零件的分析
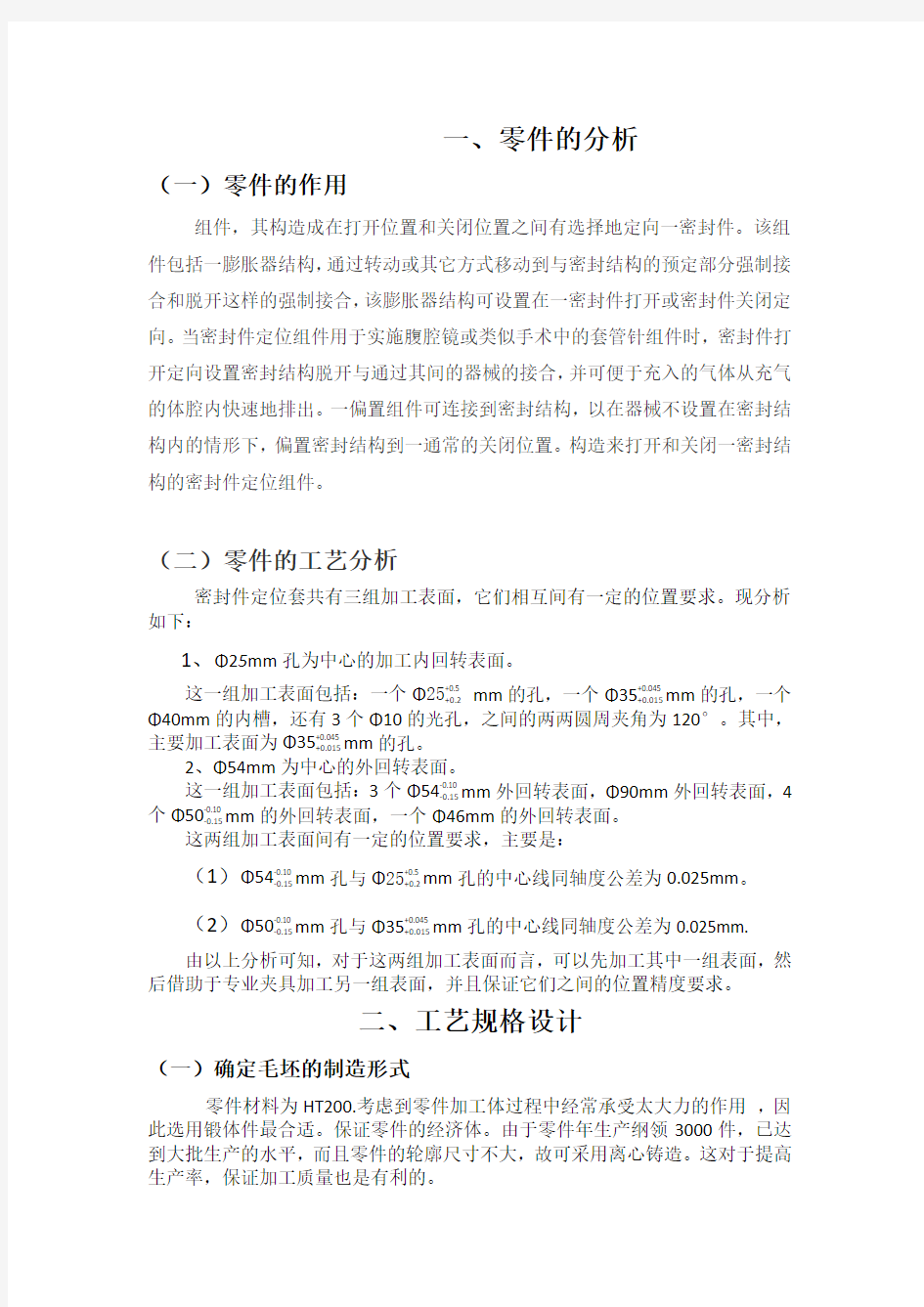

一、零件的分析
(一)零件的作用
组件,其构造成在打开位置和关闭位置之间有选择地定向一密封件。该组件包括一膨胀器结构,通过转动或其它方式移动到与密封结构的预定部分强制接合和脱开这样的强制接合,该膨胀器结构可设置在一密封件打开或密封件关闭定向。当密封件定位组件用于实施腹腔镜或类似手术中的套管针组件时,密封件打开定向设置密封结构脱开与通过其间的器械的接合,并可便于充入的气体从充气的体腔内快速地排出。一偏置组件可连接到密封结构,以在器械不设置在密封结构内的情形下,偏置密封结构到一通常的关闭位置。构造来打开和关闭一密封结构的密封件定位组件。
(二)零件的工艺分析
密封件定位套共有三组加工表面,它们相互间有一定的位置要求。现分析如下:
1、 Φ25mm 孔为中心的加工内回转表面。
这一组加工表面包括:一个Φ25+0.5 +0.2 mm 的孔,一个Φ35+0.045 +0.015mm 的孔,一个Φ40mm 的内槽,还有3个Φ10的光孔,之间的两两圆周夹角为120°。其中,主要加工表面为Φ35+0.045 +0.015mm 的孔。
2、Φ54mm 为中心的外回转表面。 这一组加工表面包括:3个Φ54-0.10 -0.15mm 外回转表面,Φ90mm 外回转表面,4个Φ50-0.10 -0.15mm 的外回转表面,一个Φ46mm 的外回转表面。
这两组加工表面间有一定的位置要求,主要是:
(1) Φ54-0.10 -0.15mm 孔与Φ25+0.5
+0.2mm 孔的中心线同轴度公差为0.025mm 。
(2) Φ50-0.10 -0.15mm 孔与Φ35+0.045 +0.015mm 孔的中心线同轴度公差为0.025mm.
由以上分析可知,对于这两组加工表面而言,可以先加工其中一组表面,然后借助于专业夹具加工另一组表面,并且保证它们之间的位置精度要求。
二、工艺规格设计
(一)确定毛坯的制造形式
零件材料为HT200.考虑到零件加工体过程中经常承受太大力的作用 ,因
此选用锻体件最合适。保证零件的经济体。由于零件年生产纲领3000件,已达到大批生产的水平,而且零件的轮廓尺寸不大,故可采用离心铸造。这对于提高生产率,保证加工质量也是有利的。
(二)基面的选择
基面的选择是工艺规程设计中的重要工作之一。基面选择的正确、合理,可以保证加工质量,提高生产效率。否则,就会使加工工艺过程问题百出,严重的还会造成零件大批报废,是生产无法进行。
1.粗基准的选择
对于一般的套类零件而言,以端面体为粗基准是完全合理的,但对零件体而言,则不合理如果以Φ90mm的端面为基准,无法加工它为精基准做准备。故
选用Φ90mm的外圆作为基准,利用三爪定心卡盘,用以消除→
u、
→
z两个自由
度,又因三抓自定心卡盘上有很多类似的V型块,故可以消除→
y、
→
u、
→
z、
→
x,达到完全定位。
错误!未指定书签。错误!未指定书签。错误!未指定书签。错误!未指定书签。
2.精基准的选择
精基准的选择主要应该考虑基准重合的问题。当设计基准与工序基准不重合时,应该进行尺寸换算。
(三)工艺路线制定
制定工艺路线的出发点,应当是使零件的几何形状、尺寸精度以及位置精度等技术要求能得到合理的保证。在生产纲领已经确定为大批量生产的条件下,可以采用万能机床配以专用工。夹具,并尽量使工序集中来提高生产率。除此以外,还应考虑经济效果,以便降低生产成本。
1.工艺路线方案一
工序1:粗车两端面
工序2:半精车Φ90mm的端面及倒角。
工序3:粗车外圆Φ54mm,Φ90mm
工序4:半精车Φ54mm的外圆
工序5:粗车Φ35mm Φ25mm的两个内孔
工序6:镗40mm的内槽
工序7:精镗Φ35mm Φ25mm的两内孔
工序8:割四个槽
工序9:磨削Φ54mm的外圆
工序10:钻3xΦ10的孔
工序11:终检
2.工艺路线方案二:
工序1:粗车外圆
工序2:Φ90mm、54mm
工序3:精车外圆Φ54mm
工序4:车两端面
工序5:粗车Φ35mm Φ25mm的两个内孔
工序6:镗40mm的内槽
工序7:精镗Φ35mm Φ25mm的两内孔
工序8:割4个宽3mm深3mm的槽
工序9:钻孔
工序10:磨削Φ50的外圆表面
工序11:钻3xΦ10的孔
工序12:终检
3.工艺方案的比较与分析
上述两个工艺方案的特点在于:方案一与方案二均采用一面二孔为精基面加工Φ10mm的孔和外圆,而方案一是直接从铸件外圆粗车一刀,然后在作为基准,加工孔和外圆。显然方案二的粗基准的选择比方案一要好,但方案一的工时稍短些,更为经济,总结两种方案的优缺利弊,集两方案之所长,而重新编排,确定具体工序如下所示:
工序1:粗车一端面和一头外圆。
工序2:粗车另一端面和另一外圆。以粗车后的端为粗精准。
工序3 : 半精车法兰盘端面。
工序4:粗镗Φ25mm和Φ35mm的孔。
工序5:半精镗Φ25mm和Φ35mm的两孔。
工序6:精镗Φ25mm和Φ35mm的两孔。
工序7:粗车Φ54mm的外圆,以工序3、4、5、6为基准。
工序8:精车Φ54mm的外圆
工序9:割Φ50和Φ46的槽
工序10:钳工划线,划3xΦ10孔的中心位置
工序11:钻3x12mm的孔
工序12:磨削加工和的外圆表面
工序13:检验
工序14:入库
以上加工方案大致看来还是合理的的。但通过仔细考虑零件的技术要求以及可能采用的加工手段之后,知上述工艺路线中,是这样拟定的。采用基准重合,即保证设计基准与工艺基准相重合。若违反了基准重合原则,则产生基准不重合误差,甚至会因超差而报废的后果。为了解决这些问题,原有的加工路线仍可大致保持不变,采用合理的装夹,最后的加工路线确定如下:
工序1:粗车一端面和一头外圆,选用CA6140卧式车床和三抓卡盘
工序2:粗车另一端面和另一头外圆,以粗车后的端面为粗基准
工序3:半精车法兰盘的端面
工序4:粗镗Φ25mmΦ和Φ35mm的两孔,选用TS4B2镗床加工
工序5:半精镗Φ25mm和Φ35mm的两孔
工序6:精镗Φ25mm和Φ35mm的两孔
工序7:粗车Φ54的外圆,以法兰盘端面和内孔为精基准和定位基准。选用CA6140卧式车床和专用夹具
工序8:精车Φ54mm的外圆
工序9:割Φ50和Φ46的槽
工序10:钳工划线,划3XΦ10孔
工序11:钻3X12mm的孔,以一面一孔定位。选用Z535立式钻床加工,专用夹具
工序12:磨削加工Φ50和Φ54的外圆端面,选用M120磨床加工,专用夹具
工序13:
工序14:入库
(四)机械加工余量、工序尺寸及毛坯尺寸确定“密封件定位套”的材料为HT200,生产类型为小批量生产,考虑零件在机床运行加工过程中所受冲击不大,零件有多个通孔,零件结构比较简单,故选择手工木模砂型铸造毛坯。又由于箱体零件的内孔需铸出,故还应该安放型芯。
根据上述原始资料及加工工艺,分别确定各加工表面的机械加工余量、工序尺寸及毛坯尺寸如下:
机械加工余量及工序尺寸
工序号工序内容单边余量
/mm
工序尺寸/mm 粗糙度值
Ra/μm
10 粗铣Ф90左端面 2.0 90 12.5
粗铣Ф54右端面 1.5 54 12.5
20
粗镗Ф35045.0
015
.0
+
+
孔
1.0 Ф35 6.3
粗镗Ф40 0.5 Ф40 6.3
粗镗Ф255.0
2.0
+
+
孔面
0.5
Ф255.0
2.0
+
+
6.3
精镗Ф40和Ф255.0
2.0
+
+
孔面及倒角
C2
1.0
Ф40、Ф255.0
2.0
+
+
和C2
1.6
粗车Ф90外圆 2 Ф90 12.5 粗车Ф90右端面 1.5 90 12.5
粗车Ф5410.0
15
.0
-
-
外圆
2.0 Ф54 12.5
(五)确定切削用量及基本工时
工序10
铣削定位套左右端面 1) 铣削定位套左端面 步骤如下。
① 确定铣刀齿数和每齿进给量:查表5—41 表5—42和表5—119.得出铣刀规格为d (铣刀直径)×D (孔直径)×L (铣刀长度)×Z (齿数)=φ160mm ×φ50mm ×45mm ×16mm 及每齿进给量fZ 取0.3mm/齿。 所以没转进给量f=ZfZ=16×0.3=4.8m/转。
② 确定背吃刀量ap :由于单边余量为1mm.即ap为1mm 。
③ 确定铣削速度Vc :查表5-124.确定Vc=30m/min ,刀具材料为高速钢。
④ 确定主轴转速n:由n=d V π.1000=8630
1000??π=59.68r /min ,
查表5-8,确定铣床实际转速为60r /min 。 ⑤ 计算基本时间Tj 。
被加工外圆表面长度l为90mm 。端面车刀选主偏角Kr=90,背吃刀量ap=1mm ,查表5-114得
L1=0.5[d-﹙d 2-ac 2﹚?]+﹙1~2) =0.5[160-﹙1602-1202﹚?]+﹙1~2﹚
=28.1~29.1mm
取l1=29 l2=1~3 L=l1+l2+90=29+2+90=121mm
Tj=
i nf
L
=
min 38.460121??=3.18min 查表5-153得,变换刀架的时间为0.05min ,变速或变换进给量的时间为
0.02min ,启动和调节切削液的时间为0.05min ,共计Tf=0.12min 。
2) 铣削定位套右端面
加工右端面步骤同上,ap ,n ,f ,V c ,Tj 都没变。 被加工外圆表面长度l变了,为191mm 。
所以L=l1+l2+191=222mm
30
粗车Ф5010
.015.0--外圆 1.5 Ф50
12.5 精车Ф5410.015.0--和Ф5010
.015.0--外圆
0.5 Ф5410.015.0--和5010
.015.0--
0.8 切槽2×Ф50和2×Ф54
1.0
2×Ф50和2×Ф54
12.5
粗车Ф90外圆 1.0 Ф90 12.5 50
钻孔3×Ф10 0.2
3×Ф10
12.5
Tj=
i nf
L
=
min 28.460222??=1.54min 查表5-153得,变换刀架的时间为0.05min ,变速或变换进给量的时间为
0.02min ,共计0.07min 。
工序20
1) 粗镗Φ35内孔,孔口倒角C2 步骤如下
① 确定背吃刀量p a :端面总加工余量为2mm ,一次走刀1mm ,p a =3.5mm. ② 确定进给量f :根据表5-102查得f=0.7~1.0mm /r ;查表5-6,根据机床的主轴进给量取f=0.74mm /r.
③ 确定削速度c v :根据表5-118,取c v =50m /min. ④ 确定机床主轴转速n :
n=
w c d v π1000=121
50
1000??πr /min=132r /min 查表5-6得相近的主轴转速n=125r /min ,所以实际的切削速度c v =47.5/min.
⑤ 计算基本时间j T :切削加工长度L=l +1l +2l +3l ,镗刀选用主偏角r K = 90,背吃刀量p a =3.5mm ,查表5-138和表5-139得1l =4mm ,2l =4mm ,3l =5mm 。
L=191+4+4+5=204mm
j T =
i nf L =min 174
.0125204
??=2.21min ⑥ 辅助时间f T :查表5-152得,装夹工件时间为0.8min ,启动机床时间为0.02min ,取量具并测量尺寸时间为0.5min ,共计f T =1.32min 。 2) 孔口倒角C 2
粗镗完Φ35mm 内孔后倒角,取粗镗切削要素,n=125r /min ,c v =47.5/min ,
j T =0.003min 。
3) 粗镗Φ25mm 内孔面 步骤如下
① 确定背吃刀量p a :端面总加工余量为7mm ,一次走刀3.5mm ,p a =3.5mm.
② 确定进给量f :根据表5-102查得f=0.7~1.0mm /r ;查表5-6,根据机床的主轴进给量取f=0.74mm /r.
③ 确定削速度c v :根据表5-118,取c v =50m /min. ④ 确定机床主轴转速n :
n=w c d v π1000=83
501000??πr /min=191.85r /min
查表5-6得相近的主轴转速n=200r /min ,所以实际的切削速度c v =52.124/min.
⑤ 计算基本时间j T :切削加工长度L=l +1l +2l +3l ,镗刀选用主偏角r K = 90,背吃刀量p a =3.5mm ,查表5-138和表5-139得1l =4mm ,2l =4mm ,3l =5mm 。
L=21+4+4+5=30mm
j T =
i nf
L =min 174.020030
??=0.2min ⑥ 辅助时间f T :查表5-152得,取量具并测量尺寸时间为0.5min ,共计
f T =0.5min 。
4) 精镗内孔Φ35mm 及退刀槽端面 步骤如下
① 确定背吃刀量p a :端面总加工余量为2mm ,一次走刀1mm ,p a =1mm. ② 确定进给量f :根据表5-102查得f=0.7~1.0mm /r ;查表5-6,根据机床的主轴进给量取f=0.7mm /r.
③ 确定削速度c v :根据表5-118,取c v =60m /min. ④ 确定机床主轴转速n :
n=
w c d v π1000=132
60
1000??πr /min=144.76r /min 查表5-6得相近的主轴转速n=160r /min ,所以实际的切削速度c v =66.32/min.
⑤ 计算基本时间j T :切削加工长度L=l +1l +2l +3l ,镗刀选用主偏角r K = 90,背吃刀量p a =3.5mm ,查表5-138和表5-139得1l =4mm ,2l =4mm ,3l =5mm 。
L=191+4+4+5=204mm
j T =
i nf L =min 17
.0160204
??=1.82min
工序30
粗车Ф90外圆、粗车Ф90外圆右端面、车外圆Ф54、Ф50 1) 粗车Ф90外圆 步骤如下。
① 确定背吃刀量ap :外圆单边总加工余量为7mm ,两次走刀加工,ap=3.5mm 。 ② 确定进给量f :根据表5-102查得f=0.7~1.0mm/r;查表5-5根据机床的纵向进给量,取f=0.94mm/r 。
③ 确定切削速度Vc :根据表5-109和表5-110,查得Cv=158,xv=0.15,yv=0.40, m=0.2;修正系数Kmv=1.0, KHv=1.0 ,Khv=0.85 , Kkrv=0.73, Ktv=0.83, 刀具寿命选T=60min ,故
Vc=v y v x p
m f
a
T Cv ·kv=(4
.015.02.094.05.360158
??83.073.085.011?????)m/min =30.1m/min
④ 确定机床主轴转速n :
n==
ωπd Vc
1000min /35min /274
1
.301000r r =??π
根据表5-5查得相近较小的机床转速为n=32r/min ,所以实际的切削速度Vc=27.5m/min 。
⑤ 计算基本时间Tj :切削加工长度l=24.5,外圆车刀选用主偏角Kr=?90,
被吃刀量ap=3.5mm ,查表5-138和表5-139得: l 1=Kr ap tan 1+(2-3)取l 1=3mm ;
l 2=4mm ,l 3=5mm 。
L=321l l l l +++=24.5+3+4+5=36.5mm Tj=
294
.0325
.36??=i nf L min ≈2.43min ⑥ 辅助时间Tf:查表5-153得,装夹工件的时间为0.8min ,启动机床的时
间为0.02min ,取量具并测量尺寸的时间为0.5min ,共计Tf=1.32min 。
2) 车削Ф90外圆右端面、车外圆Ф54、Ф50步骤同上,各类参数见工序卡。
3) 车?50和?54共四个槽
① 确定背吃刀量p a :单边加工余量为3.0mm ,一次走刀加工,p a =3mm; ② 确定进给量f :根据表5—106差得f=0.16~0.19mm/r ,查表5—5根据纵向进给量取f=0.18mm/r;
③ 确定切削速度c v :根据表5—109查得Cv=189.8,v X =0.15,v y =0.20,m =0.20,修正系数MV K =1.0,HV K =0
,hv K =0.82,v k r K =0.73,tv K =0.83,
刀具寿命T=60min ,故
v y x p m v c K f
a T C V v
v ?=
=min /)83.073.082.084.00.118
.03608
.189(
2
.015.02
.0m ??????? =41.7m/min
④ 确定机床转速n :
w
c d v n π1000=
=
min /4.8016514.37
.411000r =?? 根据表5—5取较近的转速n=80r/min ,所以实际的切削速度c v =41.4m/min;
⑤ 计算基本时间T j :查表5—138得:21
d d -+l =)3~2(tan +r p k a ,
l 2= l 3=0,车槽刀用主偏角K r =90.,故取l 1=4mm
L=
2
1
d d -+ l 1+ l 2+ l 3=(
42159165+-)mm=7mm Tj=
nf
L i=
8018.07
??4min=1.9min
⑥ 辅助时间Tf :查表5—138得,换刀时间为0.02min ,取量具并测量尺
寸时间为0.5min ,共计Tf=0.52min 。
4) 车φ46外圆切入槽
先切φ46槽,方法同上,背吃刀量为2.5mm ,进给量为0.18mm/r ,机床转速为80r/min ,切削速度为41.4m/min ,基本时间Tj=0.45min ,辅助时间Tf=0.1min 。 5) 车φ46外圆
① 确定背吃刀量a p :单边加工余量为2.5mm ,一次加工完成,a p =2.5mm ; ② 确定进给量f :根据表5—102查得f=1.01 ~2mm/r ,查表5—5,根据机床的横向进计量,取f=1.02mm/r ;
③ 确定切削速度V C :根据表5—110查得Cv=189.8,v X =0.15,v y =0.20,m =0.20,修正系数MV K =1.0,HV K =1,hv K =0.82,v k r K =0.73,tv K =0.83,
刀
具
寿
命
T=60min
,
故
v y x p m v c K f
a T C V v
v ?=
=min /)83.073.082.004.10.102
.15.2608
.189(
2
.015.02
.0m ???????
=34.5m/min
④ 确定机床转速n :
w
c d v n π1000=
=
min /6.6616514.35
.341000r =?? 根据表5—5得,相机较小的转速为63r/min ,所以实际的切削速度为32.6m/min
⑤ 计算基本时间T j :车外圆主偏角K r =90.,查表5—138和表5—139得: l 1=2.5mm ,l 2= 0,l 3=,4mm ,L=116mm
T j =
=
i f L
n =+++i f l l l l n
32116302.145.2116??++min=1.9min ⑥ 辅助时间Tf :查表5—153得,换刀时间为0.02min ,取量具并测量尺
寸为0.5min ,共计Tf=0.52min 。
工序40
钻加工孔3×Ф10 1)钻孔3×Ф10
① 确定进给量f 。根据《机械制造技术课程设计指导》表5—113和表5—3,取f=0.02d 0=0.02×13mm/r=0.26mm/r 。
② 确定切削速度Vc ,查《机械制造技术课程设计指导》表5—113,取Vc=25m/min 。
③ 确定主轴转速n 。由n=
0c 1000d V π=π
1325
1000?r/min=612.44r/min 。查《机械制造技术课程设计指导》表5—4,得实际转速n=600r/min 。
④ 计算基本时间Tj 。被加工长度l=20mm,切入量
y=[
2
d 0c ot?+(1~2)]mm =[214
cot600+(1~2)] mm=4.75~5.75mm
式中d 0为钻头直径(mm );?为钻头半顶角,常为600。 取y=5mm,切除量Δ=4mm 。
Tj=
nf y ?++l =26
.06004520?++min=0.19min ⑤ 确定辅助时间Tf 。查《机械制造技术课程设计指导》表5—153得,工
件装夹和取下时间为0.75min,变速或变换进给量的时间为0..02,启动机床时间为0.02min ,共计Tf=0.79min 。
分析零件图——零件图的审查
分析零件图——零件图的审查 在制订零件的机械加工工艺规程之前,对零件进行工艺性分析,以及对产品零件图提出修改意见,是制订工艺规程的一项重要工作。 首先应熟悉零件在产品中的作用、位置、装配关系和工作条件,搞清楚各项技术要求对零件装配质量和使用性能的影响,找出主要的和关键的技术要求,然后对零件图样进行分析。 (1) 检查零件图的完整性和正确性 在了解零件形状和结构之后,应检查零件视图是否正确、足够,表达是否直观、清楚,绘制是否符合国家标准,尺寸、公差以及技术要求的标注是否齐全、合理等。 (2) 零件的技术要求分析 零件的技术要求包括下列几个方面:加工表面的尺寸精度;主要加工表面的形状精度;主要加工表面之间的相互位置精度;加工表面的粗糙度以及表面质量方面的其它要求;热处理要求;其它要求(如动平衡、未注圆角或倒角、去毛刺、毛坯要求等)。 要注意分析这些要求在保证使用性能的前提下是否经济合理,在现有生产条件下能否实现。特别要分析主要表面的技术要求,因为主要表面的加工确定了零件工艺过程的大致轮廓。 (3) 零件的材料分析 即分析所提供的毛坯材质本身的机械性能和热处理状态,毛坯的铸造品质和被加工部位的材料硬度,是否有白口、夹砂、疏松等。判断其加工的难易程度,为选择刀具材料和切削用量提供依据。所选的零件材料应经济合理,切削性能好,满足使用性能的要求。 (4) 合理的标注尺寸 ①零件图上的重要尺寸应直接标注,而且在加工时应尽量使工艺基准与设计基准重合,并符合尺寸链最短的原则。如图4-1中活塞环槽的尺寸为重要尺寸,其宽度应直接注出。
②零件图上标注的尺寸应便于测量,不要从轴线、中心线、假想平面等难以测量的基准标注尺寸。如图4-2中轮毂键槽的深度,只有尺寸c的标注才便于用卡尺或样板测量。 ③零件图上的尺寸不应标注成封闭式,以免产生矛盾。如图4-3所示,已标注了孔距尺寸a±δ和角度α±δα,则则x、y轴的坐标尺寸就不能随便标注。有时为了方便加工,可按尺寸链计算出来,并标注在圆括号内,作为加工时的参考尺寸。 ④零件上非配合的自由尺寸,应按加工顺序尽量从工艺基准注出。如图4-4的齿轮轴,图(a)的表示方法大部分尺寸要经换算,且不能直接测量。而图(b) 图4-1 直接标注重要尺寸图4-2 键槽深度的标注图4-3 孔中心距的标注 (a) (b)
典型零件的机加工工艺分析
第4章典型零件的机械加工工艺分析 本章要点 本章介绍典型零件的机械加工工艺规程制订过程及分析,主要内容如下:1.介绍机械加工工艺规程制订的原则与步骤。 2.以轴类、箱体类、拨动杆零件为例,分析零件机械加工工艺规程制订的全过程。 本章要求:通过典型零件机械加工工艺规程制订的分析,能够掌握机械加工工艺规程制订的原则和方法,能制订给定零件的机械加工工艺规程。 §机械加工工艺规程的制订原则与步骤 §机械加工工艺规程的制订原则 机械加工工艺规程的制订原则是优质、高产、低成本,即在保证产品质量前提下,能尽量提高劳动生产率和降低成本。在制订工艺规程时应注意以下问题: 1.技术上的先进性 在制订机械加工工艺规程时,应在充分利用本企业现有生产条件的基础上,尽可能采用国内、外先进工艺技术和经验,并保证良好的劳动条件。 2.经济上的合理性 在规定的生产纲领和生产批量下,可能会出现几种能保证零件技术要求的工艺方案,此时应通过核算或相互对比,一般要求工艺成本最低。充分利用现有生产条件,少花钱、多办事。 3.有良好的劳动条件 在制订工艺方案上要注意采取机械化或自动化的措施,尽量减轻工人的劳动强度,保障生产安全、创造良好、文明的劳动条件。 由于工艺规程是直接指导生产和操作的重要技术文件,所以工艺规程还应正确、完整、统一和清晰。所用术语、符号、计量单位、编号都要符合相应标准。必须可靠地保证零件图上技术要求的实现。在制订机械加工工艺规程时,如果发现零件图某一技术要求规定得不适当,只能向有关部门提出建议,不得擅自修改零件图或不按零件图去做。 §制订机械加工工艺规程的内容和步骤 1.计算零件年生产纲领,确定生产类型。 2.对零件进行工艺分析 在对零件的加工工艺规程进行制订之前,应首先对零件进行工艺分析。其主要内容包括: (1)分析零件的作用及零件图上的技术要求。
箱体类零件图加工工艺分析
零件图加工工艺分析 数控124 吴瑞港38 一、零件图样分析 分析零件图样是工艺准备中的首要工作,直接影响零件加工程序的编制及加工结果。首先熟悉零件在产品中作用、位置、装配关系和工作条件,搞清各项技术要求对零件装配质量和使用性能的影响,找出主要的和关键的技术要求,然后对零件图样进行分析。
(1)零件结构分析如上图箱体类零件,以铣加工与钻、镗加工为主。因此,本习题可用立式加工中心加工。该箱体零件由6个螺纹孔,俩个沉孔,俩个φ50的孔,100mm×80mm×10mm的型腔和120mm×70mm×70mm的型腔以及四块肋板组成。 (2)精度分析 a.尺寸精度精度要求较高的尺寸主要有:中心距(200±0.02)mm,以及两个型腔的尺寸外形尺寸。对于尺寸精度要求,主要通过在加工过程中的精确对刀;正确选用刀具和正确选用合适的加工工艺等措施来保证。 b.表面粗糙度孔的表面粗糙度和型腔内侧的表面为Ra1.6,其他为Ra3.2。对于表面粗糙度要求,主要通过选用正确的粗、精加工路线,选用合适的切削用量等措施来保证。 (3)确定加工工艺 a.选用φ20mm精齿立铣刀(加长切削刃型)精加工120mm×70mm×70mm、用φ14mm和φ20mm的精齿铣刀精加工沉孔、用中心钻定位6个螺纹孔用φ4.2mm的钻头和φ5mm的丝锥加工六个螺纹孔。 b.面用φ16mm的精齿立铣刀精加工底面100mm×80mm×10mm 的型腔、用φ10mm的球头刀加工四型腔四周的圆弧倒角。 c.用精镗刀加工φ50mm的孔。 (4)零件毛坯的工艺性分析 在对零件图进行工艺性分析后,还应结合数控加工的特点,对所用毛坯进行工艺性分析,否则毛坯不适合数控加工,加工将很难进行,
49厂典型零件工艺分析
发动机厂典型零件的结构及其工艺分析 1 汽车发动机缸体加工工艺分析 1.1 汽车发动机缸体结构特点及其主要技术要求 发动机是汽车最主要的组成部分,它的性能好坏直接决定汽车的行驶性能,故有汽车心脏之称。而发动机缸体是发动机的基础零件,通过它把发动机的曲柄连杆机构(包括活塞、连杆、曲轴、飞轮等零件)和配气机构(包括缸盖、凸轮轴、进气门、排气门、进气歧管、排气歧管、气门弹簧,气门导管、挺杆、挺柱、摇臂、摇臂支座、正时齿轮)以及供油、润滑、冷却等机构联接成一个整体。它的加工质量会直接影响发动机的性能。 1.1.1缸体的结构特点 由于缸体的功用决定了其形状复杂、壁薄、呈箱形。其上部有若干个经机械加的穴座,供安装气缸套用。其下部与曲轴箱体上部做成一体,所以空腔较多,但受力严重,所以它应有较高的刚性,同时也要减少铸件壁厚,从而减轻其重量,而气缸体内部除有复杂的水套外,还有许多油道。 1.1.2缸体的技术要求 由于缸体是发动机的基础件,它的许多平面均作为其它零件的装配基准,这些零件之间的相对位置基本上是由缸体来保证的。缸体上的很多螺栓孔、油孔、出砂孔、气孔以及各种安装孔都能直接影响发动机的装配质量和使用性能,所以对缸体的技术要求相当严格。现将我国目前生产的几种缸体的技术要求归纳如下: 1)主轴承孔的尺寸精度一般为IT5~IT7,表面粗糙度为Ral6—0.8μm,圆柱度为0.007~0.02mm,各孔对两端的同轴度公差值为¢0.025~0.04mm。 2)气缸孔尺寸精度为IT5~IT7,表面粗糙度为Ral.6~0.8μm,有止口时其深度公差为0.03~0.05mm,其各缸孔轴线对主轴承孔轴线的垂直度为0.05mm。 3)各凸轮轴轴承孔的尺寸精度为IT6~IT7,表面粗糙度为Ra3.2~0.8μm,各孔的同轴度公差值为0.03~0.04mm。
典型零件选材及工艺分析
典型零件选材及工艺分析 一,齿轮类 机床、汽车、拖拉机中,速度的调节和功率的传递主要靠齿轮机床、汽车和拖拉机中是一种十分重要、使用量很大的零件。 齿轮工作时的一般受力情况如下: (1)齿部承受很大的交变弯曲应力; (2)换当、启动或啮合不均匀时承受击力; (3)齿面相互滚动、滑动、并承受接触压应力。 所以,齿轮的损坏形式主要是齿的折断和齿面的剥落及过度磨损。据此,要求齿材料具有以下主要性能: (1)高的弯曲疲劳强度和接触疲劳强度; (2)齿面有高的硬度和耐磨性; (3)齿轮心部有足够高的强度和韧性。 此外,还要求有较好的热处理工艺性,如变形小,并要求变形有一定的规律等。下面以机床和汽车、拖拉机两类齿轮为例进行分析。 (一)机床齿轮 机床中的齿轮担负着传递动力、改变运动速度和运动方向的任务。一般机床中的齿轮精度大部分是7级精度(GB179-83规定,精度分12级,用1、2、3、……12表示,数字愈大者,精度愈低)。只是在他度传动机构中要求较高的精度。
机床齿轮的工作条件比起矿山机械、动力机械中的齿轮来说还属于运转平稳、负荷不大、条件较好的一类。实践证明,一般机床齿轮选用中碳钢制造,并经高频感应热处理,所得到的硬度、耐磨性、强度及韧性能满足要求,而县市频淬火具有变形小、生产率高等优点。 下面以C616机床中齿轮为例加以分析。 1、高频淬火齿轮的工工艺线 2、热处理工序的作用正火处理对锻造齿轮毛坯是必需的热处理工序,它可以使同批坯料具有相同的硬度,便于切削加工,并使组织均匀,消除锻造应力。对于一般齿轮,正火处理也可作为高频淬火前的最后热处理工序。 调质处理可以使齿轮具有较高的综合机械性能,提高齿轮心部的强度和韧性,使齿轮能承受较大的弯曲应力和冲击力。调质后的齿轮由于组织为回火索氏体,在淬火时变形更小。 高频淬火及低温回火是赋予齿轮表面性能的关键工序,通过高频淬火提高了齿轮表 面硬度和耐磨性,并使齿轮表面有压应力存在而增强了抗疲劳破坏的能力。为了消除淬火应力,高频淬火后应进行低温回火(或自行回火),这对防止研磨裂纹的产生和提高抗冲击能力极为有利。 3、齿轮高频淬火后的变形情况齿轮高频淬火后,其变形一般表现为内孔缩小,外径不变或减小。齿轮外径与内径之比小于1.5时,内径略胀大;当齿轮有键槽时,内径向键槽方向胀大,形成椭圆形,齿间椭圆形,齿间亦稍有变形,齿形变化较小,一般表现为中间凹0.002~0.0005㎜。这些微小的变形对生产影响不大,因为一般机床用的7级精度齿轮,淬火回火后,均要经过滚光和推孔才成为成品。
典型轴类零件加工工艺分析
阶梯轴加工工艺过程分析? 图6—34为减速箱传动轴工作图样。表6—13为该轴加工工艺过程。生产批量为小批生产。材料为45热轧圆钢。零件需调质。
(一)结构及技术条件分析??该轴为没有中心通孔的多阶梯轴。根据该零件工作图,其轴颈M、N,外圆P,Q及轴肩G、H、I有较高的尺寸精度和形状位置精度,并有较小的表面粗糙度值,该轴有调质热处理要求。?
(二)加工工艺过程分析? 1.确定主要表面加工方法和加工方案。 传动轴大多是回转表面,主要是采用车削和外圆磨削。由于该轴主要表面M,N,P,Q的公差等级较高(IT6),表面粗糙度值较小(Ra0.8μm),最终加工应采用磨削。其加工方案可参考表3-14。 2.划分加工阶段 该轴加工划分为三个加工阶段,即粗车(粗车外圆、钻中心孔),半精车(半精车各处外圆、台肩和修研中心孔等),粗精磨各处外圆。各加工阶段大致以热处理为界。 3.选择定位基准 轴类零件的定位基面,最常用的是两中心孔。因为轴类零件各外圆表面、螺纹表面的同轴度及端面对轴线的垂直度是相互位置精度的主要项目,而这些表面的设计基准一般都是轴的中心线,采用两中心孔定位就能符合基准重合原则。而且由于多数工序都采用中心孔作为定位基面,能最大限度地加工出多个外圆和端面,这也符合基准统一原则。 但下列情况不能用两中心孔作为定位基面: ?(1)粗加工外圆时,为提高工件刚度,则采用轴外圆表面为定位基面,或以外圆和中心孔同作定位基面,即一夹一顶。? (2)当轴为通孔零件时,在加工过程中,作为定位基面的中心孔因钻出通孔而消失。为了在通孔加工后还能用中心孔作为定位基面,工艺上常采用三种方法。 ①当中心通孔直径较小时,可直接在孔口倒出宽度不大于2mm的60o内锥面来代替中心孔;
典型零件的加工工艺分析案例
典型零件的加工工艺分析案例 实例. 以图A-54所示的平面槽形凸轮为例分析其数控铣削加工工艺。 图A-54 平面槽型凸轮简图 案例分析: 平面凸轮零件是数控铣削加工中常用的零件之一,基轮廓曲线组成不外乎直线—曲线、圆弧—圆弧、圆弧—非圆曲线及非圆曲线等几种。所用数控机床多为两轴以上联动的数控铣床,加工工艺过程也大同小异。 1. 零件图纸工艺分析 图样分析要紧分析凸轮轮廓形状、尺寸和技术要求、定位基准及毛坯等。 本例零件是一种平面槽行凸轮,其轮廓由圆弧HA、BC、DE、FG和直线AB、HG以及过渡圆弧CD、EF所组成,需要两轴联动的数控机床。材料为铸铁、切削加工性较好。 该零件在数控铣削加工前,工件是一个通过加工、含有两个基准孔直径为φ280mm、厚度为18mm的圆盘。圆盘底面A及φ35G7和φ12H7两孔可用作定位基准,无需另作工艺孔定位。 凸轮槽组成几何元素之前关系清晰,条件充分,编辑时所需基点坐标专门容易求得。 凸轮槽内外轮廓面对A面有垂直度要求,只要提升装夹度,使A面与铣刀轴线垂直,即可保证:φ35G7对A面的垂直度要求由前面的工序保证。 2. 确定装夹方案
一样大型凸轮可用等高垫块垫在工作台上,然后用压板螺栓在凸轮的孔上压紧。外轮廓平面盘形凸轮的垫板要小于凸轮的轮廓尺寸,不与铣刀发生干涉。对小型凸轮,一样用心轴定位,压紧即可。 按照图A-54所示凸轮的结构特点,采纳“一面两孔”定位,设计一“一面两销”专用夹具。用一块320mm×320mm×40mm的垫块,在垫块上分别精镗φ35mm及φ12mm两个定位销孔的中心连接线与机床的x轴平行,垫块的平面要保证与工作台面平行,并用百分表检查。 图A-55为本例凸轮零件的装夹方案示意图。采纳双螺母夹紧,提升装夹刚性,防止铣削时因螺母松动引起的振动。 图A-55凸轮装夹示意图 3. 确定进给路线 进给路线包括平面内进给和深度进给两部分路线。对平面内进给,对外凸轮廓从切线方向切入,对内凹轮廓从过渡圆弧切入。在两轴联动的数控铣床上,对铣削平面槽形凸轮,深度进给有两种方法:一种是xz(或yz)平面来回铣削逐步进刀到即定深度;另一种方法是先打一个工艺孔,然后从工艺孔进刀到即定深度。 本例进刀点选在(150,0),刀具在y+15之间来回运动,逐步加深铣削深度,当达到即定深度后,刀具在xy平面内运动,铣削凸轮轮廓。为保证凸轮的工件表面有较好的表面质量,采纳顺铣方式,即从(150,0)开始,对外凸轮廓,按顺时针方向铣削,对内凸轮廓按逆时针方向铣削,图A -56所示为铣刀在水平面的切入进给路线。 图A-56 平面槽形凸轮的切入进给路线 4. 选择刀具及切削用量 铣刀材料和几何参数要紧按照零件材料切削加工性、工件表面几何形状和尺寸大小不一选择;切削用量则依据零件材料特点、刀具性能及加工
轴套零件的工艺分析和编程(毕业设计)
零件图
轴套三维图
轴套三维图
轴套类零件的工艺设计与加工 摘要:随着数控技术的发展,数控技术的应用不但给传统制造业带来了革命性的变化,使制造业成为工业化的象征,而且随着数控技术的不断发展和应用领域的扩大,它对国计民生的一些重要行业的发展起着越来越重要的作用。随着科技的发展,数控技术也在不断的发展更新,现在数控技术也称计算机数控技术,加工软件的更新快,CAD/CAM 的应用是一项实践性很强的技术。如像UG , PRO/E , Cimitron , MasterCAM ,CAXA制造工程师等。 数控技术是技术性极强的工作,尤其在模具领域应用最为广泛,所以这要求从业人员具有很高的机械加工工艺知识,数控编程知识和数控操作技能。本文主要通过c 车削加工配合件的数控工艺分析与加工,综合所学的专业基础知识,全面考虑可能影响在车削加工中的因素,设计其加工工艺和编辑程序,完成配合要求。 关键词: 车削;CAD/CAM;配合件零件加工
前言 毕业设计是专业教学工作的重要组成部分和教学过程中的重要实际性环节。 毕业设计的目的是:通过设计,培养我们综合运用所学的基础理论知识,专业理论知识和一些相关软件的学习,去分析和解决本专业范围内的一般工程技术问题的能力,培养我们建立正确的工艺设计思维,学会查找工具书,掌握数控工艺设计的一般程序,规范和方法。 本次设计选择的课题为轴类零件的车削加工工艺设计及其数控加工程序编制。 这次毕业设计让我们对机械制图的基础知识有了进一步的了解,同时也 为我们从事绘图工作奠定了一个良好的基础。并锻炼了自己的动手能力,达到了学以致用的目的。它是一次专业技能的重要训练和知识水平的一次全面体验,是学生毕业资格认定的重要依据,同时也为我们将来走向
车床零件加工工艺
轴类零件的数控加工工艺分析与编制 班级 姓名 学号 综合成绩 项目一轴类零件的数控加工工艺分析与编制 零件图 项目一轴类零件的数控加工工艺分析与编制 零件图 任务一、零件图纸的工艺分析 该零件由圆柱、槽、螺纹等表面形成 设计基准径向以轴线为基准,轴向以工件右端面为基准。 未注倒角C1 表面粗糙度为Ra3.2,Ra1.6 工件材料为45钢 任务二、工艺路线的拟定 1、表面加工的方法 粗车---精车 粗车1.5 精车0.5 精度等级 IT7,IT8 表面粗糙度 3.2,1.6 2、毛坯尺寸 ?15mm*145mm 3、工序划分 任务三、机床的选择 零件毛坯尺寸:?35mm*145mm 零件最高精度:IT7,IT8 刀具类型:外圆车刀、螺纹刀 机床:CK6141 机床参数 主电机功率:4000(kw)
刀具数量:4 最大加工长度:1000(mm) 最大加工直径:58(mm) 最大回转直径:224(mm) 精度级:IT6~IT8 卡盘:三爪卡盘 任务四、装夹方案及夹具的选择 通过对刀的方式找基准 径向基准为轴线 轴向基准为工件两端面 夹具为三爪卡盘 任务五、刀具的选择 工件材料:45钢 刀具材料:硬质合金(刀片) P类:精JC215V(黛杰) 粗JC450V 适用加工结构钢、工具钢、耐热钢、铸钢可锻造钢,是钢材连续切削加工首选刀具材料 任务六、刀片规格 外圆车刀 CNMG080404 切槽刀 N123H2-03 50-0004-GF 螺纹刀 R166.0G-16MM01-150 任务五、刀具的选择 工件材料:45钢 刀具材料:硬质合金(刀片) P类:精JC215V(黛杰) 粗JC450V 适用加工结构钢、工具钢、耐热钢、铸钢可锻造钢,是钢材连续切削加工首选刀具材料 任务六、刀片规格 外圆车刀 CNMG080404 切槽刀 N123H2-03 50-0004-GF 螺纹刀 R166.0G-16MM01-150 任务七、切削用量的选择 1.8切削用量选择
零件图分析
九、读零件图,并回答问题。(18分) (1)该零件采用了哪些视图、剖视图或其它表达方法?说明数量和名称。 B-B、C-C断面图及D-D局部 Φ45孔的轴线 (3)Φ40H7表示:基本尺寸为Φ40的孔,H7为公差带代号,H为基本偏差代号,7为公差等级。 (4)M68╳2表示,公称直径为68mm的普通细牙螺纹,M为螺纹代号,2为螺距。 (5)左视图外形略 (6)前者表示用去除材料的方法获得的表面粗糙度,Ra的值为6.3μm.;后者表示是由不去除材料的方法获得的零件表面。 八、读零件图并回答下列问题. (1)该零件采用了哪些视图、剖视图或断面图? (2)指出该零件在长、宽、高三个方向的主要尺寸基准。 (3)说明Φ40H7的意义。 (4)说明M8—7H的含义。 (5)标出各剖视图的剖切平面位置。 (6)说明符号的含义。 答案: (1)该零件图中,主视图采用了局部剖视图,左视图采用半剖视图,俯视图采用全剖视图。 (2)长度方向的基准是长度对称线,高度方向基准是零件底边,宽度方向基准是宽度对称线。 (3)Φ40H7表示:基本尺寸为Φ40的孔,H7为公差带代号,H为基本偏差代号,7为公差等级。 (4)M8—7H表示,公称直径为8mm的普通螺纹,M为螺纹代号,7H为中径的公差带代号。 (5)(图略) 6.表示主视图中右侧Φ40H7孔的中心轴线相对于左侧Φ40孔的中心轴线的同轴度公差为Φ0.02。
8. 在总体上很难说……是好还是坏,因为它在很大程度上取决于……的形势。然而,就我个人而言,我发现……。 It is difficult to say whether _____is good or not in general as it depends very much on the situation of______. However, from a personal point of view find______.
数控车床零件图15加工及工艺分析
数控车床零件图(15)加工及工艺分析 作者:李沂 摘要:当前数控技术的发展速度很快,作为一个机加工行业的人来说做好一份 设计是非常重要的。根据零件图纸的要求,从材料的选择,刀具的选用,装夹方案的确定,加工路线的设计,数值的计算,加工参数的设定,程序的编写,仿真加工,最后加工出符合零件图纸尺寸要求和形状要求的产品。 关键字:数控 , 加工 ,工艺分析 , 刀具 一、课程设计的目的 课程设计是在学完本专业所设的相关课程,并进行生产实习的基础上检查学生所学的基础理论知识与实际生产经验相结合的能力。它要求学生较全面地综合运用本专业及其有关课程的理论和实践知识,进行相应科目的课程设计。 本课程设计是数控加工工艺与编程课程设计,具体设计内容为:根据给定工件图纸,编写加工工艺规程,并说明工艺装备仪器和各项参数的计算和选取方法。其设计目的在于: 1、培养学生运用机械制造工艺学与所涉及的有关课程(机械制造基础与实践、机械设计基础、互换性与检测技术、机械制图、AutoCAD、数控机床等)的知识,结合生产实习中掌握的实践技能,独立地分析和解决工艺问题,编写工艺规程的能力。 2、培养学生熟悉并运用有关手册、规范、图表等技术资料的能力。 3、进一步巩固和加深学生识图、计算机绘图、参数计算、数控编程和编写技术文件等基本技能。 二、数控机床故障诊断与维修 随着电子技术和自动化技术的发展,数控技术的应用越来越广泛。以微处理器为基础,以大规模集成电路为标志的数控设备,已在我国批量生产、大量引进和推广应用,它们给机械制造业的发展创造了条件,并带来很大的效益。但同时,由于它们的先进性、复杂性和智能化高的特点,在维修理论、技术和手段上都发生了飞跃的变化。 数控维修技术不仅是保障正常运行的前提,对数控技术的发展和完善也起到了巨大的推动作用,因此,目前它已经成为一门专门的学科。 另外任何一台数控设备都是一种过程控制设备,这就要求它在实时控制的每一时刻都准确无误地工作。任何部分的故障与失效,都会使机床停机,从而造成生产停顿。因而对数控系统这样原理复杂、结构精密的装置进行维修就显得十分必要了。尤其对引进的CNC机床,大多花费了几十万到上千万美元。在许多行业中,这些设备均处于关键的工作岗位,若在出现故障后不及时维修排除故障,就会造成较大的经济损失。 我们现有的维修状况和水平,与国外进口设备的设计与制造技术水平还存在
典型零件的机械加工工艺的分析
型零件的机械加工工艺分析 本章要点 本章介绍典型零件的机械加工工艺规程制订过程及分析,主要内容如下: 1.介绍机械加工工艺规程制订的原则与步骤。 2.以轴类、箱体类、拨动杆零件为例,分析零件机械加工工艺规程制订的全过程。 本章要求:通过典型零件机械加工工艺规程制订的分析,能够掌握机械加工工艺规程制订的原则和方法,能制订给定零件的机械加工工艺规程。 §4.1 机械加工工艺规程的制订原则与步骤§4.1.1机械加工工艺规程的制订原则 机械加工工艺规程的制订原则是优质、高产、低成本,即在保证产品质量前提下,能尽量提高劳动生产率和降低成本。在制订工艺规程时应注意以下问题: 1.技术上的先进性 在制订机械加工工艺规程时,应在充分利用本企业现有生产条件的基础上,尽可能采用国内、外先进工艺技术和经验,并保证良好的劳动条件。 2.经济上的合理性 在规定的生产纲领和生产批量下,可能会出现几种能保证零件技术要求的工艺方案,此时应通过核算或相互对比,一般要求工艺成本最低。充分利用现有生产条件,少花钱、多办事。 3.有良好的劳动条件 在制订工艺方案上要注意采取机械化或自动化的措施,尽量减轻工人的劳动强度,保障生产安全、创造良好、文明的劳动条件。 由于工艺规程是直接指导生产和操作的重要技术文件,所以工艺规程还应正确、完整、统一和清晰。所用术语、符号、计量单位、编号都要符合相应标准。必须可靠地保证零件图上技术要求的实现。在制订机械加工工艺规程时,如果发现零件图某一技术要求规定得不适当,只能向有关部门提出建议,不得擅自修改零件图或不按零件图去做。 §4.1.2 制订机械加工工艺规程的内容和步骤 1.计算零件年生产纲领,确定生产类型。 2.对零件进行工艺分析 在对零件的加工工艺规程进行制订之前,应首先对零件进行工艺分析。其主要内容包括: (1)分析零件的作用及零件图上的技术要求。 (2)分析零件主要加工表面的尺寸、形状及位置精度、表面粗糙度以及设计基准等; (3)分析零件的材质、热处理及机械加工的工艺性。 3.确定毛坯
零件的工艺性分析
零件的工艺性分析 一、分析研究产品的零件图样和装配图样在编制零件机械加工工艺规程前,首先应研究零件的工作图样和产品装配图样,熟悉该产品的用途、性能及工作条件,明确该零件在产品中的位置和作用;了解并研究各项技术条件制订的依据,找出其主要技术要求和技术关键,以便在拟订工艺规程时采用适当的措施加以保证。工艺分析的目的,一是审查零件的结构形状及尺寸精度、相互位置精度、表面粗糙度、材料及热处理等的技术要求是否合理,是否便于加工和装配;二是通过工艺分析,对零件的工艺要求有进一步的了解,以便制订出合理的工艺规程。 如图3-8 所示的汽车钢板弹簧吊耳,使用时,钢板弹簧与吊耳两侧面是不接触的,所以吊耳内侧的粗糙度可由原来的设计要求R a3.2 μ m 建议改为R a12.5 μ m. 。这样在铣削时可只用粗铣不用精铣,减少铣削时间。 再如图3-9 所示的方头销,其头部要求淬火硬度55~60HRC ,所选用的材料为T 8A ,该零件上有一孔φ 2H7 要求在装配时配作。由于零件长度只有15mm ,方头部长度仅有4mm ,如用T 8A 材料局部淬火,势必全长均被淬硬,配作时,φ 2H7 孔无法加工。若建议材料改用20Cr
进行渗碳淬火,便能解决问题。 二、结构工艺性分析零件的结构工艺性是指所设 计的零件在满足使用要求的前提下,制造的可行性和经济性。下面将从零件的机械加工和装配两个方面,对零件的结构工艺性进行分析。(一)机械加工对零件结构的要求 1 .便于装夹零件的结构应便于加工时的定位和夹紧,装 夹次数要少。图3 -10a 所示零件,拟用顶尖和鸡心夹头装夹,但该结构不便于装夹。若改为图b 结构,则可以方便 地装置夹头。 2 .便于加工零件的结构应尽量采用标准化数值,以便使用标准化刀具和量具。同时还注意退刀和进刀,易于保证加工精度要求,减少加工面积及难加工表面等。表3-8b 所示为便于加工的零件结构示例。 3 .便于数控机床加工被加工零件的数控工艺性 问题涉及面很广,下面结合编程的可能性与方便性来作工艺性分析。 编程方便与否常常是衡量数控工艺性好坏的一个 指标。例如图3-11 所示某零件经过抽象的尺寸标注方法,若用APT 语言编写该零件的源程序,要用几何定义语句描
数控机床轴类零件加工工艺分析
数控机床轴类零件加工工 艺分析 Prepared on 22 November 2020
X X X学院 毕业 设计 任务书 论文 机械工程系数控技术专业 XX 班 毕业设计 题目 数控机床轴类零件加工工艺分析论文 专题题目 数控机床轴类零件加工工艺分析 发题日期:2010年11月15日设计、论文自2010年11月20日完成期限:至2010年月日答辩日期:2010年月日 学生姓名: 指导教师: 系主任:
毕业设计版权使用授权书 本人完全了解云南机电职业技术学院关于收集、保存、使用毕业设计的规定,同意如下各项内容:按照学校要求提交毕业设计的印刷本和电子版本;学校有权保存毕业设计的印刷本和电子版,并采用影印、缩印、扫描、数字化或其它手段保存毕业设计;学校有权提供目录检索以及提供本
毕业设计全文或者部分的阅览服务;学校有权按有关规定向国家有关部门或者机构送交毕业设计的复印件和电子版;在不以赢利为目的的前提下,学校可以适当复制毕业设计的部分或全部内容用于学术活动。 作者签名: 年月日 作者签名: 年月日 摘要 世界制造业转移,中国正逐步成为世界加工厂。美国、德国、韩国等国家已经进入发展的高技术密集时代与微电子时代,钢铁、机械、化工等重化工业发展中期。 由于数控机床综合应用了电子计算机、自动控制、伺服系统、精密检测与新型机械结构等方面的技术成果,具有高的高柔性、高精度与高度自动化的特点,因此,采用数控加工手段,解决了机械制造中常规加工技术难以解决甚至无法解决的单件、小批量,特别是复杂型面零件的加工,应用数控加工技术是机械制造业的一次技术革命,使机械制造的发展进入了一个新的阶段,提高了机械制造业的制造水平,为社会提供高质量,多品种及高可靠性的机械产品。 本次设计主要是对数控加工工艺进行分析与具体零件图的加工,首先对数控加工技术进行了简单的介绍,然后根据零件图进行数控加工分析。第一,根据本零件材料的加工工序、切削用量以及其他相关因素选用刀具及
机械制图零件图、装配图题库(有难度)分析
-------------------------------------密-----------------------封-----------------------线--------------------------------- 班级___________ 考场__________ 姓名______________ 学号_________ 徐工技校2011至2012学年度第二学期 《机械制图》期终考试试题库(零件图、装配图) 一、填空题(每空1分) 第九章 零件图 1. 主视图的投影方向应该能够反映零件的 。(难度:A ) 2. 和 公差简称为形位公差(难度:A ) 3. 尺寸公差带是由 和 两个要素组成。 确定公差带位置, 确定公差带大小。(难度:A ) 4. 配合有 和 两种基准制。配合分成间隙配合 、 和 三类。(难度:A ) 5. 允许尺寸变动的两个 称为极限尺寸。(难度:A ) 6. 极限与配合在零件图上的标注,其中一种形式是在孔或轴的基本尺寸后面注出基本偏差代号和公差等级,这种形式用于 的零件图上。第二种形式是在孔或轴的基本尺寸后面,注出偏差值,这种形式用于 的零件图上。第三种是在孔或轴的基本尺寸后面,既注出基本偏差代号和公差等级,又同时注出上、下偏差数值,这种形式用于 的零件图上。(难度:B ) 7. 形位公差的框格用 线绘制,分成 格或多格 。(难度:A ) 8. 按作用不同,可将基准分为 基准和 基准。(难度:A ) 9. 基孔制的孔(基准孔)的基本偏差代号用 符号表示,其基本偏差值为 。基轴制的轴(基准轴)的基本偏差代号用 符号表示,其基本偏差值为 。(难度:A ) 10. 基本偏差是决定公差带相对零线位置的 。(难度:A ) 11. 外螺纹的规定画法是:大径用 表示;小径用 表示;终止线用 表示。(难度:A ) 12. 当被连接零件之一较厚,不允许被钻成通孔时,可采用 连接。(难度:A ) 13. 剖切平面通过轴和键的轴线或对称面,轴和键均按 形式画出,键的顶面和轮毂键槽的底面有间隙,应画 条线。(难度:A ) 14. Tr40×14(P7)LH-8e-L 的含义_____________________________________________(难度:B ) 15. 模数大,齿距 ,齿厚、齿高也随之 ,因而齿轮的承载能力 。(难度:B ) 16. 螺纹的旋向有 和 两种,工程上常用 螺纹。(难度:B ) 17. 单个圆柱齿轮的剖视图中,当剖切平面通过齿轮的轴线时,轮齿一律按 绘制,齿根线画成 线。(难度:B ) 18. 普通平键有 、 和 三种结构类型。(难度:B ) 19. 左旋螺纹要注写 。(难度:A ) 20. 普通平键的标记:键 GB/T1096 18×11×100表示b= mm ,h= mm ,L= mm 的A 型普通平键(A 省略不注)。(难度:B ) 第十章 装配图 1. 在装配图中,当剖切平面通过某些标准产品的组合件,或该组合件已由其他图形表达清楚时,可只画出 。(难度:A ) 2. 装配图中的明细栏画在装配图右下角标题栏的 方,栏内分格线为 线,左边外框线为 线。(难度:A ) 3. 两个零件的接触表面,只用 条共有的轮廓线表示;非接触面画 条轮廓线。(难度:A ) 4. 装配图中的 ,用来表达机器(或部件)的工作原理、装配关系和结构特点。(难度:A ) 5. 在装配图中 尺寸表示机器、部件规格或性能的尺寸。(难度:A ) 6. 在各视图中,同一零件的剖面线方向与间隔必须 。(难度:A ) 7. 装配图中的指引线应自所指引部分的可见轮廓内引出,并在指引线末端画一 。若所指部分不便于画圆点时,可在指引线末端画 ,并指向该部分的轮廓线。(难度:A ) 8. 一张完整的装配图包括以下几项基本内容: 、 、 和标题栏、零件序号、明细栏。(难度:A ) 9. 装配图中零件序号应自下而上,如标题栏上方位置不够时,可将明细栏顺序画在标题栏的
零件图样分析
1.零件图样分析1.1根据零件简图分析: 该轴零件的结构具有如下特点:从形状上看该工件阶梯机构的花键轴,长度与直径比L/D≈5,所以该工件属于刚性轴。从表面加工类型看,主要加工表面有圆柱面、花键、键槽、螺纹等,属于典型的加工表面,加工容易。但有些表面精度要求较高,需要进行磨削才能满足要求。尺寸精度:1.2两端轴为±0.008,中间轴段、,花键002625??20?03.0.03?0? 外圈,键齿宽,键槽宽度,键槽底玉外圆母001.?0.01505?338065..06??0.0300?线的距 离左端面与花键左端的距离±0.3,花键左端,0225710.?与花键轴总长。轴右端面的距离95±0.3,0016626?080?.01.?0 1.3形位公差: 螺纹M24×1.5的左端面和的左端面相对于A、B026?01.?0两基面轴线的圆跳动公差为0.04mm,花键齿面相对于A、B两基面轴线的平 行度公差为38∶0.03mm,键槽玉花键轴线的对称度为0.05mm。 1.4表面粗糙度:两端轴±0.008外圆和、外圆为0026?25?20?03.?003?0.=0.8,花键齿面及左端面、螺纹M24×1.5的左端面和R?m a的右端面为=1.6,螺纹M24×1.5和花键右端面R0?26?m010?.a 1 为=3.2,其余为=6.3。RR??mm aa 1.5原图的错误并改正:1.的越层槽改为。19??92.的螺纹退刀槽改为。20??233.未注倒角为C1。 零件材料分析2 2.1图中要求的材料为40Cr. 40Cr经调制处理后,
550℃~570℃回火,具有良好的综合力学性能,低温冲击性极低的缺口敏感性,淬透性良好。油淬时可获得较高的疲劳强度,水淬时复杂形状的零件高裂纹,冷弯形塑性中等,正火或调质后,切削加工性好,但焊接性不佳,易产生裂纹,焊接前应须加热到100~150℃,一般在调质状态下使用,还可以氰化,因淬透性高于45号刚,所以还可以高频淬火处理,火焰淬火等表面硬化处理。 临界点温度Acm=780℃,正火规范;850~870℃,硬度179~229HBS,调质处理规范,淬火温度850℃±10℃。油冷,回火温度520℃±10℃。水、油冷。 40Cr的硬度:40Cr调质以后的硬度大概在HBS32~36之间,也就是说大概HBS330~380之间。 40铬(40 Cr)是碳含量为0.37%~0.45%,硅含量为2 0.17%~0.37%,锰含量为0.5%~0.8%,铬含量为0.8%~1.1%的合金结构钢。。价格适中,加工容易,经适当的热处理以后可以获得一定的韧性,塑性和耐磨性,正火可促进组织的球化,改进硬度小于160HBS 毛坯的切削性能。淬火表面硬度可达45~52HBS。 3.确定毛坯3.1毛坯类型 毛坯是用来加工各种工件的坯料,毛坯主要有:铸件,锻件,焊件,冲压件及型材等。 件)铸(1对形状较复杂的毛坯,一般可以用铸造的方法制造。目前大多数铸件采用砂型铸造,对尺寸精度要求较高的小型铸件,可采
零件的工艺性分析
零件的工艺性分析-标准化文件发布号:(9456-EUATWK-MWUB-WUNN-INNUL-DDQTY-KII
零件的工艺性分析 如图所示为接触环零件图,材料为08钢,厚度1mm,大批量生产。制定工件冲压工艺规程,设计其模具,编制零件的加工工艺规程。 6.5+0.1-0 1.1冲压件的工艺性分析 1.1.1结构与尺寸 1、由该冲压零件图可知,该零件结构简单、规则,而且尺寸较小,使得排样时废料较少。 2、冲压件的内、外的转角无太尖锐的尖角,部分区域以圆弧过渡,减少了冲压时某些尖角出出现崩刃和过快磨损现象。 3、对于08钢材料,其悬臂宽度b=1.5mm ,厚度t=1mm ,应满足b ≥1.5t ,当板料t>1mm 时按1mm 考虑,经计算悬臂宽度满足条件;臂长l 为:3.25和 1.3均小于5倍臂宽;凹槽宽度1.65>1.5t ,最小孔径d 为1.85>0.9t ,均满足要求。 结合以上分析,该冲压件的结构与尺寸均适宜于冲压加工。 1.1.2 精度 冲压件的经济精度一般不高于IT11,查表可知,该零件的基本尺寸公差除9.4接近于IT11级外,其余尺寸均低于IT12级,也没有其他特殊的要求。分析可知可知,利用普通冲裁方式可以达到零件图样要求。
1.1.3材料 根据本次设计课题材料要求为08钢,根据附表可得金属材料的力学性能:软态,带料,抗剪强度b=255MPa,伸长率占10=38%,分析可知,此材料具有较高的弹性和良好的塑性,其冲裁加工性能较好,适合冲裁加工。 1.1.4批量 课题要求该零件需大批量生产,综上分析可知,该零件在冲压加工下操作简便, 而且劳动强度低,生产效率高,成本较低,适合冲裁加工。 结论:该零件的工艺性较好,可以冲裁加工。 1.2冲裁工艺方案的确定 1.2.1工艺方案分析与选择 根据冲压零件图,分析其形状特点,确定该零件加工包括落料,冲孔两个基本工序,分析可知由以下3种工艺方案选择: (1)先落料,再冲孔。采用单工序模生产。 (2)落料—冲孔复合冲压,采用复合模生产。 (3)冲孔—落料连续冲压,采用连续模(级进模)生产。 结合单工序模、复合模以及级进模的优缺点比较可知: 方案(1)制造时上午周期短,成本也较低,但需要两道工序,导致生产效率低,且零件平面度差。难以满足零件大批量生产的需要。 方案(2)生产效稍低,因零件的孔边距太小,导致模具强度不能保证,操作较为困难,且不能保证安全性。 方案(3)生产效率高,操作方便,安全性好,通过设计合理的模具结构和排样方案可以达到较好的零件质量和避免模具强度不够的问题。 综合以上分析,并参考相关资料,可知该零件采用级进冲裁方案较好。1.3模具确定 1.3.1模具类型 根据冲压零件的冲裁方案以及设计要求,模具应采用硬质合金模。 1.3.2操作与定位方式
机械加工工艺分析与改进设计毕业论文
机械加工工艺分析与改进设计 作者:陈军 摘要:我们必须仔细了解零件结构,认真分析零件图,培养我们独立识图能力,增强我们对零件图的认识和了解,通过对零件图的绘制,不仅能增强我们的绘图能力和运用autoCAD软件的能力。
目录 摘要 (1) 目录 (2) 绪论 (3) 第三章:30*40专用夹具的设计 (11) 3.1专用夹具的设计要求 (11) 3.2夹具设计 (12) 总结 (16)
参考资料 (16) 绪论 本课题是对制动杆零件工艺规程及40×30面铣削夹具的设计,对此研究我查阅了大量的资料,首先明白机械加工工艺过程就是用切削的方法改变毛坯的形状、尺寸和材料的物理机械性质成为具有所需要的一定精度、粗糙度等的零件。 1 2 3 1 2 4、毛坯的选择 1)毛坯的种类 铸造毛坯:适合做形状复杂的零件。 锻造毛坯:适合做形状简单的零件。
型材:适合做轴、平板类零件。 焊接毛坯:适合做板类、框架类零件。 2)毛坯选择的原则 选择原则:毛坯的形状和尺寸应尽量接近零件的形状和尺寸以减少机械加工。 毛坯选择应考虑的因素: 2 1 2 3 精基准:采用加工过的表面作为基准。 基准的选择遵循以下四个原则 1)基准重合原则:(1)设计基准与定位基准不重合误差只会发生在用调整法获得加工尺寸的情况。 (2)基准不重合误差值等于设计基准与定位基准之间的差值。
2)基准统一原则:整个工艺过程或有关几道工序采用同一个定位基准来定位。 采用基准统一原则有利于:(1)简化工艺过程的制定及夹具的设计。 (2)避免基准转换带来误差。 3) 互为基准:使加工面间有较高的位置精度,又使其加工余量小而均匀,可采用反复加工互为基准原则。 4 1 1 1 2 3 2 1 2)要考虑被加工材料的性质。 3)要考虑生产纲领,及生产率和经济效率。 4)要考虑现有设备和生产条件。 1.4工艺路线的拟定
零件的工艺分析
零件的工艺分析 零件的材料为HT200,灰铸铁生产工艺简单,铸造性能优良,但塑性较差、脆性高,为此以下是杠杆需要加工表面以及加工表面的位置要求。现分析如下: (1)主要加工面: 1)小头钻Φ以及与此孔相通的Φ14阶梯孔、M8螺纹孔; 2)钻Φ锥孔及铣Φ锥孔平台; 3)钻2—M6螺纹孔; 4)铣杠杆底面及2—M6螺纹孔端面。 (2)主要基准面: 1)以Φ45外圆面为基准的加工表面 这一组加工表面包括:Φ的孔、杠杆下表面 2)以Φ的孔为中心的加工表面 这一组加工表面包括:Φ14阶梯孔、M8螺纹孔、Φ锥孔及Φ锥孔平台、2—M6螺纹孔及其倒角。其中主要加工面是M8螺纹孔和Φ锥孔平台。 杠杆的Φ25孔的轴线合两个端面有着垂直度的要求。现分述如下: 本套夹具中用于加工Φ25孔的是立式钻床。工件以Φ25孔下表面及Φ45孔外圆面为定位基准,在定位块和V型块上实现完全定位。加工Φ25时,由于孔表面粗糙度为。主要采用钻、扩、铰来保证其尺寸精度。 本套夹具中用于加工杠杆的小平面和加工Φ12.7是立式铣床。工件以孔及端面和水平面底为定位基准,在长销、支承板和支承钉上实现完全定位。加工表面:包括粗精铣宽度为30mm 的下平台、钻Ф12.7的锥孔,由于30mm的下平台的表面、孔表面粗糙度都为。其中主要的加工表面是孔Ф12.7,要用Ф12.7钢球检查。 本套夹具中用于加工与Φ25孔相通的M8螺纹底孔是用立式钻床。工件以孔及其下表面和宽度为30mm的下平台作为定位基准,在大端面长圆柱销、支承板和支承钉上实现完全定位。加工M8螺纹底孔时,先用Φ7麻花钻钻孔,再用M8的丝锥攻螺纹。 2.2杠杆加工的主要问题和工艺过程设计所应采取的相应措施2.2.1确定毛坯的制造形式