甲醇催化转化制乙烯
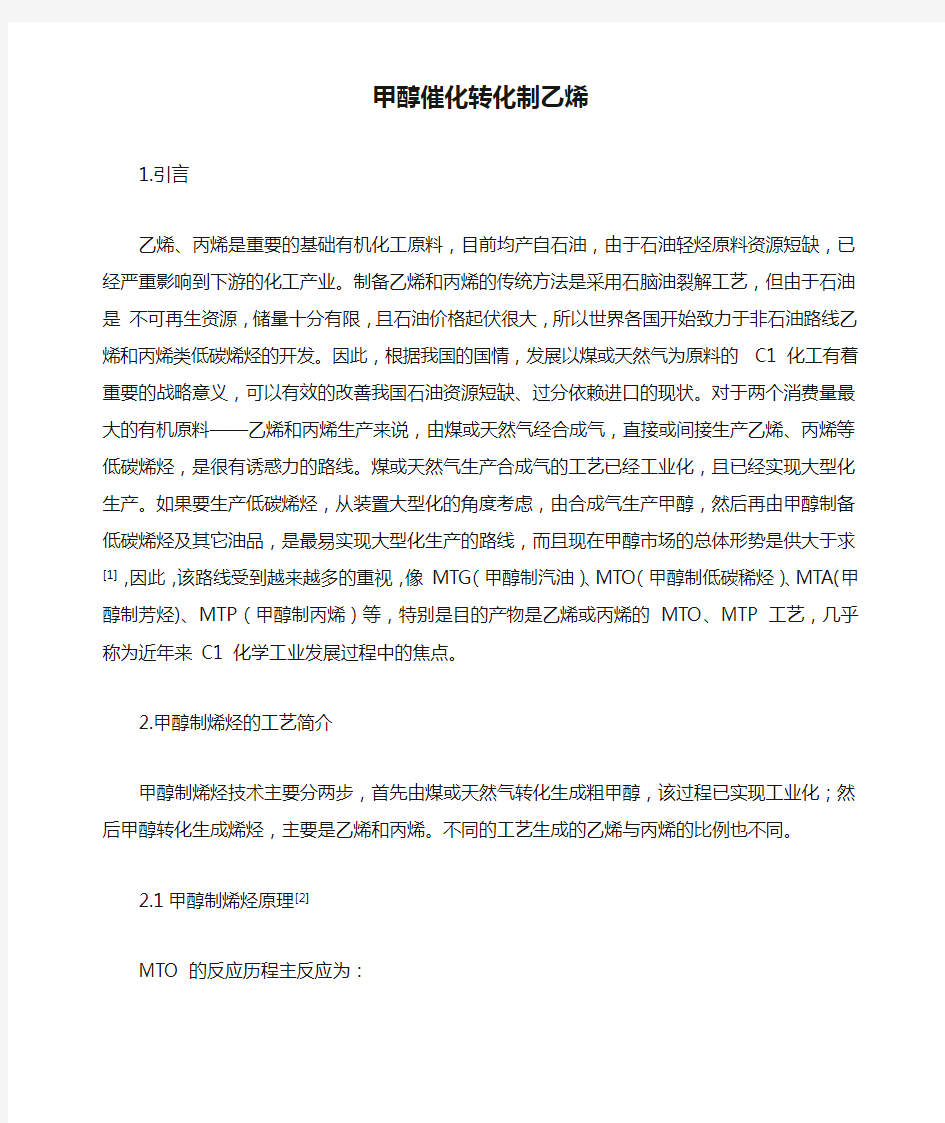
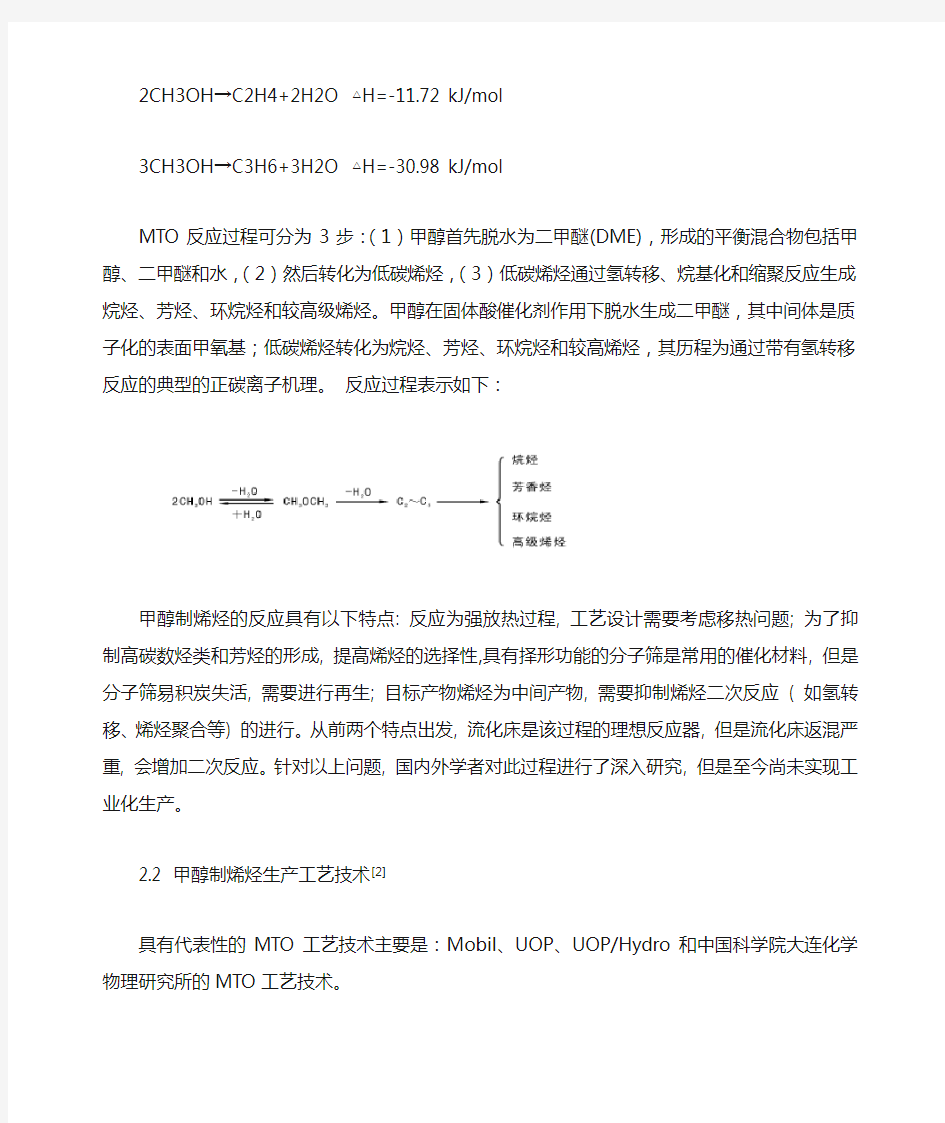
甲醇催化转化制乙烯
1.引言
乙烯、丙烯是重要的基础有机化工原料,目前均产自石油,由于石油轻烃原料资源短缺,已经严重影响到下游的化工产业。制备乙烯和丙烯的传统方法是采用石脑油裂解工艺,但由于石油是不可再生资源,储量十分有限,且石油价格起伏很大,所以世界各国开始致力于非石油路线乙烯和丙烯类低碳烯烃的开发。因此,根据我国的国情,发展以煤或天然气为原料的C1 化工有着重要的战略意义,可以有效的改善我国石油资源短缺、过分依赖进口的现状。对于两个消费量最大的有机原料——乙烯和丙烯生产来说,由煤或天然气经合成气,直接或间接生产乙烯、丙烯等低碳烯烃,是很有诱惑力的路线。煤或天然气生产合成气的工艺已经工业化,且已经实现大型化生产。如果要生产低碳烯烃,从装置大型化的角度考虑,由合成气生产甲醇,然后再由甲醇制备低碳烯烃及其它油品,是最易实现大型化生产的路线,而且现在甲醇市场的总体形势是供大于求[1],因此,该路线受到越来越多的重视,像MTG(甲醇制汽油)、MTO(甲醇制低碳稀烃)、MTA(甲醇制芳烃)、MTP(甲醇制丙烯)等,特别是目的产物是乙烯或丙烯的MTO、MTP 工艺,几乎称为近年来C1 化学工业发展过程中的焦点。
2.甲醇制烯烃的工艺简介
甲醇制烯烃技术主要分两步,首先由煤或天然气转化生成粗甲醇,该过程已实现工业化;然后甲醇转化生成烯烃,主要是乙烯和丙烯。不同的工艺生成的乙烯与丙烯的比例也不同。
2.1甲醇制烯烃原理[2]
MTO 的反应历程主反应为:
2CH3OH→C2H4+2H2O △H=-11.72 kJ/mol
3CH3OH→C3H6+3H2O △H=-30.98 kJ/mol
MTO反应过程可分为3步:(1)甲醇首先脱水为二甲醚(DME),形成的平衡混合物包括甲醇、二甲醚和水,(2)然后转化为低碳烯烃,(3)低碳烯烃通过氢转移、烷基化和缩聚反应生成烷烃、芳烃、环烷烃和较高级烯烃。甲醇在固体酸催化剂作用下脱水生成二甲醚,其中间体是质子化的表面甲氧基;低碳烯烃转化为烷烃、芳烃、环烷烃和较高烯烃,其历程为通过带有氢转移反应的典型的正碳离子机理。反应过程表示如下:
甲醇制烯烃的反应具有以下特点: 反应为强放热过程, 工艺设计需要考虑移热问题; 为了抑制高碳数烃类和芳烃的形成, 提高烯烃的选择性,具有择形功能的分子筛是常用的催化材料, 但是分子筛易积炭失活, 需要进行再生; 目标产物烯烃为中间产物, 需要抑制烯烃二次反应( 如氢转移、烯烃聚合等) 的进行。从前两个特点出发, 流化床是该过程的理想反应器, 但是流化床返混严重, 会增加二次反应。针对以上问题, 国内外学者对此过程进行了深入研究, 但是至今尚未实现工业化生产。
2.2 甲醇制烯烃生产工艺技术[2]
具有代表性的MTO工艺技术主要是:Mobil、UOP、UOP/Hydro和中国科学院大连化学物理研究所的MTO工艺技术。
20世纪80年代初, 美孚公司提出了一种使用ZSM - 5沸石为催化剂, 在列管式反应器中进行甲醇转化制C2和高级烃类的工艺流程, 于1984年进行了9个月的中试试验, 试验规模为日产100桶。在工艺过程中, 甲醇扩散到催化剂孔中进行反应, 先生成二甲醚, 再生成乙烯, 反应继续进行, 生成丙烯、丁烯和高级烯烃, 也可生成二聚物和环状化合物, 以碳选择性为基础, 乙烯收率可达60% , 烯烃总收率可达80%, 大体相当于采用常规石脑油/粗柴油管式炉裂解法收率的2倍, 但催化剂寿命不理想。巴斯夫公司采用沸石催化剂, 在德国建立了一套消耗甲醇30 t d- 1的中试装置。其反应温度为( 300~450) , 压力为( 0. 1~ 0. 5) M P a, 用各种不同沸石作催化剂, C2~ C4烯烃收率为50% ~ 60%, 收率较低。
UOP公司与联碳公司合作, 使用MTO- 100催化剂, 可使甲醇转化率接近100%, 且选择性高, 仅乙烯和丙烯两种产品的收率就达80% 以上。20世纪90 年代初, UOP 与H ydro 公司合作开发的流化床MTO 工艺最具代表性。UOP /H ydro的MTO工艺采用的催化剂是基于硅铝磷酸盐的SAPO- 34( CHA)沸石, SAPO - 34 具有独特的强选择型八元环通道结构, 可有效抑制芳烃生成, 对低碳烯烃, 尤其是乙烯选择性达93% 以上, 与其他催化剂相比, 具有孔径小、孔道密度高、可利用的比表面积大、吸附性能和水热稳定性好等优点。其日产甲醇0. 75 t的示范装置在Hydro公司投入运转, 在( 350~ 500) 和( 0. 1~ 0. 5) MPa下, 甲醇转化率99. 8%, 对C2与C3烯烃的选择性稳
定。该MTO技术可通过改变反应器的操作条件, 根据下游市场的需求情况, 在最大乙烯和最大丙烯操作模式间进行切换。MTO- 100在高丙烯工况下, 丙烯收率可达45%, 乙烯为34% , 丁烯为13% , 其余为副产品。该工艺采用流化床反应器和再生器设计, 使用基于非沸石分子筛的可再生的MTO - 100催化剂, 乙烷、丙烷、二烯烃和炔烃生成少。MTO技术面临的经济挑战是生成较多量丁烯和C+5等副产物质, 每生成1 t乙烯, 产生约0. 34 t的C+5副产品,C+5可用作燃料, 丁烯可生产1- 丁烯或通过仲丁醇转化成甲乙酮, 也可用作炼油厂的烷基化原料, 还可以将丁烯和C+5进一步转化成丙烯和乙烯。UOP/H ydro MTO示范装置运行从1995年6月正式启动,连续运转3个月, 各系统操作正常, 证明MTO- 100具有较好的稳定性和强度, 并具有一定的操作弹性,适当改变操作条件, 还可以调节乙烯和丙烯的比例。
中国科学院大连化学物理研究所早在20世纪80年代开展了由甲醇制烯烃( MTO ) 的工作。六五期间完成了实验室小试, 七五期间完成了300 t a- 1( 处理甲醇) 中试; 采用中孔ZSM - 5沸石催化剂, 达到了同期国际先进水平。80年代中后期, 率先开展了SAPO- 34分子筛合成、表征及用于甲醇制烯烃(MTO)方面的研究工作。20世纪90年代初, 首创了合成气经由二甲醚制取低碳烯烃新工艺方法(简称SDTO法), 该工艺由两段反应构成, 第一段反应是合成气(H2+ CO) 在金属- 沸石双功能催化剂上高选择性地转化为二甲醚; 第二段反应是二甲醚在新一代廉价的小孔硅铝磷酸盐( SAPO- 34) 分子筛催化剂上高选择性地转化为乙烯和丙烯等低碳烯烃, 并经过以水为溶剂分离和提浓二甲醚步骤, 将两段反应串接成完整工艺。所用催化剂为PZSM - 5, 使用固定床, 在( 500~ 550)和( 0. 1~ 0. 15) MPa条件下, 转化率100% , C2~ C4选择性达86%。为降低催化剂成本, 开发了用国产的廉价三乙胺和二乙胺为模板剂合成SAPO- 34的方法, 其成本比四乙基氢氧化胺为模板剂的产品低85% 以上。还研制了专用的MTO 催化剂DO123,DO123催化剂价格比MTO - 100催化剂低很多。
由以上各种生产技术可知,甲醇制烯烃(MTO)工艺技术开发的关键或难点主要有两点:一是选择高活性、高选择性的催化剂;二是配套合适的反应装置及分离装置。3.催化反应热力学、动力学研究及MTO工艺条件选择
3.1 催化剂研究概述
ZSM一5及SAPO一34催化剂是目前甲醇制烯烃过程中常用的催化剂。前者是上世纪七十年代Mobile公司开发得到的中孔沸石催化剂,失活速率较慢,易得到丙烯及
C4以上的烯烃,但其较大的孔道结构及较强的酸性也不可避免的生成芳香烃类大分子产物。目前由南方化学公司开发的ZSM一5改性催化剂广泛运用于Lurgi的MTP工艺,据介绍,其对丙烯选择性较高,超过70%。SAPO一34催化剂则是于上世纪八十年代由UCC(Union Carbide Corporation)首先开发得到铝磷硅分子筛催化剂,其独特的微孔道结构对以乙烯、丙烯为主的低碳烯烃有着很高的选择性,成为甲醇制烯烃过程理想的催化剂,并成为该过程研究的热点。目前很多公司都是基于SAPO一34催化剂进行改性研究和进一步的开发。如国外的UOP以及ExxonMobil公司以及国内的中科院大连化物所。本文只针对SAPO一34催化剂的甲醇制烯烃过程进行研究和分析,下面将主要介绍SAPO一34催化剂的相关特性。如图3.1所示,SAPO一34催化剂主要由四元环和八元环组成的笼体和连接笼体的六棱柱微孔道组成。孔径为0.43nm,活性位点主要存在于笼体内,酸度适中,具有强、弱两种酸中心[3,4]。以上特点使该催化剂相比ZSM一5催化剂在MTO过程中有更好的催化性能。但另一方面,SAPO一34催化剂也更易积碳失活,这是由于其独特的笼体和微通道结构,致使在笼体内形成的芳香烃等重组分更难扩散出来,而困于笼体内形成固体积碳。此外,SAPO一34催化剂还具有良好的水热稳定性。这一特性使该催化剂可在工业生产中长时间反复再生使用。目前的研究方向大多是针对该催化剂做合成工艺的改进和改性实验。合成工艺方面主要是尽量选用低成本的模板剂和优化合成条件;改性实验的研究重点则在于进一步提高低碳烯烃的选择性,降低副产物以及延长催化剂寿命等。
3.1 SAPO-34催化剂构型
3.2反应热力学
3.2.1 甲醇制烯烃反应及其热效应[5]
甲醇制烯烃反应的过程为:甲醇经加热或换热汽化成蒸汽,进入固定床或流化床反应器,在分子筛催化剂上反应生成乙烯、丙烯等低碳烯烃和副产物,然后经过一系列提纯分离装置得到所需产物。经气相色谱分析反应产物得到产物组成: H2、CO、CO2、CH4、C2H4、C2H6、C3H6、C3H8、CH3OCH3、C4、C+5、H2O、CH3OH ,相关的主反应和副反应列于下面。
气体的恒压热容Cp计算式为:
Cp= a + bT + cT2+ dT3( J / (m ol·K) , 其中a, b,c, d为常数。
查得,同反应体系组分的标准生成焓、标准熵一起列于表3.1。
主反应: (1) 2CH3OH = CH3OCH3+ H2O
(2) 2CH3OH = C2H4+ 2H2O
(3) 3CH3OH = C3H6+ 3H2O
(4) 4CH3OH = C4H8+ 4H2O
副反应:
(5)CH3OH = CO + 2H2
(6) CH3OCH3+ 2H2= 2CH4+ H2O
(7) CO + H2O = CO2+ H2
(8) 2C3H6= C2H4+ C4
(9) C4H8= 2C2H4
(10)CH3OH + C2H4= C3H6+ H2O
(11) CH3OH + C3H6= C4H8+ H2O
(12) C2H4+ H2= C2H6
(13) C3H6+ H2= C3H8
(14) C4H8+ H2= C4H10
(15) C3H8= C2H4+ CH4
(16) C4H10= C3H6+ CH4
表3.1 甲醇制烯烃反应体系组分的热力学数据
在甲醇制烯烃各反应过程中,其等压反应热Qp等于反应的焓变ΔHr,根据Kirhhoff 定律:
反应焓变ΔHr可从定压热容差ΔCp的积分求得。
ΔHr=∫CpdT
△Cp=△a +△bT +△cT2+△dT3
所以:ΔHr=△H0+△aT + (△b /2) T2+ (△c /3) T3+ (△d /4) T4(1)
将T = 298K、由标准摩尔生成焓Δf Hθm算得的反应标准焓变ΔHr(298K)值代入(1)式,可求得积分常数。利用各反应的△a、△b、△c、△d即可得到各反应的焓变与温度的关系式。现以矩阵形式列出反应(1 )~(16)的反应焓变与温度的关系式,见式(2)。
ΔHr( i) ( i为反应编号)为第i反应的反应焓变。通过式(2)可计算各反应在不同反应温度下的反应热。经计算,除了(5)、(8)、(9)、(15)、(16)几个分解反应外,甲醇制烯烃大多数反应,特别是主反应,都为强放热反应,甲醇制烯烃总反应热在37~53 kJ /mo l之间。
所以,在甲醇制烯烃反应过程中,需要不断的移除反应热,以避免反应器内温升过大。另外,考虑到甲醇制烯烃反应所用SAPO - 34分子筛催化剂有失活速率快、需要不断反复再生的特点,显然催化剂连续反应-再生的循环流化床或提升管反应器为甲醇制烯烃反应的首选反应器。
3.2.2甲醇制烯烃反应的吉布斯自由能
甲醇制烯烃反应的吉布斯自由能△GT由式(3 )计算得到:
ΔGT=ΔHr- TΔS ( 3)
其中,ΔHr可按照第1节中的方法求得。
ΔS =∫(ΔCp/ T) dT= I +△a lnT +△bT + (△c /2) T2+ (△d /3) T3(4) 甲醇制烯烃各反应在298K时的△S298值及积分常数I值列于表3.2。将I值代入
式(4)即可得到△S与温度T的关系式,从而得到△GT与温度T的关系。现在以几个不同的反应温度点计算出各反应的吉布斯自由能,从而可直观的看出各反应自发进行的程度,计算结果见表3.3。从表3中可以看出,大多数反应的△GT《0,可以自发进行,并达到较高的程度。
表3.2 甲醇制烯烃各反应的△S298值及其积分常数I值
表3.3甲醇制烯烃各反应的吉布斯自由能与温度的关系
甲醇制烯烃大多数反应为强放热反应,所以,反应过程中需不断移除反应热,以避免反应器温度剧升,导致甲醇结焦加剧和可能的甲醇分解,故及时取热并综合利用反应热十分必要。齐国祯等[5]对甲醇制低碳烯烃反应过程进行了热力学分析,计算了甲醇制烯烃主副反应的反应热、吉布斯自由能、平衡常数以及烯烃产物之间的平衡关系等,发现烯烃产物间的转化受热力学平衡限制,随反应温度增加,丙烯变化规律不同于乙烯和丁烯,可通过选择适当反应温度,使丙烯收率尽量接近平衡态。从化学平衡上分析,
MTO 主副反应均有水蒸汽生成,由于水对副反应具有抑制作用,因此反应物中加入适量水或反应器中引入适量水蒸汽,均可使化学平衡左移,抑制副反应,提高烯烃选择性,减少催化剂结焦,且可将反应热带出系统以使催化剂床层温度稳定;MTO 反应为分子数增加的反应,低压操作对主反应有利。所以,该工艺采取低压操作,使化学平衡右移,提高甲醇单程转化率和低碳烯烃质量收率。甲醇制低碳烯烃反应受热力学影响较小,主要是受动力学控制;若欲提高低碳烯烃的收率,主要需提高催化剂对烯烃的选择性。在甲醇转化反应中,为了提高乙烯选择性,应尽量提高温度,而期望多产丙烯时,应寻找最佳的反应温度。甲醇制低碳烯烃总反应热一般在-34kJ/mol~-22kJ/mol 之间,属于强放热反应。因此,在反应器的设计时,应考虑反应热的及时移出。在甲醇制低碳烯烃反应体系中,为了提高乙烯的含量,应尽量降低反应压力;而对于丙烯含量最大的生产目标,则需要寻找最优操作压力。相对于温度和压力而言,水含量对反应体系平衡组成的影响较小。
3.3反应动力学
MTO 反应动力学从近年MTO 反应动力学研究看,MTO 动力学模型可分为两类:一是采用Single Event 方法,考虑每个可能发生反应的详细动力学模型;二是采用集总方法,基于平行型反应机理的某些简化模型。由于后一种模型形式简单,可方便获得未知动力学参数用于反应器设计,因此得到广泛认可与应用。早期Park 等[7]根据过渡态理论Evans-Polanyi 关联式简化动力学模型参数,结合实验数据,估算出33 个模型参数,并在绝热固定床、等温固定床和流化床反应器进行了模拟计算。BOS 等[8]提出包括积碳的八组分集总动力学,建立包括8 个一级和 4 个二级反应的动力学模型,考虑了积碳对催化剂活性和选择性的影响,可较好的描述实验结果。Gayubo在Bos 的动力学模型基础上,采用外推法获得反应初始的产物组成分布,忽略积碳的影响,但考虑水的影响,并忽略反应较慢的步骤,建立了一个包括含氧反应物、乙烯、丙烯、丁烯、戊烯及链烷烃的五集总动力学模型可较好地描述反应初始时产物分布随催化剂与进料量比值的变化。Chen等在微量振荡天平反应器中对SAPO-34 分子筛进行了MTO 反应动力学研究,将甲烷作为单独集总,建立了包括积碳的八集总动力学模型。齐国祯[6]等以SAPO-34 为催化剂,考虑水和积碳的影响,建立了一个四集总动力学模型,并对乙烯、丙烯、丁烯在任一条件下的反应速率方程进行关联,该动力学模型计算值和实验值拟合较好。
这里主要介绍一下齐国祯等建立的动力学模型。他们在固定床反应器中, 以
SAPO-34 为催化剂, 借助集总动力学的概念, 充分考虑到水和积炭对反应过程的影响, 对MT O 反应的动力学进行了一些研究.
采用建立半经验模型的思想, 对机理模型进行一定的简化和近似. 经热力学计算, 甲醇生成二甲醚的反应平衡常数接近于1, 可以快速达到平衡,因此, 将甲醇和二甲醚看作反应物, 称为含氧反应物( MDOH) ; 甲醇生成烯烃的反应平衡常数远远大于1, 为不可逆反应, 不受化学平衡的限制; 通过甲醇转化率随空时( space time) 的变化关系实验, 证明甲醇在SAPO-34 催化剂上的分解反应对甲醇表现为一级, 所以本文所考虑的反应均为一级反应; 由于SAPO- 34 分子筛催化剂的优良择形催化性能, 乙烷、丙烷等烷烃生成量少, 予以忽略. 简化后的甲醇制烯烃反应路线如下.
通过对催化剂反应活性的考察实验发现, 在考察的实验条件下, 反应时间为0.5 h 内, 催化剂仍然可以保持初始活性.考虑水对低碳烯烃选择性和催化剂活性的显著影响[9]在反应2中加入水的影响因子进行校正.采用系数(1+ aX W)β来衡量水对生成烯烃反应的影响.由于反应进料中氮气/ 甲醇= 3 /1 ( 摩尔比) ,因此由于反应导致的反应总摩尔数变化很小, 在实验允许范围内可以忽略. 采用幂级数动力学方程,根据动力学模型, 得到3 个并行动力学方程表达式
这就构成了一个常微分方程组, 用变步长四阶Runge- Kut t a 法求解. 采用等温积分反应器一维拟均相模型, 忽略径向温度及浓度差异, 在催化剂床层中, 进口处w0= 0, yi, 0= 0 ( i = C1, C O , C5+ )。通过实验数据解得催化剂床层出口各组分浓度后, 以这些浓度的计算值和实验值之差的平方为目标函数, 采用单纯形最优化方法, 使目标函数最小,
对动力学模型进行参数估值.求得的速度方程表达式如下
通过对估值结果进行的决定性指标ρ2检验和 F 检验.得所选模型和参数估值是可靠的,并且通过对实验数据的分析发现,C2= 、C3= 、C4= 烯烃之间的摩尔比值随反应温度的变化呈现有规律的变化, 与空速、水醇比等基本无关.乙烯/ 丙烯随着温度的升高而升高, 丙烯/ 丁烯随着温度的升高而降低.基于以上规律, 采用幂指数拟合上述数据, 得出3 个经验公式, 分别关联了C2=、C3=、C4=烯烃的值, 见式( 7) ~ 式( 9) .
由此可以得到任一条件下rC2=、rC3=、rC4=的反应速率表达式, 见式( 10) ~ 式( 12) , 进而求得反应产物的组成分布.
分别对低碳烯烃的模型计算值和实验值进行了误差比较,该动力学模型的计算值与实验值吻合得较好。
随着反应时间的延长, 由于积炭等因素的影响, 催化剂的活性会逐渐降低. 现考虑催化剂失活的动力学方程形式.记录反应时间为 1.0 h 和 1.5 h 的催化剂失活实验数据, 假设催化剂承受与反应组分浓度无关的 d 级失活, 则
式中a 为活性指数, d 为失活级数, k d为失活速率常数, t 为反应时间.积分式( 13) 得
将式( 1) ~ 式( 3) 分别乘以活性指数a, 采用四阶Runge-Kutta 法和单纯形最优化法对实验数据数据进行回归求解, 得到失活速率常数kd=32.38e-14853/8.1314T、失活级数d= 1.2 及活性指数a 关系式, 最终得到考虑催化剂失活的总动力学方程式
(14)
(15)
分别对低碳烯烃的模型计算值和实验值进行了误差比较,该动力学模型的计算值与实验值吻合得较好.
3.4 MTO工艺条件选择及反应器的选择
3.4.1 MTO工艺条件选择
Wu等[9]使用SAPO - 34分子筛和固定床反应器,对MTO反应中的温度条件进行改变后发现,反应温度对MTO反应中低碳烯烃的选择性、甲醇的转化率和积炭生成速率有着最显著的影响。较高的反应温度有利于产物中n (乙烯)/ n (丙烯)值的提高。但在反应温度高于723 K时,催化剂的积炭速率加速,同时产物中的烷烃含量开始变得显著,最佳的
MTO反应温度在450℃左右。
原料空速对MTO产物中低碳烯烃分布的影响远不如温度显著,这与平行反应机理相符,但过低和过高的原料空速都会降低产物中的低碳烯烃收率[9 ]。此外,较高的空速会加快催化剂表面的积炭生成速率,导致催化剂失活加快,故对于MTO反应,最佳的原料空速应在2.6~3.6 h- 1(WHSV)之间。
Chang等在深入研究了反应压力对MTO反应的影响后发现,改变反应压力可以改变反应途径中烯烃生成和芳构化反应速率。对于这种串联反应,降低压力有助于降低2反应的耦联度,而升高压力则有利于芳烃和积炭的生成。因此通常选择常压作为MTO最佳反应条件。
在反应原料中加入稀释剂,可以起到降低甲醇分压的作用,从而有助于低碳烯烃的生成。在MTO反应中通常采用惰性气体和水蒸气作为稀释剂。水蒸气的引入除了降低甲醇分压之外,还可以起到有效延缓催化剂积炭和失活的效果。Wu等[9]通过实验发现,甲醇中混入摩尔分数20 %的水共同进料,可以得到最佳的MTO反应效果。
3.4.2 MTO反应器开发
流化床反应器比较适用于强烈放热、催化剂易于失活的甲醇制烯烃反应过程。在流化床反应器中工业催化剂除具有良好的活性、产品选择性和稳定性外,还必须满足一定的粒度分布要求并具有良好的流化性能和耐磨性。Keil对固定床和流化床反应器进行了对比分析,认为在甲醇转化制烃类反应中流化床与固定床相比,由于甲醇制烯烃反应属于强放热反应,流化床反应器的传质、传热效果好,升温、降温时温度分布稳定,催化剂可以连续再生,反应器单位产能大,单位投资低。在MTO反应过程中适宜采用流化床反应器形式更具优势。Bos[8] 从反应动力学的角度比较了常见的反应器形式,认为在甲醇制烯烃反应(MTO)中快速循环流化床和湍床是较为适合生产乙烯的反应器。目前MTO流化床技术主要是借鉴工业FCC流化床反应器技术,相关技术还在开发和改进中。湍动流化床作为目前工业上常用的操作方式,由于其气固流动的复杂性和不确定性,相关理论性研究较少,模型化方面亦无统一的认识,致使放大困难。因此利用目前各种先进的检测技术准确测量和把握湍动流化床的气固流动特性是十分有必要的,也是精细的模型化研究所必需的。
参考文献
[1] 徐维正.全球甲醇市场评述[J],国际化工信息,2005,4:6-9.
[2] 李峰,朱铨寿. 甲醇及下游产品[M],北京:化学工业出版社2008
[3] Froment,G F,Dehertog WJH,Marchi A J. Zeolite catalysis in the conversion of methanol
into olefins[J]. Catalysis,1992,9:1-64
[4] Alwahabi S M.Conversion of methaol to light olefins on SAPO-34 kinetic modeling and
reactor design[D]. Texas A &M University, 2003
[5] 齐国祯,谢在库,钟思青,等.甲醇制烯烃(MTO)反应热力学研究[J].石油与天然
气化工,2005,34(5):349-353.
[6]齐国祯,马涛,刘红星,等.甲醇制烯烃反应动力学[J].化工学报,2005,56(12):
2326-2331.
[7] Park T Y,Froment G F.Kinetic modeling of the methanol to olefinsproces.Model
formulation[J].Industrial & Engineering Chemistry Research,2001,40:4172-4186.[8]Bos A N,Tromp PJ J,Akse H N.Conversion of methanol to lower olefins:kinetic
modeling,reactor simulation and selecrion[J].Industrial & EngineeringChemistry
Research.1995,34:3808-3816.
[9]Wu Xianchun , Abraha M G, Anthony R G. Methanol conversion onSAPO-34 :Reaction
condition for fixed-bed reactor[J ] . Applied catalysisA : General :2004 ,260 :63 - 69. [10] 胡浩,叶丽萍,等国外甲醇制烯烃生产工艺与反应器开发现状[J]. 现在化工,
2008,28(1):82-86.
甲醇制芳烃实验报告doc
甲醇制芳烃实验报告 篇一:化工实训实验报告 吉林化工学院化工过程模拟实训报告 题目:甲醇-水精馏分离过程模拟计算 教学院石油化工学院专业班级化工1302班学生学号1310111218学生姓名何迪指导教师刘艳杰 XX 年12月8日 1、软件功能简介 (1)全面的单元操作:包括气/液,气/液/液,固体系统和用户模型。 (2)将工艺模型与真实的装置数据进行拟合,确保精确的和有效的真实装置模型。 (3) 优化功能:确定装置操作条件,最大化任何规定的目标,如收率、能耗、物流纯度和工艺经济条件。 (4) Design Specification 功能: 自动计算操作条件或设备参数,满足指定的性能目标。 2、已知基础数据及分离任务 (1)已知基础数据 F1:35?C ,101kPa,1080 kg/hr的甲醇(52%w)-水(48%w)。F2:20?C ,150kPa,1000kg/hr 的甲醇(40%w)-水(60%w)。F3:25?C ,120kPa,1420kg/hr 的甲醇(60%w)-水(40%w)。精馏塔进料流量:3000 kg/hr,进料温度60?C,压力150kPa。(2)分离任务 塔顶产品甲醇含量不低于99.9%(w),塔底产品水含量
不低于99.9%(w)。甲醇回收率不低于99.1%,水回收率不低于99.5%。 3、流程叙述 将温度为35 ?C,压力为101kPa,流量为1080 kg/hr 的甲醇(52%w)-水(48%w) 与温度为20 ?C,压力为150kPa,流量为1000 kg/hr的甲醇(40%w)-水(60%w)及温度为25 ?C,压力为120kPa,流量为1420kg/hr的甲醇(60%w)-水(40%w)在混合器M0101中混合。将混合后的物料经分流器S0101分流出3000kg/hr由泵P0101打入换热器E0101,在换热器中将物料加热至60 ?C后,进入精馏塔T0101进行甲醇-水混合液的精馏分离,经精馏后塔顶得到99.9%的甲醇,塔釜得到99.9%的水。流程图见图1所示。 图1 甲醇-水分离流程图 4、模拟计算过程的简述 4.1 模拟的全局设置(1)启动ASPEN 双击桌面的aspen软件快捷方式打开aspen。(2)单位制的选择 在新建页面选择General with Metric Units选项 (3)运行类型的确定 运行类型选择 Flowsheet,确认创建aspen文件。 (4)组分的输入 将本组流程命名为学号18,并且Input Data为METCHE,Output Result为METCHE。
年产20万吨乙苯脱氢制苯乙烯装置工艺设计毕业论文设计
(此文档为word格式,下载后您可任意编辑修改!) 毕业设计 20万吨年乙苯脱氢制苯乙烯装置工艺设计 摘要 苯乙烯是最重要的基本有机化工原料之一。本文介绍了国内外苯乙烯的现状及发展概况,苯乙烯反应的工艺条件,乙苯脱氢制苯乙烯催化剂,苯乙烯的生产方法和生产工艺。 本设计以年处理量20万吨乙苯为生产目标,采用乙苯三段催化脱氢制苯乙烯的工艺方法,对整个工段进行工艺设计和设备选型。根据设计任务书的要求对整个工艺流程进行了物料衡算,并利用流程设计模拟软件Aspen Plus对整个工艺流程进行了全流程模拟计算,选用适宜的操作单元模块和热力学方法,建立过程模型进行稳态模拟计算并绘制了带控制点的工艺流程图。在设计过程中对整个工艺流程进行了简化计算,将整个流程分为了反应和精馏分离两个部分,利用计算机模拟计算结果对整个工艺流程进行了模拟优化,并确定了整套装置的主要工艺尺寸。 由于本设计方案使用计算机过程模拟软件Aspen Plus进行仿真设计,减少了实际设计中的大量费用,对现有工艺进行改进及最优综合具有重要的实际意义。 关键词:乙苯,苯乙烯,脱氢,Aspen Plus,模拟优化
Abstract Styrene Monomer(SM)is one of the most important organic chemicals. This article describes the present situation and development of styrene at conditions, catalyst for ethylbenzene dehydrogenation to styrene, styrene production methods and production processes. This design is based on the annual targets, ethylbenzene three-stage dehydrogenation using styrene in the process, the entire section in the process design and equipment selection. According to the requirements of the design of the mission statement of the entire process the material balance, process design simulation software Aspen Plus simulation of the whole process of the entire process, choose the appropriate operating unit module and thermodynamic methods, process model for steady-state simulation and draw the P&ID diagram. The entire process in the design process, simplify the calculation, the whole process is divided into reaction and distillation to separate the two parts, the use of computer simulation results on the entire process flow simulation and optimization, and determine the size of the main process of the entire device . This design using computer simulation software Aspen Plus simulation designed to reduce the substantial costs of the actual design, to improve the existing process and optimal synthesis ,Aspen Plus,Simulation and optimization
乙苯制苯乙烯
南京工业大学 化学化工学院 《化工过程与工艺设计》 设计题目乙苯脱氢制苯乙烯装置工艺设计 学生姓名吴美妍班级、学号化工100704 指导教师姓名林陵 设计时间 2013年 6 月27日-2013 年7月12日 课程设计成绩:
指导教师签字 目录 第一部分设计说明书 前言·······················错误!未定义书签。第一章概述····················错误!未定义书签。 工艺路线与产品················错误!未定义书签。 ···················错误!未定义书签。 ···················错误!未定义书签。 ···················错误!未定义书签。第二章原料与产品的性质··············错误!未定义书签。 原料性质···················错误!未定义书签。 产品性质···················错误!未定义书签。第四章安全和工业卫生···············错误!未定义书签。 第五章三废排放及治理方案·············错误!未定义书签。 第七章主要设备一览表···············错误!未定义书签。 表一非定型设备一览表(一)··········错误!未定义书签。 表二非定型设备一览表(二)·········错误!未定义书签。第八章原料、动力消耗及排出一览表·········错误!未定义书签。 第二部分设计计算书 第一章物料衡算··················错误!未定义书签。 第二章主要设备物料衡算、热量衡算和设备计算····错误!未定义书签。 进料泵····················错误!未定义书签。
煤制甲醇工艺设计
煤制甲醇工艺流程化设计 主反应为:C + O 2 → C O + C O 2 + H 2 → C H 3O 副反应为: 1 造气工段 (1)原料:由于甲醇生产工艺成熟,市场竞争激烈,选用合适的原料就成为项目的关键,以天然气和重油为原料合成工艺简单,投资相对较少,得到大多数国家的青睐,但从我国资源背景看,煤炭储量远大于石油、天然气储量,随着石油资源紧缺、油价上涨,在大力发展煤炭洁净利用技术的形势下,应该优先考虑以煤为原料,所以本设计选用煤作原料。 图1-1 甲醇生产工艺示意图 (2)工艺概述:反应器选择流化床,采用水煤浆气化激冷流程。原料煤通过粉碎制成65%的水煤浆与99.6%的高压氧通过烧嘴进入气化炉进行气化反应,产生的粗煤气主要成分为CO ,CO 2,H 2等。 2423CO H CH H O +?+2492483CO H C H OH H O +?+222CO H CO H O +?+
2 净化工段 由于水煤浆气化工序制得粗煤气的水汽比高达1.4可以直接进行CO变换不需加入其他水蒸气,故先进行部分耐硫变换,将CO转化为CO2,变换气与未变换气汇合进入低温甲醇洗工序,脱除H2S和过量的CO2,最终达到合适的碳氢比,得到合成甲醇的新鲜气。 CO反应式: CO+H O=CO+H 222 3 合成工段 合成工段工艺流程图如图1。 合成反应要点在于合成塔反应温度的控制,另外,一般甲醇合成反应10~15Mpa的高压需要高标准的设备,这一项增加了很大的设备投资,在设计时,选择目前先进的林达均温合成塔,操作压力仅5.2MPa,由于这种管壳式塔的催化剂床层温度平稳均匀,反应的转化率很高。在合成工段充分利用自动化控制方法,实行连锁机制,通过控制壳程的中压蒸汽的压力,能及时有效的掌控反应条件,从而确保合成产品的质量。 合成主反应: CO+2H=CH OH 23 主要副反应: CO+3H=CH OH+H O 2232 4 精馏工段 精馏工段工艺流程图见图2。 合成反应的副产主要为醚、酮和多元醇类,本设计要求产品达质量到国家一级标准,因此对精馏工艺的合理设计关系重大,是该设计的重点工作。设计中选用双塔流程,对各物料的进出量和回流比进行了优化,另外,为了进一步提高精甲醇质量,从主塔回流量中采出低沸点物继续进预塔精馏,这一循环流程能有效的提高甲醇的质量。
乙苯脱氢制苯乙烯
乙苯脱氢制苯乙烯实验指导书 一、实验目的 1、了解以乙苯为原料,氧化铁系为催化剂,在固定床单管反应器中制备苯乙烯的过程。 2、学会稳定工艺操作条件的方法。 3、掌握乙苯脱氢制苯乙烯的转化率、选择性、收率与反应温度的关系;找出最适宜的反应温度区域。 4、了解气相色谱分析方法。 二、实验的综合知识点 完成本实验的测试和数据处理与分析需要综合应用以下知识: (1)《化工热力学》关于反应工艺参数对平衡常数的影响,工艺参数与平衡组成间的关系。 (2)《化学反应工程》关于反应转化率、收率、选择性等概念及其计算、绝热式固定床催化反应器的特点。 (3)《化工工艺学》关于加氢、脱氢反应的一般规律,乙苯脱氢制苯乙烯的基本原理、反应条件选择、工艺流程和反应器等。 (4)《催化剂工程导论》关于工业催化剂的失活原因及再生方法。 (5)《仪器分析》关于气相色谱分析的测试方法。 三、实验原理 1、本实验的主副反应 主反应: 副反应: 在水蒸气存在的条件下,还可能发生下列反应: 此外还有芳烃脱氢缩合及苯乙烯聚合生成焦油和焦等。这些连串副反应的发生不仅使反应的选择性下降,而且极易使催化剂表面结焦进而活性下降。 2、影响本反应的因素 (1)温度的影响 乙苯脱氢反应为吸热反应,?H o >0,从平衡常数与温度的关系式20ln RT H T K p p ?= ???? ????可知,
提高温度可增大平衡常数,从而提高脱氢反应的平衡转化率。但是温度过高副反应增加,使苯乙烯选择性下降,能耗增大,设备材质要求增加,故应控制适宜的反应温度。本实验的反应温度为:540~600℃。 (2)压力的影响 乙苯脱氢为体积增加的反应,从平衡常数与压力的关系式Kp=Kn= γ? ? ? ? ? ? ? ∑i n P 总可知,当?γ> 0时,降低总压P总可使Kn增大,从而增加了反应的平衡转化率,故降低压力有利于平衡向脱氢方向移动。本实验加水蒸气的目的是降低乙苯的分压,以提高乙苯的平衡转化率。较适宜的水蒸气用量为:水﹕乙苯=1.5﹕1(体积比)或8﹕1(摩尔比)。 (3)空速的影响 乙苯脱氢反应系统中有平行副反应和连串副反应,随着接触时间的增加,副反应也增加,苯乙烯的选择性可能下降,故需采用较高的空速,以提高选择性。适宜的空速与催化剂的活性及反应温度有关,本实验乙苯的液空速以0.6h-1为宜。 3、催化剂 本实验采用氧化铁系催化剂,其组成为:Fe2O3-CuO-K2O3-CeO2。 四、预习与思考 1、乙苯脱氢生成苯乙烯反应是吸热还是放热反应?如何判断?如果是吸热反应,则反应温度为多少?实验室是如何来实现的,工业上又是如何来实现的? 2、对本反应而言是体积增大还是减小?加压有利还是减压有利,工业上是如何来实现加减压操作的?本实验采用什么方法?为什么加入水蒸气可以降低烃分压? 3、在本实验中你认为有哪几种液体产物生成?有哪几种气体产物生成?如何分析? 4、进行反应物料衡算,需要—些什么数据?如何搜集并进行处理? 五、实验装置及流程 乙苯脱氢制苯乙烯实验装置及流程见图1。 六、实验步骤及方法 1、反应条件控制 汽化温度300℃,脱氢反应温度540~600℃,水﹕乙苯=1.5﹕1(体积比),相当于乙苯加料0.5mL/min,蒸馏水0.75 mL/min (50毫升催化剂)。 2、操作步骤 (1)了解并熟悉实验装置及流程,搞清物料走向及加料、出料方法。 (2)接通电源,使汽化器、反应器分别逐步升温至预定的温度,同时打开冷却水。 (3)分别校正蒸馏水和乙苯的流量(0.75mL/min和0.5mL/min) (4)当汽化器温度达到300℃后,反应器温度达400℃左右开始加入已校正好流量的蒸馏水。当反应温度升至500℃左右,加入已校正好流量的乙苯,继续升温至540℃使之稳定半小时。 (5)反应开始每隔10~20分钟取一次数据,每个温度至少取两个数据,粗产品从分离器中放入量筒内。然后用分液漏斗分去水层,称出烃层液重量。 (6)取少量烃层液样品,用气相色谱分析其组成,并计算出各组分的百分含量。 (7)反应结束后,停止加乙苯。反应温度维持在500℃左右,继续通水蒸气,进行催化剂的清焦再生,约半小时后停止通水,并降温。
甲醇制乙烯丙烯原理
甲醇制烯烃技术(MTO/MTP) 甲醇制烯烃(Methanol to Olefins,MTO)和甲醇制丙烯(Methanol to Propylene)是两个重要的C1化工新工艺,是指以煤或天然气合成的甲醇为原料,借助类似催化裂化装置的流化床反应形式,生产低碳烯烃的化工技术。 从MTG反应机理分析,低碳烯烃是MTG反应的中间产物,因而MTG工艺的开发成功促进了MTO工艺的开发。国际上的一些知名石化公司,如Mobil、BASF、UOP、Norsk Hydro 等公司都投入巨资进行技术开发。 Mobil公司以该公司开发的ZSM-5催化剂为基础,最早研究甲醇转化为乙烯和其它低碳烯烃的工作,然而,取得突破性进展的是UOP和Norsk Hydro两公司合作开发的以UOP MTO-100为催化剂的UOP/Hydro的MTO工艺。 国内科研机构,如中科院大连化物所、石油大学、中国石化石油化工科学研究院等亦开展了类似工作。其中大连化物所开发的合成气经二甲醚制低碳烯烃的工艺路线(SDTO)具独创性,与传统合成气经甲醇制低碳烯烃的MTO相比较,CO转化率高,达90%以上,建设投资和操作费用节省50%~80%。当采用D0123催化剂时产品以乙烯为主,当使用D0300催化剂是产品以丙烯为主。 一、催化反应机理 MTO及MTG的反应历程主反应为: 2CH3OH→C2H4+2H2O 3CH3OH→C3H6+3H2O 甲醇首先脱水为二甲醚(DME),形成的平衡混合物包括甲醇、二甲醚和水,然后转化为低碳烯烃,低碳烯烃通过氢转移、烷基化和缩聚反应生成烷烃、芳烃、环烷烃和较高级烯烃。甲醇在固体酸催化剂作用下脱水生成二甲醚,其中间体是质子化的表面甲氧基;低碳烯烃转化为烷烃、芳烃、环烷烃和较高级烯烃,其历程为通过带有氢转移反应的典型的正碳离子机理;二甲醚转化为低碳烯烃有多种机理论述,目前还没有统一认识。 Mobil公司最初开发的MTO催化剂为ZSM-5,其乙烯收率仅为5%。改进后的工艺名称MTE,即甲醇转化为乙烯,最初为固定床反应器,后改为流化床反应器,乙烯和丙烯的选择性分别为45%和25%。 UOP开发的以SAPO-34为活性组分的MTO-100催化剂,其乙烯选择性明显优于ZSM-5,使MTO工艺取得突破性进展。其乙烯和丙烯的选择性分别为43%~61.1%和27.4%~41.8%。 从近期国外发表的专利看,MTO研究开发的重点仍是催化剂的改进,以提高低碳烯烃的选择性。将各种金属元素引入SAPO-34骨架上,得到称为MAPSO或ELPSO的分子筛,这是催化剂改型的重要手段之一。金属离子的引入会引起分子筛酸性及孔口大小的变化,孔
甲醇制芳烃技术进展及经济分析
甲醇制芳烃技术进展及经济分析
2014年12月17日(亚化咨询-上海)
目
? 前言 ? 甲醇制芳烃技术进展
录
? 甲醇制芳烃技术经济分析 ? 结束语
前
言
芳烃,特别是轻质芳烃BTX(苯、甲苯、二甲苯) 是重要的基本有机化工材料,其产量与规模仅次 于乙烯和丙烯。其衍生物广泛地应用于化纤、塑 料和橡胶等化工产品和精细化学品的生产中。近 年来,随着石油化工及纺织工业的不断发展,世 界上对芳烃的需求量不断增长。
3
前
言
芳烃主要来源于石油路线。石油芳烃是目前芳 烃最主要的来源。 国内芳烃来源于石油和煤焦油,其中石油生产 的芳烃约占芳烃生产总量的85%以上。 国外通过石油路线生产的芳烃高达芳烃总产量 的98%以上。
前
言
从石油获取芳烃资源主要来自三个方面的 技术:石脑油重整、乙烯裂解汽油加氢抽 提和碳四、碳五芳构化技术。 已经成功工业化的甲醇甲苯甲基化成为制 取BTX的一种新技术路线。
前
言
前
言
国内市场对芳烃的需求量很大,而且增长较快。 由于我国近几年聚酯产业的迅猛发展,芳烃的产 量,尤其是PX产量难以满足国内市场快速增长的 巨大需求。2013年,我国PX表观消费量达到1650 万吨,其中国内产量760万吨,进口量890万吨。 2014年前三季度PX进口约700万吨。
前
言
2013年,我国的进口原油依存度58%,单纯依赖石油资源已 经很难满足日益增长的化工基础原料需求,同时,巨大的 石油资源缺口也已严重威胁到国家的能源安全。 我国化石能源中煤炭资源相对丰富,利用煤炭资源生产 甲醇,继而从煤基甲醇或是海外进口廉价的甲醇为原料制 取芳烃,提高甲醇下游产品的附加值,延长煤化工产业链 ,是一条发展中国特色芳烃产业的新路。
乙苯脱氢制苯乙烯
实验报告 课程名称: 化工专业实验 指导老师: 成绩:__________________ 实验名称: 乙苯脱氢制苯乙烯 实验类型: 同组学生姓名: 一.实验目的 1.了解以乙苯为原料,氧化铁为催化剂,在固定床单管反应器种制备苯乙烯的过程。 2.学会稳定工艺操作条件的方法。 3.掌握乙苯脱氢制苯乙烯的转化率,选择性,收率及反应温度的关系,找出最适宜的反应温度区域。 4.学会使用温度控制和流量控制的一般仪表,仪器。 5.了解气相色谱分析及使用方法。 二.实验原理 1.本实验的主副反应 主反应: 副反应: 在水蒸气存在的条件下,还可能发生下列反应: 此外还有芳烃脱氢缩合及苯乙烯聚合生成焦油和焦等。这些连串副反应的发生不仅使反应的选择性下降,而且极易使催化剂表面结焦进而活性下降。 2.影响本反应的因素 (1)温度的影响
乙苯脱氢反应为吸热反应,?H 0>0,从平衡常数与温度的关系式 可知,提高温度可增大平衡 常数,从而提高脱氢反应的平衡转化率。但是温度过高副反应增加,使苯乙烯选择性下降,能耗增大,设备材质要求增加,故应控制适宜的反应温度。本实验的反应温度为:540~600℃。 (2)压力的影响 乙苯脱氢为体积增加的反应,从平衡常数与压力的关系式Kp =Kn=γ ???? ? ??∑i n P 总可知,当?γ>0时,降低总压P 总可使Kn 增大,从而增加了反应的平衡转化率,故降低压力(高温反应无法采用负压操作,可以通入惰性组分使分压下降)有利于平衡向脱氢方向移动。本实验加水蒸气的目的是降低乙苯的分压,以提高乙苯的平衡转化率。较适宜的水蒸气用量为:水﹕乙苯=1.5﹕1(体积比)或8﹕1(摩尔比)。 (3)空速的影响 乙苯脱氢反应系统中有平行副反应和连串副反应,随着接触时间的增加,副反应也增加,苯乙烯的选择性可能下降,故采用较高的空速,以提高选择性。适宜的空速与催化剂的活性及反应温度有关,本实验乙苯的液空速以0.6h-1为宜。 3.催化剂 本实验采用GS-08催化剂,以Fe ,K 为主要活性组分,添加少量的IA ,IIA ,IB 族以稀土氧化物为助剂。 三.实验装置及流程 乙苯脱氢制苯乙烯实验装置及流程,用Microsoft Visio 软件绘制见下图: 1 34 2 水
实验一 乙苯脱氢制苯乙烯
4.2 实验一 乙苯脱氢制苯乙烯 一 实验目的 (1)了解以乙苯为原料,氧化铁系为催化剂,在固定床单管反应器中制备苯乙烯的过程。 (2)学会稳定工艺操作条件的方法。 二 实验原理 1.本实验的主副反应 主反应: 副反应: 在水蒸气存在的条件下,还可能发生下列反应: 此外还有芳烃脱氢缩合苯乙烯聚合生成焦油和焦等。这些连串副反应的发生不仅使反应的选择性下降,而且极易使催化剂表面结焦进而活性下降。 (1)影响本反应的因素 1)温度的影响 乙苯脱氢反应为吸热反应,00 >?H ,从平衡常数与温度的关系式 20ln RT H T K p p ?=???? ????可知,提高温度可增大平衡常数,从而提高脱氢反应的平衡转化率。但是温度过高副反应增加,使苯乙烯选择性下降,能耗增大,设备材质要求增加,故应控制适宜的反应温度。本实验的反应温度为:540~600℃。 2)压力的影响 乙苯脱氢为体积增加的反应,从平衡常数与压力的关系式n p K K =γ ???? ? ??∑i n P 总 可知,当γ?>时,降低总压总P 可使n K 增大,从而增加了反应的平衡转化率,故降低压力有利于平衡向脱氢方向移动。本实验加水蒸气的目的是降低乙苯的分压,以提高平衡转化率。较适
宜的水蒸气用量为:水∶乙苯=1.5∶1(体积比)或8∶1(摩尔比)。 3)空速的影响 乙苯脱氢反应系统中有平衡副反应和连串副反应,随着接触时间的增加,副反应也增加,苯乙烯的选择性可能下降,适宜的空速与催化剂的活性及反应温度有关,本实验乙苯的液空速以0.6h-1为宜。 (2)催化剂 本实验采用氧化铁系催化剂其组成为:Fe2O3—CuO—K2O3—CeO2。 三预习与思考 (1)乙苯脱氢生成苯乙烯反应是吸热还是放热反应?如何判断?如果是吸热反应,则反应温度为多少?实验室是如何来实现的?工业上又是如何实现的? (2)对本反应而言是体积增大还是减小?加压有利还是减压有利?工业上是如何来实现加减压操作的?本实验采用什么方法?为什么加入水蒸气可以降低烃分压? (3)在本实验中你认为有哪几种液体产物生成?哪几种气体产物生成?如何分析? 四实验装置及流程 见图4.2-1。 五实验步骤及方法 (1)反应条件控制 汽化温度300℃,脱氢反应温度540~600℃,水∶乙苯=1.5∶1(体积比),相当于乙苯加料0.5ml/min,蒸馏水0.75mL/min(50毫升催化剂) (2)操作步骤 1)了解并熟悉实验装置及流程,搞清物料走向及加料、出料方法。 2)接通电源,使汽化器、反应器分别逐步升温至预定的温度,同时打开冷却水。 3)分别校正蒸馏水和乙苯的流量(0.75mL/min和0.5mL/min) 图4.2-1 乙苯脱氢制苯乙烯工艺实验流程图 1—乙苯计量管;2,4—加料泵;3—水计量管;5—混合器;6—汽化器;7—反应器; 8—电热夹套;9,11—冷凝器;10—分离器;12—热电偶 4)当汽化器温度达到300℃后,反应器温度达400℃左右开始加入已校正好流量的蒸馏
乙苯脱氢制取苯乙烯
一、实验目的 1、了解以乙苯为原料,氧化铁系为催化剂,在固定床单管反应器中制备苯乙烯的过程。 2、学会稳定工艺操作条件的方法。 二、实验原理 1、本实验的主副反应 主反应:氢气 ?117.8kJ/mol 苯乙烯 乙苯+ 副反应:乙烯 苯 ?105.0kJ/mol 乙苯+ ? +-31.5kJ/mol 乙苯+ 氢气 苯 乙烷 乙苯+ +-54.4kJ/mol ? 乙烯 甲苯 氢气 在水蒸汽存在的条件下,还可能发生下列反应: + ? 2 + + 氢气 乙苯3 二氧化碳 水 甲苯 此外,还有芳烃脱氢缩合及苯乙烯聚合生成焦油和焦等。这些连串反应的发生不仅使反应的选择性下降,而且极易使催化剂表面结焦进而活性下降。 2、影响反应的因素 (1)温度的影响 乙苯脱氢为吸热反应,提高温度可增大平衡常数,从而提高脱氢反应的平衡转化率。但是温度过高副反应增加,使苯乙烯的选择性下降,能耗增加,设备材质要求增加,故应控制适宜的反应温度。本实验的反应温度为540~600oC。 (2)压力的影响 乙苯脱氢为体积增大的反应,降低总压可使平衡常数增大,从而增加反应的平衡转化率,故降低压力有利于平衡向脱氢方向移动。本实验加水蒸汽的目的是降低乙苯的分压,以提高平衡转化率。较适宜的水蒸汽用量为:水/乙苯=1.5/1(体积比)。 (3)空速的影响
乙苯脱氢反应系统中有平衡副反应和连串副反应,随着接触时间的增加,副反应也增加,苯乙烯的选择性可能下降,适宜的空速与催化剂的活性及反应温度有关,本实验乙苯的液空速以0.6h-1为止。 3、本实验采用氧化铁系催化剂,其组成为:Fe2O3-CuO-K2O3-CeO2。 三、实验装置及流程 实验装置及流程如图1所示。 图1乙苯脱氢制苯乙烯工艺实验流程图 1-乙苯流量计;2、4-加料泵;3-水计量管;5-混合器;6-汽化器;7-反应器;8-电热夹套;9、11-冷凝器;10-分离器;12-热电偶 四、反应条件控制 汽化温度300oC,脱氢反应温度540~600oC,水:乙苯=1.5:1(体积比),相当于乙苯加料0.5ml/min,蒸馏水0.75ml/min(50ml催化剂)。
【清华】甲醇制芳烃
内蒙古庆华集团有限公司 甲醇一步法制芳烃装置的运行情况 摘要: 甲醇一步法制芳烃(汽油)装置,在国内已经实现了工业化,由赛鼎工程有限公司设计的10万吨/年规模装置已于2012年2月16日一次开车成功,开车负荷60%,2012年4月1日满负荷运行,装置开车后运行平稳,截止目前生产芳烃已超过7.5万吨。“芳烃”是指接近于汽油组分的烃类混合物。 交流内容: 甲醇一步法制芳烃(汽油)装置的工艺流程、反应原理及工艺特点、操作要点及指标、运行控制、问题讨论、总结。 前言 由于世界煤炭储藏量远比石油和天然气多,因此,从煤炭出发制合成气--甲醇--烃类的研究曾经在国外70年代就已经开始。例如:Mobil公司曾在1976年发表了Mobil法合成油技术,其总流程是首先以煤或者天然气作原料,生产合成气,再用合成气制甲醇,最后将粗甲醇转化为高辛烷值汽油。1985年,Mobil公司与新西兰合作,在新西兰成功建设了一套日产汽油2000t的工业装置,运行10年。近年来,随着世界原油价格的不断上升,无论是由煤气化--甲醇--烃类,还是天然气转化--甲醇--烃类等工艺,都有非常广阔的发展前景。 国内许多单位也在积极开发和研究由煤炭转化为烃类的工艺,其中,山西晋煤集团引进的莫比尔MTG二步法合成油工艺,就属于煤
炭转化为烃类的范围,该公司10万吨/年规模的甲醇合成油装置已经于2009年6月完成工程建设,并一次开车成功。甲醇一步法制芳烃(汽油)的技术,目前更是受到人们的高度关注。中国科学院山西煤化所和赛鼎工程有限公司合作完成了甲醇一步法制芳烃的工艺包及催化 剂的开发,甲醇一步法制芳烃产品工艺的研究,核心技术是催化剂的研制。相关的后续工艺技术,可以用成熟的技术来匹配。一步法工艺省略了甲醇转化制二甲醚的步骤,工艺流程更简单。目前,10万吨/年规模的装置在国内已经成功运行。 一、工艺流程 甲醇一步法制芳烃(汽油)装置,采用国内技术,装置主要由芳烃合成单元、芳烃分离单元、罐区单元等组成。合成芳烃装置由甲醇蒸发、过热、合成、粗芳烃冷却及分离、催化剂还原等部分组成。芳烃分离装置由气体脱除、液化气分离、产品分离和吸收等部分组成。 大致的工艺流程是:来自罐区的精甲醇首先经预热、蒸发和过热,甲醇蒸气过热后送入合成反应器,反应产生的反应热通过一个完整的热回收体系加以利用。反应器出口产物的热量部分用来副产低压蒸汽,部分在甲醇气化系统内作为热介质,使反应热得到充分利用。从甲醇气化系统来的过热甲醇蒸气和预热的循环气混合后送往两台 正在运行的合成反应器中。合成反应器是绝热固定床反应器,甲醇在此反应器中转化为芳烃、干气和水的混合物,该混合物在粗芳烃分离器中将粗芳烃分离出来,粗芳烃经气体脱除塔,液化气分离塔,产品分离塔,分离出合格的产品---重芳烃、轻芳烃和LPG。
【完整版】10万吨年乙苯脱氢制苯乙烯装置工艺设计与实现可行性方案
10万吨/年乙苯脱氢制苯乙烯装置工艺设计方案 前言 本设计的内容为10万吨/年乙苯脱氢制苯乙烯装置,包括工艺设计,设备设计及平面布置图。
本设计的依据是采用低活性、高选择性催化剂,参照鲁姆斯(Lummus)公司生产苯乙烯的技术,以乙苯脱氢法生产苯乙烯。苯乙烯单体生产工艺技术:深度减压,绝热乙苯脱氢工艺乙苯脱氢反应在绝热式固定床反应器中进行,其特点是:转化率高,可达55%,选择性好,可达90%。特殊的脱氢反应器系统:在低压(深度真空下)下操作以达到最高的乙苯单程转化率和最高的苯乙烯选择性。该系统是由蒸汽过热器、过热蒸汽输送管线和反应产物换热器组成,设计为热联合机械联合装置。整个脱氢系统的压力降小,以维持压缩机入口尽可能高压,同时维持脱氢反应器尽可能低压,从而提高苯乙烯的选择性,同时不损失压缩能和投资费用。 所需要的催化剂用量和反应器体积较小,且催化剂不宜磨损,能在高温高压下操作,内部结构简单,选价便宜。在苯乙烯蒸馏中采用一种专用的不含硫的苯乙烯阻聚剂。它经济有效且能使苯乙烯焦油作为燃料清洁地燃烧。 工业设计的优化和设备的良好设计可使操作无故障,从而可减少生产波动. 本设计装置主要由脱氢反应和精馏两个工序系统所组成。原料来自乙苯生产装置或原料采购部门,循环水、冷冻水、电和蒸汽来由公用工程系统提供,生产出的苯乙烯产品到成品库。 此设计过程中,为了计算方便,忽略了一些计算过程,故有一定的误差,另由于计算时间比较仓促,有些问题不能够直接解决。设计中有不少错误之处,请指导老师予以批评指正,多提出宝贵意见。 苯乙烯设计任务书 一、设计题目:年产10万吨苯乙烯的生产工艺设计
CO2合成甲醇的技术发展综述
CO2合成甲醇的技术发展综述 摘要:介绍了CO2加氢合成甲醇的反应机理和特点,所用催化剂的性质和类型,尚在 研究中的新工艺以及工业应用等情况,综述了该领域的最新研究成果。 关键词:合成甲醇催化剂 CO2 Summarize for Progress in Methanol Synthesis from Carbon Dioxide Abstract: Recent advances on hydrogenation of carbon dioxide to methanol both at home and abroad are reviewed in this paper,and the research works on the direct synthesis of dimethyl ether by hydrogenation of calbon dioxide are also briefly introduced. Key words:Methanol Synthesis ;catalyst ;Carbon Dioxide 1.引言 随着全球人口的增加和人民生活水平的不断提高,对能源的需求日趋强劲。但是传统的石油、天然气资源日渐匮乏,石油短缺已关系到国家的能源安全战略,所以寻求替代能源将成为未来世界经济发展的关键[1-2]。CO2加氢被认为是目前短期间内固定大量排放CO2的既经济又有效的方法之一。为了改善气候条件并解决碳资源问题,需要开发能将CO2转化为有价值材料的技术。鉴于甲醇是重要化工原料和石油补充替代合成燃料,在所考虑的多种选项中通过加氢将CO2转化为甲醇的研究倍受关注[3]。 2.CO2合成甲醇的反应机理 2.1反应机理 CO2加氢合成甲醇的反应机理存在一些尚未解决的问题,一是CO2直接合成还是通过CO 间接合成,二是铜基催化剂的反应活性中心说法不一。随着人们对CO2加氢合成甲醇反应的不断深入研究,愈来愈多的人接受前一种观点,即CO2加氢合成甲醇不须经CO的中间过程,而由CO2直接与H2作用合成甲醇[4]。 2.2反应特点 CO2加氢制甲醇反应方程式如下: : 此反应是分子数减少的放热反应,较高的体系压力和较低的反应温度有利于甲醇的生
煤制芳烃简介
煤制芳烃简介 一、产品市场情况 我国高质量芳烃产品的生产主要来自石油技术路线,由乙烯裂解生产芳烃产品。随着对芳烃需求的日益增长,作为芳烃生产原料的石油资源,面临着越来越严重的短缺局面,已成为制约我国芳烃发展的主要瓶颈之一。 芳烃为大宗基础有机化工原料,目前我国年消费量超过2000万吨。是化纤、工程塑料及高性能塑料等的关键原料,广泛用于服装面料、航空航天、交通运输、装饰装修,电器产品、移动通讯等。 目前芳烃97%以上来源依赖于石油原料,由于受到产能影响,多年来对外依存都接近总需求量的50%。芳烃产品中产能最大、与国民经济密切相关的对二甲苯,2012年的产量是773万吨,表观消费量1382万吨,自给率55.9%。2012年,我国芳烃进口量达609万吨,对外依存度为44%。截止2013年国内PX产能仅896万吨,对外依存度达46%。预测2015PX进口1000万吨,投资空间3000亿元。 同时,中国PX产能增长一直比较缓慢。一些拟建或建成的PX装臵因种种原因未能按计划投产,导致国内PX产不足需矛盾加剧。随着厦门、福州、大连、咸阳等PX项目因当地群众抗议而被迫搁浅。中国PX正遭遇后续项目断档的危机,这为煤制芳烃的成长与发展提供了巨大的空间。 ?页岩气大规模开发,已经将石油化工领域‘三烯三苯’格局打破,将页岩气作为原料生产烯烃,产品大部分是乙烯,丙烯很少,几乎没有芳烃。造成了国际上芳烃价格的上涨。未来十年内芳烃还会处于紧缺状态,5-6年内价格还会上涨。 与芳烃缺口形成鲜明对比的是甲醇的产能过剩。来自氮肥工业协
会统计数据显示,2012年我国甲醇产量为3164万吨,同比增加 19.08%,装臵开工负荷仅61.3%。近年来,我国每年芳烃缺口约为600万至700万吨,如果按1吨芳烃消耗3吨甲醇计算,那么仅用来制芳烃的甲醇就将达到每年2000多万吨。 截止2013底,我国只建成陕西华电榆横煤化工有限公司万吨级中试装臵和内蒙庆华集团10 万吨甲醇制芳烃装臵,国内总产能达11万吨。陕西华电榆横煤制芳烃示范项目于2011年3月正式开工建设,先行建设万吨级煤制芳烃中试装臵,同时启动百万吨级工业示范项目,规模为300万吨煤制甲醇和100万吨芳烃装臵。2012年,万吨级甲醇制芳烃中试试验装臵在陕西榆林煤化工基地建成。2013年1 月13日,第一次投料原料甲醇转化率高于99.99%,油相产物中甲基苯(主要指甲苯、二甲苯和三甲苯)的含量达到90%以上。截止1月15日中午15时,原料甲醇累计进料约100吨,装臵平稳运转54小时,工业试验装臵实现了一次点火成功,一次投料试车成功,打通关键流程。2013年3月18日,该项中试技术通过了国家能源局委托和化学工业联合会组织的科技成果鉴定。中试结果显示,3.07 吨甲醇就可以生产1吨芳烃,并副产大量氢气,工艺废水不含氨氮,废气不含硫氮。2013年3月,由赛鼎公司设计的内蒙庆华集团10 万吨甲醇制芳烃装臵一次试车成功,项目顺利投产。这是赛鼎运用与中科院山西煤化所合作开发的?一种甲醇一步法制取烃类产品的工艺?专利技术设计的我国第一套甲醇制芳烃装臵。 另外,国内煤制芳烃新建拟建项目5个,总产能445万吨,在建产能165万吨。见表1。 表1我国建成和在建煤制芳烃项目万吨 建成项目
二氧化碳转化制备化学品的研究进展
二氧化碳转化制备化学品的研究进展 摘要:二氧化碳是主要的温室气体,同时也是一种廉价、丰富的C1资源,将其转化为高附加值化学品具有重要的意义,而如何实现化学转化是一个极具挑战性的科学问题。基于此,本文简要介绍了CO2转化制备化工产品的现状及其发展前景,以期为其高效转化利用提供基础。 关键词:二氧化碳;化学转化;化学品 二氧化碳是工业燃料燃烧的主要产物之一,也是主要的温室气体,在自然界普遍存在,约占大气的体积分数为0.03%。随着碳排放量逐渐增大以及其给环保带来的巨大压力,CO2的减排已成为人们关注的焦点。 CO2的资源化利用是实现其减排的首要途径。CO2 作为一种廉价、丰富的C1 资源,将其转化为高附加值化学品具有重要意义。一般而言,CO2可转化制备的多种不同的化学品,如甲醇、合成气、低烯烃、醚等等。由于CO2具有很高的标准生成热,结构非常稳定,要实现其在温和条件下的化学转化成为一个极具挑战性的科学问题。因此,有必要对CO2转化为燃料、化工中间体等的研究进展进行介绍,从而为进一步实现CO2的高效转化利用提供基础。 1 CO2转化制甲醇 CO2直接催化加氢制甲醇是一个较经济的反应过程,早在1945年首次报道了Cu-Al催化剂上CO2和H2合成甲醇的研究。在5.15MPa和275 oC下,以Cu-Zn-Al2O3为催化剂进行CO2和H2合成反应,CO2的转化率为16%,甲醇的选择性为28%。近年来,报道了采用溶胶-凝胶技术制备Cu-ZnO-SiO2催化剂,在3.0 MPa、220 oC和6000 h-1的条件下,甲醇的选择性大于90%[1]。尽管目前就CO2的转化率及对应甲醇的选择性提高方面都有了一定的研究进展,但就催化机理方面的认识还非常欠缺,如反应的中间产物、催化活性中心等都不明确,这方面的研究尚处于初级阶段[2]。另外,就催化剂的稳定性和耐毒性问题也需要作进一步深入研究。总体而言,二氧化碳转化制甲醇的方法耗能高、投资大、反应条件较为苛刻(~6 MPa,250~300 oC)。 2 CO2转化制碳酸二甲酯(DMC) 碳酸二甲酯中含有甲基、甲氧基、羰基等官能团,具有较低的毒性,是一种很好的环境友好型产品,在工业化应用中展现出潜在的价值。CO2和甲醇合成DMC反应的平衡常数很小,这样将会使得CO2的平衡转化率也很小。通过设计催化剂可以打破反应的化学平衡限制,从而有助于碳酸二甲酯的生成[3]。目前研究的较多的催化剂有锡/钛的烷氧化物、碱/碱土金属碳酸盐和ZrO2基催化剂等等。就锡/钛基催化剂而言,其催化活性较低;在超临界条件下碱/碱土金属碳酸盐也能够催化该反应,但是对应的DMC产率较低。通过引入添加剂CH3I,可以有效的提高DMC的产率。虽然人们已经开展了一系列的研究工作,但是二
甲醇合成工艺
(一)简介 甲醇是结构最为简单的饱和一元醇,最早由木材和木质素干馏制得,故又称“木醇”或“木精”。甲醇很轻、挥发度高、无色、易燃且有毒。甲醇通常由一氧化碳与氢气反应制得。 甲醇是一种重要的需求量巨大的基本有机化工原料,也是一种新型的清洁能源。在工业发达国家,它是仅次于烯烃和芳烃的基础有机化工原料,其消费量仅次于乙烯、丙烯和苯,居第四位。甲醇应用十分广泛,在石油化工、医药、轻纺、生物化工以及能源交通运输等行业均有广泛用途,在国民经济中占有十分重要的地位。近年来,随着石油资源储量的日趋减少,甲醇应用逐渐扩展到石油补充领域,围绕甲醇产品开发出了烯烃等新的替代石油产品。 (二)甲醇的工业发展史及主要生产技术比较
甲醇的工业生产始于1923年,德国BASF公司首先建成一套以CO和H2为原料,年产300吨的高压法甲醇合成装置,在全世界开拓了以合成气作为一种工业合成原料的生产史。从20世纪20年代到60年代中期,世界各国甲醇合成装置都用高压法,采用锌-铬催化剂。 1966年,英国ICI公司研制成功甲醇低压合成的铜基催化剂,并开发了甲醇低压合成工艺,简称ICI低压法(即Davy法)。1971年,德国Lurgi公司开发了另一种甲醇低压合成工艺,简称Lurgi低压法。此外,丹麦托普索公司、日本三菱瓦斯公司、德国林德公司和美国凯洛格公司等也随后开发了节能型低压生产甲醇工艺技术。 与大型低压法相比,高压法能耗要高很多,因此高压法甲醇工艺已逐步被淘汰。20世纪70年代以后,各国新建与改造的甲醇装置几乎全部采用低压法工艺,主要有Davy、Lurgi、Tops?e等方法,前两种被认为是当今较为先进的甲醇技术,约80%的甲醇装置采用这两种方法生产。 Davy法、Lurgi法和Tops?e法甲醇生产技术比较 Davy法Lurgi法Tops?e法压缩离心式压缩机离心式压缩机离心式压缩机 合成?径向合成反应器 ?压力5~10MPa ?温度230~270℃, 副产蒸汽 ?管壳式合成塔 ?压力5~10MPa ?温度240~260℃, 副产蒸汽 ?三个径向合成塔串联 ?压力5~10MPa ?温度210~290℃, 预热锅炉水 精馏双塔/三塔三塔双塔 规模t/d 最大可到5000 最大可到6700 最大可到7500 (三)我国甲醇工业及技术的发展 我国甲醇工业始于上世纪50年代,在吉林、兰州和太原由原苏联援建了采用高压法锌铬催化剂的甲醇生产装置。60~70年代,上海吴泾化工厂先后自建了以
贵阳二氧化碳制甲醇
我国首套利用合成氨尾气生产液化天然气设备在筑研发、试产成功2009年11月09日 15:07:47 来源:金阳时讯-贵阳日报记者:金卓颖金阳时讯消息截至昨日,我国首套自主研发的、利用合成氨尾气生产液化天然气设备,已在息烽县连续开机运行50多天。这标志着由市公交总公司自主研发的“变废为宝、双向减排、替代能源”项目已研发成功。 图为该项目的原料提供者――开磷集团30万吨合成氨生产线。记者孙鲁荣摄 为推进生态文明城市建设,近年来,市公交总公司大力实施“油改气”工程,目前已完成“油改气”车辆1000余辆,但现有液化天然气(LNG)气源不能完全满足燃料供给。为解决这一问题,该公司结合我市磷煤化工产业发展迅速的实际,与中国航天火箭技术发射中心、中科院大连物化所加强技术合作,共同研发“利用合成氨尾气生产液化天然气”项目。在技术上取得突破后,去年7月,市公交总公司与贵州开磷集团合作,在息烽县投资建设了联产车用液化天然气项目。该项目主要利用开磷集团生产合成氨过程中产生的工业废气作原材料,生产汽车清洁能源液化天然气。
据介绍,目前,联产车用液化天然气项目已完成建设、调试和投料试生产。试生产实现连 续开机50多天,设备运行基本正常。相关测算显示,该项目达产后,每日可利用工业废气生 产33吨液化天然气。按此计算,该项目每年可利用开磷集团排放的1800万立方米合成氨尾气,生产的液化天然气可供600辆公交车使用,并减少车辆排放废气16000立方米,节约燃料成本1200万元,可实现生态效益和经济效益的双赢。 目前,市公交总公司正准备将该项目的关键技术申请国家专利。 贵阳公交总公司综合利用合成氨尾气生产液化天然气(LNG)项目建成投 运 日前,贵阳公交总公司与中国航天火箭技术发射中心、中科 院大连物化所等科研机构合作研发的合成氨(放空气与驰放气) 生产液化天然气项目投料试生产取得成功。 该项目总投资5500万元,其设计能力为5万方/年,即从开磷集团合成氨装置每年产生的大约30万方废气中,提炼生产出5 万方液化甲烷,用作公共汽车动力燃气,从而优化能源结构,改 善大气环境。该项目于2008年7月破土动工,2009年7月建成进入调试,2009年9月15日投料试生产,是我国首套自行研发的利用合成氨尾气生产液化天然气(LNG)设备。该项目的建成,既减