车身配件的随机振动疲劳分析

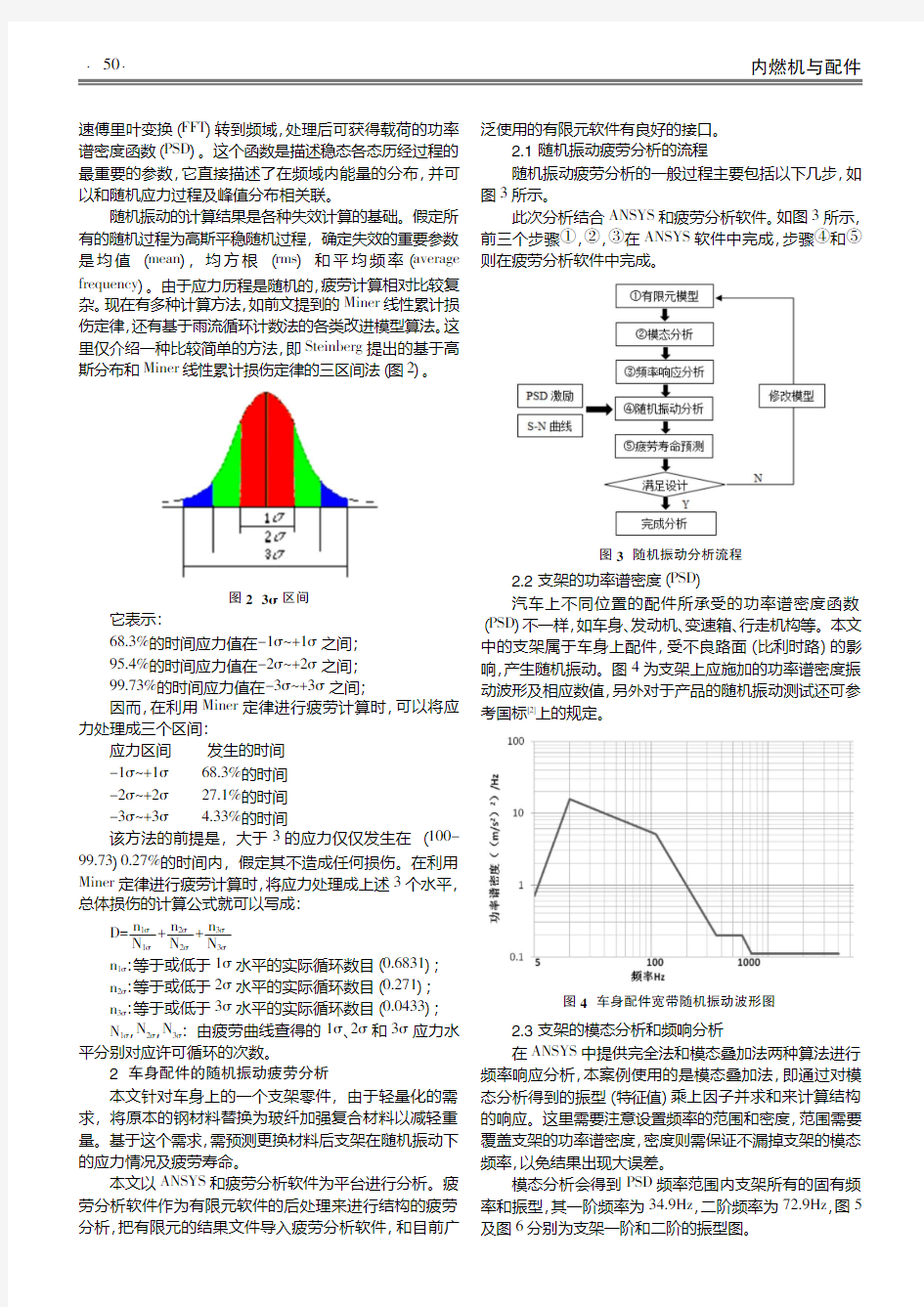
D=S1N
1+S2N
2 +…+S n N
n
=n
i=1∑
S i N
i
当D=1时,表示疲劳寿命已耗尽,预测发生了疲劳破坏。实验数据表明,各种情况下,D值相当分散,并非都等。况且疲劳损伤能否像上述线性理论中设想的简单叠加,也需要进行深入的研究。这是因为在前面的应力循环会对后继的应力循环带来影响,同时后继应力循环也会对前面已经形成的损伤带来进一步的影响。考虑到该假设的不精确性和缺点,有时也假设积累损伤D为小于1
数时也会发生疲劳破坏。当然,损伤的形成过程相当复杂,而线性积累损伤理论由于计算简单,概念直观,所以在工程中广泛应用于疲劳寿命计算。这里只简单提供积累损伤理论,还有其他计算理论,不再陈述。
1.3随机振动的分析方法
图1S-N曲线
关于汽车振动的分析
关于汽车的振动的分析 汽车振动系统是由多个子系统组成的具有质量、弹簧和阻尼的复杂的振动系统。汽车振动源主要有:路面和非路面对悬架的作用、发动机运动件的不平衡旋转和往复运动、曲轴的变动气体负荷、气门组惯性力和弹性力、变速器啮合齿轮副的负荷作用、传动轴等速万向节的变动力矩等。 在汽车工程中,多数振动是连续扰动力,而其他一些则是汽车承受的冲击力和短时间的瞬态振动力。振动又可分为周期性的和随机性的,发动机旋转质量的不平衡转动是周期振动的典型例子,而随机振动主要是由路面不平引起的。所有质量--弹性系统都有自己的固有频率,如果作用于系统的干扰频率接近振动系统的固有频率,就会发生共振现象。因此即使自身具有抗干扰能力的系统,装配到汽车上时仍有可能产生振动问题,这就要求在设计阶段准确建立系统模型及运动方程,分析自由振动特性和受迫振动响应,研究控制振动的方法。 汽车振动按照频率范围可分为: 1、影响行驶平顺性的低频振动:它产生的主要振源由于路面不平度激励使得汽车非悬挂质量共振和发动机低频刚体振动,从而引起悬架上过大的振动和人体座椅系统的共振造成人体的不舒适,其敏感频率主要在1-8Hz(最新的研究表明:当考虑人体不同方向的响应时可到16Hz)。对于乘员其评价指标一般是:针对载货汽车的疲劳降低工效界限和针对乘用汽车的疲劳降低舒适界限,或直接采用人体加权加速度均方根值进行评价;对于货物其评价指标是:车箱典型部位的均方根加速度。由于该指标于人体生理主观反映密切相关,因此试验和评价往往采用测试和主观评价相结
合。 2、车身结构振动和低频噪声:大的车身结构振动,不仅引起自身结构的疲劳损坏,而且更是车内低频结构辐射噪声源。其频率主要分布在20—80Hz 的频带内。由两方面引起:(1)激励源;主要有:道路激励、动力传动系统尤其是动力不平衡和燃烧所产生的各阶激励、空气动力激励;(2)车身结构和主要激励源系统的结构动力特性匹配不合理引起的路径传递放大。当前对于低频结构振动和噪声分析研究的方法有:计算预测分析,(1)基于有限元方法通过建立结构动力学模型取得结构固有振动模态参数对结构动力学特性进行评价,通过试验载荷分析得到振动激励并结合结构动力学模型计算振动响应;(2)基于有限元和边界元的系统声学特性计算和声响应计算。试验分析:(1)各种结构振动和声学系统的导纳测量和模态分析;(2)基于实际运行响应的工作振型分析;(3)基于机械和声学导纳测量的声学寄予率分析; 3、各种操纵机构的振动:操纵机构的振动主要是因为其安装吊挂刚度偏低或自身结构动力特性不当或车身振动过大而产生,它不仅容易使驾驶者疲劳严重时可能使操纵失控。对于这些振动各企业都有相应得评价和限值规定。最为典型的是方向盘(线性)振动(转向管柱振动),其产生的主要原因是方向盘及管柱安装总成与车身振动或其它激励源发生共振;另一重要的振动现象是行驶过程中的方向盘旋转振动(即:方向盘及转向轮摆振)。其产生的原因是:行驶过程中转向轮的跳动与自身的转动而产生的陀螺效应引起转向轮的波动并被转向结构放大从而引起方向盘旋转振动。 4、空气声:车内空气声是由于隔声吸声措施不当从而使得动力传动
疲劳分析方法
疲劳寿命分析方法 摘要:本文简单介绍了在结构件疲劳寿命分析方法方面国内外的发展状况,重点讲解了结构件寿命疲劳分析方法中的名义应力法、局部应力应变法、应力应变场强度法四大方法的估算原理。 疲劳是一个既古老又年轻的研究分支,自Wohler将疲劳纳入科学研究的范畴至今,疲劳研究仍有方兴未艾之势,材料疲劳的真正机理与对其的科学描述尚未得到很好的解决。疲劳寿命分析方法是疲分研究的主要内容之一,从疲劳研究史可以看到疲劳寿命分析方法的研究伴随着整个历史。 金属疲劳的最初研究是一位德国矿业工程帅风W.A.J.A1bert在1829年前后完成的。他对用铁制作的矿山升降机链条进行了反复加载试验,以校验其可靠性。1843年,英国铁路工程师W.J.M.Rankine对疲劳断裂的不同特征有了认识,并注意到机器部件存在应力集中的危险性。1852年-1869年期间,Wohler对疲劳破坏进行了系统的研究。他发现由钢制作的车轴在循环载荷作用下,其强度人大低于它们的静载强度,提出利用S-N 曲线来描述疲劳行为的方法,并是提出了疲劳“耐久极限”这个概念。1874年,德国工程师H.Gerber开始研究疲劳设计方法,提出了考虑平均应力影响的疲劳寿命计算方法。Goodman讨论了类似的问题。1910年,O.H.Basquin提出了描述金属S-N曲线的经验规律,指出:应力对疲劳循环数的双对数图在很大的应力范围内表现为线性关系。Bairstow通过多级循环试验和测量滞后回线,给出了有关形变滞后的研究结果,并指出形变滞后与疲劳破坏的关系。1929年B.P.Haigh研究缺口敏感性。1937年H.Neuber指出缺口根部区域内的平均应力比峰值应力更能代表受载的严重程度。1945年M.A.Miner 在J.V.Palmgren工作的基础上提出疲劳线性累积损伤理论。L.F.Coffin和S.S.Manson各自独立提出了塑性应变幅和疲劳寿命之间的经验关系,即Coffin—Manson公式,随后形成了局部应力应变法。 中国在疲劳寿命的分析方面起步比较晚,但也取得了一些成果。浙江大学的彭禹,郝志勇针对运动机构部件多轴疲劳载荷历程提取以及在真实工作环境下的疲劳寿命等问题,以发动机曲轴部件为例,提出了一种以有限元方法,动力学仿真分析以及疲劳分
利用ANSYS随机振动分析功能实现随机疲劳分析.
利用ANSYS随机振动分析功能实现随机疲劳分析 ANSYS随机振动分析功能可以获得结构随机振动响 应过程的各种统计参数(如:均值、均方根和平均频率等),根据各种随机疲劳寿命预测理论就可以成功地预测结构 的随机疲劳寿命。本文介绍了ANSYS随机振动分析功能,以及利用该功能,按照Steinberg提出的基于高斯分布和Miner线性累计损伤定律的三区间法进行ANSYS随机疲劳计算的具体过程。 1.随机疲劳现象普遍存在 在工程应用中,汽车、飞行器、船舶以及其它各种机械或零部件,大多是在随机载荷作用下工作,当它们承受的应力水平较高,工作达到一定时间后,经常会突然发生随机疲劳破坏,往往造成灾难性的后果。因此,预测结构或零部件的随机疲劳寿命是非常有必要的。 2.ANSYS随机振动分析功能介绍 ANSYS随机振动分析功能十分强大,主要表现在以下方面: 1.具有位移、速度、加速度、力和压力等PSD类型; 2.能够考虑a阻尼、 阻尼、恒定阻尼比和频率相关阻 尼比;
3.能够定义基础和节点PSD激励; 4.能够考虑多个PSD激励之间的相关程度:共谱值、二 次谱值、空间关系和波传播关系等; 5.能够得到位移、应力、应变和力的三种结果数据: 1σ 位移解,1σ速度解和1σ加速度解; 3.利用ANSYS随机振动分析功能进行疲劳分析的一般原 理 在工程界,疲劳计算广泛采用名义应力法,即以S-N 曲线为依据进行寿命估算的方法,可以直接得到总寿命。下面围绕该方法举例说明ANSYS随机疲劳分析的一般原理。 当应力历程是随机过程时,疲劳计算相对比较复杂。但已经有许多种分析方法,这里仅介绍一种比较简单的方法,即Steinberg提出的基于高斯分布和Miner线性累计损伤定律的三区间法(应力区间如图1所示): 应力区间 发生的时 间 -1σ ~+1σ68.3%的时间 -2σ ~+2σ27.1%的时间
某重型载重车辆振动分析和控制_李顶根
某重型载重车辆振动分析和控制X 李顶根 何保华 (华中科技大学能源与动力工程学院 武汉,430074) (华中科技大学水电与数字工程学院 武汉,430074) 摘要 为了有效消除某重型载重车的驾驶室水平晃动,对车架和驾驶室悬置进行了综合有限元模态分析,分析了载重车驾驶室和车架的前6阶固有频率及模态振型特征。结合试验测试的路面激振信号分析,对车架有限元模型进行了动力优化。实际结果表明,驾驶室侧向弯曲模态固有频率与路面随机激励频率错开3~4Hz后,减小了驾驶室的横向振动,改善了该型载重车的平顺性。 关键词 重型载重车 横向振动 模态分析 动力优化 中图分类号 U467 引 言 汽车的振动和噪声严重影响汽车的操纵稳定性和乘坐舒适性。某重型载重车在水泥路面行驶时,其驾驶室在水平面内的筛状晃动比较严重。以前的研究表明,汽车行驶时,当动载荷很大以及有路面随机振动载荷作用时,就有可能导致车架产生共振和动态失效[1-2]。由于该类载重车为自卸式载货车,因此分析其车架和驾驶室的综合动态特性,并对车架进行动力优化,以控制其驾驶室的横向振动现象。 1 计算模型的建立 该载重车的车架为复合式结构,分为主、副车架。主车架由左右纵梁和6根横梁组成,全长5.684 m,最大宽度2.01m,轴距3.5m。由于整个汽车车架的结构复杂,在不影响车架动力学特性的前提下,建立模型时根据具体结构情况进行了以下的简化[3]: (1)略去纵横梁上承受载荷比较小、对结构变形影响很小的部件; (2)将一些节点的自由度进行耦合,如将纵、横梁支座与大量的螺栓连接处的自由度进行耦合; (3)省去纵横梁上的一些无关紧要的装配孔; (4)把发动机、变速箱、车箱等部件总成简化为其支点上的集中载荷; (5)不考虑铆钉的预应力及焊接应力等。 与车架相连的悬架系统采用弹性边界单元模拟,边界单元刚度选用钢板弹簧悬架系统的刚度,采用四边形壳单元为基本单元进行有限元网格划分,共计50312个节点和43318个有限单元。 根据自卸式重型载重车的结构,考虑驾驶室悬置及车架的综合模态分析。采用四边形壳单元为基本单元进行有限元网格划分,局部采用六面体单元。共计83962个节点和74304个有限单元,若干质量单元、弹簧单元和连接单元。 2 驾驶室悬置和车架的综合结构模态分析 根据模态分析理论,一般的工程结构只需计算前几阶较低的固有频率和振型,因为低阶振动对结构的动力影响最大。本文结合车架的实际结构及载荷工况,运用大型有限元分析软件ANSYS模态分析中的Lanczos分析方法[4-6],将计算分析车架结构的前6阶模态。采用Lanczos算法,使用稀疏矩阵来求解广义特征值,即通过一组向量来实现Lanczo s 递归。此法精确且速度快,在工程中常用来提取模型具有对称特征值的多阶模态,而且其在有限元模型中允许有质量较差的实体与板壳单元,但其不足之处是需要较多的内存空间。 车架的弯曲及扭转振动是其结构动态特性的主要表现形式。考虑到载货汽车的运行速度与路面条件,选取0~100Hz作为其计算频段。前6阶模态分析的频率及振型特征如表1和图1~图3所示。 表1 车架和驾驶室悬置的综合模态计算值 序号f/Hz振型 1 9.68扭转模态 215.03纵向弯曲模态 321.40侧向弯曲模态 424.80纵弯局部模态 526.32扭转局部模态 629.60侧弯局部模态 第28卷第2期2008年6月 振动、测试与诊断 Jo urnal o f Vibration,M easurement&Diag nosis V ol.28N o.2 Jun.2008 X收稿日期:2007-11-30;修改稿收到日期:2008-01-24。
基于实测载荷谱的白车身疲劳寿命计算
基于实测载荷谱的白车身疲劳寿命计算 朱涛1 林晓斌2 1上海山外山机电工程科技有限公司 2英国恩科(nCode)国际有限公司上海代表处
基于实测载荷谱的白车身疲劳寿命计算 朱涛1 林晓斌2 1上海山外山机电工程科技有限公司 2英国恩科(nCode)国际有限公司上海代表处 摘要:汽车白车身疲劳分析由于缺乏真实载荷谱的输入而显得没有说服力,计算分析的结果往往与试车场或用户使用时发生的失效没有关联,这样导致了虚拟疲劳分析的强大作用无法发挥。本文通过六分力轮测试系统实测了某型乘用车在试车场的载荷谱数据,以此作为输入,并综合了多种CAE手段,包括有限元网格划分、有限元分析、多体动力学分析和疲劳分析,对该乘用车的白车身在实测载荷谱作用下的疲劳寿命分布进行了计算分析,获得了有价值的结果。同时给出了更符合真实工况的试验与虚拟相结合的白车身一体化疲劳分析流程。 关键词:白车身,虚拟疲劳分析,道路载荷谱,有限元网格划分,有限元分析,多 体动力学分析 1 前言 汽车结构疲劳的话题在当前各大整车制造企业越来越受到重视,几乎每种新开发的车型都需要考察其疲劳耐久性能。以前传统的方法,汽车企业对于新车型疲劳寿命的评估都是利用实车在各道路试车场进行路试[1],该方式虽然是最直接且最准确的,但测试时间却十分冗长且耗费人力与经费甚巨,即使发现了问题往往也很难去修改。近年来计算机软硬件的迅速发展,计算机辅助工程(CAE)分析技术在静态、碰撞、振动噪音等领域均有了相当不错的应用成果,但疲劳耐久性分析需要综合有限元应力分析和动力学载荷分析等专业技术,仍需花费非常大的计算量,且计算的准确性由于没有真实的道路载荷谱(RLD)作为计算输入而缺乏说服力。 本文针对上述问题,基于在国内汽车企业已经开始成熟运用的六分力轮测试技术实测获得的某乘用车在试车场的道路载荷谱数据[2],以此作为输入,驱动建立好的整车多刚体动力学仿真模型,获取作用在白车身各连接点上的载荷谱,同时对白车身进行有限元应力场分析。综合上述结果,调用相应的疲劳损伤模型对白车身的疲劳寿命进行了计算,从而建立起一套较为可行的更符合真实工况的车辆疲劳寿命分析技术流程。
振动分析所研究的内容
机械振动理论及其应用作业——振动分析研究的内容 学号: 专业:机械工程 学生姓名: 2013年11月24日
第一节机械振动的基本概念 所谓振动,就是物体或某种状态随时间作往复变化的现象。振动包括机械振动与非机械振动。例如,钟摆的来回摆动,房屋由于风力、地震或机械设备引起的振动,桥梁由于车辆通过引起的振动等,这一类振动属于机械振动;另一类振动属于非机械运动的振动现象,例如声波、光波、电磁波等。 机械振动所研究的对象是机械或结构,在理论分析中要将实际的机械或结构抽象为力学模型,即形成一个力学模型。可以产生机械振动的力学模型,称为振动系统。一般来说,任何具有弹性和惯性的力学系统均可能产生机械振动。 振动系统发生振动的原因是由于外界对系统运动状态的影响,即外界对系统的激励或作用。如果外界对某一个系统的作用使得该系统处于静止状态,此时系统的几何位置称为系统的静平衡位置。依据系统势能在静平衡位置附近的性质,系统的静平衡位置可以分为稳定平衡、不稳定平衡和随遇平衡等几种状况。机械振动中的平衡位置是系统的稳定平衡位置。系统在振动时的位移通常是比较小的,因为实际结构的变形时比较小的。 对于工程实际中的结构振动问题,人们关心振动会不会使结构的位移、速度、加速度等物理量过大,因为位移过大可能引起结构各个部件之间的相互干涉。比如汽车的轮轴与大梁会因为剧烈振动而频繁碰撞,造成大梁过早损坏,并危及行车安全。为了避免振动危害,甚至利用振动进行工作,我们应了解结构振动的规律,并在实际工作中应用这些规律。 第二节振动的分类 机械振动可根据不同的特征加以分类。 1、按振动的输入特性分 自由振动系统受到初始激励作用后,仅靠其本身的弹性恢复力自由地振动,其振动的特性仅决定于系统本身的物理特性(质量m、刚度k)。 受迫振动又称强迫振动,系统受到外界持续的激励作用而被迫地产生振动,其振动特性除决定于系统本身的特性外,还决定于激励的特性。 自激振动有的系统由于具有非振荡性能源或反馈特性,从而产生一种稳定持续的振动。 2、按振动的周期特性分 周期振动振动系统的某些参量(如位移、速度、加速度等)在相等的时间间隔内作往复运动。 非周期振动振动系统的参量变化没有固定的时间间隔,即没有一定的周期。3、按振动的输出特性分 简谐振动可以用简单正弦函数或余弦函数表述其运动规律的运动。 非简谐振动不可以直接用简单正弦函数或余弦函数表述其运动规律的运动。 随机振动不能用简单函数或简单函数的组合来表述其运动规律,而只能用统计的方法来研究其规律的非周期性振动。 4、按振动系统的结构参数特性分 线性振动振动系统的惯性力、阻尼力、弹性恢复力分别与加速度、速度、位移成线性关系,系统中质量、阻尼和刚度均为常数,该系统的振动可以用常系数
整车-20_车身疲劳分析规范V1.0版
车身疲劳分析规范编号:LP-RD-RF-0020 文件密级:机密 车身疲劳分析规范 V1.0 编制: 日期: 编制日期审核/会签日期批准日期
车身疲劳分析规范 修订页 编制/修订原因说明:首次编制 原章节号现章节号修订内容说明备注 编制/修订部门/人 参加评审部门/人 修订记录: 版本号提出部门/人修订人审核人批准人实施日期备注
目录 1 简介 (2) 1.1 分析背景和目的 (2) 1.2 软硬件需求 (2) 1.3 分析数据参数需求 (2) 2 模型前处理 (2) 2.1 模型处理 (2) 2.2 约束及加载方式 (3) 3 有限元分析步骤 (3) 3.1 Nastran 静力分析模块 (3) 3.2 NCODE DesignLife 疲劳分析模块 (4) 4 分析结果后处理 (10) 5 结果评价 (11)
车身疲劳分析规范 1 简介 1.1 分析背景和目的 车身在路试过程中及售后反馈中80%以上的开裂问题为疲劳破坏,车身的疲劳性能是车身质量的重要体现,有必要对车身进行疲劳分析。目前比较通用的疲劳分析方法是准静态法。 1.2 软硬件需求 软件 前处理HyperMesh – Nastran模块 求解器Nastran Solution 101,nCode DesignLife 后处理HyperView 硬件 前、后处理:HP或DELL工作站; 求解:HP服务器、HP或DELL工作站。 1.3 分析数据参数需求 所需模型为简化的TB模型,(白车身及各质量点配重) 2 模型前处理 2.1 模型处理 1)导入简化的TB模型,详细建模细则参考《CAE分析共用模型建模指南》,所有搭载在白车身上的零件均需配重; 2)将各接附点重新编号,编号细则参考《整车疲劳分析连接点编号规范》; 图2.1 简化的TB模型
客车车身骨架准静态疲劳强度分析.
第9期 2010年9月 文章编号:1001-3997(2010)09-0099-03 机械设计与制造 MachineryDesign&Manufacture 99 客车车身骨架准静态疲劳强度分析* 朱健苏小平陈本军 )(南京工业大学机械与动力工程学院,南京210009 Pseudo-staticfatiguestrengthanalysisofbusbodyframework ZHUJian,SUXiao-ping,CHENBen-jun (SchoolofMechanicalandPowerEngineering,NanjingUniversityofTechnology,Nanjing210009,China) 【摘要】运用有限元方法建立了某轻型客车车架骨架的有限元模型,在确定载荷的简化和施加方 法后,进行了该车身骨架在满载弯曲工况下的有限元仿真,以此对其进一步的疲劳分析。为该车车身骨架的优化设计和进一步研究提供了理论依据。 关键词:车身骨架;有限元;疲劳分析 【Abstract】Finiteelementmodelingofthebusframeworkisestablishedbyusingfiniteelementmeth-ods.Whenthesimplifiedloadandloadwayexertingontheframeworkareensured,thefiniteelementsimula-tionofbusframeworkisexecutedunderfullyloadedbendingcondition.Andthenfurtherfatigu eanalysisfinishes.Theseresultsprovidetheoreticalbasisforoptimizationandfurtherstudyoft hebusframework. Keywords:Busframework;Finiteelementanalysis;Fatigueanalysis 1引言 车身骨架是客车的主要承载结构,车身骨架的强度、刚度及安全性、操作稳定性等疲劳性能都直接影响着客车的使用寿命、 基本性能。本文运用通用有限元分析软件对某客车车身进行了准 *来稿日期:2009-11-06 弦弧公差:叶盆、叶背为1;进布点方法生成,选取U=V=0.5的截面, ********************************************* 的问题,提高了系统检测的安全性。
车辆疲劳耐久性分析及其优化技术研究_赵成刚
Science and Technology & Innovation ┃科技与创新 ?17? 文章编号:2095-6835(2015)06-0017-02 车辆疲劳耐久性分析及其优化技术研究 赵成刚1,屈 凡2 (1.中国汽车技术研究中心汽车工程研究院,天津 300300; 2.天津一汽夏利汽车股份有限公司产品开发中心,天津 300300) 摘 要:车辆在人们的生活、生产中占据的地位日益重要,其在运行过程中会受到各种因素的影响,进而降低了其使用效率和服务年限,因此,必须做好车辆零部件的维护管理工作。就车辆运行的实际情况看,大部分关键零部件的失效都是因疲劳使用而导致的,疲劳耐久性是衡量车辆产品性能的主要指标之一,在很大程度上代表了车辆的安全性、经济性和可靠性现状。对车辆的耐久性进行了分析,并提出了相应的优化措施。 关键词:疲劳耐久性;优化措施;循环荷载;EIFS 分布 中图分类号:U467 文献标识码:A DOI :10.15913/https://www.360docs.net/doc/ee3306019.html,ki.kjycx.2015.06.017 现代车辆的结构逐渐向高速化和载重化的方向发展,为了保证车辆运行的安全性和稳定性,就要对车辆结构和各零部件有更为严格的要求。疲劳耐久性是衡量车辆零部件和结构性能的主要指标之一,可直接反映车辆的运行状态。但就车辆疲劳耐久性研究的现状来看,还存在一定的不足。因此,为了提高对车辆疲劳耐久性研究的效果,需要对现存的不足进行分析,并选择有效的优化措施,争取不断提高车辆的运行效率。 1 车辆耐久性疲劳分析 耐久性即产品在规定使用和维修的条件下,达到极限状态前完成规定功能的能力,从本质上看,即产品在达到服务年限前,可维持正常状态的时间。对于车辆而言,经常会将汽车或零部件可以行驶一定里程而不发生故障作为衡量车辆耐久性的重要指标。但在车辆长时间运行的过程中,各零部件和构件会受到循环荷载的影响,造成结构部分发生永久性结构变化,并在多次循环后形成裂纹或断裂,这种情况称为耐久性疲劳。一旦车辆结构或零部件出现耐久性疲劳,则直接影响车辆运行的稳定性和安全性。对于车辆的耐久性疲劳而言,其产生的主要原因是循环荷载作用,与疲劳损坏还有一定的距离,且一旦发生疲劳断裂,则会导致车辆结构产生宏观塑性变形。 2 车辆耐久性分析方法 2.1 分析对象 车辆耐久性分析的对象为疲劳寿命与强度有重要联系的重要零部件,并基于结构损伤度和可靠度进行详细分析,最终判断其使用寿命。在对车辆进行耐久性分析时,可将整个车辆机械结构或一部分作为研究对象,比如圆角、紧固孔和焊接件等,尤其是应力水平高且应力水平集中的部位。 2.2 材料参数 材料参数的分析对象包括断裂韧性、EIFS 分布和表面粗糙系数等。在研究时,基本上以概率断裂力学为基础,并通过试验的手段得到相应数据。其中,对于普通材料而言,可直接在相应的数据库中搜寻相应的参数信息,比如尺寸系数、断裂韧性和表面粗糙度系数等。 2.3 使用期断裂纹扩展控制曲线 对于给定应力区,随着时间t 的变化,对细节描述的当量缺陷尺寸也会发生变化,且车辆的应力区不同,裂纹的扩展率也不同。在对车辆耐久性进行分析时,为了提高预测裂纹超越数概率的可靠性,可以结合使用期裂纹扩展控制曲线与EIFS 分布,导出EIFS 控制曲线所用的裂纹扩展方式形式一致,则使用期裂纹扩展率为: d a /dN =Q i a . (1) 式(1)中:a 为裂纹长度;N 为应力循环次数;Q i a 为使用期裂纹扩展率。 控制曲线为: y Ti (t )=a r exp (-Q i t ). (2) 式(2)中:y Ti 为当量初始缺陷尺寸;a r 为试验常数;Q i 为裂纹扩展参数。 2.4 裂纹超越数 给定应力区i 裂纹超越数即在指定时间t 内该应力区i 结构细节群中裂纹尺寸超过a r 的细节数量,用N (i ,t )表示,并作为一个离散型随机变量,且会随着时间t 的变化而变化。假设应力区每个细节相对小裂纹尺寸扩展相互独立,则每个细节在 时间t 时,裂纹尺寸可达到a r 的概率为p (i ,t ) 。如果确定应力区i 中所含细节数为N i ,则在时间t 时的裂纹尺寸超过a r 的细节数为N ’(i ,t ),服从参数为N i 与p (i ,t )二项式分布,则平均裂纹超越数为: N ’(i ,t )=N i p (i ,t ). (3) 式(3)中:N ’(i ,t )为时间t 内裂纹尺寸超过a r 的细节数;N i p (i ,t )为平均裂纹超越数。 标准差为: σN (i ,t )={N i p (i ,t ) [1-p (i ,t )]}1/2. (4) 在对车辆耐久性进行分析时,则其结构指定细节群会包含多个应力区,可用L (t )表示结构细节群中裂纹尺寸超过a r 的细节数量,且会随着时间t 的变化而变化。如果每个应力区的细节数N 都比较大时,N (i ,t )所对应的二项式分布依据中心极限定理趋近于数学期望N ’(i ,t )和方差σN 2(i ,t )正态分布,则近似有N (i ,t )~N [N ’(i ,t ),σN 2(i ,t )],则细节群裂纹超越数为: ∑==m i t i N t L 1) ,()(. (5) 式(5)中:L (t )为正态变量。 则细节群平均裂纹超越L t ()和标准差σL (i )表示为: 1m i t N t ==∑,). (6) 12 2 1 []m i i i t σσ==∑L N ()(,). (7) 3 基于CAE 技术的车辆疲劳耐久性分析 3.1 建立多体动力学模型 建立多体动力学模型时,应利用整车和零部件参数建立总成系统,以完成运动学个动力学虚拟实验,主要包括汽车操纵的稳定性、安全性和平顺性等性能的精确模拟和计算。整个ADAMS/CAR 建模过程为自下而上,逐次完成各个模板的建立,再由相应的模板生成子系统,最终由每个子系统组装成整个车的模型。其中,子系统是以模板为基础建立的,由多个零件组合而成,主要包括设计参数、模板文件和引用属性文件等多方面的说明。整车建模需要对部分零部件进行简化处理,比如将车身看作为刚体,利用车身质心位置处的质量点建模。 (下转第20页)
细解Ansys疲劳寿命分析
细解Ansys疲劳寿命分析 2013-08-29 17:16 by:有限元来源:广州有道有限元 ANSYS Workbench 疲劳分析 本章将介绍疲劳模块拓展功能的使用: –使用者要先学习第4章线性静态结构分析. ?在这部分中将包括以下内容: –疲劳概述 –恒定振幅下的通用疲劳程序,比例载荷情况 –变振幅下的疲劳程序,比例载荷情况 –恒定振幅下的疲劳程序,非比例载荷情况 ?上述功能适用于ANSYS DesignSpacelicenses和附带疲劳模块的更高级的licenses. A. 疲劳概述 ?结构失效的一个常见原因是疲劳,其造成破坏与重复加载有关 ?疲劳通常分为两类: –高周疲劳是当载荷的循环(重复)次数高(如1e4 -1e9)的情况下产生的. 因此,应力通常比材料的极限强度低. 应力疲劳(Stress-based)用于高周疲劳. –低周疲劳是在循环次数相对较低时发生的。塑性变形常常伴随低周疲劳,其阐明了短疲劳寿命。一般认为应变疲劳(strain-based)应该用于低周疲劳计算. ?在设计仿真中, 疲劳模块拓展程序(Fatigue Module add-on)采用的是基于应力疲劳(stress-based)理论,它适用于高周疲劳. 接下来,我们将对基于应力疲劳理论的处理方法进行讨论. …恒定振幅载荷 ?在前面曾提到, 疲劳是由于重复加载引起: –当最大和最小的应力水平恒定时, 称为恒定振幅载荷. 我们将针对这种最简单的形式,首先进行讨论. –否则,则称为变化振幅或非恒定振幅载荷
…成比例载荷 ?载荷可以是比例载荷, 也可以非比例载荷:–比例载荷, 是指主应力的比例是恒定的,并且主应力的削减不随时间变化. 这实质意味着由于载荷的增加或反作用的造成的响应很容易得到计算.–相反, 非比例载荷没有隐含各应力之间相互的关系,典型情况包括:?在两个不同载荷工况间的交替变化?交变载荷叠加在静载荷上?非线性边界条件
某商用车白车身结构疲劳寿命分析与优化设计
某商用车白车身结构疲劳寿命分析与优化设计 李明1李源2陈斌3 (1湖南工业大学机械工程学院,湖南株洲,412008;2国防科学技术大学指挥军官基础教育学院,湖南长沙,410072;3 湖南大学汽车车身先进设计制造国家重点实验室,湖南长沙,410082) 摘要:本文基于应力分析结果,采用有效的疲劳寿命预估方法,利用专业耐久性疲劳寿命分析系统MSC.Fatigue对该型商用车白车身进行S-N全寿命分析,得其疲劳寿命分布与危险点的寿命值。采用 结构优化、合理选材等方法,提高白车身结构的疲劳寿命。 关键词:白车身;有限元;静态分析;疲劳寿命分析;优化 Body-in-white Fatigue Analysis and Optimization Design of the Commercial Vehicle LI Ming1, LI Yuan2, CHEN Bin3 (1 School of Mechanical Engineering , Hunan University of Technology, Zhuzhou, Hunan 412008, China; 2 College of Basic Education for Officers, National University of Defense Technology, Changsha, Hunan 410072, China;3 State Key Laboratory of Advanced Design and Manufacture for Vehicle Body, Hunan University, Changsha, Hunan 410082,China) Abstract:Based on the results of stress analysis, this paper took the effective way of the fatigue life estimating, used the professional durability fatigue life analysis system MSC. Fatigue, and the S-N life-cycle analysis of the certain type of commercial vehicle body-in-white finite element model, got the distribution of fatigue life and the fatigue life value of the danger points. Finally, by the structural optimization and material selection, writer improved the fatigue life of white body structure. Keywords: B ody-in-white structure, FEM, Static analysis, Fatigue lifetime analysis; Optimization 0 前言 在车身结构疲劳领域的国内研究中,1994年,江苏理工大学陈龙在建立了车辆驾驶室疲劳强度计算的力学和数学模型基础上,提出了车辆驾驶室疲劳强度研究方法[1]。2001 年,清华大学孙凌玉[2]等首次计算机模拟了汽车随机振动过程。2002年,上海汇众汽车制造有限公司王成龙[3]等应用FATIGUE 软件的分析,结合疲劳台架试验,探讨了疲劳强度理论在汽车产品零部件疲劳寿命计算中的应用,提出了提高零部件疲劳强度的方法。2004年,同济大学汽车学院靳晓雄[4]等人提到进行零部件疲劳寿命预估,
结构振动疲劳研究的总结报告
结构振动疲劳研究的总结报告 南京航空航天大学振动工程研究所刘文光 (一)研究现状 疲劳作为结构失效的主要形式,它是指材料、零件和构件在交变载荷作用下,在某点或某些点产生局部的永久性损伤,并在一定循环次数后形成裂纹、并使裂纹进一步扩展直到完全断裂的现象。早在19世纪中叶,随着蒸汽机的发明和铁路建设的发展,研究人员发现机车车轮结构在远小于其静强度极限载荷时发生交变应力破坏现象,由此提出并发展了不同于结构静强度破坏的结构疲劳破坏问题。由于工业、交通和国防技术的发展,结构疲劳失效问题遍布在航空、航天、能源、交通、建筑、化工等诸多领域,促使抗疲劳设计得到深入的发展和广泛的应用。另外,我们很容易发现在结构疲劳破坏问题中包含了一类重要的现象,那就是当交变载荷的频率与结构的某一阶(甚至某几阶)固有频率一致或比较接近时,结构将会发生共振,这时一定的激励将会产生更大的响应,使结构更加易于产生破坏。这类振动疲劳问题,说明结构的疲劳失效与结构的振动响应密切相关。为了揭示结构的疲劳失效与结构振动响应之间的内在规律,需要利用结构动力学的理论加以研究。 在工程实际中,结构受到外部激励总会产生不同的振动响应,因此,绝大部分结构的疲劳失效都与振动有关,实际上可以归结为振动疲劳问题。振动疲劳的研究是科学技术发展的必然要求,同时也是结构疲劳失效理论与结构动力学理论相结合的必然结果。迄今为止,很少有人系统地研究过振动疲劳问题。有关文献中即使提到振动疲劳一词,不同的学者也给出了不同的定义。文献[1]作者认为“振动疲劳是结构所受动态交变载荷(如振动、冲击、噪声载荷等)的频率分布与结构固有频率分布具有交集或相接近,从而使结构产生共振所导致的疲劳破坏现象,也可以直接说成是结构受到重复载荷作用激起结构共振所导致的疲劳破坏。所以只有结构在共振带宽内或其附近受到激励导致的共振破坏才属于振动疲劳破坏,否则都属于静态疲劳问题。”文献[2]作者认为:“当振动频率与结构模态频率相当时,即可视为振动疲劳问题;如果频率远小于结构模态频率时(频率在几或十几),就是普通疲劳问题;当振动频率远大于结构模态频率,以至于与声波频率相当时,即可视为声疲劳进行处理。”文献[3]作者在其博士论文中也提到振动疲劳一词,它指出振动疲劳与噪声和频率有关,但没有揭示振动疲劳的内在本质。上述每一种定义,它都指出了振动疲劳与结构的固有频率、交变载荷的变化频率有关。为了进一步明确振动疲劳的含义,本文将振动疲劳定义为:“振动疲劳是指结构的疲劳破坏与结构的振动响应(包括结构固有频率、交变载荷变化频率、振动幅值、振动相位和结构的振型等模态)密切相关的失效现象,其破坏机理与静态疲劳破坏一致,它包括低频振动疲劳、共振振动疲劳和高频振动疲劳。” 上世纪60年代,S.H.Crandall[4]首先提出了振动疲劳的定义,它指出:“振动疲劳是指振动载荷作用下产生的具有不可逆且累积性的结构损伤或破坏。”这一定义对传统的疲劳理论,它并没有带来显著的改变,也没有涉及振动疲劳现象的动力学本质。之后,国内外陆续有部分学者展开了一些相关方面的研究。例如,文献[6]作者将高频振动实验方法引入非金属类桩基材料的疲劳损伤力学研究领域,对花岗岩、C30混凝土等非金属材料进行高频振动疲劳试验,描述该类材料在稳定状态下的循环应力应变特性,通过实验研究载荷幅值与振动频率对材料特性的影响,研究平均载荷与振幅比值对材料疲劳曲线的影响;文献[7]作者研究了装备中的小口径管道的振动疲劳问题;文献[8]作者利用有限元法,基于功率谱密度函数,在频域内分析了随机振动载荷作用下的疲劳破坏;文献[9]作者对国内外几十年来形成的主要的振动疲劳分析方法进行了归纳整理,为飞机设计和维修提供振动疲劳的设计与分析技术支持文献。还有很多研究人员[10~15]分别从不同的角度研究了振动疲劳问题。
整车-38_后背门SLAM疲劳分析规范V1.0版
后背门SLAM疲劳分析规范编号:LP-RD-RF-0038 文件密级:机密 后背门SLAM疲劳分析规范 V1.0 编制: 日期: 编制日期审核/会签日期批准日期
后背门SLAM疲劳分析规范 修订页 编制/修订原因说明:首次编制 原章节号现章节号修订内容说明备注 编制/修订部门/人 参加评审部门/人 修订记录: 版本号提出部门/人修订人审核人批准人实施日期备注
目录 1 简介 (2) 1.1 分析背景和目的 (2) 1.2 软硬件需求 (2) 软件 (2) 硬件 (2) 1.3 分析数据参数需求 (2) 2 模型前处理 (2) 2.1 模型处理 (2) 2.2 约束及加载方式 (2) 3 有限元分析步骤 (3) 3.1 Ls-Dyna动态分析模块 (3) 3.2 NCODE DesignLife 疲劳分析模块 (6) 4 分析结果后处理 (10) 4.1 HyperView模型动态姿态及沙漏能后处理 (10) 4.2 HyperView疲劳结果后处理 (10) 5 结果评价 (11)
后背门SLAM疲劳分析规范 1 简介 1.1 分析背景和目的 后背门是汽车的重要部件,后背门在日常使用过程中经常开启和关闭,很可能会发生疲劳破坏,从而导致后背门开裂题,直接影响其使用性能及用户体验。后背门开关耐久性已经成为评价后背门品质好坏的一个重要标准。 1.2 软硬件需求 软件 前处理HyperMesh –LsDyna 求解器Ls-Dyna、nCode 后处理HyperWorks 硬件 前、后处理:HP或DELL工作站; 求解:HP服务器、HP或DELL工作站。 1.3 分析数据参数需求 所需模型后背门及白车身模型 2 模型前处理 2.1 模型处理 整个分析模型建立接触关系,后背门铰链处释放转动自由度。 2.2 约束及加载方式 约束白车身截取处节点1~6自由度,后背门总成分别加载1.3m/s、1.8m/s、2.0m/s初始速度。
高铁车体结构件应力分析与疲劳强度评估 王磊 但龙 姜晓艳
高铁车体结构件应力分析与疲劳强度评估王磊但龙姜晓艳 发表时间:2019-07-15T16:09:32.903Z 来源:《当代电力文化》2019年第05期作者:王磊但龙姜晓艳 [导读] 2007年4月18日,我国的高铁开始正式投入使用,由于是刚刚开始进行高铁的建设,因此在高铁运营过程中往往会出现各种各样的问题和缺陷。 中车青岛四方机车车辆股份有限公司山东青岛 266000 摘要:2007年4月18日,我国的高铁开始正式投入使用,由于是刚刚开始进行高铁的建设,因此在高铁运营过程中往往会出现各种各样的问题和缺陷。其中有80%的机械零件都是因为疲劳破坏而失效的。高铁车体结构大部分都是采用金属材料制作的,而金属不可能做无数次的交变载荷试验,都存在一个疲劳强度,一旦所加的应力值超过金属材料的疲劳强度,就会导致金属变形,从而出现严重事故。基于此,本文首先简单的介绍一下影响疲劳强度的因素;随后详细的介绍一下计算疲劳强度的疲劳试验方法。以此仅供相关人士进行交流与参考。 关键词:高铁车体结构件;应力分析;疲劳强度评估 引言: 在这短短的十几年间,我国的高铁行业得到了突飞猛进的发展,装备生产、运行管理等质量水平也在不断的进步和提高。而机械零件作为高铁车体结构的一个重要组成部分,确实应该引起高铁部门的重视。本文首先介绍一下影响机械零件疲劳强度的因素,随后介绍一下计算机械零件疲劳强度的疲劳试验方法,从而准确的进行疲劳强度的评估,从而不断提高高铁结构件的质量。 一、影响高铁车体结构的疲劳强度因素 高铁车体结构件的疲劳强度评估研究一直都在进行,其中最初的评估方法就是对零件疲劳极限进行测定。但由于实际零件在制作过程中尺寸、形状、材料等都各有不同,因此通过测定零件疲劳极限来评估疲劳强度的试验方法在实施起来具有很大的困难。以此,我们可以通过研究影响机械零件疲劳强度的因素来评估机械零件的疲劳强度。影响机械零件疲劳强度的因素主要是应力集中与梯度;尺寸效应以及表面加工质量这三点(见图一)。 (一)应力集中与梯度 为了满足高铁车体结构的要求,机械零件的制作和加工一般都有拐角、切口、沟槽等缺口,这些缺口自然而言的就出现了应力集中,从而提高了零件的局部应力。在零件部件承载静载荷时,随着静载荷的增加,零件会出现一个宏观塑性变形的阶段,重新分配应力并趋于均匀。而对于疲劳破坏而言,零件并不会出现明显的宏观塑性变形,也不会重新分配应力,因此缺口处的疲劳强度比光滑部位高,出现问题的概率也比较大。缺口处的最大局部应力ɑmax和名义应力ɑn的比值为理论应力集中系数K,K=ɑmax/ɑn。K可以用来表示应力集中提高零件局部应力作用,也被称为形状系数,一般采用弹性力学解析方法或者是光测弹性力学试验来求解[1]。 (二)尺寸效应 机械零件的尺寸对于疲劳强度的影响较大,尺寸效应指的就是当尺寸增大时,疲劳强度就会降低。一般用尺寸系数ε来表示尺寸效应作用的大小。δ-1d为零件的疲劳极限,δ-1为几何相似式样的疲劳强度,d为试样和零件的尺寸(一般在6mm到7.5mm),所以ε=δ-1d/δ-1。引起尺寸效应的因素可以分为制作工艺因素和比例因素。制作工艺因素主要是指机械零件在加工制造过程中因为制作差异出现的尺寸变化[2]。而且铸造件的规模大小也会不同程度的增加铸造困难,一般体积越大的铸造件铸造难度更高,也比较容易出现气孔、沙眼等缺陷,这些缺陷都会成为零件的薄弱部分,从而降低零件的疲劳强度。 (三)表面加工质量 表面加工质量一般由表面粗糙度来衡量,金属种类的不同、加工方法的不同都会对表面加工质量造成影响,像金属表面切削深度、切削用量等,都会对零件部件的疲劳强度产生影响。根据相关研究证明,金属式样的疲劳强度随硬化程度的增加而增加,而且应变硬化的式样都会产生残余的压应力,这种压应力会大大提高零件的拉伸疲劳强度,进而降低零件的疲劳强度[3]。 (图一)影响高铁车体结构的疲劳强度因素 二、计算疲劳强度的疲劳试验方法 (一)常规疲劳试验方法介绍 在进行疲劳实验之前,首先要制备好疲劳式样,疲劳式样需要经过机械加工、热处理以及尺寸测量、表面检验等步骤,保证疲劳式样能够达到疲劳试验的设备要求标准。常规的疲劳试验方法主要用于式样个数不多、生产任务紧急的情况,该方法可以直接给出零件式样的
细解Ansys疲劳寿命分析
细解Ansys疲劳寿命分析 ANSYS Workbench 疲劳分析 本章将介绍疲劳模块拓展功能的使用: –使用者要先学习第4章线性静态结构分析. ?在这部分中将包括以下内容: –疲劳概述 –恒定振幅下的通用疲劳程序,比例载荷情况 –变振幅下的疲劳程序,比例载荷情况 –恒定振幅下的疲劳程序,非比例载荷情况 ?上述功能适用于ANSYS DesignSpacelicenses和附带疲劳模块的更高级的licenses. A. 疲劳概述 ?结构失效的一个常见原因是疲劳,其造成破坏与重复加载有关 ?疲劳通常分为两类: –高周疲劳是当载荷的循环(重复)次数高(如1e4 -1e9)的情况下产生的. 因此,应力通常比材料的极限强度低. 应力疲劳(Stress-based)用于高周疲劳. –低周疲劳是在循环次数相对较低时发生的。塑性变形常常伴随低周疲劳,其阐明了短疲劳寿命。一般认为应变疲劳(strain-based)应该用于低周疲劳计算. ?在设计仿真中, 疲劳模块拓展程序(Fatigue Module add-on)采用的是基于应力疲劳(stress-based)理论,它适用于高周疲劳. 接下来,我们将对基于应力疲劳理论的处理方法进行讨论. …恒定振幅载荷 ?在前面曾提到, 疲劳是由于重复加载引起: –当最大和最小的应力水平恒定时, 称为恒定振幅载荷. 我们将针对这种最简单的形式,首先进行讨论. –否则,则称为变化振幅或非恒定振幅载荷
…成比例载荷 ?载荷可以是比例载荷, 也可以非比例载荷:–比例载荷, 是指主应力的比例是恒定的,并且主应力的削减不随时间变化. 这实质意味着由于载荷的增加或反作用的造成的响应很容易得到计算.–相反, 非比例载荷没有隐含各应力之间相互的关系,典型情况包括:?在两个不同载荷工况间的交替变化?交变载荷叠加在静载荷上?非线性边界条件