350kA电解槽系列的发展

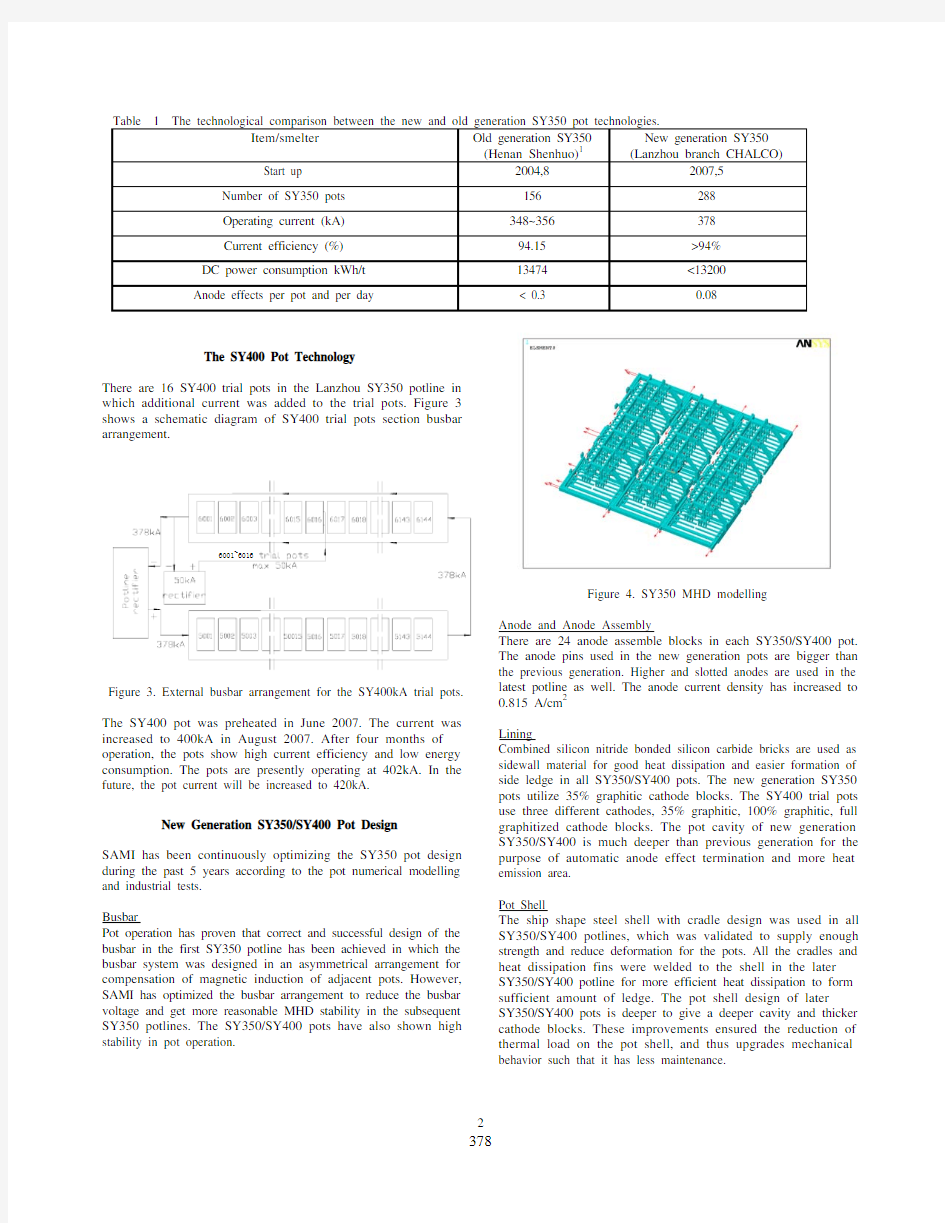
THE ADVANCEMENT OF NEW GENERATION SY350 POT
Zhu Jiaming1, Yang Xiaodong1, and Liu Yafeng1, SunKangjian1
1Shenyang Aluminum & Magnesium Engineering & Research Institute (SAMI); 184 Hepingbei St.
Shenyang, Liaoning 110001, China
Keywords: SY350 Pot, SY400 Pot, Numerical Modelling, Pot Design,
Abstract
SAMI’s high amperage SY350 pot technology was developed in 2002. Presently, there are three SY350 potlines in operation in China and nine more in design phase. Over the years, SAMI has made further improvement on the SY350 pot technology and has since increase the pot amperage up to 378kA.
SAMI has also developed the SY400 pot technology and has installed a total of 16 trial pots at one of SAMI’s latest designed potline. The trial pots are currently operating at 402kA and have been in operation successfully for more than 14 months. Good performance obtained from the trial pots with high current efficiency and low energy consumption. Presently, there are two SY400 potlines under design.
This paper will introduce the SY350 pot technology and describe some of the key advancements of the technology to date, including aspects of the SY400 trial pots.
Introduction
Shenyang Aluminium & Magnesium Engineering & Research Institute (SAMI) has developed 160kA, 190/200kA, 230/240kA, 280kA, 300kA PFPB technologies based on the effective numerical simulation model and summarizing the successful and failing engineering and operation experience from 1996 to 2002. All above successful projects are praised as “miracles” in the aluminum industry of China.
In 2002, SAMI developed its 350kA pot technology called SY350 that has saved investment compared to its previous technologies and higher productivity. The first SY350 potline began operation in June 2002 in Henan province [1]. In the past five years, SAMI has been active in optimizing its SY350 technology and has made vast improvement. The Lanzhou SY350 potline was started in 15th May 2007 in Lanzhou branch CHALCO. Sixteen trial pots in this potline have increased to 402kA by the end of 2007. There is a total of 4 pots that utilize the same structure (include the cell, lining and superstructure) as the rest of the pot design of the potline.
The SY350 Technology Development
In 2002, SAMI developed its first generation SY350 pot technology and used the technology in the Henan Shenhuo smelter. The potline was started up in Aug 2005. The new generation SY350 was started in 15th May 2007 in Lanzhou branch CHALCO.
The goal of the new generation SY350 pot is to increase the anode current density and at the same time improve the pot technology performance (current efficiency, DC power consumption, etc). Further development work of the pot technology has led to the new generation SY350 pot technology, which was implemented at the Lanzhou branch CHALCO. The new generation SY350 pot
was preheated in 15th May 2007. Presently, the potline is running
at amperage of 378kA. The potline has high current efficiency and
lower energy consumption. SAMI and Lanzhou has planned to increase the line current to 400kA in the near future.
Figure 1: The first generation SY350 pot in Henan Shenhuo
smelter.
Figure 2: The new generation SY350 pot in Lanzhou branch
CHALCO.
SAMI has spent more than two years in pot modulating, pot operation practice, pot control system to improve the pot performance and increase the potline current. A lot of measurements such as pot shell temperature, shell deformation, magnetic fields, current distribution etc. have been performed
since the first SY350, SY300 pots start up.
Light Metals 2009 Edited by: Geoff Bearne TMS (The Minerals, Metals & Materials Society), 2009
The SY400 Pot Technology
There are 16 SY400 trial pots in the Lanzhou SY350 potline in
which additional current was added to the trial pots. Figure 3
shows a schematic diagram of SY400 trial pots section busbar
arrangement.
Figure 3. External busbar arrangement for the SY400kA trial pots.
The SY400 pot was preheated in June 2007. The current was
increased to 400kA in August 2007. After four months of
operation, the pots show high current efficiency and low energy
consumption. The pots are presently operating at 402kA. In the
future, the pot current will be increased to 420kA.
New Generation SY350/SY400 Pot Design
SAMI has been continuously optimizing the SY350 pot design
during the past 5 years according to the pot numerical modelling
and industrial tests.
Busbar
Pot operation has proven that correct and successful design of the
busbar in the first SY350 potline has been achieved in which the
busbar system was designed in an asymmetrical arrangement for
compensation of magnetic induction of adjacent pots. However,
SAMI has optimized the busbar arrangement to reduce the busbar
voltage and get more reasonable MHD stability in the subsequent
SY350 potlines. The SY350/SY400 pots have also shown high
stability in pot operation.
Figure 4. SY350 MHD modelling
Anode and Anode Assembly
There are 24 anode assemble blocks in each SY350/SY400 pot.
The anode pins used in the new generation pots are bigger than
the previous generation. Higher and slotted anodes are used in the
latest potline as well. The anode current density has increased to
0.815 A/cm2
Lining
Combined silicon nitride bonded silicon carbide bricks are used as
sidewall material for good heat dissipation and easier formation of
side ledge in all SY350/SY400 pots. The new generation SY350
pots utilize 35% graphitic cathode blocks. The SY400 trial pots
use three different cathodes, 35% graphitic, 100% graphitic, full
graphitized cathode blocks. The pot cavity of new generation
SY350/SY400 is much deeper than previous generation for the
purpose of automatic anode effect termination and more heat
emission area.
Pot Shell
The ship shape steel shell with cradle design was used in all
SY350/SY400 potlines, which was validated to supply enough
strength and reduce deformation for the pots. All the cradles and
heat dissipation fins were welded to the shell in the later
SY350/SY400 potline for more efficient heat dissipation to form
sufficient amount of ledge. The pot shell design of later
SY350/SY400 pots is deeper to give a deeper cavity and thicker
cathode blocks. These improvements ensured the reduction of
thermal load on the pot shell, and thus upgrades mechanical
behavior such that it has less maintenance.
Table 1 The technological comparison between the new and old generation SY350 pot technologies.
Item/smelter Old generation SY350
(Henan Shenhuo)1
New generation SY350
(Lanzhou branch CHALCO)
Start up 2004,8 2007,5
Number of SY350 pots 156 288
Operating current (kA) 348~356 378
Current efficiency (%) 94.15 >94%
DC power consumption kWh/t 13474 <13200
Anode effects per pot and per day < 0.3 0.08
Figure 5. Shell thermo-stress modelling.
Superstructure
A center point feeding system with a total of 5 feeders is installed on the SY350/SY400 pots. Feed volume has been reduced to 0.9 liter from 1.8 liter, which has been found to be advantageous for alumina dissolution. Pot hood and fume extraction are improved for greater efficiency.
Process Control
SAMI has developed the automatic control system called fuzzy control for nearly ten years. Adjustments are made and optimized accordingly to the different pot designs. Up till now, the pot control functions such as alumina concentration control, molar ratio control and bath temperature control are improved and optimized, so that the alumina concentration is controlled accurately in 1.5-2.5% range and AE coefficient is below 0.1 AE/pot/day. The fuzzy control has contributed significantly on the pot performance.
Pot Room
The pot room ventilation in the later SY350/SY400 potlines has been improved by new pot room architecture and higher operation floor. Optimizing these features has improved the air flow between pots and heat emission from the side of the pots for better working conditions in the pot room.
Figure 6.Potroom ventilation modeling.
Pot preheat and operation
Pot Preheat and Start-Up
The new generation SY350/SY400 pot technology uses resistor coke-bed to preheat pot. After 72 hours of preheating, the cathode bottom temperature would have increased to 850~950degrees Celsius in which then 12t of bath is poured into the pot cavity. Then 24 hours later, about 16t of liquid aluminium is added into the pot. Normal pot operation will commence about three months after start-up.
Lanzhou SY350 potline is divided into three sections, with each section comprising of 98pots. On the 15th May 2007, the first group (six pots) was started up using coke bed to preheat. The first group used dry-start method and the rest used wet-start method to start-up the pots. The first two sections was successfully started up in two months.
Line Current Increase and Pot Operation
The trial SY400 pots were started up from 350kA. After about three months, the line current was increased to 400kA in 15th September 2007. Four months into operation, the trial pots showed good stability. The shell temperature is less than 320degrees Celsius. The next target is to increase the trial pot to 420kA.
The SY350 pots were started up from 350kA. After about three months, the line current was increased to 378kA. An additional set of transformer and rectifier system was installed in order to provide the whole potline with the capacity of 400kA current.
Contrast to the western technology, the traditional Chinese pot has lower anode current density, reasonable technology performance. The high anode current density is more sensible. SAMI have done research on the SY400 pot operating practice. Some operating method and thoughts have been realized in order to get better pot performance. From eight months of tapping data, the current efficiency is about 94.16% and the average DC power consumption pot is below 13250kWh/t.
New SPC control software has been used to analyse the daily data. The foreman can get the information easily and carry out actions according to the new operation manual. Also, the manager can easily identify the status of the work operation.
Conclusion
SY350 technology has been improved and optimized since 2002 by SAMI. The latest SY350 potline is operating at 378kA. The SY400 trial pots have successfully been in operation for more than 4 months now.
The new SY350/SY400 technology is now validated and available for its performance and economy. SAMI will launch a new campaign to increase more current in the latest SY350/400 potline in the next year.
Reference
[1]Cheng Xiang, Jia Xinwu, Shen Shanming “Baking start-up and operation practice of SY350 pot ”, Page Light metal(china)
2005-3,32~35
铝电解的生产管理
铝电解的生产管理 一、现代预焙槽管理的思想与方法 (一)车间管理遵循标准化、同步化和均衡化的原则 1、标准化 最低应该为下列几类管理制定具体的标准: (1)技术标准与技术条件管理。 (2)设备与工具管理。 (3)生产计划与管理。 (4)操作质量管理。 (5)产品质量管理。 (6)生产调度指挥管理。 (7)数据检测(含收集、传递、分析、汇报)管理。 (8)各级人员的岗位责任制及考核管理。 (9)生产与技术会议管理。 (10)原材料与工器具供应管理。 2、同步化 电解车间每天所进行的作业都有固定的时间和程序,这是过程平稳所要求的,也是多功能天车作业能力所决定的。因此,一到某一时刻,所有参与作业的不同工种的操作者都
必须到达现场,并且在指定的时间内完成作业。 3、均衡化 均衡化指进入电解车间物流和从电解车间移出的物流均衡。“均衡”含有两重意义:第物流不能中断;第二,投入和产出都应保持在一定范围之内。维护投入产出的均衡是生产调度的重要内容。 (二)保持平稳 电解过程需要保持平稳和安定。所谓“平稳”包含两层意义:一是指保持合理技术条件不变动,少变动,即使变动也应尽量控制变动量,使变动幅度控制在槽自调能力所能接受的范围内,做到温度、电压、铝液高度波动小,槽帮规整稳定;二是指尽量减少来自操作、原料、设备带来的干扰,创造技术条件得以平稳保持的环境) (三)技术条件比操作质量更重要 (四)依靠铝电解系统、经量减少人工干预、确保人机协调(五)重视设备管理 电解的主要操作、技术条件的调整、物流的进出都是建立在设备正常的基础上,越现代化的工艺对设备的依赖性越强。有人讲,设备好坏是电解死或活的问题,工艺的好坏是指标高或低的问题。一句话,设备不正常,标准化、同步化、均衡化均为奢谈。 (六)重视全面质量管理(含过程改善)
电解槽管理的几点看法
电解槽管理的几点看法 我公司400KA系列电解槽经过一段时期的摸索和实践,技术条件已基本受控,在炉底干净的前提下,在低温、低电压、低铝水平、低效应系数控制下,电效显著升高,槽子稳定性明显提高。 电解槽在不断运行过程中,受人为作业因素(TAP、AC等)和供料因素的影响,易使物料和热平衡受到破坏,从而影响槽子稳定运行,这时电解槽外观有明显特征,尽早处理可使改变运行方向,如果置之不理,又可进一步恶化槽子,使得槽子出现沉淀,铝水平提高,进而影响垂直电流做功,增大水平电流,引发电压波动,造成槽子发病,所以要很有效的控制。结合我公司状况,目前最有效的是管理好电解工,教会其发现、处理异常的能力,高质量维护槽况,确保稳定运行,现结合我的工作实践浅谈一下我对如何管好电解工,教会其工作的几点看法: 第一,坚持“一个中心”。 即以巡视好槽控箱的工作状态及参数变化为中心。计算机是通过槽控箱对电解槽实施跟踪检查的,可以说槽控箱是我们控制管理电解槽的中心控制点,由于电解槽内部是由电流、氧化铝、阳极、电解质、阴极来共同维持,所以哪一部分出现问题都可能造成槽控箱误判,在出现问题时不能自我纠正,引起槽子发病。比如说,由于供料缺陷,某一点打击头夹住或不会下料,造成电解质中氧化铝浓度降低,致使槽子电压明显升高,计算机误判缺料,就会出现增量期下料增多,同时下降电压,这样以来可能使槽子出现局部下料过量,局部严重缺料,伴着计算机下降电压形成压槽,改变电解质成份,降低氧化铝溶解度,形成大量沉淀,影响槽子稳定。因此这时候如果电解工能巡视槽控箱,通过发现电压高,增量期长时间不变,
继而发现下料缺陷则可避免槽子发病。 第二,做好两个“基本”工作。 电解槽两项重要工作即保证电解槽下料系统和阳极工作的稳定。槽子热平衡和物料平衡也是基于阳极工作和下料正常进行的,电解阳极在不断更换的过程中,由于人为因素易造成阳极不正常工作,它所反映的就是局部过热,这样不利于电解稳定,冷热不均易造成槽子发病,因此要在不断运行过程中发现阳极问题,及时调整解决冷热问题;再一个就是下料问题,由于下料的不正常,可使槽子物料平衡受到破坏,使槽子过冷或过热,电解质成份发生变化,引发槽子沉淀,进而影响阳极工作。因此,下料和阳极稳定是槽子最基本工作,必须要抓实抓好。 第三,开展“三个分析”。 电解槽发病是由最初的异常引起,如若重视异常,则可能避免槽子发病,从异常到发病,必须要经历一段时间,若在此期间把握好了,则不可能会发病,所以应从以下三个方面来分析。 1、分析报表 报表显现的上一班槽子工作的情况代表了槽子一时期运行方面,因此把握好报表,掌握槽子运行动向,应以报表为主分析槽子电压情况、AE类型及情况、波动情况、RC情况、加料情况等来采取合理的措施,调整阳极和下料,引导槽子进入正常的运行轨迹是很有必要的。 2、分析槽子 正常电解是以火苗有为,电解质沸腾,两水平正常等来实现的,所以观察槽子,如出现了火苗黄、电解质沸腾不好、两水平不受控等,则表明该槽已发生异常,即便电压不摆也能反映出该槽的不稳定,因此对于槽子
电解槽管理的几点看1
400KA电解槽运行实践 我公司400KA系列电解槽于2009年投产,是当时全国为数极少的大型预焙电解槽系列,管理上并没有成熟的模式可供借鉴,仅有理论上的技术参数与160KA系列的经验可供参考。经过一段紧张而忙碌的摸索和实践,技术条件已基本受控,形成了“四低、一洁净”的成熟管理模式。槽子稳定性显著提高,槽龄已超过设定值且运行平稳,吨铝直流电耗大幅度降低(从14500kwh/t〃Al下降至12800kwh/t〃Al),电效有所升高(提升近1%)。 对于系列投产的大型预焙槽来说,日常技术条件管理是铝电解生产过程中的重要因素,科学的生产技术条件管理措施是维持铝电解生产稳定运行、获得良好经济指标与较长槽寿命的前提条件,因此选择最佳的技术条件进行控制是从事铝电解生产的广大技术人员的重要任务,现结合我的工作实践浅谈一下我如何管好电解工,教会其工作的几点看法:第一,坚持“一个中心”。 即以巡视好槽控箱的工作状态及参数变化为中心。计算机是通过槽控箱对电解槽实施跟踪检查的,可以说槽控箱是我们控制管理电解槽的中心控制点,由于电解槽内部是由电流、氧化铝含量、阳极熔融电解质、阴极来共同维持,所以哪一部分出现问题都可能造成槽控箱误判,在出现问题时不能自我纠正,引起槽子发病,比如说由于下料缺陷,某一点打击头夹住或不会下料,造成电解质中氧化铝浓度降低,致使形成电压明显升高,计算机误判缺料,就会出现增量期下料增多,同时下降电压,这样以来可能使槽子出现局部下料过量,伴着计算机下降电压形成减压槽,改变电解质成份,降低氧化铝浓度,形成大量沉淀,影响槽子稳定,因此这时候如果电解工能巡视槽控箱,通过发现电压高,增量增长时间不变,既而发现下料缺陷,则可避免槽子发病。当前,大部分铝厂使用国产氧化铝粉,流动性差,溶解慢,下料口处易堵料,打击头易长包,更增大了下料的不精确性,增加了增量期的多发、沉淀的生成,通过槽控箱的巡检增量期电压的高低,及时发现解决下料异常。 第二,做好“两个基本工作”。 电解槽两项重要工作:即确保电解槽下料系统和阳极工作的稳定。槽子热平衡和物料平衡也是基于阳极工作和下料正常进行的,电解阳极在不断的更换过程中,由于人为因素易造成阳极不正常工作,它所反映的就是局部过热,这样不利于电解稳定,冷热不均易造成槽子发病,因此要在不断运行过程中发现阳极问题,及时调整解决冷热的问题;再一个就是下料问题,由于下料的不正常,可使槽子物料平衡受到破坏,使槽子过热或过冷,电解质成份发生变化,引起槽子沉淀,进而影响阳极工作。因此,下料和阳极稳定是槽子最基本工作,必须要抓实抓好。
设备管理在企业发展中的重要意义
设备管理在企业发展中的重要意义 河南万基铝业股份有限公司二分厂杜耀青 电解铝厂高温、高磁、高粉尘,电解槽、整流机组、天车、铸机、空压机、袋滤器、工艺车辆等设备多样化,复杂化,特殊性,给设备管理工作带来了很多困难,如何做好设备管理工作?如何保证生产顺利进行?如何降低检修成本?如何节约能耗?……对这些问题,浅谈几点自己的看法。 一、设备管理的基本思路 “工欲善其事,必先利其器”。设备是企业经营活动的物质基础,设备管理与安全生产、产品质量、环境保护、节能降耗、经济效益密切相关,是企业科学生产,实现可持续发展的必要保证。设备管理的目的是向设备管理要质量,向设备管理要效益,向设备管理要环保,向设备管理要安全。由此可见在企业生产经营活动中做好设备管理工作尤为重要。 二、设备管理基础工作和方法 (一)抓制度建设 “无规矩不成方圆”,设备管理也是一样。首先,要根据需要制定相关的规章制度、工艺规程来约束和规范检修,使检修工作有法可依,有章可循,如《点检维护制度》、《检修工艺规程》、《设备完好标准》、《润滑制度》、《设备缺陷管理制度》、《设备巡检制度》、《设备改造更新管理制度》、《设备统计、考核制度》等。其次,在工作过程中检查规章制度及规程的执行情况,发现问题及时纠偏,对违规行为考核教育,随时间的转移,技术水平的提高,规程制度还要不断的适时修改、
补充、完善,使之更加科学准确的指导工作。 (二)抓计划落实 计划实质上是工作的准备。有一句俗话讲的好“计划不到一辈子穷”。一件工作能否顺利进行,与准备是否充分,计划是否得当,安排是否合理有很大关系。首先要科学的编制年度检修计划、技改计划,它是全年设备检修的钢领性文件,编制时还要注意机械与电气的配合问题。然后根据年度计划制定月计划,按月计划以周为时间段组织实施。计划在执行过程中要深入现场、深入实际,了解情况,沟通思想,解决问题,保证计划按时高标准完成。同时对设备运行中出现的问题要督促各车间解决,使设备达到优参数,满负荷运行。 (三)抓检修质量 没有合格的设备,就做不出合格的产品。没有高质量性能好的设备,企业的效益、安全、环保都是一句空话。首先,要依照规程的内容对设备进行检修维护,检修过程要按工艺要求进行检查、修理。其次,要监督检修过程,发现问题,纠正问题,尤其是主要设备、精密设备、大修设备,修前还要制定详细可行的方案及组织措施。设备修好后严格执行三级验收制度,按检修标准组织验收,确保“该修就修,修就修好”。 (四)抓成本控制 一个企业只有控制成本才能增加利润。一个人要节约不可以浪费。第一,树立“第一次就把事情做对”的理念,按规章制度办事,减少返工次数,提高效率,降低消耗。第二,领用备件要本着“当用不省,
伍德迪诺拉电解槽的特点
伍德迪诺拉电解槽的特点简介 伍德迪诺拉电槽是由伍德公司与迪诺拉公司共同组建的伍德迪诺拉公司生产的,其采用了伍德的电解槽技术和迪诺拉的电极技术,集成了两家公司各自的优点。伍迪电槽由若干个独立单元槽支撑在一个大型的钢支架上,再用顶杆螺栓压紧以解决单元与单元之间的导电问题。独立单元槽由阴极半壳、离子膜和阳极半壳,四周用螺栓密封组装而成。我公司采用的伍迪电槽的单元槽数量为216个,为单元槽数量最多的电槽。现将它的特点简单介绍如下: 一、单元槽的结构特点 1、复极式的阴极和阳极两种电极面对面组装,膜装在阴、阳极之间,外圆用法兰紧固密封自一体,垫片为聚四氟乙烯。这样在停槽检修时对槽内液体处理较方便。 2、使用带孔定距条,改善定距条处阳极液循环,离子膜不起泡,大大降低烧碱中的氯化钠含量,延长离子膜的使用寿命。 3、阳极由1mm的钛板冲压成C形阳极,这样极大地增大电极工作面积,使电流密度颁均匀,加快氯气的释放,增强了电极的机械强度。阴极由镍材制成与阳极同样大小的网状阴极。 4、阴、阳极液的进出口均在单元槽的底部,出口管内有一根插入单元槽的PTFE管将气液导出。 5、电流由导电接触条导入电槽,各个单元槽由紧固机构压紧,由于单元槽是独立密封,因此紧固力较小,通常以接触良好即可。 6、在单元槽顶部阴、阳极均设有收集渠,与槽顶部上倾结构结
合,使电解槽在停车检修时离子膜处于完全浸没状态,并且使阴极室与阳极室的压差波动极小。 7、阳极室设有降液板,使其保持内部自然循环。 8、阴极片与阳极片均采用了活性涂层。 二、电解槽特点 1、唯一的单一元件设计,泄漏小。 2、每个单元槽都设置细长的PTFE软管,确保泄漏电流的泄漏率小于0.01%。并且进出料软管都是透明的,使液体流动状况可见。 3、改变垫片的厚度可安装各种离子膜。 4、操作压力可达0.03MPa。 5、检修更换离子膜比较方便,每个单元槽只取一张膜,不影响其他单元槽,并且可预先装好。 6、垫片材质为PTFE,寿命优于橡胶垫片。 7、铜排配置简单。
电解槽的主要操作
电解槽的主要操作 中心下料预焙槽的主要操作有:定时加料(简称NB),槽电阻(电压)调整(简称RC),阳极更换(简称AC),效应熄灭(简称AEB),出铝(简称TAP),提升母线(简称RR)及边部加料作业(简称iRRFEED)。 NB、AC、TAP和RR作业是维持过程连续进行所必须的,但在作业后一段时间内,对热平衡、电流分布、磁场平衡方面将产生一定程度的干扰。 过程在进行中,系统内部会出现种种不平衡因素(例如槽膛变化引起极距的变动),还会碰到来自外界的各种干扰。为消除因系统内产生的不平衡和外界干扰因素而导致的不平衡需要进行RC、AEB和iRRFEED等操作。 无论何类操作都应讲究操作质量,使前一类操作对过程的干扰减到最小程度,使系统内外的不干衡因素通过后一类操作得到调整。 在160kA中心下料预焙槽上,NB、RC及TAP的下降电压动作由过程控制计算机、槽上的打壳下料装置和阳极升降装置自动完成,不需人工操作。AEB亦可由计算机、槽控箱程序及槽上上述装置自动实现,但是,由于成功率有限,尚需人工监视和辅助。AC、TAP、iRRFEED作业完全依赖于人工配合多功能天车才能完成。 本章叙述的主要是后两种依靠人工(或机械)完成或辅助完成的作业。 3.1 阳极更换 在160kA槽上换极周期为25天。 为了减少更换阳极作业对槽子行程的干扰,排出了换极顺序表。按此表换极可大体上保证阳极各区域的残极重量相等,电流分布的均衡。 换极期间,将残极提出槽外时刻起槽电压会少许上升,新极安装上槽后的扎边部和加极上Al2O3操作会使大约100kgAl2O3溶于电解质。此时,若不提示计算机,计算机则仍按常规处置,作出下降RC,并到时发NB命令。这样,阳极母线会在残极拔出后位置下降,而影响新极安装精度。同时,换极时溶入的物料已使电解质中的Al2O3超过了正常的浓度,这时再加料,就导致Al2O3过饱和而产生沉淀。 正确的做法是,换极前通知计算机,计算机便旁路RC,推迟下次NB时刻,并监视该槽电压变化。当电压明显上升一个值,之后又下降一个值时,计算机判断新极安装已经完成,于是恢复RC,(见图3.2(1)。如果其间电压变化值较小,不能确认时,计算机便在1小时后将RC恢复。 为了确保新极安装精度,现场可采用两种方法。 在多功能天车没有阳极定位装置的情况下,采用兜尺定位。该方法实质是用兜尺作为
大数据在电解槽管理中的应用
大数据在电解槽管理中的应用 发表时间:2017-11-17T14:14:16.110Z 来源:《防护工程》2017年第18期作者:宋晓文 [导读] 化学能源公司投资引进实时数据库系统,成功将DCS、PLC、手工点、计算点、质检分析等数据导入数据库中。 七冶压力容器制造有限责任公司贵州贵阳 550014 摘要:电解槽管理主要数据有:电解槽电压、电流效率、电耗、盐水质量、出槽盐水质量、成品碱质量等。本文主要介绍了利用大数据概念自主开发的电解槽数据库管理系统。该管理系统具备电解槽运行数据异常预警、DCS数据集成平台应用、长周期电解槽运行数据对比分析、异常工况原因快速分析等功能,实现了对电解的全面管控。对管理系统的具体应用进行了简要介绍。 关键词:大数据;电解槽管理;应用 1、电解槽信息管理库开发背景 某化学能源公司投资引进实时数据库系统,成功将DCS、PLC、手工点、计算点、质检分析等数据导入数据库中,实现DCS、PLC等数据与数据库数据同步记录。在数据库使用初期,生产技术管理人员并未能深刻理解数据库对生产管理工作带来的改变,仅是数据的初级采集、生产原始记录自动生成、运行数据统计及再次计算等简单工作,未能真正发挥实时数据库应用软件和数据结合的真正能力。为实现离子膜电解装置长周期稳定运行,该能源公司氯碱厂电解车间成立电解槽管理小组,对电解槽的运行进行持续性监控及周期性分析,及早发现电解槽运行过程中出现的异常,并控制异常,最终为电解槽的长周期运行提出行之有效的管理办法。 2、数据库及应用介绍 PI(PlantInformationSystem)是由美国OSIsoft公司开发的一套基于Client/Server结构的商品化软件应用平台,是过程工业全厂信息集成的必然选择。作为工厂底层控制网络与上层管理信息系统网络连接的桥梁,PI在工厂信息集成中扮演着特殊和重要的角色。 电解槽管理小组成员利用PI-processbook软件的功能和现有数据库的数据自动同步采集的特点,将所有电解槽运行相关数据进行集合、计算、程序设定,形成了一个用于访问数据库的固定程序,组成了电解槽数据库管理系统。数据库管理系统在开发过程中共设计显示界面45个,基层数据点1342个,数据计算点289个,对标曲线图302张,“一键巡检”界面4个。 利用PI-processbook软件强大的功能与数据库匹配后,实现了电解工艺DCS数据,质检分析数据,电解槽相关电压、电耗、电流效率的实时集成显示,并根据后台程序设定,实现每个数据在微小异常情况下自动预警的功能,大大缩减了操作监控人员的劳动强度,实现了电解槽的精细化管理。数据库系统具备了以下3个区别于其他电解槽管理软件的特点。通过大数据库的应用,电解槽管理实现了以下功能。 2.1智能巡检功能 (1)通过对电解工艺运行数据进行整合,形成4条线数据对标,异常数据自动闪烁和变色报警,无须逐条翻看曲线以及填写纸板记录发现异常数据,规避了人为判断异常数据的缺点。 在DCS操作画面中,60万t/a离子膜法烧碱生产线的日常巡检任务为每次巡检需要8个仪表工,点击鼠标至少1200次,记录数据240个,每班次每人都须重复巡检12次,并同时进行纸板记录的填写,来发现生产异常数据。 (2)智能巡检系统应用后,逐步取消纸板记录,无须逐条查看曲线,只须关注一个显示画面中异常报警的数据即能发现生产异常。 2.2大数据的时间纵横向和数据间交叉分析功能 2.2.1时间纵横向和数据间交叉分析法介绍 利用PI-processbook软件的多刻度功能和数据库的实时同步采集数据的功能,可以实现多个不同数据区域内的生产数据在同一个曲线图中显示,并能很直观地发现在某段时间内几个数据的变化趋势的相关性。 这对电解槽电压、电流效率、电耗等数据的变化原因的查找非常有用,在及时发现电解槽电压异常变化时,可以快速通过将所有影响电压的数据在几秒钟制取一个趋势图,通过趋势的相关性,即可快速判断影响电解槽电压异常变化原因。当然这种方法在查找氢氯气气相压力波动、其他温度、液位波动等所有相关性数据时都非常实用。 2.2.2电解槽电压检测监控 电解槽电压是检测电解槽运行状态的重要数据,该能源公司电解槽电压检测监控主要有3种。 (1)整流系统传感器电压显示。该值导入DCS显示,波动幅度较大,在2~20V之间,不能作为电压的监控。 (2)小组电压的监控。每6片单元槽为一组电压,该值导入DCS显示,显示准确、有效;但只能检测一组电解槽电压的变化,数据较多,不易于进行记录和分析,实现不了检测整台电解槽总电压的变化。 (3)人工检测。每2h检测1次电解槽总电压。检测时间不连续,受手持式检测设备和人为因素影响较大,而且很难检测短时间内电解槽电压的变化。检测处的数据需要按时记录,通过长时间记录的数据,进行分析电压的变化,分析和监控均较为滞后。通过软件功能开发后,将每台电解槽的22组小组电压显示值进行加和计算,实现了电解槽总电压的实时在线监控。 利用软件的快速制取曲线和多刻度功能,快速将影响电压变化的主要运行参数进行拉取,曲线显示槽温和精盐水温度与电压变化趋势正好相反,显示由于盐水温度下降4℃,造成了槽温的下降,从而造成电压上升。处理后,电压得到恢复。 2.3协助技术管理人员对电解槽运行长周期的分析和总结功能 大数据应用前,电解槽管理小组定期召开小组分析会议,针对电解槽运行状况进行评估,但受限于数据少、分析问题的方法少,只能抓住较大的异常问题进行分析,很难做到精细化的分析。项目实施后,电解槽管理小组通过应用电压总和的实时显示,以及自主创新的时间纵横向和数据间交叉分析的方法,对电解槽长周期的运行情况进行了分析。 通过分析发现了以下几个问题。 (1)利用管理系统对以往电压情况进行了分析,发现在2014年10月20—30日,4条生产线的电压均上涨0.5~0.8V。利用纵横向分析方法发现这段时间内精盐水中的杂质硅离子和铝离子质量浓度同时升高,分别由0.04mg/L、0.8mg/L升高至0.08mg/L、1.3mg/L;而其他运行数据均不具备与电压上涨的相关性。经过与离子膜开发单位的沟通与交流,发现盐水中这两种杂质虽然没有超出控制指标,但在达到一定值后,通过综合作用一样可以造成在离子膜内部的富集沉淀,造成离子膜电压在短时间内的上升。针对后期盐水质量的管控提出了
电解槽正常生产的主要技术参数
电解槽正常生产的主要技术参数 铝电解槽经过焙烧、启动和后期管理之后进入正常生产阶段,正常生产阶段的电解槽是在规定的电流强度下进行生产的。其特征是:电解槽的各项技术参数已达到了规定的范围建立了较稳定的电热平衡制度,阴极周围的侧壁上已牢固的形成电解质一氧化铝 结壳(俗称伸腿)构成了较好的炉膛内形,另外可看到阳极不氧化、不着火、阳极周围的电解质均匀沸腾,电解质与炭渣分离较好,阳极底下没有过量的沉淀,炉面结壳完整并覆盖一定数量的氧化铝保温。也就是说电解槽的正常生产是在一定的技术参数和常规作业制度的密切配合下实现的。 电解槽生产的技术参数是以电解槽的类型、容量和操作人员的技术水平而定。技术参数包括:槽工作电压、极距、电解温度、电解质成份(分子比)两水平、炉底压降、效应系数。 下面我们分别来讲各项技术参数在铝电解生产中的作用: 1、系列电流强度:每个电解系列都有额定的电流强度、额定的电压、与之对应有 一定的产铝量。额定的电流强度一经确定下来,尽可能保持恒定的电流强度不变, 以保证整个电解系列生产的稳定性。 2、槽工作电压:电解槽的工作电压由阳极压降(约0.34V)、电解质压降(约 1.57V)、阴极压降(约0.36V)、母线压降(约0.20V)、极化电压(约1.70V)、效应 分摊电压(约0.10V)。只随氧化铝浓度的变化而稍有变化。 槽工作电压随生产操作而变动,但极化电压和母线压降变化较小,只随氧化铝浓度的变化而稍有变化。变化较大的是阳极压降、电解质压降和阴极压降这三项也是维持电解温度热量来源的电压。其中电解质压降时刻在变化,所以平时工作电压的高低在某种意义上来说就是电解质压降的高低。因而工作电压对电解温度有明显的影响过高或过低保持电压都会给电解槽带来变化。 1 ?槽电压过高保持不但浪费电能而且电解质热量收入增多,会使电解槽走向热 过程,炉膛熔化、原铝质量受影响,并影响电流效率。 2.槽电压保持过低也不行,虽然最初因热收入减少可能会出现低温时的坏处,电解 温度低,电解质会下缩产生沉淀的机会增多,而形成结壳会使炉底电阻增加而发热,由冷行程转为热行程。其结果的损失,可能比高电压时要大的多,槽电压过低还可能造成压槽、滚铝和不灭效应等技术事故,因而在生产中决定各种情况下的槽工作电压的保持一定要谨慎。正常生产的槽电压应该时稳定的,如果出现波动应该查明原因及时处理。 3、极距:通常所说的极距是指阳极底掌到铝液镜面之间的距离。它既是电解过程 中的电化学反应区域又是维持电解温度的热源中心,对电流效率和电解温度有着直接影响。 1.提高极距:能减少铝的损失会使电流效率提高,也就是说能减少二次反应次数