圆锥形零件拉深成形过程中接解应力分布的研究
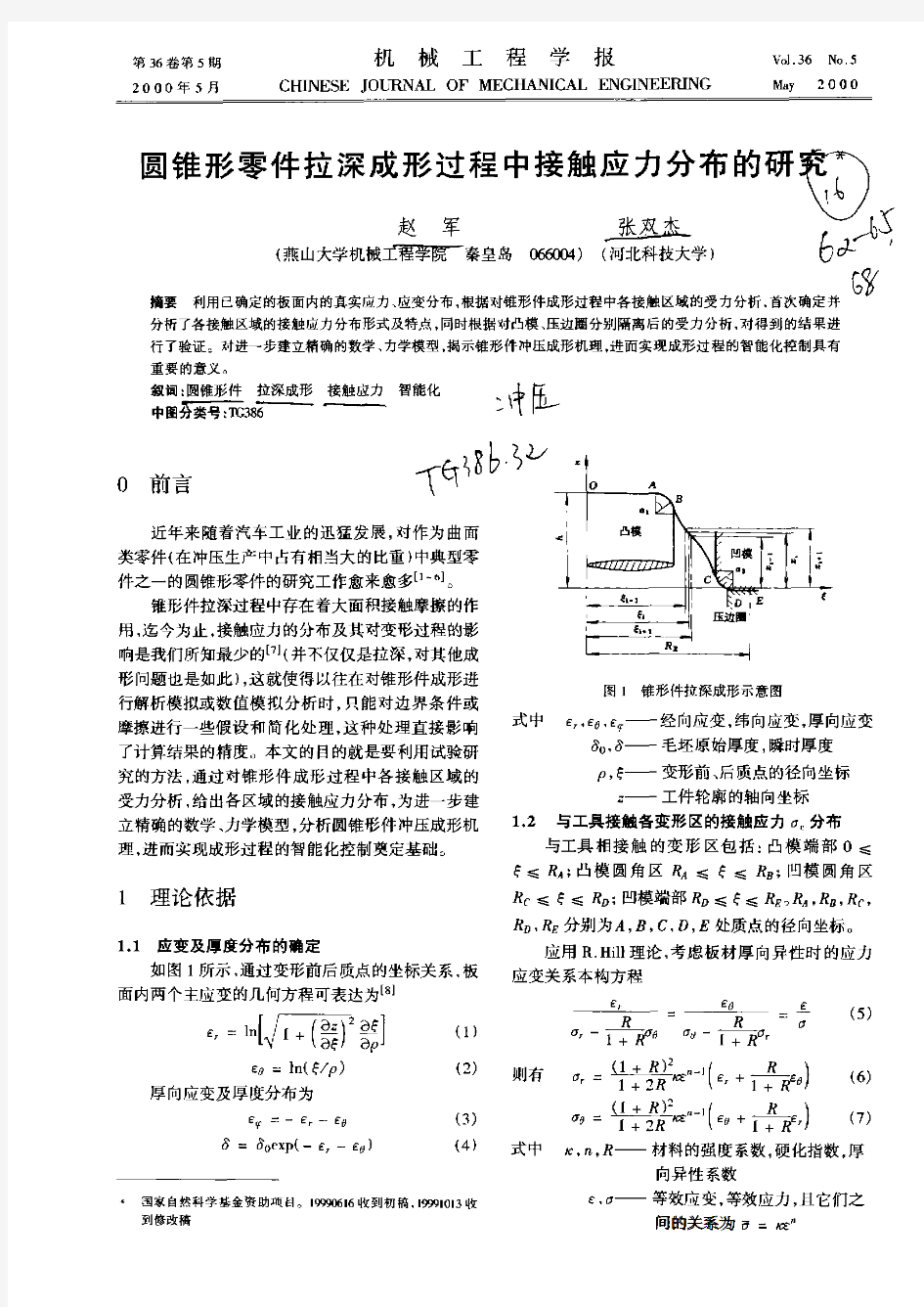

桩身应力测试分析报告
精心整理第一章工程概况
根据**院提供的岩土工程勘察报告,该场地工程地质条件如下:
三、检测桩位示意图 四、钢筋应力计在桩身埋设位置示意图 钢筋应力计在各试桩中位置示意图
二、测试设备及钢筋测力计的埋设 1、每桩钢筋应力计设置在各土层交界面处,每一个截面设2只钢筋测力计(基本呈180°对称布置),各钢筋应力计埋设截面的平、剖面图如前图; 2、JTM-V1000振弦式钢筋应力计采用焊接法固定在钢筋笼主筋上,并与桩身纵轴线平行;
3、连接在应力计的电缆线用柔性材料保护,绑扎在钢筋笼内侧并 引至地面; 4、所有应力计均用明显标记编号; 5、仪器设备:检测仪器设备采用JTM-V1000振弦式钢筋应力计、JTM-V10B 型频率读数仪、集线箱等组成。 三、测试原理 1位2ε c1j = εεs1j 3E cj 、E sj —砼弹性模量、钢筋弹性模量[E s 取2.0×108(kPa)] A cj 、A sj —同一截面处砼面积、钢筋总面积。 εcj 、εsj —同一截面处砼与钢筋的应变 4、钢筋应力计受力的计算公式: ) 2()(' 2 02 ----------------??=-?=Si Sij S i ij Sij A E F F k P ε
式中: P Sij —第i 量测截面处在j 级荷载下应力计所受轴向力(kN ) F ij —第i 量测截面处在j 级荷载下应力计的实测频率值(Hz) F i0—i 截面处钢筋应力计的初始频率值(Hz ) K A si ’—56f ij P ij —i A i 12、弦式钢筋应力计宜放在两种不同性质土层的界面处,以测量桩在不同土层中的分层摩阻力。在地面处(或以上)应设置一个测量断面作为钢筋应力计传感器标定断面。钢筋应力计埋设断面距桩顶和桩底的距离不宜小于1倍桩径。在同一断面处对称设置2个钢筋应力计。钢筋计应按主筋直径大小选择。仪器的可测频率范围应大于桩在最大加载时的频率的1.2倍; 3、使用前应对钢筋计逐个标定,得出压力(拉力)与频率之间的关系。带有接长 ) 3()(' -------------------------?= Si S Sij Sij A E P ε
放大镜模具的设计与制造
目录前言 第一章料工艺分析 1、1分析塑料使用材料得种类及工艺特征 1、2分析塑料得结构工艺性 1、3塑件精度确定 1、4 明确塑件批量生产 1、5 根据塑件得形状估算其体积与重量 1、6 确定型腔数 第二章定模具结构方案 2、1 确定型腔排列 2、2 确定分型面 2、3 脱模原理 2、4 浇注系统形式 2、4、1 主流道设计 2、4、2 分流道设计 2、4、 3、浇口设计 2、5冷却及加热系统 第三章模具设计得有关计算 3、1模具主要零件得有关尺寸设计 3、1、1型腔与型芯计算 3、2 型腔厚度与底板厚度得确定 3、3确定零件结构及尺寸 3、3、1定模座板设计 3、3、2定模型腔固定板设计 3、3、3 动模型腔固定板设计 3、3、4 支撑板设计设计
3、3、5 推杆固定板设计 第四章初选注射机 4、1计算浇注系统体积 4、1初选注射机 第五章核注射机有关工艺参数 5、1注射量得校核 5、2锁模力与注射压力 5、3模具厚度H与注射机闭合高度 第六章结束语 参考文献 摘要注塑模具就是在成型中赋予塑料以形状与尺寸得部件。模具得结构虽然由于塑料品种与性能、塑料制品得形状与结构以及注射机得类型等不同而可能千变万化,但就是基本结构就是一致得。模具主要由浇注系统、成型零件与结构零件三部分组成。其中浇注系统与成型零件就是与塑料直接接触部分,并随塑料与制品而变化,就是塑模中最复杂,变化最大,要求加工光洁度与精度最高得部分。 对此次放大镜无多大要求,它得整体尺寸不大,但要大批生产,为提高生产率,降低成本,故采用模具成批注射生产。并且该产品为放大镜要透光,所以材料采用聚苯乙烯(PS)做为材料。 对于浇注系统与成型零件得设计;浇注系统就是指塑料从射嘴进入型腔前得流道部分,包括主流道、冷料穴、分流道与浇口等。成型零件就是指构成制品形状得各种零件,包括动模、定模与型腔、型芯等。 此套放大镜模实现部分机械操作自动化,浇注系统采用普通流道,进行一模二腔注射。顶出机构由2条型芯与一条推杆顶出,型腔分动模型腔与定模型腔。 前言 此次设计为放大镜得注射成型模具设计。对于这次得设计首要制定得塑料成型工艺以及合理设计塑料成型模具得过程。 前面部分主要说明塑料成型得必要理论基础,包括高分子聚合物结构特点与性能,尤其就是聚合物得热力学性能与化学性质,还有聚合物熔体在成型过程中得流动状态及物理与化学变化。后面部分说明得就是注射成型模具设计得最复杂也最具代表性得部分,主要说明注射成型模具得设计,包括浇注系统(主流道,浇口,分流道)、成型零件(型芯,型腔,推杆等)得设计,对所选注射机得校核等有关设计。 由于塑料注射成型模具对于实践性很强,并且技术正在飞速发展中,所以在设计过程中注重理论联系实际,对于书中得知识要加以联系实际,从而使模具设计得更加合理。 第一章塑件工艺分析 1、1 分析塑件使用材料得种类及工艺特征
实验力学实验分析报告
实验力学实验报告
————————————————————————————————作者:————————————————————————————————日期:
实验力学实验报告 姓名:耿臻岑 学号:130875 指导老师:郭应征
实验一薄壁圆管弯扭组合应力测定实验 一、实验目的 1、用应变花测定薄壁圆管在弯扭条件下一点处的主应力和主方向 2、测定薄壁圆管在弯扭组合条件下的弯矩、扭矩和剪力等内力 3、进一步熟悉和掌握不同的桥路接线方法 4、初步了解在组合变形情况下测量某一内力对应应变的方法 二、实验设备 1、电阻应变仪YJ-28 2、薄壁圆管弯扭组合装置,见图1-1 本次实验以铝合金薄壁圆管EC为测试对象,圆管一段固定,另一端连接与之垂直的伸臂AC,通过旋转家里手柄将集中荷载施加在伸臂的另一端,由力传感器测出力的大小。荷载作用在伸臂外端,其作用点距圆通形心为b,圆通在荷载F 作用下发生弯扭组合变形。要测取圆筒上B截面(它到荷载F作用面距离为L)处各测点的主应力大小和方向。试样弹性模量E=72GPa,泊松比μ=0.33,详细尺寸如表1-1 图1-1 薄壁圆筒弯扭组合装置 表1-1 试样参数表 外径D(mm) 内径d(mm) b(mm) L(mm)
40 34 200 300 三、实验原理 1、确定主应力和主方向 平面应力状态下任一点的应力有三个未知数(主应力大小及方向)。应用电阻应变仪应变花可测的一点沿不同方向的三个应变值,如图1-2所示的三个方向已知的应变。根据这三个应变值可以计算出主应变的大小和方向。因而主应力的方向也可确定(与主应变方向重合) ()() () () 45450 4545 22 4545 1,2450450 4545 04545 112 2 221 2 2 22 tan2 2 1 1 x y xy E E εε εεεε γεε εε εεεεε εε α εεε σεμε μ σεμε μ - - - - - - = =+- =- + =±-+- - = -- =+ - =+ - o o o o o o o o o o o o o o o o o 图1-2 应变花示意图图1-3 B、D点贴片位置示意图 2、测定弯矩 在靠近固定端的下表面D上,粘一个与点B相同的应变花,如图1-3所示。将B点的应变片和D点的应变片,采用双臂测量接线法(自补偿半桥接线法),得:()() () 000 44 2 2 64 r T T r r E E E D d M D εεεεεε ε σε π ε =+--+= == - =
塑料成型工艺及模具设计考试试题
徐州工程学院 塑料成型工艺及模具设计考试题目及答案 一、填空(本题共10小题,每空1分,共20分) 1.顶出推板与凸模(型芯)在安装时应采用锥面配合,其目的是辅助定位,防止偏心溢料。 2.螺杆式注塑机与柱塞式相比,其优点在于__螺杆式注塑机剪切塑化能力强,塑化量大_。 3.调湿处理是针对吸湿性塑料而言,具体方法是将制品放在热水中处理。 4.压制成形与压铸成形均可用于热固性塑料,二者在模具结构上的主要差别在于压铸模具有浇注系统,而 压制成型没有。 5. ABS属于高强度塑料,在注塑成型前需要预先干燥,而且成型时的流动性也稍差。 6.在斜抽芯机构中锁紧楔的楔角一般比斜导柱的倾斜角大。主要是为了模具开模时防止造成干涉。 7.塑件允许的最小壁厚与塑料品种和塑件尺寸有关。 8.塑料模的基本结构都由动模和定模两大部分组成。 9.型腔气体的排除,除了利用顶出元件的配合间隙外,主要靠分型面,排气槽也都设在分型面上。 10. 塑件尺寸精度的影响因素有很多,在计算时需考虑的主要有:成型零部件的制造误差、成型零部件的磨损和塑料的成型收缩。 11. 当分流道设计的比较长时,其末端应留有冷料穴,以防前锋冷料阻塞浇口或进入模腔,造成充模不 足或影响制品的熔接强度。 12. 适用于要求自动切除浇口凝料的注塑模浇口方式是潜伏式浇口。 二、判断正误(本题共10小题,每题1分,共10分) 1. 厚壁塑件不容易产生表面凹陷和内部缩孔。 (×) 2. 当模具采用脱件板脱模机构时,可以采用Z形拉料杆与冷料井匹配。 (×) 3. 冷却系统的通道要尽量避开塑件的熔接痕部位,以免影响塑件的强度。 ( √ ) 4. 斜导柱侧抽芯机构中的滑块导滑长度有一定的要求,完成抽拔后,滑块留在导滑槽中 的长度不应小于
车架应力应变实验报告
车架应力应变实验 一、 实验目的: (1) 熟悉应变片的粘贴方法 (2) 学会策略电路的连接 (3) 了解数据采集仪的操作 二、 工作原理: 用以金属材料为敏感元件的应变片,测量试件应变的原理是基于金属丝的应变效应,即金属丝的电阻随其变形而改变的一种物理特性。将应变片固定在被测构件上,当构件变形时,电阻应变片的电阻值发生相应的变化。通过电阻应变测量装置(简称应变仪)可将电阻应变片中的电阻值的变化测定出来,换算成应变或输出与应变呈正比的模拟电信号(电压或电流),用记录仪记录下来,也可用计算机按预定的要求进行数据处理,得到所需要的应力或应变值。 应变片的结构:它由敏感元件、引出线、基底、覆盖层组成,用粘贴剂粘贴在一起,如图所示。 A l R ρ =
ρ=导线电阻率 L=导线长度 A=导线横截面积 电桥:将电阻、电感、电容等参量的变化转换为电压或电流输出的一种测量电路。 当输出电压i U =0时,表示电桥处于平衡,可得R 1R 3=R 2 R 4,直流电桥平衡,若在四个电阻处均接应变片,并使R 1R 3=R 2 R 4 若无应变,则输出电压i U =0 若产生应变, 43214 231i ) )((U R R R R R R R R U ?++-= ερ ρ )21(u d R dR ++=A dA l dl d R dR -+=ρρ??? ????-?+?-??+=?])(4433221 1221210i R R R R R R R R R R R R U U
三、实验流程图 本小组进行实验位置为第9测点,位置如图所示: 四、实验仪器 1.应变片 2.502胶水 3.万用表 4.电烙铁、焊锡、松香 5.绝缘胶带纸、脱脂棉、丙酮、0#砂纸、导线 6.接线盒 7.Synergy16通道采集仪 五、实验操作步骤 1.应变片的准备 贴片前,将待用的应变片进行外观检查,检查是否有锈斑等缺陷,基底和覆盖层有无损坏,引线是否完好。然后用万用表进行阻值测量。 目的在于检查敏感栅是否有断路、短路,阻值相差不得超过。同一次测 量的变计,灵敏系数必须相同。经测得阻值为120±0.5Ω。 2.车架表面处理准备 对于钢铁等金属构件,首先是清除表面油漆、氧化层和污垢;然后磨平或锉
成型零件设计
成型零件的设计 成型零件的结构设计主要是指构成模具型腔的零件,通常有凹模、型芯、各种成形杆和成形环。 模具的成型零件主要是凹模型腔和底板厚度的计算,塑料模具型腔在成型过程中受到熔体的高压作用,应具有足够的强度和刚度,如果型腔侧壁和底板厚度过小,可能因强度不够而产生塑性变形甚至破坏;也可能因刚度不足而产生挠曲变形,导致溢料飞边,降低塑件尺寸精度并影响顺利脱模。因此,应通过强度和刚度计算来确定型腔壁厚,尤其对于重要的精度要求高的或大型模具的型腔,更不能单纯凭经验来确定型腔壁厚和底板厚度。 注射模具的成型零件是指构成模具型腔的零件,通常包括了凹模、型芯、成型杆等。凹模用以形成制品的外表面,型芯用以形成制品的内表面,成型杆用以形成制品的局部细节。成形零件作为高压容器,其内部尺寸、强度、刚度,材料和热处理以及加工工艺性,是影响模具质量和寿命的重要因素。 设计时应首先根据塑料的性能、制件的使用要求确定型腔的总体结构、进浇点、分型面、排气部位、脱模方式等,然后根据制件尺寸,计算成型零件的工作尺寸,从机加工工艺角度决定型腔各零件的结构和其他细节尺寸,以及机加工工艺要求等。此外由于塑件融体有很高的压力,因此还应该对关键成型零件进行强度和刚度的校核。 在工作状态中,成型零件承受高温高压塑件熔体的冲击和摩擦。在冷却固化中形成了塑件的形体、尺寸和表面。在开模和脱模时需要克服于塑件的粘着力。在上万次、甚至上几十万次的注射周期,成型零件的形状和尺寸精度、表面质量及其稳定性,决定了塑件制品的相对质量。成型零件在充模保压阶段承受很高的型腔压力,作为高压容器,它的强度和刚度必须在容许范围内。成型零件的结构,材料和热处理的选择及加工工艺性,是影响模具工作寿命的主要因素。 一、成型零件的选材 对于模具钢的选用,必需要符合以下几点要求: 1、机械加工性能良好。要选用易于切削,且在加工以后能得到高精度零件的钢种。 2、抛光性能优良。注射模成型零件工作表面,多需要抛光达到镜面,Ra≤0.05μm。要求钢材硬度在HRC35~40为宜。过硬表面会使抛光困难。钢材的显微组织应均匀致密,极少杂质,无疵斑和针点。 3、耐磨性和抗疲劳性能好。注射模型腔不仅受高压塑料熔体冲刷,而且还受冷热温度交变应力作用。一般的高碳合金钢可经热处理获得高硬度,但韧性差易形成表面裂纹,不以采用。所选钢种应使注塑模能减少抛光修模次数,能长期保持型腔的尺寸精度,达到所计划批量生产的使用寿命期限。 4、具有耐腐蚀性。对有些塑料品种,如聚氯乙稀和阻燃性的塑料,必须考虑选用有耐腐蚀性能的钢种。
梁弯曲正应力测量实验报告
厦 门 海 洋 职 业 技 术 学 院 编号:XH03J W024-05/0 实训(验) 报告 班级: 姓名: 座号: 指导教师: 成绩: 课程名称: 实训(验): 梁弯曲正应力测量 年 月 日 一、 实训(验)目的: 1、掌握静态电阻应变仪的使用方法; 2、了解电测应力原理,掌握直流测量电桥的加减特性; 3、分析应变片组桥与梁受力变形的关系,加深对等强度梁概念的理解。 二、 实训(验)内容、记录和结果(含数据、图表、计算、结果分析等) 1、实验数据: (1) 梁的尺寸: 宽度b =9mm ;梁高h=30mm ;跨度l =600mm;AC 、BD:弯矩a=200m m。测点距轴z 距离: 21h y ==15mm;42h y ==7.5mm ;3y =0cm ;-=-=44h y 7.5mm;-=-=2 5h y 15mm;E=210Gpa 。 抗弯曲截面模量W Z =b h2/6 惯性矩J Z =bh 3 /12 (2) 应变)101(6-?ε记录:
(3) 取各测点ε?值并计算各点应力: 1ε?=16×10-6 ;2ε?=7×10-6 ;3ε?= 0 ;4ε?=8×10-6 ;5ε?=15×10 - 6 ; 1σ?=E 1ε?=3.36MPa;2σ?=E 2ε?=1.47MP a;3σ?=0 ; 4σ?=E 4ε?=1.68MPa;5σ?=E 5ε?=3.15MPa ; 根据ΔM W=ΔF ·a/2=5 N ·m 而得的理论值: 1σ?=ΔM W/W Z =3.70MPa;2σ?=ΔMWh/4(J Z)=1.85M Pa ;3σ?=0 ; 4σ?=ΔM W h/4(J Z )=1.85MPa;5σ?=ΔMW /W Z=3.70MPa; (4) 用两次实验中线形较好的一组数据,将平均值ε?换算成应力εσ?=E ,绘在坐标 方格纸上,同时绘出理论值的分布直线。
桩身应力测试报告
第一章工程概况一、工程概述
二、工程地质条件(工程地质柱状图) 根据**院提供的岩土工程勘察报告,该场地工程地质条件如下:
三、检测桩位示意图 四、钢筋应力计在桩身埋设位置示意图 钢筋应力计在各试桩中位置示意图
钢筋应力计埋设位置表
第二章桩身内力测试 一、检测目的 本次检测目的是测定在各级荷载作用下桩身不同位置的轴力和桩侧摩阻力的分布情况。 二、测试设备及钢筋测力计的埋设 1、每桩钢筋应力计设置在各土层交界面处,每一个截面设2只钢筋测力计(基本呈180°对称布置),各钢筋应力计埋设截面的平、剖面图如前图; 2、JTM-V1000振弦式钢筋应力计采用焊接法固定在钢筋笼主筋上,并与桩身纵轴线平行; 3、连接在应力计的电缆线用柔性材料保护,绑扎在钢筋笼内侧并引至地面; 4、所有应力计均用明显标记编号; 5、仪器设备:检测仪器设备采用JTM-V1000振弦式钢筋应力计、JTM-V10B型频率读数仪、集线箱等组成。 三、测试原理 1、假定:同一截面钢筋与混凝土的变形协调;桩顶下砼弹性模量相同;位于桩顶面以下1.8m处的J1截面所受轴力与静载荷试验的加
载量相同; 2、桩身范围内砼弹性模量E cij 的确定:将J1截面作为标定截面(i =1),量测该截面钢筋应力计在包括预压的各级荷载作用下频率变化值,用此推算各载荷等级下钢筋应变εs1j ,由于假定砼与钢筋协同受力,不出现裂缝,故砼应变εc1j =εs1j ,由此可以算出各载荷等级下桩身砼的弹性模量E c1j 。利用钢筋应变εs1j 与桩身砼的弹性模量E c1j 的两组数据可以拟合出关于两者之间的相关关系,根据其余各截面在各载荷等级下钢筋应变εsij ,再通过其相关关系可以得到各截面在各载荷等级下的 E cij ; 3、某一截面桩身轴力P Zj 计算公式为: 式中: E cj 、E sj —砼弹性模量、钢筋弹性模量[E s 取2.0×108(kPa)] A cj 、A sj —同一截面处砼面积、钢筋总面积。 εcj 、εsj —同一截面处砼与钢筋的应变 4、钢筋应力计受力的计算公式: 式中: P Sij —第i 量测截面处在j 级荷载下应力计所受轴向力(kN ) F ij —第i 量测截面处在j 级荷载下应力计的实测频率值(Hz) F i0—i 截面处钢筋应力计的初始频率值(Hz ) ) 2()(' 2 02 ----------------??=-?=Si Sij S i ij Sij A E F F k P ε) 1()(-----??+?=??+??=j S j S Sj j C j C j S Sj j S j C j C j C j Z A E A E A E A E P εεε) 3()(' -------------------------?= Si S Sij Sij A E P ε
塑料模具成型零件的设计
塑料模具成型零件的设计 构成塑料模具模腔的零件统称成型零件。成型零件是模具的主要部分,决定了塑件的几何形状和尺寸,主要包括凹模、凸模、镶块、小型芯和成型环等。成型零件工作时,直接与塑料熔体接触,承受熔体料流的高压冲刷、脱模磨擦等。因此,成型零件不仅要求有正确的几何形状,较高的尺寸精度和较低的表面粗糙度,而且还要求有合理的结构,较高强度、刚度及较好的耐磨性。 设计塑模的成型零件时,应根据塑件的塑料性能、使用要求、几何结构,并结合分型面和浇口位置的选择、脱模方式和排气位置的考虑来确定型腔的总体结构,根据塑件的尺寸、计算成型零件型腔的尺寸;确定型腔的组合方式;确定成型零件的机加工、热处理、装配等要求。对关键的部位进行强度和刚度校核。 1 成型零件的结构设计 1.1 凹模的结构设计 凹模亦称型腔,是成型塑件外表面的主要零件,按结构不同可分为整体式和组合式两种结构形式。 一整体式凹模结构 整体式凹模结构是在整体金属模板上加工而成的,如图5-3-1所示,其特点是牢固、不易变形,不会使塑件产生拼接线痕迹。但是加工困难,热处理不方便,常用于形状简单的中、小型模具上。 图5-3-1 整体式凹模结构 二组合式凹模结构 组合式凹模结构的型腔是由两个或两个以上的零部件组合而成的。按组合方式不同,可为整体嵌入式、局部镶嵌式和四壁拼合式等形式。 (1)整体嵌入式凹模 如图5-3-2所示,小型塑件采用多型腔模具成型时,各单个型腔采用机械加工、冷挤压、电加工等到方法加工制成,然后压入模板中。这种结构加工效率高,装拆方便,可以保证各个型腔的形状尺寸一致。图5-3-2a~c称为通孔台肩式,凹模带有台肩,从下面嵌入模板,再用垫板螺钉紧固。如果凹模镶件是回转体,而型腔是非回转体,则需要用销钉或键止转定位。图5-3-2b采用销钉定位,结构简单,装拆方便;图5-3-2c是键定位,接触面积大,止转可靠;图5-3-2d是通孔无台肩式,凹模嵌入模板内用螺钉与垫板固定;图5-3-2e是盲孔式,凹模嵌入固定板后直接用螺钉固定在固定板下部设计有装拆凹模用的工艺通孔,这种结构可省去垫板。
成型零部件结构设计
成型零部件结构设计 成型零部件的结构设计包括凹模结构设计、凸模结构设计以及螺纹型芯和螺纹型环的结构设计等。 1 .凹模结构设计 凹模用于成型塑件的外表面,又称为阴模、型腔。按其结构的不同可分为整体式、整体嵌人式、局部镶嵌式、大面积镶嵌式和因壁镶嵌式五种。总体来说,整体式强度、刚度好,但不适用于复杂的型腔。镶嵌式采用组合的模具结构,使复杂的型腔加工相对容易,可避免采用同一材料,可利用拼接间隙排气,但易在塑件表面留下镶嵌块的拼接痕迹。 对凹模的各种结构类型分别介绍如下。 ( 1 )整体式。由整块金属材料直接加工而成,如图4 一55 所示,用于形状简单的中小模具。特点是强度高、刚性好。 ( 2 )整体嵌人式。将整体式凹模作为一种凹模块直接嵌人到固定板中,或嵌人模框中,模框再嵌人到固定板中。适用于塑件尺寸不大的多腔模。特点是加工方便,易损件便于更换,凹模可用冷挤压或其他方法单独加工,型腔形状与尺寸一致性好。图4 一56 ( a ) 所示为凹模从凹模固定板下部嵌人,用支承板、螺钉将其固定;图4 一56 ( b )所示为凹模从凹模固定板上部嵌人。
( 3 )局部镶嵌式。当凹模局部形状复杂,或某一部分容易损坏需要经常更换,常采用局部镶嵌式结构。如图4 一57 所示,其中,图4 一57 ( a )所示为嵌入圆销成型塑件表面直纹;图4 一57 ( b )所示为镶件成型塑件的沟槽;图4 一57 (。)所示为镶件构成塑件圆环形筋槽;图4 一57 ( d )所示为镶件成型塑件底部复杂的构形。 ( 4 )大面积镶嵌式。对于底部或侧壁形状复杂的凹模,为了便于加工,保证精度,将凹模做成通孔式的,再镶上底,或将凹模壁做成镶嵌块。适用于深腔或底部、侧壁难于加工的组合型模具型腔,但各个结合面的研磨、抛光增加了工时.图4 一58 ( a )所示为侧壁和底部大面积镶拼的凹模结构;图4 一58 ( b )所示为底部大面积镶嵌的结构,采用圆柱面配合。
弯曲正应力实验报告
弯曲正应力实验 一、实验目的:1、初步掌握电测方法和多点测量技术。; 2、测定梁在纯弯和横力弯曲下的弯曲正应力及其分布规律。 二、设备及试样: 1. 电子万能试验机或简易加载设备; 2. 电阻应变仪及预调平衡箱; 3. 进行截面钢梁。 三、实验原理和方法: 1、载荷P 作用下,在梁的中部为纯弯曲,弯矩为1 M=2 Pa 。在左右两端长为a 的部分内为横力弯曲,弯矩为11 =()2 M P a c -。在梁的前后两个侧面上,沿梁的横截面高度,每隔 4 h 贴上平行于轴线上的应变片。温度补偿块要放置在横梁附近。对第一个待测应变片联同温度补偿片按半桥接线。测出载荷作用下各待测点的应变ε,由胡克定律知 E σε= 另一方面,由弯曲公式My I σ=,又可算出各点应力的理论值。于是可将实测值和理论值进 行比较。 2、加载时分五级加载,0F =1000N ,F ?=1000N ,max F =5000N ,缷载时进行检查,若应变差值基本相等,则可用于计算应力,否则检查原因进行复测(实验仪器中应变ε的单位是 610-)。 3、实测应力计算时,采用1000F N ?=时平均应变增量im ε?计算应力,即 i i m E σε?=?,同一高度的两个取平均。实测应力,理论应力精确到小数点后两位。 4、理论值计算中,公式中的3 1I=12 bh ,计算相对误差时 -100%e σσσσ= ?理测 理 ,在梁的中性层内,因σ理=0,故只需计算绝对误差。 四、数据处理 1、实验参数记录与计算: b=20mm, h=40mm, l=600mm, a=200mm, c=30mm, E=206GPa, P=1000N ?, max P 5000N =, k=2.19 3 -641I= =0.1061012 bh m ? 2、填写弯曲正应力实验报告表格
应力测试设备评估报告
应力测试设备评估报告
目录 目录 (2) 第1章目的和范围 (3) 1.1 1.2目的 (3) 范围 (3) 第2章应力测试设备简介 (4) 2.1应力测试设备组成及技术要点 (4) 第3章应力测试设备的原理及市场调查 (5) 3.1应力测试设备各厂家性能对比 (5) 第4章采购必要性分析 (6) 4.1 4.2 4.3现状分析 (6) 应力测试设备资源分析 (7) 分析结论 (7)
第1章目的和范围 1.1 目的 通过分析与研究应力测试设备,根据行业发展趋势,结合现有客户要求及生产条件,评估是否需要导入应力测试设备,监控产品在生产过程中的应力风险,提升产品的焊接可靠性,满足客户的质量要求,保证公司以产品质量为基石的发展策略。 1.2 范围 根据IPC-9704 印制板应变测试指导要求,应力测试设备适用于PCBA段所有产生形变的工序,主要有印刷,贴片,分板,测试,组装,压接,包装,周转等。
第2章应力测试设备简介 2.1 应力测试设备组成及技术要点 应力测试设备由测试仪主机、连接电缆线、接线盒及辅助设备(软件狗,数据线,电源适配器等)组成。 2.1.1测试仪主机 应力测试设备的主机是将应变片的信息进行储存,并通过软件狗自带的软件进行数据分析,将阻值变化的信号转化成数据量化输出应变值。 2.1.2连接电缆线 电缆线目的用于测试仪主机与应变片的信号传输。 2.1.3接线盒 接线盒主要是连接应变片的作用。 2.1.4辅助设备 辅助设备主要有下面几种: 电源适配器主要给主机供电;数据线是将仪器与电脑连接,将信号传输;软件狗主要是含采集软件,对各种数据分析报告并形成报告;
桩身应力测试报告材料
第一章工程概况
根据**院提供的岩土工程勘察报告,该场地工程地质条件如下:
三、检测桩位示意图 四、钢筋应力计在桩身埋设位置示意图 钢筋应力计在各试桩中位置示意图
第二章桩身内力测试 一、检测目的 本次检测目的是测定在各级荷载作用下桩身不同位置的轴力和桩侧摩阻力的分布情况。 二、测试设备及钢筋测力计的埋设 1、每桩钢筋应力计设置在各土层交界面处,每一个截面设2只钢筋测力计(基本呈180°对称布置),各钢筋应力计埋设截面的平、剖面图如前图; 2、JTM-V1000振弦式钢筋应力计采用焊接法固定在钢筋笼主筋上,并与桩身纵轴线平行; 3、连接在应力计的电缆线用柔性材料保护,绑扎在钢筋笼内侧并引至地面; 4、所有应力计均用明显标记编号; 5、仪器设备:检测仪器设备采用JTM-V1000振弦式钢筋应力计、JTM-V10B型频率读数仪、集线箱等组成。 三、测试原理 1、假定:同一截面钢筋与混凝土的变形协调;桩顶下砼弹性模量相同;位于桩顶面以下1.8m处的J1截面所受轴力与静载荷试验的加载量相同; 2、桩身范围内砼弹性模量E cij的确定:将J1截面作为标定截面(i=1),量测该截面钢筋应力计在包括预压的各级荷载作用下频率变化
值,用此推算各载荷等级下钢筋应变εs1j ,由于假定砼与钢筋协同受力,不出现裂缝,故砼应变εc1j =εs1j ,由此可以算出各载荷等级下桩身砼的弹性模量E c1j 。利用钢筋应变εs1j 与桩身砼的弹性模量E c1j 的两组数据可以拟合出关于两者之间的相关关系,根据其余各截面在各载荷等级下钢筋应变εsij ,再通过其相关关系可以得到各截面在各载荷等级下的E cij ; 3、某一截面桩身轴力P Zj 计算公式为: 式中: E cj 、E sj —砼弹性模量、钢筋弹性模量[E s 取2.0×108(kPa)] A cj 、A sj —同一截面处砼面积、钢筋总面积。 εcj 、εsj —同一截面处砼与钢筋的应变 4、钢筋应力计受力的计算公式: 式中: P Sij —第i 量测截面处在j 级荷载下应力计所受轴向力(kN ) F ij —第i 量测截面处在j 级荷载下应力计的实测频率值(Hz) F i0—i 截面处钢筋应力计的初始频率值(Hz ) K —应力计标定系数 A si ’—第i 量测截面应力计面积(cm 2) 5、第i 量测截面处在第j 级荷载下的桩身轴力: ) 2()(' 2 02 ----------------??=-?=Si Sij S i ij Sij A E F F k P ε) 1()(-----??+?=??+??=j S j S Sj j C j C j S Sj j S j C j C j C j Z A E A E A E A E P εεε) 3()(' -------------------------?= Si S Sij Sij A E P εSij Si S Sij Ci Cij ij A E A E P εε?+??=
圆筒件注塑成型工艺及模具设计(一模两件)
圆筒件注塑成型工艺及模具设计(一模两件)
课程设计说明书 目:圆筒件注塑成型工艺及模具设计
目录 第1 章工艺分析 1.1塑件成型工艺性分析 1.1.1 塑件结构的工艺性分析 1.1.2 成型材料性能分析 1.2模具结构形式的确定 第2 章注射机的选择 2.1 注射量的计算 2.2塑件和流道凝料及所需锁模力的计算 2.3选择注射机 第3 章注射模具结构设计 3.1 模架的确定 3.2 各板尺寸的确定 3.3 浇注系统设计 3.3.1 主流道设计 3.3.1.1主流道尺寸 3.3.1.2 定位圈的选取 3.3.1.3主流道衬套形式 3.3.2 分流道设计 3.3.2.1分流道布置形式 3.3.2.2分流道长度 3.3.2.3分流道及浇口的尺寸设计
3.4.1分型面位置的确定 3.4.2成型零件工作尺寸计算 3.4.2.1型腔径向尺寸 3.4.2.2型腔深度尺寸 3.4.2.3型芯径向尺寸 3.4.2.4型芯高度尺寸 3.4.2.5型腔壁厚计算 3.5 导向与定位机构设计 3.5.1 机构的功用 3.5.2 导向机构的设计 3.5.2.1导柱 3.5.2.2导套 3.6 推出机构设计 3.6.1 脱模推出机构的设计原则 3.6.2 塑件的推出方式 3.6.3 塑件的推出机构 3.7 排气系统设计 3.8 冷料穴设计 3.9 冷却系统设计 第4 章注射机的校核 4.1 安装参数的校核 4.1.1 模具外形尺寸校核 4.1.2 喷嘴尺寸及定位圈尺寸校核
第1 章工艺分析 1.1 塑件成型工艺性分析 1.1.1 塑件的结构工艺性分析 1. 如图1.1 所示,该塑件为一小尺寸圆筒件,形状简单;壁厚t=1.5mm,壁厚内径比(t/d)为1/60 小于1/10,该塑件为薄壁塑件,并且各处壁厚均匀。塑件为旋转体结构,结构相对简单,而且塑件质量相对较小。该塑件表面粗糙度全部为Ra0.8mm,材料为聚氯乙烯,该种塑料流动性中等。通过查阅资料该种塑料制件未注公差时应选用MT5 级精度。 2.该模具是圆筒形零件的注射模具。该塑件无侧凹、侧孔等,不需设计侧抽芯装置,相应模具结构简单。从零件图看,制件比较简单,没有苛刻的精度要求和尺寸公差要求,因此对模具的要求也较低。从生产批量考虑,本模具采用一模两腔的结构,模架和模板尺寸均根据标准选取。其中模架从标准中选取A2 型模架。由于塑件比较简单,所以模具采用一次分型,不设有二次分型与侧向分型机构。推出系统采用推杆推出,并设有
厚度为0.7mmAG玻璃测试报告
厚度为0.7mmAG 玻璃测试报告 一.目的 确认旭硝子原厂AG 玻璃测试效果,判定能否导入试产和量产 二.评估策划 研发选白lens 型号为BL-CTP068003-01-V2进行测试。生产流程按正常的生产流程作业,研发主导,工艺跟进,品质负责测量记录数据。依据生产情况和测量数据对旭硝子原厂AG 玻璃测测试结果做出判定。 三.评估事项 四.生 产 流程 5.测试数据 5.1 外观对比 依据客户提供标准,品质判定OK 。 5.2厚度测试 5.3 雾度 No 项目 评价方法 测量工具 测试地点 备注 1 外观 规格书 目检 生产车间 2 厚度 规格书 卡尺 生产车间 3 雾度 规格书 产品对比 目视 生产车间 4 落球(AG 面) 设计标准 跌落试验机 生产车间 5 四点弯曲 品质标准 弯曲测试仪 生产车间 6 表面硬度 设计标准 硬度测试仪 生产车间 7 翘曲度 设计标准 厚度规 生产车间 8 应力深度或强度 设计标准 应力测试仪 外发 流程 输入 输出 开料前检查 原材 厚度数据 外观 开料 长*宽 CNC 精修 CNC 清洗 钢化 420℃*5.5H 落球 四点弯曲 应力深度 表面硬度 钢化后清洗 外观 测试项目 标准 测试值(单位:mm) 判定 厚度 0.7±0.05mm 0.708 0.712 0.71 0.13 0.712 OK
通过以前量产雾度为70白lens 对比,目视效果无差别 5.4 落球测试(AG 面) 5.5四点弯曲测试 5.6 表面硬度测试 5.7 翘曲度测试 试验项目 标准 结果 判定 落球 64g*60cm NG OK NG NG NG NG 64g*50cm OK OK OK OK OK OK 试验项目 标准 结果(单位:Mpa) 判定 四点弯曲 ≥200Mpa 409 468 498 465 468 OK 试验项目 标准 结果 判定 表面硬度 6H 非AG 面 AG 面 OK OK 有轻微的划伤
矿泉水饮料瓶盖注射模具及成型零件加工工艺设计
矿泉水饮料瓶盖注射模具及成型零件加工工艺设计 [摘要] 本设计是对给定的材料为PP小尺寸,一般精度的矿泉水饮料瓶盖塑件进行模具设计。在综合研究了经济性、零件的成型工艺以及复杂性等诸多因素的基础上进行成型与工艺的分析与计算。文中还对注塑模具成型零件和其他相关零件的选择原则及选择方法进行了说明。期间借鉴了与塑料模具有关的文献再加上翻阅各种指导书籍,并通过大量的计算以确定模具的结构和尺寸,还在指导老师的悉心关怀和耐心指导下进行多次的反复修改,最终画出了装配图和零件图。 最终确定矿泉水饮料瓶盖塑件的设计方案,主要包其注塑模的设计的过程、以及注塑模主要零部件的设计过程等。 [关键词]注塑模具设计;模具结构;塑料瓶盖
Abstract This design is for a given material for PP small size, the general accuracy of the charger shell plastic parts for mold design. Within consideration of the economy, parts of the molding technology and complexity, and many other factors in the molding process on the basis of the analysis and calculation. It also of injection mold shaping parts, and other related parts to illustrate the selection principle and selection method. During to refer to a lot of useful information related to injection mold and leaf through all kinds of manual, And through calculation to determine the mold structure and size, Through continuous calculation and modification, And in guiding the teacher's careful care under the guidance and patience to constantly modify again and again, Finally the sure to draw the assembly drawing and part drawing. Make sure the design of the charger shell, namely the mold with one module and two cavities, side core-pulling design scheme. Then focuses on the solution, this paper mainly includes the side core-pulling of plastic parts and injection mold design process, key points of injection mold design of main components. Key words: Injection mold design; The mold structure; Plastic bottle cap
塑料拉伸性能试验中拉伸强度或拉伸断裂应力或拉伸屈服应力测量结果不确定度评定报告
塑料拉伸性能试验中拉伸强度或拉伸断裂应力或拉伸屈服应力测 量结果不确定度评定报告 1 、概述 1.1测量依据:GB/T 1040-1992《塑料拉伸性能试验方法》 1.2环境条件:温度:25℃,温度波动不大于5℃/h ,相对湿度54% 1.3测量设备:帆泰检测CMT6104微机控制电子万能拉力试验机: 测量结果的不确定度或准确度为 1 级; 使用手册中给出:大变形示值相对误差为:+0.5%; 0mm ~150mm 游标卡尺: 测量结果的扩展不确定度:U=0.01mm k=2 因温度、湿度及电源的波动对测量的影响很小,可忽略不计。 1.4被测对象:编号为WT060814-020的PC/ABS 材料制成的标准ⅠA 型试样 1.2测量方法:在塑料拉伸性能试验中,选定试验速度进行试验,记录最大负荷或断裂 负荷或屈服时的负荷及标距间伸长。并从所制成的一批标准试样中选择10根样条进行测量拉断试件所需的最大负荷或断裂负荷或屈服负荷,即拉伸强度或拉伸断裂应力或拉伸屈服应力等于试验过程中的最大负荷与横截面之比。 2 、数学模型 t p A σ= ① ①式中:σt ——拉伸强度或拉伸断裂应力或拉伸屈服应力,MPa ; p——最大负荷或断裂负荷或屈服负荷,N ; b——试样宽度,mm ; d——试样厚度,mm ; A——试样的横截面积,A=a×b, mm 2 00 () 100%s G G G ε?= × ② ②式中:S ε——断裂伸长率 ,%; 0G ——试样原始标距,mm;(注:对于ⅠA 型试样,0G =50mm ) G——试样断裂时标线间距离,mm; 3、方差和灵敏度系数 方差: ()() ()()()2 2 22212p A c t u C u C u σ=+ 或 5() ()c s c s u c u εε=× 最大负荷的灵敏系数:()412A 1.1964/t p c c N mm A A σ??== ==??
塑料成型工艺与模具设计考试题目有答案
塑料成型工艺及模具设计学校徐州工程学院姓名刘鹏班级 10机制专2 一、填空题(每空1分,共30分) 1、高聚物中大分子链的空间结构有、及三种 形式。 2、塑料成型时有三种应力形式、、和。 3、分型面的形状 有、、、。 4、合模机构应起到以下三个方面的作 用、、。 5、推出机构中设置导向装置的目的是,该导柱安装固定 在上。 6、注塑成型时,一般而言,塑料为非结晶型、熔体粘度低或为中等的,模温取 值; 为高粘度熔体的,模温取。 7、压缩模中,溢式压缩模与其他类型压缩模在结构上的区别是, 它的凸模与凹模的相对位置靠定位,这种模具不适于成型的塑料,不宜成型的制品。 8、注塑模典型浇注系统结构 由、、、等组成。 9、在实际生产中斜导柱的常用斜角a为,最大不超 过。 10、导柱结构长度按照功能不同分为三段、、。 二、单项选择题(每小题1分,共10分) 1、用螺杆式注塑机加工塑料制品过程中可以有效降低熔融粘度的方法为()。 A、增加螺杆转速 B、降低喷嘴温度 C、增加注塑压力 D、降低模具温度 2、下列塑件缺陷中不属于制品表面质量缺陷的是()。 A、应力发白 B、冷疤 C、云纹 D、缩孔 3、从尽量减少散热面积考虑,热塑性塑料注射模分流道宜采用的断面形状是()。 A、圆形 B、矩形 C、梯形 D、‘U’形 4、塑料的加工温度区间应该为()之间。 A、脆化温度与玻璃化温度 B、玻璃化温度与粘流态温度 C、粘流态温度与分解温度 D、玻璃化温度与橡胶态温度 5、在注射成型过程中,耗时最短的时间段是()。
A、注射时间 B、保压时间 C、冷却时间 D、模塑周期 6、对大型塑件尺寸精度影响最大的因素是()。 A、成型零件制造误差 B、成型零件装配误差 C、成型收缩率误差 D、成型零件磨损量 7、模具型腔的()不足很可能导致模具开模困难。 A、刚度 B、强度 C、耐磨性 D、耐腐蚀性 8、采用下列哪一种浇口类型时模具必须采用三板式结构()。 A、直接浇口 B、侧浇口 C、轮辐浇口 D、点浇口 9、合模机构不具备的作用是()。 A、导向 B、复位 C、承受一定侧压力 D、定位 10、在推杆推出模具结构中,为了保护成型零件所采用的零件是()。 A、导柱 B、销钉 C、复位杆 D、拉料杆 三、多项选择题(共10小题,每小题2分,共20分,每小题至少有两个正确答案,多选、漏选、错选不得分) 1、高分子的制备方法主要有()。 A、加聚反应 B、分解反应 C、化合反应 D、缩聚反应 E、聚变反应 2、对()几个条件进行调节就可以改变高聚物的粘度。 A、温度 B、湿度 C、真空度 D、冷却速率 E、剪切速率 3、随着温度的变化,塑料出现的几种物理状态分别为()。 A、玻璃态 B、凝聚态 C、高弹态 D、皮革态 E、粘流态 4、设计塑料产品时,脱模斜度的选择原则为()。 A、塑料收缩率大的脱模斜度取的大些 B、塑件壁厚大的脱模斜度取的大些 C、塑料收缩率大的脱模斜度取的小些 D、塑件壁厚大的脱模斜度取的小些 E、塑件内表面的脱模斜度一般应小于塑件外表面的脱模斜度 5、塑料模分型面选择的一般原则是()。 A、尽量使塑件在开模之后留在动、下模边 B、尽量保证塑件外观质量要求 C、合理利用模板的厚度 D、有利于模具制造 E、有利于排气 6、凹模的结构形式一般有()几种。 A、整体式 B、整体嵌入式 C、局部镶嵌式 D、大面积镶嵌组合式 E、四壁拼合的组合式 7、修模时,型芯容易()。 A、外径修大 B、外径修小 C、高度修高 D、高度修矮 E、高度无法修整 8、方形制品的壁厚为5mm,其侧壁上有一个直径为4mm的孔,成型模具侧向抽芯距合理取 值范围是()。 A、4~5mm B、7~8mm C、14~15mm D、4~7mm E、5~8mm