流涂机在铸造树脂砂砂型与砂芯生产中的

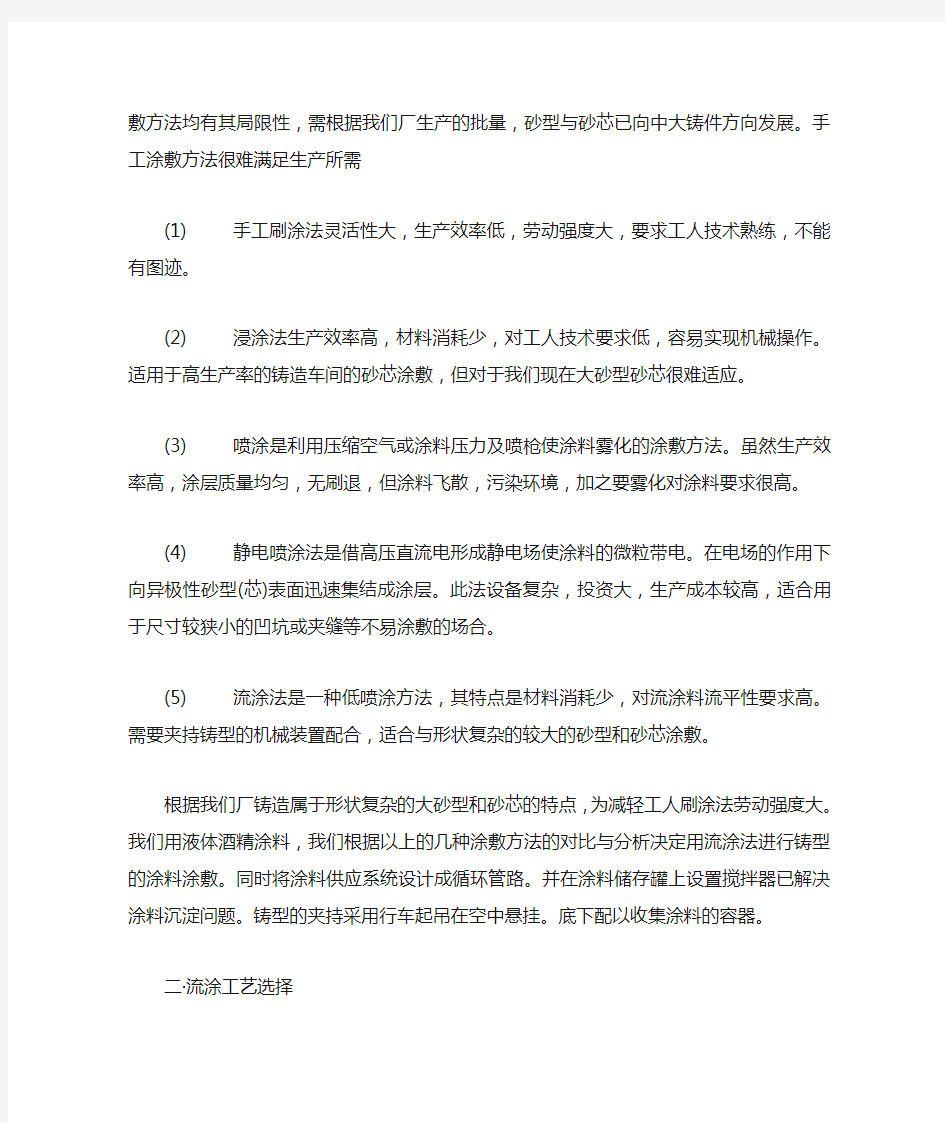
流涂机在铸造树脂砂砂型与砂芯生产中的应用
罗建昌
秦川机床工具集团有限公司
摘要:通过设计实例论述酒精涂料涂敷方法的确定及涂敷工艺的选择,喷涂系统设计方案和主要配套设备的确定。
关键词:涂料,喷涂工艺,喷涂系统
涂料是铸造生产过程中重要的辅助材料,在铸型的生产中有着重要的作用与呋喃树脂砂,自硬砂相配合。可以获得良好的铸件表面质量,防止铁水渗入砂型,对砂型,砂芯生产的大量气体形成阻挡界面。防止粘砂,气孔等铸造缺陷的出现。加固砂型,减少浇筑的冲砂现象产生冶金效应。改善铸件局部的表面性能和内在质量。
对于我厂多年的4万吨的铸件生产量。涂料涂敷方法各种各样。根据我厂生产的产品特点和使用材料的性能。经过我们多次工艺,技术的多次研究和反复实践。最后使用中压循环混气喷涂方案。在我厂的生产中取得了良好的效果。
一涂敷方法的确定
铸造生产中常用的涂料涂敷方法有,刷涂,浸涂,喷涂,流涂,静电喷涂等。各种涂敷方法均有其局限性,需根据我们厂生产的批量,砂型与砂芯已向中大铸件方向发展。手工涂敷方法很难满足生产所需
(1)手工刷涂法灵活性大,生产效率低,劳动强度大,要求
工人技术熟练,不能有图迹。
(2)浸涂法生产效率高,材料消耗少,对工人技术要求低,
容易实现机械操作。适用于高生产率的铸造车间的砂芯
涂敷,但对于我们现在大砂型砂芯很难适应。
(3)喷涂是利用压缩空气或涂料压力及喷枪使涂料雾化的涂
敷方法。虽然生产效率高,涂层质量均匀,无刷退,但
涂料飞散,污染环境,加之要雾化对涂料要求很高。
(4)静电喷涂法是借高压直流电形成静电场使涂料的微粒带
电。在电场的作用下向异极性砂型(芯)表面迅速集结成
涂层。此法设备复杂,投资大,生产成本较高,适合用
于尺寸较狭小的凹坑或夹缝等不易涂敷的场合。
(5)流涂法是一种低喷涂方法,其特点是材料消耗少,对流
涂料流平性要求高。需要夹持铸型的机械装置配合,适
合与形状复杂的较大的砂型和砂芯涂敷。
根据我们厂铸造属于形状复杂的大砂型和砂芯的特点,为减轻工人刷涂法劳动强度大。我们用液体酒精涂料,我们根据以上的几种涂敷方法的对比与分析决定用流涂法进行铸型的涂料涂敷。同时将涂料供应系统设计成循环管路。并在涂料储存罐上设置搅拌器已解决涂料沉淀问题。铸型的夹持采用行车起吊在空中悬挂。底下配以收集涂料的容器。
二·流涂工艺选择
喷涂一般分为普通压缩气体喷涂,高压气体喷涂,混合喷涂三种方式。
(1)普通压缩空气喷涂是将压缩空气直接与涂料混合,或
者利用压缩空气对涂料加压而使其雾化的涂敷方法。
这种方法是最早使用的喷涂工艺。其设备简单对喷枪
磨损小。但涂料喷出速度高,产生大量回弹和飞散,
使涂料在空气中散失达50%既浪费材料,又污染环
境。
(2)高压气体喷涂是利用高压泵将涂料加压到20Mpa左
右。然后然后从特殊设计的喷嘴中喷出的涂敷方法。
高压涂料离开喷最后立即在空气中膨胀成很细的线
流。这种线流在表面张力的作用下,变成很细的微粒
喷射到工件表面,它对工件表面的撞击作用小,固体
微粒的回弹量少,涂料散失率低;但喷出的涂料量大,
涂层较厚。此方法发明与50年代,它对设备要求高,
喷嘴必须用硬质合金制造且要十分光洁,加工比较困
难。
(3)混气喷涂是70年代发明的一种较新的喷涂工艺。其
使用的设备与高压喷涂相似:利用压力泵将涂料加
压,然后送喷嘴中喷出。所不同的是,涂料压力较低,
一般为十几或几十大气压,只能对涂料进行部分雾
化;喷嘴上增设压缩空气帽利用少量从喷帽正面和角
上喷出来的压缩空气最终完成雾化作用,特殊设计的压缩空气帽使得压缩空气对雾化的涂料产生包覆作用。减少飞溅和散失。其特点:涂料在空气中散失降低到2%~3%左右,涂料喷出数量较少涂层较薄易获得精细涂层。对喷嘴相对磨损较少。
根据几种喷涂工艺的不同特点和我厂砂型和砂芯形状。我们选用中压混涂工艺。
三流涂系统设计
铸型流涂系统是由涂料混制,涂循环输送两个系统和相应自动控制设备,及辅助涂料收集器组成。各系统工作原理如下。
(1)涂料混制系统
涂料混制系统向涂料搅拌机输送载体溶液的气动泵开始。到混制好的涂料经气动泵送到储存罐为止。该系统采用气动双隔膜泵输送载体溶液。预置式数控定量表控制载体加入量,磅秤称量,人工添加耐火骨料涂料搅拌机混制涂料。气动双隔膜泵输送涂料其工艺流程如图一
涂料搅拌器采用专门的成品双速搅拌器,混制时先启动加“酒精”“涂料”。按工艺要求加入耐火骨料。耐火骨料沉淀沉淀在搅拌机底部,阻力较大,先低速搅拌,后高速搅拌,达到工艺要求后关闭涂料搅拌机。打开(涂料输送)空气泵的进气阀,将涂料输送到储存罐。
(2) 涂料循环输送系统
涂料循环输送系统自涂料
树脂砂铸造对模具工艺的要求
树脂砂铸造对模具工艺的要求 树脂砂铸造 2009-07-05 15:46 阅读169 评论0 字号:大中小 树脂砂铸造是指型(芯)砂在室温条件下,通过加入一定量的固化剂,使型、芯在芯盒或砂箱内自行硬化成型的一种造型、制芯的方法。目前在铸造生产中得到应用的有酸固化呋喃树脂砂、酯固化碱性酚醛树脂砂和酚尿烷树脂砂等。这些工艺的共同特点是:型(芯)砂有一定的可使用时间,硬化速度与强度受室温、环境湿度的影响较大,生产效率也不太高。它们比较适合于单件、小批量、多品种的中、大型铸件的生产,例如机床、通用、重型、造船、机车等行业。在上述几种树脂自硬砂中,以酸固化的呋喃树脂砂在我国应用最多,因为它所用的原辅材料及设备能成套供应,技术成熟,积累的经验也最为丰富,据不完全统计,目前全国约有500多家采用呋喃树脂砂工艺进行铸件生产。它与粘土砂相比,铸件尺寸精度可提高2~3级,表面粗糙度明显改善,废品率明显下降。 与传统的粘土砂生产铸件相比,用树脂砂生产的铸件具有表面粗糙度小,尺寸精度高,品质好的特点,已日益受到市场的青睐,得到了迅速发展,已逐步成为铸件市场的主流产品。树脂砂上世纪50年代开始在铸造行业出现和使用,到现在已经有几十年的历史了,其生产工艺和设备已相当成熟和完善。
砂温对树脂砂硬化的影响及控制 呋喃树脂自硬砂的硬化原理是:树脂在固化剂的催化作用下逐渐发生交联反应而自行硬化,固化剂的催化作用受温度的影响较大,温度升高催化作用加速,温度下降,催化作用减慢,因而呋喃树脂自硬砂在硬化过程中,硬化反应的速率与砂温有密切的关系,同时硬化反应速率对硬化后铸型的强度有着重要的影响。所以,要得到满足生产需要的铸型强度,就必须控制砂温。 固化剂的加入量和酸值对铸型的影响及控制 固化剂的加入量是按其占树脂的比例来确定的。在固化剂酸值一定的情况下固化剂加入量愈大,树脂砂的硬化速率就愈快,反之,愈慢。在固化剂加入量一定的情况睛,所用固化剂酸值愈高,树脂砂硬化速率愈快,反之,愈慢。树脂砂铸造的硬化速率过快或过慢,都会降低铸型硬化后的强度,因此必须合理控制树脂砂的硬化速度。 树脂砂铸造生产对模具工艺的要求 与粘土砂相比,树脂砂铸件的外观质量依赖于模具的质量,因而树脂砂对模具的质量要求较高。模具工艺时使其较好的适应树脂砂造型的需要,主要在以下几个方面: 1、拔模斜度:树脂砂在起模时已具有一定的硬化强度,较小的退让性,较大的摩擦力,若采用敲击的方法起模,容易损坏模具,同时树脂砂的可修补性差,起模时,若受到破坏,较难修补。采用树脂砂造型时,应根据生产实际和产品结构加大模具的拔模斜度,能顺利
铸造材料、铸造用呋喃树脂、铸造用覆膜砂最有实力的厂家
慧聪网专访:珠海福联公司总经理谢树忠 2006/12/26/17:43 来源:慧聪网涂料行业频道 珠海市斗门福联造型材料实业有限公司总经理:谢树忠 点击此处查看全部新闻图片 慧聪网:您能否简单地给我们介绍一下贵公司的基本情况吗? 谢树忠:我司成立于1993年,是国内最早专业从事铸造造型材料研究开发、生产销售和技术服务的高科技型企业之一,现已通过ISO9001。2000国际质量认证,是广东省铸造学会副理事长单位。公司现占地3。5万平方米。已建成年产呋喃树脂6千吨的生产能力,并正着手扩大至1万吨以上产能(该项目被列为广东省06-07年度重点扶持项目);扩大后将成为我国乃至亚洲最大的呋喃树脂星产基地之一。同时,已建成年产量5千吨固化剂、1。5万吨覆膜砂、5千吨铸造涂料、5千吨酚醛树脂、5千吨压铸辅助材料和熔剂的生产能力。我司设有研究所,有专职科研工程师范10名,拥有全套精良的检测及实验设施,我们的经营宗旨是“造成顾客满意产品,铸上帝追捧名牌”,“做行业领头羊”是我们的目标。我司以:“铸力”为注册商标的系列铸造、压铸材料产品畅销全国,远销东南亚,近十年来每年保持50%以上的增长率,现已成为了我国南方规模最大的新型铸造、压铸材料生产和研究基地,并正逐步成为国内乃至亚洲同行业的 龙头企业。 慧聪网:贵公司的产品优势是什么? 谢树忠:如果在同行中没有竞争优势,我们不可能保持连续十作年的快速发展,我认为我们在产品方面的优势主要表现在:(1)产品齐全:我司是国内最早从事新型铸造材料研发和生产的企业之一,多年来瞄准市场需求大力通过自主创新,成功研发出呋喃树脂、固化剂、覆膜砂、酚醛树脂、涂料、压铸材料、熔剂等七大系列共150余个产品,产品种类齐全,使广大铸造成厂家可以实现“一站式购物”,我司几乎成为“铸造(含压铸)原辅材料超市”。(2)质量保证体系健全:人司多年前便已通过了ISO9000质量管理体
树脂砂铸造生产工艺
树脂砂铸造生产工艺 为规范树脂砂铸造的生产过程,严格执行操作工艺,减少因违反工艺或操作不当产生的废品和降低的铸件生产成本,特制定本生产操作工艺规程。本工艺规程适用于公司内所有树脂砂铸件的生产全过程和与之相关的各类操作人员。下面节选一部分供大家参考阅读。 工艺规程 主要原材料的技术要求或规格 3.1.1原砂(天然石英砂) 粒度:40/70目(中大件)或50/100目(一般件); 化学成分:SiO2 >90%、含泥量<%~%、含水量<~% 微粉含量(140目筛以下)<耗酸值<5ml、灼减量<5、粒型:圆形或多角形。 3.1.2再生砂 灼减量<%;耗酸值<;PH值<5 ; 200目筛底盘<1%;底盘量<%; 含水量<%; 粒形:圆形。 3.1.3咲喃树脂 含氮量~%; 24h抗拉强度〉;游离甲醛<%;粘度<;密度~1.25 g/cm3; 游离酚<%。 3.1.4固化剂 采用有机磺酸固化剂,其黏度一般控制在<,水不溶物的含量<%, 同时冷冻和随后的溶解之间要有可逆性。为了保证稳定的型砂可使用时间和硬化速度,可选用“ a+b”固化剂或根据季节不同选用不同酸度型号的固化剂。 3.1.5涂料
米用醇基涂料。要求涂料的固体含量高,粉料粒度细,粉料及黏结剂的耐火度高,抗爆热能力强等。具体工艺性能要求有:密度~1.35 g/cm3;黏度6~7s;悬浮性(2h) >97%;涂刷性、流平性、渗透性、抗裂性要好,涂层强度要高。对于表面球化有深度要求的铸件,应采用氧化镁涂料。 操作工艺规程 3.2.1再生砂准备 根据树脂砂再生设备的要求和工艺流程进行操作,获得满足工艺要求的再生砂。特别要注意控制好进入混砂机时的再生砂的温度,最好在25- 35C。 3.2.2砂、树脂、固化剂加入量的调整 (1)混砂机的流量测定 根据混砂机的设定要求,在正常的生产情况下,至少每四天进行一次流量测定。分别对相同时间内砂、树脂、固化剂的流量进行称量,掌握时间流量。并先将砂流量按混砂机的公称流量进行调整。 (2)树脂量的调整 根据砂流量调整树脂的加入量,树脂加入量一般控制在型砂重量的~%,厚大件取上限,中小件取下限。 (3)固化剂量的调整 固化剂加入量在正常情况下与砂温和车间环境温度有关,一般控制在树脂加入量的30~50%,高温时取下限,低温时取上限。放砂时间长的大件固化剂加入量取下限,以保证树脂砂有足够的可使用时间。 (4)混砂机的调整与准备 严格按《混砂机操作规程》进行设备的日常维护保养,特别是要及时清理搅笼内的叶片和内壁。每天放砂前应将树脂,固化剂泵单独循环1~2分
树脂砂铸造过程中应注意的几个问题
树脂砂铸造过程中应注意的几个问题 兖矿集团大陆机械有限公司华铸分公司 史明华 由于自硬树脂砂铸造具有生产出的铸件表面质量好、尺寸精度高、废品率低,适用范围广、对工人技术水平要求低,大大减轻了工人的劳动强度和改善工作环境等优点,因此国内越来越多的公司(或企业)选择自硬树脂砂铸造手段。虽然自硬树脂砂铸造技术已经成熟,但在生产过程中仍然存在许多问题。我公司于2002年新上一条年产3000吨铸铁件的自硬树脂砂生产线,经过四年多来的不断探索,本人认为在自硬树脂砂铸造生产过程中,需要注意以下几个问题。 一、要经常注意设备的运行情况 设备运行情况的好坏,直接影响着铸造生产成本和铸件质量,因此,在铸造生产中,要经常注意设备的运行情况,发现运行异常及时分析解决,着重应注意以下两方面: 1、要注意除尘设备的运行 除尘设备的好坏,直接影响着再生砂的再生成本和铸件质量,在铸造生产中,除尘设备运行出现异常往往不易发现,但如果除尘设备的除尘效果不好,不但影响着工作环境、污染空气,更重要的是影响着再生砂的微粉含量,其直接结果是导致混砂时树脂加入量的增加和由于透气性差造成铸件废品率增多。 2、要注意混砂设备的运行 混砂机是否能够正常运行,直接影响着混砂的质量,其中液料(树脂、固化剂)的加入量最为关键。一般情况下,树脂的加入量是靠控制齿轮泵电机的电压、固化剂的加入量是靠控制隔膜泵电机的电压来实现的,由于季节、天气的变化,造成液料粘度的变化,在相同电压的情况下,液料的加入量会产生波动,且固化剂易产生结晶,造成阀及管道堵塞,因此,应每班对液料管道进行清理,每周对液料的加入量进行检测,以确保液料加入量的准确。 二、要注意制定的生产工艺的正确性及合理性 生产工艺制定的合理与否,直接影响着铸件的成品率、铸件质量和铸造成本,在制定生产工艺时,主要应注意以下几项: 1、确定合适的再生砂的LOI值 LOI值即灼烧减量是衡量再生砂的脱膜率的重要指标,也是与型砂的发气量及铸件产生气孔类缺陷密切相关的指标,铸铁件一般采用呋喃树脂砂生产,实践证明LOI值控制在3%左右完全可以满足生产要求,而过分降低LOI值意义不大。我公司在生产过程中,逐步将LOI 127
树脂砂铸造生产工艺
树脂砂铸造生产工艺 为规树脂砂铸造的生产过程,严格执行操作工艺,减少因违反工艺或操作不当产生的废品和降低的铸件生产成本,特制定本生产操作工艺规程。本工艺规程适用于公司所有树脂砂铸件的生产全过程和与之相关的各类操作人员。下面节选一部分供大家参考阅读。 工艺规程 3.1 主要原材料的技术要求或规格 3.1.1原砂(天然石英砂) 粒度:40/70目(件)或50/100目(一般件); 化学成分:SiO2 >90% 、含泥量<0.2%~0.3% 、含水量 <0.1~0.2%;微粉含量(140目筛以下) ≤0.5~1.0%、耗酸值<5ml 、灼减量<5、粒型:圆形或多角形。 3.1.2再生砂 灼减量<3.0%;耗酸值<2.0ml;PH值<5 ;200目筛底盘<1%;底盘量<0.2%;含水量<0.2%; 粒形:圆形。 3.1.3呋喃树脂 含氮量2.0~5.0%;24h抗拉强度>1.5MPa;游离甲醛<0.3%;粘度<60mPa.s;密度1.15~1.25 g/cm3;游离酚<0.3%。 3.1.4固化剂 采用有机磺酸固化剂,其黏度一般控制在<200mPa.s,水不溶物的含量<0.1%,同时冷冻和随后的溶解之间要有可逆性。为了保证稳定的型砂可使用时间和硬化速度,可选用“a+b”固化剂或根据季节不同选用不同酸度型号的固化剂。
3.1.5涂料 采用醇基涂料。要求涂料的固体含量高,粉料粒度细,粉料及黏结剂的耐火度高,抗爆热能力强等。具体工艺性能要求有:密度 1.25~1.35 g/cm3;黏度6~7s;悬浮性(2h)>97%;涂刷性、流平性、渗透性、抗裂性要好,涂层强度要高。对于表面球化有深度要求的铸件,应采用氧化镁涂料。 3.2操作工艺规程 3.2.1再生砂准备 根据树脂砂再生设备的要求和工艺流程进行操作,获得满足工艺要求的再生砂。特别要注意控制好进入混砂机时的再生砂的温度,最好在25-35℃。 3.2.2砂、树脂、固化剂加入量的调整 (1)混砂机的流量测定 根据混砂机的设定要求,在正常的生产情况下,至少每四天进行一次流量测定。分别对相同时间砂、树脂、固化剂的流量进行称量,掌握时间流量。并先将砂流量按混砂机的公称流量进行调整。 (2)树脂量的调整 根据砂流量调整树脂的加入量,树脂加入量一般控制在型砂重量的0.8~1.2%,厚大件取上限,中小件取下限。 (3)固化剂量的调整 固化剂加入量在正常情况下与砂温和车间环境温度有关,一般控制在树脂加入量的30~50%,高温时取下限,低温时取上限。放砂时间长的大件固化剂加入量取下限,以保证树脂砂有足够的可使用时间。 (4)混砂机的调整与准备
铸造用自硬呋喃树脂简介
简介 自硬呋喃树脂达到国际先进水平,是环保型产品,品种齐全,适用于铸造各种类型的铸钢、铸铁及有色合金件。外观颜色从淡黄色至棕红色液体,具有以下特点: a、粘度低,便于计量,易混砂,型砂流动性好。 b、游离甲醛含量低,气味小,改善了工人工作条件,减少了环境污染。 c、比强度高,可降低树脂加入量,降低成本,同时有利干提高铸件质量。 d、型砂的溃散性好,减少清砂工作量。 e、生产的铸件尺寸精度高,轮廓清晰,表面光洁,减少清砂工时,提高劳动效率。 型号及技术指标 使用指南 a、混砂工艺 树脂加入量一般为0.6-1.5%(占砂重),固化剂加入量般为30-70%(占树脂重),用连续式或间歇式混砂机先将砂子和固化剂混匀,然后再加入树脂混匀,混砂时间一般为5-60秒,混匀后立即出砂使用。 b、树脂加入量的选择 由于各使用厂家所用的原砂粒形、粒度、含泥量等指标差别较大,型、芯的重量及复杂程度不同,树脂的加入量应以满足生产需要为原则,在强度满足生产要求的前提下尽量减少树脂的加入量。 c、脱模时间的控制 控制适当的固化速度,有助于提高型、芯强度。脱模时间可在10-90分钟内调整,一般15-40分钟,脱模达不到预定的脱模时间会产生粘模甚至损坏型、芯或塌箱;脱模超过预定的脱模时间则脱模困难甚至会损坏型、芯或模型。
d、固化速度控制 固化速度过慢,适当增加固化剂的加入量(一般不宜超过70%)或更换固化速度更快的固化剂;固化速度过快,适当减少固化剂的加入量(一般不宜低于30%)或更换固化速度更慢的固化剂。 注意事项 a、树脂与固化剂应分开存放,严禁树脂与固化剂直接混合,以防产生爆炸! b、当树脂与皮肤接触时。可能会对个别人体产生轻微刺激作用,操作者应穿戴防护手套等用品。 c、树脂应密闭储存于阴凉、干燥处,避免受热或日光照射,搬运应小心轻放。 包装 240Kg铁桶或1000Kg塑料罐。
树脂砂混砂机常见问题解决及维护
树脂砂混砂机常见问题解决及维护 树脂砂混砂机使用中常见问题的解决 一>出砂量小 1.检查砂库是否存有砂子(主电控柜面板上有缺砂报警装置)。 2.重新校验混砂机出砂量(参见混砂机说明书的操作规程)。 3.混砂机叶片磨损严重,对磨损严重的叶片进行高度调整或重新更换新叶片。4.混砂机搅笼内长时间没有清理,造成残砂结块,在混砂时致使混砂空间小,造成出砂量小。 二>固化不均匀 1.树脂及固化剂比例是否均匀。 2.固化剂泵或树脂泵的管接头是否有漏气现象。 3.供气气源的压力是否满足要求(0.4-0.6MPa)。 4.固化剂泵、树脂泵、液料阀是否有磨损需更换的地方。 5.树脂或固化剂杂质太多造成泵及管路的堵塞。 6.检查混砂机叶片是否有需要更换的地方。 7.由于固化过程砂子的温度、树脂质量、固化剂的加入量,周围环境温度都有一定的关系,检查以上条件是否有变化。 机器的安全维护 1、每班结束必须清理混砂搅笼体和叶片; 2、必须经常清理出砂口,否则出砂口会逐渐变小; 3、较长时间不用时,须将树脂和固化剂管路清洗干净; 4、泵、电机等外购件要按其使用要求进行保养,各润滑点要按要求定期加油;传动轴承每3个月至少加注一次黄油。 5、混砂过程中如遇停电,为避免混砂搅笼中砂子硬化,必须将对开式搅笼打开,清理干净搅笼中的砂子; 6、机器每月应进行一次小修,检查易损件部位的磨损情况,及时更换易损件,
要经常注意搅笼叶片的磨损情况,及时更换,否则将影响混砂质量; 7、经常检查设备上螺钉、螺母的联结情况,如有松动,应及时 拧紧; 8、经常检查电器、线路及接头,以免由于接头松动或电线绝缘 破坏造成事故; 9、经常检查管路、电气系统各元件有无损坏,不得有漏液、漏气等现象; 10、液料桶应防止尘垢进入。 11、经常检查搅笼叶片是否松动,如有松动应及时拧紧。
树脂砂铸造生产工艺修订稿
树脂砂铸造生产工艺 WEIHUA system office room 【WEIHUA 16H-WEIHUA WEIHUA8Q8-
树脂砂铸造生产工艺 为规范树脂砂铸造的生产过程,严格执行操作工艺,减少因违反工艺或操作不当产生的废品和降低的铸件生产成本,特制定本生产操作工艺规程。本工艺规程适用于公司内所有树脂砂铸件的生产全过程和与之相关的各类操作人员。下面节选一部分供大家参考阅读。 工艺规程 主要原材料的技术要求或规格 3.1.1原砂(天然石英砂) 粒度:40/70目(中大件)或50/100目(一般件); 化学成分:SiO2 >90% 、含泥量<%~% 、含水量 <~%;微粉含量(140目筛以下) ≤~%、耗酸值<5ml 、灼减量<5、粒型:圆形或多角形。 3.1.2再生砂 灼减量<%;耗酸值<;PH值<5 ;200目筛底盘<1%;底盘量<%;含水量<%;粒形:圆形。 3.1.3呋喃树脂 含氮量~%;24h抗拉强度>;游离甲醛<%;粘度<;密度~1.25 g/cm3;游离酚<%。 3.1.4固化剂 采用有机磺酸固化剂,其黏度一般控制在<,水不溶物的含量<%,同时冷冻和随后的溶解之间要有可逆性。为了保证稳定的型砂可使用时间和硬化速度,可选用“a+b”固化剂或根据季节不同选用不同酸度型号的固化剂。 3.1.5涂料
采用醇基涂料。要求涂料的固体含量高,粉料粒度细,粉料及黏结剂的耐火度高,抗爆热能力强等。具体工艺性能要求有:密度~1.35 g/cm3;黏度6~7s;悬浮性(2h)>97%;涂刷性、流平性、渗透性、抗裂性要好,涂层强度要高。对于表面球化有深度要求的铸件,应采用氧化镁涂料。 操作工艺规程 3.2.1再生砂准备 根据树脂砂再生设备的要求和工艺流程进行操作,获得满足工艺要求的再生砂。特别要注意控制好进入混砂机时的再生砂的温度,最好在25-35℃。 3.2.2砂、树脂、固化剂加入量的调整 (1)混砂机的流量测定根据混砂机的设定要求,在正常的生产情况下,至少每四天进行一次流量测定。分别对相同时间内砂、树脂、固化剂的流量进行称量,掌握时间流量。并先将砂流量按混砂机的公称流量进行调整。 (2)树脂量的调整 根据砂流量调整树脂的加入量,树脂加入量一般控制在型砂重量的~%,厚大件取上限,中小件取下限。 (3)固化剂量的调整固化剂加入量在正常情况下与砂温和车间环境温度有关,一般控制在树脂加入量的30~50%,高温时取下限,低温时取上限。放砂时间长的大件固化剂加入量取下限,以保证树脂砂有足够的可使用时间。 (4)混砂机的调整与准备 严格按《混砂机操作规程》进行设备的日常维护保养,特别是要及时清理搅笼内的叶片和内壁。每天放砂前应将树脂,固化剂泵单独循环1~2分钟,并注意检查固化剂加入孔是否有结晶堵塞现象。
浅谈树脂砂铸造中的砂芯涂刷工艺
浅谈树脂砂铸造中的砂芯涂刷工艺 摘要:涂料是影响树脂砂铸件质量的一个重要因素,对树脂砂型芯所用涂料性能和施涂工艺的正确认识,并且以此选用性能优良的涂料和正确的施涂工艺,是获得优质树脂砂铸件必不可缺少的条件。本文阐述了树脂砂铸造中的砂芯涂刷工艺的一些问题和改进措施。 关键词:树脂砂铸造,涂料,涂刷工艺,砂芯 树脂砂是铸造中常用的造型、制芯方法之一,适用于多品种、小批量铸件的生产,具有流动性好,浇出的铸件尺寸精度高,表面光洁度好,浇注后的型砂溃散性好,容易再生等特点,在机床、水利机械、工程机械、矿石机械等领域普遍使用。树脂砂铸件在铸造过程中,涂料与涂刷工艺是影响铸件表面质量的重要因素,需要重点关注。 一、涂料的作用和选择 在铸造过程中,是否使用涂料需要考虑到清沽费用、修整费用和废品率等铸件成本后决定。一般来说,涂料可以起到防止渗漏,防止冲砂,防止粘砂,改善铸件表面质量,降低清沽费用,减少废品率等作用。铸型涂料与一般涂料不同之处在于,铸型涂料受得了高温融化的金属,并且在融化的金属与铸型之间形成一个阻隔层。通常来说,铸型涂料是把高熔点物质或者耐火物质悬浮在液体当中,当然,除了有耐火物质,铸型涂料还含有其他很多成分。 在实际生产中,铸型涂料必须具有以下特质:①具有优良的触变性、流平性、渗透性、涂敷性,涂层无刷、流痕等;②涂料具有优良的悬浮稳定性,水基涂料6小时悬浮性达到99%以上。③涂料具有很好的抗粘砂性能,浇注出的铸件表面光洁度好,轮廓清楚、无粘砂。④涂料的使用方法简单方便,可用于刷涂、喷涂、浸涂、流涂等工艺。⑤涂层烘干后,具有较高的强度和高温抗裂性,1300℃爆热1~2分钟涂层不开裂、不起泡。⑥涂料质量稳定、使用方便,特别是浅(白)色涂料,对改善劳动环境有显著效果。 为了不让涂料过多的渗入到砂型深处,影响涂层的干燥程度,并保证涂层厚度,提高抗金属液渗透的能力,涂料必须有一定的浓度,在涂刷性能良好的情况下,应保证涂料浓度并在涂刷前搅匀。
混砂机
混砂机 机自02班刘高禹 2010013104 混砂机的定义 混砂机(sand mixer)是使型砂中各组分均匀混合,并使黏结剂有效地包覆在砂粒表面的设备。混砂机利用碾轮与碾盘的相对运动,将置于两者间的物料受到碾压兼磨削的作用而粉碎物料,混砂机在粉碎物料的同时还将物料混合,是生产免烧砖、灰砂砖、水泥砖、耐火砖、粉碎和混合粉煤灰、锅炉炉渣、尾矿渣及工业废渣作制砖原料的理想设备。 在混制型砂(芯砂)过程中,应满足一下两个基本要求:第一,型砂中各组分均匀混合;第二,使粘结剂有效地包覆在砂粒表面。为达到这两个基本要求,混砂机应具有搅拌、碾压和磋压的作用。 我国混砂机的发展史 我国的混砂机早期的产品是根据国外的产品资料生产的,于1966年开始了国产混砂机的研制。先后研制了S116A、S1114等机型的混砂机。根据国产混砂机的生产使用经验,在1978年,提出了我国辗轮式混砂机的基本参数标准 (JB2656—79)。该标准将我国的混砂机的发展推向了标准化、系列化的轨道。20世纪80年代,随着造型技术的发展(如气冲和静压造型技术的出现),造型线的成型速度加快,铸型紧实度提高,对型砂的流动性、透气性、起模性、含水量都有了不同要求,对新的混砂设备提出了更高的要求。国内开发出了转子式混砂机,具体又分为固定转子式混砂机,逆流转子式混砂机,行星转子式混砂机和底盘旋转式混砂机。这些新的混砂机经过在生产中的实际应用,大部分得到了社会认可,并逐渐广泛使用。 混砂机的分类 混砂机是一种被广泛应用在铸造工业中的砂处理设备,混砂机按混砂工艺特征,可以分为:以辗压﹑搓研作用为主的辗轮式混砂机;以混合作用为主的叶片式混砂机;兼有搓研﹑混合作用的逆流式或称转子式混砂机和兼有辗压﹑混合作用的摆轮式混砂机。混砂机按工作性质还可以分为间歇式和连续式两种混砂机。 常见的几种混砂机 辗轮式混砂机 出现在20世纪初,仍广泛用于以黏土为黏结剂的型(芯)砂的混制。这种混砂机配置具有一定重量的辗轮,混砂时辗轮既能围绕混砂机的主轴公转,又能围绕辗轮轴自转。辗轮在辗压的同时搓研型砂,使型砂颗粒覆上一层黏结剂的薄膜。混制面砂和芯砂时,混砂质量优於其他混砂机。50年代初曾有用弹簧加压的辗轮式混砂机。由于采用弹簧加压,辗轮自重减轻,可用较高的主轴转速,同时辗压力可以随被辗压砂层的厚度自动调节,从而保证混砂效果均匀一致,提高了混砂的效率。 转子式混砂机 转子式混砂机在1960年后开始用于铸造生产,产品发展相当迅速,机器结构也各具有特点,大有与辗轮式混砂机一争短长之势。转子式混砂机是以提高主轴转速,并利用高速转子对型砂进行抛击和搅拌,达到各种原材料混合均匀的目的。这种混砂原理的出发点是:目前高压造型机所用型砂,粘土含量高但是水分偏低,型砂的“塑性”小而“脆性”大,因此可以用加强搅拌的方法混砂,使型砂获得合适物理和机械性能。 与辗轮式混砂机比较,转子式混砂机具有下述特点: 1、转子式混砂机因为没有辗轮,而且刮板和转字最好埋在砂层中工作,所以混
自硬呋喃树脂砂
自硬呋喃树脂砂 第一章/ 概论 1 — 1 自硬呋喃树脂砂的概念 自硬呋喃树脂砂的命名来源于英语的Furan No-Bake process,它表示以呋喃树脂为粘结剂,并加入催化剂混制出型砂,不需烘烤或通硬化气体,即可在常温下使砂型自行固化的造型方法。通常被简称为“冷硬树脂砂”,甚至“树脂砂”。以下介绍两个基本概念。 一、呋喃树脂的概念 由碳原子和其它元素原子(如O、S、N等)共同组成的环叫做杂环、组成杂环的非碳原子叫杂原子。含有杂环的有机化合物叫做杂环化合物。所谓“呋喃”,是含有一个氧原子的五员杂环有机化 合物,它是表示一族化合物的基本结构总称。 在呋喃系中不带取代基的杂环作为母体,叫做“呋喃”,它的衍生物则根据母体来命名。呋喃本身在互业上并无什么用途,但它的衍生物——糠醛和糠醇,却是互业上的重要原料,它们是最重要的呋喃衍生物,糠醛学名叫α——呋喃甲醛,糠醇学名叫呋喃甲醇。它们的分子结构如下: 含有糠醇的树脂称为呋喃树脂。作为铸造粘结剂用的呋喃树脂一般是用糠醇(FA)与尿素、甲醛或苯酚等缩合而成的,如尿醛呋喃树脂(UF/FA)、酚醛呋喃树脂(PF/FA)、酚脲醛呋喃树脂(UPF-FA) 和甲醛——糠醇树脂(F/FA)等。 二、呋喃树脂的硬化机理 根据呋喃树脂的组成不同,分别可以通过加热、通入硬化气体或添加酸催化剂等方法使其固化。酸催化(即“自硬”)的呋喃树脂一般糠醇含量都超过50%。其硬化机构很复杂,现在还未完全弄清楚,但基本的树脂化反应包括了糠醇的第一醇基和呋喃环的第五位氢之间的脱水缩合,此外呋喃环的断裂生成乙酰丙酸,第一醇基间脱水生成醚和醛等等的反应。图1-1为呋喃树脂粘结剂的成分和代表 性的呋喃自硬树脂结构的一例。 初期阶段
铸造用呋喃树脂砂
第一章铸造用呋喃树脂砂概述 一、自硬呋喃树脂砂的特点 1. 优点: 1)铸件表面光洁、棱角清晰、尺寸精度高; 2)型砂的溃散性好,清理、打磨容易,从而减少了落砂清铲修整工序中对铸 件形状精度的损害; 3)由于在各个工序中都最大限度的排除了影响铸型、铸件变形和损坏的因 素,所以树脂砂铸件的铸件表面质量、铸件几何尺寸精度方面比黏土可以提高1~2级,达到了CT7~9级精度和1~2mm/600mm的平直度,表面粗糙度大有改观; 4)减轻劳动强度大大改善了劳动条件和工作环境,尤其是减轻了噪声、矽 尘等,减少了环境污染; 5)树脂砂型(芯)强度高(含高温强度高)、成型性好发气量较其它有机铸型 低、热稳定性好、透气性好,可以大大减少铸件的粘砂、夹砂、砂眼、气孔、缩孔、裂纹等铸件缺陷,从而降低废品率,可以制造出用黏土砂难以做出的复杂件、关键件; 6)旧砂回收再生容易可以达到90%左右的再生回收率。在节约新砂、减少 运输、防止废弃物公害方面效果显著。 2. 缺点: 1)对原砂要求较高,如粒度、粒形、SiO2含量、微粉含量、碱金属盐及黏土 含量等都有较严格要求; 2)气温和湿度对硬化速度和固化后强度的影响较大; 3)与无机类黏结剂的铸型相比,树脂砂发气量较高,如措施不当,易产生气 孔类缺陷; 4)与黏土砂相比,成本仍较高; 5)对球铁件或低碳不锈钢等铸件,表面因渗硫或渗碳可能造成球化不良或增 碳,薄壁复杂铸钢件上易产生裂纹等缺陷; 6)浇注时有刺激性气味及一些有害气体发生,CO气发生量较大,需要良好 的通风条件。
二、自硬呋喃树脂砂原辅材料 1. 原砂: 原砂品质对树脂用量,树脂砂强度以及铸件质量影响很大,某些工厂由于忽视对原砂质量的严格要求,给生产带来很多麻烦。表1列举了不同大小和材质的铸件采用原砂的技术指标。 表1 树脂自硬砂用原砂的技术指标(质量分数,%) ①微粉:对30/50、40/70筛号的原砂、140筛号以下为微粉;对50/100、70/140筛号的原砂,200筛号以下为微粉;对100/200筛号的原砂,270筛号以下为微粉。 酸自硬树脂砂除个别的、特殊要求之外,一般都采用硅砂,对硅砂的具体要求是: 1)原砂SiO2含量要高,一般铸钢件w(SiO2)≥97%,铸铁件w(SiO2)≥90%, 非铁合金铸件w(SiO2)≥85%; 2)酸耗值应尽可能低,一般小于等于5ml; 3)含泥量越小越好,一般质量分数小于0.2%,颗粒表面应干净、不受污染, 以保证砂粒与树脂膜之间有高的附着强度,因此应尽可能采用经过擦洗 处理的擦洗砂;
树脂砂生产线
树脂砂生产线是由磁选皮带输送机、震动破碎再生机、离心转子二次二级再生机、砂库、斗式提升机(3移动双臂连续式树脂砂混砂机(菲迪斯玛)套)、移动双臂连续式树脂砂混砂机、脉冲反吹式除尘器等设备组成的。 2工艺流程 震动破碎再生机(菲迪斯玛) 树脂砂生产线工艺流程:浇注后的砂箱及铸件由行车吊至惯性振动落砂机上,经落砂处理后,铸件运到清铲车间,砂箱运至砂箱库备用。大块夹皮,冒口由人工分拣,通过落砂栅格的砂子、砂团以及小块冷铁落至磁选皮带机,经磁选后输送至多功能振动破碎再生机进行破碎、脱膜、筛分,经过筛分后的砂子进1#斗式提升机,由提升机提升至离心转子二级再生机进行强力再生,充分脱膜。混合着微粉、灰尘、树脂膜的再生砂经流砂槽流入流幕式风选机,风选机连接着旋风除尘器及脉冲式反吹除尘器,将微粉、灰尘去除。再生砂再经 2#斗式提升机提升至砂库备用。移动双臂式连续树脂砂混砂机上方进料口由气动闸板与砂库下方出砂口相连,按下混砂机电控箱混砂按扭后,气动闸板自动打开,定好量的砂子由砂库流入混砂机。在混砂机中砂子经螺旋片向前输送至混砂开始端,自近端控制阀加入固化剂,经小叶片搅拢预混至后面的近端阀加入树脂,进入混砂端。固化剂、树脂、再生砂充分混匀后送至前端出料口自动流入准备好的砂箱内用于造型、制芯。此设备由进口PLC(编程可控)控制自动化性能卓越,适用于树脂砂工艺的中小铸造企业。 3基本参数 1、S3305破碎机 2、S524Ⅲ贯通式磁选机 3、S524ⅣC离心转子二次二级再生机 4、S524Ⅶ型斗式提升机 5、S255L移动双臂连续式树脂砂混砂机 6、除尘系统DMC.64 脉冲式反吹除尘器。
4意义 树脂砂生产的意义:(1)最大限度地减少因废砂排除造成的环境污染,使90%以上的废砂可以再生回用。(2)由于再生砂颗粒表面光滑,粒度分布均匀,微粉少,可节约昂贵的树脂20%以上。(3)再生砂热稳定性好,热膨胀少,化学性能稳定,酸耗值降低,树脂砂性能容易控制,有利于提高铸件质量,减少脉纹、机械粘砂等缺陷。呋喃自硬树脂砂的特点:1、型(芯)强度高,溃散性好,能够保证铸件的尺寸精度和表面质量。2、流动性好,能提高型(芯)的充填性,提高型(芯)质量和劳动生产率,减轻工人的劳动强度。3、节约能耗,铸型(芯)只需烘烤,就满足浇注要求。4、旧砂可再生回用,可进一步降低成本。5操作规程 二、生产线的构成 1、落砂系统:主要包括落砂机、震动输送机、磁选机、1#斗提机、1#砂斗上料位。 2、破碎系统:主要包括1#砂斗下料位、振动给料机、破碎机、冷却分离机、提升机、砂库上料位。 3、再生系统:主要包括砂库下料位、磁选机、再生机、风选机、斗提机、砂库上料位。 4、砂调系统:主要包括砂温调节器、冷却塔风机、循环水泵、斗提机、温控仪等。 5、气送系统:主要包括砂库闸门、罐闸门、发送阀、增压器、截止阀等 三、生产操作 首先检查水源、电源、气压是否正常。(电源三相380V,气源压力至少在0.6MP) 1、落砂系统 ⑴、开机前准备 ①、认真检查每台振动电机固定螺栓是否松动;引出线绝缘是否损坏;台面及框架有无断裂;弹簧如断裂应及时更换;电机是否需要补充润滑脂;发现问题应及时处理或汇报有关人员。 ②检查振动输送机电机固定螺栓是否松动、引出线绝缘是否损坏,发现问题应及时处理或汇报有关人员。 ③检查磁选机是否有螺栓松动、皮带松动或跑偏现象。
呋喃树脂砂铸件常见缺陷及预防措施
一、气孔与针孔 1.产生原因 1.1树脂添加量过多,树脂中氮含量过高。 1.2醇基涂料的溶剂中有变质酒精、含水分较多或涂料的浓度太低,点火后干燥不彻底。 1.3水基涂料干燥不充分。 1.4造型互艺方案不良。其中影响较大的因素有:浇注速度过慢;通气方案不良;浇注系统尺寸合比例不当;压头太低。 1.5回收再生砂的灼减量过高。 1.6造型(芯)后尚未充分固化就过早合箱浇注,造成发起量过大。 1.7造型操作不当。如芯铁外露,芯头钻铁等。 2.气孔类缺陷的预防措施针对以上各条产生原因,采取以下相应对策: 2.1降低树脂添加量: 2.11 2.12 2.13 2.14 选择含N 量较低的树脂,选用粒型圆整、粒度适中、含微粉量低、耗 酸量低的原砂;添加偶联剂; 选用强度性能好的树脂及适当的固化剂等,尽可能将树脂添加量将至砂重的1.2%以下。 2.2涂料 2.2.1重视涂料
的溶剂质量;酒精快干涂料的酒精浓度一般不小于95%。2.2.2涂刷前对涂料充分搅拌,浓度应大于30“ B;e 2.2.3涂刷料后即时点火干燥。 224使用水基涂料后应在小于180C温度下烘烤1小时?2小时以上,务必使涂料充分干燥。 2.3制定互艺方案时要注意提高浇注速度,合理有效的设计通气;掌握快速、封闭、底注、不紊流的设计原则。 2.4回用砂灼减量控制在 3.0%?3.5%以下。主要措施有尽量降低砂铁比,选择优良的再生设备,注意再生砂的管理。 2.5型芯最好隔天使用,铸型也应在造型4小时?6小时以后再上涂料及合箱浇注。 2.6 严格控制造型(芯)、配模的操作过程。芯骨不要外漏,芯头要有防止钻铁措施,以免呛火造成气孔缺陷。 以上主要讨论了因呋喃铸型本身而造成的侵入型气孔缺陷,实际生产中因铁水温度及溶炼质量等因素引起的气孔比例也不小,要注意具体分析、对症下药。 二、机械粘砂与脉纹 1.产生原因 1.1型砂骨料粒度分布不当及造型(芯)时紧实度太低。 1.2涂料耐火度低、涂层厚度不够。 1.3新砂用量较大时易产生渗铁与脉纹,尤其当新砂的SiO 2 含量很高时。 1.4造型操作不当引起的型砂强度过低、表面稳定性差,促使粘砂脉纹的发生。 如使用超过了可使时间的型砂,连续式混砂机的头砂尾砂充当面砂,修模型砂(芯)表面时引起的表面稳定性降低、砂温过高等。 2.预防措施
树脂砂造型的特点及工艺流程
树脂砂造型的特点及工艺流程 树脂砂造型工艺以其生产的铸件表面轮廓清晰、光洁,几何精度、尺寸精度高;生产工艺简单易于控制,而越来越为铸造企业接受和应用。这几年随着机械产品质量要求的不断提高,包括材质、尺寸精度,尤其是表面质量要求的提高,树脂砂这一较先进工艺得到了大力的推广。另外随着对原砂的处理及树脂、催化剂、混砂设备、工艺等方面的改进,树脂砂成本得到降低,也大大促进了树脂砂技术的推广。 树脂砂造型的特点: 1、成品率高 铸铁件成品率一般情况下≥92%,较高情况可达96~98%。2、表面光洁 比普通湿型粘土砂造型高2~3个等级,表面粗糙度可达Ra12.5。 3、尺寸精度高 由于型砂强度较高,铸件尺寸精度比一般潮模砂高2个级别,可达IT8~10级。后续加工余量可减少,刀具磨损小。 4、工艺简洁,易于控制 树脂砂造型工艺属自硬型,工艺要点由设备保证,只要掌握好工艺参数,就完全可以保证铸件质量,所以对操作工的技术素质要求较低,且节省劳动力,减轻劳动强度,车间单位面积的铸件产量比粘土砂烘模工艺翻一番,清砂效率也有大幅提高。同时扬尘点与散落砂少,所以工作环境较整洁。 5、高的工作效率
采用树脂砂造型提高了工作效率,单位面积的工作量提高,节约了车间面积。 6、减轻劳动强度 树脂砂大大减轻了制芯、造型、落砂、清理工人的劳动强度。 工艺流程如下: 落砂机——振动输送机——悬挂磁选机-------1#链式斗提机——1#砂斗——振动给料机——破碎机——2#斗提机——惯通式磁选机——2#砂斗——3#斗提机——3#砂斗——4#斗提机——再生机——风选机——5#斗提机——砂温调节器————6#斗提机——4#砂斗——气力输送罐----—固定双臂混砂机
树脂砂铸造工艺
树脂砂铸造工艺 第一章 / 概论 1 — 1 自硬呋喃树脂砂的概念 自硬呋喃树脂砂的命名来源于英语的 Furan No-Bake process,它表示以呋喃树脂为粘结剂,并加入催化剂混制出型砂,不需烘烤或通硬化气体,即可在常温下使砂型自行固化的造型方法。通常被简称为“冷硬树脂砂”,甚至“树脂砂”。以下介绍两个基本概念。 一、呋喃树脂的概念 由碳原子和其它元素原子 (如 O、 S、 N等 )共同组成的环叫做杂环、组成杂环的非碳原子叫杂原子。含有杂环的有机化合物叫做杂环化合物。所谓“呋喃”,是含有一个氧原子的五员杂环有机化合物,它是表示一族化合物的基本结构总称。在呋喃系中不带取代基的杂环作为母体,叫做“呋喃”,它的衍生物则根据母体来命名。呋喃本身在互业上并无什么用途,但它的衍生物——糠醛和糠醇,却是互业上的重要原料,它们是最重要的呋喃衍生物,糠醛学名叫α——呋喃甲醛,糠醇学名叫呋喃甲醇。它们的分子结构如下: 含有糠醇的树脂称为呋喃树脂。作为铸造粘结剂用的呋喃树脂一般是用糠醇 (FA)与尿素、甲醛或苯酚等缩合而成的 ,如尿醛呋喃树脂( UF/FA)、酚醛呋喃树脂 (PF/FA)、酚脲醛呋喃树脂( UPF- FA)和甲醛——糠醇树脂 (F/FA)等。 二、呋喃树脂的硬化机理 根据呋喃树脂的组成不同,分别可以通过加热、通入硬化气体或添加酸催化剂等方法使其固化。酸催化(即“自硬”)的呋喃树脂一般糠醇含量都超过 50%。其硬化机构很复杂,现在还未完全弄清楚,但基本的树脂化反应包括了糠醇的第一醇基和呋喃环的第五位氢之间的脱水缩合,此外呋喃环的断裂生成乙酰丙酸,第一醇基间脱水生成醚和醛等等的反应。图 1- 1为呋喃树脂粘结剂的成分和代表性的呋喃自硬树脂结构的一例。 ?初期阶段 1 — 2 自硬呋喃树脂砂的优缺点 一、自硬呋喃树脂砂具有以下优点: 1 .铸件表面光洁、棱角清晰、尺寸精度高。 这是由于树脂砂造型可以排除许多使型(芯)变形的因素。如:( 1)型砂流动性好,不需捣固机紧实,减少了模样(芯盒)的伤损和变形;( 2)砂型(芯)固化后起模,减少了因起模前松动模样和起模时碰坏砂型(芯)引起的变形;( 3)无需修型,减少了修型时引起的变形;( 4)无需烘烤,减少了因烘烤造成的铸型(芯)变形;( 5)铸型强度高、表面稳定性好,故芯头间隙小、分型负数小,减少了下芯、配模过程中铸型的破损和变形,保证了配模精度;( 6)铸型(芯)硬度高,热稳定性好,可以有效地抵御浇注时的型壁退让、迁移现象,减少了铸型的热冲击变形(如胀砂等);( 7)型砂的溃散性好,清理、打磨容易,从而减少了落砂清铲修整工序中对铸件形状精度的损害。综上所述,由于在各个工序中都最大限度地排除了影响铸型、铸件变形和损坏的因素,所以树脂砂铸件的铸件表面质量、铸件几何尺寸精度方面比粘土烘模砂可以提高 1— 2级,达到 CT7-9级精度和 1- 2mm / 600mm的平直度,表面粗糙度更大有改观。 2 .造型效率高,提高了生产率和场地利用率,缩短了生产周期。 这是由于( 1)、型砂流动性好,不需捣固机紧实,节省了大量的捣固工作量,使造型
浅析树脂砂铸造生产的工艺流程及模型要求
浅析树脂砂铸造生产的工艺流程及模型要求 为规范树脂砂铸造的生产过程,严格执行操作工艺,减少因违反工艺或操作不当产生的废品和降低的铸件生产成本,特制定本生产操作工艺规程。本工艺规程适用于公司内所有树脂砂铸件的生产全过程和与之相关的各类操作人员。下面节选一部分供大家参考阅读。 工艺规程 3.1 主要原材料的技术要求或规格 3.1.1原砂(天然石英砂) 粒度:40/70目(中大件)或50/100目(一般件); 化学成分:SiO2 >90% 、含泥量< 0.2%~0.3% 、含水量<0.1~0.2%; 微粉含量(140目筛以下) ≤0.5~1.0%、耗酸值<5ml 、灼减量<5、粒型:圆形或多角形。 3.1.2再生砂 灼减量<3.0%;耗酸值<2.0ml;PH值<5 ;200目筛底盘<1%;底盘量<0.2%;含水量<0.2%;粒形:圆形。 3.1.3呋喃树脂 含氮量2.0~5.0%;24h抗拉强度>1.5MPa;游离甲醛<0.3%;粘度<60mPa.s;密度1.15~1.25 g/cm3;游离酚<0.3%。 3.1.4固化剂 采用有机磺酸固化剂,其黏度一般控制在<200mPa.s,水不溶物的含量<0.1%,同时冷冻和随后的溶解之间要有可逆性。为了保证稳定的型砂可使用时间和硬化速度,可选用“a+b”固化剂或根据季节不同选用不同酸度型号的固化剂。 3.1.5涂料 采用醇基涂料。要求涂料的固体含量高,粉料粒度细,粉料及黏结剂的耐火度高,抗爆热能力强等。具体工艺性能要求有:密度1.25~1.35 g/cm3;黏度6~7s;悬浮性(2h)>97%;涂刷性、流平性、渗透性、抗裂性要好,涂层强度要高。对于表面球化有深度要求的铸件,应采用氧化镁涂料。 3.2操作工艺规程 3.2.1再生砂准备 根据树脂砂再生设备的要求和工艺流程进行操作,获得满足工艺要求的再生砂。特别要注意控制好进入混砂机时的再生砂的温度,最好在25-35℃。 3.2.2砂、树脂、固化剂加入量的调整 (1)混砂机的流量测定 根据混砂机的设定要求,在正常的生产情况下,至少每四天进行一次流量测定。分别对相同时间内砂、树脂、固化剂的流量进行称量,掌握时间流量。并先将砂流量按混砂机的公称流量进行调整。 (2)树脂量的调整 根据砂流量调整树脂的加入量,树脂加入量一般控制在型砂重量的0.8~1.2%,厚大件取上限,中小件取下限。 (3)固化剂量的调整 固化剂加入量在正常情况下与砂温和车间环境温度有关,一般控制在树脂加入量的30~50%,高温时取下限,低温时取上限。放砂时间长的大件固化剂加入量取下限,以保证树脂砂有足够的可使用时间。(4)混砂机的调整与准备 严格按《混砂机操作规程》进行设备的日常维护保养,特别是要及时清理搅笼内的叶片和内壁。每天放砂前应将树脂,固化剂泵单独循环1~2分钟,并注意检查固化剂加入孔是否有结晶堵塞现象。
树脂砂再生设备
参考资料:https://www.360docs.net/doc/dd1155890.html,/ https://www.360docs.net/doc/dd1155890.html,/ 树脂砂再生设备 树脂砂再生设备主要由砂块破碎机、磁选机、再生机、风选装置、树脂砂混砂机等组成。 (1)振动破碎再生机:从振动落砂机落下的旧砂必须首先经过破碎,将大小不等的砂块破碎成砂粒,然后经过磁选和过筛去除砂中的铁质和杂物。我厂生产的多功能振动再生机通过安装在底部的两台交叉对称的振动电机,使砂块相互撞击,砂块在振动和输送过程中破碎,同时靠砂块之间的摩擦去掉砂粒表面得树脂膜、烧枯的碳化物质,使旧砂得到再生。这种再生装置兼有破碎和再生两种功能,但一般脱膜率比离心撞击式低。只经过振动破碎再生机再生的过程有时也称为“软再生”。 (2)离心撞击式再生机:又称离心转子再生机,旧砂从上部导管落下,经高速旋转地抛砂盘,将砂子抛向冲击环圈,在冲击环圈中,砂子三次撞击折射,砂粒间相互摩擦、撞击,使小砂团破碎,砂粒表面的惰性膜破裂,达到脱膜目的。一次循环脱膜率达不到要求时,可将旧砂再返回处理或将二、三台同样机组串联使用。 (3)微粉分离设备又称风选器,也称流幕式微粉分离器,工作原理:砂子从砂斗、挡板处流下,从进风口水平方向鼓风,将颗粒小、密度低的微粉及粉尘经抽风口带走,进入沉降室,正常的砂粒直接落下到立挡板上再进行第二次分选。调节挡板可控制砂子流量,通过调节风量、风速可以控制除尘效果。(4)正确选择混砂设备对树脂砂性能影响较大。对混砂机的要求是定量准确
(如树脂、固化剂的流量误差不得超过3%,砂流量误差不得超过5%)、混碾均匀(混砂均匀性不得超过10%,并尽量做到减少头砂、尾砂不均匀现象)、覆膜效果好,混砂过程中型(芯)砂发热少。此外,还应考虑到设备、制造质量使用的可靠性、维修方便、产品价格等因素。 树脂砂混砂机分为单臂和双臂两种,皆为连续式混砂机。 其特点如下: 粘结剂供给系统采用电动变量隔膜泵(意大利进口)和齿轮泵,重量轻、体积结构紧凑、流量稳定可靠。 砂子混制均匀,有效地保证了造型(制芯)的质量。 混砂时间短,无头、尾砂,停机后排料干净。 全开式混砂搅拢臂,便于叶片清理或调整,操作维修方便。 混砂机进口处可根据生产需要配置新旧砂比例调节器,可准确控制旧砂的出砂量及其配比。 电器采用PLC控制,制约保护充分,模拟显示,工作稳定,实现自动化生产。