精馏操作及精馏DCS操作精讲
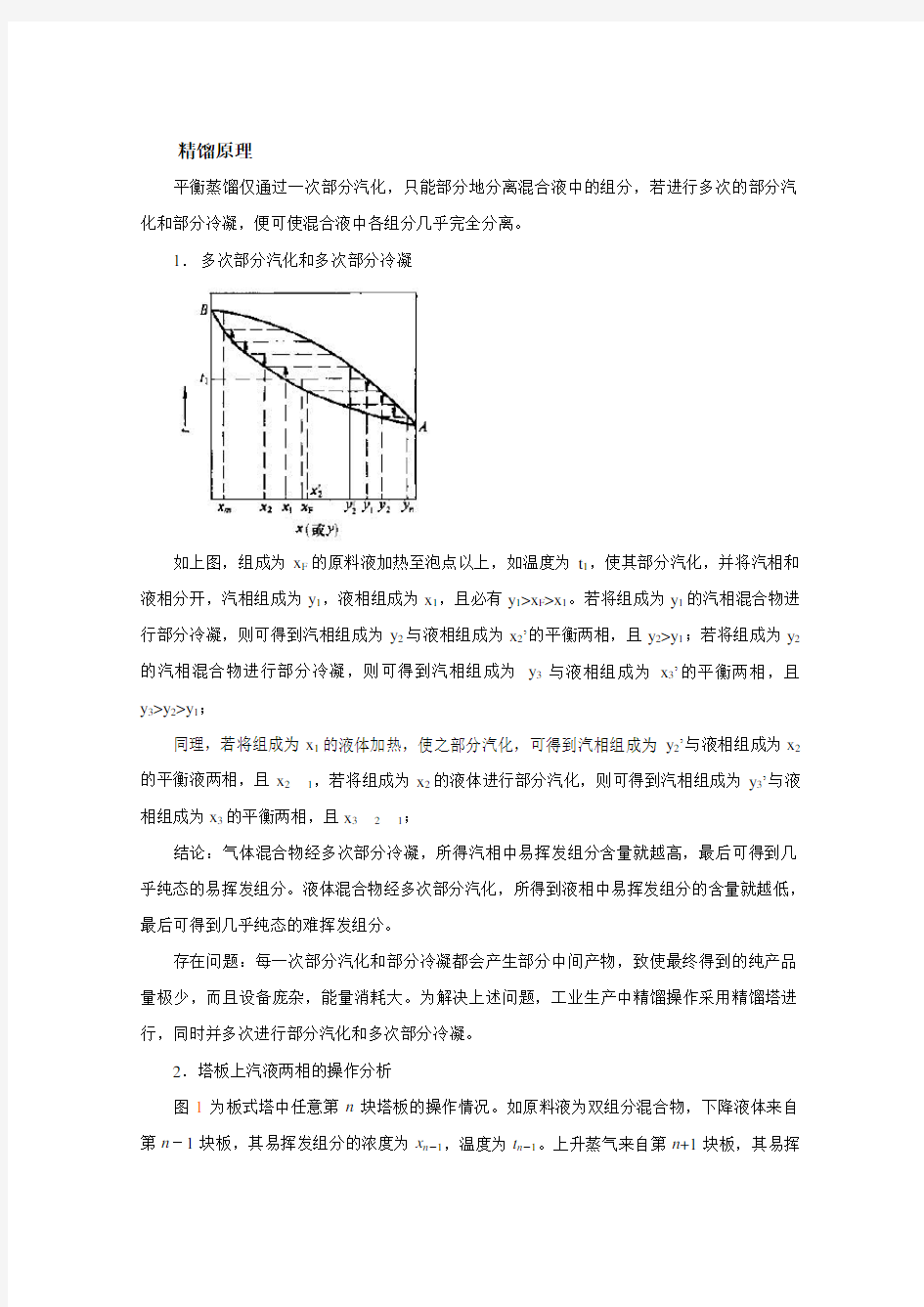

精馏原理
平衡蒸馏仅通过一次部分汽化,只能部分地分离混合液中的组分,若进行多次的部分汽化和部分冷凝,便可使混合液中各组分几乎完全分离。
1.多次部分汽化和多次部分冷凝
如上图,组成为x F的原料液加热至泡点以上,如温度为t1,使其部分汽化,并将汽相和液相分开,汽相组成为y1,液相组成为x1,且必有y1>x F>x1。若将组成为y1的汽相混合物进行部分冷凝,则可得到汽相组成为y2与液相组成为x2’的平衡两相,且y2>y1;若将组成为y2的汽相混合物进行部分冷凝,则可得到汽相组成为y3与液相组成为x3’的平衡两相,且y3>y2>y1;
同理,若将组成为x1的液体加热,使之部分汽化,可得到汽相组成为y2’与液相组成为x2的平衡液两相,且x2 结论:气体混合物经多次部分冷凝,所得汽相中易挥发组分含量就越高,最后可得到几乎纯态的易挥发组分。液体混合物经多次部分汽化,所得到液相中易挥发组分的含量就越低,最后可得到几乎纯态的难挥发组分。 存在问题:每一次部分汽化和部分冷凝都会产生部分中间产物,致使最终得到的纯产品量极少,而且设备庞杂,能量消耗大。为解决上述问题,工业生产中精馏操作采用精馏塔进行,同时并多次进行部分汽化和多次部分冷凝。 2.塔板上汽液两相的操作分析 图1为板式塔中任意第n块塔板的操作情况。如原料液为双组分混合物,下降液体来自第n-1块板,其易挥发组分的浓度为x n-1,温度为t n-1。上升蒸气来自第n+1块板,其易挥 发组分的浓度为y n+1,温度为t n+1。当气液两相在第n块板上相遇时,t n+1>t n-1,因而上升蒸气与下降液体必然发生热量交换,蒸气放出热量,自身发生部分冷凝,而液体吸收热量,自身发生部分气化。由于上升蒸气与下降液体的浓度互相不平衡,如2所示,液相部分气化时易挥发组分向气相扩散,气相部分冷凝时难挥发组分向液相扩散。结果下降液体中易挥发组分浓度降低,难挥发组分浓度升高;上升蒸气中易挥发组分浓度升高,难挥发组分浓度下降。 若上升蒸气与下降液体在第n块板上接触时间足够长,两者温度将相等,都等于t n,气液两相组成y n与x n相互平衡,称此塔板为理论塔板。实际上,塔板上的气液两相接触时间有限,气液两相组成只能趋于平衡。 图1塔板上的传质分析图2 精馏过程的t-x-y示意图 由以上分析可知,气液相通过一层塔板,同时发生一次部分汽化和一次部分冷凝。通过多层塔板,即同时进行了多次进行部分汽化和多次部分冷凝,最后,在塔顶得到的气相为较纯的易挥发组分,在塔底得到的液相为较纯的难挥发组分,从而达到所要求的分离程度。 3.精馏必要条件 为实现分离操作,除了需要有足够层数塔板的精馏塔之外,还必须从塔底引入上升蒸汽流(气相回流)和从塔顶引入下降的液流(液相回流),以建立气液两相体系。塔底上升蒸汽和塔顶液相回流是保证精馏操作过程连续稳定进行的必要条件。没有回流,塔板上就没有气液两相的接触,就没有质量交换和热量交换,也就没有轻、重组分的分离。 、精馏操作流程 精馏过程可连续操作,也可间歇操作。精馏装置系统一般都应由精馏塔、塔顶冷凝器、塔底再沸器等相关设备组成,有时还要配原料预热器、产品冷却器、回流用泵等辅助设备。 连续精馏装置流程如下图,所示。以板式塔为例,原料液预热至指定的温度后从塔的中段适当位置加入精馏塔,与塔上部下降的液体汇合,然后逐板下流,最后流入塔底,部分液体作为塔底产品,其主要成分为难挥发组分,另一部分液体在再沸器中被加热,产生蒸气, 蒸气逐板上升,最后进入塔顶冷凝器中,经冷凝器冷凝为液体,进入回流罐,一部分液体作为塔顶产品,其主要成分为易挥发组分,另一部分回流作为塔中的下降液体。 通常,将原料加入的那层塔板称为加料板。加料板以上部分,起精制原料中易挥发组分的作用,称为精馏段,塔顶产品称为馏出液。加料板以下部分(含加料板),起提浓原料中难挥发组分的作用,称为提馏段,从塔釜排出的液体称为塔底产品或釜残液 精馏塔的操作 一、影响精馏操作的主要因素 对于现有的精馏装置和特定的物系,精馏操作的基本要求是使设备具有尽可能大的生产能力,达到预期的分离效果,操作费用最低。影响精馏装置稳态、高效操作的主要因素包括操作压力、进料组成和热状况、塔顶回流、全塔的物料平衡和稳定、冷凝器和再沸器的传热性能,设备散热情况等。以下就其主要影响因素予以简要分析。 1.物料平衡的影响和制约 根据精馏塔的总物料衡算可知,对于一定的原料液流量F和组成x F,只要确定了分离程度x D和x W,馏出液流量D和釜残液流量W也就被确定了。而x D和x W决定了汽液平衡关系、x F、q、R和理论板数N T(适宜的进料位置),因此D和W或采出率D/F与W/F只能根据x D 和x W确定,而不能任意增减,否则进、出塔的两个组分的量不平衡,必然导致塔内组成变化, 操作波动,使操作不能达到预期的分离要求。 在精馏塔的操作中,需维持塔顶和塔底产品的稳定,保持精馏装置的物料平衡是精馏塔稳态操作的必要条件。通常由塔底液位来控制精馏塔的物料平衡。 2、塔顶回流的影响 回流比是影响精馏塔分离效果的主要因素,生产中经常用回流比来调节、控制产品的质量。例如当回流比增大时,精馏产品质量提高;反之,当回流比减小时,x D减小而x W增大,使分离效果变差。 回流比增加,使塔内上升蒸汽量及下降液体量均增加,若塔内汽液负荷超过允许值,则可能引起塔板效率下降,此时应减小原料液流量。 调节回流比的方法可有如下几种。 (1)减少塔顶采出量以增大回流比。 (2)塔顶冷凝器为分凝器时,可增加塔顶冷剂的用量,以提高凝液量,增大回流比。 (3)有回流液中间贮槽的强制回流,可暂时加大回流量,以提高回流比,但不得将回流贮槽抽空。 必须注意,在馏出液采出率D/F规定的条件下,籍增加回流比R以提高x D的的方法并非总是有效。此外,加大操作回流比意味着加大蒸发量与冷凝量,这些数值还将受到塔釜及冷凝器的传热面的限制。 3.进料热状况的影响 当进料状况(x F和q)发生变化时,应适当改变进料位置,并及时调节回流比R。一般精馏塔常设几个进料位置,以适应生产中进料状况,保证在精馏塔的适宜位置进料。如进料状况改变而进料位置不变,必然引起馏出液和釜残液组成的变化。 进料情况对精馏操作有着重要意义。常见的进料状况有五种,不同的进料状况,都显著地直接影响提馏段的回流量和塔内的汽液平衡。精馏塔较为理想的进料状况是泡点进料,它较为经济和最为常用。对特定的精馏塔,若x F减小,则将使x D和x W均减小,欲保持x D不变,则应增大回流比。 4.塔釜温度的影响 釜温是由釜压和物料组成决定的。精馏过程中,只有保持规定的釜温,才能确保产品质量。因此釜温是精馏操作中重要的控制指标之一。 提高塔釜温度时,则使塔内液相中易挥发组分减少,同时,并使上升蒸汽的速度增大,有利于提高传质效率。如果由塔顶得到产品,则塔釜排出难挥发物中,易挥发组分减少,损失减少;如果塔釜排出物为产品,则可提高产品质量,但塔顶排出的易挥发组分中夹带的难挥发组分增多,从而增大损失。因此,在提高温度的时候,既要考虑到产品的质量,又要考虑到工艺损失。一般情况下,操作习惯于用温度来提高产品质量,降低工艺损失。 当釜温变化时,通常是用改变蒸发釜的加热蒸汽量,将釜温调节至正常。当釜温低于规定值时,应加大蒸汽用量,以提高釜液的汽化量,使釜液中重组分的含量相对增加,泡点提高,釜温提高。当釜温高于规定值时,应减少蒸汽用量,以减少釜液的汽化量,使釜液中轻组分的含量相对增加,泡点降低,釜温降低。此外还有与液位串级调节的方法等。 5.操作压力的影响 塔的压力是精馏塔主要的控制指标之一。在精馏操作中,常常规定了操作压力的调节范围。塔压波动过大,就会破坏全塔的气液平衡和物料平衡,使产品达不到所要求的质量。 提高操作压力,可以相应地提高塔的生产能力,操作稳定。但在塔釜难挥发产品中,易挥发组分含量增加。如果从塔顶得到产品,则可提高产品的质量和易挥发组分的浓度。 影响塔压变化的因素是多方面的,例如:塔顶温度,塔釜温度、进料组成、进料流量、回流量、冷剂量、冷剂压力等的变化以及仪表故障、设备和管道的冻堵等,都可以引起塔压的变化。例如真空精馏的真空系统出了故障、塔顶冷凝器的冷却剂突然停止等都会引起塔压的升高。 对于常压塔的压力控制,主要有以下三种方法。 (1)对塔顶压力在稳定性要求不高的情况下,无需安装压力控制系统,应当在精馏设备(冷凝器或回流罐)上设置一个通大气的管道,以保证塔内压力接近于大气压。 (2)对塔顶压力的稳定性要求较高或被分离的物料不能和空气接触时,若塔顶冷凝器为全凝器时,塔压多是靠冷剂量的大小来调节。 (3)用调节塔釜加热蒸汽量的方法来调节塔釜的气相压力。 在生产中,当塔压变化时,控制塔压的调节机构就会自动动作,使塔压恢复正常。当塔压发生变化时,首先要判断引起变化的原因,而不要简单地只从调节上使塔压恢复正常,要从根本上消除变化的原因,才能不破坏塔的正常操作。如釜温过低引起塔压降低,若不提釜温,而单靠减少塔顶采出来恢复正常塔压,将造成釜液中轻组分大量增加。由于设备原因而 影响了塔压的正常调节时,应考虑改变其它操作因素以维持生产,严重时则要停车检修。 精馏塔的开车、停车操作 (一)开车操作 (1)接到开车命令后,马上与有关岗位联系,进行开车。 (2)严格遵守工艺规程,岗位操作法,加强巡回检查。 (3)精心调节。进料要求平稳,塔釜见液面后,按其升温速度缓慢升温至工艺指标。随着塔压力的升高,逐渐排除设备内的惰性气体,并逐渐加大塔顶冷凝器的冷剂量,当回流液槽的液面达1/2以上时,开始打回流。当釜液面达2/3时,可根据釜温的情况,决定是否采出釜液或减少以至停止塔的进料量,但是一定要保持塔釜液面在1/2~2/3处。操作平稳后,应进行物料分析,对不合格的物料可进行少量地采出或全回流操作,待分析合格后,转入连续生产。 空塔加料时,由于没有回流液体,精馏段的塔板上是处于干板操作的状态。由于没气液接触,气相中的难挥发组分容易被直接带入精馏段。如果升温速度过快,则难挥发组分会大量地被带到精馏段,而不易为易挥发组分所置换,塔顶产品的质量不易达到合格,造成开车时间长。当塔顶有了回流掖,塔板上建立了液体层后,升温速度可适当的提高。减压精馏塔的升温速度,对于开车成功与否的影响,将更为显著。例如,对苯酚的减压精馏,已有经验证明,升温速度一般应维持在塔内上升蒸汽的速度为1.5~3米/秒,每块塔板的阻力为1~3mmhg。如果升温速度太快,则顶部尾气的排出量太大,真空设备的负荷增大,在真空泵最大负荷的限制下,可能使塔内的真空度下降,开车不易成功。 (4)开车时,对阀门,仪表的调节一定要勤调,慢调,合理使用。 (5)发现有不正常现象应及时分析原因,果断进行处理。 (二)停车操作 精馏塔的停车,可分为临时停车和长期停车两种情况: 1.临时停车 接停车命令后,马上停止塔的进料、塔顶采出和塔釜采出,进行全回流操作。适当的减少塔顶冷剂量及塔釜热剂量,全塔处于保温、保压的状态。如果停车时间较短,可根据塔的具体情况处理,只停塔的进料,可不停塔顶采出(此时为产品),以免影响后工序的生产,但塔釜采出应关闭。这种操作破坏了正常的物料平衡,不可长时间的应用,否则产品质量就会下 降。 2.常期停车 按停车命令后,立即停止塔的进料,产品可继续进行采出,当分析结果不合格时,可停止采出,同时停止塔釜加热和塔顶冷凝,然后放尽釜液。对于分离低沸点物料的塔,釜液的放尽要缓慢地进行,以防止节流造成过低的温度使设备材质冷脆。放尽完毕后,把设备内的余压泄除,再用氮气置换,合格后才能进行检修。若设备内须进人检修,还需用空气置换氮气,在设备内气体中的氧含量达19%(体积)以上时,才允许检修人员进入。 精馏塔操作仿真训练 训练准备 熟悉工艺流程及原理。 本单元是一种加压精馏操作,原料液为脱丙烷塔塔釜的混合液,分离后馏出液为高纯度的C4产品,残液主要是C5以上组分。 67.8℃的原料液经流量调节器FICl01控制流量(14056kg/h)后,从精馏塔DA405的第16块塔板(全塔共32块塔板)进料。塔顶蒸气经全凝器EA419冷凝为液体后进入回流罐FA408;回流罐FA408的液体由泵GA412A/B抽出,一部分作为回流液由调节器FCl04控制流量(9664kgm)送回DA405第32层塔板;另一部分则作为产品,其流量由调节器FCl03控制(6707kg /h)。回流罐的液位由调节器LCl03与FCl03构成的串级控制回路控制。DA405操作压力由调节器PCI02分程控制为5.0kg/m2,其分程动作如图3所示。同时调节器PCI01将调节回流罐的气相出料,保证系统的安全和稳定。 图3调节阀PVl02分程动作示意图 塔釜液体的一部分经再沸器EA408A/B回精馏塔,另一部分由调节器FCl02控制流量(7349kg/h),作为塔底采出产品。调节器LCl01和FCl02构成串级控制回路,调节精馏塔的 液位。再沸器用低压蒸汽加热,加热蒸汽流量由调节器TCl01控制,其冷凝液送FA414。 FA414的液位由调节器LCl02调节。其工艺流程如图4所示。 图4精馏塔单元带控制点工艺流程图 ●训练步骤(要领) (一)冷态开车 进料前确认装置冷态开工状态为精馏塔单元处于常温、常压、氮气吹扫完毕的氮封状态,所有阀门、机泵处于关停状态、所有调节器置于手动状态。 1.进料及排放不凝气 (1)打开PVl01(开度>5%)排放塔内不凝气; (2)打开FVl01(开度>40%),向精馏塔进料; (3)进料后,塔内温度略升、压力升高;当压力升高至0.5atm(表)时 (4)控制塔顶压力大于1.0atm(表),不超过4.25atm(表)。 2.启动再沸器 (1)待塔顶压力PCI01升至0.5atm(表),逐渐打开冷凝水调节阀PVl02A(至开度为50%); (2)待塔釜液位LICl01升至20%以上,全开加热蒸汽入口阀V13,手动缓开调节阀TVl01, 给再沸器缓慢加热; (3)将蒸气缓冲罐FA414的液位LCl02设定为50%,投自动; (4)逐渐开大TVl01至50%,,使塔釜温度逐渐上升至100℃,灵敏板温度升至75℃。 3.建立回流 (1)待回流罐液位LICl03升至20%,灵敏板温度TCl01指示值高于75o C,塔釜温度高于100o C后,依次全开回流泵GA412A入口阀V19,启动泵,全开泵出口阀V17; (2)手动打开调节阀FVl04(开度>40%),全回流操作:维持回流罐液位升至40%。 4.调整至正常 (1)待塔压稳定后,将PCI01和PCI02投自动; (2)逐步调整进料量为14056kg/h,稳定后将FICl01投自动; (3)通过TICl01调节再沸器加热量使灵敏板温度稳定在89.3℃在109.3℃,将TICl01投自动; (4)在保证回流罐液位和塔顶温度的前提下,逐步加大回流量,将调节阀FVl04开至50%,最后当FCl04流量稳定在9664kWh,将其投自动; (5)当塔釜液位无法维持时,逐渐打开FCl02,采出塔釜产品;同时将LICl01输出设为50%,投自动:当塔釜产品采出量稳定在7349kg/h,将FCl02先投自动,再投串级: (6)当回流罐液位无法维持时,’逐渐打开:FVl03,采出塔顶产品;同时将LCl03输出为50%,投自动:待采出量稳定在6707kgth,将FICl03先投自动,再投串级。 (二)正常运行 熟悉工艺流程,维持各工艺参数稳定;密切注意各工艺参数的变化情况,发现突发事故时,应先分析事故原因,并做及时正确的处理。 (三)正常停车 1.降负荷 (1)手动逐步关小调节阀FVl01(开度<35%),使进料降至正常进料量的70%; (2)同时保持灵敏板温度TCl01和塔压:PCI02的稳定性,使精馏塔分离出合格的产品; (3)降负荷过程中,断开LCl03和FCl03的串级,手动开大FVl03(开度>90%),尽量通过FVl03排出回流罐中的液体产品,至回流罐液位降至20%左右: (4)同时,断开LCl01和FCl02的串级,手动开大FVl02(开度>90%)出塔釜产品,使液位 LCl01降至30%左右。 2.停进料和再沸器 在负荷降至正常的70%,且产品已大部分采出后,停进料和再沸器。 (1)精馏塔进料,关闭调节阀FVl01 (2)停加热蒸汽,关闭调节阀TVl01,关加热蒸汽阀V13; (3)停止产品采出,手动关闭FVl02和FVl03; (4)打开塔釜泄液阀V10,排出不合格产品; (5)手动打开LVl02,对FA414进行泄液。 3.停回流 (1)手动开大FVl04,将回流罐内液体全部打入精馏塔,以降低塔内温度; (2)当回流罐液位降至0%,停回流,关闭调节阀FVl04; (3)依次关泵出口阀V17,停泵GA412A,关入口阀V19。 4.降压、降温 (1)塔内液体排完后,进行降压,手动打开PVl01,当塔压降至常压后,关闭PVl01; (2)灵敏塔板温度降至50℃以下,关塔顶冷凝器冷凝水,手动关闭PVl02A(开度为0%)。 (3)当塔釜液位降至0%后,关闭泄液阀V10。 ●思考与分析 1.回流量过大,精馏塔塔顶温度、压力、塔釜液位会发生什么变化?对产品分离有什么影响? 2.若精馏塔灵敏板温度过高或过低,则意味着分离效果如何?应通过改变哪些变量来调节至正常? 3.精馏塔塔釜液位过高,可以通过哪几种方法调节至正常? 4.精馏塔塔顶温度过高,对产品分离有什么影响?哪些因素会导致这种现象 5.精馏塔压力过高的原因有哪些?可以通过哪些手段调节至正常? 6.请分析本流程中如何通过分程控制来调节精馏塔正常操作压力的。可以采取的措施是什么? ●拓展型训练 常见事故处理见表3-6。 表3-6 常见事故处理 阅读资料多组分精馏简介 工业上常遇到的精馏操作是多组分精馏。虽然多组分精馏与双组分精馏在基本原理上是相同的,但因多组分精馏中溶液的组分数目增多,故影响精馏操作的因素也增多。 双组分溶液的普通精馏过程在一个精馏塔可以进行分离,但对多组分溶液精馏则不然。 因受汽液平衡的限制,所以要在一个普通精馏塔内同时得到几个相当纯的组分是不可能的。例如分离三组分溶液时需要两个塔,四组分溶液时需要三个塔,……,n组分溶液时需要n-1个塔。应当指出,塔数越多,导致流程组织方案也多。 在化工生产中,多组分精馏流程方案的分类,主要是按照精馏塔中组分分离的顺序安排而区分的。第一种是按挥发度递减的顺序采出馏分的流程;第二种是按挥发度递增的顺序采出馏分的流程;第三种是按不同挥发度交错采出的流程。 供选择的分离流程的方案数,随组分增加而急剧递增。如何确定最佳的分离方案,是一个很关键的问题。分离方案的选择应尽量做到以下几点:(1)满足工艺要求;(2)减少能量消耗;(3)节省设备投资。若进料中有一个组分的含量占主要时,应先将它分离掉,以减少后续塔及再沸器的负荷;若进料中有一个组分具有强腐蚀性,则应尽早将它除去,以便后续塔无需采用耐腐蚀材料制造,相应减少设备投资费用。确定多组分精馏的最佳方案时,通常先以满足工艺要求,保证产品质量和产量为主,然后再考虑降低生产成本等问题。 在待分离的多组分溶液中,选取工艺中最关心的两个组分,规定它们在塔顶和塔底产品中的组成或回收率(即分离要求),那么在一定的分离条件下,所需的理论板层数和其它组分的组成也随之而定。由于所选定的两个组分对多组分溶液的分离起控制作用,故称它们为关键组分,其中挥发度高的组分称为轻关键组分,挥发度低的称为重关键组分。 在进料中,轻关键组分和比其沸点更低的组分绝大部分进入塔顶馏出液中;重关键组分和比其沸点更高的组分绝大部分进入塔底产品中。换言之,关键组分的分离程度达到要求,其它组分的分离程度也达到要求。对多组分物系的分离简化为对两个关键组分的分离。 主要符号 C——负荷因子,m/s; c pc——冷却介质的比热容,kJ/(kg·℃);D——塔顶产品的流量,Kmol/h;D——塔径,m; E T——全塔效率,%; E MV——汽相单板效率,%; E ML——液相单板效率,%;F——原料的流量,Kmol/h;Hz——塔有效高度,m; H T——塔板间距,m;Ha——顶部空间高度,m;Hb——底部空间高度,m;Hs——裙座高度,m; I F——原料液焓,KJ/Kmol; I V、I V’——加料板上、下的饱和蒸汽焓,KJ/Kmol; I L、I L’ ——加料板上、下的饱和液体焓,KJ/Kmol; I VD——塔顶上升蒸汽的焓,kJ/kmol; I LD——塔顶馏出液的焓,kJ/kmol; I B——加热介质的焓,kJ/kg; I VW——再沸器中上升蒸汽的焓,kJ/kmol; I LW——釜残液的焓,kJ/kmol; I Lm——提馏段底层塔板下降液体的焓, kJ/kmol; L——精馏段下降液体的摩尔流量,kmol/h;L’——提馏段下降液体的摩尔流量,kmol/h;N T——理论板层数; N P——实际塔板层数; N min——全回流时的最小理论板数;V——精馏段上升蒸汽的摩尔流量,kmol/h;V’——提馏段上升蒸汽的摩尔流量,kmol/h;V S——操作条件下塔内上升蒸汽的体积流量,m3/s; v i——溶液中组分的挥发度; R——回流比; Rmin——最小回流比; r ——加热蒸汽的汽化热,kJ/kg; W——塔底产品的流量,Kmol/h; u——空塔速度,m/s; u max——最大允许气速,m/s; P——操作压力,Pa; p A、p B——溶液上方A,B组分的平衡分压,Pa; p0——在溶液温度下纯组成的饱 和蒸汽压,Pa; Q B——再沸器的热负荷,kJ/h; Q L——再沸器的热损失,kJ/h; Q C——全凝器的热负荷,kJ/h; q——进料热状态参数; t—温度,℃; W h——加热介质消耗量,kg/h; W C——冷却介质消耗量,kg/h; x A 、x B——溶液中A,B组分的 摩尔分数; x F——原料中易挥发组分的摩尔分数; x D——塔顶产品中易挥发组分的摩尔分数;x W——塔底产品中易挥发组分的摩尔分数;x n——精馏段第n层板下降液体中易挥发组分的摩尔分数; x’m——提馏段第m层板下降液相中易挥发组分的摩尔分数; x* n ——与y n成平衡的液相组成; y* n ——与x n成平衡的汽相组成; y n+1——精馏段第n十1层板上升蒸汽中易挥发组分的摩尔分数; y’m+1——提馏段第m+1层板上升蒸汽中易挥发组分的摩尔分数; x q、y q——相平衡线与进料线交点坐标; ρL——液相密度,kg/m3; ρV——气相密度,kg/m3; ——相对挥发度; αm——全塔平均相对挥发度; μL——塔顶与塔底平均温度下的液体粘度。 精馏原理 平衡蒸馏仅通过一次部分汽化,只能部分地分离混合液中的组分,若进行多次的部分汽化和部分冷凝,便可使混合液中各组分几乎完全分离。 1.多次部分汽化和多次部分冷凝 如上图,组成为x F的原料液加热至泡点以上,如温度为t1,使其部分汽化,并将汽相和液相分开,汽相组成为y1,液相组成为x1,且必有y1>x F>x1。若将组成为y1的汽相混合物进行部分冷凝,则可得到汽相组成为y2与液相组成为x2’的平衡两相,且y2>y1;若将组成为y2的汽相混合物进行部分冷凝,则可得到汽相组成为y3与液相组成为x3’的平衡两相,且y3>y2>y1; 同理,若将组成为x1的液体加热,使之部分汽化,可得到汽相组成为y2’与液相组成为x2的平衡液两相,且x2 发组分的浓度为y n+1,温度为t n+1。当气液两相在第n块板上相遇时,t n+1>t n-1,因而上升蒸气与下降液体必然发生热量交换,蒸气放出热量,自身发生部分冷凝,而液体吸收热量,自身发生部分气化。由于上升蒸气与下降液体的浓度互相不平衡,如2所示,液相部分气化时易挥发组分向气相扩散,气相部分冷凝时难挥发组分向液相扩散。结果下降液体中易挥发组分浓度降低,难挥发组分浓度升高;上升蒸气中易挥发组分浓度升高,难挥发组分浓度下降。 若上升蒸气与下降液体在第n块板上接触时间足够长,两者温度将相等,都等于t n,气液两相组成y n与x n相互平衡,称此塔板为理论塔板。实际上,塔板上的气液两相接触时间有限,气液两相组成只能趋于平衡。 图1塔板上的传质分析图2 精馏过程的t-x-y示意图 由以上分析可知,气液相通过一层塔板,同时发生一次部分汽化和一次部分冷凝。通过多层塔板,即同时进行了多次进行部分汽化和多次部分冷凝,最后,在塔顶得到的气相为较纯的易挥发组分,在塔底得到的液相为较纯的难挥发组分,从而达到所要求的分离程度。 3.精馏必要条件 为实现分离操作,除了需要有足够层数塔板的精馏塔之外,还必须从塔底引入上升蒸汽流(气相回流)和从塔顶引入下降的液流(液相回流),以建立气液两相体系。塔底上升蒸汽和塔顶液相回流是保证精馏操作过程连续稳定进行的必要条件。没有回流,塔板上就没有气液两相的接触,就没有质量交换和热量交换,也就没有轻、重组分的分离。 、精馏操作流程 精馏过程可连续操作,也可间歇操作。精馏装置系统一般都应由精馏塔、塔顶冷凝器、塔底再沸器等相关设备组成,有时还要配原料预热器、产品冷却器、回流用泵等辅助设备。 连续精馏装置流程如下图,所示。以板式塔为例,原料液预热至指定的温度后从塔的中段适当位置加入精馏塔,与塔上部下降的液体汇合,然后逐板下流,最后流入塔底,部分液体作为塔底产品,其主要成分为难挥发组分,另一部分液体在再沸器中被加热,产生蒸气, aspen模拟塔设计(转载) 一、板式塔工艺设计 首先要知道工艺计算要算什么?要得到那些结果?如何算?然后再进行下面的计算步骤。(参考) 其次要知道你用的软件(或软件模块)能做什么,不能做什么?你如何借助它完成给定的设计任务。 记住:你是工艺设计者,没有 aspen 你必须知道计算过程及方法,能将塔设计出来,这是你经过课程学习应该具有的能力,理论上讲也是进入毕业设计的前提。只是设计过程中将复杂的计算过程交给 aspen 完成, aspen 只替你计算,不能替你完成你的设计。做不到这一点说明工艺设计部份还不合格,毕业答辩就可能要出问题,实际的这是开题时要做的事的一部份,开题答辩就是要考察这个方面的问题。 设计方案,包括设计方法、路线、分析优化方案等,应该是设计开题报告中的一部份。没有很好的设计方案,具体作时就会思路不清晰,足见开题的重要性。下面给出工艺设计计算方案参考,希望借此对今后的结构和强度设计作一个详细的设计方案,明确的一下接下来所有工作详细步骤和方法,以便以后设计工作顺利进行。 板式塔工艺计算步骤 1.物料衡算(手算) 目的:求解 aspen 简捷设计模拟的输入条件。 内容:(1) 组份分割,确定是否为清晰分割; (2)估计塔顶与塔底的组成。 得出结果:塔顶馏出液的中关键轻组份与关键重组份的回收率 参考:《化工原理》有关精馏多组份物料平衡的内容。 2.用简捷模块(DSTWU)进行设计计算 目的:结合后面的灵敏度分析,确定合适的回流比和塔板数。 方法:选择设计计算,确定一个最小回流比倍数。 得出结果:理论塔板数、实际板数、加料板位置、回流比,蒸发率等等RadFarce 所需要的所有数据。 精馏塔单元仿真实训指导书 目录 一、工艺流程说明 (1) 1、工艺说明 (1) 2、本单元复杂控制方案说明 (2) 3、设备一览 (2) 二、精馏单元操作规程 (2) 1、冷态开车操作规程 (2) 2、正常操作规程 (3) 3、停车操作规程 (4) 4、仪表一览表 (6) 三、事故设置一览 (7) 四、仿真界面 (9) 附:思考题 (11) 一、工艺流程说明 1、工艺说明 本流程是利用精馏方法,在脱丁烷塔中将丁烷从脱丙烷塔釜混合物中分离出来。精馏是将液体混合物部分气化,利用其中各组分相对挥发度的不同,通过液相和气相间的质量传递来实现对混合物分离。本装置中将脱丙烷塔釜混合物部分气化,由于丁烷的沸点较低,即其挥发度较高,故丁烷易于从液相中气化出来,再将气化的蒸汽冷凝,可得到丁烷组成高于原料的混合物,经过多次气化冷凝,即可达到分离混合物中丁烷的目的。 原料为67.8℃脱丙烷塔的釜液(主要有C4、C5、C6、C7等),由脱丁烷塔(DA-405)的第16块板进料(全塔共32块板),进料量由流量控制器FIC101控制。灵敏板温度由调节器TC101通过调节再沸器加热蒸汽的流量,来控制提馏段灵敏板温度,从而控制丁烷的分离质量。 脱丁烷塔塔釜液(主要为C5以上馏分)一部分作为产品采出,一部分经再沸器(EA-418A、B)部分汽化为蒸汽从塔底上升。塔釜的液位和塔釜产品采出量由LC101和FC102组成的串级控制器控制。再沸器采用低压蒸汽加热。塔釜蒸汽缓冲罐(FA-414)液位由液位控制器LC102调节底部采出量控制。 塔顶的上升蒸汽(C4馏分和少量C5馏分)经塔顶冷凝器(EA-419)全部冷凝成液体,该冷凝液靠位差流入回流罐(FA-408)。塔顶压力PC102采用分程控制:在正常的压力波动下,通过调节塔顶冷凝器的冷却水量来调节压力,当压力超高时,压力报警系统发出报警信号,PC102调节塔顶至回流罐的排气量来控制塔顶压力调节气相出料。操作压力 4.25atm (表压),高压控制器PC101将调节回流罐的气相排放量,来控制塔内压力稳定。冷凝器以冷却水为载热体。回流罐液位由液位 精馏操作实训 一、实训目标 1.熟悉板式精馏塔的工作原理、基本结构及流程。 2.了解精馏塔控制时需要检测及控制的参数、检测位置、检测传感器及控制方法。 3.观察塔板上气-液传质过程全貌,掌握精馏塔的操作及影响因素,进行现场故障分析。 4.能识读精馏岗位的工艺流程图、设备示意图、设备的平面图和设备布置图; 5.了解掌握工业现场生产安全知识。 二、实训内容 1.简要叙述精馏操作气-液相流程,指出精馏塔塔板、塔釜再沸器、塔顶全凝器等主要装置的作用。 2.独立地进行精馏岗位开、停车工艺操作,包括开车前的准备、电源的接通、冷却水量的控制、电源加热温度的控制等。 3.进行全回流操作,通过观测仪表对全回流操作的稳定性作出正确的判断; 4.进行部分回流操作,通过观测仪表对部分回流操作的稳定性作出正确的判断,按照生产要求达到规定的产量指标和质量指标。 5.及时掌握设备的运行情况,随时发现、正确判断、及时处理各种异常现象,特殊情况能进行紧急停车操作。 6.能掌握现代信息技术管理能力,采用DCS集散控制系统,应用计算机对现场数据进行采集、监控和处理异常现象。 7.正确填写生产记录,及时分析各种数据。 三、基本原理 精馏利用液体混合物中各组分挥发度的差异,使液体混合物部分汽化并随之使蒸气部分冷凝,从而实现其所含组分的分离。精馏广泛应用于炼油、化工、轻工等领域。通过加热料液使它部分汽化,易挥发组分在蒸气中得到增浓,难挥发组分在剩余液中也得到增浓,这在一定程度上实现了两组分的分离。两组分的挥发能力相差越大,则上述的增浓程度也越大。在工业精馏设备中,使部分汽化的液相与部分冷凝的汽相直接接触,以进行汽液相际传质,结果是汽相中的难挥发组分部分转入液相,液相中的易挥发组分部分转入汽相,也即同时实现了液相的部分汽化和汽相的部分冷凝。 四、实训装置及流程 (一)流程介绍 (1)常压精馏流程 化 工 单 元 操 作 仿 真 实 训 总 结 姓名:XX 班级;XX班 学号:XXXX 目录 一、实训内容 1、精馏塔仿真 2、液位控制仿真 3、吸收解吸仿真 4、萃取仿真 5、灌区仿真 6、真空仿真 二、仿真总结 一、实训内容 1、精馏塔仿真 1.1操作原理: 精馏原理精馏操作迫使混合物的气、液两相在精馏塔体中作逆向流动,在互相接触过程中,液相中的轻组分逐渐转入气相,而气相中的重组分则逐渐进入液相。精馏过程本质上是一种传质过程,也伴随着传热。在恒定压力下,对单组分液体在沸腾时继续加热,其温度保持不变。但对于多组分的理想溶液来说,在恒定压力下,沸腾溶液的温度却是可变的。一般而言,在恒定压力下,溶液气液相平衡与其组分有关。高沸点组分的浓度越高,溶液平衡温度越高。与纯物质的气液平衡相比较,溶液气液平衡的一个特点是:在平衡态下,气相浓度与液相浓度是不相同的。一般情况下,气相中的低沸点组分的浓度高于它在液相中的数值.对于纯组分的气液相平衡,把恒定压力下的平衡温度称为该压力下的沸点或冷凝点。但对于处在相平衡的溶液,则把平衡温度称为在该压力下某气相浓度的露点温度或对应的液相浓度的泡点温度。对于同一气相和液相来说,露点温度与泡点一般是不相等的,前者比后者高。 1.2工艺流程: 进料及排放不凝气 启动再沸器 建立回流 调整至正常 1.3仿真图: 2.1操作原理: 缓冲罐V101仅一股来料,8Kg/cm2压力的液体通过调节产供阀FIC101向罐V101充液,此罐压力由调节阀PIC101分程控制,缓冲罐压力高于分程点(5.0Kg/cm2)时,PV101B自动打开泄压,压力低于分程点时,PV101B自动关闭,PV101A自动打开给罐充压,使V101压力控制在5Kg/cm2。缓冲罐V101液位调节器LIC101和流量调节阀FIC102串级调节,一般液位正常控制在50%左右,自V101底抽出液体通过泵P101A或P101B(备用泵)打入罐V102,该泵出口压力一般控制在9Kg/cm2,FIC102流量正常控制在20000Kg/hr。 罐V102有两股来料,一股为V101通过FIC102与LIC101串级调节后来的流量;另一股为8Kg/cm2压力的液体通过调节阀LIC102进入罐V102,一般V102液位控制在50%左右,V102底液抽出通过调节阀FIC103进入V103,正常工况时FIC103的流量控制在30000 kg/hr。 罐V103也有两股进料,一股来自于V102的底抽出量,另一股为8kg/cm2压力的液体通过FIC103与FI103比值调节进入V103,比值系数为2:1,V103底液体通过LIC103调节阀输出,正常时罐V103液位控制在50%左右。 2.2工艺流程: 缓冲罐V-101充压及液位建立 中间罐V-102液位建立 产品罐V-103建立液位 2.3、仿真图: 文档编号:精馏塔操作手册.DOC 精馏塔单元仿真培训系统 操作说明书 北京东方仿真控制技术有限公司 二零零四年八月 一工艺流程说明 本流程是利用精馏方法,在脱丁烷塔中将丁烷从脱丙烷塔釜混合物中分离出来。精馏是将液体混合物部分气化,利用其中各组分相对挥发度的不同,通过液相和气相间的质量传递来实现对混合物分离。本装置中将脱丙烷塔釜混合物部分气化,由于丁烷的沸点较低,即其挥发度较高,故丁烷易于从液相中气化出来,再将气化的蒸汽冷凝,可得到丁烷组成高于原料的混合物,经过多次气化冷凝,即可达到分离混合物中丁烷的目的。 原料为67.8℃脱丙烷塔的釜液(主要有C4、C5、C6、C7等),由脱丁烷塔(DA-405)的第16块板进料(全塔共32块板),进料量由流量控制器FIC101控制。灵敏板温度由调节器TC101通过调节再沸器加热蒸汽的流量,来控制提馏段灵敏板温度,从而控制丁烷的分离质量。 脱丁烷塔塔釜液(主要为C5以上馏分)一部分作为产品采出,一部分经再沸器(EA-418A、B)部分汽化为蒸汽从塔底上升。塔釜的液位和塔釜产品采出量由LC101和FC102组成的串级控制器控制。再沸器采用低压蒸汽加热。塔釜蒸汽缓冲罐(FA-414)液位由液位控制器LC102调节底部采出量控制。 塔顶的上升蒸汽(C4馏分和少量C5馏分)经塔顶冷凝器(EA-419)全部冷凝成液体,该冷凝液靠位差流入回流罐(FA-408)。塔顶压力PC102采用分程控制:在正常的压力波动下,通过调节塔顶冷凝器的冷却水量来调节压力,当压力超高时,压力报警系统发出报警信号,PC102调节塔顶至回流罐的排气量来控制塔顶压力调节气相出料。操作压力4.25atm (表压),高压控制器PC101将调节回流罐的气相排放量,来控制塔内压力稳定。冷凝器以冷却水为载热体。回流罐液位由液位控制器LC103调节塔顶产品采出量来维持恒定。回流罐中的液体一部分作为塔顶产品送下一工序,另一部分液体由回流泵(GA-412A、B)送回塔顶做为回流,回流量由流量控制器FC104控制。 本单元复杂控制方案说明: 吸收解吸单元复杂控制回路主要是串级回路的使用,在吸收塔、解吸塔和产品罐中都使用了液位与流量串级回路。 串级回路:是在简单调节系统基础上发展起来的。在结构上,串级回路调节系统有两个闭合回路。主、副调节器串联,主调节器的输出为副调节器的给定值,系统通过副调节器的输出操纵调节阀动作,实现对主参数的定值调节。所以在串级回路调节系统中,主回路是定值调节系统,副回路是随动系统。 《化工单元操作技术》仿真实训报告 实训项目:精馏单元仿真操作 班级:12化工301 学号: 报告人:王帅林 操作成绩: 报告成绩: 1.精馏工作原理 将液体混合物部分气化,利用其中各组分相对挥发度的不同,通过液相和气相间的质量传递来实现对混合物分离。 2. 工艺流程简介 本流程是利用精馏方法,在脱丁烷塔中将丁烷从脱丙烷塔釜混合物中分离出来。将脱丙烷塔釜混合物部分气化,由于丁烷的沸点较低,即其挥发度较高,故丁烷易于从液相中气化出来,再将气化的蒸汽冷凝,可得到丁烷组成高于原料的混合物,经过多次气化冷凝,即可达到分离混合物中丁烷的目的。 原料为67.8℃脱丙烷塔的釜液(主要有C4、C5、C6、C7等),由脱丁烷塔(DA-405)的第16块板进料(全塔共32块板),进料量由流量控制器FIC101控制。灵敏板温度由调节器TC101通过调节再沸器加热蒸汽的流量,来控制提馏段灵敏板温度,从而控制丁烷的分离质量。 脱丁烷塔塔釜液(主要为C5以上馏分)一部分作为产品采出,一部分经再沸器(EA-418A、B)部分汽化为蒸汽从塔底上升。塔釜的液位和塔釜产品采出量由LC101和FC102组成的串级控制器控制。再沸器采用低压蒸汽加热。塔釜蒸汽缓冲罐(FA-414)液位由液位控制器LC102调节底部采出量控制。 图1 列管换热器DCS流程图 图2列管换热器现场图 三、主要设备、调节器、各类仪表和阀件 1.主要设备 2.各类仪表 四、实训步骤 (一)冷态开车 1.进料过程 ①开FA-408顶放空阀PC101排放不凝气,稍开FIC101调节阀(不超过20%),向精馏塔进料; 技能训练二精馏塔操作仿真训练 ●训练目标 能利用仿真系统操作精馏塔。 ●训练准备 熟悉工艺流程及原理。 本单元是一种加压精馏操作,原料液为脱丙烷塔塔釜的混合液,分离后馏出液为高纯度的C4产品,残液主要是C5以上组分。 67.8℃的原料液经流量调节器FICl01控制流量(14056kg/h)后,从精馏塔DA405的第16块塔板(全塔共32块塔板)进料。塔顶蒸气经全凝器EA419冷凝为液体后进入回流罐FA408;回流罐FA408的液体由泵GA412A/B抽出,一部分作为回流液由调节器FCl04控制流量(9664kgm)送回DA405第32层塔板;另一部分则作为产品,其流量由调节器FCl03控制(6707kg/h)。回流罐的液位由调节器LCl03与FCl03构成的串级控制回路控制。DA405操作压力由调节器PCI02分程控制为5.0kg/m2,其分程动作如图3-34所示。同时调节器PCI01将调节回流罐的气相出料,保证系统的安全和稳定。 图3-34调节阀PVl02分程动作示意图 塔釜液体的一部分经再沸器EA408A/B回精馏塔,另一部分由调节器FCl02控制流量(7349kg/h),作为塔底采出产品。调节器LCl01和FCl02构成串级控制回路,调节精馏塔的液位。再沸器用低压蒸汽加热,加热蒸汽流量由调节器TCl01控制,其冷凝液送FA414。 FA414的液位由调节器LCl02调节。其工艺流程如图3-35所示。 图3-58 精馏塔单元带控制点工艺流程图 ●训练步骤(要领) (一)冷态开车 进料前确认装置冷态开工状态为精馏塔单元处于常温、常压、氮气吹扫完毕的氮封状态,所有阀门、机泵处于关停状态、所有调节器置于手动状态。 1.进料及排放不凝气 (1)打开PVl01(开度>5%)排放塔内不凝气; (2)打开FVl01(开度>40%),向精馏塔进料; (3)进料后,塔内温度略升、压力升高;当压力升高至0.5atm(表)时 (4)控制塔顶压力大于1.0atm(表),不超过4.25atm(表)。 2.启动再沸器 (1)待塔顶压力PCI01升至0.5atm(表),逐渐打开冷凝水调节阀PVl02A(至开度为50%); (2)待塔釜液位LICl01升至20%以上,全开加热蒸汽入口阀V13,手动缓开调节阀TVl01,给再沸器缓慢加热; (3)将蒸气缓冲罐FA414的液位LCl02设定为50%,投自动; (4)逐渐开大TVl01至50%,,使塔釜温度逐渐上升至100℃,灵敏板温度升至75℃。 3.建立回流 (1)待回流罐液位LICl03升至20%,灵敏板温度TCl01指示值高于75o C,塔釜温度高于100o C后,依 化工单元仿真实训-固定床精馏塔 ————————————————————————————————作者: ————————————————————————————————日期: ? 注意: 实训报告必须手写,统一用信纸。封面可以打印。 本学期考试周前交回来本学期才有成绩。逾期本学期该实训成绩算缺考。 化工单元仿真实训 实 习 报 告 班级: 学号: 姓名: 日期: 实训一固定床反应器单元 一、工艺流程说明 1、工艺说明 固定床反应器,又称填充床反应器,装填有固体催化剂或固体反应物用以实现多相反应过程的一种反应器。固体物通常呈颗粒状,粒径2~15mm左右,堆积成一定高度(或厚度)的床层。床层静止不动,流体通过床层进行反应。它与流化床反应器及移动床反应器的区别在于固体颗粒处于静止状态。固定床反应器主要用于实现气固相催化反应,如氨合成塔、二氧化硫接触氧化器、烃类蒸汽转化炉等。用于气固相或液固相非催化反应时,床层则填装固体反应物。 本流程为利用催化加氢脱乙炔的工艺。乙炔是通过等温加氢反应器除掉的,反应器温度由壳侧中冷剂温度控制。 主反应为:nC2H2+2nH2→(C2H6)n,该反应是放热反应。每克乙炔反应后放出热量约为34000千卡。温度超过66℃时有副反应为:2nC2H4→(C4H8)n,该反应也是放热反应。 冷却介质为液态丁烷,通过丁烷蒸发带走反应器中的热量,丁烷蒸汽通过冷却水冷凝。 反应原料分两股,一股为约-15℃的以C2为主的烃原料,进料量由流量控制器FIC1425控制;另一股为H2与CH4的混合气,温度约10℃,进料量由流量控制器FIC1427控制。FIC1425与FIC1427为比值控制,两股原料按一定比例在管线中混合后经原料气/反应气换热器(EH-423)预热,再经原料预热器(EH-424)预热到38℃,进入固定床反应器(ER-424A/B)。预热温度由温度控制器TIC1466通过调节预热器EH-424加热蒸汽(S3)的流量来控制。 ER-424A/B中的反应原料在2.523MPa、44℃下反应生成C2H6。当温度过高时会发生C2H4聚合生成C4H8的副反应。反应器中的热量由反应器壳侧循环的加压C4冷剂蒸发带走。C4蒸汽在水冷器EH-429中由冷却水冷凝,而C4冷剂的压力由压力控制器PIC -1426通过调节C4蒸汽冷凝回流量来控制,从而保持C4冷剂的温度。 2、本单元复杂控制回路说明 FFI1427:为一比值调节器。根据FIC1425(以C2为主的烃原料)的流量,按一定的比例,相适应的调整FIC1427(H2)的流量。 比值调节:工业上为了保持两种或两种以上物料的比例为一定值的调节叫比值调节。对于比值调节系统,首先是要明确那种物料是主物料,而另一种物料按主物料来配比。在本单 第六节精馏塔单元 一、精馏塔工作原理: 精馏是化工生产中分离互溶液体混合物的典型单元操作,其实质是多级蒸馏,即在一定压力下,利用互溶液体混合物各组分的沸点或饱和蒸汽压不同,使轻组分(沸点较低或饱和蒸汽压较高的组分)汽化,经多次部分液相汽化和部分气相冷凝,使气相中的轻组分和液相中的重组分浓度逐渐升高,从而实现分离。 精馏过程的主要设备有:精馏塔、再沸器、冷凝器、回流罐和输送设备等。精馏塔以进料板为界,上部为精馏段,下部为提留段。一定温度和压力的料液进入精馏塔后,轻组分在精馏段逐渐浓缩,离开塔顶后全部冷凝进入回流罐,一部分作为塔顶产品(也叫馏出液),另一部分被送入塔作为回流液。回流液的目的是补充塔板上的轻组分,使塔板上的液体组成保持稳定,保证精馏操作连续稳定地进行。而重组分在提留段中浓缩后,一部分作为塔釜产品(也叫残液),一部分则经再沸器加热后送回塔中,为精馏操作提供一定量连续上升的蒸气气流。 二、工艺流程说明: 本流程是利用精馏方法,在脱丁烷塔中将丁烷从脱丙烷塔釜混合物中分离出来。精馏是将液体混合物部分气化,利用其中各组分相对挥发度的不同,通过液相和气相间的质量传递来实现对混合物分离。本装置中将脱丙烷塔釜混合物部分气化,由于丁烷的沸点较低,即其挥发度较高,故丁烷易于从液相中气化出来,再将气化的蒸汽冷凝,可得到丁烷组成高于原料的混合物,经过多次气化冷凝,即可达到分离混合物中丁烷的目的。 原料为67.8℃脱丙烷塔的釜液(主要有C4、C5、C6、C7等),由脱丁烷塔(DA-405)的第16块板进料(全塔共32块板),进料量由流量控制器FIC101控制。灵敏板温度由调节器TC101通过调节再沸器加热蒸汽的流量,来控制提馏段灵敏板温度,从而控制丁烷的分离质量。 脱丁烷塔塔釜液(主要为C5以上馏分)一部分作为产品采出,一部分经再沸器(EA-418A、B)部分汽化为蒸汽从塔底上升。塔釜的液位和塔釜产品采出量由LC101和FC102组成的串级控制器控制。再沸器采用低压蒸汽加热。塔釜蒸汽缓冲罐(FA-414)液位由液位控制器LC102调节底部采出量控制。 塔顶的上升蒸汽(C4馏分和少量C5馏分)经塔顶冷凝器(EA-419)全部冷凝成液体,该冷凝液靠位差流入回流罐(FA-408)。塔顶压力PC102采用分程控制:在正常的压力波动下,通过调节塔顶冷凝器的冷却水量来调节压力,当压力超高时,压力报警系统发出报警信号,PC102调节塔顶至回流罐的排气量来控制塔顶压力调节气相出料。操作压力4.25atm (表压),高压控制器PC101将调节回流罐的气相排放量,来控制塔压力稳定。冷凝器以冷却水为载热体。回流罐液位由液位控制器LC103调节塔顶产品采出量来维持恒定。回流罐中的液体一部分作为塔顶产品送下一工序,另一部分液体由回流泵(GA-412A、B)送回塔顶做为回流,回流量由流量控制器FC104控制。 四、本仿真单元的控制点分析: 化工单元操作仿真实训总 结 姓名:XX 班级;XX班 学号:XXXX 目录 一、实训内容 1、精馏塔仿真 2、液位控制仿真 3、吸收解吸仿真 4、萃取仿真 5、灌区仿真 6、真空仿真 二、仿真总结 一、实训内容 1、精馏塔仿真 1.1操作原理: 精馏原理精馏操作迫使混合物的气、液两相在精馏塔体中作逆向流动,在互相接触过程中,液相中的轻组分逐渐转入气相,而气相中的重组分则逐渐进入液相。精馏过程本质上是一种传质过程,也伴随着传热。在恒定压力下,对单组分液体在沸腾时继续加热,其温度保持不变。但对于多组分的理想溶液来说, 在恒定压力下,沸腾溶液的温度却是可变的。一般而言,在恒定压力下,溶液气液相平衡与其组分有关。高沸点组分的浓度越高,溶液平衡温度越高。与纯物质的气液平衡相比较,溶液气液平衡的一个特点是:在平衡态下,气相浓度与液相浓度是不相同的。一般情况下,气相中的低沸点组分的浓度高于它在液相中的数值.对于纯组分的气液相平衡,把恒定压力下的平衡温度称为该压力下的沸点或冷凝点。但对于处在相平衡的溶液,则把平衡温度称为在该压力下某气相浓度的露点温度或对应的液相浓度的泡点温度。对于同一气相和液相来说,露点温度与泡点一般是不相等的,前者比后者高。 1.2工艺流程: 进料及排放不凝气 启动再沸器 建立回流 调整至正常 1.3仿真图: 2、液位控制仿真 2.1操作原理: 缓冲罐V101仅一股来料,8Kg/cm2压力的液体通过调节产供阀FIC101向罐V101充液,此罐压力由调节阀PIC101分程控制,缓冲罐压力高于分程点(5.0Kg/cm2)时,PV101B自动打开泄压,压力低于分程点时,PV101B自动关闭,PV101A自动打开给罐充压,使V101压力控制在5Kg/cm2。缓冲罐V101液位调节器LIC101和流量调节阀FIC102串级调节,一般液位正常控制在50%左右,自V101底抽出液体通过泵P101A或P101B(备用泵)打入罐V102,该泵出口压力一般控制在9Kg/cm2,FIC102流量正常控制在20000Kg/hr。 罐V102有两股来料,一股为V101通过FIC102与LIC101串级调节后来的流量;另一股为8Kg/cm2压力的液体通过调节阀LIC102进入罐V102,一般V102液位控制在50%左右,V102底液抽出通过调节阀FIC103进入V103,正常工况时FIC103的流量控制在30000 kg/hr。 罐V103也有两股进料,一股来自于V102的底抽出量,另一股为8kg/cm2压力的液体通过FIC103与FI103比值调节进入V103,比值系数为2:1,V103底液体通过LIC103调节阀输出,正常时罐V103液位控制在50%左右。2.2工艺流程: 缓冲罐V-101充压及液位建立 中间罐V-102液位建立 产品罐V-103建立液位 2.3、仿真图: 精馏塔单元仿真实训指导书 阿拉善经济开发区中等职业技术学校 化工教研室 2011 年 4月 目录 一、工艺流程说明 (2) 1、工艺说明 (2) 2、本单元复杂控制方案说明 (2) 3、设备一览 (3) 二、精馏单元操作规程 (3) 1、冷态开车操作规程 (3) 2、正常操作规程 (4) 3、停车操作规程 (5) 4、仪表一览表 (6) 三、事故设置一览 (7) 四、仿真界面 (9) 附:思考题 (11) 一、工艺流程说明 1、工艺说明 本流程是利用精馏方法,在脱丁烷塔中将丁烷从脱丙烷塔釜混合物中分离出来。精馏是将液体混合物部分气化,利用其中各组分相对挥发度的不同,通过液相和气相间的质量传递来实现对混合物分离。本装置中将脱丙烷塔釜混合物部分气化,由于丁烷的沸点较低,即其挥发度较高,故丁烷易于从液相中气化出来,再将气化的蒸汽冷凝,可得到丁烷组成高于原料的混合物,经过多次气化冷凝,即可达到分离混合物中丁烷的目的。 原料为67.8℃脱丙烷塔的釜液(主要有C4、C5、C6、C7等),由脱丁烷塔(DA-405)的第16块板进料(全塔共32块板),进料量由流量控制器FIC101控制。灵敏板温度由调节器TC101通过调节再沸器加热蒸汽的流量,来控制提馏段灵敏板温度,从而控制丁烷的分离质量。 脱丁烷塔塔釜液(主要为C5以上馏分)一部分作为产品采出,一部分经再沸器(EA-418A、B)部分汽化为蒸汽从塔底上升。塔釜的液位和塔釜产品采出量由LC101和FC102组成的串级控制器控制。再沸器采用低压蒸汽加热。塔釜蒸汽缓冲罐(FA-414)液位由液位控制器LC102调节底部采出量控制。 塔顶的上升蒸汽(C4馏分和少量C5馏分)经塔顶冷凝器(EA-419)全部冷凝成液体,该冷凝液靠位差流入回流罐(FA-408)。塔顶压力PC102采用分程控制:在正常的压力波动下,通过调节塔顶冷凝器的冷却水量来调节压力,当压力超高时,压力报警系统发出报警信号,PC102调节塔顶至回流罐的排气量来控制塔顶压力调节气相出料。操作压力4.25atm (表压),高压控制器PC101将调节回流罐的气相排放量,来控制塔内压力稳定。冷凝器以冷却水为载热体。回流罐液位由液位控制器LC103调节塔顶产品采出量来维持恒定。回流罐中的液体一部分作为塔顶产品送下一工序,另一部分液体由回流泵(GA-412A、B)送回塔顶做为回流,回流量由流量控制器FC104控制。 2、本单元复杂控制方案说明 吸收解吸单元复杂控制回路主要是串级回路的使用,在吸收塔、解吸塔和产品罐中都使用了液位与流量串级回路。 串级回路:是在简单调节系统基础上发展起来的。在结构上,串级回路调节系统有两个闭合回路。主、副调节器串联,主调节器的输出为副调节器的给定值,系统通过副调节器的输出操纵调节阀动作,实现对主参数的定值调节。所以在串级回路调节系统中,主回路是定值调节系统,副回路是随动系统。 分程控制:就是由一只调节器的输出信号控制两只或更多的调节阀,每只调节阀在调节器的输出信号的某段范围中工作。 化工单元操作仿真实训总结 姓名:XX 班级;XX班 学号:XXXX 目录 一、实训内容 1、精馏塔仿真 2、液位控制仿真 3、吸收解吸仿真 4、萃取仿真 5、灌区仿真 6、真空仿真 二、仿真总结 一、实训内容 1、精馏塔仿真 1.1操作原理: 精馏原理精馏操作迫使混合物的气、液两相在精馏塔体中作逆向流动,在互相接触过程中,液相中的轻组分逐渐转入气相,而气相中的重组分则逐渐进入液相。精馏过程本质上是一种传质过程,也伴随着传热。在恒定压力下,对单组分液体在沸腾时继续加热,其温度保持不变。但对于多组分的理想溶液来说,在恒定压力下,沸腾溶液的温度却是可变的。一般而言,在恒定压力下,溶液气液相平衡与其组分有关。高沸点组分的浓度越高,溶液平衡温度越高。与纯物质的气液平衡相比较,溶液气液平衡的一个特点是:在平衡态下,气相浓度与液相浓度是不相同的。一般情况下,气相中的低沸点组分的浓度高于它在液 相中的数值.对于纯组分的气液相平衡,把恒定压力下的平衡温度称为该压力下的沸点或冷凝点。但对于处在相平衡的溶液,则把平衡温度称为在该压力下某气相浓度的露点温度或对应的液相浓度的泡点温度。对于同一气相和液相来说,露点温度与泡点一般是不相等的,前者比后者高。 1.2工艺流程: 进料及排放不凝气 启动再沸器 建立回流 调整至正常 1.3仿真图: 2、液位控制仿真 2.1操作原理: 缓冲罐V101仅一股来料,8Kg/cm2压力的液体通过调节产供阀FIC101向罐V101充液,此罐压力由调节阀PIC101分程控制,缓冲罐压力高于分程点 (5.0Kg/cm2)时,PV101B自动打开泄压,压力低于分程点时,PV101B自动关闭,PV101A自动打开给罐充压,使V101压力控制在5Kg/cm2。缓冲罐V101液位调节器LIC101和流量调节阀FIC102串级调节,一般液位正常控制在50%左右,自V101底抽出液体通过泵P101A或P101B(备用泵)打入罐V102,该泵出口压力一般控制在9Kg/cm2,FIC102流量正常控制在20000Kg/hr。 罐V102有两股来料,一股为V101通过FIC102与LIC101串级调节后来的流量;另一股为8Kg/cm2压力的液体通过调节阀LIC102进入罐V102,一般V102液位控制在50%左右,V102底液抽出通过调节阀FIC103进入V103,正常工况时FIC103的流量控制在30000 kg/hr。 罐V103也有两股进料,一股来自于V102的底抽出量,另一股为8kg/cm2压力的液体通过FIC103与FI103比值调节进入V103,比值系数为2:1,V103底液体通过LIC103调节阀输出,正常时罐V103液位控制在50%左右。 2.2工艺流程: 缓冲罐V-101充压及液位建立 中间罐V-102液位建立 产品罐V-103建立液位 2.3、仿真图: 精馏塔单元仿真培训系统 操作说明书 一、工艺流程说明 1、工艺说明 本流程是利用精馏方法,在脱丁烷塔中将丁烷从脱丙烷塔釜混合物中分离出来。精馏是将液体混合物部分气化,利用其中各组分相对挥发度的不同,通过液相和气相间的质量传递来实现对混合物分离。本装置中将脱丙烷塔釜混合物部分气化,由于丁烷的沸点较低,即其挥发度较高,故丁烷易于从液相中气化出来,再将气化的蒸汽冷凝,可得到丁烷组成高于原料的混合物,经过多次气化冷凝,即可达到分离混合物中丁烷的目的。 原料为67.8℃脱丙烷塔的釜液(主要有C4、C5、C6、C7等),由脱丁烷塔(DA-405)的第16块板进料(全塔共32块板),进料量由流量控制器FIC101控制。灵敏板温度由调节器TC101通过调节再沸器加热蒸汽的流量,来控制提馏段灵敏板温度,从而控制丁烷的分离质量。 脱丁烷塔塔釜液(主要为C5以上馏分)一部分作为产品采出,一部分经再沸器(EA-418A、B)部分汽化为蒸汽从塔底上升。塔釜的液位和塔釜产品采出量由LC101和FC102组成的串级控制器控制。再沸器采用低压蒸汽加热。塔釜蒸汽缓冲罐(FA-414)液位由液位控制器LC102调节底部采出量控制。 塔顶的上升蒸汽(C4馏分和少量C5馏分)经塔顶冷凝器(EA-419)全部冷凝成液体,该冷凝液靠位差流入回流罐(FA-408)。塔顶压力PC102采用分程控制:在正常的压力波动下,通过调节塔顶冷凝器的冷却水量来调节压力,当压力超高时,压力报警系统发出报警信号,PC102调节塔顶至回流罐的排气量来控制塔顶压力调节气相出料。操作压力 4.25atm (表压),高压控制器PC101将调节回流罐的气相排放量,来控制塔内压力稳定。冷凝器以冷却水为载热体。回流罐液位由液位控制器LC103调节塔顶产品采出量来维持恒定。回流罐中的液体一部分作为塔顶产品送下一工序,另一部分液体由回流泵(GA-412A、B)送回塔顶做为回流,回流量由流量控制器FC104控制。 2、本单元复杂控制方案说明 吸收解吸单元复杂控制回路主要是串级回路的使用,在吸收塔、解吸塔和产品罐中都使用了液位与流量串级回路。 串级回路:是在简单调节系统基础上发展起来的。在结构上,串级回路调节系统有两个闭合回路。主、副调节器串联,主调节器的输出为副调节器的给定值,系统通过副调节器的输出操纵调节阀动作,实现对主参数的定值调节。所以在串级回路调节系统中,主回路是定值调节系统,副回 . 化工单元操作仿真实训总结 . 姓名:XX 班级;XX班 学号:XXXX 目录 一、实训内容 1、精馏塔仿真 2、液位控制仿真 3、吸收解吸仿真 4、萃取仿真 5、灌区仿真 6、真空仿真 二、仿真总结 一、实训内容 1、精馏塔仿真 1.1操作原理: 精馏原理精馏操作迫使混合物的气、液两相在精馏塔体中作逆向流动,在互相接触过程中,液相中的轻组分逐渐转入气相,而气相中的重组分则逐渐进入液相。精馏过程本质上是一种传质过程,也伴随着传热。在恒定压力下,对单组分液体在沸腾时继续加热,其温度保持不变。但对于多组分的理想溶液来说,在恒定压力下,沸腾溶液的温度却是可变的。一般而言,在恒定压力下,溶液气液相平衡与其组分有关。高沸点组分的浓度越高,溶液平衡温度越高。与纯物质的气液平衡相比较,溶液气液平衡的一个特点是:在平衡态下,气相浓度与液相浓度是不相同的。一般情况下,气相中的低沸点组分的浓度高于它在液相中的数值.对于纯组分的气液相平衡,把恒定压力下的平衡温度称为该压力下的沸点或冷凝点。但对于处在相平衡的溶液,则把平衡温度称为在该压力下某气相浓度的露点温度或对应的液相浓度的泡点温度。对于同一气相和液相来说,露点温度与泡点一般是不相等的,前者比后者高。 1.2工艺流程: 进料及排放不凝气 启动再沸器 建立回流 调整至正常 1.3仿真图: 2、液位控制仿真 2.1操作原理: 缓冲罐V101仅一股来料,8Kg/cm2压力的液体通过调节产供阀FIC101向罐V101充液,此罐压力由调节阀PIC101分程控制,缓冲罐压力高于分程点(5.0Kg/cm2)时,PV101B自动打开泄压,压力低于分程点时,PV101B自动关闭,PV101A自动打开给罐充压,使V101压力控制在5Kg/cm2。缓冲罐V101液位调节器LIC101和流量调节阀FIC102串级调节,一般液位正常控制在50%左右,自V101底抽出液体通过泵P101A或P101B(备用泵)打入罐V102,该泵出口压力一般控制在9Kg/cm2,FIC102流量正常控制在20000Kg/hr。 注意: 实训报告必须手写,统一用信纸。封面可以打印。 本学期考试周前交回来本学期才有成绩。逾期本学期该实训成绩算缺考。 化工单元仿真实训 实 习 报 告 班级: 学号: 姓名: 日期: 实训一固定床反应器单元 一、工艺流程说明 1、工艺说明 固定床反应器,又称填充床反应器,装填有固体催化剂或固体反应物用以实现多相反应过程的一种反应器。固体物通常呈颗粒状,粒径2~15mm左右,堆积成一定高度(或厚度)的床层。床层静止不动,流体通过床层进行反应。它与流化床反应器及移动床反应器的区别在于固体颗粒处于静止状态。固定床反应器主要用于实现气固相催化反应,如氨合成塔、二氧化硫接触氧化器、烃类蒸汽转化炉等。用于气固相或液固相非催化反应时,床层则填装固体反应物。 本流程为利用催化加氢脱乙炔的工艺。乙炔是通过等温加氢反应器除掉的,反应器温度由壳侧中冷剂温度控制。 主反应为:nC2H2+2nH2→(C2H6)n,该反应是放热反应。每克乙炔反应后放出热量约为34000千卡。温度超过66℃时有副反应为:2nC2H4→(C4H8)n,该反应也是放热反应。 冷却介质为液态丁烷,通过丁烷蒸发带走反应器中的热量,丁烷蒸汽通过冷却水冷凝。 反应原料分两股,一股为约-15℃的以C2为主的烃原料,进料量由流量控制器FIC1425控制;另一股为H2与CH4的混合气,温度约10℃,进料量由流量控制器FIC1427控制。FIC1425与FIC1427为比值控制,两股原料按一定比例在管线中混合后经原料气/反应气换热器(EH-423)预热,再经原料预热器(EH-424)预热到38℃,进入固定床反应器(ER-424A/B)。预热温度由温度控制器TIC1466通过调节预热器EH-424加热蒸汽(S3)的流量来控制。 ER-424A/B中的反应原料在2.523MPa、44℃下反应生成C2H6。当温度过高时会发生C2H4聚合生成C4H8的副反应。反应器中的热量由反应器壳侧循环的加压C4冷剂蒸发带走。C4蒸汽在水冷器EH-429中由冷却水冷凝,而C4冷剂的压力由压力控制器PIC-1426通过调节C4蒸汽冷凝回流量来控制,从而保持C4冷剂的温度。 2、本单元复杂控制回路说明 FFI1427:为一比值调节器。根据FIC1425(以C2为主的烃原料)的流量,按一定的比例,相适应的调整FIC1427(H2)的流量。 比值调节:工业上为了保持两种或两种以上物料的比例为一定值的调节叫比值调节。对于比值调节系统,首先是要明确那种物料是主物料,而另一种物料按主物料来配比。在本单元中,FIC1425(以C2为主的烃原料)为主物料,而FIC1427(H2)的量是随主物料(C2 Aspen精馏模拟的步骤 一、板式塔工艺设计 二、首先要知道工艺计算要算什么要得到那些结果如何算然后再进行下面的计算步骤。 三、其次要知道你用的软件(或软件模块)能做什么,不能做什么你如何借助它完成给定 的设计任务。 四、设计方案,包括设计方法、路线、分析优化方案等,应该是设计开题报告中的一部份。 没有很好的设计方案,具体作时就会思路不清晰,足见开题的重要性。下面给出工艺设计计算方案参考,希望借此对今后的结构和强度设计作一个详细的设计方案,明确的一下接下来所有工作详细步骤和方法,以便以后设计工作顺利进行。 五、板式塔工艺计算步骤 六、 1.物料衡算(手算) 七、目的:求解aspen 简捷设计模拟的输入条件。 八、内容:(1) 组份分割,确定是否为清晰分割; 九、 (2)估计塔顶与塔底的组成。 十、得出结果:塔顶馏出液的中关键轻组份与关键重组份的回收率 十一、参考:《化工原理》有关精馏多组份物料平衡的内容。 十二、 2.用简捷模块(DSTWU)进行设计计算 十三、目的:结合后面的灵敏度分析,确定合适的回流比和塔板数。 十四、方法:选择设计计算,确定一个最小回流比倍数。 十五、得出结果:理论塔板数、实际板数、加料板位置、回流比,蒸发率等等RadFarce 所需要的所有数据。 十六、 3.灵敏度分析 十七、目的:1.研究回流比与塔径的关系(NT-R),确定合适的回流比与塔板数。 十八、 2.研究加料板位置对产品的影响,确定合适的加料板位置。 十九、方法:可以作回流比与塔径的关系曲线(NT-R),从曲线上找到你所期望的回流比及塔板数。 二十、得到结果:实际回流比、实际板数、加料板位置。 二十一、 4. 用DSTWU再次计算 二十二、目的:求解aspen塔详细计算所需要的输入参数。 二十三、方法:依据步骤3得到的结果,进行简捷计算。 二十四、得出结果:加料板位置、回流比,蒸发率等等RadFarce 所需要的所有数据。 二十五、 5. 用详细计算模块(RadFrace)进行初步设计计算 二十六、目的:得出结构初步设计数据。 二十七、方法:用RadFrace 模块的Tray Sizing(填料塔用PAking Sizing),利用第4步(DSTWU)得出的数据进行精确设计计算。 二十八、主要结果:塔径。 二十九、 6. 核算 三十、目的:确定工艺计算的最后结果。 三十一、方法:对第 5 步的计算结果(如:塔径等)按设计规范要求进行必要的圆整,用RateFrace 或RateFrace 模块的Tray Rating(填料塔用PAking Sizing),对塔进行设计核算。三十二、结果:塔工艺设计的所有需要的结果。 三十三、如果仅是完成设计,至此,工艺计算全部完成。 三十四、工艺计算说明书内容要求精馏操作及精馏DCS操作精讲
aspen吸收、精馏塔模拟设计(转载)
精馏塔仿真指导书
精馏操作实训
化工单元操作仿真实训总结
精馏塔单元操作手册
姓名-精馏单元仿真操作实训报告
技能训练二 精馏塔操作仿真训练
化工单元仿真实训固定床精馏塔
东方仿真--精馏塔单元
化工单元操作仿真实训总结
[VIP专享]精馏塔仿真指导书
化工单元操作仿真实训总结
精馏塔单元仿真培训系统
化工单元操作仿真实训总结
化工单元仿真实训-固定床精馏塔
aspen精馏模拟步骤