落料拉深复合模具
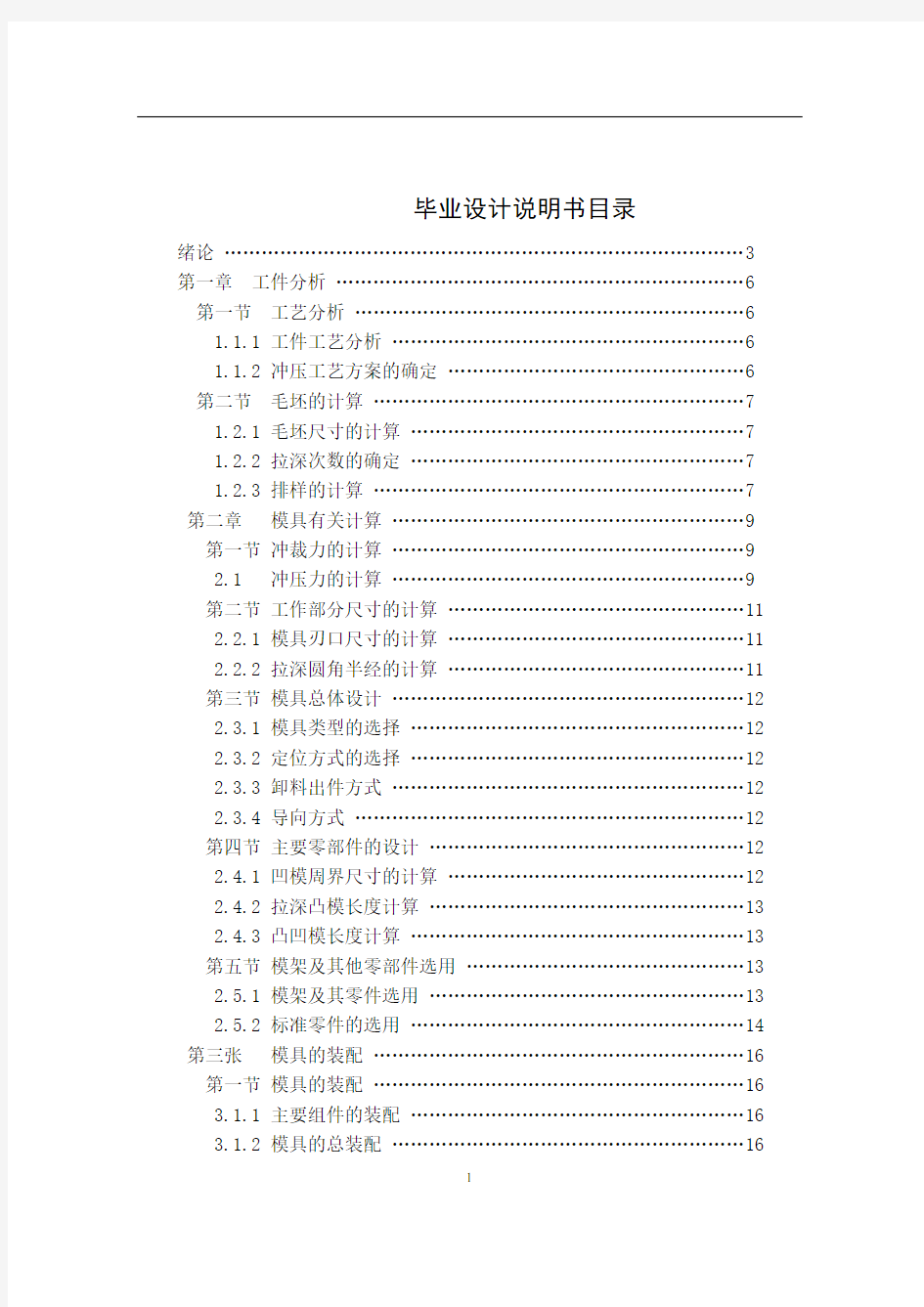

毕业设计说明书目录
绪论 (3)
第一章工件分析 (6)
第一节工艺分析 (6)
1.1.1 工件工艺分析 (6)
1.1.2 冲压工艺方案的确定 (6)
第二节毛坯的计算 (7)
1.2.1 毛坯尺寸的计算 (7)
1.2.2 拉深次数的确定 (7)
1.2.3 排样的计算 (7)
第二章模具有关计算 (9)
第一节冲裁力的计算 (9)
2.1 冲压力的计算 (9)
第二节工作部分尺寸的计算 (11)
2.2.1 模具刃口尺寸的计算 (11)
2.2.2 拉深圆角半经的计算 (11)
第三节模具总体设计 (12)
2.3.1 模具类型的选择 (12)
2.3.2 定位方式的选择 (12)
2.3.3 卸料出件方式 (12)
2.3.4 导向方式 (12)
第四节主要零部件的设计 (12)
2.4.1 凹模周界尺寸的计算 (12)
2.4.2 拉深凸模长度计算 (13)
2.4.3 凸凹模长度计算 (13)
第五节模架及其他零部件选用 (13)
2.5.1 模架及其零件选用 (13)
2.5.2 标准零件的选用 (14)
第三张模具的装配 (16)
第一节模具的装配 (16)
3.1.1 主要组件的装配 (16)
3.1.2 模具的总装配 (16)
3.1.3 装配注意事项 (17)
3.1.4 模具装配技术要求 (18)
第二节模具的调试及工作 (18)
3.2.1 模具的调试 (18)
3.2.2 模具的工作过程 (19)
结论 (20)
致谢 (21)
参考文献 (22)
绪论
第一章工件分析
工件:圆筒
工件如图:材料为10号钢,料厚1.0mm ,制件尺寸精度IT14级,形状简单,尺寸叫小,大批量生产,属普通冲压件。
第一节工艺分析
1.1.1 工件工艺分析
该工件为圆筒件拉深,形状简单,工件的厚度也无严格要求,易于成型。根据尺寸对应关系,可设计一副模具完成落料、拉深。
1.1.2冲压工艺方案的确定
该工件包括落料、拉深两道工序。
方案一:先落料,在拉深,采用单工序模具。
方案二:落料、拉深复合模具。
方案三:拉深——落料级进冲压模具。
方案比较:
方案一中,模具结构简单,但要做到两副模具才能完成,对于大批量生产的工件,采用单工序模具回降低工作效率。方案二中,只需要一副模具,机构比方
案一复杂,但对于结构对称的工件,模具的制造也并不困难,可一次性完成落料、拉深,生产效率高,适于大批量生产。方案三中,采用级进模具,也只需要一副模具,模具结构复杂,而且在送料时较困难,拉深后工件边缘质量不好,综合考虑采用方案二较好。
第二节 毛坯的计算
1.2.1毛坯尺寸的计算
r dr d
h H d D 2
2
56.072.1)(4--?++=
因板料厚度为1mm ,可按板厚中径计算。 d=34mm H=16.5mm r=3.5mm 查表得: mm h 2.1=? 计算得:D=56.20mm
1.2.2 拉深次数的确定
坯料的相对厚度为: t/D=1/56.20X100%=1.779%
根据数据查表,可用压边圈也可不用,但为保险操作,仍需采用压边圈。 总的拉深系数为:
587.020.56/33/===D d m
总
查表,08钢首次拉深系数为0.5mm ,m m 1≥总 所以,可采用一次完成拉深。 拉深件的高度计算: h=H+h ?=16.5+1.2=17.2mm
1.2.3 排样的计算
[1] 冲裁件的面积
A=mm D
2
22
794.24*14.34/20.56==π
[2] 条料宽度的计算
因模具中已设有压边圈,无需侧压装置,则条料的宽度为: B=D+2a
查表:工件间最小料宽 : mm a 8.01= 侧面料搭边: a=1m 则条料的宽度为:B=56.20+2=58.20mm 查表:条料的偏差为0.6mm ,即 2.580
6.0- [3] 步距s 的计算
s=D+mm a 578.020.561=+= [4] 材料的利用率
%74%100*/==Bs A η
第二章 模具有关计算
第一节 冲裁力的计算
2.1 冲压力的计算
2.2.2 拉深圆角半径的计算
[1] 拉深凹模圆角半径的确定:
t d D r A )(8.01
-=
r
A 1
-凹模圆角半径 D-坯料直径
t -料厚 d -凹模内径
1)535.3320.56(8.01
X r
A -==3.8
[2]. 拉深凸模圆角半径的确定:
r r A T 11)0.1~7.0(= 取系数为:0.8
则:r T 1=0.8*3.8=3mm
第三节 模具总体设计
2.3.1 模具类型的选择
分析冲压工艺性,采用复合模具生产效率高,模具结构容易制造,模具类型为落料-拉深复合模。
2.3.2 定位方式的选择
模具中冲压采用条料进给,用两个导料销导料,送进步距采用挡料销。
2.3.3 卸料、出件方式
模具中采用弹性卸料装置,倒装复合模,在拉深完成后,由推杆将工件从凸凹模型腔中推出,用压力机工作台下标准缓冲器提供压边力。
2.3.4 导向方式
为了便于条料从侧面送进,用后侧导柱的导向方式。
第四节主要零部件的设计
2.4.1 凹模周界尺寸的计算
因制件形状简单,制件尺寸较小,只有一个工位,故选用整体式圆形凹模比较合理。
由于本模具为落料、拉深倒装复合模,凹模选取的厚度要考虑到拉深见的深度,以及考虑到拉深凸模的端面要低于落料凹模一定距离,采用标准件厚度选取为28mm,查书《冲压模具设计与制造》中凹模尺寸计算公式:
W=1.2H(H-凹模的厚度)
则W=33.6mm
落料凹模的外形直径为:
d=2W+落料凹模刃口尺寸=60+56.20=123.4mm
取标准为:125mm
模具的装配
模具的装配就是根据模具的结构特点和技术条件,以一定的装配顺序和方法,将符合图样技术要求的零件,经协调加工组装成满足使用要求的模具。在装配的过程中,即要保证配合零件的配合精度,又要保证零件之间的位置精度,对于具有相对运动的零部件,还必须保证他们之间的运动精度。因此,模具装配是最后实现冲模设计和冲压工艺意图的过程,是模具制造中的关键工序。模具装配的质量直接影响制件的冲压质量、模具的使用与维护和模具的寿命。
第一节模具的装配
3.1.1 主要组件的装配
[1] 模柄的装配
模柄与上模是压入式配合,在安装垫板前先要装模柄,模柄与上模座的配合要求为:H7/n6 。将模柄压如上模座,最后将模柄的底座磨平,检查其平行度和垂直度。
[2] 凸凹模的装配
凸凹模与固定板的配合要求是H7/n6 ,装配时,先在压力机上将凸凹模压入固定板内,检查其垂直度,然后和固定板的上平面一起磨平。
[3] 拉深凸模的装配
凸模和下固定板的装配也为压入配合,配合要求也为H7/n6,在压力机上将凸模压入固定板,检查凸模垂直度,然后将固定板的下平面与凸模尾部一起磨平。
3.1.2 模具的总装配
为了便于装配,首先装上模,再装下模。
[1] 上模的装配
A:将上模座倒置,然后把垫板、推杆、推件块、压入固定板的凸凹模一起安放在上模座上,用推杆将推件块撑起,以防止推件块在凸凹模内腔中倾斜。
再把卸料板套在凸凹模上,在卸料板和上模座之间垫平行垫块,用平行夹板夹紧它们,根据卸料板上的螺纹孔和固定板中的螺纹孔、销钉孔在上模座上投窝,将垫板、固定板、卸料板拆下,最后在上模座上钻螺钉孔和销钉孔,装入销钉,拧紧螺钉。
B:上模间隙,安装弹簧。
[2] 下模的装配
A:边圈套在已压入下模垫板的拉深凸模上。保证与拉深凸模合理的间隙值。
B : 料凹模上按尺寸要求加工挡料销孔、导料销孔,并根据配合精度装配挡料销、
导料销。
C: 在下模座上找正位置,将下模垫板、固定板、落料凹模一起装于下模座上。
对下模座上投窝,加工螺纹孔、销钉孔,并用螺钉、销钉将他们连接成一
个整体。
[3] 上、下模装配在一起,安装其他的零件。
[4] 对模具进行试冲、调整。
3.1.3 装配时注意事项
[1] 推件块
推件块采用刚性装置,装与上模,它是在冲压结束后上模回程时,利用压力机滑块上的打料杆,撞击上模内的打杆与推件块,将拉深凹模内的工件推出,推力大,工作可靠。由于推件块的外形简单,它与拉深凹模采用间隙配合H8/f8。推件块在自由状态下要高出凸凹模刃口面0.2~0.5mm。[2] 压边圈
压边圈在模具中起压料和顶出制件的作用,出件力不达,但出件平稳。
压边圈与落料凹模配合采用间隙配合H8/f8,与拉深凸模之间要留单边间隙
为0.1~0.2mm。
[3] 导料销的安装:
导料销是对条料导向,保证条料正确的送进方向。由于条料是从右往左边送进,导料销要安放在模具的后侧。
[4] 固定板
上模固定板和下模固定板分别与凸凹模、凸模按一定位置压入固定,作为一个整体安装在上、下模座上,平面尺寸与凹模、卸料板外形相同。固定板与凸凹模、凸模均采用过渡配合H7/m6,在压入一起后,凸模和凸凹模的下端面要与固定板一起磨平。固定板基面和压装配合面的表面粗糙度为
R a1.6~0.8mμ,另一非基准面可适当降低要求。
[5] 垫板
垫板的作用是直接承受和扩散凸模传递的压力,以降低模座所受的单位压力,防止模座被局部压陷。垫板外形和固定板相同,其厚度一般取3~10mm。
垫板的材料为45钢,淬火硬度为43~48HRC。垫板上、下表面应磨平,表面粗糙度为R a1.6~0.8mμ,以保证平行度要求。为了便于模具装配,垫板上销钉通过孔直径可比销钉直径大0.3~0.5mm。
[6] 该模具采用了弹性卸料板,在装配时,要保证它和凸模之间的单边间隙
(0.1mm~0.2mm), 卸料板在自由状态下应高出凸凹模刃口面0.5~1.0mm.,以便利于卸料。
[7] 模具装配后要保证间隙合理均匀,落料凹模刃口面要高出拉深凸模工作
端面3mm,保证先落料后拉深。
3.1.4 模具装配技术要求
[1] .装配时要保证凸凹模间隙均匀一致.配合间隙符合设计要求,不允许采用使
凸、凹模变形的方法修正间隙
[2] 推料、卸料机构必须灵活,卸料板和推件块在冲模开启状态时,一般应突出
凸、凹模表面0.5~1.0mm.
[3] 落料、冲孔的凹模刃口高度,按设计要求制造。
[4] 冲模所有活动部分应平稳灵活,各紧固用的螺钉、销钉不得松动,并保证螺
钉和销钉的端面不突出上下模表面。
[5] 个卸料螺钉沉孔深度保证一致,卸料螺钉、顶杆的长度应保证一致。
[6] 拉深凸模的垂直度必须在凸凹模间隙允许的范围内。
[7] 冲模的装配必须符合模具装配图、明细表及技术条件的规定。
第二节模具的调试及工作
3.2.1 模具的调试
模具按图样技术要求加工与装配后,必须在符合实际生产条件的环境中进行试冲压生产。通过试冲可以发现模具设计制造中的缺陷,找出产生原因,对模具进行适当的调整和修理后再进行试冲,直到模具能正常工作。
模具调试的要点:
[1] . 模具闭合高度的调试。模具应与冲压设备配合好,保证模具应有的闭合
高度和开启度。
[2] . 导向机构的调试。导柱、导套要有好的配合精度,保证模具运动平稳、
可靠。
[3] 凸、凹模刃口的调试。冲裁刃口锋利,间隙均匀。
[4] . 定位装置的调试。定位要准确、可靠。
[5] . 卸料及出件装置的调试。卸料及出件要畅通,不能有卡住的现象。
3.2.2 模具的工作过程
模具上模部分通过模柄安装在压力机滑块上,下模部分通过螺栓、压板安装在压力机的工作台面上。模具的下模部分设有挡料销和导料销,用于条料送进时定位,控制送料步距离。条料送给,上模随压力机的滑块一起下行,先完成落料,在拉深。完成一次冲压后,上模随压力机的滑块一起上行,压边圈在顶杆的推动作用下,将工件从拉深凸模上顶出,使工件随凸凹模一起上行,卸料板将卡在凸凹模上的废料卸下,凸凹模上行一定距离,靠推件块的作用将工件从拉深凹模腔中推出。