甲醇水筛板式精馏塔工艺设计方案

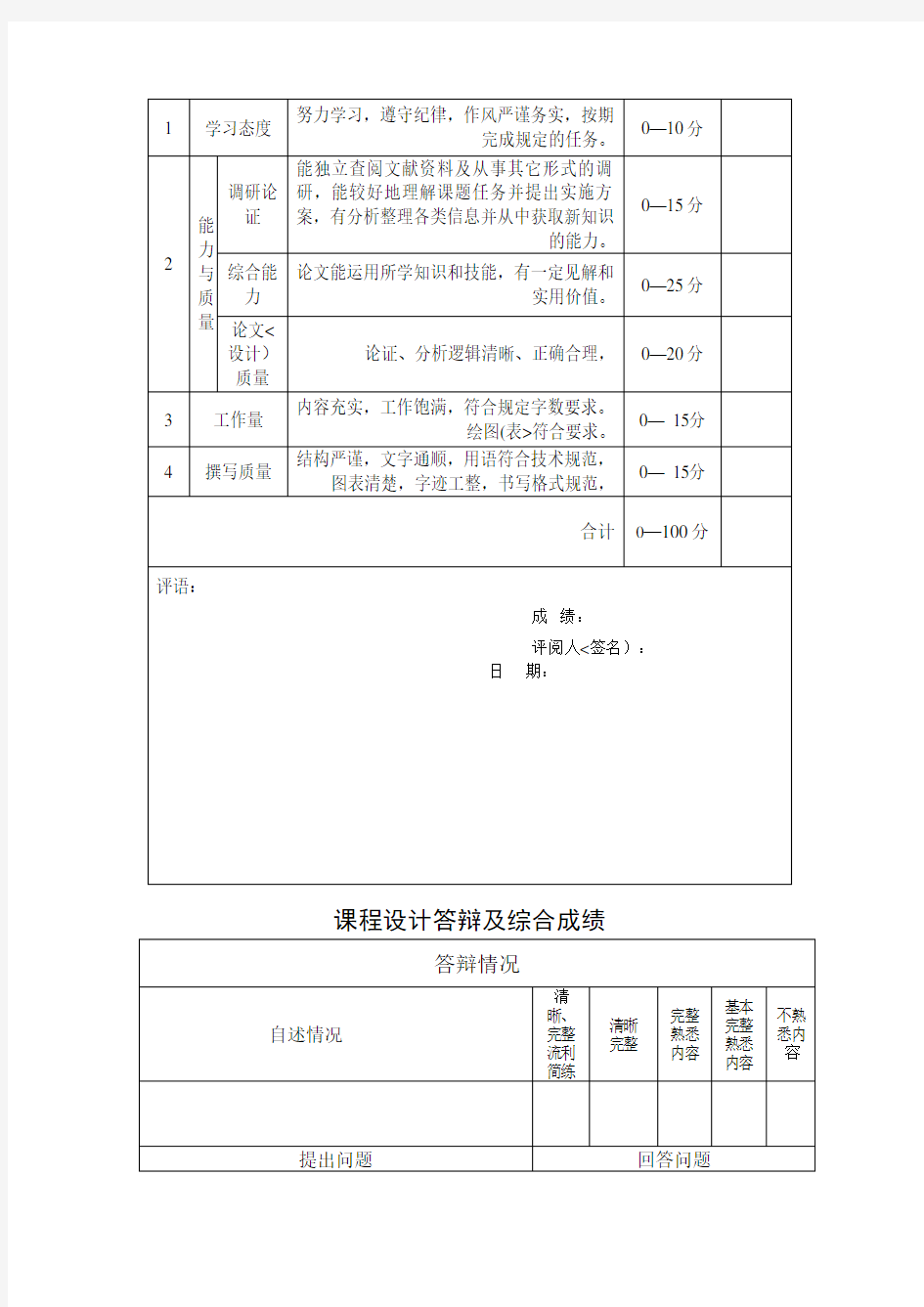
新疆工业高等专科学校
课程设计任务书
班级石化10-5<3)班专业石油化工生产技术姓名吕志鹏日期2018-6-9
1、论文<设计)题目:甲醇-水筛板式精馏塔工艺设计
2、论文设计任务要求:
<1)学生应在教师指导下按时完成所规定的内容和工作量,最好是独立完成。
<2)选题有一定的理论意义与实践价值,必须与所学专业相关。
<3)主题明确,思路清晰。
<4)文献工作扎实,能够较为全面地反映论文研究领域内的成果及其最新进展。
<5)格式规范,严格按系部制定的论文格式模板调整格式。
<6)所有学生必须在5月15日之前交论文初稿。
3、论文<设计)日期:任务下达日期 2018.5.1
完成日期 2018.6.16
4、指导教师签字:
新疆工业高等专科学校
课程设计成绩评定
报告
课程设计答辩及综合成绩
甲醇-水精馏塔工艺设计
学号:2018232708 学生:吕志鹏
(新疆工业高等专科学校, 乌鲁木齐 830091>
摘要:
精馏是一种利用回流使液体混合物得到高纯度分离的蒸馏方法,是工业上应用最广的液体混合物分离方法,广泛应用于石油、化工、食品、冶金等行业。精馏的基本原理是将液体混合物部分汽化,利用其中各组分挥发度不同的特性,实现分离目的的单元操作。
本设计选择板式精馏塔,塔板为筛板式,设计题目为甲醇-水板式精馏塔工艺设计。
关键词:甲醇-水,精馏,板式,筛板塔
目录
概述1
1.物料衡算3
1.1原料液及塔顶塔底产业品的摩尔分率3
1.2 物料衡算3
2.相对挥发度的计算及回流比的确定3
2.1 用内插法求塔顶进料塔釜的温度3
2.2 用内插法求3
2.3 相对挥发度的确定4
2.4 回流比的确定4
3.操作线的确定4
3.1 精馏塔内的气液相负荷4
3.2 精馏段操作线方程4
3.3 提馏段操作线方程4
4.塔板数的确定4
4.1 理论半数的确定4
4.2 实际塔板数的确定5
5.精馏塔主要尺寸的设计计算5
5.1 塔和塔板设计的主要依据和条件6
5.1.1 塔顶条件下的流量及物性参6
5.1.2 进料条件下的流量及物性参数7
5.1.3 精馏段的流量及物性参数8
6.空塔气速计算8
7.筛板塔工艺尺寸的计算9
7.1 塔的有效高度9
7.2 塔径与实际空塔气速9
7.3 溢流装置9
7.4 塔板分布10
7.5 筛孔计算及排列10
8.筛板的流体力学验算10
8.1 相关阻力的计算11
8.2 液沫夹带11
8.3 漏液12
8.4 液泡现象12
9.塔板负荷性能图12
9.1 漏液线12
9.2 液沫夹带线13
9.3 液相负荷下相线14
9.4 液相负荷上限线14
9.5 液泛线14
10.附录16
11.参考文献18
12.致谢19
概述
精馏塔是进行精馏的一种塔式气液接触装置,又称为蒸馏塔。有板式塔与填料塔两种主要类型。根据操作方式又可分为连续精馏塔与间歇精馏塔。
蒸馏的基本原理是将液体混合物部分气化,利用其中各组份挥发度不同<相对挥发度)的特性,实现分离目的的单元操作。蒸馏按照其操作方法可分为:简单蒸馏、闪蒸、精馏和特殊精馏等。
气液传质设备的种类繁多,根据塔内气液接触情况可分为两大类:一类是逐级接触式的板式塔,一类是连续接触是的填料塔。逆流条件下传质平均推动力最大,因此这两类塔总体上都是逆流装置<填料塔可采用并流,但大多为逆流操作)。
板式塔通常由圆柱状的塔体及按一定间距水平设置的若干塔板构成,塔内气体在压差作用下由下而上,液体在自身重力作用下由上而下总体呈逆流流动。板式塔可分为有溢流堰式和无溢流堰式<又称穿流式)两大类。对于有溢流式板式塔,在这类塔中塔板上由溢流堰维持一定液层,实际气液接触过程是在一块块塔板上逐级进行的,总体逆流,但在每块塔板上气液呈错流流动,即从上方降液管流下的液体横向流过塔板,翻过溢流堰进入降液管再流向下层塔板,而气体则由下而上穿过板上横流的液层,在液层中实现气液相密切接触然后离开液层,在塔板上方空间汇合后进入上层塔板,每一块塔板相当于一个混合分离器,既要求上升气流与下降气流在板上充分接触,又要求经传质后的气液两相完全分离,各自进入相邻塔板。因此,塔板上的主要部件是气液接触部件和溢流部件,在有的塔型中还设置了促进气液分离的部件。
气液接触部件的任务是引导气流进入液层,并保证气液充分、均匀而良好的接触,形成大量的又是不断更新的气液传质界面,而且要使气液间最后能够较易分离。不同类型的塔板具有不同的气液接触部件,溢流部件主要是维持液体在板上和板间顺序而均匀地流动,保持板上一定的液层,为气液接触提供场所。不同类型塔板的溢流部件基本一致。
塔板上有组织的气液流动应当使气液两相间保持充分、均匀、有效而良好的接触。这是指:相间接触面积要大且具有较强的湍动;气液分布要均匀且能按总体逆流、板上错流的原因保持最大的传质推动力;理论和实践又指出传质表面的不断更新也有利于降低传质阻力,提高传质速率。努力达到这种理想状态是塔板设计和操作改进的下一个方向。
气体通过筛板时的速度不同,气液两相在塔板上的接触状况就不同。塔板上气液两相接触状态有三种状态:鼓泡接触状态、泡沫接触状态、喷射接触状态。对于鼓泡接触状态,当孔速很低时,气体以鼓泡形式穿过板上清液层,此
时塔板上的气泡数量很少,板上液层清晰可见,两相的接触面积为气泡表面,
液体为连续相,气体为分散相。因为气泡数量较少,气泡表面的湍动程度较低,因而传质阻力较大,传质表面积较小,表面更新率也低;对于泡沫接触状态,随着孔速的增大,气泡的数量增多并形成泡沫,此时气液两相的传质面积主要为面积很大的液膜,液体仍为连续相,气体仍为分散相。因为泡沫层的高度湍动,液膜和气膜不断发生破裂与并和又重新形成,为两相传质创造了良好的流动力学条件;而喷射接触状态,当孔速继续增加,动能很大的气体从筛孔喷出穿过液层,将板上的液体破碎成许多大小不等的液滴而抛向踏板上方空间,当液滴回落合并后再次被抛碎成液滴抛出。此时两相传质面积是液滴外表面,液体为分散相,气体为连续相。因为液滴多次形成与合并,使传质表面不断更新,为两相传质创造了较好的流体力学条件。因此,工业生产中气液两相接触一般为泡沫或喷射状态。
当一定物系在塔板结构尺寸已确定的塔内操作时,只有气体和液体的流量是可能变化的因素。对板式精馏塔而言,气液流量随进料量、进料热状况及回流情况不同而异,这些参数的变化直接影响到塔是否能够正常操作以及能否达到规定的分离要求。为了维持塔的正常操作,生产中必须将气液流量控制在一个由塔板结构条件所决定的许可范围内,这个范围就是塔板的负荷<操作)性能图限定的范围。负荷性能图是以气体的体积流量为纵坐标,液体的体积流量为横坐标,在直角坐标系里标绘,图中曲线包括两种:一种是气液流量的流体力学上下限;另一种是塔板工作线或实际负荷线。
气液流体的流体力学上下限是由塔板的结构条件决定的,它包括五条线:(1>漏液线,也称为气相负荷下限线,它表示塔板在严重漏液时的气体流量与液体流量之间的关系,当气体流量低于此线时,将发生严重的漏液。<2)液体流量下限线,当 m时板上液体流动严重不均匀,使塔板效率急剧下降。(3>液体流量上限线,对于一定截面积和高度的降液管,其液体停留时间太短,气泡来不及分离,造成气泡夹带返混,严重时可能导致降液管内液泛,从而降低板效率。<4)过量液沫夹带线,气液流量超过此线时,将产生过量的液沫夹带,使板效率严重下降。液体流量越大,板上清液层与泡沫层高度越高,就越会增加液沫夹带,引起过量液沫夹带的气体量将有所降低。<5)液泛线,当气液负荷过大时,降液管内泡沫层高度有可能过高而引发液泛。液泛线表示降液管中泡沫层高度达到最大允许值时的气液负荷关系,气液负荷超过此线,则
塔不能正常操作。
塔板工作线或实际负荷线是由操作要求决定的气液流量关系线。实际气液流量的变化必落在这条直线上,塔板工作线与流体力学上下限比有两个交点,此两交点纵坐标的最大值与最小值之比即为操作弹性,操作弹性打,其操作范围大
即允许的气液负荷变化范围就大,说明塔的适应能力强。
1.物料衡算
1.1原料液及塔顶塔底产业品的摩尔分率
甲醇的摩尔质量水的摩尔质量
1.2 物料衡算
原料处理量
总物料衡算甲醇物料衡算
2.相对挥发度的计算及回流比的确定2.1 用内插法求塔顶进料塔釜的温度
塔顶温度
进料温度
塔釜温度
2.2 用内插法求
精馏段的平均温度
得
提馏段的平均温度
得
2.3 相对挥发度的确定
将分别代入得
故
2.4 回流比的确定
因为泡点进料所以把代入
得则
取操作回流比为
3.操作线的确定
3.1 精馏塔内的气液相负荷
3.2 精馏段操作线方程
3.3 提馏段操作线方程
4.塔板数的确定
4.1 理论半数的确定
有逐板计算法计算板数及相应的组成如下表4-1
1 2 3 4 5 6 7 8 9 10 11
0.950 0.886 0. 799 0.716 0.659 0.556 0.403 0.241 0.120 0.052 0.019
0.816 0.645 0.482 0.371 0.311 0.226 0.136 0.069 0.031 0.013 0.0045
4.2 实际塔板数的确定
全塔的平均温度:
利用内插法计算:
甲醇:
水:
利用内插法计算:
全部塔效率:
实际塔板数:
5.精馏塔主要尺寸的设计计算5.1 塔和塔板设计的主要依据和条件
5.1.1 塔顶条件下的流量及物性参
塔顶液相平均相对分子质量:
利用内插法求:
塔顶气相平均相对分子质量:
气相密度:
用内插法可以求得液相的密度、黏度和平均表面张力:液相密度:
液相黏度:
液相表面张力:
5.1.2 进料条件下的流量及物性参数
进料液相平均相对分子质量:
利用内插法求:
进料气相平均相对分子质量:
气相密度:
里用内插法可以求得液相的密度、黏度和平均表面张力:液相密度:
液相黏度:
5.1.3 精馏段的流量及物性参数
气相平均相对分子质量
液相平均相对分子质量
气相密度
液相密度
液相黏度
液相平均表面张力
6.空塔气速计算
则
取塔板间距板上液层高度那么分离空间
从史密斯关联图查得因为
因为适宜的空塔气速公式
因此需要先计算出最大允许空速
取安全系数为0.7则空塔气速为
7.筛板塔工艺尺寸的计算
7.1 塔的有效高度
在进料板上方开一人孔高度为0.8故精馏塔的有效高度为10.5+0.8=11.3
7.2 塔径与实际空塔气速
按标准塔径圆整后为
实际空塔气速
7.3 溢流装置
堰长取
溢流堰高度因为选用平直堰
弓形降液管宽度和面积由查弓形降液管参数图得
故由
式可以计算出液体在降液管中停留时间
降液管底隙高度取
则
故降液管底隙高度设计合理
7.4 塔板分布
塔板布置因故塔板采用分块式查表得塔块分为4块边缘区宽度
的确定取
开孔区面积计算:
7.5 筛孔计算及排列
甲醇-水物系无腐蚀性故可用碳钢板取筛孔直径筛孔按正三角形排列取孔中心距
筛孔数目:个
开孔率:
气体通过阀孔的气速为:
8.筛板的流体力学验算
8.1 相关阻力的计算
干板阻力的计算即由查干筛孔的流量系数图得
气体通过液层的阻力由计算
查充气系数关联图得
液体表面张力的阻力计算
气体通过每层塔板的液柱高度
气体通过每层塔板的压降为
8.2 液沫夹带
液沫夹带量:
故在设计中液沫夹带量在允许的范围内
8.3 漏液
对筛板塔漏液点气速可由公式计算得:
实际孔速:
稳定系数:
故在本设计中无明显漏液
8.4 液泡现象
为防止塔内发生液泛降液管由液层应服从甲醇-水物系属一般物系取则
而板上不设进口堰可由公式计算得
故在本设计中不会发生液泡现象
9.塔板负荷性能图
9.1 漏液线
由
在操作范围内任取几个值依上式计算出值计算结果
9.2 液沫夹带线
以
在操作范围内任取几个值依上式计算出值计算结果列于表9-2中
图9-2 Ls—Vs关系图
0.0006 0.0015 0.0030 0.0045
3.4106 3.2262 3.0807 2.9215 由上表数据即可作出液沫夹带线2.
9.3 液相负荷下相线
对于平直堰,取堰上液层高度作为最小液体负荷标准
取则
据此可作出与气体流量无关的垂直液相负荷下限线3
9.4 液相负荷上限线
以作为液体在降液管中停留时间的下限
故
据此可作出与气体流量无关的垂直液相负荷上限线4.
9.5 液泛线
令
由
联立得
忽略将,,关系式代入上式并整理得
式中
将有关数据代入得
故:
在操作范围内任取几个值依上式计算出值计算结果
表9—3 Ls—Vs关系图
0.0006 0.0015 0.0030 0.0045
2.49 2.4267 2.3172 2.1945 由上表数据即可作出液泛线.
10.附录
表10-1符号表示
A—塔板开孔区面积m; A—奖液管截面积m
A—筛孔总面积m; A—塔截面积m
d—筛孔直径,m D—塔径,m; e—液沫夹带量kg(液>/kg(气> E—液流收缩系数 E—总板效率
F—气相动能因子,kg /(s m>。
h—与板上液层阻力相当的液柱高度,m
h—板上清液层高度,m; h—降液管的底隙该度,m
h—堰上液层高度,m; h—出口堰高度,m
h —与克服的压降相当的液柱高度,m
H——塔底空间高度;m H——降液管内清液层高度, m
H——塔顶空间高度,m H——塔板间距,m K ——稳定系数 L——堰长,m L——液体体积流量,m/s n——筛孔数目
△P——气体通过每层筛板的压降,Pa
r——鼓泡区半径,m t——筛孔的中心距,m
u——空塔气速,m/s U——泛点气速。m/s
U——气体通过筛孔的速度。
m/s U——漏液点气速。m/s
V——气体体积流量,m /s W——液体质量流量 kg/s W——气体质量流量,kg/s W——边缘无效区宽度,m
W——边缘区宽度,
m W——安定区宽度,m
表10-2甲醇标准温度下气液相摩尔分数
甲醇摩尔分数温度/C 甲醇摩尔分数温度/C
化工原理甲醇—水连续填料精馏塔
化工原理课程设计说明书 设计题目:甲醇—水连续填料精馏塔 设计者: 专业: 学号: 指导老师: 2007年7 月13日
目录 一、设计任务书 (1) 二、设计的方案介绍 (1) 三、工艺流程图及其简单说明 (2) 四、操作条件及精熘塔工艺计算 (4) 五、精熘塔工艺条件及有关物性的计算 (14) 六、精馏塔塔体工艺尺寸计算 (19) 七、附属设备及主要附件的选型计算 (23) 八、参考文献 (26) 九、甲醇-水精熘塔设计条件图
一、设计任务书 甲醇散堆填料精馏塔设计: 1、处理量:12000 吨/年(年生产时间以7200小时计算) 2、原料液状态:常温常压 3、进料浓度:41.3%(甲醇的质量分数) 塔顶出料浓度:98.5%(甲醇的质量分数) 塔釜出料浓度:0.05%(甲醇的质量分数) 4、填料类型:DN25金属环矩鞍散堆填料 5、厂址位于沈阳地区 二、设计的方案介绍 1、进料的热状况 精馏操作中的进料方式一般有冷液加料、泡点进料、汽液混合物进料、饱和蒸汽进料和过热蒸汽加料五种。本设计采用的是泡点进料。这样不仅对塔的操作稳定较为方便,不受厦门季节温度影响,而且基于恒摩尔流假设,精馏段与提馏段上升蒸汽的摩尔流量相等,因此塔径基本相等,在制造上比较方便。 2、精熘塔的操作压力 在精馏操作中,当压力增大,混合液的相对挥发度减小,将使汽相和液相的组成越来越接近,分离越来越难;而当压力减小,混合液的相对挥发度增大,α值偏离1的程度越大,分离越容易。但是要保持精馏塔在低压下操作,这对设备的要求相当高,会使总的设备费用大幅度增加。在实际设计中,要充分考虑这两
筛板式精馏塔机械设计说明书
一、塔设备课程设计任务书 ㈠设计课题 筛板式精馏塔机械设计 ㈡工艺条件 物料名称:甲醇-水 设计压力:0.1a MP 设计温度:C 100 物料平均密度:3 957m kg 产品特性:易燃、有毒 设计基本风压值:2 300m N 地震烈度:7度 ㈢工艺尺寸 塔内径 精馏段板数 提留段板数 板间距 堰长 1400 33 17 500 980 堰高 筛孔直径 孔间距 塔顶蒸汽出口管径 50 6 24 200D g 管口 符号 公称尺寸 用途 a Dg273 进料管口 b Dg38 出料管口 c Dg325 塔顶蒸汽出口 d Dg38 回流液口 e Dg20 液面计接口 f Dg38 釜液出口 设计要求 1、筛板精馏塔机械设计及整体结构设计。 2、绘制筛板式精馏塔装配图(一张一号图纸) 二、设计方法及步骤 1、材料选择 设计压力MPa p 1.0 ,属于低压分离设备,一类容器,未提技术要求;产品特性为易燃、易挥发;设计温度为C 100,介质为甲醇和水,年腐蚀欲度很小,考虑到设备材料经济性,筒体,封头和补强圈材料选用R Q 245,裙座选用A Q 235。 2、塔设备主要结构尺寸的确定
㈠塔高 1)塔主体高度 ()mm H Z 2450050011733=?-+= 2)塔的顶部空间高度 mm H a 1500= 3)塔的底部空间高度 mm H b 2000= 4)裙座高度 mm H S 3000= 5)封头高度 mm H c 390= 6)塔高 mm H H H H H H c S b a Z 3139039030002000150024500=++++=++++= 取m mm H 3232000== m mm H H H H H S b a Z 3131000300020001500245001==+++=+++= ㈡塔径 1)筒体厚度计算 []mm p pD t i 56.01 .085.014721400 1.02=-???= -= φσδ 式中:[]t σ——材料的许用应力。R Q 245在C 100厚度为3~16mm 时, []MP a t 147=σ。 φ——塔体焊接接头系数。采用双面对接焊,局部无损探伤,85.0=φ 名义厚度mm C n 86.23.256.0=+=+=δδ 厚度附加量mm C C C 3.223.021=+=+= 1C ——厚度负偏差。按709T JB 中的B 类要求R Q 245负偏差取mm C 3.01=。 2C ——腐蚀裕量。取mm C 22=。 对于碳素钢、低合金钢制容器mm 3min ≥δ,故按刚度条件,筒体厚度仅需3mm ,但考虑此塔较高,风载荷较大,取塔体名义厚度=n δ10mm 。
填料精馏塔设计示例
4.3 填料精馏塔设计示例 4.3.1 化工原理课程设计任务书 1 设计题目 分离甲醇-水混合液的填料精馏塔 2 设计数据及条件 生产能力:年处理甲醇-水混合液0.30万吨(年开工300天) 原料:甲醇含量为70%(质量百分比,下同)的常温液体 分离要求:塔顶甲醇含量不低于98%,塔底甲醇含量不高于2% 建厂地址:沈阳 3 设计要求 (1)编制一份精馏塔设计说明书,主要内容: ①前言; ②流程确定和说明; ③生产条件确定和说明; ④精馏塔的设计计算; ⑤主要附属设备及附件的选型计算; ⑥设计结果列表; ⑦设计结果的自我总结评价与说明; ⑧注明参考和使用的设计资料。 (2)编制一份精馏塔工艺条件单,绘制一份带控制点的工艺流程图。 4.3.2 前言
在炼油、石油化工、精细化工、食品、医药及环保等部门,塔设备属于使用量大,应用面广的重要单元设备。塔设备广泛用于蒸馏、吸收、萃取、洗涤、传热等单元操作中。所以塔设备的研究一直是国内外学者普遍关注的重要课题。 塔设备按其结构形式基本上可分为两类:板式塔和填料塔。以前,在工业生产中,当处理量大时多用板式塔,处理量小时采用填料塔。近年来由于填料塔结构的改进,新型的、高负荷填料的开发,既提高了塔的通过能力和分离效能又保持了压降小以性能稳定等特点。因此填料塔已被推广到大型汽液操作中。在某些场合还代替了传统的板式塔。如今,直径几米甚至几十米的大型填料塔在工业上已非罕见。随着对填料塔的研究和开发,性能优良的填料塔必将大量用于工业生产中。 板式塔为逐级接触式汽液传质设备,它具有结构简单、安装方便、操作弹性大、持液量小等优点。同时也有投资费用较高、填料易堵塞等缺点。 本设计目的是分离甲醇-水混合液,处理量不大,故选用填料塔。 塔型的选择因素很多。主要因素有物料性质、操作条件、塔设备的制造安装和维修等。 1 与物性有关的因素 ①易起泡的物系在板式塔中有较严重的雾沫夹带现象或引起液泛,故选用填料塔为宜。因为填料不易形成泡沫。本设计为分离甲醇和水,故选用填料塔。 ②对于易腐蚀介质,可选用陶瓷或其他耐腐蚀性材料作填料,对于不腐蚀的介质,则可选金属性质或塑料填料,而本设计分离甲醇和水,腐蚀性小可选用金属填料。 2 与操作条件有关的因素 ①传质速率受气膜控制的系统,选用填料塔为宜。因为填料塔层中液相为膜状流、气相湍动,有利于减小气膜阻力。 ②难分离物系与产品纯度要求较高,塔板数很多时,可采用高效填料。 ③若塔的高度有限制,在某些情况下,选用填料塔可降低塔高,为了节约能耗,故本设计选用填料塔。 ④要求塔内持液量、停留时间短、压强小的物系,宜用规整填料。 4.3.3 流程确定和说明 1 加料方式 加料方式有两种:高位槽加料和泵直接加料。采用高位槽加料,通过控制液位高度,可以得到稳定的流量和流速。通过重力加料,可
化工原理课程设计,甲醇和水的分离精馏塔的设计
郑州轻工业学院 ——化工原理课程设计说明书 课题:甲醇和水的分离 学院:材料与化学工程学院 班级: 姓名: 学号: 指导老师: 目录 第一章流程确定和说明 (2) 1.1.加料方式 (2)
1.2.进料状况 (2) 1.3.塔型的选择 (2) 1.4.塔顶的冷凝方式 (2) 1.5.回流方式 (3) 1.6.加热方式 (3) 第二章板式精馏塔的工艺计算 (3) 2.1物料衡算 (3) 2.3 塔板数的确定及实际塔板数的求取 (5) 2.3.1理论板数的计算 (5) 2.3.2求塔的气液相负荷 (5) 2.3.3温度组成图与液体平均粘度的计算 (6) 2.3.4 实际板数 (7) 2.3.5试差法求塔顶、塔底、进料板温度 (7) 第三章精馏塔的工艺条件及物性参数的计算 (9) 3.1 平均分子量的确定 (9) 3.2平均密度的确定 (10) 3.3. 液体平均比表面积张力的计算 (11) 第四章精馏塔的工艺尺寸计算 (12) 4.1气液相体积流率 (12) 4.1.1 精馏段气液相体积流率: (12) 4.1.2提馏段的气液相体积流率: (13) 第五章塔板主要工艺尺寸的计算 (14) 5.1 溢流装置的计算 (14) 5.1.1 堰长 (14) 5.1.2溢流堰高度: (15) 5.1.3弓形降液管宽度 (15) 5.1.4 降液管底隙高度 (16) 5.1.5 塔板位置及浮阀数目与排列 (16) 第六章板式塔得结构与附属设备 (24) 6.1附件的计算 (24) 6.1.1接管 (24) 6.1.2 冷凝器 (27) 6.1.3再沸器 (28) 第七章参考书录 (28) 第八章设计心得体会 (29)
筛板式精馏塔课程设计说明
筛板式精馏塔课程设计说明
第一章绪论 1.1 化工原理课程设计的目的和要求 课程设计是《化工原理》课程的一个总结性教学环节,是培养综合运用本门课程及有关选修课程的基本知识去解决某一设计任务的一次训练。在整个教学计划中,它也起着培养独立工作能力的重要作用。 1.2 精馏操作对塔设备的要求 为了满足工业生产和需要,塔设备还得具备下列各种基本要求: (1) 气(汽)、液处理量大,即生产能力大时,仍不致发生大量的雾沫夹带、拦液或液泛等破坏操作的现象。 (2) 操作稳定,弹性大,即当塔设备的气(汽)、液负荷有较大范围的变动时,仍能在较高的传质效率下进行稳定的操作并应保证长期连续操作所必须具有的可靠性。 (3) 流体流动的阻力小,即流体流经塔设备的压力降小,这将大大节省动力消耗,从而降低操作费用。对于减压精馏操作,过大的压力降还将使整个系统无法维持必要的真空度,最终破坏物系的操作。 (4) 结构简单,材料耗用量小,制造和安装容易。 (5) 耐腐蚀和不易堵塞,方便操作、调节和检修。 (6) 塔内的滞留量要小。 实际上,任何塔设备都难以满足上述所有要求,不同的塔型各有某些独特的优点,设计时应根据物系性质和具体要求,抓住主要矛盾,进行选型。 1.3板式塔类型 在化学工业和石油工业中广泛应用的诸如吸收、解吸、精馏、萃取等单元操作中,气液传质设备必不可少。塔设备就是使气液成两相通过精密接触达到相际传质和传热目的的气液传质设备之一。 塔设备一般分为级间接触式和连续接触式两大类。前者的代表是板式塔,后者的代表则
为填料塔,在各种塔型中,当前应用最广泛的是筛板塔与浮阀塔。筛板塔在十九世纪初已应用与工业装置上,但由于对筛板的流体力学研究很少,被认为操作不易掌握,没有被广泛采用。五十年代来,由于工业生产实践,对筛板塔作了较充分的研究并且经过了大量的工业生产实践,形成了较完善的设计方法。 筛板塔和泡罩塔相比较具有下列特点:生产能力大于10.5%,板效率提高产量15%左右;而压降可降低30%左右;另外筛板塔结构简单,消耗金属少,塔板的造价可减少40%左右;安装容易,也便于清理检修。然而筛板塔也存在着一些缺点: (1)塔板安装的水平度要求较高,否则气液接触不匀; (2)操作弹性较小(约2~3); (3)小孔筛板容易堵塞。 本次设计就是针对水甲醇体系,而进行的常压二元筛板精馏塔的设计及其辅助设备的选型。 1.4精馏塔的工作原理和工艺流程 精馏塔是进行精馏的一种塔式汽液接触装置,又称为蒸馏塔。蒸气由塔底进入,与下降液进行逆流接触,两相接触中,下降液中的易挥发(低沸点)组分不断地向蒸气中转移,蒸气中的难挥发(高沸点)组分不断地向下降液中转移,蒸气愈接近塔顶,其易挥发组分浓度愈高,而下降液愈接近塔底,其难挥发组分则愈富集,达到组分分离的目的。由塔顶上升的蒸气进入冷凝器,冷凝的液体的一部分作为回流液返回塔顶进入精馏塔中,其余的部分则作为馏出液取出。塔底流出的液体,其中的一部分送入再沸器,热蒸发后,蒸气返回塔中,另一部分液体作为釜残液取出。 精馏原理 (Principle of Rectify) 蒸馏的基本原理是将液体混合物部分气化,利用其中各组份挥发度不同(相对挥发度,α)的特性,实现分离目的的单元操作。
板式精馏塔设计方案
板式精馏塔设计方案 一、设计方案确定 1.1 精馏流程 精馏装置包括精馏塔,原料预热器,再沸器,冷凝器,釜液冷却器和产品冷却器等,为保持塔的操作稳定性,流程中用泵直接送入塔原料,乙醇、水混合原料液经预热器加热至泡点后,送入精馏塔。塔顶上升蒸汽采用全凝器冷凝后经分配器一部分回流,一部分经过冷却器后送入产品储槽,塔釜采用间接蒸汽再沸器供热,塔底产品经冷却后为冷却水循环利用。 塔板是板式塔的主要构件,分为错流式塔板和逆流式塔板两类,工业中以错流式为主,常用的错流式塔板有:泡罩塔板,筛孔塔板,浮阀塔板。泡罩塔板是工业上应用最早的塔板,其主要的优点是操作弹性较大,液气比围较大,不易堵塞;但由于生产能力及板效率底,已逐渐被筛孔塔板和浮阀塔板所替代。筛孔塔板优点是结构简单,造价低,板上液面落差小,气体压强底,生产能力大;其缺点是筛孔易堵塞,易产生漏液,导致操作弹性减小,传质效率下降。而浮阀塔板是在泡罩塔板和筛孔塔板的基础上发展起来的,它吸收了前述两种塔板的优点。浮阀塔板结构简单,制造方便,造价底;塔板开孔率大,故生产能力大;由于阀片可随气量变化自由升降,故操作弹性大;因上升气流水平吹入液层,气液接触时间长,故塔板效率较高。但浮阀塔板也有缺点,即不易处理易结焦、高粘度的物料,而设计的原料是乙醇-水溶液,不属于此类。故总结上述,设计时选择的是浮阀塔板。 1.2设计方案论证及确定 1.2.1 生产时日及处理量的选择:设计要求塔年处理11.5万吨乙醇—水溶液系统,年工作日300d,每天工作24h。 1.2.2 选择用板式塔不用填料塔的原因:因为精馏塔精馏塔对塔设备的要求大致如下: (1)生产能力大:即单位塔截面大的气液相流率,不会产生液泛等不正常流动。
甲醇-水溶液连续精馏塔课程设计91604
目录 设计任务书 一、概述 1、精馏操作对塔设备的要求和类型 (4) 2、精馏塔的设计步骤 (5) 二、精馏塔工艺设计计算 1、设计方案的确定 (6) 2、精馏塔物料衡算 (6) 3、塔板数的确定 (7) 的求取 (7) 3.1理论板层数N T 3.2实际板层数的求取 (8) 4、精馏塔的工艺条件及有关物性数据的计算 4.1操作温度的计算 (11) 4.2平均摩尔质量的计算 (11) 4.3平均密度的计算 (12) 4.4液相平均表面张力计算 (12) 4.5液体平均粘度计算 (13) 5、精馏塔塔体工艺尺寸计算 5.1塔径的计算 (14) 5.2精馏塔有效高度的计算 (15) 6、塔板主要工艺尺寸计算 6.1溢流装置计算 (16) 6.2塔板的布置 (17) 6.3浮阀计算及排列 (17) 7、浮阀塔流体力学性能验算 (19) 8、塔附件设计 (26) 7、精馏塔结构设计 (30)
7.1设计条件 (30) 7.2壳体厚度计算………………………………………………… 7.3风载荷与风弯矩计算………………………………………… 7.4地震弯矩的计算………………………………………………… 三、总结 (27) 化工原理课程设计任务书 一、设计题目: 甲醇-水溶液连续精馏塔设计 二、设计条件: 年产量: 95%的甲醇17000吨 料液组成(质量分数): (25%甲醇,75%水) 塔顶产品组成(质量分数): (95%甲醇,5%水) 塔底釜残液甲醇含量为6% 每年实际生产时间: 300天/年,每天24小时连续工作 连续操作、中间加料、泡点回流。 操作压力:常压 塔顶压力4kPa(表压) 塔板类型:浮阀塔 进料状况:泡点进料 单板压降:kPa 7.0 厂址:安徽省合肥市 塔釜间接蒸汽加热,加热蒸汽压力为0.5Mpa 三、设计任务 完成精馏塔的工艺设计,有关附属设备的设计和选型,绘制精馏塔系统工艺流程图和精馏塔装配图,编写设计说明书. 设计内容包括: 1、 精馏装置流程设计与论证 2、 浮阀塔内精馏过程的工艺计算 3、 浮阀塔主要工艺尺寸的确定 4、 塔盘设计 5、 流体力学条件校核、作负荷性能图 6、 主要辅助设备的选型 四、设计说明书内容 1 目录 2 概述(精馏基本原理) 3 工艺计算 4 结构计算 5 附属装置评价 6 参考文献 7 对设计自我评价 摘要:设计一座连续浮阀塔,通过对原料,产品的要求和物性参数的确定及对主
甲醇精馏的方法
1.4.2 甲醇精馏的典型工艺流程甲醇精馏产生工艺有多种,分为单塔精馏,双塔精馏,三塔精馏与四塔精馏(即三塔加回收塔) (1) 单塔流程描述 采用铜系催化剂低压法合成甲醇,由于粗甲醇中不仅还原性杂质的含量大大减少,而且二甲醚的含量几十倍地降低,因此在取消化学净化的同时,可将预精馏及甲醇-水-重组分的分离在一台主精馏塔内同时进行,即单塔流程,就能获得一般工业上所需要的精甲醇。单塔流程更适用于合成甲基燃料的分离,很容易获得燃料级甲醇。 单塔流程(见图1.1)为粗甲醇产品经过一个塔就可以采出产品。粗甲醇塔中部加料口送入,轻组分由塔顶排出,高沸点的重组分在进料板以下若塔板处引出,水从塔底排出,产品甲醇在塔顶以下若干块塔板引出。 (2) 双塔流程描述 双塔工艺是由脱醚塔,甲醇精馏塔或者主塔组成。主塔在工厂中产量在100万吨/年以下,仅仅能提供简单的过程,所以设备和投资较低。 传统的工艺流程,是最早用于30MPa压力下以锌铬催化剂合成粗甲醇的精制。主要步骤有:中和、脱醚、预精馏脱轻组分杂质、氧化净化、主精馏脱水和重组分,最终得到精甲醇产品。在传统工艺流程上,取消脱醚塔和高锰酸钾的化学净化,只剩下双塔精馏(预精馏塔和主精馏塔)。其高压法锌铬催化剂合成甲醇和中、低压法铜系催化剂合成甲醇都可适用。 从合成工序来的粗甲醇入预精馏塔,此塔为常压操作。为了提高预精馏塔后甲醇的稳定性,并尽可能回收甲醇,塔顶采用两级冷凝。塔顶经部分冷凝后的
大部分甲醇、水及少量杂质留在液相作为回流返回塔,二甲醚等轻组分(初馏分)及少量的甲醇、水由塔顶逸出,塔底含水甲醇则由泵送至主精馏塔。主精馏塔操作压力稍高于预精馏塔,但也可以认为是常压操作,塔顶得到精甲醇产品,塔底含微量甲醇及其它重组分的水送往水处理系统(见图1.2)。 (3) 三塔流程描述 三塔工艺是由脱醚塔,加压精馏塔和常压精馏塔组成,形成二效精馏与二甲醇精馏塔甲醇产品的镏出物的混合物。三塔流程(见图1.3)的主要特点是,加压塔塔顶冷凝潜热用作常压塔塔釜再沸器的热源,形成双效精馏二效精馏,因此热量交换在加压塔顶部和常压塔底部之间进行。这种形式节省大约30%~40%的能源,同时降低了循环冷却水的速度。 从合成工序来的粗甲醇入预精馏塔,在塔顶除去轻组分及不凝气,塔底含水甲醇由泵送加压塔。加压塔操作压力为57bar(G),塔顶甲醇蒸气全凝后,部分作为回流经回流泵返回塔顶,其余作为精甲醇产品送产品储槽,塔底含水甲醇则进常压塔。同样,常压塔塔顶出的精甲醇一部分作为回流,一部分与加压塔产品混合进入甲醇产品储槽。 (4) 四塔流程描述 四塔流程(见图1.4)包含预精馏塔、加压精馏塔、常压精馏塔和甲醇回收塔。粗甲醇经换热后进入预精馏塔,脱除轻组分后(主要为不凝气、二甲醚等),塔底甲醇及高沸点组分加压后进入加压精馏塔,加压精馏塔顶的气相进入冷凝蒸发器,利用加压精馏塔和常压精馏塔塔顶、塔底的温差,为常压塔塔底提供热源,同时对加压塔塔顶气相冷凝。冷凝后的精甲醇进入回流罐,一部分作为加压塔回流,一部分作为精甲醇产品出装置,加压塔塔底的甲醇、高沸组分、
筛板式精馏塔的设计
1.概述 本设计为分离乙醇-水混合物,采用筛板式精馏塔。 1.1本设计在生产上的实用意义 乙醇的结构简式为C2H5OH,俗称酒精,它在常温、常压下是一种易燃、易挥发的无色透明液体,它的水溶液具有特殊的、令人愉快的香味,并略带刺激性。乙醇是一种很好的溶剂,既能溶解许多无机物,又能溶解许多有机物,所以常用乙醇来溶解植物色素或其中的药用成分,也常用乙醇作为反应的溶剂,使参加反应的有机物和无机物均能溶解,增大接触面积,提高反应速率。乙醇的用途很广,可用乙醇来制造醋酸、饮料、香精、染料、染料等,是农药、医药、橡胶、塑料、人造纤维、洗涤剂等的制造原料。医疗上也常用体积分数为70%——75%的乙醇作消毒剂等。 工业上一般用淀粉发酵法或乙烯直接水化法制取乙醇。 1.发酵法制乙醇是在酿酒的基础上发展起来的,在相当长的历史时期内,曾是生产乙醇的唯一工业方法。发酵法的原料可以是含淀粉的农产品,如谷类、薯类或野生植物果实等;也可用制糖厂的废糖蜜;或者用含纤维素的木屑、植物茎秆等。这些物质经一定的预处理后,经水解(用废蜜糖作原料不经这一步)、发酵,即可制得乙醇。 2.乙烯直接水化法,就是在加热、加压和有催化剂存在的条件下,是乙烯与水直接反应,生产乙醇:CH2═CH2 + H─OH→C2H5OH(该反应分两步进行,第一步是与醋酸汞等汞盐在水-四氢呋喃溶液中生成有机汞化合物,而后用硼氢化钠还原)。 若想要获得不同浓度的乙醇,可以采取精馏这种方法。譬如,75%的乙醇可以用蒸馏的方法蒸馏到95.5%,此后形成恒沸物,不能提高纯度。 化工生产常需进行液体混合物的分离以达到提纯或回收有用组分的目的。互溶液体混合物的分离有多种方法,精馏是其中最常用的一种。精馏是一种利用回流使液体混合物得到高纯度分离的蒸馏方法,精馏操作其基本原理是利用互溶液体混合物相对挥发度的不同,实现各组分分离的单元操作,是工业上应用最广的液体混合物分离操作,广泛用于石油、化工、轻工、食品、冶金等部门。 1.2 流程、设备及操作条件的确定 流程可由以下5个方面来确定。 (一)加料方式 加料分两种方式:泵加料和高位槽加料。高位槽加料通过控制液位高度,可以得到稳定流量,但要求搭建塔台,增加基础建设费用;泵加料属于强制进料方式,本次加料可选泵加料,泵和自动调节装置配合控制进料。 (二)加料状态 进料方式一般有冷液进料,泡点进料,气液混合物进料,露点进料,加热蒸汽进料五种。泡点进料对塔操作方便,不受季节温度影响。由于泡点进料时塔的制造比较方便,而其他进料方式对设备的要求高,设计起来难度相对加大,所以采用泡点进料。 (三)冷凝方式 选全凝器,塔顶出来的气体温度不高。冷凝后回流液和产品温度不高,无需再次冷凝,且本次分离是为了分离乙醇和水,制造设备较为简单,为节省资金,选全凝器。 (四)回流方式 宜采用重力回流,对于小型塔,冷凝液由重力作用回流如塔。优点:回流冷凝器无需支撑结构;缺点:回流控制较难安装,但强制回流需用泵,安装费用、点耗费用大,故不用强制回流,塔顶上升蒸汽采用冷凝回流入塔内。 (五)加热方式
甲醇-水精馏塔设计报告
《化工原理课程设计》报告
一、概述...................................................................................................................................... - 4 - 1.1 设计依据....................................................................................................................... - 4 - 1.2 技术来源....................................................................................................................... - 4 - 1.3设计任务及要求........................................................................................................... - 4 - 二、计算过程.............................................................................................................................. - 5 - 2. 1 设计方案.................................................................................................................... - 5 - 2.2 塔型选择....................................................................................................................... - 5 - 2.3工艺流程简介................................................................................................................ - 5 - 2.4 操作条件的确定........................................................................................................... - 6 - 2.41 操作压力............................................................................................................. - 6 - 2.4.2 进料状态............................................................................................................ - 6 - 2.4.3 热能利用............................................................................................................ - 6 - 2.5 有关的工艺计算........................................................................................................... - 6 - 2.5.1精馏塔的物料衡算...................................................................错误!未定义书签。 2.5.2物料衡算............................................................................................................. - 7 - 2.6 塔板数的确定............................................................................................................... - 7 - 2.6.1 理论板层数NT的求取 .................................................................................... - 7 - 2.6.2 实际板层数的求取............................................................................................ - 8 - 2.7精馏塔的工艺条件及有关物性数据的计算............................................................... - 8 - 2.7.1操作压力的计算................................................................................................. - 8 - 2.7.2操作温度的计算(详见附录一(1)) ................................................................ - 9 - 2.7.3 平均摩尔质量的计算........................................................................................ - 9 - 2.7.4 平均密度的计算................................................................................................ - 9 - 2.7.5液相平均表面力的计算................................................................................... - 11 - 2.7.6 液体平均粘度的计算...................................................................................... - 11 - 2.8 精馏塔的塔底工艺尺寸计算..................................................................................... - 12 - 2.8.1塔径的计算....................................................................................................... - 12 - 2.8.2 精馏塔有效高度的计算.................................................................................. - 13 - 2.9 塔板主要工艺尺寸的计算......................................................................................... - 14 - 2.9.1溢流装置的计算............................................................................................... - 14 - 2.9.2 塔板布置.......................................................................................................... - 15 - 2.10 筛板的流体力学验算............................................................................................... - 16 - 2.10.1 塔板压降........................................................................................................ - 16 - 2.10.2 液面落差........................................................................................................ - 18 - 2.10.3 液沫夹带........................................................................................................ - 18 - 2.10.4 漏液................................................................................................................ - 18 - 2.10.5 液泛................................................................................................................ - 18 - 2.11 塔板负荷性能图....................................................................................................... - 19 - 2.11.1液漏线............................................................................................................. - 19 - 2.11.2液沫夹带线..................................................................................................... - 20 - 2.11.3液相负荷下限线............................................................................................. - 20 - 2.11.4液相负荷上限线............................................................................................. - 21 - 2.11.5液泛线............................................................................................................. - 21 -
甲醇-水精馏课程设计—化工原理课程设计
甲醇-水分离过程板式精馏塔的设计 1.设计方案的确定 本设计任务为分离甲醇和水混合物。对于二元混合物的分离,应采用连续精馏流程。设计中采用泡点进料,将原料液通过预热器加热至泡点后送入精馏塔内。塔顶上升蒸气采用全凝器冷凝,冷凝液在泡点下一部分回流至塔内,其余部分经产品冷凝冷却后送至储罐。该物系属易分离物系,最小回流比较小,故操作回流比取最小回流比的1.8倍。塔釜采用间接蒸汽加热①。 2.精馏塔的物料衡算 2.1.原料液及塔顶、塔顶产品的摩尔分率 甲醇的摩尔质量M A=32.04kg/kmol 水的摩尔质量M B=18.02 kg/kmol x F= 0.46/32.04 0.324 0.46/32.040.54/18.02 = + x D= 0.95/32.04 0.914 0.95/32.040.05/18.02 = + x W= 0.03/32.04 0.0171 0.03/32.040.97/18.02 = + 2.2.原料液及塔顶、塔底产品的平均摩尔质量 M F=0.324*32.04(10.324)*18.0222.56 +-=kg/kmol M D=0.914*32.04(10.914)*18.0230.83 -=kg/kmol M W=0.0171*32.04(10.0171)*18.0218.26 +-=kg/kmol 2.3.物料衡算 原料处理量F= 30000*1000 184.7 24*300*22.56 =kmol/h 总物料衡算184.7=D+W 甲醇物料衡算184.7*0.324=0.914D+0.0171W 联立解得D=63.21 kmol/h W=121.49 kmol/h 3.塔板数的确定 3.1.理论塔板层数N T的求取 3.1.1.由手册查的甲醇-水物系的气液平衡数据
分离苯-甲苯筛板式精馏塔设计[优秀]
食品工程原理课程设计说明书 筛板式精馏塔设计
目录 第一部分概述 一、设计题目 (3) 二、设计任务 (3) 三、设计条件 (3) 四、工艺流程图 (3) 第二部分工艺设计计算 一、设计方案的确定 (4) 二、精馏塔的物料衡算 (4) 1.原料液及塔顶、塔底产品的摩尔分数 (4) 2.原料液及塔顶、塔底产品的平均摩尔质量 (4) 3.物料衡算原料处理量 (4) 三、塔板数的确定 (4) N的求取 (4) 1.理论板层数 T 2.实际板层数的求取 (6) 四、精馏塔的工艺条件及有关物性数据的计算 (6) 1.操作压力计算 (6) 2.操作温度计算 (6) 3.平均摩尔质量计算 (6) ⑴塔顶摩尔质量计算 (6) ⑵进料板平均摩尔质量计算 (6) ⑶提馏段平均摩尔质量 (7) 4.平均密度计算 (7) ⑴气相平均密度计算 (7) ⑵液相平均密度计算 (7) 5.液相平均表面张力计算 (7) ⑴塔顶液相平均表面张力计算 (7) ⑵进料板液相平均表面张力计算 (7) 6.液相平均粘度计算 (8) ⑴塔顶液相平均粘度计算 (8) ⑵进料板液相平均粘度计算 (8) 五、精馏塔的塔体工艺尺寸计算 (8) 1.塔径的计算 (8) 2.精馏塔有效高度计算 (9) 六、塔板主要工艺尺寸的计算 (9) 1.溢流装置计算 (9) l (9) ⑴堰长 W h (9) ⑵溢流堰高度 W
⑶弓形降液管宽度d W 和截面积f A ..........................9 2.塔板布置....................................................................................................9 ⑴塔板的分块.............................................9 ⑵边缘区宽度确定.........................................9 ⑶ 开孔区面积计算........................................9 ⑷筛孔计算及其排列 (10) 七、筛板的流体力学验算 (11) 1.塔板压降....................................................................................................11 ⑴干板阻力c h 计算........................................11 ⑵气体通过液层的阻力L h 计算..............................11 ⑶液体表面张力的阻力 h 计算..............................11 2.液面落差...................................................................................................12 3.液沫夹带...................................................................................................12 4.漏液...........................................................................................................12 5.液泛.. (12) 八、塔板负荷性能图 (13) 1.漏液线.......................................................................................................13 2.液沫夹带线...............................................................................................13 3.液相负荷下限线.......................................................................................14 4.液相负荷上限线.......................................................................................14 5.液泛线.......................................................................................................14 九、设计一览表.. (16) 十、参考文献 (17)
板式精馏塔课程设计
《化工原理》课程设计报告 苯-氯苯分离过程板式精馏塔设计 学院 专业 班级 学号 姓名 合作者 指导教师
化工原理设计任务书 一、设计题目: 苯-氯苯分离过程板式精馏塔设计 二、设计任务 1)进精馏塔的原料液中含氯苯为38%(质量百分比,下同),其余为苯。 2)塔顶馏出液中含氯苯不高于2%。 3)生产能力为日产纯度为99.8%的氯苯Z吨产品。年工作日300天,每天24小时连续运行。(设计任务量为3.5吨/小时) 三、操作条件 1.塔顶压强4kPa(表压); 2.进料热状况,自选; 3.回流比,自选; 4.塔釜加热蒸汽压力0.5MPa; 5.单板压降不大于0.7kPa; 6. 设备型式:自选 7.厂址天津地区 四、设计内容 1.精馏塔的物料衡算; 2.塔板数的确定; 3.精馏塔的工艺条件及有关五行数据的计算; 4.精馏塔的塔体工艺尺寸计算; 5.塔板的主要工艺尺寸计算; 6.塔板的流体力学计算; 7.塔板负荷性能图; 8.精馏塔接管尺寸计算; 9.绘制生产工艺流程图; 10.绘制精馏塔设计条件图; 11.绘制塔板施工图; 12.对设计过程的评述和有关问题的讨论
五、基础数据 1.组分的饱和蒸汽压 i p (mmHg ) 2.组分的液相密度ρ(kg/m 3) 纯组分在任何温度下的密度可由下式计算 苯 t A 187.1912-=ρ 氯苯 t B 111.11127-= ρ 式中的t 为温度,℃。 3.组分的表面张力σ(mN/m ) 双组分混合液体的表面张力m σ可按下式计算: A B B A B A m x x σσσσσ+= (B A x x 、为A 、B 组分的摩尔分率) 4.氯苯的汽化潜热 常压沸点下的汽化潜热为35.3×103kJ/kmol 。 纯组分的汽化潜热与温度的关系可用下式表示: 38 .01212??? ? ??--=t t t t r r c c (氯苯的临界温度:C ?=2.359c t ) 5.其他物性数据可查化工原理附录。