常见台架试验
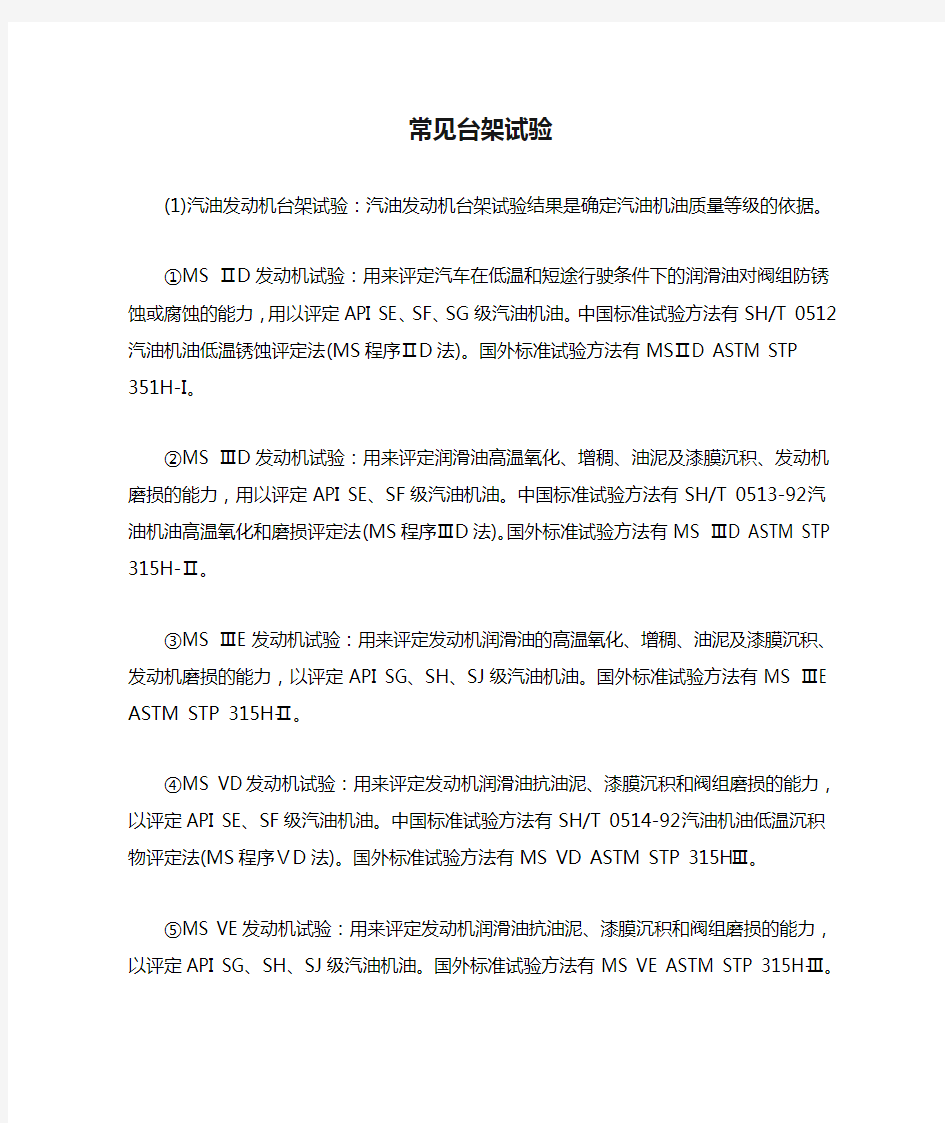

常见台架试验
(1)汽油发动机台架试验:汽油发动机台架试验结果是确定汽油机油质量等级的依据。
①MS ⅡD发动机试验:用来评定汽车在低温和短途行驶条件下的润滑油对阀组防锈蚀或腐蚀的能力,用以评定API SE、SF、SG级汽油机油。中国标准试验方法有SH/T 0512汽油机油低温锈蚀评定法(MS程序ⅡD法)。国外标准试验方法有MSⅡD ASTM STP 351H-I。
②MS ⅢD发动机试验:用来评定润滑油高温氧化、增稠、油泥及漆膜沉积、发动机磨损的能力,用以评定API SE、SF级汽油机油。中国标准试验方法有SH/T 0513-92汽油机油高温氧化和磨损评定法(MS程序ⅢD法)。国外标准试验方法有MS ⅢD ASTM STP 315H-Ⅱ。
③MS ⅢE发动机试验:用来评定发动机润滑油的高温氧化、增稠、油泥及漆膜沉积、发动机磨损的能力,以评定API SG、SH、SJ 级汽油机油。国外标准试验方法有MS ⅢE ASTM STP 315H-Ⅱ。
④MS VD发动机试验:用来评定发动机润滑油抗油泥、漆膜沉积和阀组磨损的能力,以评定API SE、SF级汽油机油。中国标准试验方法有SH/T 0514-92汽油机油低温沉积物评定法(MS程序ⅤD法)。国外标准试验方法有MS VD ASTM STP 315H-Ⅲ。
⑤MS VE发动机试验:用来评定发动机润滑油抗油泥、漆膜沉积和阀组磨损的能力,以评定API SG、SH、SJ级汽油机油。国外标准试验方法有MS VE ASTM STP 315H-Ⅲ。
(2)柴油发动机台架试验:柴油发动机台架试验结果是确定柴油
机油质量等级的依据。
①Caterpillar 1H2发动机试验:用来评定润滑油的环粘结、环和气缸磨损、活塞沉积物生成倾向,以评定API CC级柴油机油。中国标准试验方法有GB/T 9932内燃机油性能评定法(卡特皮勒1H2法)。国外标准试验方法有ASTM STP 509A-Ⅱ Caterpillar 1H2发动机试验法。
②Caterpillar 1G2发动机试验:用来评定润滑油的环粘结、环与气缸磨损、活塞沉积物生成倾向,以评定API CD、CD-Ⅱ、CE级柴油机油。中国标准试验方法有GB/T 9933-92内燃机油性能评定法(卡特皮勒1G2法)。国外标准试验方法有ASTM STP 509A-Ⅰ Caterpillar 1G2发动机试验法。
③CRC L-38发动机试验:用来评定内燃机油在高温条件下的氧化和轴瓦腐蚀性能。中国标准试验方法有SH/T 0265-92内燃机油高温氧化和轴瓦腐蚀评定法(L-38法)。国外标准试验方法有FED 3405.2(L?38)、FTM 791-3405润滑剂性能评定法。
(3)齿轮油台架试验:
①CRC L-37高扭矩试验:用来评定齿轮润滑剂承载能力、磨损及极压特性,以评定API GL-5车辆齿轮油。国外标准试验方法有美国FTM 6506.1高扭矩后桥试验。
②CRC L-42高速冲击试验:用来评价齿轮润滑剂的抗擦伤性能,以评定API GL-5车辆齿轮油。国外标准试验方法有美国FTM 6507.1高速冲击试验。
③CRC L-33齿轮润滑剂的潮湿腐蚀试验:用来评价含水齿轮油对金属零件的腐蚀情况,以评定API GL-5车辆齿轮油。国外标准试验方法有美国FTM 5326.1齿轮润滑剂的潮湿腐蚀试验。
④CRC L-60齿轮润滑剂热氧化安定性试验:用来评定齿轮油的热氧化安定性,以评定API GL-5车辆齿轮油。中国标准试验方法有GB/T 8119车辆齿轮油热氧化安定性评定法(L-60)。国外标准试验方法有美国FTM 2504 CRC L-60热氧化安定性试验。
(4)液压油台架试验:
叶片泵试验采用V-104叶片泵评定泵的总磨损量,以试验后叶片泵和定子总失重的毫克数来表示。中国标准试验方法有SH/T 0307石油基液压油磨损特性测定法(叶片泵法)。国外标准试验方法有美国ASTM D 2882、英国IP 281 V-104叶片泵试验法。
转向架静载试验台
转向架静载试验台(地下式) (1)概述 本试验台用于广州地铁四、五、六号线车辆转向架静载试验。试验台通过测定轮重以及弹簧位移变化,自动计算出弹簧刚度和构架抗扭刚度,并可给出相应点的加垫厚度。试验台采用下沉式安装,试验台导轨与两端厂房标准轨道水平连接,转向架为通过式静载试验。 (2)主要技术性能 1)在模拟车体重量的情况下测量转向架四角高度。能对拖车、动车转向架加载进行高度检查,并预测空气弹簧底部垫片所需厚度。 2)模拟车体的重量对转向架进行加载,并检测各轮轮重,加载点可调整。能称量各车轮在不同载荷下的轮重。 3)可在试验台上对转向架进行加垫操作。 4)具有设备安全保障功能和设备自检功能,可随时监视设备的运行情况,并显示其故障的位置。 5)可方便地显示、查询当前及以往数据,如操作日期、时间、试验者姓名、转向架号及检测数据。 6)随时打印各有关数据和报表,自动生生成检测报告。 7)具有在线帮助和良好的人机对话界面,能进行程序管理,如添加、删除、设置等,各类转向架必要参数可设置、取舍、保存和调用。 8)在不同载荷和位移条件下,能自动测量轮轴的平行度。 9)有足够的刚度和良好的平稳性,噪声符合我国环保要求,能在环境温度-10℃~40℃,相对湿度≤98%条件下正常工作。 10)在试验台能方便人工测量轨面距(踏面)一系簧支撑、二系簧座的高度。 (3)主要技术参数 1)轨距:1435mm 2)二系加载力:0-100 kN×2,精度±1.5‰ F.S 3)加载油缸行程:≤400mm,位移测量精度5‰(F.S) 4)二系加载力位置调节范围横向:300-2000mm,定位精度±1mm
5)轴距测量范围:1800-2200mm,测量精度±0.2mm 6)轮重测量范围:<6t,测量精度±1.5‰ F.S 7)基准平台:水平误差<0.25mm
汽车转向节总成性能要求及台架试验方法
《汽车转向节总成性能要求及台架试验方法》编制说明 (标准送审稿) a.工作简况 1、任务来源 本标准依据中国汽车工程学会2014年12月12日印发中汽学函[2014]73号《中国汽车工程学会技术规范起草任务书》/任务书编号2014-3制定,标准名称《汽车转向节总成性能要求及台架试验方法》。本标准主要完成单位:中国汽车工程研究院股份有限公司、浙江万安科技股份有限公司。 2、主要工作过程 2014年3月由中国汽车工程研究院股份有限公司向中国汽车工程学会(以下简称中汽学会)提出制定《汽车转向节总成性能要求及台架试验方法》标准的申请,当年成立了标准工作组,提出撰写思路并进行分工。 工作组于2015年2月召开标准讨论会,确认撰写大纲和章节目录;会后形成标准试验验证稿,并对标准相关项目进行试验验证工作分工、确定试验验证单位和责任人。 2015年3月-2015年5月中国汽车工程研究院股份有限公司承担了以下试验验证项目:1、正向冲击;2、吸能冲击;3、主销孔冲击;4、转向节臂冲击;5、耐腐蚀性;6、总成耐久性;7、转向节臂耐久性等项目。 试验验证工作完成后,标准工作小组即对标准的文稿和图进行了修改编制,形成了征求意见稿。 标准于2015年6月18日由中国汽车工程学会技术发展部将标准征求意见稿发给5家相关单位征求意见,未收到任何意见。 2016年3月根据2015年12月中国汽车工程学会北京标准工作会议要求工作组对标准征求意见稿做了如下修改:1、标准名称正式确定为《汽车转向节总成性能要求及台架试验方法》;2、按照GB/T 1.1-2009给出的规则规范了标准的格式;3、完善和修改了标准用图。 标准于2016年4月20日形成送审稿请转向技术委员会专家函审。 3 主要参加单位和工作组成员及主要工作 本标准负责起草单位:中国汽车工程研究院股份有限公司。 本标准参加起草单位:浙江万安科技股份有限公司。 本标准主要起草人: 本标准参加起草人: 中国汽车工程研究院股份有限公司,邓飞、廖梦楠、颜尧、赵赢、欧家福。编写本标准文本、标准用图、验证试验计划与实施、收集资料、征集意见与技术交流、工作汇报; 浙江万安科技股份有限公司,侯宗刚。提供验证样品;负责收集整理有关汽车转向节生产方面的术语、数据、措施、质量管理等方面的内容。 b.标准编制原则和主要内容的论据 1、标准制订的主要依据 力求与国际接轨,参考国外公司产品的相关技术资料的同时,又考虑国内生产、试验条件的可行性,力求全面的包括汽车转向节总成的所有重要性能,通过所规定的试验项目能描述出汽车转向节总成的基本性能和特殊要求,能够指导该产品的进一步发展。 2、标准制订的原则 在进行了大量的台架验证试验后,我们对国内企业现有的技术水平和国外同类产品进行
QC T 545-1999汽车筒式减振器 台架试验方法
QC T 545-1999汽车筒式减振器台架试验方 法 QC/T 545—1999 汽车筒式减振器台架试验方法代替JB 3901—85 本标准适用于汽车悬架用筒式减振器的台架试验。 1示功试验 1.1目的:测取试件的示功图和速度图。 1.2设备:按本标准附录A规定的减振器试验台。 1.3条件: 1.3.1试件温度:20±2℃。 1.3.2试件试验行程S:(100±1)mm。 1.3.3试件频率n:(100±2)c、p、m。 1.3。4速度V:按照1.3.2和1.3.3并由下式决定的减振器活塞速度。 在减振器行程较小,不宜选用100mm的试验行程时由制造厂与用户商定 试验速度值。 1.3.5方向,铅垂方向。 1.3.6位置:大致在减振器行程的中间部分。 1.4试验方法 1.4.1定期按本标准附录B的试验台标定方法取得测力元件标定常数1 (N/mm)。 1.4.2按1.3加振,在试件往复3~5次内记录示功图。 1.4.3在不装试件时,画出基准线。 1.5阻力运算:参见图1
2速度特性试验 2.1目的:检测减振器在不同活塞速度下的阻力,取得试件的速度特性。 2.2设备:按标准附录A规定的减振器示功试验台,配以相应的电测量装置。 2.3条件: 2.3.1试件温度:20±2℃ 2.3.2试件试验行程S:20~100mm 2.3.3速度:V 2.3.4方向:铅垂方向。 2.3.5位置:大致在减振器行程的中间部分。 2.4试验方法: 制造厂或研制单位可按照具体情形选用下述方法之一。 2.4.1直截了当记录法: 在标准附录A规定的试验台上,采纳相应的电测量装置,利用传感元件取 得减振器活塞速度和相应的阻力信号;将该两信号同时输入记录装置而直截了当获 得减振器的速度特性。 速度特性曲线如图2所示。 2.4.2多工况合成法 按照2.3.3能够变化行程(S),或频率(n)之一,而取得变化的速度值 (V),及相应工况下的阻力(P)形成速度特性的若干点,最终光滑连接构成
台架方案模板
CNG发动机试验台架方案 一、方案概述 发动机测控系统采用湘仪的GW40电涡流测功机与FC 《发动机自动测控系统》 发动机测试系统采用的CAN现场总线通讯协议符合国际标准: ISO11898( CAN) 发动机性能试验符合QC/T524-1999《发动机性能试验方法》, GB/T18297- 《汽车发动机性能试验方法》 发动机可靠性试验符合GB/T19055- 《汽车发动机可靠性试验方法》 发动机的转速、气耗、温度、压力等参数的测量精度不低于标准中规定的要求 试验台一体原则: 本试验台为布置一体, 能完成多功能的整体试验台 试验台的设计首先考虑成熟可靠, 选择成熟的技术和成熟的设备 二、试验台架拟定试验项目 怠速试验 总功率试验 净功率试验
燃气发动机性能试验 活塞漏气量试验 三、试验台架工作环境要求 为满足发动机试验要求和保证试验的正常进行, 实验室需具备以下条件: 动力电源3相, 380V, 50HZ 仪器电源单相, 220V , 50HZ 环境温度- 10~50℃ 相对湿度≤95%, ≥85%时, 一周内必须通电1小时 台架安装基础设计、施工完毕 试验室地下管道网、地沟布置、设计、施工完毕 台架一体化铸铁底板、地沟盖板设计、加工、安装 室外高位水箱、冷却水池设计、施工, 带过滤 测功机冷却系统 发动机冷却水系统设计 发动机机油冷却管道设计、施工, 带机油冷却器; 发动机燃气罐、输气管道设计、安装施工; 水泵、管道泵、风机等试验设备安装; 试验室排气管路系统设计、安装; 试验室通风系统设计、安装; 试验室电路设计、布线、施工; 电动葫芦及其安装;
配备轴流风机、启动电源等试验用辅助设备; 发动机常规试验需要的其它辅助装置、器具、附件等; 发动机与测功机对中联接完毕 四、实验室布置方式 发动机试验间与台架控制室隔离, 台架控制室安装双层消音玻璃窗用于发动机的监控, 发动机试验间与台架控制室间由一安全通道门相通。 发动机试验间推荐尺寸: 8000mm×6000mm×5000mm 台架控制室推荐尺寸: 4000mm×6000mm×5000mm 试验台基础用于安装测功机和发动机。由于发动机在运转试验时会产生较大的震动, 基础设计的好坏将直接影响到试验质量和测试精度。台架基础设计时, 下列原则应加以考虑。 ①基础应该有足够的质量, 以使发动机试验时的振动降到最低限度。 ②试验台基础及其上的结构件应有足够的刚性, 否则在强烈的振动下会产生扰性变形。特别要注意结构件的谐振频率应避开发动机运行时产生的震动频率。 ③试验台应采取有效的隔振措施, 减小试验台振动能量向外界传递。简单的方法是在混凝土基础上下面垫一层黄沙, 并在基础四周开隔振沟。更佳者为在基础下设置橡胶减振垫。 试验台基础由以下部分组成: 水泥基础: 根据发动机功率确定基础质量
发动机台架试验 -可靠性试验
学生实验报告实验课程名称:发动机试验技术
目录 一、试验目的 二、试验内容 1.试验依据 2.试验条件 3.试验仪器设备 4.试验样机 5.试验内容与方案 (1)交变负荷试验 (2)混合负荷试验 (3)全速负荷试验 (4)冷热冲击试验 (5)活塞机械疲劳试验 (6)活塞热疲劳试验 三、试验进度安排 四、试验结果的提供
摘要 国外在可靠性试验方面己做了许多有益的研究工作,但到目前为止尚未形成统一的试验方法,而且考虑到该试验的非普遍性及技术保密性,将来也不可能形成统一的试验规范。相对于热疲劳研究状况来讲,国内对机械疲劳的研究还比较少。为适应发动机比功率和排放法规日益提高的苛刻要求,发动机面临着更高机械负荷和热负荷的严峻考验。国内高强化发动机最大爆发压力已超过22 Mpa。活塞的机械疲劳损伤主要体现在销孔、环岸等部位。活塞环岸、销座及燃烧室等部位由于在较高的工作温度下承受着高频冲击作用的爆发压力,润滑状况较差,摩擦磨损,其他破坏可靠性的腐蚀磨损(缸套一环换向区、排气门/排气门座锥面等)、疲劳磨损(挺杆、轴瓦、齿轮表面等)、微动磨蚀(轴瓦钢背、飞轮压紧处、飞轮壳压紧处、湿缸套止口处等)、电蚀(火花塞电极等)和穴蚀(水泵叶轮等)这些都是可靠性试验的主要目标,也是实施可靠性设计、试验研究的重点部位。 众所周知,在内燃机整机上进行零部件可靠性试验成本昂贵。本文将参照原有的可靠性试验方法,通过看一些关于可靠性的零部件加速寿命实验技术制定一种评价内燃机可靠性的考核规范,包括活塞机械疲劳试验和活塞热疲劳试验,可迅速做出其可靠性恰当的评价,可以降低研发成本、缩短研发时间。 一、试验目的 1通过理解内燃机可靠性评估,评定发动机的可靠性。 1.1了解评估的多种理论方法,如数学模型法、上下限法、相似设备法、蒙特卡洛法、故障分析( 包括故障模式影响分析和故障树分析) 等。并掌握故障分析法。 1.2学会可靠性试验评估,为进行可靠性设计奠定基础理论,为发动机及相关零部件提供测试、验证以及改进的技术支持。 2掌握可靠性试验方法 2.1掌握内燃机可靠性综合性试验及专项试验。综合性试验的考核对象是零件的可靠性、零件表面性状的变化和发动机性能的保持性;专项试验是超水温( 耐热性) 、超负荷、混合负荷、交变负荷循环、超爆发压力、超速等试验。 二、试验内容 1试验依据 参考的试验标准: GB /T 19055-2003 汽车发动机可靠性试验方法 GB /T 18297-2001 汽车发动机性能试验方法 JB/T 5112-1999 中小功率柴油机产品可靠性考核 2试验条件 一般试验条件: 2.1燃料及机油:采用制造厂所规定的牌号,柴油中不得有消烟添加剂。
QC T 304-1999汽车转向拉杆接头总成台架试验方法
QC T 304-1999汽车转向拉杆接头总成台架试 验方法 QC/T 304—1999 汽车转向拉杆接头总成台架试验方法代替ZB T 23 006—87 1主题内容与适用范畴 本标准规定了汽车转向拉杆接头总成的摆动力矩测定、旋转力矩测定、最大 轴向位移量测定和耐久性试验等台架试验方法。 本标准适用于汽车转向拉杆接头总成,出厂试验与型式试验的项目与要求由 相应的技术条件规定。 2术语及定义 2.1摆动力矩T1 球销以一定的频率,在接头总成的对称平面或设计指定平面内作连续摆动时 的最大力矩(N·m)。 2.2旋转力矩T2 球销轴线与接头球座孔轴线重合,球销绕轴线匀速旋转时的最大力矩(N·m)。 2.3最大轴向位移量δ 球销轴线与接头球座孔轴线重合,沿该轴线对球销施加压力,使总成内部除 弹性零件外的其他零件均不发生变形时,球销的最大位移量(mm)。 3试验项目及试验方法 3.1摆动力矩下的测定 3.1.1测试装置的工作原理见示意图1。
3.1.2试验条件 3.1.2.1环境温度:常温。 3.1.2.2测试仪器精度不低于1%。 3.1.3测试样品许多于3件。 3.1.4试验程序 3.1.4.1测试前拆除总成的防尘装置。 3.1.4.2向总成内注满规定牌号的润滑脂。 3.1.4.3使球销处于接头总成的对称平面或设计指定平面内,以4~6min-1 的频率连续摆动,摆动角为设计值的80%~90%。 3.1.4.4测试时球销先往复摆动5次再记录T1值,并运算5次测试结果的均值。 3.2旋转力矩T2的测定。 3.2.1测试装置的工作原理见示意图2。 3.2.2试验条件 3.2.2.1环境温度:常温。 3.2.2.2测试仪器精度不低于1%。 3.2.3测试样品许多于3件。 3.2.4试验程序 3.2.4.1测试前拆除总成的防尘装置。 3.2.4.2向总成内注满规定牌号的润滑脂。 3.2.4.3使球销轴线与接头球座孔轴线重合,球销以4~6r/min的转速绕轴线 匀速旋转。 3.2.2.4测试时球销先旋转5圈再记录T2值,并运算5次测试结果的均值。 3.3最大轴向位移量δ的测定。
汽车简式减振器台架试验方法
减振器台架试验及评定方法 主题和范围:本方法规定了PLD 汽车悬架用筒式减振器的台架试验和试验件评定方法。 本方法包含筒式减振器的示功试验、速度特性试验、温度特性试验、耐久性试验。 1 示功试验 1.1 目的:测取试件的示功图和速度图。 1.2 设备:PLD 系列微机控制电液伺服汽车减振器试验台。 1.3 条件: 1.3.1 试件温度:20士2℃。 1.3.2 试件试验行程S :(100±1)mm 。 1.3.3 试件频率n :(100±2) c 、p 、m 。 1.3.4 速度ν根据1.3.2和1.3.3并由下式决定的减振器活塞速度。 (m /s )520106 4.n S π=???=-ν 1.3.5 方向:铅垂方向。 1.3.6 位置:将减振器拉伸至最大行程并测定其行程中间位置A m ,并纪录。 1.4 试验方法 1.4.1 按1.3加振,待f P 、y P 微机显示值稳定后,停止试验并记录相应得数值。 f P …………复原阻力,N ; y P …………压缩阻力,N ; 1.5 评定 1.5.1 示功图应丰满、圆滑,不得有空程、畸形等。 1.5.2 减振器在示功试验中,不得有漏油和明显的噪声等异常现象。 1.5.3 复原阻力和压缩阻力应符合附录A 要求,复原阻力和压缩阻力的允差值应符合下式规定: 复原阻力的允许差值为±(14%f P +40)N ,f P —额定复原阻力; 压缩阻力的允许差值为±(14%y P +40)N ,y P —额定压缩阻力; 2 速度特性试验 2.1 目的:检测减振器在不同活塞速度下的阻力,取得试件的速度特性。 2.2 设备:PLD 系列微机控制电液伺服汽车减振器试验台。 2.3 温度条件: 试件温度:20±2℃ 试件试验行程S :20~100 mm ,速度)/(.s m 520=ν;最高速度须高于1.5 m /s 。 方向:铅垂方向。 位置:A m 。 试验方法:本方法采用多工况合成法测试速度特性P 一v 曲线 每个测点工况皆按本标准1.4实施; 最后如图4所示取得试验速度特性:
驻车制动杆台架试验规范
驻车制动操纵杆台架试验规范
前言 本标准编写格式符合GB/T1.1-2009标准规定。 本标准通过纸版发布,是受控文件,复印的文件为非受控文件,仅供参考。
驻车制动操纵杆台架试验规范 1 范围 本规范适用于机械式驻车制动操纵杆总成的外观、结构、参数及性能等的台架试验; 本标准适用于驻车制动操纵杆总成的台架试验。 2 规范性引用文件 下列文件对于本文件的应用是必不可少的,凡是注日期的引用文件,仅注日期的版本适用于本文件。凡是不注日期的引用文件,其最新版本(包括所有的修改单)适用于本文件。 QC/T484 汽车油漆涂层 GB/T1818 金属表面洛式硬度试验方法 GB/T4340.1 金属维式硬度试验第1部分:试验方法 3. 试验内容及要求 3.1 外观质量 3.1.1 不允许有碰伤、损坏、锈蚀及毛刺等缺陷。 3.1.3 棘轮板的齿形应规则、统一,与棘爪啮合应牢固。 3.1.3 铆接牢固,铆接部位无龟裂等,铆后该部位涂无色透明漆。 3.1.4 操纵应灵活、可靠,无卡滞、噪声等缺陷。 3.3 涂层质量 涂层表面应光滑平整、色泽一致;漆膜厚度不低于30μm。 3.3热处理要求 棘轮板与棘爪应渗碳淬火、回火,齿部表面硬度为HR30N64-73,在550HV的硬化深度为0.15-0.30mm。 3.4 偏摆范围 在操纵杆的动作范围内,驻车制动杆的偏摆量不得超过3mm,耐久性试验后不超过5mm。 3.5 抗拉强度 3.5.1 按钮与推杆在98N的轴向力下不得松动、脱落。 3.5.3 驻车制动杆手柄在经受热循环试验后,其手柄拉脱力应不小于300N,转动力矩应不小于5.0N·m,且无龟裂、变形等。 3.6 圆周方向负荷强度 试验后应满足3.4的要求。 3.7 横向刚性 按4.7的方法试验,Q点的横向偏移不超过5mm。 3.8 横向负荷强度 试验后应满足3.4的要求。 3.9 止动强度
台架试验类型
台架试验 台架试验是指产品出厂前,一般还要进行某些模拟台架试验,包括一些发动机试验,通过之后方能投入使用。主要台架试验有1)汽油发动机台架试验:汽 油发动机台架试验结果是确定汽油机油质量等级的依据。①MSⅡD发动机试验:用来评定汽车在低温和短途行驶条件下的润滑油对阀组防锈蚀或腐蚀的能力,用以评定API SE、SF、SG级汽油机油。中国标准试验方法有SH/T0512汽油机油低温锈蚀评定法(MS程序ⅡD法)。国外标准试验方法有MSⅡD ASTM STP 351H-I。②MSⅢD发动机试验:用来评定润滑油高温氧化、增稠、油泥及漆膜沉积、发动机磨损的能力,用以评定API SE、SF级汽油机油。中国标准试验方 法有SH/T0513-92汽油机油高温氧化和磨损评定法(MS程序ⅢD法)。国外标准试验方法有MSⅢD ASTM STP315H-Ⅱ。③MSⅢE发动机试验:用来评 定发动机润滑油的高温氧化、增稠、油泥及漆膜沉积、发动机磨损的能力,以评定API SG、SH、SJ级汽油机油。国外标准试验方法有MSⅢE ASTM STP 315H-Ⅱ。④MS VD发动机试验:用来评定发动机润滑油抗油泥、漆膜沉积和 阀组磨损的能力,以评定API SE、SF级汽油机油。中国标准试验方法有SH/T 0514-92汽油机油低温沉积物评定法(MS程序ⅤD法)。国外标准试验方法有MS VD ASTM STP315H-Ⅲ。⑤MS VE发动机试验:用来评定发动机润滑油抗油泥、漆膜沉积和阀组磨损的能力,以评定API SG、SH、SJ级汽油机油。国外标准试验方法有MS VE ASTM STP315H-Ⅲ。(2)柴油发动机台架试验:柴油 发动机台架试验结果是确定柴油机油质量等级的依据。①Caterpillar1H2发动机试验:用来评定润滑油的环粘结、环和气缸磨损、活塞沉积物生成倾向,以评定API CC级柴油机油。中国标准试验方法有GB/T9932内燃机油性能评定法(卡特皮勒1H2法)。国外标准试验方法有ASTM STP509A-ⅡCaterpillar1H2发动机试验法。②Caterpillar1G2发动机试验:用来评定润滑油的环粘结、环与气缸 磨损、活塞沉积物生成倾向,以评定API CD、CD-Ⅱ、CE级柴油机油。中国标准 试验方法有GB/T9933-92内燃机油性能评定法(卡特皮勒1G2法)。国外标准试验方 法有ASTM STP509A-ⅠCaterpillar1G2发动机试验法。③CRC L-38发动机试验:用来评定内燃机油在高温条件下的氧化和轴瓦腐蚀性能。中国标准试验方法有SH/T0265-92内燃机油高温氧化和轴瓦腐蚀评定法(L-38法)。国外标准试验方法有FED3405.2(L?38)、FTM791-3405润滑剂性能评定法。(3)齿轮油台架试验:①CRC L-37高扭矩试验:用来评定齿轮润滑剂承载能力、磨损及极压特性,以评定API GL-5车辆齿轮油。国外标准试验方法有美国FTM6506.1高扭矩后桥试验。②CRC L-42高速冲击试验:用来评价齿轮润滑剂的抗擦伤性能,以评定API GL-5车辆齿轮油。国外标准试验方法有美国FTM6507.1高速冲击试验。③CRC L-33齿轮润滑剂的潮湿腐蚀试验:用来评价含水齿轮油对金属零件的腐蚀情况,以评定API GL-5车辆齿轮油。
发动机台架试验
昆明理工大学交通工程学院学生实验报告实验课程名称:发动机试验技术
目录 一、试验目的 二、试验内容 1.试验依据 2.试验条件 3.试验仪器设备 4.试验样机 5.试验内容与方案 (1)交变负荷试验 (2)混合负荷试验 (3)全速负荷试验 (4)冷热冲击试验 (5)活塞机械疲劳试验 (6)活塞热疲劳试验 三、试验进度安排 四、试验结果的提供 摘要 国外在可靠性试验方面己做了许多有益的研究工作,但到目前为止尚未形成统一的试验方法,而且考虑到该试验的非普遍性及技术保密性,将来也不可能形成统一的试验规范。相对于热疲劳研究状况来讲,国内对机械疲劳的研究还比较少。为适应发动机比功率和排放法规日益提高的苛刻要求,发动机面临着更高机械负荷和热负荷的严峻考验。国内高强化发动机最大爆发压力已超过22 Mpa。活塞的机械疲劳损伤主要体现在销孔、环岸等部位。活塞环岸、销座及燃烧室等部位由于在较高的工作温度下承受着高频冲击作用的爆发压力,润滑状况较差,摩擦磨损,其他破坏可靠性的腐蚀磨损(缸套一环换向区、排气门/排气门座锥面等)、疲劳磨损(挺杆、轴瓦、齿轮表面等)、微动磨蚀(轴瓦钢背、飞轮压紧处、飞轮壳压紧处、湿缸套止口处等)、电蚀(火花塞电极等)和穴蚀(水泵叶轮等)这些
都是可靠性试验的主要目标,也是实施可靠性设计、试验研究的重点部位。 众所周知,在内燃机整机上进行零部件可靠性试验成本昂贵。本文将参照原有的可靠性试验方法,通过看一些关于可靠性的零部件加速寿命实验技术制定一种评价内燃机可靠性的考核规范,包括活塞机械疲劳试验和活塞热疲劳试验,可迅速做出其可靠性恰当的评价,可以降低研发成本、缩短研发时间。 一、试验目的 1通过理解内燃机可靠性评估,评定发动机的可靠性。 1.1了解评估的多种理论方法,如数学模型法、上下限法、相似设备法、蒙特卡洛法、故障分析( 包括故障模式影响分析和故障树分析) 等。并掌握故障分析法。 1.2学会可靠性试验评估,为进行可靠性设计奠定基础理论,为发动机及相关零部件提供测试、验证以及改进的技术支持。 2掌握可靠性试验方法 2.1掌握内燃机可靠性综合性试验及专项试验。综合性试验的考核对象是零件的可靠性、零件表面性状的变化和发动机性能的保持性;专项试验是超水温( 耐热性) 、超负荷、混合负荷、交变负荷循环、超爆发压力、超速等试验。 二、试验内容 1试验依据 参考的试验标准: GB /T 19055-2003 汽车发动机可靠性试验方法 GB /T 18297-2001 汽车发动机性能试验方法 JB/T 5112-1999 中小功率柴油机产品可靠性考核 2试验条件 一般试验条件: 2.1燃料及机油:采用制造厂所规定的牌号,柴油中不得有消烟添加剂。 2.2磨合:按制造厂规定的磨合规范进行。 2.3冷却系温度:水冷机的冷却液的出口温度控制在361 K±5K,必要时可减少温度允差。 2.4机油温度:按制造厂的规定或控制在368 K±5K,必要时可减少温度允差。2.5燃料温度:柴油温度控制在311 K±5K;汽油温度控制在298 K±5K。 2.6排气背压:按制造厂的规定或低于6.7 k Pa。 2.7发动机标准进气状态
【CN109946090A】车辆台架试验系统及其试验方法【专利】
(19)中华人民共和国国家知识产权局 (12)发明专利申请 (10)申请公布号 (43)申请公布日 (21)申请号 201910170121.3 (22)申请日 2019.03.05 (71)申请人 浙江吉利汽车研究院有限公司 地址 318000 浙江省台州市临海市城东闸 头 申请人 浙江吉利控股集团有限公司 (72)发明人 靳晓朴 董远明 刘如意 王海沛 (74)专利代理机构 广州三环专利商标代理有限 公司 44202 代理人 郝传鑫 贾允 (51)Int.Cl. G01M 17/007(2006.01) G01M 13/00(2019.01) (54)发明名称 车辆台架试验系统及其试验方法 (57)摘要 本发明公开了一种车辆台架试验系统及其 试验方法,该试验系统包括:激励机构,包括作动 器;承载机构,其一端与作动器的输出轴连接,另 一端承载待测试车辆的轮胎,以将作动器产生的 垂直向上的激励传递至待测试车辆;其中,承载 机构包括托板,托板包括水平设置的轮胎承载部 及向外扩张的轮胎复位部,轮胎承载部具有能够 平稳放置轮胎的平直的承载面,轮胎复位部具有 呈倾斜设置的复位面;复位面的表面光滑且与所 述承载面平缓过渡连接,以构成使得轮胎移动后 能够复位的凹槽。采用本发明,具有可使得轮胎 在运动过程降低托板对轮胎的磨损,且还可降低 对轮胎侧面的磨损,消除轮胎破损的风险,提高 试验过程的安全性,进而缩短整个试验周期优 点。权利要求书2页 说明书9页 附图3页CN 109946090 A 2019.06.28 C N 109946090 A
权 利 要 求 书1/2页CN 109946090 A 1.一种车辆台架试验系统,其特征在于,包括: 激励机构,包括作动器; 承载机构,其一端与所述作动器的输出轴连接,另一端承载待测试车辆的轮胎,以将所述作动器产生的垂直向上的激励传递至待测试车辆; 其中,所述承载机构包括托板,所述托板包括水平设置的轮胎承载部及向外扩张的轮胎复位部,所述轮胎承载部具有能够平稳放置轮胎的平直的承载面,所述轮胎复位部具有呈倾斜设置的复位面;所述复位面的表面光滑且与所述承载面平缓过渡连接,以构成能够容纳至少部分轮胎、且不与轮胎侧面发生干涉以及使得轮胎移动后能够复位的凹槽。 2.根据权利要求1所述的车辆台架试验系统,其特征在于,所述复位面为弧形面,所述弧形面的纵向弧线具有远离所述承载面的远端点,所述纵向弧线在所述远端点处的切线相对于承载面具有倾斜角,所述倾斜角的最大值为15-30°。 3.根据权利要求1所述的车辆台架试验系统,其特征在于,所述轮胎承载部与轮胎复位部一体成型,且构成下沉式凹槽结构; 所述承载面设有用于防止轮胎打滑的若干防滑细槽或防滑纹,所述防滑细槽为环形细槽或条形细槽或带图案的细槽。 4.根据权利要求1-3任一所述的车辆台架试验系统,其特征在于,还包括连接机构, 所述连接机构包括过渡件、第一连接件和第二连接件,所述过渡件的一端通过所述第一连接件与所述作动器的输出轴向下可拆卸连接,所述过渡件的另一端通过所述第二连接件与所述托板上背对承载面的一侧可拆卸连接。 5.根据权利要求4所述的车辆台架试验系统,其特征在于,所述第二连接件向上可拆卸地安装于所述过渡件上,且所述第二连接件靠近托板的的端部置于所述托板的内部; 所述托板上靠近所述过渡件的一侧设有供所述第一连接件插入的凹口槽,且所述第一连接件的头部与凹口槽的底部之间留有间隙。 6.根据权利要求4所述的车辆台架试验系统,其特征在于,所述承载机构还包括轮胎夹紧件,所述轮胎复位部上设有若干用于安装所述轮胎夹紧件的安装孔; 所述第二连接件为螺栓,且所述螺栓的紧固力矩大于等于70N.m。 7.根据权利要求1-3任一所述的车辆台架试验系统,其特征在于,还包括位移检测装置和试验控制器; 所述位移检测装置与待测试车辆的车身连接,用于检测待测试车辆在水平方向上跳动的偏移量; 所述试验控制器与作动器连接,用于若判断所接收的偏移量超过预设保护区间,则控制所述作动器停止提供激励。 8.根据权利要求7所述的车辆台架试验系统,其特征在于,还包括数据采集仪, 所述数据采集仪一端与所述位移检测装置连接,另一端与所述试验控制器连接,用于采集所述位移传感器所检测的偏移量数据并发送给试验控制器。 9.根据权利要求7或8所述的车辆台架试验系统,其特征在于,所述位移检测装置包括分别检测待测试车辆在第一方向和第二方向上的偏移量的第一位移检测组件和第二位移检测组件, 所述第一位移移检测组件和第二位移检测组件均包括位移传感器和固定座,所述位移 2
汽车电动真空泵性能要求及台架试验方法编制说明
汽车电动真空泵性能要求及台架试验方法(征求意见稿) 编制说明 1工作简况 1.1任务来源 工业和信息化部 2010 年 5 月 29 日印发的 2010 年第一批行业标准修订计划,项目编号为 2010-1883T-QC。 1.2主要工作过程 标准计划下达后,标准起草牵头单位浙江万安科技股份有限公司(以下简称“万安科技”)根据全国汽车标准化技术委员会和全国汽车标准化技术委员会制动分技术委员会要求,向国内部分主机厂和零部件生产企业发出邀请函,根据回函情况,最后确定邀请北京汽车集团有限公司(以下简称“北汽集团”)和安徽江淮汽车股份有限公司(以下简称“安徽江淮”)两家公司为标准编制工作小组参与单位。 2010 年 7 月,根据北汽集团和安徽江淮的回函,成立了由浙江万安科技股份有限公司、北京汽车集团有限公司和安徽江淮汽车股份有限公司组成的《电动真空泵性能要求及台架试验方法》标准起草小组。其中,万安科技作为标准的主起草单位,负责标准主体的编制、实验项目的验证及实验数据的处理分析工作。北汽集团和安徽江淮作为参与起草单位,负责反馈电动真空泵在整车运行中的工作情况及相关支持性工作。 根据标准起草工作需要和各起草参与单位实际情况,确定由李小攀、唐胜男、钟焕祥(万安科技)、詹文章(北汽集团)、董良(安徽江淮)等组成标准起草小组,李小攀任起草小组组长,负责标准编制过程总体规划工作,唐胜男负责标准主要技术文件的编写工作,钟焕祥主要负责技术支持,为标准的编制提供实验数据。詹文章和董良作为主机厂相关人员,主要负责标准的技术审查工作,确保标准中涉及的各项技术指标符合主机厂使用要求。 根据标准起草小组工作内容的分配,万安科技利用一年左右的时间完成了电动真空泵基本性能测试、耐久性试验、振动试验、噪声试验及盐雾腐蚀试验等试验的全部试验过程及试验数据的整理分析工作。于 2011 年 6 月编制完成了《电动真空泵性能要求及台架试验方法》标准初稿。该标准初稿主要包含电动真空泵、湿式真空泵、抽气速率、抽气效率和最低启动温度五个术语和定义,以及电动真空泵基本性能要求、极限真空度、工作电流、密封性、工作耐久性、振动耐久性、耐腐蚀性、低温启动性能、噪音和防护等级等十项性能指标及相对应的测试方法和相关试验设备、试验条件要求。 在标准初稿完成后,万安科技首先组织公司内部的标准化工作人员、电动真空泵工程师、技术检测员及制造单位人员对标准初稿进行讨论。在讨论会上,与会人员主要提出了如下问题: a)标准编制格式不符合 GB/T 1.1-2009 的相关要求;b)测试人员指出,在进行常温耐 久性测试时,电动真空泵连续工作一段时间之后,泵体 表面温度升高。从温度对内部零部件的影响及人员安全角度考虑,建议对产品最高工作温度进行控制,在标准中增加表面最高工作温度性能指标要求及相关试验。 根据起草小组第一次讨论会议建议,标准起草小组对标准初稿进行了相应的修改,并对新增项目的实验数据进行了采集、整理分析。根据试验结果,起草小组完成了标准初稿
电动助力转向试验台架设计
电动助力转向试验台架设计 第1章引言 从上世纪50年代出现了汽车助力转向系统以来,经历了机械式、液压式、电控液压式等阶段,80年代开始研制电子控制式电动助力转向系统,简称EPS(Electric Power Steering)。EPS在机械式助力转向系统的基础上,用输入轴的扭矩信号和汽车行驶速度信号控制助力电机,使之产生相应大小和方向的助力,获得最佳的转向特性。EPS用仅在转向时才工作的助力电机代替了在汽车运行过程中持续消耗能量的液压助力装置,简化了结构,降低了能耗,动态地适应不同的车速条件下助力的特性,操作轻便,稳定性和安全性好,同时,不存在油液泄露和液压软管不可回收等问题。可以说,EPS是集环保、节能、安全、舒适为一体的机电一体化设计。 在EPS研究伊始,因为成本问题难以投入商业生产,再实验室阶段停留了许多年。随着控制元件成本大幅度降低,使EPS的实际应用成为可能。1988年3月日本铃木公司率先开发出商用EPS,1993年本田汽车公司将EPS装备于爱克NSX跑车,取得良好的市场效果。不久,美国的德尔费公司生产的EPS被菲亚特轿车作为标准装备。此后,日本的大发、三菱、本田,美国的TRW,德国的ZF都相继研制出各自的EPS产品。1999年,奔驰和西门子开始投巨资开发EPS。据专家预测,到2010年,全世界30%的轿车将会安装EPS。 国产汽车的动力转向器目前还处在机械—液压阶段,EPS的研究尚处于起步阶段。仅有为数有限的高校对EPS进行过系统结构方案设计、系统建模和动力分析等探索性研究。 为了便于了解其性能,开始了电动助力转向性能实验台的研制。由于这种实验台还没有相关的行业标准,本文借鉴了普通汽车转向器总成台架以及汽车动力转向器总成台架实验方法,并针对电动助力转向器的特点进行了实验方法的设计和实验台架的设计。实验方法设计中根据普通转向器以及汽车动力转向器总成台架实验方法中提到的几项常规实验和重要性能实验,结合现有的技术及设备条件进行归纳总结,确定八项功能实验,测定十项性能,以及进行可靠性实验,并规
QCT29096—92汽车转向器总成台架试验方法
QC T 29096—92汽车转向器总成台架试验方法 汽车转向器总成台架试验方法 1主题内容与适用范畴 本标准规定了汽车转向器总成台架试验方法。 本标准适用于蜗杆滚轮式、循环球式、蜗杆指销式及齿轮齿条式汽车转向器 总成。 本标准不适用于动力转向器。 2总则 2.1本标准包括下列三种试验: a.性能试验 b.强度试验 c.疲劳寿命试验 2.2产品在进行性能和疲劳寿命试验前,应在下述工况下进行磨合: a.输入轴转角不小于全转角的90%; b.加在转向摇臂轴或齿条上的载荷,为额定输出扭矩或额定输出力的40%; c.循环次数不低于1.5X 103次; d.磨合时,输入轴的转速不大于10r/ min; e.磨合后更换润滑油。 2.3转向器试验时,在设计规定的条件下进行润滑。 2.4有专门要求的转向器,可由有关部门在此基础上另作补充规定。 3性能检验 3.1试验项目 3.1. 1输入轴全转角 3.1. 2传动比特性
3.1. 3传动间隙特性
3. 1. 4 传动效率特性 3. 1. 5 转动力矩 3. 1. 6 刚性 3. 2 输入轴全转角的测定 旋转输入轴,从一极端位置至另一极端位置,测出总圈数。 3.3传动比特性的测定 3讪3传动比特性的测定 3.3.1. 角传动比运算公式如下: 如]角传动比& 3.3. 1. 2测定范畴不小于输入轴全转角的的90%。 3. 3. 1. 3测量点间隔:输入轴转角增量不大于45°;变速比转向器输入轴 转角增量不大于18°。 3. 3. 1. 4测定方法: 驱动输入轴,测出输入轴转角和转向摇臂轴相应转角,取其增量,代入公式 (1),可得出角传动比。输入轴转角的测量误差不大于10',转向摇 臂轴转角的 误差不大于1.5'测量结果按附录訝*-1及附录图」T的格式给出。 -3」」3 . -2亠线角传动比的测定P 3 3?:珥线角传动比运算公式如下: 3. 3. 2. 2测定范畴不小于输入轴全转角的90%。 3. 3. 2. 3测量点间隔:输入轴转角增量不大于45 °;变速比转向器输入转角 增量不大于18°。 3. 3. 2. 4测定方法: 驱动输入轴,测出输入轴转角和齿条相应位移,取其增量,代入公式(2), 可得出线角传动比。输入轴转角的测量误差不大于10',齿条位移的 测量误差不 大于0.01mm。测量结果按附录表2及附录图2的格式给出。 3. 4传动间隙特性的测定
乘用车悬架系统台架试验标准规范
乘用车悬架系统台架试验规范 1 范围 本标准规定了乘用车悬架系统台架试验规范。 本标准适用于基础(新)底盘平台结构乘用车前、后悬架系统台架试验。对于在基础平台上延伸车型(如油改电),若轴荷增加<10%,悬架系统的强度及耐久性可视同原基础平台车,若轴荷增加≥10%,悬架系统的强度及耐久性可参照使用。 2 规范性引用文件 无 3 术语和定义 下列术语和定义适用于本标准。 3.1 麦弗逊悬架 mcPherson suspension 汽车独立悬架的一种结构类型,普遍应用于前悬架。由滑柱、控制臂、副车架及稳定杆等部件组成。 3.2 双叉臂悬架 double wishbone suspension 汽车独立悬架的一种结构类型,适应于前后悬架。由滑柱、上控制臂、下控制臂、副车架及稳定杆等部件组成。 3.3 多连杆悬架 multilink rear suspension 汽车独立悬架的一种结构类型,适应于后悬架。是指单边由三根或三根以上连接拉杆构成,能够提供多个方向的控制力,使轮胎具有更加可靠的行驶轨迹的悬架机构。 3.4 扭力梁后悬架 torsion beam rear suspension 汽车半独立悬架的一种结构类型,适应于后悬架。是通过一个扭力梁来平衡左右车轮的上下跳动,以减小车辆的摇晃,保持车辆的平稳性。 3.5 整体桥式非独立悬架 integral axle non independent suspension 汽车非独立悬架一种结构类型,在乘用车领域多用于偏重越野的SUV车型。通过一根硬轴将左右两个车轮相连。
3.6 验证样件 validation sample 试验过程中需要验证的工程样件,应是正式工装制造的样件。验证样件经过一项台架耐久试验循环后不可重复使用。 3.7 非验证样件 nonvalidation sample 试验过程中不需要验证的样件,在试验中可重复使用。 4 符号(代号、缩略语) 下列符号(代号、缩略语)适用于本文件。 g——重力加速度,单位为m/s2。 G——满载条件下车轮轮荷。 5 试验设备及工装要求 试验设备采用双通道柔性耐久试验台。试验设备载荷传感器应第三方校准,符合试验要求。试验过程中加载方向应与试验要求保持一致;耐久性试验中加载方式应采用连续加载方式,最大载荷的误差范围应在±5%以内;试验中连接部位所用的工装的刚度应不小于样件刚度的10倍。 6 耐久性能要求 6.1 纵向力耐久 按照8.1进行试验,悬架系统各验证零部件(除胶套外)在20万次试验后,不允许出现裂纹;紧固件不允许出现松动,松脱力矩大于初始拧紧力矩70%;40万次不允许出现严重塑性变形或断裂现象(裂纹超过10mm)。 6.2 侧向力耐久 按照8.2进行试验,悬架系统各验证零部件(除胶套外)在20万次试验后,不允许出现裂纹;紧固件不允许出现松动,松脱力矩大于初始拧紧力矩70%;40万次不允许出现严重塑性变形或断裂现象(裂纹超过10mm)。 6.3 同向垂直力耐久 按照8.3进行试验,悬架系统各验证零部件(除胶套外)在20万次试验后,不允许出现裂纹;紧固件不允许出现松动,松脱力矩大于初始拧紧力矩70%;40万次不允许出现严重塑性变形或断裂现象(裂纹超过10mm)。 6.4 异向垂直耐久 对于独立悬架结构如麦弗逊前悬架、双叉臂悬架及多连杆后悬架等:按照8.4进行试验,悬架系统各验证零部件(除胶套外)在20万次试验后,不允许出现裂纹;紧固件不允许出现松动,松脱力矩大于初始拧紧力矩70%。
货车、客车制动器台架试验方法-QC-T-479-1999
中华人民共和国国家标准 QC/T 479一1999 货车、客车制动器台架试验方法代替GB/T 12780一91 1 主题内容与适用范围 本标准规定了货车、客车的制动器总成(以下简称制动器)台架试验的试验项目、方法及程序。 本标准适用于总质量为1800kg至30000kg的货车、客车液力驱动或气力驱动的行车制动器。 2 引用标准 GB 3730.l汽车和半挂车的木语和定义车辆类型 GB 5620.1~5620.2汽车和挂车制动名词术语及其定义 JB 3936汽车制动器温度测量和热电偶安装 3 术语 3.1 制动周期 在连续制动过程中,从本次制动开始到下一次制动开始所经过的时间。 3.2 恒定输入方式 在一次制动过程中,使输入管路压力保持不变的控制方式。 3.3 恒定输出方式 在一次制动过程中,使被试制动器输出的制动力矩保持不变的控制方式。 3.4 制动器初温 开始制动时制动鼓(盘)或制动衬片(衬块)的温度,当多个制动器同时试验时,以其中温度最高者为准。
3.5 最大制动力矩 3.6 最小制动力矩 3.7 平均制动力矩 指一次制动过程中的上制动过程,制动力矩与制动时间所围的面积,除以主制动时间所得的纵坐标值。 3.8 制动时间 制动器作用的时间包括制动力增长时间,主制动时间、放松时间。
3.9 拖磨 在不切断输入动力情况下进行制动。 4 符号 5 试验项目 5.1 制动器效能试验 5.2 制动器热衰退恢复试验 5.3 制动器噪声测定 5.4 制动衬片/衬块磨损试验 6 试验条件 6.1 试验设备 惯性式试验设备(单端或双端)及测量记录仪器。 6.2 被试制动器应为符合图纸及技术文件规定的合格制动器。 6.3 试验台转动惯量的确定 车辆总质量加上旋转部分当量修正值,然后把相当于该质量的转动惯量按各轴制动力分配比分配。旋转部分的修正值取空车质量的7%。所选飞轮片的转动惯量(应考虑试验台旋转部分的惯量)允差±5%。
发动机试验台架方案DOC
试验室柴油发动机试验台架 技 术 方 案 xxxx公司 2013年xx月xx日
公司 公司是一家拥有完善的自动化控制系统产品开发、生产、销售、服务结构体系的企业,本公司专业从事工业自动化系统、建筑物自动化监控系统、智能小区管理系统的设计、产品生产、工程安装、系统调试、技术支持等一系列服务。 本公司技术实力雄厚、工程经验丰富、质量优良,有一批具有专业自控技术和软件经验的一流技术人员,能为用户提供高性价比自动化产品一体化解决方案。本公司的产品以其技术先进、开放灵活、高性价比的特点,已经在化工、冶金、电力、电子、测控、楼宇自控等领域得到广泛的应用。
一、台架试验室规划 1、试验室布置 2、供电(气)系统 3、冷却水系统(测功机冷却水系统,发动机冷却水系统) 4、通风系统 5、发动机进气与排气系统 6、消声与隔震 7、燃油,机油供给系统 8、安全防范(消防)与图像监控系统 9、测功机、油耗仪、烟度仪 10、计算机测试系统 二、试验目的与依据 2.1目的 安装在试验台上的发动机能模拟标准的使用条件或尽可能地接近标准使用条件;便于安装、调整、检查和更换发动机;有良好的通风、消音、消烟、隔振设施,尽可能改善试验人员的工作条件。 通过对台架的设计、制造、安装,完成发动机出厂测试试验,出厂试验基于发动机在各种试验工况下监控其运行参数,与发动机出厂试验规范数据对比,检查测试数据有效性完成出厂试验,生成出厂测试报告。试验过程记录数据项目包括以下: 1、发动机磨合 2、发动机额定工况 3、发动机最大扭矩工况 4、电子工况
5、怠速工况 测试参数包括以下 发动机的转速、扭矩、油耗、温度、压力等参数的测量精度不低于标准中规定的要求试验台一体原则,能完成多功能的整体试验。 2.2依据标准 《发动机性能试验方法》GB/T18297-2001 《发动机可靠性试验方法》GB/T19055-2003 《工业自动化仪表工程施工及验收规范》(GBT 93-86) 《自动化仪表安装工程质量检验标准》(GBJ 132-90) 《电器装置安装工程电缆线路施工及验收规范》(GB 50168-92) 《大楼通用综合布线系统》(YD/T925.1-97) 《电气装置安装工程施工及验收规范》(GB50254-50259-96)