σ2 σˊ……单位奥氏体晶粒的界面能;
R ˊ……晶界曲率半径,若晶粒为球形时R 即为其半径。
可以看出,界面能越大、晶粒尺寸越小,奥氏体晶粒长大的驱动力越大,长大的倾向越大,即晶界越容易迁移。
2、第二项颗粒对晶粒长大的影响
对实际金属材料而言,不是在所有情况下晶界都能自发迁移。在晶粒边界及晶粒内部。往往存在着很多细小难熔的第二相颗粒,它们
将阻碍晶界移动,起着钉扎晶界的作用。
假设晶粒A 和晶粒B 之间的晶界,沿X 轴的方
向移动,与半径为r 的小颗粒相遇,当晶界迁移到
小颗粒的Y 轴时(即小颗粒的直径平面),因颗粒
的存在省去了部分(πr 2)晶界,此时晶界具有最低
的界面能。当晶界向前移动时,不仅晶界面积增大,同时,因为需要保持界面张力的平衡,必须使
φ=θ,即晶界与颗粒表面相交处必须保持垂直,这样就引起距离颗粒较近的一部分晶界发生弯曲,导致晶界面积进一步增大,且第二相颗粒越小,晶界弯曲的曲率越大,晶界面积增加越多,将会导致界面能的增大。显然,这是一个使系统自由能增加的过程,是可能自发进行的。第二相颗粒的存在相当于晶界移动的阻力,当驱动力与阻力平衡时,晶界停止移动,晶粒停止长大。
研究指出,第二相颗粒对晶界移动的最大阻力G m 可用下式表示:
r
f G m 23σ= r ……第二相颗粒的半径;σ……界面能;f ……单位体积内第二相颗粒的数目。
如果晶界移动的驱动力完全来自晶界能,那么当晶界能所提供的驱动力正好和弥散的颗粒对晶界移动的阻力相等时,正常的晶粒长大便告停止。所以在一定温度下,奥氏体晶粒的平均极限半径R ˊlim 决定于第二相颗粒的半径r 及数量的多少,可用下式表示:
f
r R 34lim =' 总之,晶粒长大是一种自发过程,它是由大晶粒吞并小晶粒的不均匀长大和大晶粒进一步长大的均匀长大两个联合体组成。晶粒的长大主要表现为晶界的移动,高度弥散的、难熔的非金属或金属化合物颗粒对晶粒长大起很大的抑制作用,为了获得细小的奥氏体晶粒,必须保证钢中有足够数量和足够细小难熔的第二相颗粒。
(三)影响奥氏体晶粒度的因素
1、加热温度和保温时间
晶粒长大和原子的扩散密切相关,所以温度越高相应的保温时间越长,奥氏体晶粒将越粗大。在每一个温度下奥氏体晶粒的长大都有一个加速长大期,当晶粒长大到一定尺寸后,长大过程将减弱并停止。温度越高,奥氏体晶粒长大进行的越快。因此,为了得到一定尺寸的晶粒度,必须同时控制温度和保温时间。
2、加热速度
在保证奥氏体成分均匀的前提下,快速加热短时保温能够获得细小的奥氏体晶粒。这是因为,加热速度越大,奥氏体转变时的过热度越大,奥氏体的实际形成温度越高,则奥氏体的形核率越高,起始晶粒越细小。如果在高温下保温时间很短,奥氏体晶粒来不及长大,因此,可以得细晶粒组织。但是,如果在高温下长时间保温,晶料则很容易长大。
3、钢的含碳量的影响
钢中含碳量对奥氏体晶粒长大的影响很大。含碳量在一定范围内,随含碳量的增加,奥氏体晶粒长大的倾向增大。但是含碳量超过某一限度时,奥氏体晶粒反而随含碳量的增加而变的细小。这是因为随着含碳量的增加,碳在钢中的扩散速度以及铁的自扩散速度均增加,故增加了奥氏体晶粒长大的倾向性。但是,当碳含量超过一定限度以后,加热奥氏体化时会出现第二相,如二次渗碳体,且随着碳含量的增加,第二相的数量增多,将阻碍奥氏体晶界的迁移,故奥氏体晶粒反而细小。
4、脱氧剂及合金元素
用Al 脱氧的钢奥氏体晶粒长大倾向小,属于本质细晶粒钢。而用Si 、Mn 脱氧的钢奥氏体晶粒长大倾向大,一般属于本质粗晶粒钢。Al 能细化晶粒的主要原因是残留的Al 在钢中能形成大量难熔的六方点阵结构的AlN ,它们弥散析出在晶界上,阻碍了晶界的移动,防止晶粒长大。而Si 和Mn 在钢中则不能形成类似的化合物,因此,没有阻碍奥氏体晶粒长大的作用。
钢中加入适量的Ti (钛)、Zr (锆)、Nb (铌)、V (钒)、Ta (钽)等合金元素,有强烈细化奥氏体晶粒、升高粗化温度的效果。因为这些元素是强碳、氮化物形成元素,在钢中形成熔点高、稳定性强、不易聚集长大的NbC 、NbN 、Nb(C 、N)等化合物。
能产生稳定碳化物的元素W、Mo、Cr等也有细化晶粒的作用;Ni、Co、Cu等稍有细化晶粒的作用;而P、O等则是粗化晶粒的元素。
按阻碍奥氏体晶粒长大程度不同,可将合金元素分成如下几类:
强烈阻碍晶粒长大的:Ti钛、Zr锆、Nb铌、V钒、Ta钽、Al铝等;
有中等阻碍作用的:W、Mo、Cr等;
稍有阻碍作用或不起作用的:Ni、Co、Cu、Si等;
增大晶粒长大倾向的:C、P、Mn、O等。
5、原始组织
原始组织细小,相界面积大,奥氏体形核率大,则起始晶粒细小,但晶粒长大倾向大,即过热敏感性增大,不可采用过高的加热温度和长时间保温,宜采用快速加热、短时保温的工艺方法。
思考题
1、钢中奥氏体的点阵结构,碳原子可能存在的部位及其在单胞中的最大含量。
2、以共析碳钢为例说明奥氏体的形成过程,并讨论为什么奥氏体全部形成后还会有部分渗碳体未溶解?
3、合金元素对奥氏体形成的四个阶段有何影响。
4、钢在连续加热时珠光体奥氏体转变有何特点。
5、何谓奥氏体的本质晶粒度、起始晶粒度和实际晶粒度。钢中弥散析出的第二相对奥氏体晶粒的长大有何影响。
6、试讨论奥氏体等温形成动力学的特点。
7、试讨论影响奥氏体形成速度的因素。
8、试叙述奥氏体晶粒的长大过程及影响因素。
金属热处理原理及工艺总结 整理版(精编文档).doc
【最新整理,下载后即可编辑】 5.实际晶体中的点缺陷,线缺陷和面缺陷对金属性能有何影响? 答:如果金属中无晶体缺陷时,通过理论计算具有极高的强度,随着晶体中缺陷的增加,金属的强度迅速下降,当缺陷增加到一定值后,金属的强度又随晶体缺陷的增加而增加。因此,无论点缺陷,线缺陷和面缺陷都会造成晶格崎变,从而使晶体强度增加。同时晶体缺陷的存在还会增加金属的电阻,降低金属的抗腐蚀性能。 6.为何单晶体具有各向异性,而多晶体在一般情况下不显示出各向异性? 答:因为单晶体内各个方向上原子排列密度不同,造成原子间结合力不同,因而表现出各向异性;而多晶体是由很多个单晶体所组成,它在各个方向上的力相互抵消平衡,因而表现各向同性。 7.过冷度与冷却速度有何关系?它对金属结晶过程有何影响?对铸件晶粒大小有何影响? 答:①冷却速度越大,则过冷度也越大。②随着冷却速度的增大,则晶体内形核率和长大速度都加快,加速结晶过程的进行,但当冷速达到一定值以后则结晶过程将减慢,因为这时原子的扩散能力减弱。③过冷度增大,ΔF大,结晶驱动力大,形核率和长大速度都大,且N的增加比G增加得快,提高了N与G的比值,晶粒变细,但过冷度过大,对晶粒细化不利,结晶发生困难。 8.金属结晶的基本规律是什么?晶核的形成率和成长率受到哪些因素的影响?答:①金属结晶的基本规律是形核和核长大。②受到过冷度的影响,随着过冷度的增大,晶核的形成率和成长率都增大,但形成率的增长比成长率的增长快;同时外来难熔杂质以及振动和搅拌的方法也会增大形核率。 9.在铸造生产中,采用哪些措施控制晶粒大小?在生产中如何应用变质处理?答:①采用的方法:变质处理,钢模铸造以及在砂模中加冷铁以加快冷却速度的方法来控制晶粒大小。②变质处理:在液态金属结晶前,特意加入某些难熔固态颗粒,造成大量可以成为非自发晶核的固态质点,使结晶时的晶核数目大大增加,从而提高了形核率,细化晶粒。③机械振动、搅拌。 第二章金属的塑性变形与再结晶 2.产生加工硬化的原因是什么?加工硬化在金属加工中有什么利弊? 答:①随着变形的增加,晶粒逐渐被拉长,直至破碎,这样使各晶粒都破碎成细碎的亚晶粒,变形愈大,晶粒破碎的程度愈大,这样使位错密度显著增加;同时细碎的亚晶粒也随着晶粒的拉长而被拉长。因此,随着变形量的增加,由于晶粒破碎和位错密度的增加,金属的塑性变形抗力将迅速增大,即强度和
钢的热处理(原理及四把火)
钢的热处理 钢的热处理:是将固态钢材采用适当的方式进行加热、保温和冷却以获得所需组织结构与性能的工艺。热处理不仅可用于强化钢材,提高机械零件的使用性能,而且还可以用于改善钢材的工艺性能。其共同点是:只改变内部组织结构,不改变表面形状与尺寸。 第一节钢的热处理原理 热处理的目的是改变钢的内部组织结构,以改善钢的性能,通过适当的热处理可以显著提高钢的机械性能,延长机器零件的使用寿命。热处理工艺不但可以强化金属材料、充分挖掘材料性能潜力、降低结构重量、节省和能源,而且能够提高机械产品质量、大幅度延长机器零件的使用寿命。 热处理工艺分类:(根据热处理的目的、要求和工艺方法的不同分类如下) 1、整体热处理:包括退火、正火、淬火、回火和调质; 2、表面热处理:包括表面淬火、物理和化学气相沉积等; 3、化学热处理:渗碳、渗氮、碳氮共渗等。 热处理的三阶段:加热、保温、冷却
一、钢在加热时的转变 加热的目的:使钢奥氏体化 (一)奥氏体( A)的形成 奥氏体晶核的形成以共析钢为例A1点则W c =0.0218%(体心立方晶格F)W c =6.69%(复杂斜方渗碳体)当T 上升到A c1 后W c =0.77%(面心立方的A)由此可见转变过程中必须经过C和Fe原子的扩散,必须进行铁原子的晶格改组,即发生相变,A的形成过程。在铁素体和渗碳体的相界面上形成。有两个有利条件①此相界面上成分介于铁素体和渗碳体之间②原子排列不规则,空位和位错密度高。 1、奥氏体长大由于铁素体的晶格改组和渗碳体的不断溶解,A晶核一方面不断向铁素体和渗碳体方向长大,同时自身也不断形成长大。 2、残余 Fe 3 C的溶解 A长大同时由于有部分渗碳体没有完全溶解,还需一段时间才能全溶。(F比Fe 3 C先消失) 3、奥氏体成分的均匀化残余Fe 3 C全溶后,经一段时间保温,通过碳原子的扩散,使A成分逐步均匀化。 (二)奥氏体晶粒的长大 奥氏体大小用奥氏体晶粒度来表示。分为 00,0,1,2…10等十二个等级,其中常用的1~10级,4级以下为粗晶粒,5-8级为细晶粒,8级以上为超细晶粒。影响 A晶粒粗大因素 1、加热温度越高,保温时间愈长,奥氏体晶粒越粗大。因此,合理选择加热和保温时间。以保证获得细小均匀的奥氏体组织。(930~950℃以下加热,晶粒长大的倾向小,便于热处理) 2、A中C含量上升则晶粒长大的倾向大。
第四章 有色金属热处理原理与工艺
第四章有色金属热处理原理与工艺 一、概述 热处理是有色加工的重要组成部分 有色金属材料:黑色金属以外的所有金属及其合金。 分类:轻有色、重有色、稀有色、贵金属 作用:改善工艺性能,保证后续工序顺利进行;提高使用性能,充分发挥材料潜力。 类型:退火、淬火、时效、形变热处理 退火:加热到适当温度,保温一定时间,缓慢速度冷却。 有色中的退火:去应力退火、再结晶退火、均匀化退火 二、均匀化退火 对象:铸锭、铸件—→浇铸冷速大,造成成分偏析以及内应力 目的:提高铸件的性能,消除内应力,稳定尺寸与组织,消除偏析枝晶,改善性能。 非平衡铸态组织特征:晶内偏析or枝晶偏析;伪共晶or离异共晶;非平衡第二相;最大固溶度偏移。非平衡组织对性能的影响:枝晶偏析&非平衡脆性相—→塑性↓; 晶内偏析、浓度差微电池—→耐腐蚀性↓; 粗大的枝晶和严重的偏析—→各向异性&晶间断裂倾向↑; 非平衡针状组织—→性能不稳定。 固相线以下100~200℃长时间保温—→也称为扩散退火 组织变化:获得均匀的单相、晶粒长大、过饱和固溶体的分解、第二相聚集与球化 性能变化:塑性↑、改善冷变形的工艺性能、耐蚀性↑、尺寸形状稳定、消除残余应力 缺点:加热温度高,时间长,耗时耗能;高温长时间出现变形、氧化以及吸气缺陷;产品强度下降。制定均匀化推过规程的原则: (1)加热温度:温度越高,原子扩散越快,均匀化过程越快,但不宜过高,易发生过烧。一般为 0.90~0.95T m ①高温均匀化退火:在非平衡相线温度以上但在平衡固相线温度以下进行均匀化退火。 适用:大截面工件or铝合金 ②分级加热均匀化退火:现在低于非平衡固相线温度加热,待非平衡相部分溶解及固溶体 内成分不均匀部分降低,从而非平衡固相线温度升高后,再加热 至更高温度保温,在此温度下完成均匀化退火过程。 目的:均匀化更迅速、更彻底,且避免过烧 适用:镁合金 (2)保温时间:包括非平衡相溶解及消除晶内偏析所需的时间 取决于退火温度:T↑,D↑,时间↓; 铸锭原始组织特征:合金化程度、第二相分散度、尺寸 铸锭的致密程度 (3)加热速度与冷却速度 原则:铸锭不产生裂纹和大的变形,不能过快or过慢 主要采用均匀化退火的合金:Al合金、Mg合金、Cu合金中的锡磷青铜、白铜
铝合金热处理原理
铝合金热处理原理 铝合金铸件的热处理就是选用某一热处理规范,控制加热速度升到某一相应温度下保温一定时间并以一定得速度冷却,改变其合金的组织,其主要目的是提高合金的力学性能,增强耐腐蚀性能,改善加工型能,获得尺寸的稳定性。 铝合金热处理特点 众所周知,对于含碳量较高的钢,经淬火后立即获得很高的硬度,而塑性则很低。然而对铝合金并不然,铝合金刚淬火后,强度与硬度并不立即升高,至于塑性非但没有下降,反而有所上升。但这种淬火后的合金,放置一段时间(如4~6昼夜后),强度和硬度会显著提高,而塑性则明显降低。淬火后铝合金的强度、硬度随时间增长而显著提高的现象,称为时效。时效可以在常温下发生,称自然时效,也可以在高于室温的某一温度范围(如100~200℃)内发生,称人工时效。 铝合金时效强化原理 铝合金的时效硬化是一个相当复杂的过程,它不仅决定于合金的组成、时效工艺,还取决于合金在生产过程中缩造成的缺陷,特别是空位、位错的数量和分布等。目前普遍认为时效硬化是溶质原子偏聚形成硬化区的结果。 铝合金在淬火加热时,合金中形成了空位,在淬火时,由于冷却快,这些空位来不及移出,便被“固定”在晶体内。这些在过饱和固溶体内的空位大多与溶质原子结合在一起。由于过饱和固溶体处于不稳定状态,必然向平衡状态转变,空位的存在,加速了溶质原子的扩散速度,因而加速了溶质原子的偏聚。 硬化区的大小和数量取决于淬火温度与淬火冷却速度。淬火温度越高,空位浓度越大,硬化区的数量也就越多,硬化区的尺寸减小。淬火冷却速度越大,固溶体内所固定的空位越多,有利于增加硬化区的数量,减小硬化区的尺寸。 沉淀硬化合金系的一个基本特征是随温度而变化的平衡固溶度,即随温度增加固溶度增加,大多数可热处理强化的的铝合金都符合这一条件。沉淀硬化所要求的溶解度-温度关系,可用铝铜系的Al-4Cu 合金说明合金时效的组成和结构的变化。图3-1铝铜系富铝部分的二元相图,在548℃进行共晶转变L→α+θ(Al2Cu)。铜在α相中的极限溶解度5.65%(548℃),随着温度的下降,固溶度急剧减小,室温下约为0.05%。 在时效热处理过程中,该合金组织有以下几个变化过程: 形成溶质原子偏聚区-G·P(Ⅰ)区 在新淬火状态的过饱和固溶体中,铜原子在铝晶格中的分布是任意的、无序的。时效初期,即时效温度低或时效时间短时,铜原子在铝基体上的某些晶面上聚集,形成溶质原子偏聚区,称G·P(Ⅰ)区。G·P(Ⅰ)区与基体α保持共格关系,这些聚合体构成了提高抗变形的共格应变区,故使合金的强度、硬度升高。 G·P区有序化-形成G·P(Ⅱ)区 随着时效温度升高或时效时间延长,铜原子继续偏聚并发生有序化,即形成G·P(Ⅱ)区。它与基体α仍保持共格关系,但尺寸较G·P(Ⅰ)区大。它可视为中间过渡相,常用θ”表示。它比G·P(Ⅰ)区周围的畸变更大,对位错运动的阻碍进一步增大,因此时效强化作用更大,θ”相析出阶段为合金达到最大强化的阶段。 形成过渡相θ′ 随着时效过程的进一步发展,铜原子在G·P(Ⅱ)区继续偏聚,当铜原子与铝原子比为1:2时,形成过渡相θ′。由于θ′的点阵常数发生较大的变化,故当其形成时与基体共格关系开始破坏,即由完全共格变为局部共格,因此θ′相周围基体的共格畸变减弱,对位错运动的阻碍作用亦减小,表现在合金性能上硬度开始下降。由此可见,共格畸变的存在是造成合金时效强化的重要因素。 形成稳定的θ相 过渡相从铝基固溶体中完全脱溶,形成与基体有明显界面的独立的稳定相Al2Cu,称为θ相此时θ相与基体的共格关系完全破坏,并有自己独立的晶格,其畸变也随之消失,并随时效温度的提高或时间的
“钢的热处理原理及工艺”作业题
“钢的热处理原理及工艺”作业题 第一章固态相变概论 1、扩散型相变和无扩散型相变各有哪些特点? 2、说明晶界和晶体缺陷对固态相变成核的影响。 3、说明相界面和应变能在固态相变中的作用,并讨论它们对新相形状的影响。 4、固-固相变的等温转变动力学曲线是“C”形的原因是什么? 第二章奥氏体形成 1、为何共析钢当奥氏体刚刚完成时还会有部分渗碳体残存?亚共析钢加热转变时是否也存在碳化物溶解阶段? 2、连续加热和等温加热时,奥氏体形成过程有何异同?加热速度对奥氏体形成过程有何影响? 3、试说明碳钢和合金钢奥氏体形成的异同。 4、试设计用金相-硬度法测定40钢和T12钢临界点的方案。 5、将40、60、60Mn钢加热到860℃并保温相同时间,试问哪一种钢的奥氏体晶粒大一些? 6、有一结构钢,经正常加热奥氏体化后发现有混晶现象,试分析可能原因。 第三章珠光体转变 1、珠光体形成的热力学特点有哪些?相变主要阻力是什么?试分析片间距S与过冷度△T的关系。 2、珠光体片层厚薄对机械性能有什么影响?珠光体团直径大小对机械性能影响如何? 3、某一GCr15钢制零件经等温球化退火后,发现其组织中除有球状珠光体外,还有部分细片状珠光体,试分析其原因。 4、将40、40Cr、40CrNiMo钢同时加热到860℃奥氏体化后,以同样冷却速度使之发生珠光体转变,它们的片层间距和硬度有无差异? 5、试述先共析网状铁素体和网状渗碳体的形成条件及形成过程。 6、为达到下列目的,应分别采取何热处理方法? (1)为改善低、中、高碳钢的切削加工性; (2)经冷轧的低碳钢板要求提高塑性便于继续变形; (3)锻造过热的60钢毛坯为细化其晶粒; (4)要消除T12钢中的网状渗碳体; 第四章、马氏体转变
金属热处理原理与工艺复习提纲精选版
金属热处理原理与工艺 复习提纲 Document serial number【KKGB-LBS98YT-BS8CB-BSUT-BST108】
一、名词解释 1.正火:把零件加热到临界温度以上30-50℃,保温一段时间,然后在空气中冷却的热处理工艺。 2.退火:将钢加热、保温后,随炉冷却后,获得接近平衡状态组织的热处理工艺。 3.回火:将淬火钢重新加热到A1线以下某一温度,保温一定时间后再冷却到室温的热处理工艺。 4.淬火:将钢加热到AC1或AC3以上某一温度,保温一定时间,以大于临界冷却速度进行快速冷却,获得马氏体或下贝氏体组织的热处理工艺。 5.淬硬性:钢淬火后的硬化能力。 6.淬透性:钢淬火时获得马氏体的能力。 7.贝氏体:过冷奥氏体中温转变的产物。 8.马氏体:C原子溶入 -Fe形成的饱和间隙固溶体。 9.贝氏体转变:奥氏体中温转变得到贝氏体的过程。 10.马氏体转变:将奥氏体快速冷却到Ms点以下得到马氏体组织的过程。 11.脱溶:从过饱和固溶体中析出第二相(沉淀相)、形成溶质原子聚集区以及亚稳定过渡相的过程称为脱溶或沉淀,是一种扩散型相变。 12.固溶:将双相组织加热到固溶度线以上某一温度保温足够时间,获得均匀的单相固溶体的处理工艺。 13.固溶强化:当溶质原子溶入溶剂原子而形成固溶体时,使强度、硬度提高,塑性、韧性下降的现象。 14.渗碳:向钢的表面渗入碳原子的过程。
15.渗氮:向钢的表面渗入氮原子的过程。 16.化学热处理:将零件放在特定的介质中加热、保温,以改变其表层化学成分和组织,从而获得所需力学或化学性能的工艺总称。 17.表面淬火:在不改变钢的化学成分及心部组织情况下,利用快速加热将表层奥氏体化后进行淬火以强化零件表面的热处理方法。 二、简答题 1.材料的强韧化机制及其应用 答:固溶强化; 位错强化; 第二相强化; ④细晶强化。 2.相变应力/组织应力是什么对组织性能有什么影响 3. 答:组织应力又称相变应力:金属制品在加热和冷却时发生相变,由于新旧相之间存在着结构和比容差异,制品各部分又难以同时发生相变,或者各部分的相变产物有所不同,也会引起应力,这种因组织结构转变不均均而产生的应力称为组织应力。 热应力:金属制品在加热和冷却过程中,由于各部分加热速度或冷却速度不同造成制品各部分温度差异,从而热胀冷缩不均匀所引起的内应力。4.奥氏体化的形成及控制(形成过程、机理、及控制措施)其中包含的化学反应有哪些? 答:奥氏体:C溶于γ–Fe的八面体间隙形成间隙式固溶体
《金属热处理原理与工艺》课程设计
2.1、什么是热处理 所谓钢的热处理,就是对于固态范围内的钢,给以不同的加热、保温和冷却,以改变它的性能的一种工艺。钢本身是一种铁炭合金,在固态范围内,随着加温和冷却速度的变化,不同含炭量的钢,其金相组织发生不同的变化。不同金相组织的钢具有不同的性能。因此利用不同的加热温度和冷却速度来控制和改变钢的组织结构,便可得到不同性能的钢。例如,含炭量百分之0.8的钢称为共析钢,在723摄氏度以上十时为奥氏体,如果将它以缓慢的速度冷却下来,它便转变成为珠光体。但如果用很快的速度把它冷却下来,则奥氏体转变成为马氏体。马氏体和珠光体在组织上决然不同,它们的性能差别悬殊,如马氏体具有比珠光体高的多的硬度和耐磨性。因此,钢的热处理在钢的使用和加工中,占有十分重要的地位。 2.2、热处理的作用 机床、汽车、摩托车、火车、矿山、石油、化工、航空、航天等用的大量零部件需要通过热处理工艺改善其性能。拒初步统计,在机床制造中,约60%~70%的零件要经过热处理,在汽车、拖拉机制造中,需要热处理的零件多达70%~80%,而工模具及滚动轴承,则要100%进行热处理。总之,凡重要的零件都必须进行适当的热处理才能使用。 材料的热处理通常指的是将材料加热到相变温度以上发生相变,再施以冷却再发生相变的工艺过程。通过这个相变与再相变,材料的内部组织发生了变化,因而性能变化。例如碳素工具钢T8在市面上购回的经球化退火的材料其硬度仅为20HRC,作为工具需经淬火并低温回火使硬度提高到60~63HRC,这是因为内部组织由淬火之前的粒状珠光体转变为淬火加低温回火后的回火马氏体。同一种材料热处理工艺不一样其性能差别很大。热处理工艺(或制度)选择要根据材料的成份,材料内部组织的变化依赖于材料热处理及其它热加工工艺,材料性能的变化又取决于材料的内部组织变化,材料成份-加工工艺-组织结构-材料性能这四者相互依成的关系贯穿在材料加工的全过程之中。
铝合金热处理原理及工艺
铝合金热处理原理及工艺 3.1铝合金热处理原理 铝合金铸件得热处理就是选用某一热处理规范,控制加热速度升到某一相应温度下保温一定时间以一定得速度冷却,改变其合金的组织,其主要目的是提高合金的力学性能,增强耐腐蚀性能,改善加工型能,获得尺寸的稳定性。 3.1.1铝合金热处理特点 众所周知,对于含碳量较高的钢,经淬火后立即获得很高的硬度,而塑性则很低。然而对铝合金并不然,铝合金刚淬火后,强度与硬度并不立即升高,至于塑性非但没有下降,反而有所上升。但这种淬火后的合金,放置一段时间(如4~6昼夜后),强度和硬度会显著提高,而塑性则明显降低。淬火后铝合金的强度、硬度随时间增长而显著提高的现象,称为时效。时效可以在常温下发生,称自然时效,也可以在高于室温的某一温度范围(如100~200℃)内发生,称人工时效。 3.1.2铝合金时效强化原理 铝合金的时效硬化是一个相当复杂的过程,它不仅决定于合金的组成、时效工艺,还取决于合金在生产过程中缩造成的缺陷,特别是空位、位错的数量和分布等。目前普遍认为时效硬化是溶质原子偏聚形成硬化区的结果。 铝合金在淬火加热时,合金中形成了空位,在淬火时,由于冷却快,这些空位来不及移出,便被“固定”在晶体内。这些在过饱和固溶体内的空位大多与溶质原子结合在一起。由于过饱和固溶体处于不稳定状态,必然向平衡状态转变,空位的存在,加速了溶质原子的扩散速度,因而加速了溶质原子的偏聚。 硬化区的大小和数量取决于淬火温度与淬火冷却速度。淬火温度越高,空位浓度越大,硬化区的数量也就越多,硬化区的尺寸减小。淬火冷却速度越大,固溶体内所固定的空位越多,有利于增加硬化区的数量,减小硬化区的尺寸。 沉淀硬化合金系的一个基本特征是随温度而变化的平衡固溶度,即随温度增加固溶度增加,大多数可热处理强化的的铝合金都符合这一条件。沉淀硬化所要求的溶解度-温度关系,可用铝铜系的Al-4Cu合金说明合金时效的组成和结构的变化。图3-1铝铜系富铝部分的二元相图,在548℃进行共晶转变L→α+θ(Al2Cu)。铜在α相中的极限溶解度5.65%(548℃),随着温度的下降,固溶度急剧减小,室温下约为0.05%。 在时效热处理过程中,该合金组织有以下几个变化过程: 3.1.2.1 形成溶质原子偏聚区-G·P(Ⅰ)区 在新淬火状态的过饱和固溶体中,铜原子在铝晶格中的分布是任意的、无序的。时效初期,即时效温度低或时效时间短时,铜原子在铝基体上的某些晶面上聚集,形成溶质原子偏聚区,称G·P(Ⅰ)区。G·P(Ⅰ)区与基体α保持共格关系,这些聚合体构成了提高抗变形的共格应变区,故使合金的强度、硬度升高。 3.1.2.2 G·P区有序化-形成G·P(Ⅱ)区 随着时效温度升高或时效时间延长,铜原子继续偏聚并发生有序化,即形成G·P(Ⅱ)区。它与基体α仍保持共格关系,但尺寸较G·P(Ⅰ)区大。它可视为中间过渡相,常用θ”表示。它比G·P(Ⅰ)区周围的畸变更大,对位错运动的阻碍进一步增大,因此时效强化作用更大,θ”相析出阶段为合金达到最大强化的阶段。 3.1.2.3形成过渡相θ′ 随着时效过程的进一步发展,铜原子在G·P (Ⅱ)区继续偏聚,当铜原子与铝原子比为1:2时,形成过渡相θ′。由于θ′的点阵常数发生较大的变化,故当其形成时与基体共格关系开始破坏,即由完全共格变为局部共格,因此θ′相周围基体的共格畸变减弱,对位错运动的阻碍作用亦减小,表现在合金性能上硬度开始下降。由此可见,共格畸变的存在是造成合金时效强化的重要因素。 3.1.2.4 形成稳定的θ相 过渡相从铝基固溶体中完全脱溶,形成与基体有明显界面的独立的稳定相Al2Cu,称为θ相此时θ相与基体的共格关系完全破坏,并有自己独立的晶格,其畸变也随之消失,并随时效温度的提高或时间的延长,θ相的质点聚集长大,合金的强度、硬度进一步下降,合金就软化并称为“过时效”。θ相聚集长大而变得粗大。 铝-铜二元合金的时效原理及其一般规律对于其他工业铝合金也适用。但合金的种类不同,形成的G·P区、过渡相以及最后析出的稳定性各不相同,时效强化效果也不一样。几种常见铝合金系的时效过程及其析出的稳定相列于表3-1。从表中可以看到,不同合金系时效过程亦不完全都经历了上述四个阶段,有的合金不经过G·P(Ⅱ)区,直接形成过渡相。就是同一合金因时效的温度和时
金属热处理工艺学课后习题答案及资料
1.热处理工艺:通过加热,保温和冷却的方法使金属和合金内部组织结构发生变化,以获得工件使用性能所要求的组织结构,这种技术称为热处理工艺。 2.热处理工艺的分类:(1)普通热处理(退火、正火、回火、淬火)(2)化学热处理(3)表面热处理(3)复合热处理 3.由炉内热源把热量传给工件表面的过程,可以借辐射,对流,传导等方式实现,工件表面获得热量以后向内部的传递过程,则靠热传导方式。 4.影响热处理工件加热的因素:(1)加热方式的影响,加热速度按随炉加热、预热加热、到温入炉加热、高温入炉加热的方向依次增大;(2)加热介质及工件放置方式的影响:①加热介质的影响;②工件在炉内排布方式的影响直接影响热量传递的通道;③工件本身的影响:工件的几何形状、表面积与体积之比以及工件材料的物理性质等直接影响工件内部的热量传递及温度场。 5.金属和合金在不同介质中加热时常见的化学反应有氧化,脱碳;物理作用有脱气,合金元素的蒸发等。 6.脱碳:钢在加热时不仅表面发生氧化,形成氧化铁,而且钢中的碳也会和气氛作用,使钢的表面失去一部分碳,含碳量降低,这种现象称为脱碳钢脱碳的过程和脱碳层的组织特点: ①钢件表面的碳与炉气发生化学反应(脱碳反应),形成含碳气体逸出表面, 使表面碳浓度降低②由于表面碳浓度的降低,工件表面与内部发生浓度差,从而发生内部的碳向表面扩散的过程。 半脱碳层组织特点;自表面到中心组织依次为珠光体加铁素体逐渐过渡到珠光体,再至相当于该钢件未脱碳时的退火组织。(F+P—P+C—退火组织) 全脱碳层组织特点:表面为单一的铁素体区,向里为铁素体加珠光体逐渐过渡到相当于钢原始含碳量缓冷组织 在强氧化性气体中加热时,表面脱碳与表面氧化往往同时发生。在一般情况下,表面脱碳现象比氧化现象更易发生,特别是含碳量高的钢。 7.碳势:即纯铁在一定温度下于加热炉气中加热时达到既不增碳也不脱碳并与炉气保持平衡时表面的含碳量。 8.退火:将组织偏离平衡状态的金属或合金加热到适当的温度,保持一定时间,然后缓慢冷却以达到接近平衡状态组织的热处理工艺称为退火。退火的目的在于均匀化学成分,改善机械性能及工艺性能,消除或减少内应力,并为零件最终热处理准备合适的内部组织。 9.钢件退火工艺按加热温度分类:(1)在临界温度以上的退火,又称相变重结晶退火,包括完全退火,不完全退火。扩散退火和球化退火。(2)在临界温度以下的退火,包括软化退火,再结晶退火及去应力退火。按冷却方式可分为连续冷却退火及等温退火。 10.正火:是将钢材或钢件加热到Ac3(或Accm)以上适当温度,保温适当时间后在空气中冷却,得到珠光体类组织的热处理工艺。目的是获得一定的硬度,细化晶粒,并获得比较均匀的组织和性能。 11.扩散退火: 将金属铸锭,铸件或锻坯,在略低于固相线的温度下长期加热,消除或减少化学成分偏析及显微组织(枝晶)的不均匀性,以达到均匀化目的的热处理工艺称为扩散退火,又称均匀化退火。 12.完全退火:将钢件或钢材加热到Ac3点以上,使之完全奥氏体化,然后缓慢冷却,获得接近于平衡组织的热处理工艺称为完全退火。
金属热处理原理复习参考
《金属热处理原理及工艺》习题一 (参考答案) 1.金属固态相变有哪些主要特征?哪些因素构成了相变阻力? 主要特征:①界面能-惯习面 ②界面能-位向关系 ③弹性应变能 ④缺陷的影响 ⑤原子迁移率低 ⑥有亚稳过渡相形成 相变阻力:界面能+弹性应变能。 2.固态相变的形核位置有哪些?为什么非均匀形核成为固态相变的主要形核方式? 均匀形核、晶界形核(界面、界棱、界隅)、位错、空位等。 原因:1)固态下原子激活能大,均匀形核率低; 2)非均匀形核降低了临界形核功,提供补充能量。 3.试计算奥氏体含2.11%的碳(wt%)时,平均几个γ-Fe晶胞才有一个碳原子? 设n个晶胞有一个碳原子: = n .2 48 4.以共析钢为例,说明奥氏体是怎样形成的。并讨论为什么在铁素体消失的瞬间,还有 部分渗碳体未溶解? 奥氏体形成驱动力:奥氏体与珠光体自由能差值,转变通过扩散进行,分以下4个阶段: 1)奥氏体核在铁素体和渗碳体交界处通过C原子扩散形成; 2)奥氏体核通过渗碳体溶解、C在奥氏体中扩散以及在奥氏体两侧边界向铁素体、渗碳体推移进行;
3)渗碳体溶解; 4)奥氏体均匀化。 铁素体消失的瞬间,还有部分渗碳体未溶解的原因:奥氏体/渗碳体界面处的碳浓度差远远大于奥氏体/铁素体界面处的浓度差,所以只需溶解一小部分渗碳体就可以使其相界面处的奥氏体达到饱和,而必须溶解大量的铁素体才能使其相界面处奥氏体的碳浓度趋于平衡。故在共析钢中总是铁素体先消失,有剩余渗碳体残留下来。 5.快速加热时奥氏体的形成与恒温下的奥氏体形成对比,有哪些不同?为什么? ①快速加热A形成是在一定温度范围内形成。 ②加热速度越快,A晶粒越细小,但易长大。 ③随加热速度加快,A成分不均匀性增大。 6.什么叫组织遗传?如果淬火过热,应如何返修? 组织遗传:相变后,新相仍保持旧相晶粒的大小和形状。 返修:1)中速加热; 2)采用快速或慢速加热到高于临界点150~200℃,使粗晶粒通过再结晶细化; 3)先进行一次退火以获得平衡组织,然后再进行加热。 7.试计算奥氏体八面体间隙大小。 8.试讨论Fe-Fe3C状态图所给出临界点与实际加热冷却时临界点的关系。 在平衡点有ΔGv=0,实际加热过程中过冷(热)度提供了相变的驱动力。且随着加热温度或加热速度的提高,相变临界点升高;随冷却温度或冷却速度的降低,临界点降低。有A C1>A1>A r1、A C3>A3>A r3、A Ccm>A cm>A rcm。
金属热处理原理与工艺复习提纲
、名词解释 1.正火:把零件加热到临界温度以上30-50 C,保温一段时间,然后在空气中冷却的热处理工艺。 2.退火:将钢加热、保温后,随炉冷却后,获得接近平衡状态组织的热处理工艺。 3.回火:将淬火钢重新加热到A1线以下某一温度,保温一定时间后再冷却到室温的热处理工艺。 4.淬火:将钢加热到AC1或AC3以上某一温度,保温一定时间,以大于临界冷却速度进行快速冷却,获得马氏体或下贝氏体组织的热处理工艺。 5.淬硬性:钢淬火后的硬化能力。 6.淬透性:钢淬火时获得马氏体的能力。 7.贝氏体:过冷奥氏体中温转变的产物。 8.马氏体:C原子溶入-Fe形成的饱和间隙固溶体。 9.贝氏体转变:奥氏体中温转变得到贝氏体的过程。 10.马氏体转变:将奥氏体快速冷却到Ms点以下得到马氏体组织的过程。 11.脱溶:从过饱和固溶体中析出第二相(沉淀相)、形成溶质原子聚集区以及亚稳定过渡相的过程称为脱溶或沉淀,是一种扩散型相变。 12.固溶:将双相组织加热到固溶度线以上某一温度保温足够时间,获得均匀的单相固溶体的处理工艺。 13.固溶强化:当溶质原子溶入溶剂原子而形成固溶体时,使强度、 硬度提高,塑性、韧性下降的现象。 14.渗碳:向钢的表面渗入碳原子的过程。
15.渗氮:向钢的表面渗入氮原子的过程。 16.化学热处理:将零件放在特定的介质中加热、保温,以改变其表层化学成分和组织,从而获得所需力学或化学性能的工艺总称。 17.表面淬火:在不改变钢的化学成分及心部组织情况下,利用快速加热将表层奥氏体化后进行淬火以强化零件表面的热处理方法。 二、简答题 1.材料的强韧化机制及其应用 答:固溶强化; 位错强化; 第二相强化; ④细晶强化。 2.相变应力/组织应力是什么?对组织性能有什么影响? 答:组织应力又称相变应力:金属制品在加热和冷却时发生相变,由于新旧相之间存在着结构和比容差异,制品各部分又难以同时发生相变,或者各部分的相变产物有所不同,也会引起应力,这种因组织结构转变不均均而产生的应力称为组织应力。 热应力:金属制品在加热和冷却过程中,由于各部分加热速度或冷却速度不同造成制品各部分温度差异,从而热胀冷缩不均匀所引起的内应力。 3.奥氏体化的形成及控制(形成过程、机理、及控制措施)其中包含的化学反应有哪些? 答:奥氏体:C溶于Y- Fe的八面体间隙形成间隙式固溶体 形成过程:形核:通常在铁素体与渗碳体的两相界面处或珠光体团的边界
金属热处理原理
金属热处理原理 绪论 一、研究的内容和任务 金属热处理原理是以金属学原理为基础,着重研究金属及合金固态相变的基本原理和热处理组织与性能之间关系的一门课程。 金属学原理:着重讨论的是金属及合金的本质及影响因素、缺陷及其交互作用和它们对性能的影响、状态图、塑性变形、回复、再结晶等等。 热处理原理:着重讨论的是金属及合金在固态下的相变规律、影响因素、动力学、非平衡转变,以及在热处理中的应用,研究热处理组织和性能之间的关系等等。 金属材料从服役条件出发,选择什么样的材料、如何对材料进行处理,在使用和处理过程中会出现什么问题,如何解决出现的问题,最终可能得到什么样的性能,如何改进现有材料、挖掘其潜力,试制新材料等,无不与热处理原理有着密切的关系。 固态金属(包括纯金属及合金)在温度和压力改变时,组织和结构会发生变化,这种变化统称为金属固态相变。金属中固态相变的类型很多,有的金属在不同的条件下会发生几种不同类型的转变。掌握金属固态相变的规律及影响因素,就可以采取措施控制相变过程,以获得预期的组织,从而使其具有预期的性能。对于金属材料常用的措施就是特定加热和冷却,也就是热处理。 二、热处理发展概况 人们在开始使用金属材料起,就开始使用热处理,其发展过程大体上经历了三个阶段。 1、民间技艺阶段 根据现有文物考证,我国西汉时代就出现了经淬火处理的钢制宝剑。史书记载,在战国时期即出现了淬火处理,据秦始皇陵开发证明,当时已有烤铁技术,兵马俑中的武士佩剑制作精良,距今已有两千多年的历史,出土后表面光亮完好,令世人赞叹。古书中有“炼钢赤刀,用之切玉如泥也”,可见当时热处理技术发展的水平。但是中国几千年的封建社会造成了贫穷落后的局面,在明朝以后热处理技术就逐渐落后于西方。虽然我们的祖先很有聪明才智,掌握了很多热处理技术,但是把热处理发展成一门科学还是近百年的事。在这方面,西方和俄国的学者走在了前面,新中国成立以后,我国的科学家也作出了很大的贡献。 2、技术科学阶段(实验科学)—金相学 此阶段大约从1665年1895年,主要表现为实验技术的发展阶段。 1665年:显示了Ag—Pt组织、钢刀片的组织; 1772年:首次用显微镜检查了钢的断口; 1808年:首次显示了陨铁的组织,后称魏氏组织; 1831年:应用显微镜研究了钢的组织和大马士革剑; 1864年:发展了索氏体; 1868年:发现了钢的临界点,建立了Fe—C相图; 1871年:英国学者T. A. Blytb 著“金相学用为独立的科学”在伦敦出版; 1895年:发现了马氏体; 3、建立了一定的理论体系—热处理科学 “S”,曲线的研究,马氏体结构的确定及研究,K—S关系的发现,对马氏体的结构有了新的认识等,建立了完整的热处理理论体系。
热处理工艺设计
50CrVA钢调速弹簧的 热处理工艺设计 1 热处理工艺课程设计的意义 热处理工艺课程设计是高等工业学校金属材料工程专业一次专业课设计练习,是热处理原理与工艺课程的最后一个教学环节。其目的是: (1)培养学生综合运用所学的热处理课程的知识去解决工程问题的能力,并使其所学知识得到巩固和发展。 (2)学习热处理工艺设计的一般方法、热处理设备选用和装夹具设计等。(3)进行热处理设计的基本技能训练,如计算、工艺图绘制和学习使用设计资料、手册、标准和规范。 2热处理课程设计的任务 ①普通热处理工艺设计 ②特殊热处理工艺设计 ③制定热处理工艺参数 ④选择热处理设备 ⑤设计热处理工艺所需的挂具、装具或夹具 ⑥分析热处理工序中材料的组织和性能 ⑦填写工艺卡片 350CrVA调速弹簧的技术要求及选材 3.1 技术要求 50CrVA钢喷油泵调速弹簧技术要求如下: 硬度:HRC46~51 3.2 零件图 喷油泵调速弹簧的零件如图3.1所示。
图3.1 喷油泵调速弹簧 3.3 材料的选择 3.3.1零件用途 喷油泵调速弹簧,利用弹簧的受力形变和恢复来调节气门的开合,从而调节喷油泵的喷油速度与喷油量。 3.3.2工作条件 (1)喷油泵调速弹簧工作时,要承受高应力。 (2)喷油泵调速弹簧要承受高频率往复运动。 (3)喷油泵调速弹簧要在较高的温度下工作。 3.3.3性能要求 弹簧的性能要求为如下几个方面:
力学性能:由于弹簧是在弹性范围内工作,不允许有永久变形。要求弹簧材料有良好的微塑性变形能力,即弹性极限、屈服极限和屈强比要高。 理化性能方面:喷油泵调速弹簧的工况很复杂,要在较高的温度下长期工作,因此要求弹簧材料有良好的耐热性,即有高的蠕变极限、蠕变速率较小和较低的应力松弛率。 工艺性能方面:尺寸较小的弹簧热处理时变形大、难以校正和保证弹簧产品质量,宜选用已强化的弹簧材料,冷成型后不经淬火、回火,只须进行低温退火。这样更能保证大批量小弹簧的产品质量和成本低廉。 3.3.4材料选择 选用50CrVA钢热轧弹簧钢丝卷制。由于50CrVA钢中含有铬能够提高淬透性并且可降低锰引起过热的敏感性,铬熔于铁素体中使弹性极限提高。钒可以细化组织,减少过热敏感性,提高钢的强度和冲击韧性。可用作特别重要的承受高应力的各种尺寸的螺旋弹簧,也可也用作在300°C以下工作的重要弹簧,如各种阀门弹簧,喷油嘴弹簧。 3.3.550CrVA钢化学成分及合金元素作用 表3.1 50CrVA钢的化学成分[1](GB/T3077-1990)ω/% C Si Mn Cr V Ni P S 0.44~0.54 0.17~0.37 0.50~0.80 0.80~1.10 0.10~0.20 ≤0.35 ≤0.035 ≤0.030 50CrVA钢的化学成分示于表3.1 化学元素作用: ① C :保证形成碳化物所需要的碳和保证淬火马氏体能够获得的硬度 ② Cr:提高钢的淬透性并有二次硬化作用,是刚在高温时仍具高强度和高硬度,增加钢的耐磨性,增高钢的淬火温度。 ③ Si:能提高钢的淬透性和抗回火性,对钢的综合机械性能,还能增高淬火温度,阻碍碳元素溶于钢中。 ④ Mn:能增加钢的强度和硬度,有脱氧及脱硫的功效(形成MnS),防止热脆,故Mn能改善钢的锻造性和韧性,可增进刚的硬化深度,降低钢的下临界点,增加奥氏体冷却时的过冷度,细化珠光体组织以改善机械性能。 ⑤ V:可以细化组织,减少过热敏感性,提高钢的强度和冲击韧性。
热处理原理与工艺设计课程设计报告
* * 大学 热处理原理与工艺课程设计 题目: 50Si2Mn弹簧钢的热处理工艺设计 院(系):机械工程学院 专业班级:** 学号:******* 学生姓名:** 指导教师:** 起止时间:2014-12-15至2014-12-19
课程设计任务及评语 院(系):机械工程学院教研室:材料教研室 学号******* 学生姓名** 专业班级*** 课程设计 题目 50Si2Mn弹簧钢的热处理工艺设计 课程设计要求与任务一、课设要求 熟悉设计题目,查阅相关文献资料,概述50Si2Mn弹簧钢的热处理工艺,制定出热处理工艺路线,完成工艺设计;分析50Si2Mn弹簧钢的成分特性;阐述50Si2Mn弹簧钢淬火、回火热处理工艺理论基础;阐述各热处理工序中材料的组织和性能;阐明弹簧钢的热处理处理常见缺陷的预防及补救方法;选择设备;给出所用参考文献。 二、课设任务 1.选定相应的热处理方法; 2.制定热处理工艺参数; 3.画出热处理工艺曲线图; 4分析各热处理工序中材料的组织和性能; 5.选择热处理设备 三、设计说明书要求 设计说明书包括三部分:1)概述;2)设计内容;3)参考文献。
工作计划 集中学习0.5天,资料查阅与学习,讨论0.5天,设计6天:1)概述0.5天,2)服役条件与性能要求0.5天,3)失效形式、材料的选择0.5天,4)结构形状与热处理工艺性0.5天,5)冷热加工工序安排0.5天,6)工艺流程图0.5天,7)热处理工艺设计1.5天,8)工艺的理论基础、原则0.5天, 09)可能出现的问题分析及防止措施0.5天,10)热处理质量分析0.5天,设计验收1天。 指 导 教 师 评 语 及 成 绩 成绩:学生签字:指导教师签字: 年月日
金属热处理原理
金属热处理原理 一、热处理的作用 机床、汽车、摩托车、火车、矿山、石油、化工、航空、航天等用的大量零部件需要通过热处理工艺改善其性能。拒初步统计,在机床制造中,约60%~70%的零件要经过热处理,在汽车、拖拉机制造中,需要热处理的零件多达70%~80%,而工模具及滚动轴承,则要100%进行热处理。总之,凡重要的零件都必须进行适当的热处理才能使用。 材料的热处理通常指的是将材料加热到相变温度以上发生相变,再施以冷却再发生相变的工艺过程。通过这个相变与再相变,材料的内部组织发生了变化,因而性能变化。例如碳素工具钢T8在市面上购回的经球化退火的材料其硬度仅为20HRC,作为工具需经淬火并低温回火使硬度提高到60~63HRC,这是因为内部组织由淬火之前的粒状珠光体转变为淬火加低温回火后的回火马氏体。同一种材料热处理工艺不一样其性能差别很大。表6-1列出45钢制直径为F15mm的均匀园棒材料经退火、正火、淬火加低温回火以及淬火加高温回火的不同热处理后的机械性能,导致性能差别如此大的原因是不同的热处理后内部组织截然不同。同类型热处理(例如淬火)的加热温度与冷却条件要由材料成分确定。这些表明,热处理工艺(或制度)选择要根据材料的成份,材料内部组织的变化依赖于材料热处理及其它热加工工艺,材料性能的变化又取决于材料的内部组织变化,材料成份-加工工艺-组织结构-材料性能这四者相互依成的关系贯穿在材料加工的全过程之中。 二、热处理的基本要素 热处理工艺中有三大基本要素:加热、保温、冷却。这三大基本要素决定了材料热处理后的组织和性能。 加热是热处理的第一道工序。不同的材料,其加热工艺和加热温度都不同。加热分为两种,一种是在临界点A1以下的加热,此时不发生组织变化。另一种是在A1以上的加热,目的是为了获得均匀的奥氏体组织,这一过程称为奥氏体化。 保温的目的是要保证工件烧透,防止脱碳、氧化等。保温时间和介质的选择与工件的尺寸和材质有直接的关系。一般工件越大,导热性越差,保温时间就越长。 冷却是热处理的最终工序,也是热处理最重要的工序。钢在不同冷却速度下可以转变为不同的组织。 三、热处理的基本类型 根据加热、冷却方式的不同及组织、性能变化特点的不同,热处理可以分为下列几类:1.普通热处理包括退火、正火、淬火和回火等。 2.表面热处理包括感应加热表面淬火、火焰加热表面淬火、电接触加热表面淬火、渗碳、氮化和碳氮共渗等。
金属热处理原理及工艺 期末总结
正火:将钢材或钢件加热到临界点AC3或ACM 以上的适当温度保持一定时间后在空气中冷却,得到珠光体类组织的热处理工艺。 退火:将亚共析钢工件加热至AC3以上20—40度,保温一段时间后,随炉缓慢冷却(或埋在砂中或石灰中冷却)至500度以下在空气中冷却的热处理工艺 固溶热处理:将合金加热至高温单相区恒温保持,使过剩相充分溶解到固溶体中,然后快速冷却,以得到过饱和固溶体的热处理工艺 时效:合金经固溶热处理或冷塑性形变后,在室温放置或稍高于室温保持时,其性能随时间而变化的现象。Al-4Cu合金在时效过程中,过饱和固溶体的各个沉淀阶段,其顺序可概括为:α过饱和→G.P.区θ''→过渡相θ'→过渡相θ→(CuAl2)稳定相 固溶处理:使合金中各种相充分溶解,强化固溶体并提高韧性及抗蚀性能,消除应力与软化,以便继续加工成型 时效处理:在强化相析出的温度加热并保温,使强化相沉淀析出,得以硬化,提高强度时效处理有自然时效和人工时效两种。 淬火:将钢奥氏体化后以适当的冷却速度冷却,使工件在横截面内全部或一定的范围内发生马氏体等不稳定组织结构转变的热处理工艺 回火:将经过淬火的工件加热到临界点AC1以下的适当温度保持一定时间,随后用符合要求的方法冷却,以获得所需要的组织和性能的热处理工艺 调质处理:将钢件淬火,随之进行高温回火,这种复合工艺称调质处理。 表面热处理:改变钢件表面组织或化学成分,以其改面表面性能的热处理工艺。 表面淬火:是将钢件的表面通过快速加热到临界温度以上,但热量还未来得及传到心部之前迅速冷却,这样就可以把表面层被淬在马氏体组织,而心部没有发生相变,这就实现了表面淬硬而心部不变的目的。适用于中碳钢。 化学热处理:是指将化学元素的原子,借助高温时原子扩散的能力,把它渗入到工件的表面层去,来改变工件表面层的化学成分和结构,从而达到使钢的表面层具有特定要求的组织和性能的一种热处理工艺 渗碳:向钢的表面渗入碳原子,提高表面含碳量,提高材料表面硬度、抗疲劳性和耐磨性。 渗氮:在工件表面渗入氮原子,形成一个富氮硬化层的过程。提高材料表面硬度、抗疲劳性和耐磨性,且渗氮性能优于渗碳。 碳氮共渗:碳氮同时渗入工件表层。提高表面硬度、抗疲劳性和耐磨性,并兼具渗碳和渗氮的优点 完全退火和等温退火又称重结晶退火,一般简称为退火,这种退火主要用于亚共析成分的各种碳钢和合金钢的铸,锻件及热轧型材,有时也用于焊接结构。一般常作为一些不重工件的最终热处理,或作为某些工件的预先热处理。 球化退火主要用于过共析的碳钢及合金工具钢(如制造刃具,量具,模具所用的钢种)。其主要目的在于降低硬度,改善切削加工性,并为以后淬火作好准备。 去应力退火又称低温退火(或高温回火),这种退火主要用来消除铸件,锻件,焊接件,热轧件,冷拉件等的残余应力。如果这些应力不予消除,将会引起钢件在一定时间以后,或在随后的切削加工过程中产生变形或裂纹。 铁素体(F)1.组织: 碳在α-Fe(体心立方结构的铁)中的间隙固溶体2.特性: 呈体心立方晶格.溶碳能力最小,最大为0.02%;硬度和强度很 低,HB=80-120,σb=250N/mm^2;而塑性和韧性很好,δ=50%,ψ=70-80%.因此,含铁素体多的钢材(软钢)中用来做可压、挤、冲板与耐冲击震动的机件.这类钢有超低碳钢,如 0Cr13,1Cr13、硅钢片等 奥氏体1.组织: 碳在γ-Fe(面心立方结构的铁)中的间隙固溶体。2.特性:呈面心立方晶格.最高溶碳量为2.06%,在一般情况下,具有高的塑性,但强度和硬度低,HB=170-220,奥氏体组织除了在高温转变时产生以外,在常温时亦存在于不锈钢、高铬钢和高锰钢中,如奥氏体不锈钢等 渗碳体(C)1.组织: 铁和碳的稳定化合物(Fe3C) 2.特性: 呈复杂的八面体晶格.含碳量为6.67%,硬度很高,HRC70-75,耐磨,但脆性很大,因此,渗碳体不能单独应用,而总是与铁素体混合在一起.碳在铁中溶解度很小,所以在常温下,钢铁组织内大部分的碳都是 以渗碳体或其他碳化物形式出现 珠光体(P)1.组织; 铁素体和渗碳体组成的机械混合物(F+Fe3c 含碳0.8%)铁素体片和渗碳体