潍柴所有机型各个间隙调整方法
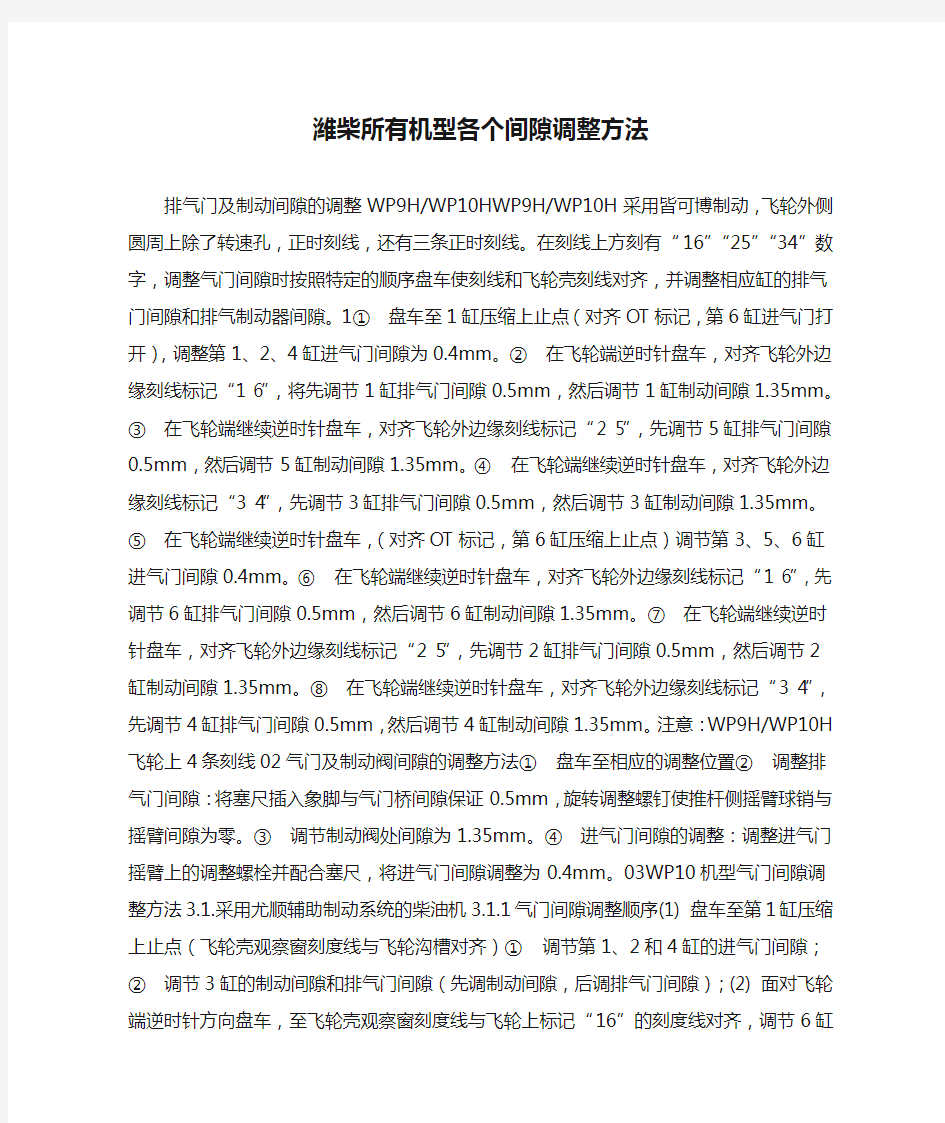

潍柴所有机型各个间隙调整方法
排气门及制动间隙的调整WP9H/WP10HWP9H/WP10H 采用皆可博制动,飞轮外侧圆周上除了转速孔,正时刻线,还有三条正时刻线。在刻线上方刻有“16”“25”“34”数字,调整气门间隙时按照特定的顺序盘车使刻线和飞轮壳刻线
对齐,并调整相应缸的排气门间隙和排气制动器间隙。1①盘车至1缸压缩上止点(对齐OT标记,第6缸进气门打开),调整第1、2、4缸进气门间隙为0.4mm。②在飞轮端逆时针盘车,对齐飞轮外边缘刻线标记“1 6”,将先调节1缸排气门间隙0.5mm,然后调节1缸制动间隙1.35mm。③在飞轮端继续逆时针盘车,对齐飞轮外边缘刻线标记“2 5”,先调节5缸排气门间隙0.5mm,然后调节5缸制动间隙
1.35mm。④在飞轮端继续逆时针盘车,对齐飞轮外边缘刻线标记“3 4”,先调节3缸排气门间隙0.5mm,然后调节3缸制动间隙1.35mm。⑤在飞轮端继续逆时针盘车,(对齐OT标记,第6缸压缩上止点)调节第3、5、6缸进气门间隙0.4mm。⑥在飞轮端继续逆时针盘车,对齐飞轮外边缘刻线标记“1 6”,先调节6缸排气门间隙0.5mm,然后调节6缸制动间隙1.35mm。⑦在飞轮端继续逆时针盘车,对齐飞轮外边缘刻线标记“2 5”,先调节2缸排气门间隙0.5mm,然后调节2缸制动间隙1.35mm。⑧在飞轮端继续逆时针
盘车,对齐飞轮外边缘刻线标记“3 4”,先调节4缸排气门间隙0.5mm,然后调节4缸制动间隙1.35mm。注意:
WP9H/WP10H飞轮上4条刻线02气门及制动阀间隙的调整方法①盘车至相应的调整位置②调整排气门间隙:将塞尺插入象脚与气门桥间隙保证0.5mm,旋转调整螺钉使推杆侧摇臂球销与摇臂间隙为零。③调节制动阀处间隙为
1.35mm。④进气门间隙的调整:调整进气门摇臂上的调整螺栓并配合塞尺,将进气门间隙调整为0.4mm。03WP10机型气门间隙调整方法3.1.采用尤顺辅助制动系统的柴油机3.1.1气门间隙调整顺序(1) 盘车至第1缸压缩上止点(飞轮壳观察窗刻度线与飞轮沟槽对齐)①调节第1、2和4缸的进气门间隙;②调节3缸的制动间隙和排气门间隙(先调制动间隙,后调排气门间隙);(2) 面对飞轮端逆时针方向盘车,至飞轮壳观察窗刻度线与飞轮上标记“16”的刻度线对齐,调节6缸的制动间隙和排气门间隙(先调制动间隙,后调排气门间隙)。(3) 面对飞轮端逆时针方向盘车,至飞轮壳观察窗刻度线与飞轮上标记“25”的刻度线对齐,调节2缸的制动间隙和排气门间隙(先调制动间隙,后调排气门间隙);(4) 面对飞轮端逆时针方向盘车,至飞轮壳观察窗刻度线与飞轮上标记“34”的刻度线对齐,①调节第3、5和6缸的进气门间隙;②调节4缸的制动间隙和排气门间隙(先调制动间隙,后调排气门间隙);(5) 面对飞轮端逆时针方向
盘车,至飞轮壳观察窗刻度线与飞轮上标记“16”的刻度线对齐,调节1缸的制动间隙和排气门间隙(先调制动间隙,后调排气门间隙);(6) 面对飞轮端逆时针方向盘车,至飞轮壳观察窗刻度线与飞轮上标记“25”的刻度线对齐,调节5缸的制动间隙和排气门间隙(先调制动间隙,后调排气门间隙);3.1.2排气门间隙及制动间隙调整方法:(1)盘车至相应的调整位置(2)制动间隙调整:将塞尺插入排气门桥与排气摇臂小活塞之间,调节推杆侧调节螺栓,保持制动间隙为2.05mm;(3)排气门间隙调整:将塞尺插入排气门桥与垫块之间,调整排气门间隙为3.00mm。3.2采用皆可博辅助制动系统柴油机3.2.1气门间隙调整顺序(1) 盘车到一缸压缩上止点,调节1、2、4缸进气门间隙;(2) 在飞轮端逆时针盘车至飞轮上“25”刻线与飞轮壳OT刻线对齐,调节摇臂5制动间隙和排气门间隙(先调制动间隙,后调排气门间隙);
(3) 在飞轮端逆时针盘车至飞轮上“34”刻线与飞轮壳OT
刻线对齐,调节摇臂3制动间隙和排气门间隙(先调制动间隙,后调排气门间隙);(4) 在飞轮端逆时针盘车至飞轮上“16”刻线与飞轮壳OT刻线对齐,调节摇臂6制动间隙和排气门间隙(先调制动间隙,后调排气门间隙);(5) 在飞轮端逆时针盘车至飞轮上凹槽与飞轮壳OT刻线对齐,调节第3、5和6缸的进气门间隙(先调制动间隙,后调排气门间隙);
(6) 在飞轮端逆时针盘车至飞轮上“25”刻线与飞轮壳OT
刻线对齐,调节摇臂2的制动间隙和排气门间隙(先调制动间隙,后调排气门间隙);(7) 在飞轮端逆时针盘车至飞轮上“34”刻线与飞轮壳OT刻线对齐,调节摇臂4的制动间隙和排气门间隙(先调制动间隙,后调排气门间隙);(8) 在飞轮端逆时针盘车至飞轮上“16”刻线与飞轮壳OT刻线对齐,调节摇臂1的制动间隙和排气门间隙(先调制动间隙,后调排气门间隙);3.2.2排气门间隙及制动间隙调整方法(1)盘车至相应的调整位置(2)排气门间隙调整:将塞尺插入排气门桥与排气摇臂的垫块之间,调节推杆侧调整螺栓,保持气门桥间隙为4.06mm;(3)EVB间隙调整:将塞尺插入排气门桥与支架之间,调整制动间隙为0.4mm。WP12/13机型气门间隙调整方法:1. 检查、调整进排气门间隙a. 普通机型气门间隙调整①柴油机冷车状态下,正盘车(按柴油机运转方向)到1、6缸上止点,此时飞轮上的刻槽与观察孔盖板上的指针对齐。②拆下缸盖上的气门摇臂罩,判断1缸或是6缸处压缩冲程(处于压缩冲程的气缸进排气门与摇臂间都有间隙)③按表10用塞尺检查气门桥上平面与气门摇臂间的间隙,若间隙过大或过小,可通过调整摇臂上的调整螺栓来达到上述间隙要求。④检查完1缸或6缸后,再正盘车360°,使6缸或1缸处于工作冲程,检查调整剩余的气门。①活塞位于压缩上止点位置。②松开螺母1调整螺栓1,直到与气门桥的接触间隙为0③松开螺母2
调整调整螺栓2,在调整螺栓2与气门桥之间插入0.6mm,转动调整螺栓直到塞尺无间隙,保持次状态,锁紧螺母④
调整螺栓1,在气门桥与调整螺栓1之间插入0.4mm塞尺,调整螺栓1,至小活塞到底夹住塞尺为止,保持此状态,锁紧螺母c. 采用尤顺辅助制动系统机型①盘车至第1缸压缩上止点(飞轮壳观察窗刻度线与飞轮沟槽对齐)调整第1、2和4缸的进气门间隙,进气门间隙0.4mm;调节3缸的制动间隙和排气门间隙(先调制动间隙,后调排气门间隙);②面对飞轮端逆时针方向盘车,至飞轮壳观察刻度线与飞轮上标记“16”的刻度线对齐,调整6缸的制动间隙和排气门间隙(先调制动间隙,后调排气门间隙)③面对飞轮端逆时针方向盘车,至飞轮壳观察窗刻度线与飞轮上标记“25”的刻度线对齐,调节2缸的制动间隙和排气门间隙(先调制动间隙,后调排气门间隙);④面对飞轮端逆时针方向盘车,至飞轮壳观察窗刻度线与飞轮上标记“34”的刻度线对齐。调节第3、5和6缸的进气门间隙,进气门间隙0.4mm;调节4缸的制动间隙和排气门间隙(先调制动间隙,后调排气门间隙);⑤面对飞轮端逆时针方向盘车,至飞轮壳观察窗刻度线与飞轮上标记“16”的刻度线对齐,调节1缸的制动间隙和排气门间隙(先调制动间隙,后调排气门间隙);
⑥面对飞轮端逆时针方向盘车,至飞轮壳观察窗刻度线与飞轮上标记“25”的刻度线对齐,调节5缸的制动间隙和排
气门间隙(先调制动间隙,后调排气门间隙);①排气门间隙及制动间隙调整方法:盘车至相应的调整位置制动间隙调整:将塞尺插入排气门桥与排气摇臂小活之间,调节推杆侧调整螺栓,保持制动间隙为2.05mm;排气门间隙调整:将塞尺插入排气门桥与垫块之间,调整排气门间隙为
3.00mm。排气推杆侧调整螺母(M10)拧紧力矩:(30~36)N·m排气门间隙调整螺母(M8)拧紧力矩:(18~23)N·m。进气门调整螺母拧紧力矩为(45±5)N·m进气门冷态间隙、制动间隙、排气门冷态间隙调整完后,应检查一缸进气开和排气关,并在记录卡上做好记录。
发那科OI-M系统排刀方法
发那科OI-MD系统机械手排刀、不能换刀故障排除方法 一、梯图版本号为:SH4B-B2。 二、Z轴不在第二参考点的时候,在MDI下输入一个换刀指令,例如:T1 M6;按程式启动键后,Z轴不动,没有回第二参考点的动作。马上出现#1002 Z AXIS NOT 2 POSITIONO(Z轴不在换刀点)报警。 但是单独输入一个G91 G30 Z0的回第二参考点程式,Z轴又能够回到第二参考点,在第二参考点再输入一个换刀指令,例如:T1 M6;按程式启动键后,刀臂有时候不动,有时候又会执行换刀动作,但到把刀送到主轴以后就又不动了,刀臂卡在那里。但这个时候刀杯又开始回刀动作了,刀杯卡到刀臂上,幸好这个时候没有刀头,没有造成大的损失,(只是刀杯损坏了一点)。然后刀盘开始不停的正转一会、反转一会,找不到刀号,按任何键都停不下来,只有按下急停按钮。另外一种现象就是如果输入的刀号不是倒下来的刀杯号的话,例如:倒下来的是#1刀,如果要换#3刀的话,输入T3 M6,按程式启动键后刀臂不会动,刀盘在那里不停的正转、反转,找不到相应的刀号,重复上面的第一种情况。 经检查与刀库有关的输入、输出点位一切正常。 X5.2--------刀库定位与记数; X5.3--------刀杯向下到位检测; X5.1--------刀杯向上到位检测; X11.4-------紧刀到位检测; X11.5-------松刀到位检测; Y5.2---------刀杯向上; Y7.2---------刀杯向下; Y4.6---------刀臂正转; Y5.0---------刀臂反转; Y0.5---------刀盘正转; Y1.5---------刀盘反转; Y7.0---------主轴松刀。 刀臂动作时序表;
气门间隙的调整
气门间隙的调整 教学目标:掌握调整气门间隙的步骤和技术要求; 熟练掌握调整气门间隙的操作技能。 教学重点:一、四缸活塞压缩上止点的确定; 逐缸和两次检查调整气门间隙的方法。 教学难点:两次检查调整气门间隙的原理和方法。 教具:1、教具:总装好的四缸四冲程发动机总成。 2、工、量具:一字螺丝刀、梅花扳手一套,擦拭布 教学过程: 【课前复习】1、如何确定发动机的前后? 2、找出该发动机的第一缸、第三缸。 3、四缸四冲程式发动机,其点为顺序是1—3—4—4,如果一缸 处在压缩压缩行程,其它三个缸各处在什么行程? 【新课】 一、气门间隙存在的意义 发动机起动后温度升高,气门及传动件受热膨胀伸长,如果在装配时(常温下)没有留有气门间隙或气门间隙过小时,便会把气门顶开,使气门关闭不严,造成漏气;但气门间隙过大,则造成工作时气门脚响及进气不足、排气不彻底。 二、进气门和排气门的确认方法。 1、根据气门与所对应的气道确定。进气歧管所对的是进气门,排气歧管所对的是排气门。 2、用转动曲轴观察确定。方法是:转动曲轴,观察各缸的两个气门,先动为排气门,随后动的为进气门,并在气门上作记号。结论:排---进---进---排---排---进---进---排。(先教师试范,后请四个学生分二组实验) 【思考】除了以上两种方法外,还有没有其它方法? 三、发动机的点火顺序的确认。 确定各缸的进气门之后,顺时针转动发动机的曲轴,先观察第一缸的进气门,当一缸的进气门打开后,再观察二、三、四缸的进气门,看哪一个缸的进气门紧接一缸的进气门之后打开,之后,再观察其它两个缸的进气门。结论:1---3---4---2
盘式制动器制动间隙调整测量方法
盘式制动器制动间隙调整测量方法 为确保前轴盘式制动器正确使用,现对前轴盘式制动器制动间隙的 制动间隙的测测量方法进一步明确规范,请认真参阅执行。测量制动间隙前,应首 应首先先 活塞总成)可以正常工作。本确认间隙自动调整机构((AZ9100443500 AZ9100443500 AZ9100443500活塞总成) 文首先表述如何判断活塞总成是否可靠工作,再进一步说明制动间 再进一步说明制动间隙隙的测量方法。
(盘式制动器外形)外形)/ /(各部件名称)判断活塞总成是否有效: 1、用SW10SW10扳手逆时针转动手调轴至极限位置(大体上逆时针旋转扳手逆时针转动手调轴至极限位置(大体上逆时针旋转扳手逆时针转动手调轴至极限位置(大体上逆时针旋转两两周),而后反向微调少许(以防螺纹发卡),而后反向微调少许(以防螺纹发卡); ;2、在气压足够大的情况下,原地连续踩刹车、在气压足够大的情况下,原地连续踩刹车101010次左右。注意:踩刹 次左右。注意:踩刹车时将扳手扣在手调轴上,以观察刹车时手调轴是否转动,正常现正常现象象应该是开始几次制动时扳手转动(顺时针)角度较大,越来越小,最后稳定到某个角度,此时即表明间隙已经调整到设计值。如果踩刹如果踩刹车车时手调轴不转动或者有逆时针转动状况,则该自动调整机构(活塞(活塞总总成)已不能正常工作,必须更换。 图一图一//图二图二/ /图三
制动间隙的测量: 盘式制动器从设计结构上已设定了制动间隙,并且制动间隙是自动并且制动间隙是自动调 调整的,不允许人为调整,制动间隙在0.80.8~ ~1.0mm 范围内是正常的。如果整车使用过程中出现左右制动力差值偏大、制动力不足或制动制动力不足或制动过过热等故障现象时,可按如下步骤检查制动间隙: 1、拆下压板(如塞尺插入方便可不拆压板),向箭头所指方向推动向箭头所指方向推动钳 钳体,使外侧制动块与制动盘紧密结合。(图一) 2、拨动内侧制动块使其靠近制动盘,测量间隙活塞总成整体推盘与制动块背板之间的间隙。(图二) 3、整体推盘与制动块背板之间的间隙应在、整体推盘与制动块背板之间的间隙应在0.80.80.8~ ~1.mm 之间,如小于0.8mm 0.8mm,应更换间隙自动调整机构(,应更换间隙自动调整机构(,应更换间隙自动调整机构(AZ9100443500AZ9100443500AZ9100443500活塞总成)(图三)活塞总成)注意事项: 盘式制动器从设计结构上已设定了制动间隙,并同时保证了制动间并同时保证了制动间隙 隙的自动调整。制动块和制动盘的间隙在制动块寿命期内是永远保持制动块和制动盘的间隙在制动块寿命期内是永远保持不不变的,只需按整车维修保养手册,定期检查制动块的磨损情况。因因此 此1.必须按上述正确方法测量制动间隙; 2.当制动块的摩擦材料的最小厚度小于2mm 时,必须更换制动块(此情况属于正常磨损,不属于三包范围)
裁断车间工序注意事项1
裁断车间工序注意事项 一、冲切工序:、 1、把待冲切的布整平,刀放正,操作时杜绝出现帮片中低斜的现象。 2、排刀时掌握左右上下刀间隙不宜太宽,一般在5毫米以下。 3、每冲切一趟要把布整理完好后再切下趟,以防不齐出现坏片。 4、排刀时根据布料及鞋号情况合理利用刀号,特别是布边沿根据剩布多少冲切鞋号。附件冲切,整平整齐体操下脚料再切。 5、冲切造成的坏片由操作人员包赔损失,按材料成本价扣工资,坏片谁操作谁处理。 6、冲切布头由操作工各自处理,并当天清理完毕,不准积压。 7、根据车间下达的冲切任务认真完成,不准少切、多切;用错刀、切错号根据材料损失情况酌情扣工资。 8、下班后搞好冲切机周围的环境卫生及设备清理保养,使设备保持清洁、干净、无油污。 9、设备保养,上班前先给设备加油,一天最少四次,保持设备运转良好。 二、摊布合布工序
1、首先检查所用原材料布料是否符合技术部门要求,是否有花色、跳纱、抽纱、宽窄不一致,EV A布面是否重批、烂胶片,及合布不符要求现象。对不合格的原材料操作人员应及时上报,并停止使用。使用不合格的布料所造成的损失,由操作人员负责。 2、摊布时一定掌握保持布边一边齐,不能出现摊布有皱现象,特别是中底布;EV A面布在缝边时一定注意两边对称,每针间距50厘米,把缝线拉紧;每层布两头要摊齐,不准长短不一。 3、合布严格按技术部门下达的工艺要求进行操作,中底布合好后及时摊出,以防焦烧损坏中底,因不摊而焦烧的布由操作人员负责损失。合面布时掌握好上浆量,不能出现太软及粘合不牢情况。搞好合布机周围的环境卫生,做到天天清理。 三、帮子印号 1、邦子数量问题:首先查准该号码帮子数量与计划单数量相同,不多不少。如出现差错,按差错比率扣操作人员的工资,一月内出现三次差错调离工作岗位。 2、帮子印号字迹清晰,印号标准,印错印不到位,印错号等造成损失的由操作人员包赔。 3、清理坏片。不合格的帮子不准流入下道工序,清出后进行补片,如数补。
气门间隙调整方法
发动机在冷态下,当气门处于关闭状态时,气门与传动件之间的间隙称为气门间隙。 间隙过大: 进、排气门开启迟后,缩短了进排气时间,降低了气门的开启高度,改变了正常的配气相位,使发动机因进气不足,排气不净而功率下降,此外,还使配气机构零件的撞击增加,磨损加快。间隙过小: 发动机工作后,零件受热膨胀,将气门推开,使气门关闭不严,造成漏气,功率下降,并使气门的密封表面严重积碳或烧坏,甚至气门撞击活塞。采用液压挺柱的配气机构不需要留气门间隙。 首先大家要知道气门摇臂与气门的间隙(即气门间隙)之所以存在,是因为进排气门均安装在燃烧室的顶端,也是温度最高之处,为了留有膨胀的空间,因而必须存有空隙,至于间隙的气门间隙 [1]大小,因厂家设计不同而不一致,通常进气门间隙在 0.2~ 0.25毫米之间,而排气门间隙由于受热膨胀比进气门侧的大,所以间隙更大些,一般在 0.29~ 0.35之间。发动机气门摇臂与此气门之间经过长久的动作及磨耗,间隙会愈变愈大,所以才有气门脚间隙的调整。然而并非所有汽车均需调整气门脚间隙,有些车辆气门间隙属于油压自动调整,就不需要调整气门间隙了。 (1)拆下气门室盖。 拆下气门室盖的固定螺丝,小心取下气门室盖,注意不要损坏气门室盖衬垫。用抹布擦净气门及摇臂轴上的油污,以方便气门调整作业。 (2)找到一缸压缩上止点。
用摇手柄转动曲轴或撬动飞轮,使一缸处于压缩上止点位置。从发动机前面看,曲轴皮带轮的正时凹坑与正时记号对准。在部分大型车上飞轮壳的检视孔1-6缸刻线与飞轮壳正时记号对齐。例如: 东风EQ6100-1型发动机,飞轮1-6缸刻线应与飞轮壳的钢球对齐。此时从气门处看: 一缸的气门应都处于关闭的状态。如果一缸的气门不全是关闭状态,说明一缸活塞在下止点位置,您应再转动曲轴360度,使一缸处于压缩上止点位置。 (3)确定各缸处于压缩上止点的方法。 根据发动机构造原理我们知道,各缸处于压缩上止点时,该缸的气门均处于关闭状态。 因此,您可以打开分电器盖并确定各缸高压分线的位置,摇转曲轴,当分火头指向该缸高压分线位置时,触点张开的瞬间位置,则该缸处于压缩行程的上止点位置。这们您便可以比较准确的确定各缸压缩上止点的位置,方便地调整气门。 (4)测量气门间隙。气门间隙有冷车值和热车值之分,您在测量时应在符合该车的规定的状态下进行。 气门间隙 选出符合规格的塞规插入气门杆与气门摇臂(或凸轮)之间。稍微拉动塞规,如有轻微的阻力,表示间隙正确。为了确定间隙是否在规定范围内,一般用范围极限值来测量(例如间隙范围值为 0.29mm到 0.35mm之间),先用 0.29mm的塞尺插入气门间隙,此时,塞规应如果可以通过,则是正常;再用
LEHYIII曳引机制动器间隙检查及均匀性调整
3.3.3.检查制动器间隙 制动器间隙要求: 松闸时,确认制动盘的摩擦片与制动盘不发生摩擦; 抱闸时,制动器间隙(制动器电枢与衔铁之间的间隙)为0.4mm~0.55mm。制动器间隙检查位置: 如图3- 6所示,制动器间隙为制动器电枢与衔铁之间的间隙; 如图3- 7所示,用塞尺分别在制动器圆周三个不同的位置进行间隙检查。 图3- 6 制动器间隙位置 图3- 7 制动器间隙检查示意图
3.3. 4. 检查制动器摩擦片磨损量 若制动器摩擦片与沉头螺钉的间隙≤0.8mm 时或制动器间隙大于0.8mm 时,需要更换制动器摩擦片组件或更换制动器。沉头螺钉位置参照图3- 6所示。 3.3.5. 检查与调整制动器间隙均与性 (1) 松闸状态下,间隙均匀性调节螺栓头部应接触定子机座安装面, 图3- 8 间隙均匀性调节螺栓位置照片 (2) 单个制动器松闸状态下,用塞尺检查每个制动器两侧摩擦片分别与制动盘表面的间 隙A 与B (精确到0.01mm ), (3) 确保0.05A B mm ?≤, (4) 若A >B ,则逆时针旋出间隙均匀性调节螺栓;若A <B ,则顺时针旋入间隙均匀 性调节螺栓, (5) 锁紧间隙均匀性调节螺母,固定间隙均匀性调节螺栓,并用记号笔在螺栓上做记号。 注意: 每个制动器配置有左右两处间隙均匀性调节螺栓,操作时应同时拧紧。 间隙均匀性 调节螺栓
图3- 9 制动器间隙均匀性调节示意图 3.3.6.检查制动器吸合时动作声音 制动器内部设有用于吸收制动器吸合时动作声音的缓冲橡胶。 在制动器间隙满足要求的前提下,若制动器吸合时动作声音明显变大,应及时调整或更换制动器缓冲橡胶。参照3.3.7进行制动器缓冲橡胶调整。 注意: 出厂时制动器动作噪音要求小于60dB(A),经过较长时间动作,制动器噪音会相应增加,尤其是摩擦片磨损后,噪音增加会更明显。制动器动作噪音不应超过70dB(A)。 3.3.7.调整制动器缓冲橡胶 制动器缓冲橡胶调整参照如下步骤,如图3- 10所示: (1)擦除六角螺母和内六角平端紧定螺钉处(共4处)的标记线; (2)使制动器处于断电抱闸状态,松开六角螺母(注意操作时应防止螺钉随螺母跟转), 顺时针拧紧内六角平端紧定螺钉10°; (3)拧紧六角螺母(注意操作时应防止螺钉随螺母跟转),锁紧内六角平端紧定螺钉;
如何调整气压制动和制动器间隙
如何调整制动间隙 现在很多车主对自己爱车的制动性能都特别关心,城市用车刹车制动的情况太多,会不会时间久了刹车就越来越差?制动距离会不会越来越长?制动失效怎么办?现在我们围绕着汽车制动系统聊一聊。 首先,我们先聊下什么是制动蹄片? 制动蹄片这个词可能很多人不太清楚,那它的另一个名称估计就都知道了,制动蹄片也就是我们俗称的刹车片,刹车片是受到刹车凸轮或推杆的作用而被推向外展开压制刹车鼓,进而起到制动作用的配件。 其次,平时车辆制动系统都易出哪些方面的问题呢? 制动磨损这个是避免不了的,伴随着磨损,制动间隙也会随之增大。磨损易导致制动器间隙不一致,并容易产生制动工作时间延长,车辆跑偏、车辆甩尾等问题。第三,为解决这些问题,制动系统相关养护工作要做好。 1.车辆正常行驶5000公里必须检查刹车片,包括刹车片剩余厚度、刹车片磨损状态、两边磨损程度等。 2.不要让刹车片磨没了再更换,即便看着还能用一段时间,也会大大降低制动效果,影响驾车安全。 3.刹车片更换最好选择原厂提供的备件,目的是制动效果最好,磨损最小。 4.更换完后踩几下刹车踏板,消除刹车片与制动盘之间非固定间隙。 5.新的刹车片更换好后,要谨慎制动,适应新的刹车状态。 最后,刹车片间隙调整 刹车片与制动鼓之间必须留有一定的间隙。刹车片间隙不符合要求,将直接影响汽车的制动性能。
1.顶起车轮并确认轮毂无摇动,拆下调整孔的防尘塞,检查刹车片状况,若磨损到使用极限标记时,及时更换蹄片。 2.检查车轮制动器蹄片与制动鼓间隙时,将制动踏板踩到底,测量制动踏板外边缘至驾驶室前围板的距离应不小于规定值。若小于规定值,说明制动摩擦片磨损,间隙增大,应进行调整。 3.调整时,由调整孔插入螺丝刀,向箭头所示方向拨动调整齿轮,直到车轮不能转动为止。踩下数次制动踏板,再次确认车轮不能转后,倒拨4~5齿。此时,将选择好的厚度合适的塞尺插入到制动鼓,拔出塞尺,若感到有一定的阻力为合适。如不合要求,可拨动调整齿轮进行调整。用同样的方法调整另一侧蹄片间隙。 4.用手转动车轮,车轮应能圆滑转动,没有滞磨现象。如感到有滞磨现象,可将调整齿轮再松回1~2齿。装上调整孔防尘塞,然后起动汽车,以30km/h的速度试验制动器的制动效果,检查有无偏刹或其他异常现象。如有偏刹或其他异常现象,应重新调整制动器。 5.部分新车的鼓式制动器装有蹄片间隙自调装置。自调装置在倒车时起作用,因此要在慢慢倒车时,踩下制动踏板。有的车自调装置是通过手制动作用的。在这种情况下,要拉起手制动杆,就可以达到调整车轮蹄片间隙的目的。 车辆制动系统间隙的调整,这些工作由专业维修技师来完成,车主只要注意爱车的使用情况,平时注意感知车辆的行车状态,按照正常的制动系统养护周期,到有车辆维修及保养资质的单位,给爱车做好保养服务就可以了。
调整制动间隙
调整制动间隙 车轮制动器制动间隙的调整分局部调整和全面调整两种。局部调整只需调整制动蹄的张开端,通常用于车辆在运行过程中因蹄鼓的间隙变大而进行的调整。全调整需同时调整制动蹄片两端的位置,通常用于更换制动蹄衬片或镗削制动鼓后为保证制动蹄与制动鼓的正确接触而进行的调整。对于不设置固定端的自动增力式车轮制动器而言,没有全面调整和局部调整之分。 (1)液压制动系鼓式车轮制动器 其局部调整的步骤如下: 1)顶起车轮,一边转动车轮,一边向外转动调整凸轮螺栓,直至制动蹄压紧制动鼓为止。转动车轮时,应有一定的方向,即调整前轮两蹄和后轮的前制动蹄时向前转动车轮;调整后轮后制动蹄时向后转动车轮。 2)向内转动调整凸轮螺栓,直至车轮能自由转动而制动蹄与制动鼓不碰擦。 3)用同样的方法调整其他调整凸轮螺栓。 4)用塞尺检查蹄鼓间隙应符合规定。 全面调整的方法如下: 1)按局部调整的方法转动调整凸轮螺栓至制动鼓不能转动为止 2)向能够转动支承销的方向转动支承销。 3)重复上述的1)、2)两步,直至调整凸轮螺栓与支承销均不能转动为止。 4)锁紧支销后,向内转动偏心轮螺栓,直至车轮能自由转动且制动筛与制动鼓不碰擦。 5)在检视孔用塞尺测量蹄鼓间隙。支承轴端为0.15m.张开端为0.3mm。 (2)气压制动系鼓式车轮制动器 局部调整的步骤如下: 1)支起车桥,使车轮能够自由转动。 2)推进调整臂的锁止套. 用扳手转动蜗杆轴使制动路压紧制动鼓(搬动蜗杆轴时应注意观察凸轮轴的转动方向应为其工作方向),至蜗杆轴不能再转动为止。 3)以反方向退回蜗杆轴至车轮自由转动且石碰擦制动鼓。 4)用塞尺检查制动器蹄鼓间隙,靠近凸轮端为0.4~0.7mm,靠近支承销端为0.22~0.5mm。5)用锁止套锁紧蜗杆轴。局部调整时应注意不允许用改变制动气室推杆总长度的方法来 调整制动间隙,因为这样会减小使蹄片张开的推动力。 全面调整的步骤如下: 1)松开凸轮轴支架的固定螺栓,使凸轮获得一定的自由度,以便其自动找正中心。 2)转动调整臂的蜗杆轴使制动蹄压向制动鼓,至蜗杆轴不能再转动为止。晃动凸轮轴支架,使凸轮位置居中。 3)向可以转动的方向转动两支承销,直至制动蹄片固定端抵住制动鼓,支承销不能再转动力止: 4)重复②、③两步,直至制动蹄片的两端均抵住制动鼓,蜗杆轴和支承销不能再转动为止。在此位置上,先将凸轮轴支架固定和支承销固定,然后转动调整臂的螺杆袖,使制动肺片退回,两端出现间隙。 5)用厚薄规检查制动蹄鼓的间隙应符合要求。
配刀方法
配刀方法和换刀程序 一、示意图及方法 图中: B—刀轴宽度;b—成品宽度;C—刀片宽度;s—水平间隙(厚度的6-10%);k—上下刀重合量(厚度的1/3-1/2)。 1.正公差配刀 ①以公刀外侧宽度作为成品宽度; ②对中装刀,按X2=(B-Σb)/2确定下刀轴传动侧到第一把刀的间距,用隔套和刀片装好下刀轴第一把刀; ③则上刀轴第一把刀距传动侧的间距为X1=X2-s,用隔套和刀片装好上刀轴第一把刀(注意X1包含的隔套组合和1把刀片的宽度);
④公刀隔套间距=成品宽度b-2*刀片宽度C; ⑤母刀隔套间距=成品宽度b+2*水平间隙s。 举例说明: 原卷宽度1250,厚度1.0,要求纵剪为226宽度的带钢5条+90宽度1条,刀轴宽度为1750,刀片宽度为15,水平间隙为0.08,正公差如何配刀? ①X2=(B-Σb)/2 =[1750-(226*5+90*1)]/2=265; ②X1= X2-s=265-0.08=264.92,因此取15宽度的刀片1片和249.92宽度的隔套组合; ③226公刀隔套间距=成品宽度b-2*刀片宽度C=226-2*15=196; ④226母刀隔套间距=成品宽度b+2*水平间隙s=226+2*0.08=226.16。 ⑤90公刀隔套间距=成品宽度b-2*刀片宽度C=90-2*15=60; ⑥90母刀隔套间距=成品宽度b+2*水平间隙s=90*2*0.08=90.16。 2.负公差配刀 ①以母刀内侧宽度作为成品宽度; ②对中装刀,按X1=(B-Σb)/2确定上刀轴传动侧到第一把刀的间距,用隔套和刀片装好上刀轴第一把刀(注意X1包含的隔套组合和1把刀片的宽度); ③则下刀轴第一把刀距传动侧的间距为X2=X1+s,用隔套和刀片装好下刀轴第一把刀; ④公刀隔套间距=成品宽度b-2*刀片宽度C-2*水平间隙s; ⑤母刀隔套间距=成品宽度b。 举例说明: 原卷宽度1250,厚度1.0,要求纵剪为226宽度的带钢5条+90宽度1条,刀轴宽度为1750,刀片宽度为15,水平间隙为0.08,正公差如何配刀? ①X1=(B-Σb)/2 =[1750-(226*5+90*1)]/2=265;,因此取15宽度的刀片1片和250宽度的隔套组合; ②X2=X1+s=265+0.08=265.08; ③226公刀隔套间距=成品宽度b-2*刀片宽度C-2*水平间隙 s=226-2*15-2*0.08=195.84;
气门间隙调整方法和步骤
气门间隙两次调整法最简单的调整步骤 周利顺 【摘要】:正气门间隙两次调整法最简单的调整步骤: (1)摇转曲轴,使第一缸处于压缩上止点位置,借助于厚薄规测量,将所有缸(注意:即发动机的各个气缸)的进、排气门均调至规定间隙。 【关键词】:两次调整法气门间隙调整步骤多缸发动机压缩上止点厚薄规曲轴排气门简单摇转 【正文快照】: 气门间隙两次调整法最简单的调整步骤: (l)摇转曲轴,使第一缸处于压缩上止点位置,借助于厚薄规测量,将所有缸(注意:即发动机的各个气缸)的进、排气门均调至规定间隙。(2) 摇转曲轴360…,用厚薄规检查除第一缸以外的其他缸各个气门的间隙。若间隙减小或未变,则该气门已调整准确 气门间隙调整——检查调整步骤 首先大家要知道气门摇臂与气门的间隙(即气门间隙)之所以存在,是因为进排气门均安装在燃烧室的顶端,也是温度最高之处,为了留有膨胀的空间,因而必须存有空隙,至于间隙的大小,因厂家设计不同而不一致,通常在0.2~smarttags" />0.25毫米之间。发动机气门摇臂与此气门之间经过长久的动作及磨耗,间隙会愈变愈大,所以才有气门脚间隙的调整。然而并非所有汽车均需调整气门脚间隙,有些车辆气门间隙属于油压自动调整,就不需要调整气门间隙了。 (1)拆下气门室盖。拆下气门室盖的固定螺丝,小心取下气门室盖,注意不要损坏气门室盖衬垫。用抹布擦净气门及摇臂轴上的油污,以方便气门调整作业。 (2)找到一缸压缩上止点。用摇手柄转动曲轴或撬动飞轮,使一缸处于压缩上止点位置。m e93R6d)m9e 从发动机前面看,曲轴皮带轮的正时凹坑与正时记号对准。在部分大型车上飞轮壳的检视孔1-6缸刻线与飞轮壳正时记号对齐。例如:东风EQ6100-1型发动机,飞轮1-6缸刻线应与飞轮壳的钢球对齐。( #?+B6w c9r 此时从气门处看:一缸的气门应都处开关闭的状态。如果一缸的气门不全是关闭状态,说明一缸活塞在下止点位置,您应再转动曲轴360度,使一缸处于压缩上止点位置。-p8I&A! F8q}~k(@(3)确定各缸处于压缩上止点的方法。根据发动机构造原理我们知道,各缸处于压缩上止点时,该缸的气门均处于关闭状态。因此,您可以打开分电器盖并确定各缸高压分线的位
纸张模切异常改善方法
纸张模切异常改善方法 模切压痕加工技术,适用于各类印刷品的表面加工,特别针对各种档次的纸箱、纸盒、商标、艺术品等表面的整饰加工,同时也是实现包装设计的重要手段之一。模压技术下仅对包装的最终质量和效果起着重要作用,同时可以在很大程度上提高印刷晶的艺术效果,并且还赋予印刷品新的功能,已成为印刷品增值和促销的重要手段。因此,模切压痕技术越来越受到人们的青睐,使用的范围也越来越广。 包装中使用的各类纸箱其平面展开结构由轮廓裁切线和压痕线组成,并经模切压痕技术成型,模压是其主要的工艺特点。尤其是对于一些非直线的异形外廓和功能性结构,如内外摇盖不等高、开有提手孔、通风yl、开窗孔等结构的纸箱,只有采用模压方法,才便于成型。由于模压加工的这些特点,使其越来越广泛地应用于各类印刷纸板的成型b口工中,已经成为纸箱企业成型加工不可缺少的重要环节。 模切工艺 模压前,需先根据产品设计要求,用钢刀(即模切刀)口铜线(即压线刀)或钢模排成模切压痕版(简称模压版),将模压版装到模压机上,在压力作用下,将纸板轧切成型并压出折叠线或其他模纹。模压版结构及工作原理如图1所示,图2为圆压模切,图3为平压模切。模切压痕的主要工艺及操作过程(如图4所示)
钢刀进行轧切,是一个剪切的过程;而铜线或钢模则对纸板起到压力变形的作用:弹性胶条(或海绵)用于使成品或废品易于从模切刀刃上分离出来垫版的作用类似砧板。 故障分析及解析 在模切压痕工艺中,常常出现一系列的问题,影响生产的顺利进行。在介绍了模切工艺原理的基础上,对模切压痕生产中所遇到的常见问题进行进一步分析,探讨其解决方法。希望对纸箱企业的实际生产有所帮助。 1 模切精度不高 模切中出现偏差是生产中的最常见问题。模切的精度是衡量模切质量最为重要的标准之一,是合格产品的重要保证。影响模切精度的原因很多,如机械的原因,模切版本身的问题,也有来自印刷品的问题,作业环境,人员操作的问题等。不同的问题有不同的解决办法,这里一一进行分析。 ■纸板传送过程中,主传动链条磨损拉长,将直接影响模切前的定位精度,此时要图4模切操更换链条。间歇机构磨损,造成牙排在停止或起动过程中发生抖动,也会影响模切精度。这种情况下一般只对定位精度产生影响,此时,应对司歇机构进行检修 ■前、后定位摆架定位距离过小。因为链条本身长度有一定的误差,如果定位距离过小,则在前、后定位时不能消除链条误差,从而影响模切精度。此时应调整前定位摆架的调整螺杆或后定位摆架的凸轮位置,使前后定位架能拨动牙排2mm~3mm距离为宜
制动器间隙调整
制动器 适用于安装在旋转的制动盘上,用于停机制动、工作制动和紧急制动 制动器安装在齿轮箱的高速轴侧。该制动器是一个液压动作的盘式制动器,为常闭式,具有刹车间隙自动补偿功能。 主动式与被动式制动器 ?主动式:加压制动、泄压打开(SL3000) ?被动式:加压打开、泄压制动(SL1500) ?在首次安装制动器时,必 须检查主动制动器刹车片保 持架与制动盘之间的距离。 该距离必须大于1mm,小 于3mm。 刹车片更换: 取下制动器尾帽上的两个传感器; 手动打开制动器; 在尾帽中间传感器的安装孔内安装 气隙螺栓和垫圈,并手动拧紧 ①刹车片磨损传感器 ②制动器打开与未调整传感器 ③气隙螺栓和垫片
制动器最小打开压力、泵启动压力、停止压力、溢流压力、系统最大可承受压力 制动器最小打开压力:125bar 液压泵站启动压力:130bar 液压泵站停止压力:160bar 溢流压力:190bar 系统最大可承受压力:210bar
1:AWA定位装置的位置 主定位系统 辅助定位系统 2:制动间隙调整 2.1:制动器的安装,见下图 2.2制动间隙的调整 1)制动间隙调整前的制动钳相对于制动盘的位置。(见图2-1) O型圈 图2-1 图2-2 2)调试前先拆除制动器上的O型圈,位置在制动钳与基座之间。(见图2-2)3)松开主定位系统、辅助定位系统的螺栓、螺母。
图2-3 图2-4 完全拧松 4)检查滑动轴是否滑动顺畅。应能够用手指推动滑动轴上下运动。 若滑动不畅则可以松开顶部的螺栓进行微调。(产生原因为:拧紧安装螺栓(或螺母)时液压扳手有可能会带动AWA的安装基板产生位移。)同时检查滑动轴与定位轴之间的平面的间隙。 图2-5 图2-6 在滑动轴滑动不畅时此U型孔可进行微调。此时滑动轴应可以轻易滑动。 5)手动加压8~10次,注意:任何情况下手动加压的次数不应少于8次,目的是为了将制动器的制动间隙调整为2mm。间隙全部位于被动钳一侧 图2-7 图2-8 主动钳被动钳制动间隙2mm 6)泄压后使制动器进入闭闸状态。
气门间隙调整方法_D6114
1.气门间隙调整方法: 1.1打开气门罩壳,盘车至第1缸进、排气门摇臂静止不动,并且第6缸进、排气门摇臂相向移动(进、排气门一个上移、一个下移),停止盘车; 1.2 调整1、2、4缸进气门和1、3、5缸排气门间隙; 1.3 调整完毕后,再盘车360度左右,至第6缸进、排气门摇臂静止不动,并且第1缸进、排气门摇臂相向移动(进、排气门一个上移、一个下移),停止盘车,此时调整3、5、6缸进气门和2、4、6缸排气门间隙。 备注:其中进气门间隙为(0.3±0.08)mm 排气门间隙为(0.5±0.08)mm 2.判断上止点方法: 2.1 首先打印附图1(★该图片不得进行缩放打印)的纸带并裁剪,同时制作一个临时指针(如:细铁丝); 2.2 打开气门罩壳,盘车至第1缸进、排气门摇臂静止不动,并且第6缸进、排气门摇臂相向移动(进、排气门一个上移、一个下移),停止盘车,此时拆下第1缸摇臂,进气门上座、弹簧、气门锁夹,并将进气门按到底; 2.3装上不平度检测装置,其中探头装在进气门杆顶端面、另一头放在一个固定平面上(如:齿轮室上),此时来回小幅盘车(★注意:必须小幅盘车,以免气门掉进气缸)待仪表指针返回瞬间,停止盘车,此时刻即为第一缸做功冲程上止点; 2.4找到上止点后,在曲轴减震器外圆周面上贴上打印好的纸带(可以使用胶粘贴),再将临时指针一端指向纸盘0刻度,另一端固定在某个固定物体上(如发动机齿轮室上★在找到上止点至装配好指针过程中不允许盘车),装配的指针要保证盘车时不被干扰; 2.5再装上弹簧、进气门上座、气门锁夹、此时要用铜棒或木棒敲击气门杆端部以确保气门锁夹完全装配到位,再装摇臂和气门罩壳。 3.调整提前角: 3.1按常规方法利用临时指针和纸盘刻度调整提前角。调整完毕撤除临时指针和纸带。 4.特殊机型简便方法 4.1此特殊机型指的是油泵含插销的机型(见附图2); 4.2拆下油泵上正时螺栓,拿出插销,盘车至插销能与油泵里面卡口插上时,此时刻即为发动机上止点。 4.2.1如此时维修发动机无需盘车,拆检或者更换油泵时保证油泵正时位置(即油泵插销能插上的位置)即可直接装上油泵,无需调整提前角。 4.2.2如维修需要盘车,此时在减震器和和齿轮室罩壳以及高油泵齿轮和齿轮室上用记号笔各画一个记号,拆下维修发动机,在装油泵之前盘车至这两个记号同时对上,将处在正时位置的的油泵(即油泵插销能插上的位置)直接装上即可,无需调提前角。 5、相关照片见附图2
纵剪线操作规程(定稿1)
纵剪线操作规程 一、纵剪线设备组成及工艺流程 1、设备组成 1700×10mm纵剪线主要由上卷小车、双锥头开卷机、直头机、 夹送处理机、1#侧立导辊、、 2#侧立导辊、水平导辊、园盘纵剪机、 边丝卷取机、活套装置、张力机、卷取机、分隔器、卸卷小车等设备 组成。 夹送处理机、园盘纵剪机及卷取机的三台直流主电机采取英国 CT-MENTOR全数字式直流调速器进行拖动控制,两台边丝卷取机采取 电磁调速异步电动机(滑差电机)进行拖动控制;全生产线包括液压 系统、气动系统等均由日本三菱PLC进行自动程序控制,可接工控 机或PC机等上位机进行过程控制和管理操作。 2、工艺流程 上卷→开卷→直头→矫直→切头(尾)→纵剪分条(边丝卷取)→带钢卷取(打捆)→卸卷 3、工艺参数 钢卷材质:低碳钢或低合金钢带钢厚度:2.0~10mm 钢卷宽度:700~1550mm 钢卷内径:¢500~760mm 最大卷重:30吨成品钢卷内径:¢760mm 典型分条条数: 带厚(mm) 3.6 4.5 6.0 8.6 分条条数 11 8 5 3
二、工艺操作程序 A、点动穿带作业 1、各岗位检查设备没有异常(同时各操作台按扭、电位器归零复位),依次送电(受电柜总开关→PLC控制柜→CT-MENTOR控制柜(直流主电机风机)→液压站油泵→空压机等)。 2、中央主控操作台将生产线选为“点动”状态。 3、开卷作业(1#操作台) 点动上料小车到待料位置,配合天车工将钢卷吊放至小车鞍型托架上,注意钢卷板头要处于上部稍偏右顺时针方向(面对生产线),横移上料小车至开卷机双锥头中心位置,上升小车;双锥头对中直至夹紧钢卷,上料小车下降脱离钢卷,直头机压辊下降压住钢卷,铲刀伸出铲断钢卷捆带(或人工剪断),捆带回收。根据带钢宽度调整1#侧立导辊开口度,点动双锥头,在直头机压辊配合下将钢卷板头沿铲刀牵引至夹送处理机的夹送辊里,按下夹送处理机架上的下降按钮,夹送辊下降压住钢卷板头(压力要适中,以板头不产生塑性变形为原则),横移上料小车至待料位置。 4、矫直、切头、分条作业(2#操作台) 点动夹送辊(此时开卷机处微制动状态),压下三辊矫直辊(视带钢表面弯曲程度调整压下量),牵引带钢至斜刃横剪机。根据带钢头部缺陷情况决定横剪多少?压下斜刃剪,剪去板头(落入料筐)。根据带钢宽度和厚度调整2#侧立导辊和水平导辊的开口度,继续点动夹送辊,牵引带钢至园盘纵剪机。压下水平上导辊,点动园盘纵剪
鼓式制动器设计说明书
课程设计 小型轿车后轮鼓式制动器设计 学生姓名: 专业班级: 指导教师: 学院: 年月
东北林业大学 课程设计任务书 小型轿车后轮鼓式制动器设计 学生姓名: 专业班级: 指导教师: 学院:
小型轿车后轮鼓式制动器设计 摘要 随着汽车保有量的增加,带来的安全问题也越来越引起人们的注意,制动系统是汽车主动安全的重要系统之一。如何开发出高性能的制动器系统,为安全行驶提供保障是我们要解决的主要问题。另外,随着汽车市场竞争的加剧,如何缩短开发周期、提高设计效率,降低成本等,提高产品的市场竞争力,已经成为企业成功的关键。 本说明书主要介绍了小型轿车(0.9t)后轮鼓式制动器的设计计算,主要零部件的参数选择的设计过程。 关键词:汽车;鼓式制动器
目录 摘要 1绪论.........................................................................................................错误!未定义书签。 1.1概述 .................................................................................................... 错误!未定义书签。 1.2设计要求 ............................................................................................ 错误!未定义书签。 1.3设计目标 ............................................................................................ 错误!未定义书签。 2 鼓式制动器结构参数选择.....................................................................错误!未定义书签。 2.1制动鼓直径D或半径R.................................................................... 错误!未定义书签。 2.2制动蹄摩擦衬片的包角β和宽度b................................................. 错误!未定义书签。 2.3 摩擦衬片起始角β0 ........................................................................... 错误!未定义书签。 2.4 张开力P的作用线至制动器中心的距离a ..................................... 错误!未定义书签。 2.5制动蹄支撑销中心的坐标位置k与c.............................................. 错误!未定义书签。 2.6 摩擦片系数f ..................................................................................... 错误!未定义书签。 2.7 制动轮缸直径 d和管路压力p....................................................... 错误!未定义书签。 w 3制动蹄片上制动力矩的有关计算..........................................................错误!未定义书签。 4 鼓式制动器主要零部件结构设计及校核计算.....................................错误!未定义书签。 4.1鼓式制动器主要零件结构设计 ........................................................ 错误!未定义书签。 4.1.1 制动鼓............................................................................................. 错误!未定义书签。 4.1.2 制动蹄............................................................................................. 错误!未定义书签。 4.1.3 制动底板......................................................................................... 错误!未定义书签。 4.1.4 制动蹄的支撑................................................................................. 错误!未定义书签。 4.1.5 制动轮缸......................................................................................... 错误!未定义书签。 4.1.6 自动间隙调整机构......................................................................... 错误!未定义书签。 4.1.7 制动蹄回位弹簧............................................................................. 错误!未定义书签。 4.2 校核 .................................................................................................... 错误!未定义书签。 4.2.1 摩擦力矩和摩擦材料的校核......................................................... 错误!未定义书签。 4.2.2 摩擦衬片的磨损特性计算............................................................. 错误!未定义书签。 4.2.3 制动蹄支撑销剪切应力的校核计算............................................. 错误!未定义书签。结论 (14) 参考文献 (15) 附录 (16) 致谢 (17)
江西金阳带钢分条机工作原理及分条排刀示意图
分条机工作原理及分条排刀示意图 一、分条加工的原理 分条加工流程示意图如下图所示: 由开卷将原料展开并送入圆盘剪分条后再经过收卷机将其重新收卷成卷,通过刀片的旋转可作不定长度之板材剪切。 在分条行业中,刀片的选择、刀片套环的选择、刀片的水平间隙及刀片的重叠量都很重要,关系到剪切成品精度及质量。 二、刀片的选择 1. 材料选择 在分条机裁剪行业中,通常选用刀片,根据金属元素组成可知: A. 含Cr的金属制品可以使金属组织细微化,可起到防锈的功能; B. 含Mo的金属制品可增加金属之强度、硬度,使其具有更高的切削性能; C. 含钒的金属对于抗冲击及疲劳性有很大的作用;
三、刀片排组 1. 按现行的刀片排组方法,通常把隔片组合分成两大类: A. 下切组合:按行业习惯称其为“公”,其组合方法按所分条规格、板材质地、厚度而定,若以公式形式表示则为:公=分条规格(母)-刀片厚度×2-单边水平间隙×2 B. 分条规格组合:按行业习惯称其为“母”,又称内切组合,其组合方式则以所需分条成品宽度而定,假如分条所需规格为80,其组合长度则排80即可。 例如:分条规格为80,板厚为1.0的普板,则刀片长度为10,水平间隙0.1,母=80mm 公=80-10×2-0.1×2=59.8mm 2. 以上为刀片隔套及刀片排组方法,在分条作业中,如何才能将分剪成品平整地推出内切片刀,则需要有相应的退料装置,按常规退料方式有:A、橡胶圈B、板条等 A. 橡胶圈退料方法(适用于较厚或宽条成品板材): ①我们使用的退料胶圈通常采用耐油耐磨橡胶,如聚胺脂,又称优力胶,化学名称符号表示为“PU”,另一种常用橡胶为丁晴橡树脂,这些材料都具有较高的耐油耐磨、抗腐蚀的功能和较好的形变回复能力,根据其剪切材料的不同,我们在制造该配件时视剪切板材的厚度、质地等作相应的硬度调节处理,一般的硬度范围在HS60~90°。 ②胶圈尺寸的选择:胶圈尺寸通常按刀片的尺寸,刀片隔片的尺寸来决定其内径大小,在剪切不同厚度板材时使用相应外径之退料胶圈,方可确保分条成品的外观平整及表面品质。但考虑到板材厚度的多样性,我们在订制胶圈外径时,通常选择两种外径的退料胶圈:即与刀片外径相同和比刀片外径大1~2mm的退料胶圈,在制造胶圈时,考虑其尺寸的不同,我们可以将其用不同颜色区分开来,如:与刀片一样大选择红色,比刀片略大胶圈选择黑色等,因剪切规格不同,其厚度趋于万能组合。按以上说法,可能有人会问,制定两种外径的胶圈是否可满足所有厚度板材之使用?这里较正确的回答当然是不行和行两结果:“不行”是按绝对的逻辑推算结果来说的,而“行”又是按相对的在实际使用中切实可行的结果来说的,但必须辅以相应的辅件来完成,这里的辅件则指胶圈定位拉簧等。 ③胶圈排组方法:通常采用“母”刀内装较小胶圈,“公”刀内装相对较大胶圈,这样确保分条成品能平整退出,又在公刀刀片下切挤压时确保成品带材无刀片压痕、压印,其方法如下:
鼓式制动器问题讨论
鼓式制动器问题讨论 2007-4-16 11:15:11 问:关于多数客车的后制动器---CHHUA 答:在鼓式制动器的客车长期使用中我们不难发现其后制动器在使用中时常存在两个制动蹄上的磨擦片磨损不一致,其下片比上片要磨损得多,而且随着使用时间增长伴随着发生制动力不足,发奠烫、冒烟等情况,特别是城市公交车更是如此,其主要的原因有2点 1鼓式制动器的制动蹄有增势、减势之分,由于后置式客车车桥的主减速器设于车桥的后方,所以多数桥厂家都将制动器的凸轮轴安装在车桥的前方,因此制动蹄的上片为减势片、下片为增势片其下片比上片要磨损得多, 2我前面提到了由于上、下两个制动蹄都挂在凸轮轴上,至使导致凸轮轴的下方及衬套相应的位置磨损,造成了整个制动蹄园心的下移,造成了下制动蹄与制动鼓相贴进,在车辆向前行驶时自动形成制动。 我们的做法是 1将上制动片的面积适当减少,将上制动片的中部锯掉三分之一左右,以提高上制动片的单位面积压力,让上、下片之间的磨损趋向平均。 2十分注重刹车凸轮轴和凸轮轴衬相应的磨损量, 3十分注重制动蹄与鼓的同心度 4注重制动鼓与轮较 问:我是公交车司机最近车子做了二保后制动时感觉车辆不平稳比较冲好象制动力时大时小还有车速上了50码方向就发抖请教是什么原因啊 答:根据以上朋友的介绍我认为是制动鼓存在失园现象或制动盘有不平行现象存在,应为在制动过程中当制动分泵以一定的压力推出时会产生大小不一的制动力,此种现象在冷车时会特别明显,但连续踩刹车让制动鼓温度上升后会明显减弱,建议将制动间隙尽量调小然后用手搬转轮子察看阻力有否大小变化,如果有就对刹车鼓进行同心度光削。我们己多次排除该类故障。 问:传动轴的夹角大概多少度是正常的(后置的发动机) 答:满载时4度,最大不超过7度,一般的万向节计没角度允许至25度,而建议小于7度使用 问: 制动间隙自动调的问题,新车的第一年里根本不用调,刹车很好。现在差不多了三年车了,换上人工调的,几乎没一两天都要调一次。嫌烦,于是重金买来两个后轮的自动调的调整臂。装上试用一趟,发现托刹。另外的车发现刹车效果不好,根本没有自动调的效果。 答:根据想象该车为后置发动机的客车,由于此类车辆的主减安装于车轿的后方而迫使刹车分泵及刹车凸软轴安装在车桥的前方,当车辆行驶时间及里程的增加造成了凸轮轴及衬套的磨损(同时两块刹车蹄重量是全部压在凸轮轴上),造成了凸轮轴下沉而使刹车蹄与刹车鼓不同心,当正常制动时下端的制动蹄先与制动鼓接触而托起凸轮轴,而自动调节器所判断的间隙是按此时的情况下测量的,当解除制动时造成了上制动蹄与制动鼓的间隙为(正常间隙+