哈工大机械设计课程设计

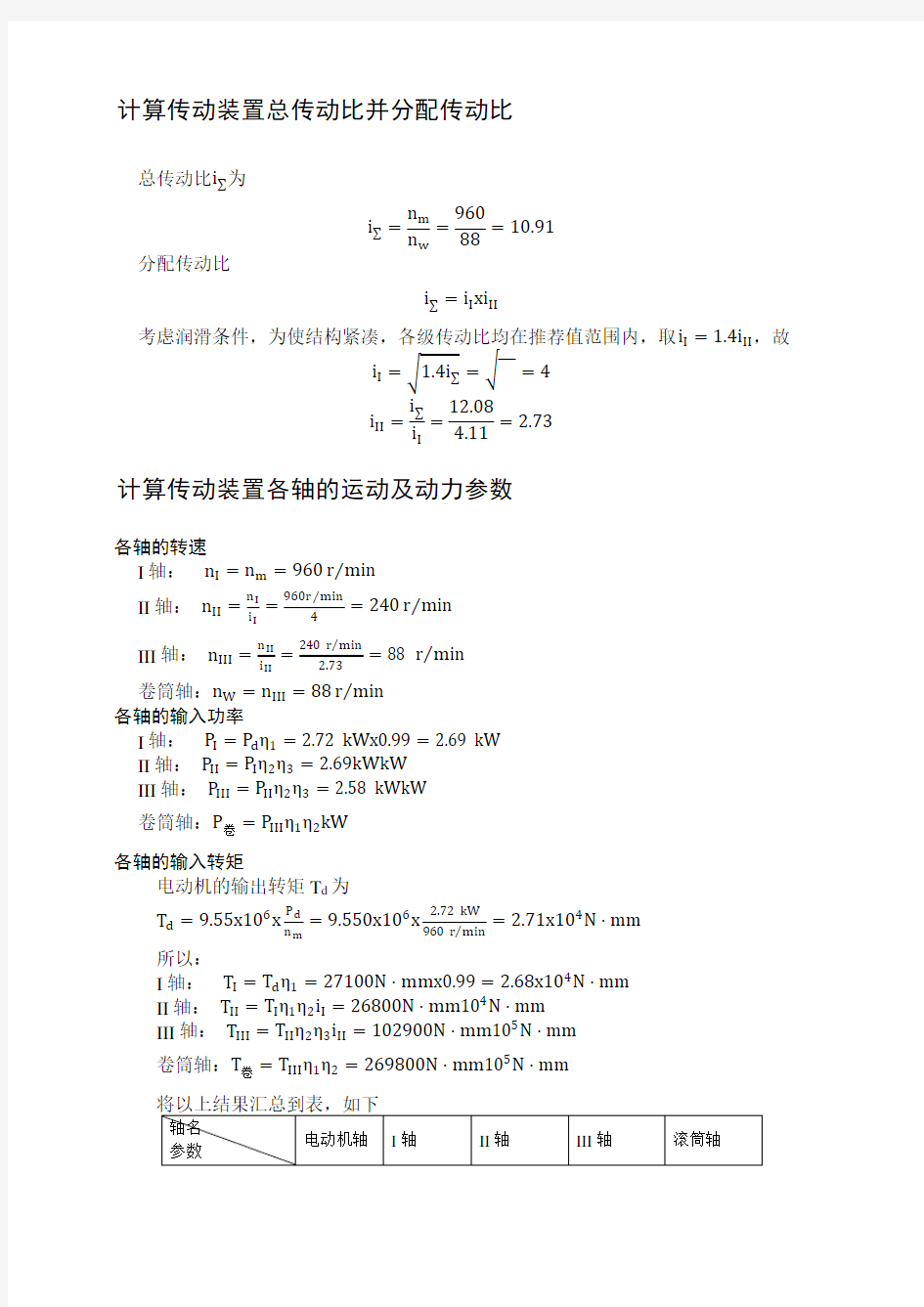
一、传动装置的总体设计
电动机的选择
选择电动机类型
根据设计要求和工作条件选用Y 系列三相鼠笼型异步电动机,其结构为全封闭自扇冷式结构,电压为380 V 。 选择电动机容量
根据设计数据,工作机的有效功率为
P w =Fxv 1000=2130Nx1.1m s ?1000
=2.343Kw
从电动机到工作机输送带之间的总效率为:
η∑=η12η24η32
η4
式中,η1、η2、η3、η4分别为联轴器、轴承、齿轮传动和卷筒的传递效率。由表取η1=、
η2=、η3=、η4=,则
η∑=η12η24η32
η4=0.992x0.994x0.972x0.97=0.86
所以电动机所需工作功率为
P d =P w η∑=2.343kW
0.86
=2.72kW
确定电动机转速
按表推荐的传动比合理范围,二级圆柱齿轮减速器传动比i ∑′=8~40,而工作机卷筒轴的转速为
n w =60x1000xv πd =60x1000x1.1
πx240
r min ?≈88 r min ?
所以电动机转速的可选范围为
n d =i ∑‘n w =(8~40)x88r min ?=(704~3520) r min ?
符合这一范围的同步转速有750r/min 、1000r/min 和1500r/min 三种。综合考虑电动机
和传动装置的尺寸、质量、及价格等因素,为使传动装置结构紧凑,决定选用同步转速为1000 r/min 的电动机。
计算传动装置总传动比并分配传动比总传动比i∑为
i∑=n m
n w
=
960
88
=10.91
分配传动比
i∑=i I xi II
考虑润滑条件,为使结构紧凑,各级传动比均在推荐值范围内,取i I=1.4i II,故
i I=√1.4i∑=√=4
i II=i∑
i I
=
12.08
4.11
=2.73
计算传动装置各轴的运动及动力参数各轴的转速
I轴:n I=n m=960r min
?
II轴:n II=n I
i I =960r min
?
4
=240r min
?
III轴:n III=n II
i II =240 r min
?
2.73
=88 r min
?
卷筒轴:n W=n III=88r min
?
各轴的输入功率
I轴:P I=P dη1=2.72 kWx0.99=2.69 kW II轴:P II=P Iη2η3=2.69kWkW
III轴:P III=P IIη2η3=2.58 kWkW
卷筒轴:P
卷
=P IIIη1η2kW
各轴的输入转矩
电动机的输出转矩T d为
T d=9.55x106x P d
n m =9.550x106x 2.72 kW
960 r min
?
=2.71x104N·mm
所以:
I轴:T I=T dη1=27100N·mmx0.99=2.68x104N·mm II轴:T II=T Iη1η2i I=26800N·mm104N·mm
III轴:T III=T IIη2η3i II=102900N·mm105N·mm
卷筒轴:T
卷
=T IIIη1η2=269800N·mm105N·mm
转速n/(r/min ) 88 88 功率P/(kW)
扭矩T/(N ·mm)
传动比i 1 1 效率
二、传动件设计
高速级斜齿圆柱齿轮传动设计
选择齿轮材料、热处理方式和精度等级
考虑到带式运输机为一般机械,故大、小齿轮均选用45钢,采用软齿面,由文献[1]表得:小齿轮调制处理,齿面硬度为217~25HBW ,平均硬度为236HBW ;为保证小齿轮比大齿轮具有更好的机械性能,大齿轮正火处理,齿面硬度为162~217HBW ,平均硬度为190HBW 。大小齿轮齿面评价硬度差为46HBW ,在30~50HBW 之间。选用8级精度。 初步计算传动主要尺寸
因为是软齿面闭式传动,故按齿面接触疲劳强度进行设计。由 式中各参数为:
(1) 小齿轮传递的转矩
。由前面设计可知,1
26800T N mm =?
(2) 设计时,因v 值未知,不能确定,故可初选载荷系数K t = ~,此处初取K t = 。
(3) 由表取齿宽系数 1.0d ?=。 (4) 由表查得弹性系数。
(5) 初选螺旋角
由图查得节点区域系数45.2=H Z 。
(6) 齿数比14U i ==。
(7) 初选= 21, 则2184Z UZ == ,取285Z =。传动比误差<5%,符合设计要求。 端面重合度
εα=[1.88 ?3.2(1z 1
+1z 2
)]cos β= [1.88 ?3.2(117+1
89)]×cos 12°=1.66。
轴面重合度
εβ=0.318Φd z 1tan β=0.318×1.1×21×tan 12°=1.42
由图查得重合度系数Z ε=0.825由图查得螺旋角系数Z β=0.99 (8) 接触许用应力可由
[σ]H = Z N σHlim
S H
求得,由图(e )、(a )得接触疲劳极限应力σHlim1=570MPa ,σHlim2=390MPa ,S H =1.0。
大小齿轮1、2的应力循环次数分别为
N 1=60n 1aL h =60×960×1.0×3×8×250×5=1.728×109
N 2= N 1
i 1
= 4.32×108
由图查得寿命系数Z N1=1.0,Z N2=1.1(允许有局部点蚀);由表,取安全系数S H =1.0。
[σ]H1= Z N1σHlim S H = 1.0×570
1.0 =570.0MPa
[σ]H2= Z N2σHlim S H = 1.1×390
1.0
=429.0MPa
故取[σ]H = [σ]H2= 429.0MPa
计算小齿轮1的分度圆直径d 1t , 得 d 1t ≥√2K t T ⅠΦd ?u +1u
?(Z E Z H Z εZ β[σ]H )
2
3
=√2×1.4×268001.0?4+14?(189.8×2.45×0.825×0.99429
)2
3
=42.01 mm
确定传动尺寸
(1) 计算载荷系数K 。 由表查得使用系数K A =。 齿轮线速度如下式
v = πd 1t n 160×1000=π×42.01×96060000
=2.11 m/s
由图查得动载荷系数K V = (设轴刚性大);
由图查得齿向载荷分布系数K β=1.10; 由表查得齿间载荷分布系数K α=1.2,故
K =K A K V K βK α=1.0×1.13×1.10×1.2=1.49
(2) 对 d 1t 进行修正。因为K 与K t 有较大差异,故需对按照K t 值设计出来的 d 1t 进行修正,即
d 1= d 1t √K
K t
3
=42.89mm
(3) 确定模数m n
m n =
d 1cos βz 1= 42.89×cos 12°
21
=2.00
按表,取m n=2
(4)计算传动尺寸。中心距
a=m n(z1+z2)
2cosβ
=
2×(21+85)
2×cos12°
=108.37 mm
圆整为a=109mm,则螺旋角
β=arccos m n(z1+z2)
2a
=arccos
2×(21+85)
2×109
=13.47°
因为β值与初选值相差较大,故与β有关的数值需修正,修正后的结果是εα=1.64,εβ=1.61,Zε=0.78,Zβ=0.98,d1=40.31。显然β值改变后,d1的计算值变化很小,因此不再修正m n和a。故
d1=m n z1
=
2×21
=43.189 mm
d2=m n z2
=
2×85
=174.811 mm
b=Φd×d1=1.0×43.189=43.189 mm 圆整为b=45 mm。
取b2=b=45mm,b1=50mm。
校核齿根弯曲疲劳强度
σF=2KT
Ⅰ
n1
Y F Y s YεYβ≤[σF]
式中各参数:
(1)K、T
Ⅰ
、m n同前。
(2)齿宽b = b2=45 mm。
(3)齿形系数Y F与应力修正系数Y s。当量齿数
z v1=
z1
cos3β
=
21
cos13.47°
=22.85
z v2=
z2
cos3β
=
85
cos13.47°
=91.41
查图得齿形修正系数Y F1=2.68,Y F2=2.22。
由图查得应力修正系数Y s1=1.57,Y s2=1.81。
(4)查图得重合度系数Yε=0.72。
(5)查图得螺旋角系数Yβε=0.90。
(6)许用弯曲应力可由下式算得
[σ]F=
Y NσFlim
F
查得弯曲疲劳极限应力
σFlim1=220 MPa,σFlim2=170 MPa 查得寿命系数Y N1=Y N2=1.0。
查得安全系数S F=1.25,故
[σ]F1=Y N1σFlim1
S F
=
1.0×220
1.25
=176 MPa
[σ]F2=Y NσFlim2
S F
=
1.0×170
1.25
=136 MPa
故
σF1=2KT
Ⅰ
bm n d1
Y F1Y s1YεYβ=
2×1.52×16813.38
40×2×36.05
×2.68×1.57×0.72×0.90 =48.32 MPa <[σF1]
σF2=σF1
Y F2Y s2
Y F1Y s1
=48.32×
2.22×1.81
2.68×1.57
=46.14 MPa<[σF2]
满足齿根弯曲疲劳强度要求。
齿轮传动其它几何尺寸
圆柱齿轮几何尺寸表
序号项目代号计算公式计算结果
1 齿数齿轮1 z1/ 21 齿轮
2 z2/ 85
2 法面模数(mm) m n/ 2
3 端面模数(mm) m t m n/cosβ
4 法面压力角(度) αn/ 20
5 端面压力角(度) αt
6 齿顶高系数h an?/ 1
7 顶隙系数c n?/
8 标准中心距(mm) a m n(z1+z2)
2cosβ
109
9 实际中心距(mm) a′109
10 螺旋角β/
11 变位系数齿轮1 x10 齿轮2 x20
12 齿顶高(mm) 齿轮1 h a1
h an?cosβ?m t
2 齿轮2 h a2 2
13 齿根高(mm) 齿轮1 h f1
(h an?+c n?)cosβ?m t 齿轮2 h f2
14 分度圆直径(mm) 齿轮1 d1
m t?z 齿轮2 d2
15 齿顶圆直径(mm) 齿轮1 d a1
d a= d+2xh a 齿轮2 d a2
16 齿根圆直径(mm) 齿轮1 d f1
d f= d-2xh f 齿轮2 d f2
与高速级一样,低速级大、小齿轮均选用45#钢,采用软齿面,小齿轮调制处理,齿面硬度为217~25HBW,平均硬度为236HBW;为保证小齿轮比大齿轮具有更好的机械性
能,大齿轮正火处理,齿面硬度为162~217HBW ,平均硬度为190HBW 。大小齿轮齿面评价硬度差为46HBW ,在30~50HBW 之间。选用8级精度。 初步计算传动主要尺寸
因是闭式软齿面传动,按齿面接触疲劳强度进行设计。根据
d 3≥√2KT 3Φd ?u +1u
?(Z E Z H Z ε[σ]H )2
3
式中各参数为:
(1) 小齿轮传递的转矩T 2。
T 2=102900N ·mm
(2) 设计时,因v 值未知,K v 不能确定,故可初选载荷系数K t = ~,此处初取K t = 。 (3) 由参考文献[1]表取齿宽系数Φd =1.0。
(4) 由参考文献[1]表查得弹性系数Z E =189.8√MPa 。
(5) 由参考文献[1]图查得节点区域系数Z H =2.5。 (6) 齿数比u = i 2=2.73。
(7) 初选z 3=23, 则z 4=uz 3=2.73×23=62.79 ,取z 4=63。传动比误差<5%,符合设计要求。
εα=[1.88 ?3.2(1z 3
+1z 4
)]cos β= [1.88 ?3.2(123+1
63)]×1.0=1.69。
由图查得重合度系数Z ε= 0.87 (8) 接触许用应力可由[σ]H =
Z N σHlim
S H
算得,由高速级齿轮设计可知σHlim3=
570MPa ,σHlim4=390MPa ,S H =1.0。而N 3=N 2,故寿命系数Z N3=Z N2=1.05(允许有局部点蚀),N 4= N 3
i 2
=
4.915×108
2.94
=1.33×108,由参考文献[1]图查得寿命系数Z N4=
1.15(允许有局部点蚀);则
[σ]H3= Z N3σHlim S H = 1.05x570
1.0 =598.5 MPa [σ]H4
= Z N2σHlim S H = 1.15x3901.0
=448.5MPa
故取
[σ]H = [σ]H4= 448.5MPa
计算小齿轮3的分度圆直径d 3t d 3t
≥√2K t T 2Φd ?u +1u
?(Z E Z H Z ε[σ]H )
23
=√2×1.3×83925.301.2×2.73+12.73×(189.8×2.5×0.87448.5
)2
3
=67.473mm
确定传动尺寸
(1) 计算载荷系数K 。
由参考文献[1]表查得使用系数K A =。 齿轮线速度如下式
v=
πd3t n II
60×1000
=
π×67.473×240
60×1000
=0.85 m/s
由参考文献[1]图6.得动载荷系数K V = ;由参考文献[1]图载荷分布系数Kβ=1.1参考文献[1]表得齿间载荷分布系数Kα=1.2故
K=K A K V KβKα=1.0×1.07×1.1×1.2=1.41
(2)因为K与K t相差较大,故需按K t值计算出的d3t进行修正,即
d3=d3t√K K t
3
=67.473×√1.41 1.3
3
=69.325mm (3)确定模数m
m=d3
z3
=
69.325
23
=3.01 mm (按表6.1取m=3mm)
(4)计算传动尺寸。中心距
a=1
2
m(z3+z4)=
1
2
×3×(23+63)=129mm
a)计算传动尺寸
d3=mz3=3×23=69mm
d4=mz4=3×63=189mm
b=Φd d3=69取b3=70 mm,b4=75 mm 。
校核齿根弯曲疲劳强度
σF=2KT
Y F Y s Yε≤[σF]
式中各参数:
(1)K、T2、m同前。
(2)齿宽b = b3=70mm。
(3)齿形系数Y F与应力修正系数Y s。
查参考文献[1] 图得Y F3=2.67,Y F4=2.23
查参考文献[1] 图得Y s3=1.57,Y s4=1.77
查参考文献[1] 图得重合度系数Yε=0.70。
许用弯曲应力可由下式算得
[σF]=
Y NσFlim
F
查得弯曲疲劳极限应力
σFlim3=220 MPa
σFlim4=170 MPa
由前面计算N3=N2=4.915×108,N4=1.33×108查参考文献[1] 图得寿命系数Y N3=Y N4=1.0。
查参考文献[1] 表得安全系数S F =1.25,故
[σF3]= Y N3σFlim3S F = 1.0×220
1.25=176 MPa
[σF4]= Y N σFlim4S F = 1.0×170
1.25
=136 MPa
故
σF3= 2KT II bmd 3Y F3Y s3Y ε= 2×1.45×83925.3070×2.5×57.5
×2.67×1.57×0.70=70.97 MPa
σF4= σF3Y F4Y s4Y F3Y s3=70.97×2.23×1.77
2.67×1.57
≈66.82 MPa
容易看出
σF1<[σF3] σF2<[σF4]
设计满足齿根弯曲疲劳强度要求。 齿轮其他几何尺寸计算
圆柱齿轮几何尺寸表
序号 项目 代号 计算公式
计算结果 1 齿数 齿轮1 z 3 / 23 齿轮2
z 4 / 63 2 模数(mm) m / 3 4 压力角(度) α / 20 6 齿顶高系数 h a ? / 1 7 顶隙系数 c ? / 8 标准中心距(mm) a m (z 3+z 4)
2 129 9 实际中心距(mm) a ′ /
129 11 变位系数 齿轮3 x 3
0 齿轮4 x 4 0
12 齿顶高(mm) 齿轮3 h a3 ?a ?×m
3 齿轮
4 h a4 3 13 齿根高(mm) 齿轮3 h f3 (c ?+h a ?)×m
齿轮4 h f4 14 分度圆直径(mm) 齿轮3 d 3 m ×z 69 齿轮4 d 4 189 15 齿顶圆直径(mm) 齿轮3 d a3 d a = d +2×h a 75 齿轮4 d a4 195 16
齿根圆直径(mm)
齿轮3 d f3 d f = d ?2?h f
齿轮4 d f4
参考参考文献[2]表,a=129mm ,介于100~200mm 之间,用插值法得齿轮最小侧隙
j bnmin =
由参考文献 [2] 式()求得
E sns =- j bnmin /2cos αn =- 2cos20°=
计算齿轮的分度圆直径
d 2=m n z=3ⅹ63=189mm
由表查得,径向跳动公差为
F r =
由表和表查得,切齿径向进刀公差
b r ==ⅹ=
由式求得,齿厚公差
T sn =√F r 2+b r 2×2tan ∝n =√0.0562+0.1452×2tan20°mm=
故由式求得,齿厚下偏差为
E sni =E sns -T sn =由式和得
公法线长度上偏差E bns =E sns ×cos αn =×°mm= 公法线长度下偏差E bni =E sni ×cos αn =×°mm= 公法线长度查表得W K =3×23.0233mm =
三、减速器装配草图设计 草图准备
选定联轴器类型
对于连接电动机和减速器高速轴的联轴器,为了减小启动转矩,其联轴器类型应具有较小的转动惯量和较好的减震性能,故采用弹性柱销联轴器,对于输出轴为了具有减震的作用也采用弹性柱销联轴器。 确定滚动轴承类型 对于高速级斜齿圆柱齿轮传动,因有轴向力,选择角接触轴承;低速级采用深沟球轴承。
确定滚动轴承的润滑和密封方式
由前面计算可知高速级齿轮线速度s,低速级齿轮线速度s,根据最大齿轮(低速级大齿轮),选择油润滑故滚动轴承采用油润滑,并在轴上安装挡油板(避免润滑油对齿轮的冲击)。考虑减速器工作环境有尘,故采用唇形圈密封。
确定轴承端盖的结构形式
凸缘式轴承端盖调整轴承间隙比较方便,密封性能也好,故选用凸缘式轴承端盖,采用铸铁铸造成型。
确定减速器机体的结构方案
考虑工艺性能、材料消耗和制造成本,选用剖分式机体,铸铁材料铸造成型。结构示例图如下图所示:
草图第一阶段
间距确定
(1) 取中间轴上两齿轮轴向间距?4=6mm 。
(2) 因采用油润滑,轴承外圈端面至机体内壁的距离要留出安放挡油板的空间,取
?3=4 mm ;取挡油板宽度C=4 mm 。
(3) 取中间轴上齿轮2端面至机体内壁的距离?2=10 mm 高速轴轴系部件设计
(1) 选择轴的材料
因传递功率不大,且对质量与结构尺寸无特殊要求,故选用45钢并进行调制处理。 (2) 初步轴径d min ,并根据相配联轴器的尺寸确定轴径d 1和长度L 1
对于转轴,按扭转强度初算轴径,由参考文献[3]第759页得,C=97~106,考虑轴端弯矩比转矩小,取C= 97,则
d min
=C √P Ⅰn Ⅰ3
=97×√2.69960
3=13.68 mm
考虑键槽影响,取d min =13.68×(1+5%) mm =14.36 mm 。
(3) 确定轴的轴向固定方式
因为齿轮减速器输出轴的跨距不大,且工作温度变化不大,故轴向固定采用两端固定方式。
(4) 联轴器及轴段①
前面计算的d min 即为轴段①的直径,又考虑轴段①上安装联轴器,因此轴段①的设计与联轴器的设计同时进行。
由前面设计可知,选用弹性柱销联轴器。查文献[1]表取K A =,计算转矩
T c1= K A T Ⅰ=1.5×26.8=40.2 N ·m
由参考文献[2]表查询可得GB/T 5014-2003中的LH1型弹性柱销联轴器符合要求,其参数为:公称转矩160 N ·m ,许用转速为7100 r/min ,轴孔直径范围是12~24 mm 。满足电动机轴径要求。取与轴相连端轴径16 mm ,轴孔长度30 mm ,J 型轴孔,选用A 型键,联轴器主动端代号为HL2 16×30 GB T ?5014?2003。
相应的,轴段①的直径d 1=16mm ,轴段长度应该比联轴器略短,故取其长度为l 1=28 mm
(5) 密封圈与轴段②
联轴器右端采用轴肩固定,取轴肩高度h=1 mm ,则轴段②的直径d_2=18 mm 。 (6) 轴承与轴段③及轴段⑦
由前面设计知,轴承类型为角接触轴承,暂取轴承型号为7304C ,由文献[2]表查得内径d=20 mm ,外径D=52 mm ,宽度B=15 mm ,定位轴肩直径d amin =27 mm ,。故轴段③的直径d 3=20 mm 。
轴段⑦的直径应与轴段③相同,即d 7=20 mm 。 (7) 轴段④
由于齿轮齿根圆直径较小,若选择d 4=30mm ,
d f1?d 4?t 1=38?30?3.3<2.5m n
故轴与齿轮应做成齿轮轴,取过渡轴段d 4=27 mm (8) 齿轮轴段⑤
取l 5=b 1=50 mm 。 (9) 轴段⑥
在轴段⑦和齿轮轴段间取过渡轴段段d 6=27mm (10) 机体与轴段②③④⑥⑦的长度
因采用凸缘式轴承盖,其凸缘厚度e=9 mm 。由于所选联轴器不影响轴承端盖螺栓的拆卸,轴肩与轴承端盖之间的间隙取K=10 mm 。
在确定齿轮、机体、轴承、轴承盖的相互位置与尺寸之后,即可确定各轴段的长度。 取轴段③⑦的长度l 3=l 7=15 mm ; 轴段②的长度l 2=52mm ; 轴段⑥的长度l 6=14 mm ;
轴段④的长度l 4= 93 mm 。
轴的各部分尺寸均确定。取联轴器轮毂中间位置为力的作用点,可得跨距L 1=77.8;L 2=128.8 mm ;L 3=43.2mm 。完成的结构草图如下所示。
(11) 键连接设计
联轴器与轴之间采用A 型普通平键连接,型号为:键 5×25 GB/T 1096—2003,h=5,t 1=2.3 mm 。 中间轴轴系部件设计
(1) 选择轴的材料
因传递功率不大,且对质量与结构尺寸无特殊要求,故选用45钢并进行调制处理。 (2) 初步轴径d min ,并根据相配联轴器的尺寸确定轴径d 1和长度L 1
对于转轴,按扭转强度初算轴径,由参考文献[3]第759页得,C=97~106,考虑轴端弯矩比转矩小,取C= 97,则
d min2
=C √P 2
n 23
=97×√2.58240
3=21.41 mm
(3) 确定轴的轴向固定方式
因为齿轮减速器输出轴的跨距不大,且工作温度变化不大,故轴向固定采用两端固定方式。
(4) 轴承与轴段①及轴段⑤
由前面设计知,轴承类型为角接触轴承,暂取轴承型号为7305C ,由文献[2]表查得内径d=25 mm ,外径D=62 mm ,宽度B=17 mm ,定位轴肩直径d amin =32 mm ,。故轴段①的直径d 1=25 mm 。
轴段⑤的直径应与轴段①相同,即d 5=25 mm 。 (5) 齿轮3与轴段②
为了便于齿轮的安装,d 2应略大于d 1,取d 2=27 mm ,齿轮3左端用套筒固定,则轴段②的长度应略小于齿轮3的宽度b 3,取l 2=73mm 。 (6) 轴段③
齿轮3右端用轴肩固定,取d 3=32 mm 。l 3=6 mm (7) 齿轮2与轴段④
齿轮2左端也用轴肩固定。可取d 4=27mm ,齿轮2右端用套筒固定,则轴段④的长度应略小于齿轮2的宽度b 2,取l 4=43 mm 。 (8) 轴段①⑤的长度
l 1=33 mm l 5=36 mm
完成的结构草图如下所示。 (9) 键连接设计
齿轮2、齿轮3与轴之间采用A 型普通平键连接,型号分别为: 键 8×40GB/T 1096—2003,h=7,t 1=3.3 mm ; 键 8×70 GB/T 1096—2003,h=7,t 1=3.3 mm 。 低速轴轴系部件设计
(1) 选择轴的材料
因传递功率不大,且对质量与结构尺寸无特殊要求,故选用45钢并进行调制处理。 (2) 初步轴径d min ,并根据相配联轴器的尺寸确定轴径d 1和长度L 1 对于转轴,按扭转强度初算轴径,取C=97,则
d min
=C √P 3
n 33
=97×√2.4888
3=29.52 mm
考虑键槽影响,取d min =29.52×(1+5%) mm =30.99mm 。
(3) 确定轴的轴向固定方式
因为齿轮减速器输出轴的跨距不大,且工作温度变化不大,故轴向固定采用两端固定方式。
(4) 联轴器及轴段①
前面计算的即为轴段①的直径,又考虑轴段①上安装联轴器,因此轴段①的设计与联轴器的设计同时进行。
由前面设计可知,选用弹性柱销联轴器。查文献[1]表取K A =,计算转矩
T c3= K A T 3=1.5×264.4=396.6 N ·m
由参考文献[2]表查询可得GB/T 5014-2003中公称转矩630 N ·m 的弹性柱销联轴器满足要求,其许用转速为5000 r/min ,轴孔直径范围是30-48mm 。取与轴相连端轴径32 mm ,轴孔长度为L 1=60 mm ,J 型轴孔。相应的,轴段①的直径d 1=32mm ,取其长度为l 1=58 mm 。
(5) 密封圈与轴段②
联轴器右端采用轴肩固定,取轴段②的直径d 2=38 mm 。 (6) 轴承与轴段③及轴段⑦
由前面设计知,轴承类型为深沟球轴承,暂取轴承型号为6208,由文献[2]表查得内径d=40 mm ,外径D=80 mm ,宽度B=18 mm ,定位轴肩直径d amin =47mm ,。故轴段③的直径d 3=40 mm 。
轴段⑦的直径应与轴段③相同,即d 7=40 mm 。 (7) 轴段⑥
为了便于齿轮的安装,d 6应略大于d 7,取d 6=42 mm ,齿轮3右端用挡油板固定,则轴段⑥的长度应略小于齿轮4的宽度b 6,取l 6=68 mm 。
(8) 轴段⑤
齿轮4右端用轴肩固定,取d 5=48mm 。 (9) 轴段④
取过渡轴段④直径d 4=47mm 。 (10) 机体与轴段②③④⑤⑦的长度
因采用凸缘式轴承盖,其凸缘厚度e=9 mm 。由于所选联轴器不影响轴承端盖螺栓的拆卸,轴肩与轴承端盖之间的间隙取K=10 mm 。
在确定齿轮、机体、轴承、轴承盖的相互位置与尺寸之后,即可确定各轴段的长度。 取轴段③的长度l 3=18 mm ;
轴段②的长度l 2=49 mm ; 轴段⑦的长度l 7=37 mm ; 取轴段⑤的长度l 5=4 mm ; 取轴段④的长度l 4=66mm
轴的各部分尺寸均确定。取联轴器轮毂中间位置为力的作用点,可得跨距L 1=88;L 2=114 mm ;L 3=61 mm 。完成的结构草图如下所示。
(11) 键连接设计
联轴器、和齿轮4与轴之间采用A 型普通平键连接,型号分别为: 键 10×50 GB/T 1096—2003,h=8,t 1=3.3 mm 。 键 12×63 GB/T 1096—2003,h=8,t 1=3.3 mm 。 轴系部件校核计算
本设计已完成高、中、低速轴的轴系部件校核计算,均满足设计要求,此处只给出低速轴校核计算过程。
(1) 轴的受力分析 a. 画受力简图
圆周力F t =
2T Ⅲd
=
2x2.698x105
189
=2855.03 N
径向力F r =F t x tan α=2855.03x tan 20°=1039.14 N b. 计算支反力
F H1=F r xL 3
L 2+L 3
=362.21N
F H2=F r ?F H1=676.93 N
F V1=F t xL 3
23
=995.18 N
F V2=F t ?F V1=1859.85 N
轴承1的总的支反力为
F R1=√F V12+F H122
=√(995.18)2+(362.21)22
=1059.05 N
轴承2的总的支反力为
F R2=√F V22+F H222
=√(1859.85)2+(676.93)22
=1979.21 N
c. 画弯矩图
在水平面上,轴承1处,A-A 面左侧
M aH1=F H1L 2=362.21Nx114 mm =41291.94N ·mm
A-A 面右侧
M aH2=F H2L 3= 676.93 Nx61mm =41292.73 N ·mm
垂直面上,弯矩为
M aV = F V1L 2= 995.18 Nx114mm =113450.52 N ·mm M aV ′=F V2L 3=1859.85 Nx61mm =113450.85N ·mm
A-A 面左侧
M a = √M aH12+M aV 2=58396.18 N ·mm
A-A 面右侧
M a ′= √M aH22+M aV 2=160443.50 N ·mm
d. 画转矩图
T =269800N ·mm
(2) 校核轴的强度
A-A 剖面右侧弯矩大,有转矩,为危险截面。 该截面抗弯模量为
W =0.1d 63?bt (d 6?t )26=0.1x423
?12x5(42?5)2=6430.94 mm 3
该截面的抗扭截面模量为
W T =0.2d 63
?bt (d 6?t )22d 6=0.2x423?12x5(42?5)22x42
=13839.74 mm 3
弯曲应力
σb = M = 160443.50N ·mm 3
=24.95 MPa
σa =σb =24.95 MPa
σm =0
扭剪应力
τT =T W T =269800N ·m 13839.74 mm 3
=19.49 MPa
τa =τm =τT
2
=9.75MPa
调质处理的45钢,由参考文献[3]可以查得σb =650 MPa ,σ?1=300 MPa ,τ?1=155 MPa ;材料等效系数Ψσ=0.2,Ψτ=0.1。
键槽引起的应力集中系数可由参考文献[1]附表得:K σ=1.825,K τ=。 查参考文献[1]附图得εσ=0.8,ετ=0.76。
61mm
114mm 88mm
41292.73
113450.52 160443.50
269800
41291.94
113450.85
58396.18
查参考文献[1]附图与附表得β=0.92。由此,安全系数计算如下:
Sσ=
σ?1
Kσ
βεσσa
+Ψσσm
=
300
1.825
0.92×0.8×24.95+0.2×0
=4.85
Sτ=
τ?1
Kτ
βεττa
+Ψττm
=
155
1.625
0.92×0.76×9.75+0.1×9.75
=6.56
S=στ
√S
σ
2+S
τ
2
=3.90
由参考文献[1]表得许用安全系数[S]=~,显然S>[S],故A-A截面安全。
(3)校核键连接的强度
滚筒与轴连接处为平键连接,挤压应力
σp=4T dhl
式中:d——键连接处的轴径,mm;
T——传递的转矩,N·mm;
h——键的高度,mm;
l——键连接长度,mm;
故
σp=4T
dhl
=
4x269800
42x8x63
= 50.98 MPa
键、轴材料均为45钢,[σp]= 120~150MPa。σp<[σp],故强度满足需要。
(4)校核轴承强度
由参考文献[2]查得6208轴承的C r=29500 N,C0=18100N。轴承工作环境无轴向力,轴承1的工作环境比轴承2工作环境恶劣,故只需校核轴承2。
计算当量动载荷
P=XF r
其中,X为动载荷径向系数,F r为轴承径向载荷。由参考文献[1]表可知,X=1。
则
P=XF r=F r=F R2=1979.21 N
(5)校核轴承寿命
轴承在100℃下工作,f T=1。根据其载荷性质,取f P=1.1。
轴承寿命为
L h=
106
60xn
Ⅲ
(
f T C r
Pf P
)
3
=
106
60x88
x(
1x29500
)
3
=4.71×105 h
已知减速器使用五年,三班工作制,则预期寿命为
L h`=8x3x250x5=30000 h 轴承寿命很充裕。
草图第二阶段
传动件的结构设计
(1)齿轮2结构设计
齿轮2 齿顶圆直径d a2=mm,为了减少质量和节约材料,采用腹板式结构。
采用自由锻毛坯结构,如下图所示。
图中各尺寸如下:
d h=27 mm
D1≈1.6d h=1.6×27=43.2 mm
取
D1=45 mm
D2≈d a?10m=178.81?10?2=158.81 mm,为增强齿根部强度,取D2=160 mm
c=(0.2~0.3)b=(0.2~0.3)×45=9~13.5 mm
取c=10 mm
r=0.5c=0.5×10=5 mm
D0=0.5(D1+D2)=0.5×(45+160)=102.5mm
d0≈0.25(D2?D1)=0.25×(160?45)=28.75 mm
L=(1.2~1.5)d h=42~52.5=45mm
(2)齿轮3结构设计
齿轮3 齿顶圆直径d a3=75mm<200 mm,做成实心式结构。
(3)齿轮4结构设计
齿轮4 齿顶圆直径d a4=195mm,为了减少质量和节约材料,采用腹板式结构。考虑节约成本,采用自由锻毛坯结构,如前图所示。
图中各尺寸如下:
d h=42 mm
D1≈1.6d h=1.6×42=67.2 mm
取D1=70 mm
D2≈d a?10m=195?10×3=165 mm,
取D2=165 mm
c=(0.2~0.3)b4=(0.2~0.3)×70=14~21 mm
取c=18 mm
r=0.5c=0.5×18=9 mm
D0=0.5(D1+D2)=0.5×(70 +165)=117.5 mm
取
D0=120 mm
d0≈0.25(D2?D1)=0.25×(165?70)=22.5mm
取
d0=25 mm
轴承端盖的设计
采用凸缘式轴承端盖,结构如下图所示:
(1)高速轴轴承端盖设计
由前面设计可知,轴承外径D=52mm,d3=8mm,
D2=D+(5~5.5)d3=92~96 mm,取D2=94 mm
D0=0.5(D2+D)=0.5×(94+52)=73mm
d1=18 mm,b1=11mm
(2)中间轴轴承端盖设计
由前面设计可知,轴承外径D=62 mm,d3=8 mm,
D2=D+(5~5.5)d3=102~106 mm,取D2=104 mm。
D0=0.5(D2+D)=0.5×(104+62)=83mm
d1=25 mm,b1=9mm
(3)低速轴轴承端盖设计
由前面设计可知,轴承外径D=80mm,d3=8 mm,
D2=D+(5~5.5)d3=120~124 mm,取D2=122 mm。
D0=0.5(D2+D)=0.5×(122+80)=101 mm
由参考文献[2]表可知, d1=38 mm,b1=12mm
挡油板的设计
挡油板结构如左图所示
套筒设计
(1)中间轴套筒设计
①取内径d1=25 mm,外径d2=34 mm,d2=32 mm长度l=14 mm。
②取内径d1=25 mm,外径d2=34 mm,d2=32 mm长度l=17 mm
(2)低速轴套筒设计
取内径d1=40 mm,外径d2=50 mm,d2=47 mm,长度l1=5 mm,l1=12 mm。
草图第三阶段
减速器机体的结构设计
(1)机体中心高和油面位置的确定
为防止浸油齿轮将油池底部沉积物搅起,大齿轮的齿顶圆到油池底面的距离应不小于30~50 mm。应保证齿轮浸入深度应不小于10 mm,最高油面应比最低油面高出10~15mm,且齿轮浸油深度最多不超过齿轮半径的1/3。按照以上原则,选择机体中心高H=165 mm,油面高度为65mm,满足以上要求。
验算油量:单级减速器传递1kW功率需要油量为~dm3,本设计为二级齿轮减速器,传递的需油量
V0=2×(0.35~0.7)dm3
kW
×2.72kW=(1.904~3.808)×106mm3
油池容量
V=59×150×439=3.89×106mm3
V>V0,满足设计,润滑条件较好。
(2)其他结构设计详见A0图纸。
减速器的附件设计
(1)窥视孔盖和窥视孔
在机盖顶部开有窥视孔,能看到传动零件齿合区的位置,并有足够的空间,以便于能伸入进行操作,窥视孔有盖板,机体上开窥视孔与铸造的凸缘一块,有便于机械加工出支承盖板的表面并用垫片加强密封,盖板用钢板焊接制成,用M6螺栓紧固。
按要求选取A=90,B=60,A
1=120,B
1
=90,C=105,C
1
=70,C
2
=75,R=5,螺钉尺寸M6 20
螺钉数目为4,具体尺寸见参考文献[2]P167页。
(2)放油螺塞
放油孔位于油池最底处,并安排在减速器中部,以便放油,放油孔用螺塞堵住,并加皮封油圈加以密封。选用六角螺塞M12(JB/ZQ 4450-1986),油圈 22×15 ZB 70-62。
(3)油标指示器
选取M12的杆式油标。参数如下:
具体尺寸见参考文献[3]P14页。油标位置箱体中部。油尺安置的部位不能太低,以防油进入油尺座孔而溢出.
(4)通气孔
由于减速器运转时,机体内温度升高,气压增大,为便于排气,在机盖顶部的窥视孔改上安装通气器,以便达到体内为压力平衡。由于是在有尘的环境下,只需使用简易通气孔。选取简易通气孔。具体尺寸选取查阅参考文献[3]P14页。
(5)吊钩和吊耳
吊耳参数如下:d=(1.8~2.5)δ1=(14.4~20) mm,取d=16 mm;e=(0.8~1.0)d= (12.8~16),取e=16 mm;s=2δ1=16 mm;取R=16mm。
在机盖上上直接铸出吊耳和吊钩,用以起吊或搬运较重的物体。吊钩参数如下:B= c1+c2=30;s=2δ=20 mm;H=(0.8~1.0)B=(24~30)mm,取H=30 mm;h= (0.5~0.6)H=(15~18)mm,取h=15 mm;r=0.25B=7.5
具体尺寸由参考文献[3]P15页的经验公式选取。
(6)定位销:
为保证剖分式机体的轴承座孔的加工及装配精度,在机体联结凸缘的长度方向各安装一圆锥定位销,以提高定位精度。选取公称直径为8的圆锥销,采用非对称布置。具体尺寸见参考文献[2]P118页表圆柱销(GB/)。
(7)启盖螺钉
启盖螺钉上的螺纹长度要大于机盖联结凸缘的厚度。选取与机盖和机座连接螺栓相同规格的螺栓作为启盖螺栓。螺钉杆端部要做成圆柱形或大倒角,以免破坏螺纹。
参考文献:
[1]王黎钦,宋宝玉. 机械设计. 哈尔滨:哈尔滨工业大学出版社,2010
[2]宋宝玉. 机械设计课程设计指导书.高等教育出版社,2006
[3]宋宝玉. 简明机械设计课程设计图册.高等教育出版社,2007