fluent 旋转机械讲座 adv-rm-v6.2-lect-04a-mixing-plane
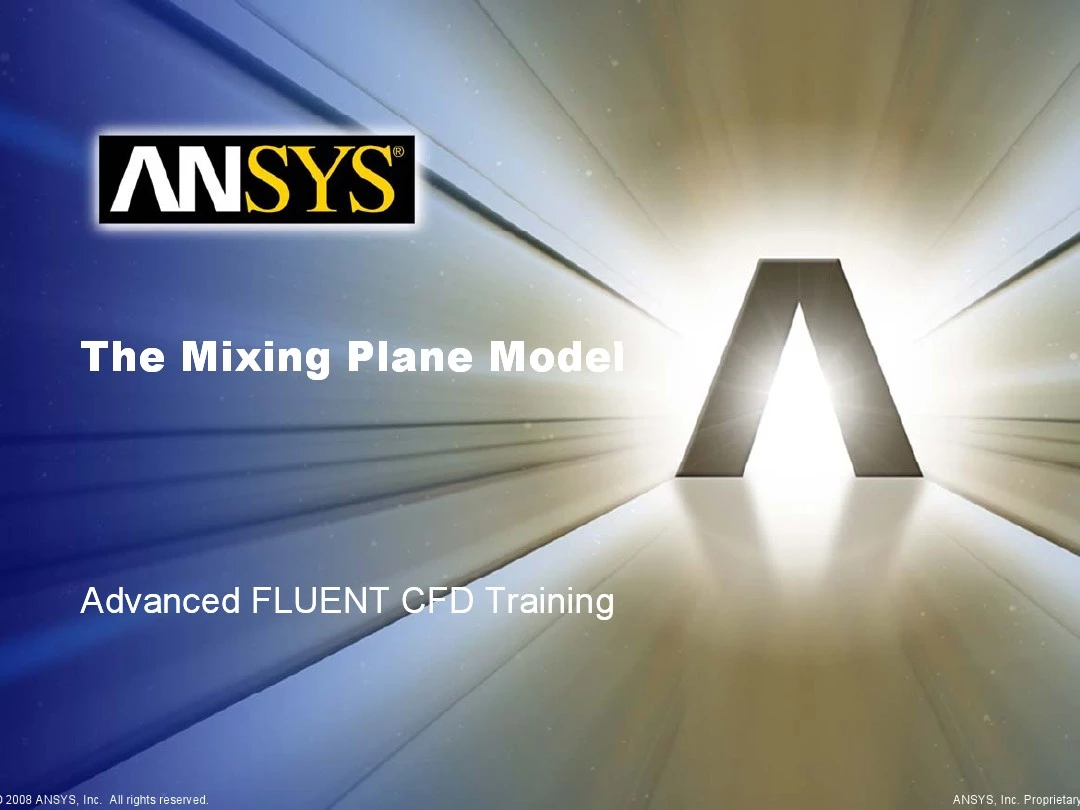

(机械制造行业)第四章旋转机械检修技术(检修钳工李和春主编)
第四章 旋转机械检修技术 一、填空题 1.无键联接的工件在拆卸时,推进器与轮毂外端面间应留一定间隙,其值不宜超过 ,以防轮毂高速推出时伤害工件和人。 2.尺型联轴器中间套筒对正连接后,应有一定的 浮动量,其值一般在3~6mm 。选值原则是:在 浮动量下应保证两轮毂外齿能同时全齿啮合。在 浮动量下不会因转子位移发生轮毂与接筒卡死。 3.离心式压缩机筒式内缸体段间密封在高压工况下选用O 形环,要和 同时使用,若单向受压,选用 背环,背环装配在 侧。若双向交替受压则选用 背环,在O 形环的两侧各置一个背环。 4.液力连轴器又称液力 器。它是利用液体 能来传递功率的液力传动机构。 5.风机按排气压力(p d )来分,可分为三大类。当排气压力p d ≤14.7kPa ,称为 ;当排气压力p d 在14.7kPa <p d ≤0.2MPa 时,称为 ;当排气压力p d >0.2MPa ,称为 。 6.一般的平衡精度转子,动平衡时可直接采用 的支承,对精度要求高的转子做高度动平衡时,必须采用 的原配轴承,并应在 环境下进行。 7.国产气轮机驱动的压缩机组用增速齿轮箱,以齿形分有 类。分别是 齿面圆弧齿斜齿或人字齿轮和 齿面渐开线斜齿或认字齿轮。 8.离心式压缩机组的连接方法有三种,它们依次是 、 和 。 9.干式气缸套不与 接触,仅起衬套作用,常用于压缩机的 、 压段,湿式气缸套的外表面与冷却水接触,常用在压缩机的低压段,装配要 。 10. Cl - 对奥氏体不锈钢的破坏属于 ,其作用条件除湿度因素外,还有两个重要条件是 和液相中 。 11.应力腐蚀、腐蚀疲劳和氢脆现象,都是金属材料受介质侵袭而导致的 破坏性。 12.起重吊钩应在 区作出永久标志,内容包括 载荷、厂表、产品编号。吊钩应设置 机构。手动吊钩的试验载荷为标志载荷的 倍,25t 以下的机用吊钩的试验载荷为标志载荷的2倍,吊钩开口增大 %,扭转变形≥10%,吊钩应报废。 13.叶轮作功的大小,取决于叶轮通道,特别是 截面到 截面气流速度的变化。为表示其变化情况,通常把 速度、 速度ω和 速度c 做成矢量图,称为气流速度三角形。 14.离心式压缩机的性能曲线是指在一定的转速和进气条件下,机器的 、 、 等性能参数随流量变化的关系曲线。 15.离心式压缩机所采用的叶轮,其出口安装角2A β都不大于90度,径向直叶轮2A β为 ,后弯形叶轮2A β为 ,强后弯形叶轮2A β为 。 16.新配置叶轮或者经修复的叶轮,在装到转子上之前应进行超速试验,超试转速为正常工作转速的 倍,超速时间 min ,超速试验后各部尺寸变化不超过 %。 17.在一定转速下工作的离心式压缩机,由于工艺方面的原因,如果系统压力突然 或进气温度 ,一旦出现压缩机排气压力 系统压力即会发生喘振。 18.引起离心式压缩机轴向推力增大的原因有: 、 、 、 。 19.离心式压缩机振动频率分析,当振频与转速同频时多因 ,振频小于或等于1/2转速频率时一般是因 、 。 20.齿轮增速箱接触精度检查要求:齿轮接触斑点渐开线齿轮要求齿高方向为 %,
转动设备机械对中技术大全(内容详实)
XX公司机泵维修钳工培训教程 联轴器对中 炼化工业用的大部分旋转机器,都趋向于高速、大功率和不设备机。对于高速机械,就需要提高机器平衡和对中的精确性,以便尽量减小振动和减轻轴承、联轴器及轴封的过早磨损。单机功率的增大和不设备机两个因素提高了机器可靠性在经济上的重要性,而机器的可靠性又取决于减少机器关键零件的过早磨损和损坏。长期以来平衡作为减少振动和磨损的其中一种手段,已受到机器制造厂和用户的充分注意。 大型机组的运行状况除了与工艺状况直接相关外,还与机组的安装质量,检修质量有着密切的关系。而经验证明,相当多的机械损坏是由于对中不准造成的。对中是减少机器损坏,防止和排除突发故障及减少维修时间必不可少的重要环节。机械轴对中,以及确保安装过程中各部件之间的同心度是动力机械等装配工作中十分重要的一步,是机组安装及检修过程中保证质量的关键一环。 随着大型机组在各行业中的的应用越来越多,对中在使用、维护单位以及设计单位都逐渐被重视起来,特别是运行过程中对中的变化对机组运行有着十分重要的影响,因为所有因热膨胀或转子在轴承内运行时的偏移都会最终影响到轴承的受力,从而影响到机组的振动、轴承温度等关键特性。因此从设计制造厂到用户都对冷态对中曲线有着特别的关注。这些都需要对在冷态时相关联两转子之间的相对关系进行准确测量。但是应该看到,对中也是检修中最费时费力的。 任何方式的对中,甚至是用直尺对中,总比不对中要好,而用二只百分表的精确对中又要比粗糙的对中要好,特别是对3000rpm以上的机器,精确对中尤为重要。精确对中可大大地改善轴承和轴封的寿命、降低振动和得到良好的总体可靠性。然而,对中工
现代高速列车用旋转类设备机械故障预判技术研究
现代高速列车用旋转类设备机械故障预判技术研究 摘要介绍了旋转类设备机械故障诊断的意义及其理论基础。以NR6317ASW-02型牵引电机冷却风机为例论证了诊断技术的可行性。 关键词旋转机械;故障诊断;离心通风机;噪声 Abstract this paper introduces the significance of rotating machinery fault diagnosis such equipment and its theoretical basis.NR6317ASW - 02 type traction motor cooling fan for example demonstrates the feasibility of diagnosis technology. Key words rotating machinery;Fault diagnosis;Centrifugal fan;noise 引言 旋转类设备机械故障预判技术是随着現代工业大生产的发展而发展起来的一项设备诊断技术。它是研究设备运行中或停机时基本不拆卸的情况下,掌握设备的运行状态,判定设备是否存在故障及故障严重程度和状态,预测设备可靠性和寿命,并提出解决方案的技术。对旋转类设备进行诊断包括对设备的性能进行诊断和对设备的故障进行预判两方面内容。随着我国高铁技术的迅猛发展及大批量的高速列车投入运营,高速列车用旋转类设备的正常工作是保障高速列车正常运营的关键设备,对这些设备开展性能监测与故障预判工作,具有重要的意义。 1 现实要求 当前我国对该类设备的维护仍采用传统的计划、定期维修。而这种方法带有很大的盲目性,设备有无故障、故障类型、故障部位及故障程度难以准确把握;另外,由于良好部位的反复拆卸,机械性能往往不理想,甚至低于检修前;易造成设备过修或欠修,设备的故障率无法掌控,从而影响EMU的正常行车秩序。故障诊断仪器的广泛应用,使对机械设备的维护由计划、定期检修走向状态、预知检修变为现实,使机械设备的维护方式发生了根本性革命。使得能够及时准备维修部件,安排维修计划,克服了定期维修带来的不必要的经济损失和设备性能的下降;完善的诊断能力可准确指出故障类型和故障部位,避免维修的盲目性,使监测简单易行,大大缩短了维修工期;完善的设备管理软件,又可使EMU设备管理自动化。由此可见,状态检测给EMU检修带来的经济效益是十分显著的[1]。 2 旋转类设备机械故障诊断技术理论基础 旋转机械的主要功能是由旋转部件来完成的,转子是其最主要的部件。旋转机械常见的故障表现主要为异常噪声及异常振动,其噪声信号从幅域、频域和时域反映了机器的故障信息。因此,了解旋转机械在故障状态下的异常噪声,对于监测机器的运行状态和提高诊断故障的准确率都非常重要。利用噪声检测系统对
高速旋转机械的振动频谱分析
高速旋转机械的振动频谱分析 一、前言我公司绝大多数关键设备为旋转机械设备,如各类风机、空压机、大型电机等。设备的日常维护和安装调试过程中,经常遇到因剧烈振动而无法正常生产的情况,而振动的原因错综复杂,仅靠耳听、手摸的原始方法,很难全面准确的分析判断故障的原因。采用先进的设备状态检测和故障诊断技术,通过振动检测掌握各类设备在一定时期的运行状态,为从事设备维护、安装、调试的工程技术人员提供一套完整的设备运行状态资料,根据这些资料进行数据分析,可以准确的分析判断故障原因,缩短检修工期,合理的安排关键设备的预防维修计划,从而避免因突发性设备故障而造成的经济损失,确保产生的顺利进行。 二、采用故障诊断技术处理设备故障的几个实例 1.氧气厂2#DA350一61型空压机组振动故障的处理氧气厂DA350~61型空压机是制氧机的动力设备,机组进行是否正常,直接关系到第一炼钢厂的生产,是总公司的关键设备。1999年4月份,该机组借第一炼钢厂停产机会,解体大修,组装后试车时,机组振动超标,无法正常运行,严重影响检修工期。如解体检查至少需要3天的时间,况且对能否检查到故障点也没有十分把握。于是我们利用NG 一8902多通道数据采集故障诊断系统,对该机组进行了全面的测试。(1)空压机组的测点布置如图1所示。(2) 机组的测试情况(取振动值最大的方向)见表1 测点振动值,mm/s 特征频率,Hz 1 S(水平)0.12 50 2 S(水平)0.14 50 3 C(垂直)0.344 146 4 C(垂直)0.776 146 5 C(垂直)0.28 146 6 C(垂直)0.577 146 7 C(垂直)2.79 146 8 C(垂直)8.25 146 由表1可见,1#、2#、3#、4#、5#、6#测点,振动情况良好。7#、8#测点振动速度超标,8#测点振值8.25mm/s,严重超标,7#、8#测点的轴向振动谱图如图2、图3又测量了7#、8#测点的振动加速度,见表2(取振动值最大的方向)。测点振动速度值,mm/s 特征频率,Hz 8#瓦S(水平)5.67 2487 C(垂直)12.67 2625 Z(轴向)14.61 2625 7#瓦 S(水平)1.58 438 C(垂直)1.66 146 Z(轴向)11.24 2625 根据以上的振动测量及频谱图分析,空压机组的振动故障分析如下:3#、4#、5#、6#测点振动速度良好,说明大小齿轮运行状态正常,振源不在大小
(精选)旋转机械的应用
现场中旋转机械故障诊断应用 班级:装备0901 姓名:王峥 学号:200906080609
这学期我们学习的这门课为《机械设备故障诊断技术与应用》,设备诊断技术是一种了解和掌握设备在使用过程中的状态,确定其整体或局部是正常或异常,早期发现故障及其原因,并能预报故障发展趋势的技术。机械设备故障诊断技术日益获得重视与发展的原因是,随着科学技术与生产的发展,机械设备工作强度不断增大,生产效率、自动化程度越来越高,同时设备更加复杂,各部分的关联愈加密切,往往某处微小故障就爆发链锁反应,导致整个设备乃至与设备有关的环境遭受灾难性的毁坏。 一、设备故障的信息获取和检测方法 设备故障信息的获取方法: 1、直接观测法 2、参数测定法 3、磨损残余物的测定 4、设备性能指标的测定 设备故障的检测方法: 1、振动和噪声的故障检测 (1)振动法:对机器主要部位的振动值如位移、速度、加速度、转速及相位值等进行测定,与标准值进行比较,据此可以宏观地对机器的运行状况进行评定,这是最常用的方法。 (2)特征分析法:对测得的上述振动量在时域、频域、时—频域进行特征分析,用以确定机器各种故障的内容和性质。 (3)模态分析与参数识别法:利用测得的振动参数对机器零部件的模态参数进行识别,以确定故障的原因和部位。 (4)冲击能量与冲击脉冲测定法:利用共振解调技术以测定滚动轴承的故障。 (5)声学法:对机器噪声的测量可以了解机器运行情况并寻找故障源。 2、材料裂纹及缺陷损伤的故障检测 (1)超声波探伤法:该方法成本低,可测厚度大,速度快,对人体无害,主要用来检测平面型缺陷。 (2)射线探伤法:主要采用X 射线。该方法主要用于展示体积型缺陷,适用于一切材料,测量成本较高,对人体有一定损害,使用时应注意。 (3)渗透探伤法:主要有荧光渗透与着色渗透两种。该方法操作简单,成本低,应用范围广,可直观显示,但仅适用于有表面缺陷的损伤类型。 (4)磁粉探伤法:该法使用简便,较渗透探伤更灵敏,能探测近表面的缺陷,但仅适用于铁磁性材料。 (5)涡流探伤法:这种方法对封闭在材料表面下的缺陷有较高的检测灵敏度,它属于电学测量方法,容易实现自动化和计算机处理。 3、设备零部件材料的磨损及腐蚀故障检测 (1)光纤内窥技术:它是利用特制的光纤内窥探测器直接观测到材料表面磨损及情况。(2)油液分析技术:油液分析技术可分为两大类:一类是油液本身的物理、化学性能分析,另一类是对油液污染程度的分析。具体的方法有光谱分析法与铁谱分析法。 4、温度、压力、流量变化引起的故障检测机械设备中的有些故障往往反映在一些工艺参数,如温度、压力、流量的变化中,在温度测量中除常规使用的装在机器上的热电阻、热电偶等接触式测温仪外,还有在特殊场合使用的非接触式测温方法。 二、旋转机械简介
旋转机械故障诊断技术在炼钢设备的应用
旋转机械故障诊断技术在炼钢设备的应用 发表时间:2019-08-05T11:51:14.593Z 来源:《基层建设》2019年第11期作者:荣银龙[导读] 摘要:炼钢设备在运营当中,由于受到多种因素影响,导致炼钢设备经常出现故障,影响着炼钢设备的正常运行。旋转机械故障诊断技术作为全新的技术,在炼钢设备当中的应用,能够及时诊断出故障出现的原因,帮助技术人员处理设备出现的故障,不但提高了旋转机械设备诊断的效率,也极大提高了设备诊断的质量。 中国船舶重工集团公司第七一三研究所河南省郑州市 450001 摘要:炼钢设备在运营当中,由于受到多种因素影响,导致炼钢设备经常出现故障,影响着炼钢设备的正常运行。旋转机械故障诊断技术作为全新的技术,在炼钢设备当中的应用,能够及时诊断出故障出现的原因,帮助技术人员处理设备出现的故障,不但提高了旋转机械设备诊断的效率,也极大提高了设备诊断的质量。因此,炼钢企业在故障诊断过程当中,要注重发挥旋转机械故障诊断技术的应用,并不断强化其科技投入,提升该技术的科技含量,充分发挥旋转机械故障诊断技术的优势,从而推动机械设备的正常运行。基于此,本文对旋转机械故障诊断技术在炼钢设备的应用进行分析。 关键词:旋转机械;故障诊断技术;炼钢设备;应用 1旋转机械故障特点旋转机械故障的故障特点与其他类型的机械故障存在一定的区别,且是机械设备中最为常用的一类,所以有必要对其进行单独的深入研究。旋转机械故障是指有转子系统的机械设备在运行过程中出现异常的工作状态,比如不正常的噪声、异常大的振动、温度急剧升高,或者其他指标不正常。旋转机械的结构复杂,故障发生具有一定的阶段性,并且部分故障的发生有一个渐进的过程,在进行故障诊断时,必须综合考虑多项因素,使得进行准确故障诊断的难度较大。 2结合振动分析诊断旋转机械设备的故障 2.1仪器松动 仪器发生松动是旋转机械发生最普遍的故障,松动分为两种,一是螺栓松动,它会引发整个仪器都松动;二是构件配合之间发生松动,比如内圈与转轴、滚动与轴承等,因此造成配合精度减小。因为松动而引发的振动是非线性的,它的信号频率非常复杂,刨除基频,还会产生分频波动,进而造成旋转机器故障。 2.2转子不平衡 转子不平衡带来的而影响是巨大的,因其是核心组成部分,引发的故障也是十分常见的。对于转子发生不平衡原因有材料的不合格、长时间损耗以及配件偏离中心,或是固件松动引发附着物堆积等因素,都是致使转子发生不平衡的原因以及质心出现偏移。不平衡分为两种模式,一是动不平衡,二是静不平衡。在发生不平衡时它的振率与平时会有极大的不同,主要对转子旋转的频率进行观察即可。另外,发生不平衡振动以后会连带着其他构件的频率。产生不平衡振动的原因有三种,其中包含了转子的速度、转子的质量以及偏心距。转子在旋转过程中会产生一个力即为离心力,离心力的功能就是支撑轴承,其方向是与轴承垂直的。在进行故障诊断时,一定要将其以上因素进行深入分析。 2.3油膜振荡和油膜涡动故障 因为旋转机械在高速运行中大多用的是流体动压滑动轴承。油膜涡动由涡动力产生,使转轴除了自转外还绕中心进行公转。在共振的状态下,油膜振荡非常强烈,造成共振现象破坏力极大的,对高速旋转机械危害很大。转子的一阶自振频率为:当油膜涡动的特征频率约为旋转频率的一半,油膜振荡时其转速与涡动的频率无关。 3现行故障识别与诊断分析方法简介 3.1基于控制模型的故障诊断 对于一个旋转机械系统,若通过理论或实验方法能够建立其模型,则系统参数或状态的变化可以直接反映该系统及其动态过程,从而为故障诊断提供依据。基于控制模型的故障诊断方法主要涉及到模型建立、参数与状态估计和观测器应用等技术。其中,参数与状态估计技术是该方法的关键"参数估计的参数包含两类:第一,系统参数,即描述系统动态特性的参数。基于系统参数估计的故障诊断方法与状态估计方法相比较,前者更有利于故障的分离,但是它也存在不足之处:求解物理元件参数很困难;系统故障引起系统模型结构和参数变化的形式是不确定的,目前还缺少有效的方法。第二,故障参数,即用于描述系统出现的故障时信号自身特性的参数。其基本思想是:对故障系统构造适当形式的包含有可调参数的状态观测器,并使其处于零状态"当系统发生故障时,用观测器中的可调部分来补偿故障对系统状态和输出的影响,使得观测器在系统处于故障状态下仍然保持零状态观测误差,此时观测器中可调部分的输出即为故障参数的估计结果。使用该方法的优点是可对故障信号进行在线建模,但是当系统出现强非线性时,目前仍无有效算法。 3.2基于模式识别的故障诊断 故障诊断实质上是利用被诊断系统运行的状态信息和系统的先验知识进行综合处理,最终得到关于系统运行状况和故障状况的综合评价过。如果事先对系统可能发生的故障模式进行分类,那么故障诊断问题就转化为模式识别问题。当系统的模型未知或者非常复杂时,模式识别则为解决故障诊断问题提供了一种简便有效的手段。基于模式识别的故障诊断方法主要分为统计模式识别和句法模式识别两大类,它们在旋转机械故障诊断领域中得到广泛应用。基于BayeS分类器的统计模式识别法是旋转机械故障诊断中一种经典方法。 3.3基于人工神经网络的故障诊断 神经网络具备可学习性和并行计算能力,能够实现分类、自组织、联想记忆和非线性优化等功能,它是通过试图模拟生物神经系统而建立的自适应非线性动力学系统。在故障诊断领域中使用神经网络,可以解决诊断推理和趋势预测问题。一旦输入特定的设备状态模式,则经过大量标准样本学习的故障诊断系统网络将会通过各个神经元之间的互连与权值构成的大规模非线性并行处理模式来进行计算,从而实现隐含的专家知识的应用,最终得出诊断推理结果。 4旋转机械故障诊断的实际案例分析某地区的炼钢厂煤气风机,其高压电机(6000V)驱动耦合器,型号为JK850-2,850kW额定功率、额定转数为2970r/min,50Hz频率,在进行炼钢工艺吹氧操作时,风机为高速运转状态,而其他时则保持低速的运行状态。 4.1测量振动值分析
海洋钻机关键机械设备减振技术探讨
海洋钻机关键机械设备减振技术探讨 发表时间:2018-03-14T13:21:22.207Z 来源:《防护工程》2017年第31期作者:岳宗林 [导读] 海洋钻井平台上的机械设备将对平台产生冲击和振动,降低了平台的可靠性。 中海油能源发展装备技术有限公司天津 300452 摘要:海洋钻井平台上的机械设备将对平台产生冲击和振动,降低了平台的可靠性。为减少动态加载平台,提高平台的使用寿命,本文阐述了旋转设备振动的原因,进行了理论分析,并提出如何设计平台,安装减振装置来减少振动的产生,对平台上的合理机械设备安装提供了理论依据和参考。 关键词:钻机;振动;激振频率;固有频率 引言 海洋钻井平台因建筑在环境恶劣的条件下,会受到各种载荷的作用。平台的振动和破坏主要包括:地震、波浪、风力、海水侵蚀及平台上的机器和设备。为了降低运行维护成本,在海洋环境荷载作用下,降低平台动载荷、提高平台寿命和可靠性,采用大量的隔振减振技术,取得良好的社会效益和经济效益。 一、旋转机械振动的产生 在钻井平台机械设备中,大多数都有旋转零部件,旋转机械是指由旋转动作来完成的机械,尤其是指转速较高的机械。这种高速旋转机械的工作条件通常是振动响应和振动频率谱分析,观察特征频率分量的变化,是使用振动信号监测的旋转机械的主要内容。旋转机械振动的原因有很多,如:轴承阀座刚度引起的振动;转动速度周期性变化引起的振动;轴向刚度的非线性振动;旋转阀体的不平衡引起的振动,设备实现功能要求的震动等。通常,旋转机械如:压缩机组、高压泥浆泵、风机等是由转子、轴承和密封组成,在转子轴的操作支承的动态油膜下,叶轮与液体物料相互作用,电机转子要受电磁场作用,借助联轴器,转子间也要相互作用。即:转子在离心力、重力、磁场力、刚体间、刚体和流体相互作用下,产生各频率的振动。尤其用于泥浆初始净化的振动筛设备,为完成井口返回泥浆及杂质物料筛分作业,振动筛由两台偏心电机带动激振器驱动料网、主体结构等构件高幅度运转,对底座固定结构有较高的要求。当旋转机械的转速与旋转轴的固有频率重合时,将会有一个强烈的振动现象,称为旋转轴的临界速度。实际的旋转机械,由于加工和装配的误差,以及材料的不均匀性,不可避免地有点偏心,也就是说,重心偏离了旋转轴的轴线。这种偏心力在转速和频率的同时产生周期性的强迫力,由强迫力引起的强迫振动使一个谐振状态低于临界数字,产生一个强的旋转振动。这种现象,如高旋转的存在,会对整个机械造成严重破坏,甚至造成严重的事故发生。 二、旋转机械振动的基本原理分析 1、如图所示,01是轴,02是旋转体的重心,y是旋转的轴,e是偏心。如在这种状态下,振动对轴的转动刚度沿径方向作用有弹性鼻,而在02重心上作用有离心力,在旋转振动时,应相互平衡。 因此Fl=F2,即:P为轴的横向振动固有频率,y与系统的强迫振动的振幅关系式相同。当即旋转振动轴的绕度变为无限大;表示旋转轴转速处于临界速度。 2、旋转体的失衡与均衡:轴失衡对旋转机械的平衡运转是有害的,使轴承受到负荷,从而轴上发生剩余应力,因此应减小轴的失衡。作用在旋转体各部分上的离心力与旋转体的全部质量集中在重心上所产生的离心力相同。由于这种离心力的方向改变着转速旋转,因此成为周期性的外力,并构成振动的原因。 3、对于旋转机械,振动信号检测的关键是转子系统。由于转子是旋转机械设备的核心部件,整个装置的正常运行依赖于转子的正常运行。因是通过转子轴承支承座及外壳和基础之上,构成所谓的转子轴承系统,在许多情况下,支承的动力学特性在某种程度上也会影响转子的运动。因此,转子的运行状态和其他旋转部件之间是相互联系的。旋转机械的大部分机械故障和转子及其部件都是直接相关的,除了配备非接触式涡流传感器外,对转子的轴向振动也实现连续监测,一般需要轴承阀座和壳体振动试验。监测转子比测试轴承座或底盘的振动更敏感,这是由于油膜轴承有一个较大的轴承间隙,因此相对振动和轴承座的振动有显著差异,尤其是支承系统的刚度较大时,轴颈的振动频率比轴承座的振动大。 三、机械设备减振技术的措施 1、合理选择参数,提高设备动态特性的幅度和频率。根据振动理论,激振力和位移的传递与频率有关。频率可分为自然频率和激发频率。固有频率来源于产品的结构特征,由质量、中心位置、刚度等多种因素相互作用决定。应避免激发频率。在满足强度要求的情况下,选用低刚度材料,特别是支撑部件,是减少振动的有效方法。自行式机械、改变弹性悬架的刚性悬挂:固定设备、弹性、阻尼部分和质量形成串联和并联,多种形式组成系统的弹性支撑装置,可按照预定的要求,使系统的等效刚度小于原来的刚度,从而达到减振的目的。另外,通过降低刚度和降低固有频率,提高减振性能是不可取的。一方面:随着刚度的降低,系统设备的静态位移也会增加,这将使空间布局、弹性尺寸和结构设计变得困难。另一方面:对于不同的工作需求,通常有最低限度的最小刚性值。通过分析,到产品使用中将处于既有竖向振动,又有俯仰角振动等耦合振型,特别要注意结构的合理性、质量对称分布的可能性,并确定零点的振幅在“节点”的结构,对敏感的振动机械仪表、仪器设置在“节点”或其附近。 2、合理制作设备的支撑。弹性支撑对称布置避免了耦合振动机械设备的安装,与弹性支撑不可分离,可用于隔离激振的传递和响应。如弹性支撑不合适,则容易造成耦合振动。对称排列的设备当弹性支撑四个角时,重心在垂直干扰力时,只设置每个垂直振动,不会导致
旋转机械(转子)故障诊断
旋转机械(转子)故障诊断 摘要:旋转机械故障诊断技术在企业中的应用能够及早发现设备故障、防止生产线停工、避免重大事故。本文首先展示了国内外转子故障诊断技术现状,回顾过往不平衡模拟实验通过对振动特征的分析研究总结了不平衡的振动特征。而后再利用振动信号分析处理方法以及时一频分析技术,对转子系统的不平衡、不对中两个典型的故障诊断做了详细的介绍。由于技术发展,以后的转子故障诊断将朝着自动化、智能化方向发展。 关键词:旋转机械;不平衡;不对中;故障诊断 Vibration Faults in Rotor System Abstract: Application of the rotating machinery fault diagnosis technology in the enterprise can predicte equipment failure, prevent shutdown the production line , avoid major accidents. This paper shows the present situation of rotor fault diagnosis technology at home and abroad at first, retrospects the imbalance simulation experiment based on the analysis of the vibration characteristics of the study summarized the unbalanced vibration characteristics. Then,with the vibration signal analysis method and spectrum analysis technology, I will introduce imbalance and misalignment two typical fault diagnosis in detail. Due to the technical development, the rotor fault diagnosis will develop in automatic and intelligent direction. Keywords: Rotating Machinery; Imbalance;Misalignment ; Fault Diagnosis
高速旋转运动的伤害
高速旋转运动的伤害 在绝大多数机械、机器和设备的运行过程中,许多机械部件在做高速旋转 运动,这些部件具有较大的运动能量,如有缺损和变形将导致运转失稳和振动,一旦断裂或脱落逆流作用于人体将造成伤害事故。 1. 旋转部件的种类 水电站涡轮发电机的叶轮;飞机和轮船的螺旋桨;鼓风机和通风机的叶片;发 电机和电动机的转子;铸造生产中螺旋搅拌机的叶片,皮带运输机的驱动轮;锻 造和冲压机械传动系统运动中的飞轮、齿轮、曲轴等;切削加工中车床的卡盘、 花盘、拨盘、鸡心夹,较大的工件;机床(车床、刨床、剪切机) 的皮带轮、链轮、齿轮、链条、旋转轴和轴头等;铣床的刀具;磨削的砂轮;等等。 2. 旋转部件对人体的伤害及方式 旋转的搅拌机叶片将把不慎伸入的手绞伤;旋转中的飞轮、齿轮、链轮、链条、旋转轴和轴头会把人体接触到的部位擦伤,正面撞击会造成骨折等肢体损伤;人手伸入皮带、链条和飞轮或齿轮间将被碾伤;卡盘、花盘、拨盘、鸡心夹 的突出部可能勾住衣服、手套、头巾、发辫等而把人体或局部拖入机械造成伤 害甚至死亡;高速旋转中的铣刀、砂轮接触人体会造成伤害;曲轴、未固定好的 长棒料会把靠近的人体部位打伤。 3. 旋转部件的防护措施 (1) 安全防护装置 为了防止机械的旋转部件对人体造成意外伤害,一般在危险部位加设安全 防护装置。安全防护装置是预防操作者和其他人员接触机械旋转部件或接近机
械设备危险区域造成伤害的辅助装置。安全防护装置包括防护罩、防护栏杆、 防护栅栏、防护挡扳等遮挡式的防护装置。 1) 防护罩 用防护罩对高速旋转的部件加以隔离,如皮带轮、链轮、齿轮、链条、旋 转轴、法兰盘和轴头等。例如回转的车床附件和工件,以及在车削过程中形成 的边缘较锋利,是车削过程中最主要的不安全因素。车削加工中因工件造成的 工伤事故远高于其他切削加工。对安全影响大的车床回转附件主要是装卡工件 的卡盘、花盘、拨盘、鸡心夹等。使用卡盘或花盘安装工件时,主要危险部分 是卡盘爪,它在转动时可能钩住工人的衣服。为此,可在卡盘周围安置防护罩,将卡爪罩起来。 2) 防护栏杆 不能在地面上操作的机床,操纵台周围应设置高度不低于0.8m的栏杆;容 易伤人的大型机床运动部位,如龙门刨床床身两端也应加设栏杆,以防工作台 往复运动时撞人。 在危险性很高的部位,防护装置应设计成顺序联锁结构。当取下或打开防 护装置时,机床的动力源就被切断。有一种比较简单轻便的联锁结构——电锁,它可用于各种形式和尺寸防护罩的门上。转动它的旋钮,安装在防护罩门上的 销体内的门闩就进入固定不动的插座内,关闭防护罩的门。与此同时,三个电 源插片也伸出进人插孔而使机床三相电源接通。由于门闩与插片是联锁同时动作,因此打开防护罩门,插片退出插孔,机床电源也就被切断。
高速旋转式压片机详细说明
高速旋转式压片机使用说明 1、使用前须重复检查冲模的质量,是否有缺边、裂缝、变形和紧松不全情况及装置是否完整良好等工作。 2、检查颗粒原料的粉子是否干燥及颗粒中的粉末含量最好不超过10%。如不合格的不要硬压,否则会影响机器的正常运转及使用寿命和原料损耗。 3、初次试车应将压力调节器控制的指示针放置6上,将粉子倒入斗内,用手转动试车手轮,同时调节充填和压力,逐步增加到片剂的重量和硬软程度达到成品要求,然后先开动电动机,再开离合器,进行正式运转生产,在生产过程中,须定时抽验片剂的质量,是否符合要求,必要时进行调整之。 4、速度的选择对机器使用的寿命有直接的影响,由于原料的性质粘度及片径大小和压力在使用上不能作统一规定,本机的结构无级变速装置,慢速适用于压制矿物、植物草素、大片径、粘度差等和快速难以成型的物料。快速适用于压制粘合,滑润性好的和易于成型物料。因此,使用者必须根据实际情况而定。 5、管理人员必须熟悉本机的技术性能,内部构造,控制机构的使用原理及运转期间不得闻开工作地点,为防止发生故障而损坏机件,借以保证安全生产为前提。 6、在使用中要随时注意机器响声是否正常,遇有尖叫声和怪声即行停车进行检查消除之,不得勉强使用。 高速旋转式压片机安装说明 1、本机为整台装箱,拆箱后搬至适当使用地方,垫平后即可使用,如地位固定可加装地脚螺钉。 2、电气线路和装置,应注意电压,用户未提出者,一律规定为380伏,并在接线时应注意电动机旋转方向,必须与机上箭头方向一致,切勿倒转,为保证电气安全必须装接有效地线。 3、本机应置在干燥清洁,光线充足的室内使用。 旋转式压片机机件润滑 1、本机的一般机件润滑,在机件的外表均装有油杯和油嘴,可按油杯的类型,分别注以黄油和机油,开车使用前应全部加油一次,中途可按各轴承的温升和运转情况添之。 2、上盖的玻璃油杯是润滑转盘和轴承,在运转中以每分钟2-4滴。 3、蜗杆上的旋盖油杯是润滑蜗杆蜗轮,在运转中按实际润滑情况加之。 4、传动轴的两端装有滚动轴承,轴壳外装有油嘴,可以每二星期加油一次,用油枪压入。 5、冲杆的尾部与曲线轨导用黄油润滑,注意不宜过多,防止油污渗入粉子而影响片剂的质量。 6、在加油时应注意不要使油溢出杯外,更不要流到机器的周围和地上,因为油类很容易使物料染污影响片剂质量。 高速旋转式压片机保养说明 1、定期检查机件,每月进行1-2次,检查项目为蜗轮、蜗杆、轴承、压轮、曲轴、上下导轨等各活动部分是否转动灵活和磨损情况,发现缺陷应及时修复使用。 2、一次使用毕或停工时,应取出剩余粉剂,刷清机器名部分的残留粉子,如停用时间较长,必须将冲模全部拆下,并将机器全部揩擦清洁,机器的光面涂上防锈油,用布蓬罩好。 3、冲模的保养应放置在有盖的铁皮箱内,使冲模全部浸入油中,并要保持清洁,勿使生锈和碰伤,最好能定制铁箱以每一种规格装一箱,可避免使用时造成装错及有助于掌握损缺情况。 4、使用场所应经常打扫清洁,尤其对医药和食用的片剂制造更不宜有灰砂、飞尘存在。 注意事项