汽车仪表板冲压工艺及模具设计

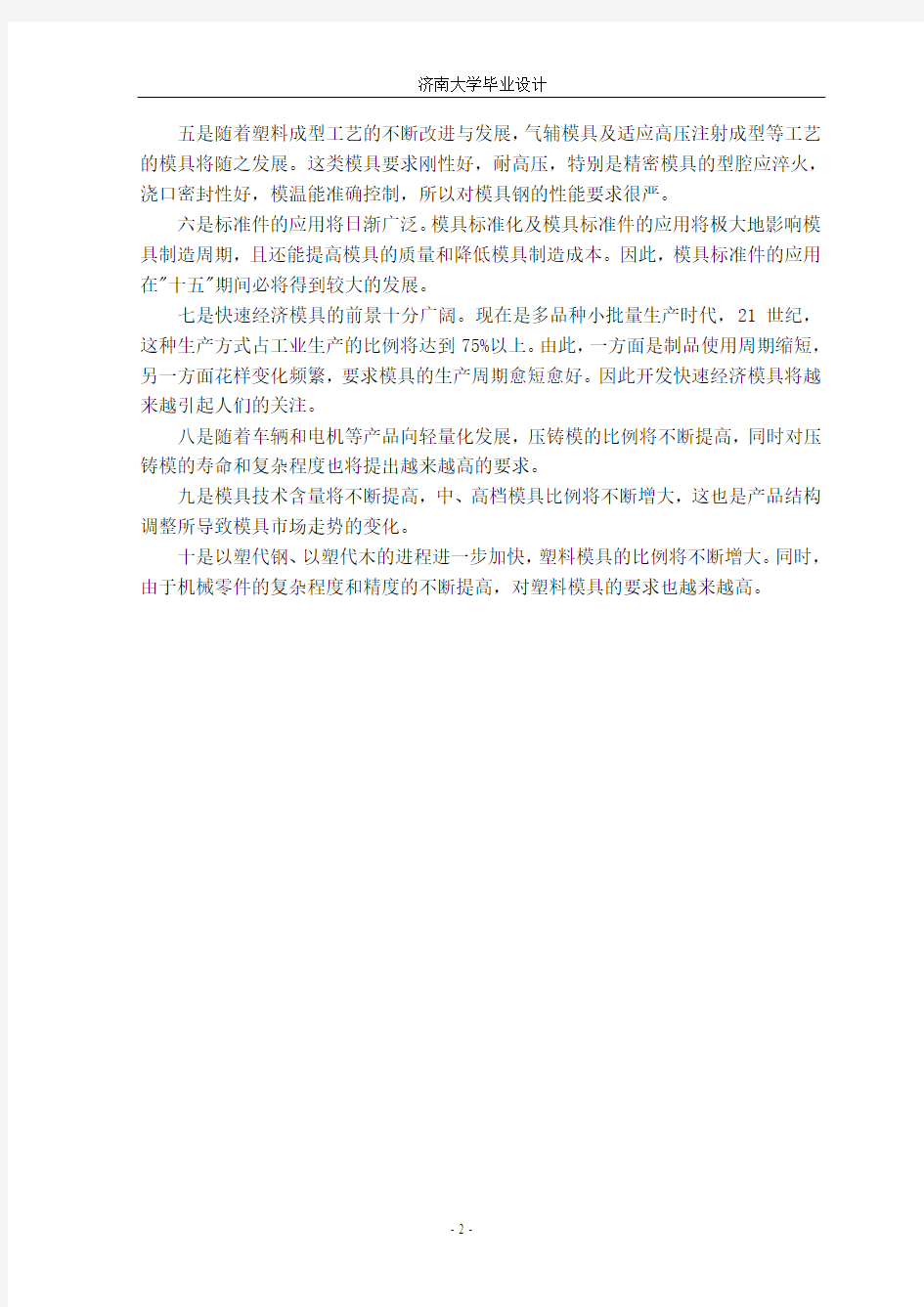
第一章前言
1.1中国模具的发展现状
模具是机械、汽车、电子、通讯、仪表、家电工业产品的基础工艺装备,模具制造是一切制造业之首,模具行业实现工业化和商品化生产,是制造业生产技术进步的标志。现代模具设计与制造技术,涉及机械工程、信息与电子工程、冶金与材料工程、工程管理等学科专业范围。
中国经济的高速发展对模具工业提出了越来越高的要求,也为其发展提供了巨大的动力。近10年来,中国模具工业一直以每年15%左右的增长速度快速发展。
目前,根据专家统计统计,中国约有模具生产厂点2万余家,从业人员有50多万人,全年模具产值达534亿元人民币。近年来,模具行业结构调整步伐加快,主要表现为大型、精密、复杂、长寿命模具标准件、模具标准件发展速度高于行业的总体发展速度;塑料模和压铸模比例增大;面向市场的专业模具厂家数量及能力增加较快;随着经济体制改革的不断深入,“三资”及民营企业的发展很快。
中国模具工业的发展在地域分布上存在不平衡性,东南沿海地区发展快于中西部地区,南方的发展快于北方。模具生产最集中的地区在珠江三角和长江三角地区,其模具产值约占全国产值的三分之二以上。
1.2 中国模具的发展趋势
“十二五”时期是我国妥善应对国内外发展环境重大变化、加快实现全面建设小康社会目标的关键时期,也是我国模具制造行业健康发展的关键时期,国内外环境不确定因素虽然很多,但我国经济发展仍在高速增长期内,我国模具在国际模具市场上的比较优势仍旧存在,国内模具市场预期也继续看好,模具行业发展呈现大趋势。
一是模具的精度越来越高。10年前,精密模具的精度一般为5微米,现在已达到2~3微米,不久1微米精度的模具将上市。这要求超精加工。
二是模具日趋大型化。这是由于模具成型的零件日渐大型化和高生产效率要求而发展的"一模多腔"所造成的。
三是多功能复合模具将进一步发展。新型多功能复合模具除了冲压成型零件外,还担负叠压、攻丝、铆接和锁紧等组装任务,对钢材的性能要求也越来越高。
四是热流道模具在塑料模具中的比重逐渐提高。由于采用热流道技术的模具可提高制件的生产率和质量,并能大幅度节约制作的原材料,因此热流道技术的应用在外国发展很快,许多塑料模具厂生产的塑料模具一半以上采用了热流道技术,有的厂家使用率达到80%以上,效果十分明显。热流道模具在我国也已生产,有些企业使用率上升到20%~30%。
五是随着塑料成型工艺的不断改进与发展,气辅模具及适应高压注射成型等工艺的模具将随之发展。这类模具要求刚性好,耐高压,特别是精密模具的型腔应淬火,浇口密封性好,模温能准确控制,所以对模具钢的性能要求很严。
六是标准件的应用将日渐广泛。模具标准化及模具标准件的应用将极大地影响模具制造周期,且还能提高模具的质量和降低模具制造成本。因此,模具标准件的应用在"十五"期间必将得到较大的发展。
七是快速经济模具的前景十分广阔。现在是多品种小批量生产时代,21世纪,这种生产方式占工业生产的比例将达到75%以上。由此,一方面是制品使用周期缩短,另一方面花样变化频繁,要求模具的生产周期愈短愈好。因此开发快速经济模具将越来越引起人们的关注。
八是随着车辆和电机等产品向轻量化发展,压铸模的比例将不断提高,同时对压铸模的寿命和复杂程度也将提出越来越高的要求。
九是模具技术含量将不断提高,中、高档模具比例将不断增大,这也是产品结构调整所导致模具市场走势的变化。
十是以塑代钢、以塑代木的进程进一步加快,塑料模具的比例将不断增大。同时,由于机械零件的复杂程度和精度的不断提高,对塑料模具的要求也越来越高。
第二章 工艺方案的制订
2.1 零件的工艺性分析
本零件为汽车仪表板,材料为Q235,板厚为1)(m m ,大批量生产。
图2.1 汽车仪表板
该零件有四处90度弯曲,有多处冲孔。因而此工件包含了落料,弯曲,冲孔等工艺步骤。其工件最小圆角半径1mm 符合最小圆角半径要求。从技术要求和使用条件来看,零件的精度要求一般,适合冲压生产。工件的冲压精度和粗糙度都要求不高,符合冲裁要求。
2.2 毛胚尺寸计算
工件的主要成形工序为落料、弯曲、冲孔,零件尺寸如图2.4,所以毛坯的尺寸即为弯曲件的展开尺寸。
U 型弯曲件的毛胚展开长度计算公式
)(321δx r l l l L ++++= (2-1) 式中 1l —U 型弯曲件直边长度)(m m
2l —U 型弯曲件直边长度)(m m
3l —U 型弯曲件直边长度)(m m
r —弯曲半径)(m m
δ—弯曲件厚度)(m m
x —中性层位移系数
则工件毛坯的长度L 1为
)(404)128.01(38488L 1mm =?++++=π
工件毛坯的宽度L 2为
)(350)128.01(33088L 2mm =?++++=π
依上所述,该零件的坯料尺寸可定为长度404)(m m ,宽度350)(m m 。
2.3 工艺方案的制定
经过以上分析,可以进一步明确,该零件的冲压加工包括以下基本工序:落料、冲孔、弯曲。此工件的成形工艺可以有以下几种方案:
方案一:按照基本工序顺序:落料→冲孔→弯曲
方案二:落料→弯曲→冲孔
方案三:落料、冲孔复合,其他按照基本工序:落料、冲孔→弯曲
分析以上三种方案,可以看到:
方案一:按照基本工序排列的冲压工艺每步工序都只使用简单模具,结构简单,制造周期短,成本较低,但不能保证冲孔件孔的精度。
方案二:落料后先弯曲,再冲孔,不仅使模具结构简单,制造周期短,成本较低,而且保证冲孔件孔的精度。
方案三:将落料、冲孔复合,实现二道工序在一副模具上完成,减少了工序数和模具数,但模具复杂,提高了生产成本。
通过上述对三种方案的分析,最终选用方案二:落料→弯曲→冲孔
(1) 零件的排样图,如图2.2。
搭边的最小宽度大于塑变区的宽度,由板厚1)(m m 查搭边数值表,沿边搭边为2)(m m ,工件间搭边为1.5)(m m 。
图2.2排样图(2)第一步工序:落料,工件如图2.3。
图2.3落料工件图(3)第二步工序:弯曲,工件如图2.4
图2.4弯曲工件图(4)第三步工序:冲孔,工件如图2.5。
图2.5冲孔工件图
第三章落料模设计
3.1冲压工艺的计算
3.1.1排样方案
查表2-12 合理搭边值[1],确定搭边数值。当t=1)
(m m,
(m m时,沿边搭边为2)工件间搭边为1.5)
(m m。
图3.1 排样图
一个进距的材料利用率η
100nA bh
η=?% (3-1) 式中 A —冲裁件的面积;
n —一个进距内冲裁件数目;
b —条料宽度;
h —进距;
所以 η=%1005
.351408)10104404350(1????-?? =98.32%
3.1.2冲压压力的计算
(1) 落料冲裁力
b L f F δσ10= (3-2)
式中 f 1—系数;取决于材料的屈强比,可从图2-5 f 1与材料屈强比的关系[1]求得,因此取f 1=0.65;
L —落料件周长;)(m m ;
δ— 材料厚度;)(m m ;
b σ—材料抗拉强度;)(MPa ;Q235 b σ=375~460)(MPa ,取b σ=420)(MPa ;
所以 b L f F δσ10=
=0.65×2(404+350)×1×420
=411.68(KN)
(2) 推件力的计算
022F nk F = (3-3)
式中 n —卡在凹模洞口里的工件数;
k 2—推件力系数;查表2-7 卸料力、推件力和顶件力系数[1],取k 2=0.055; F 0—落料力;
所以 022F nk F =
=1×0.055×411.68
=22.64(KN)
(3) 总冲压力的计算
20F F F += (3-4)
=411.68+22.64
=434.32(KN)
(4) 压力机的初步选择
选择压力机吨位时,考虑刃口磨损和材料厚度及波动、力学性能等因素,实际冲裁力可能增大,所以取
1.3F F =总 (3-5) 3
2.434
3.1?=
=564.62(KN)
因此初步选择压力机的型号为J23—63开式双柱可倾压力机,公称压力为630KN ,最大封闭高度为360)(m m ,最小封闭高度为270)(m m 。
3.1.3模具的压力中心的计算
由于毛坯内外周边形状对称,所以模具的几何中心就是压力中心。
3.1.4模具刃口尺寸的计算
根据表2-4 冲裁模始用间隙[1]查得间隙值Z min =0.10)(m m ,Z max =0.14)(m m 。 根据表2-15凸凹模的制造公差表[1]查得凸凹模的制造公差为:
凸模)(040.01mm p =δ
)(035.02mm p =δ
)(040.03mm p =δ
)(035.04mm p =δ
凹模)(060.01mm d =δ
)(050.02mm d =δ
)(060.03mm d =δ
)(050.04mm d =δ
为了保证冲模的间隙小于最大合理间隙:
)(100.0060.0040.03311mm d p d p =+=+=+δδδδ
)(085.0050.0035.04422mm d p d p =+=+=+δδδδ
)(04.010.014.0m in m ax mm Z Z =-=-
因为 m i n
m a x 44223311>>Z Z d p d p d p d p -+=++=+δδδδδδδδ 则 )(016.004.04.0)(4.0min max 4321mm Z Z p p p p p =?=-=====δδδδδ
)(024.004.06.0)(6.0min max 4321mm Z Z d d d d d =?=-=====δδδδδ
由于零件形状比较简单,所以凸凹模可以分开加工,且零件的公差等级为IT12,精度要求不高。
由零件的基本尺寸L 1=404)(m m ,L 2=350)(m m ,L 3=384)(m m ,L 4=330)(m m 查表
3-2常用尺寸的标准公差数值表[6]得公差)(57.0)
(57.0)
(57.0)
(63.04321m m m m m m m m =?=?=?=?查表2-7 系数x [7]得系数
5.05
.05
.05
.04321====x x x x
则落料凹模的尺寸:
d x L L d δ+?-=0
1111)( (3-6) 024.00)63.05.0404(+?-= )(69.403024.00mm += d x L L d δ+?-=02222)( 024.00)57.05.0350(+?-= )(72.349024.00mm += d x L L d δ+?-=03333)( 024.00)57.05.0384(+?-= )(6.403024.00mm += d x L L d δ+?-=04444)( 024.00)57.05.0330(+?-= )(72.329024.00mm += 落料凸模的尺寸:
0m i n 1111)(p Z x L L P δ--?-= (3-7)
0016.0)10.069.403(--=
)(59.4030016.0mm -= 0min 2222)(p Z x L L P δ--?-=
016.0)10.072.349(--=
)(62.3490016.0mm
-= 0
min 3333)(p Z x L L P δ--?-=
016.0)10.072.383(--=
)(62.3830016.0mm
-= 0
min 4444)(p Z x L L P δ--?-=
016.0)10.072.329(--=
)(62.3290016.0mm
-= 3.2落料模主要零件的设计
3.2.1落料凹模
(1) 厚度Ha
查表9-6 凹模厚度H 和壁厚C [1],从凹模孔的最大宽度(404﹥200)及料厚(1>0.8~1.5),取凹模厚度H a =30)(m m ,壁厚C=48)(m m 。
(2) 凹模的外形尺寸
由壁厚C=48)(m m ,可确定凹模的外形尺寸。
凹模长:404+48+48=500)(m m
凹模宽:350+48+48=446)(m m
(3) 刃壁形式
因此落料模结构简单,且材料较薄,结合表9-3 常见冲裁凹模刃口及孔壁结构形式[1]选择序号4直壁形式。
(4) 凹模的固定形式
利用销钉和螺钉固定在下模座上。
3.2.2落料凸模
(1) 凸模的刃口形式
凸模加工成等截面结构。
(2) 凸模的固定形式
利用销钉和螺钉固定在上模座上。
(3) 凸模的长度
凸模的长度根据零件的结构来确定
l H ta +++=321δδδ (3-8) 式中 H ta —凸模的长度;)(m m
1δ—凸模固定板厚度;)(m m
2δ—卸料板厚度;)(m m
3δ—导尺厚度;)(m m
l —自由长度;)(m m
则 H ta =0+14+8+60=82 )(m m
所以取凸模长度H ta =85)(m m 。
3.2.3卸料板的设计
由于此件的厚度较小,且要求表面平整,可采用固定卸料版,查表9-15卸料板厚度[1]。
选用卸料板长度 500)(m m
卸料板宽度 446)(m m
卸料板厚度 h 0=18)(m m
卸料板材料选用45钢,不用热处理淬硬。
3.2.4模座的设计
(1) 模座的外形尺寸
由于凹模的最大外形尺寸为500)(m m ,查模架标准结构表[4],可确定下模座的尺寸为80500500??)(m m ,上模座的尺寸为65500500??)(m m 。
(2) 模座的材料
一般选用铸铁HT200,也可选用A3,A5结构钢,但从为了降低模具成本,本设计则考虑选用铸铁HT200。
(3) 垫板选择
查表9-23 垫板尺寸[1],从凹模尺寸(500×446)凸模尺寸(404×350)可确定 上垫板尺寸500×446×12)(m m
下垫板尺寸404×350×12)(m m
3.2.5挡料装置的设计
挡料装置在单工序落料或复合模中,主要作用保持冲件轮廓的完整和适量的搭边。
根据此落料模的设计,选用导尺进行导料。挡料装置利用挡料销进行挡料。
3.2.6冲模闭合高度的确定
模具闭合高度H 模是模具在最低的工作位置时,下模座的底平面至上模座的顶平
面之间的距离(不含模柄高度)。
压力机的闭合高度是指滑块在下止点时工作台面(不含垫板高)至滑块下平面件的距离。
即: ?-+++++=ta a H H H H H H H 4321模 (3-9) 式中 模H —冲模闭合高度;)(m m
1H —上模座厚度;)(m m
2H —下模座厚度;)(m m
3H —上垫板厚度;)(m m
4H —下垫板厚度;)(m m
a H —凹模厚度;)(m m
ta H —凸模的长度;)(m m
?—凸模刃口进入凹模刃口的深度;)(m m
则 )(2831853012128065mm H =-+++++=模
冲模设计时,必须使冲模的闭合高度与压力机的闭合高度相适应,通常应满足下列关系:
)(10)(5min max mm H H mm H +≥≥-模 (3-10) 式中 m a x H —压力机最大闭合高度,max H =360)(m m ;
m i n H —压力机最小闭合高度,min H =270)(m m ;
由于冲模闭合高度满足280283355≥≥,则模具的闭合高度为283)(m m 符合要求。
3.2.7模柄、导柱、导套的选用
根据所选压力机的模柄孔,根据标准件表[4],查得相应标准的模柄,选标标准的压入式模柄d=50)(m m ,D=54)(m m 。
根据标准件表[4],选用标准的导柱、导套,导柱)(27050mm ?,导套)(7512050mm ??。
3.2.8模具材料的选用
凸模和凹模是在强压、连续使用和有很大冲击的条件下工作,并伴有温度的升高,工作条件极其恶劣。所以对凸凹模的材料要求有较好的耐磨性,耐冲击性,淬透性和切削性。硬度要大,热处理变形小,而且价格要低廉。
结合上述原则,由凸、凹模材料的选用与热处理表[5]
推荐材料有:
1) 凸模,凹模采用9Mn2V ;
2) 导柱,导套采用20 钢;
3) 挡料销,定位销采用Q235 钢;
4) 卸料板采用45钢;
5) 上、下模座采用HT200;
第四章 弯曲模设计
4.1弯曲件工艺计算
4.1.1弯曲件展开长度计算
因为零件弯曲半径r >0.5δ,所以弯曲件的展开长度按直边区与圆角区分段进行计算。视直边区在弯曲前后长度不变,圆角区展开长度则在按弯曲前后中性层长度不变的条件下进行计算。
根据前面冲压件毛坯尺寸的计算,可得出此弯曲件展开尺寸如图2.4所示。
汽车操纵杆固定板冲压工艺及模具设计
1前言 1.1冲压模具工业的特点 模具是国民经济的基础工业,模具工业的发展水平从某种意义上来说代表着一个国家的工业发展水平。由于模具自身的特点,现代模具企业大多体现出技术密集、资金密集和高素质劳动力密集以及高社会效益的特点,模具制造业已成为高新技术制造产业的一部分。模具设计与生产越来越成为现代加工制造业的重要组成部分,模具做为高效率的生产工具的一种,是工业生产中使用极为广泛与重要的工艺装备。采用模具生产制品和零件,具有生产效率高,可实现高速大批量的生产;节约原材料,实现无切屑加工;产品质量稳定,具有良好的互换性;操作简单,对操作人员没有很高的技术要求;利用模具批量生产的零件加工费用低;所加工出的零件与制件可以一次成形,不需进行再加工;能制造出其它加工工艺方法难以加工、形状比较复杂的零件制品;容易实现生产的自动化的特点。 1.2中国冲压模具的发展现状及发展方向 随着与国际接轨的脚步不断加快,市场竞争的日益加剧,人们已经越来越认识到产品质量、成本和新产品的开发能力的重要性。而模具制造是整个链条中最基础的要素之一,模具制造技术现已成为衡量一个国家制造业水平高低的重要标志,并在很大程度上决定企业的生存空间。目前我国冲压模具无论在是数量上,还是在质量、技术和能力等方面都已经由了很大发展,但与国民经济需求和世界先进水平相比,差距仍很大,一些大型精密复杂的高档模具每年仍大量进口,特别是中高档轿车的覆盖件模具,目前仍主要依靠进口。一些低档次的简单冲模,已趋供过于求,市场竞争激烈。 在国家产业政策的正确引导下,过几十年努力,在我国冲压模具的设计与制造能力已达到较高水平。包括信息工程和虚拟技术等许多现代设计制造技术已在很多模具企业得到应用。虽然如此,国的冲压模具设计制造能力与市场需要和国际先进水平相比仍有较大差距。这一些主要表现在高档轿车和大中型汽车覆盖件模具及高精度冲模方面.无论在设计还是加工工艺和能力方面.都有较大差距.轿车覆盖件模具,设计和制造难度大质量和精度要求高的特点,可代表覆盖件模具的水平。虽然在设计制造方法和手段方面基本达到了国际水平,模具结构周期等方面,与国外相比还存在一定的差距。 近年许多模具企业加大了用于技术进步的投资力度,将技术进步视为企业发展的重要动力。一些国内模具企业已普及了二维CAD,并陆续开始使用UG、Pro/Engineer、I-DEAS、Euclid-IS等国际通用软件,个别厂家还引进了Moldflow、C-Flow、DYNAFORM、Optris和MAGMASOFT等CAE软件,并成功应用于冲压模的设计中。以汽车覆盖件模具为代表的大型冲压模具的制造技术已取得很大进步,东风汽车公司
冲压工艺及模具设计一
第一章概述 内容简介: 本章讲述冲压冲压模具设计的基础知识。涉及冲压和冲模概念、冲压工序和冲模分类;常见冲压设备及工作原理、选用原则;冲压成形基本原理和规律;冲压成形性能及常见冲压材料;模具材料种类;模具制造特点、模具零件加工方法及应用等。 章节内容: 1.1冲压的定义 1.2冲压工序分类 1.3冲压工艺的特点及其应用 1.4冲压变形的理论基础 1.5冲压用板料 1.6冲压设备简介 学习目的与要求: 1.掌握冲压和冲模概念、冲压工序和冲模分类; 2.认识常见冲压设备,掌握选用原则; 3.了解屈服准则、塑性变形时应力应变关系、体积不变条件、硬化规律、等冲压成形基本规律; 4.了解冲压成形性能与机械性能关系; 5.认识模具制造特点,掌握模具零件加工方法。 重点内容: 冲压成形基本概念、冲压设备及选用、冲压成形基本规律及应用、冲压成形性能与机械性能关系、常用模具零件加工方法及应用。 难点内容: 冲压成形基本规律、冲压成形性能与机械性能关系。
主要参考书: [1] 王同海.实用冲压设计技术.北京:机械工业出版社,2000 [2] 冯炳尧.模具设计与制造简明手册.上海:上海科学技术出版社,2000 复习思考题:<参考答案下载> 1-1什么是冲压加工? 1-2 冲压加工又何特点? 1-3冲压加工又哪几种类型? 1-4什么是分离工序? 1-5 什么是塑性变形工序? 1-6 我国冲压技术的发展方向是怎么样的? 1-7 常用的冲压设备有哪几种? 1-8 通用曲柄压力机的工作原理是怎么样的? 1-9 选用冲压设备的基本原则是什么? 1-10怎样根据冲压工艺来选择压力机的种类? 1-11怎样选择压力机规格大小? 1-12如何正确使用压力机? 1-13使用时如何正确地调整压力机? 1-14冲压材料常用的备料设备有哪些? 1-15剪板机由哪几部分组成? 1-16如何正确使用剪板机? 例题与解答: [1]冲压塑性变形辅助分析 [2]拉深变形中的变形趋向:注意变形过程、变形区与传力区、变形缺陷 电子教材 1.1 冲压的定义 冲压是利用冲模在冲压设备上对板料施加压力(或拉力),使其产生分离或变形,从而获得一定形状、尺寸和性能的制件的加工方法。冲压加工的对象一般为金属板料(或带料)、薄壁管、薄型材等,板厚方向的变形一般不侧重考虑,因此也称为板料冲压,
《冲压模具课程设计》范例
【范例】 (1)题目:东风EQ-1090汽车储气简支架 (2)原始数据 数据如图7—1所示。大批量生产,材料为Q215,t=3mm。 图7-1零件图 (3)工艺分析 此工件既有冲孔,又有落料两个工序。材料为Q235、t=3mm的碳素钢,具有良好的冲压性能,适合冲裁,工件结构中等复杂,有一个直径φ44mm的圆孔,一个60mm×26mm、圆角半径为R6mm的长方形孔和两个直径13mm的椭圆孔。此工件满足冲裁的加工要求,孔与孔、孔与工件边缘之间的最小壁厚大于8mm。工件的尺寸落料按ITll级,冲孔按IT10级计算。尺寸精度一般,普通冲裁完全能满足要求。 (4)冲裁工艺方案的确定 ①方案种类该工件包括落料、冲孑L两个基本工序,可有以下三种工艺方案。 方案一:先冲孔,后落料。采用单工序模生产。 方案二:冲孔一落料级进冲压。采用级进模生产。 方案三:采用落料一冲孔同时进行的复合模生产。 ②方案的比较各方案的特点及比较如下。 方案一:模具结构简单,制造方便,但需要两道工序,两副模具,成本相对较高,生产效率低,且更重要的是在第一道工序完成后,进入第二道工序必然会增大误差,使工件精度、质量大打折扣,达不到所需的要求,难以满足生产需要。故而不选此方案。
方案二:级进模是一种多工位、效率高的加工方法。但级进模轮廓尺寸较大,制造复杂,成本较高,一般适用于大批量、小型冲压件。而本工件尺寸轮廓较大,采用此方案,势必会增大模具尺寸,使加工难度提高,因而也排除此方案。 方案三:只需要一套模具,工件的精度及生产效率要求都能满足,模具轮廓尺寸较小、模具的制造成本不高。故本方案用先冲孔后落料的方法。 ③方案的确定综上所述,本套模具采用冲孔一落料复合模。 (5)模具结构形式的确定 复合模有两种结构形式,正装式复合模和倒装式复合模。分析该工件成形后脱模方便性,正装式复合模成形后工件留在下模,需向上推出工件,取件不方便。倒装式复合模成形后工件留在上模,只需在上模装一副推件装置,故采用倒装式复合模。 图7 2粗画排样图 (6)工艺尺寸计算 ①排样设计 a .排样方法的确定根据工件的形状。确定采用无废料排样的方法不可能做到,但能采用有废料和少废料的排样方法。经多次排样计算决定采用直对排法,初画排样图如图7 2所示。 b .确定搭边值查表,取最小搭边值:工件间a l =2.8,侧面a=3.2。 考虑到工件的尺寸比较大,在冲压过程中须在两边设置压边值,则应取。a=5;为了方便计算取a l =3。 c. 确定条料步距步距:257.5mm ,宽度:250+5+5=260mm . d .条料的利用率 21752052.35%257.5260 η?==? e .画出排样图根据以上资料画出排样图,如图7-3所示。
【汽车专业文献翻译】汽车后底板的冲压模具设计分析
汽车后底板的冲压模具设计分析 Fuh-kuo Chen,Jia-Hong Liu 台湾国立大学机械工程系,台北,台湾 1994年10月10日接收 摘要 本文研究了客车后底板的冲压制造过程。使用圆栅格分析和3-D有限元方法,对产生拉深开裂缺陷的最初的冲模设计进行了分析。开裂缺陷是由于压边圈下大范围的金属限制了向杯状区域的流动。优化的冲模设计,包括一个分离的冲模面和一个楔形机构组成的凹模结构,目的是在不添加工序的情况下,向杯状区域提供额外金属、消除开裂缺陷。这种优化的冲模设计在第一次和第二次拉深的圆栅格分析结果中得到验证,获得了合格的拉深面板。 关键字:冲压模具;后底板;开裂;圆栅格分析 1.绪论 一般冲压过程中的主要缺陷是开裂,在最近的十年中,很多研究都使用了成型极限分析和有限元分析方法来研究开裂问题的起因和解决办法。自Keeler和Backofen在1963年第一次引入成型极限图(FLDS),在冲压车间里它们就已经被广泛的使用在金属的结构分析中。即使这个成型过程极快,FLDS也可以显示出应力并提供一个有用的工具去测定,同时有限元方法能够精确的计算冲压部分的分布应力,并且预知是否可能产生开裂缺陷。 一般来说,解决开裂问题的办法是在主要的拉深过程开始前,向危险地带提供更多的金属,这样可以通过减少压边圈的压力或是改善润滑条件而达到,但是为了输送更多的金属到危险区域,最好最直接的方法是增加一个额外的工序,然而,这个额外的工序会多增加一套模具和额外的劳力从而增加生产成本。 在目前的研究中,优化的模具设计,包括一个分离的冲模面和一个楔形机构组成的凹模结构,目的是为了消除发生在客车面板冲压过程中的开裂缺陷。这种特殊的模具面和楔形结构能为发生开裂缺陷的危险区域提供额外的金属,而不增加
汽车模具工艺案例分析
覆盖件冲压工艺设计 一、工艺设计前的准备工作 在拿到冲压件进行工艺设计前,必须查阅有关资料,以便明确产品的具体要求、现有的条件等,为设计合理而可行的冲压工艺做好必要的准备。 这些资料主要有: 1,零件图或产品图,可以参考的模型。 2,冲压件的公差。 3,类似零件的成型性及作业性的有关资料、曾出现的各种质量问题及解决方法。 4,关于产品所用钢材的有关资料,如材料的各项性能参数值,表面质量等。 5,各种摸具设计的标准和模具零件的规格。 6,现有压力机的参数和附属装置、生产率等方面的资料。 7,产量和要求的时间。 通过对零件图和拉深件图的研究,应该了解该零件所应具有的功能、所要求的单个零件的强度,表面质量以及相关零件之间所要求的相关精度。并明确下列事项: 1,零件轮廓、法兰、侧壁及底部是否有形状急剧变化的部分、负角的部位等,以及其他成形困难的形状。 2,该零件和有关零件的焊接面、装配面、镶嵌面有什么要求。
3,孔的精度(直径、位置)、孔和孔的间距的要求,这些孔的位置在何处(平面部分、倾斜部分、侧壁部分)。 4,各个凸缘精度允许达到什么程度(包括长度、凸缘面的位置、回弹)。 5,焊接、装配的基准面和孔在何处。 6,零件冲压成形需要解决的重点问题有哪些。 7,材料的利用率如何。 在进行工艺设计之前,必须对冲压件进行合理全面的工艺分析。根据冲压件本身原始信息(包含产品的材质,料厚,产品形状),冲压件的公差和车身中装配位置,客户和本工厂的压力机参数和生产方式(自动线,手工线),冲压件的生产批量大小以及客户提出的模具设计的技术要求来进行冲压件的工艺分析。 二、零件的工艺分析 下面我们以东风项目中前碰撞梁为例 零件名称:前碰撞梁 材料:DC04
冲压工艺及模具设计
冲压模具成型工艺及模具设计 设计课题:工件如下图所示,材料Q235,板料厚度1mm,年产量8万件,表面不允许有明显的划痕。设计成型零件的模具。 技术要求:未注圆角为R1;未注公差为IT14级;材料厚度t=1mm 一、冲压工艺分析 1、该零件的材料是Q235,是普通的碳素工具钢,板厚为1mm,具有良好 的可冲压性能。 2、该零件结构简单,并在转角处有R1的圆角,所冲的三个孔都是Φ5的 尺寸,工艺性比较好,整个工件的结构工艺性好。 3、尺寸精度,零件上的三个孔的尺寸精度为IT12~13级,三个孔的位置 精度是IT11~12级,其余尺寸的公差为IT12~14,精度比较低。 结论:适合冲压生产。 二、工艺方案确定 该工件包括落料、冲孔两个基本工序,有以下3种工艺方案: 方案一:先落料,后冲孔。采用单工序模具生产。 方案二:落料—冲孔复合冲压,采用复合模生产。 方案三:冲孔—落料级进冲压,采用级进模生产。 方案一模具结构简单,但需要两道工序两幅模具,成本高而生产率低,难以满足中批量生产需求。
方案二只需一副模具,工件精度及生产效率都较高。 方案三也只需要一副模具,生产效率高,操作方便,但位置精度不如复合模具冲裁精度高。 通过对上述三种方案的分析比较,成型该零件应该采用方案二复合模具成型。 三、确定模具类型及结构形式 1、该零件质量要求不高,板的厚度有1mm, 孔边距有6mm,所以可以选用 倒装复合模。 2、定位方式的选择:控制条料的送进方向采用两个导料销,控制条料的 送进步距采用挡料销。 3、卸料、出件方式的选择:采用弹性卸料。下出件,上模刚性顶件。 4、导向方式的选择:为了方便操作,该模具采用后侧导柱的导向方式。 冲压件的形状简单、精度要求不高、生产批量为中批量,为了使得模具寿命较高,采用有导向、弹性卸料、下出件的模具结构形式。 四、工艺计算 1、确定最佳排样方式,并计算材料利用率,选择板料规格。 该零件为近似矩形零件,设计排样1、排样2三种排样方式,如图:排样1: 排样2:
汽车锁座零件冲压工艺分析及模具设计
汽车锁座零件冲压工艺分析及模具设计 摘要:模具是现代工业生产中的重要工艺装备,本论文要紧涉及冲压模具工艺设计和弯曲模具工艺设计,整个过程包括工艺方案、工序安排、工序尺寸、使用的设备及模具类型,并依照设计出的冲裁凸凹模的尺寸及技术要求制定其机加工工艺规程,最终绘制出正确的冲裁模具装备图和弯曲模具装备图。 依照零件的技术要求,确定工艺方案为:先进行冲裁然后弯曲。在冲裁工艺时期,拟定两种落料与冲孔方案:一种是落料与冲孔复合;一种是先落料在冲孔。通过各方面计算与比较,确定第一种方案更优。在弯曲时期,由于孔接近变形区,弯曲后需要钳工修磨,以达到工艺要求。 在凸凹模的制造过程中,由于模具制造与一般机械制造相比较,有着专门的技术要求和明显的特点,必须区不对待,(1)单件生产:每种模具一般生产1~2副,普遍采纳修锉、修配方法加工,工序组合相对集中对工人技术水平要求较高。(2)制造质量高:一般地,模具工作零件的制造精度比产品零件高2~4级,需采纳坐标磨床、数控机床加工。(3)形状复杂:一般加工难度大,有时需要特种加工或专门化机床。(4)材料硬度高:一般采纳工具钢淬火、低温回火,需要采纳特种加工方法。 关键词:模具冲裁弯曲工艺
Block lock parts of car stamping prodess and die design Abstract: Mold is an important technique and equipment in modern industrial production, In this paper, the main process involved in design of stamping die and design of bending mold,the entire process including planning of process, organization of process, size of process, use of equipment and types of mold. And in accordance to the size of convex and concave mold and the its technical requirements complete the development of its machining process planning, eventually draw the correct assembling drawing of blanking dies and bending . According to the technical requirements of parts, Technology program is determined to blanking firstly and then bending. In the Stage of blanking process, The development of blanking and punching two programs: one is the composite blanking and punching; anther is blank firstly then punch. Through calculation and comparison of various aspects, the first program was to identify better.In the Stage of bending. As the deformation zone be in near of the hole, it need to bending fitter after grinding in order to meet the technical requirements. In the manufacturing process of Bump of Blanking Die, mold manufacturing is compared with the general machinery
冲压工艺及模具设计设计书
课程设计说明书题目:冲孔模具设计 课程名称:冲压工艺及模具设计_________________________ 姓名:王宇学号:20114526 学院(系):材料科学与工程专业:材料成型与控制工程班级:材型一班指导教师:宋继顺
目录 一、课程设计目的 (2) 二、工艺分析 (2) 2.1.1材料分析 (2) 08#钢为极软的碳素钢,强度、硬度很低,而韧性和塑性极高,具有良好的深冲、拉延、弯曲和镦粗等冷加工性能、焊接性能。但存在时效敏感性,淬硬性及淬透性极低。大多 轧制成高精度的薄板或冷轧钢带用以制造易加工成形,强度低的深冲压或深拉延的覆盖 零件和焊接构件。 (2) 2.1.2结构分析 (3) 2.1.3确定精度 (3) 三、工艺计算 (4) 刃口尺寸计算 (4) 3.2对于孔φ730+0.08 (5) 3.3冲裁力 (5) 对于直径为φ73的孔 (6) 3.4压力中心的计算 (7) 四、设备选择 (7) 4.1压力机的选择 (7) 4.1.1依据滑块的驱动力分类 (7) 4.1.2依据滑块的数目分类 (8) 4.1.3依据滑块的驱动机构分类 (8) 4.1.4依据滑块驱动机构的配置分类 (8) 4.1.5依据机架的形式来分类 (8) 4.2其他零部件的选择 (8) 五、装配图及零件图绘制 (9) 六、参考文献 (10)
一、课程设计目的 二、工艺分析 冲压件的工艺性是指冲压件对冲压工艺的适应性。冲裁件的工艺性是否合理,对冲裁件的质量、模具寿命和生产率有很大影响,在一般情况下,对冲压件工艺性影响最大的几何形状尺寸和精度要求。良好的冲压工艺性应能满足材料较省、工序较少、模具加工较容易、寿命较高、操作方便及产品质量稳定等要求。 图1.1 零件 Fig1.1 Parts 2.1.1材料分析 材料:08#钢 材料厚度:0.6mm 生产为大批量生产, 08#钢为极软的碳素钢,强度、硬度很低,而韧性和塑性极高,具有良好的深冲、拉延、弯曲和镦粗等冷加工性能、焊接性能。但存在时效敏感性,淬硬性及淬透性极低。大多轧制成高精度的薄板或冷轧钢带用以制造易加工成形,强度低的深冲压或深拉延的覆盖零件和焊接构件。
冲压工艺及模具设计的应用
2017-2018-1 学期 XXXX学院 《冲压工艺与模具设计》课程报告 学院:机械与汽车工程学院 专业:材料成型及控制工程 学生: ____________________________ 学号: ____________________________ 指导教师:__________________________
完成日期 ____________ 年月—日
冲压工艺与模具的发展应用 摘要:模具是工业生产中积极重要而又不可或缺的特殊的基础工艺装备,工业要发 展,模具须先行。没有高水平的模具,就没有高水平的工业产品。现在,模具工业水平既是衡量一个制造业国家水平高低的重要的标志,也是一个工业国家产品保持国际竞争力的重要保证之一。本文主要介绍冲压工艺及模具当前的状况以及其未来发展趋势。 关键词:冲压模具现状发展应用 1概述 1.1冲压的概念 冲压(sheet metal forming;stamping)利用模具在压力机上将金属板材制成各种板片状零件和壳体、容器类工件,或将管件制成各种管状工件。这类在冷态进行的成型工艺方法称为冷冲压,简称冲压。 冲压加工是借助于常规或专用冲压设备的动力,使板料在模具里直接受到变形力并进行变形,从而获得一定形状,尺寸和性能的产品零件的生产技术。板料,模具和设备是冲压加工的三要素。按冲压加工温度分为热冲压和冷冲压。前者适合变形抗力高,塑性较差的板料加工;后者则在室温下进行,是薄板常用的冲压方法。它是金属塑性加工(或压力加工)的主要方法之一,也隶属于材料成型工程技术。 冲压所使用的模具称为冲压模具,简称冲模。冲模是将材料(金属或非金属)批量加工成所需冲件的专用工具。冲模在冲压中至关重要,没有符合要求的冲模, 批量冲压生产就难以进行;没有先进的冲模,先进的冲压工艺就无法实现。冲压工艺与模具、冲压设备和冲压材料构成冲压加工的三要素,只有它们相互结合才能得出冲 压件[1]。 1.2冲压的特点 冲压是高效的生产方法,采用复合模,尤其是多工位级进模,可在一台压力机(单工位或多工位的)上完成多道冲压工序,实现由带料开卷、矫平、冲裁到成形、精整的全自动生产。生产效率高,劳动条件好,生产成本低,一般每分钟可生
汽车模具文档
左右翼子板拉延模装配调试指导书 已有 603 次阅读2009-6-5 15:35|个人分类:机械类| 左/右翼子板外板拉延模装配、调试指导书 一、凸模组装 a)根据图纸确定凸模装配定位型式(底面定位键定位),检查数铣是否 加工凸模底面和下底板凸模安装面上的定位键槽,并测量键槽尺寸、 位置是否有较大误差,是否相互匹配; b)按图纸明细到库房领取定位键(件号502),确认领取的定位键规格、 数量与明细一致,并且检查定位键是否符合标准尺寸公差要求(宽度 公差0 ),检查是否与定位键槽匹配; -0.025 c)将定位键装于下底板凸模安装面上的定位键槽里,由定位键的螺栓过 孔引出螺栓安装螺纹孔中心,钻螺纹底孔,孔口倒角,攻丝,将定位 键用螺栓固定; d)将下底板凸模安装面均匀涂色(红丹或蓝油),研配凸模底面,保证 着色率90%以上; e)根据凸模上螺栓过孔引出下底板上螺栓安装螺纹孔,将凸模用螺栓固 定于下底板; f)转数铣加工型面、轮廓。 二、热处理 a)热处理前检查凸模、凹模及压边圈(材质均为GM246)的型面是否进 行小刀清根,未清根时需返回数铣重新清根; b)对拉延筋、筋槽R角、局部拉延面、凸起棱线进行火焰淬火处理,保 证硬度达HRC55以上,保证淬火硬度均匀,防止过烧现象; c)转数铣进行型面精加工、清根工序。 三、导板的装配及导板/导滑间隙的调整
a)按图纸明细到库房领取导板(件号503、504、505、506),确认所领 取的导板数量、规格型号与图纸明细一致,并检查导板是否符合标准 尺寸公差要求; b)按图纸确认导板在模具上的对应位置并做好标记,标记要醒目易懂; c)检查导板安装面加工尺寸是否有较大误差及缺陷(根据上序提供的数 据及自测),如有异常现象提前做好处理; d)检查导板与安装面贴合率并进行研合,贴合率要大于90%,贴合间隙 要小于0.03mm; e)以导板螺栓过孔位置引出螺栓安装螺纹孔中心位置,钻螺纹底孔,孔 口倒角,攻丝,安装螺纹孔要垂直于导板安装面,孔边毛刺要清除干 净; 安装螺纹孔≥M6时,先用小直径钻头钻出底孔,再用大直径钻头扩到螺纹底孔直径,螺纹底孔直径要符合标准,防止过大或过小影响紧固效果和加大攻丝难度; 攻丝时,用力要均匀并垂直于安装面,注意排屑,防止丝锥断裂造成数铣返工的现象。 f)根据上序提供的导板/导滑面数值及测量的导板厚度数值初计算相对 应导板/导滑面配合间隙值; g)在凸模导板上均匀涂色(红丹或蓝油),将压边圈用天车平稳吊起套 在凸模上,吊起、落下反复数次,观察导滑面着色情况,估计凸模与 压边圈相对应导板配合间隙;用相同方法估计上模与压边圈相对应导 板配合间隙; h)根据初计算值及着色情况确定导滑面推光量,间隙小于0.03mm时用 120#油石推光导滑面无刀痕;在0.03-0.05mm时用180#油石推光导滑 面隐约见刀痕,大于0.05mm时用120#油石推光导滑面不保留刀痕并 将导板间隙垫至0.03-0.05mm。 四、敦死垫、调整垫及顶杆垫块的安装
冲压工艺学课件
绪论 容简介: 本章讲述冲压及模具的概念;冲压的特点、发展及应用,冲压工序的分类及基本冲压工序。 学习目的与要求: 1、掌握冲压及模具的概念; 2、了解冲压冲压的特点、发展及应用; 3、掌握冲压工序的分类,认识基本冲压工序。 重点: 冲压及模具的概念、冲压的特点、发展及应用,冲压工序的分类。 难点:冲压基本工序。 1.1 冲压的概念 1.1.1 冲压 冲压:在室温下,利用安装在压力机上的模具对被冲材料施加一定的压力,使之产生分离和塑性变形,从而获得所需要形状和尺寸的零件(也称制件)的一种加工方法。因为通常使用的材料为板料,故也常称为板料冲压。 冲压成形产品示例一——日常用品:易拉罐、餐盘、垫圈等。 冲压成形产品示例二——兵器产品:子弹壳等。 冲压成形产品示例三——高科技产品:汽车覆盖件、飞机蒙皮等。 1.1.2 冲模
冲压模具:将材料加工成所需冲压件的一种工艺装备,称为冲压模具(俗称冲模) 1.1.2 冲压生产的三要素: 冲压生产的三要素:合理的冲压工艺、先进的模具、高效的冲压设备 1.2 冲压加工特点与应用 1.2.1 冲压加工的特点 (1)生产率高、操作简单。高速冲床每分钟可生产数百件、上千件。 (2)一般无需进行切削加工,节约原料、节省能源。 (3)冲压件的尺寸公差由冲模来保证,产品尺寸稳定、互换性好。“一模一样” (4)冲压产品壁薄、量轻、刚度好,可以加工形状复杂的小到钟表、大到汽车纵梁、覆盖件等。 局限性:由于冲模制造是单件小批量生产,精度高,是技术密集型产品,制造成本高。因此,冲压生产只适应大批量生产。 1.2.2 冷冲压的应用 由于冷冲压在技术上和经济上的特别之处,因而在现代工业生产中占有重要的地位。在汽车、拖拉机、电器、电子、仪表、国防、航空航天以及日用品中随处可见到冷冲压产品。如不锈钢饭盒,搪瓷盆,高压锅,汽车覆盖件,冰箱门板,电子电器上的金属零件,枪炮弹壳等等。据不完全统计,冲压件在汽车、拖拉机行业中约占60%,在电子工业中约占85%,而在日用五金产品中占到约90%。
最新冲压工艺及模具设计学习
冲压工艺及模具设计 学习
《冲压工艺及模具设计》课程学习指南 20 —20 学年第学期 机学生使用 任课教师:王芳 一、课程基本情况、性质、研究对象和任务 总学时:40学时课堂教学:36学时实验教学:4学时 先修课:机械设计金属与塑料成型设备 《冲压工艺及模具设计》是高等工业院校材料成型方向开设的一门主干专业技术课,也是制造类其它专业的一门重要选修课。它是一门将冲压成形加工原理、冲压设备、冲压工艺、冲模设计与冲模制造有机融合,综合性和实践性较强的课程。本课程的主要任务是分析各类冲压成形的变形规律,认识典型冲压成形工艺方法和模具结构,掌握冲压工艺与模具设计方法。 通过本课程学习,使学生在下列能力培养方面得到锻炼与提高: 1.能应用冲压变形理论,分析中等复杂冲压件变形特点,制定合理冲压工艺规程。 2.协调冲压设备与模具的关系,选择冲压设备的能力。 3.熟悉掌握冲模设计计算方法,具备中等复杂冲模结构选择和设计的能力,所设计的冲模应工作可行、操作方便、便于加工和装配,技术经济性好。 二、教材处理 本课程选用机械工业出版社出版,姜奎华主编的《冲压工艺及模具设计》。本教材内容比较全面,结构编排严谨。但由于学时限制不可能对所有教材内容一一详细讲解。所以应紧
紧抓住本课的重点内容,搞清模具设计的有共性的规律,从而能做到举一反三,逐类旁通,为今后的学习工作打下基础。 三、学习参考书 1.刘建超、张宝忠主编.冲压模具设计与制造.北京:高等教育出版社,2004年 2.王孝培主编.冲压手册.北京:机械工业出版社,1990年 3.冲模设计手册编写组编著.冲模设计手册.北京:机械工业出版社,2000年 4.模具实用技术丛书编委会.冲模设计应用实例.北京:机械工业出版社,1994 5.冯炳尧、韩泰荣、蒋文森编.模具设计与制造简明手册(第二版).上海科学技术出版社,1998年 6.模具设计与制造技术教育丛书编委会.模具制造工艺与装备.北京:机械工业出版社,2003年7.国家技术监督局.冲模模架.北京:中国标准出版社,1991 8.许发越主编.模具标准应用手册.北京:机械工业出版社,1994年 9.李天佑主编.冲模图册.北京:机械工业出版社, 1988 四、关于考试的说明 期末考试:100% 五、各次课基本内容,重点难点,自我测验及作业
最新汽车覆盖件冲压模具设计
目录 关键词:刹车片附件弯曲冲压模 (1) Key words:Brake Accessory;Bending ;Punching Die; (2) 第1章零件的工艺性分析和工艺方案的确定 (3) 1.2 确定冲裁工艺方案 (4) 1.3 模具结构形式的确定 (5) 第2章模具设计工艺计算 (5) 2.1毛坯尺寸的计算 (6) 2.2 回弹量的计算及弯曲参数的选择 (6) 2.3排样、步距的确定 (7) 2.3.2步距 (7) 2.4材料利用率的计算 (8) 第3章冲裁力的计算 (8) 3.1 冲裁部分冲压力的计算 (8) 3.1.1切断时冲裁力的计算 (8) 3.1.2冲孔时冲裁力的计算 (8) 3.1.3 卸料力、推件力的计算 (9) 3.2弯曲部分冲压力的计算 (9) 3.2.1弯曲力的计算 (9) 3.2.2 顶件力的计算 (10) 第4章模具压力中心与计算 (11) 第5章工作部分尺寸计算 (13) 5.1冲裁间隙 (13) 5.1.1 间隙对尺寸精度及模具寿命的影响 (14) 5.1.2 合理间隙值的确定原则 (14) 5.1.3 合理间隙值的确定 (15)
5.2冲裁模刃口尺寸的计算 (15) 5.2.1 凸、凹模刃口尺寸计算原则 (15) 5.2.2 冲裁凸、凹模刃口尺寸计算 (15) 5.3弯曲刃口尺寸的计算 (17) 5.3.1 凸、凹模圆角半径的确定 (18) 5.3.2 凹模深度的确定 (19) 第7章压力机的校核 (35)
汽车覆盖件冲压模设计 摘要:本次设计是从汽车覆盖件模板支架的工艺性分析开始,根据工艺要求来确定设计的基本思路。在分析冲压变形过程及冲压件质量影响因素的基础上,经过方案比较,选择级进冲模作为该模具工艺生产方案。然后设计模具的工作部分,即凸、凹模的设计。包括冲压工艺计算、工艺方案制订和冲模设计以及典型零件的工艺分析。 设计中涉及冲压变形过程分析、冲压件质量及影响因素、间隙确定、刃口尺寸计算原则和方法、排样设计、冲压力与压力中心计算、冲压工艺性分析与工艺方案制定、冲压典型结构、零部件设计及模具标准应用、冲模设计方法与步骤等。根据模具的装配原则,完成模具的装配,装配模具试冲通过试冲可以发现模具设计和制造的不足,并找出原因给予纠正,并对模具进行适当的调整和修理,本冲压模设计完全能生产出合格的零件。 关键词:汽车覆盖件冲压模 The Design of Punching Die for Brake Accessory
2020年(工艺技术)冲压工艺学
绪论 内容简介: 本章讲述冲压及模具的概念;冲压的特点、发展及应用,冲压工序的分类及基本冲压工序。 学习目的与要求: 1、掌握冲压及模具的概念; 2、了解冲压冲压的特点、发展及应用; 3、掌握冲压工序的分类,认识基本冲压工序。 重点: 冲压及模具的概念、冲压的特点、发展及应用,冲压工序的分类。 难点:冲压基本工序。 1.1 冲压的概念 1.1.1 冲压 冲压:在室温下,利用安装在压力机上的模具对被冲材料施加一定的压力,使之产生分离和塑性变形,从而获得所需要形状和尺寸的零件(也称制件)的一种加工方法。因为通常使用的材料为板料,故也常称为板料冲压。 冲压成形产品示例一——日常用品:易拉罐、餐盘、垫圈等。 冲压成形产品示例二——兵器产品:子弹壳等。 冲压成形产品示例三——高科技产品:汽车覆盖件、飞机蒙皮等。 1.1.2 冲模
冲压模具:将材料加工成所需冲压件的一种工艺装备,称为冲压模具(俗称冲模) 1.1.2 冲压生产的三要素: 冲压生产的三要素:合理的冲压工艺、先进的模具、高效的冲压设备 1.2 冲压加工特点与应用 1.2.1 冲压加工的特点 (1)生产率高、操作简单。高速冲床每分钟可生产数百件、上千件。 (2)一般无需进行切削加工,节约原料、节省能源。 (3)冲压件的尺寸公差由冲模来保证,产品尺寸稳定、互换性好。“一模一样” (4)冲压产品壁薄、量轻、刚度好,可以加工形状复杂的小到钟表、大到汽车纵梁、覆盖件等。 局限性:由于冲模制造是单件小批量生产,精度高,是技术密集型产品,制造成本高。因此,冲压生产只适应大批量生产。 1.2.2 冷冲压的应用 由于冷冲压在技术上和经济上的特别之处,因而在现代工业生产中占有重要的地位。在汽车、拖拉机、电器、电子、仪表、国防、航空航天以及日用品中随处可见到冷冲压产品。如不锈钢饭盒,搪瓷盆,高压锅,汽车覆盖件,冰箱门板,电子电器上的金属零件,枪炮弹壳等等。据不完全统计,冲压件在汽车、拖拉机行业中约占60%,在电子工业中约占85%,而在日用五金产品中占到约90%。
冲压工艺及模具设计与制造
冲压工艺及模具设计与制造 doc文档可能在WAP端扫瞄体验不佳。建议您优先选择TXT,或下载源文件到本机查看。 冲压工艺及模具设计与制造》拆装与测绘指导冲压工艺及模具设计与制造》 1模具折装测绘的目的关心学生了解模具内部结构及感性知识。( 1 ) 关心学生了解模具内部结构及感性知识。 搞清模具零件的名称结构及常用材料和一样热处理要求。1) 搞清模具零件的名称结构及常用材料和一样热处理要求。 搞清模具零件的相互联接与配合关系。2) 搞清模具零件的相互联接与配合关系。 搞清典型模具的结构及组成。3) 搞清典型模具的结构及组成。培养学 生的实践动手能力。( 2 ) 培养学生的实践动手能力。 ( 3 ) 复习巩固制图知识 2冷冲压模拆装与测绘的任务拆开模具测画模具非标准件的零件图。( 1 ) 拆开模具测画模具非标准件的零件图。 非标准件包括:凸模、凹模,凸凹模、固定板、卸料板、垫板、侧刃及侧刃挡非标准件包括:凸模、凹模,凸凹模、固定板、卸料板、垫板、料(始用挡块、固定挡料) 、导料板、承料板、模柄、推板、打板、上下模座等。始用挡块、固定挡料) 、导料板、承料板、模柄、推板、打板、上下模座等。 )、导料板 画模具装配图。( 2 ) 画模具装配图。 3注意事项 ( 1 ) 不准用锒头直截了当敲打模具,防止模具零件变形。不准用锒头直截了当敲打模具,防止模具零件变形。 ( 2 )分开模具前要将各零件接联接关系做好记号。分开模具前要将各零件接联接关系做好记号。 上下模座的导柱,导套不要拆开,( 3 )上下模座的导柱,导套不要拆开,上模座与导套,下模座与导柱不要拆
开,否则不能还原。否则不能还原。画模具装配图时,应打开上模画下模的府视图。( 4 )画模具装配图时,应打开上模画下模的府视图。 装配图的右上角为冲件工序图,工序图的下边为排样图。( 5 )装配图的右上角为冲件工序图,工序图的下边为排样图。 模具零件可不标公差和表面粗糙度,但要注明零件名称,( 6 )模具零件可不标公差和表面粗糙度,但要注明零件名称,材料及必要的热处理要求。 处理要求。 4冷冲压模具拆装与测绘过程 ( 1 )级进模拆装过程用撬杠或铜棒分开下下模。1)用撬杠或铜 棒分开下下模。拆开下模(凹模部分)2)拆开下模(凹模部分)由 下模座面向凹模方向打出销钉,卸下螺钉,分开凹模和下模座。 (a )由下模座面向凹模方向打出销钉,卸下螺钉,分开凹模和下模座。卸下螺钉,导料板与凹模的销钉,使导料板和凹模分开。(b )卸下螺钉,导料板与凹模的销钉,使导料板和凹模分开。 测画下模各零件。(c )测画下模各零件。 3)拆开上模(凸模部分)拆开上模(凸模部分) (a )卸下卸料螺钉,取下卸料板。卸下卸料螺钉,取下卸料板。 由上模底顶面向固定板方向打出销钉,卸下螺钉、分开上模座、 (b )由上模底顶面向固定板方向打出销钉,卸下螺钉、分开上模座、上垫板和凸模及固定板。和凸模及固定板。将凸模从固定模板中打出。 (c )将凸模从固定模板中打出。 将模柄从上模座中打出。(d )将模柄从上模座中打出。 测画上模各零件。(e )测画上模各零件。 4)组装模具 将模柄装入上模座待用。(a )将模柄装入上模座待用。将凸模装入固 定板待用。(b )将凸模装入固定板待用。组装下模。(c )组装 下模。 ① 将凹模放在下模座上,初步拧紧螺钉,装入销钉后再将螺钉拧紧。 将凹模放在下模座上,初步拧紧螺钉,装入销钉后再将螺钉拧紧。
限位板冲压模具设计
限位板冲压模具设计 1.1 模具市场发展趋势 模具,是工业生产的基础工艺装备,在电子、汽车、电机、电器、仪表、家电和通讯等产品中,60%—80%的零部件都依靠模具成形,模具质量的高低决定着产品质量的高低,因此,模具被称之为“百业之母”。模具又是“效益放大器”,用模具生产的最终产品的价值,往往是模具自身价值的几十倍、上百倍。 模具生产的工艺水平及科技含量的高低,已成为衡量一个国家科技与产品制造水平的重要标志,它在很大程度上决定着产品的质量、效益、新产品的开发能力,决定着一个国家制造业的国际竞争力。 我国模具工业的技术水平近年来也取得了长足的进步。大型、精密、复杂、高效和长寿命模具上了一个新台阶。大型复杂冲模以汽车覆盖件模具为代表,已能生产部分新型轿车的覆盖件模具。体现高水平制造技术的多工位级进模的覆盖面,已从电机、电器铁芯片模具,扩展到接插件、电子枪零件、空调器散热片等家电零件模具。在大型塑料模具方面,已能生产48英寸电视的塑壳模具、6.5K g
大容量洗衣机全套塑料模具,以及汽车保险杠、整体仪表板等模具。在精密塑料模具方面,已能生产照相机塑料模具、多型腔小模数齿轮模具及塑封模具等。在大型精密复杂压铸模方面,国内已能生产自动扶梯整体踏板压铸模及汽车后桥齿轮箱压铸模。其他类型的模具,例如子午线轮胎活络模具、铝合金和塑料门窗异型材挤出模等,也都达到了较高的水平,并可替代进口模具。 根据国内和国际模具市场的发展状况,有关专家预测,未来我国的模具经过行业结构调整后,将呈现十大发展趋势:一是模具日趋大型化;二是模具的精度将越来越高;三是多功能复合模具将进一步发展;四是热流道模具在塑料模具中的比重将逐渐提高;五是气辅模具及适应高压注射成型等工艺的模具将有较大发展;六是模具标准化和模具标准件的应用将日渐广泛;七是快速经济模具的前景十分广阔;八是压铸模的比例将不断提高,同时对压铸模的寿命和复杂程度也将提出越来越高的要求;九是塑料模具的比例将不断增大;十是模具技术含量将不断提高,中高档模具比例将不断增大,这也是产品结构调整所导致的模具市场未来走势的变化 1.2 冲压模具的现状和技术发展 一、现状 改革开放以来,随着国民经济的高速发展,市场对模具的需求量不断增长。近年来,模具工业一直以15%左右的增长速度快速发展,模具工业企业的所有制成分也发生了巨大变化,除了国有专业模具厂外,集体、合资、独资和私营也得到了快速发展。浙江宁波和黄岩地区的“模具之乡”;广东一些大集团公司和迅速崛起的乡镇企业,科龙、美的、康佳等集团纷纷建立了自己的模具制造中心;中外合资和外商独资的模具企业现已有几千家。 随着与国际接轨的脚步不断加快,市场竞争的日益加剧,人们已经越来越认识到产品质量、成本和新产品的开发能力的重要性。而模具制造是整个链条中最基础的要素之一。 近年许多模具企业加大了用于技术进步的投资力度,将技术进步视为企业发展的重要动力。一些国内模具企业已普及了二维CAD,并陆续开始使用UG、 Pro/Engineer、I-DEAS、Euclid-IS等国际通用软件,个别厂家还引进了Moldflow、C-Flow、DYNAFORM、Optris和MAGMASOFT等CAE软件,并成功应用于冲压模的设计中。
冲压工艺及模具设计
《冲压工艺及模具设计》课程设计任务书 设计题目:“垫片”零件冲压工艺及模具设计 内容及任务: 一、设计的主要技术参数:见产品图 二、设计任务:完成该产品的冲压工艺方案、设计说明书、模具装配图及工作零件图。 三、设计工作量 1、制订冲压工艺方案 2、模具总装图1张,凸模及凹模零件图2张 3、设计说明书1份,20页左右 四、设计要求 1、图纸用CAD绘制并交纸质图及电子档 2、本任务书应与说明书、图纸一同装订成册,并加封面,装入资料袋中,否则不接收 3、设计必须认真仔细,允许讨论,但严禁抄袭、复制或复印。
名称:垫片 批量:大批量 材料:A3(Q235) 厚度:3mm 摘要 冲裁工艺在工业生产中应用广泛,冲压模具设计与制造技术是一项技术性和经验都很强的工作。本次课程设计任务书提供的零件图纸要求,用Auto CAD 进行设计分析。根据分析结果选择合理的冲压工艺和合理的模具结构,在此基础上优化零件结构和选择合适的零件材料。经过查阅资料,首先要对零件进行工艺分析,经过工艺分析和对比,采用落料工序,通过冲裁力、顶件力、卸料力等计算,确定压力机的型号。再分析对冲压件加工所需的模具类型,选择所需设计的模具类型。 本文首先叙述了冲压模具的发展状况,模具在现代工业中的作用,和在整个国民经济中的地位。说明了冲压模具的重要性与本次设计的意义,接着是简单说明了模具设计的基本概念和模具设计的一般步骤、模具的分类、模具零件的分
类、模具的结构形式、冲压的基本概念、冲压工艺基础理论、塑性力学基础理论。然后对冲压件进行工艺分析,完成了工艺方案的确定,对零件排样图的设计,完成了材料利用率的计算。再进行冲裁工艺力的计算和冲裁模工作部分的设计计算,为选择冲压设备提供依据。其次对主要零部件的设计和标准件的选择,为本次模具零件图的绘制和模具的成型提供依据,以及为装配图各尺寸提供依据。通过前面的设计方案画出模具各零件和装配图。 本次设计阐述了冲压复合模的结构设计及工件过程。本模具性能可靠,运行平稳,提高了产品质量和生产效率,降低劳动强度和生产成本。 关键字:冲孔;落料;倒装复合模;模具结构 冲压工艺及模具设计课程设计 一、原始数据 如图所示的垫片,外形直径D=80mm,内孔直径=40mm,厚度t=3mm,材料为A3(Q235),生产批量:大批量。 二、工艺分析 1、冲压工序 只有冲孔、落料两道工序。 2、材料性能