重油催化裂化装置催化剂损耗因素与经济效益

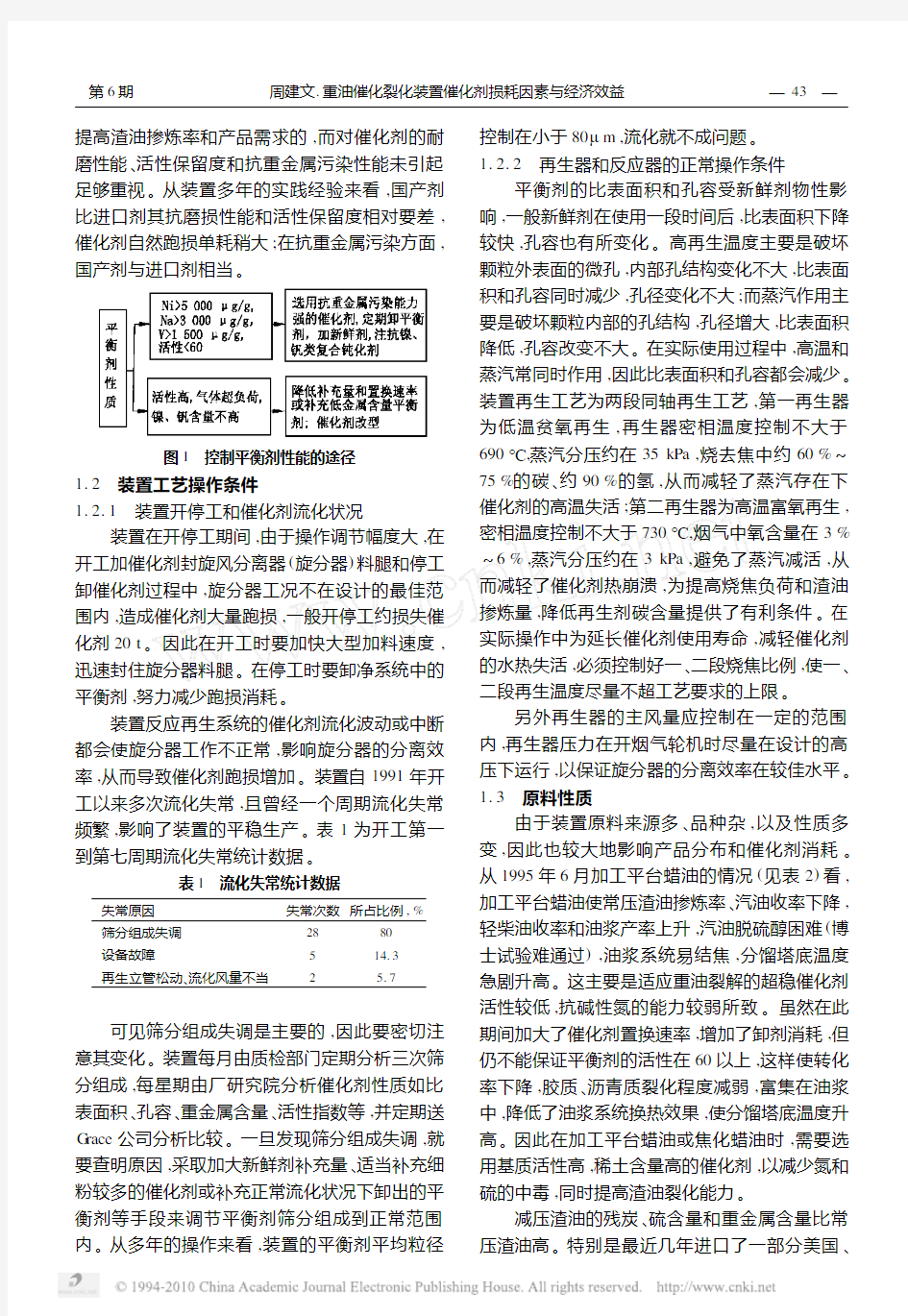
重油催化裂化装置催化剂损耗因素与经济效益
周建文
金陵石油化工公司炼油厂(江苏省南京市210033)
摘要:结合金陵石油化工公司炼油厂重油催化裂化装置的运行情况,分析了催化剂品种及其性质、装置操作状况、原料性质、产品构成及其质量要求、旋风分离器效率等对催化剂消耗的影响,通过对装置各项经济指标的分析,提出了降低催化剂单耗的措施和适宜的催化剂单耗控制范围。
主题词:渣油 流化催化裂化装置 催化剂 单耗 影响因素 经济效益
在催化裂化装置的实际操作中应努力提高操作平稳率,降低催化剂自然跑损,同时应适当控制卸剂单耗。但是如果催化剂的总单耗(包括自然跑损单耗和卸剂单耗)过低则会造成平衡催化剂(平衡剂)的活性和选择性下降,产品分布变差,总体效益下降,而增加催化剂的消耗又会引起加工成本的增加,这就需要对催化剂的总单耗进行优化。本文结合金陵石油化工公司炼油厂重油催化裂化装置的运行情况对这一问题进行探讨。
1 催化剂单耗的影响因素
1.1 催化剂品种和物化性质
新鲜催化剂(新鲜剂)的筛分组成、机械强度和水热稳定性决定了催化剂在系统中的耐热和抗磨损性能,从而影响催化剂的自然跑损。催化剂的活性保留度和抗重金属污染能力决定了催化剂的产品选择性,从而影响催化剂的卸剂置换速率。
平衡剂上的重金属含量说明原料的性质优劣和催化剂的中毒程度。控制平衡剂的重金属污染,一般采取三个方法:①选择抗重金属污染能力强的催化剂,因为在原料性质无大变化和保持同样的反应转化率下,如果催化剂抗重金属能力由镍含量6000μg/g、钒含量2000μg/g提高到镍含量8000μg/g、钒含量4000μg/g,则催化剂按同比例跑损和重金属沉积计算,催化剂消耗可下降约25%,每吨原料的加工成本降低约8RM B。②卸出平衡剂,补充新鲜剂。③注复合钝化剂,如采用石油大学开发的抗镍、钒、钠、铁的复合钝化剂,在1999年装置炼进口常压重油时,平衡催化剂的钠、镍、钒含量分别达4000,7000,3600μg/g的情况下,活性仍能保持在60以上。
另外如果催化剂的抗水热稳定性提高,老化失活速度慢,催化剂在系统中活性保留度较好,则也可降低催化剂的单耗。不同的催化剂其减活程度不同。Z C M27沸石表面积在减活条件下8小时后降低很大,而Octacat2D经16小时蒸汽老化处理后仍保持50%的比表面积。在装置上的实际使用结果也反映了在同样的催化剂补充速率下, Octacat2D催化剂比表面积维持在125m2/g左右, Z C M27催化剂在110m2/g,而O+/XP280L和Reduxion催化剂在135m2/g左右。因此提高催化剂活性保留度也是催化剂选型的一个重要方面。
系统平衡剂性能的总体反映是催化剂的活性和选择性,因此从产品结构和收率可以判断平衡剂的状态。为了控制平衡剂的性能在最佳范围,使产品结构最优,装置经济效益最高,一方面要根据原料性质优选催化剂,另一方面要控制好一、二段烧焦比,采取适当的工艺条件以发挥催化剂的最大作用,而最常用的调整手段是根据催化剂的性能置换平衡剂,以控制平衡剂的重金属污染水平,见图1。
不同催化剂品种其抗磨损性能,重油裂解、抗重金属污染能力和再生性能各有不同。虽然,装置在催化剂选型上每年进行更新换代,积极进行催化剂的筛选,但由于不同时期产品市场对产品的需求都有不同,因而对催化剂选型主要是针对
收稿日期:2000-01-24;修改稿收到日期:2000-04-16。
作者简介:工程师,1988年毕业于石油大学炼制系,现在该厂从事催化裂化装置工艺管理工作。
炼 油 设 计
2000年6月 PETRO LE UM REFI NERY E NGI NEERI NG 第30卷第6期
提高渣油掺炼率和产品需求的,而对催化剂的耐磨性能、活性保留度和抗重金属污染性能未引起足够重视。从装置多年的实践经验来看,国产剂比进口剂其抗磨损性能和活性保留度相对要差,催化剂自然跑损单耗稍大;在抗重金属污染方面,国产剂与进口剂相当
。
图1 控制平衡剂性能的途径
1.2 装置工艺操作条件
1.2.1 装置开停工和催化剂流化状况
装置在开停工期间,由于操作调节幅度大,在
开工加催化剂封旋风分离器(旋分器)料腿和停工卸催化剂过程中,旋分器工况不在设计的最佳范围内,造成催化剂大量跑损,一般开停工约损失催化剂20t 。因此在开工时要加快大型加料速度,迅速封住旋分器料腿。在停工时要卸净系统中的平衡剂,努力减少跑损消耗。
装置反应再生系统的催化剂流化波动或中断都会使旋分器工作不正常,影响旋分器的分离效率,从而导致催化剂跑损增加。装置自1991年开工以来多次流化失常,且曾经一个周期流化失常频繁,影响了装置的平稳生产。表1为开工第一到第七周期流化失常统计数据。
表1 流化失常统计数据
失常原因失常次数所占比例,%
筛分组成失调2880设备故障
514.3再生立管松动、流化风量不当
2
5.7
可见筛分组成失调是主要的,因此要密切注意其变化。装置每月由质检部门定期分析三次筛分组成,每星期由厂研究院分析催化剂性质如比表面积、孔容、重金属含量、活性指数等,并定期送G race 公司分析比较。一旦发现筛分组成失调,就
要查明原因,采取加大新鲜剂补充量、适当补充细粉较多的催化剂或补充正常流化状况下卸出的平衡剂等手段来调节平衡剂筛分组成到正常范围内。从多年的操作来看,装置的平衡剂平均粒径
控制在小于80μm ,流化就不成问题。1.2.2 再生器和反应器的正常操作条件
平衡剂的比表面积和孔容受新鲜剂物性影响,一般新鲜剂在使用一段时间后,比表面积下降较快,孔容也有所变化。高再生温度主要是破坏颗粒外表面的微孔,内部孔结构变化不大,比表面积和孔容同时减少,孔径变化不大;而蒸汽作用主要是破坏颗粒内部的孔结构,孔径增大,比表面积降低,孔容改变不大。在实际使用过程中,高温和蒸汽常同时作用,因此比表面积和孔容都会减少。装置再生工艺为两段同轴再生工艺,第一再生器为低温贫氧再生,再生器密相温度控制不大于690℃,蒸汽分压约在35kPa ,烧去焦中约60%~75%的碳、约90%的氢,从而减轻了蒸汽存在下催化剂的高温失活;第二再生器为高温富氧再生,密相温度控制不大于730℃,烟气中氧含量在3%~6%,蒸汽分压约在3kPa ,避免了蒸汽减活,从而减轻了催化剂热崩溃,为提高烧焦负荷和渣油掺炼量,降低再生剂碳含量提供了有利条件。在实际操作中为延长催化剂使用寿命,减轻催化剂的水热失活,必须控制好一、二段烧焦比例,使一、二段再生温度尽量不超工艺要求的上限。
另外再生器的主风量应控制在一定的范围内,再生器压力在开烟气轮机时尽量在设计的高压下运行,以保证旋分器的分离效率在较佳水平。1.3 原料性质
由于装置原料来源多、品种杂,以及性质多
变,因此也较大地影响产品分布和催化剂消耗。从1995年6月加工平台蜡油的情况(见表2)看,加工平台蜡油使常压渣油掺炼率、汽油收率下降,轻柴油收率和油浆产率上升,汽油脱硫醇困难(博士试验难通过),油浆系统易结焦,分馏塔底温度急剧升高。这主要是适应重油裂解的超稳催化剂活性较低,抗碱性氮的能力较弱所致。虽然在此期间加大了催化剂置换速率,增加了卸剂消耗,但仍不能保证平衡剂的活性在60以上,这样使转化率下降,胶质、沥青质裂化程度减弱,富集在油浆中,降低了油浆系统换热效果,使分馏塔底温度升高。因此在加工平台蜡油或焦化蜡油时,需要选用基质活性高,稀土含量高的催化剂,以减少氮和硫的中毒,同时提高渣油裂化能力。
减压渣油的残炭、硫含量和重金属含量比常压渣油高。特别是最近几年进口了一部分美国、
—
34—第6期 周建文.重油催化裂化装置催化剂损耗因素与经济效益
日本及东南亚的蜡油和常压重油,其硫、重金属和钠含量比管输油高很多,最高时镍加钒含量大于50μg/g,钠含量高达20μg/g,在装置上直接加工时,造成操作紊乱,产品分布变差。为维持重油的裂化能力和平衡剂活性、选择性,使催化剂消耗增加很多。如按原料中的重金属在催化剂上的沉积量为50%计,则原料中的镍加钒含量由5μg/g增加到10μg/g,平衡剂上重金属含量每天会上升约50μg/g(处理量按3000t/d计),要维持平衡剂上重金属相同的污染水平,则要增加催化剂消耗约0.3kg/t,即加工每吨原料成本增加约6RM B。因此要优化原料配给,使原料轻重搭配,保证原料性质稳定,同时加强常减压蒸馏装置的脱盐和控制进口蜡油、重油的物化性质不要大差,尽量使进入装置加工的原料中镍加钒含量不大于10μg/g,钠含量不大于2μg/g,以降低催化剂的消耗。
表2 炼平台蜡油操作情况
项 目未炼平台蜡油(1995—05)
炼平台蜡油
(1995—06)
混合原料性质
密度/kg?m-3903.9900.4 残炭,% 2.0 2.4 总硫,%0.360.57 碱性氮/μg.g-11530常压渣油掺炼率,%61.535产品质量收率,%
干气 3.81 3.95 液化石油气16.6114.10 汽油47.3945.63 柴油18.0421.65 油浆7.258.14
催化剂Octacat2D+
ZC M27
Octacat2D+
ZC M27
平衡剂性质
比表面积/m2?g-1125120
活性指数42.3139.10
重金属含量/μg?g-1
Ni49004300
V10001500
催化剂单耗/kg?t-1 1.26 1.65
精制汽油硫醇含量/μg?g-1<10>10
1.4 产品构成及其质量要求
产品构成应以市场为导向,因此生产方案须经常调整,这就对催化剂的消耗产生影响。在市场需要多产液化石油气和丙烯时,需增加催化剂消耗和辛烷值助剂用量以提高系统平衡剂的活性,增强裂化强度;在增产柴油时,需要缓和的反应条件,因而催化剂消耗可适当降低。
1.5 旋分器工况
旋分器工况的好坏直接影响系统平衡剂细粉的回收,从而影响平衡剂的筛分组成和催化剂的流化。因此应加强平衡剂分析检测和第三级旋分器回收废剂的监控,以随时判断旋分器的工况。另外根据经验和经济测算,旋分器的效率随着时间的推移会逐渐下降,因此旋分器每隔5年左右需更新,以保证装置长周期平稳运行。
2 催化剂消耗大小对装置经济效益的影响因影响全装置利润的因素众多,且互相制约,为此需利用量本利分析法进行剖析。表3为1996年装置各月份的原料和产品构成、催化剂性质和消耗、成本和利润。图2为1996年新鲜剂单耗和利润趋势的对应图。
图2 1996年新鲜剂单耗与利润趋势对应图
从表3和图2中可看出:
(1)吨油总成本变化趋势不大,最大与最小差值为86.1RM B,吨油产品收入最大与最小差值为73.4RM B,利润差值达122.6RM B,说明在降低成本提高产品收入方面,有潜力可挖。
(2)催化剂消耗与吨油利润的变化趋势(除11月份检修外)相一致,而且催化剂的变化在先,即催化剂消耗变化后下个月利润随之也相应变化,说明催化剂消耗对利润的影响起了决定作用。
(3)总成本构成中原料成本占90%以上,催化剂成本占总成本分率很小,因此优化原料配给,降低原料成本是提高利润的一大途径。1996年2~3月份催化剂的补充量和置换量较少,而原料为镍钒含量高、性质很差的阿曼油,致使催化剂的选择性下降,产品分布变差,到5月份渣油掺炼率降为24.53%,汽油收率降到39.96%,达最低点。自5月份后增加了催化剂消耗,渣油掺炼率逐月上升,吨油成本反而下降或维持在低水平。说明
—
4
4
—炼 油 设 计 2000年第30卷
提高催化剂置换速率,大大改善了平衡剂性质,重金属含量大幅下降,比表面积、活性有了提高,催化剂的跑损量也有所下降,因此催化剂的活性和选择性趋向合理。10月份与不卸剂的5月份相比,液体产品收率(液化石油气+丙烯+汽油+柴油)增加了2.42%,渣油掺炼率提高到42.81%,总成本降低了67.40RM B/t,利润增加122.6 RM B/t,而催化剂消耗只由4月份的0.948kg/t 提高到10月份的1.306kg/t左右,经济效益巨大,因此牺牲一些催化剂以提高液体产品收率是值得的。
表3 1996年各月份的生产状况分析
月 份123456789101112原料构成,%
蜡油42.3554.8350.0357.1175.4772.3461.9068.7464.4257.1944.4664.71 常压渣油57.6545.1749.9730.3242.00 5.03 减压渣油12.5724.5327.6638.1031.2635.5842.8113.5430.26产品构成,%
干气 5.32 5.22 5.0 6.097.597.05 6.87 5.71 6.997.47 6.69 6.09 液化石油气11.7111.0710.1210.5010.1312.1511.6810.099.9911.2312.0510.87 丙烯 4.38 4.04 4.06 3.81 3.85 4.39 4.04 3.84 3.94 4.35 3.63 3.91 汽油45.3344.2342.8141.9639.9642.6944.0144.4443.8546.0743.4743.09 柴油17.9120.1522.6320.8521.0916.5218.1020.9019.8615.8017.0720.81 油浆7.507.958.099.129.269.137.427.227.627.309.267.55经济核算/RM B?t-1
总成本1082.71105.51095.61078.51086.81088.01039.31064.21041.91019.41061.61055.6 收入1393.41383.81374.01348.71320.01359.51369.31368.31354.21375.21354.01366.7 利润310.7278.3278.4270.2233.2271.5330.0304.1312.3355.8292.4311.1催化剂消耗/kg?t-1
新剂单耗0.980 1.137 1.0140.948 1.220 1.942 1.422 1.373 1.041 1.306 2.124 1.135 跑损剂耗0.649 1.1370.8540.799 1.220 1.310 1.1500.5320.5700.6000.6330.558平衡剂性质3
活性626459546065616463585756 镍含量/μg?g-1420044004800590060004800430042004200540064006600 钒含量/μg?g-1210021002000180020001400110011001100140016001600 31996年催化剂为Octacat2D,O+/XP280L,Reduxion250L和Ultima447;平衡剂性质数据由G race公司分析所得。
适当增加催化剂消耗可带来如下好处:
①可降低平衡剂上的重金属含量,改善平衡剂的活性和选择性,从而适应原料性质的变化。
②在保持再生器烧焦负荷的情况下,能改善产品分布,提高轻油和液体产品收率。
③提高渣油掺炼率,改变原料构成,降低原料成本,从而抵消催化剂成本的增加,单位加工总成本反而下降。
当然催化剂的置换量不能太大,当超过1.4 kg/t时,每增加0.1kg/t,就要增加加工费用约2.3 RM B/t左右,而液体产品收率提高较小,此时综合经济效益反而下降,因此要控制好适当的催化剂置换速率。经过多年的摸索得出,最佳催化剂消耗在1.1~1.5kg/t,催化剂消耗差值(新鲜剂单耗-跑损单耗)在0.5kg/t较合适,对国产催化剂可适当增加些,当然对不同的催化剂,应根据其老化程度、使用寿命及其价格进行平衡,以达到最大效益。
3 结论
(1)对掺炼重油的重油催化裂化装置,催化剂的筛分组成、抗磨损性能、水热稳定性和装置操作条件、旋分器运行工况影响自然跑损单耗;催化剂的抗重金属污染能力、活性保留度和原料的金属含量影响卸剂单耗。为减少催化剂消耗,应注意如下几点:
①在催化剂选型上,除要求能多掺炼重油、生焦率低和满足产品的需求外,对催化剂的抗重金属污染能力和老化寿命应予足够重视。
②提高操作平稳率,避免流化波动,控制适当
—
5
4
—
第6期 周建文.重油催化裂化装置催化剂损耗因素与经济效益
的再生温度、再生器压力、主风量,使旋分器工况处在最佳分离效率内。
③优化原料配给,保证原料性质稳定,严格控制原料的重金属镍加钒含量不大于10μg/g,钠含量不大于2μg/g。
(2)根据原料和平衡剂的分析数据,应用经济分析手段得出,我厂重油催化裂化装置催化剂单耗控制在1.1~1.5kg/t较合适。
(编辑 杨金鹏)
CATALYST LOSS AN D ECONOMIC BENEFITS OF RFCCU
Zhou Jianwen
Refinery o f Jinling Petrochemical Company(Nanjing,Jiangsu210033)
Abstract In fluences of kinds and characteristics of catalyst,operating conditions,feedstock characteristics, product slate and quality as well as the efficiency of cyclone on economic benefits were analyzed.Measures reducing catalyst loss and appropriate control range for catalyst loss were proposed.
K eyw ords residue,FCC U,catalyst,single consum ption,in fluence factor,economic benefits
国外动态
MT BE装置改造的前景
环境调查表明,MT BE已污染了美国49个州的饮用
水,作为汽油添加剂的MT BE的前途正面临着威胁。加利福尼亚州空气资源局(C AR B)已于1999年12月签署法令,该州政府将执行Davis法案,要求炼油厂于2000年12月31日后中止使用MT BE。
炼油厂也面临提高汽油辛烷值、MT BE装置及其原料出路的挑战。最近,美国凯洛格?布朗2路特(K BR)和芬兰F ortum油气公司联合,以及意大利斯纳姆帕洛盖蒂公司分别开发了利用现有的MT BE装置改产异辛烷烷基化油的新工艺。
该工艺由二个独立的反应步骤组成(见附图):第一步异丁烯二聚为异辛烯馏分(或部分醚化为MT BE),第二步将异辛烯加氢为异辛烷。该技术可使炼油厂将现有闲置的MT BE装置转换成生产异辛烷的装置,异辛烷是既可替代汽油中MT BE用于提高辛烷值,改造费用又比较低。将现有MT BE装置改产异辛烷烷基化油,使用异丁烯高选择性二聚工艺,无需HF酸或硫酸烷基化装置。
该装置产品为高质量异辛烷,有很高的辛烷值和适宜的蒸气压,异丁烯转化率高达99%;循环量极少,投资费用低;无废弃物流处理的环境问题。
K BR和F ortum油气公司开发的这种工艺称为Nex oc2 tane,
该工艺成为F ortum油气公司子公司纳斯特工程公司纳斯特醚化技术———Nexethers和Nextame的分支,已在芬兰的装置上得到验证。
斯纳姆帕洛盖蒂公司开发的工艺称为SP2Is oether。反应过程采用该公司的水冷法管式反应器(WCTR)。异丁烯二聚为高放热反应,反应温度难以控制,其结果会导致产品低聚。WCTR的优点是催化剂床层一旦产生热量即可除去,低聚反应得以控制,使二聚具有高的选择性,从而提高产品质量。WCTR的另一优点是可用于一次通过操作,减少了产生低聚的可能。该公司已进行过几次试验。在美国生产了2000t异辛烷,在意大利与埃尼公司合作也生产了几千吨异辛烷。
(钱伯章摘编自ECN2000,72(1894):39;72(1893),35)
—
6
4
—炼 油 设 计 2000年第30卷
重油催化裂化
对重油催化裂化分馏塔结盐原因分析及对策 王春海 内容摘要 分析了重油催化裂化装置发生分馏塔结盐现象的原因,并提出了相应的对策。分馏塔结盐是由于催化原料中的有机、无机氯化物和氮化物在提升管反应器中发生反应生成HCl和NH3 ,二者溶于水形成NH4Cl溶液所致。可采取尽可能降低催化原料中的含盐量、对分馏塔进行在线水洗、利用塔顶循环油脱水技术等措施,预防和应对分馏塔结盐现象的发生。 关键词: 重油催化裂化分馏塔结盐氯化铵水洗循环油脱水
目前,催化裂化装置( FCCU)普遍通过掺炼渣油及焦化蜡油进行挖潜增效,但由于渣油中的氯含量和焦化蜡油中的氮含量均较高,势必导致FCCU 分馏塔发生严重的结盐现象。另外,近年来国内市场柴油消费量迅速增长,尽管其生产量增长也很快,但仍不能满足市场的需求。因此许多FCCU 采用降低分馏塔塔顶温度(以下简称顶温)的操作来增产柴油,但顶温低致使分馏塔顶部水蒸气凝结成水,水与氨(NH3)和盐酸(HCl)一起形成氯化铵(NH4Cl)溶液,从而加速分馏塔结盐。随着分馏塔内盐层的加厚,沉积在塔盘上的盐层会影响传质传热效果,致使顶温失控而造成冲塔;沉积在降液管底部的盐层致使降液管底部高度缩短,塔内阻力增加,最终导致淹塔.。可见,如何避免和应对分馏塔结盐现象的发生,是FCCU 急需解决的生产难题。 一、分馏塔结盐原因及现象分析 (一)原因 随着FCCU所用原料的重质化,其中的氯和氮含量增高。在高温临氢催化裂化的反应条件下,有机、无机氯化物和氮化物在提升管反应器中发生反应生成HCl和NH3 ,其反应机理可用下式表示: : 催化裂化反应生成的气体产物将HCl和NH3从提升管反应器中带入分馏塔,在分馏塔内NH3 和HCl与混有少量蒸汽的油气在上升过程中温度逐渐降低,当温度达到此环境下水蒸气的露点时,就会有冷凝水产生,这时NH3和HCl溶于水形成NH4Cl溶液。NH4Cl溶液沸点远高于水的沸点,其随塔内回流液体在下流过程中逐渐提浓,当盐的浓度超过其在此温度下的饱和浓度时,就会结盐析出,沉积在塔盘及降液管底部。 (二)现象 1.由于塔顶部冷凝水的存在,形成塔内水相内回流 ,致使塔顶温度难以控制 ,顶部循环泵易抽空,顶部循环回流携带水。 2.由于沉积在塔盘上的盐层影响传热效果,在中段回流量、顶部循环回流量发生变化时,塔内中部、顶部温度变化缓慢且严重偏离正常值。 3.由于沉积在塔盘上的盐层影响传质效果,导致汽油、轻柴油馏程发生重叠,轻柴油凝
重油催化裂化反应-再生系统工艺设计
毕业设计 题目重油催化裂化反应-再生系统工艺设计系(部)化学工程系 专业石油化工生产技术 指导教师 学生 时间2013/5/19 目录
前言 第一节设计原则 第二节装置状况 第三节工艺流程概述 3.1反应部分工艺流程 3.2再生部分工艺流程 第四节设计基础数据 4.1原料油物性 4.2催化剂的物化性质 4.3助剂及相关功用 第五节反应再生系统工艺计算 5.1再生器物料平衡计算 5.2再生器热平衡 5.3反应器的热平衡和物料平衡 5.4再生器主要附件 5.5提升管主要附件 5.6两器压力平衡(反应器和再生器) 5.7主要设备计算结果汇总 第六节主要设备选择 第七节反应部分工艺技术方案及特点 第八节再生部分工艺技术方案及特点
第九节能耗分析和节能措施 第十节环境保护及职业安全卫生 10.1污染源及治理措施 10.2安全措施 总结……… 参考文献…….
前言 催化裂化是一项重要的炼油工艺。其技术复杂程度位居各类炼油工艺首位,但因其投资省,效益好,因而在炼油工业中占有举足轻重的地位。催化裂化过程是原料在催化剂存在时,在470~530度和0.1~0.3mpa的条件下,发生裂解等一系列的化学反应,转化为气体,汽油,柴油等轻质产品和焦炭的工艺过程。其原料一般是重质馏分油,如减压馏分油和焦化馏分油等,随着催化裂化技术和催化剂的不断发展,进一步扩大原料来源,部分或全部渣油也可以作为催化裂化的原料。 近年来,我国汽车工业飞速发展,2003年全国生产汽车444万辆,截止2003底.全国汽车保有量达到2420辆。专家预测2020年汽车保有量将超过1亿辆(此外还有1亿辆摩托车)。在调整车型结构提高燃油经济性的前提下,汽油需求量超过7400万吨、柴油需求量将超过1亿吨。我过约80%的商品汽油和30%的商品柴油来自催化裂化,使催化裂化成为我国应输燃料最重要的生产装置。 从以上两个方面可见,催化裂化在实际生产中有很重要的意义,研究其工艺很有价值。在原油价格居高不下,炼化企业的效益日益恶化的背景下,使用劣质原料来获得优质质,是炼厂的必然选择。因此,要不断开发催化裂化新技术、新工艺,以增加产品收率、提高产品质量,这也是炼化企业在21世纪可持续发展的重大战略措施。 第一节设计原则 1 工程设计采用国内开发的先进可靠的工艺技术,成熟可靠的新设备、新材料等,以达到装置技术先 进,经济合理。 2 除少量关键仪表及特殊设备需引进外,其它设备及仪表立足国内。 3 尽量采用“清洁工艺”减少环境污染。严格遵循环保、安全、卫生有关法规,确保装置的安全生产。 4 充分吸收国内生产装置长期实践积累的有利于长周期运转,降低能耗以及简化操作等方面的经验, 确保装置投产后高水平,安、稳、长、满、优生产。 第二节装置概况 1采用集散型控制系统(DCS),提高自动控制水平。 2采用HSE(health, safety, environment)管理体系,以便减少可能引起的人员伤害、财产损失和环境污染。 3 原料油 设计采用的原料油为胜利减压流出油。
关于编制重油催化热裂解制烯烃项目可行性研究报告编制说明
重油催化热裂解制烯烃项目可行性研究报告 编制单位:北京中投信德国际信息咨询有限公司编制时间:https://www.360docs.net/doc/d19802316.html, 高级工程师:高建
关于编制重油催化热裂解制烯烃项目可行 性研究报告编制说明 (模版型) 【立项 批地 融资 招商】 核心提示: 1、本报告为模板形式,客户下载后,可根据报告内容说明,自行修改,补充上自己项目的数据内容,即可完成属于自己,高水准的一份可研报告,从此写报告不在求人。 2、客户可联系我公司,协助编写完成可研报告,可行性研究报告大纲(具体可跟据客户要求进行调整) 编制单位:北京中投信德国际信息咨询有限公司 专 业 撰写节能评估报告资金申请报告项目建议书 商业计划书可行性研究报告
目录 第一章总论 (1) 1.1项目概要 (1) 1.1.1项目名称 (1) 1.1.2项目建设单位 (1) 1.1.3项目建设性质 (1) 1.1.4项目建设地点 (1) 1.1.5项目主管部门 (1) 1.1.6项目投资规模 (2) 1.1.7项目建设规模 (2) 1.1.8项目资金来源 (3) 1.1.9项目建设期限 (3) 1.2项目建设单位介绍 (3) 1.3编制依据 (3) 1.4编制原则 (4) 1.5研究范围 (5) 1.6主要经济技术指标 (5) 1.7综合评价 (6) 第二章项目背景及必要性可行性分析 (7) 2.1项目提出背景 (7) 2.2本次建设项目发起缘由 (7) 2.3项目建设必要性分析 (7) 2.3.1促进我国重油催化热裂解制烯烃产业快速发展的需要 (8) 2.3.2加快当地高新技术产业发展的重要举措 (8) 2.3.3满足我国的工业发展需求的需要 (8) 2.3.4符合现行产业政策及清洁生产要求 (8) 2.3.5提升企业竞争力水平,有助于企业长远战略发展的需要 (9) 2.3.6增加就业带动相关产业链发展的需要 (9) 2.3.7促进项目建设地经济发展进程的的需要 (10) 2.4项目可行性分析 (10) 2.4.1政策可行性 (10) 2.4.2市场可行性 (10) 2.4.3技术可行性 (11) 2.4.4管理可行性 (11) 2.4.5财务可行性 (12) 2.5重油催化热裂解制烯烃项目发展概况 (12)
重油催化裂化基础知识
重油催化裂化基础知识 广州石化总厂炼油厂重油催化裂化车间编 一九八八年十二月
第一章概述 第一节催化裂化在炼油工业生产中的作用 催化裂化是炼油工业中使重质原料变成有价值产品的重要加工方法之一。它不仅能将廉价的重质原料变成高价、优质、市场需要的产品,而且现代化的催化裂化装置具有结构简单,原料广泛(从瓦斯油到常压重油),运转周期长、操作灵活(可按多产汽油、多产柴油,多产气体等多种生产方法操作),催化剂多种多样,(可按原料性质和产品需要选择合适的催化剂),操作简便和操作费用低等优点,因此,它在炼油工业中得到广泛的应用。 第二节催化裂化生产发展概况 早在1936年美国纽约美孚真空油公司(、)正式建立了工业规模的固定床催化裂化装置。由于所产汽油的产率与辛烷值均比热裂化高得多,因而一开始就受到人们的重视,并促进了汽车工业发展。如图所示,片状催化剂放在反应器内不动,反应和再生过程交替地在同一设备中进行、属于间歇式操作,为了使整个装置能连续生产,就需要用几个反应器轮流地进行反应和再生,而且再生时放出大量热量还要有复杂的取热设施。由于固定床催化裂化的设备结构复杂,钢材用量多、生产连续性差、产品收率与性质不稳定,后为移动床和流化床催化裂化所代替。 第一套移动床催化裂化装置和第一套流化床催化裂化(简称装置都是1942年在美国投产的。
固定床反应器 移动床催化裂化的优点是使反应连续化。它们的反应和再生过程分别在不同的两个设备中进行,催化裂化在反应器和再生器之间循环流动,实现了生产连续化。它使用直径约为3毫米的小球型催化剂。起初是用机械提升的方法在两器间运送催化剂,后来改为空气提升, 生产能力较固定床大为提高、 空气
国内外催化裂化催化剂技术的新进展
国内外催化裂化催化剂技术的新进展一、催化裂化催化剂发展 21世纪以来,随着人们生活水平的不断发展,在大量使用石油产品的同时,其环保意识也在不断地增强,环保立法也不断完善,继而推动了清洁燃料的生产。随着对轻质油品特别是对汽油需求量的增加,催化裂化无论是加工能力、装置规模,还是工艺技术均以较高的速度发展起来,其中催化裂化催化剂在催化裂化中的使用决定了催化裂化装置的生产水平。 催化剂是一种能影响化学反应速度,但其本身并不因化学反应的结果而消耗,也不会改变反应的最终热力学平衡位置的物质。在工业催化裂化装置中,催化剂不仅对处理能力、产品分布和产品质量起着主要影响,而且对生产成本也有着重要影响。催化剂的发展可以促进催化裂化工艺技术的发展,如分子筛催化剂的出现促进了催化裂化工艺的重大变革,提升管催化裂化工艺就是在这种情况下开发成功的。 最早的催化剂取自天然白土如高岭土等。全合成硅酸铝催化剂由硅酸钠、硅酸铝、氢氧化镁等原料组成,由于无晶体结构,因此也称 为无定形硅酸铝催化剂。较早使用的催化剂中Al 2O 3 含量为10%~13%, 称为低铝硅酸铝催化剂。后期又出现了Al 2O 3 含量为24%~26%的高铝 硅酸铝催化剂,以满足市场要求。半合成硅酸铝催化剂结合了全合成硅酸铝催化剂和天然白土催化剂的优点,其中的合成硅酸铝成分,改进了催化剂的化学选择性,天然成分改善了催化剂的不稳定性,提高了催化剂的抗老化和抗失活能力,同时还降低了生产成本。分子筛裂化催化剂的出现,带来了催化裂化的一次飞跃,这种结晶硅酸铝,比无定型硅酸铝有高的多的活性、更好的选择性,因此逐步取代了无定形硅酸铝催化剂。目前使用的分子筛主要是Y型分子筛,其中又分为REY、REHY、HY、USY等类型,早期的分子筛催化剂分子筛含量约8%~10%,随着催化剂工艺的发展,催化剂中的分子筛含量逐步上升。 二、国内外催化裂化技术的新进展 1、国内催化剂技术进展
重油催化裂化装置安全基本常识
重油催化裂化装置安全基本常识 1.应急电话:火警:119;急救:120。 2.集团公司安全生产方针:安全第一、预防为主、全员动手、 综合治理。 3.三级安全教育:厂级安全教育、车间级安全教育、班组安 全教育。 4.三违:违章作业、违章指挥、违反劳动纪律。 5.三不伤害:不伤害自己、不伤害他人、不被他人伤害。 6.三不用火:没有经批准的用火作业许可证不用火、用火监 护人不在现场不用火、防火措施不落实不用火。 7.四不放过:事故原因分析不清不放过、事故责任者不受处 理不放过、事故责任者和群众没有受到教育不放过、防范措施不落实不放过。 8.三同时:一切新建、改建、扩建的工程项目,必须做到主 体工程与安全、环保、卫生技术措施和设施同时设计、同时施工、同时投用。
9.消防三懂、三会:懂火灾危险性、懂预防措施、懂扑救方 法;会报警、会使用灭火器材、会扑救初起火灾。 10.四全监督管理原则:全员、全过程、全方位、全天侯。 11.安全气分析: 1)可燃气体浓度:当爆炸下限大于4.0%时,指标为小于 0.5%;当爆炸下限小于4.0%时,指标为小于0.2%。 2)氧含量:19.5%~23.5%。 3)有毒有害物质不超过国家规定的“空气中有毒物质最 高容许浓度”的指标。 注:进入设备作业应保证以上三项同时合格,取样要有代表性、全面性。 12.生产装置、罐区的防火间距: 1)液态烃储罐、可燃气体储罐,防火间距为22.5米。(设 备边缘起)。 2)其它各类可燃气体储罐,防火间距为15米。 3)含可燃液体的敞口设备,如水池、隔油池等,防火间 距为22.5米。
13.石化集团公司HSE目标是:追求最大限度地不发生事故、 不损害人身健康、不破坏环境,创国际一流的HSE业绩。 14.济南分公司HSE方针:安全第一,预防为主;全员动手, 综合治理。 济南分公司HSE目标:层层落实HSE责任制,加大隐患治理力度,狠抓“三基”工作,严格事故责任追究,杜绝重大事故,减少人员伤亡和一般事故,争创HSE新业绩。15.每个职工应具备的HSE素质和能力: 1)对本职工作认真、负责,遵章守纪,有高度的责任感 和事业心; 2)在异常情况下,处置果断,有较强的生产处理和事故 应变能力; 3)业务精通、操作熟练,能正确分析解决生产操作和工 艺设备问题; 4)有较强的安全、环境与健康意识,能自觉做好HSE工 作; 5)能正确使用消防气防、救护器材,有较强的自救互救
石油化工重油催化裂化工艺技术
石油化工重油催化裂化工艺技术 石油化工行业的稳定发展,对于各类化工产品的稳定出产,以及社会经济的稳定发展产生了较大的影响。因此在实际发展中关于石油化工行业发展中的各类工艺技术发展现状,也引起了研究人员的重视。其中石油化工重油催化裂化工艺技术,则为主要的关注点之一。文章针对当前石油化工重油催化裂化工艺技术,进行简要的分析研究。 标签:重油催化裂化;催化剂;生产装置;工艺技术 重油催化裂化在石油化工行业的发展中,占据了较大的比重。良好的重油催化裂化对于液化石油气,汽油,柴油的生产质量提升,发挥了重要的作用。因此在实际发展中如何有效的提升重油的催化裂化质量,并且提升各类生产产品的生产稳定性,成为当前石油化工行业发展中主要面临的问题。笔者针对当前石油化工重油催化裂化工艺技术,进行简要的剖析研究,以盼能为我国石油化工行业发展中重油催化裂化技术的发展提供参考。 1 重油催化裂化工艺技术 重油催化裂化为石油化工行业发展中,重要的工艺技术之一。其工艺技术在实际应用中,通过催化裂化重油生产了高辛烷值汽油馏分,轻质柴油等其他化工行业发展中的气体需求材料。具体在工艺技术应用的过程中,其在工艺操作中对重油加入一定量的催化剂,使得其在高温高压的状态下产生裂化反应,最终生产了相应的产物。该类反应在持续中反应深度较高,但生焦率及原料损失较大,并且后期的产物需进行深冷分离。因此关于重油催化裂化工艺技术的创新和提升,也为行业研究人员长期研究的课题。 2 当前重油催化裂化工艺技术的发展现状 分析当前我国石油化工行业在发展中,关于重油催化裂化工艺技术,宏观分析整体的发展态势较为稳定。但从具体实施的过程分析,我国重油催化裂化工艺技术的发展现状,还存在较大的提升空间。分析当前重油催化裂化工艺技术的发展现状,实际发展中主要存在的问题为:工艺催化剂生产质量低、工艺运行装置综合效率低、工艺自动化水平低。 2.1 工艺催化剂生产质量低 当前我国重油催化裂化工艺技术在发展中,工艺应用催化剂的生产质量低,为主要存在的问题之一。工艺应用催化剂的生产质量较低,造成工艺技术的发展存在先天不足。分析当前在关于催化剂的生产发展现状,主要存在的问题为:催化剂生产成本高、催化剂保存技术不完善,催化剂精细程度较低等现象。 2.2 工艺运行装置综合效率低
重油催化裂解生产烯烃技术
——重油催化裂解制烯烃技术评介 (提要) 前言——石油与重油的深度加工利用问题 一、重油加工利用技术进展 二、重油催化裂解制烯烃技术综合评介 1、技术开发背景 2、技术特点 (1)CPP技术 (2)HCC技术 2、技术进展情况 (1)工业化进展 (2)工试结果 3、技术经济与社会效益分析 (1)技术经济分析 (2)社会效益分析 三、应用前景与发展建议 1、应用前景 (1)对石化工业发展的意义 (2)对中小炼油企业发展的意义 2、发展建议
重油催化裂解制烯烃技术评介 前言—— 石油及其深度加工利用问题,一直是炼油和石化工业发展的重大课题 ?石油逐渐得到人类社会的重视和利用——现代石油工业从 1859年世界上真正具有工业生产意义的第一口工业石油井 ——美国埃德温〃德雷克算起,还不足150年的历史。石 油在开初仅用来提炼灯油,其余的轻、重组份(汽油和重 油)都被排弃。十九世纪八十年代电灯的发明,使灯油市 场也受到打击,但是当十九世纪末福特发明汽车后使汽油 得到利用,随后,重油等其它石油炼制产品也逐渐得到了 重视和利用。 ?石油成为世界经济的发动机——二十世纪的两次世界大 战,使石油成为世界经济的发动机和世界工业发展的润滑 剂与促进剂;以石油为龙头所牵动工业经济的是一条不断 延长的产业链—石油工业带动了整个工业的发展。例如, 廉价的石油剌激了以内燃机为动力的汽车、飞机等新兴工 业产业的发展, 而这些产业的发展又带动了钢铁、冶金、 橡胶、玻璃等工业的发展。 ?石油开创了人类社会的新文明——石油工业的发展促进了 以石油为原料的化学工业的发展,产生了新型的石化工业、
合成材料工业、化肥工业┉等等。这不仅使现代石化产品渗透到人类社会和生活的各个角落,也促进了农业生产的发展,大幅度提高了粮食产量,从而改善和丰富人类的生活。百年来的世界经济发展历史表明:世界经济因石油的发展而迅速发展,也因石油的短缺而放慢脚步。因此,经济学界有一种观点:二十世纪是石油世纪。石油开创了人类社会的新文明——石油文明,使世界上一些发达国家的生活发生了翻天覆地的变化,普遍出现了 "三高"(高工资、高福利、高消费)的局面,家庭劳动和社会服务业普遍实现了电气化,各种家用电器急剧增加,跨地域和跨国家的旅游文化越来越普及,小汽车已成为普通百姓的代步交通工具。人类在二十世纪所创造的史无前例的文明进步,无不与石油文明有关。 ?石油对世界经济的发展产生着巨大影响——据世界经济合 作暨发展组织(WECD)的一个量化估价(较为权威):大约世界原油价格每桶上涨10美元,将会推动通货膨胀上升0.5%, 经济增长放慢0.25% 。 ?石油的优良性质和低廉价格促进了它的深加工利用——石 油所以对世界经济发展有如此巨大作用,主要在于石油具有“物美价廉”的优势——首先,石油的热值高是煤的两倍,而且石油的基本组份烃类具有极高的开发利用价值; 其次,石油是液体,易于储运管理;而特别值得一提的是
石油化工催化裂化装置工艺流程图.docx
炼油生产安全技术一催化裂化的装置简介类型及工艺流程 催化裂化技术的发展密切依赖于催化剂的发展。有了微球催化剂,才出现了流化床催化裂化装置;分子筛催化剂的出现,才发展了提升管催化裂化。选用适宜的催化剂对于催化裂化过程的产品产率、产品质量以及经济效益具有重大影响。 催化裂化装置通常由三大部分组成,即反应?再生系统、分馏系统和吸收稳定系统。其中反应--再生系统是全装置的核心,现以高低并列式提升管催化裂化为例,对几大系统分述如下: ㈠反应--再生系统 新鲜原料(减压馏分油)经过一系列换热后与回炼油混合,进入加热炉预热到370 C左右,由原料油喷嘴以雾化状态喷入提升管反应器下部,油浆不经加热直接进入提升管,与来自再生器的高温(约650 C ~700C )催化剂接触并立即汽化,油气与雾化蒸汽及预提升蒸汽一起携带着催化剂以7米/秒~8米/秒的高线速通过提升管,经快速分离器分离后,大部分催化 剂被分出落入沉降器下部,油气携带少量催化剂经两级旋风分离器分出夹带的催化剂后进入分馏系统。 积有焦炭的待生催化剂由沉降器进入其下面的汽提段,用过热蒸气进行汽提以脱除吸附在催 化剂表面上的少量油气。待生催化剂经待生斜管、待生单动滑阀进入再生器,与来自再生器底部的空气(由主风机提供)接触形成流化床层,进行再生反应,同时放出大量燃烧热,以维持再生器足够高的床层温度(密相段温度约650 C ~68 0 C )。再生器维持0.15MPa~0?25MPa (表)的顶部压力,床层线速约0.7米/秒~1.0米/秒。再生后的催化剂经 淹流管,再生斜管及再生单动滑阀返回提升管反应器循环使用。 烧焦产生的再生烟气,经再生器稀相段进入旋风分离器,经两级旋风分离器分出携带的大部 分催化剂,烟气经集气室和双动滑阀排入烟囱。再生烟气温度很高而且含有约5%~10%CO 为了利用其热量,不少装置设有Co锅炉,利用再生烟气产生水蒸汽。对于操作压力较高的 装置,常设有烟气能量回收系统,利用再生烟气的热能和压力作功,驱动主风机以节约电 能。 ㈡分馏系统 分馏系统的作用是将反应?再生系统的产物进行分离,得到部分产品和半成品。 由反应?再生系统来的高温油气进入催化分馏塔下部,经装有挡板的脱过热段脱热后进入分 馏段,经分馏后得到富气、粗汽油、轻柴油、重柴油、回炼油和油浆。富气和粗汽油去吸收稳定系统;轻、重柴油经汽提、换热或冷却后出装置,回炼油返回反应--再生系统进 行回炼。油浆的一部分送反应再生系统回炼,另一部分经换热后循环回分馏塔。为了取走 分馏塔的过剩热量以使塔内气、液相负荷分布均匀,在塔的不同位置分别设有4个循环回流:顶循环回流,一中段回流、二中段回流和油浆循环回流。 催化裂化分馏塔底部的脱过热段装有约十块人字形挡板。由于进料是460 C以上的带有催化 剂粉末的过热油气,因此必须先把油气冷却到饱和状态并洗下夹带的粉尘以便进行分馏和避免堵塞塔盘。因此由塔底抽出的油浆经冷却后返回人字形挡板的上方与由塔底上来的油 气逆流接触,一方面使油气冷却至饱和状态,另一方面也洗下油气夹带的粉尘。 ㈢吸收--稳定系统: 从分馏塔顶油气分离器出来的富气中带有汽油组分,而粗汽油中则溶解有C3 C4甚至C2 组分。吸收--稳定系统的作用就是利用吸收和精馏的方法将富气和粗汽油分离成干气 (≤ C2)、液化气(C3、C4)和蒸汽压合格的稳定汽油。 一、装置简介 (一)装置发展及其类型
重油催化裂解技术研究进展_盖希坤
2011年第30卷第6期CHEMICAL INDUSTRY AND ENGINEERING PROGRESS ·1219· 化工进 展 重油催化裂解技术研究进展 盖希坤1,田原宇2,夏道宏1,邢仕杰2 (1中国石油大学(华东)化工学院,山东青岛 266555;2山东科技大学化工学院,山东青岛 266510)摘 要:重油催化裂解技术以增产乙烯、丙烯等低碳烯烃为主要目标,是重油轻质化的有效手段。对催化裂解技术的研究,催化剂和反应器是其核心。本文综述了重油催化裂解技术中采用的各种催化剂和反应器的研究进展,阐述了不同催化剂的适用条件和不同类型反应器的流体特性,并指出深入研究下行床反应器及开发与之匹配的催化剂将是今后开发重油催化裂解技术最具潜力的研究方向。 关键词:重油;催化裂解;催化剂;下行床;提升管 中图分类号:TE 624 文献标志码:A 文章编号:1000–6613(2011)06–1219–05 Progress of heavy oil catalytic cracking GAI Xikun1,TIAN Yuanyu2,XIA Daohong1,XING Shijie2 (1Chemical Engineering Institute,China University of Petroleum(Huadong),Qingdao 266555,Shandong,China;2Chemical Engineering Institute,Shandong University of Science and Technology, Qingdao 266510,Shandong,China) Abstract:Heavy oil catalytic cracking is an effective technology to convert heavy oil to lighter and more valuable product,including ethylene and propylene. The catalyst and reactor play an important role in the technology. In this paper,various catalysts and reactors for heavy oil catalytic cracking are summarized,and the application conditions of the catalysts and the hydrodynamic characteristics of the reactors are elaborated. Development of downer reactor and the corresponding catalyst are suggested to be the most promising research direction. Key words:heavy oil;catalytic pyrolysis;catalyst;downer reactor;riser 随着世界石油资源的日益短缺和原油重质化的加剧,重油因其在全世界的资源总量巨大,将成为21世纪的重要能源。我国的原油中重质油含量比较高,一般为60%~80%,有的甚至高达80%~100%。近年来,重质原油的开采速度加快,其产量已占全国石油年产量的1/10左右,如何将这些日益增长的重油轻质化,成为我国炼油工业的重大课题。 重油催化裂解技术是在重油催化裂化的基础上随着催化剂的改进、新型反应器的开发和工艺条件的优化而逐步发展起来的。重油催化裂化的反应温度为480~530 ℃,重油催化裂解的温度为550~650 ℃。与催化裂化技术相比,重油催化裂解技术采用更高的反应温度,重油与催化剂接触,进行深度裂解以增产乙烯、丙烯等低碳烯烃,并同时兼产轻质芳烃。传统的蒸汽热裂解温度为840 ℃左右,与传统的蒸汽热裂解技术相比,重油催化裂解技术不仅可以降低反应温度,获得更高的低碳烯烃选择性,而且提高了裂解产品分布的灵活性,是重油轻质化的有效手段。本文对重油催化裂解技术的核心部分——催化剂和反应器的研究进展进行了评述。 1 催化剂的研究进展 催化剂是影响重油催化裂解产品分布的重要 收稿日期:2010-12-02;修改稿日期:2010-12-16。 第一作者:盖希坤(1982—),男,博士研究生。E-mail gaixikun@ https://www.360docs.net/doc/d19802316.html,。联系人:田原宇,教授,主要从事能源与设备一体化研究。E-mail tianyy1008@https://www.360docs.net/doc/d19802316.html,。 DOI:10.16085/j.issn.1000-6613.2011.06.029
重油催化裂化装置长周期安全运行几点考虑
编号:SY-AQ-03170 ( 安全管理) 单位:_____________________ 审批:_____________________ 日期:_____________________ WORD文档/ A4打印/ 可编辑 重油催化裂化装置长周期安全 运行几点考虑 Considerations on long term safe operation of RFCC unit
重油催化裂化装置长周期安全运行 几点考虑 导语:进行安全管理的目的是预防、消灭事故,防止或消除事故伤害,保护劳动者的安全与健康。在安全管理的四项主要内容中,虽然都是为了达到安全管理的目的,但是对生产因素状态的控制,与安全管理目的关系更直接,显得更为突出。 2002年10月,为了提高原油深度加工能力,提高轻油收率,第二催化裂化装置历时56天进行了由蜡油催化改为重油催化的技术改造,改造后的装置掺炼重油加氢渣油比例由原来20%提高到了50%以上。现在装置原料以减压馏份油、VRDS常压渣油、VRDS 减压渣油、焦化蜡油为主。装置改造后,装置操作相应发生比较大的变化,装置设备增多,设备管理难度加大,如何保证重油催化裂化装置长周期安全运行,成为生产管理中的难点和重点。 一、要确保关键转动设备的运行平稳度 催化裂化装置大机组较多,技术含量高,有主风机、烟机、气压机、增压机等,只有保证了大机组的连续高效运行,催化裂化装置才能长周期运行,所以我们首先要在检修中提高大机组的检修深
度和检修质量,确保大机组的机械部分、仪表部分、电气部分、自控部分和附属系统设备的可靠好用。在日常生产维护中加强对大机组的检查力度,组织安装投用了s8000大型旋转机械在线状态监测与分析系统,为机组的安全运行提供了有力保障。 二、要确保关键静设备——反再系统的运行平稳度 要保证公用系统的可靠性,尽量避免公用系统故障造成装置大面积操作波动,严格按照工艺指标平稳操作,不超温不超压,操作的平稳对催化裂化设备安全运行尤为关键。另外组织技术人员加强对反再系统壁温的检测和检查,及时发现避免衬里损坏超温、低温露点腐蚀等设备隐患。 三、要确保能量回收系统的运行平稳度 催化裂化装置最大的节能点在于能量回收系统,对于关键设备烟机、锅炉给水泵、外取热器、油浆蒸汽发生器等必须要管理好。从设备选型、设备制造、现场安装、日常运行等各个环节把握好,否则烟机振动问题、锅炉给水泵频繁串轴问题、余热锅炉炉管泄漏问题、油浆蒸汽发生器管束泄漏等问题将不可避免。能量回收系统
重油催化裂化装置的结焦机理
目前,对重油催化裂化装置的结焦原因探讨很多,对结焦问题的认识还停留在经验阶段[41],尽管取得了很大的成绩,但还没有根本性的突破,主要有以下几种结焦机理。 1. 液相重组分高温缩合机理 季根忠等[42]认为催化裂化结焦可能通过以下四种假设模型: 模型一:油气结焦 模型二:油气结焦 模型三:原料油气结焦 模型四:原料油结焦 在提升管反应器中,原料中的重组分未能充分气化,而以液相形式粘附在催化剂颗粒的表面,在提升管油剂活塞流运动过程中,催化剂颗粒间相互接触传热的机会较少。粘附重组分液相的催化剂颗粒的加热,只能靠从别的催化剂颗粒上气化或者裂化产生的油气来完成,这种热量的传递是有限的。当这些催化剂离开提升管后,就会很容易粘附在沉降器器壁上形成结焦中心。因此,粘附在催化剂颗粒表面上的未气化的原料油重组分,在沉降器及汽提段温度条件下发生缩合反应,结焦遵从模型四的机理。 重油的沸程目前尚无法用实验直接测定,利用石油大学重质油国家重点实验室初步建立的模拟计算渣油沸程的方法估算,0.3Mpa、600℃及7wt%蒸汽(相对原料)条件下,大庆常压渣油的平衡气化率约为55wt%,即在此条件下,大庆常压渣油中沸点>500℃的部分(相当于减渣)约有40wt%~50wt%的气化率,未气化的液相部分在重油原料中占相当大的比例,在渣油催化裂化时,原料中的减压渣油部分有相当一部分并未气化[43]。对济南炼油厂工业提升管在不同高度取样的分析结果[44]也间接地证明了上述气化率估算的合理性。重油中的胶质和沥青质绝大部分存在于577℃以上的馏分中,而提升管中剂油混合点温度一般在560℃以下,故此类物质喷到催化剂表面时多以液态存在。另外,胶质、沥青质含极性物质较多,所含极性物质越多,则越难挥发气化,越易分解和缩合,有明显的生焦倾向。 催化裂化沉降器的结焦,主要原因是原料油中多环芳烃通过热聚合反应的结果。在催化裂化反应过程中,一部分反应产物形成高分子烃类,在操作条件下不易挥发,附着在沉降器内壁上。这种高分子烃类即为“结焦前身物”,他们在与较低温度的器壁接触时冷凝为液相,进而缩合为焦炭。根据以上机理,在沉降器温度下,原料和反应产物中的重组分一部分以液滴形式存在,其粘附性很强,它们很容易粘附催化剂颗粒。当它们碰撞到沉降器内壁上时,会粘附在沉降器内壁上,经过一段时间后缩合为焦炭。 2.
催化裂化催化剂的种类
催化裂化催化剂--渣油裂化催化剂 ORBIT系列 产品性能和技术特点简介: ORBIT-3000催化剂着重于提高目的产物中汽油和柴油的产率。在该催化剂制备过程中采取了如下技术措施:采用复合的分子筛活性组份,使该催化剂既具有优异的焦炭选择性,又具有良好的活性稳定性;在超稳分子筛生产过程中,通过改性技术处理,注重开发超稳分子筛的中孔,使其适应于重油大分子的裂化反应;在改进分子筛性能的同时,采用活性氧化铝技术对担体进行改性处理,有效地提高了担体的大分子裂化能力。 ORBIT-3300催化剂是在ORBIT-3000催化剂所具备的大分子裂化活性高、焦炭选择性好、适合重油加工的基本性能的基础上,通过改变活性组份开发成功的新型重油裂化催化剂。该剂主要适合于加工量较大但剂油比较低的重油催化裂化装置,在装置分馏稳定、气压机系统等的弹性工作范围内,不需改造即可使用。ORBIT-3300催化剂在制备过程中通过对活性组份的调整,增加了产品的抗重金属污染能力,可在原料性质较差和多变的情况下使用。 ORBIT-3600催化剂是针对加工中东进口高钒原料油和增加总液体收率的要求,在ORBIT-3300催化剂的基础上,通过优化活性组元和担体改性处理,开发成功的新型重油裂化催化剂。该剂在制备过程中为满足加工重质原料油需要,在改进分子筛性能的同时,对担体进行改性处理,增加了抗重金属污染组分,有效地提高了催化剂抗重金属(特别是钒)污染性能;添加了择型分子筛组元,可适当增加液态烃产率。 ORBIT-3600B催化剂是以抗钒催化剂ORBIT-3600为基础开发的抗钒降烯烃催化剂。工业应用结果表明该剂具有重油裂化能力强、轻质油收率高、汽油辛烷值高、降烯烃能力强等特点。 为了实现在抗钒重油裂化催化剂ORBIT-3600基础上达到降低汽油烯烃含量的目的,ORBIT-3600B催化剂具有以下特点:通过Y型分子筛的改性处理和活性组分的复配,在维持产品重油裂化活性的基础上增强氢转移活性,达到降低汽油烯烃含量的目的;合理调节催化剂的酸性分布,减少焦炭和干气的产生。 生产单位:催化剂齐鲁分公司 应用单位:中石化荆门分公司、湛江东兴炼厂,大连西太平洋等 ZC系列
FDFCC-Ⅲ重油催化裂化工艺
FDFCC-Ⅲ重油催化裂化工艺 FDFCC-Ⅲ工艺特有的技术特点: (1)开发了实现“低温接触、大剂油比”高效催化技术(HECT)。即利用汽油提升管待生剂相对较低的温度和较高的剩余活性,将汽油提升管待生剂引入重油提升管底部与再生剂混合,降低干气和焦炭产率,提高丙烯收率,改善产品分布。 (2)采用双提升管、双沉降器和双分馏塔工艺流程,即分别设置重油提升管和汽油
提升管,两根提升管后均设有沉降器和分馏塔,从而充分利用汽油提升管的改质效果,使催化汽油的烯烃含量直接满足欧Ⅲ标准。 4. 采用了带预混合管的烧焦罐高效再生技术,具有较高的烧焦强度和较低的再生剂含炭。为降低再生系统压降2007年FDFCC技术改造取消了预混合管和大孔分布板。 5. 采用了可调性强的下流式外取热器,取出两器热平衡多余的热量。 6. 能量回收机组采用了烟气轮机-轴流式主风机-汽轮机-电动/发电机四机组同轴新设备,回收了能量,降低了装置能耗。烟气轮机轮盘和叶片使用的是国研制的新型高温合金和喷涂材料。 7. 设有余热锅炉回收系统,回收热量,降低能耗,为防止省煤器炉管低温腐蚀,在烟气低温位置采用了20G钢炉管,过热器高温段采用12CrMo材质。 8. 选用了高效旋风器和电液冷壁滑阀等设备。 生产原理 1. 反应—再生部分 重油催化裂化提升管和汽油提升管用的催化剂为分子筛催化剂。原料油与高温催化剂在提升管接触,在一定的压力和温度下发生一系列化学反应,主要有裂化、异构化、氢转移、芳构化、缩合等反应,生成包括干气、液化气、汽油、柴油、回炼油、油浆馏份的高温油气和焦炭,生成的焦炭附着在催化剂上。在沉降器反应油气和催化剂分离,反应油气到主、副分馏塔进行分离,重油反应器附有焦炭的催化剂经汽提段汽提直接回到再生器,汽油反应器附有焦炭的催化剂经汽提后一路直接回到再生器烧焦一路返回重油提升管底部与重反再生剂混合。再生器催化剂在一定的温度、压力及通入主风的条件下,烧去催化剂上的积炭(即催化剂的再生过程)。催化剂活性、选择性恢复后回提升管循环使用。焦炭燃烧放出的热量除满足工艺需要外,多余的热量由外取热器取出,焦炭燃烧后生成的高温烟气经烟气轮机和余热炉后排入大气。 2. 分馏部分 重油催化分馏部分的作用是把从反应器来的高温油气混合物按沸点围分割成为富气、汽油、轻柴油、回炼油及油浆馏分,并保证各个馏分的质量符合产品要求。此外分馏系统还完成原料预热及热量回收的任务。催化分馏塔与常减压装置的常压塔原理基本相同。不同之处在于: (1).催化分馏塔的进料是过热气相进料。 (2).催化分馏塔气相进料中携带了一部分催化剂颗粒。 因此,催化分馏塔除了按分馏原理完成一般的产品分割外,还设有油浆循环以完成脱过热(将高温过热油气冷却到饱和状态)并和回炼油返塔一起洗涤反应油气中的催化剂。 3. 吸收稳定部分 吸收稳定部分由吸收塔、解吸塔、再吸收塔、稳定塔、容器、冷换及机泵等组成。吸收稳定部分的任务是加工来自分馏塔顶油气分离器的粗汽油和富气(富气经气压机压缩),从中分离出干气(C3≯3%(V)),液化气(C2≯3%(V),C5≯1.0%(V))和稳定汽油,并要求稳定汽油的蒸汽压合格(冬季≯88kpa,夏季≯74kpa)。吸收、解吸、再吸收塔主要解决C2与C3馏份的分离,是吸收和解吸过程;其原理是利用气体混合物中各组分在液体中溶解度的不同来分离气体混合物。 稳定塔完成C3、C4馏份与汽油馏份的分离,是精馏过程;其原理是利用液体混合物各组分的挥发度不同进行分离。 4. 柴油碱洗 碱洗就是利用碱溶液(非加氢精制剂DF-01)和油品中的酸性非烃化合物起反
催化裂化装置工艺条件一览表
催化裂化装置工艺条件一览表 一、催化裂化装置主要工艺指标 1、反应再生单元 序号工艺指标名称单位仪表位号控制范围 1 重油提升管出 口温度℃TRCA22101 A 500~530 2 芳烃提升管出 口温度 芳烃提升管出 口温度 ℃ ℃ TRCA22101 B TRCA22101 B 440~480 (低硫) 480~530 (高硫) 3 反应压力MPa PR22102 0.13~0.19 4 再生压力MPa PRCA22101 0.16~0.22 5 两器压差MPa PdRCA2210 4A 0.03~0.05 6 再生器温度℃TRCA22102 660~710 7 再生器稀相温 度 ℃TIA22123 ≤730 8 沉降器藏量t WRCA22101 35~48 9 再生器藏量t WR22105 90~130 10 原料油预热温 度 ℃TRCA22103 180~225 11 主风流量Nm3/h FRCA22604 140000~
160000 12 待生套管流化 Nm3/h FRCA22110 3000~6000 风量 Nm3/h FRCA22109 3500~8000 13 外取热流化风 量 14 烟气氧含量v%AR22101 ≤3 15 过热蒸气温度℃TIC22461 380~410 MPa PRA22421 3.5~4.1 16 外取热汽包压 力 ℃TI22468 >122 17 省煤器上水温 度 18 外取热汽包液 %LRC22421 50±20 位 2、分馏单元 序号工艺指标名称单位仪表位号控制范围 1 重油分馏塔塔顶℃TRCA2220120~150 2 芳烃分馏塔塔顶℃TRCA2222125~150 3 重油分馏塔16层℃TI22209 220~240 4 芳烃分馏塔16层℃TI22238 210~230 5 重油分馏塔塔底℃TRC22217 ≤350 6 芳烃分馏塔塔底℃TRC2223 7 ≤340 7 油浆外甩温度℃TR22250 ≤95 8 油浆固体含量g/l ≤6 9 V22201液位%LIK22209 50±20 10 T22201A液位%LC22201 50±20
重油加工催化剂的选择
2018年催化剂技术交流会发言材料 一、当今催化裂化工艺所处的地位: 1、重油轻质化工艺主要有: 重油加氢工艺;重油催化工艺;延迟焦化工艺。2007年中石化加工原油1.7亿吨(占全国的52%),其中催化装置加工了0.47亿吨原料油,占原油一次加工量的28%(其中掺渣量约为0.16亿吨,占原油一次加工量的约10%;延迟焦化加工渣油量占原油一次加工量的17%;合占原油一次加工量的27%,约占全部渣油量的90%以上)。 2、催化与焦化的区别:
分析: 渣油不算太差,去催化更简单,但是烧焦负荷太大(可称为催化CFB锅炉);加氢催化组合液收最高、产品质量最好、也最为环保,问题是投资大、运行费用高等(耗氢1.5%;能耗23kgEO/t,一年一次的换剂费用8000万元,310万的建设费用10亿元,是未来发展的方向。2006年统计,美国82%,日本91%,俄罗斯40%,中国仅为14%)。 [丁烷脱沥青+(加氢处理)+催化裂化组合工艺]的效果与[焦化+(加氢处理)+催化裂化组合工艺]相比哪个更好(新建青岛大炼油和扩建洛阳石化等均为该流程)?前者约30%的脱沥青油如何处理?约70%的脱油沥青还要去催化;后者以生产柴油为目的等。 1)延迟焦化生焦率比渣油催化要高。
2)延迟焦化装置用于加工高硫、高金属、高残炭的原料油;主要产品是柴油;为催化提供改质原料油(焦化蜡油);焦化汽油马达法辛烷值约68、烯烃50%,不宜作为汽油调和组分,可作为化工轻油(乙烯裂解料和催化重整料);焦化液化气含烯烃少,不能作化工原料,更适合作民用烃;焦化干气适合作制氢原料或燃料。 3)催化裂化装置主要用于加工低硫或含硫、低金属、一定残炭的原料油;主要产品是运输燃料汽油和化工原料轻烃(液化气);催化烧焦部分相当于“CFB”锅炉,为全厂提供部分动力蒸汽[其能源热效率约90%;其能源利用效率(熵)约60%已超过一般加热炉和锅炉;对装置能耗的影响是:反应生焦率1%,装置能耗增加1-2个单位]。 3、三种重油轻质化工艺的效益比较: 通常情况下,原油价格越高,重油加氢组合工艺(重油加氢处理+催化裂化)效益就越好;原油价格越高,延迟焦化的效益就越差。 4、前几年催化裂化工艺所遇到的突出问题有:汽油质量问题和汽柴油价格。质量问题已基本得到解决(主要得利于反应工程的改进和催化剂、助剂的研发加之质量指标的放宽);成品油与原油价格形成联动机制的时间将不会太久,催化裂化工艺方兴未艾,新一轮的催化装置建设已经开始。 5、油变焦与煤制油不仅矛盾而且也不符合国情(实现更多渣油轻质化。据了解,目前日本只有两套延迟焦化装置,最多只有1340万吨,占全部渣油处理能力的21%)。2007年全国进口原油量已占加工总