全液体空分工艺流程说明

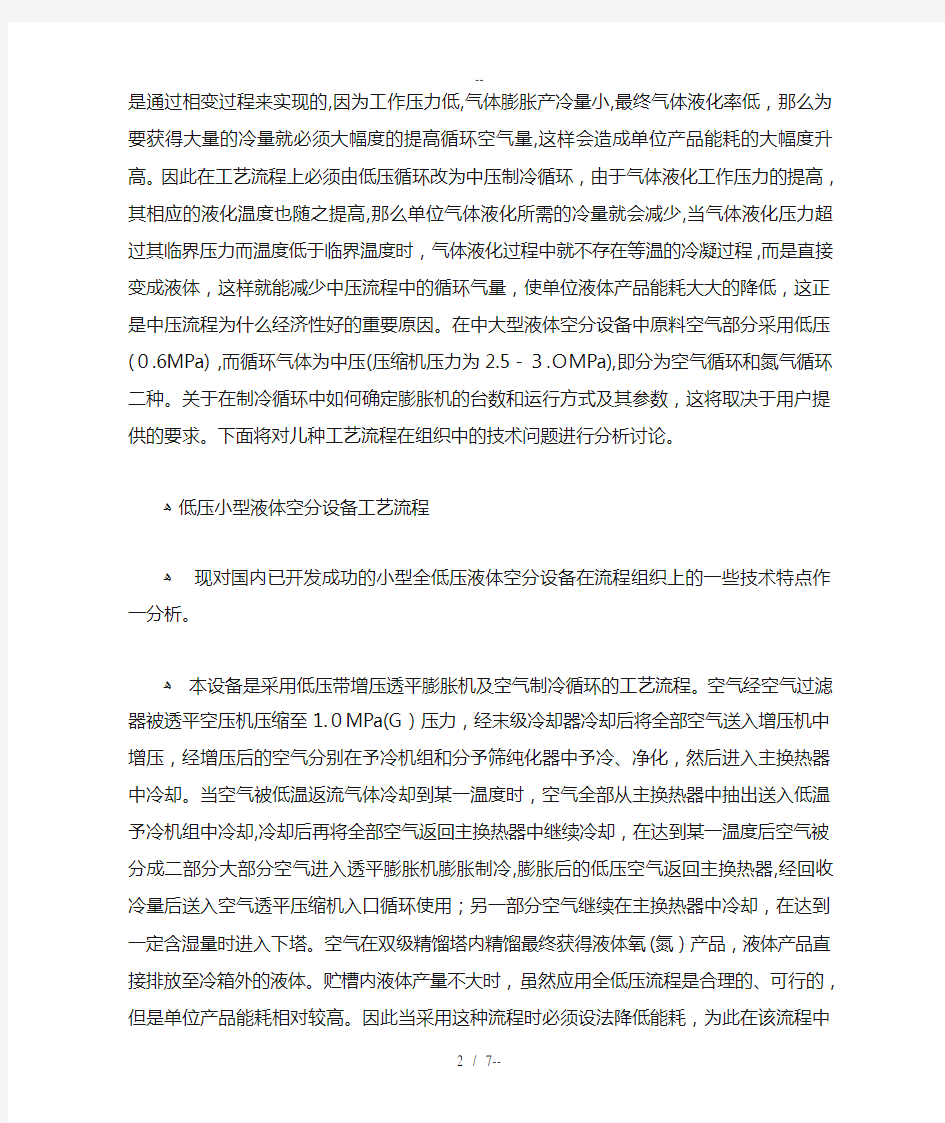
全液体空分工艺流程说明
液体空分设备通常是指以直接生产液氧、液氮产品的空分设备,这种空分设备一般不生产或少量生产气体产品。
为了要获得大量的液氧和液氮产品,目前大致有二种方法:一是先生产气态产品,然后再根据需要采用液化装置将气态产品液化,这种方法能耗相对较高;另一种方法是直接采用液体空气设备生产液氧和液氮产品,与前者相比该法能耗较低,液体空分设备从流程的组织上来看可以视为是常规气态产品空分设备和液化装置的二者结合体,因此其流程要相对复杂一些。为了降低液体空分设备产品的中耗,应根据用户提出的需求条件,在工艺流程的组织上要进行多个方案的技术比较。
?目前液体空分设备根据工作压力的等级不同,一般可分为低压循环和中压循环二大类,在低压循环中按照制冷系统的组织方式不同又分成带增压透平膨胀机制冷和带增压透平膨胀机加低温予冷机制冷的二种流程。在中压循环流程中因采用的制冷循环工质的不同一般分成空气循环和氮气循环,同样在中压循环中按照制冷系统的组织方式不同也分成带增压透平膨胀机加低温予冷机制冷和带高、低温增压透平膨胀机制冷的二种流程。
?液体空气设备流程的选择应根据用户提出的液体产品产量、纯度、品种等要求,来选择和确定液体空分设备的工艺流程、单元设备的结构形式和组织方式。一般来说液氧产量小于1000Lh的属小型液体空分设备,目前多数是采用全低压(1.OMPa)利用空气循环制冷的工艺流程。因为液体产量较小,同时为简化流程,达到操作方便,一般在流程中原料空气和制冷循环空气可由一台压缩机提供。这种流程单位产品能耗较高。
?当液体产品在2000-3000m立方/h(折成气态)以上时,将属于中大型液体空气设备,由于液体产品数量加大,要求装置必须提供更多的冷量。而在低压流程中气体的液化是通过相变过程来实现的,因为工作压力低,气体膨胀产冷量小,最终气体液化率低,那么为要获得大量的冷量就必须大幅度的提高循环空气量,这样会造成单位产品能耗的大幅度升高。因此在工艺流程上必须由低压循环改为中压制冷循环,由于气体液化工作压力的提高,其相应的液化温度也随之提高,那么单位气体液化所需的冷量就会减少,当气体液化压力超过其临界压力而温度低于临界温度时,气体液化过程中就不存在等温的冷凝过程,而是直接变成液体,这样就能减少中压流程中的循环气量,使单位液体产品能耗大大的降低,这正是中压流程为什么经济性好的重要原因。在中大型液体空分设备中原料空气部分采用低压(0.6MPa),而循环气体为中压(压缩机压力为2.5-3.OMPa),即分为空气循环和氮气循环二种。关于在制冷循环中如何确定膨胀机的台数和运行方式及其参数,这将取决于用户提供的要求。下面将对儿种工艺流程在组织中的技术问题进行分析讨论。
?低压小型液体空分设备工艺流程
?现对国内已开发成功的小型全低压液体空分设备在流程组织上的一些技术特点作一分析。
?本设备是采用低压带增压透平膨胀机及空气制冷循环的工艺流程。空气经空气过滤器被透平空压机压缩至1.0MPa(G)压力,经末级冷却器冷却后将全部空气送入增压机中增压,经增压后的空气分别在予冷机组和分予筛纯化器中予冷、净化,然后进入主换热器中冷却。当空气被低温返流气体冷却到某一温度时,空气全部从主换热器中抽出送入低温予冷机组中冷却,冷却后再将全部空气返回主换热器中继续冷却,在达到某一温度后空气被分成二部分大部分空气进入透平膨胀机膨胀制冷,膨胀后的低压空气返回主换热器,经回收冷量后送入空气透平压缩机入口循环使用;另一部分空气继续在主换热器中冷却,在达到一定含湿量时进
入下塔。空气在双级精馏塔内精馏最终获得液体氧(氮)产品,液体产品直接排放至冷箱外的液体。贮槽内液体产量不大时,虽然应用全低压流程是合理的、可行的,但是单位产品能耗相对较高。因此当采用这种流程时必须设法降低能耗,为此在该流程中采用了以下几项提高其经济性的措施:
?(1)采用全部空气进行增压,该法优于仅对膨胀部分空气进行增压的方法,因为这不尽提高了膨胀前空气压力,更重要的是提高了入塔部分空气的压力,由于入塔空气压力的提高,入塔空气的露点温度即液化温度也相应提高,从而可以提高膨胀前空气的温度,这有利于提高单位膨胀空气的制冷量。如果装置所需的冷量一定时,膨胀空气量就能减少,最终使总的加工空气量下降,经计算分析其能耗一般可下降约2%。?? (2)采用常温和低温二级予冷的方法,提高了有效能的利用,从计算得知入塔空气的液化率会有较大幅度的提高,单位液体产品的能耗一般可下降2-3%左右。?? (3)流程中采用了全部加工空气先经增压再进入予冷机组和分予筛纯化器的方法,由于工作压力升高,二机组的体积尺寸和分予筛吸附剂用量都将会相应减少,同时又选用了空气下进下出内加温节能型结构的分予筛纯化器。?? (4)冷箱内采用先进的保温措施。?
另外在这一流程的设计和选择中,曾考虑到空气从压缩机出来去增压的过程中,当环境温度过低时,管道内空气会发生机械水析出影响增压机叶轮寿命的问题。如改用压缩后的空气先经予冷、净化后再去增压或对膨胀部分的空气进行增压的方案,可避免这一问题发生,但经计算分析比较认为后者方案存在以下缺点:a)会引起加工空气和膨胀部分空气入塔温度升高;b)如仅对膨胀?部分空气增压会造成二股入塔空气温度不一致,同时换热器面积加大通道结构相对复什c)予冷、净化机组尺寸,分予筛吸附剂用量相应加大;d)操作不便,单位液体产品能耗高,最终没有被采用。
为了防止带压空气去增压的过程中,因环境温度过低会有机械水析出损坏增压机叶轮的问题,除在流程中增设特殊的水分器外,在工艺配管上又作了多项改进,这一设备在实际运行中,曾因环境温度变化出现过机械水析出,但由于所采用的措施正确,避免了机械水损坏增压机叶轮的问题。经实际运行考验情况良好,备项技术经济指标在同类产品中处于领先水平,这些技术在小型液体空分设备上的应用成功,具有一定的技术创新。
?中压空气循环膨胀制冷流程??目前中大型液体空分设备的需求量在不断增长,对于以液氧产品为第一工况的液体空分设备,应用空气循环流程是比较合适的,因为这种流程不仅可以获得液氧和部分液氮产品外,还可以最大限度的提取液氩产品。在中压空气循环流程中,膨胀制冷系统的组织方式现一般有二种一种是配置高、低温增压透平膨胀机;另一种是低温予冷机组加低温增压透平膨胀机。?
这一流程的特点是将分子筛纯化器后的低压空气和高、低温膨胀机膨胀后返回主换机器经冷量回收后的低压空气一起送至中压循环压缩机入口,经压缩后的中压空气分成二部分:一部分空气经主换热器冷却到一定温度后送入高温级增压透平膨胀机膨胀制冷,膨胀后的低压空气经主换热器回收冷量后返回至中压压缩机入口;另一部分空气直接进入高、低温级透平膨胀机的增压机中连续增压,增压后的这部分空气在主换热器中予冷到一定温度后再分成二股一股送入低温级增压透平膨胀机膨胀制冷后按规定量进入下塔;?另一股空气在主换热器中继续冷却当达到一定含湿量经节流后进入下塔,空气在双级精馏塔内精馏最终获得液体氧(氮)产品,液体产品直接排放至冷箱外的液体贮槽内。在流程中由于没有设置高温级透平膨胀机,那么经计算在流程中必须增设低温予冷机组,否则单位液体产品能耗将会上升。众所周知在流程中设置高温级透平膨胀机或低温予冷机组,其目的都是用来补充主换热器中热段的冷量,最终缩小主换热器热端温差,减少返流气量即循环空气量达到提高流程的经济性。为进一步降低单位产品的能耗,在配套部机的设计和选型中应作如下考虑:??原料空气和中压循环空气压缩机均采用高效定型的透平压缩机;分予筛纯化器应用双层床结构;主换热器
为高效、结构紧凑的中低压气体复合型板翅式换热器;上塔使用规整填料塔;氩的提取为全精馏制氩全套装置的控制采用当今较为先进的DCS系统。
?中压氮气循环膨胀制冷流程?
目前有很多用户要求在生产液氧产品的同时,又能够生产较大量的液氮产品,有的甚至液氮产量要超过液氧产量,在这种情况下为提高其整个液体空分装置的合理性和经济性,在工艺流程的组织上,建议采用氮气循环制冷的流程。??在流程中循环氮气的抽取方法现有二种:一种是从上塔顶部抽取低压产品氮气增压至中压;另一种是从下塔抽取压力氮气再增压至中压。关于制冷循环的组织与空气循环一样,有设置高、低温增压透平膨胀机的制冷循环和低温予冷机加低温增压透平膨胀机的制冷循环。?
流程的主要特点是采用由上塔顶出冷箱的低压产品氮气作为循环氮气和液氮产品的原料气,低压氮气经低压和中压二台透平压缩机压缩至2.5~3. OMPa压力,然后将压缩后的中压氮气分成二部分:一部分中压氮气在主换热器中予冷到一定温度后送入高温级增压透平膨胀机,膨胀后的氮气经主换热器回收冷量后返回至中压氮压?缩机入口;另一部分中压氮气直接送入高、低温级透平膨胀机的增压风机中连续增压,经过增压后的这部分压力较高的中压氮气经主换热器予冷到一定温度时再分成二股:一股送入低温级增压透平膨胀机,膨胀后的氮气经主换热器回收冷量后返回至中压氮压缩机入口;另一小股继续冷却经节流后生产液氮,其中一部分液氮作为产品,其余液氮送至下塔作回流液。流程的特点是从下塔抽取压力氮作为循环氮气并设有低温予冷机组。总之这种液体空分装置可以说是由一套全精馏的气体空分设备和一套氮循环的液化设备所组成。该流程完全可以根据用户要求在生产液氧、液氮产品的同时提取高纯氛和高纯氧等产品。
?流程组织中应注意的问题??工艺流程的确定依据和原则??液体空分设备的流程确定和组织,完全是针对用户的需求来进行的,其中产品数量、纯度、品种、能耗、控制水平和变工况参数等都是流程确定和组织中应考虑的重点。由于液体空分设备提供的是高品位的低温液体产品,单位产品能耗显然要高于气体空分设备,因此如何降低能耗就成了流程组织中的关键问题,同时液体空分设备的产量又受到产品储存、市场需求等因素的制约,所以在确定其产量规模时必须慎重。为进一步降低单位液体产品的能耗,在设计中应尽量做到选配高效定主主主}J产品,努力提高换热器和精馏设备的传热传质效率。
制冷循环方式的确定??对于只设置一台低温级增压透平膨胀机的中压空气循环和中压氮气循环的这二种流程,我们认为要提高其装置的经济性,降低单位液体产品能耗,经计算分析,在流程中应设置蒸发温度在-35℃了l右的低温予冷机组。
?当设置了高、低级膨胀机后,在流程中一般就不再配置低温予冷机组。这里应指出的是无论采用哪种循环流程,因为工作压力的提高,在提供的冷量一定时这将会造成进入膨胀机气体体积流量的减少,使高效透平膨胀机的设计及制造带来一定困难,为此必须对流程进行多个方案的计算比较,以便给膨胀机设计提供最佳的参数。对于液体空分设备中的膨胀机目前均希望能采用气体在含湿条件下工作的高效增压透平膨胀机,要求在该工况条件下能提供更多的为使产品液化的高品位冷量。?
精馏系统工况分析??通常在液体空分设备中进入下塔空气中的含湿量是相当大的,这会使下塔的精馏工况发生一定的变化,对于装置要在生产液氧、液氮产品的同时再提取高纯度氮、氧、氛产品,因此在对上、下塔的设计中一定要注意正确的解决好备物料的进出位置、塔板效率和塔板及填料结构等问题。例如在下塔的设计中为改善精馏工况和提高氛的提取率,一般将入下塔空气中的液空部分分离出来,并从入下塔空气位置向上计数的第9~12块塔板处导入为宜。?
关于如何提高液体空分设备氛提取率的问题,经计算分析发现氛的提取率与从下塔抽取的液氮产品量有着很大的关系。具体说液氮抽量直接影响到上塔精馏段的液气比大小,产品液
氮抽量加大,上塔精馏段液气比减小,氛提取率下降,如果液氮抽量达到入塔空气量的15%左右时,氛的提取率将大幅度下降,这与气体空分设备在提氛过程中,加大入上塔膨胀空气量会使氛提取率下降的影响是相类似的。
?关于装置的控制方法问题,对小型不带氩的液体空分设备一般选用PLC加就地控制柜的方法为宜;对中大型液体空分设备因系统组织复什、产品种类多,适宜选用DCS系统控制。??中大型液体空分设备目前国内生产的并不多,但具有良好的发展前景,随着精馏技术的不断提高,单位液体产品能耗的不断降低,因此液体空分设备的设计、制造一定会在不久的将来达到一个新的高度。