分程控制系统.doc

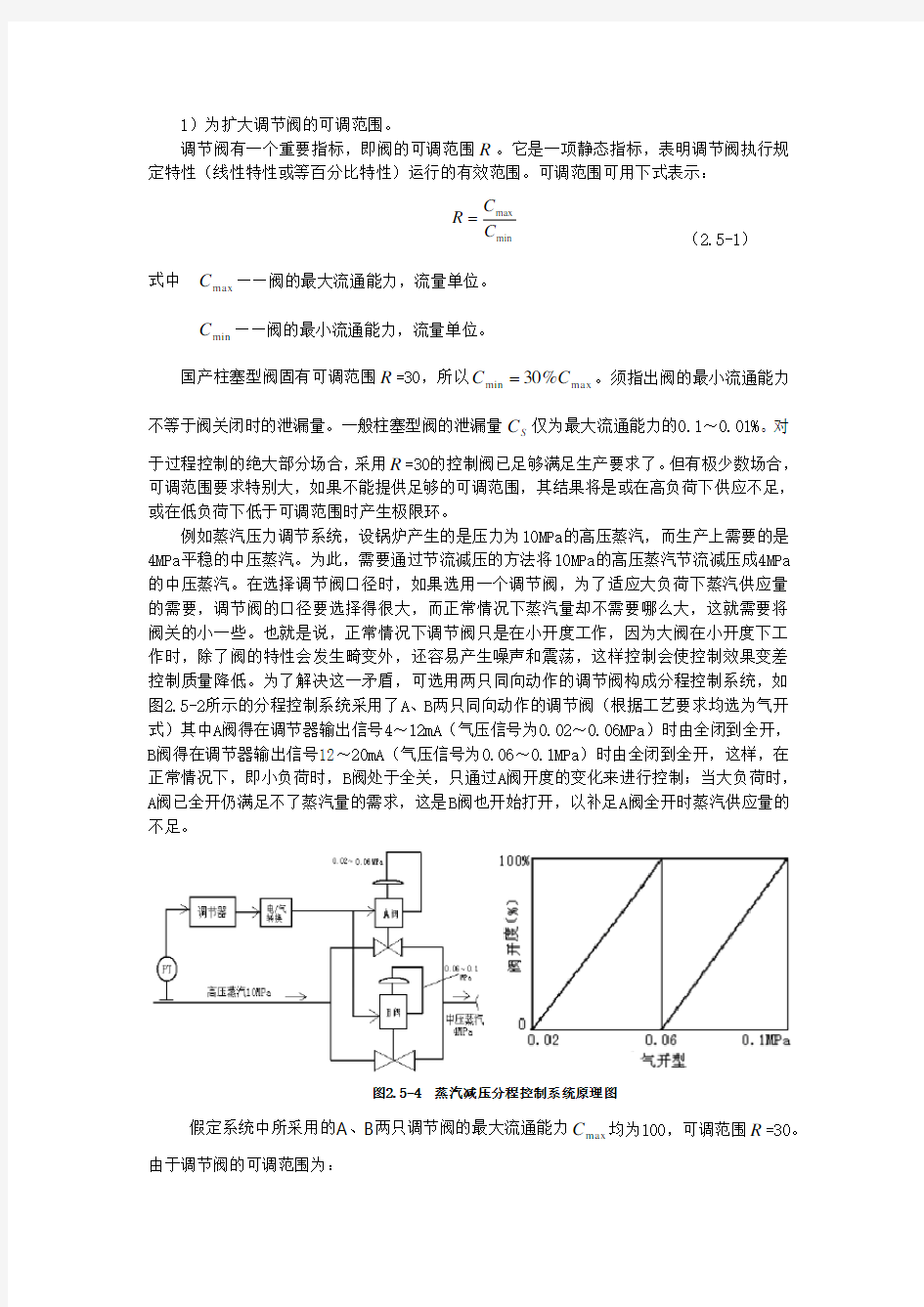
2.5 分程控制系统
2.5.1 分程控制系统的基本概念
1.分程调节系统
一般来说,一台调节器的输出仅操纵一只调节阀,若一只调节器去控制两个以上的阀并且是按输出信号的不同区间去操作不同的阀门,这种控制方式习惯上称为分程控制。
图2.5-1表示了分程控制系统的简
图。图中表示一台调节器去操纵两只调节
阀,实施(动作过程)是借助调节阀上的
阀门定位器对信号的转换功能。例如图中
的A、B两阀,要求A阀在调节器输出信号
压力为0.02~0.06MPa变化时,作阀得全
行程动作,则要求附在A阀上的阀门定位
器,对输入信号0.02~0.06MPa时,相应
输出为0.02~0.1MPa,而B阀上的阀门定
位器,应调整成在输入信号为0.06~0.1 图2.5-1 分程控制系统示意图
MPa时,相应输出为0.02~0.1MPa。按照这些条件,当调节器(包括电/气转换器)输出信号小于0.06MPa时A阀动作,B阀不动;当输出信号大于0.06MPa时,而B阀动作,A阀已动至极限;由此实现分程控制过程。
分程控制系统中,阀的开闭形式,可分同向和异向两种,见图2.5-2和图2.5-3。
图2.5-2 调节阀分程动作(同向)
图2.5-3 调节阀分程动作(异向)
一般调节阀分程动作采用同向规律的是为了满足工艺上扩大可调比的要求;反向规律的选择是为了满足工艺的特殊要求。
2.分程控制系统的应用
1)为扩大调节阀的可调范围。
调节阀有一个重要指标,即阀的可调范围R 。它是一项静态指标,表明调节阀执行规定特性(线性特性或等百分比特性)运行的有效范围。可调范围可用下式表示: min max
C C R = (2.5-1)
式中 max C ——阀的最大流通能力,流量单位。
min C ——阀的最小流通能力,流量单位。
国产柱塞型阀固有可调范围R =30,所以max min %30C C =。须指出阀的最小流通能力不等于阀关闭时的泄漏量。一般柱塞型阀的泄漏量S C 仅为最大流通能力的0.1~0.01%。对于过程控制的绝大部分场合,采用R =30的控制阀已足够满足生产要求了。但有极少数场合,可调范围要求特别大,如果不能提供足够的可调范围,其结果将是或在高负荷下供应不足,或在低负荷下低于可调范围时产生极限环。
例如蒸汽压力调节系统,设锅炉产生的是压力为10MPa 的高压蒸汽,而生产上需要的是4MPa 平稳的中压蒸汽。为此,需要通过节流减压的方法将10MPa 的高压蒸汽节流减压成4MPa 的中压蒸汽。在选择调节阀口径时,如果选用一个调节阀,为了适应大负荷下蒸汽供应量的需要,调节阀的口径要选择得很大,而正常情况下蒸汽量却不需要哪么大,这就需要将阀关的小一些。也就是说,正常情况下调节阀只是在小开度工作,因为大阀在小开度下工作时,除了阀的特性会发生畸变外,还容易产生噪声和震荡,这样控制会使控制效果变差控制质量降低。为了解决这一矛盾,可选用两只同向动作的调节阀构成分程控制系统,如图2.5-2所示的分程控制系统采用了A 、B 两只同向动作的调节阀(根据工艺要求均选为气开式)其中A 阀得在调节器输出信号4~12mA (气压信号为0.02~0.06MPa )时由全闭到全开,B 阀得在调节器输出信号12~20mA (气压信号为0.06~0.1MPa )时由全闭到全开,这样,在正常情况下,即小负荷时,B 阀处于全关,只通过A 阀开度的变化来进行控制;当大负荷时,A 阀已全开仍满足不了蒸汽量的需求,这是B 阀也开始打开,以补足A 阀全开时蒸汽供应量的不足。
图2.5-4 蒸汽减压分程控制系统原理图
假定系统中所采用的A 、B 两只调节阀的最大流通能力max C 均为100,可调范围R =30。由于调节阀的可调范围为:
min max C C R = (2.5-2) 据上式可求得 30max min C C ==33.330100= (2.5-3) 当采用两支阀构成分程控制系统时,最小流通能力不变,而最大流通能力为两阀最大流通
能力之和max
2C '=200,因此A 、B 两阀组合后的可调范围应是: 6033
.3200min max =='='C C R 这就是说采用两支流通能力相同的调节阀构成分程控制系统后,其调节阀的可调范围比单只调节阀增大一倍。
2)满足工艺操作的特殊要求。
在某些间歇式生产化学反应过程中,当反应物投入设备后,为了使其达到反应温度,往往在反应开始前需要给它提供一定的热量。一旦达到反应温度后,就会随着化学反应的进行不断释放出热量,这些热量如不及时移走,反应就会越来越激烈,以致会有爆炸的危险。因此对于这种间歇式化学反应器既要考虑反应前的预热问题,又要考虑反应过程中及时移走反应热的问题。为此设计了如图2.5-5所示的分程控制系统。
图2.5-5 间歇式化学反应器分程控制系统图
图中温度调节器选择反作用,冷水调节阀选择气关式(A 阀),热水调节阀选择气开式(B 阀)。该系统工作过程如下:在进行化学反应前的升温阶段,由于温度测量值小于给定值,因此调节器输出增大,B 阀开大,A 阀关闭,即蒸汽阀开、冷水阀关,以便使反应器温度升高。当温度达到反应温度时,化学反应发生,于是就有热量放出,反应物的温度逐渐提高。当温升使测量值大于给定值时,调节器输出将减小(由于调节器是反作用),随着调节器的输出的减小,B 阀将逐渐关小乃至完全关闭,而A 阀则逐渐打开。这时反应器夹套中流过的将不再是热水而是冷水。这样一来,反应所产生的热量就被冷水所带走,从而达到维持反应温度的目的。
2.5.2分程控制系统的方案实施
1.分程区间的决定
分程控制系统设计主要是多个阀之间的分程区间问题,设计原则:
① 先确定阀的开关作用形式(以安全生产为主);
② 再决定调节器的正反作用;
③最后决定各个阀的分程区间。
2.分程阀总流量特性的改善
当调节阀采用分程控制,如果它们得流通能力不同,组合后的总流通特性,在信号交接处流量的变化并不是光滑的。例如选用4max =C 和100min =C 这两只调节阀构成分程控
制,两阀特性及它们的组合总流量特性如图2.5-6所示。
图2.5-6 分程系统大、小阀连接组合特性图
由图2.5-6可以看出,原来线性特性很好的两只控制阀,当组合在一起构成分程控制时,其总流量特性已不再呈现线性关系,而变成非线性关系了。特别是在分程点,总流量特性出现了一个转折点。由于转折点的存在,导致了总流量特性的不平滑。这对系统的平稳运行是不利的,为了使总流量特性达到平滑过渡,可采用如下方法。
解决在0.06处出现了大的转折,呈严重的非线性方法①选用等百分比阀此时可自然解决;②线性阀则可通过添加非线性补偿调节的方法将等百分比特性校正为线性。
2.5.3 阀位控制系统
1.概述
一个控制系统在受到外界干扰时,被控变量将偏离原先的给定值,而发生变化,为了克服干扰的影响,将被控变量拉回到给定值,需要对控制变量进行调整。对一个系统来说,可供选择作为控制变量的可能是多个,选择控制变量既要考虑它的经济性和合理性,又要考虑它的快速性和有效性。但是,在有些情况下,所选择的控制变量很难做到两者兼顾。阀门控制系统就是在综合考虑控制变量的快速性、有效性、经济性和合理性基础上发展起来的一种控制系统。
阀位控制系统的原理结构如图2.5-7
所示。在阀位控制系统中选用了两个控制
G和物料量Q,其中控制变
变量蒸汽量
s
G从经济性和工艺的合理性考虑比较
量
s
合适,但是对克服干扰的影响不够及时有
效。控制变量Q却正好相反,快速性、有
效性较好,但经济性、工艺的合理性较差。图2.5-7 阀位控制系统结构原理图
这两个控制变量分别由两支控制器来控制。其中控制变量Q的为主控制器TC,控制变量s G
的为阀位控制器VPC。主控制器的给定值即产品的质量指标,阀门控制器的给定值是控制变量管线上控制阀的阀位,阀位控制系统也因此而得名。
2.阀位控制系统的工作原理
如图2.5-8的阀位控制系统,假定A阀、B阀均选为气开阀,主控制器TC(温度调节器)为正作用,阀位控制器VPC为反作用。系统稳定情况下,被控变量 等于主控制器的设定值R,A阀处于某一开度,控制B阀处于阀位调节器VPC所设置的小开度r。当系统受到外界干
扰使原油出口温度上升时,温度调节器的输出将增大,这一增大的信号送往两处:其一去B阀;其二去VPC。送往B阀的信号将使B阀的开度增大,这会将原油出口温度拉下来;送往VPC的信号是作为后者的测量值,在r不变的情况下,测量值增大,VPC的输出将减小,A阀的开度将减小,燃料量则随之减小,出口温度也将因此而下降。这样A、B 两只阀动作的结果都将会使温度上升的趋势减低。随着出口温度上升趋势的下降,温度调节器的输出逐渐减小,于是B阀的开度逐渐减小,A阀的开度逐渐加大。这一过程一直进行到温度调节器及阀位调节器的偏差都等于0时为止。温度调节器偏差等于0,意味着出口温度等于给定值,即阀位调节器偏差等于零,意味着调节阀B的阀压与阀位调节器VPC的设定值r相等,而B的开度与阀压是有着一一对应的关系的,也就是说阀B最终会回到设定值r所对应的开度。
由上面的分析可以看到:本系统利用控制变量Q的有效性和快速性,在干扰一旦出现影响到被控变量偏离给定值时,先行通过对控制变量Q的调整来克服干扰的影响。随着时间的增长,对控制变量Q的调整逐渐减弱,而控制出口温度的任务逐渐转让给控制变量s G来
担当。最终阀B停止在一个很小的开度(由设定值r来决定)上,而维持控制的合理性和经济性。
2.6 选择性控制系统
2.6.1 概述
选择性控制系统又叫取代控制,也称超驰控制。
通常自动控制系统只能在生产工艺处于正常情况下进行工作,一旦生产出现事故状态,控制器就要改为手动,待事故排除后,控制系统再重新投入工作。在大型生产工艺过程中,除了要求控制系统在生产在正常情况下能够克服外界的干扰,平稳操作外,还必须考虑事故状态下安全生产。即当生产操作达到安全极限时,应有保护性措施。
属于生产保护性措施的有两类:一类是硬保护措施;一类是软保护措施。
所谓硬保护措施就是当生产操作达到安全极限时,有声、光报警产生。此时有操作工将控制器切换到手动,进行手动操作、处理;或是通过专门设置的联锁保护线路实现自动停车,达到保护生产的目的。对于连续生产过程来说,即使短暂的设备停车,也会造成巨大的经济损失。因此这种硬保护措施已逐渐不为人们所欢迎,相应地出现了软保护措施。
所谓软保护措施,就是通过一个特定设计的选择性控制系统,在生产短期内处于不正常情况时,生产设备不须停车,由选择性控制系统自动改变操作方式,使参数脱离极限值。并且当参数恢复正常时原控制系统自动恢复,避免停车而且无需人的参入与。
2.6.2超驰控制设计应用
如图(2.6-1)(a)、(b)可用来说明氨蒸发器是如何从一个能够满足正常生产情况下的控制方案,演变成为烤炉极限条件下的超驰控制的实例。
图2.6-1 液氨蒸发器的控制方案
液氨蒸发器是一个换热设备,它是利用液氨的汽化需要大量的热量,以此来冷却流经管内的被冷物料。在生产中,往往要求物料的出口温度稳定,即构成一个以被冷物料的出口温度为被控变量,以液氨流量为操纵变量的控制方案。见图2.6-1(a),这一控制方案用的是改变传热面积来调节传热量的方法。因液位高度会影响热交换器的浸润传热面积,因此液位高度反应传热面积的变化。由此可见液氨蒸发器实质上是一个单输入(液氨流量)两输出(温度和液位)系统。通过工艺合适设计,正常情况下温度得到控制以后,液位也应该在一定允许区间。
超限现象是因为出现了非正常工况的缘故。不妨假设有杂质油漏入被冷物料管线,使传热系数猛降,为了取走同样的热量,就要大大增加传热面积。但当液位淹没了换热器的所有列管时,传热面积的增加已达极限,如果继续增加氨蒸发器内的液氨量,并不会提高传热量。但是液位的继续升高,却可能带来生产事故。这是因为气化的氨是要回收重复使用的,气氨将进入压缩机入口,若气氨带液,液滴会损坏压缩机叶片,因而液氨蒸发器上部必须留有足够的气化空间,所以就要限制液位不要超过某一限高。为此就必须在原有温度控制的基础上加一个防液位超限的控制系统。
两个控制系统的工作规律如下:正常情况下,由温度控制器操纵阀门进行温度控制;当出现非正常工况,引起氨液位达到高限时,被冷却物料的温度即使仍偏高,此时温度的偏离给定值暂时成为次要因素,而保护氨压缩机已经上升为主要矛盾,于是液位控制器取代温度控制器工作。等引起不正常的因素消失,液位恢复到正常区域,此时又应恢复温度控制的闭环运行。
实现上述功能的防超限控制方案如图2.6-1(b),它具有两台控制器,通过选择器对两个输出信号的选择来实现对控制阀的两种控制方式。正常情况下应该选温度控制器输出信号,当液位达到极限时,则应选上液位控制器输出。这种控制方式,习惯上称为“超驰控制”。
总之,选择性控制系统工作过程是:(1)在正常情况下,温度调节系统进行调节工作(2)当液面达到高限时,LC调节器抢夺(3)当液面恢复正常值时,TC温度调节的恢复正常工作。
选择性控制系统的特点是:(1)实现工艺要求的逻辑关系或极值条件(2)系统中具体实现逻辑功能的选择器(3)保护性系统必须是短时的(4)“救急”的控制系统。
选择性调节系统的设计:(1)被调节参数的选择(2)调节器的选型及参数整定(3)选择器的选择步骤,先确定阀的开、关形式;再确定出调节器的正反作用;最后看超驰系统参数的极限输出,是高选择器选为高选。是低为低选。正常回路参数变化与选择器选择无关。
2.6.3 关于防积分饱和的方法
由于选择性控制系统中,总有一台控制器处于开环状态,因此易产生积分饱和。防积分饱和的三种方法:
①限幅法:用高低值限幅器,控制器积分反馈信号限定在某个区域。
②外反馈法:在控制器开环状态下,不再使它自身的信号做积分反馈,而是采用合适的外部信号作为积分反馈信号。从而也切断了积分正反馈,防止了进一步的偏差积分作用。
③积分切除法:它是从控制器本身的线路结构上想办法。使控制器积分线路在开环情况下,会暂时自动切除,使之仅具有比例作用。所以这类控制器称为PI-P控制器。
因为积分切除法,主要是涉及仪表内部线路设计,在这里不作进一步的讨论。关于限幅器与外反馈方法,因为它们的防积分饱和原理不一致,功能亦有差别,在应用中应注意它们各自的适用场合。对于选择性控制系统的防积分饱和,应选择外反馈法。其积分外