薄壁板高速铣削加工过程中的让刀误差预测
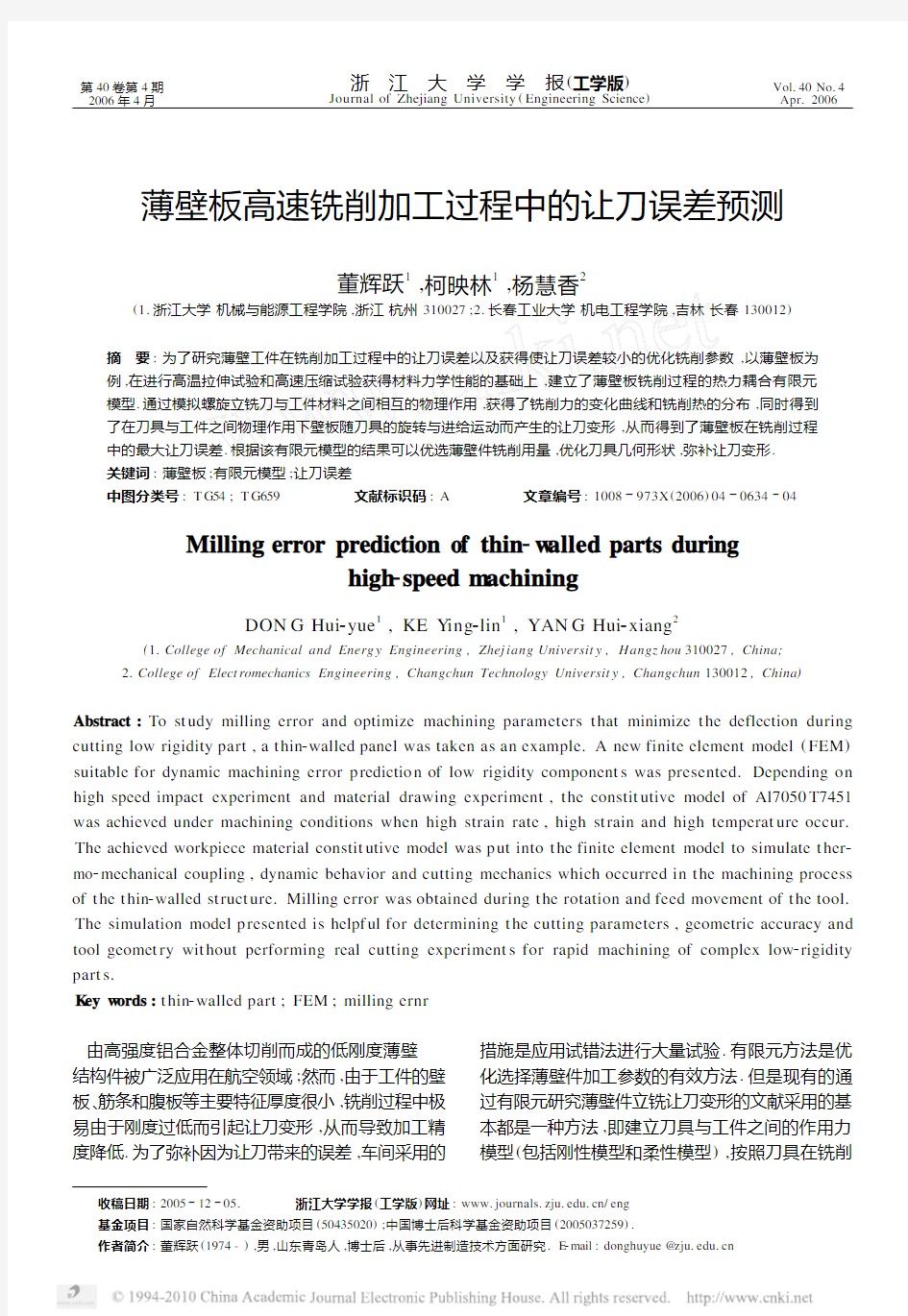

第40卷第4期2006年4月
浙 江 大 学 学 报(工学版)
Journal of Zhejiang University (Engineering Science )
Vol.40No.4
Apr.2006
收稿日期:20051205.
浙江大学学报(工学版)网址:https://www.360docs.net/doc/cd1313280.html,/eng
基金项目:国家自然科学基金资助项目(50435020);中国博士后科学基金资助项目(2005037259).
作者简介:董辉跃(1974-),男,山东青岛人,博士后,从事先进制造技术方面研究.E 2mail :donghuyue @https://www.360docs.net/doc/cd1313280.html,
薄壁板高速铣削加工过程中的让刀误差预测
董辉跃1,柯映林1,杨慧香2
(1.浙江大学机械与能源工程学院,浙江杭州310027;2.长春工业大学机电工程学院,吉林长春130012)
摘 要:为了研究薄壁工件在铣削加工过程中的让刀误差以及获得使让刀误差较小的优化铣削参数,以薄壁板为例,在进行高温拉伸试验和高速压缩试验获得材料力学性能的基础上,建立了薄壁板铣削过程的热力耦合有限元模型.通过模拟螺旋立铣刀与工件材料之间相互的物理作用,获得了铣削力的变化曲线和铣削热的分布,同时得到了在刀具与工件之间物理作用下壁板随刀具的旋转与进给运动而产生的让刀变形,从而得到了薄壁板在铣削过程中的最大让刀误差.根据该有限元模型的结果可以优选薄壁件铣削用量,优化刀具几何形状,弥补让刀变形.关键词:薄壁板;有限元模型;让刀误差
中图分类号:T G54;T G659 文献标识码:A 文章编号:1008973X (2006)04063404
Milling error prediction of thin 2w alled parts during
high 2speed m achining
DON G Hui 2yue 1,KE Y ing 2lin 1,YAN G Hui 2xiang 2
(1.College of Mechanical and Energ y Engineering ,Zhej iang Universit y ,H angz hou 310027,China;
2.College of Elect romechanics Engineering ,Changchun Technology Universit y ,Changchun 130012,China )
Abstract :To st udy milling error and optimize machining parameters t hat minimize t he deflection during cutting low rigidity part ,a t hin 2walled panel was taken as an example.A new finite element model (FEM )suitable for dynamic machining error p redictio n of low rigidity component s was presented.Depending on high speed impact experiment and material drawing experiment ,t he constit utive model of Al7050T7451was achieved under machining conditions when high strain rate ,high st rain and high temperat ure occur.The achieved workpiece material constit utive model was p ut into t he finite element model to simulate t her 2mo 2mechanical coupling ,dynamic behavior and cutting mechanics which occurred in t he machining process of t he t hin 2walled st ruct https://www.360docs.net/doc/cd1313280.html,ling error was obtained during t he rotation and feed movement of t he tool.The simulation model p resented is helpf ul for determining t he cutting parameters ,geometric accuracy and tool geomet ry wit hout performing real cutting experiment s for rapid machining of complex low 2rigidity part s.
K ey w ords :t hin 2walled part ;FEM ;milling ernr
由高强度铝合金整体切削而成的低刚度薄壁结构件被广泛应用在航空领域;然而,由于工件的壁板、筋条和腹板等主要特征厚度很小,铣削过程中极易由于刚度过低而引起让刀变形,从而导致加工精度降低.为了弥补因为让刀带来的误差,车间采用的
措施是应用试错法进行大量试验.有限元方法是优化选择薄壁件加工参数的有效方法.但是现有的通过有限元研究薄壁件立铣让刀变形的文献采用的基本都是一种方法,即建立刀具与工件之间的作用力模型(包括刚性模型和柔性模型),按照刀具在铣削
过程中旋转的角度,依次将铣削力离散地施加到单元的节点上[125].这种方法的切削力是作为已知量施加到模型当中的.然而切削力是刀具和工件相互作用的结果,是因为这种结果的存在才导致薄壁件的变形.虽然文献中施加的切削力是随着刀刃的切入长度变化的,但是将切削力通过边界条件施加到单元节点上的过程是一个静态过程,而切削实际是一个动态的热力耦合过程[627].另外,文献中很少涉及到切削温度[8].切削温度和切削力一样,都是刀具和工件相互作用的结果.本研究中所建立的刀具和工件的有限元模型,通过刀具的旋转和进给,实现刀具与工件的互作用,真实地模拟材料实际切除的热力耦合过程.在该过程中,切削力和切削热是因为刀具与工件材料之间相互的物理作用而产生的;切削力和切削热的共同作用引起了工件的让刀现象.
1 铝合金7050T7451力学性能测试
铝合金铣削过程中,伴随着切屑的生成,在第一
剪切区和第二剪切区(刀屑接触面)铝合金都会产生非常高的应变率和较大的变形.在这两个变形区以及整个切屑上的温度都非常高.金属的应变率、应变和温度对金属的力学性能会产生较大的影响.为了使模拟结果更加接近铝合金的真实切削过程,必须进行高温拉伸试验、准静态压缩试验和高温、高速压缩试验以获得各种温度和各种应变率下的金属力学性能.1.1 高温拉伸试验在25T SHIMADZU 电子万能试验机上进行铝合金静态拉伸试验以获得各个温度(20、100、125、
150、200、225、250和300℃)下的弹性模量、屈服极
限和强度极限.试验结果见图
1.
图1 铝合金高温拉伸真实应力2应变曲线
Fig.1 True stress 2strain curves of 7050T7451under differ 2
ent temperatures
1.2 准静态压缩试验和高温、高速压缩试验
使用M TS 仪器测量测试4个温度点(20、100、
200和300℃)下应变率为0.001s -1时的应力、应
变曲线,每种试验取两组有效数据进行平均.
高速压缩试验采用直径为14.5mm 的SHPB (split hopkinson press bar ).试样是直径为8mm 、长度为4mm 的圆柱体,用电子加热炉升至高温,测试4
个温度点(20、100、200和300℃
)下应变率分别为2000、3000、4000和5000s -1时的应力2应变曲线.试验前后的试样见图2.图3所示的是应变率为2000/s 时材料4
个温度点的应力2应变曲线.
图2 高速压缩前后的铝合金试样
Fig.2 Un
2compressed and compressed 7050T7451sample
图3 应变率为2000/s 时各个温度下的应力2应变曲线
Fig.3 Stress 2strain curve when strain rate is 2000/s and tem 2
peratures are different
在通过准静态压缩试验和高速压缩试验获得材料动态力学性能曲线的基础上,采用适合于金属材料的Jo hnson 2Cook 模型(式(1))拟合试验数据.σ=(A +B εn
)1+C ln εε?01-θ-
θr
θm -θr
m
.(1)
式中:σ、ε、 ε和θ分别为试件材料的应力、应变(塑性应变)、应变率(塑性应变率)和环境温度.在这里由于一般Johnson 2Cook 模型适用于大应变、高应变率的场合,弹性应变相对很小,可以略
去不计. ε0为10-3s -1
,相当于准静态实验的试件应变率.θr 和θm 分别为室温和试件材料的熔化温度.式(1)中第一个括号表示室温条件下准静态的应力2
应变关系,参数A 为试件材料的静态屈服应力,B
和n 则反映了试件材料的应变硬化特性;式中第二个括号表示材料的应变率效应,表明材料的强度提高是与材料的应变率的对数成线性关系;C 反映了材料应变率效应的敏感程度;公式中第三个括号表示环境温度的影响,式中的m 反映了材料对环境温度热软化效应的敏感程度.
5
36第4期董辉跃,等:薄壁板高速铣削加工过程中的让刀误差预测
2 壁板铣削加工的有限元模拟
2.1 壁板铣削加工有限元模型的建立
在低刚度薄壁工件中,腹板、壁板和筋条是3种主要特征.这3种特征的共同之处是厚度尺寸非常小.本文以壁板为例,采用有限元方法模拟壁板在铣削过程中的让刀现象.将以上材料性能试验获得的铝合金7050T7451的材料力学性能以及相关的热物理性能作为有限元模型中的材料模型,并采用表1中的刀具参数和切削用量,建立如图4所示的壁板铣削加工有限元模型.工件材料的失效模型见式(2),当失效参数达到1时,材料失效,即切削过程中切削层从工件上分离形成切屑.
ω=(
∑
Δ εpl )/ε-
pl
f .(2)
式中:ω为失效参数,Δ εpl 为等效塑性应变增量, εpl
f 为失效应变.
表1 试验条件
Tab.1 Experiment conditions
参数名称
数值
刀具直径/mm 20刀具前角20°刀具后角15°
刀具螺旋角30°刀具齿数2铣削深度/mm 3.42单齿进给/(mm ?齿-1)0.3铣削宽度/mm 10.0主轴转速/(r ?min )
10
000
图4 壁板铣削加工的有限元模型
Fig.4 FEM of machining thin 2walled plate
假设刀具为刚体,其材料属性只赋予热物理属
性,刀刃圆弧半径为0(锋利刀具),采用四面体单元划分网格.壁板加工后的厚度为1.7mm ,采用六面体单元划分网格,并且在被切削部位采用高密度单元,以提高计算效率和精度.刀具在绕主轴(Z 轴)旋转的同时沿X 方向作进给运动,同时约束壁板底面和两端面的自由度.在切削过程中,刀具和工件的初
始温度都为20℃,刀2屑间的热传递系数为11W/
(mm 2?℃).实际切削中刀屑间的摩擦为滑动摩擦和黏性摩擦,本文简化为滑动摩擦,摩擦系数为0.3.2.2 铣削过程模拟
图5为铣削过程中某一时刻的结果,随着刀具的旋转和进给运动,刀具和工件的相互作用生成了切屑.与文献[425]不同的是:文献中没有提到切屑的生成过程,只是计算不同时刻的切削力后离散地施加到工件有限元模型的节点上;而本文模拟了刀具、工件之间相互的物理作用,再现了材料去除的物理过程
.
图5 壁板的铣削过程
Fig.5 Machining process of thin 2walled plate
针对壁板来说,引起壁板让刀现象的主要作用力是垂直于刀轴的负Y 向铣削分力.有限元模拟获得的负Y 向切削刀力曲线如图6所示.由于刀具在旋转的同时作进给运动,切削厚度在不断增大,负Y 向切削力基本呈直线上升趋势.在切削时间为4.0×10-4s 时负Y 向切削力达到了最大值,约为200N (因为单元网格的破裂与分离导致切削力曲线存在波动).图7所示为刀刃的切削部位在切削了1.125×10-3s 时刻的温度分布,等温线基本与刀刃
平行分布,最高温度约为179.3℃
.
图6 负Y 向铣削力
Fig.6 Cutting force in 2Y direction
2.3 切削力的试验验证
为了对铣削加工的有限元模型进行验证,采用K istler 9257A 测力仪和材料为K10的立铣刀在DMU eV70高速加工中心进行了铣削力测试,铣削方式为顺铣,试验条件见表1.试验获得的轴向铣削
6
36浙 江 大 学 学 报(工学版) 第40卷
图7 刀具温度分布
Fig.7 Distribution of tool temperature
力最大值约为125N.轴向铣削力模拟峰值与试验峰值的误差约为11%.存在误差的主要原因如下:
(1)虽然进行了材料高温、高应变率试验,但是实际铝合金高速铣削过程中的应变率高达104~106s -1,而本研究得到的高速压缩试验的应变率只达到5000s -1,但是铝合金属于应变率不敏感材料,这
种误差是非常有限的;(2)有限元模型中刀具的切削刃为绝对锋利的刚体,而实际切削加工中切削刃存在一定大小的圆弧半径,且非刚体;(3)刀具前刀面与切屑之间的摩擦被假设为滑动摩擦,而忽略了黏性摩擦.考虑以上建立有限元模型过程中采用的近似及假设条件,该有限元模拟结果基本合理.
图8 6.75×10-4s 时壁板的变形
Fig.8 Deformation of thin wall when 6.75×10-4s
passed
3 壁板在铣削过程中的让刀变形
壁板在铣削过程中的让刀变形主要发生在与刀刃走刀轨迹对应的背面上.图8为切削时间为6.75×10-4s 时壁板被加工部位背面的变形,因为
刀具螺旋角的存在使得变形量等直线与刀具轴向(Z 向)成一定的角度.图9显示了壁板被加工部位的背面随刀具旋转和进给运动过程中,4个时刻出现的让刀变形情况.从图9中也可以看出图8所示的变形规律.另外还可看出,壁板背面的让刀变形量随着切削力的增大(图6)而增大,在切削时间为1.125×10-3s 时刀具切削刃底部开始切出工件,
在
图9 壁板在铣削过程中的让刀变形
Fig.9 Deformation of thin wall during machining process
该时刻背面变形最大,约为0.039mm.负Y 向切削
力在4.0×10-4s 时达到最大值,而背面的最大变形却在刀刃开始切出工件的时刻.背面变形最大值产生时刻滞后于负Y 向切削力达到最大值时刻的原因是:由于刀刃螺旋角的存在,切削力主要集中在离壁板底面较近的加工部位,由此产生的力矩较小,而在刀刃切出时刻,切削力主要集中在离壁板底面较高的加工部位,切削力产生的力矩恰好达到最大值,于是引起最大的让刀变形.
如果采用位移变形测量设备对壁板背面的变形进行测量,测得的都是一些离散点的变形量,不易找到最大的变形点,也就不易测得最大的变形量;而有限元模拟所得到的是整个侧面的变形分布情况和变
(下转第703页)
7
36第4期董辉跃,等:薄壁板高速铣削加工过程中的让刀误差预测
(42):4764.
[2]B EKKER M G.I ntroduction to the terrain2vehicle sys2
tems[M].Ann Arbor:The University of Michigan Press,1969.
[3]KARA FIA T H L L,NOWA TZK E A.越野车辆工程土
力学[M].张克健,王瑞麟,译.北京:机械工业出版社,1986.
[4]WON G J Y.地面车辆理论[M].张声涛,译.哈尔滨:
黑龙江科学技术出版社,1987.
[5]庄继德.汽车地面力学[M].北京:机械工业出版社,
1980.
[6]PARK S A.POPOV A,COL E D J.Vehicle suspension
optimisation for heavy vehicles on deformable ground[J].
V ehicle System Dynamics Supplem ent,2004,41:3
[7]WA Y T HOMAS R,ERBACH DONALD C,BA IL EY
AL V IN C,et al.Soil displacement beneath an agricul2 tural tractor drive tire[J].Journal of T erramech anics, 2005,42(1):3546.
[8]王福建,吴国雄,孙勇.三维实体模型在公路设计中的应
用研究[J].浙江大学学报:工学版,2002,36(1):711.
WAN G Fu2jian,WU Guo2xiong,SUN Y ong.Applica2 tion of3D sol id model in highway design[J].Journal of Zhejiang U niversity:E ngineering Science,2002,36(1): 711.
[9]蔡忠法,章安元.汽车模拟驾驶模型与仿真的研究[J]
浙江大学学报:工学版,2002,36(5):327330.
CA I Zhong2fa,ZHAN G An2yuan.Study of automobile emulated dr iv ing model and simulation[J].Journal of Zhejiang U niversity:E ngineering Science,2002,36(5): 327330.
[10]张永林,钟毅芳.车辆路面不平度输人的随机激励时
域模型[J].农业机械学报,2004,35(2):912.
ZHAN G Y ong2lin,ZHON G Y i2fang.Time domain model of road undulation excitation to vehicles[J].
T ransactions of the Chinese Society for Agricultural Ma2 chinery,2004,35(2):912.
[11]MITSCH KE M.Dynamik der K raftfahrzeuge[M].
Berlin:Springer2Verlag,1972.
(上接第637页)
形的变化情况,同时显示了最大变形位置和变形量.所以通过建立准确的有限元模型仿真低刚度薄壁结构件的加工让刀变形,从而有针对性的改进工艺,将有益于提高薄壁件的加工精度和加工质量.
4 结 语
本文以薄壁板为例,通过模拟刀具与工件之间在切削中相互的物理作用,建立了热力耦合有限元模型,获得了底面最大的变形量和变形规律.但实际加工除了采用两齿刀具外,还采用了多齿刀具,这可以有两个或多个刀齿同时参与切削,薄壁板的变形规律将比两齿刀具复杂的多.有关文献中通过施加静态切削力的方法已经考虑到这种情况.另外,刀屑间的实际摩擦非常复杂,在本研究中仅简化为滑动摩擦,所以本文的有限元模型需要进一步完善,才能使模拟结果更接近实际.
参考文献(R eferences):
[1]RA TCH EV S,L IU S,HUAN G W,et https://www.360docs.net/doc/cd1313280.html,ling error
prediction and compensation in machining of low2rigidity parts[J].I nternational Journal of Machine Tools& Manufacture,2004,44(15):16291641.
[2]TSA I J,L IAO C.Finite2element modeling of static sur2
face errors in the peripheral milling of thin2walled work2 pieces[J].Journal of Materials Processing T echnology, 1994,94:2352246.[3]RA TCH EV S,GOV ENDER E,NIKOV S,et al.Force
and deflection modelling in milling of low2rigidity com2 plex parts[J].Journal of Materials Processing T echnolo2 gy,2003,143/144:796801.
[4]RA TCH EV S,L IU S,HUAN G W,et al.A flexible
force model for end milling of low2rigidity parts[J].
Journal of Materials Processing T echnology,2004,153/ 154:134138.
[5]武凯,何宁,姜澄宇,等.有限元技术在航空薄壁件立
铣变形分析中的应用[J].应用科学学报,2003,21(1): 6871.
WU K ai,HE Ning,J IAN G Cheng2yu,et al.The applica2 tion of the FEM technology on the deformation analysis of the thin2wall workpieces milling in aerospace industries[J].
Jou rnal of Applied S cience,2003,21(1):6871.
[6]杨勇,柯映林,董辉跃.金属切削加工中航空铝合金板
材的本构模型[J].中国有色金属学报,2005,15(6): 854859.
YAN G Y ong,KE Y ing2lin,DON G Hui2yue.Constitu2 tive model of aviation aluminum2alloy material in metal machining[J].The Chinese Journal of Nonferrous Met2 als.2005,15(6):854859.
[7]DON G Hui2yue,KE Y ing2lin.Simulation of3D chip
shaping of aluminum alloy7075in milling process[J].
T ransactions of N onferrous Metals Society of China, 2005,15(6):13151321.
[8]RA TCH EV S,N IKOV S,MOUAL EK I.Material re2
moval simulation of peripheral milling of thin wall low2 rigidity structures using FEA[J].Advances in E ngineer2 ing Softw are,2004,35(8/9):481491.
307
第4期王乾廷,等:变形路面上越野汽车悬架优化的仿真分析
MTS软件铣削仿真
MTS软件铣削仿真 MTS软件铣削仿真分二步,第一步编辑工艺表格,主要包括五方面的内容:输入坯料参数、查询材料类型与型号、选择夹具、选择刀具和设置工件坐标系原点。第二步编写加工程序,有人机交互式编程和直接在工艺表格文件中编写程序二种方法。 1. 建立工艺表格 1)输入坯料参数 选安装方式→工件→新工件菜单,根据零件的外形与结构尺寸,输入坯料的长、宽、高为110、95、25(图1)。 图1 输入坯料尺寸 2)查询材料类型与型号 先后选择工件材料→祥细选择→显示工件材料菜单,分别打开材料类型和材料型号对话框,接着选取工件材料类型与型号,查询工件材料机械性能参数。 3)选择夹具 铣削夹具的类型有三种:虎钳、磁性吸盘和压板。通过更换夹具菜单,根据零件的外形与结构尺寸选择夹具类型,在夹具型号对话框中选用夹具型号(图2),选工件位置与夹具位置菜单之后,根据工件加工要求分别调整工件在夹具中的位置以及夹具在工作台中的位置。
图2选择夹具 4)选择刀具 选刀具基准→刀库装备→Equipment→选择刀具菜单,打开旋转刀塔对话框,然后分别选取对应刀具号的刀具类型与刀具型号。在旋转刀塔中可安装16把刀(图3),每把刀都有其指定的刀具代码,由于各把刀具的结构尺寸不同,刀具选定后必须对刀具进行补偿,按菜单中的Valid offsets 按钮,即对所选各把刀具完成了刀具补偿。 图3 铣床旋转刀塔 5)设置工件坐标系原点 按基准重合的原则设定工件坐标系,一般以刀具代码T01的刀具作为基准刀,通过基准刀的
对刀操作设定工件坐标系原点,对于对称工件,把位于工件的对称中心作为X轴和Y轴的原点;对于非对称工件,把位于工件左边与工件前面的交点作为X轴和Y轴的原点,Z轴的原点一般设在工件的上表面位置上。本例题以零件图的左、右中心线与前、后中心线的交点作为工件坐标系X轴与Y轴的原点。设定工件坐标系原点后,选设置基准菜单,基准记录会显示在G54程序段中,其中地址符X289.029、Y134.305、Z89分别表示工件坐标系原点在机床坐标系中的坐标值(图4)。 设置工件坐标系原点的具体方法,选刀具更换菜单,调用一号刀为基准刀,通过键盘按钮操作,置刀尖位置于工件坐标系的原点,然后分别置X、Y、Z坐标值为零,即设定了工件坐标系的原点。 键盘中方向鍵的功能: 向右方向键→,刀具向X轴正方向移动; 向左方向键←,刀具向X轴负方向移动; 向上方向键↑,刀具向Z轴正方向移动; 向下方向键↓,刀具向Z轴负方向移动; Page Up键,刀具向Y轴正方向移动; End键,刀具向Y轴负方向移动。 图4 设置工件坐标系原点 完成输入坯料参数、查询材料型号、选择夹具型号、选择刀具型号和设置工件坐标系原点后,返回编辑主菜单,建立工艺表格文件,储存工艺参数。 选安装表格→建立菜单,打开建立文件对话框(图5),输入文件名,按保存按钮,建成工艺表格文件,以后编写的加工程序也储存工艺表格文件之中。 选程序编辑→Select program菜单,打开程序选择对话框,输入工艺表格文件名,在打开的工艺表格文件中存储了已选用的数控系统、工件坯料尺寸、工件材料型号、夹具型号、刀具型号和设定的工件坐标系参数,接着在工艺表格文件中编写加工程序。
开题报告_数控铣削加工过程仿真
毕业设计(论文)开题报告 学生姓名:李赢学号: 1015070124 专业:机械设计制造及其自动化 设计(论文)题目:数控铣削加工过程仿真 指导教师:张学军 2014 年3月28 日
开题报告填写要求 1.开题报告(含“文献综述”)作为毕业设计(论文)答辩委员会对学生答辩资格审查的依据材料之一。此报告应在指导教师指导下,由学生在毕业设计(论文)工作前期内完成,经指导教师签署意见及所在系审查后生效; 2.开题报告内容必须用黑墨水笔工整书写或按教务处统一设计的电子文档标准格式打印,禁止打印在其它纸上后剪贴,完成后应及时交给指导教师签署意见; 3.“文献综述”应按论文的格式成文,并直接书写(或打印)在本开题报告第一栏目内,学生写文献综述的参考文献应不少于10篇(不包括辞典、手册); 4.有关年月日等日期的填写,应当按照国标GB/T 7408—94《数据元和交换格式、信息交换、日期和时间表示法》规定的要求,一律用阿拉伯数字书写。如“2002年4月26日”或“2002-04-26”。
毕业设计(论文)开题报告
二、国内外发展现状 虚拟加工过程仿真系统是虚拟制造的底层关键技术,包括几何仿真系统和物理仿真系统两大部分。几何仿真系统是将数控机床、刀具、工件和夹具组成的工艺系统当作一个刚性系统,不考虑系统的各种物理因素而建立的仿真系统,解决对加工过程直观的动态图形描述和精度检验。目前在几何仿真系统方面的研究出现了Pro/E、UG、MasterCAM等商业软件。 Pro/E是美国PTC公司开发的,采用面向对象的统一数据库和全参数化造型技术,其工业设计方案可直接读取内部的零件和装配文件。提供刀具加工路径控制和工路径的创建,支持高速加工和多轴加工,并带有多种图形文件接口。UG/CAM是将数控虚拟加工仿真模块连接起来,从车削到复杂曲面的铣削,为用户提供了一个方便实用的仿真环境.在刀具移动过程中,用户既可基于图形编辑刀具路径,对其进行扩展、缩短或修改,同时还可定制出自己的菜单和对话框。MasterCAM是美国CNC公司产品,功能主要包括二维绘图、曲线、曲面加工、曲面设汁、点位加工、二轴到五轴铣削加工、数控车削、二轴到四轴的线切割、火焰切割和激光切割。其数控加工功能提供多种走刀方法,对加工路径的选择、干涉检查、加工时的进退刀方式、多曲面加工、粗精加工、刀具管理、毛坯材料管理、走刀模拟、测量等方面具有很强的功能。 在国内,几何仿真的研究成果典型的有CAXA是北京航空航天大学开发的CAD/CAM系列软件,功能与国外的CAD/CAM软件相似,是针对数控车床、数控线切割等机床开发的CAD/CAM软件,并且其三维CAD软件是目前国内CAD市场上性能价格比最高的三维零件设计软件.其他一些专门的数控虚拟加工仿真软件有:南京数控培训中心和上海天傲科技有限公司合作开发的TNS-Vvr2.0数控仿真系统;南京宇航自动化技术研究所开发的数控仿真软件;上海宇龙软件工程有限公司开发的数控仿真软件和由广州红地技术有限公司开发的V-CNC数控虚拟加工仿真教学软件等。这些仿真软件可以让用户交互式仿真数控机床的操作,具有与真实机床运动完全相同的二维或三维的加工仿真功能,可在计算机上对加工中的机床、刀具的切削运动以及工件余量去除过程获得真实感的动态显示,并进行过切与欠切检验以及机床、夹具与刀具的碰撞检验,在计算机上实现快捷有效的零件程序检验。其中,有些仿真软件还可进行简单的切削负荷和速度优化检验。 而物理仿真系统则是考虑整个工艺系统的动态特性对实际切削过程影响而建立
关于高速铣削加工工艺的浅论
高速切削技术论文 机械工程学院 1001011435 张伟
1 关于高速铣削加工工艺的浅论* 张伟 (1. 沈阳理工大学,机械工程学院,机械设计制造及其自动化沈阳201311;) 摘要:传统意义上的高速切削是以切削速度的高低来进行分类的,而削机床则是以转速的高低进行分类。如果从切削变形的机理来看高速切削,则前一种分类比较合适;但是若从切削工艺的角度出发,则后一种更恰当。随着主轴转速的提高,机床的结构,刀具结构,刀具装夹和机床特性都有本质上的改变。高速意味着高离心力,传统的7:24锥柄,弹簧夹头,液压夹头在离心力的作用下,难以提供足够夹持力,同时为避免切削振动要求刀具系统具有更高的动平衡精度。高速切削的最大优势并不在于速度,进给速度提高所导致的效率提高,而由于采用了更高的切削速度和进给速度,允许采用较小的切削用量进行切削加工。由于切削用量的降低,切削力和切削热随之降低,工艺系统变形减小,可以避免铣削振动。利用这一特性可以通过高速铣削工艺加工薄壁结构零件。 关键词:高速铣削加工工艺 中图分类号:TG156 About High Speed Milling Technology Discussion ZHANG Wei (1. Shenyang Li gong University, School of Mechanical Engineering, Mechanical Design, Manufacturing and Automation, Shenyang 201311;) Abstract:Traditional high-speed cutting is to classify the level of cutting , and the cutting speed of the machine is based on the level of classification. If the view of the cutting mechanism of deformation speed cutting, the former is more appropriate classification ; However, if the angle of the cutting process , the latter is more appropriate. As the spindle speed increases , the structure of the machine tool structure , tool clamping and machine characteristics are essentially changed. High speed means high centrifugal force , the traditional 7:24 taper , collet chuck , hydraulic chuck under the effect of centrifugal force , it is difficult to provide sufficient clamping force , as well as to avoid cutting vibration requires balancing tool system has higher precision . The biggest advantage of high-speed cutting is not the speed, feed speed increased efficiency resulting from , but thanks to the higher cutting speed and feed rate, allowing the use of smaller cutting for cutting. Since the reduction cutting , cutting force and cutting heat decreases, reducing deformation process system to avoid vibration milling . Using this feature can speed milling machining thin-walled structural components . Key words:High speed Milling Processing technology 0 前言1 普通铣削加工采用低的进给速度和大的切削参数,而高速铣削加工则采用高的进给速度和小的切削参数,高速铣削加工相对于普通铣削加工具有如下特点: (1)高效高速铣削的主轴转速一般为15000r/min~40000r/min,最高可达100000r/min。 *高速切削技术论文.20131005下载模板.20131101完成初稿.20131127终稿. 在切削钢时,其切削速度约为400m/min,比传统的 铣削加工高5~10倍;在加工模具型腔时与传统的加工方法(传统铣削、电火花成形加工等)相比其效率提高4~5倍。 (2)高精度高速铣削加工精度一般为10μm,有的精度还要高。 (3)高的表面质量由于高速铣削时工件温升小(约为3°C),故表面没有变质层及微裂纹,热变形也小。最好的表面粗糙度Ra小于1μm,减少了后续磨削及抛光工作量。
高速铣削加工效率的一般计算与分析
高速铣削加工效率的一般计算与分析(转) 随着高速切削技术的发展,高速铣削工艺的应用日益广泛,越来越受到制造企业和科研工作者的关注。信息产业部某研究所自1999年7月从瑞士MIKRON公司购进第一台HSM-700型高速立式铣削中心后,2001年10月又购进三台HSM-700型高速铣床用于生产。笔者通过对这批先进高速铣床的加工效率进行深入、细致的调查研究,对比了不同铣床的加工效率,推导了高速铣削加工效率的计算公式。 1.加工效率的计算 按照传统切削理论,切削加工效率Zw(cm3/min)可通过下列公式计算: Zw=v×f×ap (1) 式中:v——切削速度,f——进给量,ap——切削深度 根据分析与研究,我们认为式(1)不适用于高速铣削加工效率的计算,原因主要有两点: ①高速铣床的主轴转速相当高(如HSM-700型高速铣床最高转速达42000r/min,加工平面时转速也在35000r/min以上),如此高的转速使刀具并非每一转都在切削金属; ②在实际加工中,设定的转速和进给量只是最大转速和最大进给量,实际的刀具转速和进给量时刻都在变化(HSM-700机床的自测功能可以显示整个切削过程中的变化情况),切削过程中的实际转速和进给量总是从较低值迅速达到较高值又很快降到较低值,如此反复变化,这是铣削过程的客观反映,而不像车削过程中可以保持转速和进给量恒定不变。 因此,我们提出用单位时间内的金属去除量Z(cm3/min)表示加工效率,即: Z=W/t (2) 式中:W——切削过程总的金属去除量(cm3),t——切削时间(min)(>0) 式(2)更符合高速铣削的实际情况,用式(2)很容易实现对高速铣削加工效率的计算,同时也便于不同铣床加工效率的比较。例如,原来在普通铣床上加工某零件,为了缩短生产周期,一部分零件现采用高速铣床加工。这样,可通过该零件的加工来比较两种加工设备的加工效率。
高速加工技术现状及发展趋势
高速加工技术现状及发展趋势 1引言 对于机械零件而言,高速加工即是以较快的生产节拍进行加工。一个生产节拍:零件送进--定位夹紧--刀具快进--刀具工进(在线检测)--刀具快退--工具松开、卸下--质量检测等七个基本生产环节。而高速切削是指刀具切削刃相对与零件表面的切削运动(或移动)速度超过普通切削5~10倍,主要体现在刀具快进、工进及快退三个环节上,是高速加工系统技术中的一个子系统;对于整条生产自动线而言,高速加工技术表征是以较简捷的工艺流程、较短、较快的生产节拍的生产线进行生产加工。这就要突破机械加工传统观念,在确保产品质量的前提下,改革原有加工工艺(方式):或采用一工位多工序、一刀多刃,或以车、铰、铣削替代磨削,或以拉削、搓、挤、滚压加工工艺(方式)替代滚、插、铣削加工…等工艺(方式),尽可能地缩短整条生产线的工艺流程;对于某一产品而言,高速加工技术也意味着企业要以较短的生产周期,完成研发产品的各类信息采集与处理、设计开发、加工制造、市场营销及反馈信息。这与敏捷制造工程技术理念有相同之处。 高速加工技术产生于近代动态多变的全球化市场经济环境。在激烈的市场竞争中,要求企业产品质量高、成本低、上市快、服务好、环境清洁和产品创新换代及时,由此牵引高速加工技术不断发展。自二十世纪八十年代,高速加工技术基于金属(非金属)传统切削加工技术、自动控制技术、信息技术和现代管理技术,逐步发展成为综合性系统工程技术。现已广泛实用于生产工艺流程型制造企业(如现代轿(汽)车生产企业);随着个性化产品的社会需求增加,其生产条件为多品种、
单件小批制造加工(机械制造业中,这种生产模式将占到总产值的70%),高速加工技术必将在生产工艺离散型或混和型企业中(如模具、能源设备、船舶、航天航空…等制造企业)得到进一步应用和发展。 二十世纪末期,我国变革计划经济体制,改革开放,建成有中国特色社会主义市场经济体制。实用的高速加工技术跟随引进的先进数控自动生产线、刀具(工具)、数控机床(设备),在机械制造业得到广泛应用,相应的管理模式、技术、理念随之融入企业。企业家们对现代信息技术和企业制度、机制在未来可持续发展、市场竞争中的重要地位和作用,认识日益深刻。社会主义市场经济环境,不仅促进企业转制、调整产业、产品结构和技改,还给企业展现出应用和发展高速加工技术良好而广阔的前景。 2我国引进数控轿车自动生产线中的高速加工技术 二十世纪八十年代以来,我国相继从德国、美国、法国、日本…等国引进了多条较先进的轿车数控生产自动线,使我国轿车制造工业得到空前发展。其中较典型的是来自德国的一汽--大众捷达轿车和上海大众桑塔纳轿车自动生产线,其处于国际二十世纪九十年代中期水平。其中应用了较多较实用的高速加工技术。从中可部分了解到世界高速加工技术的现状与发展趋势。本文重点介绍一汽--大众捷达轿车传、发生产线。 引进的捷达数控轿车自动生产线概况 一汽--大众捷达轿车自动生产线由冲压、焊接、涂装、总装、发动机及传动器等高速生产线组成。同步引进德国大众汽车公司并行工程管理模式与管理技术,
刀具轨迹生成与动态切削过程仿真
刀具轨迹生成与动态切削过程仿真五坐标数控加工 丁1,*,双qingzhen2,朱利民2 华中科技大学数字制造装备与技术国家重点实验室,,武汉430074; 上海交通大学机械系统与振动国家重点实验室,,上海200240 2009年10月9日2009年12月29日收到 五轴数控加工提供了一种有效、高效的方法来制造复杂形状的机械零件,这是一种有效的方法广泛应用于航空航天,能源和国防工业。其技术创新在最近备受关注岁月。在本文中,国家的最先进的技术,五轴加工工艺规划的总结和挑战从刀具路径生成,集成几何/机械仿真和分析的问题进行了分析加工稳定性分析。基于可访问性的刀具定位优化方法研究进展线接触和三点接触加工,刀具包络面形状控制和铣削稳定性预测详细介绍。最后,新兴趋势和未来的挑战进行了简要讨论。 关键词:五轴加工,刀具轨迹生成,集成几何/机械仿真,动力学仿真 引文: 在传统的三轴数控加工的翻译刀具的运动是允许的,而刀具方向可以改变一五轴机床因为另外两个旋转轴。优势五坐标数控加工主要依赖于控制工具取向:(1)零件间的碰撞可通过选择可访问的工具的方向,它提供了机器的能力复杂的形状,如航空航天,涡轮叶片和船用螺旋桨。(2)大的加工条带宽度如果工具方向被正确地规划,则可获得工具提示几何匹配的零件几何。再者,高效的刀面研磨可以应用于机器航空叶轮用一五轴机床。(3)在五轴加工中,切削条件可以得到改善。例如,它是可以缩短的工具悬挑长度如果工具定位优化。确定在一个密闭的空间中,当表面被机械加工时,安全和最短的刀具长度是非常有用的小直径铣刀可用于。切割区域的刀具,从而影响切削力,刀具磨损和机械加工表面质量也可以通过改变来控制刀具导向。 除了上述优点外,还有一些具有挑战性的五轴加工中的问题。自工具方向是可调的,很难像图像的复杂工具的空间运动。因此,它更难以生成无碰撞和高效率的刀具路径,这限制了它的广泛应用。此外,切割力预测和动力学模拟更为复杂因为所涉及的切削参数是随时间变化的在加工过程中。约五轴电流工作机械加工分为三类1类:刀具轨迹生成,集成几何/机械模拟动力学仿真,如图1所示。 刀具轨迹生成是计划的过程,相对于基于零件模型、加工方法和公差要求。刀具轨迹对切削效率和质量有很大的影响。它也是基金会集成的几何/机械模拟,这取决于切削几何与切削力模型的研究技术。切削几何反映了网格的状态在刀具和工件之间的材料清除过程。通过整合切割的几何形状和切削力模型,可以预测的瞬态切削力。切削力,然后可以应用到动态模拟,进给率优化,预测补偿变形。动态仿真目标是预测切削稳定性和加工表面基于切削力和动力学特性的研究机床夹具系统的研究。力学仿真有助于优化切削参数和刀具路径。
高速切削
1. 论述高速切削的特点。 材料去除率高,切削力较小,工件热变形小,工艺系统振动小,可加工各种难加工材料,可实现绿色制造,简化加工工艺流程。高速切削追求高转速、中切深、快进给、多行程的加工工艺,高速切削加工可大大降低加工表面粗糙度,加工表面质量可提高1~2等级。加快产品开发周期,大大降低制造成本。 2.阐述高速切削技术研究体系、关键技术。 数控高速切削加工技术是建立在机床结构与材料、高速主轴系统、高性能CNC控制系统、快速进给系统、高性能刀具材料、数控高速切削加工工艺、高效高精度测试技术等许多相关的软件和硬件技术基础之上的一项复杂的系统工程,是将各单元技术集成的一项综合技术。关键技术:高速切削机理;高速切削刀具技术;高速切削机床技术;高速切削工艺技术;高速加工的测试技术。 3.阐述高速切削发展趋势。 机床结构将会具有更高的刚度和抗振性,使在高转速和高级给情况下刀具具有更长的寿命;将会用完全考虑高速要求的新设计概念来设计机床;在提高机床进给速度的同时保持机床精度;快换主轴;高、低速度的主轴共存;改善轴承技术;改进刀具和主轴的接触条件;更好的动平衡;高速冷却系统。(新一代高速大功率机床的开发和研制;新一代抗热振性好、耐磨性好、寿命长的刀具材料的研制及适宜于高速切削的刀具结构的研究;进一步拓宽高速切削工件材料及其高速切削工艺范围;高速切削机理的深入研究;高速切削动态特性及稳定性的研究;开发适用于高速切削加工状态的监控技术;建立高速切削数据库,开发适于高速切削加工的编程技术以进一步推广高速切削加工技术;基于高速切削工艺,开发推广干式(准干式)切削绿色制造技术;基于高速切削,开发推广高能加工技术) 4结合典型工件材料和加工工艺方法,讨论高速切削的速度范围。 (1)根据工件材料:刚才380m/min以上、铸铁700m/min以上、铜材1000m/min以上、铝材1100m/min以上、塑料1150m/min以上时,认为是合适的速度范围。(2)根据加工工艺方法:车削700~7000m/min,铣削300~6000m/min,钻削200~1100m/min,磨削5000~10000m/min,认为是合适的速度范围。 5讨论高速切削加工的切削力变化规律。 (1)切削用量对切削力的影响:背吃刀量ap增大,切削力成正比增加,背向力和进给力近似成正比增加。进给量f增大,切削力与增大,但切削力的增大与f不成正比(75%)(2)工件材料对切削力的影响:较大的因素主要是工件材料的强度、硬度和塑性。a材料的强度、
数控铣削加工工艺设计及加工仿真
数控铣削加工工艺设计及加工仿真 题目数控铣削加工工艺设计及加工仿真 学院专业机械设计制造及其自动化年级 2009 级学号姓名指导 教师成绩 2013年 5 月 7 日 目录 摘 要 .................................................................... 1 关键 词 (1) Abstract ................................................................ 1 Key words (1) 1工艺方案的分析 ........................................................ 2 1.1零件图 .......................................................... 2 1.2零件图分析 ...................................................... 3 1.3加工方法 ........................................................ 3
1.4加工方案 ........................................................ 3 2工件的装 夹 (3) 2.1 定位基准 ........................................................ 3 2.2装夹方式的选择 .................................................. 3 3刀具及切削用 量 (3) 3.1选择数控刀具的原则 .............................................. 3 3.2选择数控铣削刀具 ................................................ 4 3.3切削用量 ........................................................ 4 4数控程序的编 制 (5) 4.1 Mastercam软件编程简介 .......................................... 5 4.2建立坐标系 ...................................................... 6 4.3Mastercam编程截图 ............................................... 6 4.4Mastercam编程程序 ............................................... 9 5数控加工程序的仿 真 (14)
数控铣削加工工艺范围及铣削方式
页脚内容1 数控铣削加工工艺范围及铣削方式 铣削是铣刀旋转作主运动,工件或铣刀作进给运动的切削加工方法。铣削的主要工作及刀具与工件的运动形式如图所示。 在铣削过程中,根据铣床,铣刀及运动形式的不同可将铣削分为如下几种: (1)根据铣床分类 根据铣床的结构将铣削方式分为 立铣和卧铣。由于数控铣削一个工序中一般要加工多个表面,所以常见的数控铣床多为立式铣床。 (2)根据铣刀分类 根据铣刀切削刃的形式和方位将铣削方式分为周铣和端铣。用分布于铣刀圆柱面上的刀齿铣削工作表面,称为周铣,如图6-2(a )所示;用分布于铣刀端平面上的刀齿进行铣削称为端铣,如图6-2 (b )所示。 图中平行于铣刀轴线测量的切削层参数ap 为背吃刀量。垂直于铣刀轴线测量的切削层参数ac 为切削宽度,fz 是每齿进给
量。单独的周铣和端铣主要用于加工平面类零件,数控铣削中常用周、端铣组合加工曲面和型腔。 (3)根据铣刀和工件的运动形式公类 根据铣刀和工作的相对运动将铣削方式分为顺铣和逆铣。铣削时,铣刀切出工件时的切削速度方向与工件的进给方向相同,称为顺铣如图(6-3)a 所示;铣削时,铣刀切入工件时的切削速度方向 与工件进给方向相反,称为逆铣,如图(6-3)b所示。 顺铣与逆铣比较:顺铣加工可以提高铣刀耐用度2~3倍, 工件表面粗糙度值较小,尤其在铣削难加工材料时,效果更 加明显。铣床工作台的纵向进给运动一般由丝杠和螺母来实 现,采用顺铣法加工时,对普通铣床首先要求铣床有消除进 给丝杠螺母副间隙的装置,避免工作台窜动;其次要求毛坯 表面没有破皮,工艺系统有足够的刚度。如果具备这样的条件,应当优先考虑采用顺铣,否则应采用逆铣。目前生产中采用逆铣加工方式的比较多。数控铣床采用无间隙的滚球丝杠传动,因此数控铣床均可采用顺铣加工。 数控铣削主要特点 (1)生产率高 (2)可选用不同的铣削方式 (3)断续切削 (4)半封闭切削 数控铣削主要加工对象 (1)平面类零件 页脚内容2
铣床对刀详细图解与手动编程-斯沃数控仿真软件
, FANUC OiM为铣床。是铣床加工中心。 右下方面板, 一、基础设置: 1、机床开关,程序保护,1行5 (第一行第5个按钮)归零, 点X轴归零,Y轴归零,Z 轴归零,右上面板出现 显示模式-床身显示模式,切换三种模式。 2、更换刀架类型:最上面的命令栏:机床操作,机床参数,。 3、机床操作,刀具管理,或左边命令栏的图标,选中编号001,添加到刀盘,1号刀位。 MDI手动输入方式(1行3),点右上角操作面板的程序,左边界面窗口,点MDI下面的按键, ,输入M06T01;,(记得点EOB键,最后加分号“;”), 插入,注意:接着把光标移动到程序的开头,不然会出现无法换刀。再回到右下面板,
循环启动(5行2)。装刀完毕, 工件操作-工件放置,调节工件在托架的位置。 工件操作-工件装夹-平口钳装夹,加紧上下调整,使工件突出平口钳。 二、开始对刀 1、 MDI手动输入方式(1行3),点右上角操作面板的程序,左边界面窗口,点MDI下面的按键,,输入MO3S500,(M03为 主轴正转,转速S为500r/min),回车换行,得到, 插入。(点,可选择上下指令。输错编程字母就取消,删除,替换,选择 上下字母)。回到右下面板。循环启动(5行2) 2、点击上方第二栏,XZ平面视图。JOG手动进给(1行6),点,使工件的 中点大概对正刀具的中心。如果觉得速度太慢,可点快速进给。点,把刀往下走。调整X、Y和Z方向(注意不要漏了Y方向,如果显示刀已切入工件,但没出现铁屑,则检查 Y方向)。微调时用(1行8)手轮进给,再点击机床界面左上角,,打开手轮界 面,方向指向Z,倍率为X100。直到轻轻碰到工件的左侧面。。
高速切削加工技术
高速切削加工技术 在现代机械切削加工技术中,高速切削正在越来越多地被人提及,其技术已开始被使用,随之而来的,首先是高速机床,那么,高速切削与传统切削技术究竟有什么不同? 其实现的条件是什么? 实现它有哪些益处? 其适用性怎么样呢? 本文将试图回答这些问题,并且尽可能结合目前在世界上居领先水平的瑞士MIKRON公司的机床的结构、特点来分析,用它同目前国内仍在普遍应用的传统的加工方法和切削理论相比较,促进高新技术在国内的应用和普及。 缩短加工时的切削与非切削时间,对于复杂形状和难加工材料及高硬度材料减少加工工序,最大限度地实现产品的高精度和高质量,是我们提高劳动生产率、实现经济性生产的一个重要的目标。有人认为,一提高速加工,就是主轴转速要几万转;只要主轴转速一达到几万转,就可以实现高速切削,这其实是不全面的。 随着科学技术的发展,现代机床已经具备了下面的条件,也只有具备这些条件,才会使得高速切削成为可能。 1.机电一体化的主轴,即所谓电主轴。现代化的主轴是电机与主轴有机地结合成一体,采用电子传感器来控制温度,自有的水冷或油冷循环系统,使得主轴在高速下成为“恒温”;又由于使用油雾润滑、混合陶瓷轴承等新技术,使得主轴可以免维护、长寿命、高精度。由于采用了机电一体化的主轴,减去了皮带轮、齿轮箱等中间环节,其主轴转速就可以轻而易举地达到0~42000r/min,甚至更高。不仅如此,由于结构简化,造价下降,精度和可*性提高,甚至机床的成本也下降了。噪声、振动源消除,主轴自身的热源也消除了。MIKRON公司便采用了本集团“STEP-TEC”公司生产的电主轴,这种电主轴采用了其特别的、最先进的矢量式闭环控制、高动平衡的主轴结构、油雾润滑的混合陶瓷轴承,可以随室温调整的温度控制系统,确保主轴在全部工作时间内温度衡定。 何为矢量式闭环控制呢?其实就是借助数/模转换,将交流异步电动机的电量值变换为直流电模型,这样,既可实现用无电刷的交流电机来实现直流电机的优点,即在低转速时,保持全额扭矩,功率全额输出,主轴电机快速起动和制动。以UCP710机床切削45#钢为例,用STEP-TEC 的主轴铣削,铣刀直径?63mm, 主轴转速为1770r/min,金切量为540cm3/min;在无底孔钻孔时,钻头直径?50mm, 转速1350r/min,可一次钻出,而无需常用的先打中心孔,而后钻孔再扩孔的方法。 2.机床普遍采用了线性的滚动导轨,代替过去的滑动导轨,其移动速度、摩擦阻力、动态响应,甚至阻尼效果都发生了质的改变。用手一推就可以将几百公斤甚至上千公斤的重工作台推动。其特有的双V型结构,大大提高了机床的抗扭能力;同时,由于磨损近乎为零,导轨的精度寿命较之过去提高几倍。又因为配合使用了数字伺服驱动电机,其进给和快速移动速度已经从过去最高的6m/min,提高到了现在的20~60m/min,MIKRON公司的最新型机床使用线性电机,进给和快移速度可达80m/min。 3.目前最先进的数控系统已经可以同时控制8根以上的轴,实现五轴五联动,甚至六轴五联动,多个CPU,数据块的处理时间不超过0.4ms;同时,均配置功能强大的后置处理软件,运算速度快,仿真能力强且具备程序运行中的“前视”功能,随时干预,随时修改。外接插口,数据传输速度快,甚至可以与以太网直联;加上全闭环的测量系统,配合使用数字伺服驱动技术,机床的线性移动可以实现1~2g的加速和减速运动。 4.机床床身结构进一步优化,现代机床均采用落地式床身,整体铸铁结构,龙门式框架的主轴立柱,尽可能由主轴部件来实现二轴甚至三轴的线性移动,考虑到刀具重量的变化极小,这样,在工件乃至工作台不进行快速线性移动的情况下,机床快速线性移动的部件的重量近乎常量,因此,更容易实现快速加速和减速情况下的运动惯量及实现动态平衡,减少由于动态冲击所带来的
advantedge三维铣削步骤
Advantage三维铣削仿真设置步骤 1.设置铣削类型: 1)新建选择3D; 2)弹出milling opinion单选框:刀具类型三选一,分别是solid tool (整体式)、indexable tool(机夹式)、stacked inserts(堆叠式)。 铣削方式六选一,分别是side cutting、Corner cutting、face milling、ramp milling、plunge milling、pocket milling。 3)上一步确定后,弹出选择顺逆铣。 2.导入刀具:(如果你要导入刀片就要在上一步中选择indexable tool)1)这里以STL格式为例,刀具在建模时坐标中心最好在模型对称中心上,可以避免导入后刀具定位的一些问题。 2)导入后弹出刀具在软件中定位、平移、旋转等选项可以设置。 其次还有,resolution分辨率、lend angle螺旋升角、radial rake angle 径向倾角、axial rake angle 轴向倾角、cutter diameter半径、number of teeth 刀片数。 3)导入后,应用redraw-tool and workpices 刷新视图。 4)tool material设置刀具材料、coating material设置刀具涂层材料。 3.设置工件: 1)create/edit standard workpiece 创建工件。可以设置工件几何参数。(长、宽、高)
2)workpiece material 设置工件材料。Region为各国标准,后面具体跟具体材料牌号;例如选JIS为日本标准,S45C就为国内45#钢。材料硬度可以默认,可以修改。 3)edit custom workpiece自定义新材料,给出软件定义新材料需要的各项参数即可。 4)设置好工件后,应用redraw-tool and workpices 刷新视图。4.仿真过程参数设置: 1)process-process parameters工艺参数设置:可以设置主轴转速、进给量、径向切深、纵向切深、温度、仿真度数等。 2)friction摩擦设置最好默认、coolant开启后最好默认、 注意这里最重要的是设置:径向切深、纵向切深即软件中的woc 和doc。对影响结果很大,必须计算正确。 5.运行仿真: 1)simulation-submit-submit current job。 2)耐心等待计算机运行完所设置度数。 6.查看结果: 1)simulation-results。 2)利用advantedge quick analysis可以查看:温度、力、应力、应变等。
高速铣削加工技术的主要优点及应用介绍
高速铣削加工技术的主要优点及应用介绍由于生产的发展和产品更新换代的速度加快,对模具的生产效率和制造质量提出了越来越高的要求,于是电火花加工存在的问题就暴露出来。所谓高速铣削是指主轴转速可达10000?C80000转/分,快速进给速度可达30-40米/分,加速度可达1g,换刀时间可提高到1-2秒并可获得粗糙度Ra0.6mm以上,还可以加工硬度达60HRC的模块。形成对电火花加工的挑战,它与传统铣削加工相比,具有温升低热变形小等优点。 从物理本质上来说,电火花加工是靠放电烧蚀的“微切削”工艺。对加工过程非常之缓慢表面进行局部高温放电烧蚀过程中,工件表面的物理机械性能会受到一定程度的损伤,常在型腔表面形成微细裂纹,表面粗糙度也达不到模具的要求,因而还有进行费力,费时手工研磨和抛光。因此,生产效率低,质量不稳定,模具已成为新产品开发速度的一关键因素,与电火花加工相比,高速铣削加工的主要优点:1、产品质量好。高速铣削以高于常规切削速度10倍左右的切削速度对零件进行高速加工,毛坯材料的余量还来不及充分变形在瞬间被切离工件、工件表面的残余应力非常小;切削过程的绝大多数热量约95%被切削屑带走,工件热变形小;高速加工过程中,机床主轴高速运转,激振频率远离“机床—刀具—工件”系统的固有频率范围,加工过程平稳无冲击。因此,零件的加工精度高,表面质量好,粗糙度可达0.6mm,型腔表面质量可达到磨削水平。
2、生产效率高。用高速铣削加工的模具,可在一次装夹中完成粗、精加工和模具零件其他部位的机械加工,即所谓“一次过”技术,不需后续的手工研磨与抛光,又容易实现加工过程自动化。它还能加工形状复杂的零件和薄壁零件。由于高速切削时切削力大为减少,尤其是横向(Py)切削力很小,这就有利于加工复杂模具型腔中一些细筋和薄壁,其壁厚甚至小于1mm。 总之高速铣削完全符合现代制造技术“高效率、高精度和高自动化”的发展方向,有广阔的应用前景。而电火花成型加工对一些尖角、窄槽、深小孔和过于复杂的型腔表面和精密加工还是有用的。两者应该扬长避短,相辅相成。建议先在厦门、福州、泉州等地有实力的企业,引进高速铣削机床,然后全省逐渐推广。 台州亚古机床设备有限公司 https://www.360docs.net/doc/cd1313280.html,
铣削仿真系统的开发与应用_万敏
铣削仿真系统的开发与应用 万敏,杨昀,张卫红 (西北工业大学现代设计与集成制造技术教育部重点实验室,陕西西安 710072) 摘要:铣削工艺过程的仿真已成为当今先进铣削加工技术的重要研究方向。本文基于本课题组对铣削工艺过程力学建模和仿真的理论成果,应用C#与MATLAB 混合编程技术,开发出具有铣削力系数标定、铣削力计算、加工误差分析、表面形貌仿真等功能的铣削工艺过程仿真系统,并对该系统的铣削力计算和铣削力系数标定功能进行了简要介绍。该系统可快速有效地预测铣削过程中的铣削力、加工零件的表面误差和表面形貌,结果可靠,具有一定的工程参考价值。 关键词:铣削;仿真;C#;MATLAB Development and application of milling simulation system WAN Min, YANG Yun, ZHANG Weihong (Key Laboratory of Contemporary Design & Integrated Manufacturing Technology, Ministry of Education, Northwestern Polytechnical University, Xi'An, Shaanxi710072, China) Abstract: Milling simulation has become a key issue for performing advanced machining technology. Based on the theoretical results, C# and MATLAB codes are integrated to develop a milling simulation system, which includes the modules of cutting force coefficient calibration, cutting force prediction, form errors prediction and surface topography simulation. As an example, a brief introduction to the cutting force prediction module and cutting force coefficients calibration module is given. This system can effectively predict the cutting force, the form error and the surface topography, etc. The prediction results are reliable and useful for practical engineering case. Key words: milling; simulation; C#; MATLAB 1 引言 随着数控技术的不断普及和应用,切削加工的加工效率和加工质量已经比早些年有大幅度的提高。为进一步提高切削加工效率和加工质量,近年来,国内外研究者将数控技术与计算机技术相结合,致力于切削过程仿真的研究[1]。因此切削过程仿真已成为先进铣削加工技术的研究核心。目前,切削过程仿真主要集中在切削力、加工误差、表面形貌、切削稳定性和误差控制等方面。本文基于所在课题组前期在铣削力建模、加工误差分析和表面形貌仿真等方面所做的研究[2-15],利用C#与MATLAB混合编程技术,开发出铣削过程仿真系统软件。该软件具有铣削力计算、加工误差分析、表面形貌仿真和铣削力系数标定等功能,并且仿真结果可靠。 2 软件结构功能 该软件以Visual C#为开发平台,利用C#与MATLAB混合编程开发[16,17]。MATLAB编写仿真系统中的核心算法,具有高效、方便的特点。Visual C#编写软件的
数控铣床加工零件及数控编程
辽宁工程技术大学《数控技术》综合训练二班级:机自14-2 学号: 姓名:张钦雷 指导教师:王洁 完成日期: 2017-04-20
任务书 一、设计原始资料 由教师指定。 二、设计任务 (1)对教师给定的装配体或零件进行设计,内容包括:二维图绘制和三维建模,建模软件可根据自己熟练程度选择。 (2)对零件进行结构分析,学生自行选择分析软件。 (3)针对某工步进行虚拟仿真制造,生成程序代码。 三、设计成果 (1)零件图(A4或A3)1张 (2)三维模型及仿真过程1份 (3)数控程序代码1份 (4)说明书(2000-5000字)1份 四、成绩评定 指导教师:王洁 日期: 摘要 本次研究的目的是加深对于二维,三维软件的应用,学习用数控仿真进行模拟加工。利用二维软件对零件进行结构和使用要求的分析。利用三维软件对零件尺寸进行建模。再通过CAM对零件进行加工轨迹,刀具参数,程序代码生
成等相关参数设定。进而生成仿真动画,立体直观的了解零件仿真的全过程。最后完成对零件仿真的整个过程。 关键词:二维软件,三维软件,建模,CAM,仿真 Abstract The purpose of this research is to deepen for 2 d, 3 d software applications, learning to use numerical simulation to simulate machining. Using two-dimensional software components for the analysis of the structure and the use requirement. Parts size to make use of 3 d software modeling. Travel through the CAM track of parts processing, cutting tool parameters, application code generation and related parameters setting. , in turn, generate simulation animation, three-dimensional visual simulation during the process of understanding of parts. Finally complete the whole process of simulation of parts. Keywords: 2 d software, 3 d software, modeling, CAM, simulation 目录 1.工件二维图形的绘制 (5) 1.1绘制二维图的软件 caxa (5) 1.2工件的平面图及零件加工工艺分析 (5) 2.工件的三维建模 (6) 2.1三维软件的介绍Inventor (6) 2.2工件的三维建模过程 (6) (7) (7) 3.工件的仿真 (11) 3.1仿真所用的软件 CAM (11) 3.2仿真过程及参数的确定 (12)