(完整版)疲劳分析的数值计算方法及ANSYS疲劳分析实例
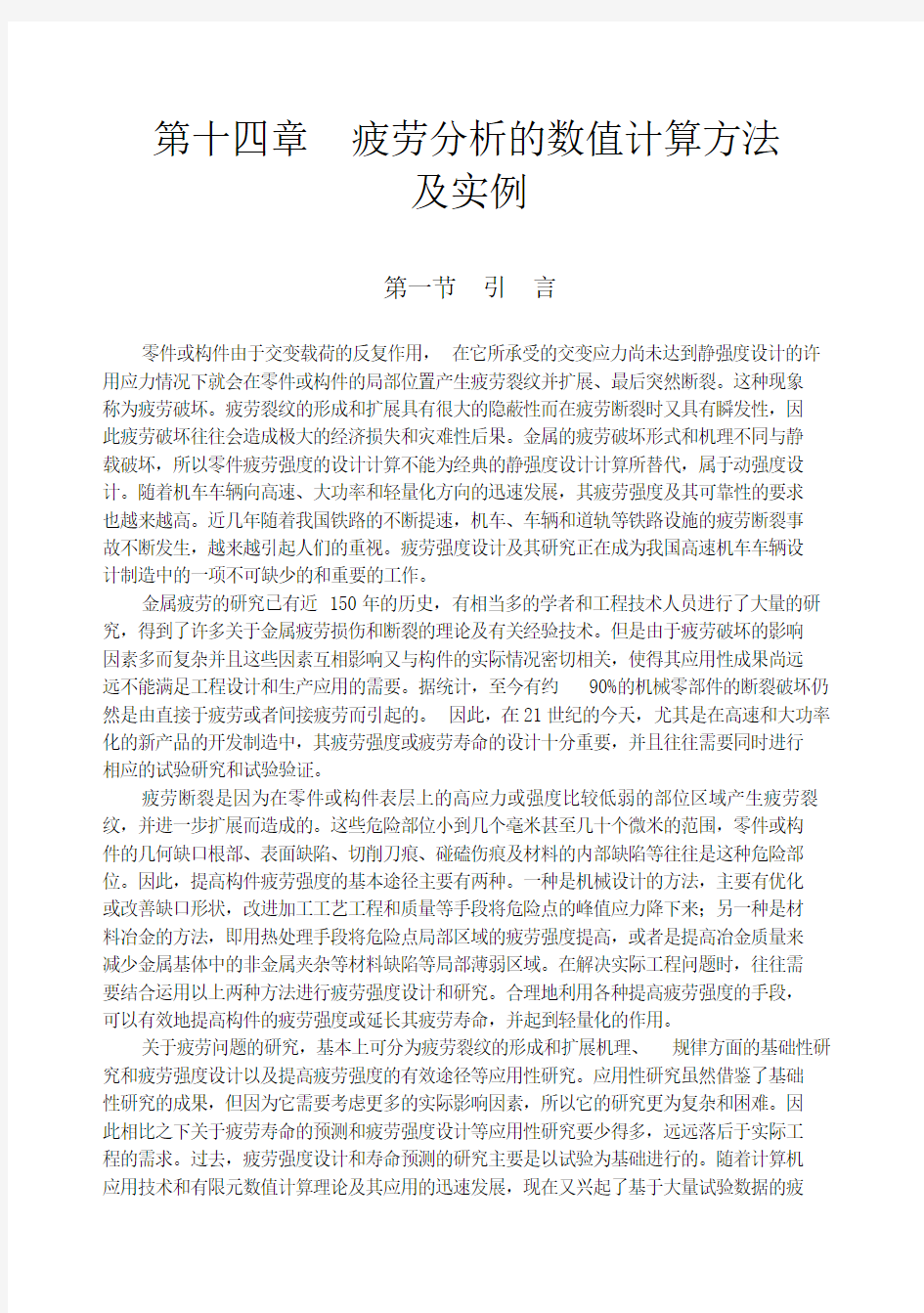

第十四章疲劳分析的数值计算方法
及实例
第一节引言
零件或构件由于交变载荷的反复作用,在它所承受的交变应力尚未达到静强度设计的许用应力情况下就会在零件或构件的局部位置产生疲劳裂纹并扩展、最后突然断裂。这种现象称为疲劳破坏。疲劳裂纹的形成和扩展具有很大的隐蔽性而在疲劳断裂时又具有瞬发性,因此疲劳破坏往往会造成极大的经济损失和灾难性后果。金属的疲劳破坏形式和机理不同与静载破坏,所以零件疲劳强度的设计计算不能为经典的静强度设计计算所替代,属于动强度设计。随着机车车辆向高速、大功率和轻量化方向的迅速发展,其疲劳强度及其可靠性的要求也越来越高。近几年随着我国铁路的不断提速,机车、车辆和道轨等铁路设施的疲劳断裂事故不断发生,越来越引起人们的重视。疲劳强度设计及其研究正在成为我国高速机车车辆设计制造中的一项不可缺少的和重要的工作。
金属疲劳的研究已有近150年的历史,有相当多的学者和工程技术人员进行了大量的研究,得到了许多关于金属疲劳损伤和断裂的理论及有关经验技术。但是由于疲劳破坏的影响因素多而复杂并且这些因素互相影响又与构件的实际情况密切相关,使得其应用性成果尚远远不能满足工程设计和生产应用的需要。据统计,至今有约90%的机械零部件的断裂破坏仍然是由直接于疲劳或者间接疲劳而引起的。因此,在21世纪的今天,尤其是在高速和大功率化的新产品的开发制造中,其疲劳强度或疲劳寿命的设计十分重要,并且往往需要同时进行相应的试验研究和试验验证。
疲劳断裂是因为在零件或构件表层上的高应力或强度比较低弱的部位区域产生疲劳裂纹,并进一步扩展而造成的。这些危险部位小到几个毫米甚至几十个微米的范围,零件或构件的几何缺口根部、表面缺陷、切削刀痕、碰磕伤痕及材料的内部缺陷等往往是这种危险部位。因此,提高构件疲劳强度的基本途径主要有两种。一种是机械设计的方法,主要有优化或改善缺口形状,改进加工工艺工程和质量等手段将危险点的峰值应力降下来;另一种是材料冶金的方法,即用热处理手段将危险点局部区域的疲劳强度提高,或者是提高冶金质量来减少金属基体中的非金属夹杂等材料缺陷等局部薄弱区域。在解决实际工程问题时,往往需要结合运用以上两种方法进行疲劳强度设计和研究。合理地利用各种提高疲劳强度的手段,可以有效地提高构件的疲劳强度或延长其疲劳寿命,并起到轻量化的作用。
关于疲劳问题的研究,基本上可分为疲劳裂纹的形成和扩展机理、规律方面的基础性研究和疲劳强度设计以及提高疲劳强度的有效途径等应用性研究。应用性研究虽然借鉴了基础性研究的成果,但因为它需要考虑更多的实际影响因素,所以它的研究更为复杂和困难。因此相比之下关于疲劳寿命的预测和疲劳强度设计等应用性研究要少得多,远远落后于实际工程的需求。过去,疲劳强度设计和寿命预测的研究主要是以试验为基础进行的。随着计算机应用技术和有限元数值计算理论及其应用的迅速发展,现在又兴起了基于大量试验数据的疲
劳强度设计和寿命计算的有限元数值计算方法,有力地推动着零部件疲劳强度设计的研究及应用的发展。
当前,业已发展形成了专用的疲劳分析软件,如MSC/FA TIGUE 等。此外许多著名的有限元分析软件也嵌套有功能较为齐全的疲劳强度计算模块,如MARC ,ANSYS ,以及I-Deas 中的CAE 等。这些软件疲劳强度计算模块的细节虽然不尽相同,但是其基本思路与算法大都相似。
本章将阐述疲劳强度设计的基本概念、疲劳强度的主要影响因素、疲劳强度设计的有关理论、基本设计方法等。最后,还将对疲劳强度分析的实例进行介绍。
第二节 疲劳载荷类型与S-N 曲线:
一、疲劳载荷的类型与基本术语
使零件或构件发生疲劳破坏的动载荷称为疲劳载荷,可分为为两类。一类是其大小和正负方向随时间周期性地变化的交变载荷,另一类是大小和正负方向随时间随机变化的随机载荷。交变载荷又称为循环载荷,是最为简单和基本的疲劳载荷形式。所研究结构部位因交变载荷引起的应力称为交变应力。
图14-1(a )是一个典型的交变应力-时间的变化历程。图中循环应力的大小和正负方(拉压)向随着时间的变化而作周期性的变化。一个周期的应力变化过程称为一个应力循环。应力循环特点可用循环中的最大应力σmax 、最小应力σmin 和周期T (或频率f=1/T )来描述。因为最大应力和最小应力的绝对值相等而正负号相反,故称这种交变载荷为对称循环应力。典型的循环载荷如圆轴类杆件的旋转弯曲、轴向拉压和平板零件的双向弯曲等,都可以在零件的表面或内部产生这样的交变应力。另外,轴类零件的双向扭转也可以产生类似的交变应力。
图14-1(a ) 对称循环交变载荷
图14-1(b ) 不对称循环交变载荷 在疲劳载荷的描述中经常使用应力幅σa 和应力范围△σ(也称为应力振幅、应力幅度)的概念,定义如下。 (14-1)
(14-2) a σσσσ2=-=?min max 2min max a σσσ-=
应力幅σa 反映了交变应力在一个应力循环中变化大小的程度,它是使金属构件发生疲劳破坏的根本原因。
当研究的部位除承受有动载荷外,还有静载分量荷时,动静载荷的共同作用下的应力-时间变化曲线如图14-1(b )所示。此时的载荷时间-变化曲线相当于把图14-1(a )的对称循环应力曲线向上平移一个了静应力分量。这种的循环载荷称为不对称循环载荷,并用最小应力与最大应力的比值R 来描述循环应力的不对称程度,R 称为应力比,有时又称为不对称系数,即
(14-4)
由定义可知,当R =-1时的循环应力即为对称循环应力,当R ≠0时统称不对称循环应力。其中,R =0时为拉伸脉动应力,R =-∞时为压缩脉动循环。
循环应力中的静载分量通常称为平均应力,用σm 表示,可由下式求出。
(14-5) 静载分量或平均应力对构件的疲劳强度有一定的影响。压缩平均应力往往提高构件的疲劳强度,而拉伸平均应力往往降低构件的疲劳强度。因此,在疲劳强度和疲劳寿命的研究中,给定一个循环应力水平时,需要同时给出应力幅σa 和应力比R 、或者同时给出最大应力σmax 和平均应力σm ,也有时直接给出最大应力σmax 和最小应力σmin 来表示循环应力水平。
由以上各式可知,在应力幅、平均应力、应力比、最大应力和最小应力的参数中,只要已知其中的两个便可求出其它。如当已知σa 、R 时,其它参数便可由下式得到。 (14-6) 或者已知或σa 、σm 时,
(14-7)
二、材料的S-N 曲线与基本术语
一般情况下,材料所承受的循环载荷的应力幅越小,到发生疲劳破断时所经历的应力循环次数越长。S-N 曲线就是材料所承受的应力幅水平与该应力幅下发生疲劳破坏时所经历的应力循环次数的关系曲线。S-N 曲线一般是使用标准试样进行疲劳试验获得的。如图14-2所示,纵坐标表示试样承受的应力幅,有时也表示为最大应力,但二者一般都用σ表示;横坐标表示应力循环次数,常用N f 表示。为使用方便,在双对数坐标系下S-N 曲线被近似简化成两条直线。但也有很多情况只对横坐标取对数,此时也常把S-N 曲线近似简化成两条直线。
S-N 曲线中的水平直线部分对应的应力水平就是材料的疲劳极限,其原意为材料经受无
max min σσ=R a m a a R R R
R R σσσσσσ-+=-=-=1121212min max 2
min max m σσσ+=a m a m σσσσσσ-=+=min max
图14-2 S-N 疲劳曲线
数次应力循环都不发生破坏的应力极限,对钢铁材料此“无限”的定义一般为107次应力循环。但现代高速疲劳试验机的研究成果表明,即使应力循环次数超过107材料仍然有可能发生疲劳断裂。不过107次的应力循环次数,对于实际的工程中的疲劳强度设计已经完全能够满足需要。疲劳极限又称持久极限,对于无缺口的光滑试样,多用σw0表示,而应力比R =-1时的疲劳极限常用σ-1来表示。某些不锈钢和有色金属的S-N 中没有水平直线部分,此时的疲劳极限都一般定义为108次应力循环下对应的应力幅水平。疲劳极限是材料抗疲劳能力的重要性能指标,也是进行疲劳强度的无限寿命设计的主要依据。
斜线部分给出了试样承受的应力幅水平与发生疲劳破断时所经历的应力循环次数之间的关系,多用如幂函数的形式表示。
(14-8)
式中σ为应力幅或最大应力,N 为达到疲劳破断时的应力循环次数,m ,C 材料常数。
如果给定一个应力循环次数,便可由上式求出或由斜线量出材料在该条件下所能承受的最大应力幅水平。反之,也可以由一定的工作应力幅求出对应的疲劳寿命。因为此时试样或材料所能承受的应力幅水平是与给定的应力循环次数相关联的,所以称之为条件疲劳极限,或称为疲劳强度。斜线部分是零部件疲劳强度的有限寿命设计或疲劳寿命计算的主要依据。
材料或构件到发生疲劳破坏时所经历的应力循环次数称为材料或构件的疲劳寿命,通常它包括疲劳裂纹的萌生寿命与扩展寿命之和。疲劳裂纹萌生寿命为构件从开始使用到局部区域产生疲劳损伤累积、萌生裂纹时的寿命;裂纹扩展寿命为构件在裂纹萌生后继续使用而导致裂纹扩展达到疲劳破坏时的寿命。在疲劳强度设计中,疲劳破坏可能被定义为疲劳破断或规定的报废限度。
S-N 曲线又称为应力-寿命曲线,主要用于构件的变形在弹性变形范围内的情形。一般说
来,这种应力状态下的疲劳达到破坏时的循环次数比较高,往往达到106以上,所以这种疲
劳又称为高周疲劳。相对地,达到疲劳破坏的循环次数较低时的疲劳称为低周疲劳,发生低周疲劳时构件在局部位置发生了塑性变形。近三十年来,对于低周疲劳,基于塑性应变幅εa
C N m =σN
的疲劳寿命曲线(εa -N )在工程中得到应用。对于带缺口的零件,其工作载荷变动较大时,在应力集中的局部区域将会发生塑性变形,此时疲劳寿命估算则要求基于应力和基于塑性应变的两种材料疲劳性能曲线。这种方法目前还不能用于高周疲劳的寿命估算。
第三节、疲劳强度的影响因素
通常我们通过手册所获得的S-N 曲线大多是无缺口的标准试样的试验结果。但是实际零部件的形状、尺寸、表面状态、工作环境和工作载荷的特点都可能大不相同,而这些因素都对零部件的疲劳强度产生很大的影响。疲劳强度的影响因素可分为力学、冶金学和环境三个方面。这些因素互相联系影响,使得在疲劳强度设计和疲劳寿命预测时,综合评价这些因素影响变得复杂。
三类因素中,力学因素从根本上讲可归结为应力集中和平均应力的影响;冶金学因素可归纳为冶金质量即材料的纯净度和材料的强度;而环境因素主要有腐蚀介质和高温的影响。对于铁路车辆零部件大多数的情况是在大气和常温环境下工作的,所以一般情况下应主要考虑力学和冶金学两类因素。它们包括缺口形状的影响、尺寸的影响、表面状态的影响和平均应力的影响等。关于这些因素对疲劳极限影响的具体数据相关的经验公式,可查阅有关手册和资料。这里主要讨论疲劳强度设计和疲劳寿命预测时需要了解的一些比较重要的影响规律或现象,以及必须或应该考虑到的注意事项。
一、缺口形状效应
零件或构件常常带有如轴肩类的台阶、螺栓孔和油孔、键槽等所谓的缺口。如图2-1所示,它们的共同特点是零件的横截面积在缺口处发生了突变,而在这些缺口根部应力会急剧升高,这种现象叫做应力集中。
缺口处的应力集中是造成零部件疲劳强度大幅度下降的最主要的因素。应力集中使得缺口根部的实际应力远大于名义应力,使该处产生疲劳裂纹,最终导致零件失效或破坏。应力集中的程度用应力集中系数(又称理论应力集中系数)K t 来描述,表达式如下。
(14-9)
这里,σmax 为最大应力,σ0为载荷除以缺口处净截面积所的得平均应力,又称名义应力。
在一定范围内,缺口根部的曲率半径ρ越小,应力集中程度越大,疲劳强度降低的程度也就越大。但是,对于低中碳钢等塑性材料,当缺口根部的曲率半径进一步减小甚至小于零点几个毫米时,疲劳强度的降低程度会变的越来越小甚至不再降低。此时应力集中系数就无法真实地反映缺口对疲劳强度的影响。因此常用疲劳缺口系数K f (fatigue notch factor ,过去又被称为有效应力集中系数)来更直接地反映疲劳强度的真实的降低程度。
(14-10)
这里,σw0,σw 分别为无缺口光滑试样和缺口试样的疲劳极限。
0σσmax =t K w wo f K σσ=
图14-4为钢的应力集中系数K t 与疲劳缺口系数K f 之间的关系。由图可见,对于低中碳钢,在应力集中系数小于2~2.5时K t 与K f 基本相同,但当超过此数值时,K f 的增长速度明显变慢。而对于高碳钢等强度比较高的钢,K f 随K t 线性递增的关系保持很长的范围。由此可知,高强度钢的疲劳强度对缺口的敏感性高而低中强度钢的疲劳强度对缺口的敏感性较低。
一般情况下,K f <K t ,但对于高碳钢尖锐缺口,还有可能存在K t >K f 的现象。对于螺栓类零件也存在这种现象,有时出现K t 为约4左右而K f 为8~10的情况。这主要是因为每个螺纹所分担的载荷不均甚至载荷几种在某扣螺纹上所致。
对于光滑材料,通过表面淬火、表面渗碳、表面氮化等表面热处理可以有效地提高其疲劳强度。但是对于缺口材料,这些方法可能变的没有效果甚至使疲劳强度反而降低。这是因为通过热处理使其表面强度提高的同时,使缺口敏感性也变高的缘故。图14-5为高强度钢和塑性较好的低强度钢的缺口材料的疲劳强度随应力集中程度的增加而变化的情况。在应力集中K t 较小的范围内,高强度钢的疲劳强度明显比低强度钢的高。但随着应力集中系数的增加,高强度钢的疲劳强度的降低速度明显大于低强度钢者,以致于高强度钢的疲劳强度与低强度钢的疲劳强度相差无几。
对于焊接构件,由于焊接热影响区在许多情况下恰好处于结构性缺口部位或在其附近,加之焊接缺陷、焊接残余拉应力的作用等,使得疲劳强度可能大幅下降几倍甚至十几倍。
疲劳缺口系数还受零部件尺寸大小的影响,一般地在具有相同缺口的情况下,随着尺寸的增大其疲劳缺口系数也有所增大。
因此对于缺口材料或带有缺口的零部件,为了提高其疲劳寿命,最有效的方法是合理地
応力集中系数K t 图14-4
钢的应力集中系数K t 与疲劳缺口系数K σ的关系
疲劳缺口系数K f
图14-5 缺口材料的疲劳强度随应力集中程度的变化
进行结构设计和工艺选择等手段来设法降低或改进它的应力集中情况。而一味地选用高强度钢材,未必能够达到目的,相反在表面较粗糙和尺寸较大的情况下有可能反而使构件的疲劳强度下降。
二、零件尺寸效应
用于疲劳试验的式样的直径一般都在5~10mm 的范围内,这和实际零部件的尺寸有很大的差异。一般地,对于弯曲和扭转载荷下的零件,随着尺寸的增大疲劳强度降低。但是对于轴向拉伸和压缩载荷的情况,尺寸大小的影响不大。尺寸对疲劳极限影响的大小用尺寸影响系数ε来表示。
(14-11)
这里,σd ,σd0分别为任意尺寸和标准尺寸光滑试样的疲劳极限。
高强度钢的尺寸效应比低强度钢的尺寸效应大,表面粗糙的零件的尺寸效应较大。 尺寸效应的产生主要是因为较大尺寸的材料的组织状态和应力梯度对疲劳强度产生了影响。材料的尺寸越大制造工艺过程越难控制,材料组织的致密性和均匀性等越差、冶金缺陷越多,表面积越大这些缺陷的数量也越多,因此大尺寸试样表面产生疲劳、裂纹的机会也就越大。而这些从根本上来说又都可以归结为冶金缺陷造成了局部应力集中而导致了疲劳裂纹的产生。
关于应力梯度的影响,在承受弯曲、扭转等载荷的情况下,零件的尺寸越大工作应力的梯度越小,单位面积内的平均应力就越高,疲劳裂纹越易产生。
三、表面状况的影响 表面状况包括表面粗糙度、表面应力状态、表面塑性变形程度和表面缺陷等因素。在试0d d σσε=
应力集中系数K t
验中采用的是表面磨光(或抛光)的标准试样,但实际的零部件的表面则往往是机械加工表面锻造表面和铸造表面。
机械加工会在零件表面产生塑性加工硬化。切削加工往往会在零件表面产生一定的残余压应力,这对疲劳强度是有利的但效果有限。但是在磨削时往往会产生对疲劳强度不利的残余拉应力。另一方面,机械加工表面的显微尺度上的凸凹不平引会起应力集中而使疲劳强度降低。这些因素综合作用的结果,使疲劳强度比标准试样的要降低一些。而锻造或铸造表面一般具有更高的表面粗糙度,且部存在表面加工硬化层和表面残余压应力,因此会更加明显地降低疲劳强度。因此从形式上看,越是粗糙的表面加工方法,对疲劳强度的降低影响就越大。表面加工状况对疲劳强度的影响用表面加工系数β来表示。
(14-12)
这里,σβ为某种表面状态下标准光滑试样的疲劳极限,σβ0为磨光标准光滑试样的疲劳极限,国外为表面磨光的标准光滑试样。
从冶金角度看,粗加工对高强度材料的疲劳强度的影响更大,以至于在粗加工状态下高强度钢可能起不到丝毫的提高疲劳强度的作用。这主要是因为高强度材料对粗糙表面的缺口敏感性高的缘故,加之机械加工对于高强度钢的表面的加工硬化作用也很小。
关于表面脱碳、表面碰磕伤痕和划伤等表面缺陷等对疲劳强度的影响的研究较少,但这些偶然原因造成的表面缺陷会对疲劳强度造成很大的影响。因此,在设计尤其是制造过程中需要给予足够的重视。
对于光滑材料,表面热处理等表面改性方法可以提高疲劳强度,但对于实际零部件等带有缺口的材料,这些方法都效果不大,甚至产生相反的作用。因此多用喷丸、辊压的方法使表面产生加工硬化和残余压应力,从而提高构件的疲劳强度,但是这两种方法一般对孔口类缺口的零件的疲劳强度的提高作用并不明显。
最新的研究表明,用简单的金属模具对孔口边缘进行少量倒角从而使缺口部位残生局部塑性变形的方法,对疲劳强度有明显的提高,甚至可以完全消除缺口降低疲劳极限的影响。过去大多认为,表面塑性加工的方法提高疲劳强度的主要原因是在表面产生了残余压应力从而抵消了部分工作应力的缘故。实际上是残余压应力在缺口部位产生的压缩集中应力抵消了缺口的不利影响;塑性变形使得缺口附近组织中的微小薄弱区域得到强化,使组织性能变的更加均匀一致,整体强度得到提高,从而使产生疲劳裂纹的应力水平得到提高。同时,残余压应力还使疲劳裂纹扩展停止而成为停留裂纹。
四、平均应力的影响
如前所述,产生疲劳破坏的根本原因是动应力分量,但静应力分量即平均应力对疲劳极限也有一定的影响。在一定的静应力范围内,压缩的静应力提高疲劳极限,拉伸的静应力降低疲劳极限。一般认为,残余应力对疲劳极限的作用同平均应力的作用相同。对一种材料, 可根据它在各种平均应力或应力比R 下的疲劳极限结果画出疲劳极限图。
图14-6的横坐标为平均应力σm (或残余应力)和强度极限σb 的比值,纵坐标为应力
0ββσσβ=
图14-6 钢在107次循环寿命下的疲劳极限线图
幅σa 和对称循环疲劳极限σ-1的比值,两者都是无量纲的量。从图中可以看出,多数试验数据点落在直线与曲线之间。这条直线称为古德曼(Goodman)线,见式(14-13);曲线就是杰柏(Gerber)抛物线,见式(14-14);用屈服极限σs 代替σb 得到索德柏格(Soderberg)线,见式(14-15);用断裂真应力σf 代替σb ,得到摩儒(Morrow)线,见式(14-16)。
Goodman 线 (14-13) Gerbe 线 (14-14) Sodeberrg 线 (14-15) Morrow 线 (14-16)
古德曼(Goodman)线对于延性金属略偏保守且简单方便,在疲劳设计中应用最广。常用的还有另一种叫做理想的改进Goodman 图。图14-7为工字形型钢对接梁弯曲疲劳载荷下理想的改进Goodman 图。横坐标表示最小应力σmin ,纵坐标表示最大应力σmax ,其直线方程式为
(14-17)
式中,m 是Goodman 线的斜率,b 为直线在y 轴上的截距,它是最小应力等于零时即脉动循环的疲劳极限。疲劳极限用最大应力表示时,即σw =σmax ,考虑到应力比R =σmax /σmin ,由式(14-6)有
)(b m a σσσσ-=-11])([211b m a σσσσ-=- )(s m a σσσσ-=-11)(f m a σσσσ-=-11b m +=min max
σσ
图14-7 理想的改进Goodman 图
(14-18)
由式(14-18)即可求出应力比为R 时的疲劳极限。实际车辆的具体结构要远比获得S-N 曲线时的试验条件复杂,例如焊接形式及应力集中等等,美国AAR 标准为我们提供了许多典型焊接结构疲劳强度方面的有价值的参考,所以,实际计算中的b 与m 均取自于AAR 标准。
试验研究表明,静载分量对应力集中系数、尺寸系数、表面系数的影响较小,可以忽略。
第四节 疲劳强度设计
通过设计计算来预测构件或零件的疲劳强度和疲劳寿命,是多少年来无数学者和工程技术人员孜孜以求的目标。但是至今还没能够形成一种对实际工程适用的、比较准确的疲劳强度和寿命的计算方法。这是因为,研究对象在结构上的千变万化、加工制造工艺及其质量的不稳定性、材料组织性能不稳定性和内部及表面缺陷的不确定性、外部载荷的复杂和随几性以及结构的动态响应问题等等,诸如这些因素很难归纳成为一个统一的物理或数学模型。因此至今关于疲劳强度的计算都有一定的误差存在甚至误差很。即使计算结果是比较准确的,其结果也具有统计性,而不是针对每一个零部件而言。
对于新产品的开发,应至少对于某些重要零部件等,同时进行试验研究和试验验证。如果受试验条件等的限制,可以根据零部件的特点进行合理简化来进行模拟性试验,这也是非常有用的。诸多纷杂的因素中,对于疲劳强度危害最大的是应力集中。因此,从设计和制造的过程来看,危害最大的第一是结构的不合理性;第二是工艺缺陷如焊接缺陷、机械加工缺陷、材料内部缺陷,还包括偶然因素造成的表面伤痕等等;第三是材料的选择。因此如果为提高疲劳强度,在设计和制造过程中最重要的就是降低应力集中。对于实际零部件还需要注意的是,因为其往往带有形状缺口,所以未必选择高强度钢就可提高其疲劳强度。
到目前为止,疲劳强度的设计实质上还是基于大量试验结果的估算。近年来已经出现了有关疲劳强度设计的专用软件,使得这项工作的效率更高和更易趋于合理准确,但对于它的mR b w -=1σ
使用同样需要具有一定的疲劳强度设计的经验。
疲劳强度设计包括疲劳安全系数的校核和疲劳寿命的估算两项内容。具体的设计计算方法有应力-寿命法和局部应力-应变法。局部应力应变法目前还只适用于零部件的应力集中处发生了塑性变形的低周疲劳。应力-寿命设计法主要用于只发生弹性变形的高周疲劳,设计所用的基本参数是零部件危险点处的名义应力,所以这种方法又叫名义应力法,它的研究和使用历史较长,资料丰富,至今仍被广泛使用。名义应力法包括无限寿命设计和有限寿命设计两种设计思路,本节只就名义应力法的内容进行讨论。
名义应力法的关键点也是它的难点有三,一是疲劳极限降低系数和应力-寿命曲线的确定,二是危险点应力的确定计算,三是外载荷的获得。而要解决好这些问题计算和试验而这都不可偏废。
一、无限寿命设计法
无限寿命设计法的基本思路是,使得零件或构件的危险部位的工作应力低于其疲劳极限,从而保证它在设计的工作应力下能够长久工作而不发生破坏。当零件的结构比较简单应力集中较小时,恒幅交变应力、过载应力小且次数很少时可用这种方法。对应力集中较大的构件使用该方法进行疲劳强度设计将会使结构变的粗大笨重。对于过载应力较大且次数较多的交变载荷情况和随机载荷一般也不宜采用此种方法。
(一)对称循环载荷:
R=-1,疲劳强度条件为
正应力 (14-19)
剪应力 (14-20)
式中,n σ,n τ-安全系数;σa ,τa -应力幅;
σ-1,τ-1,σ-1D ,τ-1D -分别为对称循环下材料和零件的疲劳极限,且有
(14-21)
式中,K σD ,K τD 是对称循环下零件的疲劳强度降低系数,它包含了前面讨论的疲劳强度的诸影响因素。该系数的选择无疑将对疲劳强度的估算产生很大的影响。它有多种计算用经验表达式形式,现只列出比较常见的几种。
(14-22) (14-23)
(14-24)
][n K n a D a D ≥==--σσσσσσ11][n K n a D a D ≥==--ττττττ11D D D D K K τσττσσ1111----==, )(11-+=βεσσK K D )]([111-+=βεσσK K D εβσσK K D =
式中, K σ,K τ-疲劳缺口系数,ε-尺寸系数,β-表面加工系数。
以上三式的主要不同点在于对表面加工系数β的处理。第一式认为β、K σ、ε三者互不影响;第二式认为β随着K σ的增加而减弱;第三式认为β随着K σ/ε值增加而减小。从试用的情况来看,在K σ较低的范围内三者的差别不大。在K σ较大的情况下,第一式的结果偏大,而第二式的结果比第三式的结果略大。关于表面粗糙度等表面加工情况对疲劳缺口系数的影响,未见到有关的研究报道。但参照多重缺口材料的疲劳缺口系数的研究结果推断,随着疲劳缺口变尖锐表面粗糙度的影响不应增大。考虑材料强度对表面加工系数的影响,高强度钢适合采用第二式,而对于塑性比较好的低中强度钢适合采用第三式。
(二)不对称循环载荷:
1.R 保持不变时的疲劳强度条件为
正应力
(14-25)
剪应力
(14-26)
式中,σaD ,τaD -应力比为R 时的疲劳极限;σm ,τm -平均应力;ψσ,ψτ-平均应力折算系数,对于Goodman 方程(14-13)有ψσ=σm /σb ,其它符号意义同上。
2.平均应力保持不变时:
(14-27)
式中符号意义同上。
二、有限寿命设计法
当交变载荷有较多的冲击过载或工作载荷为随机载荷时,工作应力在某些时刻会越过疲劳极限。此时,疲劳寿命设计主要是保证构件在设计的寿命之内不发生疲劳破坏而正常工作,也即设计使构件具有有限的疲劳寿命。考虑到偶然因素的影响,为确保安全在设计时一般使设计寿命为使用寿命的数倍。
有限寿命设计法主要基于疲劳累积损伤理论,故先作简单介绍然后讨论疲劳强度校核问题。
(一)迈因纳累积损伤理论:金属疲劳累积损伤的假说多达数十种,但其中最简单、适用的是迈因纳(Palmgren —Miner)理论,习惯称之为线性累积损伤理论。迈因纳理论认为材料的疲劳破坏是由于循环载荷的不断作用而产生损伤并不断积累造成的;疲劳损伤累积达到破坏时吸收的净功W 与疲劳载荷的历史无关,并且材料的疲劳损伤程度与应力循环次数成正比。设材料在某级应力下达到破坏时的应力循环次数为N 1、经n 1次应力循环而疲劳损伤吸收的净功为W 1,根据迈因纳理论有
][n K n m a D a aD ≥+==-σψσσσσσσσ1][n K n m a D a D a ≥+==-τψτττττττ1][n K n a D D a aD ≥-==-σψσσσσσσ111
1N n W W =
则在i 个应力水平级别下分别对应经过n i 次应力循环时,材料疲劳累积损伤为 (14-28)
式中,n i —第i 级应力水平下经过的应力循环数;N i —第i 级应力水平下的达到破坏时的应力循环数。
当D 值等于1时,认为被评估对象开始破坏。
应该指出迈因纳理论没有考虑加载顺序的影响和平均应力的影响,只是一种近似理论。但是,由于该理论简单便于利用,在工程上得到了广泛应用。针线性累积损伤理论所存在的问题,又提出了非线性累积损伤理论以提高其计算精度,但应用不如前者广。
(二)随机载荷的处理
零部件承受的变幅载荷尤其是对承受随机载荷实需要测得到。利用累积损伤理论进行疲劳设计时,需要先对实测得到的载荷-时间历程进行编谱,即用概率统计的方法将其简化成典型的载荷谱或应力谱。因为引起疲劳的最根本的原因是动载分量应力幅值和它的循环次数,所以一般用统计记数法来处理波形与频次的关系等问题。在各种统计记数法中,被国际上广泛用于疲劳强度设计的是雨流计数法,它被认为最符合材料的疲劳损伤规律。这种方法把整个载荷-时间历程中出现的应力幅范围划分为若干个等差的应力幅级别,然后统计出各级应力幅级别内所出现的循环次数,从而得到载荷-频次曲线等各种形式的载荷的统计结果。
实测的载荷-时间历程的半波数往往是数以几十万、几百万个,用手算的方法几乎是不可能的。所以工程上编制了雨流法的计算机处理程序,可以便捷地进行编谱分析。
(三)疲劳强度校核:设计中为保证不发生疲劳破坏,需D ≤1,即
(14-29)
由式(4-18)得
(14-30)
(14-29)左边分子与分母同乘以σi m 并结合(14-30),可得安全强度条件
故等效应力σd 为
(14-31) 安全系数
(14-32)
式中,N 0—S-N 曲线的拐点对应的循环数; ∑=i i N n D 1≤∑i i N n 10-≤∑σσm i m i N n N N m i m i d N n N N ∑
=σσ0
d D d D K n σσσσσ111---==01N N m i m i -=σσ
σ-1 —材料疲劳极限;
m —式(14-8)中的指数;
σi —第i 级应力水平的应力幅;
N i —第i 级应力水平的循环应力作用下,材料达到破坏时的应力循环次数;
N —设计疲劳寿命即总应力循环次数;
n i —在设计疲劳寿命下第i 级应力水平的循环次数;
n i /N —第i 级应力的循环次数与总应力循环次数之比,当载荷谱已知时为一不变值; K -iD 同前。
可见随着设计寿命的增加,等效应力增大而安全系数降低。
(四)疲劳寿命估算:根据迈因纳理论,达到疲劳破坏时有
(14-33)
式中,N T 为载荷谱下出现损伤的循环次数即所求的总寿命;n i 为i 级应力水平σi 的循环次数;αi 为i 级应力水平σi 的循环次数在总寿命中所占比例;N i 表示在应力σi 作用下导致破坏的循环数。在应力谱已知的情况下,N i 的估算是此项估算工作的关键。
对于每级应力水平下导致的破坏循环寿命的确定,可参照工程标准,许多软件安排了一些常用的准则供用户选用。这里仅以I-Deas 为例,即:
(1) 应力-寿命(Stress life )准则
(2) 应变-寿命(Strain life )准则
(3) SWT 准则(Smith-Watson ——Topper )
(4) 美国机械工程学会(ASME )锅炉和压力容器规范
(5) 英国焊接研究所(BWI )公式(Btitish Weld Institute formulation )
另外,它还允许用户自定义些特殊的应力或应变寿命准则,程序为此已留有相应的接口。 以应力-寿命(Stress life )准则确定N i ,是依据材料的应力寿命曲线或零件本身的应力寿命曲线的斜线部分来确定。首先可用应变片测定危险点处的应力或用材料力学或有限元等方法求出危险点的应力幅σa ,然后再根据斜线部分求出对应于应力水平K --1D σi 时的断裂寿命即为所求N i 。如果使用零件的S-N 曲线进行计算则可直接根据此曲线求得对应于应力幅σa 的N i 。也可先根据材料的S-N 曲线等现有资料对材料的S-N 曲线进行修整从而得到画出零件的S-N 曲线,然后进行与上相同的N i 的计算。在以上三种方法中,要根据所掌握资料的情况,优先选择最接近所设计对象的一种。
三、复合应力下的疲劳强度设计
以上讨论是单向应力的情况,对于复合应力的情况也也有类似的疲劳强度校核与疲劳寿命的估算方法,只是此时所用的应力幅变成了对应强度理论下的等效应力幅,下面作一简单讨论。
1=?=∑
∑T i i T i i N n N N N n )/(i i T N N α∑=1T i N n =α
在构件危险点处的应力分别为σx 、σy 、σz 、τxy 、τyz 、τzx 时,该处的第三、第四强度理论的等效应力分别为 (14-34)
(14-35)
用主应力表示时,分别有
(14-36)
(14-37)
这时的强度条件的一般表式为
(14-38)
式中,K σD 、σ-1、σd 为疲劳强度降低系数、材料的疲劳极限和对应的等效应力。
试验表明,在平面弯扭组合疲劳应力σ、τ的情况下,高当材料达到疲劳破坏时满足如下方程
(14-39)
式中,σ-1、τ-1分别为材料的弯曲和扭转的疲劳极限,此式由高夫首先提出。该式两边同乘以σ-1并开方,有
对于σ-1、τ-1,在第三、第四强度理论时分别有,
(14-40) 故上式又可变为
(14-41)
(14-42)
式(14-39)式(14-40)正好是式(14-32)和式(14-33)在平面弯扭组合情况下的结果。由零件的疲劳强度校核条件式(14-36)及式(14-38),有
(14-43)
313σσσ-=d 2
234xy y x d τσσσ+-=)()(])()()[(2222224321zx yz xy x z z y y x d τττσσσσσσσ+++-+-+-=])()()[(223232221421σσσσσσσ-+-+-=d d D K n σσσ1-=12121=???? ??+???? ??--ττσσ122112---=???? ??+σττσσ1224-=+στσ1223-=+στσ212111)/()/(---+==ττσσσσσσσD D d D K K K n 3
4211211==----)/(,)/(τστσ
设n σ=σ-1/σ,n τ=τ-1/σ-1,分别为纯弯和纯扭转时安全系数,则上式为
(14-44)
以上疲劳强度校核公式适用于钢等延性材料,载荷为对称循环。
对于非对称循环载荷,有类似公式
(14-45)
式中,σrd -应力比为r 时的等效应力
(14-46)
式中,ψσ-平均应力折算系数,见式(14-26)。
第五节 如何用有限元法进行疲劳分析
一、有限元法疲劳分析的基本思路
用有限元法进行疲劳分析,其基本思路是:首先进行静或动强度分析,然后进入到后处理器取出相关的应力应变结果,在后处理器中再定义载荷事件,循环材料特性,接着根据所需要的疲劳准则对每一个载荷事件进行寿命计算,最后根据累计损伤理论判断是否开始破坏。由于结构受力状态往往是一复杂的应力状态,而在实验中测得的结构材料S-N 曲线又常是在简单应力状态下获得的,因此常用最小能量屈服准则或其它等效准则,将所研究的疲劳点上的复杂应力用一个等效应力替代。对有限元法而言,这一过程很容易实现。等效替代以后,即可参照原始材料的S-N 曲线进行疲劳寿命评估。上述方法称之为应力-寿命法或S-N 法,该方法不严格区分裂纹产生和裂纹扩展,而是给出结构发生突然失效前的全寿命估计。当然,还可以采用更加现代化的局部应变法或初始裂纹法。因篇幅所限,下面结合I-Deas 软件,仅讨论S-N 法。
二、I-DEAS 疲劳分析
I-DEAS 软件可以进行静态疲劳分析(Static Durability Analysis)、瞬态疲劳分析(Transient Durability Analysis)。
由于车辆结构的零部件属于低应力、高循环疲劳,故常使用Stress life 准则,并使用修正Goodman 图,此时,S-N 曲线的经验公式修正为:
(14-47)
计算中需要的材料参数包括:弹性模量、疲劳强度系数、疲劳强度指数、强度极限。 其具体的分析过程是:
1. 建立物理模型(Physical Model)
对于疲劳分析来说,物理模型即包含结点、单元、物理特性和材料特性的有限元模型。 b f m a )(2N )-(b f b σσσσσ'=2211τσn n n /+=rd D K n σσσ1-=m D d rd K σ?σσσσ+=
图14-7 定义事件流程图
2.建立数学模型(Mathematical Model)
数学模型也就是使用物理模型计算应力或应变。可通过 Model Solution或其它求解
器来建立。求解后,可从后处理器中获取相关的应力或应变。
3.荷工况(Loading Conditions)
对于静态疲劳分析来说,可以用建立载荷函数的方式施加载荷。
4.定义事件(Events)
在进行疲劳评估之前,必须先定义事件。它由物理模型、数学模型、载荷工况组成,如图14-7所示。
5.评估(Evaluation)
一般来说,我们可进行下列估算:
●事件损伤(Event Damage)
●事件损伤方向(Event Damage Direction)
●损伤累积(Accumulated Damage)
●事件寿命估算(Event Life Estimate)
6.后处理(Post Processing)
疲劳分析的后处理与静力学的后处理完全一致,此处不再重复。
第六节实例分析
一、摇枕的疲劳累积损伤分析及结果评价
选择一个转向架摇枕进行疲劳分析,并参照TB/T1959-91《铁道货车铸钢摇枕试验评定方法》进行。
图 14-8 摇枕(俯视图)
图 14-9 摇枕(仰视图)
(一)试验载荷
B1 B2 R
2.3P 0.32P 1.0P
其中:P—一个转向架承受的总载荷
P=(2x轴重-转向架自重)·g(KN)
P=444.4KN
B1 B2 R
1022.1KN 142.21KN 444.4KN
摇枕侧滚载、浮沉载荷曲线及加载位置如图14-10,载荷R在旁承Z、Z’点交替进行加载,载荷B1、B2在心盘Q点进行加载。
(a)加载位置
(b)侧滚与浮沉载荷
图14-10 侧滚与浮沉载荷加载位置
侧滚频率为:1.25Hz
浮沉频率为:5.0Hz
载荷循环次数
侧滚载荷循环(Z-Z’) 25,000
浮沉载荷循环(作用于心盘中心Q) 75,000
总计100,000
载荷型式循环次数
侧滚载荷循环(Z-Z’) 175,000
浮沉载荷循环(作用于心盘中心Q) 525,000
总计700,000
(二)摇枕疲劳分析过程
(1)对摇枕划分有限元网格后,在Z、Z’、Q点按照静力学求解方式分别建立Load Set,并求解。
(2)建立侧滚载荷函数f_cycle_z、f_cycle_z1、和沉浮载荷函数f_cycle_q。
(3)将f_cycle_z、f_cycle_z1分别施加于Z、Z’,形成一个事件,设定循环次数为25000,计算其损伤。
(4)进入Post Process,检查结果。若累积损伤<1,说明未损伤;若累积损伤≥1,则认为结构已经破坏。
(5)将f_cycle_q施加于Q,形成一个事件,设定循环次数为75000,计算其损伤及与上一事件的累积损伤。
(6)进入Post Process,检查结果。若累积损伤<1,说明未损伤;若累积损伤≥1,则认为结构已经破坏。
(7)重复(3)-(6)步骤,并在(3)中计算损伤累积,若累积损伤<1,未损伤;若累积损伤≥1,则认为结构已破坏,停止计算。若累积循环次数达到700000次,也停止计算。
(三)结果评价
从计算来看,累积损伤<1,表明该构件安全。计算结果如图14-11、12、13所示。
ansys疲劳分析基本方法
疲劳是指结构在低于静态极限强度载荷的重复载荷作用下,出现断裂破坏的现象。例如一根能够承受300 KN 拉力作用的钢杆,在200 KN 循环载荷作用下,经历1,000,000 次循环后亦会破坏。导致疲劳破坏的主要因素如下: 载荷的循环次数; 每一个循环的应力幅; 每一个循环的平均应力; 存在局部应力集中现象。 真正的疲劳计算要考虑所有这些因素,因为在预测其生命周期时,它计算“消耗”的某个部件是如何形成的。 3.1.1 ANSYS程序处理疲劳问题的过程 ANSYS 疲劳计算以ASME锅炉和压力容器规范(ASME Boiler and Pressure Vessel Code)第三节(和第八节第二部分)作为计算的依据,采用简化了的弹塑性假设和Mimer累积疲劳准则。 除了根据ASME 规范所建立的规则进行疲劳计算外,用户也可编写自己的宏指令,或选用合适的第三方程序,利用ANSYS 计算的结果进行疲劳计算。《ANSYS APDL Programmer‘s Guide》讨论了上述二种功能。
ANSYS程序的疲劳计算能力如下: 对现有的应力结果进行后处理,以确定体单元或壳单元模型的疲劳寿命耗用系数(fatigue usage factors)(用于疲劳计算的线单元模型的应力必须人工输入); 可以在一系列预先选定的位置上,确定一定数目的事件及组成这些事件的载荷,然后把这些位置上的应力储存起来; 可以在每一个位置上定义应力集中系数和给每一个事件定义比例系数。 3.1.2 基本术语 位置(Location):在模型上储存疲劳应力的节点。这些节点是结构上某些容易产生疲劳破坏的位置。 事件(Event):是在特定的应力循环过程中,在不同时刻的一系列应力状态,见本章§3.2.3.4。 载荷(Loading):是事件的一部分,是其中一个应力状态。 应力幅:两个载荷之间应力状态之差的度量。程序不考虑应力平均值对结果的影响。 3.2 疲劳计算
ansys疲劳分析解析
1.1 疲劳概述 结构失效的一个常见原因是疲劳,其造成破坏与重复加载有关。疲劳通常分为两类:高周疲劳是当载荷的循环(重复)次数高(如1e4 -1e9)的情况下产生的。因此,应力通常比材料的极限强度低,应力疲劳(Stress-based)用于高周疲劳;低周疲劳是在循环次数相对较低时发生的。塑性变形常常伴随低周疲劳,其阐明了短疲劳寿命。一般认为应变疲劳(strain-based)应该用于低周疲劳计算。 在设计仿真中,疲劳模块拓展程序(Fatigue Module add-on)采用的是基于应力疲劳(stress-based)理论,它适用于高周疲劳。接下来,我们将对基于应力疲劳理论的处理方法进行讨论。 1.2 恒定振幅载荷 在前面曾提到,疲劳是由于重复加载引起: 当最大和最小的应力水平恒定时,称为恒定振幅载荷,我们将针对这种最简单的形式,首先进行讨论。 否则,则称为变化振幅或非恒定振幅载荷。 1.3 成比例载荷 载荷可以是比例载荷,也可以非比例载荷: 比例载荷,是指主应力的比例是恒定的,并且主应力的削减不随时间变化,这实质意味着由于载荷的增加或反作用的造成的响应很容易得到计算。 相反,非比例载荷没有隐含各应力之间相互的关系,典型情况包括: σ1/σ2=constant 在两个不同载荷工况间的交替变化; 交变载荷叠加在静载荷上; 非线性边界条件。 1.4 应力定义
考虑在最大最小应力值σmin和σmax作用下的比例载荷、恒定振幅的情况: 应力范围Δσ定义为(σmax-σmin) 平均应力σm定义为(σmax+σmin)/2 应力幅或交变应力σa是Δσ/2 应力比R是σmin/σmax 当施加的是大小相等且方向相反的载荷时,发生的是对称循环载荷。这就是σm=0,R=-1的情况。 当施加载荷后又撤除该载荷,将发生脉动循环载荷。这就是σm=σmax/2,R=0的情况。 1.5 应力-寿命曲线 载荷与疲劳失效的关系,采用的是应力-寿命曲线或S-N曲线来表示: (1)若某一部件在承受循环载荷, 经过一定的循环次数后,该部件裂纹或破坏将会发展,而且有可能导致失效; (2)如果同个部件作用在更高的载荷下,导致失效的载荷循环次数将减少; (3)应力-寿命曲线或S-N曲线,展示出应力幅与失效循环次数的关系。 S-N曲线是通过对试件做疲劳测试得到的弯曲或轴向测试反映的是单轴的应力状态,影响S-N曲线的因素很多,其中的一些需要的注意,如下: 材料的延展性,材料的加工工艺,几何形状信息,包括表面光滑度、残余应力以及存在的应力集中,载荷环境,包括平均应力、温度和化学环境,例如,压缩平均应力比零平均应力的疲劳寿命长,相反,拉伸平均应力比零平均应力的疲劳寿命短,对压缩和拉伸平均应力,平均应力将分别提高和降低S-N曲线。 因此,记住以下几点:一个部件通常经受多轴应力状态。如果疲劳数据(S-N 曲线)是从反映单轴应力状态的测试中得到的,那么在计算寿命时就要注意:(1)设计仿真为用户提供了如何把结果和S-N曲线相关联的选择,包括多轴应力的选择;(2)双轴应力结果有助于计算在给定位置的情况。 平均应力影响疲劳寿命,并且变换在S-N曲线的上方位置与下方位置(反映出在给定应力幅下的寿
ansys疲劳分析基本方法
疲劳就是指结构在低于静态极限强度载荷的重复载荷作用下,出现断裂破坏的现象。例如一根能够承受 300 KN 拉力作用的钢杆,在 200 KN 循环载荷作用下,经历 1,000,000 次循环后亦会破坏。导致疲劳破坏的主要因素如下: 载荷的循环次数; 每一个循环的应力幅; 每一个循环的平均应力; 存在局部应力集中现象。 真正的疲劳计算要考虑所有这些因素,因为在预测其生命周期时,它计算“消耗”的某个部件就是如何形成的。 3、1、1 ANSYS程序处理疲劳问题的过程 ANSYS 疲劳计算以ASME锅炉与压力容器规范(ASME Boiler and Pressure Vessel Code)第三节(与第八节第二部分)作为计算的依据,采用简化了的弹塑性假设与Mimer累积疲劳准则。 除了根据 ASME 规范所建立的规则进行疲劳计算外,用户也可编写自己的宏指令,或选用合适的第三方程序,利用 ANSYS 计算的结果进行疲劳计算。《ANSYS APDL Programmer‘s Guide》讨论了上述二种功能。 ANSYS程序的疲劳计算能力如下: 对现有的应力结果进行后处理,以确定体单元或壳单元模型的疲劳寿命耗用系数(fatigue usage factors)(用于疲劳计算的线单元模型的应力必须人工输入); 可以在一系列预先选定的位置上,确定一定数目的事件及组成这些事件的载荷,然后把这些位置上的应力储存起来; 可以在每一个位置上定义应力集中系数与给每一个事件定义比例系数。 3、1、2 基本术语 位置(Location):在模型上储存疲劳应力的节点。这些节点就是结构上某些容易产生疲劳破坏的位置。 事件(Event):就是在特定的应力循环过程中,在不同时刻的一系列
ANSYSWORKBENCH疲劳分析指南第三章
ANSYSWORKBENCH疲劳分析指南第三章 发表时间:2009-2-21 作者: 安世亚太来源: e-works 关键字: CAE ansys Workbench疲劳分析 第三章不稳定振幅的疲劳 在前面一章中,考察了恒定振幅和比例载荷的情况,并涉及到最大和最小振幅在保持恒定的情况下的循环或重复载荷。在本章将针对不定振幅、比例载荷情况,尽管载荷仍是成比例的,但应力幅和平均应力却是随时间变化的。 3.1 不规律载荷的历程和循环(History and Cycles) 对于不规律载荷历程,需要进行特殊处理: 计算不规律载荷历程的循环所使用的是“雨流”rainflow循环计算,“雨流”循环计算(Rainflowcycle counting)是用于把不规律应力历程转化为用于疲劳计算的循环的一种技术(如右面例子),先计算不同的“平均”应力和应力幅(“range”)的循环,然后使用这组“雨流”循环完成疲劳计算。 损伤累加是通过Palmgren-Miner 法则完成的,Palmgren-Miner法则的基本思想是:在一个给定的平均应力和应力幅下,每次循环用到有效寿命占总和的百分之几。对于在一个给定应力幅下的循环次数Ni,随着循环次数达到失效次数Nfi时,寿命用尽,达到失效。 “雨流”循环计算和Palmgren-Miner损伤累加都用于不定振幅情况。 因此,任何任意载荷历程都可以切分成一个不同的平均值和范围值的循环阵列(“多个竖条”),右图是“雨流”阵列,指出了在每个平均值和范围值下所计算的循环次数,较高值表示这些循环的将出现在载荷历程中。 在一个疲劳分析完成以后,每个“竖条”(即“循环”)造成的损伤量将被绘出,对于“雨流”阵列中的每个“竖条”(bin),显示的是对应的所用掉的寿命量的百分比。在这个例子中,即使大多数循环发生在低范围/平均值,但高范围(range)循环仍会造成主要的损伤。依据Per Miner法则,如果损伤累加到1(100%),那么将发生失效。 3.2 不定振幅程序 a 建立引领分析(线性,比载荷) b 定义疲劳材料特性(包括S-N曲线)
ANSYSworkbench教程—疲劳分析
第一章简介 1.1 疲劳概述 结构失效的一个常见原因是疲劳,其造成破坏与重复加载有关。疲劳通常分为两类:高周疲劳是当载荷的循环(重复)次数高(如1e4 -1e9)的情况下产生的。因此,应力通常比材料的极限强度低,应力疲劳(Stress-based)用于高周疲劳;低周疲劳是在循环次数相对较低时发生的。塑性变形常常伴随低周疲劳,其阐明了短疲劳寿命。一般认为应变疲劳(strain-based)应该用于低周疲劳计算。 在设计仿真中,疲劳模块拓展程序(Fatigue Module add-on)采用的是基于应力疲劳(stress-based)理论,它适用于高周疲劳。接下来,我们将对基于应力疲劳理论的处理方法进行讨论。 1.2 恒定振幅载荷 在前面曾提到,疲劳是由于重复加载引起: 当最大和最小的应力水平恒定时,称为恒定振幅载荷,我们将针对这种最简单的形式,首先进行讨论。 否则,则称为变化振幅或非恒定振幅载荷。 1.3 成比例载荷 载荷可以是比例载荷,也可以非比例载荷: 比例载荷,是指主应力的比例是恒定的,并且主应力的削减不随时间变化,这实质意味着由于载荷的增加或反作用的造成的响应很容易得到计算。 相反,非比例载荷没有隐含各应力之间相互的关系,典型情况包括: σ1/σ2=constant 在两个不同载荷工况间的交替变化; 交变载荷叠加在静载荷上; 非线性边界条件。 1.4 应力定义 考虑在最大最小应力值σmin和σmax作用下的比例载荷、恒定振幅的情况: 应力范围Δσ定义为(σmax-σmin) 平均应力σm定义为(σmax+σmin)/2 应力幅或交变应力σa是Δσ/2 应力比R是σmin/σmax 当施加的是大小相等且方向相反的载荷时,发生的是对称循环载荷。这就是σm=0,R=-1的情况。 当施加载荷后又撤除该载荷,将发生脉动循环载荷。这就是σm=σmax/2,R=0的情况。 1.5 应力-寿命曲线 载荷与疲劳失效的关系,采用的是应力-寿命曲线或S-N曲线来表示: (1)若某一部件在承受循环载荷, 经过一定的循环次数后,该部件裂纹或破坏将会发展,而且有可能导致失效;(2)如果同个部件作用在更高的载荷下,导致失效的载荷循环次数将减少; (3)应力-寿命曲线或S-N曲线,展示出应力幅与失效循环次数的关系。 S-N曲线是通过对试件做疲劳测试得到的弯曲或轴向测试反映的是单轴的应力状态,影响S-N曲线的因素很多,其中的一些需要的注意,如下: 材料的延展性,材料的加工工艺,几何形状信息,包括表面光滑度、残余应力以及存在的应力集中,载荷环境,包括平均应力、温度和化学环境,例如,压缩平均应力比零平均应力的疲劳寿命长,相反,拉伸平均应力比零平均应力的疲劳寿命短,对压缩和拉伸平均应力,平均应力将分别提高和降低S-N曲线。 因此,记住以下几点:一个部件通常经受多轴应力状态。如果疲劳数据(S-N 曲线)是从反映单轴应力状态的测试中得到的,那么在计算寿命时就要注意:(1)设计仿真为用户提供了如何把结果和S-N曲线相关联的选择,包括多轴应力的选择;(2)双轴应力结果有助于计算在给定位置的情况。 平均应力影响疲劳寿命,并且变换在S-N曲线的上方位置与下方位置(反映出在给定应力幅下的寿命长短):(1)对于不同的平均应力或应力比值,设计仿真允许输入多重S-N曲线(实验数据);(2)如果没有太多的多重S-N曲线(实验数据),那么设计仿真也允许采用多种不同的平均应力修正理论。 早先曾提到影响疲劳寿命的其他因素,也可以在设计仿真中可以用一个修正因子来解释。 1.6 总结
细解Ansys疲劳寿命分析
细解Ansys疲劳寿命分析 2013-08-29 17:16 by:有限元来源:广州有道有限元 ANSYS Workbench 疲劳分析 本章将介绍疲劳模块拓展功能的使用: –使用者要先学习第4章线性静态结构分析. ?在这部分中将包括以下内容: –疲劳概述 –恒定振幅下的通用疲劳程序,比例载荷情况 –变振幅下的疲劳程序,比例载荷情况 –恒定振幅下的疲劳程序,非比例载荷情况 ?上述功能适用于ANSYS DesignSpacelicenses和附带疲劳模块的更高级的licenses. A. 疲劳概述 ?结构失效的一个常见原因是疲劳,其造成破坏与重复加载有关 ?疲劳通常分为两类: –高周疲劳是当载荷的循环(重复)次数高(如1e4 -1e9)的情况下产生的. 因此,应力通常比材料的极限强度低. 应力疲劳(Stress-based)用于高周疲劳. –低周疲劳是在循环次数相对较低时发生的。塑性变形常常伴随低周疲劳,其阐明了短疲劳寿命。一般认为应变疲劳(strain-based)应该用于低周疲劳计算. ?在设计仿真中, 疲劳模块拓展程序(Fatigue Module add-on)采用的是基于应力疲劳(stress-based)理论,它适用于高周疲劳. 接下来,我们将对基于应力疲劳理论的处理方法进行讨论. …恒定振幅载荷 ?在前面曾提到, 疲劳是由于重复加载引起: –当最大和最小的应力水平恒定时, 称为恒定振幅载荷. 我们将针对这种最简单的形式,首先进行讨论. –否则,则称为变化振幅或非恒定振幅载荷
…成比例载荷 ?载荷可以是比例载荷, 也可以非比例载荷:–比例载荷, 是指主应力的比例是恒定的,并且主应力的削减不随时间变化. 这实质意味着由于载荷的增加或反作用的造成的响应很容易得到计算.–相反, 非比例载荷没有隐含各应力之间相互的关系,典型情况包括:?在两个不同载荷工况间的交替变化?交变载荷叠加在静载荷上?非线性边界条件
ANSYS疲劳分析的应用
ANSYS疲劳分析的应用 在传统的设计过程中,设计人员在概念或详细设计阶段通常使用简单而不真实的计算来估计产品的寿命,而对这些估计寿命的验证通常是通过一定量物理样机的耐久试验得到。不但试验周期长、耗资大,而且许多参数与失效的定量关系也不能在试验中得出,试验结论还可能受许多偶然因素的影响。因此对于产品疲劳寿命的仿真分析方法越来越受到产品设计人员的关注。 在塑料机械中,模板是注塑机最重要的零件之一,它的成本是注塑机成本的主要组成部分,模板断裂,注塑机就不能正常工作。从强度出发,当然是选用高质量的材料,而且尽量将模板做得厚一些,但这两点均提高模板造价,影响整机成本。目前模板大部分采用球墨铸铁铸造。这主要考虑:(1) 在模板上铸出加强筋或将模板掏空,可有效减少质量;(2) 由于球铁较易于精铸(树脂砂铸造),使加工余量大大减少,可有效减少加工成本;(3) 球铁刚性较好,也具有一定强度。虽然设计者充分考虑了模板的强度、刚度,但仍然有许多模板断裂的事故发生,其原因在于模板断裂不是因为静力破坏而是因为疲劳破坏。 一、元原理及模型建立 当材料或结构受到多次重复变化的载荷作用后,在应力值虽然始终没有超过材料的强度极限,甚至比弹性极限还低的情况下就可能发生破坏。这种在交变载荷作用下材料或结构的破坏现象称为疲劳破坏[1 ] 。
结构的疲劳破坏,首先在局部区域产生裂缝,一般是在零件和构件的表面,也可能在零件内部有缺陷处,即应力最高的区域。由于该区域代表了整个结构的疲劳强度,所以该区域称为危险区,危险区的应力、应变变化情形为结构疲劳分析中所需的应力或应变2时间历程。因此,结构疲劳应力分析的目的,就是要求得结构在承受各种负荷时,对其危险区的应力或应变响应,作为结构疲劳设计的依据之一。 在进行工程结构疲劳分析时,常应用ANSYS 软件为分析工具来确定结构的高应力危险区,并进行负荷谱转化为应力谱或应变谱的工作。本工作将引用基本理论[2]: 其中,式中,[ B ] 为应变矩阵;[ D] 为弹性矩阵;{ f e} 及[ Ke ] 为单元节点力及单元刚度矩阵。建立一组以结点位移为未知量的代数方程组,解这些方程组就可以求出物体上有限个离散结点上的位移,从而得到所需的应力和应变。 利用三维通用软件UGNX310 建立供分析用的三维几何模型。根据零件的受力情况及要求,建模时作了一些简化:(1) 忽略模板上一些对整体受力影响不大的小孔;(2) 忽略模板上四台柱孔处的小凸台;(3) 忽略顶出联接台;(4) 忽略大部分较小的圆角并作了一定的简化。同时利用ANSYS 的前处理器进行网格划分,得图1 模型。
ansys workbench疲劳分析流程
ansys workbench疲劳分析流程 基于S-N曲线的疲劳分析的最终目的是将变化无规律的多轴应力转化为简单的单轴应力循环,以便查询S-N曲线,得到相应的疲劳寿命。ansys workbench的疲劳分析模块采用如下流程,其中r=Smin/Smax,Sa为应力幅度,Sm应力循环中的应力均值,注意后一个m不是大写:): (1)无规律多轴应力-->无规律单轴应力 这个转换其实就是采用何种应力(或分量)。只能有以下选择: V on-Mises等效应力;最大剪应力;最大主应力;或某一应力分量(Sx,Syz等等)。有时也采用带符号的Mises应力(大小不变等于Mises应力,符号取最大主应力的符号,好处是可以考虑拉或压的影响(反映在平均应力或r上))。同强度理论类似,V on-Mises等效应力和最大剪应力转换适用于延展性较好的材料,最大主应力转换用于脆性材料。 (2)无规律单轴应力-->简单单轴应力循环 其本质是从无规律的高高低低的等效单轴应力--时间曲线中提取出一系列的简单应力循环(用Sa,Sm表征)以及对应的次数。有很多种方法可以完成此计数和统计工作,其中又分为路径相关方法和路径无关方法。用途 最广的雨流法(rain flow counting method)就是一种路径相关方法。其算法和原理可见“Downing, S., Socie, D. (1982) Simplified rain flow counting algorithms. Int J Fatigue,4, 31–40“。 经过雨流法的处理后,无规律的应力--时间曲线转化为一系列的简单循环(Sa,Sm和ni,ni为该循环的次数,Sm如果不等于0,即r!=-1,需要考虑r的影响)。然后将r!=-1的循环再转化到r=-1对应的应力循环(见下),这样就可以根据损伤累计理论(Miner准则)计算分析了:Sum(ni/Ni) Ni为该应力循环对应的寿命(考虑Sa,Sm)。 (3)r!=-1的简单单轴应力循环-->r=-1的r!=-1的简单单轴应力循环 如果有不同r值下的S-N曲线,一般采用插值方法确定未知r值下的S-N曲线。如果只有r=-1的S-N曲线,可采用如下的公式计算等效的应力(就是将r!=-1的单轴应力转换为r=-1时的单轴应力,即等效应力): (Sa/Se)+(Sm/Su)^n=1 ^为指数运算符。 其中,Sa为半应力幅值,Se为欲求的等效应力,Sm为平均应力,Su和n不同的取值,构成不同的理论: Theory Su n ------------------------------------------------------------------ Soderberg yield stress (sy) 1 Goodman ultimate tensile stress (su) 1 Gerber ultimate tensile stress (su) 2 Morrow true fracture stress (sf) 1 ----------------------------------------------------------------- 至此,已经可以查询标准的S-N曲线了,结合Miner准则,可以计算疲劳寿命了。
ansys-workbench疲劳分析流程
ansys workbench困乏分析流程 基于S-N曲线的困乏分析的最终目的是将变化无规律的多轴应力转化为简单的单轴应力循环,以便查询S-N曲线,得到相应的困乏寿命。ansysworkbench 的困乏分析模块采用如下流程,其中r=Smin/Smax,Sa为应力幅度,Sm应力循环中的应力均值,注意后一个m不是大写:): (1)无规律多轴应力-->无规律单轴应力 这个转换其实就是采用何种应力(或分量)。只能有以下选择: Von-Mises等效应力;最大剪应力;最大主应力;或某一应力分量(Sx,Syz 等等)。有时也采用带符号的Mises应力(大小不变等于Mises应力,符号取最大主应力的符号,好处是可以考虑拉或压的影响(反映在平衡应力或r 上))。同强度理论类似,Von-Mises等效应力和最大剪应力转换适用于延展性较好的材料,最大主应力转换用于脆性材料。 (2)无规律单轴应力-->简单单轴应力循环 其本质是从无规律的高高低低的等效单轴应力--时间曲线中提取出一系列的简单应力循环(用Sa,Sm表征)以及对应的次数。有很多种方法可以完成此计数和统计工作,其中又分为路径相关方法和路径无关方法。用途 最广的雨流法(rainflowcountingmethod)就是一种路径相关方法。其算法和原理可见“Downing, S., Socie, D. (1982) Simplified rain flow counting algorithms. Int J Fatigue,4, 31–40“。 经过雨流法的处理后,无规律的应力--时间曲线转化为一系列的简单循环(Sa,Sm和ni,ni为该循环的次数,Sm如果不等于0,即r!=-1,需要考虑r的影响)。然后将r!=-1的循环再转化到r=-1对应的应力循环(见下),这样就可以根据损伤累计理论(Miner准则)计算分析了:Sum(ni/Ni) Ni为该应力循环对应的寿命(考虑Sa,Sm)。 (3)r!=-1的简单单轴应力循环-->r=-1的r!=-1的简单单轴应力循环
ANSYSWORKBENCH疲劳分析指南
ANSYSWORKBENCH疲劳分析指南 第一章简介 1.1 疲劳概述 结构失效的一个常见原因是疲劳,其造成破坏与重复加载有关。疲劳通常分为两类:高周疲劳是当载荷的循环(重复)次数高(如1e4 -1e9)的情况下产生的。因此,应力通常比材料的极限强度低,应力疲劳(Stress-based)用于高周疲劳;低周疲劳是在循环次数相对较低时发生的。塑性变形常常伴随低周疲劳,其阐明了短疲劳寿命。一般认为应变疲劳(strain-based)应该用于低周疲劳计算。在设计仿真中,疲劳模块拓展程序(Fatigue Module add-on)采用的是基于应力疲劳(stress-based)理论,它适用于高周疲劳。接下来,我们将对基于应力疲劳理论的处理方法进行讨论。 1.2 恒定振幅载荷 在前面曾提到,疲劳是由于重复加载引起: 当最大和最小的应力水平恒定时,称为恒定振幅载荷,我们将针对这种最简单的形式,首先进行讨论。 否则,则称为变化振幅或非恒定振幅载荷。 1.3 成比例载荷 载荷可以是比例载荷,也可以非比例载荷: 比例载荷,是指主应力的比例是恒定的,并且主应力的削减不随时间变化,这实质意味着由于载荷的增加或反作用的造成的响应很容易得到计算。 相反,非比例载荷没有隐含各应力之间相互的关系,典型情况包括: σ1/σ2=constant 在两个不同载荷工况间的交替变化; 交变载荷叠加在静载荷上; 非线性边界条件。
1.4 应力定义 考虑在最大最小应力值σ和σ作用下的比例载荷、恒定振幅的情况:应力范围Δσ定义为(σ-σ) 平均应力σ定义为(σ+σ)/2 应力幅或交变应力σa是Δσ/2 应力比R是σ/σ 当施加的是大小相等且方向相反的载荷时,发生的是对称循环载荷。这就是 σm=0,R=-1的情况。 当施加载荷后又撤除该载荷,将发生脉动循环载荷。这就是σ=σ/2,R=0的情况。 1.5 应力-寿命曲线 载荷与疲劳失效的关系,采用的是应力-寿命曲线或S-N曲线来表示: (1)若某一部件在承受循环载荷, 经过一定的循环次数后,该部件裂纹或破坏将会发展,而且有可能导致失效; (2)如果同个部件作用在更高的载荷下,导致失效的载荷循环次数将减少; (3)应力-寿命曲线或S-N曲线,展示出应力幅与失效循环次数的关系。 S-N曲线是通过对试件做疲劳测试得到的弯曲或轴向测试反映的是单轴的应力状态,影响S-N曲线的因素很多,其中的一些需要的注意,如下:材料的延展性,材料的加工工艺,几何形状信息,包括表面光滑度、残余应力以及存在的应力集中,载荷环境,包括平均应力、温度和化学环境,例如,压缩平均应力比零平均应力的疲劳寿命长,相反,拉伸平均应力比零平均应力的疲劳寿命短,对压缩和拉伸平均应力,平均应力将分别提高和降低S-N曲线。 因此,记住以下几点:一个部件通常经受多轴应力状态。如果疲劳数据(S-N 曲线)是从反映单轴应力状态的测试中得到的,那么在计算寿命时就要注意:(1)设计仿真为用户提供了如何把结果和S-N曲线相关联的选择,包括多轴应力的选择;(2)双轴应力结果有助于计算在给定位置的情况。
细解Ansys疲劳寿命分析
细解Ansys疲劳寿命分析 ANSYS Workbench 疲劳分析 本章将介绍疲劳模块拓展功能的使用: –使用者要先学习第4章线性静态结构分析. ?在这部分中将包括以下内容: –疲劳概述 –恒定振幅下的通用疲劳程序,比例载荷情况 –变振幅下的疲劳程序,比例载荷情况 –恒定振幅下的疲劳程序,非比例载荷情况 ?上述功能适用于ANSYS DesignSpacelicenses和附带疲劳模块的更高级的licenses. A. 疲劳概述 ?结构失效的一个常见原因是疲劳,其造成破坏与重复加载有关 ?疲劳通常分为两类: –高周疲劳是当载荷的循环(重复)次数高(如1e4 -1e9)的情况下产生的. 因此,应力通常比材料的极限强度低. 应力疲劳(Stress-based)用于高周疲劳. –低周疲劳是在循环次数相对较低时发生的。塑性变形常常伴随低周疲劳,其阐明了短疲劳寿命。一般认为应变疲劳(strain-based)应该用于低周疲劳计算. ?在设计仿真中, 疲劳模块拓展程序(Fatigue Module add-on)采用的是基于应力疲劳(stress-based)理论,它适用于高周疲劳. 接下来,我们将对基于应力疲劳理论的处理方法进行讨论. …恒定振幅载荷 ?在前面曾提到, 疲劳是由于重复加载引起: –当最大和最小的应力水平恒定时, 称为恒定振幅载荷. 我们将针对这种最简单的形式,首先进行讨论. –否则,则称为变化振幅或非恒定振幅载荷
…成比例载荷 ?载荷可以是比例载荷, 也可以非比例载荷:–比例载荷, 是指主应力的比例是恒定的,并且主应力的削减不随时间变化. 这实质意味着由于载荷的增加或反作用的造成的响应很容易得到计算.–相反, 非比例载荷没有隐含各应力之间相互的关系,典型情况包括:?在两个不同载荷工况间的交替变化?交变载荷叠加在静载荷上?非线性边界条件
疲劳分析软件 ANSYS FE_SAFE 简介(转)
问题1:ANSYS后处理疲劳功能与ANSYS/Fe-safe疲劳功能的关系是什么? 回答1:ANSYS后处理疲劳功能是依据线性累积损伤理论,利用S-N曲线、应力时间历程以及雨流计数技术直接计算疲劳寿命使用系数,属于简单的名义应力疲劳寿命评估,对疲劳的影响因素的考虑有限,适用于粗略估算。ANSYS/Fe-safe则是专用的高级疲劳分析模块,采用先进的单/双轴疲劳计算方法,允许计算弹性或弹塑性载荷历程,综合多种影响因素(如平均应力、应力集中、缺口敏感性、(焊接成型等)初始应力、表面光洁度、表面加工性质等),按照累积损伤理论和雨流计数,根据各种应力或应变进行疲劳寿命和耐久性分析设计,或者根据疲劳材料以及载荷的概率统计规律进行概率疲劳设计以及疲劳可靠性设计,或者按照断裂力学损伤容限法计算裂纹扩展寿命。Fe-safe疲劳计算技术先进,精度很高,广泛实用于各类金属、非金属以及合金等材料。总之,ANSYS后处理疲劳功能仅仅是Fe-safe疲劳功能的一个很少部分,Fe-safe作为复杂环境下的疲劳耐久性计算是ANSYS疲劳的补充与延伸。 问题2:什么是高周疲劳和低周疲劳?它们与应力疲劳法和应变疲劳法之间的关系是什么? 回答2:根据疲劳断裂时交变载荷作用的总周次,疲劳可分为低周疲劳、中周疲劳和高周疲劳。一般将断裂时的总周次在以下时,称为低周疲劳;断裂时的总周次大于时,称为高周疲劳。在高周疲劳中,构件在破坏之前一般仅发生极小的弹性变形,而在低周疲劳中,应力往往大到足以使每个循环产生可观的宏观的塑性变形。因此,低周疲劳较高周疲劳而言显示出了延性状态。高周疲劳传统上用应力范围来描述疲劳破坏所需的时间或循环数,即按应力疲劳法评估疲劳寿命。低周疲劳(短寿命)传统上用应变范围来描述全塑性区域疲劳破坏所需的时间或循环数,即按(局部)应变疲劳法评估疲劳寿命。 ANSYS FE-SAFE是一款高级疲劳耐久性分析和信号处理的软件,它是多轴疲劳分析解决方案的领导者,算法先进,功能全面细致,是世界公认精度最高的疲劳分析软件。 ANSYS FE-SAFE既支持基于疲劳试验测试应力和应变信号的疲劳分析技术,也支持基于有限元分析计算的疲劳仿真设计技术。 ANSYS FE-SAFE具有完整的材料库、灵活多变的载荷谱定义方法、实用的疲劳信号采集与分析处理功能以及丰富先进的疲劳算法,完整的输出疲劳结果。 疲劳分析软件ANSYS FE_SAFE 简介(转) 来源:刘兴兴的日志
【ANSYS精品资源】利用ANSYS随机振动分析功能实现随机疲劳分析
利用ANSYS随机振动分析功能实现随机疲劳分析 ANSYS随机振动分析功能可以获得结构随机振动响应过程的各种统计参数(如:均值、均方根和平均频率等),根据各种随机疲劳寿命预测理论就可以成功地预测结构 的随机疲劳寿命。本文介绍了ANSYS随机振动分析功能,以及利用该功能,按照Steinberg提出的基于高斯分布和Miner线性累计损伤定律的三区间法进行ANSYS 随机疲劳计算的具体过程。 1.随机疲劳现象普遍存在 在工程应用中,汽车、飞行器、船舶以及其它各种机械或零部件,大多是在随机载 荷作用下工作,当它们承受的应力水平较高,工作达到一定时间后,经常会突然发生 随机疲劳破坏,往往造成灾难性的后果。因此,预测结构或零部件的随机疲劳寿命是 非常有必要的。 2.ANSYS随机振动分析功能介绍 ANSYS随机振动分析功能十分强大,主要表现在以下方面: 1.具有位移、速度、加速度、力和压力等PSD类型; 2.能够考虑a阻尼、 阻尼、恒定阻尼比和频率相关阻尼比; 3.能够定义基础和节点PSD激励; 4.能够考虑多个PSD激励之间的相关程度:共谱值、二次谱值、空间关系和波 1
传播关系等; 5.能够得到位移、应力、应变和力的三种结果数据:1σ位移解,1σ速度解和 1σ加速度解; 3.利用ANSYS随机振动分析功能进行疲劳分析的一般原理 在工程界,疲劳计算广泛采用名义应力法,即以S-N曲线为依据进行寿命估算的方法,可以直接得到总寿命。下面围绕该方法举例说明ANSYS随机疲劳分析的一般原理。 当应力历程是随机过程时,疲劳计算相对比较复杂。但已经有许多种分析方法,这 里仅介绍一种比较简单的方法,即Steinberg提出的基于高斯分布和Miner线性累计 损伤定律的三区间法(应力区间如图1所示): 应力区间发生的时间 -1σ ~+1σ68.3%的时间 -2σ ~+2σ27.1%的时间 -3σ ~+3σ 4.33%的时间 99.73% 大于3σ的应力仅仅发生在0.27%的时间内,假定其不造成任何损伤。在利用Miner 定律进行疲劳计算时,将应力处理成上述3个水平,总体损伤的计算公式就可以写成: 其中: 2
ANSYSWORKBENCH疲劳分析指南
ANSYS WORKBENCH 疲劳分析指南 第一章简介 1.1 疲劳概述 结构失效的一个常见原因是疲劳,其造成破坏与重复加载有关。疲劳通常分为两类:高周疲劳是当载荷的循环(重复)次数高(如1e4 -1e9)的情况下产生的。因此,应力通常比材料的极限强度低,应力疲劳(Stress-based)用于高周疲劳;低周疲劳是在循环次数相对较低时发生的。塑性变形常常伴随低周疲劳,其阐明了短疲劳寿命。一般认为应变疲劳(strain-based)应该用于低周疲劳计算。 在设计仿真中,疲劳模块拓展程序(Fatigue Module add-on)采用的是基于应力疲劳(stress-based)理论,它适用于高周疲劳。接下来,我们将对基于应力疲 劳理论的处理方法进行讨论。 1.2 恒定振幅载荷 在前面曾提到,疲劳是由于重复加载引起: 当最大和最小的应力水平恒定时,称为恒定振幅载荷,我们将针对这种最简 单的形式,首先进行讨论。 否则,则称为变化振幅或非恒定振幅载荷。 1.3 成比例载荷 载荷可以是比例载荷,也可以非比例载荷: 比例载荷,是指主应力的比例是恒定的,并且主应力的削减不随时间变化, 这实质意味着由于载荷的增加或反作用的造成的响应很容易得到计算。 相反,非比例载荷没有隐含各应力之间相互的关系,典型情况包括: σ1/σ2=constant 在两个不同载荷工况间的交替变化; 交变载荷叠加在静载荷上; 非线性边界条件。 1.4 应力定义 考虑在最大最小应力值σmin和σmax作用下的比例载荷、恒定振幅的情况: 应力范围Δσ定义为(σmax-σmin) 平均应力σm定义为(σmax+σmin)/2 应力幅或交变应力σa是Δσ/2 应力比R是σmin/σmax 当施加的是大小相等且方向相反的载荷时,发生的是对称循环载荷。这就是 σm=0,R=-1的情况。 当施加载荷后又撤除该载荷,将发生脉动循环载荷。这就是σm=σmax/2,R=0的情况。 1.5 应力-寿命曲线 载荷与疲劳失效的关系,采用的是应力-寿命曲线或S-N曲线来表示: (1)若某一部件在承受循环载荷, 经过一定的循环次数后,该部件裂纹或破坏将会发展,而且有可能导致失效; (2)如果同个部件作用在更高的载荷下,导致失效的载荷循环次数将减少; (3)应力-寿命曲线或S-N曲线,展示出应力幅与失效循环次数的关系。
ansysworkbench疲劳分析实例.
AHSYS 作业A12 疲劳 作业M2-目标 Sha^cFMer AN、、、? H ■: d■気ro tanavM?律》枫fi人??.aewwwRt *4) 口?■fMTEMir ?|? ?£ FulN *屮?少 4W0WW-
sASNV mmuMJiAua t 胡尺?乙2彳卜 曲…sASNV iMlOUViin.imWV ? 毘m却… ^pwu**vs sASNV I吹OIU¥Q5T2H 冷.?■ ? sASNV ■?*>? I?in?ws. Mfbrn W■哥MHV■? J? D ?d tiw^im-iuun i ?(? W ^VUI> WMM||^fK?diJW ? 砂-"仇#
Shape …沁Ad过程 9. ?命*朋广■rvmawwn, 10. 止心疫”臭金K*一 1化怪人一牛■址!l雯鼻 mRi . tpw?1 - ? J.DMMBOt CvMrieal Support *11! 12. rtW RadW Eed .?U??rwl rangemiBlz Fr' ANSYS ??e Sh^fx hnfef 作求解杖IF ANSY、 w? 、. Rxh4iT 皂 1Z RMB * tn*cn > Stress ? Equivalent (wn M M IB RMB > biMd > OUcHiMtion > Totol. IL ?? Sha^FMer …?作业A12-过粹 入r??m. Sha^FMer 作业M2-求解设需 ? MAWIguoioei (?. 倉出?oluMon 苣 ANSYS ?.2
AIMSYS ZMCT ANSY< A i2—求样设栄 ?从Dewhof gRgr ■“: 21.尼乂M■良也山3*54『巧尹》318) 便""o■停■补尤一*样??? Sha^FMer 作业M2-求解设胃 ?? Fell0wTo(iaMI; 0■八?3吋Fictor (*±se>: RMS ?kiMcl > Fatigue ? 3My Ftclof ? azamof “MtryF■:tor ■口:?-仗?缸论呼佢 皿9“ UK .卯 * 环次■ 34 4 IV OR Mhoe W7)U?R1 ■为M仇ft I itW. Shape FMcr 作WA12-求駢设国 ANSYS ??r> ? iQWZYgeWf集); 27.}tA*Fm*gue Sensitivity ^?* Sh^pcFMr AN、Y, 作业A12 -求解设SF ? AFMI9M TocMMl): ? ?A mtSe^ttpo- mtB ? kwel ? FMgue ■ Baiwiv NGtoon ? MDeiwtoofl FmweSmsitivny Su; 28WR-亍钛两賢4
ANSYS疲劳分析
ANSYS疲劳分析 疲劳是指结构在低于静态极限强度载荷的重复载荷作用下,出现断裂破坏的现象。例如一根能够承受300 KN 拉力作用的钢杆,在200 KN 循环载荷作用下,经历1,000,000 次循环后亦会破坏。导致疲劳破坏的主要因素如下: 载荷的循环次数; 每一个循环的应力幅; 每一个循环的平均应力; 存在局部应力集中现象。 真正的疲劳计算要考虑所有这些因素,因为在预测其生命周期时,它计算“消耗”的某个部件是如何形成的。 1.ANSYS程序处理疲劳问题的过程 ANSYS 疲劳计算以ASME锅炉和压力容器规范(ASME Boiler and Pressure Vessel Code)作为计算的依据,采用简化了的弹塑性假设和Mimer累积疲劳准则。除了根据ASME 规范所建立的规则进行疲劳计算外,用户也可编写自己的宏指令,或选用合适的第三方程序,利用ANSYS 计算的结果进行疲劳计算。《ANSYS APDL Programmer’s Guide》讨论了上述二种功能。ANSYS程序的疲劳计算能力如下: (1)对现有的应力结果进行后处理,以确定体单元或壳单元模型的疲劳寿命耗用 系数(fatigue usage factors)(用于疲劳计算的线单元模型的应力必须人工输 入); (2)可以在一系列预先选定的位置上,确定一定数目的事件及组成这些事件的载 荷,然后把这些位置上的应力储存起来; (3)可以在每一个位置上定义应力集中系数和给每一个事件定义比例系数。 2.基本术语 位置(Location):在模型上储存疲劳应力的节点。这些节点是结构上某些容易产生疲劳破坏的位置。 事件(Event):是在特定的应力循环过程中,在不同时刻的一系列应力状态。 载荷(Loading):是事件的一部分,是其中一个应力状态。 应力幅:两个载荷之间应力状态之差的度量。程序不考虑应力平均值对结果的影
ANSYS疲劳分析的应用
ANSYS疲劳分析的应用在传统的设计过程中,设计人员在概念或详细设计阶段通常使用简单而不 真实的计算来估计产品的寿命,而对这些估计寿命的验证通常是 通过一定量物理样机的耐久试验得到。不但试验周期长、耗资 大,而且许多参数与失效的定量关系也不能在试验中得出,试验结 论还可能受许多偶然因素的影响。因此对于产品疲劳寿命的仿真分 析方法越来越受到产品设计人员的关注。 在塑料机械中,模板是注塑机最重要的零件之一,它的成本是注塑机成本的主要组成部分,模板断裂,注塑机就不能正常工作。从强度出发,当然是选用高质量的材料,而且尽量将模板做得厚一些,但这两点均提高模板造价,影响整机成本。目前模板大部分采用球墨铸铁铸造。这主要考虑:(1) 在模板上铸出加强筋或将模板掏空,可有效减少质量;(2) 由于球铁较易于精铸(树脂砂铸造) ,使加工余量大大减少,可有效减少加工成本;(3) 球铁刚性较好,也具有一定强度。虽然设计者充分考虑了模板的强度、刚度,但仍然有许多模板断裂的事故发生,其原因在于模板断裂不是因为静力破坏而是因为疲劳破坏。 一、元原理及模型建立 当材料或结构受到多次重复变化的载荷作用后,在应力 值虽然始终没有超过材料的强度极限,甚至比弹性极限还低的情况下就可能发生破坏。这种在交变载荷作用下材料或结构的破坏现象称为疲劳破坏[1 ] 。 结构的疲劳破坏,首先在局部区域产生裂缝,一般是在零件
和构件的表面,也可能在零件内部有缺陷处,即应力最高的区域。由于该区域代表了整个结构的疲劳强度,所以该区域称为危险区,危险区的应力、应变变化情形为结构疲劳分析中所需的应力或应变2 时间历程。因此,结构疲劳应力分析的目的,就是要求得结构在承受各种负荷时,对其危险区的应力或应变响应,作为结构疲劳设计的依据之一。 在进行工程结构疲劳分析时,常应用ANSYS软件为分析 工具来确定结构的高应力危险区,并进行负荷谱转化为应力谱或应变谱的工作。本工作将引用基本理论[2] : 其中,式中,[ B ] 为应变矩阵;[ D] 为弹性矩阵;{ f e} 及[ Ke ] 为单元节点力及单元刚度矩阵。建立一组以结点位移为未知量的代数方程组,解这些方程组就可以求出物体上有限个离散结点上的位移,从而得到所需的应力和应变。 利用三维通用软件UGNX310建立供分析用的三维几何 模型。根据零件的受力情况及要求,建模时作了一些简化: (1) 忽略模板上一些对整体受力影响不大的小孔;(2) 忽略模板上四台柱孔处的小凸台;(3) 忽略顶出联接台;(4) 忽略大部分较小的圆角并作了一定的简化。同时利用ANSYS的前处理器进行网格划分,得图1 模型。
ANSYS WORKBENCH 疲劳分析指南
A NSYS WORKBENCH 疲劳分析指南 第一章 简介 1.1 疲劳概述 结构失效的一个常见原因是疲劳,其造成破坏与重复加载有关。疲劳通常分为两类:高周疲劳是当载荷的循环(重复)次数高(如1e 4 -1e9)的情况下产生的。因此,应力通常比材料的极限强度低,应力疲劳(Stress-based )用于高周疲劳;低周疲劳是在循环次数相对较低时发生的。塑性变形常常伴随低周疲劳,其阐明了短疲劳寿命。一般认为应变疲劳(stra in-based)应该用于低周疲劳计算。 在设计仿真中,疲劳模块拓展程序(Fati gu e Modu le ad d-o n)采用的是基于应力疲劳(s tre ss-ba sed)理论,它适用于高周疲劳。接下来,我们将对基于应力疲劳理论的处理方法进行讨论。 1.2 恒定振幅载荷? 在前面曾提到,疲劳是由于重复加载引起:? 当最大和最小的应力水平恒定时,称为恒定振幅载荷,我们将针对这种最简单的形式,首先进行讨论。 否则,则称为变化振幅或非恒定振幅载荷。 1.3 成比例载荷? 载荷可以是比例载荷,也可以非比例载荷: 比例载荷,是指主应力的比例是恒定的,并且主应力的削减不随时间变化,这实质意味着由于载荷的增加或反作用的造成的响应很容易得到计算。 相反,非比例载荷没有隐含各应力之间相互的关系,典型情况包括:? σ1/σ2=c onst ant ? 在两个不同载荷工况间的交替变化;? 交变载荷叠加在静载荷上;? 非线性边界条件。 1.4 应力定义 考虑在最大最小应力值σmi n和σmax 作用下的比例载荷、恒定振幅的情况: 应力范围Δσ定义为(σm ax -σmin )? 平均应力σm 定义为(σm ax+σm in )/2 应力幅或交变应力σa 是Δσ/2 应力比R 是σmin /σm a x 当施加的是大小相等且方向相反的载荷时,发生的是对称循环载荷。这就是σm=0,R=-1的情况。? 当施加载荷后又撤除该载荷,将发生脉动循环载荷。这 就是σm =σmax /2,R=0的情况。 1.5 应力-寿命曲线 载荷与疲劳失效的关系,采用的是应力-寿命曲线或S-N 曲线来表示: (1)若某一部件在承受循环载荷, 经过一定的循环次数后,该部件裂纹或破坏将会发展,而且有可能导致失效;? (2)如果同个部件作用在更高的载荷下,导致失效的载荷循环次数将减少;? (3)应力-寿命曲线或S-N 曲线,展示出应力幅与失效循环次数的关系。 S-N曲线是通过对试件做疲劳测试得到的弯曲或轴向测试反映的是单轴的应力状态,影响S-N 曲线的因素很多,其中的一些需要的注意,如下: 材料的延展性,材料的加工工艺,几何形状信息,包括表面光滑度、残余应力以及存在的应力集中,载荷环境,包括平均应力、温度和化学环境,例如,压缩平均应力比零平均应力的疲劳寿命长,相反,拉伸平均应力比零平均应力的疲劳寿命短,对压缩和拉伸平均应力,平均应力将分别提高和降低S -N 曲线。