锂电工序英文名称
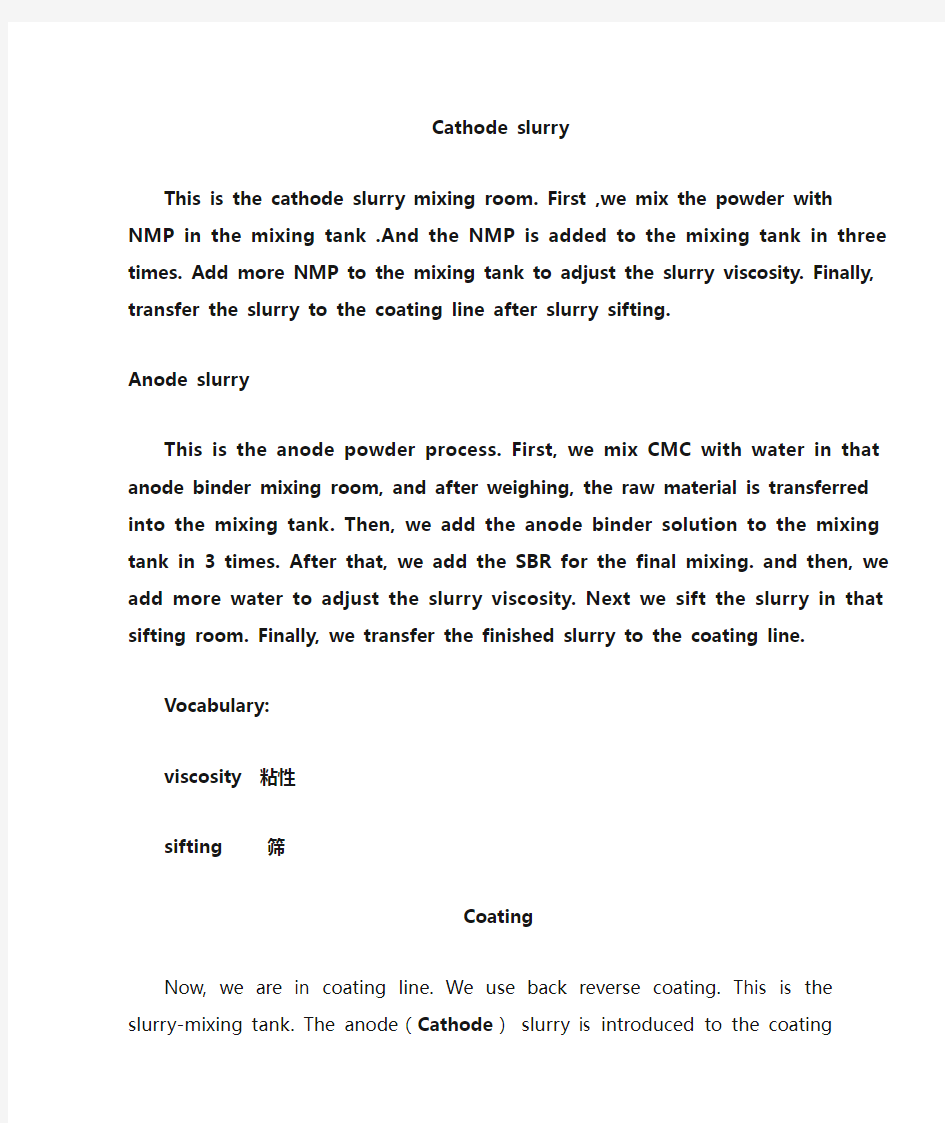
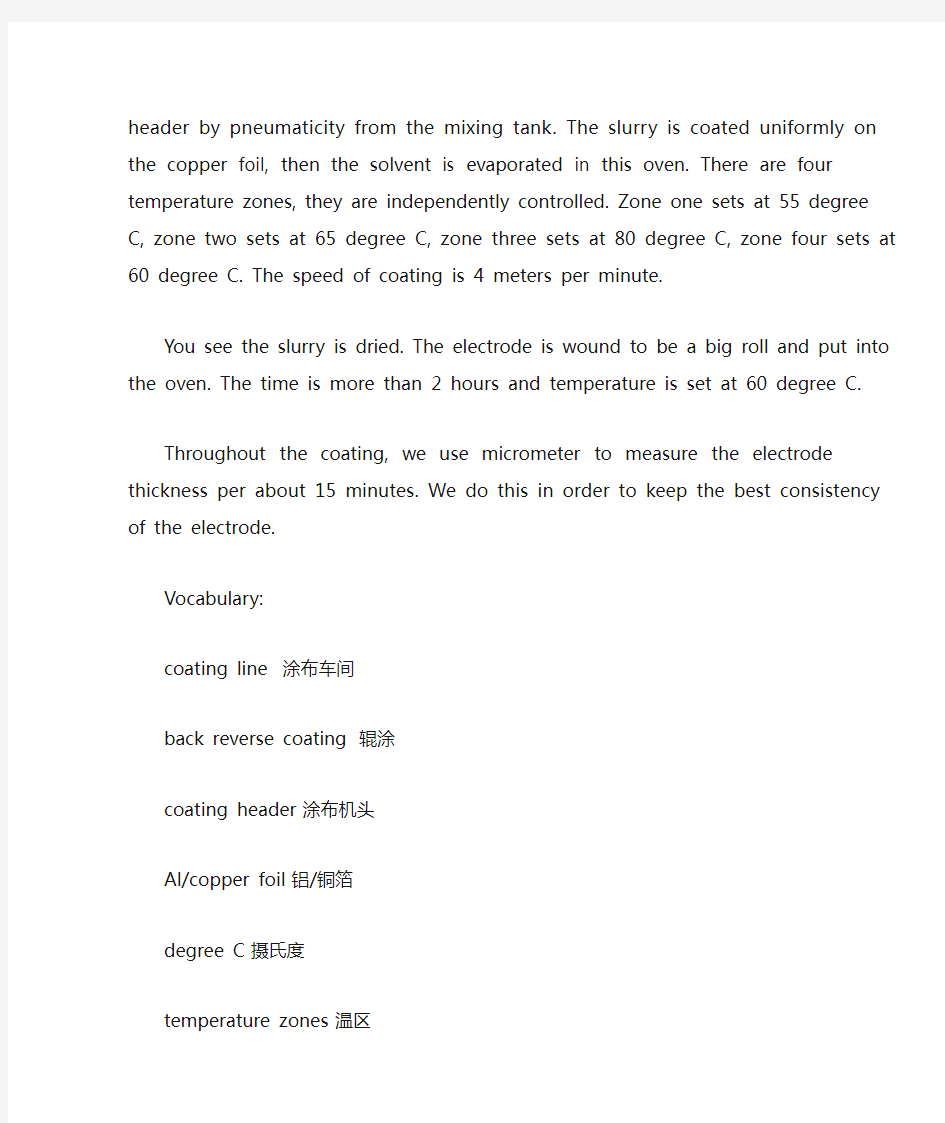
Cathode slurry
This is the cathode slurry mixing room. First ,we mix the powder with NMP in the mixing tank .And the NMP is added to the mixing tank in three times. Add more NMP to the mixing tank to adjust the slurry viscosity. Finally, transfer the slurry to the coating line after slurry sifting.
Anode slurry
This is the anode powder process. First, we mix CMC with water in that anode binder mixing room, and after weighing, the raw material is transferred into the mixing tank. Then, we add the anode binder solution to the mixing tank in 3 times. After that, we add the SBR for the final mixing. and then, we add more water to adjust the slurry viscosity. Next we sift the slurry in that sifting room. Finally, we transfer the finished slurry to the coating line.
Vocabulary:
viscosity 粘性
sifting 筛
Coating
Now, we are in coating line. We use back reverse coating. This is the slurry-mixing tank. The anode (Cathode)slurry is introduced to the coating header by pneumaticity from the mixing tank. The slurry is coated uniformly on the copper foil, then the solvent is evaporated in this oven. There are four temperature zones, they are independently controlled. Zone one sets at 55 degree C, zone two sets at 65 degree C, zone three sets at 80 degree C, zone four sets at 60 degree C. The speed of coating is 4 meters per minute.
You see the slurry is dried. The electrode is wound to be a big roll and put into the oven. The time is more than 2 hours and temperature is set at 60 degree C.
Throughout the coating, we use micrometer to measure the electrode thickness per about 15 minutes. We do this in order to keep the best consistency of the electrode. Vocabulary:
coating line 涂布车间
back reverse coating 辊涂
coating header 涂布机头
Al/copper foil 铝/铜箔
degree C 摄氏度
temperature zones 温区
wind to be a(big)roll 收卷
evenly/uniformly 均匀
oven 烘箱
evaporate 蒸发
electrode 极片
Electrode
After coating we compress the electrode with this cylindering machine at about 7meters per minute. Before compress we clean the electrode with vacuum and brush to eliminate any particles. Then the compressed electrode is wound to a big roll. We use micrometer to measure the compressed electrode thickness every 10 minutes. After compressing we cut the web into large pieces. We tape the cathode edge to prevent any possible internal short. The large electrode with edge taped is slit into smaller pieces. This is ultrasonic process that aluminum tabs are welded onto cathodes using ultrasonic weld machine. We tape the weld section to prevent any possible internal short. And finally, we clean the finished electrodes with vacuum and brush.
Vocabulary:
cylindering 柱形辊压
vacuum 真空
particle 颗粒
wound 旋紧卷绕
micrometer 千分尺
internal short 内部短路
slit 分切
ultrasonic 超声波
weld 焊接
Anode making
In anode making process, we cut the nickel roll into certain length strips. At the mean time, we put a small piece of insulation tape to the tab in order to prevent any possible internal short. Then the prepared nickel tab is
riveted on anode and pat plain. We also tape the rivet section to prevent any possible internal short. And finally, we clean the finished electrodes with vacuum and brush.
Jelly roll
This is Jelly roll, a manual winding process. In the course of Jelly roll, firstly, we place the separator in between central pins, press the foot switch to turn central pins about 120 degrees. Secondly, place the anode to the edge of central pins, and turn central pins about 180 degrees. Lastly, place the cathode to the edge of central pins. During the winding process, we apply tension by pressing the electrodes and the separator. We put the termination tape at the end.
After Jelly roll, we check the short circuit, then form the Jelly roll by pressing, so that it is easier to insert the Jelly roll into the can.
Control points:
1. When winding to the end of the anode, covering the anode completely by the separator.
2. In the whole process, it is the most important points to ensure the best alignment among the cathode, the anode and the separator for the Jelly roll. The separator has to cover the anode and the cathode, and the anode has to cover the cathode completely. These points are mainly checked before short checking.
Vocabulary:
Jelly roll 卷绕
Manual 手工的
Separator 隔膜纸
central pin 卷针
foot switch 脚踏开关
anode 负极片
cathode 正极片
termination tape 尾端胶纸
short circuit 短路
alignment 整齐
Taping&inserting
Put the tape on the two side of J/R, To prevent J/R being hurt in the insertion process.
Put a piece of tape between cathode tab and
J/R .Because anode electrode is wider than cathode electrode.
Put the bottom tape.
Insert the finished J/R into the can manually and then short circuit check by multi-meter.
Spot welding Ni tab to cap.
Ultrasonic welding the Al tab to cap using ultrasonic weld.
We have the second spot welding to ensure the best contact between the tab and cap.
Apply top insulator, to prevent Ni tab contacting with can.
Final J/R insertion by the centrifuge.
Cap positioning by hand. Then check the cap in the suitable position, or the defects is put into red bin ,Finally , short circuit check again to ensure that there be no internal short J/R flowing to next line.
Vocabulary:
J/R 极芯
tape 胶纸
electrode 极片
multi-meter 万用表
Spot welding 点焊
Ni tab 极耳
Ultrasonic weld 超焊
Insulator 隔圈
centrifuge machine 甩壳机
defect 次品
red bin 红盒
Laser welding
This is the Laser welding room! The first process is welding for the aluminum cap, specially connect the rivet with the weld plate to prevent the cell impedance excursion.
The second process is the Laser seam welding. In the process, it must ensure the intensity and airproof characters of the weld.
After the cell is welded, we would perform the leak checking, the short circuit checking and the weighing checking.
Vocabulary:
Laser welding room 激光焊接车间
Cap 盖板
Rivet 铆钉
Plate 镍片
impedance excursion 内阻漂移
intensity 强度
leak checking 检漏
short circuit checking 测短路
weighing checking 称重
Oven drying electrolyte filling and storing
This is the process of cells oven drying at 80℃for more than 12 hours under vacuum. After oven drying, the cells are transferred to the process of electrolyte filling through this channel. The electrolyte filling performs in dry room. The electrolyte is injected in two times so that it can be filled easily and sufficiently. When filling, vacuum first, then inject electrolyte. After that, we repeat vacuum and vent to room pressure several times. Finally the cell is put off at room pressure, then weigh the cell in order to check the amount of electrolyte. After weighing, we seal with tape onto the filling port to prevent the cells absorbing water during storing.
We store the filled cells for 24 hours at room temperature so that the electrolyte can be saturated sufficiently by the anodes and cathodes.
Vocabulary:
oven drying 烘烤
vacuum 真空
electrolyte filling 注液
electrolyte 电解液
room pressure 大气压
filling port 注液孔
storing 陈化
saturated 浸润
anode 正极
cathode 负极
Pre-charge and ball seal
At first, we place a piece of absorb cotton above the filling port to absorb the excess electrolyte. This is the first process.
The second process is performing a pre-charge at 0.1C rate for 390 minutes.
After the pre-charge, we take a voltage checking to the cell at once. If the voltage is lower than the standard, it needs to be re-charged.
The fourth process is the ball seal. we must complete this process in 15 minutes.
First, put the steel ball in the right place. Then, give pressure to it so that the steel ball can fill the filling port.
In the whole process, we must make sure that the temperature and humidity are in the regular range.
Finally, the process is cleaning to eliminate the electrolyte on the cell surface with acetone solvent.
Vocabulary:
filling port 注液孔
electrolyte 电解液
pre-charge 预先充电
voltage checking 量电压
ball seal 封口
regular range 合格范围
eliminate 消除
acetone solvent 丙酮溶剂
Aging and Formation
Welcome! I am the owner! This is the high temperature aging room. Because the temperature is very high, Let’s go out and I will introduce it. We age the cells at 35~40 Degree Celsius for 7 days. The temperature is controlled by two heating units. Then we transfer the cells to the testing workshop.
Let me introduce the next process. First, we check the volt of cells with multi-meters over there. In this process we must ensure the multi-meters can normally work. Then we charge the cells at 1 C rate to 4.2.V olt. According to capacity, we divide the cells into 7 grades --A0、A1、A2、A3、B、D、E。the cells of A0、A1、A2 and A3 grades are acceptable, the cells of B and D grades are defects, the cells of E grade are discarded as useless. and we check thickness and impedance. Finally, we transfer the cells to the warehouse.
Vocabulary:
aging room 老化房Celsius 摄氏
heating unit 加热器testing workshop 检测车间voltage 电压multi-meter 万用表acceptables 良品defects 次品
formation 化成thickness 尺寸,厚度impedance 内阻warehouse 仓库
锂电池各项工序控制重点
锂电池各项工序控制重点 锂离子电池的生产要一丝不苟,各个工序需要做到尽善尽美。新能源前线整理了锂电池实际生产的工艺流程。 (一) 配料: 1.溶液配制: a) PVDF(或CMC)与溶剂NMP(或去离子水)的混合比例和称量; b) 溶液的搅拌时间、搅拌频率和次数(及溶液表面温度); c) 溶液配制完成后,对溶液的检验:粘度(测试)\溶解程度(目测)及搁置时间; d) 负极:SBR+CMC溶液,搅拌时间和频率。 2.活性物质: a) 称量和混合时监控混合比例、数量是否正确; b) 球磨:正负极的球磨时间;球磨桶内玛瑙珠与混料的比例;玛瑙球中大球与小球的例; c) 烘烤:烘烤温度、时间的设置;烘烤完成后冷却后测试温度。 d) 活性物质与溶液的混合搅拌:搅拌方式、搅拌时间和频率。 e) 过筛:过100目(或150目)分子筛。 f) 测试、检验: 对浆料、混料进行以下测试:固含量、粘度、混料细度、振实密度、浆料密度。 (二)涂布 1.集流体的首检: a) 集流体规格(长宽厚)的确认; b) 集流体标准(实际)重量的确认;
c) 集流体的亲(疏)水性及外观(有无碰伤、划痕和破损)。 2.敷料量(标准值、上、下限值)的计算: a) 单面敷料量(以接近此标准的极片厚度确定单面厚度); b) 双面敷料量(以最接近此标准的极片厚度确定双面的极片厚度。) 3.浆料的确认:是否过稠(稀)\流动性好,是否有颗粒,气泡过多,是否已干结. 4.极片效果: a) 比重(片厚)的确认; b) 外观:有无划线、断带、结料(滚轮或极片背面)是否积料过厚,是否有未干透或烤焦,有无露铜或异物颗粒; 5.裁片:规格确认有无毛刺,外观检验。 (三)制片(前段): 1.压片: a) 确认型号和该型号正、负极片的标准厚度; b) 最高档次极片压片后(NO.1或NO.1及NO.2)的厚度、外观有无变形、起泡、掉料、有无粘机、压叠。 c) 极片的强度检验; 2.分片: a) 刀口规格、大片极片的规格(长宽)、外观确认; b) 分出的小片宽度; c) 分出的小片有无毛刺、起皱、或裁斜、掉料(正)。 3.分档称片: a) 称量有无错分; b) 外观检验:尺寸超差(极片尺寸、掉料、折痕、破损、浮料、未刮净等)。
锂离子电池工艺流程
锂离子电池工艺流程 正极混料 ●原料的掺和: (1)粘合剂的溶解(按标准浓度)及热处理。 (2)钴酸锂和导电剂球磨:使粉料初步混合,钴酸锂和导电剂粘合在一起,提高团聚作用和的导电性。配成浆料后不会单独分布于粘合剂中,球磨时间一般为2小时左右;为避免混入杂质,通常使用玛瑙球作为球磨介子。 ●干粉的分散、浸湿: (1)原理:固体粉末放置在空气中,随着时间的推移,将会吸附部分空气在固体的表面上,液体粘合剂加入后,液体与气体开始争夺固体表面;如果固体与气体吸附力比与液体的吸附力强,液体不能浸湿固体;如果固体与液体吸附力比与气体的吸附力强,液体可以浸湿固体,将气体挤出。 当润湿角≤90度,固体浸湿。 当润湿角>90度,固体不浸湿。 正极材料中的所有组员都能被粘合剂溶液浸湿,所以正极粉料分散相对容易。 (2)分散方法对分散的影响: A、静置法(时间长,效果差,但不损伤材料的原
有结构); B、搅拌法;自转或自转加公转(时间短,效果佳,但有可能损伤个别 材料的自身结构)。 1、搅拌桨对分散速度的影响。搅拌桨大致包括蛇形、蝶形、球形、桨形、齿轮形等。一般蛇形、蝶形、桨型搅拌桨用来对付分散难度大的材料或配料的初始阶段;球形、齿轮形用于分散难度较低的状态,效果佳。 2、搅拌速度对分散速度的影响。一般说来搅拌速度越高,分散速度越快,但对材料自身结构和对设备的损伤就越大。 3、浓度对分散速度的影响。通常情况下浆料浓度越小,分散速度越快,但太稀将导致材料的浪费和浆料沉淀的加重。 4、浓度对粘结强度的影响。浓度越大,柔制强度越大,粘接强度 越大;浓度越低,粘接强度越小。 5、真空度对分散速度的影响。高真空度有利于材料缝隙和表面的气体排出,降低液体吸附难度;材料在完全失重或重力减小的情况下分散均匀的难度将大大降低。
锂离子电池制作工序控制重点
锂离子电池制作工序控制重点 (一) 配料: 1.溶液配制: a) PVDF(或CMC)与溶剂NMP(或去离子水)的混合比例和称量; b) 溶液的搅拌时间、搅拌频率和次数(及溶液表面温度); c) 溶液配制完成后,对溶液的检验:粘度(测试)\溶解程度(目测)及搁置时间; d) 负极:SBR+CMC溶液,搅拌时间和频率。 2.活性物质: a) 称量和混合时监控混合比例、数量是否正确; b) 球磨:正负极的球磨时间;球磨桶内玛瑙珠与混料的比例;玛瑙球中大球与小球的比例; c) 烘烤:烘烤温度、时间的设置;烘烤完成后冷却后测试温度。 d) 活性物质与溶液的混合搅拌:搅拌方式、搅拌时间和频率。 e) 过筛:过100目(或150目)分子筛。 f) 测试、检验: 对浆料、混料进行以下测试:固含量、粘度、混料细度、振实密度、浆料密度。 (二)涂布 1.集流体的首检: a) 集流体规格(长宽厚)的确认; b) 集流体标准(实际)重量的确认; c) 集流体的亲(疏)水性及外观(有无碰伤、划痕和破损)。 2.敷料量(标准值、上、下限值)的计算: a) 单面敷料量(以接近此标准的极片厚度确定单面厚度); b) 双面敷料量(以最接近此标准的极片厚度确定双面的极片厚度。) 3.浆料的确认:是否过稠(稀)\流动性好,是否有颗粒,气泡过多,是否已干结. 4.极片效果: a) 比重(片厚)的确认; b) 外观:有无划线、断带、结料(滚轮或极片背面)是否积料过厚,是否有未干透或烤焦,有无露铜或异物颗粒; 5.裁片:规格确认有无毛刺,外观检验。 (三)制片(前段): 1.压片: a) 确认型号和该型号正、负极片的标准厚度; b) 最高档次极片压片后(NO.1或NO.1及NO.2)的厚度、外观有无变形、起泡、掉料、有无粘机、压叠。 c) 极片的强度检验; 2.分片: a) 刀口规格、大片极片的规格(长宽)、外观确认; b) 分出的小片宽度; c) 分出的小片有无毛刺、起皱、或裁斜、掉料(正)。 3.分档称片: a) 称量有无错分; b) 外观检验:尺寸超差(极片尺寸、掉料、折痕、破损、浮料、未刮净等)。
锂电池生产工序
各工序控制重点 (一) 配料: 1.溶液配制: a) PVDF (或CMC)与溶剂NMP(或去离子水)的混合比例和称量; b) 溶液的搅拌时间、搅拌频率和次数(及溶液表面温度); c) 溶液配制完成后,对溶液的检验:粘度(测试)\溶解程度(目测)及搁置时间; d) 负极:SBR+CMC溶液,搅拌时间和频率。 2.活性物质: a) 称量和混合时监控混合比例、数量是否正确; b) 球磨:正负极的球磨时间;球磨桶内玛瑙珠与混料的比例;玛瑙球中大球与小球的比例; c) 烘烤:烘烤温度、时间的设置;烘烤完成后冷却后测试温度。 d) 活性物质与溶液的混合搅拌:搅拌方式、搅拌时间和频率。 e) 过筛:过100目(或150目)分子筛。 f) 测试、检验: 对浆料、混料进行以下测试:固含量、粘度、混料细度、振实密度、浆料密度。 (二)涂布 1.集流体的首检: a) 集流体规格(长宽厚)的确认; b) 集流体标准(实际)重量的确认; c) 集流体的亲(疏)水性及外观(有无碰伤、划痕和破损)。 2.敷料量(标准值、上、下限值)的计算: a) 单面敷料量(以接近此标准的极片厚度确定单面厚度); b) 双面敷料量(以最接近此标准的极片厚度确定双面的极片厚度。) 3.浆料的确认:是否过稠(稀)\流动性好,是否有颗粒,气泡过多,是否已干结. 4.极片效果: a) 比重(片厚)的确认; b) 外观:有无划线、断带、结料(滚轮或极片背面)是否积料过厚,是否有未干透或烤焦,有无露铜或异物颗粒; 5.裁片:规格确认有无毛刺,外观检验。 (三)制片(前段): 1.压片: a) 确认型号和该型号正、负极片的标准厚度; b) 最高档次极片压片后(NO.1或NO.1及NO.2)的厚度、外观有无变形、起泡、掉料、有无粘机、压叠。 c) 极片的强度检验;
揭秘!锂电池制造工艺设计全解析
---------------------------------------------------------------最新资料推荐------------------------------------------------------ 揭秘!锂电池制造工艺设计全解析 WORD 格式-可编辑揭秘!锂电池制造工艺全解析锂电池结构锂离子电池构成主要由正极、负极、非水电解质和隔膜四部分组成。 目前市场上采用较多的锂电池主要为磷酸铁锂电池和三元锂电池,二者正极原材料差异较大,生产工艺流程比较接近但工艺参数需变化巨大。 若磷酸铁锂全面更换为三元材料,旧产线的整改效果不佳。 对于电池厂家而言,需要对产线上的设备大面积进行更换。 锂电池制造工艺锂电池的生产工艺比较复杂,主要生产工艺流程主要涵盖电极制作的搅拌涂布阶段(前段)、电芯合成的卷绕注液阶段(中段),以及化成封装的包装检测阶段(后段),价值量(采购金额)占比约为(35~40%):(30~35)%:(30~35)%。 差异主要来自于设备供应商不同、进口/国产比例差异等,工艺流程基本一致,价值量占比有偏差但总体符合该比例。 专业知识--整理分享 1/ 7
WORD 格式-可编辑锂电生产前段工序对应的锂电设备主要包括真空搅拌机、涂布机、辊压机等;中段工序主要包括模切机、卷绕机、叠片机、注液机等;后段工序则包括化成机、分容检测设备、过程仓储物流自动化等。 除此之外,电池组的生产还需要 Pack 自动化设备。 锂电前段生产工艺锂电池前端工艺的结果是将锂电池正负极片制备完成,其第一道工序是搅拌,即将正、负极固态电池材料混合均匀后加入溶剂,通过真空搅拌机搅拌成浆状。 配料的搅拌是锂电后续工艺的基础,高质量搅拌是后续涂布、辊压工艺高质量完成的基础。 涂布和辊压工艺之后是分切,即对涂布进行分切工艺处理。 如若分切过程中产生毛刺则后续装配、注电解液等程序、甚至是电池使用过程中出现安全隐患。 因此锂电生产过程中的前端设备,如搅拌机、涂布机、辊压机、分条机等是电池制造的核心机器,关乎整条生产线的质量,因此前端设备的价值量(金额)占整条锂电自动化生产线的比例最高,约35%。 锂电中段工艺流程锂电池制造过程中,中段工艺主要是完成电池的成型,主要工艺流程包括制片、极片卷绕、模切、电芯卷绕成型和叠片成型等,是当前国内设备厂商竞争比较激烈的一个领域,占锂电池生产线价值量约 30%。 目前动力锂电池的电芯制造工艺主要有卷绕和叠片两种,对应的
锂离子电池基本原理 配方及工艺流程
锂离子电池原理及工艺流程 一、原理 1.0 正极构造 LiCoO2+ 导电剂+ 粘合剂(PVDF) + 集流体(铝箔)正极 2.0 负极构造 石墨+ 导电剂+ 增稠剂(CMC) + 粘结剂(SBR) + 集流体(铜箔)负极 3.0工作原理 3.1 充电过程: 一个电源给电池充电,此时正极上的电子e从通过外部电路跑到负极上,正锂离子Li+从正极“跳进”电解液里,“爬过”隔膜上弯弯曲曲的小洞,“游泳”到达负极,与早就跑过来的电子结合在一起。
正极上发生的反应为 LiCoO2 ?→Li1-x CoO2+ x Li++ xe(电子) 负极上发生的反应为 6C + xLi++ x e?→Li x C6 3.2 电池放电过程 放电有恒流放电和恒阻放电,恒流放电其实是在外电路加一个可以随电压变化而变化的可变电阻,恒阻放电的实质都是在电池正负极加一个电阻让电子通过。由此可知,只要负极上的电子不能从负极跑到正极,电池就不会放电。电子和Li+都是同时行动的,方向相同但路不同,放电时,电子从负极经过电子导体跑到正极,锂离子Li+从负极“跳进”电解液里,“爬过”隔膜上弯弯曲曲的小洞,“游泳”到达正极,与早就跑过来的电子结合在一起。 3.3 充放电特性 电芯正极采用LiCoO2、LiNiO2、LiMn2O2,其中LiCoO2本是一种层结构很稳定的晶型,但当从LiCoO2拿走x个Li离子后,其结构可能发生变化,但是否发生变化取决于x的大小。 通过研究发现当x > 0.5时,Li1-x CoO2的结构表现为极其不稳定,会发生晶型瘫塌,其外部表现为电芯的压倒终结。所以电芯在使用过程中应通过限制充电电压来控制Li1-X CoO2中的x值,一般充电电压不大于4.2V那么x小于0.5 ,这时Li1-X CoO2的晶型仍是稳定的。 负极C6其本身有自己的特点,当第一次化成后,正极LiCoO2中的Li被充到负极C6中,当放电时Li回到正极LiCoO2中,但化成之后必须有一部分Li留在负极C6中心,以保证下次充放电Li的正常嵌入,否则电芯的压倒很短,为了保证有一部分Li留在负极C6中,一般通过限制放电下限电压来实现:安全充电上限电压≤ 4.2V,放电下限电压≥ 2.5V。 记忆效应的原理是结晶化,在锂电池中几乎不会产生这种反应。但是,锂离子电池在多次充放后容量仍然会下降,其原因是复杂而多样的。主要是正负极材料本身的变化,从分子层面来看,正负极上容纳锂离子的空穴结构会逐渐塌陷、堵塞;从化学角度来看,是正负极材料活性钝化,出现副反应生成稳定的其他化合物。物理上还会出现正极材料逐渐剥落等情况,总之最终降低了电池中可以自由在充放电过程中移动的锂离子数目。 过度充电和过度放电,将对锂离子电池的正负极造成永久的损坏,从分子层面看,可以直观的理解,过度放电将导致负极碳过度释出锂离子而使得其片层结构出现塌陷,过度充电将把太多的锂离子硬塞进负极碳结构里去,而使得其中一些锂离子再也无法释放出来。 不适合的温度,将引发锂离子电池内部其他化学反应生成我们不希望看到的化合物,所以在不少的锂离子电池正负极之间设有保护性的温控隔膜或电解质添加剂。在电池升温到一定的情况下,复合膜膜孔闭合或电解质变性,电池内阻增大直到断路,电池不再升温,确保电池充电温度正常。 二锂电池的配方与工艺流程 1. 正负极配方
锂离子电池电解液材料及生产工艺详解
锂离子电池电解液材料及生产工艺详解液体电解液生产工艺---流程图 电解液生产工艺---精馏和脱水 –对于使用的有机原料分别采取精馏或脱水处理以达到锂电池电解液使用标准。
–在精馏或脱水阶段,需要对有机溶剂检测的项目有:纯度、水分、总醇含量。 液体电解液生产工艺---产品罐 –在对有机溶剂完成精馏或脱水后,检测合格后经过管道进入产品罐、等待使用。 –根据电解液物料配比,在产品罐处通过电子计量准确称取有机溶剂。 –如果产品罐中的有机溶剂短时间未使用,需要再次对其进行纯度、水分、总醇含量的检测,继而根据生产的需要准确进入反应釜。 体电解液生产工艺---反应釜 –依据物料配比和加入先后顺序,有机溶剂依次加入反应釜充分搅拌、混匀,然后通过锂盐专用加料口或手套箱加入所需的锂盐和电解液添加剂。 –在加入物料开始到结束,应控制反应釜的搅拌速度、釜内温度等。不同的物料配比搅拌混匀的时间不同,但都必须使电解液混合均匀,此时对电解液检测的项目有:水分、电导率、色度、酸度 液体电解液生产工艺---灌装 –经检测合格的液体电解液被灌入合格的包装桶,充入氩气保护,最终进入仓库等待出厂。 –由于电解液自身的物理、化学性质等因素,入库的电解液应在短时间内使用,防止环境等因素导致电解液的变质 液体电解液---使用注意事项 –电解液桶有氩气保护,有一定压力,在使用中切勿拆卸气相阀头和液相阀头,也不允许随意按下快开接头的凸头,以免造成泄漏或其它危险。接管时一定要戴防护眼罩,使用时一定要使用专用快开接头
–检测合格的电解液建议一次性用完,开封的电解液很容易因为没有气氛保护等原因而变质,请客户在使用过程中注意及时充入氩气保护,防止变色电解液不建议使用玻璃器皿盛放,玻璃的主要成分是氧化硅,氧化硅和氢氟酸反应生成腐蚀性、易挥发的气体四氟化硅,此气体有毒会对人造成伤害 –现场可以使用的电解液容器和管道材料包括:不锈钢、塑料PP/PE、四氟乙烯等 –本产品对人体有害,有轻微刺激和麻醉作用。使用过程中避免身体直接接触 液体电解液的组成 –有机溶剂 –锂盐 –添加剂 有机溶剂---有机溶剂的选择标准 –有机溶剂对电极应该是惰性的,在电池的充放电过程中不与正负极发生电化学反应 –较高的介电常数和较小的黏度以使锂盐有足够高的溶解度,从而保证高的电导率 –熔点低、沸点高,从而使工作温度范围较宽 –与电极材料有较好的相容性,即电极能够在电解液中表现出优良的电化学性能 –电池循环效率、成本、环境因素等方面的考虑 液体电解液的组成---有机溶剂 –碳酸酯 –醚 –含硫有机溶剂
锂电池制片工艺要点
篇四锂电池制造正极制片 四部分正极制片 1、正极涂布干燥完,需要在工艺时间内进行对辊。对辊即对极片进行压实,目前有热压和冷压两种工艺。热压压实相对冷压高,反弹率较低;但冷压工艺相对简单易操作控制。对辊主要设备到如下工艺值,压实密度、反弹率、延伸率。同时要注意极片表面无脆片、硬块、掉料、波浪边等现象且间隙处不允许断裂。此时车间环境温度:≤23℃,湿度:≤25%。 压实:单位体积敷料的质量,目前常规物料的真密度数据 反弹率:一般反弹2-3um 延伸率:正极极片一般在≈1.002 2、正极对辊完接下来就是分条,即将整片极片分裁剪宽度一样的小条(对应电
池高度),分条要注意极片的毛刺,需要全检极片的X和Y向的毛刺(借助二次元设备),纵向毛刺长度工艺Y≤1/2 H隔膜厚度。车间环境温度≤23℃露点≤-30℃
篇五负极制片 1、负极制片与正极同样操作,但工艺设计不同,车间环境温度:≤23℃,湿度:≤25%。常见负极物质的真密度 反弹率:一般在4-8um 延伸率:一般在≈1.0012 2、负极分条与正极分条工艺类似,X和Y向毛刺都需要控制。车间环境温度≤23℃露点≤-30℃
篇六正极片制备 1、分条完毕后,需对正极片进行干燥处理(120℃),再就是焊接铝极耳和极耳包胶工艺。此时需要考虑极耳长度和整形宽度。 以**650型设计为例,设计极耳外露主要考虑到正极耳要焊接盖帽和滚槽时合理配合。极耳外露过长,滚槽时易使极耳与钢壳短路;过短极耳无法焊接盖帽。极目前超声焊头有线状和点状,国内工艺较多采用线状(过流、焊强考虑)。另采用高温胶将极耳包覆,主要考虑到金属毛刺和金属碎屑造成短路风险。此车间环境温度≤23℃,露点≤-30℃,正极水份含量≤500-1000ppm。
锂离子电池仓储及重要工序的预防措施
锂离子电池仓储及重要工序的预防措施 1、成品锂离子电池贮存的预防措施 (1)存放仓库的温度应保持在摄氏20±5℃度,最高不得超过30℃。 (2)要有良好的抽(排)风系统。 (3)仓库应有湿度控制,应避免长时间处于极端湿度(相对湿度高于95%或低于40%)下。 2、半成品锂离子电池贮存的预防措施 基于数次火灾事故的教训,半成品锂离子电池的贮存是电池制造企业安全管理工作的重中之重,应做到如下要求: (1)严格控制贮存量,不可大量存放未安装保护板的半成品锂离子电池。半成品锂离子电池不得使用产品电池的外包装材料。(2)仓库温度应保持在摄氏20±5℃度,最高不得超过30℃。(3)要有良好的抽(排)风系统。
(4)仓库应有湿度控制,应避免长时间处于极端湿度(相对湿度高于95%或低于40%)下。 (5)每块电池的正(负)极位置应有绝缘保护措施。应实现一块电池一个包装; (6)贮存电池的货架应用不燃材料分隔成小空间,避免因一块电池短路放电发热、燃烧而造成其他电池受热,导致事故扩大;(7)每一小隔间应有一个感烟报警器和感温报警器,并联接到报警处理中心。在小隔间内安装气体自动灭火装置; (8)加强仓库管理,安排专人负责检查半成品电池存放情况,发现险情及时处理。仓库贮存的电池发生冒烟、燃烧可以使用金属事故电池处理柜进行处理; (9)作业人员在处理事故电池时应做好个体防护,应佩戴能过滤氟化物的防毒面具或自助式空气呼吸器; (10)企业应在仓库安装全角度视频监控系统,并安排人员值班,保证24小时不间断,以便及时发现险情迅速处理,将事故消
灭在初始阶段。 3、化成与分容工序的预防措施 (1)改革化成柜与分容柜。化成柜与分容柜宜设计成方格型,每一格内放置的电池不宜超过20块,以方便电池发生燃烧时进行处理,也可防止事故电池发生爆炸影响到其它电池而产生连锁反应。 (2)安装烟感报警器。 (3)安装自动惰性气体灭火装置。 (4)安装排风装置,将化成与分容时电池泄漏的可燃气体及时排出。 (5)制作事故电池处理柜。 (6)加强管理措施。作业现场要不间断有人值班巡查,发现险情及时处理。为保证安全、正确、及时处理发生事故的电池,作业人员应注意以下事项: 1)作业人员在处理事故电池时应做好个体防护,宜佩戴能过
锂离子电池生产工艺
目录 1.设计的目的与任务 (1) 1.1课程设计背景 (1) 1.2课程设计目的与任务 (1) 2.设计的详细内容 (2) 2.1原材料及设备的选取 (2) 2.2电池的工作原理 (3) 2.3电池的制备工艺设计 (3) 2.3.1制片车间的工艺设计 (3) 2.3.2装配车间的工艺设计 (6) 2.3.3化成车间工艺设计 (7) 2.3.4包装车间工艺设计 (9) 2.4厂房设计 (9) 3.经济效益 (10) 4.对本设计的评述 (11) 参考文献 (12)
1.设计的目的与任务 1.1课程设计背景 自从1990年SONY采用可以嵌锂的钴酸锂做正极材料以来,锂离子电池满足了非核能能源开发的需要,同时具有工作电压高、比能量大、自放电小、循环寿命长、重量轻、无记忆效应、环境污染少等特点,现成为世界各国电源材料研究开发的重点[1~3]。锂离子电池已广泛应用于移动电话、便携式计算机、摄像机、照相机等的电源,并在电动汽车技术、大型发电厂的储能电池、UPS电源、医疗仪器电源以及宇宙空间等领域具有重要作用[4~5]。 正极材料作为决定锂离子电池性能的重要因素之一,研究和开发更高性能的正极材料是目前提高和发展锂电池的有效途径和关键所在。目前,已商品化的锂电池正极材料有钴酸锂、锰酸锂、镍酸锂等,而层状钴酸锂正极材料凭借其电压高、放电平稳、生产工艺简单等优点占据着市场的主要地位,也是目前唯一大量用于生产锂离子电池的正极材料[6~8]。 18650电池是指外壳使用65mm高,直径为18mm的圆柱形钢壳为外壳的锂离子电池。自从上个世纪90年代索尼推出之后,这种型号的电池一直在生产,经久不衰。经过近20年的发展,目前制备工艺已经非常成熟,性能有了极大的提升,体积能量密度已经提高了将近4倍,而且成本在所有锂离子电池中也是最低,目前早已走出了原来的笔记本电脑的使用领域,作为首选电池应用于动力及储能领域。 1.2课程设计目的与任务 如前文所述,在目前商业化的锂离子电池中,很多厂家都选用层状结构的 作为正极材料。其理论容量为274mAh/g,实际容量为140mAh/g左右,也有LiCoO 2 作为正极材料的18650锂电报道实际容量已达155mAh/g。本设计拟通过以LiCoO 2 池电芯器件作为模型,从原料选择、设计原理、制备工艺、封装条件、工作情况等方面进行系统调研,并设计出相应的电池器件。设计者将通过查阅资料、课题讨论、技术交流等方式,逐渐设计出合理、科学的18650锂电池电芯,培养初步的科研思维和科研能力;通过这一综合训练,使我对实际的新能源产品有初步的、
锂电池各工序控制重点
锂电池各工序控制重点 (一) 配料: 1.溶液配制: a) PVDF(或CMC)与溶剂NMP(或去离子水)的混合比例和称量; b) 溶液的搅拌时间、搅拌频率和次数(及溶液表面温度); c) 溶液配制完成后,对溶液的检验:粘度(测试)\溶解程度(目测)及搁置时间; d) 负极:SBR+CMC溶液,搅拌时间和频率。 2.活性物质: a) 称量和混合时监控混合比例、数量是否正确; b) 球磨:正负极的球磨时间;球磨桶内玛瑙珠与混料的比例;玛瑙球中大球与小球的比例; c) 烘烤:烘烤温度、时间的设置;烘烤完成后冷却后测试温度。 d) 活性物质与溶液的混合搅拌:搅拌方式、搅拌时间和频率。 e) 过筛:过100目(或150目)分子筛。 f) 测试、检验: 对浆料、混料进行以下测试:固含量、粘度、混料细度、振实密度、浆料密度。 (二)涂布 1.集流体的首检: a) 集流体规格(长宽厚)的确认; b) 集流体标准(实际)重量的确认; c) 集流体的亲(疏)水性及外观(有无碰伤、划痕和破损)。 2.敷料量(标准值、上、下限值)的计算: a) 单面敷料量(以接近此标准的极片厚度确定单面厚度); b) 双面敷料量(以最接近此标准的极片厚度确定双面的极片厚度。) 3.浆料的确认:是否过稠(稀)\流动性好,是否有颗粒,气泡过多,是否已干结. 4.极片效果: a) 比重(片厚)的确认; b) 外观:有无划线、断带、结料(滚轮或极片背面)是否积料过厚,是否有未干透或烤焦,有无露铜或异物颗粒; 5.裁片:规格确认有无毛刺,外观检验。 (三)制片(前段): 1.压片: a) 确认型号和该型号正、负极片的标准厚度; b) 最高档次极片压片后(NO.1或NO.1及NO.2)的厚度、外观有无变形、起泡、掉料、有无粘机、压叠。 c) 极片的强度检验; 2.分片: a) 刀口规格、大片极片的规格(长宽)、外观确认; b) 分出的小片宽度; c) 分出的小片有无毛刺、起皱、或裁斜、掉料(正)。 3.分档称片: a) 称量有无错分; b) 外观检验:尺寸超差(极片尺寸、掉料、折痕、破损、浮料、未刮净等)。 4.烘烤: a) 烤箱温度、时间的设置;
锂离子电池生产过程中的重要质量管控点
锂离子电池生产过程中的重要质量管控点 第38卷 2008正第5期 lO月 电池 BATTERY BIMONTHLY V01.38.NO.5 Oct..2008 锂离子电池生产过程中的重要质量管控点吴雪平 (无锡日立麦克赛尔有限公司,江苏无锡214028) 摘要:介绍了锂离子电池封口体组件、卷绕、组装、注液、化成和特性检查过程中的一些重要的质量管控点,对焊接强度、毛刺、电极状态和短路等的控制目的及控制方法进行了说明。强调了x射线检查、耐电压检测、电压差管理等在质量管理上的重要性。 关键词:锂离子电池; 生产过程;质量控制点;X射线检查; 电压差管理 中图分类号:TM912.9文献标识码:A 文章编号:1001—1579(2008)05—0305—04 Important quality control points in manufacturing process of Li?ion battery WU Xue—ping (Wuxi Hitachi Maxell Co.,Ltd.,Wuxi,Jmn伊u 214028,China) Abstract:The important quality control points in manufacturing process of Li?ion battery such a8gasket sealing unit assembling, jelly roll winding,assembly,electrolytepouring,formation and characteristics checking wereintroduced.Control purpose andcontrol methods of welding intensity,cutting burr,dectrode alignment and short circuit were analyzed.The importance of X‘ray impection,with8t 龃ding voltage test and voltage drop control were emphasized. Key words:Li-ion battery;manufacturing process;quality control points;X—ray inspection;voltage drop control 锂离子电池的质量,尤其是安全性能受到了越来越多的消费者的关注。在电池设计上,有专门针对极端情况,即万一发生严重质量问题时的保护措施,如在电池的铝壳(正极罐)上有安全阀(开裂阀),还采用专门的保护电路(PCM) 和热敏电阻(PTC),防止过充电、过放电和过电流等情况下电池发热、起火及爆炸等危害人身和财产的事故…。更重要的是各生产厂家在生产过程中应针对一些薄弱点加强质量管控,从源头上防止出现各种可能涉及安全性能的质量异常。这些异常一旦出现,仅靠最终的出厂质量检查手段是很难全部检出和排除的。