(完整版)Asprova排程算法及数据模型
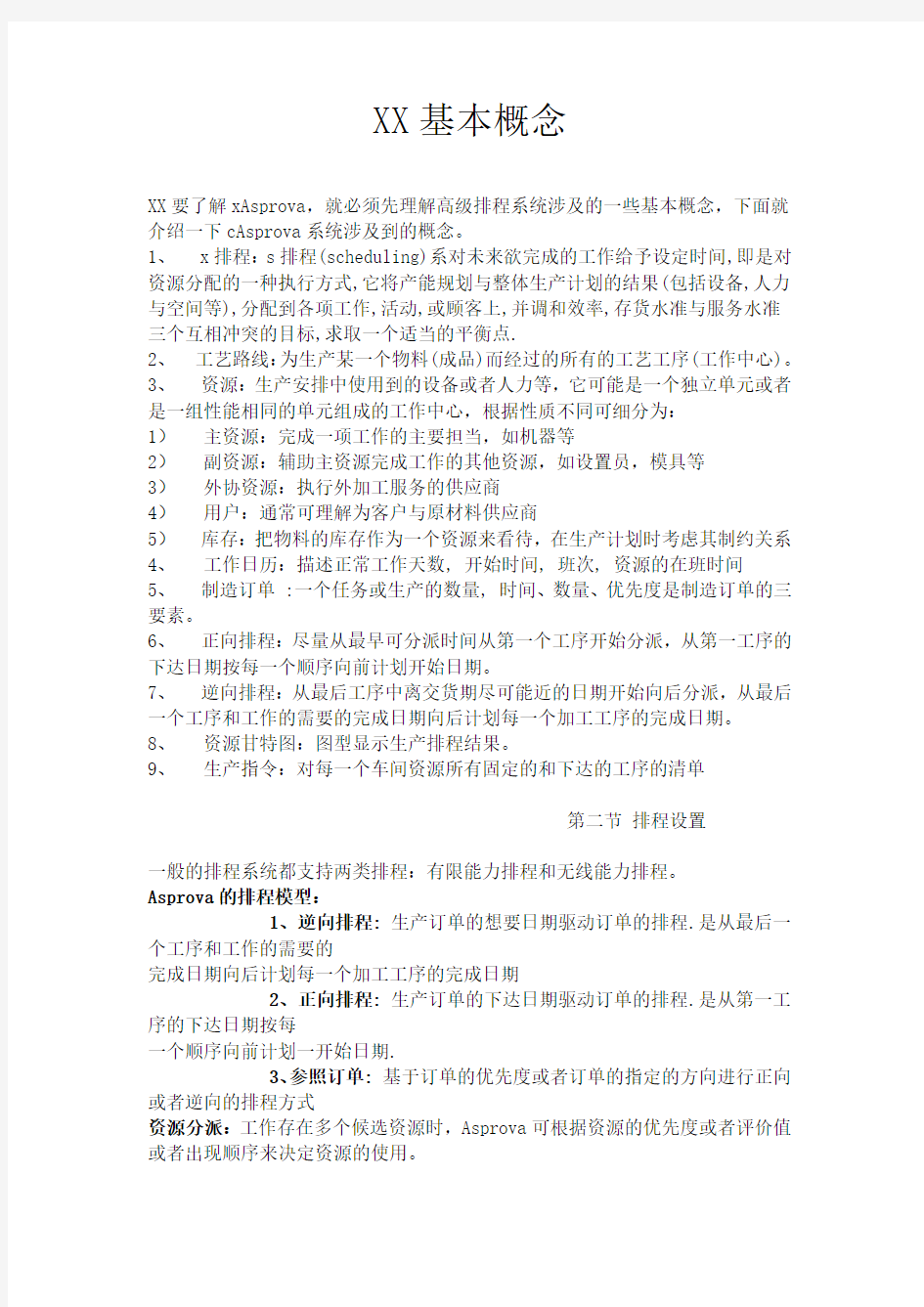
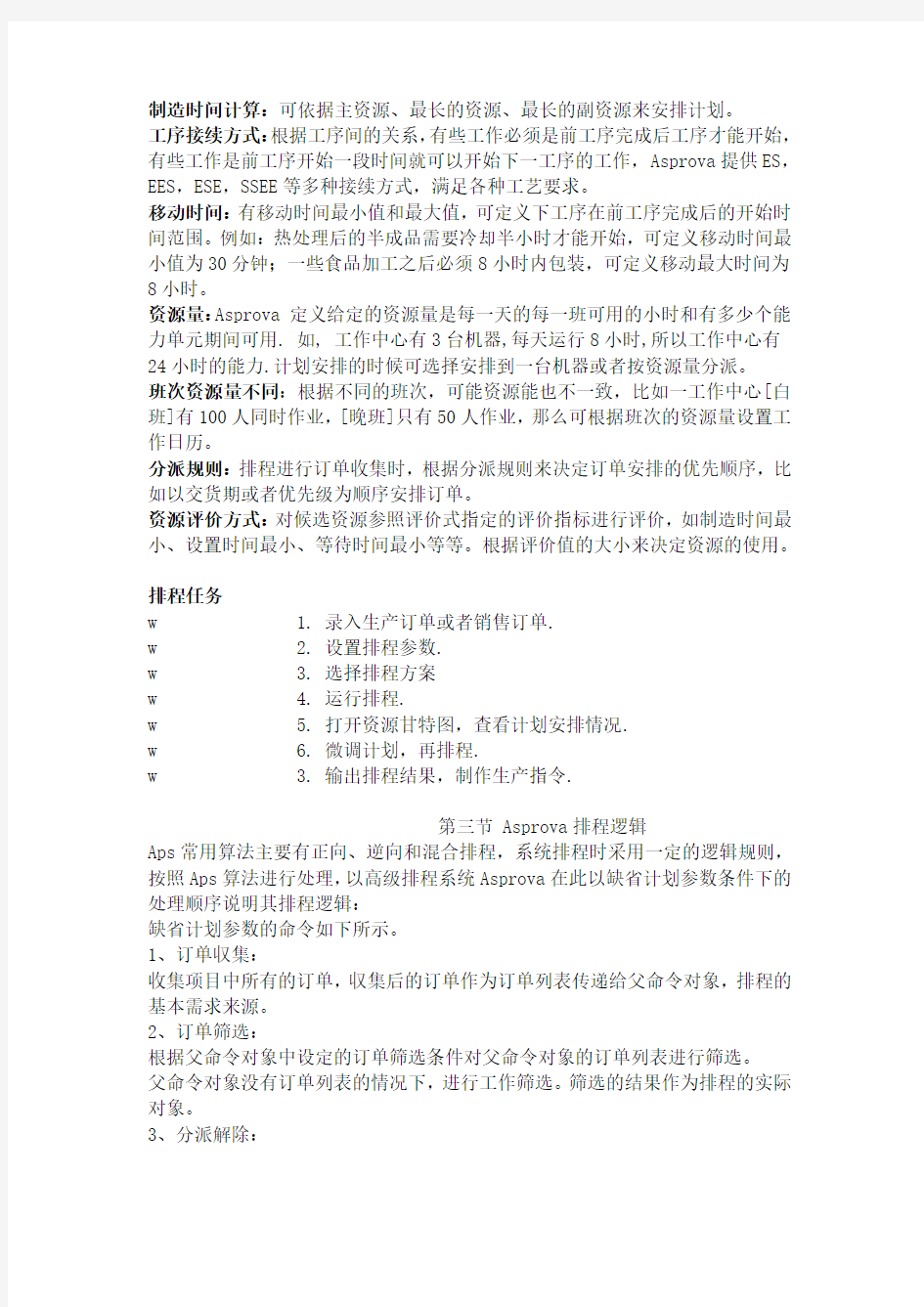
XX基本概念
XX要了解xAsprova,就必须先理解高级排程系统涉及的一些基本概念,下面就介绍一下cAsprova系统涉及到的概念。
1、 x排程:s排程(scheduling)系对未来欲完成的工作给予设定时间,即是对资源分配的一种执行方式,它将产能规划与整体生产计划的结果(包括设备,人力与空间等),分配到各项工作,活动,或顾客上,并调和效率,存货水准与服务水准三个互相冲突的目标,求取一个适当的平衡点.
2、工艺路线:为生产某一个物料(成品)而经过的所有的工艺工序(工作中心)。
3、资源:生产安排中使用到的设备或者人力等,它可能是一个独立单元或者是一组性能相同的单元组成的工作中心,根据性质不同可细分为:
1)主资源:完成一项工作的主要担当,如机器等
2)副资源:辅助主资源完成工作的其他资源,如设置员,模具等
3)外协资源:执行外加工服务的供应商
4)用户:通常可理解为客户与原材料供应商
5)库存:把物料的库存作为一个资源来看待,在生产计划时考虑其制约关系
4、工作日历:描述正常工作天数, 开始时间, 班次, 资源的在班时间
5、制造订单 :一个任务或生产的数量, 时间、数量、优先度是制造订单的三要素。
6、正向排程:尽量从最早可分派时间从第一个工序开始分派,从第一工序的下达日期按每一个顺序向前计划开始日期。
7、逆向排程:从最后工序中离交货期尽可能近的日期开始向后分派,从最后一个工序和工作的需要的完成日期向后计划每一个加工工序的完成日期。
8、资源甘特图:图型显示生产排程结果。
9、生产指令:对每一个车间资源所有固定的和下达的工序的清单
第二节排程设置
一般的排程系统都支持两类排程:有限能力排程和无线能力排程。
Asprova的排程模型:
1、逆向排程: 生产订单的想要日期驱动订单的排程.是从最后一个工序和工作的需要的
完成日期向后计划每一个加工工序的完成日期
2、正向排程:生产订单的下达日期驱动订单的排程.是从第一工序的下达日期按每
一个顺序向前计划一开始日期.
3、参照订单:基于订单的优先度或者订单的指定的方向进行正向或者逆向的排程方式
资源分派:工作存在多个候选资源时,Asprova可根据资源的优先度或者评价值或者出现顺序来决定资源的使用。
制造时间计算:可依据主资源、最长的资源、最长的副资源来安排计划。
工序接续方式:根据工序间的关系,有些工作必须是前工序完成后工序才能开始,有些工作是前工序开始一段时间就可以开始下一工序的工作,Asprova提供ES,EES,ESE,SSEE等多种接续方式,满足各种工艺要求。
移动时间:有移动时间最小值和最大值,可定义下工序在前工序完成后的开始时间范围。例如:热处理后的半成品需要冷却半小时才能开始,可定义移动时间最小值为30分钟;一些食品加工之后必须8小时内包装,可定义移动最大时间为8小时。
资源量:Asprova 定义给定的资源量是每一天的每一班可用的小时和有多少个能力单元期间可用. 如, 工作中心有3台机器,每天运行8小时,所以工作中心有24小时的能力.计划安排的时候可选择安排到一台机器或者按资源量分派。
班次资源量不同:根据不同的班次,可能资源能也不一致,比如一工作中心[白班]有100人同时作业,[晚班]只有50人作业,那么可根据班次的资源量设置工作日历。
分派规则:排程进行订单收集时,根据分派规则来决定订单安排的优先顺序,比如以交货期或者优先级为顺序安排订单。
资源评价方式:对候选资源参照评价式指定的评价指标进行评价,如制造时间最小、设置时间最小、等待时间最小等等。根据评价值的大小来决定资源的使用。
排程任务
w 1. 录入生产订单或者销售订单.
w 2. 设置排程参数.
w 3. 选择排程方案
w 4. 运行排程.
w 5. 打开资源甘特图,查看计划安排情况.
w 6. 微调计划,再排程.
w 3. 输出排程结果,制作生产指令.
第三节 Asprova排程逻辑
Aps常用算法主要有正向、逆向和混合排程,系统排程时采用一定的逻辑规则,按照Aps算法进行处理,以高级排程系统Asprova在此以缺省计划参数条件下的处理顺序说明其排程逻辑:
缺省计划参数的命令如下所示。
1、订单収集:
收集项目中所有的订单,収集后的订单作为订单列表传递给父命令对象,排程的基本需求来源。
2、订单筛选:
根据父命令对象中设定的订单筛选条件对父命令对象的订单列表进行筛选。
父命令对象没有订单列表的情况下,进行工作筛选。筛选的结果作为排程的实际对象。
3、分派解除:
对父命令对象的工作列表中所有工作解除分派。父命令对象中没有工作列表的时候,对父命令对象的订单列表中所有关联工作解除分派。父命令对象中没有订单列表的时候,不进行任何处理。
4、订单展开:
根据模板数据(BOM)进行订单展开。需要事先在订单収集,订单筛选命令中收集展开了的订单。订单展开中,从订单展开对象的订单中进行工作的生成。已经有工作存在的时候,保留其工作,只对生产数量等信息进行更新。但是,考虑到相应订单不存在的情况,或模板数据的构成改变的情况,对不需要的工作进行删除。工作生成的同时,输入指令与输出指令也生成。输入指令为其工作中的使用指令中品目和数量(即其工作中进行投入的品目),输出指令为从其工作中的使用指令输出的品目和数量(即其工作中生产出的品目)。
工作,输入指令,输出指令基本上按照模板数据输入指令与模板数据输出指令的属性及订单的生产数量进行生成。
5、实绩工作分派:
父命令对象的工作列表中的工作,只对状态确定,指示完毕的工作及输入了实绩的工作进行分派。
6、固定工作分派:
父命令对象的工作列表中的工作,只对时间固定的工作进行分派。
7、订单分派/关联:
按定义好的分派规则和资源选择规则分派所有工作,包括分派采购订单、分派销售订单、分派制造订单,最后关联相关订单。
8、调整:
分派结果,超过分派开始时间,分派结束时间等的时间进行分派的工作,或者该工作中包含的订单根据在计划参数的命令中设定的属性进行分派调整。
9、计划评价:
参照指定的指标,对本次排程结果进行评价。评价指标包括逾期制造订单数、逾期采购订单数、逾期销售订单数、平均等待时间、设置时间率等。10、报告:
将分派的结果信息在消息窗口输出。
排程逻辑是排程时的执行命令顺序,在执行某道命令的时候,系统都需要参照计划参数来处理,比如订单的优先规则,是以交货期作优先条件按照顺序执行,还是其他属性,都必须事先定义;资源的选择规则也是非常重要的,在考虑候选资源时需要考虑哪些因素,如均衡生产、制造时间最小等,也必须明确给出。这一部分是整个生产排程里最重要的,必须定义出明确的、可执行的计划参数,生产计划排程才能正常运行。一般来说,咨询公司与客户一起制作排程模型,共同完成排程系统的导入。
APS中生产计划排程模块的基本原理
供应链管理(SCM)涉及企业间的集成以及在产销网络中协调物流和信息流的各个方面。作为企业信息中枢的ERP系统,现在已经在许多企业中用于作业处
理和定单执行。高级计划系统(APS,AdvancedPlanningSystems)作为ERP 的补充,用于协调物流、开发瓶颈资源和保证交货日期。APS应用各种优化技术,并根据企业的商业目标来改进计划。APS包括需求和供应计划、运输和生产计划排程等各种供应链计划模块,本文主要介绍APS中生产计划排程(ProductionPlanningandScheduling)模块的基本原理[1]。
?查看Asprova实现本文章中的番茄酱模型的例子-最大移动时间保证番茄酱的新鲜度
决策状况描述
生产计划排程的目的是为车间生成一个详细的短期生产计划。排产计划(Productionschedule)指明了计划范围内的每一个定单在所需资源上的加工开始时间和结束时间,也即指出了在给定资源上定单的加工工序。排产计划可以通过直观的甘特图(Ganttchart)形式给出。
排产计划的计划间隔可以从一天到几周,取决于具体的工业生产部门。合理的计划长度取决于几个因素:一方面,它至少应当涵盖与一个定单在生产单元中最大的流动时间(flowtime)相对应的时间间隔;另一方面,计划间隔受到已知顾客定单或可靠需求预测的可用性限制。很显然,只有当排产计划适度稳定时,在一个资源上进行定单排程才是有用的。也就是说,它们不应受不期望事件经常变化的影响(如定单数量改变或中断)。
对某些生产类型(如jobshop),生产计划排程需要对(潜在)瓶颈资源上的任务定单进行排序和计划;而对另一些生产类型(如成组技术),生产计划排程要能自动地、按时段检查资源组的能力,看其是否能够在下一个时间段内完成成组加工的一组定单。然后,可以手工排序这组定单在下一个时间段内的加工次序。
排产计划任务能够而且也应当分散来做,这样可以利用每个地点人们的专业知识和车间当前状况的知识(例如人员的可用性)。
生产计划排程受到上层主生产计划的约束,主生产计划设立了在分散的决策单位中执行生产计划排程的框架。从主计划中可获得的相应指导包括:使用超时或加班的数量;在不同时间点上来自供应链上游设施物料项的可用性;涉及来自供应商输入物料的采购协议。此外,由于主生产计划在供应链上有更宽的视点和更长的计划区间,从中我们还可以得到:
计划结束时需要建立的各物料项的季节性库存量;
交付给供应链下游设施的定单截止日期(下游设施可以是紧接着的下一级生产单位,分销商或最终顾客)。
排产计划生成
由车间模型生成排产计划的一般程序可简单地描述为下面6个步骤(如图1所示)。
1、建模
车间模型必须详细地捕捉生产流程的特征和相应的物流,以便以最小的成本生成可行的计划。
由于一个系统的产出率只受潜在瓶颈资源的限制,因此,我们只需对车间现有全部资源的一部分–也即那些可能成为瓶颈的资源,建立一个清晰的模型。关于建模方法的细节我们将在后面进一步阐述。
2、提取需要的数据
生产计划排程使用的数据来自ERP系统、主生产计划和需求计划。生产计划排程仅利用这些模块中可用数据的一个子集,因此,在建立一个给定生产单元的模型时,必须指明它实际需要哪些数据。
3、生成一组假定(生产状况)
除了从ERP系统、主生产计划和需求计划这些数据源中接收的数据之外,车间或生产单位的决策者或许对车间当前或未来的状况会有更进一步的知识或期望,这些信息在其它地方(如软件模块中)是不能得到的。再者,对车间的可用能力或许也可以有多种选择(如柔性的倒班安排等)。因此,决策人员必须有能力修改数据和建立某种生产状况(见图1中的第三步,点划线框表示这一步必须由决策人员执行,并且是可选的)。
4、生成一个(初始)排产计划
在有了模型和数据之后,就可以针对给定的生产状况,利用线性规划、启发式算法和基因算法等各种复杂的优化方法来生成排产计划。这项工作可以一步完成,也可以通过两级计划层次(先综合的生产计划,后详细的排产计划)完成。
5、排产计划分析和交互修改
如果通过两级计划层次完成,也即先生成综合资源的上层生产计划。那么,在生成一个详细的排产计划之前,人们或许首先要对这个生产计划进行分析。特别地,如果生产计划不可行,决策人员可以交互地指定一些计划途径来平衡生产能力(如增加班时或指定不同的加工路径)。这或许要比修改在单个资源上的加工工序(下层排产计划)更加容易。
APS采用了例外管理(Management Byexception)的技术,如果出现问题和不可行性(如超过定单交货期或资源过载),APS就会发出警告(alerts)。这些警告首先被“过滤”,然后,正确的警告被传递到供应链中正确的组织单位。
此外,针对一种生产状况产生的排产方案还可以通过结合决策者的经验和知识交互地改进。当然,为了提供真正的决策支持,必要的修改次数应当受到限制。
6、生产状况核准
当决策人员确定已经评估了所有可选方案时,他/她将选择那个体现最佳生产状况的排产计划去执行。
7、执行和更新排产计划
决策人员选定的排产计划将被传递给:MRP模块(分解计划)、ERP系统(执
行计划)和运输计划模块(在顾客定单完成时安排装运车辆)。
MRP模块把在瓶颈资源上计划的所有活动分解成在非瓶颈资源上生产的那些物料或由供应商交付的物料;此外,对某些加工定单所必需的物料也将被预定。
排产计划将持续执行到某个事件信号发生时才进行更新,也即直到修改一个排产计划看来是可取的时候(见图1中的LoopII)。这个事件可以是一个新定单的到来、机器故障或冻结的计划部分已执行完毕(后面我们还将对排产计划的更新作详细讨论)。
改变车间生产模型的情况不太经常(如图1中的LoopI)。如果结构保持不变和只是数量上受到影响(例如一个机床组中的机床数或某些已知产品的新变种),那么,通过下载ERP系统中的数据,APS能自动更新模型。但当变化很大时(例如具有某些新特征的新生产阶段的引入),那么,由专家对模型进行手动调整则是可取的。
下面我们将对车间生产流程模型的建模方法作更详细的阐述。
图1、排产计划的一般步骤
生产流程建模
车间模型必须结合所有必要的生产流程细节来决定顾客定单的完成时间,模型需要的输入来自有关的物料和潜在的瓶颈资源。排产计划中每一步的时间间隔通常很小(如几个小时),有时甚至可以是连续的。
1、模型
我们可以把建模的范围限制在(潜在)瓶颈上执行的运作,因为只有这些资源限制了车间的产出。由于生产计划排程并不打算控制车间(这个任务留给了ERP系统),一些车间的细节(如监视定单当前状况的控制点)可以被忽略。
在模型的两个连续活动之间,在非瓶颈资源上执行的所有流程步骤都只被表达为固定的提前期差度(fixedleadtimeoffset)。这种处理方法与众所周知的“高级计划给出提前期只是作为计划的结果而不是一个事先给定的常数”这一叙述并没有矛盾。在这里,提前期差度仅包括前述非瓶颈资源上的加工和运输时间,因为等待时间不会存在。
模型可以通过关联的数据来定义,这些数据可分为结构数据(structuraldata)和状况相关数据(situationdependentdata)。
结构数据包括:生产地点,工件,物料单,工艺路径和相关的操作指令,(生产)资源,供应商清单,准备时间矩阵,和时间表(工厂日历)。
对车间分布在不同地方的一个大型供应链,把所有数据归集到一个专门地点或许会有好处。这样的话,一个零件就可以通过它的生产地点来识别,尽管它在顾客眼中是一样的。
物料清单通常是基于单层描述(存放在一个物料文件中),也即每一个零件号只连接到它下一层物料的那些零件号。一个给定零件的完整物料清单很容易在计算机上通过连接这些单层表达来构造。
每个工件的资源消耗可以从工艺路径和操作说明中得到。每个定单的工件数以及每个工件的资源消耗是计算单个定单顺序和排程所必须的。因此,可以用生产流程模型(PPM,ProductionProcessModel)来清晰地表达物料加工路径和生产操作。
图2给出了一个PPM的例子,它描述了一个特定尺寸和商标的瓶装蕃茄酱的两级生产流程。第一个PPM表达液体蕃茄酱的生产,包括清洗搅拌池,搅拌配料,和等待装瓶。一旦蕃茄酱准备好了,它将在24小时内被装瓶。蕃茄酱可同时用于不同尺寸的瓶子,每一种尺寸都将对应一个PPM。
图2、两级蕃茄酱生产流程模型(PPM)
?查看Asprova实现本文章中的番茄酱模型的例子-最大移动时间保证番茄酱的新鲜度
一个PPM至少由一个运作(operation)组成,而每个运作包含一个或几个活动(activities)。一个运作总是与一个基本资源相关(如搅拌池)。二级资源–比如人员–也可归属于一个活动。活动或许要求一些输入物料并能产生一些物料作为输出。当然,我们必须指明什么时候需要输入物料和什么时候输出物料可用。在一个运作中,活动的技术顺序(也称为优先关系)可以用箭头线表示,就如同在项目计划活动中一样,可以用结束开始,结束结束,开始结束,开始开始关系和最大最小时间距离来连接。这就允许非常准确地建立包括平行执行活动(重叠的活动)在内的两个生产活动之间的时间约束模型。
一个顾客定单的计时、资源和物料需求可以通过有向标界线(peggingarcs)连接相关的PPMs导出(见图3中的粗体线和虚线)。有向标界线把一个PPM 的输出物料(节点)与后一级PPM的输入物料(节点)连在一起。结果,从最后一级生产流程开始展开一个定单(如图3中的定单C505X)和相应的PPMs,就可以在各时间窗中生成关于资源和物料消耗的信息。这些时间窗可直接用于成生可行排产计划[2]。
工厂日历指明了休息日和其它资源工时的中断,另外还包括车间(或资源)是否以一班,两班或三班运作的信息。高级计划系统(APS)通常提供几个典型日历可供选择。
图3、标界线:连接两个生产流程模型(PPMs)
状况相关数据随车间当前的状况而变,它包括:初始库存(含在制品库存)、资源的准备状态、和给定时间间隔内要加工的一组定单。由用户指定的运作规则数据包括:批量规则,优先规则和加工路径选择。
尽管建立批量规则最好是根据实际生产情况–例如资源的利用和相关成本的
情况,但APS通常要求事先输入一些简单规则。这些规则可以是固定批量、最小批量或给定定单间隔时间的批量。APS软件包或是提供一组规则可供选取,或是以高级编程语言的形式来编写它。在某个资源上决定定单优先次序的规则以类似的方式处理[3]。
如果执行一个生产定单存在可选路径,那么人们会期望APS在生成排产计划的过程中选择最佳路径。但经验表明,用户得自己选择一个适当的路径。有时可选路径是作为一个优先列表输入,只有当一个宁愿的路径导致不可行计划,求解器才会去试第二个最佳路径,然后试第三个最佳,等等。
2、目标
最后还要指定一个优化目标。这些目标指导寻找一个好的、期望能接近最优的计划方案。在生产计划排程模块中选择优化目标时,我们看到主要有下面一些面向时间的目标:
Makespan,完成所有定单任务所需要的时间。使makespan最小是多机床任务排序问题中常见的优化目标;
Lateness,定单任务完成时间和它的到期时间之差。使所有定单的lateness 总和最小,或使单个定单中最大的lateness最小,是常见的排程目标。
Flowtime,一个定单任务在生产系统中花费的时间。使所有定单的flowtime 总和最小也是一个优化目标。
Setuptime,每个定单任务的生产准备时间。使所有定单的setuptime总和最小也可以作为一个优化目标。
另外,还有三个与成本相关的目标,分别是:使可变生产成本总和最小;使
生产准备成本总和最小;和使惩罚成本总和最小。
尽管在排产这个计划层对成本的自由度影响很有限,但我们可以看到,对于不同加工路径的选择(例如,是安排标准定单或是紧急定单),也还是要以货币的术语来评估。
如果需要对“软约束”建模(例如,为备货生产定单履行计划的交货时间),我们可以把惩罚成本包含在目标函数中。惩罚成本也称为缺货成本,它是当需求出现时没有足够的现货来满足需求所招致的成本。
如果决策人员想要同时追求上面几个优化目标,使每个目标都达到最优,这样“理想”的解答通常是不存在的。那么,只好寻求一个妥协方案。一种方法是建立上面单个目标的加权和,这个组合目标函数可以象单目标函数一样对待,因此,可以应用同样的求解方法[4]。
3、解的表达
表达一个模型的解也即详细的排产计划,有几种选择。它可以简单地表达为一个任务清单,上面列出了每个任务在分配给它的资源上的起始和完成时间。要把排产计划传送到其它模块中,这是最恰当的表达方式。
决策人员通常更喜欢排产计划以甘特图表达(如图4所示),用甘特图可以在一定的时间间隔上平行地显示所有资源。人们既可以专注于一个指定顾客定单和它在相应生产阶段的排程,也可以把注意力集中在单个资源及其在时间上的排程。
如果决策人员允许交互地改变排产计划,例如把一个运作交互地移到另一个资源,那么以平行方式显示所有资源的甘特图是最好的表达。
下面我们再来看看更新一个现有排产计划的一些选择。
排产计划更新
生产计划排程假定所有数据是确定已知的,也即决策状况是确定的。尽管这是一个理想的假设,但对一些时间段还是可以进行调整。为了处理不确定性(例如非计划的生产率变化或未预料的资源停工),软件工具允许监控人们假定发生在车间的变化,并生成一个更新了的期望的定单完成时间。这些变化是否大到需要重新优化排程将基于决策者的判断。在一个计划实际交付车间实施之前,可以通过提供大量的可选状况的生成和测试能力来帮助决策者的判断。这种方法也称为仿真,目前的APS软件工具都提供仿真手段(见图1的第3到第5步)。
在这里要提到的另一个特征是两步计划方法,也称为增量式计划。假定有一个新的定单到来。如果它落在生产计划排程的计划范围内,这个新顾客定单的活动可以插入到它所需资源上已排序好的定单中。在现行排产计划中寻找时间空隙,以便新定单的排程只须做微小的调整。如果能维持排产计划的可行性,那么就能导出新定单的一个计划交货期,并送回给顾客。
由于上面这一基本排程可以通过不同的定单顺序来改进,所以重新优化经常会被考虑,以便通过新的排序来减少成本。
下面我们就来举例说明。假定有4个定单需要在某个机床上排程,表1给出了定单交货时间,优化的目标是使顺序相关的生产准备时间总和最小。如果实际开始时间在100(时间单位),所有定单的加工时间相同(1个时间单位),顺序相关的准备时间是0,1/3,2/3或1个时间单位(表2给出了准备时间矩阵)。那么,最优的排程显然是ABCD(如图4所示)。
在开始加工定单A之后,我们被要求检查是否能够接收一个交货时间为107的新定单E。假定不允许因为一个新(紧急)定单而中断一个已经开始执行的定单,那么我们可以检查在完成定单A,B,C或D之后,把工作E直接插入现行排程(如图5所示)。由于在定单A和E这个子顺序之间存在一个正的准备时间,插在A之后会违反定单B的交货期,因此是不可行的。依理可以找到三个可行排程,其中可选方案c)具有最小的准备时间总和。因此,交货期为107
的新定单E可以被接受(假定定单E值一个时间单位的附加生产准备时间)。
当重新执行排程优化时,我们可以得到一个新的包括定单E的可行排产方案,它减少了1/3的生产准备时间(如图6所示)
。
生成一个新的定单排程是费时的,并且通常会导致一些紧张(nervousness)。这些紧张是因为与先前的实际计划相比改变了定单开始的时间和生产的数量。紧张可能导致车间的额外工作,例如某些输入物料或许要更早交付,而这又要与供应商一起检查。为了减少紧张,通常可以把在一个资源上接下来的几个定单固定,也即它们的加工顺序是固定的而不作为重新优化的一部分。开始时间落在一个给定时间段(称为冻结范围)的所有定单都将被固定[5]。
结束语
假定已经生成了主生产计划,我们就可以为不同的车间和生产单元导出详细的排产计划。生产计划排程是在一个计划层中完成还是分两个计划层次来做,很大程度上取决于车间的生产类型。在一个资源上的定单排序通常有许多可选方案,要找到一个最优的排产计划,对一个资源上的n个定单理论上要评估n!种不同的排序。尽管强有力的求解算法已经开发出来减少寻找好的方案所要评估的解的数量,优化的计算量仍会随着排程定单的数量而急剧增加。幸运的是生成一个排产计划通常不必从零开始,因为先前计划的一部分已经是固定的(例如落在冻结区中的定单)。同样,把生产计划排程分为两个计划层次来做也减少了在低计划层上生成可行定单顺序的数量。此外,增量式计划或由决策者指定的部分排程的重新优化也限制了计算量。
(来源:E-works)
数据分析算法与模型一附答案
精品文档 数据分析算法与模型模拟题(一) 一、计算题(共4题,100分) 1、影响中国人口自然增长率的因素有很多,据分析主要因素可能有:(1)从宏观经济上看,经济整体增长是人口自然增长的基本源泉;(2)居民消费水平,它的高低可能会间接影响人口增长率。(3)文化程度,由于教育年限的高低,相应会转变人的传统观念,可能会间接影响人口自然增长率(4)人口分布,非农业与农业人口的比率也会对人口增长率有相应的影响。为了全面反映中国“人口自然增长率”的全貌,选择人口增长率作为被解释变量,以反映中国人口的增长;选择“国名收入”及“人均GDP”作为经济整体增长的代表;选择“居民消费价格指数增长率”作为居民消费水平的代表。暂不考虑文化程度及人口分布的影响。 从《中国统计年鉴》收集到以下数据(见表1): 表1 中国人口增长率及相关数据 人口自然增长率国民总收入居民消费价格指数增长人均GDP 年份(元)率((亿元) CPI(%。))% 1366 15037 1988 15.73 18.8 1519 1989 18 17001 15.04 1644 18718 1990 14.39 3.1 1893 21826 3.4 1991 12.98 2311 26937 11.6 6.4 1992 2998 35260 14.7 11.45 1993 4044 48108 1994 24.1 11.21 5046 17.1 10.55 59811 1995 5846 70142 1996 10.42 8.3 6420 10.06 1997 2.8 78061 -0.8 1998 9.14 83024 6796 8.18 7159 1999 88479 -1.4 7858 2000 0.4 7.58 98000 精品文档. 精品文档
排程
报告大纲 排程概論排程概论 排程問題的型式排程问题的型式 範例(單機排程問題)范例(单机排程问题) 排程問題的求解方法排程问题的求解方法 結論结论 何謂排程何谓排程 排程(scheduling )是一個決策過程。排程(scheduling )是一个决策过程。 在最佳化(optimization )特定目標函數(objective function )下,決定各個工作(task )在各資源上的執行順序。在最佳化(optimization )特定目标函数(objective function )下,决定各个工作(task )在各资源上的执行顺序。 何謂排程何谓排程 排程結果不但顯示每一個工作在某一資源上的執行順序。排程结果不但显示每一个工作在某一资源上的执行顺序。 也顯示每一個工作在資源上的開始及完成時間。也显示每一个工作在资源上的开始及完成时间。 何謂排程何谓排程 因此,排程同時包含工作和資源的時程安排。因此,排程同时包含工作和资源的时程安排。所以,如何將有限的資源做最有效率的使用,便成為管理者在排程時所必須考慮的重要問題。所以,如何将有限的资源做最有效率的使用,便成为管理者在排程时所必须考虑的重要问题。 何謂排程何谓排程 一個良好的排程(schedule )不但可以減少資源的閒置時間(idle time ),增加資源的利用率(utilization )。一个良好的排程(schedule )不但可以减少资源的闲置时间(idle
time ),增加资源的利用率(utilization )。 更可以使工作盡量如期完成,滿足顧客的需求。更可以使工作尽量如期完成,满足顾客的需求。 所以,排程結果將影響組織之競爭力及獲利能力。所以,排程结果将影响组织之竞争力及获利能力。 何謂排程何谓排程 資源在組織中的呈現方式:资源在组织中的呈现方式: 工場中的機器工场中的机器 機場的跑道、登機門机场的跑道、登机门 醫院中的手術室、檢驗設施、醫護人員医院中的手术室、检验设施、医护人员 學校的教室、實驗室、老師学校的教室、实验室、老师 電腦的CPU 电脑的CPU 何謂排程何谓排程 工作在組織中的呈現方式:工作在组织中的呈现方式: 工場中等待加工處理的工件工场中等待加工处理的工件 等待起飛、降落的飛機等待起飞、降落的飞机 等待開刀、身體檢查的病人等待开刀、身体检查的病人 學校的各項課程学校的各项课程 等待執行的指令、程式等待执行的指令、程式 排程問題的型式排程问题的型式 排程問題隨著假設、工場的特性、目標函數的不同,而有各種不同的型態,一般而言,可分為下列基本類型。排程问题随着假设、工场的特性、目标函数的不同,而有各种不同的型态,一般而言,可分为下列基本类型。 排程問題的基本類型排程问题的基本类型
APS排程系统的生产模型
APS排程系统的生产模型 建立生产模型,让软件接受企业的详细生产过程,这的确很麻烦,但并非是无法完成的,真正的难点在于下一步:根据模型和生产请求得到详细的作业计划,也就是详细生产排程。ERP的真正技术瓶颈就发生在这里。 详细生产排程的结果是‘生产作业计划’,是针对每个人员每个设备的生产资源的工作计划。作业计划必须满足在生产工艺上不能有半点差错。首先,工序之间必须满足特定的逻辑关系,以及要求某些工序必须连续、同时、或者间隔进行等等,这是对作业计划最基本的要求。其次,作业计划必须满足资源能力限制,一个资源在一个时间内只能干一件事情,生产作业计划中不能有资源冲突;最后,作业计划必须满足物料供应的限制,没有原材料不能开始生产。也就是说:作业计划必须同时满足多种复杂的约束条件。TOC约束理论早已有之,只是需要比较高级的算法和数学理论,在这方面需要进行长期投入才会有所收获。因此国内理论界对此的研究还很少。 有了按照TOC理论计算出来的计划,满足企业生产工艺要求是不是就行了?很遗憾,这还是差的很远。现在我们以一个假想例子来说明。 一个ERP生产调度系统,很顺利接受了某企业的全部生产细节,并计算出了一套生产作业计划,打印成一份给所有生产资源安排工作的作业计划。现在,由一个有经验的老调度师来决断这个ERP计划系统是不是可以用的,他将如何做? 首先,他会逐一检查每个工序的时间安排,看它们之间的次序和逻辑关系是不是符合企业生产工艺的逻辑关系要求;其次,他会观察这个计划中对每个资源的安排是不是合理,有没有一个时间干两个活这种冲突的情况发生;最后他要看在计划时间内物料能不能供应的上。这些都没有问题了,他必须承认:这个计划已经是一个‘可行’的计划了,也就是说,照此计划一定可以完成生产任务。 但是,还有一个关键的事情,老调度师根据自己习惯的做法,也手工制定了一个作业计划,他把这两个计划一对E比,发现问题了。手工的计划可以8个小时完成全部工作,而计算机的计划需要9个小时。或者手工计划可以在8:00完成而计算机的计划要在9:00点完成。原因在于:计算机对某几个工序的顺序安排虽然可行但是不合理,而老调度师根据长期经验早已清楚此时安排工序应该哪个先、哪个后、哪些并行比较好,结果可以得到更短时间完成的计划。这是一种优化安排,而计算机没有找到这种安排方法,所以计算机给出的是一个‘可行’的,但是‘不好’的计划!理想中计算机应自动计算出一个比手工计划更好更优化的排产方案结果,指导人如何工作。这样的软件才能体现出‘企业资源计划’的威力。否则,不能满足最优化排程的ERP在企业生产中还是无法代替手工。 这隔例子凸现出了一个世界性的关键技术瓶颈:一个生产过程可能有无穷多种‘可行’的安排方式,但是必须从其中找出一个‘最优’的计划,即使不能达到最优,起码要比人的手工计划更优,这才是一套可用的生产排程软件,否则企业还是用不起来。 找出‘可行’计划的难度已经很大,找出‘优化’计划的难度更大。不仅要处理错综复杂的约束条件,还要从几乎无穷多种满足约束的可行方案中找到优化排程方案。怎样才能找到这种优化的计划?这是ERP系统共同面对的真正瓶颈问题,是世界性的技术难题。其中的关键在于算法,算法的基础是数学模型,特别是高级图论、离散数学与线性代数中的矢量矩阵技术。对此,国外已经作出了
生产调度方法
监控方式和调度手法 管理是指对生产调度的计划、实施、检查、总结(PDCA)循环活动的管理。生产调度工作狭义上是指生产调度管理方面的技术性工作,其内容是指生产调度对生产经营动态的了解、掌握、预防、处理、以及对关键部位的控制和部门间的协调配合。概括地说,生产调度工作是生产调度管理的具体表现,它的完成是生产调度管理在实际上完成的具体表现。 一、开生产调度会议是生产调度管理的重要工作内容,也是一种 有效的工作方法。 1.召开生产碰头会 1)每天接班后,各部门的生产负责人都到调度会议室碰头,同当 班调度做简单的情况介绍和提出要求,听取基层的一些反映, 并做简单的生产平衡。 2)这种会议有话则长,无话则短;力争简洁精炼,一般不超过半 个小时,会议大多在白班进行。 2.召开生产调度会 1)生产调度会常由生产计划调度主持,参加者有车间主任、主管 以及各基层主管生产的负责人和各职能科室的负责人。 2)会议内容: a)主要是听取生产计划调度对有关生产活动的汇报,一周或一月 的生产作业进度,各生产技术经济指标的完成情况;存在的问 — 1 —
题和所要采取的措施;对某些部门或基层的要求等。 b)同时听取各基层负责人的情况反映、提出的问题和要求,并针 对这些问题的性质和对生产活动的影响,经过协商和平衡,责 成有关部门或单位限期解决。 c)生产调度会的召开次数各厂不一,有的一天一次,类似每天的 生产碰头会;有的三天一次或周一、三、五进行;有的为每周 一次。 3.召开生产平衡会 1)在落实计划安排时,就要召开会议进行平衡。 2)月生产作业计划平衡会大多在上个月末或下个月初举行,经过 平衡后的生产作业计划就可以下发执行,并成为下个月调度工 作的主要依据,成为各生产环节组织生产的依据。 3)在正常生产的情况下,在月中应对生产计划的完成情况进行一 次全面检查,找出计划指标和实际完成指标的偏差。如偏差较 大,就要对计划进行修正,与实有生产能力进行新的平衡。修 正后的计划作为原生产作业计划的补充,指导后期的生产活 动,以保证整体计划的完成。 4.召开调度专业会 1)调度专业会议由调度系统负责人主持,内容主要是政治、业务 学习,工作总结、经验介绍,检查劳动竞赛情况等。目的是要 不断地提高调度人员的政治素质、业务水平和工作质量。 2)由于调度工作的轮班制,人员难以集中,调度专业会议以每季— 2 —
常用的分组调度算法
[编辑本段]常用的分组调度算法 对于调度算法有两个重要的设计参数:一个是吞吐量,另一个是公平性。调度算法是数据业务系统的一个特色,目的是充分利用信道的时变特性,得到多用户分集增益,提高系统的吞吐量。吞吐量一般用小区单位时间内传输的数据量来衡量。公平性指小区所有用户是否都获得一定的服务机会,最公平的算法是所有用户享有相同的服务机会。奸的调度算法应该兼顾吞吐量和公平性,根据算法的特点,调度算法主要可分为:轮询(Round Robin, RR)算法;最大C/I算法(MaxC/1);正比公平(Proportional Fair,PP)算法。 (1)轮询算法 在考虑公平性时,一般都把循环调度算法作为衡量的标准。这种算法循环地调用每个用户,即从调度概率上说,每个用户都以同样的概率占用服务资源(时隙、功率等)。循环调度算法每次调度时,与最大C/I算法相同,并不考虑用户以往被服务的情况,即是无记忆性方式。循环调度算法是最公平的算法,但算法的资源利用率不高,因为当某些用户的信道条件非常恶劣时也可能会得到服务,因此系统的吞吐量比较低。 图7-35给出了以时分方式使用高速下行共享信道(High Speed Downlink Share CHannel, HS-DSCH)信道的一种可能的资源分配方式。从图中可以看出,尽管UEl和UE2的信道环境不同(与基站的距离不同),但是分配了相同的信道使用时间给UEl和UE2。 (2)最大C/I算法 最大C/I算法在选择传输用户时,只选择最大载干比C/I的用户,即让信道条件最好的用户占用资源传输数据,当该用户信道变差后,再选择其他信道最好的用户。基站始终为该传输时刻信道条件最好的用户服务。 最大C/I算法获取的吞吐量是吞吐量的极限值,但在移动通信中,用户所处的位置不同,其所接收的信号强度不一样,最大C/I算法必然照顾了离基站近、信道好的用户,而其他离基站较远的用户则无法得到服务,基站的服务覆盖范围非常小。这种调度算法是最不公平的。 图7-36给出了以时分方式使用HS-DSCH信道的一种可能的资源分配方式。该图假定了服务过程中UEl的信道条件始终好于UE2。从图中可以看出,只有当信道条件较好的UEI缓冲区数据全部传输完毕,系统才调度UE2服务。
剖析大数据分析方法论的几种理论模型
剖析大数据分析方法论的几种理论模型 做大数据分析的三大作用,主要是:现状分析、原因分析和预测分析。什么时候开展什么样的数据分析,需要根据我们的需求和目的来确定。 作者:佚名来源:博易股份|2016-12-01 19:10 收藏 分享 做大数据分析的三大作用,主要是:现状分析、原因分析和预测分析。什么时候开展什么样的数据分析,需要根据我们的需求和目的来确定。 利用大数据分析的应用案例更加细化的说明做大数据分析方法中经常用到的几种理论模型。 以营销、管理等理论为指导,结合实际业务情况,搭建分析框架,这是进行大数据分析的首要因素。大数据分析方法论中经常用到的理论模型分为营销方面的理论模型和管理方面的理论模型。 管理方面的理论模型: ?PEST、5W2H、时间管理、生命周期、逻辑树、金字塔、SMART原则等?PEST:主要用于行业分析 ?PEST:政治(Political)、经济(Economic)、社会(Social)和技术(Technological) ?P:构成政治环境的关键指标有,政治体制、经济体制、财政政策、税收政策、产业政策、投资政策、国防开支水平政府补贴水平、民众对政治的参与度等。?E:构成经济环境的关键指标有,GDP及增长率、进出口总额及增长率、利率、汇率、通货膨胀率、消费价格指数、居民可支配收入、失业率、劳动生产率等。?S:构成社会文化环境的关键指标有:人口规模、性别比例、年龄结构、出生率、死亡率、种族结构、妇女生育率、生活方式、购买习惯、教育状况、城市特点、宗教信仰状况等因素。
?T:构成技术环境的关键指标有:新技术的发明和进展、折旧和报废速度、技术更新速度、技术传播速度、技术商品化速度、国家重点支持项目、国家投入的研发费用、专利个数、专利保护情况等因素。 大数据分析的应用案例:吉利收购沃尔沃 大数据分析应用案例 5W2H分析法 何因(Why)、何事(What)、何人(Who)、何时(When)、何地(Where)、如何做(How)、何价(How much) 网游用户的购买行为: 逻辑树:可用于业务问题专题分析
(推荐)生产计划APS高级自动排程思想
生产计划APS高级自动排程思想 技术领域 本思想可推荐或应用于绝大多数离散型制造类企业,尤其是汽车、家电等行业的生产计划高级排程。可以用来作为企业构建排程思想、完善排产体系、设计APS软件的参考。 背景技术 ※APS简介 高级计划与排程(Advanced Planning and Scheduling),是对所有资源具有同步的,实时的,具有约束能力的,模拟能力,不论是物料,机器设备,人员,供应,客户需求,运输等影响计划因素。不论是长期的或短期的计划具有优化,对比,可执行性。其将要采用基于内存的计算结构,这种计算处理可以持续的进行计算。这就彻底改变了批处理的计算模式。可以并发考虑所有供应链约束。当每一次改变出现时,APS 就会同时检查能力约束,原料约束,需求约束,运输约束,资金约束,这就保证了供应链计划在任何时候都有效。这样,APS计划的编制与顺序的安排就可以提供给制造商解决全球的优先权和工厂本地的优化顺序问题,来满足制造业对客户响应越来越强烈的需求。 目前ERP以生产为核心,这点是业界公认的,但如何以生产为核心却极少有详细的论述,其根本原因在于“详细生产排程”这个技术瓶颈。一般说,生产作业计划越详细,它给出的信息越丰富、越有价值,相应计算起来也就越困难。企业总是希望自动得到尽可能详细的作业计划。 用一句话来形容APS的主要功能:它可以自动给出满足多种约束条件、手工排程无法找到的、优化的排产方案。其实关键就是‘可行’和‘优化’这两个概念。这个说起来很简单的功能意义十分重大,主要体现在它可以给传统ERP带来以下几个关键的变化:
1)对企业来说,在不增加生产资源的情况下,通过最大限度发挥当前资源能力的方式实现了提高企业生产能力的目标。
调度算法
2015年10月21日
实验一 进程调度 1.实验目的: 通过对进程调度算法的模拟,进一步理解进程的基本概念,加深对进程运行状态和进程调度过程、调度算法的理解。 2.实验内容: (1)用C 语言(或其它语言,如Java )实现对N 个进程采用某种进程调度算法(如先来先服务调度、短作业优先调度、优先权调度、时间片轮转调度、多级反馈队列调度)的调度。 (2)为了清楚地观察每个进程的调度过程,程序应将每个进程的被调度情况显示出来。 (3)分析程序运行的结果,谈一下自己的收获。 3.设计实现: 1)流程图 主流程图: choice!=1&&choice!=2 c hoice==2 c hoice==1 Y N 开 始 初始化参数 输入函数 输入chioce FCFS SJF 输入有误,请重新输入! 是否继续? 结束
输入函数流程图: 请输入进程个数:Num N Y i=0 N i=0 N 先来先服务流程图: i=0 N Y N Y 开始 Num>0&&Num<=100 i 短作业优先算法流程图: i =0 N i = 0 开始 计算第一次NowTime 和第一个进程的完成时间 输出 i 数据分析算法与模型模拟题(一) 一、计算题(共4题,100分) 1、影响中国人口自然增长率的因素有很多,据分析主要因素可能有:(1)从宏观经济上看,经济整体增长是人口自然增长的基本源泉;(2)居民消费水平,它的高低可能会间接影响人口增长率。(3)文化程度,由于教育年限的高低,相应会转变人的传统观念,可能会间接影响人口自然增长率(4)人口分布,非农业与农业人口的比率也会对人口增长率有相应的影响。为了全面反映中国“人口自然增长率”的全貌,选择人口增长率作为被解释变量,以反映中国人口的增长;选择“国名收入”及“人均GDP”作为经济整体增长的代表;选择“居民消费价格指数增长率”作为居民消费水平的代表。暂不考虑文化程度及人口分布的影响。 从《中国统计年鉴》收集到以下数据(见表1): 表1 中国人口增长率及相关数据 人口自然增长率国民总收入居民消费价格指数增长人均GDP 年份(元))% 率((亿元)(%。)CPI1366 15037 1988 15.73 18.8 1519 15.04 17001 18 1989 1644 3.1 18718 1990 14.39 1893 12.98 1991 21826 3.4 2311 11.6 26937 1992 6.4 2998 35260 1993 11.45 14.7 4044 11.21 48108 1994 24.1 5046 59811 1995 10.55 17.1 5846 8.3 10.42 1996 70142 6420 78061 10.06 2.8 1997 6796 9.14 1998 83024 -0.8 7159 1999 88479 8.18 -1.4 7858 2000 98000 7.58 0.4 8622 6.95 2001 0.7 108068 9398 -0.8 2002 6.45 119096 10542 1.2 6.01 2003 135174 12336 3.9 5.87 2004 159587 14040 1.8 184089 5.89 2005 16024 1.5 5.38 213132 2006 设定的线性回归模型为: 算法1多元线性回归.xlsx (1)求出模型中的各个参数,试从多个角度评价此线性回归模型,并检验模型 保证调度算法 基本思想:向用户做出明确的性能保证,然后去实现它.如你工作时有n个用户的登录,则你将获得cpu处理能力的1/n 算法实现:跟踪计算各个进程已经使用的cpu时间和应该获得的cpu时间,调度将转向两者之比最低的进程 五,保证调度算法 思想:向用户做出明确的性能保证,然后去实现它. 算法:容易实现的一种保证是:当工作时己有n个用户登录在系统,则将获得CPU处理能力的1/n.类似的,如果在一个有n个进程运行的用户系统中,每个进程将获得CPU处理能力的1/n. 实现方法:OS应记录及计算,各个进程在一定时间段内,已经使用的CPU时间和应该得到的CPU时间,二者之比小者优先级高. 5. 保证调度 一种完全不同的调度算法是向用户作出明确的性能保证,然后去实现它。一种很实际并很容易实现的保证是:若用户工作时有n个用户登录,则用户将获得CPU处理能力的1/n。类似地,在一个有n个进程运行的单用户系统中,若所有的进程都等价,则每个进程将获得1/n的CPU时间。看上去足够公平了。 为了实现所做的保证,系统必须跟踪各个进程自创建以来已使用了多少CPU时间。然后它计算各个进程应获得的CPU时间,即自创建以来的时间除以n。由于各个进程实际获得的CPU时间是已知的,所以很容易计算出真正获得的CPU时间和应获得的CPU时间之比。比率为0.5说明一个进程只获得了应得时间的一半,而比率为2.0则说明它获得了应得时间的2倍。于是该算法随后转向比率最低的进程,直到该进程的比率超过它的最接近竞争者为止。 彩票调度算法 基本思想:为进程发放针对系统各种资源(如cpu时间)的彩票;当调度程序需要做出决策时,随机选择一张彩票,持有该彩票的进程将获得系统资源 合作进程之间的彩票交换 六,彩票调度算法 彩票调度算法: 为进程发放针对各种资源(如CPU时间)的彩票.调度程序随机选择一张彩票,持有该彩票的进程获得系统资源. 彩票调度算法的特点: 平等且体现优先级:进程都是平等的,有相同的运行机会.如果某些进程需要更多的机会,可被给予更多彩票,增加其中奖机会. 易计算CPU的占有几率:某进程占用CPU的几率,与所持有的彩票数成正比例.该算法可实现各进程占用CPU的几率. 响应迅速 各个进程可以合作,相互交换彩票. 容易实现按比例分配如图象传输率,10帧/s,15帧/s,25帧/s 生产排程的方法 时间:2014-05-06 11:32来源:本站整理作者:秩名点击: 1637 次 生产排程指的是为特定的订单(制造命令)分配作业期间(着手时期和完成时期)。为了完成订单,有必要与同一时期内必需的相同生产资源(设备、作业人员、模具等)的其他订单协调一致,以提高整体的运转率。以此为目的的生产排程的方法有如下三种。 前导式排程 前导式排程指的是一旦获得订单立刻着手的思路。医院的挂号采取的就足该思路。其缺点是在很多情况下会增加工序之间的半成品库存。 后导式排程 后导式排程指的是以最终交货期为起点沿着加工物的流程倒推工序,并以工序前置期为基础决定各个工序的着手和完成时刻的思路。后导式排程由于交货期明确,因此容易理解,被许多制造行业所采用。 瓶颈工序排程 即最大限度地利用瓶颈工序产能的排程方法。 为了进行排程,所需信息有加工数量、交货期、加工顺序、工作中心、各项作业的更换作业程序的时间、作业时间、等待加工的时间、移动时间、等待移动的时间、工作中心的可利用产能等。 排程结果的评价 排程的结果根据如下基准进行评价。 ·完工时间最短 ·设备机械的运转率最大 ·工序的半成.品库存最小 ·交货的延迟时间最短 在现实中,机械故障、质量方面的难题、断货以及其他障碍的发生往往会使情况变得复杂,因此制订最佳日程较为繁复。 订单生产型(BTO)企业的生产运作流程图时间:2008-10-29 17:21来源:https://www.360docs.net/doc/e37726414.html, 作者:yuyang 点击: 3943 次订单生产型(BTO)企业的生产运作流程图 瓶颈工序的排程 时间:2014-05-27 15:14来源:本站整理作者:秩名点击: 231 次 TOC(约束理论)考虑如何最大限度地利用瓶颈工序的产能,从生产计划的观点来看,这就变成了为了达到提高瓶颈工序运转率的目的,如何有效进行排程的问题。因此,大致可以按照以下步骤进行排程。 TOC的排程步骤 ①在日程计划中,首先决定瓶颈工序的着手日。 ②前道工序进行后导式排程,后道工序进行前导式排程。 ③为了防止因前道工序发生生产变动等原因造成瓶颈工序没有可进行作业的加工物的情况,要在瓶颈工序之前预备时间缓冲。 ④用天为单位表示时间缓冲的所需时间。 ⑤在前道工序中,向原材料投入工序的投入时间点要参照时间缓冲的状况进行。 时间缓冲是为了使瓶颈工序能够以最大限度的运转率进行作业的缓冲。因此,为了在前道工序出现生产变动而造成无加工物的情况下也能够进行作业,需要事先准备半成品库存。另外,在瓶颈工序以外的工序中,不会准备富余的半成品库存。所有的缓冲都必须设置存时间缓冲之中。 生产自动排程系统如何实现优化排产 生产自动排程系统如何实现优化排产 关键字:生产排程APS生产调度高级计划排程永凯软件永凯APS生产计划生产管理生产计划管理生产计划软件生产管理软件生产管理系统优化排程优化管理生产计划排程高级计划和生产排程PMC软件 全面解决生产计划与物料控制APS精益生产敏捷制造高级智能快速自动柔性社会功能层排程计划生产订单意向销售订单制令制单工单派工单委外外协工令工序工艺BOM机台生产线车间班次作业计划任务工作排程生产指示甘特图流程图表进度MRPMPS物料替代模拟排产资源调度滚动一键式网络手动优化结果精益生产敏捷制造即时响应快速排程 APS为何成为制造企业困境中的“救命稻草” 一、为什么多品种、小批量、短生命周期及短交货期是制造业面临的困境? 如果单单只是短交货期,企业可以通过大量库存就可以解决。然而当企业采用多品种、小批量的生产模式时,库存将涉及许多方面,特别是小批量时,产品需要的时间比较分散。为了防止因库存量不足而产生的机会损失,产品的安全库存量往往比较高,因此企业总体的库存水平也非常高。另一方面,由于产品短的生命周期,这些大量的库存可能一瞬间就会成为不良库存。 由于物流商和销售商都不想尽量持有库存,从而要求工厂交货时间要短。但“多品种、小批量”的产品在短时间交货是很不容易。 多品种、小批量生产时,会增加生产上的(切换)时间,同时还增加了物料管理的难度。由于产品不同,工序不同,交货期短,当工序为最后一道工序时,为了满足交货期可以很容易判断从哪个产品开始生产,但是对于中间工序而言就不容易判断从哪里开始生产。 很多企业期望通过增加库存来解决所面临的困境。如果仅增加库存就可以解决吗?殊不知增加库存会造成库存积压,恶化资金流通,并发生不良库存,陷入“减少库存量将迟延交货期,增加库存则产生不良库存”尴尬困境。 那要如何面对这种困境呢?增加产能?义务加班?也许可以临时解决,但是长期这么做会使企业增加经营成本,员工感到疲惫不堪。 二、到底怎样才能解决“制造业所面临的困境”? 对于多品种、小批量、短生命周期、短交货期的生产模式,缩短制造提前期是一个有效的方法,这是因为: 1、可应对短交货期要求; 2、减少生产过程中的中间品的库存浪费; 3、减少生产结束后的中间品的安全库存量; 4、改善资金流通,消减不良库存。 三、那怎样缩短制造提前期呢? 一、做出详细生产作业计划需要哪些条件? 在许多生产管理者眼中,生产作业计划是不重要的,如果我们只停留在小加工作坊的规模,大脑就能把一个月的订单、物料、资源记得清清楚楚,那么生产计划排程的必要性确实不太大,但事实上,随着生产规模的扩大,人脑已经不可能完成如此大数据量的存储功能,这时就到了生产管理的Excel时代,许多生产管理人员对Excel使用非常熟悉,并乐在其中,但如果要问他计划的详细信息,计划的优劣以及可执行性问题,这就遇到了困难,道理很简单,Excel只是将数据的存储从大脑移到了电脑,增大了容量,却仍然没有实质性的改进,但Excel的存储作用却是不言而喻的,它是生产计划排程数据准备的重要手段,但Excel相对于文本来说只是多了一个方便操作的表格,并没有严格的二维数据关系,这时就到了生产管理的ERP/MES时代。 这些基础数据主要包括如下几种: (1)所有产品结构信息。 即生产管理中BOM管理,有了产品结构才能方便的进行订单分解,分解成实际生产的任务。 (2)所有产品的制造工艺信息。 简单来说,就是要能知道任何一个制造任务(如一个零件)可以分解为几步以及每一步之间的逻辑关系,每一步用到哪些物料、需要哪种设备、需要哪些辅助工具,即是生产管理中常说的工艺流程。 (3)所有使用的资源信息。 资源是必备的生产主体,没有资源,生产无从谈起,所以需要对生产所需要的全部资源进行管理,这里所说的资源包含物料、设备、工具等。对资源的管理主要是对资源能力和成本的管理。 资源的能力分为两个方面,一是资源的单位能力,即一个资源能同时加工的工序数,比如说有些设备只能加工一道工序,而有的设备能同时加工两道同样的工序,那么,这两台设备的单位能力是不同的,能力的另一方面是资源的数量,如果一种设备有同样的五台,另一种设备只有一台,如果它们的单位能力都是相同的话,那么显然,五台的设备能力大于一台的能力。这就是生产管理中常说的设备能力,比如有些数控设备是多主轴,可以同时加工多个零件,这就是设备的单位能力,另一方面资源的数量就是指资源库存了。资源拥有生产的能力,使用能力则必定产生成本,成本的定义根据资源的类型决定,非消耗性的资源用时间定义成本,使用的时间越长,消耗的成本越大,消耗性资源则用消耗的数量进行定义,消耗的数量越多,消耗的成本越大。 (4)其它信息,包括订单,日历等信息。 订单是生产计划排程的源头,所以重要性是不言而喻的,订单主要信息包括数量,交货期等;日历是生产制造正常进行的规则,所以也是必须的数据。 上面所列出的数据需要完备性,缺少任意一种均不能进行有限资源能力的排程,同时所有数据也需要准确性,基础数据的准确性决定着计划排程的可执行性。 二、如何做一个可执行的生产计划排程与排程? 在具备了生产计划排程的数据条件之后,如何能制定出一个可执行的计划,成为生产计划排程人员头痛的问题,因为面对纷繁复杂的工序逻辑关系,面对有限能力的资源竞争,再聪明、再有丰富经验的生产计划排程人员也无法准确的计算出每道工序的工作时间。 这时,生产计划排程人员总是靠经验找出负荷最重的瓶颈设备,再结合优先级按照工艺流程的逻辑顺序将瓶颈设备上的工序先进行排程,再安排其它上设备上的工序,这样制定出 经典调度算法的实现 学院: 专业: 姓名: 学号: 指导老师: 2014-3-18 目录 一、课设简介 (3) 1. 课程设计题目 (3) 2. 课程设计目的 (3) 3. 课程设计的内容 (3) 4. 课程设计要求 (3) 二、原理分析 (4) 1. 先来先服务算法介绍与分析 (4) 2. 短作业优先算法介绍与分析 (4) 3. 高响应比优先调度算法介绍与分析 (4) 4. 流程图 (5) 三、主要功能模块 (7) 1. 先来先服务算法实现代码 (7) 2. 短作业优先算法实现代码 (8) 3. 高响应比优先调度算法实现代码 (8) 四、测试与运行结果 (9) 1. 主界面 (9) 2. 先来先服务算法测试 (10) 3. 短作业优先算法测试 (11) 4. 高响应比优先调度算法测试 (13) 五、总结 (16) 六、参考文献 (16) 七、附录 (16) 一、课设简介 1.课程设计题目 经典调度算法的实现 2.课程设计目的 操作系统课程设计是计算机专业重要的教学环节,它为学生提供了一个既动手又动脑,将课本上的理论知识和实际有机的结合起来,独立分析和解决实际问题的机会。 ●进一步巩固和复习操作系统的基础知识。 ●培养学生结构化程序、模块化程序设计的方法和能力。 ●提高学生调试程序的技巧和软件设计的能力。 ●提高学生分析问题、解决问题以及综合利用 C 语言进行程序设计的能力。 3.课程设计的内容 实现以下几种调度算法 1 FCFS 2 SJF 3 高响应比优先调度算法。 4.课程设计要求 1.不同的功能使用不同的函数实现(模块化),对每个函数的功能和调用接口要注释清楚。对程序其它部分也进行必要的注释。 2.对系统进行功能模块分析、画出总流程图和各模块流程图。 3.用户界面要求使用方便、简洁明了、美观大方、格式统一。所有功能可以反复使用,最好使用菜单。 4.通过命令行相应选项能直接进入某个相应菜单选项的功能模块。 5.所有程序需调试通过。 高级计划系统(APS)中生产计划排程 供应链管理(SCM)涉及企业间的集成以及在产销网络中协调物流和信息流的各个方面。作为企业信息中枢的ERP系统,现在已经在许多企业中用于作业处理和定单执行。高级计划系统(APS,Advanced Planning Systems)作为ERP的补充,用于协调物流、开发瓶颈资源和保证交货日期。APS应用各种优化技术,并根据企业的商业目标来改进计划。APS包括需求和供应计划、运输和生产计划排程等各种供应链计划模块,本文主要介绍APS中生产计划排程(Production Planning and Scheduling)模块的基本原理[1]。 决策状况描述 生产计划排程的目的是为车间生成一个详细的短期生产计划。排产计划(Production schedule)指明了计划范围内的每一个定单在所需资源上的加工开始时间和结束时间,也即指出了在给定资源上定单的加工工序。排产计划可以通过直观的甘特图(Gantt chart)形式给出。 排产计划的计划间隔可以从一天到几周,取决于具体的工业生产部门。合理的计划长度取决于几个因素:一方面,它至少应当涵盖与一个定单在生产单元中最大的流动时间(flow time)相对应的时间间隔;另一方面,计划间隔受到已知顾客定单或可靠需求预测的可用性限制。很显然,只有当排产计划适度稳定时,在一个资源上进行定单排程才是有用的。也就是说,它们不应受不期望事件经常变化的影响(如定单数量改变或中断)。 对某些生产类型(如job shop),生产计划排程需要对(潜在)瓶颈 资源上的任务定单进行排序和计划;而对另一些生产类型(如成组技术),生产计划排程要能自动地、按时段检查资源组的能力,看其是否能够在下一个时间段内完成成组加工的一组定单。然后,可以手工排序这组定单在下一个时间段内的加工次序。 排产计划任务能够而且也应当分散来做,这样可以利用每个地点人们的专业知识和车间当前状况的知识(例如人员的可用性)。 生产计划排程受到上层主生产计划的约束,主生产计划设立了在分散的决策单位中执行生产计划排程的框架。从主计划中可获得的相应指导包括:使用超时或加班的数量;在不同时间点上来自供应链上游设施物料项的可用性;涉及来自供货商输入物料的采购协议。此外,由于主生产计划在供应链上有更宽的视点和更长的计划区间,从中我们还可以得到: 计划结束时需要建立的各物料项的季节性库存量; 交付给供应链下游设施的定单截止日期(下游设施可以是紧接着的下一级生产单位,分销商或最终顾客)。 排产计划生成 由车间模型生成排产计划的一般程序可简单地描述为下面6个步骤(如图1所示)。 1、建模 车间模型必须详细地捕捉生产流程的特征和相应的物流,以便以最小的成本生成可行的计划。 优先级调度算法 1、调度算法 考虑到紧迫型作业进入系统后能得到优先处理,引入了高优先级优先调度算法。 优先级调度的含义: (1)当该算法用于作业调度时,系统从后背作业队列中选择若干个优先级最高的,且系统能满足资源要求的作业装入内存运行;(2)当该算法用于进程调度时,将把处理机分配给就绪进行队列中优先级最高的进程。 2、调度算法的两种方式 非抢占式优先级算法:在这种调度方式下,系统一旦把处理机分配给就绪队列中优先级最高的进程后,该进程就能一直执行下去,直至完成;或因等待某事件的发生使该进程不得不放弃处理机时,系统才能将处理机分配给另一个优先级高的就绪队列。 抢占式优先级调度算法:在这种调度方式下,进程调度程序把处理机分配给当时优先级最高的就绪进程,使之执行。一旦出现了另一个优先级更高的就绪进程时,进程调度程序就停止正在执行的进程,将处理机分配给新出现的优先级最高的就绪进程。常用于实时要求比较严格的实时系统中,以及对实时性能要求高的分时系统。 3、优先级的类型 进程的优先级可采用静态优先级和动态优先级两种,优先级可由用户自定或由系统确定。 静态优先级调度算法 含义:静态优先级是在创建进程时确定进程的优先级,并且规定它在进程的整个运行期间保持不变。 确定优先级的依据: 1)进程的类型。 2)进程对资源的需求。 3)根据用户的要求。 优点:简单易行;系统开销小。 缺点:不太灵活,很可能出现低优先级的作业,长期得不到调度而等待的情况;静态优先级法仅适合于实时要求不太高的系统。 动态优先级调度算法 含义:动态优先级是创建进程时赋予该进程一个初始优先级,然后其优先级随着进程的执行情况的变化而改变,以便获得更好的调度性能。 优点:使相应的优先级调度算法比较灵活、科学,可防止有些进程一直得不到调度,也可防止有些进程长期垄断处理机。 缺点:需要花费相当多的执行程序时间,因而花费的系统开销比较大。 4、实时调度算法 由于在任何一个实时系统中毒存在着若干个实时进程或任务,用来反应或控制相应的外部事件,并往往具有某种程度的紧迫性,所以对实时系统中的调度算法提出了某些特殊要求。 对实时系统的要求 高级计划系统()中生产计划排程 供应链管理()涉及企业间的集成以及在产销网络中协调物流和信息流的各个方面。作为企业信息中枢的系统,现在已经在许多企业中用于作业处理和定单执行。高级计划系统(,)作为的补充,用于协调物流、开发瓶颈资源和保证交货日期。应用各种优化技术,并根据企业的商业目标来改进计划。包括需求和供应计划、运输和生产计划排程等各种供应链计划模块,本文主要介绍中生产计划排程()模块的基本原理[1]。 决策状况描述 生产计划排程的目的是为车间生成一个详细的短期生产计划。排产计划()指明了计划范围内的每一个定单在所需资源上的加工开始时间和结束时间,也即指出了在给定资源上定单的加工工序。排产计划可以通过直观的甘特图()形式给出。 排产计划的计划间隔可以从一天到几周,取决于具体的工业生产部门。合理的计划长度取决于几个因素:一方面,它至少应当涵盖与一个定单在生产单元中最大的流动时间()相对应的时间间隔;另一方面,计划间隔受到已知顾客定单或可靠需求预测的可用性限制。很显然,只有当排产计划适度稳定时,在一个资源上进行定单排程才是有用的。也就是说,它们不应受不期望事件经常变化的影响(如定单数量改变或中断)。 对某些生产类型(如),生产计划排程需要对(潜在)瓶颈资源上的任务定单进行排序和计划;而对另一些生产类型(如成组技术),生产计划排 程要能自动地、按时段检查资源组的能力,看其是否能够在下一个时间段内完成成组加工的一组定单。然后,可以手工排序这组定单在下一个时间段内的加工次序。 排产计划任务能够而且也应当分散来做,这样可以利用每个地点人们的专业知识和车间当前状况的知识(例如人员的可用性)。 生产计划排程受到上层主生产计划的约束,主生产计划设立了在分散的决策单位中执行生产计划排程的框架。从主计划中可获得的相应指导包括:使用超时或加班的数量;在不同时间点上来自供应链上游设施物料项的可用性;涉及来自供货商输入物料的采购协议。此外,由于主生产计划在供应链上有更宽的视点和更长的计划区间,从中我们还可以得到: 计划结束时需要建立的各物料项的季节性库存量; 交付给供应链下游设施的定单截止日期(下游设施可以是紧接着的下一级生产单位,分销商或最终顾客)。 排产计划生成 由车间模型生成排产计划的一般程序可简单地描述为下面6个步骤(如图1所示)。 1、建模 车间模型必须详细地捕捉生产流程的特征和相应的物流,以便以最小的成本生成可行的计划。 由于一个系统的产出率只受潜在瓶颈资源的限制,因此,我们只需 一、设计目的 通过CPU调度相关算法的实现,了解CPU调度的相关知识,通过实现CPU调度算法,理解CPU的管理,以及不同的CPU调度算法实现过程。体会算法的重要性。 二、设计要求 1、编写算法,实现FCFS、非抢占SJF、可抢占优先权调度 2、针对模拟进程,利用CPU调度算法进行调度 3、进行算法评估,计算平均周转时间和平均等待时间 4、调度所需的进程参数由输入产生(手工输入或者随机数产生) 5、输出调度结果 6、输出算法评价指标 三、设计说明 1、采用数组、指针 2、FCFS 先来先服务调度算法是一种最简单的调度算法,当作业调度中采用该算法时,每次调度都是从后备作业队列中选择一个最先进入该队列的作业 3、非抢占SJF 短作业优先调度算法,是指对短作业有限调度算法。是从后备队列中选择一个估计运行时间最短的作业将他们调入内存。 4、可抢占优先权调度 在这种方式下,系统把处理机分配给优先权最高的进程,使之执行。但在其执行期间,只要出现另一个其优先权更高的进程,进程调度程序就立即停止当前进程(原优先权最高的进程)的执行,重新将处理及分配给新到的优先权最高的进程。 四、程序流程图。 1、可抢占优先权调度算法 2、FCFS 3、非抢占SJF 五、程序部分 1、FCFS #include APS排程系统 企业为能准确快速响应顾客订单的需求,并充分利用有限资源,除了企业资源规划系统(ERP),还需要先进规划与排程(Advanced Planning and Scheduling; APS)系统的强化,才能快速规划出能满足顾客需求及优化资源指派的作业排程,以面对日益竞争激烈的市场。鼎诛igiChain APS排程系统主要是针对台湾产业的特性设计,提供企业生产现场的需求配置与资源利用合理化,其智能型的排程不仅可帮助企业提升生产力,并具备有交期设定、订单承诺/查询、紧急插单与实时异常处理等多项功能。 生产现场的排程困境 随着整合上下游供货商的供应链管理模式的推行,及采购、生产与配销整体呋I活动日益复杂,采用已有30年历史的物料需求规划 (MRP) 系统已无法赶上e世代对生产规划与排程的种种需求,其中最困扰生管人员的莫过于对生产制造现场无法掌握实际的产能状况,以致大多采「有单就接」的接单政策。同时,由于无法有效掌握物料取得的前置时间及缺乏一实时可靠的顾客订单允诺(Available-to-Promise或Capable-to-Promise;ATP或CTP)机制,导致生管人员常以加班或增加机台设备为满足订单交期的恶性循环。再者,对于能显现现场排程最有效益的排程方法是需要投料(order release)与排程能协同合作的完美搭配;换言之,投料方法与排程方法必须一致,否则很难获得良好的排程效益。以目前业界常用的MRP与CRP模块而 言,生管人员常依据MRP的规划结果,针对顾客订单所需相关料件进行采购命令(PO)及制造命令(MO)的发放,然而,由于MRP系依据交期(due-date)利用前置时间向前递推(lead time off-setting)的逻辑来决定相关料件的采购、领料、交期或预计开工期,除非生产现场的排程方法亦是依据交期由后往前推(backward)以决定各作业的排程,否则无法获得排程效益。而上述根据交期由后向前推的排程方法通常仅能适用于最终装配线的排程(Final Assembly Schedule; FAS),此乃由于MRP系根据BOM中各料件预计采购或制造前置时间进行递推,众周皆知的,以此「不准确的」前置时间所递推出BOM各阶料件的交期一定不准确,此不合理交期自然无法作为制造现场作业的排程与派工依据。 目前,虽然有些业界试图利用CRP针对MRP规划结果进行产能负荷分析,然而基于前述理由,现场管理人员将仍然无法利用此修正后「假设合理」的MRP规划结果。此外,由于无法利用计算机做有效的现场作业排程规划,一旦外在环境变动(例如,顾客订单交期或数量改变、现场产能状况改变),采购单位可能又得耗用相当人力修正受到影响的原物料、零组件采购计划。当然,对顾客最重要的除了准时达交外,如何快速有效响应顾客一个最短且可行的交期,也是立足e世代的企业所面临的挑战。 为解决上述问题,一个妥善、有效的利用制造现场资源(如机器、人员、工具、物料等)来满足订单交期,达到产出量最大、瓶颈资源使用率最高及前置时间最短等生产策略,并能协助生管人员规划出实际可行的现场排程系统已迫在眉睫。有鉴于此,鼎召Y讯DigiChain APS解决方案利用先进的信息科技及规划技术处理复杂的排程作业,改进传统MRP咚阆拗频娜秉c,数据分析算法与模型一附答案
几种操作系统调度算法
生产排程的方法
生产自动排程系统如何实现优化排产教学内容
如何做一个可执行的生产计划排程
经典调度算法的实现
完整word版,高级计划系统(APS)中生产计划排程
优先级调度算法
高级计划系统中生产计划排程
CPU调度算法
APS排程系统概念