钻孔灌注桩质量通病的成因及其预防措施

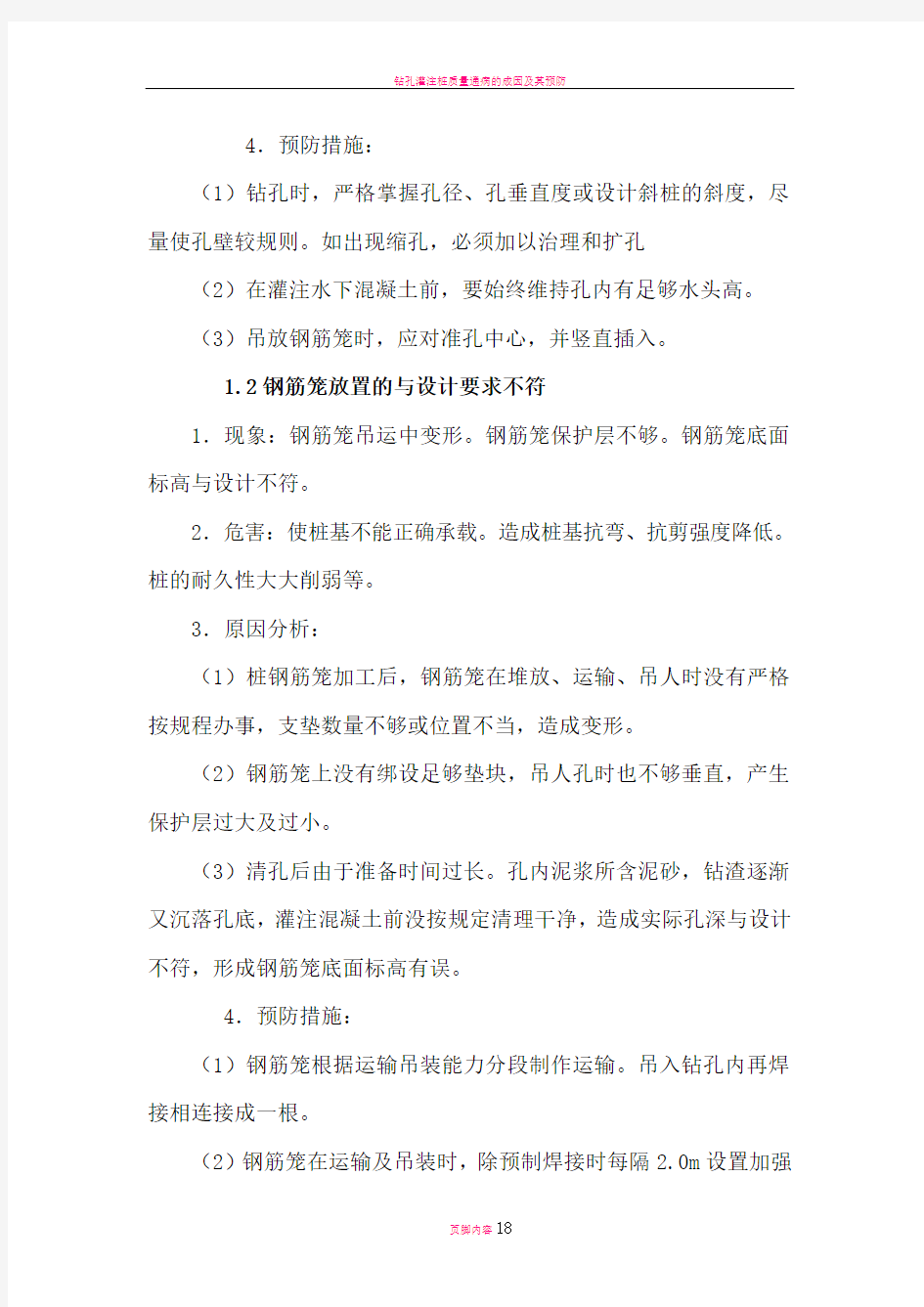
钻孔灌注桩质量通病的成因及其预防措施
钻孔灌注桩可以穿越各种土质复杂或软硬变化较大的土层(如各类黏性土、砂土、碎砾石土、风化岩及多夹层的岩层)对地基进行加固处理,其对承载力的适应范围广(为300~20000 kN),施工机具简单,且施工过程具有噪音低、对相邻楼宇影响小、施工安全性好等诸多优点,因而在基础加固工程中得到广泛地应用。但由于钻孔灌注桩的施工环节较多,技术要求高,工艺较复杂,需要在一个较短的时间内快速完成水下灌注混凝土隐蔽工程的灌注,无法直观的对质量进行控制,人为因素的影响较大,若稍有疏忽,很容易出现一些质量问题,甚至造成病桩、断桩等重大质量事故,危及桩基工程的安全。以下针对本工程的特点从分析桩基病害的成因入手,采取一些控制桩身质量病害的技术方法。
一、钻孔灌注桩质量通病与防冶措施
1.1 钢筋笼碰坍桩孔
1.现象:吊放钢筋笼入孔时。已钻好的孔壁发生坍塌。
2.危害:施工无法正常进行,严重时埋住钢筋笼。
3.原因分析:
(1)钻孔孔壁倾斜、出现缩孔等孔壁极不规则时,由于钢筋笼入孔撞击而坍孔。
(2)吊放钢筋笼时。孔内水位未保持住坍孔。
(3)吊放钢筋笼不仔细,冲击孔壁产生坍孔。
4.预防措施:
(1)钻孔时,严格掌握孔径、孔垂直度或设计斜桩的斜度,尽量使孔壁较规则。如出现缩孔,必须加以治理和扩孔
(2)在灌注水下混凝土前,要始终维持孔内有足够水头高。
(3)吊放钢筋笼时,应对准孔中心,并竖直插入。
1.2钢筋笼放置的与设计要求不符
1.现象:钢筋笼吊运中变形。钢筋笼保护层不够。钢筋笼底面标高与设计不符。
2.危害:使桩基不能正确承载。造成桩基抗弯、抗剪强度降低。桩的耐久性大大削弱等。
3.原因分析:
(1)桩钢筋笼加工后,钢筋笼在堆放、运输、吊人时没有严格按规程办事,支垫数量不够或位置不当,造成变形。
(2)钢筋笼上没有绑设足够垫块,吊人孔时也不够垂直,产生保护层过大及过小。
(3)清孔后由于准备时间过长。孔内泥浆所含泥砂,钻渣逐渐又沉落孔底,灌注混凝土前没按规定清理干净,造成实际孔深与设计不符,形成钢筋笼底面标高有误。
4.预防措施:
(1)钢筋笼根据运输吊装能力分段制作运输。吊入钻孔内再焊接相连接成一根。
(2)钢筋笼在运输及吊装时,除预制焊接时每隔2.0m设置加强
箍筋外,还应在钢筋笼内每隔3.0~4.0m装一个可拆卸的十字形临时加强架,待钢筋笼吊入钻孔后拆除。
(3)钢筋笼周围主筋上,每隔一定间距没混凝上垫块或塑料小轮状垫块,使混凝上垫块厚和小轮半径符合设计保护层厚。
(4)最好用导向钢管固定钢筋笼位置,钢筋笼顺导向钢管吊入孔中。这样,不仅可以保证钢筋的保护层厚符合设计要求,还可保证钢筋笼在灌注混凝土时,不会发生偏离。
(5)做好清孔,严格控制孔底沉淀层厚度,清孔后,及早进行混凝土灌注。
现场钻孔桩在灌注水下混凝土时的质量通病及防治
1.3 导管进水
1.现象:灌注桩首次灌注混凝土时,孔内泥浆及水从导管下口灌入导管;灌注中,导管接头处进水;灌注中,提升导管过量,孔内水和泥浆从导管下口涌人导管等现象。
2.危害:导管进水,轻者造成桩身混凝土离析,轻度央泥;重者产生桩身混凝土有夹层甚至发生断桩事故。
3.原因分析:
(1)首次灌注混凝土时,由丁灌满导管和导管下口至桩孔底部问隙所需的混凝土总量计箅不当,使首灌的混凝土不能埋住导管下口,而是全部冲出导管以外,造成导管底口进水事故。
(2)灌注混凝土中,山于未连续灌注,在导管内产生气囊。当又一次聚集大量混凝士拌合物猛灌,导管内气囊产生高压,将两节导
管间加入的封水橡皮垫挤出,致使导管接口漏空而进水。
(3)导管拼装后,未进行水密性试验。由于接头不严密,水从接口处漏入导管。
(4)测深时,误削造成导管提升过量,致使导管底口脱离孔内的混凝上液面,使泥水进入。
4.预防措施:
(1)确保首批灌注的混凝土总方量,能满足填充导管下口与桩孔底面间隙和使导管下口首灌时被埋没深度≥1m的需要。首灌前,导管下口距孔底一般不超过0.4m。
(2)在提升导管前,用标准测深锤(锤重不小于4kg,锤呈锥状。吊锤索用质轻,拉力强,浸水不伸缩的尼龙绳)测好混凝上表面的深度,控制导管提升高度,始终将导管底口埋于已灌入混凝上液面下不少于2m。
(3)下导管前。导管应进行试拼,并进行导管的水密性、承压性和接头抗拉强度的试验。试拼的导管,还要检查其轴线是否住一条直线上。试拼合格后,各节导管应从下而上依次编号,并标示累计长度。入孔拼装时,各节导管的编号及编号所在的圆周方位,应与试拼时相同,不得错、乱,或编号不在一个方位。
(4)首灌混凝土后,要保持混凝土连续地灌注。尽量缩短间隔时间。当导管内混凝上不饱满时,应徐徐地灌注,防止导管内形成高压气囊。
5.治理方法:首灌底口进水和灌注中导管提升过量的进水,一
旦发生,停止灌注。利用导管作吸泥管,以空气吸泥法,将已灌注的混凝土拌合物全部吸出。针对发生原因,予以纠正后,重新灌注混凝土。
1.4 导管进水
导管堵管
1.现象:导管已提升很高,导管底口埋入混凝土接近1m。但是灌注在导管中的混凝土仍不能涌翻上来。
2.危害:造成灌注中断,易在中断后灌注时形成高压气囊。严重时,易发展为断桩。
3.原因分析:
(1)由于各种原因使混凝土离析,粗骨料集中而造成导管堵塞。
(2)由于灌注时间持续过长,最初灌注的混凝土已初凝,增大了管内混凝二卜下落的阻力,使混凝土堵在管内。
4.预防措施:
(1)灌注混凝土的坍落度宜在18~22cm之间。并保证具有良好和易性。在运输和灌注过程中不发生显著离析和泌水。
(2)保证混凝土的连续灌注,中断灌注不应超过30min。
5.治理方法:灌注开始不久发生堵管时,可用长杆冲、捣或用振动器振动导管。若无效果,拔出导管,用空气吸泥机或抓斗将已灌入孔底的混凝土清出。换新导管,准备足够储量混凝土,重新灌注。
1.5 导管进水
提升导管时,导管卡挂钢筋笼
1.现象:导管提升时,导管接头法兰盘或螺栓挂住钢筋笼,无法提升导管。
2.危害:使灌注混凝土中断,易诱发导管堵塞。易演变成断桩、埋导管事故。
3.原因分析:
(1)导管拼装后,其轴线不顺直,弯折处偏移过大,提升导管时,挂住钢筋笼。
(2)钢筋笼搭接时,下节的主筋摆在外侧,上节的主筋在里侧,提升导管时被卡挂住。钢筋笼的加固筋焊在主筋内侧,也易挂在导管上。
(3)钢筋笼变形成折线或者弯曲线,使导管与其发生卡、挂。
4.预防措施:
(1)导管拼装后轴线顺直,吊装时,导管应位于井孔中央,并在灌注前进行升降是否顺利的试验。法兰盘式接口的导管,在连接处罩以圆锥形白铁罩。白铁罩底部与法兰盘大小一致,白铁罩顶与套管头上卡住。
(2)钢筋笼分段入孔前,应在其下端主筋端部加焊一道加强箍,入孔后各段相连时,应搭接方向适宜,接头处满焊。
5.治理方法:
(1)发生卡挂钢筋笼时。可转动导管,待其脱开钢筋笼后,将导管移至孔中央继续提升。
(2)如转动后仍不能脱开时,只好放弃导管,造成埋管。
1.6 钢筋笼在灌注混凝土时上浮
1.现象:钢筋笼入孔后,虽已加以固定。但在孔内灌注混凝土时,钢筋笼向上浮移。
2.危害:钢筋笼一旦发生上浮,基本无法使其归位,从而改变桩身配筋数量,损害桩身抗弯强度。
3.原因分析:混凝土由漏斗顺导管向下灌注时,混凝土的位能产生一种顶托力。该种顶托力随灌注时混凝土位能的大小,灌注速度的快慢,首批混凝土的流动度。首批混凝土的表面标高大小而变化。当顶托力大于钢筋笼的重量时。钢筋笼会被浮推上升。
4.预防措施:
(1)摩擦桩应将钢筋骨架的几根主筋延伸至孔底,钢筋骨架上端在孔口处与护筒相接固定。
(2)灌注中,当混凝土表面接近钢筋笼底时,应放慢混凝土灌注速度,并应使导管保持较大埋深,使导管底口与钢筋笼底端问保持较大距离.以便减小对钢筋笼的冲击。
(3)混凝土液面进入钢筋笼一定深度后,应适当提升导管,使钢筋笼在导管下口有一定埋深。但注意导管埋入混凝土表面应不小于2m。
1.7 灌注混凝士时桩孔坍孔
1.现象:灌注水下混凝土过程中,发现护简内泥浆水位忽然上升溢出护筒,随即骤降并冒出气泡,为坍孔征兆。如用测深锤探测混