制程检验作业指导书

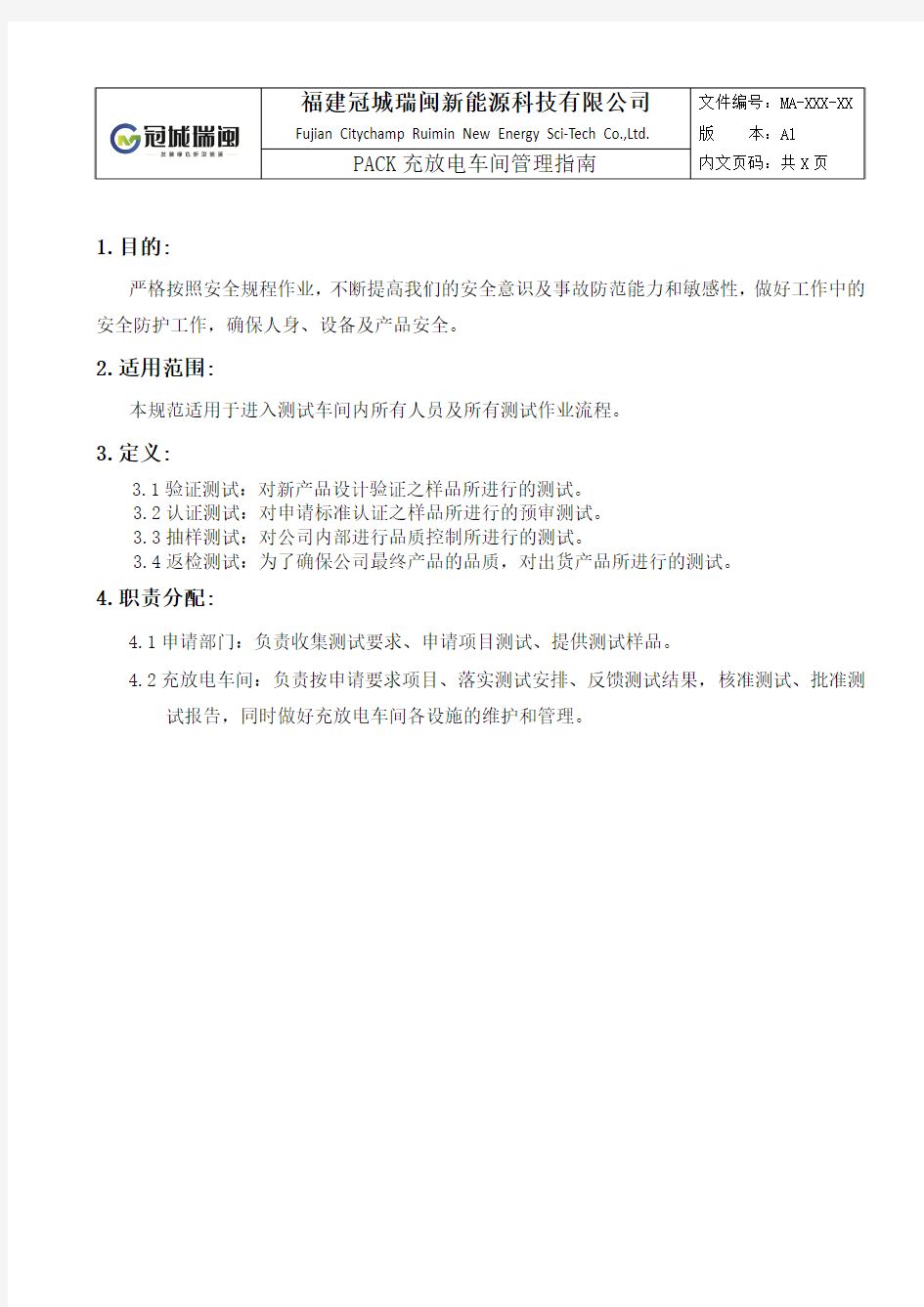
1.目的:
严格按照安全规程作业,不断提高我们的安全意识及事故防范能力和敏感性,做好工作中的安全防护工作,确保人身、设备及产品安全。
2.适用范围:
本规范适用于进入测试车间内所有人员及所有测试作业流程。
3.定义:
3.1验证测试:对新产品设计验证之样品所进行的测试。
3.2认证测试:对申请标准认证之样品所进行的预审测试。
3.3抽样测试:对公司内部进行品质控制所进行的测试。
3.4返检测试:为了确保公司最终产品的品质,对出货产品所进行的测试。
4.职责分配:
4.1申请部门:负责收集测试要求、申请项目测试、提供测试样品。
4.2充放电车间:负责按申请要求项目、落实测试安排、反馈测试结果,核准测试、批准测
试报告,同时做好充放电车间各设施的维护和管理。
5.流程图
6. 程序内容:
6.1 区域管理:现场管理、安全管理、仪器设备管理。
6.1.1现场管理:
6.1.1.1凡进入充放电车间人员须严格遵守管理制度,并服从管理人员安排。
6.1.1.2充放电车间人员应穿着工服、工鞋,测试过程中佩戴安全防护用品。
6.1.1.3请勿携带杂物和佩戴饰品进入车间(如手表、戒指等)。
6.1.1.4车间内不得食用任何食物、饮料(包括白开水)。
6.1.1.5禁止抽烟、打闹、玩手机等与工作无关事宜。
6.1.1.6凡进入车间人员未经许可,禁止私自拍照。
6.1.1.7严格按区域责任制落实5S工作。
6.1.1.8测试过程中产生的“三废”按相关规定妥善处理,不得随意倾倒。
6.1.2安全管理:
6.1.2.1未经培训合格,严禁操作设备。
6.1.2.2安全第一,预防为主;做好防电、防火、防爆、防毒、防潮等工作。
6.1.2.3测试员需严格执行操作规程,测试完毕及下班前必须关闭设备电气开关。
6.1.2.4设备出现故障时,必须先切断电源后方可进行检查。
6.1.2.5火灾发生时应及时采取相应消防措施(消防沙、灭火器)并立即上报。
6.1.2.6盗窃事故发生及时上报处理。
6.1.2.7测试标准、视频、记录、报告等资料不得私自外传。
6.1.3仪器设备管理:
6.1.3.1使用的仪器设备需定期校验及保养。
6.1.3.2报废的仪器、设备按公司仪器设备管理规定执行。
6.1.3.3仪器、设备故障时使用人员应立即按规定上报并及时做好故障记录。
6.1.3.4未经许可仪器设备不得私自外借,外借仪器需要及时登记。
6.2申请测试:需求部门根据产品的实际测试需求(验证测试、认证测试、抽样测试、返检
测试)等填写《测试要求》,在获得需求部门领导签名确认后,将《测试要求》提交充
放电车间负责人批准。
6.3 测试项目评估:根据《测试要求》填写内容评估现有的测试设备能力、条件、方法等是否符合测试的需求,若符合需求,则批准。.
6.3.1若目前条件无法满足测试需求时,必须及时转告送检部门并安排委外测试。委外
测试前,测试车间应对委外的费用、完成时间、测试具体要求咨询检测机构,并
填在测试申请单上。
6.3.2若内外都无法满足该测试,建议终止申请或变更测试标准。充放电车间应阐明意
见,并在《测试要求》签字。
6.4 产品提供:由需求部门提供经初步判断外观、常规电性能测试、控制逻辑合格的样品。
6.5 产品检查评估:检查产品外观、常规电性能是否合格,对所需的样品数量、规格型号、
技术资料和零配件进行全面核对,准确无误后方可接收。
6.6 接收产品:
6.6.1 接收:申请部门送来的产品应存放于指定地点粘贴《标示卡》。
6.6.2 编号:产品一旦接收,测试员需将其记录在《电池系统接收记录表》中,确定
单号,保证送检单号的唯一性,并按阿拉伯数字从小到大依次对样品进行编码。
例如:该批有3个产品,分别编号为1#、2#、3#。
6.6.3 保管:产品测试期间其标示的编码和状态都应保留,在测试尚未结束之前,充
放电车间应妥善保管测试产品,避免丢失或人为损坏。
6.6.4标识:对于合格的样品应贴上合格标签,不合格的应贴上不合格标签并注明问题
点。样品编号后应将产品放置于产品待测区域内,测试后,产品分不良品和良
品放置于“测试完成区”的“不良品区”或“良品区”内。
6.7制定测试方案
6.7.1测试所需的标准按公司或申请方提供的测试标准、作业指导书及申请方提供的技
术资料进行。根据送样的先后顺序、设备利用状况、任务分工以及申请方测试
的紧急状况,制定具体的测试方案。
6.7.2依据具体测试方法分配样品。对于破坏性的试验,应先将电池的常规性能和环境
性能测试完成后再进行相关的破坏性试验。
6.8 实施测试:
6.8.1依据企业测试规范或申请方已指定的测试标准、工艺标准、作业指导书、设备操
作规程等要求对样品实施检测。应随时关注测试过程及结果并做好记录。
6.8.2测试数据的备份方法如下:备份数据的保存路径:电脑D盘+送样部门+送检单号+样品型号/订单编号+送样日期+样品编码+测试员。
6.8.3每周对测试计划的执行情况作一次统计,并将统计结果填写在“周报”中。
6.9 汇总数据:测试结束后,应系统收集、统计各环节的测试结果,并整理成电子文档,文
档需注明“何时的申请部门何项目何种测试”,如“2017年/5月/PACK设计部/BJ17B/
容量测试”。
6.10 编制报告:针对汇总的各测试结果,应进行归纳、判定,并整理成测试报告,经校对
准确无误后打印成纸质档。
6.11审批:测试报告经充放电车间技术负责人批准签字后加盖公章后生效。测试报告一式
两份,一份交申请单位,一份由充放电车间归档保存。
6.12报告归档、签收:
6.12.1测试报告批准后,充放电车间应通知申请部门到充放电车间领取报告并签收。
对于已测试完成后的产品由申请部门领回。
6.12.2测试报告等相关记录的归档:充放电车间每月对该月的所有记录进行归档保存,
并在每类记录的表面加装封面说明记录的类别和保存期限。
7.相关文件:
7.1 电动汽车用动力电池包和系统测试规程、国家标准、企业标准等。
8.相关记录:
8.1 随工单、工艺标准
8.2温湿度记录表
8.3 出货检验记录表报告
8.4 设备维护记录表
8.5 产品接收登记表
8.6 仪器设备借用登记表
LED灯制程巡检作业指导书
LED灯制程巡检作业指导书
LED灯制程巡检指导书 一目的: 规范半成品、成品制程巡检检测项目、方法、频率及标准,确保生产过程符合工艺要求和作业规范,从而保证产品质量符合客户要求;同时通过制程巡检收集生产制程的数据,有效地监控制程的变化,并以此推动制程的持续改善。 二范围: 所有LED应用产品半成品和成品制程; 四权责: 4.1 QE:负责制定制程巡检的作业规范; 4.2检验员:负责按制程巡检作业指导书进行检验; 五内容: 5.1 巡检项目:
5.3.1刷锡检测:每2小时抽检5PCS不能有偏移、歪斜、模糊、漏刷现 象; 5.3.2贴片检测:每2小时抽检5PCS元件有无按用料、贴片是否标准, 有无歪斜、偏移,假焊、漏焊、极性元件反向等现象 5.3.3电阻加工:剪脚长度(1-2mm)套管长度(24-25mm)焊接导线 5.3.4-1剪脚长度检测:检查卡尺使用归零OK,取已剪好脚之元件,用 游标卡尺测量剪脚后留余长度,标准参作业指导书; 5.3.4-2套管长度检测:每2小时抽检5PCS检查卡尺使用归零OK,每2 小时抽检5PCS,用游标卡尺其长度,标准参作业指导书; 5.3.4-3焊接导线;每2小时抽检5PCS,320+10度25W-35W电烙铁、焊 点品质要求;无假焊、漏焊、虚焊、锡点过大、拉尖、少锡; 5.3.4回流焊温度检测:每2小时目测烤箱温控器有无在规格范围内(+-20度); 5.3.5焊正负极:每2小时抽检5PCS,目视检查是否有正负极焊反:
5.3.7-1套管长度检测:每2小时抽检5PCS;检查卡尺使用归零OK, 每2小时抽检5PCS,用游标卡尺其长度,具体操作、标准参作 业指导书; 5.3.8 点亮测试:每批次抽检5PCS,使用调压电源、测试箱具体操作、 标准参照作业指导书; 5.3.9后焊组检测方法: 5.3.9-1装反光罩:每2小时抽检5PCS;反光罩表面要光滑整洁无破损、沾胶、倾斜、破损、异物等不良; 5.3.9-2烙铁温度检测:每班(上午上班、下午上班、晚上加班)对 烙铁温度,用温度计进行检测,标准320+-20度,准参照作业指 导书; 5.3.9-3焊点外观检测:每2小时抽检5PCS检验其手工焊接部位, 焊点品质要求,无短路、假焊、漏焊、虚焊、锡渣、锡珠、拉尖、 残留助焊剂;焊点要光滑; 5.4半成品检测方法: 5.4.1散热座外观检测方法:每2小时抽检5PCS取产线已检查OK之 散热座,确认其无杂物、划痕、碰伤、缺料色差、黑点等外观不 良;尺寸按图纸要求检验; 5.4.2点胶量(散热硅脂):每2小时抽检5PCS确认其散热硅脂,在使 用保质期范围内;目视其涂抹在散热座内表面的胶量、位置均匀, 适当,铝板外表面无残余脂类; 5.4.3测扭力:每2小时检测一次电批的扭力,无滑牙、漏锁、锁爆等 不良:扭力计; 5.4.4压灯头:每2小时抽检5PCS,品质要求:无压偏、变形、生锈、 压不到位等不良现象 5.4.5功能测试:取产线作业员已测试OK之半成品,进行外观,功能 等检验,参数标准参照当天生产产品作业指导书; 5.4.6老化巡查:每2小时巡查一次,检查老化记录表是否有按要求记 录上下架时间和数量,老化时间不能低于14小时,确认有无不亮、 死灯、色差、延时、灯衰等不良现象,发现不良第一时间开出品 质异常维修单交技术分析,并跟进回复处理结果;
IPQC检验作业指导书
制程控制检验作业指导书 1.目的: 为检验员提供检验规则和检验方法,指导其正确检验从而稳定产品质量。 2.适用范围: 适用于本公司产品制程检验的控制。 3.职责: 品质部:负责产品制作过程中质量的监控及不合格原因的分析,并跟踪责任部门改善对策的实施效果。 4.检验流程: 4.1定义: 新产品首样检验:新开发试制产品的首样检验。 首样检验:常规产品在开机后或模具、工装、设备调整后的首件检验。 4.3检验工具: 检验员根据相关《检验作业指导书》选择便于准确测量的检验工具。 注:所有检测工具精度必须等于或高于被检测产品的要求精度。 4.4首样检验: 4.4.1操作者参照图纸、工艺文件对产品进行自检,并在流程卡自检栏上签名确认,检验合格后,送IPQC检验。并在生产过程中不定期的抽检。当发现不良品时,对其标识隔离后,立即报告检验员与现场主管。 4.4.2新产品首次制作、新模具首次生产及工艺更改后的首样产品,检验员将检验的结果填写于《首件检验报表》中,提交技术部跟单人员及QE确认。 4..4.3常规产品开机后的首样或模具、工装、设备调整后的首件产品,检验员根据图纸、工艺文件及检验作业指导书的相关要求对产品进行首样检验。检验结果记录于《首件检验报表》中,在备注栏中注明“首样”及首样状态(新开机、模具维修、工装调整、设备调整)。只有首样加工合格后的产品才能进行批量性生产。首样加工不合格时通知操作人员进行调整,重新送样。直至首样加工合格后才能批量性生产。
4.5巡回检验: 4.5.1首件检验合格后的批量生产,IPQC对生产的各个工位进行巡检,巡检的频率为1次/小时。抽检2-3个加工尺寸或其他项目, 并记录在<<制程巡检\终检报告>>中.巡检结果记录于《制程巡检、终检报告》中。巡检过程中,对产品的性能及尺寸、外观进行检验。NC冲工序在巡检时加工尺寸可用“首件样板”比对检验。巡检的目的是监控生产过程处于稳定的、符合客户要求的状态下批量生产。 4.5.2当某一工序加工完毕后转序时,IPQC检验人员对该批产品的重要尺寸、性能、外观按照GB2828-87中正常检查一次抽样方案Ⅱ进行检验,并从样品中任意提取3-5PCS产品检测数椐做为记录.严重缺陷:AQL值为0.65, 轻微缺陷:AQL值为2.5。各工序的的转序检验均盖上质检员的“合格”或“不合格”盖章。抽检中发现该工序批不合格时,在《半成品工序转移单》中注明,通知操作人员筛选、返修。 4.5.3巡检过程中,检验员对可能影响产品质量的各个环节进行监控(包括材料、工装模具、人员的技能、熟练程度、加工的方法、设备精度与稳定性、现场环境、物料摆放、产品的标识等)。发现有对质量构成隐患的因素时,在《制程巡检、终检报告》中记录,并报告现场生产主管、部门主管。 4.5.4巡检过程中发现不良品时,用红色不良品标签在不合格品外表面或外包装的醒目位置进行标识,必要时用红色箭头标签指明缺陷位置。并将不良品放置于不良品区内。对正在加工的产品仍存在有不合格的隐患时,通知操作者停止生产,并与操作者、现场主管对不良品产生的原因进行分析。生产部门及时的对不良品进行返修,并采取针对性的纠正和预防措施。当产品材料错误或不良率高于公司规定允许的不良率时,检验人员依照检验结果填写《不合格品处理单》交品质部。由品质部根据描述的缺陷分析不良品产生的原因与责任部门。 4.5.5品质部检验人员在《不合格品处理单》效果确认栏中对责任部门改善对策的实施与效果进行跟踪验证,并加以记录。 4.5.6 不合格品返修后必须重新报检确认,若确认不合格必须重新再返修,直至返修合格为止。 5.检验记录 5.1《首件检验报告》《制程巡检、终检报告》 5.1.1检验员在巡检中要及时把巡检结果记录在《制程巡检、终检报告》中,能从《制程巡检、终检报告》中能真实的反映检验员的工作情况及当时产品的质量情况。
制程检验规范99120
适用于公司生产制程品管检验控制。 3.定义 3.1 首件:指生产制程中加工生产的产品,经自我确认、判定符合要求后,拟进行批量生产前的1-3台(个) 产品(半成品、成品)。 3.2全检:对制程中的产品或产品的某些检验项目进行100%检验。 3.3巡检:指对生产过程中影响产品品质的因素进行随机抽样检验、确认。 4.职责 4.1品管部 4.1.1 负责制程中产品外观、检验流程、检验标准、检验规范、检验站的编制和设置. 4.1.2 IPQC:负责对产品、物料首件确认的主导工作,并对产品首件做出合格与否的判定;制程品质检控, 品质异常之追踪与确认;主导不合格品或异常品管问题的提出、跟进、落实、效果确认。 4.1.3 FQC:负责制程中产品外观、产品指定项目的全检。 4.1.4 测试员:负责制程中产品接地、耐压、点亮的全检 4.2工程部 4.2.1 参与新产品、试产、设计变更首件的确认,负责制程中产品电气、结构、功能、测试标准,品质异 常、不合格品原因的分析及改善对策的提出。 4.2.2 负责制程中产品SOP的制定,工装夹具制作,工艺跟进改善,产能效率的提升,结构性能异常的跟 进与落实。 4.2.3 负责制程中仪器、设备测试规范的制定;机器、设备、仪器、仪表、治夹具、工具运行状况的监控, 设备的正常运转的巡视及日常保养工作监管。 4.3 业务部:参与新客户第一次生产及客户要求变更后首次生产时首件的确认。 4.4 生产部 4.4.1 负责首件的制作与送样确认,自验互检。 4.4.2 制程中5M1E 的落实及制造过程的监控,配合IPQC与PIE的工作;品质异常的受理与改善,改善对 策的具体实施. 5.作业内容 5.1生产、检验前作业准备 5.1.1生产部门 5.1.1.1生产部门在开拉生产前进行自我核查,发现不合格品及异常,采取措施立即纠正,再行生产。 5.1.1.2 生产部门开拉生产前需查核领用物料是否与制令工单相符,是否有相应的BOM、或样品,工作环 境是否符合产品生产需求,各作业工站是否悬挂相应的SOP,人员对作业方法、产品品质是否清 楚了解。【首件确认报告】、【耐压/极性测试记录表】 5.1.1.3 机器、设备、作业工具是否处于正常状态,风批、电批扭力设置是否正确符合作业需求。 5.1.2品管部门
产品巡检检验作业指导书
1.0 目的: 为规范成品制程巡检检测的项目、方法、频次、标准、不合格的处理.从而保证产品质量符合客户要求,同时通过制程巡检收集生产制程的原始记录,有效的监控制程的变化,并以此保证和推动制程的持续改善。 2.0 适用范围: 适用于本公司内所有规格产品制程的控制。 3.0 定义: 3.1 IPQC:即生产过程品质控制,是指产品从物料投入生产到产品最终包装过程的品质控制; 3.2批量不良——某一时段出现的品质不良均属于同一种现象。 3.3 RoHS: Restriction of the Use of Certain Hazardous Substances in Electrical and Electronic Equipment(电子电气设备中限制使用某些有害物质指令); 3.4 致命缺陷(以CR表示):影响质量安全的所有缺陷,影响难以纠正的非正常的情况,会影响 寿命的,会造成产品故障的或造成产品使用困难的或造成下道工序混乱的缺陷都称为致命缺陷。 如:混料、假焊、虚焊、焊点小、拉力不够,B部纵向划伤、尺寸超标,A部尺寸超标,CP线露铜、尺寸超标,T部厚度超标等。 3.5 严重缺点(以MA表示):可能造成产品损坏,功能异常或因材料而影响产品使用寿命的缺点。 如:焊点毛刺、炸焊枪、偏焊、半焊、斜接、焊点大,B部夹伤、线槽、油污多,A部毛刺、夹层、偏心、缺角、夹伤、歪头、蝴蝶、圆棒、油污多,CP线尾端毛刺等 3.6 次要缺点(以MI表示):不影响产品功能和使用寿命,一些外观上的瑕疵问题及机构组装上 的轻微不良或差异的缺点。如:B部扭曲,A部切不断、弧形、黑斑、无光洁、铝屑,CP线弯曲等。 4.0 职责与权限 4.1生产部:负责生产首件的制作和自检。负责生产设备、仪器的日常保养和现场规范管理。 负责现场品质的改善。 4.2 IPQC负责对产品的检验和判定。 4.3 IPQC负责制程巡检实施和生产线首件的确认。 4.4 IPQC负责对异常品质问题要求相关部门提出纠正措施。 4.5 IPQC有权要求相关部门对制程品质不符合采取纠正预防措施,包括要求生产停线。
过程检验作业指导书
过程检验作业指导书 1.目的 为了加强产品生产现场品质的管控,有效的控制和降低潜在的质量风险,确保生产过程中产品品质处于受控状态。 2.适用范围 适用本公司所有产品的从领料生产到包装完成各工序的检验。 3.检验依据 产品图纸、检验指导书、样品、装配工艺等产品资料文件。 4.检验程序 4.1.物料入场检验 1.1人员及职责 装配线设置物料专员,负责从仓库领取当天装配水炮所用物料,分配不同物料给不同工位装配人员。 1.2具体工作内容 1.2.1从仓库领取装配所需的物料。 1.2.2清点物料数量,分配物料给各个工位。 1.2.3检查物料的质量,包括规格型号、外观、一致性、性能等,检验无误后,开始组装。 2.部件组装检验 2.1自检 装配人员每装配完成第一个部件后,进行自检合格后在装配剩余部分,整批装配完成后逐个进行自我检验,全部无误后,才能流到下一工序。 如果组装的部件有一部分部件组成,则装配人员需要对上一工序的部
件进行检验,合格后方能使用。 2.2互检 装配人员在一批部件自检完成后,要求相邻工序装配人员或下一工序装配人员给做互检,互检完成后,检验人签字确认。 2.3巡检 4巡检是生产过程中,检验员对生产出的产品进行巡回检验,质检员对产品进行抽样家宴,目的是为了防止成批不合格品的发生或工艺发生异常。 检验员对个生产工序产品品质状况进行巡回检查,在巡检过程中需特别注意物料加工的工位、常换人、有新人上岗的工位以及关键工位,如有发现异常及时通知生产管理负责人进行改善。 巡检过程中同时注意操作人员是否按照《作业指导书》进行操作,如发现操纵人未按照作业指导书进行操作,应立即要求作业人员改善。检验员有权对不符合规定的操作,现场易引发质量问题和生产效率的操作,要求进行整改。 5.不合格的处理方法 5.1由自检、互检发现的由装配人员引起的不合格品,由装配人员自行返工维修,返工后的产品需要重新检验。返工返修仍然不能解决的,可以做报废处理。 5.2巡检发现不合格品,必须标识隔离单独存放,进行集中统一处理。并调查原因,改进装配流程、方法。 6.出现以下情况,检验员可以拒检 6.1 使用未按周期检定或校准的仪器、设备生产出来的产品
机动车尾气排放检测作业指导书的操作流程
三、操作规程 (一)外观检测员 1、维护好外检区的检测秩序; 2、指导客户填写车辆登记表; 3、对照行驶证信息,确认外检表内容和车辆信息是否相符; 4、检测车辆要检查轮胎有无明显缺气,左右气压是否一致,轮胎有无裂痕及划伤,是否夹有杂物及过多沙石; 5、检查车辆进、排气系统,发动机变速箱和冷却系统,不得有任何破损、泄漏,车辆的发动机变速箱和冷却系统等应无液体渗漏; 6、确定车辆驱动形式,断开ABS和防侧滑(ASR),和引车员做好交接,提醒引车员驱动形式; 7、检查车辆的机械状况,无影响安全或引起试验偏差的机械故障; 8、关闭空调、暖风,音响等附属装备,装备牵引力控制装置的车辆应关闭牵引力控制装置。受检车辆不能载客,也不能装载货物; 9、判断受检车辆所适用的检测方法。 (二)录入员 1、熟悉汽车检测工艺流程、检测业务和检测技术; 2、熟练操作计算机,熟悉本公司的检测业务范围内的机动车相关参数,耐心答复解释送检车辆单位提出的询问,做好对外窗口的文明服务; 3、开启计算机及服务器电源,对设备进行预热,并填写开机记
录; 4、信息录入做到迅速而准确; 5、核对外检单信息,对照车辆行驶证信息确定检测方法,并准确无误的录入信息并入库; 6、对外地转入,异地委托审验的车辆,应符合相关检测要求,并留行车证或车辆登记证书证书复印件; 7、严格遵守《安全用电管理制度》和《登录计算机操作规程》。 (三)操作员 操作员负责电脑仪器的操作,引导引车员、辅助员完成检测工作。 1、设备预热 (1)在开检前半小时打开控制柜后面的电源开关,开启电脑、测控仪和尾气分析仪,启动检测程序,按照电脑提示输入正确的操作员用户名和密码进入检测程序,进行检测系统预热,测功机预热时间为10分钟,分析仪预热为15分钟。填写开机记录。 (2)对台架进行加载滑行和空载滑行试验(每天一次)填写使用记录。并上传。 (3)对五气分析仪进行校准(调零,密封性检测,低流量检测)(每天一次)填写使用记录。并上传。预热完毕后,分析仪进入清零、检漏程序,此时应堵住尾气取样探头,检漏过程为17秒,如有漏气,系统会提示“有泄漏,请堵塞取样探头”,并重复进行检漏程序,如无漏气系统会提示“无泄漏”, (4)对流量计进行校准和自检,(流量检测,流量计【O2】量
质检作业指导书
质检作业指导书
精密数控综合加工中心 制程检验作业指导书 版本/版次:A/1 总页数:5页 文件编号: 生效日期: 编制:审核:核准:
精密数控综合加工中心品质管理工作细则制程检验作业指导书文件 编号 版本/ 版次 A/1 页 次 2/5 生效 日期
文件修改记录 制定/修订日期修订内容摘要页次版本/版次总页数 制定审 核 批 准
精密数控综合加工中心品质管理工作细 则 制程检验作业指导书文件编 号 版本/ 版次 A/1 页 次 3/5 生效日 期
精密数控综合加工中心品质管理工作细则 文件编号 1、目的:本作业指导书是为规范制程检验的流程以及发现问题的处理程序,确保公司产品在加工 过程的质量控制。 2、适用范围:所有产品的加工过程的质量控制按此作业指导书执行。 3.职责和权限 3.1、品保部负责产品加工过程的各工序的首件确认和制程巡检; 3.2、车间技术员或操作员负责首件的自检和送检,负责处理品保部判定的不合格品;负责 生产现场的不良品标识。 4.程序 4.1首件检验 4.1.1、首件检验的时机: A )新产品投入生产时,必须做首检; B )停机超过4个小时以上时,必须做首检; C )机器设备修理后或夹具修理后,必须首检; D )正常生产时,换生产其它产品时,必须做首检; E )临时要求做首件的情况。 4.1.2、车间按订单要求进行安排生产时,如有4.1.1的情况时,由车间技术员或班组长 先自行调整好设备和夹具试生产3-5PCS 产品进行自行确认,经自行确认合格后,开出《首件检验报告》和产品传递给车间质检人员进行确认,经车间质检人员确定合格后,签样和签报告后,才可批量生产。并且把签样和报告置于设备的明显处,便于自检。如果车间质检确定为不合格时,车间技术员或班组长必须调机或找相关人员跟踪解 决,直至合格后才可批量生产。 4.2制程巡检 4.2.1制程巡检的时机与频次 A )当首件判定合格后,质检员必须对生产过程的各工序进行巡回检查,主要是通过技术要求 、图纸和作业指导书对生产过程产品进行判定,指导员工进行有效生产; 制 定 审 核 批 准
制袋作业指导书
金億包装制袋作业指导书 一、目的:规范制袋生产管理过程,确保成品满足客户和相关标准要求: 二、范围:适用于本公司制袋生产作业的管理控制: 三、职责: 3.1制袋班长负责制袋生产作业过程中实施全面监督,安排人员和生产计划; 3.2操作工负责生产过程中的制袋作业: 作业内容 一)生产确认 1.机长认真审阅《计划单》,包括:成品名称、规格、数量、热封位置、热封边宽、切刀位置、冲孔位置、冲孔尺寸、使用材料及特别要求等; 2.机长将生产安排及注意事项向各工位人员讲解,各工位人员应认真了解生产要求和制程注意事项。 3、强调所做产品的控制要点及重视安全生产、责任到人。 二)人员、环境 l、制袋员工头发应扎起,手指不得带有棱角的饰品; 2、助手不得擅自操作或更改制袋机操作屏所设置的相关参数;
3 、各人员应保持周围环境整洁,通道畅通。 三)设备检查 A、检查各导辊传动及定型板有无毛刺或污垢、杂质; B、安排人员进行设备保养。给每日需润滑部位加油,并填写《设备日常保养表》; C、检查设备周围是否有灰尘、杂物、并将其清除: 四)领料、装料 l、机长根据生产安排和计划单要求安排人员领取相应名称规格的膜卷; 2、用手推车把卷膜移到放卷架依袋样穿过相应导辊,上料前应注意材料的热封面,卷膜应放置在放料架中间,并同时调整位置。 3、将卷膜固定后,注意送膜的方向为热封面朝上,不要装反。 五)开机前准备工作 1、按计划单和工艺要求调整好袋的尺寸,安装好热封刀,并初步分切刀和热封刀的位置; 2、打开电源,按工艺文件要求设定热封刀温度; 3、输入制袋的相关数据以及每扎的所需个数; 4、选择色差较大的图案边沿左右调节光眼灵敏度,使其达到要求; 六)开机生产 1、启动主电机,低速运转,随即调整边封光电,将膜对分
IPQC制程巡检检验规范
IPQC制程巡检检验规范 一、为了规范IPQC制程品质控制重点及作业方法,使产品在生产过程中得到有效控 制,特制定本流程。 二、适用范围:适用于本公司内的IPQC检验工作。 三、定义 (1)IPQC:即生产过程品质控制,是指领料生产以后,到成品加工完成时的品质管理活动。 (2)BOM:物料清单。 (3)首件:生产过程每批量,经自检合格的第一件成品或材料变更,工艺变更后自检合格的第一件成品,必要时数量可为2-5PCS或一箱。 四、职责 (1)品管部IPQC依据本文件规定对生产过程品质进行检查控制。 (2)IPQC对异常现象进行确认: 1.若异常现象IPQC能够立即判定原因,并且能够解决,则与生产组长一起制定纠 正措施并执行,IPQC进行跟踪验证,验证数量不少于20PCS无问题方可正常生产。 2.若IPQC不能立即判定原因,则立即通知上级。 3.找出真正的不良原因之后,相关的责任单位应在二个工作时之内给出纠正措施, 四工作时内给出预防措施;IPQC跟进改善措施实行后的50PCS(若批量小于 50PCS则需跟踪同型号下一批次的生产),以确定改善措施是否有效,如果措施有效,对此不良问题结案,必要时将措施纳入相关作业文件;如果改善措施无 效,责任单位重新制定改善措施;直到经跟踪验证有效为止。 4.若半小时内不能分析出异常原因,则品管立即要求生产停止,对已生产的产品 进行标识并隔离,并做好标示。 五、作业程序 (1)巡检频率及方法:
1.IPQC巡检频率为每1小时巡检一次,每次对每个管制点进行一次检验。 2.对重点岗位及易防错误岗位,不定时进行巡检。 (2)检验前准备:作业前IPQC需熟知和理解产品规格书,BOM表及相关检查工作指引,了解产品的功能及检测重点,对照样品和规格资料,掌握相关检测方法;(3)熟悉装配作业指导书及相关标准; 1.生产作业规范监控:根据BOM表、规格书、样品监督生产线的物料使用状况,包 括物料的使用有效期、使用规则等等。 2.监督各工具,仪器设备的检查、校验和记录状况,是否在合格状态下使用,例如: 《设备维护保养记录表》; 3.依产品规格资料、装配作业指导书等资料监督各作业岗位是否按标准作业,如测试 仪器的参数设定、换料记录等; 4.监督生产线测试岗位、修理岗位是否有不良品标示和区分; 4.1不良品摆放是否规范; 4.2监督和确认包装方式是否正确,包括产品包装标识、型号、箱数、数量、包装方 法和包装外观; 4.3对生产线返工状况进行全过程跟踪确认; 4.4在生产人员每次换拉时,随机抽取3-5种物料与工位和相应的作业指导书比对。 六、本规范解释权归品质部。 七、本规范生效日期2015年6月15日。 编制:孙玲玲审核:
制袋制程及最终检验标准QC
适用范围: 本标准适用于制袋工序生产过程中生产人员对所生产产品的自检、质量控制及品管人员对制袋产品的制程检验和制袋成品包装缴库时的完工检验和出货前的出厂检验。 标准内容: 1.抽取样本 依制袋机生产顺序,确定检验对象,在已确定的品种被制袋成型为成品状态的产品中随机抽样。 生产人员每一百只自检一次,制程检验人员每两小时抽查一次。 成品包装缴库前进行完工检验。产品出货前作出厂检验。完工检验和出厂检验的抽样规格及数量执行以下标准: 以产品个数抽样的抽样标准 以产品包装件数抽样的抽样标准 上述指标全部合格则判定为合格;上述指标有一项不合格,则判定为不合格。 首检合格才允许正式生产,制程检验发现不合格及时通知生产人员调整,必要时停机处理。生产过程中意外停机或生产人员调整后须重复首件检验直至合格。 制程检验发现的不合格品和出厂检验发现的不合格品,如果可以筛选或修复的由当班生产人员负责筛选或修复,无法筛选或修复的不合格品要开出《不合格产成品报告处理单》进行相应处理。
生产成品缴库前须由品管人员按计划缴库数量抽样作完工检验,完工检验不合格的产品不可缴库;库存产品出厂前须由仓库人员通知品管按照出货量进行抽检,作出厂检验。 4.记录与区分 分切和制袋制程检验及判定结果,分别填入《分切/制袋制程检验记录》,生产人员自检不做记录。 产品缴库前的完工检验由品管记录检验数据和判定结果于《完工检验报告》上作为缴库依据;产品出厂前由品管人员作出厂检验,将出厂检验的数据和判定结果记录于《出厂检验报告》上,作为出厂放行的依据。 对所有已检、未检产品作出明确、固定的标识,区分摆放。已检合格的成品放入待包装区域。已检不合格产品可返工,重修的退还生产部门返工,若不合格又不能返工利用的,放入待处理品区域,同时填写《不合格产成品报告处理单》呈报公司批示后处理。 5.成品的卫生指标由品管部每季度送样到有资质检验机构检验并保存检验记录。 6.附录1: 表5 拉断力、断裂伸长率
注塑成型制程检验规范
成型制程检验规范 一. 目的 规范制程检验,正确监控制程以预防品质异常,确保产出品质及满足客户要求。 二. 适用范围 本规范使用于塑件成型所有产品。 三. 定义 无 四. 权责 4.1工程部: 4.1.1.负责提供生产作业标准,技朮支持; 4.1.2.负责提供标准生产工时。 4.1.3.制程中生产重点参数的提供与变更。 4.1.4.与制程相应的文件、规范、条件及标准的编制。 4.1. 5.协助分析检讨改善制程异常。 4.2企划部: 4.2.1.负责提供生产计划表,跟进提供成型生产所需原料及零件给产线生产。 4.2.2.负责代工客户的订单处理,物料跟进及制定《出货通知单》及出货明细。 4.3塑件品质部: 4.3.1.负责制定各产品品质检验规范。 4.3.2.制程中各项重要参数的稽核与确认,确保产品满足检验规范/规格及客户需求。 4.3.3.制程中的首件检验,巡回检验,最终检验。 4.3.4.制程异常初步确认,不良品的确认。 4.3. 5.产品质量数据之统计,分析,并传达相关单位。 4.3.6.矫正与预防措施效果的跟踪与效果确认。 4.4其它单位: 4.6.1协助生产过程中相关事项处理,保证生产顺利进行。
五. 作业流程 六. 作业内容 6.1 获取产品制作所需信息 6.1.1.产品在生产前,生产各相关人员必需获得以下工程资料方可生产:产品工程图、BOM 表、作业指导书、作业流程及包装规范。 品管 成型单位企划
6.1.2.品管检验人员在产品生产前必需获得该产品的SIP、蓝图、评估报告、样品等资料, 以作为检验该产品的依据。 6.1.3.以上工程资料及检验资料必需为文控中心正式发行的资料。 6.1.4.生产必需依各相关产品的工程资料要求进行产品制造。若生产条件或生产流程需要 任何变更时, 由工程填写工程变更通知单,经相关部门签核同意后,由文控中心 统一变更受控发行,具体操作参照《文件资料管理程序》。 6.2生产计划管制 6.2.1.企划部生管员依客户或各厂区需求制订每周生产计划。 6.2.2.企划部生管员需依生产计划跟进采购或供应商按时供给成型原料,并由生管员开出 《发料单》,通知货仓备料发料,生产领料。 6.2.3.生产接到企划课的每周生产计划后,由生产课长或组长对每周生产计划审核并作生 产排配,当不能达成时,应及时反馈企划课,由企划课协调解决。 6.3原料投入 6.3.1.生产单位依据发料单和生产计划表到仓库领料,原料生产前需先对原料进行烘烤, 烘烤温度和烘烤时间参照《标准成型条件表》进行。 6.3.2.生产塑胶料次料添加比例参照《BOM表》或《塑件产品次料添加标准》进行。每次 加料/拌料前需记录在<次料添加记录表>上,并通知品管签名确认。 6.3.3.成型在加料或拌料前,需先清理干净之前料筒内余料,预防余料和加入原料颜色、 成型温度等特性不一致混用,造成产品混色、料花、粘模等异常。 6.4成型模具等周边设备连接/成型条件设定。 6.4.1.成型周边设备安装: A、上模安装:查找产品对应之成型模具,依《标准成型条件表》规定将模具安装在合 适吨位之机台上。 B、依《标准成型条件表》连接模具所需用的标准模温(常温水、冷冻水、模温水)。 6.4.2.依照《标准成型条件表》调试自检OK后,由成型课技术员开出《成型首/终件记录 表》,品管检验OK后再开机生产。 6.5初件检验 6.5.1.I PQC接收到成型技术员送检的《成型初/终件记录表》和首件样品后,应在2小时内 给出判定结果。 6.5.2.初件检验过程当发现成型条件记录超出《标准成型条件表》时,应通知生产&工程检 讨标准成型条件是否合理,。如工程评估可进行变更,则跟进工程对此标准成型条件发 出工程变更通知单,并跟进产品外观和尺寸是否符合产品标准。 6.6制程作业员作业 6.6.1.生产前IPQC及现场人员应事先确认相关工程数据(蓝图、承认书、包规、作业指导
IPQC制程巡检作业指导书(含表格)
IPQC制程巡检作业指导书 (ISO9001-2015) 1、目地: 规范半成品/成品制程巡检检测的项目、方法、频次、标准、不合格的处理.从而保证产品质量符合客户要求,同时通过制程巡检收集生产制程的原始记录,有效地监控制程的变化,并以此保证和推动制程的持续改善。 2、范围: 适用于我司所有之半成品和成品制程的控制。 3、术语(定义): 3.1首件检验:对每个班次刚开始时或过程发生改变后加工的第一个或前几件产品进行的检验。 3.2巡检:制程检验。 3.3终检:对产品在完成一道工序后,准备转入下工序或入库之前,进行的一个全面的检验。 3.3品质状态:红色盒子装不合格品;红色标签代表不合格品绿色、蓝色盒子装合格品;绿色标签代表合格品黄色盒子装待检品;黄色标签代表特采品。4、权责: IPQC:负责按制程巡检作业指导书对产品进行巡回检验。
品质主管:负责制定产品检验规范和作业指导,及重大品质异常的协调与处理。PMC:负责产品的生产进度和质量问题整体统筹安排,以保证产品按期交付于客户。 生产部:负责保质保量完成生产计划任务。 5、作业内容: 5.1客户订单 5.1.1PMC部根据客户订单,转化为内部生产指令单,下达生产任务给相关生产 工序部门,并随时跟进每天的生产进度和产品质量状况,以确保按期交付产品于客户。 5.2生产试作与首件送检 5.2.1生产部门根据生产指令单,及时准备好工装治具/机台/生产线和相关辅料,制定生产计划控制进度,准备试产调试或改机。 5.2.2生产根据工程图纸及客户要求等技术指标,开始试作3-5PCS,对产品外观/尺寸/同轴度/跳动度进行自主检查,检查OK后,填写好首件单,送检给品质部IPQC做首件确认检查。 5.3首件检验 5.3.1IPQC收到首件单和试作样品后,根据样板/检验规范/工程图/客户要求等技术资料,对产品进行全面检查和记录。 5.3.2首件确认OK后,IPQC签核首件样板,通知生产批量生产,并且把检验的数
生产过程检验作业指导书
生产过程检验作业指导书 (ISO9001-2015) 1.0目的 保证所有产品在生产过程中都通过规定的检验后才进入下一道工序,生产出符合规定要求与特性(包括顾客需求)的产品。 2.0范围 适用于本公司所有正在生产的在制品(半成品)、成品。 3.0定义 3.1首件确认:按规定对生产线的每批订单首件进行检查确认。 3.2自检:作业员在作业过程中对作业条件、作业方法和工序制品的自主检查。 3.3制程全检:LQC对生产的在制品进行100%的检查动作。 3.4巡检:IPQC在生产现场按一定时间间隔对有关工序的产品和生产条件进行的检验和监督。 4.0权责 4.1生产单位:负责自检工作,并同品保单位一道做好首件品确认。 4.2品保单位:负责首件确认、制程巡回检查,以及工序在制半成品、成品的抽检。 5.0作业内容 5.1首件确认 5.1.1IPQC依据产品承认书、检验规范、BOM、工程样品等相关标准,对每批订单、生产过程中因换线、换机种以及换工装、设备调整或重大质量异常纠正后等改变条件后生产的产品做首件确认,首件检查完成时间正常情况下不能超过
二十分钟,确认结果记录在“首件检验报告”中。 5.1.2首件检查合格时,由IPQC在首件上签名确认并展示于生产线前端,作为生产样本,同时通知生产单位可量产。 5.1.3首件检查不合格时,IPQC指出不合格部位,要求其改善。重新加工首件,合格后方可继续生产。开始下线到最终确认合格的时间段生产的产品暂时作标识/隔离,待分析原因后视不合格影响程度作特收或全检或重工处理。 5.1.4新产品第一次试量产的首件确认必须会同研发、品保、生产等一同到现场进行首件确认,合格后方可批量生产。 5.1.5经确认合格之首件,当批生产完后,由IPQC收回与当批首件检验报告存档,保存期限为两年,到期后统一报废处理。 5.2自主检查 生产车间作业员要在生产中进行100%自主检验。自主检查中作业员如发现产品质量异常时,应及时停止作业,并向生产现场管理人员报告,寻求改善对策。 5.3制程全检 LQC依据产品检验规范以及首件对正在生产的在制品、半成品进行100%检查并做记录。若发现质量异常,应及时通知PE或生产现场管理人员寻求改善对策。 5.4巡回检查 5.4.1IPQC按“产品承认书”、BOM、“产品检验规范”、QC工程图的要求每小时一次对各生产线进行巡查并作好“IPQC巡检记录表”,巡查时不仅应按规定抽查产品,而且应观察作业者的作业方法及设备、工装、量具使用等方法,如发现问题应及时联络生产现场管理人员加以纠正,不合格品应标识好并进行隔离。 5.4.2如巡检中发现严重质量问题,IPQC应及时向主管报告,主管视情况的严
制程品管检验课后复习规范标准
宜兴硅谷电子科技有限公司 □程序书规范 文件名称制程品管检验作业规范发行日期年月日编号F P Q C 0 1 3 0 0 2 - A 1 有效日期年月日 沿革版序A1 发行日期 版序 发行日期 新增 变更沿用废止总页数23页 内容摘要说明 项次 页 次 项次页次 1.目的 3 2.适用范围 3 3.权责单位 3 4.参考文件 3 5.内容说明 3 6.附件4-5 会签单位系统部制造一部制造二部制造三部制造工程部产品工程部工务部生产计划部会签 会签单位品检部技术中心资材部品质管理部 会签 分发单位系统部制造一部制造二部制造三部制造工程部产品工程部工务部生产计划部签收 分发单位品检部技术中心资材部品质管理部 签收 制定部门品检部撰写及修定者陈波制定日期2012.11.28 主管审核审核日期 标准化检查检查日期 核准核准日期 传阅
SD032002-02A1 背景沿革及修订一览表
SD032002-03A1
制程品管检验作业规范 1.目的 1.1.检验与监控各制造单位品质异常之发生,确保各制程品质水平之稳定。 2.适用范围 2.1.厂内各制造单位如:内层、钻孔、压合、电镀、外层、防焊、成型及各表面处理流程。 3.职责 3.1.品检部品管课负责各制造单位生产之首板及出货时抽检; 3.2.各制造单位负责生产中自主检验。 4.参考文件 4.1.《产品标识与追溯作业程序书》(FPQC012001) 4.2.《品质管制运作管理程序书》(FPQC012002) 4.3.《不合格品管制程序书》(FPQC012003) 4.4.《矫正和预防措施管制程序书》(FPQC012004) 4.5.《Excursion运作管理程序书》(FPQC012007) 4.6.《切片与背光检验规范》(FPQC013004) 5.定义 5.1.IPQC(In process quality control):对生产过程中各项品质以AQL抽样准则对其进行检验并 监控.以确保各站品质达到客户品质需求.
车间各工艺作业指导书
浙江名家工贸有限公司 剪板作业指导书 1.开机时检查机器运转是否正常,如不正常,立即停止,并告知相关 人员修理。直至到正常方可开始工作。 2.对单生产,检查门面花形是否符合生产单; 3.按图纸生产,检查所使用的图纸是否有效;如有疑问立即停止生产 并即时上报技质部解决。 4.认真核对板材厚度是否与生产单所规定相符,不得出现混淆隐患。 5.检查门面花形的压形深度是否到位,有无压裂、划伤、严重凹凸不 平等现象; 6.经检查确认花形无误、板料合格后方可投入本序首件生产; 7.首件生产时必须按单生产,检查工艺尺寸是否与图纸要求相符,确 保对角线误差不大于1.5mm,并注意区分左右方向; 8.检查首件表面是否有划伤、划痕、凹凸点及压机模型遗留压痕; 9.首件生产后经检验员确认尺寸无误、表面合格后方可批量生产; 10.批量生产过程中应经常抽检,防止靠山松动、移动引起尺寸误 差,避免批量质量事故的发生;同时应注意生产过程中,花形是否存在偏位,上下左右尺寸是否同步; 11.门面板料堆放时花形要吻合,门面板料要整齐,不得堆放过高 (同一花型不超过120件,不同花形不超过20件),防止板料堆放过多引起产品变形; 12.在生产过程中必须保证轻拿轻放,以防碰伤、划伤; 13.在流入下道工序前进行全方位自检,自检合格后方可流入下道 工序。 14.完工时做好机器的保养与6S工作方可离岗。
15.安全注意:机器在运转时手严禁伸入刀口内,如机器发生故障 必须等机器停止运转后方可修理,以防安全事故发生。 浙江名家工贸有限公司 冲门面作业指导书 1、开机时检查机器运转是否正常,如不正常,立即停止,并告知相 关人员修理。直至到正常方可开始工作。 2、冲床人员在首件生产前,应对上序流入本序的产品进行全方位互 检;检查工艺尺寸是否与生产单相符,表面是否有划伤、凹凸点等,确认合格后方可流入本序按有效图纸进行首件生产;如图纸有疑问立即停止生产并即时上报技质部解决。 3、每道冲孔工序首件生产时必须按单生产,分清工件型号规格,检 查冲孔及定位尺寸是否符合生产单工艺标准(横向及纵向尺寸),并分清上下头及左右方向; 4、检查门面铰链孔数量、类别及锁孔类别是否与生产单一致; 5、检查在操作过程中工件表面是否有划伤、碰伤、凹凸、折痕等质 量隐患的出现。每次只能冲一片,并注意冲孔不得有毛刺,以防影响外观和流程中划伤其它产品表面。 6、首件生产后经检验员确认尺寸无误、表面合格后方可批量生产; 7、批量生产过程中应经常抽检,防止靠山松动、移位引起尺寸误差, 避免批量质量事故的发生;同时一定要看清每件工件,防止冲倒、冲反等现象的发生; 8、工件在流转过程中必须轻拿轻放平整流转,不可翻转,以免工件 折伤及其它设备硬件对工件造成伤害而引起质量隐患; 9、在流入下道工序前进行全方位自检,自检合格后方可流入下道工
产品巡检检验作业指导书_图文.
1.0 目的: 为规范成品制程巡检检测的项目、方法、频次、标准、不合格的处理 . 从而保证产品质量符合客户要求,同时通过制程巡检收集生产制程的原始记录,有效的监控制程的变化,并以此保证和推动制程的持续改善。 2.0 适用范围: 适用于本公司内所有规格产品制程的控制。 3.0 定义: 3.1 IPQC:即生产过程品质控制,是指产品从物料投入生产到产品最终包装过程的品质控制; 3.2批量不良——某一时段出现的品质不良均属于同一种现象。 3.3 RoHS: Restriction of the Use of Certain Hazardous Substances inElectrical and Electronic Equipment(电子电气设备中限制使用某些有害物质指令 ; 3.4 致命缺陷(以 CR 表示 :影响质量安全的所有缺陷,影响难以纠正的非正常的情况,会影响寿命的,会造成产品故障的或造成产品使用困难的或造成下道工序混乱的缺陷都称为致命缺陷。如:混料、假焊、虚焊、焊点小、拉力不够, B 部纵向划伤、尺寸超标, A 部尺寸超标, CP 线露铜、尺寸超标, T 部厚度超标等。 3.5 严重缺点 (以 MA 表示 :可能造成产品损坏, 功能异常或因材料而影响产品使用寿命的缺点。如:焊点毛刺、炸焊枪、偏焊、半焊、斜接、焊点大, B 部夹伤、
线槽、油污多, A 部毛刺、夹层、偏心、缺角、夹伤、歪头、蝴蝶、圆棒、油污多, CP 线尾端毛刺等 3.6 次要缺点(以 MI 表示 :不影响产品功能和使用寿命,一些外观上的瑕疵问题及机构组装上的轻微不良或差异的缺点。如:B 部扭曲, A 部切不断、弧形、黑斑、无光洁、铝屑, CP 线弯曲等。 4.0 职责与权限 4.1生产部:负责生产首件的制作和自检。负责生产设备、仪器的日常保养和现场规范管理。负责现场品质的改善。 4.2 IPQC负责对产品的检验和判定。 4.3 IPQC负责制程巡检实施和生产线首件的确认。 4.4 IPQC负责对异常品质问题要求相关部门提出纠正措施。 4.5 IPQC有权要求相关部门对制程品质不符合采取纠正预防措施 , 包括要求生产停线。
焊接检验作业指导书
焊接检验作业指导书 1.目的 为焊接人员作业和自检,以及检验员检验提供检验规则及检验方法,指导其正确生产、检验,从而稳定产品质量。对本作业指导书未规定的要求,应在图纸和相关工艺资料中规定。 2.适用范围 本指导书适用于混合气(二氧化碳+氩气)保护焊的焊接操作和检验。 3.焊前准备 焊接工件的合格与否决定于焊接的三要素:合格的焊接材料,一流的焊接设备和优秀的操作人员。 3.1焊接材料 3.1.1焊接前,应将焊接位置的毛刺、飞边、尖角等打磨干净。 3.1.2焊接前,应将焊接面的水、锈、油污及其它杂质清除干净。 3.1.3根据焊接母材选择与之相适应的焊丝。 3.2焊接设备 3.2.1焊接设备应该有接地装置,并可靠接地。 3.2.2焊接设备应处于正常工作状态,安全可靠,各仪表显示正常。 3.2.3供气系统应处于正常工作状态,必须使用符合国家标准或相关行业标准的气体。并根据焊接母材调整二氧化碳比例到合适范围。 3.3焊接人员 3.3.1焊接主管必须具备专业的理论知识和熟练的实际操作能力。 3.3.2焊接主管必须能够熟练操作焊接设备,对设备的一般性故障能够进行排查和维修,并承担设备的维护和保养工作。 3.3.3焊接主管必须读懂图纸及焊接工艺,能够明确焊接工艺中所规定的焊接要求。 3.3.4焊接主管必须熟悉常见的焊接缺陷及其产生原因,并在实际生产中予以避免。(常见焊接缺陷见附件一) 3.3.5 焊工经过焊接主管培训,并经焊接主管考核合格后,方可担任指定项目的焊接工作。
3.3.6 焊工作为焊接生产的直接执行者,经主管培训后,必须掌握 3.3.1~3.3.4中的相关技能,具备判定焊接件是否合格的能力。并对所焊接的产品质量负责。 4.焊接生产 正式的焊接生产过程中,焊接工装、夹具的可靠,焊接设备的正确使用以及焊接过程中对工件的检验是保证焊接产品质量的主要因素。 4.1工装、夹具 4.4.1焊接工装必须保证各零件的正确装配,各零件的相对位置必须符合图纸及相关焊接工艺等技术文件的要求,重要位置可留出焊缝收缩余量或制定预变形工艺。 4.4.2各零件通过焊接工装正确装配后,必须通过夹具可靠固定,在焊接过程中,各零件不得有相对移动。 4.4.3施焊前,焊接工装必须固定在焊接实验台上,牢靠无松动。 4.2焊接作业及自检 4.2.1组装焊接前检查各零部件形状、尺寸是否符合图纸或工艺要求。检查合格后通过焊接工装正确组合装配,并通过夹具牢靠固定。 4.2.2焊接主管根据各零件的装配关系,设定出合理的焊接顺序,编制焊接程序。对已经编制出程序的产品,再次生产时,必须对程序进行重新验证。 4.2.3根据焊件的厚度及焊缝位置,选择合适的焊丝直径、焊接电流、焊接电压和焊接速度,并在焊接试板上试焊。 4.2.4根据试板上的焊缝成形情况,适当调整焊接电流、焊接电压、气体流量以及焊丝伸出长度等,以达到最佳的焊接规范。(最佳焊接规范的特征:焊缝成形好、外形美观,没有烧穿、气孔、咬边、裂纹等缺陷,熔深控制在合适范围内。焊接过程稳定,飞溅小。电焊机的电压表、电流表的指针稳定,摆动小。) 4.2.5焊接主管指导焊工进行首件焊接,并对焊接好的首件进行检验。主要检验项目:焊接后尺寸必须符合图纸和焊接工艺等技术资料;不得有漏焊;不得有影响产品外观和质量的气孔、裂纹、烧穿等焊接缺陷;不得有影响外观及配合的焊瘤;对焊缝高度有要求的重要配合位置必须保证焊缝高度,不得有影响产品结构的焊接变形等。可与焊接合格样本进行比对。如有不符合检验要求的,应立