压铸件常缺陷原因及解决方法
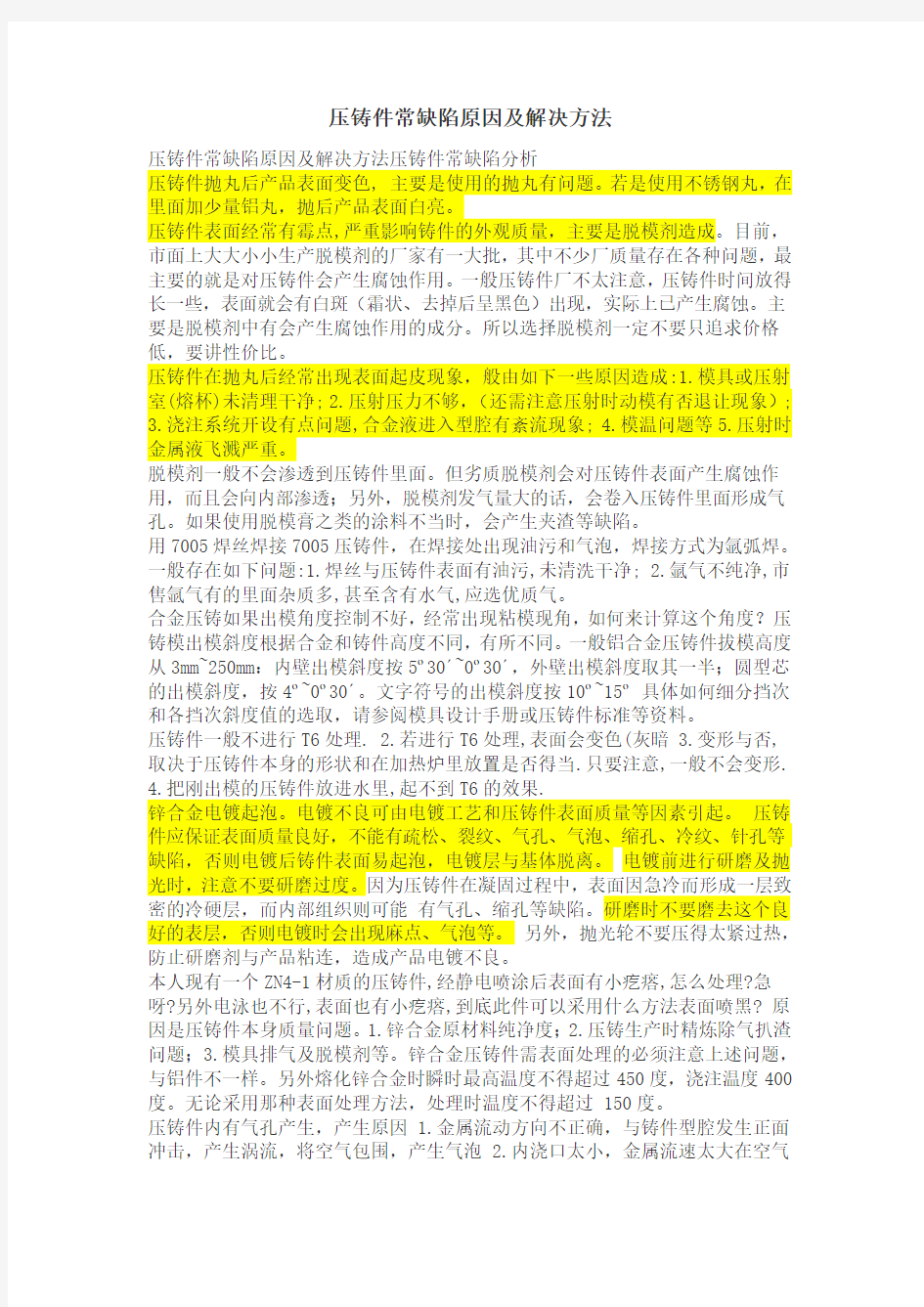
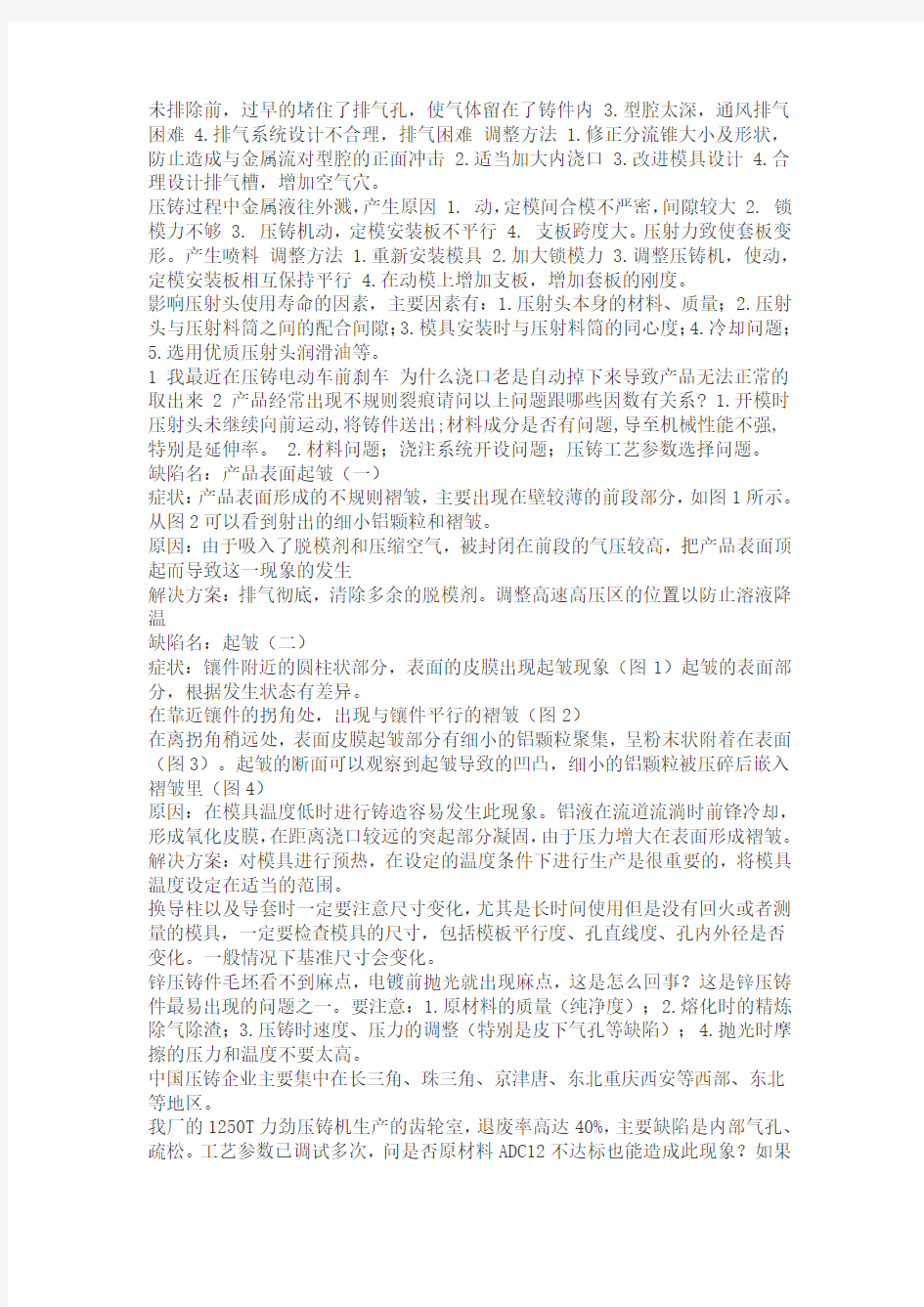
压铸件常缺陷原因及解决方法
压铸件常缺陷原因及解决方法压铸件常缺陷分析
压铸件抛丸后产品表面变色, 主要是使用的抛丸有问题。若是使用不锈钢丸,在里面加少量铝丸,抛后产品表面白亮。
压铸件表面经常有霉点,严重影响铸件的外观质量,主要是脱模剂造成。目前,市面上大大小小生产脱模剂的厂家有一大批,其中不少厂质量存在各种问题,最主要的就是对压铸件会产生腐蚀作用。一般压铸件厂不太注意,压铸件时间放得长一些,表面就会有白斑(霜状、去掉后呈黑色)出现,实际上已产生腐蚀。主要是脱模剂中有会产生腐蚀作用的成分。所以选择脱模剂一定不要只追求价格低,要讲性价比。
压铸件在抛丸后经常出现表面起皮现象,般由如下一些原因造成:1.模具或压射室(熔杯)未清理干净; 2.压射压力不够,(还需注意压射时动模有否退让现象);
3.浇注系统开设有点问题,合金液进入型腔有紊流现象;
4.模温问题等
5.压射时金属液飞溅严重。
脱模剂一般不会渗透到压铸件里面。但劣质脱模剂会对压铸件表面产生腐蚀作用,而且会向内部渗透;另外,脱模剂发气量大的话,会卷入压铸件里面形成气孔。如果使用脱模膏之类的涂料不当时,会产生夹渣等缺陷。
用7005焊丝焊接7005压铸件,在焊接处出现油污和气泡,焊接方式为氩弧焊。一般存在如下问题:1.焊丝与压铸件表面有油污,未清洗干净; 2.氩气不纯净,市售氩气有的里面杂质多,甚至含有水气,应选优质气。
合金压铸如果出模角度控制不好,经常出现粘模现角,如何来计算这个角度?压铸模出模斜度根据合金和铸件高度不同,有所不同。一般铝合金压铸件拔模高度从3mm~250mm:内壁出模斜度按5o30′~0o30′,外壁出模斜度取其一半;圆型芯的出模斜度,按4o~0o30′。文字符号的出模斜度按10o~15o具体如何细分挡次和各挡次斜度值的选取,请参阅模具设计手册或压铸件标准等资料。
压铸件一般不进行T6处理. 2.若进行T6处理,表面会变色(灰暗 3.变形与否,取决于压铸件本身的形状和在加热炉里放置是否得当.只要注意,一般不会变形.
4.把刚出模的压铸件放进水里,起不到T6的效果.
锌合金电镀起泡。电镀不良可由电镀工艺和压铸件表面质量等因素引起。压铸件应保证表面质量良好,不能有疏松、裂纹、气孔、气泡、缩孔、冷纹、针孔等缺陷,否则电镀后铸件表面易起泡,电镀层与基体脱离。电镀前进行研磨及抛光时,注意不要研磨过度。因为压铸件在凝固过程中,表面因急冷而形成一层致密的冷硬层,而内部组织则可能有气孔、缩孔等缺陷。研磨时不要磨去这个良好的表层,否则电镀时会出现麻点、气泡等。另外,抛光轮不要压得太紧过热,防止研磨剂与产品粘连,造成产品电镀不良。
本人现有一个ZN4-1材质的压铸件,经静电喷涂后表面有小疙瘩,怎么处理?急呀?另外电泳也不行,表面也有小疙瘩,到底此件可以采用什么方法表面喷黑? 原因是压铸件本身质量问题。1.锌合金原材料纯净度;2.压铸生产时精炼除气扒渣问题;3.模具排气及脱模剂等。锌合金压铸件需表面处理的必须注意上述问题,与铝件不一样。另外熔化锌合金时瞬时最高温度不得超过450度,浇注温度400度。无论采用那种表面处理方法,处理时温度不得超过 150度。
压铸件内有气孔产生,产生原因 1.金属流动方向不正确,与铸件型腔发生正面冲击,产生涡流,将空气包围,产生气泡 2.内浇口太小,金属流速太大在空气
未排除前,过早的堵住了排气孔,使气体留在了铸件内 3.型腔太深,通风排气困难 4.排气系统设计不合理,排气困难调整方法 1.修正分流锥大小及形状,防止造成与金属流对型腔的正面冲击 2.适当加大内浇口 3.改进模具设计 4.合理设计排气槽,增加空气穴。
压铸过程中金属液往外溅,产生原因 1. 动,定模间合模不严密,间隙较大 2. 锁模力不够 3. 压铸机动,定模安装板不平行 4. 支板跨度大。压射力致使套板变形。产生喷料调整方法 1.重新安装模具 2.加大锁模力 3.调整压铸机,使动,定模安装板相互保持平行 4.在动模上增加支板,增加套板的刚度。
影响压射头使用寿命的因素,主要因素有:1.压射头本身的材料、质量;2.压射头与压射料筒之间的配合间隙;3.模具安装时与压射料筒的同心度;4.冷却问题;
5.选用优质压射头润滑油等。
1 我最近在压铸电动车前刹车为什么浇口老是自动掉下来导致产品无法正常的取出来
2 产品经常出现不规则裂痕请问以上问题跟哪些因数有关系? 1.开模时压射头未继续向前运动,将铸件送出;材料成分是否有问题,导至机械性能不强,特别是延伸率。 2.材料问题;浇注系统开设问题;压铸工艺参数选择问题。
缺陷名:产品表面起皱(一)
症状:产品表面形成的不规则褶皱,主要出现在壁较薄的前段部分,如图1所示。从图2可以看到射出的细小铝颗粒和褶皱。
原因:由于吸入了脱模剂和压缩空气,被封闭在前段的气压较高,把产品表面顶起而导致这一现象的发生
解决方案:排气彻底,清除多余的脱模剂。调整高速高压区的位置以防止溶液降温
缺陷名:起皱(二)
症状:镶件附近的圆柱状部分,表面的皮膜出现起皱现象(图1)起皱的表面部分,根据发生状态有差异。
在靠近镶件的拐角处,出现与镶件平行的褶皱(图2)
在离拐角稍远处,表面皮膜起皱部分有细小的铝颗粒聚集,呈粉末状附着在表面(图3)。起皱的断面可以观察到起皱导致的凹凸,细小的铝颗粒被压碎后嵌入褶皱里(图4)
原因:在模具温度低时进行铸造容易发生此现象。铝液在流道流淌时前锋冷却,形成氧化皮膜,在距离浇口较远的突起部分凝固,由于压力增大在表面形成褶皱。解决方案:对模具进行预热,在设定的温度条件下进行生产是很重要的,将模具温度设定在适当的范围。
换导柱以及导套时一定要注意尺寸变化,尤其是长时间使用但是没有回火或者测量的模具,一定要检查模具的尺寸,包括模板平行度、孔直线度、孔内外径是否变化。一般情况下基准尺寸会变化。
锌压铸件毛坯看不到麻点,电镀前抛光就出现麻点,这是怎么回事?这是锌压铸件最易出现的问题之一。要注意:1.原材料的质量(纯净度);2.熔化时的精炼除气除渣;3.压铸时速度、压力的调整(特别是皮下气孔等缺陷);4.抛光时摩擦的压力和温度不要太高。
中国压铸企业主要集中在长三角、珠三角、京津唐、东北重庆西安等西部、东北等地区。
我厂的1250T力劲压铸机生产的齿轮室,退废率高达40%,主要缺陷是内部气孔、疏松。工艺参数已调试多次,问是否原材料ADC12不达标也能造成此现象?如果
工艺参数已反复调试过,仍有问题,那么主要是浇注系统开设有问题。原材料问题是次要的。
在生产汽车配件一样壳体时抽芯处老是出现凹槽请问下有些什么原因?1.浇注系统、排溢系统开设问题;2.压铸工艺参数选择问题;3.原材料质量等。
如何检验锌合金压铸件是否合格?和抛光后如何检验?我们在电镀后的麻点及起泡一直得不到解决锌合金压铸稍不注意就会出现这个问题。要从以下几个方面着手:1.原材料要纯净;2.熔炼时要精炼除渣;3.严格压铸工艺(建议:压速低一些,压力大一些);4.注意脱模剂等材料的质量。另外,进行抛光等工序时,也要加以注意。至于检验,应着重内部气孔和渣孔等缺陷。抛光后表面要细看,有些小点很易忽视。
压铸件在去浇口或冲孔时容易因分层掉肉,在内浇口与压铸件接合处加一个小倒角,会有改善。
压铸产品经过洗水烤干后会起泡,原因是压铸件皮下气孔烘烤后膨胀所至。建议烘干温度在150度以下。
LM6(SA)或AL SI 12(CU)这2种材料分别是英国标准和德国标准的表示方法,相当于国标的YL102铝合金。
1. 铝压铸件在(不锈钢)抛丸以后可以进行阳极氧化处理。
2.根据产品需要进行阳极氧化处理。它可以增加铝压铸件表面抗氧化、腐蚀等功能。
模具费=设计费+材料费(特别是型芯型腔用的热模钢)+加工费(先计算工时,然后折算成费用)+热处理费+表面处理费+税金. 根据图纸上零件大小及要求,从型芯型腔用的材料算起. 铝压铸件的单价=材料费(需加上烧损量)+合模费(根据压铸机类型和大小,压铸件的复杂程度)+模具费(折算到每个零件上)+税金. 这是一种计算方法.
铝压铸产品抛光后出现小针孔,怎么解决?1.压铸生产时,就要注意表面质量;
2.抛光研磨时加压不要太大,注意清理粉屑。
铝产品一面会镀上一面镀不上为什么? 如果压铸件表面未粘附上什么有害物,那就让电镀单位查找原因.
压铸铝合金都可以阳极氧化处理,但处理后一般呈黑灰色。若要处理成本色或其它颜色,可用ADC6压铸铝合金。因阳极氧化属于普通表面处理,找一般正规电镀企业即可。
压铸锌合金材料熔炼损耗率视选用的原材料不同,一般用2~5%来计算。
耐压问题:使用真空压铸一般能够达到此要求。若用普通压铸模生产,只要注意:1.模具浇、排系统开设合理;2. 压铸工艺掌握得当,(速度尽量慢,以能成型为标准;增压压力要大;脱模剂挥发要小等),产品合格率还是很高的。
A6061-T6的铝合金是否可压铸,此牌号铝合金不属于压铸铝合金。但近年来,不少外商定单中,其图纸标示为6061铝合金,压铸是可以的,但T6就不行(T6为淬火+完全人工时效)。除非确保压铸件内部无气孔。
压铸过程中铝合金材料损耗有哪几方面的?另外104的铝压铸好后用来镀青古铜表面为啥有起泡??压铸过程中铝合金材料损耗有以下几方面: 1.熔炼中的烧损及挥发; 2.除渣时带出; 3. 压铸件飞边毛刺; 4.浇口、料饼、废铸件等重熔的烧损及挥发; 5.因机床、模具等原因,造成压铸件重量增加。起泡是压铸件皮下气孔受热膨胀所至。在表面处理过程中,温度最好不要超过180℃,否则就易起泡。
二级速度是在压射头封住浇料口时开始,按工艺需要调节,是我们平时所说的压
射速度的主要部分。
压铸日件常缺陷原因及解决方法压铸件常缺陷分析
压铸件抛丸后产品表面变色, 主要是使用的抛丸有问题。若是使用不锈钢丸,在里面加少量铝丸,抛后产品表面白亮。
压铸件表面经常有霉点,严重影响铸件的外观质量,主要是脱模剂造成。目前,市面上大大小小生产脱模剂的厂家有一大批,其中不少厂质量存在各种问题,最主要的就是对压铸件会产生腐蚀作用。一般压铸件厂不太注意,压铸件时间放得长一些,表面就会有白斑(霜状、去掉后呈黑色)出现,实际上已产生腐蚀。主要是脱模剂中有会产生腐蚀作用的成分。所以选择脱模剂一定不要只追求价格低,要讲性价比。
压铸件在抛丸后经常出现表面起皮现象,般由如下一些原因造成:1.模具或压射室(熔杯)未清理干净; 2.压射压力不够,(还需注意压射时动模有否退让现象);
3.浇注系统开设有点问题,合金液进入型腔有紊流现象;
4.模温问题等
5.压射时金属液飞溅严重。
脱模剂一般不会渗透到压铸件里面。但劣质脱模剂会对压铸件表面产生腐蚀作用,而且会向内部渗透;另外,脱模剂发气量大的话,会卷入压铸件里面形成气孔。如果使用脱模膏之类的涂料不当时,会产生夹渣等缺陷。
用7005焊丝焊接7005压铸件,在焊接处出现油污和气泡,焊接方式为氩弧焊。一般存在如下问题:1.焊丝与压铸件表面有油污,未清洗干净; 2.氩气不纯净,市售氩气有的里面杂质多,甚至含有水气,应选优质气。
合金压铸如果出模角度控制不好,经常出现粘模现角,如何来计算这个角度?压铸模出模斜度根据合金和铸件高度不同,有所不同。一般铝合金压铸件拔模高度从3mm~250mm:内壁出模斜度按5o30′~0o30′,外壁出模斜度取其一半;圆型芯的出模斜度,按4o~0o30′。文字符号的出模斜度按10o~15o具体如何细分挡次和各挡次斜度值的选取,请参阅模具设计手册或压铸件标准等资料。
压铸件一般不进行T6处理. 2.若进行T6处理,表面会变色(灰暗 3.变形与否,取决于压铸件本身的形状和在加热炉里放置是否得当.只要注意,一般不会变形.
4.把刚出模的压铸件放进水里,起不到T6的效果.
锌合金电镀起泡。电镀不良可由电镀工艺和压铸件表面质量等因素引起。压铸件应保证表面质量良好,不能有疏松、裂纹、气孔、气泡、缩孔、冷纹、针孔等缺陷,否则电镀后铸件表面易起泡,电镀层与基体脱离。电镀前进行研磨及抛光时,注意不要研磨过度。因为压铸件在凝固过程中,表面因急冷而形成一层致密的冷硬层,而内部组织则可能有气孔、缩孔等缺陷。研磨时不要磨去这个良好的表层,否则电镀时会出现麻点、气泡等。另外,抛光轮不要压得太紧过热,防止研磨剂与产品粘连,造成产品电镀不良。
本人现有一个ZN4-1材质的压铸件,经静电喷涂后表面有小疙瘩,怎么处理?急呀?另外电泳也不行,表面也有小疙瘩,到底此件可以采用什么方法表面喷黑? 原因是压铸件本身质量问题。1.锌合金原材料纯净度;2.压铸生产时精炼除气扒渣问题;3.模具排气及脱模剂等。锌合金压铸件需表面处理的必须注意上述问题,与铝件不一样。另外熔化锌合金时瞬时最高温度不得超过450度,浇注温度400度。无论采用那种表面处理方法,处理时温度不得超过 150度。
压铸件内有气孔产生,产生原因 1.金属流动方向不正确,与铸件型腔发生正面冲击,产生涡流,将空气包围,产生气泡 2.内浇口太小,金属流速太大在空气未排除前,过早的堵住了排气孔,使气体留在了铸件内 3.型腔太深,通风排气
困难 4.排气系统设计不合理,排气困难调整方法 1.修正分流锥大小及形状,防止造成与金属流对型腔的正面冲击 2.适当加大内浇口 3.改进模具设计 4.合理设计排气槽,增加空气穴。
压铸过程中金属液往外溅,产生原因 1. 动,定模间合模不严密,间隙较大 2. 锁模力不够 3. 压铸机动,定模安装板不平行 4. 支板跨度大。压射力致使套板变形。产生喷料调整方法 1.重新安装模具 2.加大锁模力 3.调整压铸机,使动,定模安装板相互保持平行 4.在动模上增加支板,增加套板的刚度。
影响压射头使用寿命的因素,主要因素有:1.压射头本身的材料、质量;2.压射头与压射料筒之间的配合间隙;3.模具安装时与压射料筒的同心度;4.冷却问题;
5.选用优质压射头润滑油等。
1 我最近在压铸电动车前刹车为什么浇口老是自动掉下来导致产品无法正常的取出来
2 产品经常出现不规则裂痕请问以上问题跟哪些因数有关系? 1.开模时压射头未继续向前运动,将铸件送出;材料成分是否有问题,导至机械性能不强,特别是延伸率。 2.材料问题;浇注系统开设问题;压铸工艺参数选择问题。
缺陷名:产品表面起皱(一)
症状:产品表面形成的不规则褶皱,主要出现在壁较薄的前段部分,如图1所示。从图2可以看到射出的细小铝颗粒和褶皱。
原因:由于吸入了脱模剂和压缩空气,被封闭在前段的气压较高,把产品表面顶起而导致这一现象的发生
解决方案:排气彻底,清除多余的脱模剂。调整高速高压区的位置以防止溶液降温
缺陷名:起皱(二)
症状:镶件附近的圆柱状部分,表面的皮膜出现起皱现象(图1)起皱的表面部分,根据发生状态有差异。
在靠近镶件的拐角处,出现与镶件平行的褶皱(图2)
在离拐角稍远处,表面皮膜起皱部分有细小的铝颗粒聚集,呈粉末状附着在表面(图3)。起皱的断面可以观察到起皱导致的凹凸,细小的铝颗粒被压碎后嵌入褶皱里(图4)
原因:在模具温度低时进行铸造容易发生此现象。铝液在流道流淌时前锋冷却,形成氧化皮膜,在距离浇口较远的突起部分凝固,由于压力增大在表面形成褶皱。解决方案:对模具进行预热,在设定的温度条件下进行生产是很重要的,将模具温度设定在适当的范围。
换导柱以及导套时一定要注意尺寸变化,尤其是长时间使用但是没有回火或者测量的模具,一定要检查模具的尺寸,包括模板平行度、孔直线度、孔内外径是否变化。一般情况下基准尺寸会变化。
锌压铸件毛坯看不到麻点,电镀前抛光就出现麻点,这是怎么回事?这是锌压铸件最易出现的问题之一。要注意:1.原材料的质量(纯净度);2.熔化时的精炼除气除渣;3.压铸时速度、压力的调整(特别是皮下气孔等缺陷);4.抛光时摩擦的压力和温度不要太高。
中国压铸企业主要集中在长三角、珠三角、京津唐、东北重庆西安等西部、东北等地区。
我厂的1250T力劲压铸机生产的齿轮室,退废率高达40%,主要缺陷是内部气孔、疏松。工艺参数已调试多次,问是否原材料ADC12不达标也能造成此现象?如果工艺参数已反复调试过,仍有问题,那么主要是浇注系统开设有问题。原材料问
题是次要的。
在生产汽车配件一样壳体时抽芯处老是出现凹槽请问下有些什么原因?1.浇注系统、排溢系统开设问题;2.压铸工艺参数选择问题;3.原材料质量等。
如何检验锌合金压铸件是否合格?和抛光后如何检验?我们在电镀后的麻点及起泡一直得不到解决锌合金压铸稍不注意就会出现这个问题。要从以下几个方面着手:1.原材料要纯净;2.熔炼时要精炼除渣;3.严格压铸工艺(建议:压速低一些,压力大一些);4.注意脱模剂等材料的质量。另外,进行抛光等工序时,也要加以注意。至于检验,应着重内部气孔和渣孔等缺陷。抛光后表面要细看,有些小点很易忽视。
压铸件在去浇口或冲孔时容易因分层掉肉,在内浇口与压铸件接合处加一个小倒角,会有改善。
压铸产品经过洗水烤干后会起泡,原因是压铸件皮下气孔烘烤后膨胀所至。建议烘干温度在150度以下。
LM6(SA)或AL SI 12(CU)这2种材料分别是英国标准和德国标准的表示方法,相当于国标的YL102铝合金。
1. 铝压铸件在(不锈钢)抛丸以后可以进行阳极氧化处理。
2.根据产品需要进行阳极氧化处理。它可以增加铝压铸件表面抗氧化、腐蚀等功能。
模具费=设计费+材料费(特别是型芯型腔用的热模钢)+加工费(先计算工时,然后折算成费用)+热处理费+表面处理费+税金. 根据图纸上零件大小及要求,从型芯型腔用的材料算起. 铝压铸件的单价=材料费(需加上烧损量)+合模费(根据压铸机类型和大小,压铸件的复杂程度)+模具费(折算到每个零件上)+税金. 这是一种计算方法.
铝压铸产品抛光后出现小针孔,怎么解决?1.压铸生产时,就要注意表面质量;
2.抛光研磨时加压不要太大,注意清理粉屑。
铝产品一面会镀上一面镀不上为什么? 如果压铸件表面未粘附上什么有害物,那就让电镀单位查找原因.
压铸铝合金都可以阳极氧化处理,但处理后一般呈黑灰色。若要处理成本色或其它颜色,可用ADC6压铸铝合金。因阳极氧化属于普通表面处理,找一般正规电镀企业即可。
压铸锌合金材料熔炼损耗率视选用的原材料不同,一般用2~5%来计算。
耐压问题:使用真空压铸一般能够达到此要求。若用普通压铸模生产,只要注意:1.模具浇、排系统开设合理;2. 压铸工艺掌握得当,(速度尽量慢,以能成型为标准;增压压力要大;脱模剂挥发要小等),产品合格率还是很高的。
A6061-T6的铝合金是否可压铸,此牌号铝合金不属于压铸铝合金。但近年来,不少外商定单中,其图纸标示为6061铝合金,压铸是可以的,但T6就不行(T6为淬火+完全人工时效)。除非确保压铸件内部无气孔。
压铸过程中铝合金材料损耗有哪几方面的?另外104的铝压铸好后用来镀青古铜表面为啥有起泡??压铸过程中铝合金材料损耗有以下几方面: 1.熔炼中的烧损及挥发; 2.除渣时带出; 3. 压铸件飞边毛刺; 4.浇口、料饼、废铸件等重熔的烧损及挥发; 5.因机床、模具等原因,造成压铸件重量增加。起泡是压铸件皮下气孔受热膨胀所至。在表面处理过程中,温度最好不要超过180℃,否则就易起泡。
二级速度是在压射头封住浇料口时开始,按工艺需要调节,是我们平时所说的压射速度的主要部分。
压铸件常缺陷原因及解决方法压铸件常缺陷分析
压铸件抛丸后产品表面变色, 主要是使用的抛丸有问题。若是使用不锈钢丸,在里面加少量铝丸,抛后产品表面白亮。
压铸件表面经常有霉点,严重影响铸件的外观质量,主要是脱模剂造成。目前,市面上大大小小生产脱模剂的厂家有一大批,其中不少厂质量存在各种问题,最主要的就是对压铸件会产生腐蚀作用。一般压铸件厂不太注意,压铸件时间放得长一些,表面就会有白斑(霜状、去掉后呈黑色)出现,实际上已产生腐蚀。主要是脱模剂中有会产生腐蚀作用的成分。所以选择脱模剂一定不要只追求价格低,要讲性价比。
压铸件在抛丸后经常出现表面起皮现象,般由如下一些原因造成:1.模具或压射室(熔杯)未清理干净; 2.压射压力不够,(还需注意压射时动模有否退让现象);
3.浇注系统开设有点问题,合金液进入型腔有紊流现象;
4.模温问题等
5.压射时金属液飞溅严重。
脱模剂一般不会渗透到压铸件里面。但劣质脱模剂会对压铸件表面产生腐蚀作用,而且会向内部渗透;另外,脱模剂发气量大的话,会卷入压铸件里面形成气孔。如果使用脱模膏之类的涂料不当时,会产生夹渣等缺陷。
用7005焊丝焊接7005压铸件,在焊接处出现油污和气泡,焊接方式为氩弧焊。一般存在如下问题:1.焊丝与压铸件表面有油污,未清洗干净; 2.氩气不纯净,市售氩气有的里面杂质多,甚至含有水气,应选优质气。
合金压铸如果出模角度控制不好,经常出现粘模现角,如何来计算这个角度?压铸模出模斜度根据合金和铸件高度不同,有所不同。一般铝合金压铸件拔模高度从3mm~250mm:内壁出模斜度按5o30′~0o30′,外壁出模斜度取其一半;圆型芯的出模斜度,按4o~0o30′。文字符号的出模斜度按10o~15o具体如何细分挡次和各挡次斜度值的选取,请参阅模具设计手册或压铸件标准等资料。
压铸件一般不进行T6处理. 2.若进行T6处理,表面会变色(灰暗 3.变形与否,取决于压铸件本身的形状和在加热炉里放置是否得当.只要注意,一般不会变形.
4.把刚出模的压铸件放进水里,起不到T6的效果.
锌合金电镀起泡。电镀不良可由电镀工艺和压铸件表面质量等因素引起。压铸件应保证表面质量良好,不能有疏松、裂纹、气孔、气泡、缩孔、冷纹、针孔等缺陷,否则电镀后铸件表面易起泡,电镀层与基体脱离。电镀前进行研磨及抛光时,注意不要研磨过度。因为压铸件在凝固过程中,表面因急冷而形成一层致密的冷硬层,而内部组织则可能有气孔、缩孔等缺陷。研磨时不要磨去这个良好的表层,否则电镀时会出现麻点、气泡等。另外,抛光轮不要压得太紧过热,防止研磨剂与产品粘连,造成产品电镀不良。
本人现有一个ZN4-1材质的压铸件,经静电喷涂后表面有小疙瘩,怎么处理?急呀?另外电泳也不行,表面也有小疙瘩,到底此件可以采用什么方法表面喷黑? 原因是压铸件本身质量问题。1.锌合金原材料纯净度;2.压铸生产时精炼除气扒渣问题;3.模具排气及脱模剂等。锌合金压铸件需表面处理的必须注意上述问题,与铝件不一样。另外熔化锌合金时瞬时最高温度不得超过450度,浇注温度400度。无论采用那种表面处理方法,处理时温度不得超过 150度。
压铸件内有气孔产生,产生原因 1.金属流动方向不正确,与铸件型腔发生正面冲击,产生涡流,将空气包围,产生气泡 2.内浇口太小,金属流速太大在空气未排除前,过早的堵住了排气孔,使气体留在了铸件内 3.型腔太深,通风排气困难 4.排气系统设计不合理,排气困难调整方法 1.修正分流锥大小及形状,
防止造成与金属流对型腔的正面冲击 2.适当加大内浇口 3.改进模具设计 4.合理设计排气槽,增加空气穴。
压铸过程中金属液往外溅,产生原因 1. 动,定模间合模不严密,间隙较大 2. 锁模力不够 3. 压铸机动,定模安装板不平行 4. 支板跨度大。压射力致使套板变形。产生喷料调整方法 1.重新安装模具 2.加大锁模力 3.调整压铸机,使动,定模安装板相互保持平行 4.在动模上增加支板,增加套板的刚度。
影响压射头使用寿命的因素,主要因素有:1.压射头本身的材料、质量;2.压射头与压射料筒之间的配合间隙;3.模具安装时与压射料筒的同心度;4.冷却问题;
5.选用优质压射头润滑油等。
1 我最近在压铸电动车前刹车为什么浇口老是自动掉下来导致产品无法正常的取出来
2 产品经常出现不规则裂痕请问以上问题跟哪些因数有关系? 1.开模时压射头未继续向前运动,将铸件送出;材料成分是否有问题,导至机械性能不强,特别是延伸率。 2.材料问题;浇注系统开设问题;压铸工艺参数选择问题。
缺陷名:产品表面起皱(一)
症状:产品表面形成的不规则褶皱,主要出现在壁较薄的前段部分,如图1所示。从图2可以看到射出的细小铝颗粒和褶皱。
原因:由于吸入了脱模剂和压缩空气,被封闭在前段的气压较高,把产品表面顶起而导致这一现象的发生
解决方案:排气彻底,清除多余的脱模剂。调整高速高压区的位置以防止溶液降温
缺陷名:起皱(二)
症状:镶件附近的圆柱状部分,表面的皮膜出现起皱现象(图1)起皱的表面部分,根据发生状态有差异。
在靠近镶件的拐角处,出现与镶件平行的褶皱(图2)
在离拐角稍远处,表面皮膜起皱部分有细小的铝颗粒聚集,呈粉末状附着在表面(图3)。起皱的断面可以观察到起皱导致的凹凸,细小的铝颗粒被压碎后嵌入褶皱里(图4)
原因:在模具温度低时进行铸造容易发生此现象。铝液在流道流淌时前锋冷却,形成氧化皮膜,在距离浇口较远的突起部分凝固,由于压力增大在表面形成褶皱。解决方案:对模具进行预热,在设定的温度条件下进行生产是很重要的,将模具温度设定在适当的范围。
换导柱以及导套时一定要注意尺寸变化,尤其是长时间使用但是没有回火或者测量的模具,一定要检查模具的尺寸,包括模板平行度、孔直线度、孔内外径是否变化。一般情况下基准尺寸会变化。
锌压铸件毛坯看不到麻点,电镀前抛光就出现麻点,这是怎么回事?这是锌压铸件最易出现的问题之一。要注意:1.原材料的质量(纯净度);2.熔化时的精炼除气除渣;3.压铸时速度、压力的调整(特别是皮下气孔等缺陷);4.抛光时摩擦的压力和温度不要太高。
中国压铸企业主要集中在长三角、珠三角、京津唐、东北重庆西安等西部、东北等地区。
我厂的1250T力劲压铸机生产的齿轮室,退废率高达40%,主要缺陷是内部气孔、疏松。工艺参数已调试多次,问是否原材料ADC12不达标也能造成此现象?如果工艺参数已反复调试过,仍有问题,那么主要是浇注系统开设有问题。原材料问题是次要的。
在生产汽车配件一样壳体时抽芯处老是出现凹槽请问下有些什么原因?1.浇注系统、排溢系统开设问题;2.压铸工艺参数选择问题;3.原材料质量等。
如何检验锌合金压铸件是否合格?和抛光后如何检验?我们在电镀后的麻点及起泡一直得不到解决锌合金压铸稍不注意就会出现这个问题。要从以下几个方面着手:1.原材料要纯净;2.熔炼时要精炼除渣;3.严格压铸工艺(建议:压速低一些,压力大一些);4.注意脱模剂等材料的质量。另外,进行抛光等工序时,也要加以注意。至于检验,应着重内部气孔和渣孔等缺陷。抛光后表面要细看,有些小点很易忽视。
压铸件在去浇口或冲孔时容易因分层掉肉,在内浇口与压铸件接合处加一个小倒角,会有改善。
压铸产品经过洗水烤干后会起泡,原因是压铸件皮下气孔烘烤后膨胀所至。建议烘干温度在150度以下。
LM6(SA)或AL SI 12(CU)这2种材料分别是英国标准和德国标准的表示方法,相当于国标的YL102铝合金。
1. 铝压铸件在(不锈钢)抛丸以后可以进行阳极氧化处理。
2.根据产品需要进行阳极氧化处理。它可以增加铝压铸件表面抗氧化、腐蚀等功能。
模具费=设计费+材料费(特别是型芯型腔用的热模钢)+加工费(先计算工时,然后折算成费用)+热处理费+表面处理费+税金. 根据图纸上零件大小及要求,从型芯型腔用的材料算起. 铝压铸件的单价=材料费(需加上烧损量)+合模费(根据压铸机类型和大小,压铸件的复杂程度)+模具费(折算到每个零件上)+税金. 这是一种计算方法.
铝压铸产品抛光后出现小针孔,怎么解决?1.压铸生产时,就要注意表面质量;
2.抛光研磨时加压不要太大,注意清理粉屑。
铝产品一面会镀上一面镀不上为什么? 如果压铸件表面未粘附上什么有害物,那就让电镀单位查找原因.
压铸铝合金都可以阳极氧化处理,但处理后一般呈黑灰色。若要处理成本色或其它颜色,可用ADC6压铸铝合金。因阳极氧化属于普通表面处理,找一般正规电镀企业即可。
压铸锌合金材料熔炼损耗率视选用的原材料不同,一般用2~5%来计算。
耐压问题:使用真空压铸一般能够达到此要求。若用普通压铸模生产,只要注意:1.模具浇、排系统开设合理;2. 压铸工艺掌握得当,(速度尽量慢,以能成型为标准;增压压力要大;脱模剂挥发要小等),产品合格率还是很高的。
A6061-T6的铝合金是否可压铸,此牌号铝合金不属于压铸铝合金。但近年来,不少外商定单中,其图纸标示为6061铝合金,压铸是可以的,但T6就不行(T6为淬火+完全人工时效)。除非确保压铸件内部无气孔。
压铸过程中铝合金材料损耗有哪几方面的?另外104的铝压铸好后用来镀青古铜表面为啥有起泡??压铸过程中铝合金材料损耗有以下几方面: 1.熔炼中的烧损及挥发; 2.除渣时带出; 3. 压铸件飞边毛刺; 4.浇口、料饼、废铸件等重熔的烧损及挥发; 5.因机床、模具等原因,造成压铸件重量增加。起泡是压铸件皮下气孔受热膨胀所至。在表面处理过程中,温度最好不要超过180℃,否则就易起泡。
二级速度是在压射头封住浇料口时开始,按工艺需要调节,是我们平时所说的压射速度的主要部分。
常见铸件缺陷分析
常见铸件缺陷分析缺陷种类,缺陷名称生产原因 多肉类飞翅(飞边) 1.砂型表面不光洁,分型面不增整 2.合理操作xx准确 3.砂箱未固紧 4.未放压铁,或过早除去压铁 5.芯头与芯座间有空隙 6.压射前机器调整、操作不正确 7.模具镶块、活块已磨损或损坏,锁紧元件失效8.模具强度不够,发生变形 9.铸件投影面积过大,锁模力不够 10.型壳内层有裂隙,涂料层太薄 毛刺 1.合型操作不准确 2.砂箱未固紧 3.芯头与芯座间有空隙 4.分型面加工精度不够 5.参考飞翅内容 抬箱 1.砂箱未固紧
2.压铁质量不够,或过早除去压铁 胀砂 1.砂型紧实度低: 壳型强度低 2.砂型表面硬度低 3.金属液压头过高 冲砂 1.砂型紧实度不够,型壳强度不够 2.浇注系统设计不合理 3.金属流速过快,充型不稳定 4.压射压力过高,压射速度过快 5.金属液头过高 掉砂 1.合型操作不正确 2.型砂紧实度不够 3.型壳强度不够,发生破裂 铸件缺陷分析 缺陷种类缺陷名称产生原因 多肉类外渗物(外渗豆)内渗物(内渗豆) 1.铸型、型号、型芯发气最大,透气性低,排气不畅2.合金液有偏析倾向
3.凝固温度范围宽或凝固速度过慢 xx类气孔、针孔 1.铸件结构设计不正确,热节过多、过大 2.铸型、型壳、型芯、涂料等发气量大,透气性低,排气不畅 3.凝固温度范围宽,凝固速度数低 4.合金液含气量高,氧化夹杂物多 5.凝固时外压低 6.冷铁表面未清理干净,未挂涂料或涂料烘透 7.铜合金脱氧不彻底 8.浇注温度过高,浇注速度过快 缩孔 1.铸件结构设计不合理,壁厚悬殊,过渡外圆角太小: 热节过多、过大 2.浇注系统、冷铁、冒口安放不合理,不利于定向凝固 3.冒口补缩效率低 4.浇注温度过高 5.压射建压时间长,增压不起作用撮终补压压力不足,或压室的充满度不合理 6.比压太小,余料饼术薄,补压不起作用 7.内浇道厚度过小,溢流槽容量不够 8.熔模的模组分布不合理,造成局部散热困难
铸件常见缺陷和处理
铸件常见缺陷和处理Last revision on 21 December 2020
铸件常见缺陷、修补及检验 一、常见缺陷 1.缺陷的分类 铸件常见缺陷分为孔眼、裂纹、表面缺陷、形状及尺寸和重量不合格、成 份及组织和性能不合格五大类。(注:主要介绍铸钢件容易造成裂纹的缺陷)孔眼类缺陷 孔眼类缺陷包括气孔、缩孔、缩松、渣眼、砂眼、铁豆。 1.1.1气孔:别名气眼,气泡、由气体原因造成的孔洞。 铸件气孔的特征是:一般是园形或不规则的孔眼,孔眼内表面光滑,颜色 为白色或带一层旧暗色。(如照片) 气孔 照片1 产生的原因是:来源于气体,炉料潮湿或绣蚀、表面不干净、炉气中水蒸 气等气体、炉体及浇包等修后未烘干、型腔内的气体、浇注系统不当,浇 铸时卷入气体、铸型或泥芯透气性差等。 1.1.2缩孔 缩孔别名缩眼,由收缩造成的孔洞。 缩孔的特征是:形状不规则,孔内粗糙不平、晶粒粗大。
产生的原因是:金属在液体及凝固期间产生收缩引起的,主要有以下几点:铸件结构设计不合理,浇铸系统不适当,冷铁的大小、数量、位置不符实际、铁水化学成份不符合要求,如含磷过高等。浇注温度过高浇注速度过快等。 1.1.3缩松 缩松别名疏松、针孔蜂窝、由收缩耐造成的小而多的孔洞。 缩松的特征是:微小而不连贯的孔,晶粒粗大、各晶粒间存在明显的网状孔眼,水压试验时渗水。(如照片2) 缩松 照片2 产生的原因同以上缩孔。 1.1.4渣眼
渣眼别名夹渣、包渣、脏眼、铁水温度不高、浇注挡渣不当造成。 渣眼的特征是:孔眼形状不规则,不光滑、里面全部或局部充塞着渣。(如照片3) 渣眼 照片3 产生的原因是:铁水纯净度差、除渣不净、浇注时挡渣不好,浇注系统挡渣作用差、浇注时浇口未充满或断流。 1.1.5砂眼 砂眼是夹着砂子的砂眼。 砂眼的特征是:孔眼不规则,孔眼内充塞着型砂或芯砂。 产生的原因是:合箱时型砂损坏脱落,型腔内的散砂或砂块未清除干净、型砂紧实度差、浇注时冲坏型芯、浇注系统设计不当、型芯表面涂料不好等。 1.1.6铁豆 铁豆是夹着铁珠的孔眼、别名铁珠、豆眼、铁豆砂眼等。
压铸件的缺陷分析及检验要点
压铸件的缺陷分析及检验 一、流痕 ( 条纹 )( 抛光法去除 )A. 、模温低于 180( 铝合金 )b 、填充速度太高 c 、涂料过量 D 。金属流不同步。对 a 采取措施:调整内浇口面积 二、冷接: A 料温低或模温低, B ,合金成份不符,流动性差。 C ,浇口不合理,流程太长 D 。填充速度低 E 。排气不良。 F 、比压偏低。 三、。擦伤(扣模、粘模、拉痕、拉伤): A 型芯铸造斜度太小。 B ,型芯型壁有压伤痕。 C ,合金粘附模具。 D ,铸件顶出偏斜,或型芯轴线偏斜。 E ,型壁表面粗糙。 F ,脱模水不够。 G ,铝合金含铁量低于 0 。 6 %。措施:修模,增加含铁量。 四、凹陷(缩凹,缩陷,憋气,塌边) A .铸件设计不合理,有局部厚实现象,产生节热。 B ,合金收缩量大。 C ,内浇口面积太小。 D ,比压低。 E ,模温高 五、,气泡(皮下): A ,模温高。 B ,填充速度高。 C ,脱模水发气量大。 D ,排气不畅。 E ,开模过早。 F ,料温高。 六、气孔: A ,浇口位置和导流形状不当。 B ,浇道形状设计不良。 C ,压室充满度不够。 D ,内浇口速度太高,产生湍流。 E ,排气不畅。 F ,模具型腔位置太深。 G ,脱模水过多。 H ,料不纯。 七、缩孔: A ,料温高。 B ,铸件结构不均匀。 C ,比压太低。 D ,溢口太薄。 E ,局部模温偏高 八、花纹: A ,填充速度快。 B ,脱模水量太多。 C ,模具温度低。 九、裂纹: A ,铸件结构不合理,铸造圆角小等。 B ,抽芯及顶出装置在工作中受力不均匀,偏斜。 C ,模温低。 D ,开模时间长。 E ,合金成份不符。(铅锡镉铁偏高:锌合金,铝合金:锌铜铁高,镁合金:铝硅铁高 十、欠铸 A ,合金流动不良引起。 B ,浇注系统不良 C ,排气条件不良 十一、印痕(镶块或活动块及顶针痕等) 十二、网状毛刺: A ,模具龟裂。 B ,料温高。 C ,模温低。 D ,模腔表面不光滑。 E ,模具材料不当或热处理工艺不当。 F ,注射速度太高。
铸件常见缺陷和处理
铸件常见缺陷和处理 The pony was revised in January 2021
铸件常见缺陷、修补及检验 一、常见缺陷 1.缺陷的分类 铸件常见缺陷分为孔眼、裂纹、表面缺陷、形状及尺寸和重量不合格、成份及组织和性能不合格五大类。(注:主要介绍铸钢件容易造成裂纹的缺陷) 孔眼类缺陷 孔眼类缺陷包括气孔、缩孔、缩松、渣眼、砂眼、铁豆。 1.1.1气孔:别名气眼,气泡、由气体原因造成的孔洞。 铸件气孔的特征是:一般是园形或不规则的孔眼,孔眼内表面光滑,颜色为白色或带一层旧暗色。(如照片) 气孔 照片1
产生的原因是:来源于气体,炉料潮湿或绣蚀、表面不干净、炉气中水蒸气等气体、炉体及浇包等修后未烘干、型腔内的气体、浇注系统不当,浇铸时卷入气体、铸型或泥芯透气性差等。 1.1.2缩孔 缩孔别名缩眼,由收缩造成的孔洞。 缩孔的特征是:形状不规则,孔内粗糙不平、晶粒粗大。 产生的原因是:金属在液体及凝固期间产生收缩引起的,主要有以下几点:铸件结构设计不合理,浇铸系统不适当,冷铁的大小、数量、位置不符实际、铁水化学成份不符合要求,如含磷过高等。浇注温度过高浇注速度过快等。 1.1.3缩松 缩松别名疏松、针孔蜂窝、由收缩耐造成的小而多的孔洞。 缩松的特征是:微小而不连贯的孔,晶粒粗大、各晶粒间存在明显的网状孔眼,水压试验时渗水。(如照片2)
缩松 照片2 产生的原因同以上缩孔。 1.1.4渣眼 渣眼别名夹渣、包渣、脏眼、铁水温度不高、浇注挡渣不当造成。 渣眼的特征是:孔眼形状不规则,不光滑、里面全部或局部充塞着渣。(如照片3)
渣眼 照片3 产生的原因是:铁水纯净度差、除渣不净、浇注时挡渣不好,浇注系统挡渣作用差、浇注时浇口未充满或断流。 1.1.5砂眼 砂眼是夹着砂子的砂眼。 砂眼的特征是:孔眼不规则,孔眼内充塞着型砂或芯砂。 产生的原因是:合箱时型砂损坏脱落,型腔内的散砂或砂块未清除干净、型砂紧实度差、浇注时冲坏型芯、浇注系统设计不当、型芯表面涂料不好等。 1.1.6铁豆 铁豆是夹着铁珠的孔眼、别名铁珠、豆眼、铁豆砂眼等。
铸件外观缺陷图
铸件常见缺陷 常见缺陷 缺陷的分类:铸件常见缺陷分为孔眼、裂纹、表面缺陷、残缺类缺陷、形状及尺寸和重量不合格、成份及组织和性能不合格六大类。 1孔眼类缺陷 孔眼类缺陷包括气孔、缩孔、缩松、渣眼、砂眼、等。 1.1.1气孔:别名气眼,气泡、由气体原因造成的孔洞。 铸件气孔的特征是:其表面一般比较光滑,主要呈梨形\圆形和椭圆形.一般在铸件表面露出,大孔常孤立存在,小孔则成群出现。(如图) 产生的原因是:来源于气体,炉料潮湿或绣蚀、表面不干净、炉气中水蒸气等气体、炉体及浇包等修后未烘干、型腔内的气体、浇注系统不当,浇铸时卷入气体、铸型等。 1.1.2缩孔 缩孔别名缩眼,由收缩造成的孔洞。 缩孔的特征是:形状不规则,孔壁粗糙并带有技状晶,常出现在铸件最后凝固的部位,广义的缩孔包括缩松。(如图)
产生的原因是:金属在液体及凝固期间由于补缩不良而产生的孔洞,主要有以下几点:铸件结构设计不合理,浇铸系统不适当,冷铁的大小、数量、位置不符实际、铁水化学成份不符合要求,如含磷过高等。浇注温度过高浇注速度过快等。 1.1.3缩松 缩松别名疏松、针孔蜂窝、由收缩耐造成的小而多的孔洞。 缩松的特征是:铸件断面上出现的分散而细小的缩孔.助高倍放大镜才能发现的缩松称为显微缩松,铸件有缩松的部位,在气密性实验时易渗漏。(如图) 产生的原因同以上缩孔。 1.1.4渣眼 渣眼别名夹渣、包渣、脏眼、铁水温度不高、浇注挡渣不当造成。
渣眼的特征是:铸件浇注位置上表面的非金属夹杂物。通常在加工后发现与气孔并存,孔径大小不一,成群集结。(如图) 产生的原因是:铁水纯净度差、除渣不净、浇注时挡渣不好,浇注系统挡渣作用差、浇注时浇口未充满或断流。 1.1.5砂眼 砂眼是夹着砂子的砂眼。 砂眼的特征是:铸件内部或表面带有砂粒的孔洞(如图)。 。
压铸件常见缺陷和处理
铸件常见缺陷和处理 一、飞边: 飞边就是铸件在分型面上(或活动部位处)突出过多的金属薄片。产生的原因有: 1.压射前机器的调整、操作不合适。 2.模具及滑块损坏,闭锁原件损坏 3.模具镶块及滑块磨损 4.模具强度不够造成变形 5.分型面上杂物未清理干净 6.投影面积计算不正确,超过锁模力 二、气泡 铸件表面下,聚齐气体因热胀将表面鼓起的泡,称为气泡。产生的原因: 1.模具温度过高 2.金属液卷入气体过多 3.涂料过多,浇入前未燃净,使挥发气体被包在铸件表面。 4.排气不畅 5.开模过早 三、孔穴 孔穴包括气孔和缩孔 气孔,气孔有两种:一种是金属液卷入气体形成内表面光亮和光滑、形状较为规则的孔洞,另一种是合金熔炼不正
确或精炼不够,气体溶解于合金中。压铸时,激冷甚剧,凝固很快,溶于金属中的气体来不及析出,使金属内的气体留在铸件内形成孔洞。产生的原因有: 1.浇口位置选择和导流不当,导致金属液进入型腔产生正面撞击及漩涡。 2.流道形状设计不良, 3.压室充满度不够 4.内浇口速度太高,形成端流。 5.排气不畅 6.模具型腔位置太深 7.机械加工于量太大 8.涂料过多,在填充前未燃尽 9.炉料不干净,精炼不良 缩孔,铸件在凝固过程中,由于金属补充不足形成的暗色、形状不规则的孔洞。产生的原因有: 1.合金规范不合适,浇入温度过高 2.金属液过热时间太长 3.比压太低 4.余料柄太薄,最终补压不到作用 5.内浇口截面积过小(主要是厚度不够) 6.溢流槽位置不对或容量不够
7.铸件结构不合理,有热节部位,并且该处无法用溢流槽解决 8.铸件的壁厚变化太大 四、夹杂 夹杂又称为夹物、砂眼、夹渣。在铸件表面或内部形成不规则的孔穴部分或全部充塞着杂物,产生的原因有: 1.炉料不干净 2.合金精炼不够,熔渣未除净 3.舀取金属液时带入熔渣及金属氧化物 4.模具未清里干净 5.涂料中石墨太多 五、冷豆 冷豆也称铁豆,其表现是嵌在铸件表面,未和铸件完全融合的金属颗粒,产生的原因有: 1.浇注系统设置不当 2.填充速度过快 3.金属过早进入型腔 六、麻面 产生的原因是由于填充时,金属液分散成密集液滴,高速撞击型壁,结果形成具有强烈流向的细小、密集的麻点区域。 七、印痕
锌合金压铸件常见缺陷及处理方法【干货】
锌合金压铸件常见缺陷及处理方法 内容来源网络,由“深圳机械展(11万㎡,1100多家展商,超10万观众)”收集整理! 更多cnc加工中心、车铣磨钻床、线切割、数控刀具工具、工业机器人、非标自动化、数字化无人工厂、精密测量、3D打印、激光切割、钣金冲压折弯、精密零件加工等展示,就在深圳机械展. 锌合金压铸件是一种压力铸造的零件,是使用装好铸件模具的压力铸造机械压铸机,将加热为液态的锌或锌合金浇入压铸机的入料口,经压铸机压铸,铸造出模具限制的形状和尺寸的锌零件或锌合金零件,这样的零件通常就被叫做锌合金压铸件。 特点及应用: 近年来,我国锌合金压铸技术快速发展,带来的经济利益与市场效益不容小觑,据专家介绍,锌合金压铸技术主要有以下特点: 1、相对比重大。 2、铸造性能好,可以压铸形状复杂、薄壁的精密件,铸件表面光滑。 3、可进行表面处理:电镀、喷涂、喷漆、抛光、研磨等。 4、熔化与压铸时不吸铁,不腐蚀压型,不粘模。 5、有很好的常温机械性能和耐磨性。 6、熔点低,容易压铸成型。 要了解锌合金压铸首先要明白锌合金的一些特点,锌合金对锌合金压铸来说起着重要的作用。 锌合金压铸的主要特点有,锌合金的熔点较低,温度到达四百度时锌合金就产生融化过程,这在锌合金压铸中来说比较好成型。锌合金在融化和压铸的过程中不吸铁,而且锌合金
铸造性能好,在压铸过程中可以把很多形状复杂的精密件,压铸完成后铸件的表面显得十分光滑。同时,锌合金的比重相对较大。 锌合金压铸技术广泛应用在注塑工艺上,它的主要的优点就是在注重提高铸件质量。了解锌合金压铸的都知道,在铸件中流道和余料是铸件的一部分,在铸件里面它们苏没有什么利用的价值,但是这些还是被计入了铸件是成本上。同时型合金还有可回收性,一般的在会把这些余料返回原来的供货商,以换取新的材料。在供货商没有进行良好的处理,那么会导致空气的污染,会带来环境危害。锌合金压铸的回收方式还有很多种,而且锌合金压铸是以锌为主要的元素组成的合金,还有其他的一些合金元素,像铝、铜等。锌合金压铸的制造工艺通常也分为两种,一种为铸造锌合金,一种为变形锌合金。每种方式对锌合金铸造来说都有不同的特点所在。 锌合金压铸件目前广泛应用于各类装饰的表面,比如:皮带扣,领带夹,玩具,建筑装饰,家具配件,各类金属饰扣等,通常铸件表面的质量要求非常高.但在生产过程中,也难免会发生缺陷,东莞锌合金压铸厂家给大家介绍下锌合金压铸件常见缺陷原因和解决方法。 1、锌合金压铸件局部变形或表面有裂纹 原因:铸件壁太薄,收缩后变形;顶料杆数量不够或分布不均,导致受力不均匀;推料杆固定板在工作时发生偏斜,导致一面受力小,一面受力大,使产品产生裂纹和发生变形。解决方法为:调整和重新安装推杆固定板;增加顶料杆的数量,调整其分布位置,使铸件顶出受力均衡。 2、锌合金压铸件有一部分没有成形,型腔充不满 原因:空气排不出来;压机压力太小,金属液温度低,压铸模温度太低,金属液不足,压射速度太高。锌合金压铸厂告诉大家,可以采取的方法为:更换大压力的压铸机;提高压铸模和金属液温度;加足够的金属液,减小压射速度,加大进料口厚度。
铸造铸件常见缺陷分析报告文案
铸造铸件常见缺陷分析 铸造工艺过程复杂,影响铸件质量的因素很多,常见的铸件缺陷名称、特征和产生的原因,见表。 常见铸件缺陷及产生原因 .学习帮手.
缺陷名称特征产生的主要原因 气孔 在铸件部或表 面有大小不等 的光滑孔洞①炉料不干或含氧化物、杂质多;②浇注工具或炉前添加剂未烘干;③型砂含水过多或起模和修型时刷水过多;④型芯烘干不充分或型芯通气孔被堵塞;⑤春砂过紧,型砂透气性差;⑥浇注温度过低或浇注速度太快等 缩孔与缩松缩孔多分布在 铸件厚断面 处,形状不规 则,孔粗糙①铸件结构设计不合理,如壁厚相差过大,厚壁处未放冒口或冷铁;②浇注系统和冒口的位置不对; ③浇注温度太高;④合金化学成分不合格,收缩率过大,冒口太小或太少 砂眼在铸件部或表 面有型砂充塞 的孔眼①型砂强度太低或砂型和型芯的紧实度不够,故型砂被金属液冲入型腔;②合箱时砂型局部损坏;③浇注系统不合理,浇口方向不对,金属液冲坏了砂 .学习帮手.
型;④合箱时型腔或浇口散砂未清理干净 粘砂铸件表面粗 糙,粘有一层 砂粒①原砂耐火度低或颗粒度太大;②型砂含泥量过高,耐火度下降;③浇注温度太高;④湿型铸造时型砂中煤粉含量太少;⑤干型铸造时铸型未刷涂斜或涂料太薄 夹砂铸件表面产生 的金属片状突 起物,在金属 片状突起物与 铸件之间夹有 一层型砂①型砂热湿拉强度低,型腔表面受热烘烤而膨胀开裂;②砂型局部紧实度过高,水分过多,水分烘干后型腔表面开裂;③浇注位置选择不当,型腔表面长时间受高温铁水烘烤而膨胀开裂;④浇注温度过高,浇注速度太慢 错型铸件沿分型面 有相对位置错①模样的上半模和下半模未对准;②合箱时,上下砂箱错位;③上下砂箱未夹紧或上箱未加足够压 .学习帮手.
铸件常见缺陷修补及检验
铸件常见缺陷的鉴别、起因、修补及检验----------------------------------------------福联造型,呋喃树脂、酚醛树脂、覆膜砂专家 1.缺陷的分类 铸件常见缺陷分为孔眼、裂纹、表面缺陷、形状及尺寸和重量不合格、成份及组织和性能不合格五大类。(注:主要介绍铸钢件容易造成裂纹的缺陷) 1.1孔眼类缺陷 孔眼类缺陷包括气孔、缩孔、缩松、渣眼、砂眼、铁豆。 1.1.1气孔:别名气眼,气泡、由气体原因造成的孔洞。 铸件气孔的特征是:一般是园形或不规则的孔眼,孔眼内表面光滑,颜色为白色或带一层旧暗色。(如照片) 气孔 照片1 产生的原因是:来源于气体,炉料潮湿或绣蚀、表面不干净、炉气中水蒸气等气体、炉体及浇包等修后未烘干、型腔内的气体、浇注系统不当,浇铸时卷入气体、铸型或泥芯透气性差等。 1.1.2缩孔 缩孔别名缩眼,由收缩造成的孔洞。 缩孔的特征是:形状不规则,孔内粗糙不平、晶粒粗大。
产生的原因是:金属在液体及凝固期间产生收缩引起的,主要有以下几点:铸件结构设计不合理,浇铸系统不适当,冷铁的大小、数量、位置不符实际、铁水化学成份不符合要求,如含磷过高等。浇注温度过高浇注速度过快等。 1.1.3缩松 缩松别名疏松、针孔蜂窝、由收缩耐造成的小而多的孔洞。 缩松的特征是:微小而不连贯的孔,晶粒粗大、各晶粒间存在明显的网状孔眼,水压试验时渗水。(如照片2) 缩松 照片2 产生的原因同以上缩孔。 1.1.4渣眼
渣眼别名夹渣、包渣、脏眼、铁水温度不高、浇注挡渣不当造成。 渣眼的特征是:孔眼形状不规则,不光滑、里面全部或局部充塞着渣。(如照片3) 渣眼 照片3 产生的原因是:铁水纯净度差、除渣不净、浇注时挡渣不好,浇注系统挡渣作用差、浇注时浇口未充满或断流。 1.1.5砂眼 砂眼是夹着砂子的砂眼。 砂眼的特征是:孔眼不规则,孔眼内充塞着型砂或芯砂。 产生的原因是:合箱时型砂损坏脱落,型腔内的散砂或砂块未清除干净、型砂紧实度差、浇注时冲坏型芯、浇注系统设计不当、型芯表面涂料不好等。 1.1.6铁豆 铁豆是夹着铁珠的孔眼、别名铁珠、豆眼、铁豆砂眼等。
铝铸件常见缺陷及分析
. 铝铸件常见缺陷及分析 -------------------------------------------------------------------------------- 氧化夹渣一 缺陷特征:氧化夹渣多分布在铸件的上表面,在铸型不通气的转角部位。断口多呈灰白色 光透视或在机械加工时发现,也可在碱洗、酸洗或阳极化时发现或黄色,经x 产生原因:.炉料不清洁,回炉料使用量过多1 浇注系统设计不良2. 3.合金液中的熔渣未清除干净4.浇注操作不当,带入夹渣5.精炼变质处理后静置时间不够防止方法:1.炉料应经过吹砂,回炉料的使用量适当降低2.改进浇注系统设计,提高其挡渣能力3.采用适当的熔剂去渣4.浇注时应当平稳并应注意挡渣.精炼后浇注前合金液应静置一定时间5 气泡二气孔一般是发亮的氧化皮,具有光滑的表面,缺陷特征:三铸件壁内气孔一般呈圆形或椭圆形,光透视或机械加X有时呈油黄色。表面气孔、气泡可通过喷砂发现,内部气孔气泡可通过光底片上呈黑色气泡在X工发现气孔产生原因:.浇注合金不平稳,卷入气体1) 马粪等如煤屑、草根芯)砂中混入有机杂质(.型2( 3.铸型和砂芯通气不良4.冷铁表面有缩孔5.浇注系统设计不良:防止方法1.正确掌握浇注速度,避免卷入气体。砂中不得混入有机杂质以减少造型材料的发气量(芯)2.型砂的排气能力芯)3.改善( 4.正确选用及处理冷铁5.改进浇注系统设计缩松三缺陷特征:铝铸件缩松一般产生在内浇道附近飞冒口根部厚大部位、壁的厚薄转接处和具 光底x在铸态时断口为灰色,浅黄色经热处理后为灰白浅黄或灰黑色在有大平面的薄壁处。断口等检查方法发现片上呈云雾状严重的呈丝状缩松可通过X光、荧光低倍产生原因:1.冒口补缩作用差2.炉料含气量太多. . .内浇道附近过热3 .砂型水分过多,砂芯未烘干4 5.合金晶粒粗大6.铸件在铸型中的位置不当7.浇注温度过高,浇注速度太快 防止方法: 1.从冒口补浇金属液,改进冒口设计 2.炉料应清洁无腐蚀 3.铸件缩松处设置冒口,安放冷铁或冷铁与冒口联用 4.控制型砂水分,和砂芯干燥 5.采取细化品粒的措施 6.改进铸件在铸型中的位置降低浇注温度和浇注速度 四裂纹 缺陷特征: 1.铸造裂纹。沿晶界发展,常伴有偏析,是一种在较高温度下形成的裂纹在体积收缩较大的合金和形状较复杂的铸件容易出现 2.热处理裂纹:由于热处理过烧或过热引起,常呈穿晶裂纹。常在产生应力和热膨张系数较大的合金冷却过剧。或存在其他冶金缺陷时产生 产生原因:1.铸件结构设计不合理,有尖角,壁的厚薄变化过于悬殊 2.砂型(芯)退让性不良 3.铸型局部过热
压铸件常见缺陷和处理
压铸件常见缺陷和处理Last revision on 21 December 2020
铸件常见缺陷和处理 一、飞边: 飞边就是铸件在分型面上(或活动部位处)突出过多的金属薄片。产生的原因有: 1.压射前机器的调整、操作不合适。 2.模具及滑块损坏,闭锁原件损坏 3.模具镶块及滑块磨损 4.模具强度不够造成变形 5.分型面上杂物未清理干净 6.投影面积计算不正确,超过锁模力 二、气泡 铸件表面下,聚齐气体因热胀将表面鼓起的泡,称为气泡。产生的原因: 1.模具温度过高 2.金属液卷入气体过多 3.涂料过多,浇入前未燃净,使挥发气体被包在铸件表面。 4.排气不畅 5.开模过早 三、孔穴 孔穴包括气孔和缩孔 气孔,气孔有两种:一种是金属液卷入气体形成内表面光亮和光滑、形状较为规则的孔洞,另一种是合金熔炼
不正确或精炼不够,气体溶解于合金中。压铸时,激冷甚剧,凝固很快,溶于金属中的气体来不及析出,使金属内的气体留在铸件内形成孔洞。产生的原因有: 1.浇口位置选择和导流不当,导致金属液进入型腔产生正面撞击及漩涡。 2.流道形状设计不良, 3.压室充满度不够 4.内浇口速度太高,形成端流。 5.排气不畅 6.模具型腔位置太深 7.机械加工于量太大 8.涂料过多,在填充前未燃尽 9.炉料不干净,精炼不良 缩孔,铸件在凝固过程中,由于金属补充不足形成的暗色、形状不规则的孔洞。产生的原因有: 1.合金规范不合适,浇入温度过高 2.金属液过热时间太长 3.比压太低 4.余料柄太薄,最终补压不到作用 5.内浇口截面积过小(主要是厚度不够) 6.溢流槽位置不对或容量不够
铸造铸件常见缺陷分析
铸造铸件常见缺陷分析 工艺过程复杂,影响铸件质量的因素很多,常见的铸件缺陷名称、特征和产生的原因,见表。 1
常见铸件缺陷及产生原因 缺陷名称特征产生的主要原因 气孔 在内部或表面 有大小不等的 光滑孔洞①炉料不干或含氧化物、杂质多;②浇注工具或炉前添加剂未烘干;③型砂含水过多或起模和修型时刷水过多;④型芯烘干不充分或型芯通气孔被堵塞;⑤春砂过紧,型砂透气性差;⑥浇注温度过低或浇注速度太快等 缩孔与缩松缩孔多分布在 铸件厚断面 处,形状不规 则,孔内粗糙①铸件结构设计不合理,如壁厚相差过大,厚壁处未放冒口或冷铁;②浇注系统和冒口的位置不对; ③浇注温度太高;④合金化学成分不合格,收缩率过大,冒口太小或太少 2
砂眼 在铸件内部或 表面有型砂充 塞的孔眼①型砂强度太低或砂型和型芯的紧实度不够,故型砂被金属液冲入型腔;②合箱时砂型局部损坏;③浇注系统不合理,内浇口方向不对,金属液冲坏了砂型;④合箱时型腔或浇口内散砂未清理干净 粘砂铸件表面粗 糙,粘有一层 砂粒①原砂耐火度低或颗粒度太大;②型砂含泥量过高,耐火度下降;③浇注温度太高;④湿型铸造时型砂中煤粉含量太少;⑤干型铸造时铸型未刷涂斜或涂料太薄 夹砂铸件表面产生 的金属片状突 起物,在金属 片状突起物与 铸件之间夹有①型砂热湿拉强度低,型腔表面受热烘烤而膨胀开裂;②砂型局部紧实度过高,水分过多,水分烘干后型腔表面开裂;③浇注位置选择不当,型腔表面长时间受高温铁水烘烤而膨胀开裂;④浇注温度过高,浇注速度太慢 3
一层型砂 错型铸件沿分型面 有相对位置错 移①模样的上半模和下半模未对准;②合箱时,上下砂箱错位;③上下砂箱未夹紧或上箱未加足够压铁,浇注时产生错箱 冷隔铸件上有未完 全融合的缝隙或洼坑,其交接处是圆滑的①浇注温度太低,合金流动性差;②浇注速度太慢或浇注中有断流;③浇注系统位置开设不当或内浇道横截面积太小;④铸件壁太薄;⑤直浇道(含浇口杯)高度不够;⑥浇注时金属量不够,型腔未充满 浇不足 铸件未被浇满 裂纹铸件开裂,开 裂处金属表面①铸件结构设计不合理,壁厚相差太大,冷却不均匀;②砂型和型芯的退让性差,或春砂过紧;③落 4
铸件常见缺陷和处理
铸件常见缺陷、修补及检验 一、常见缺陷 1.缺陷的分类 铸件常见缺陷分为孔眼、裂纹、表面缺陷、形状及尺寸和重量不合格、成份及组织和性能不合格五大类。(注:主要介绍铸钢件容易造成裂纹的缺陷) 1.1孔眼类缺陷 孔眼类缺陷包括气孔、缩孔、缩松、渣眼、砂眼、铁豆。 1.1.1气孔:别名气眼,气泡、由气体原因造成的孔洞。 铸件气孔的特征是:一般是园形或不规则的孔眼,孔眼内表面光滑,颜色为白色或带一层旧暗色。(如照片) 气孔 照片1 产生的原因是:来源于气体,炉料潮湿或绣蚀、表面不干净、炉气中水蒸气等气体、炉体及浇包等修后未烘干、型腔内的气体、浇注系统不当,浇铸时卷入气体、铸型或泥芯透气性差等。 1.1.2缩孔 缩孔别名缩眼,由收缩造成的孔洞。
缩孔的特征是:形状不规则,孔内粗糙不平、晶粒粗大。 产生的原因是:金属在液体及凝固期间产生收缩引起的,主要有以下几点:铸件结构设计不合理,浇铸系统不适当,冷铁的大小、数量、位置不符实际、铁水化学成份不符合要求,如含磷过高等。浇注温度过高浇注速度过快等。 1.1.3缩松 缩松别名疏松、针孔蜂窝、由收缩耐造成的小而多的孔洞。 缩松的特征是:微小而不连贯的孔,晶粒粗大、各晶粒间存在明显的网状孔眼,水压试验时渗水。(如照片2) 缩松 照片2 产生的原因同以上缩孔。
1.1.4渣眼 渣眼别名夹渣、包渣、脏眼、铁水温度不高、浇注挡渣不当造成。 渣眼的特征是:孔眼形状不规则,不光滑、里面全部或局部充塞着渣。(如照片3) 渣眼 照片3 产生的原因是:铁水纯净度差、除渣不净、浇注时挡渣不好,浇注系统挡渣作用差、浇注时浇口未充满或断流。 1.1.5砂眼 砂眼是夹着砂子的砂眼。 砂眼的特征是:孔眼不规则,孔眼内充塞着型砂或芯砂。 产生的原因是:合箱时型砂损坏脱落,型腔内的散砂或砂块未清除干净、型砂紧实度差、浇注时冲坏型芯、浇注系统设计不当、型芯表面涂料不好等。 1.1.6铁豆
压铸件常见缺陷及处理1
压铸件常见缺陷及处理 一、飞边: 飞边就是铸件在分型面上(或活动部位处)突出过多的金属薄片。产生的原因有: 1.压射前机器的调整、操作不合适。 2.模具及滑块损坏,闭锁原件损坏 3.模具镶块及滑块磨损 4.模具强度不够造成变形 5.分型面上杂物未清理干净 6.投影面积计算不正确,超过锁模力 二、气泡 铸件表面下,聚齐气体因热胀将表面鼓起的泡,称为气泡。产生的原因: 1.模具温度过高 2.金属液卷入气体过多 3.涂料过多,浇入前未燃净,使挥发气体被包在铸件表面。 4.排气不畅 5.开模过早 三、孔穴 孔穴包括气孔和缩孔 气孔,气孔有两种:一种是金属液卷入气体形成内表面光亮和光滑、形状较为规则的孔洞,另一种是合金熔炼不正确或精炼不够,气体溶解于合金中。压铸时,激冷甚剧,凝固很快,溶于金属中的气体来不及析出,使金属内的气体留在铸件内形成孔洞。产生的原因有: 1.浇口位置选择和导流不当,导致金属液进入型腔产生正面撞击及漩涡。 2.流道形状设计不良, 3.压室充满度不够 4.内浇口速度太高,形成端流。 5.排气不畅 6.模具型腔位置太深 7.机械加工于量太大 8.涂料过多,在填充前未燃尽 9.炉料不干净,精炼不良 缩孔,铸件在凝固过程中,由于金属补充不足形成的暗色、形状不规则的孔洞。产生的原因有: 1.合金规范不合适,浇入温度过高 2.金属液过热时间太长 3.比压太低 4.余料柄太薄,最终补压不到作用 5.内浇口截面积过小(主要是厚度不够) 6.溢流槽位置不对或容量不够 7.铸件结构不合理,有热节部位,并且该处无法用溢流槽解决 8.铸件的壁厚变化太大 四、夹杂
夹杂又称为夹物、砂眼、夹渣。在铸件表面或内部形成不规则的孔穴部分或全部充塞着杂物,产生的原因有: 1.炉料不干净 2.合金精炼不够,熔渣未除净 3.舀取金属液时带入熔渣及金属氧化物 4.模具未清里干净 5.涂料中石墨太多 五、冷豆 冷豆也称铁豆,其表现是嵌在铸件表面,未和铸件完全融合的金属颗粒,产生的原因有: 1.浇注系统设置不当 2.填充速度过快 3.金属过早进入型腔 六、麻面 产生的原因是由于填充时,金属液分散成密集液滴,高速撞击型壁,结果形成具有强烈流向的细小、密集的麻点区域。 七、印痕 顶出原件引起:表现是在铸件表面上出现凹痕或凸痕,产生原因: 1.顶出原件调整不正确 2.推杆端部模损 3.推杆面积太小 4.开模过早 镶件或活动部分引起:表现在铸件平整的表面上出现阶梯痕迹,产生的原因有: 1.镶件部分松动 2.活动部分松动或磨损 3.镶件的侧壁表面由动定模互相穿插的镶件所形成 八、裂纹 铸件的基体被破坏或断开,形成细长的缝隙,呈不规则线性,在外力的作用下有发展的趋势,这种缺陷称为裂纹 原因: 铸件结构和形状引起的: 1.铸件的壁厚处与壁薄相接处转变剧烈 2.铸件上的转折处圆角不够 3.铸件上能安装推杆的位置不够,造成推杆分布不均衡 4.铸件设计上考虑不周收缩时产生应力而撕裂 模具的成型零件表面质量不好,装固不稳引起的: 1.成型表面沿出模方向有凹陷(或凹坑),铸件脱出撕裂 2.凸的成型表面其根部加工痕迹未能消除,铸件被撕裂 3.成型零件装固有偏斜,阻碍铸件脱出 顶出造成的: 1.模具的顶出原件安置不合理(位置或个数) 2.顶出机构偏斜,顶出力不均衡 3.模具的顶出机构与压铸机上的顶出器的连接不合理,或有歪斜,或动作不协调 4.顶动顶出时的机器顶杆长短不一致,液压顶出的顶棒长短不一致 合金的成分引起:
锌合金压铸件缺陷及原因
压铸件常见缺陷分析 一、锌合金压铸件表面有花纹,并有金属流痕迹产生原因: 1、通往铸件进口处流道太浅。 2、压射比压太大,致使金属流速过高,引起金属液的飞溅。 调整方法:1、加深浇口流道。2、减少压射比压。 二、锌合金压铸件表面有细小的凸瘤产生原因: 1、表面粗糙。 2、型腔内表面有划痕或凹坑、裂纹产生。 调整方法:1、抛光型腔。2、更换型腔或修补。 三、铸件表面有推杆印痕,表面不光洁,粗糙产生原因: 1、推件杆(顶杆)太长; 2、型腔表面粗糙,或有杂物。 调整方法:1、调整推件杆长度。2、抛光型腔,清除杂物及油污。 四、锌合金压铸件表面有裂纹或局部变形产生原因: 1、顶料杆分布不均或数量不够,受力不均: 2、推料杆固定板在工作时偏斜,致使一面受力大,一面受力小,使产品变形及产生裂纹。 3、铸件壁太薄,收缩后变形。 调整方法: 1、增加顶料杆数量,调整其分布位置,使铸件顶出受力均衡。 2、调整及重新安装推杆固定板。 五、锌合金压铸件表面有气孔产生原因: 1、润滑剂太多。 2、排气孔被堵死,气孔排不出来。 调整方法:1、合理使用润滑剂。2、增设及修复排气孔,使其排气通畅。 六、铸件表面有缩孔产生原因: 压铸件工艺性不合理,壁厚薄变化太大。金属液温度太高。 调整方法:1、在壁厚的地方,增加工艺孔,使之薄厚均匀。2、降低金属液温度。 七、铸件外轮廓不清晰,成不了形,局部欠料产生原因: 1、压铸机压力不够,压射比压太低。 2、进料口厚度太大; 3、浇口位置不正确,使金属发生正面冲击。 调整方法: 1、更换压铸比压大的压铸机; 2、减小进料口流道厚度; 3、改变浇口位置,防止对铸件正面冲击。 八、铸件部分未成形,型腔充不满产生原因: 1、压铸模温度太低; 2、金属液温度低; 3、压机压力太小, 4、金属液不足,压射速度太高; 5、空气排不出来。 调整方法:1、提高压铸模,金属液温度;2、更换大压力压铸机。3、加足够的金属液,减小压射速度,加大进料口厚度。 九、压铸件锐角处充填不满产生原因: 1、内浇口进口太大; 2、压铸机压力过小; 3、锐角处通气不好,有空气排不出来。 调整方法:1、减小内浇口。2、改换压力大的压铸机。3、改善排气系统 十、铸件结构疏松,强度不高产生原因: 1、压铸机压力不够; 2、内浇口太小; 3、排气孔堵塞。
锌合金压铸件常见缺陷及处理方法
锌合金压铸件常见缺陷及处理方法 锌合金压铸件目前广泛应用于各种装饰方面,如家具配件、建筑装饰、浴室配件、灯饰零件、玩具、领带夹、皮带扣、各种金属饰扣等,因此对铸件表面质量要求较高,同时要求有良好的表面处理性能。 缺陷表征:压铸件表面有突起小泡、压铸出来就发现、抛光或加工后显露出来、喷油或电镀后出现。产生原因: 1.孔洞引起:主要是气孔和收缩机制,气孔往往是圆形,而收缩多数是不规则形。 (1)气孔产生原因:a金属液在充型、凝固过程中,由于气体侵入,导致铸件表面或内部产生孔洞。b涂料挥发出来的气体侵入。c合金液含气量过高,凝固时析出。当型腔中的气体、涂料挥发出的气体、合金凝固析出的气体,在模具排气不良时,最终留在铸件中形成的气孔。 (2)缩孔产生原因:a金属液凝固过程中,由于体积缩小或最后凝固部位得不到金属液补缩,而产生缩孔。b厚薄不均的铸件或铸件局部过热,造成某一部位凝固慢,体积收缩时表面形成凹位。由于气孔和缩孔的存在,使压铸件在进行表面处理时,孔洞可能会进入水,当喷漆和电镀后进行烘烤时,孔洞内气体受热膨胀;或孔洞内水会变蒸气,体积膨胀,因而导致铸件表面起泡。 2.晶间腐蚀引起: 锌合金成分中有害杂质:铅、镉、锡会聚集在晶粒交界处导致晶间腐蚀,金属基体因晶间腐蚀而破碎,而电镀加速了这一祸害,受晶间腐蚀的部位会膨胀而将镀层顶起,造成铸件表面起泡。特别是在潮湿环境下晶间腐蚀会使铸件变形、开裂、甚至破碎。 3.裂纹引起:水纹、冷隔纹、热裂纹。 水纹、冷隔纹:金属液在充型过程中,先进入的金属液接触型壁过早凝固,后进入金属液不能和已凝固金属层熔合为一体,在铸件表面对接处形成叠纹,出现条状缺陷。水纹一般是在铸件表面浅层;而冷隔纹有可能渗入到铸件内部。 热裂纹:a当铸件厚薄不均,凝固过程产生应力;b过早顶出,金属强度不够;c顶出时受力不均d过高的模温使晶粒粗大;e有害杂质存在。 以上因素都有可能产生裂纹。当压铸件存在水纹、冷隔纹、热裂纹,电镀时溶液会渗入到裂纹中,在烘烤时转化为蒸气,气压顶起电镀层形成起泡。 解决缺陷方案: 控制气孔产生,关键是减少混入铸件内的气体量,理想的金属流应不断加速地由喷嘴经过分流锥和浇道进入型腔,形成一条顺滑及方向一致的金属流,采用锥形流道设计,即浇流应不断加速地由喷嘴向内浇口逐渐减少,可达到这个目的。在充填系统中,混入的气体是由于湍流与金属液相混合而形成气孔,从金属液由浇铸系统进入型腔的模拟压铸过程的研究中,明显看出浇道中尖锐的转变位和递增的浇道截面积,都会使金属液流出现湍流而卷气,平稳的金属液才有利于气体从浇道和型腔进入溢流槽和排气槽,排出模外。 对于缩孔:要使压铸凝固过程中各个部位尽量同时均匀散热,同时凝固。可通过合理的水口设计,内浇口厚度及位置,模具设计,模温控制及冷却,来避免缩孔产生。对于晶间腐蚀现象:主要是控制合金原料中有害杂质含量,特别是铅<0.003%。注意废料带来的杂质元素。 对于水纹、冷隔纹,可提高模具温度,加大内浇口速度,或在冷隔区加大溢流槽,来减少冷隔纹的出现。 对于热裂纹:压铸件厚薄不要急剧变化以减少应力产生;相关的压铸工艺参数作调整;降低模温。
铸造铸件常见缺陷分析
铸造铸件常见缺陷分析铸造工艺过程复杂,影响铸件质量的因素很多,常见的铸件缺陷名称、特征和产生的原因,见表。
常见铸件缺陷及产生原因缺陷名称特征产生的主要原因 气孔 在铸件内部或表面有 大小不等的光滑孔洞①炉料不干或含氧化物、杂质多;②浇注工具或炉前添加剂未烘干;③型砂含水过多或起模和修型时刷水过多;④型芯烘干不充分或型芯通气孔被堵塞;⑤春砂过紧,型砂透气性差;⑥浇注温度过低或浇注速度太快等 缩孔与缩松缩孔多分布在铸件厚 断面处,形状不规则, 孔内粗糙①铸件结构设计不合理,如壁厚相差过大,厚壁处未放冒口或冷铁;②浇注系统和冒口的位置不对;③浇注温度太高;④合金化学成分不合格,收缩率过大,冒口太小或太少
砂眼 在铸件内部或表面有 型砂充塞的孔眼①型砂强度太低或砂型和型芯的紧实度不够,故型砂被金属液冲入型腔;②合箱时砂型局部损坏;③浇注系统不合理,内浇口方向不对,金属液冲坏了砂型; ④合箱时型腔或浇口内散砂未清理干净 粘砂铸件表面粗糙,粘有一 层砂粒①原砂耐火度低或颗粒度太大;②型砂含泥量过高,耐火度下降;③浇注温度太高;④湿型铸造时型砂中煤粉含量太少;⑤干型铸造时铸型未刷涂斜或涂料太薄 夹砂铸件表面产生的金属 片状突起物,在金属片 状突起物与铸件之间①型砂热湿拉强度低,型腔表面受热烘烤而膨胀开裂;②砂型局部紧实度过高,水分过多,水分烘干后型腔表面开裂;③浇注位置选择不当,型腔表面长时间受高温铁水烘烤而膨胀开裂;④浇注温度过高,浇注速度太慢
夹有一层型砂错型 铸件沿分型面有相对位置错移①模样的上半模和下半模未对准;②合箱时,上下砂箱错位;③上下砂箱未夹紧或上箱未加足够压铁,浇注时产生错箱 冷隔铸件上有未完全融合 的缝隙或洼坑,其交接 处是圆滑的①浇注温度太低,合金流动性差;②浇注速度太慢或浇注中有断流;③浇注系统位置开设不当或内浇道横截面积太小;④铸件壁太薄;⑤直浇道(含浇口杯)高度不够;⑥浇注时金属量不够,型腔未充满
常见铸件缺陷分析
常见铸件缺陷分析 缺陷种类,缺陷名称生产原因 多肉类飞翅(飞边) 1.砂型表面不光洁,分型面不增整 2.合理操作朱准确 3.砂箱未固紧 4.未放压铁,或过早除去压铁 5.芯头与芯座间有空隙 6.压射前机器调整、操作不正确 7.模具镶块、活块已磨损或损坏,锁紧元件失效 8.模具强度不够,发生变形 9.铸件投影面积过大,锁模力不够 10.型壳内层有裂隙,涂料层太薄 毛刺 1.合型操作不准确 2.砂箱未固紧 3.芯头与芯座间有空隙 4.分型面加工精度不够 5.参考飞翅内容 抬箱 1.砂箱未固紧 2.压铁质量不够,或过早除去压铁 胀砂 1.砂型紧实度低:壳型强度低 2.砂型表面硬度低 3.金属液压头过高 冲砂 1.砂型紧实度不够,型壳强度不够 2.浇注系统设计不合理 3.金属流速过快,充型不稳定 4.压射压力过高,压射速度过快 5.金属液头过高 掉砂 1.合型操作不正确 2.型砂紧实度不够 3.型壳强度不够,发生破裂 铸件缺陷分析 缺陷种类缺陷名称产生原因 多肉类外渗物(外渗豆)内渗物(内渗豆) 1.铸型、型号、型芯发气最大,透气性低,排气不畅
2.合金液有偏析倾向 3.凝固温度范围宽或凝固速度过慢 孔洞类气孔、针孔 1.铸件结构设计不正确,热节过多、过大 2.铸型、型壳、型芯、涂料等发气量大,透气性低,排气不畅 3.凝固温度范围宽,凝固速度数低 4.合金液含气量高,氧化夹杂物多 5.凝固时外压低 6.冷铁表面未清理干净,未挂涂料或涂料烘透 7.铜合金脱氧不彻底 8.浇注温度过高,浇注速度过快 缩孔 1.铸件结构设计不合理,壁厚悬殊,过渡外圆角太小:热节过多、过大2.浇注系统、冷铁、冒口安放不合理,不利于定向凝固 3.冒口补缩效率低 4.浇注温度过高 5.压射建压时间长,增压不起作用撮终补压压力不足,或压室的充满度不合理 6.比压太小,余料饼术薄,补压不起作用 7.内浇道厚度过小,溢流槽容量不够 8.熔模的模组分布不合理,造成局部散热困难 缩松疏松 1.合金的凝固温度范围宽,或凝固速度低 2.合金液体含气量高,透气性差 3.参见缩孔类 裂纹、冷隔类冷裂 1.铸件结构设计不合理,如易变形产品道部位未加工艺加强肋,未给出预变形量:壁厚悬殊等 2.铸型、型壳、砂芯、模具等退让性差 3.铸件冷却过程中,冷却不均匀 4.铸型、型壳、模具温度过低 5.钢液中含氧量过高 6.铸件落砂过早 7.水爆温度过高 热裂 1.铸件结构设计不合理,壁厚悬殊,造成过渡区应力集中 2.铸型、型壳、型芯,模具退让性差 3.压铸件留模时间过长 4.浇注温度过高:晶粒粗大 5.合金液中气体、夹杂含量过高
压铸件常见缺陷及产生原因
铝合金压铸件常见缺陷及产生原因 压铸件的缺陷特征,产生原因,防止方法 名称流痕及花纹网状毛翅脆性裂纹缩孔缩松 特征及检查方法外观检查:铸件表面上有与金属液流动方向一致的条纹,有明显可见的与金属基体颜色不一样无方向性的纹路,无发展趋势。外观检查:压铸件表面上有网状发丝一样凸起或凹陷的痕迹,随压铸次数增加而不断扩大和延伸外观检查或金相检查:合金晶粒粗大或极小,使铸件易断裂或碰碎外观检查:将铸件放在碱性溶液中,裂纹处呈暗灰色金属基体的破坏与裂开呈直线或波浪形,纹路狭小而长,在外力作用下有发展趋向裂纹有穿透和不穿透两种解剖外观检查或探伤检查;缩孔表面呈暗色并不光滑,形状不规则的孔洞,大而集中的为缩孔,小而分散的为缩松 产生原因 1,首先进入型腔的金属液形成一个极薄的而又不完全的金属层后,被后来的金属液所弥补而留下的痕迹。2,模温过低3,内浇道截面积过小及位置不当产生喷溅。4,作用于金属液上的压力不足花纹:涂料用量过多。 1,压铸模型腔表面龟裂2,压铸模材质不当或热处理工艺不正确3,压铸模冷热温差变化太大4,浇注温度过高5,压铸模预热不足6,型腔表面粗糙7,压铸模壁薄或有尖角 1,合金过热太大或保温时间过长2,激烈过冷,结晶过细3,铝合金含有锌铁等杂质太多4,铝合金中含铜超出规定范围在铸件上由于应力或外力而产生的裂纹1,锌合金铸件的裂纹(1)锌合金中有害杂质铅,锡,铁和镉的含量超过了规定范围(2)铸件从压铸模中取出过迟(3)型芯的抽出或推出受力不均(4)铸件的厚薄相接处转变剧烈(5)熔炼温度过高 2,铝合金铸件的裂纹(1)合金中铁含量过高或硅含量过低(2)合金中有害杂质的含量过高,降低了合金的的可塑性(3)铝硅合金:铝硅铜合金含锌或含铜量过高;铝镁合金中含镁量过多(4)模具,特别是型芯温度太低(5)铸件壁厚有剧烈变化之处(6)留模时间过长(7)顶出时受力不均 3,镁合金铸件的裂纹(1)合金中铝硅含量高(2)模具温度低(3)铸件壁厚薄变化剧裂(4)顶出和抽芯受力不均匀 4,铜合金铸件的裂纹(1)黄铜中锌的含量过高(冷裂)或过低(热裂)(2)硅黄铜中硅的含量高(3)开模时间晚,特别是型芯多的铸件缩孔是压铸件在冷凝过程中,内部补偿不足而造成的孔穴1,浇注温度过高2,压射比压低