炉衬损毁机理.
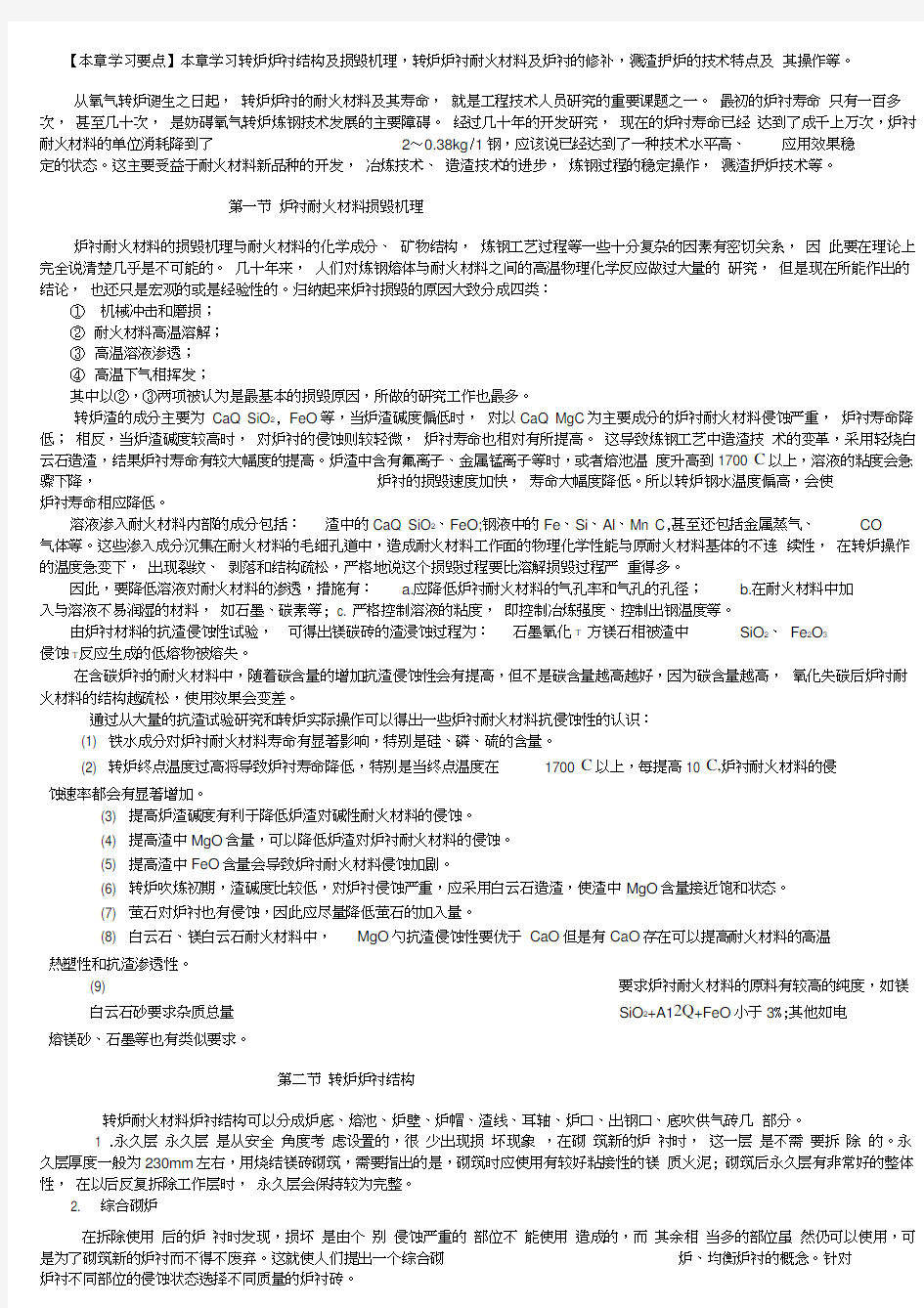

【本章学习要点】本章学习转炉炉衬结构及损毁机理,转炉炉衬耐火材料及炉衬的修补,溅渣护炉的技术特点及其操作等。
从氧气转炉诞生之日起,转炉炉衬的耐火材料及其寿命,就是工程技术人员研究的重要课题之一。最初的炉衬寿命只有一百多次,甚至几十次,是妨碍氧气转炉炼钢技术发展的主要障碍。经过几十年的开发研究,现在的炉衬寿命已经达到了成千上万次,炉衬耐火材料的单位消耗降到了2?0.38kg/1钢,应该说已经达到了一种技术水平高、应用效果稳
定的状态。这主要受益于耐火材料新品种的开发,冶炼技术、造渣技术的进步,炼钢过程的稳定操作,溅渣护炉技术等。
第一节炉衬耐火材料损毁机理
炉衬耐火材料的损毁机理与耐火材料的化学成分、矿物结构,炼钢工艺过程等一些十分复杂的因素有密切关系,因此要在理论上完全说清楚几乎是不可能的。几十年来,人们对炼钢熔体与耐火材料之间的高温物理化学反应做过大量的研究,但是现在所能作出的结论,也还只是宏观的或是经验性的。归纳起来炉衬损毁的原因大致分成四类:
①机械冲击和磨损;
②耐火材料高温溶解;
③高温溶液渗透;
④高温下气相挥发;
其中以②,③两项被认为是最基本的损毁原因,所做的研究工作也最多。
转炉渣的成分主要为CaQ SiO2, FeO等,当炉渣碱度偏低时,对以CaQ MgC为主要成分的炉衬耐火材料侵蚀严重,炉衬寿命降低;相反,当炉渣碱度较高时,对炉衬的侵蚀则较轻微,炉衬寿命也相对有所提高。这导致炼钢工艺中造渣技术的变革,采用轻烧白云石造渣,结果炉衬寿命有较大幅度的提高。炉渣中含有氟离子、金属锰离子等时,或者熔池温度升高到1700 C以上,溶液的粘度会急骤下降,炉衬的损毁速度加快,寿命大幅度降低。所以转炉钢水温度偏高,会使
炉衬寿命相应降低。
溶液渗入耐火材料内部的成分包括:渣中的CaQ SiO2、FeO;钢液中的Fe、Si、Al、Mn C,甚至还包括金属蒸气、CO
气体等。这些渗入成分沉集在耐火材料的毛细孔道中,造成耐火材料工作面的物理化学性能与原耐火材料基体的不连续性,在转炉操作的温度急变下,出现裂纹、剥落和结构疏松,严格地说这个损毁过程要比溶解损毁过程严重得多。
因此,要降低溶液对耐火材料的渗透,措施有: a.应降低炉衬耐火材料的气孔率和气孔的孔径; b.在耐火材料中加
入与溶液不易润湿的材料,如石墨、碳素等; c. 严格控制溶液的粘度,即控制冶炼强度、控制出钢温度等。
由炉衬材料的抗渣侵蚀性试验,可得出镁碳砖的渣浸蚀过程为:石墨氧化T方镁石相被渣中SiO2、Fe2O3
侵蚀T反应生成的低熔物被熔失。
在含碳炉衬的耐火材料中,随着碳含量的增加抗渣侵蚀性会有提高,但不是碳含量越高越好,因为碳含量越高,氧化失碳后炉衬耐火材料的结构越疏松,使用效果会变差。
通过从大量的抗渣试验研究和转炉实际操作可以得出一些炉衬耐火材料抗侵蚀性的认识:
(1) 铁水成分对炉衬耐火材料寿命有显著影响,特别是硅、磷、硫的含量。
(2) 转炉终点温度过高将导致炉衬寿命降低,特别是当终点温度在1700 C以上,每提高10 C,炉衬耐火材料的侵
蚀速率都会有显著增加。
(3) 提高炉渣碱度有利于降低炉渣对碱性耐火材料的侵蚀。
(4) 提高渣中MgO含量,可以降低炉渣对炉衬耐火材料的侵蚀。
(5) 提高渣中FeO含量会导致炉衬耐火材料侵蚀加剧。
(6) 转炉吹炼初期,渣碱度比较低,对炉衬侵蚀严重,应采用白云石造渣,使渣中MgO含量接近饱和状态。
(7) 萤石对炉衬也有侵蚀,因此应尽量降低萤石的加入量。
(8) 白云石、镁白云石耐火材料中,MgO勺抗渣侵蚀性要优于CaO但是有CaO存在可以提高耐火材料的高温
热塑性和抗渣渗透性。
(9) 要求炉衬耐火材料的原料有较高的纯度,如镁
白云石砂要求杂质总量SiO2+A12Q+FeO小于3%;其他如电
熔镁砂、石墨等也有类似要求。
第二节转炉炉衬结构
转炉耐火材料炉衬结构可以分成炉底、熔池、炉壁、炉帽、渣线、耳轴、炉口、出钢口、底吹供气砖几部分。
1 .永久层永久层是从安全角度考虑设置的,很少出现损坏现象,在砌筑新的炉衬时,这一层是不需要拆除的。永久层厚度一般为230mm左右,用烧结镁砖砌筑,需要指出的是,砌筑时应使用有较好粘接性的镁质火泥; 砌筑后永久层有非常好的整体性,在以后反复拆除工作层时,永久层会保持较为完整。
2. 综合砌炉
在拆除使用后的炉衬时发现,损坏是由个别侵蚀严重的部位不能使用造成的,而其余相当多的部位虽然仍可以使用,可是为了砌筑新的炉衬而不得不废弃。这就使人们提出一个综合砌炉、均衡炉衬的概念。针对
炉衬不同部位的侵蚀状态选择不同质量的炉衬砖。
渣线、耳轴区是转炉炉衬中使用条件最苛刻的部位,受到钢液、炉渣的冲刷、侵蚀以及炉内气体的冲刷作用,要求使用抗侵蚀性最好的砖砌筑。
炉帽区主要受炉内气体的冲刷作用,以及吹炼时炉渣的喷溅作用,这部分衬砖的主要问题是剥落和掉砖。炉帽区的衬砖大都处于一种悬臂状态,加之炉体的经常摇动,反复的加料、出钢时的机械碰撞等原因
造成了掉砖现象。解决掉砖的方法有几种:①将这部分衬砖的外面包装铁皮,高温下铁皮熔结在一起,使炉
帽区的衬砖整体性更好;②在铁皮的外侧焊接绞链并将绞链同炉壳连接在一起;③在砌筑炉帽区衬砖时,背
部使用以树脂为结合剂的粘接泥料,使炉衬有更好的整体性。
炉壁区的衬砖,特别是装料侧的炉衬砖,受到钢水、炉渣的冲刷作用,要求具有较高的高温强度。
熔池和炉底的衬砖主要受到钢液的侵蚀,应具有很好的抗侵蚀性。
炉衬砖的长度为500?800mm个别部位的砖长度在Im以上,这种砖有很大的生产难度,一般要用高吨位真空压
砖机成型。
转炉炉衬砖都采用干砌法,不希望砌得过分紧密,甚至还在砖缝中夹一些纸板。目前的衬砖大多是镁碳砖,或者泥砌一些含碳的镁白云石砖。这些砖在高温下均有不同程度的膨胀,砌筑过分紧密会因为膨胀产生剪切应力,容易造成衬砖断裂,破坏炉衬的整体性。
综合砌炉,应根据不同厂家的具体情况,选择3?6个不同档次的砖种,分别砌筑在渣线、耳轴、炉壁、熔池等部位,以求获得最好的经济效益。
3.底吹供气砖在转炉炉衬中底吹供气砖是一个具有特殊地位的砖种。在顶底复合吹炼中,底吹Ar,CO2,N2 就是通过这块砖
吹入炉内的,严格地讲,底吹供气砖已经脱离了原有耐火砖的概念,而具有一定的功能特征。因此,一般定义这类耐火材料为功能性耐火材料。
最初的底吹供气砖是单管式或狭缝式的,由于难于满足顶底复合吹炼工艺的要求,现在都已弃用,而改用技术更先进的直通孔式供气砖。
直通孔式供气砖是由不锈钢管埋设在镁碳质耐火材料中构成的,不锈钢管焊接在均压气室上。不锈钢管内经1?
2mm外径2.0?2.5mm, —支供气砖需要埋设几十根不锈钢管。
直通孔式供气砖生产技术难度较大,以高纯电熔镁砂、高纯石墨、酚酣树脂结合剂为原料,添加高效抗氧化剂,用等静压机成型。
通过供气砖向炉内吹入CO、N2 Ar,在钢水中形成大量气泡、搅动钢水,使供气砖及其周边的炉底衬砖受到严重冲刷和侵蚀。尽管采用的是优质镁碳质耐火材料,但还是难以达到与整个炉衬同步损毁的目的。因此,如果炉衬寿命在几千上万次时,中途则要更换供气砖。
技术水平要求高的供气砖则装有预警装置,当损耗达到一定程度后,会发出警报,提醒更换供气砖。更换供气砖是连同一小块炉底衬砖一起更换。在转炉钢壳外装置成一小块活动炉底,更换时拆下炉底,将损坏的供气砖连同周边的炉衬砖一起取下来,再将预先砌好的带有供气砖的小炉底装上去。接缝处压入镁碳质压人料,更换即完成,更换约需7?8h。一
个新的炉衬当使用到I000 ?1200炉时,则需要更换供气砖了,新更换的供气砖可以使用500?700次:
4 .出钢口
在转炉炉衬中,出钢口砖是另一个具有特殊意义的砖种。大型转炉出钢口由于通钢量大,受到钢液的冲刷,使用条件十分苛刻,一般寿命都比较短,远远不能与炉衬同步使用,只有100 次左右。所以要经常更换出钢口砖,每换一次约需2?4h。出钢口砖从样式上分,可以分成整体式和分段组装式;从材质上分,可以分成镁碳质和烧成镁质。目前认为镁碳质整体出钢口使用效果比较好,寿命长,更换方便。这种砖是以高纯原料等静压机成型的。
第三节转炉炉衬耐火材料
50 年代氧气转炉初创时期,炉衬沿用了平炉、电炉使用的镁砖、沥青白云石砖;经过几次更新换代,炉衬寿命有了大幅度提高。以下是几十年来曾经使用过以及目前正在使用的转炉炉衬耐火材料。
1.焦油白云石砖焦油白云石砖是我国应用时间最长,使用量最大的一种炉衬耐火材料。将天然白云石和焦油混合配料,投入煅烧白
云石砂,其理化指标为:Ca0 55%?60%, MgO32%?36%、杂质总量(Si0 2+Fe203+A1Q)4 %?7%,体积密度2. 95?3. 05g /cm3。白云石砂预热300?600C,加入结合剂焦油沥青混料,振动成型或机压成型,生产出焦油白云石炉衬砖。这种砖的优点是生产成本低,但炉衬寿命也比较低,现在已很少使用。
2.二步料白云石砖
用二步煅烧法生产白云石砂或镁白云石砂。将天然白云石在900 C下轻烧,加水消化,细磨,同时加入轻烧
MgO粉,调节MgO含量,压球或机压成坯,在1650 C以上煅烧成二步白云石砂或镁白云石砂。同竖窑煅烧的白云石
砂相比, 杂质含量低, 烧结程度好, 抗水化性能优, 制砖后炉衬寿命也较高。
3.镁白云石碳砖
以优质白云石砂、镁白云石砂为基本原料,添加优质石墨,以焦油沥青或树脂为结合剂,机压成型生产炉衬砖。由于添加石墨,这种砖的抗侵蚀性有大幅度提高。
4.镁碳砖
以优质烧结镁砂、电熔镁砂为基本原料,添加优质石墨,以焦油沥青或树脂为结合剂混料,高吨位压砖机成型。这是目前使用效果很好的炉衬砖。
5 .抗氧化镁碳砖
在生产镁碳砖的配料中,加入金属Al、Mg Si粉,或Mg-Al、Al —Si合金粉,可以提高镁碳砖的抗氧化性和高温强度,它是价格最昂贵的炉衬砖。
6 .油浸砖
将成型后的炉衬砖,包裹在焦炭粉中或在还原气氛下,在600?900 C轻烧;轻烧后置于真空加压罐内浸渍焦油沥青。
经油浸处理的炉衬砖,气孔率降低、透气性降低,残碳量增加,高温强度提高。相应抗侵蚀性提高,炉衬寿命也有所提高。
第四节转炉炉衬的修补
转炉炉衬的修补是延长炉衬寿命、均衡炉衬损毁、降低生产成本的有力措施。由于转炉操作的不稳定因素,炉衬某些部位会出现过早地损毁,这时修补就应该开始,而且这种修补要维持到炉衬寿命中止。到炉衬使用的后期,修补量会不断增加,修补所用的时间也不断延长,已经影响到转炉的稳定操作,这时炉衬寿命就应该中止了。在整个炉衬耐火材料消耗量中,修补耐火材料的用料量占l /3?1/2被认为是比较合理的修补量。
1 .投补
将投补料从炉口投入炉内,摇动炉体。投补料在炉内余热的作用下,出现流动性并铺展在炉衬的蚀损部位。投补料应具有以下工艺性能:
1) 投补料在转炉炉衬的余热温度下(800?1200C )有很好的铺展性;
2) 投补料在铺展后能很快固化;
3) 固体后的投补料与原炉衬材料有较好的粘结性;
4) 投补料自身应有很好的抗侵蚀性。
投补料以镁砂、镁白云石砂为基本原料,工艺性能则主要决定于结合剂。常用的结合剂是沥青、树脂,或两者的混合物。由于价格便宜,应用方便,我国钢厂实际使用的投补料是以沥青为结合剂的。
2.半干法喷补半干法喷补实施喷补作业的喷补机包括贮料罐、压缩空气输运机构、喷嘴;贮料罐中的喷补料经压缩空气送到喷嘴,混入适量水分(10 %?18 %),在空气压力下以一定速度喷射到炉衬工作面上,喷补料最后粘结固化。影响喷补效果的
工艺因素有:
(1) 炉衬喷补是在热态下进行的,工作面的残余温度对喷补效果有明显影响,一般认为800?1000C比较好;
(2) 喷补料的颗料组成、结合剂、加水量、空气压力等对喷补料的附着率有重要影响。喷补料的基本原料是镁砂和镁白云石砂,
结合剂则主要是粉状硅酸钠、磷酸钠,及钙、钾的磷酸盐、铬酸盐等。结合
剂的作用是使喷补料有粘附性,能有效地附着在炉衬工作面上;另一个作用是在高温下能形成高温矿物相,使喷补料不但能与炉衬工作面牢固地烧结成一个整体,而且使自身有很好的抗侵蚀性。形成的高锰矿物相为Mg2Ca4(P04)SiO 4,熔点1735 C。可以看出,在喷补料组分中,含有一定量CaO是必要的。喷补料的有效性用附着率和使用次数来衡量,一般附着
率要求大于85%。使用次数为3?5次。
3.火焰喷补火焰喷补最先应用于焦炉的修补,后来扩展到转炉炉衬上,是一项技术难度较大的新技术。对于转炉炉衬,半干
法喷补是既简单又方便的方法。但是它有致命的弱点,即在喷补过程中加入水分,这些水分在接触到修补工作面时,由于残余热量的作用,会产生大量蒸汽.并会蓄集一定的蒸汽压,给喷补料和工作面的粘结以及喷补料的使用留下隐患。但火焰喷补不添加水分,
而是配入可燃性物料,可燃性气体和氧气,喷补料在喷射过程中燃烧发热,一部分物料成熔融态,接触到有相当高温度的工作面时,会马上熔融烧结成一个整体。
配入的可燃性物料和可燃性气体包括焦炭粉、煤粉、丙烷、甲烷、氧气等。火焰喷补多在转炉出钢后的作业间隙中进行,喷补时间很短,炉衬残余温度比较高,粘附效果好,因此使用寿命比较长,一般l0 ?20 次。由于火焰喷补技术比较复杂,目前在国内外转炉厂采用的较少。
4.转炉炉衬的溅渣维护采用激光测厚技术精确地测定出炉衬的残余厚度,运用溅渣技术维护炉衬,使转炉炉衬延长使用长寿,这是转炉护炉技术的重大进步。
第五节镁碳砖
镁碳砖是70 年代初出现的,先是在超高功率电炉,接着在转炉、炉外精炼炉上使用,获得了非常好的效果。由此,人们才认识到石墨、碳素材料和高温耐火氧化物之间结合所产生的作用。断裂韧性差、高温剥落、抗渣渗透性差,这是高温烧成耐火制品的致命缺点,含碳耐火制品的出现突破了这些弱点。在镁碳砖中氧化镁和石墨之间彼此相互包裹,不存在传统概念中的所谓烧结;石墨具有热传导系数高,弹性模量低,热膨胀系数小,不容易被熔渣浸润等优点,因此,由于石黑的引入,使炉衬耐火制品的断裂韧性和抗渣渗透性有本质的改善。镁碳砖的主要特征是在微观结构上形成碳的结合物,这种结合是由有机结合剂在高温下结焦碳化形成的。
镁碳砖是一种不烧制品,其理化指标为:MgO70-85%, C 10?20%,显气孔率w 3%,体积密度2.87g /cmf,耐压强度40?
50MPa 1400 C抗折强度10?15MPa
影响镁碳砖性能的工艺因素主要有原料、结合剂、添加剂等。
1 .镁砂
国外最初生产镁碳砖时采用的是高纯烧结镁砂, 随着对镁碳砖使用过程的深入研究发现, 高温下有如下反应:MgO+& Mgf +COt
这个反应一般在1650 C开始,到1750 C时反应加剧,这是镁碳砖使用过程中损耗的重要原因之一,也是镁碳砖在1700C以上使用损耗明显加剧的原因。镁砂中的杂质SiO2, Fe2O3等对上述反应有促进作用,因此,希望镁砂有较高
的纯度。
电熔镁砂相对烧结镁砂来说, 结晶结构更完整, 对碳的还原作用也更稳定, 特别是大结晶电熔镁砂这些特征表现得更为突出,所以镁碳砖的生产开始转向使用电熔镁砂。考虑到碳的结合状态和结合剂的浸润性, 也可以电熔镁砂烧结镁砂混合使用。我国的镁碳砖基本上是使用电熔镁砂。
镁碳砖的使用结果表明,用MgO含量高、方镁石相结晶颗粒大、钙硅比大于2的镁砂,生产镁碳砖效果最好。
2 .石墨石墨是镁碳砖中另一个基本组分。石墨具有很好的耐火材料基本特性, 主要理化指标:固定碳85%?98%,灰分13%?2 % (主要成分SiO2, AI2Q等),相对密度2. 09?2. 23,熔点3640K(挥发)。由于石墨非常容易被氧化,所以长期以来没有引起人们的重视。
镁碳砖使用过程中,石墨的氧化有三种原因:
(1) 空气中氧对石墨的氧化;
(2) 渣中氧化物对石墨的氧化;
(3) 石墨本身所含杂质氧化物对石墨的氧化。
这些氧化物主要指SiO2和FeO。
镁碳砖中杂质氧化物和石墨反应后, 造成砖体结构疏松, 透气性增大、强度下降,这是镁碳砖损毁的内因。因此, 生产镁碳砖大都选用纯度高、磷片结晶大的石墨。
3. 结合剂
结合剂对镁碳砖及其他含碳耐火制品来说, 作用至关重要。石墨和耐火氧化物之间没有互溶关系, 也不可能相互烧结,常温下他们要靠结合剂粘接固化。高温下,结合剂则要结焦碳化, 和石墨形成碳结合, 一般这种结合剂是指树脂类、沥青类等有机物。结合剂高温结焦碳化后形成约3%左右的碳, 这个量虽然不多, 但在镁碳砖或其他含碳制品中却是最具有活力的组成部分, 对制品的高温性能有重要影响。我国镁碳砖或其他含碳制品生产过程和产品质量不够稳定,其中一个重要原因是结合剂不稳定造成的。
镁碳砖结合剂大体可以分三种类型:酚醛树脂类、改性沥青类、石油裂解副产品类, 其中使用效果最好、用量最多的是酚醛树脂类。
4. 添加物
在镁碳砖的损毁过程中, 石墨的氧化是最主要的原因之一。由于氧化失碳, 致使砖体结构疏松, 强度下降。损毁过程遵循氧化失碳T结构疏松T侵蚀T冲刷溶损的路途。为了提高镁碳砖的抗氧化性,可以加入一定量的添加物,包括硅粉、铝粉、FeSi
合金、CaSi合金、SiC,Si3N,B4C等。添加物的另一个作用是在耐火氧化物和石墨之间“搭桥”,使石墨和耐火氧化物形成牢固
的结合,这种作用是由于添加物在一定温度下形成新的矿物相促成的。
我国生产镁碳砖及其他含磷耐火制品,最常用的添加物是铝粉、硅粉和SiC粉。
第六节镁钙碳砖
我国镁白云石、白云石资源相当丰富, 几乎每个省都发现有白云石资源, 是一种大量存在的耐火原料。特别是在缺乏菱镁矿资源的我国东南、西南地区,也都蕴藏有质地优良的镁白云石、白云石资源。合理开发利用这些资源, 缓解对镁砂资源的依赖性, 是一件非常有意义的事。
含CaO的炉衬耐火材料,高温热机械性能、高温塑性都比较稳定。CaO对改善钢中夹杂物性质,以及对脱硅、脱硫、脱磷都有利。因此,镁自云石、白云石质耐火材料在冶炼纯净钢方面将有很好的应用前景。
我国在开发应用镁白云石、白云石质耐火材料方面有很好的基础,竖窑煅烧白云石砂、焦油沥青振动大砖、烧成油浸白云石砖等在我国钢铁发展过程中都起到过非常重要的作用。近年来由于大量使用MgO-C砖,才使这些已有
的工艺生产线闲置起来。不少学者呼吁,一味追求镁碳砖的做法并不见得合理,我国炼钢炉衬材料应走一条镁质、镁钙质并举的技术路线。
1 .镁钙砂
优质镁钙砂是生产含CaO炉衬耐火材料的基础。
在开发MgO--CaO系耐火材料过程中,主要工作有两个方面:第一,提高镁钙砂的烧砂质量,包括化学纯度、体积密度。第二,提高MgO--CaO系耐火制品的抗水化性能。
2 ?镁钙砖、镁钙碳砖
在镁钙砖、镁钙碳砖生产过程中,水化问题是一个关键。一般要采用无水结合剂,成品还要进行防水处理。处理
的方法有涂层、浸清焦油沥青、真空铝箔包装等,保存期为6个月到一年,在这个期间砖的理化指标不应有明显的下降。第七节溅渣护炉
一、溅渣护炉技术的发展和特点
1 ?发展概况
炉龄是转炉炼钢一项综合性技术经济指标。提高炉龄不仅可以降低耐火材料消耗,提高作业率、降低生产成本,
而且有利于均衡组织生产,促进生产的良性循环。所以,大幅度提高转炉炉龄是炼钢工作者多年追求的目标。
转炉炉衬工作在高温、高氧化性条件下,通常以0.2?0. 8mmT炉的速度被侵蚀。为保证转炉正常生产和提高炉衬寿命,我国冶金工作者做了许多工作,如采用焦油白云石砖、轻烧油浸白云石砖,贴补、喷补、摇炉挂渣等措施,使炉龄逐
步提高到1000炉以上;进入80年代,转炉普遍采用镁碳砖,综合砌炉,使用活性石灰造渣,改进操作,采用挂渣、喷补相结合的护炉方法,使转炉炉龄又有明显提高。
溅渣护炉是近年来开发的一项提高炉龄的新技术。该技术最先是在美国共和钢公司的大湖分厂,由普莱克斯气
体有限公司开发的,在大湖分厂和格棱那也特市分厂实施后,并没有得到推广。1991年,美国LTV公司的印地安那哈鲍
厂(1ndianaHabor)用溅渣作为全面护炉的一部分。1994年9月该厂232t顶吹转炉的炉衬寿命达到15658炉,喷补料
消耗降到0 ? 38kg/1钢,喷补料成本节省66%,转炉作业率由1984年的78%提高到1994年的97%。之后,美国有15家以上钢厂采用该技术,美国内陆钢公司炉龄已超过20000炉。加拿大、英国、日本等也已相继投入试验和应用。
我国从1994年开始转炉溅渣护炉试验,采用和发展的速度很快。鞍钢、首钢、宝钢、武钢、太钢等一些转炉厂采用溅渣护护技术,炉龄大幅度提高,取得了明显效果。其中,宝钢、武钢、首钢炉龄已逾万炉。2003年武钢二炼钢创造了
30368炉的转炉炉龄记录。
溅渣护炉是转炉护炉技术的重大进步,这项能够大幅度提高转炉炉龄、降低耐火材料消耗的技术,在我国展示了
广阔的推广应用前景。
2.技术特点
溅渣护炉的技术特点有:
(1) 操作简便根据炉渣粘稠程度调整成分后,利用氧枪和自动控制系统,改供氧气为供氮气,即可降枪进行溅
渣操作;
(2) 成本低充分利用了转炉高碱度终渣和制氧厂副产品氮气,加少量调渣剂(如菱镁球、终渣改性料、轻烧白
云石等)就可实现溅渣,还可以降低吨钢石灰消耗;
(3) 时间短一般只需3?4min即可完成溅渣护炉操作,不影响正常生产;
(4) 溅渣均匀覆盖在整个炉膛内壁上,基本上不改变炉膛形状;
(5) 工人劳动强度低,无环境污染;
(6) 炉膛温度较稳定,炉衬砖无急冷急热的变化;
(7) 由于炉龄提高,节省修砌炉时间,对提高钢产量和平衡、协调生产组织有利;
(8) 由于转炉作业率和单炉产量提高,为转炉实现“二吹二”或“一吹一”生产模式创造了条件。
二、溅渣护炉工艺和实践
1.基本原理和操作方法
溅渣补炉的基本原理是在转炉出钢后,调整终渣成分,并通过喷枪向渣中吹氮气,使炉渣溅起并附着在炉衬上,形
成对炉衬的保护层,减轻炼钢过程对炉衬的机械冲刷和化学侵蚀,从而达到保护炉衬、提高炉龄的目的。
图11 —1为某厂50t转炉溅渣与未溅渣时残留炉衬对比图,两者炉龄分别为4409和1196次。按该钢厂的三段
溅渣法(前期不溅,中期间隔溅,后期炉溅),溅渣时炉衬最大平均侵蚀速度为0.095mm/炉,相当于不溅渣时侵蚀速度的1
/3。有些厂侵蚀速度还要小,几乎趋向“零”侵蚀。溅渣后消除了渣线、耳轴部位的严重侵蚀现象,各部位侵蚀均匀,炉衬残留厚度基本接近。
(b)
图11—1溅渣(a)与未溅渣(b)时残留炉衬比较
溅渣护炉操作步骤如下:
(1) 将钢出尽后留下全部或部分炉渣;
(2) 观察炉渣稀稠、温度高低,决定是否加入调渣剂,并观察炉衬侵蚀情况;
(3) 摇动炉子使炉渣涂挂到前后侧大面上;
(4) 下枪到预定高度,开始吹氮、溅渣,使炉衬全面挂上渣后,将枪停留在某一位置上,对特殊需要溅渣的地方进行溅渣;
(5) 溅渣到所需时间后,停止吹氮,移开喷枪;
(6) 检查炉衬溅渣情况,是否尚需局部喷补,如已达到要求,即可将渣出到渣罐中,溅渣操作结束。
如何有效地利用高速氮气射流将炉渣均匀地喷溅在炉衬表面,是溅渣护炉的技术关键,其效果取决于:
――熔池内留渣量和渣层厚度;
——熔渣的物化性质,包括成分、熔点、过热度、表面张力和粘度;
――溅渣气体的动力学参数,包括喷吹压力和流量,枪位及喷枪孔数和夹角等。
2 .基本工艺参数
1) 熔池内的合适渣量
按照国内几家钢厂溅渣实践和效果表明,渣量在100kg/1较为合适。
2) 炉渣性质
(1) 渣成分目前,转炉大都使用镁碳砖作为炉衬,减少炉衬侵蚀的重要措施是提高渣中MgO含量。当渣中
MgC达到饱和时,炉衬中MgO溶解量就会减少,从而提高了炉衬寿命。渣中MgO含量与炉渣碱度有关,有的厂在终
渣碱度(CaO/ SiO2% )为3左右、MgO含量在8%左右就可以保证MgO达到炮和。国内外转炉溅渣的MgO含量一般控制在8%?14 %。
渣中FeO含量高低对炉衬侵蚀和溅渣效果有很大影响。渣中FeO的矿物组成大多为各类低熔点铁酸盐,熔点远
低于出钢温度,而且FeO含量越高,铁酸盐就越多,渣流动性就越好,对炉衬侵蚀作用加大且不容易附着在炉衬上。如果
渣中FeO含量过低,又会造成转炉造渣和去除P、S困难。因此操作中必须严格控制渣中FeO含量。
(2) 炉渣粘度若炉渣粘度大,则渣稠不易溅起,溅渣量迅速下降,为了保持溅渣量,需要消耗更多的射流冲击能。
此外,稠渣则在炉衬上的附着力差;粘度小,渣稀,溅渣覆盖较易,但覆盖层较薄。摇炉有挂渣流落现象,需加渣料调整,
以保证炉渣粘度适当。
(3) 调渣剂溅渣层抗侵蚀能力是影响护炉效果的重要因素。抗侵蚀能力差,需要每炉溅渣,不仅增加氮气用量而
且也延长冶炼周期。为此,有必要提高渣的熔化温度,以利于提高护护效果。为此,需加入调渣剂,使炉渣改质,以满足
提高熔化温度的需要。
调渣剂不仅具有提高溅渣熔点的作用,还有使炉渣更容易溅起而改善溅渣的动力学条件。此外,在渣中能产生弥
散固相质点,从而提高了渣与炉衬的结合能力。
3) 氮气压力和流量
高压氮气是溅渣的动力,其压力、流量直接影响溅渣效果。按照各厂溅渣经验,氮气压力一般与氧气压力接近时,可取得较好效果。由于转炉公称容量不同,所以溅渣的氮气压力、流量存在差异。
4) 顶吹喷枪工艺参数
(1) 枪位枪位对溅渣高度有明显影响,最佳枪位应根据自身条件在实践中确定。枪位过高或过低都使溅渣量减
少。较低枪位有利于转炉下部溅渣;反之对上部溅渣有利。
(2) 喷枪夹角12 °喷孔夹角喷枪溅渣效果优于14 .5°夹角喷枪。喷孔夹角为12°喷枪射流与熔池接触面积小,
形成冲击力大,同时产生的反向射流与水平面的夹角也大,这都有利于增加溅渣的有效覆盖面积。
5) 复吹转炉底气对溅渣的影响
溅渣护炉存在的问题之一是炉底上涨、底吹喷孔堵塞。这一问题在国内外均未得到很好解决。武钢、鞍钢在采用适当
的操作工艺参数后较好地解决了炉底上涨问题。使溅渣下复吹比达到50 %以上,说明采用该技术可以实现高复吹比。
6) 溅渣时间
溅渣时间通常是根据炉子吨位、供气量、炉内渣量、炉渣状况及生产节奏等因素综合考虑,目前我国各钢厂一般吹氮时间为3?5min。
吹氮的目的是提供溅渣的动力,此外它还有冷却炉渣的作用。一般在吹氮的前2min 时间内主要是冷却炉渣,因为在这段时间内炉渣还比较稀,即使溅到炉壁上也附挂不好。当吹氮到2min 以上时,炉渣才开始大量溅起,可喷溅到炉帽处,倒炉观察时炉衬挂渣情况良好。实践中发现,溅渣时间越长,炉衬挂渣越多,但时间过长会造成炉底、熔池炉壁沾挂渣过多,造成炉底上涨,同时。溅渣时间过长会影响生产节奏。因此,溅渣时间要根据自身具体条件加以确定。
3 .溅渣护炉和冶炼工艺的相互影响
1 )溅渣护炉对冶炼工艺的影响
(1) 对冶炼操作的影响
实践得知,由于溅渣炉底会有上涨现象,因此枪位控制要比未溅渣炉役相应提高,以避免造成喷溅、炉渣返干和增加氧气消耗量。
(2) 对钢中氮含量和质量的影响
吹氮溅渣后,主要是防止阀门漏气造成吹炼终点氮含量高。通过对未装溅渣护炉设备和装溅渣护炉设备炉次的终点钢样分析,[N]分别为21.0 X 10「6和21.5 X 10「6,两者氮含量水平相当。
通过对采用溅渣工艺前后轧后废品分析比较表明,用氮气溅渣对钢质量没有影响。对冶炼过程脱硫、脱磷情况抽样统计,没有发现对脱硫、磷有明显影响。
2)冶炼对溅渣的影响
(1) 冶炼终点温度对溅渣覆盖层的影响
冶炼终点温度对溅渣覆盖层有较大的影响。温度高对溅渣不利。据统计,采用溅渣护炉技术后出钢温度每降低I C,
转炉炉龄可提高l20 炉。
(2) 炉渣氧化性的影响
终渣氧化性对溅渣覆盖层也有较大的影响。把终渣FeO控制在低限,对保护炉衬有利。
(3) 炉渣粘度渣稀侵蚀严重,渣偏稠不侵蚀而且容易挂上炉壁。
(4) 炉渣成分
为提高溅渣护炉效果,应在适当的范围内,尽量提高MgO含量及终渣碱度。
3)提高溅渣效果的途径
目前对溅渣层与炉衬结合机理研究还很不够,对两者间是化学结合还是物理结合,或是两者都存在的看法不一,但是对进一步提高溅渣效果的途径,普遍认为:
(1) 采用溅渣护护技术后,炉衬材质的性能不应降低。耐火材料成分对溅渣护炉有一定影响,其中碳含量不宜过高,对现场使用的含碳I4 %?20%的镁碳砖,碳含量宜控制在下限。
(2) 进一步控制和降低渣中(FeO) 含量。
(3) 合理调整渣中(MgO)含量。
(4) 提高溅渣层熔化性温度,以降低炉渣过热度。
(5) 降低出钢温度,提高终点命中率减少一次倒炉到出钢的时间,合理匹配转炉操作工序。
三、溅渣护炉带来的问题溅渣护炉带来的问题包括炉龄的稳定、炉底上涨、炉底透气砖寿命、喷枪粘结、设备维修、经济炉龄等,应通过采取不同的措施加以妥善解决。
1 .炉底上涨
炉渣在炉底停留的时间越长,粘结在炉底的就越多,导致炉底上涨。炉底上涨将影响正常操作,堵塞底气喷孔。因此,要控制好溅渣时间、渣量、氮气压力和流量,尽量减少炉底上涨。在停吹后要尽快将渣出尽。在复吹转炉上,要尽量控制好底气压力和流量,减少炉底上炉渣的停留和粘结量。在炉底上涨太多时,可向炉底吹氧,将上涨部分侵蚀掉。
2 .喷枪粘结溅渣时喷枪头部有时粘结有炉渣,需要及时清理。当冷却水足够,冷却强度大时,喷枪不易结渣,即使有粘渣,移出喷枪喷水冷却,粘渣就会掉落。由于喷枪水冷强度不够,或炉温过高有热枪的情况则应更换喷枪,用预备的冷枪进行溅渣操作,冷枪上粘结的炉渣并不牢固,冷却后易脱落。如果炉内有残留钢液,则会使喷枪表面粘钢,这时,粘结的炉渣在冷却后不易脱落,故炉内要尽量不留钢液,这样对提高钢水收得率也有利。
3 .设备维修问题随着炉衬寿命的延长,原来更换炉衬时维修的项目如水冷烟罩、管道的清理维修、转炉驱动装置、冷却系统、除尘系统、盛钢桶车、吊车等都有相应延长服役时间问题,现在一些钢厂采用不同炉龄段计划维修的办法,既解决了设备影响炉龄的问题,又满足了溅渣护炉的需要,是个好办法。当然,对于设备的大、中修不应包含在此范围。
4.经济炉龄问题经济炉龄与炉龄和原料价格有关。通常,每个转炉厂不同阶段都有一个经济炉龄区,即吨钢成本最低,取得最佳经济效益炉龄区。经济分析表明,炉衬砖和修砌费的成本与炉龄成反比关系,而氮气、补炉料、稠渣剂等的费用随炉龄增长而消耗量增加,对降低成本的负效应也越大。当然,随着冶炼和溅渣护炉工艺水平的提高,最经济的炉龄区要相应增高。但是,是炉龄越高经济效果越好,还是在一个适当的炉龄区经济效果最好?对此,还需要进一步加以研究。
5.经济效益的计算问题
采用溅渣护炉技术,能大幅度提高炉龄和降低耐火材料消耗,减少砌炉次数,提高转炉作业率,提高钢产量,对炼钢生产有较大的正面效益。但溅渣护炉造成炉底上涨,转炉复吹效果变差,钢水终点氧含量升高,合金消耗增加,此外还产生设备上的一些问题,也带来了一定的负面影响。因此,溅渣护炉经济效益的计算还有待商榷。
复习思考题
1.简述炉衬损坏的原因。