CGMA001-2012车辆渗碳齿轮钢技术条件

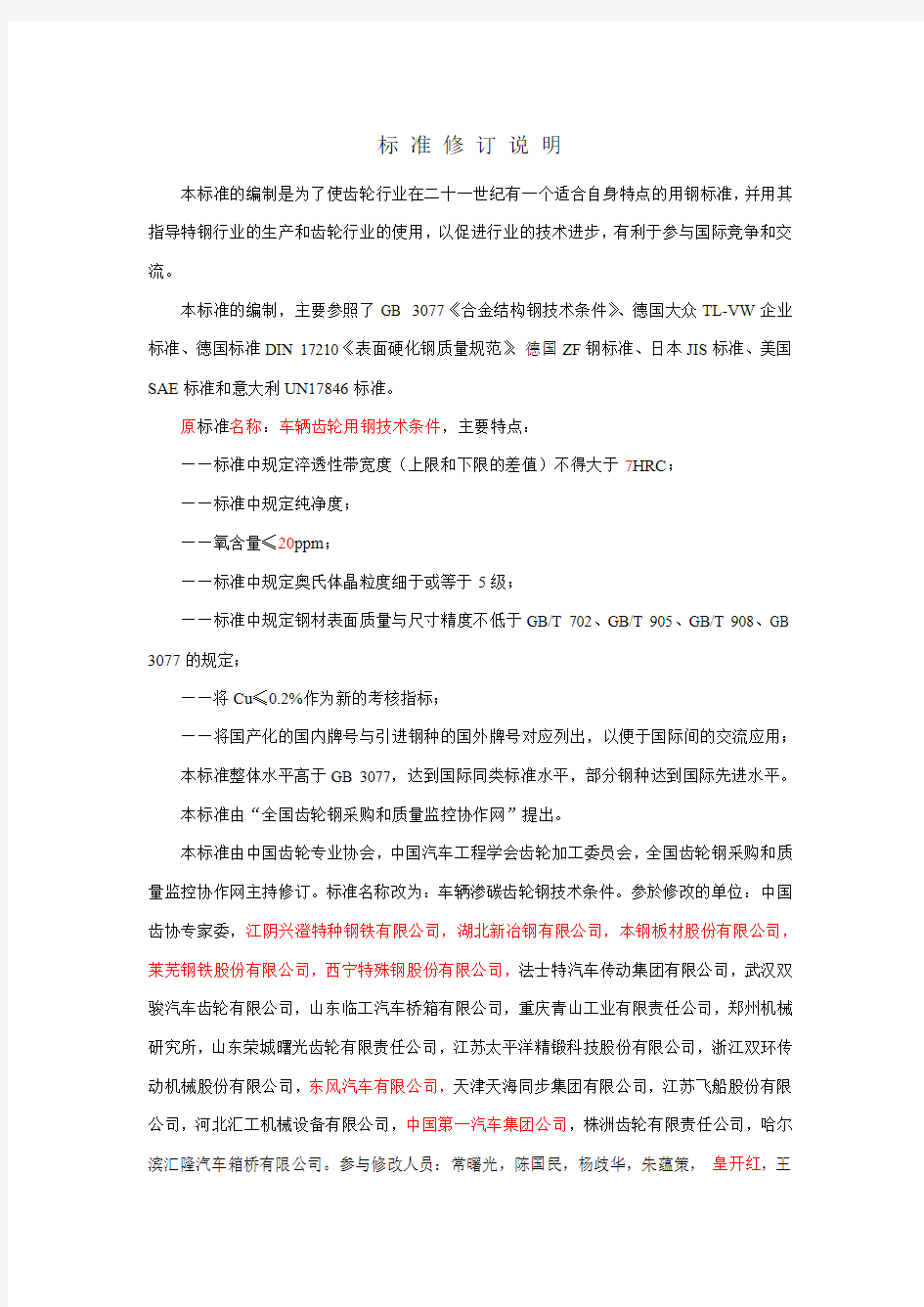
车辆渗碳齿轮钢技术条件 CGMA001-1:2012
中国齿轮专业协会
中国汽车工程学会齿轮加工委员会
标准修订说明
本标准的编制是为了使齿轮行业在二十一世纪有一个适合自身特点的用钢标准,并用其指导特钢行业的生产和齿轮行业的使用,以促进行业的技术进步,有利于参与国际竞争和交流。
本标准的编制,主要参照了GB 3077《合金结构钢技术条件》、德国大众TL-VW企业标准、德国标准DIN 17210《表面硬化钢质量规范》、德国ZF钢标准、日本JIS标准、美国SAE标准和意大利UN17846标准。
原标准名称:车辆齿轮用钢技术条件,主要特点:
——标准中规定淬透性带宽度(上限和下限的差值)不得大于7HRC;
——标准中规定纯净度;
——氧含量≤20ppm;
——标准中规定奥氏体晶粒度细于或等于5级;
——标准中规定钢材表面质量与尺寸精度不低于GB/T 702、GB/T 905、GB/T 908、GB 3077的规定;
——将Cu≤0.2%作为新的考核指标;
——将国产化的国内牌号与引进钢种的国外牌号对应列出,以便于国际间的交流应用;
本标准整体水平高于GB 3077,达到国际同类标准水平,部分钢种达到国际先进水平。
本标准由“全国齿轮钢采购和质量监控协作网”提出。
本标准由中国齿轮专业协会,中国汽车工程学会齿轮加工委员会,全国齿轮钢采购和质量监控协作网主持修订。标准名称改为:车辆渗碳齿轮钢技术条件。参於修改的单位:中国齿协专家委,江阴兴澄特种钢铁有限公司,湖北新冶钢有限公司,本钢板材股份有限公司,莱芜钢铁股份有限公司,西宁特殊钢股份有限公司,法士特汽车传动集团有限公司,武汉双骏汽车齿轮有限公司,山东临工汽车桥箱有限公司,重庆青山工业有限责任公司,郑州机械研究所,山东荣城曙光齿轮有限责任公司,江苏太平洋精锻科技股份有限公司,浙江双环传动机械股份有限公司,东风汽车有限公司,天津天海同步集团有限公司,江苏飞船股份有限公司,河北汇工机械设备有限公司,中国第一汽车集团公司,株洲齿轮有限责任公司,哈尔滨汇隆汽车箱桥有限公司。参与修改人员:常曙光,陈国民,杨歧华,朱蕴策,皇开红,王
春光,许威夷,赵红军,史天振,宋庆东,陈葵,魏有全,李进宝,陆小兵,张茂国,杨钟胜,金荣植,谢飞,曹正,瞿正龙,李博鹏,曹红福,赵千水,王海龙。
针对齿轮热处理变形大,噪声高;渗碳层非马氏体严重,齿轮寿命低,特别是重载驱动桥锥齿轮的保质期与国际先进水平差距过大;对标准进行修订。修订后的标准有如下特点:1.针对重载驱动桥锥齿轮热处理变形大,引入热处理变形小,淬透性高的17Cr2Mn2TiH
钢,用于代替17CrNiMo6H,22CrNiMoH,20CrNi3H,22CrMoH,20CrMnTiH5-6钢。
2.针对齿轮热处理变形大,本标准各钢种的淬透性带宽压窄到宽度(上限和下限的差值)
不得大于6HRC;接近国际先进水平。
3.针对CrMn(Ti),Cr系列齿轮钢抗内氧化能力低,齿根非马氏体严重,降低强力喷丸
效果,将Si含量规定≤0.12。
4.针对各类钢材齿轮表面硬化层缺口敏感度高;针对CrMn(Ti),Cr系列齿轮钢抗内氧
化能力低,齿根非马氏体组织严重;本标准推荐:应采用高碳势稀土-碳共渗工艺。
5.为满足“干切”工艺要求,修改后的标准规定S含量为0.015-0.040,接近国际先进水平。
6.修改后的标准添加了5种有害元素的要求;具有国际先进水平。
其总和As+Sn+Pb+Sb+Bi 应不大于0.045
7修改后的纯净度提高:(1)氧含量≤15ppm,具有国际先进水平(2)夹杂物级别加严。
1 范围
本标准规定了车辆渗碳齿轮用钢的采购通则、技术要求、试验方法、检验规则及包装、标志和质量保证书等。
本标准适用于制造汽车、摩托车齿轮用的热轧圆钢或方钢、锻造圆钢或方钢和冷拉圆钢。
本标准其它行业齿轮用钢亦可参照使用。
2 引用标准
下列文件中的条款通过下列标准的部分的引用而成为本部分的条款。凡是不注明日期的引用文件,其最新版本适用于本部分。
GB/T 222 钢的成品成分允许偏差
GB/T20066 钢和铁化学成份测定用试样的取样和制样方法
GB/T 225 钢的淬透性末端淬火验方法
GB/T 226 钢的低倍组织及缺陷酸蚀检验方法
GB/T 228 金属拉伸试验方法
GB/T 229 金属材料夏比摆锤冲击试验方法
GB/T 230 金属材料洛氏硬度试验
GB/T 231.1 金属布氏硬度试验
GB/T 702 热轧圆钢和方钢尺寸、外形、重量及允许偏差
GB/T 905 冷拉圆钢、方钢、六角钢尺寸、外形、重量及允许偏差
GB/T 908 锻制钢棒尺寸、外形、重量及允许偏差
GB/T 1979 结构钢低倍组织缺陷评级图
GB/T 2101 型钢验收、包装、标志及质量保证书的一般规定
GB/T 2975 钢及钢产品力学性能试验取样位置及试样制备
GB/T 3077 合金结构钢技术条件
GB/T6394 金属平均晶粒度测定法
GB/T4336 碳素钢和中低合金钢的光电发射光谱分析方法
GB/T 6397 金属拉伸试验试样
GB/T 5216 保证淬透性结构钢技术条件
GB/T 10561 钢中非金属夹杂物显微评定方法
GB/T11261 钢铁氧含量的测定-脉冲加热惰气熔融-红外线吸收法
GB/T 13299 钢的显微组织评定法
3 采购通则
3.1 订货内容
按本标准订货的合同或订单一般应包括下列内容:
a)标准编号;
b)产品名称;
c)牌号;
d)交货的质量(数量);
e)规格;
f)加工用途;
g)交货状态;
h)应由需供双方协商,并在合同中注明的项目或指标(如未注明时则由供方选择)。
3.2 特殊订货和附加条款
订货内容由需供双方商定增加或减少,可以增设附加条款。
4 技术要求
4.1 尺寸
4.1.1 钢材的尺寸及其允许偏差
热轧钢材的尺寸及其允许偏差应符合GB/T 702中2组的规定。
锻制钢材的尺寸及其允许偏差应符合GB/T 908中2组的规定。
冷拉钢材的尺寸及其允许偏差应符合GB/T 905中h11组规定。
经双方协商并在合同上注明,亦可按其它级别规定。
4.2 钢材交货长度
热扎钢材交货长度为4000mm-6000mm。
锻制钢材的交货长度为3000mm-6000mm。
冷拉钢材的交货长度为4000mm-6000mm。
经双方协商并在合同上注明,钢材交货长度允许变动。
按定尺或倍尺交货钢材,其长度允许偏差应符合GB/T 702,GB/T 908或GB/T 905的规定。
4.3 外形
4.3.1 钢材的不圆度
钢材的不圆度应符合GB/T 702,GB/T 908或GB/T 905的规定。
4.3.2 钢材的弯曲度
钢材的弯曲度按表1的规定
表1 钢材的变曲度
4.3.3 钢材的扭转
钢材不得有显著扭转
4.3.4 钢材的端头形状
热轧(锻)圆钢端头应锯切或剪切整齐,不得有马蹄形、飞边、毛刺及影响使用的切斜和压扁。
冷拉圆钢的端头不应切弯,用剪断机剪切钢材时,被剪切的一端允许有剪切变形,变形后端头的最大尺寸不得大于公称尺寸加公差值。
根据需方要求,并合同注明,可对热轧(锻)钢材的一端或两端进行倒角,如有具体倒角形状要求应在合同中注明。
4.4 牌号及化学成分
钢的牌号及化学成分(熔炼分析)按表5的规定。
钢材(或坯)的化学成分允许偏差应符合GB/T 222中的规定。
钢材的5种有害元素应符合表2要求:
其总和As+Sn+Pb+Sb+Bi 应不大于0.045
4.5 冶炼方法
电炉或氧气转炉冶炼加真空精炼(或加电渣);采用模铸或连铸生产,钢坯断面应保证钢材的压缩比不小于8.0;对锻造用钢材的钢胚断面应保证压缩比不小于5.0。
4.6 交货状态
钢材的交货状态一般为热轧、锻制和冷拉。
用户若需以退火、正火或剥皮等其他状态交货,应在合同中注明。
4.7 力学性能
钢材的力学性能按表6的规定。
4.8 末端淬透性
钢材的末端淬透性应符合表7的规定。
4.9 低倍组织
酸浸横截面试片上或断口,不允许有肉眼可见的缩孔、气泡、裂纹、夹杂、翻皮、白点及铸态枝晶、酸浸低倍组织按表3规定。
表3 低倍组织
低倍偏析检验时,其方框尖角位置应在1/2半径圆周之内(根据需方要求,可不对此项作出规定)。
切削加工用钢的皮下缺陷深度不得大于公称直径的公差的50%。
4.10 带状组织
带状组织按GB/T 13299检验,CrMo,CrNiMo钢应≤3级,其他钢种带状组织应≤2级。
4.11 非金属夹杂物
钢中非金属夹杂物的测试方法应符合GB/T 10561规定,并按附录A评级图评级,其合格级别应符合表4规定。
对硫含量有上下限要求的钢种,A类夹杂物级别可放宽到小于等于3.0级或者根据需方要求,可按其它标准评定,合格级别可以变动。
注:1 表5中各钢种的氧含量应≤15ppm
2 17Cr2Mn2TiH3,17Cr2Mn2TiH4,20CrMnTiH1钢在末端淬透性检验合格的前提下,允许Cr,Mn元素的熔炼分析值有不大于0.05的偏差。
3 上述表中Si≤0.12的钢种,Si元素的熔炼分析值允许有不大于0.02的偏差。
4 经供需双方协商,表5中不含Ti的钢种,允许含有0.01-0.06的Nb。
注:1.表6中规定热处理温度的允许调整范围:淬火±15℃、高温回火±20℃、低温回火±50℃。2.表6中机械性能除钢材供货状态硬度外,其他供参考。
表7 末端淬透性
带*号标记的数据供参考。
4.12晶粒度:各钢材晶粒度试样的处理及检验方法按表7规定执行。
表8(续)
注:根据需方要求,可以改变试样热处理方法。
4.13 表面质量
压力加工用钢材的表面不得有裂纹、结疤、折叠及夹杂,如有上述缺陷必须消除,消除深度从钢材实际尺寸算起应符合表9规定,消除宽度不小于深度的5倍;同一截面达到的最大深度不大于1处;允许有从实际尺寸算起不超过尺寸公差之半的个别细小划痕、麻点及深度不超过0.2mm的小裂纹存在。
根据需方要求,可对特殊加工用钢材表面质量提出更严格的规定。
4.14 特殊要求
根据需方要求,经供需双方协商,可提出以下要求:
——规定钢材的锻轧比;
——对钢中氢含量作出规定;
——对ZF齿轮钢应进行弯冲值试验;
——交货状态下,其硬度在表6规定之外;
——对钢材检验取样方法作出规定;
——酸洗状态交货;
——加严检验项目的指标;
——需对连铸钢材进行白亮带检测;
——交货状态下,对钢材金相组织作出规定;
——对钢材带状组织级别做出规定;
——对钢材进行塔形检验,对发纹组织级别做出规定;
——其它特殊要求。
5 试验方法
每批钢材的取样部位及试验方法应符合表11规定。
注:有特殊要求时,还应符合供需双方合同书规定。
6 检验规则
6.1 检查和验收
钢材的检查和验收由供方技术质量监督部门进行自检,需方有权按本标准对钢材进行验收或免检。
6.2 组批规则
钢材应成批检查和验收。每批由同一牌号,同一炉号,同一尺寸、同一交货状态或同一热处理方法的钢材组成。
6.3 取样数量
取样数量按表11规定。
6.4 判定规则
在检验项目中,若出现不合格情况(白点除外),可重新双倍取样,对不合格项目进行复验。复验结果中(包括该项试验所要求的全部指标)有任一指标不合格时,则整批判为不合格。对不合格批,供方可以重新进行热处理,合格后可作为新一批的检查和验收,但应将复验合格的钢材另行标识和区分,并告知需方。
需供双方对钢材质量有争议时,由齿轮钢材采购和质量监控协作网的职能机构,按“产品质量仲裁检验”和“产品质量鉴定管理办法”等进行裁定。
7 包装、标志和质量证明书
包装、标志和质量证明书应符合GB/T 2101的有关规定。
钢材捆扎必须牢固,每捆的捆扎不少于3道。
每种炉号批号钢材要有标记,严格区分。
附录
推荐热处理工艺:齿轮的表面硬化工艺,建议采用高碳势稀土-碳共渗工艺。其中,有效硬化层较薄的变速箱,轻型车驱动桥齿轮可采用低温共渗工艺;有效硬化层较厚的重载驱动桥锥齿轮,可采用高温共渗工艺。
浅谈齿轮渗碳淬火有效硬化层及硬度梯度
浅谈齿轮渗碳淬火有效硬化层及硬度梯度 随着机械工业的发展,对齿轮的质量要求日益提高,而齿轮的强度寿命和制造精度与热处理质量有很大关系。为了检验齿轮材料热处理质量,在1987年以前,我国的齿轮渗碳淬火内在质量检验标准多为终态金相检验标准。由于检测仪器的精度、分辨率等因素以及检验人员的经验参差不齐,造成检验结果有很大差异和争议。为了解决金相法内在检验存在的弊端,机械部在1987年借鉴了DIN.ISO等标准中有关内容,修订了我国现行齿轮渗碳淬火内在质量检验标准。此检验标准中,其金相组织检验标准基本与原标准相似,主要是对渗碳层深度及碳浓度梯度的测定作了较大的修改。下面就渗碳层深度和碳浓度梯度分别采用金相法与硬度法测定进行简述。 一、渗碳层深度的检测 1.1、金相法 1.1.1、取本体或与零件材料成分相同,预先热处理状态基本 相似的圆试样或齿形试样进行检测。 1.1.2、送检试样热处理状态为平衡状态,即退火状态。 1.1.3、低碳钢渗层深度为:过共析层+共析层+1/2亚共析层。 1.1.4、低碳合金钢渗层深度为:过共析层+共析层+亚共析层。 1.2、硬度法 1.2.1、取样方法同金相法取样方法一致。 1.2.2、送检试样状态为淬火+回火状态。 1.2.3、渗碳深度用有效硬化层来表示,其极限硬度根据不同要
求进行选择。 1.2.4、有效硬化层深度(DCp):从试样表面测至极限硬度(如 HV550)之间垂直距离。 1.3、两种关于渗碳深度检测的方法存在着一定的对应关系,下面 用图形来描述。 从图中可看出:DCp(芯部)>DCp(HV500)>DCp(HV550) DCp(HV550)对应渗碳层中碳含量约为0.35~0.38%,此界限处即为金相法中1/2亚共析层处。 DCp(HV500)对应渗碳层中碳含量约为0.31~0.33%,此界限处为金相法中1/2亚共析层处。 DCp(芯部)对应渗碳层中碳含量为基体碳含量,一般为0.17~0.23%,此界限处为金相法中基体组织。
渗碳淬火质量验收规范
11111111精密机械有限公司 企业标准 YQB/4003-2016 渗碳淬火质量验收规范 发布时间:2016年 3 月 22 日实施时间:2016年 3 月 22 日11111111精密机械有限公司发布
1、目的 规范自制及委外产品渗淬质量测试的方法和依据,使得渗淬有所依循、保证检测的准确性、稳定性,从而使产品质量得到有效控制,确保本公司向客户提供满意的产品; 2、适用范围 适用于各类自制或委外产品的渗淬质量检控; 3、引用标准 (1) GB/T13299-91 金属显微组织评定方法依据; (2) JB/T 9211-1999 中碳钢与中碳合金结构钢马氏体等级标准; (3) GBT 25744-2010 钢件渗淬回火金相检验标准; (4)GB/T 9450-2005 钢件渗淬硬化层深度的测定和校核依据; (5)GB/T11354-2005 金相组织检验依据; 4、名词解释 (1) 渗淬:渗碳淬火; (2)0收1退:同批次件抽检1件,如合格则整批次接受,不合格整批次退货; (3)试块:渗淬的随炉圆柱形试块,直径25mm*长度50mm,粗糙度Ra3.2; (4)心部硬度:在齿宽中部横截面上,轮齿中心线与齿根圆相交处的硬度; 5、验收项目及标准 渗淬零部件表面硬度、心部硬度、硬化层深、金相组织、表面质量、脱碳层深等; 5.1渗淬件表面质量的检验 1)为得到较为准确的检测结果,零件的检测部位均应进行表面打磨、去掉氧化皮等杂质(成品件或不允许表面打磨的零件检测时,先不进行表面打磨直接在零件不影响外观表面检测。若检测结果不合格时,则须进行破坏性打磨检测,若打磨后检测合格,则判定合格); 2)每一零件原则上应至少检测三次,取其平均值作为评价结果。(第一针为测试针,零件较小或无法取多点除外);
齿轮表面渗碳及渗碳深度
仪器在400倍以上的放大倍数下测量压痕。 测定应在各方约定的位置上,在制备好的试样表面上的两条或更多条硬化线上进行,并绘制出每一条线的硬度分布曲线 二.齿轮固体渗碳工艺 (一)渗碳剂的成份及其作用: 固体渗碳剂主要是由木炭粒和碳酸盐(BaCO3或Na2CO3等组成。木炭粒是主渗剂,碳酸盐是催渗剂。 木炭颗粒均匀,并要求3—6mm左右的占80%,1—3mm左右占20%左右,1mm以下的不大于1%,如果是大零件渗碳,大颗粒木炭应多些,小零件,小颗粒应多些。常用的渗碳剂成份如表1所示。 常用渗碳剂的成份 渗碳加热时,炭与其间隙中的氧作用(不完全燃烧),生成一氧化碳。 2C+O2—→2CO 一氧化碳在渗碳条件下,是不稳定的。活性碳原子被钢件表面吸收,并向内部扩散。整个反反应过程可用下式示意表示:C+CO2—→2CO—→CO2+[C]单独用木炭进行渗碳,周期长,效果差,为了增加渗碳剂的活性,增加活性碳原子数量,一般加入一定数量的碳酸盐作为催渗剂。催渗剂在高温下与木碳产生如下反应:BaCO3+C—→BaO2+CO Na2CO3 + C(木炭) —→ Na2O + 2CO 2CO —→ CO2 + [C]渗碳过程中,木炭受到了烧损,但催渗剂分解氧化物,在开箱冷却时与空气接触,如按下方程式进行还原,这使催渗剂消耗大为减少。BaO+CO2—→BaCO3,Na2O+CO2—→Na2CO3 为了提高催渗剂再生效果,在此介绍一种有效的方法,即将高温下倒出来的渗碳剂,立刻用水喷洒(水的重量是渗碳剂重量的4—5%)。通过这样的处理,碳酸盐可得较完全的再生,其原因是:BaO+CO2—→BaCO3这个过程随温度下降而缓慢,如果在高温下喷水,就能使BaO变成氢氧化钡,而氢氧化钡向碳酸钡转变
齿轮加工标准
齿轮基面辨识方法 1、齿轮基面: 齿轮基面是指齿轮的一侧端面,该端面为齿轮一次装夹后车削端面时,同时车削了齿轮的内孔,即内孔与端面一刀车成的端面。 2、齿轮基面标识 (1)工件重量≤10Kg 的零件(通常此类工件无起吊孔),采用单侧打标记的方法,即在非基面侧端面环槽内刻字,基面侧端面不车90°V型基面线。 (2)工件重量>10Kg 的零件(通常此类工件均有起吊孔),采用基面标识的方法,即在工件基面侧起吊孔中心线处车 90°V型0.5mm 深的基面线(标记圆),非基面侧无标识(不车基面线),但是要在非基面侧端面环槽内刻字。 3、基面辨识方法 (1)通过齿轮基面标识的描述去辨别工件基面。 (2)基面侧的外圈端面是车光面,非基面侧的外圆端面为黑皮面。此方法作为辅助判断,不作为辨识基面的标准。 (3)基面侧不打螺纹孔。 (4)基面侧的外圈端面和内圈端面都有圆跳动位置精度的要求。(圆跳动公差
是被测要素在某一固定参考点绕基准轴线旋转一周(零件和测量仪器件无轴向位移)时,指示器值所允许的最大变动量。符号用“↗”表示。) 4、非基面辨识方法 (1)端面环槽内打标记的面都是非基面。 (2)非基面侧只有内圈端面处有圆跳动位置精度要求。
标准齿轮热前粗车留量标准与定义适用范围:减速机上使用的常规齿轮;其中,薄轮不适用本标准,薄轮为:直径/ 厚度≥8 有键齿轮粗车留量标准 1、内孔尺寸(mm) a)内孔直径=(内孔名义值-2*H)±0.1 b)其中H=CHD+0.4,CHD(或Eht)为图纸所标注热处理渗碳层厚度名义值。 c)内孔留量需根据图纸是否要求热后硬度有关联,如内孔热后不需要硬度, 则热前留量需大于有效渗碳层,如内孔热后需要硬度,则热前留量需调整。 2、内圈端面尺寸(mm) a)内圈厚度=(厚度名义值+2* H)±0.1,两侧均匀留量。 b)其中H=CHD+0.4,CHD(或Eht)为图纸所标注热处理渗碳层厚度名义值。 3、外圈端面尺寸(mm) a)外圈厚度=厚度名义值+0.3~0.5 ,余量留在基面侧;公差执行原图纸公差 要求. 4、内孔倒角 a)内孔倒钝0.2~0.5*45°
齿轮热处理
1 齿轮热处理概述众所周知,齿轮是机械设备中关键的零部件,它广泛的 用于汽车、飞机、坦克、齿轮传动是近代机它具有传动准确、结构紧凑使用寿命长等优点。轮船等工业领域。是机械产品重要器中最常见的一种机械振动是传递机械动力和运动的一种重要形式、基础零件。它与带、链、摩擦、液压等机械相比具有功率范围大,传动效率高、圆周速度高、传动比准确、使用寿命长、尺寸结构小等一系列优点。因此它已成为许多机由于齿轮在工业械产品不可缺少的传 动部件,也是机器中所占比例最大的传动形式。得益于近年来汽车、风电、. 发 展中的突出地位,使齿轮被公认为工业化的一种象征据大规格齿轮加工机床的需求增长十分耀眼。核电行业的拉动,汽车齿轮加工机床、近年来涉及齿轮加工机床制造的企业也日益增随着齿轮加工机床需求的增加,了解,多。无论是传统的汽车、船舶、航空航天、军工等行业,还是近年来新兴的高铁、铁对齿轮加工机床制都对机床工具行业的快速发展提出了紧迫需求,路、电子等行业,万吨。但 我国齿轮的质量年将达到200 2012 造商提出了新的要求。据权威部门预测主要 表现在齿轮的平均使用寿与其他发达国家的同类产品相较还是具有一定的差距,本设计是在课堂学习热处理知识后的探索和单位产品能耗、生产率这几方面上。命、并按重点是制定合理的热处理规程,尝试,其内容讨论如何设计齿轮的热处理工艺,此设计齿轮的热处理方法。齿轮是机械工业中应用最广泛的重要零件之一。其主要作用是传递动力,改变运 动速度和方向。是主要零件。其服役条件如下:齿轮工作时,通过齿面的接触来传递动力。两齿轮在相对运动过程中,既有滚动,(1)在齿根部位受因此,齿轮 表面受到很大的接触疲劳应力和摩擦力的作用。又有滑动。到很大的弯曲应力作用;word 编辑版. ⑵高速齿轮在运转过程中的过载产生振动,承受一定的冲击力或过载;⑶在一些特殊环境下,受介质环境的影响而承受其它特殊的力的作用。因此,齿轮的表面有高的硬度和耐磨性,高接触疲劳强度,有较高的齿根抗弯强度,高的心部 抗冲击能力。齿轮常用材料有。20Cr ,20CrMnTi, 18Cr2Ni4WA①20Cr降温直接淬火对渗碳时有晶粒长大倾向,有较高的强度及淬透性,但韧性较差。可切削性良好,冲击韧性影响较大,因而渗碳后进行二次淬火提高零件心部韧性;20Cr 为珠光体,焊接性较好,焊后一般不需热处理。但退火后较差;②20CrMnTi 20CrMnTi是性能良好的渗碳钢,淬透性较高,经渗碳淬火后具有高的强度和 韧性,特别是具有较高的低温冲击韧性,切削加工性良好,加工变形小,抗疲劳性能好。 ③18Cr2Ni4WA
渗碳淬火质量验收规范
精密机械有限公司 企业标准 YQB/4003-2016 渗碳淬火质量验收规范 发布时间:2016年 3 月 22 日实施时间:2016年 3 月 22 日 精密机械有限公司发布
1、目的 规范自制及委外产品渗淬质量测试的方法和依据,使得渗淬有所依循、保证检测的准确性、稳定性,从而使产品质量得到有效控制,确保本公司向客户提供满意的产品; 2、适用范围 适用于各类自制或委外产品的渗淬质量检控; 3、引用标准 (1) GB/T13299-91 金属显微组织评定方法依据; (2) JB/T 9211-1999 中碳钢与中碳合金结构钢马氏体等级标 准; (3) GBT 25744-2010 钢件渗淬回火金相检验标准; (4)GB/T 9450-2005 钢件渗淬硬化层深度的测定和校核依据; (5)GB/T11354-2005 金相组织检验依据; 4、名词解释 (1) 渗淬:渗碳淬火; (2)0收1退:同批次件抽检1件,如合格则整批次接受,不合格整批次退货; (3)试块:渗淬的随炉圆柱形试块,直径25mm*长度50mm,粗糙度; (4)心部硬度:在齿宽中部横截面上,轮齿中心线与齿根圆相交处的硬度; 5、验收项目及标准
渗淬零部件表面硬度、心部硬度、硬化层深、金相组织、表面质量、脱碳层深等; 渗淬件表面质量的检验 1)为得到较为准确的检测结果,零件的检测部位均应进行表面打磨、去掉氧化皮等杂质(成品件或不允许表面打磨的零件检测时,先不进行表面打磨直接在零件不影响外观表面检测。若检测结果不合格时,则须进行破坏性打磨检测,若打磨后检测合格,则判定合格); 2)每一零件原则上应至少检测三次,取其平均值作为评价结果。(第一针为测试针,零件较小或无法取多点除外); 3)当热处理零件表面产生脱碳现象时,须将零件表面磨深~2mm后再进行检测; 4)渗淬件不允许外观有任何磕碰、锈蚀、尤其是齿面不得磕碰、缺肉;硬化层深度检验 金相法测量硬化层深度 金相检验层深法是指从边界观察其金相直至金相过渡区为界限,使用此种方法检验可以借助金相显微镜,钢件可以借助4%硝酸酒精腐蚀法; 1)显微镜放大倍数为100倍(用带刻度10倍的目镜与10倍的物镜),每小格的尺度为; 2)低碳钢淬火试样要进行正火,磨抛后用4%硝酸酒精浸蚀。渗层总层深=过共析+共析+亚共析的1/2处; 3)低碳合金钢淬火试样要进行等温退火(或渗碳后缓冷试样),磨抛后用4%硝酸酒精浸蚀;
轴承钢的热处理工艺及参数和发展
轴承钢热处理工艺参数 时间:2010-06-14 08:59:46 来源:机械社区作者:
时间:2010-04-19 16:29:25 来源:中国金属加工在线作者:轴承钢是质量要求很严格的钢类。目前对轴承钢提出的要求有:用户免加工和检查、提高质量、规格细化和提高尺寸精度等,而且,对这些要求的重要程度越来越高。为满足这些要求,JFE制钢使用了各种保证产品质量和进行精加工的设备生产轴承钢。这些设备与新开发的提高质量的技术相结合,可以生产尺寸范围宽、质量高、附加值高的热处理和热轧轴承钢。 JFE轴承钢制造技术的特点是: 1)表面质量精细加工和质量检查体系 用对钢坯进行火焰清理和将连铸坯轧制成小型圆坯的方法,均匀去除表面瑕疵、皮下夹杂物和脱碳层。对质量要求特别高的材料,实施钢坯扒皮作业高度清除缺陷。为保证小型圆坯的表面质量,用自动涡流探伤仪和磁粉探伤仪进行检查;对内部缺陷,用圆坯全断面超声波探伤仪检测内部孔隙和夹杂物。 2)轴承钢的精细制造技术和质量保证 在线材-棒材厂,在棒材轧制线上增设线材轧制线,进行联合轧制。对棒材和线材都采用4辊精轧机进行精轧,棒钢的尺寸精度在0.01mm以下,用户可以省略扒皮和拉拔加工。对线材可进行自由尺寸轧制,并可以生产Φ4.2mm的小尺寸线材。由于把线材已经轧制到锻造的尺寸,所以用户可以省略拔丝、热处理和表面处理工序。 3)提高钢的洁净度 近年来,JFE制钢为了提高钢的洁净度,采用了PERM(加减压精炼)、LF(炉外精炼炉)对钢的生产工艺进行了改进。PERM法是在转炉冶炼时,使氮、氢等气体溶解在钢中,然后,用RH炉(真空脱气)迅速减压,使钢中产生气体,利用这种气体捕捉并排除钢液中的夹杂物。 JFE制钢还在2008年新建LF炉,大大提高了夹杂物的去除能力。采用上述工艺和设备的效果是:与原有工艺相比,夹杂物个数预测指数减少34%、夹杂物最大直径指数减少29%、夹杂物最大直径指数分布的标准偏差减少了73%。 由于采用了具有上述特点的制造技术,JFE制钢今后将继续向用户 轴承钢资料 时间:2010-08-17 11:44:25 来源:热加工行业论坛作者:轴承钢全名叫滚动轴承钢,具有高的抗压强度与疲劳极限,高硬度,高耐磨性及一定韧性,淬透性好,对硫和磷控制极严,是一种高级优质钢,可做冷做摸具钢。 比重:7.81 (一)轴承钢锻造温度
齿轮材料热处理规范及其质量要求
齿轮材料热处理规范及其质量要求 正确选择齿轮固然很重要,但如果没有选择好适宜的热处理,那将是前功尽弃,可以说材料选择是前提,热处理方法得当是关键。 一、齿轮热处理方式与其性能特性 1、调质处理: 调质处理使材料获得优良的综合性能,这种热处理常常用于中碳钢和中碳合金钢,如45#、40Cr或40MnB材料,如果齿轮受到的冲击应力和齿面接触应力不是很大的情况下,这种热处理是适宜的,这种材料强韧性使得齿轮齿根抗弯曲能力强,抗疲劳能力也是优良的。但是调质处理齿轮齿面硬度不够,耐磨性偏差。 2、调质处理+表面淬火: 这种热处理方式补充单一调质处理的不足,使齿轮齿面硬度得到提高,耐磨性也随之增强,但是另一个问题仍未解决,就是中碳钢和中碳合金钢材料经过处理后,其冲击韧性尚不能令人满意,在高冲击应力的场合下仍不宜使用。 表面淬火有两种工艺:火焰淬火和高频淬火。 3、正火+渗碳淬火回火 这种热处理是针对低碳合金渗碳钢(如20CrMnTi、20CrNiMo等)而使用的,正火是用以改善原材料组织,便于齿轮粗加工;渗碳使齿面含碳量提高,在其后淬火回火中获得高硬度的回火马氏体组织,以提高齿轮的耐磨性。同时齿轮心部在淬火回火中获得低碳回火马氏体,强度高、韧性好,不仅可以承受高的载荷、大的冲击应力,而且抗疲劳性能也十分优异。 这种热处理也不是没有缺点,首先齿轮在渗碳淬火回火还要精加工,硬度过高会给精加工带来了困难;其次,渗碳淬火回火为了得到回火马氏体,回火温度低(200-300℃),热处理应力未能完全消除,在以后的使用中会逐渐释放造成齿轮微小变形,所以不能用于精密传动的齿轮。 这里的渗碳淬火回火,也包含碳氮共渗淬火回火。 4、调质+渗氮
轴承钢牌号、化学成分及标准对比
调研报告内容: 1、概述(研究目的与意义) 2、该产品研究国内外研究与发展现状(发展过程、现状及发展前景) 3、技术、市场分析(重点介绍) 3.1 国内生产现状 (包括主要生产厂家、各厂家生产该产品采用的生产工艺流程、生产设备、关键技术、生产规格、执行标准或技术条件、产品产量和质量状况、现有及潜在用户、市场占有情况等)(重点介绍) 3.2市场分析 (包括现有和潜在市场容量、产品规格、售价、利润情况、主要品种、主要目标用户及加工工艺、技术质量要求等) (重点介绍) 4、可行性分析 莱钢开发生产该产品的必要性和可行性分析(主要分析莱钢现有装备和工艺条件是否满足、产品利润预测等) 5、其它: 特殊要求品种需要介绍一下钢种定义、性能特点、主要用途、用户个性化要求等)
1、概述(研究目的与意义) 作为合金钢的一种,轴承钢包括高碳铬轴承钢、渗碳轴承钢、高温轴承钢、不锈轴承钢及特殊工况条件下应用的特殊轴承钢。目前,我国轴承钢总产量已达220万t左右,其中高碳铬轴承钢约占轴承钢总产量的90%以上。轴承钢是所有合金钢中质量要求最严格、检验项目最多、生产难度最大的钢种之一,主要用于制造滚动轴承。世界公认轴承钢的生产水平是一个国家冶金水平的标志。对于一个企业来说,轴承钢的生产水平也是一个企业冶金水平的标志,纵观国际及国内的知名特钢生产企业,无一不将轴承钢特别是高标准轴承钢作为其产品调整、发展战略的一个重要目标。我国的一些知名特钢生产企业如:兴澄特钢、东北特钢、上海宝钢特钢生产的轴承钢具有品质高(通过国际知名轴承公司SKF、FAG、Timken 认证),产量大(年产量基本维持在30-50万吨的水平)等特点。 莱钢特钢作为一个老牌特钢生产企业,目前轴承钢生产只能按国内标准生产,档次低、品种单一、产量低(年产量在1万吨左右),与国际、国内的知名特钢生产企业相比差距明显。根据现有装备和生产水平,开发高品质轴承钢,并适当扩大产量不仅对于进一步调整、优化企业产品结构,提高莱钢特钢产品的附加值及经济效益,增强市场竞争能力具有重要意义,而且有利于提升企业的知名度。 2、轴承钢研究国内外研究与发展现状(发展过程、现状及发展前景) 2.1国内外轴承钢钢种系列发展状况 轴承用钢的质量是所有合金钢中要求最严格、检验项目最多的钢种。世界公认轴承钢的水平是一个国家冶金水平的标志。随着科学技术迅猛发展,轴承钢使用条件日益恶劣,对轴承提出了非常苛刻的要求。由于轴承的工作环境、使用条件不同,除了大量生产高碳铬轴承钢外,还发展了渗碳轴承钢、中碳轴承钢、不锈轴承钢、高温轴承钢等系列钢种。 高碳铬轴承钢是轴承钢的代表钢种,各国对之都有专用的技术标准。例如, ISO/FDIS683-17中纳标的高碳铬轴承钢钢种有: 100Cr6、100CrMnSi4-1、100CrMnSi6-4、100CrMnSi6-6、100CrMo7、100CrMo7-3、100CrMo7-4、100CrMnMoSi8-4-6。美国的ASTM A295的高碳铬轴承钢包括:52100、5195、UNSK19526、1070M、5160。此外,美国对高淬透性的高碳铬轴承钢,有专用标准ASTM A485,其包括的钢种有: Grade1~Grade4、100CrMnSi4-4、100CrMnSi6-4、100CrMnSi6-6、100CrMo7、100CrMo7-3、100CrMo7-4、100CrMnMoSi8-4-6。 中国的高碳铬轴承钢(GB/T18254-2002)包括的钢种有: GCr15、GCr15SiMn、GCr4、GCr15SiMo、GCr18Mo。 渗碳轴承钢的表面经渗碳处理后具有高硬度和高耐磨性,而心部仍有良好的
齿轮渗碳淬火变形原因及其控制
齿轮及齿圈渗碳淬火变形原因及其控制的措施 1 引言 齿轮渗碳淬火的变形直接关系到齿轮质量指标。对于渗碳淬火的齿轮,特别是大型齿轮,其变形量很大,且难以控制。较大的变形不仅会使磨齿加工的磨量增加,成本提高,而且影响齿轮制造精度,降低承载能力,最终寿命也会大大下降。齿轮渗碳淬火热处理变形主要是由于工件在机加工时产生的残余应力,热处理过程中产生的热应力和组织应力以及工件自重变形等共同作用而产生的。影响齿轮渗碳淬火变形的因素很多,包括齿轮的几何形状、原材料及冶金质量、锻造和机加工的残余应力、装料方式和热处理工艺及设备等诸方面。掌握变形规律,减少齿轮渗碳淬火变形,能够提高齿轮的承载能力和使用寿命,对缩短制造周期,降低生产成本也都具有重要意义。 2 齿轮渗碳淬火变形规律 对齿轮质量和寿命影响最大的变形来自齿轮外径、公法线长度和螺旋角等。一般说来,变形趋势如下: 2.1 齿轮变形规律:齿轮渗碳淬火后齿顶圆外径呈明显胀大趋势,且上下不均匀呈锥形;径长比越大,外径胀大量越大。碳浓度失控偏高时,齿轮外径呈收缩趋势。 2.2 齿轮轴变形规律:齿顶圆外径呈明显收缩趋势,但一根齿轴的齿宽方向上,中间呈缩小,两端略有胀大。 2.3 齿圈变形规律:大型齿圈经渗碳淬火后,其外径均胀大,齿宽大小不同时,齿宽方向呈锥形或腰鼓形。 3 渗碳淬火变形原因 3.1 渗碳件变形的实质 渗碳的低碳钢,原始相结构是由铁素体和少量珠光体组成,铁素体量约占整个体积的80%。当加热至AC1以上温度时,珠光体转变为奥氏体,900℃铁素体全部转变为奥氏体。910—930℃渗碳时,零件表面奥氏体区碳浓度增加至0.75—1.2%,这部分碳浓度高的奥氏体冷至Ar1以下才开始向珠光体、索氏体转变,而心部区的低碳奥氏体在900℃即开始分解为铁素体,冷至550℃左右全部转变完成。心部奥氏体向铁素体转变是比容增大的过程,表层奥氏体冷却时是热收缩量增加的变化过程。在整个冷却过程中,心部铁素体生成时总是受着表层高碳奥氏体区的压应力。此外,齿轮由于模数大、渗层深,渗碳时间较长,由于自重影响,也会增加变形。 3.2 齿轮渗碳淬火变形的原因 工件淬火时,淬火应力越大,相变越不均匀,比容差越大,则淬火变形越严重。淬火变形还与钢的屈服强度有关,塑性变形抗力越大,其变形程度就越小。 3.3齿圈变形原因 3.3.1齿圈厚薄的影响,淬火冷却时各部位冷却速度的差别而导致组织转变的不同; 3.3.2因装夹等不当及零件自重导致变形; 3.3.3淬火时产生的应力不平衡是变形的主原因。
渗碳层有效层标准修订事项说明2013.3.23
关于《拖拉机渗碳齿轮金相检验》标准修订的说明 一、有关渗碳齿轮金相检验标准 1.意大利菲亚特公司标准: 经过表面渗碳硬化热处理的齿轮零件的机械性能和组织特征检验方法(Q.NL/0025) A.表面硬度HRC58~60 心部硬度HRC33.5~43.5 (检测部位齿根圆) B.层深有效硬化层深(硬度法),测至525HV5处。齿根有效硬化层深应 不小于节圆所示深度的70%。 C.表面非马氏体层深≤0.01mm。 D.金相组织检测6项:碳化物、残余奥氏体、心部铁素体、氧化层、贝氏 体、显微裂纹。 2 . 汽车行业渗碳齿轮检验标准: 1)汽车渗碳齿轮金相标准BR5-74 (参照50-60年代前苏联标准) A.硬度按产品图心部硬度检测部位2/3齿高处 B. 层深渗碳层深法(金相法) C. 表面非马氏体层深无规定。 D.金相组织检测4项:碳化物、残余奥氏体、马氏体、心部铁素体。 2)汽车渗碳齿轮金相检验ZB T04 001-88 A.硬度按产品图心部硬度检测部位齿根圆 B.层深有效硬化层深法测至515HV5或550HV1处。 C. 表面非马氏体层深≤0.02mm。 D. 金相组织检测3项:碳化物、残余奥氏体、马氏体。 3)汽车渗碳齿轮金相检验QC/T262-1999
A.硬度按产品图心部硬度检测部位齿根圆 B.层深有效硬化层深法测至515HV5或550HV1处。 C.表面非马氏体层深按“齿轮材料及热处理质量检验的一般规定”GB 8539 D. 金相组织检测3项:碳化物、残余奥氏体、马氏体。 3.重载渗碳齿轮标准: 重载齿轮渗碳质量检验JB/T6141.2-1992 重载齿轮渗碳金相检验JB/T6141.3-1992 A.表面硬度HRC58~62 心部硬度HRC30~46(检测部位齿根圆) B.层深有效硬化层深法测至550HV1(或HRC 52)处。允许齿根部位的 有效硬化层深度比节圆处小15%。 C.金相组织检测4项:碳化物、残余奥氏体、马氏体、心部铁素体。 4 .拖拉机渗碳齿轮检验标准: 1)拖拉机渗碳齿轮金相检验标准:YTQ310.5-90 A. 硬度按产品图心部硬度检测部位2/3齿高处 B. 层深渗碳层深法(金相法) C. 表面非马氏体层深无规定。 D.金相组织检测3项:碳化物、残余奥氏体、心部铁素体。 2)新修订的拖拉机渗碳齿轮检验标准:Q/YT 310.5-2008 A. 硬度按产品图心部硬度检测部位齿根圆 B. 层深有效硬化层深法,测至515HV5或550HV1处。 C. 表面非马氏体层深≤0.04mm。 D.金相组织检测3项:碳化物、残余奥氏体、心部铁素体。
渗碳齿轮的盐浴淬火
渗碳齿轮的盐浴淬火 【关键词】渗碳齿轮盐浴 【摘要】本文对渗碳齿轮的盐浴淬火技术进行了系统的介绍,对其中的关键问题进行了探讨。【keywords】carburized gear liquid salt 【abstract】In the paper, the technique about the carburized gear quchening in liquid salt is totally introduced, and the key problems of this are discussed. 1 前言 在热处理行业,根据组份和配比,盐浴可用来对工件进行加热,能起到防止工件氧化脱碳的作用,也可用于工件的淬火冷却,如ADI球铁的淬火处理、轴承的贝氏体等温淬火处理等,能够使工件获得优异的性能。 作为渗碳齿轮,其淬火冷却介质最常用的是淬火油,其缺点是淬火时产生油烟,损耗量较大,生产成本高。盐浴作为渗碳齿轮淬火冷却介质在国外(特别是欧美等工业发达国家)于上世纪六十年代就获得应用并推广,该技术于八十年代在国内开始应用,但一直未获得推广。 本文对渗碳齿轮的盐浴淬火技术进行了系统的介绍,对其中的关键问题进行了探讨。 2盐浴淬火技术探讨 2.1盐浴淬火机理 渗碳齿轮典型的盐浴淬火工艺如图1。 图1 渗碳齿轮的盐浴淬火工艺 上述工艺中,盐浴温度设定稍高于材料的Ms点(注:该Ms点指的是齿轮渗碳后表层材料的Ms点),一般在145~170℃之间。表1显示了几种典型齿轮材料的Ms点和盐浴温度。因此,从本质上来讲,渗碳齿轮的盐浴淬火为“盐—空”分级淬火。齿轮加热奥氏体化后,先进行盐浴冷却,心部将在盐浴中发生马氏体转变,而渗碳表层材料的马氏体转变将在空冷时进行。由于空气是缓和的冷却介质,因此采用盐浴淬火会降低齿轮的淬火应力,从而减少齿轮的淬火变形。 表1 典型渗碳齿轮钢的Ms点及盐浴温度
齿轮渗碳淬火工艺培训讲义(1)
齿轮渗碳淬火工艺培训讲义 一、齿轮受力状态及失效形式: 1、受力状态:齿面摩擦力、齿面接触应力和齿根弯曲应力。 2、失效形式: 齿面剥落:表面网状碳化物和渗碳过渡区拉应力是造成齿面剥落的原因。 麻点:齿面金属的塑性变形和齿面的摩擦力导到齿面产生疲劳裂纹,润滑油挤入加速裂纹扩展,由此而产生麻点。 断裂:表现为断齿或断轴,原因为齿轮基体强度不夠。 二、齿轮渗碳淬火通用技术要求: 1、对原材料的要求要: 根据不同使用要求对材料疏松、成份偏析、非金属夹物、带状组织、原始晶粒度和材料淬透性等均有不同级别要求。 2、对预备热处理组织状态和热处理硬度的要求: 包括组织状态、基体硬度、晶粒度等。 3、对最终热处理质量的要求: 包括渗碳淬火表面硬度、渗碳层深度和渗层金相组织、工件基体组织及硬度、强度等。 三、齿轮渗碳淬火工艺规程: 1、渗碳淬火齿轮(低速重载和高速齿轮) 选材: 2、渗碳齿轮工艺流程:锻造---正火---机加工---渗碳淬火---精加工---强力喷丸。
3、齿轮渗碳淬火技术要求: 4、正火热处理:
5、齿轮渗碳工艺: 渗碳淬火工艺曲线 温度 时间 6、使用设备: 可控气氛多用炉。 7、装炉工装及装料方式:详见附图。 (1)使用工装: 工装料架应为抗渗碳、抗热疲劳、高温具有高强度的高Ni-Cr 含量材质的工装。工装结构视工件大小、结构特征而定。工装的结构应保证工件加热、冷却均匀,有利于减小工件淬火变形。 (2)、装料方式: 一般齿轮类工件垂直挂装,套类齿轮多层碼放。工件间应留有一定间隙,以保证不同工件和相同工件不同部位加热和冷却均匀。 滚动件均匀、薄层应平摊于料筛底部,采用多层料筛叠放装料的形式较好。 8、淬火介质及淬火冷却方式: (1)、淬火介质采用德润宝或好富顿淬火油较好。因为这类淬火油蒸气膜持续时间短,蒸气薄且厚度均匀,奥氏体不稳定区冷速较高,有利于避免其产生非马转变;马氏体转变温度下的冷却速度较慢,有利于减小工件淬火应力和淬火变形。 (2)、淬火介质的搅拌强度和循环方向: 选择强力向下搅拌为宜,但最终应根据工件淬火效果确定。
轴承钢与碳钢的优劣势比较
轴承钢与碳钢的优劣势比较 成都昌明仪器公司提供 根据调查分析的研究结果显示,轴承钢与碳钢轴虽然外形区别不大,但实质上它们各自的优缺点是非常的明显的。下面是具体的调查分析结果: 第一,在使用寿命长短方面。它们的使用时间寿命有很大的差异,轴承钢的使用寿命长,许多垃圾轴承都是碳钢轴承,主要是硬度和耐磨性都不如轴承钢轴承。 第二,在耐磨性能方面。低碳钢只在表层渗碳表层淬火,并没有全部淬透。市场上很多低档碳钢轴承根本就淬不硬,耐磨性能极差。 第三,在工艺和使用效果方面。轴承使用效果好坏与使用环境有关,并不是说碳钢轴承不好,这要看用到哪个机械上,因为有些并不需要高档的,用碳钢周轴承就合适了。当然洛钢的要好但造价就高多了,标准轴承钢是Gcr15。 第四,在轴承材料与性能方面。例如轴承的套圈和滚动体一要反复承受高接触压力,另外进行伴随有滑动的滚动接触,同时保持高精度旋转。因此,对轴承的套圈、滚动体及保持架的材料及性能是否达到了以下的要求:弹性极限高;滚动疲劳强度高;要有高硬度;耐磨性好;抗冲击负荷的韧性好;尺寸稳定性好。此外,还要加工性好。经证实,轴承钢具有以上所要求的性能,但是碳钢轴承就不能保证了。第五,并不是说碳钢轴承所具有的优点没有轴承钢的好就无处可用了,这得看用到哪里。碳钢轴承的噪音大,寿命特别短,承受的压力特别小,但可用在硬度、极限转速相对较小的地方。表面强化技术可以从不同的角度形成多种分类方法,按表层强化技术的物理化学过程进行分类,大致可分为五大类:表面变形强化、表面热处理强化、化学热处理强化、表面冶金强化、表面薄膜强化。 1、轴承表面变形强化 通过机械的方法使金属表面层发生塑性变形,从而形成高硬度和高强度的硬化层,这种表面强化方法称为表面变形强化,也称为加工硬化。包括喷丸、喷砂、冷挤压、滚压、冷碾和冲击、爆炸冲击强化等。其多数方法已在轴承工业中得到应用:滚动体的表面撞击强化就是这类方法的应用,精密碾压已成为新的套圈加工和强化方法。 2、轴承表面热处理强化 利用固态相变,通过快速加热的方法对零件的表面层进行淬火处理称为表面热处理,俗称表面淬火。包括火焰加热淬火、高(中)频感应加热淬火、激光加热或电子束加热淬火等。这些方法的特点是:表面局部加热淬火,工件变形小;加热速度快,生产效率高;加热时间短,表面氧化脱碳很轻微。该方法特别是对提高承受一定冲击载荷的大型和特大型轴承零件的耐磨性和疲劳强度效果显著。 3、轴承化学热处理强化 利用某种元素的固态扩散渗入,来改变金属表面层的化学成分,以实现表面强化的方法称为化学热处理强化,也称之为扩散热处理。渗碳轴承钢零件的处理工艺和滚针轴承套的表面渗氮强化处理均属这一类强化方法。
QJ410325-2015 S-20CrMnTiH合金渗碳齿轮钢技术规范
QJ B3100JQAQ(2015)003 QJ410325 上海汽车变速器有限公司 企业标准 QJ410325-2015 S-20CrMnTiH 合金渗碳齿轮钢技术规范 2015-02-28发布 2015-02-29实施 上海汽车变速器有限公司 发 布
QJ410325-2015 前言 本标准是根据GB/T 1.1-2009《标准化工作导则第1部分:标准的结构和编写》的基本规定和格式要求进行制定的。 本标准由上海汽车变速器有限公司提出。 本标准由上海汽车变速器有限公司标准化室归口。 本标准起草单位:上海汽车变速器有限公司技术中心。 本标准主要起草人:马森林。
S-20CrMnTiH合金渗碳齿轮钢技术规范 1 范围 本技术规范按照GB/T 5216,ISO 683,ISO 6336-5等相关材料标准制定,主要适用于可控气氛渗碳或碳氮共渗齿轮类零件。本技术规范适用于直径为25~100mm的热轧钢材。 2 规范性引用文件 下列文件对于本文件的应用是必不可少的。凡是注日期的引用文件,仅所注日期的版本适用于本文件。凡是不注日期的引用文件,其最新版本(包括所有的修改单)适用于本文件。 GB/T 226 钢的低倍组织及缺陷酸浸检验法 GB/T 225 钢的淬透性末端淬火试验方法 GB/T 231.1 金属布氏硬度试验第1部分:试验方法 GB/T 702 热轧圆钢和方钢尺寸、外形、重量及允许偏差 GB/T 1979 结构钢低倍组织缺陷评级图 GB/T 5216 保证淬透性结构钢 GB/T 3077 合金结构钢 GB/T 4162 锻轧钢棒超声波检验方法 GB/T 13299 钢的显微组织评定方法 GB/T 20066 钢和铁化学成分测定用试样的取样和制样方法 GB/T 222 钢的化学分析用试样取样方法及成品化学成分允许偏差 ASTM A534 耐磨轴承用渗碳钢 ASTM E45 钢中非金属夹杂物显微评定方法 ASTM E112 金属平均晶粒度测定方法 3 尺寸、外形、重量及允许偏差 3.1尺寸允许偏差 3.1.1热轧不剥皮材料:尺寸及允许的尺寸偏差按照GB/T 702 I或者II组执行。 3.1.2银亮剥皮材(仅适用于?30~?70mm)的钢棒,则按照下表1执行。
齿轮气体渗碳热处理工艺
我公司齿轮气体渗碳热处理工艺及其质量控制 主要内容与使用范围 本标准结合中国齿轮标准化技术委员会、机械工业部郑州机械研究所起草的《齿轮气体渗碳热处理工艺及其质量控制》,根据我公司齿轮材料及性能所编写的基本符合产品要求的一般规定。 本标准适用于钢制齿轮的气体渗碳、淬火和回火处理。 一、标准篇 1、GB1818金属表面洛氏硬度试验方法 2、GB1979结构钢低倍组织缺陷评级图 3、GB3077合金结构钢技术条件 4、GB5216保证淬透性结构钢技术条件 5、GB6394金属平均晶粒度测定方法 6、GB8539齿轮材料及热处理质量检验的一般规定 7、GB9450钢件渗碳淬火有效硬化层深度的测定与校核 8、GB9452热处理炉有效加热区测定方法 9、GB10561钢中非金属夹杂物显微组织评定法 10、GB/T230金属洛氏硬度试验方法 11、GB/T13299钢的显微组织评定法 12、GB/T225-88钢的末端淬透性试验方法 13、ZB G51 108钢件在吸热式气氛中的热处理 14、ZB J36 012 钢件在吸热式气氛中的热处理 15、ZB T04 001汽车渗碳齿轮金相检验
二、材料篇 1、适合我公司齿轮产品的材料(见表一) (遵循我国齿轮行业车辆齿轮钢采购标准CGMA001-2004钢号淬透能力) 表一 2、齿轮材料的冶金质量 1)化学成分 合金结构钢化学成分应符合GB/T3077-88《合金结构钢技术条件》中的有关规定,保证淬透性结构钢化学成分应符合GB/5216-85《保证淬透性结构钢条件》中的有关规定。检验标准执行GB223。 2)纯净度
钢材氧含量≤20.0×10-6,含氢量为≤5.0×10-6 ,含硫量<0.015%,当有特殊要求时,按双方协议规定。 3)低倍组织 一般疏松≤2级,中心疏松≤2级,偏析≤2.5级。检验标准执行GBl979-80《结构钢低倍组织缺陷评级图》。 4)非金属夹杂物 非金属夹杂物按GB/T10561-89中Ⅸ级标准检验,A≤2,B≤2,C≤1,D≤1。氧化物<3级,硫化物<3级,氧化物+硫化物<5.5级。检验标准执行GB/T10561-89《钢中非金属夹杂物显微评定方法》。 5)带状组织 钢中带状组织≤3级。检验标准执行GB/T13299-91《钢的显微组织评定方法》。 6)晶粒度 经930℃×3h渗碳后空冷,奥氏体晶粒度≥5级。检验标准执行GB6394-86《金属平均晶粒度测定法》。 7)末端淬透性 根据齿轮具体使用要求,按淬透性带订货,同炉钢中最大离散值为4HRC。检验标准执行GB /T225-88《钢的末端淬透性试验方法》。 三、锻件质量控制篇 1、原材料的控制 1)锻件用原材料(含钢锭)应有质量保证书,并符合工艺文件规定的材料牌号、尺寸规格和性能要求。 2)原材料或坯料进厂后需经材料检验部门复检,锻造用的锻材及锻坯,都必须有复检合格单。复检合格的原材料应有复检印记,不合格料应作出明显的标记。 3)合格料、待检料、不合格料应有明显的标记,且应分区存放,严禁混料。 4)合格料的入库、出库必须有严格的管理制度。 2、锻件的检验 1)工序检验 ①每批锻件必须进行“首检三件”制度,检验合格后方可正式投产。生产中严格执行自检、互检和专检。 ②工序检验员应对生产现场进行巡回检查,对锻件加热炉温度的控制、锻造操作情况进行监控,并定期抽检锻件的外行尺寸和表面质量。 ③锻件或坯料经检验合格后,检验员应在工序卡或记录卡上签字后方可转入下道工序。 2)锻件终检 ①模锻件终检应按锻件图及GB12361、GB12362及合同等有关规定进行。 ②自由锻锻件终检应按锻件图及JB4249、JB4385、ZB J32 003.1~003.8、ZB J32 001或合同等有关
与齿轮相关的行业标准
1.[QC汽车标准] 汽车渗碳齿轮金相检验QC/T 262-1999 汽车渗碳齿轮金相检验QC/T 262-1999 中华人民共和国汽车行业标准本标准规定了汽车钢制渗碳齿轮金相组织,渗碳层有效层深层深度的含义及检测方法. 本标准适用于渗碳淬硬层有效深度大于0.3MM的汽车齿轮. 本标准用于齿轮在完成所有热处理工序后的质量检查. 日期:2009-04-13 人气:952 2.[JB机械标准] 液压齿轮泵JB/T 7041-2006 液压齿轮泵JB/T 7041-2006 中华人民共和国机械行业标准本标准规定了液压齿轮泵的基本参数、技术要求、试验方法、检验规则及标志和包装要求。本标准适用于以液压油液或性能相当的其他液体为工作介质的齿轮泵。 日期:2009-04-25 人气:877 3.[JB机械标准] JB-T 9168[1].9切削加工通用工艺守则齿轮加工 JB-T 9168[1].9切削加工通用工艺守则齿轮加工 日期:2007-03-09 人气:800 4.[JB机械标准] 圆柱齿轮减速器JB/T 8853-2001 圆柱齿轮减速器JB/T 8853-2001 Reduction cylindrical gear units 本标准规定了圆柱齿轮减速器(以下简称减速器)的基本参数、型式、尺寸、技术要求、承载能力与选用方法等。本标准规定的减速器适用于冶金、矿山、运输、水泥、建筑、化工、纺织、轻工及能源等.. 日期:2008-12-10 人气:472 5.[JB机械标准] 船用齿轮箱铜基湿式粉末冶金摩擦片产品质量分等(内部使用)JB/T 53344-1999 船用齿轮箱铜基湿式粉末冶金摩擦片产品质量分等(内部使用)JB/T 53344-1999 本标准规定了船用齿轮箱铜基湿式粉末冶金摩擦片(以下简称摩擦片)产品质量等级水平。本标准适用于压制—烧结—机械加工方法和用喷撒法生产的摩擦片产品在质量考核、企业升级和创.. 日期:2007-03-20 人气:362 6.[JB机械标准] 圆柱齿轮减速器加载试验方法JB/T 9050.3-1999 圆柱齿轮减速器加载试验方法JB/T 9050.3-1999 中华人民共和国机械行业标准Load test method of reduction cylindrical gear units 本标准规定了圆柱齿轮减速器加载试验和数据处理的方法,同时也规定了对试验件、测试装置的要求。本标准主要适用于渐开线齿.. 日期:2008-12-15 人气:359 7.[JB机械标准] 工业闭式齿轮的润滑油选用方法JB/T 8831-2001 工业闭式齿轮的润滑油选用方法JB/T 8831-2001 Methods for oil selection of industrial enclosed gears 本标准规定了工业闭式齿轮的润滑油选用方法,包括选择润滑油的种类、黏度以及润滑方式。本标准适用于具有如下齿轮类型的工业闭式齿轮传动的润滑:包括渐.. 日期:2008-12-09 人气:351 8.[JB机械标准] 圆柱齿轮减速器通用技术条件JB/T 9050.1-1999
齿轮标准大全
齿轮标准大全 (精度部分) 1、GB/T 2821-92 齿轮几何要素代号(已作废) (注:已有GB/T 2821-2003 在标准参考资料<十二> 中) 2、GB1356-88 渐开线圆柱齿轮基本齿廓(已作废) (注:已有GB/T 1356-2001 在标准汇编中) 3、GB1357-87 渐开线圆柱齿轮模数(已作废) (注:已有“GB/T 1357-2008 通用机械和重型机械用圆柱齿轮模数”在标准汇编第九部分中) 4、GB1356-88 渐开线圆柱齿轮基本齿廓、GB1357-87 渐开线圆柱齿轮模数编制说明 5、GB10095-88 渐开线圆柱齿轮精度(已作废) 6、GB10095-88 渐开线圆柱齿轮精度编制说明 (注:已有GB/T 10095.1.2-2001 在标准参考资料<九> 中) 7、GB10096-88 齿条精度 8、GB10096-88 齿条精度编制说明 9、GB6443-86 渐开线圆柱齿轮图样上应注明的尺寸数据 10、GB6443-86 渐开线圆柱齿轮图样上应注明的尺寸数据编制说明 11、GB/T13924-94 渐开线圆柱齿轮精度检验规范 12、GB/T13924-94渐开线圆柱齿轮精度检验规范编制说明 (注:已有GB/T 13924-2008 渐开线圆柱齿轮精度检验细则在标准参考资料<九> 中)13、JB/T53441-94 渐开线圆柱齿轮产品质量分等通则(注:标准出版社出版标准汇编中没有)
14、JB/T53441-94渐开线圆柱齿轮产品质量分等通则编制说明
1、GB10085-88 圆柱蜗杆传动基本参数 2、GB10085-88圆柱蜗杆传动基本参数编制说明 3、GB10086-88 圆柱蜗杆传动、蜗轮术语及代号 4、GB10087-88 圆柱蜗杆基本齿廓 5、GB10087-88 圆柱蜗杆基准齿形编制说明 6、GB10088-88 圆柱蜗杆模数和直径 7、GB10088-88 圆柱蜗杆模数和直径编制说明 8、GB10089-88 圆柱蜗杆、蜗轮精度 9、GB10089-88 圆柱蜗杆、蜗轮精度编制说明 10、GB/T12760-91 圆柱蜗杆、蜗轮图样上应注明的尺寸数据